DFMEA-底盘之制动系统零部件设计失效模式分析
设计失效模式及效应分析(DFMEA)

6
Development of a Design FMEA 设计FMEA的开始 设计 的开始
First Step of DFMEA: IDENTIFY DESIGN INTEND 第一步 : 确定设计意图 “Listing of what design is expected to do and what is expected not to do” “列出设计期望做什么和不期望做什么?
FMEA Date (Orig.) ______(Rev.)____ehicle(s)____________________
7
8 Core Team__________________________________________________________________________________________________________________________
Subsystem Level
Frame Function: –Provides stable attachment for seat support Potential Failure Mode(s) Structural failure seat support Excessive deflection of seat support Function: –Provides pleasing appearance Potential Failure Modes(s) Finish (shine)deteriorates Paint chips
Component Level Upper Frame
DFMEA(设计失效模式与效应分析)-20121123

※ RPN(風險順序數):計算並記錄糾正後的RPN值的結果。
14
設計FMEA分析步驟
15
設計FMEA嚴重度評估標準
16
設計FMEA發生率評估標準
17
設計FMEA難檢度評估標準
18
設計FMEA改善對策提出時機
The timing to provide solution / 提出改善對策之時機
以利追蹤
※ Planning Stage(設計階段):填上依據目前所進行分析標的物所處之開發階段 ※ Design Responsibility (設計責任):填入負責的設計與開發之工程師全名
※ Prepared By(編制者):填入負責編制DFMEA的工程師的姓名
※ Part Name/Program(系統、子系統或零部件的名稱及編號):填入適當的分析級別並
12
設計FMEA分析表說明(Ⅲ)
※ POTENTIAL CAUSE(S) / MECHANISM(S) OF FAILURE(失效的潛在原因或機理) :填入每一
個失效模式的所有可以想到的失效原因或失效機理。
※ DESIGN CONTROLS(現行設計管制):填入已經完成或承諾要完成的預防措施、設計確認
DFMEA(設計失效模式與效應分析)
Design Failure Mode and Effect Analysis
1
什麽是FMEA ?
※
FMEA是一種系統方法,使用制式表格及問題解決
方法以確認潛在失效模式及其效應,並評估其嚴重度、 發生度、難檢度(探測/偵測)及目前管制方法,從而計算
風險優先指數(RPN),最後採取進一步改善方法,如此
持續進行,以達防患失效模式及效應發生於未然
DFMEA-底盘-行车制动系各零件
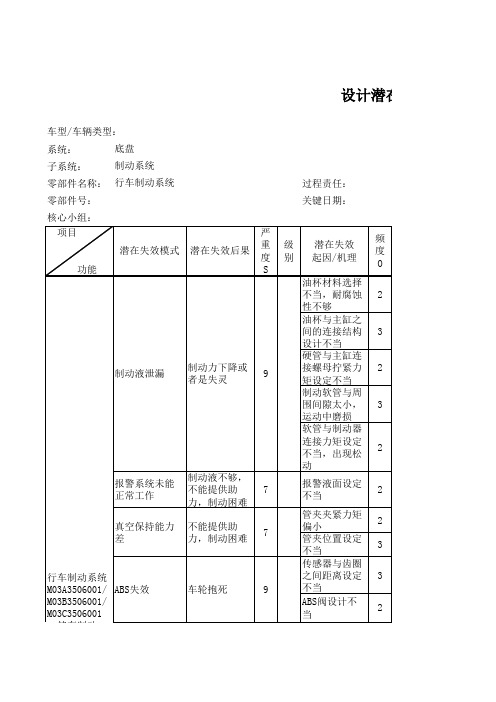
系统:子系统:零部件名称:过程责任:零部件号:关键日期:核心小组:液;·监控制动液液面高度;·辅助人力制动;行车制动系统设计潜在失(车型/车辆类型:底盘制动系统M03A3506001/M03B3506001/M03C3506001设计潜在失(系统:子系统:零部件名称:过程责任:零部件号:关键日期:核心小组:车型/车辆类型:底盘制动系统制动器系统:子系统:零部件名称:过程责任:零部件号:关键日期:核心小组:·向制动盘提供制动力·配合制动其提供制动力制动盘设计潜在失(车型/车辆类型:底盘制动系统系统:子系统:零部件名称:过程责任:零部件号:关键日期:核心小组:M03A3501011/号给制动尾灯车型/车辆类型:底盘制动系统制动踏板总成设计潜在失(系统:子系统:零部件名称:过程责任:零部件号:关键日期:核心小组:构中人力的直接作用对象;·提供制动信号给发动机ECU;·调节管路压力,分配制动力。
避免在制动时后轮先抱死侧滑,同时尽可能充分地利用附着条件,产生较大的制动力。
漏比例阀设计潜在失(车型/车辆类型:底盘制动系统系统:子系统:零部件名称:过程责任:零部件号:关键日期:核心小组:M03B3540100/M03C3540100/M03D3540100/M03E3540100·储存制动液;·提供助力辅车型/车辆类型:底盘制动系统带主缸真空助力器总成设计潜在失(比例阀比例阀进出油系统:子系统:零部件名称:过程责任:零部件号:关键日期:核心小组:制动主缸设计潜在失(车型/车辆类型:底盘制动系统带主缸真空助系统:子系统:零部件名称:过程责任:零部件号:关键日期:核心小组:车型/车辆类型:底盘制动系统真空助力器设计潜在失(系统:子系统:零部件名称:过程责任:零部件号:关键日期:核心小组:总成M03A3561130真空助力软管总成设计潜在失(车型/车辆类型:底盘制动系统·提供助力,辅助人力制动系统:子系统:零部件名称:过程责任:零部件号:关键日期:核心小组:ABS支架M03A3550210·安装固定ABS总成车型/车辆类型:底盘制动ABS支架设计潜在失(系统:子系统:零部件名称:过程责任:零部件号:关键日期:核心小组:M03A3561110/M03A3561150/M03B3561150·供油制动软管总成设计潜在失(车型/车辆类型:底盘制动系统:子系统:零部件名称:过程责任:零部件号:关键日期:核心小组:灵车型/车辆类型:底盘制动制动硬管总成设计潜在失(FMEA编号:编制人:修订人:第 1 页共 12 潜在失效模式及后果分析(DFMEA)附件6潜在失效模式及后果分析(DFMEA)附件6FMEA编号:编制人:修订人:第 2 页共 12FMEA编号:编制人:修订人:第 3 页共 12 潜在失效模式及后果分析(DFMEA)附件6FMEA编号:编制人:修订人:第 4 页共 12 潜在失效模式及后果分析(DFMEA)附件6FMEA编号:编制人:修订人:第 5 页共 12 潜在失效模式及后果分析(DFMEA)附件6FMEA编号:编制人:修订人:第 6 页共 12 潜在失效模式及后果分析(DFMEA)附件6FMEA编号:编制人:修订人:第 7 页共 12 潜在失效模式及后果分析(DFMEA)附件6FMEA编号:编制人:修订人:第 8 页共 12 潜在失效模式及后果分析(DFMEA)附件6FMEA编号:编制人:修订人:第 9 页共 12 潜在失效模式及后果分析(DFMEA)附件6FMEA编号:编制人:修订人:第 10 页共 12 潜在失效模式及后果分析(DFMEA)附件6FMEA编号:编制人:修订人:第 11 页共 12 潜在失效模式及后果分析(DFMEA)附件6FMEA编号:编制人:修订人:第 12 页共 12 潜在失效模式及后果分析(DFMEA)附件612 页果件6件6果12 页12 页果件6果12 页件612 页果件6果12 页件612 页果件6果12 页件612 页果件6果12 页件612 页果件6果12 页件6。
(DFMEA)汽车行业设计失效模式分析
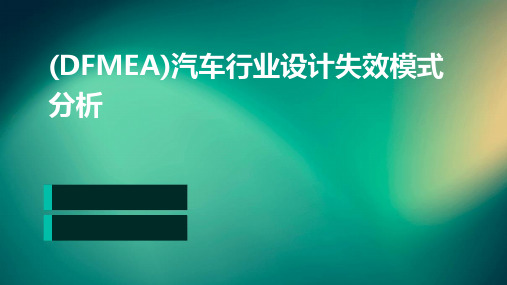
性能下降
随着使用时间的增加,发动机性能可能会逐渐下 降,导致汽车动力不足、加速缓慢等问题。这可 能是由于发动机内部零件磨损、燃油系统堵塞或 点火系统故障等原因引起的。
振动过大
发动机振动过大可能会对车辆的舒适性和稳定性 产生不良影响,同时也会增加零部件的磨损和疲 劳破坏。振动过大的原因可能包括发动机平衡性 差、零部件松动或损坏等。
不断更新表格,以反 映产品设计的更改和 改进。
确保表格内容完整、 准确,为后续分析提 供基础数据。
绘制设计流程图
01 详细绘制产品设计的流程图,包括各个组件的相 互关系和作用。
02 明确各个设计阶段的输入和输出,以便更好地理 解设计的整体流程。
03 分析流程图,找出可能存在的设计缺陷和失效模 式。
优化方法
采用先进的优化算法和仿真技术,对设计方案进行多目标优化。
优化过程
充分考虑制造工艺、材料特性等因素,确保优化方案的可行性。
提高制造质量
制造工艺
采用先进的制造工艺,提高零部件和整车的制造 精度和质量。
质量控制
建立严格的质量控制体系,确保每个环节的制造 质量符合要求。
质量检测
采用多种质量检测手段,如无损检测、功能检测 等,确保产品合格率。
03
基于影响评估,为每个故障模式制定相应的改进措施
和优先级。
03 汽车行业中的设计失效模 式
发动机系统
总结词
发动机系统是汽车的核心部分,其设计失效模式 主要表现在性能下降、过热、振动过大等方面。
过热
发动机过热是常见的失效模式之一,可能导致拉 缸、润滑油变质等严重后果。过热的原因可能包 括冷却系统故障、发动机负荷过大、散热器堵塞 等。
传动系统
DFMEA失效模式分析报告-范本

DFMEA失效模式分析报告-范本1. 引言本报告旨在对产品的DFMEA(Design Failure Mode and Effects Analysis,设计失效模式与影响分析)进行详细分析和评估。
通过DFMEA,我们可以识别潜在的设计问题,并采取相应的改进措施,以确保产品的可靠性和质量。
本范本报告将为您提供一个参考,以便在进行具体的DFMEA分析时提供方向和指导。
2. 设计失效模式与影响分析DFMEA是一种系统化的方法,用于根据设计和工程知识,识别并评估可能的失效模式及其对产品质量和性能的影响。
以下是DFMEA分析的步骤和关键要素:2.1 分析步骤1. 确定分析的设计元素或子系统。
2. 列出可能的失效模式。
3. 对每个失效模式进行评估,包括失效原因、失效对系统功能的影响和失效对其他部件的影响。
4. 根据评估结果,确定和优先级排序失效模式。
2.2 关键要素在DFMEA分析中,以下要素需要特别关注:1. 设计元素:将设计分解为适当的子系统或元素,以便更好地进行分析和识别失效模式。
2. 失效模式:失效模式是指产品在设计元素或子系统中可能发生的故障或失效情况,需要针对每个设计元素列出所有可能的失效模式。
3. 失效原因:为每个失效模式确定可能的原因,例如材料问题、制造过程问题或设计缺陷等。
4. 影响评估:评估失效模式对系统功能和其他部件的影响,包括性能降低、功能丧失或安全风险等。
5. 排序:根据评估结果,对失效模式进行排序,以确定需要采取的优先改进措施。
3. 报告结论通过对产品进行DFMEA分析,我们可以识别潜在的失效模式并确定相应的改进措施。
这有助于减少设计风险,提高产品的可靠性和质量。
然而,请注意,本报告仅为范本,具体的DFMEA分析需要根据实际情况进行定制。
4. 参考资料[1] AIAG. (2019). Potential Failure Mode and Effects Analysis (FMEA) (4th ed.). AIAG.。
DFMEA- 悬挂系统各零部件设计失效模式分析

系统:子系统:零部件名称:过程责任:零部件号:关键日期:核心小组:后悬架装置设计潜在车型/车辆类型:底盘悬架系统系统:子系统:零部件名称:过程责任:零部件号:关键日期:核心小组:车型/车辆类型:底盘悬架系统后轴焊接总成设计潜在系统:子系统:零部件名称:过程责任:零部件号:关键日期:核心小组:系统:子系统:零部件名称:过程责任:车型/车辆类型:底盘悬架系统后减振器带缓冲块总成设计潜在后螺旋弹簧设计潜在车型/车辆类型:底盘悬架系统零部件号:关键日期:核心小组:设计潜在系统:子系统:零部件名称:过程责任:零部件号:关键日期:核心小组:后减振器带缓冲块总成车型/车辆类型:底盘悬架系统系统:子系统:零部件名称:过程责任:零部件号:关键日期:核心小组:车型/车辆类型:底盘悬架系统后减振器带缓冲块总成设计潜在附件计潜在失效模式及后果分析(DFMEA)FMEA编号:编制人:修订人:第 1 页共计潜在失效模式及后果分析(DFMEA)FMEA编号:编制人:修订人:第 2 页共计潜在失效模式及后果分析(DFMEA)FMEA编号:编制人:修订人:第 3 页共计潜在失效模式及后果分析(DFMEA)FMEA编号:编制人:修订人:第 4 页共计潜在失效模式及后果分析(DFMEA)FMEA编号:编制人:修订人:第 5 页共计潜在失效模式及后果分析(DFMEA)FMEA编号:编制人:修订人:第 6 页共附件6共 6 页共 6 页共 6 页共 6 页共 6 页共 6 页。
DFMEA失效模式结果分析

目的
生產品設計開發初期, 分析產品潛在失效 模式與相關產生原因提出未來分析階段 注意事項, 建立有效的质量控制計劃
失效的定義 失效的定義
失效 :
– 在規定條件下(環境、操作、時間)不能完成既定
功能。
– 在規定條件下, 產品參數值不能維持在規定的上
下限之間。
– 產品在工作範圍內, 導致零組件的破裂、斷裂、
13)分 13) 分級
這個欄位用來區分任何對零件、子系統或系 統、將要求附加於制程管制的特殊產品特性 (如關鍵的、主要的、次要的)。 任何項目被認為是要求的特殊过程控制, 將 被以適當的特征或符號列入設計FMEA的分 级欄位內, 並將於建議措施欄位被提出。 每一個於設計FMEA列出的項目, 將在过程 FMEA的特殊过程管制中被列出。
12)嚴重度( 12) 嚴重度(S)
严重度是潜在失效模式发生时对下序零 件、子系统、系统或顾客影响后果的严 重程度(列于前一栏中)的评价指标。 严重度仅适用于后果 要减少失效的严重度级别数值,光能通 过修改设计来实现,严重度的评估分为1 到10级。
严重度的等级
严重度 评定准则:后果的严重度 无警告的 这是一种非常严重的失效形式,它是在没有任何失效预兆的情 10 严重危害 况下影响到行车安全和/或不符合政府法规 有警告的 这是一种非常严重的失效形式,是在具有失效预兆的前提下所 9 严重危害 发生的,并影响到行车安全和/或不符合政府法规 很高 车辆/系统不能运行,丧失基本功能 8
推荐的评估准则
(设计小组对评定准则和分级规则应意见一致,即使因为个别产品分析作 了修改也应一致) 失效发生可能性 可能的失效率 频度数 很高:失效几乎是不可避免的 ≥1/2 1/3 高:反复发生的失效 1/8 1/20 1/80 中等:偶尔发生的失效 1/400 1/2000 低:相对很少发生的失效 1/15000 1/150000 极低:失效不太可能发生 ≤1/1500000 10 9 8 7 6 5 4 3 2 1
DFMEA--设计潜在失效模式及后果分析(2)

效模式 之效應 功能
失效機制
嚴 重 性
等 級
發 預防性 生 頻 率
探測性
風 難險 檢優 度先
數
完成日期 已採取行動 風
嚴發難險 重生檢優 性度度先
數
9
10
11
12 13
14
15
16
17 18 19
20
21
22
9
FMEA表格
1. DFMEA 編號
➢ 文件編號,作為追蹤之用
2. 系統、次系統、零件的名稱和編號
6
開展DFMEA
列出設計目的 客戶的要求
➢ 產品要求 ➢ 製造要求 ➢ 裝配要求 …
7
開展DFMEA (續)
使用流程圖和方塊圖建立:
➢ 輸入訊息 ➢ 過程(功能) ➢ 可交付產品或輸出
表示主要的關係和邏輯順序
8
FMEA表格 – DFMEA
___ 系統 __________________
12. 嚴重程度(S)
➢ 評估潛在的失效效應的嚴重性 ➢ 發生的話,對客戶做成影響的程度 ➢ 對下個零件組、次系統或系統的影響
23
FMEA表格
12. 嚴重程度(S) (續)
➢ 應訂立公司的一套指標 ➢ 設計小組對 評定準則和分級規則應意見
一致,即使因為個別產品分析作了修改 也應一致 ➢ 只有進行設計更改,才可以降低嚴重程 度的排序指指標
➢ 應有FMEA的 初稿日期 和 最近修訂日期
8. FMEA小組
➢ 釐訂和/或執行任務的負責人、個人和 部門
➢ 最好為工作小組成員製作一份分發清單, 列出他們的姓名、部門和聯絡方法等
12
FMEA表格
9. 項目/功能
DFMEA设计失效模式及后果分析
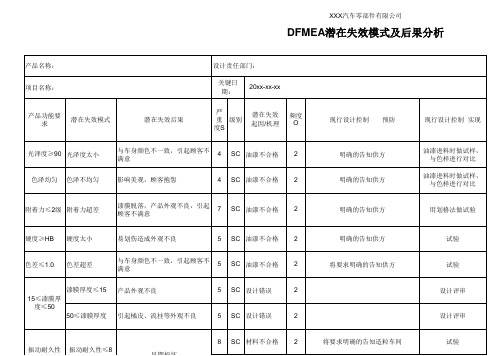
设计评审
3
设计评审
中间开口、 开孔或边沿 无尖角、无
尖边缘
中间开口、开孔 或边沿有尖角、
尖边缘
外观不良,易产生飞边,并导致 后期修整困难
6
圆柱、卡扣 座、安装筋 等结构强度
足够
圆柱、卡扣座、 安装筋等结构强 加强筋少、矮,壁厚太薄 度不够,易断裂
6
安装方便
安装困难 效率低、拆卸不方便
8 SC 材料不合格 2
耐高温性 不耐高温性 性能下降、强度下降发粘异臭味 8 SC 材料不合格 2
耐热循环性 能良好
耐热循环性能差 易变形、早期失效
耐振动性性 能良好
耐振动性性能差
易变形、断裂、脱落
振动性耐久 振动性耐久性能
性能良好
差
易断裂、早期失效
耐气候老化 耐气候老化性能
性能良好
差
变色、早期失效
试验验证
3
将窄、细、薄等部位加强
设计评审
3
将要求明确的告知造粒车间
试验验证
4
增加定位点
设计评审
3
将要求明确的告知造粒车间
试验验证
4
设计定位面、槽、柱等结构
设计评审
5
图样评审、数模验证
2
设计评审
2
设计评审
2
在三维数模进行面分析
设计评审
壁厚不能超过本体壁厚的1/3,最大不 3 能超过1/2。必须超过时,须对根部进
6
产品易于涂 装
产品难涂装 外观不良
6
尽量避免嵌 件结构 嵌件数量多
效率低、不安全、易损伤模具或 产品
6
嵌件不脱落 、不转动
DFMEA-底盘-驻车制动系各零件
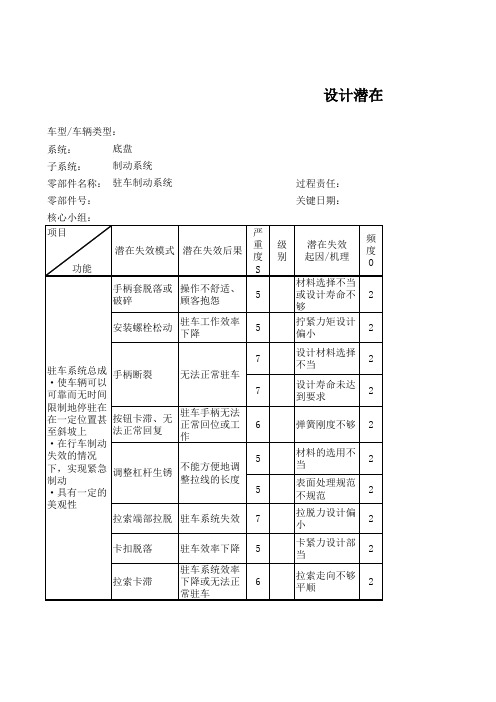
系统:子系统:零部件名称:过程责任:零部件号:关键日期:
核心小组:
驻车制动系统
设计潜在失
(
车型/车辆类型:底盘制动系统
系统:子系统:零部件名称:过程责任:零部件号:关键日期:
核心小组:
系统:
设计潜在失
(
车型/车辆类型:底盘
车型/车辆类型:底盘制动系统
驻车手柄总成
设计潜在失
(
子系统:零部件名称:过程责任:零部件号:关键日期:
核心小组:
系统:子系统:
零部件名称:过程责任:零部件号:关键日期:
核心小组:杆操纵作用力·连接驻车手柄和驻车制动器
车型/车辆类型:底盘制动系统
驻车拉线总成设计潜在失
(
驻车制动器总成
制动系统
FMEA编号:编制人:修订人:
第 1 页
共 4 页潜在失效模式及后果分析
(DFMEA)
附件6
附件6
FMEA编号:编制人:修订人:
潜在失效模式及后果分析
(DFMEA)
第 2 页
共 4 页潜在失效模式及后果分析
(DFMEA)
附件6
附件6
FMEA编号:编制人:修订人:
FMEA编号:编制人:修订人:
第 4 页
共 4 页第 3 页
共 4 页潜在失效模式及后果分析
(DFMEA)
附件6
页
页
页
页。
DFMEA设计失效模式及后果分析

盐雾试验
2 28
现行设计 控制探测
探 测 度 D
RPN
责任及目
措
建议措施
标完成日 期
实际完成 日期
采取措施
施 S
结 O
果 D
RPN
摩擦片开裂
制动力矩不够、使用 寿命短、客户抱怨
8
关 铆接压力设定过大, 键 导致摩擦片有裂纹
3
摩擦片强度分析
硬度检测 2 48
气压0.8MPa下,额定 制动力矩≥
摩擦系数低
制动力矩不够、客户 抱怨
潜在的失效模式及后果分析
项目名称 零件类型/过程 (或产品型号)
核心小组
制动器总成 总成
焊接类
DFMEA 编 号 责任部门
关键日期
第1 页 共1 页 DFMEA-GS-01 项目小组
编制日期
编制 修订日期
项目功能要求
潜在失效模式
潜在失效后果
严 重级 度别 S
潜在失效 起因/机理
频 度 现行设计控制预防 O
8
关 摩擦片配方设计不合
键
理
2
选择合适的摩擦片配方
性能试验
2 32
18000N.m;制动性 能符合标准
QC/T239-2015《行 车制动器技术要求 及台架试验方法》
滚轮孔磨损严重
制动力矩不够、使用 寿命短、客户抱怨
8
蹄销孔配合间隙 大
制动力矩不够、使用 寿命短、客户抱怨
8
关 键
淬火硬度设定不合理
3
关 蹄销孔轴配合间隙设
键 计不合理
2
有限元分析 结构分析
疲劳试验验证 3 72 量检具 3 48
中4.0性能要求;制 动18万次后疲劳强
DFMEA——设计失效模式和后果分析(一)
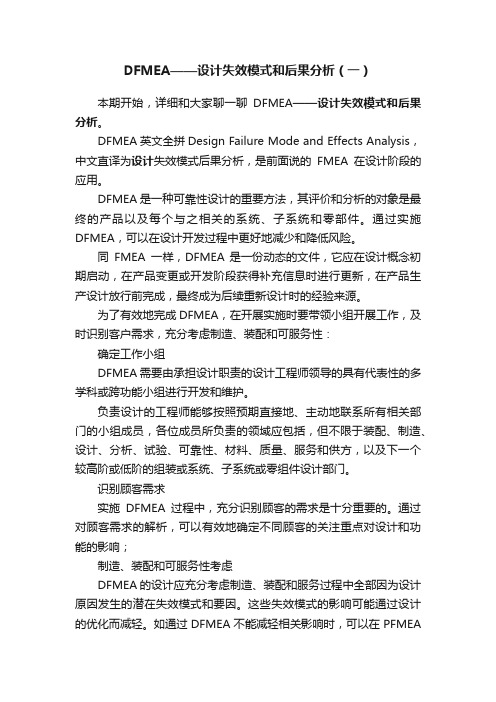
DFMEA——设计失效模式和后果分析(一)本期开始,详细和大家聊一聊DFMEA——设计失效模式和后果分析。
DFMEA英文全拼Design Failure Mode and Effects Analysis,中文直译为设计失效模式后果分析,是前面说的FMEA在设计阶段的应用。
DFMEA是一种可靠性设计的重要方法,其评价和分析的对象是最终的产品以及每个与之相关的系统、子系统和零部件。
通过实施DFMEA,可以在设计开发过程中更好地减少和降低风险。
同FMEA一样,DFMEA 是一份动态的文件,它应在设计概念初期启动,在产品变更或开发阶段获得补充信息时进行更新,在产品生产设计放行前完成,最终成为后续重新设计时的经验来源。
为了有效地完成DFMEA,在开展实施时要带领小组开展工作,及时识别客户需求,充分考虑制造、装配和可服务性:确定工作小组DFMEA需要由承担设计职责的设计工程师领导的具有代表性的多学科或跨功能小组进行开发和维护。
负责设计的工程师能够按照预期直接地、主动地联系所有相关部门的小组成员,各位成员所负责的领域应包括,但不限于装配、制造、设计、分析、试验、可靠性、材料、质量、服务和供方,以及下一个较高阶或低阶的组装或系统、子系统或零组件设计部门。
识别顾客需求实施DFMEA过程中,充分识别顾客的需求是十分重要的。
通过对顾客需求的解析,可以有效地确定不同顾客的关注重点对设计和功能的影响;制造、装配和可服务性考虑DFMEA的设计应充分考虑制造、装配和服务过程中全部因为设计原因发生的潜在失效模式和要因。
这些失效模式的影响可能通过设计的优化而减轻。
如通过DFMEA不能减轻相关影响时,可以在PFMEA或后续的风险分析中进行控制。
DFMEA实施的主旨不应仅仅依靠过程控制去克服潜在设计弱点,但它可以充分考虑在制造和装配过程中增加技术和物理限制,更好的识别和控制风险。
DFMEA 的开展应聚焦于交付于最终顾客产品、过程或服务的设计。
DFMEA设计失效模式及影响分析

创建设计清单
总结词
列出产品设计的所有组件和子系统
详细描述
根据设计目标,列出产品设计的所有组件和子系统,包括硬件、软件、机械、电子等部分,为后续分 析提供基础。
确定设计需求
总结词
明确各组件和子系统的功确其功能需求、性能指标和设计约束等,以确保产 品设计的合理性和可靠性。
DFMEA有助于发现潜在的设计缺陷和安全 隐患,从而采取措施避免对用户造成伤害 或损失。
降低产品开发成本
提高客户满意度
在产品设计阶段发现问题并进行改进,可 以避免在生产或测试阶段才发现问题而导 致的成本增加和时间延误。
通过提高产品质量和可靠性,增强客户对 产品的信任和满意度。
DFMEA的步骤和流程
制定改进措施
根据分析结果,制定相应的改进措施,并进 行实施。
分析评估
对每个失效模式进行严重度、频度和探测度 的评估,确定改进措施的优先级。
跟踪与验证
对改进措施进行跟踪和验证,确保问题得到 有效解决。
02 DFMEA的七个分析步骤
确定设计目标
总结词
明确产品的设计目的和预期功能
详细描述
在开始DFMEA分析之前,需要明确产品的设计目标,包括产品的主要功能、性能指标和适用范围等,以确保后 续分析的针对性和有效性。
随着人工智能技术的发展,未来 可能会有更加智能化的DFMEA工 具出现,能够自动识别和分析失 效模式。
与其他工具集成
DFMEA可以与其他设计工具和方 法集成,形成一个完整的设计流 程,提高设计的效率和可靠性。
跨学科应用
DFMEA不仅可以在机械、电子等 领域应用,也可以扩展到其他领 域,如生物医学、软件工程等。
和安全性。
03 失效模式分析
DFMEA设计潜在失效模式及后果分析

7
項目
潛在失 潛在失效
潛在原因/ 8 現行設計控制
建議行動 責任與目標
行動結果
效模式 之效應 功能
失效機制
嚴 重 性
等 級
發 預防性 生 頻 率
探測性
風 難險 檢優 度先
數
完成日期 已採取行動 風
嚴發難險 重生檢優 性度度先
數
9
10
11
12 13
14
15
16
17 18 19
20
21
22
8
FMEA表格
0.010 / 1000
發生度
10 9 8 7 6 5 4 3 2 132
FMEA表格
• 現行設計控制
➢ 現有的設計控制可以預防或驗證出該失效模式 及/或失效原因
➢ 一般可分為下 2 種設計控制
1.
的控制 2.
的控制
預防該失效模式/效 應/原因/機制出現 或減低出現頻次
用分析或測試方式, 可以失效模式/效應 /原因/機制出現前 偵查出來
➢ 是量度失效的風險指數 ➢ 數值愈高,代表風失效風險愈高 ➢ 應在設計發展過程前盡早完成控制
37
FMEA表格
• 建議行動
➢ RPN排序完成後,應該對排序最高的、 極為重要的項目首先採取行動
➢ 建議先處理高於 100分風險度的項目 ➢ 不論RPN指數為多少,應對一些高嚴重
性(S)的項目多加留意,例如S=9, 10
➢ 應根據公司過住的記錄,自行訂立指標 ➢ 設計小組對 評定準則和分級規則應意見
一致,即使因為個別產品分析作了修改也 應一致
31
發生度(O)的提議指標
失效發生的可能性
很高: 持續的ห้องสมุดไป่ตู้效 高: 反複發生的失效 中等: 偶然發生的失效
DFMEA设计失效模式与影响分析

用专业赋能创造价值上海蓝草企业管理咨询有限公司FMEA是QS9000/TS16949质量管理体系标准的一种重要的工具,是新产品设计开发和制程设计常用的分析技术,有降低损失、预防缺陷及减少变异与浪费之功效。
为可靠性工程中常用的手法,FMEA于1960年首此应用于航空工业中的阿波罗任务(Apollo),美国军方于80年代正式订为军方规范(MIL–STD-1629A)其目的在改善产品和制造的可靠性,在设计、生产阶段就可提升设计和制造的质量,降低损失成本,为近代常用手法之一。
自1992年由美国三大汽车公司推出以来,在全球各地得到了广泛应用。
掌握DFMEA之根本精神和用意,了解可靠性工程是在设计规划阶段就可以加以规划和改善的,并运用实例,使学员有学以致用的机会,亲自直接领略DFMEA之好处,并符合当代质量系统如TS16949/QS9000等。
培训特色:用客户或公司的产品为案例,学员以小组的方式,学习DFMEA;帮助学员学会真正将DFMEA作为产品设计工程师必需掌握的工具。
培训形式:小组讨论与发表、研讨、案例分析、情景仿真、自带企业资料现场诊断和实作对策、游戏、学员与学员交流、讲师与学员互动相辅而成、少讲理论多讲实践经验,要求学员在课堂结合本公司实际情况量身订做提出问题(可在课堂打断讲师思路),不是纯粹填鸭灌输,也不是研究客观案例,而是让学员体验执行过程,关注现场现实事例。
培训对象: 产品设计人员、系统设计人员、质量人员、质量工程师、产品采购人员、设计部门主管、厂长、可靠性工程师;直接负责过程标准化和改进的人员,那些直接负责引进新产品或新制造过程的人员。
培训教材:每位参加人员将获得一套我公司版权所有的培训教材。
课程时间:1天/6小时课程大纲:一、第五版FMEA的变化点与FMEA基本认识:1.第四版FMEA的变化点;为什么要变化?2.什么是FMEA? 什么是失效模式、什么是后果分析、FMEA过程和定义3.FMEA渊源,FMEA与可靠性,军工产品与汽车产品为什么强调可靠性?4.为什么需要FMEA?美国项目管理公理与失败成本5.风险管理与FMEA6.FMEA基本精神7.FMEA应用的三种实践:新产品、过程、管理系统8.FMEA类型、谁来做、实施时机二、什么是什么是产品设计和过程设计,过程设计与产品设计的差异在哪里?1.产品设计设计什么?产品设计输入和输出2.过程设计设计什么?过程设计输入和输出3.产品设计与过程设计的差异在哪里三、DFMEA进行步骤和案例分析1.DFMEA的简介2.进行DFMEA的步骤3.挑选跨功能小组成员4.确定范围:以设计文件(设计概念、初步设计或设计方案、或设计草案、设计图纸等)为依据,从功能、性能等方面的要求确定设计产品(系统、子系统、零部件)的定义,明确设计意图(如功能,要做什么,不要做什么)5.创建描述产品功能或结构的框图。
整车设计失效模式分析 DFMEA

3
设计评审
74/61/EEC; 按QC T 6271999汽车电动 门锁装置 按 GB 84102006测定; 按 GB 84102006测定; 按 GB 84102006测定;
不能有效的防盗
顾客财产遭损 失,顾客抱怨
8
T
3
设计评审
3 3 3
设计评审 设计评审 设计评审
顾客财产遭损 不能有效的防火 失,市场竞争 力下降
最高车速低 <170Km/h
顾客抱怨最高 车速低
7
I
3
加速时间长①(0 ~60km/h)>9s② (0~100km/h) 顾客抱怨加速 >20s ③ 时间长 40~ 100km/h>35s
S
9 动力系统不匹配 3
按GB/T 整车动力经济性 12544一90 测 计算 定;
最大爬坡度小 <30%
顾客抱怨最大 爬坡度小
灯光照度不够
影响行车安 全,违反法规
9
R
灯光照明系统设 计不合理 灯光指示和信号 报警系统设计不 合理 车身乘员舱区强 度不足 车身骨架前部强 度设计不足 车身骨架前部强 度设计过大 行驶系统设计不 合理
3
计算校核设计评 审
3
设计评审
3
CAE碰撞分析
碰撞试验;
R
碰撞后,不能对 乘员提供有效的 保护
乘员伤亡
潜在失效模式及后果分析 (设计FMEA)
项目名称: 车型年度/车辆: 核心小组: 过程功能 MPV
设计责任: 关键日期:
现行设计控制 潜在失效模式
( 潜在失效后果 S 严 )重 度
分 类
潜在失效起因/ 机理P
频 度
预防
DFMEA失效模式分析报告

DESIGN FMEA
产品名称:日期:
NAME:DATE:
客户产品型号:
CUSTOMER TYPE NO:
产品EP401M潜在失效模式及后果分析(设计FMEA)
子系统
潜在失效模式
潜在失效后果
严重度S
级别
潜在失效起因/机理
频度O
现行控制
探测度D
RPN
建议措施
责任及目标完成日期
措施结果
功能要求
3
54
无
LED灯(LED1-LDE5)
影响产品性能
2
3
1
零件认可产品试作产品验证
3
18
无
PCBA
EPON各项指标合客户要求
FLASH(U30)
影响产品性能
2
1
1.元器件一致性不足2.器件破损
2
1.元件降额使用,最小确保元件使用降额90% 2.要求所有器件严格测试
零件认可产品试作产品验证
3
12
无
DDR(U400)
影响产品性能
2
1
2
零件认可产品试作产品验证
2
8
无
网口接口(J2)
影响产品组装
2
1
2
零件认可产品试作产品验证
3
12
无
电源接口(J5)
影响产品组装
2
1
1
零件认可产品试作产品验证
3
6
无
变压器(T2)
影响产品性能
3
1
2
零件认可产品试作产品验证
2
12
无
结构器件
满足外观及结构要求
下壳
DFMEA失效模式分析
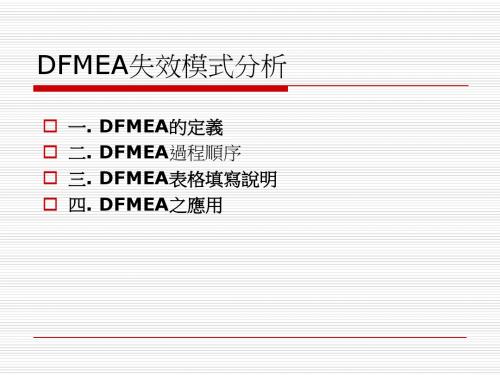
一. 二. 三. 四. DFMEA的定義 DFMEA過程順序 DFMEA表格填寫說明 DFMEA之應用
DFMEA的定義
DFMEA-----潛在失效模式及后果分析 DFMEA是一组系统化的活动,其目的是
发现、评价产品/过程中潜在的失效及其后果。 找到能够避免或减少这些潜在失效发生的措施。 对设计过程的完善。 在失效分析中,首先要明確產品的失效是什麼,對失效的產品進行分 析,找出零組件之失效模式,鑑定出它的失效原因,研究該項失效模 式對系統會產生什麼影響。 失效分析在找出零組件或系統的潛在弱點,提供設計、製造、品保等 單位採取可行之對策。 設計潛在DFMEA是由“設計主導工程師/小組”早期采用的一种技 術分析,在設計階段使用DFMEA,能夠降低產品的失效風險,有助于對 設計要求的評估及對設計方案的相互權衡。
風險優先數計算
風險優先數是嚴重度(S)、發生度(O)、和 難檢度(D)的乘積。 RPN=(S)(O) (D)
是一項製程風險的指標。當RPN較高時, 設計小組應提出矯正措施來降低RPN數。一般 實務上,會特別注意注意嚴重度較高之失效模 式,而不理會RPN之數值。
DFMEA過程順序
系統有那功能,特徵,需要條件? 會有那些錯誤? 發生錯誤會有多慘? 那些錯誤是什麼造成的?
發生之頻率?
有那些預防和檢測?
檢測方法能多好程度? 我們能做什麼? -設計變更 -過程變更 -特殊控制 -改變標準程序或指南
嚴重度評鑑表
(對顧客影響) (對製造/組裝影響) 當潛在失效模式結果發生在最終客戶和/或製造/組 當潛在失效模式結果發生在最終客戶和/或製造/組 裝過程時,最終客戶應該被優先考慮,並決定等級 裝過程時,最終客戶應該被優先考慮,並決定等級 非常高的嚴重級等級將危害機器或組裝作業員。當失 或無警告性而可能危及操作者(機台或組裝) 無警告 效模式影響到車輛操作安全和/或牽涉到違反政府法 的危險 規時,沒有警告產生。 非常高的嚴重等級將危害機器或組裝作業員。失效模 或無警告性而可能危及操作者(機台或組裝) 有警告 式影響到車輛操作安全和/或牽涉到違反政府法規 的危險 時,有警告產生。 嚴重瓦解生產線,100%產品須報廢;車輛無法操作, 或 100%的產品可能必須報廢,或車輛維修在維修部門 非常高的 喪失基本功能,客戶非常不滿意。 須花 1 小時以上。 輕微影響生產線,產品須篩選和部份報廢;車輛可以 或 100%的產品可能必須報廢,或車輛維修在維修部門 高的 操作,但降低功能等級,客戶不滿意。 須花 1/2 至 1 小時以上。 輕微影響生產線,部份產品須報廢;車輛可以操作, 低於 100%之產品,無選別報廢或在維修部門修車低於 適中的 但令人舒適或便利的項目無法運作,客戶會感受到不 1/2 小時時間。 舒適。 輕微影響生產線,產品須 100%重工;車輛可以操作, 或 100%產品必須重工或非線上的維修。 低的 但令人舒適或便利的項目無法運作,客戶有時會不滿 意。 輕微影響生產線,產品須篩選和部份重工;裝備整修 或產品必須抽驗不用報廢,和<100%之重工。 非常低的 或各種雜音造成不舒適,這些缺點大部分客戶都會發 現。 輕微影響生產線,部份產品在線上重工,裝備整修或 或少部份<100%的產品,必須重工不用報之,但是在 次要的 各種雜音造成不舒適,這些缺點可能被客戶發現。 觀察站外的線上。 輕微影響生產線,部份產品在線上重工,裝備整修或 或少部份<100%的產品,必須重工不用報之,但是在 非常次要的 各種雜音造成不舒適,這些缺點會被有經驗的客戶發 觀察站內的線上。 現。 沒有 沒有影響。 稍微困難的操作,或不影響。 影響 等級 10
汽车线束DFMEA设计失效模式和影响分析
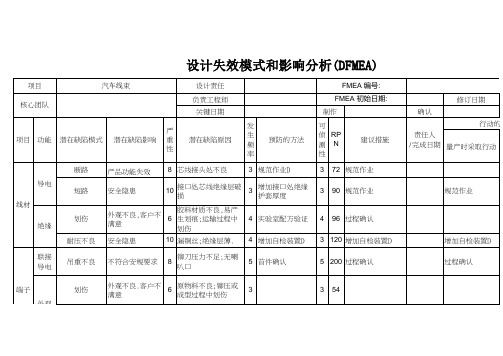
3 修模
1 18 过程确认
影响分析(DFMEA)
核准
行动的结果
严 重 性
发 生 频 率
可 侦 测 性
RP N
10 2 3 60
10 3 3 90 8 3 3 72
10 2 2 40 10 2 1 20
3 规范作业D
安全隐患
10
接口处芯线绝缘层破 损
3
增加接口处绝缘 护套厚度
外观不良,客户不 满意
6
胶料材质不良,易产 生划痕;运输过程中 划伤
安全隐患
10 漏铜丝;绝缘层薄.
4 实验室配方验证 4 增加自检装置D
3 72 规范作业 3 90 规范作业
4 96 过程确认 3 120 增加自检装置D
联接 导电
过程确认
pvc 胶壳
外观
不满胶
影响外观;严重时 产品失效
6
压力小;温度低;射速 慢;胶量少
3 实验室验证
4 72 过程确认
披锋
影响外观
膨胀
影响外观
合模线粗 影响外观
6
模具磨损; 压力大,胶良多
5 实验室验证;修模 3 90 过程确认
6 射速快
3 实验室验证
3 54 过程确认
6
模具磨损;上下模未 对齐
吊重不良
不符合安规要求
8
铆刀压力不足;无喇 叭口
5 首件确认
5 200 过程确认
端子 外观
划伤
外观不良.客户不 满意
6
原物料不良;铆压或 成型过程中划伤
3
3 54
修订日期 确认
行动的结 责任人 /完成日期 量产时采取行动
规范作业
增加自检装置D 过程确认
- 1、下载文档前请自行甄别文档内容的完整性,平台不提供额外的编辑、内容补充、找答案等附加服务。
- 2、"仅部分预览"的文档,不可在线预览部分如存在完整性等问题,可反馈申请退款(可完整预览的文档不适用该条件!)。
- 3、如文档侵犯您的权益,请联系客服反馈,我们会尽快为您处理(人工客服工作时间:9:00-18:30)。
系统:子系统:零部件名称:零部件号:
长
制动装置
车型/车辆类型:底盘制动系统
系统:子系统:零部件名称:零部件号:
·建立油压;·采集车轮转速·分配制动力;·产生行车制动力矩
Q00A35011311·配合制动其提供制动力
损,凹凸不平
前制动盘
车型/车辆类型:底盘制动系统
系统:子系统:零部件名称:零部件号:
车型/车辆类型:底盘制动系统制动踏板总成
系统:子系统:零部件名称:零部件号:
系统:子系统:零部件名称:零部件号:车型/车辆类型:底盘制动系统制动主缸
带主缸真空助力器总成
车型/车辆类型:底盘制动系统
系统:子系统:
零部件名称:零部件号:真空助力器
车型/车辆类型:
底盘
制动系统
系统:子系统:零部件名称:零部件号:
系统:子系统:零部件名称:
ABS支架
车型/车辆类型:底盘制动车型/车辆类型:底盘制动系统
真空软管管总成
零部件号:
系统:子系统:零部件名称:零部件号:失效
·供油
车型/车辆类型:底盘制动
制动管路装置
系统:子系统:零部件名称:零部件号:制动硬管总成
车型/车辆类型:底盘制动
系统:子系统:零部件名称:零部件号:车型/车辆类型:
车型/车辆类型:底盘制动真空泵
Q04B3506110/Q04B 3506210/Q06A3506320/Q06A3506420/Q04B3506310/Q04B
系统:子系统:零部件名称:零部件号:
真空度传感器
底盘制动
设计潜在失效模式及后果分析
(DFMEA)
过程责任:
关键日期:
设计潜在失效模式及后果分析
(DFMEA)
过程责任:
关键日期:
设计潜在失效模式及后果分析
(DFMEA)
过程责任:
关键日期:
过程责任:关键日期:
过程责任:关键日期:
度
制探测
O
起因/机理
设计潜在失效模式及后果分析
(DFMEA)
设计潜在失效模式及后果分析
(DFMEA)
过程责任:关键日期:设计潜在失效模式及后果分析
(DFMEA)
过程责任:关键日期:
过程责任:设计潜在失效模式及后果分析
(DFMEA)
设计潜在失效模式及后果分析
(DFMEA)
关键日期:
设计潜在失效模式及后果分析
(DFMEA)
过程责任:
关键日期:
设计潜在失效模式及后果分析
(DFMEA)
过程责任:
关键日期:
设计潜在失效模式及后果分析
(DFMEA)
过程责任:
关键日期:
设计潜在失效模式及后果分析
(DFMEA)
过程责任:关键日期:
附件6 FMEA编号:
编制人:
修订人:
附件6
附件6 FMEA编号:
编制人:
修订人:
附件6 FMEA编号:
编制人:
修订人:
附件6 FMEA编号:
编制人:
修订人:
附件6 FMEA编号:
编制人:
修订人:
日期
附件6 FMEA编号:
编制人:
修订人:
附件6 FMEA编号:
编制人:
修订人:
附件6 FMEA编号:
编制人:
修订人:
附件6 FMEA编号:
编制人:
修订人:
附件6 FMEA编号:
编制人:
修订人:
附件6 FMEA编号:
编制人:
修订人:
附件6
FMEA编号:编制人:修订人:。