OEE:设备整体效能概述(doc 4页)
OEE(设备整体效能)-

(Overall Equipment Effectiveness )
0
OEE
A. 导言
B. OEE概念
C. OEE模型与术语 D. OEE报表
E. OEE六大损失及改进
F. OEE应用及好处 G. 注意事项 H. 计算与练习 I. 组织结构与职责 J. 案例介绍
1
A1.导言
起源
价值操作时间
Q
Q
计划损失(公司认可损失)
停机损失(利用率)
性能损失 (表现率)
不良损失 周期时间╳合格品产量 (质量比率)
Q/G G/D Q/D Q/A ---OEE ---Sateration ---Utilization ---TEEP
OEE=价值操作时间 /计划生产时间 =利用率╳表现率╳质量比率 =Q/G Saturation饱和度 =计划生产时间 /可利用生产时间 =G/D Utilization=OEE ╳ Saturation=Q/D TEEP(Total effective Equipment Productivity)=Q/A
D1. OEE 报表说明
A TOTAL TIME(总时间) 公式 定义 B1 DAYS NOT WORKED(非工作日) B2 EXCEPTIONAL EVENTS(突发异常事件) 班 B LOSS FOR DAYS NOT WORKED(非工作日损失) B=B1+B2 长 C MACHINES NOT AVAILABLE FOR PRODUCTION(设备不能用于生产) TIME AVAILABLE FOR PRODUCTION(可利用生产时间) D=A-(B+C) 统 E1 NON PROGRAMMED(无计划) 设备没有计划用来生产的时间,实际的产能大于需求 计 假如没有代替的操作工,由于操作工休息而损失的时间(设备停机) E2 OPERATOR REST + UNION ALLOWANCES(员工休息) 员 假如没有代替的操作工,由于操作工就餐而损失的时间(设备停机) E3 CANTEEN(就餐时间) E PROGRAMMED MdO LOSS(计划性时间损失) E=E1+E2+E3 填 F1 PLANNED ABSENCE(无人员) 假如没有代替的操作工,由于操作工培训,会议等等而损失的时间(设备停机) 写 在工作时间内由于计划性维修活动导致的停机时间 F2 PREVENTIVE MAINTENANCE(预防性维护) F3 INDUSTRIALIZATION(工业化) 用来试验新产品,新工艺,技术改进,新产品预生产的时间 F ORGANIZATIONAL LOSS(组织性的损失) F=F1+F2+F3 TIME PROGRAMMED FOR PRODUCTION(计划生产时间) G=D-(E+F) H1 MACHINE BREAKDOWN(机器停机) 设备停机的时间(大于15分钟) H2 EQUIPMENT CHANGE & SET-UP(更换规格) 从最后一个合格产品生产结束到第一个新规格生产时间(停机时间+设定时间) H3 WORKING CYCLES(工作循环) 当程序停止后,设备的设定时间(工作开始/ 结束) H4 WAITING FOR MATERIAL(待料) 在正常生产中,设备由于缺料或器具而停机.包括使上游和下游的物料流通中断 H5 QUALITY(质量) 由于质量问题而损失的时间.(半成品问题/重修不合格品/直接导致停机的问题) H6 MATERIAL CHANGE(换料) 由于更换材料而损失的时间 H7 ABSENCE NOT PLANNED(非计划性停机 由于人员的缺席而导致的停机时间(旷工,迟到,早退等) H NON AVAILABILITY LOSS(不可利用损失) OPERATING TIME(操作时间) I=G-H K1 SPEED LOSS(速度损失) 指当设备的周期时间要比标准时间慢而产生的损失 K2 LOSS FOR MINOR STOPPAGES(小停机) 指任何低于15分钟的设备停机 K LOW PERFORMANCE LOSS(低表现损失) EFFECTIVE OPERATING TIME(有效操作时间) L=I-K M SCRAP LOSS(废品损失) DECLARED LOSS(明确损失) N=E+F+H+K+M NOT DECLARED LOSS(不明确损失) O=P-N TOTAL LOSS(总损失) P=D-Q VALUABLE OPERATING TIME(有价值的操作时间) Q=(R*T)/60 PRODUCTION - SCRAPS(生产的总产品-废品) SCRAP(废品) CAPACITY(产能) S=D*R/((D-E1) CYCLE TIME(周期时间) PRACTICAL OUTPUT (tyres/day/mach)(实际产能) U=1440*R/((D-E1)*60) AVAILABILITY(利用率) V=[(G-H)/G] PERFORMANCE EFFICIENCY(表现率) W=T*(R+M)/I QUALITY RATE(质量指数) X=R/(R+M) O.E.E Y=V*W*X=Q/G UTILIZATION(利用率) Z=Q/D
oee设备综合效率

OEE设备综合效率
生产效率在制造业中起着至关重要的作用,而OEE(Overall Equipment Effectiveness)设备综合效率是一个关键的评估指标。
本文将探讨OEE设备综合效率的定义、计算方法、影响因素以及提高OEE的策略。
1. OEE设备综合效率的定义
OEE是一个综合性指标,用于衡量设备在生产过程中的综合表现。
它综合考虑了设备的开动率、性能率和质量率,反映出设备的整体运行效率。
2. OEE的计算方法
OEE的计算方法为:OEE = 开动率 x 性能率 x 质量率。
其中,开动率指的是设备实际运行时间占总时间的比例,性能率表示设备运行速度与设计速度之比,质量率表示合格品数量与总产量之比。
3. OEE设备综合效率的影响因素
影响OEE设备综合效率的因素多种多样,包括设备故障率、设备维护计划、操作人员技能等。
有效管理这些因素对提高OEE至关重要。
4. 提高OEE的策略
4.1 定期维护
定期维护设备可以减少故障率,提高设备的可靠性和稳定性,进而提升OEE。
4.2 持续改善
不断优化生产流程和设备设置,引入先进技术和管理方法,可以提高设备的性能率和质量率。
4.3 操作人员培训
提高操作人员的技能和知识水平,可以减少操作失误,提高设备的开动率和生产质量。
结语
OEE设备综合效率是一个关键的生产效率指标,通过科学的管理和技术手段提高设备的OEE,可以提升生产效率、降低生产成本,实现制造业的可持续发展。
有效管理OEE,是企业迈向产业4.0的重要一步。
以上内容仅为理论探讨,实践中具体落地还需根据不同企业的实际情况和需求来进行调整和优化。
OEE设备综合效率

OEE的重要性
01
02
03
04
提高生产效率
通过提高设备的OEE,可以减 少设备停机时间、降低故障率,
从而提高生产效率。
降低生产成本
高OEE意味着更少的废品和更 高的产出,从而降低生产成本
机械和工艺性能。
良品率
03
指设备在生产过程中能够生产出合格品的比例,反映了设备的
质量控制能力和产品合格率。
02 影响OEE设备综合效率的 因素
设备故障与维护
设备故障
设备故障是影响OEE的重要因素之一 。定期维护和检查设备,确保其正常 运行,可以减少故障发生的概率。
预防性维护
实施预防性维护计划,定期更换磨损 部件,可以延长设备使用寿命,降低 故障率。
备件管理
建立完善的备件库存管理 制度,确保备件及时供应, 缩短设备维修时间。
优化生产计划与调度
均衡生产计划
合理安排生产计划,确保 设备在不同时间段内负载 均衡,避免设备过度使用 或闲置。
实时调度调整
根据生产实际情况,实时 调整生产计划和调度,确 保设备利用率最大化。
优先级排序
根据产品需求和设备能力, 合理安排生产优先级,提 高关键设备的利用率。
培育改进文化
通过培育改进文化,使员工树立起持续改进的意识,将改进工作融入 日常工作中,形成全员参与的氛围。
06 OEE设备综合效率的实际 应用案例
案例一:某制造企业的OEE提升
总结词
通过实施精益生产,提高设备利用率
VS
详细描述
该制造企业通过引入精益生产理念,优化 生产流程,减少浪费,实现了OEE的提升 。具体措施包括定期维护保养设备、采用 自动化技术减轻工人负担、制定合理的生 产计划等。这些措施有效地提高了设备的 利用率和生产效率,降低了生产成本。
OEE设备综合效率介绍

OEE设备综合效率介绍OEE的计算方式为:OEE = 设备利用率(Availability)× 性能率(Performance)× 质量率(Quality)设备利用率是指设备实际运行时间与计划运行时间的比值,表示设备的运行稳定程度;性能率是指实际生产数量与理论最大生产数量的比值,反映了设备运行速度和效率;而质量率则是指合格产品数量与实际生产数量的比值,代表了产品质量的好坏。
OEE的优点在于它同时考虑了设备的运行时间、性能和质量三个方面的指标,能够综合评估设备的整体生产效率,从而帮助企业发现生产过程中的瓶颈和问题,并及时采取改善措施。
另外,OEE还可以用来比较不同设备的生产效率,帮助企业选择合适的设备进行生产。
通过对OEE进行监控和分析,企业可以及时了解设备的运行情况,找出影响生产效率的问题和瓶颈,有针对性地进行改善和优化,从而提高设备的生产综合效率,降低生产成本,提升企业的竞争力。
因此,OEE在现代生产管理中具有非常重要的作用,是企业提高生产效率和管理水平的重要工具之一。
OEE(Overall Equipment Effectiveness)是一种广泛应用于制造业的关键绩效指标,它提供了一个全面的视角,帮助企业综合评估设备的生产效率。
通过OEE的监测和分析,制造企业可以更好地了解设备的运行状态,提高设备利用率、性能和产品质量,实现生产成本的优化和效率的提升。
首先,OEE可以帮助企业实现对设备利用率的提高。
设备利用率是指设备实际运行时间与计划运行时间的比值,它反映了设备的运行稳定性和生产中断的程度。
通过对设备的实际运行时间进行监测和分析,企业可以及时发现设备的停机原因和频率,以便有针对性地采取措施进行改善,如提高设备的维护保养质量、减少设备故障率、优化生产计划等,从而提高设备的利用率,减少生产中断,提高生产效率。
其次,OEE还有助于提高设备的性能。
性能率是指实际生产数量与理论最大生产数量的比值,它反映了设备的运行速度和效率。
OEE(设备综合效率)简介

完成停止时间+加班时间
加班时间 实际作业时间
负荷时间:为了完成生产计划、设备必须运转的时间
负荷时间 = 实际作业时间 - 计划停止时间
计划停止时间包含早晚例会、休息时间、始业点检、安全点检、
自主保全、体制展开、试作、计划停止时间等时间
利用时间= 负荷时间-停线时间
负荷时间 实际作业时间
停线时间:工具更换、调整、故障停止、上下流等待、
15
3. 启动/热机调整
• 定义:启动损失是指从设备启动到稳定生产期间发生的质 量损失,损失的大小取决于工序状态的稳定度,设备的 维护水平,操作工的技能水平等。
• 通常在实际生产中,这种损失量还是相当大的,应尽可 能减少到最小程度。
16
4. 短暂停机
• 定义:机器故障停工或换线以外的原因造成的计划停工所损 失的时间。 比如因工件卡堵、倾斜、掉落、污损、不良 警报等,必须进行少于十分钟的停机或空转予以处理的暂停 损失。另外如开工推迟/完工提前等)
OEE(设备综合效率)简介
2014年2月10日
OEE(设备综合效率)的定义
OEE是一个独立的测量工具,它用来表现实际的生产能 力相对于理论产能的比率。其本质就是实际合格产量 与负荷时间内理论产量的比值。
国际上对OEE的定义为: OEE是Overall Equipment Effectiveness的缩写 ,翻 译为设备综合效率,也叫设备整体效率。
14
2. 更换品种(换线)
• 定义 :未经调整的全速的由最后一件产品转入另一种产品的运 作,设备全速运转情况下最后一件良好的产品到另一种第一件 良好的产品间的时间。
• 通过操作员预定系统来测量
• 应对措施 – 运用SMED方法来缩短换线时间(包括运转中更换原材料, 如用新线) – 通过业绩管理来按照标准监控换线时间是否合格 – 实施持续改善行动
OEE:设备整体效能概述

OEE:设备整体效能概述引言OEE,即设备整体效能(Overall Equipment Efficiency),是一种用于衡量设备运作效率和生产效果的指标。
它是一个综合性指标,可以帮助企业评估设备的稳定性和效率,发现生产线的瓶颈,并做出相应的改进。
本文将介绍OEE的定义、计算方法以及应用,并探讨如何通过OEE来提高设备的整体效能和生产效率。
1. OEE的定义OEE是一个包含三个维度的综合指标,分别是设备的可用时间、性能和质量。
这三个维度反映了设备在生产过程中的故障、速度限制以及产品质量问题,是评估设备运营效率的基础。
•可用时间(Availability)指设备在计划生产时间内的实际工作时间占比。
也就是说,设备的可用时间包括了正常运行时间以及计划性维护时间,但不包括非计划性停机时间(如故障停机)。
•性能(Performance)指设备在实际运行中的生产速度相对于理论最佳速度的比例。
这一维度用于衡量设备在生产过程中的速度限制,例如调整时间、小停机和速度丧失等。
•质量(Quality)指设备在生产过程中合格产品的比例。
这一维度用来评估设备在生产产品时的质量问题,包括废品产生的数量和产品的非标准品率。
OEE的计算公式为:OEE = Availability × Performance × Quality2. OEE的计算方法要计算设备的OEE,我们需要收集以下数据:•设备的可用时间(Total Production Time):即计划生产时间减去计划性维护时间。
•设备的实际工作时间(Operating Time):可用时间减去非计划性停机时间(如故障停机)。
•实际生产数量(Total Good Count):合格产品的数量。
•理论生产数量(Maximum Possible Count):设备在理论最佳状态下的生产数量。
•废品数量(Total Reject Count):废品或非标准品的数量。
最新OEE(设备综合效率)简介
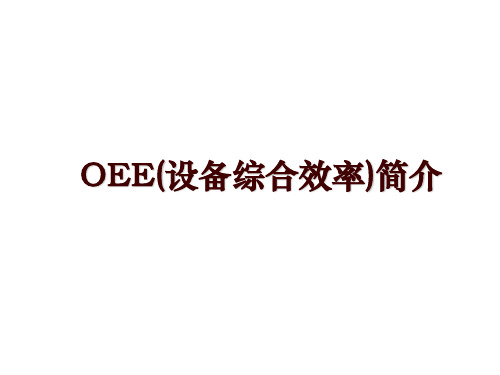
= (产量×实际速度)/利用时间
• 设备性能率
= 速度开动率×净开动率 = (产量×设计速度)/利用时间
*需按照不同设计速度的规格折算
名词说明
计划作业时间=从事生产活动的时间 (上,下班时间)减去午休时间
作业时间 计划作业时间 午休时间
实际作业时间= 计划作业时间-生产
生产完成停止时间
计划不均衡 : 前后计划中由于别的因素引起的作业停止或 者担当设备后工程(设备)的生产数量或者目标 量已达成而停止情况的时间
其 它 : 由以上原因以外的原因引发的设备停止时间
设备综合效率的应用
(1) 适用对象
作业对象 设备 设备 + 人
人
适用范围 一定适用 部分适用 适用不了
备
注
以设备效率为参照的生产力管理
1.计划性停机和试车 2.无生产订单
操作时间
计划性 停产时间
负荷时间
用餐 时间
(有效)利用时间
停机损失
1.故障 2.更换品种 / 清洁
/ 调节/刀具调整 3.启动 / 热机、调整
设备综合效率
时间利用率
净利用时间 性能损失
创造价值 缺陷 的时间 损失
4.短暂停机 / 空转 5.速度减慢损失
6.质量缺陷返工
15
3. 启动/热机调整
• 定义:启动损失是指从设备启动到稳定生产期间发生的质 量损失,损失的大小取决于工序状态的稳定度,设备的 维护水平,操作工的技能水平等。
• 通常在实际生产中,这种损失量还是相当大的,应尽可 能减少到最小程度。
16
4. 短暂停机
• 定义:机器故障停工或换线以外的原因造成的计划停工所损 失的时间。 比如因工件卡堵、倾斜、掉落、污损、不良 警报等,必须进行少于十分钟的停机或空转予以处理的暂停 损失。另外如开工推迟/完工提前等)
OEE(设备整体效能)-

B1 非工作日 设备关闭的天数,或者用当月的天数减去成型车间运行的天数
B2 突发异常事件 工作的天数与工厂运营的时间差异。这个差异可能是由罢工,临时解雇,暂停工作,缺乏能源以及考虑的但没有工作的天数。 加班和额外的天数(在计划中没有预见的天数)需要减去。
C 设备不可用于生产 这部分指的是设备由于(试验,调试,升级,检修,移动)等原因不能用于正常生产的时间
T 周期时间-生产单位产品所需要的时间
7
D1. OEE 报表说明
A TOTAL TIME(总时间)
公式
定义
B1 DAYS NOT WORKED(非工作日)
B2 EXCEPTIONAL EVENTS(突发异常事件)
班
B LOSS FOR DAYS NOT WORKED(非工作日损失)
B=B1+B2 长
背景
随着市场竞争的日益激烈,制造商要想持续获得高的经济效益,最大化地挖掘和改善生产车间的生产效率 显得极其重要,在某些方面,它甚至成为企业是否可以赢利的决定性因素。然而,在现在的制造业中,看似 良好运作的生产车间实际上并没有以最好的状态进行工作,设备和操作人员的价值存在很大的改善空间,这 无形中为企业带来了巨大的损失。为了解决这一问题,国际制造业提出了全局设备效率(OEE)的概念。
H6 MATERIAL CHANGE(换料) H7 ABSENCE NOT PLANNED(非计划性停机 H NON AVAILABILITY LOSS(不可利用损失)
填 由于更换材料而损失的时间 由于人员的缺席而导致的停机时间(旷工,迟到,早退等)
写
I OPERATING TIME(操作时间)
I=G-H
L=I-K
M SCRAP LOSS(废品损失)
OEE简介

工厂整体效率
评估整体绩效
OEE可以用来评估整个工厂或生产车间的绩效,通过计算工厂或 车间的可用性、性能和质量,反映工厂或车间的整体效率。
对比不同工厂或车间
通过比较不同工厂或车间的OEE,可以评估不同工厂或车间的效率 水平,找出需要改进的环节。
改进生产管理
通过对工厂或车间的OEE进行监测和分析,可以发现生产管理中的 问题和浪费,进而进行改进。
OEE简介
汇报人: 日期:
目录
• OEE定义及意义 • OEE的应用场景 • OEE的改善方法 • OEE的实践案例 • OEE的未来趋势
CHAPTER 01
OEE定义及意义
OEE的定义
设备综合效率(Overall Equipment Effectiveness,简称OEE)是一种衡量设备 性能、产量和质量的指标,它通过将设备的实际产量与理论产量进行比较,以评 估设备的整体效率。
某食品制造企业OEE提升案例
总结词
某食品制造企业通过引入自动化生产线、加强品质管理 和实施5S管理等方法提高OEE。
详细描述
该企业在生产线上引入了自动化设备,提高了生产效率 和产品质量。同时,该企业加强了品质管理,通过严格 的质量控制标准和流程,减少了产品不合格率。此外, 该企业还实施了5S管理,即整理、整顿、清洁、清洁检 查和素养,提高了生产现场的秩序和卫生状况。这些措 施使得该企业的OEE得到了显著提升。
CHAPTER 05
OEE的未来趋势
智能化OEE监控与管理
实时监控
01
通过物联网技术和传感器,实现对设备运行状态的实时监控,
及时发现异常情况并进行预警。
数据分析
02
利用大数据和人工智能技术,对设备运行数据进行分析,提供
整体设备效率(OEE)综述

质量
质量 损失
可用性
McKinsey & Company
| 7
目录
▪ ▪ ▪
定义和效果
计算方法
减少亏损
– 计划闲置时间 – 换模
– – – – –
故障
小停机 速度损失 废品 返工
▪
总结及要点
McKinsey & Company
| 8
减少计划停机时间的损失
OEE 百分比
113 13
不计名客户实例
有必要减少计划停机 时间,从而提高可用 时间
减少换模损失
不计名客户实例
减少换模损失 OEE 百分比
113 13 100 4
换模损失中包括 设备启动损失
94.5 1.5 28
实际OEE 的51%
14
52.5 2.5 1
49
总时间 计划闲置 可用 时间
故障
换模
操作 时间
小停 机
速度 损失
运作 时间
废品
返工 有效时间
可用性损失
性能损失
质量损失
McKinsey & Company
14
52.5 2.5 1
49
总时间
可用 计划 停机时间 时间
故障
换模
操作 时间
小停 机
速度 损失
运作 时间
废料
返工 有效时间
可用性损失
性能损失
质量
McKinsey & Company
| 17
透过设备状况的改善来减少速度损失
过去
现在
马达布满灰尘且没有过滤器
马达清洁干净且装有空气滤芯
改善行动
对OEE的影响
什么是整体设备效能(OEE)?
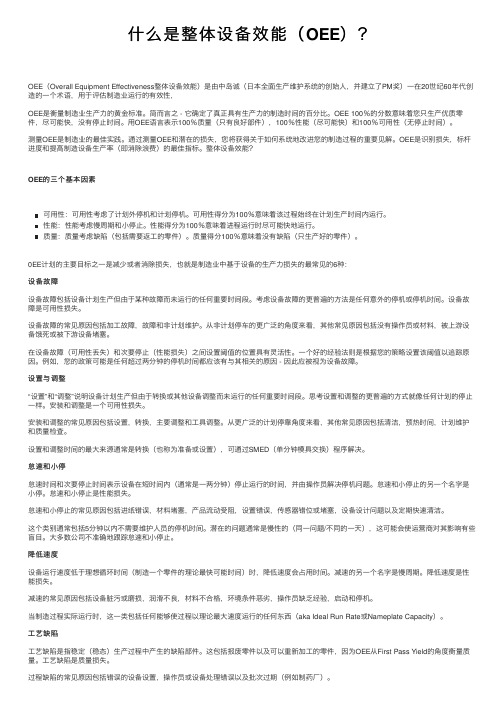
什么是整体设备效能(OEE)?OEE(Overall Equipment Effectiveness整体设备效能)是由中岛诚(⽇本全⾯⽣产维护系统的创始⼈,并建⽴了PM奖)⼀在20世纪60年代创造的⼀个术语,⽤于评估制造业运⾏的有效性,OEE是衡量制造业⽣产⼒的黄⾦标准。
简⽽⾔之 - 它确定了真正具有⽣产⼒的制造时间的百分⽐。
OEE 100%的分数意味着您只⽣产优质零件,尽可能快,没有停⽌时间。
⽤OEE语⾔表⽰100%质量(只有良好部件),100%性能(尽可能快)和100%可⽤性(⽆停⽌时间)。
测量OEE是制造业的最佳实践。
通过测量OEE和潜在的损失,您将获得关于如何系统地改进您的制造过程的重要见解。
OEE是识别损失,标杆进度和提⾼制造设备⽣产率(即消除浪费)的最佳指标。
整体设备效能?OEE的三个基本因素0EE计划的主要⽬标之⼀是减少或者消除损失,也就是制造业中基于设备的⽣产⼒损失的最常见的6种:设备故障设备故障包括设备计划⽣产但由于某种故障⽽未运⾏的任何重要时间段。
考虑设备故障的更普遍的⽅法是任何意外的停机或停机时间。
设备故障是可⽤性损失。
设备故障的常见原因包括加⼯故障,故障和⾮计划维护。
从⾮计划停车的更⼴泛的⾓度来看,其他常见原因包括没有操作员或材料,被上游设备饿死或被下游设备堵塞。
在设备故障(可⽤性丢失)和次要停⽌(性能损失)之间设置阈值的位置具有灵活性。
⼀个好的经验法则是根据您的策略设置该阈值以追踪原因。
例如,您的政策可能是任何超过两分钟的停机时间都应该有与其相关的原因 - 因此应被视为设备故障。
设置与调整“设置”和“调整”说明设备计划⽣产但由于转换或其他设备调整⽽未运⾏的任何重要时间段。
思考设置和调整的更普遍的⽅式就像任何计划的停⽌⼀样。
安装和调整是⼀个可⽤性损失。
安装和调整的常见原因包括设置,转换,主要调整和⼯具调整。
从更⼴泛的计划停靠⾓度来看,其他常见原因包括清洁,预热时间,计划维护和质量检查。
OEE(设备整体效能)

面反映设备的综合表现。
03
OEE的计算公式为:OEE = 时间利用率 * 性能指数 *
质量指数。
OEE的重要性
01
02
03
提高生产效率
通过提高设备的OEE,可 以减少停机时间和浪费, 提高生产效率。
降低生产成本
OEE的提高意味着设备利 用率的提高,从而降低生 产成本。
提高产品质量
通过提高设备的性能和效 率,可以减少不良品和废 品,提高产品质量。
OEE的组成部分
时间利用率
01
衡量设备可用性的指标,反映了设备在计划停机时间和非计划
停机时间内的表现。
性能指数
02
衡量设备性能的指标,反映了设备在单位时间内完成的有效工
作量。
质量指数
03
衡量设备生产出的产品质量水平的指标,反映了设备生产出的
产品合格率。
02 影响OEE的主要因素
设备故障
故障频率
备件管理和库存优化
合理管理备件库存,确保备件供应及时可靠,减少因备件不足或等 待时间过长而导致的停机时间。
THANKS FOR WATCHING
感谢您的观看
通过实验和数据分析,优化设备运行参数, 提高设备运行效率。
自动化与智能化
引入自动化和智能化技术,减轻人工操作负 担,提高设备运行精度和稳定性。
工艺改进
不断改进和优化工艺流程,提高产品质量和 生产效率。
标准化操作
制定标准操作规程,规范操作人员的操作行 为,确保设备稳定运行。
提升产品质量控制
严格把控原料质量
制定改进计划
根据数据分析结果和改进措施,制定详细的改进计划, 包括改进目标、实施步骤、时间安排等。
实施改进计划
OEE(设备综合效率)
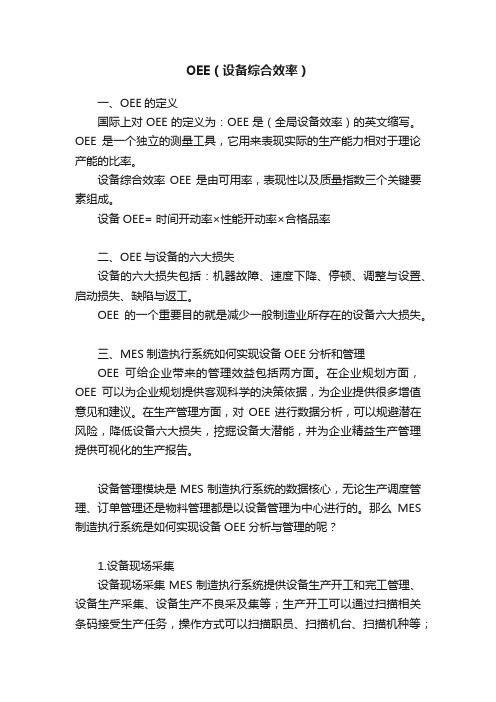
OEE(设备综合效率)一、OEE的定义国际上对OEE的定义为:OEE是(全局设备效率)的英文缩写。
OEE是一个独立的测量工具,它用来表现实际的生产能力相对于理论产能的比率。
设备综合效率OEE是由可用率,表现性以及质量指数三个关键要素组成。
设备OEE= 时间开动率×性能开动率×合格品率二、OEE与设备的六大损失设备的六大损失包括:机器故障、速度下降、停顿、调整与设置、启动损失、缺陷与返工。
OEE的一个重要目的就是减少一般制造业所存在的设备六大损失。
三、MES制造执行系统如何实现设备OEE分析和管理OEE可给企业带来的管理效益包括两方面。
在企业规划方面,OEE可以为企业规划提供客观科学的決策依据,为企业提供很多增值意见和建议。
在生产管理方面,对OEE进行数据分析,可以规避潜在风险,降低设备六大损失,挖掘设备大潜能,并为企业精益生产管理提供可视化的生产报告。
设备管理模块是MES制造执行系统的数据核心,无论生产调度管理、订单管理还是物料管理都是以设备管理为中心进行的。
那么MES 制造执行系统是如何实现设备OEE分析与管理的呢?1.设备现场采集设备现场采集MES制造执行系统提供设备生产开工和完工管理、设备生产采集、设备生产不良采及集等;生产开工可以通过扫描相关条码接受生产任务,操作方式可以扫描职员、扫描机台、扫描机种等;生产数据采集MES系统支持手动汇报和自动汇报模式,手动采集通过MES制造执行系统小键盘输入生产数量、停工时间、停工原因(扫描停工原因条码),自动采集通过生产设备自动采集生产数量、停工时间等信息。
2.设备异常呼叫管理MES制造执行系统提供Andon功能,当生产出现异常时,操作员通过MES制造执行系统可以直接按下安灯按钮,激活Andon系统,该信息通过操作工位信号灯、Andon看板、广播将信息发布出去,提醒所有人注意;同时记录异常发生开始的时间;班组长响应MES制造执行系统的呼叫,如果班组长可以解决问题,重新按下安灯按钮,系统恢复正常。
OEE(设备综合效率)简介

– 班组长应花时间观察流程,注意并记录短暂停工时间(“ 周期练习”)
– 理解计划外停工的主要原因,实施有重点的根源问题解决 法
– 明确确定工作时间标准 – 通过监控来记录的停工时间,不断提高数据准确性能
17
5. 速度减慢
• 定义:由于机器运转速度低于流程设计标准而造成的时间损失。
实际节拍 :作业环境和限制条件等发生影响后实际稼 动时得到的结果上平均使用的稼动速度.
停线时间
停线时间 : 由于以下的原因而引起的设备不能稼动的时间 机器故障 : 因机器故障引起的设备不能生产的时间 机种变更 : 因材料不良, 品质等偶然发生的因素,依据生
产计划变更时发生的设备停止时间 准备调整 : 制品生产结束时或开始时工具类的调整、 整
设备综合效率 = 时间利用率 ×设备性能率 ×合格率 = 0.88 × 0.909 × 0.95 × 100 = 75.9%
提升设备综合效率
时间利用率
➢设备短暂停工零化 ➢TPM改善活动 ➢设备开动损失递减 ➢换模调整损失递减 ➢设备故障零化
设备性能率
合格率
➢临时停止、速度损 失显现化活动
➢性能提升改善活动
完成停止时间+加班时间
加班时间 实际作业时间
负荷时间:为了完成生产计划、设备必须运转的时间
负荷时间 = 实际作业时间 - 计划停止时间
计划停止时间包含早晚例会、休息时间、始业点检、安全点检、
自主保全、体制展开、试作、计划停止时间等时间
利用时间= 负荷时间-停线时间
负荷时间 实际作业时间
停线时间:工具更换、调整、故障停止、上下流等待、
计划不均衡 : 前后计划中由于别的因素引起的作业停止或 者担当设备后工程(设备)的生产数量或者目标 量已达成而停止情况的时间
oee_精品文档

oeeOEE(Overall Equipment Efficiency)以效率为核心的整体设备效率,是一个指标,用于衡量生产系统的效能。
它由三个概念组成:设备可用率(Availability)、设备生产率(Performance)和合格品率(Quality)。
OEE是一个综合指标,能够直观地反映设备的稳定性和生产效益,是现代生产管理中不可或缺的工具。
设备可用率是指设备在规定时间内的正常运行时间与总运行时间的比例。
设备发生故障、停机以及维修等非计划停止期间被视为不可用时间。
设备可用率的提高,意味着更少的停机时间,更好的设备运行效率。
以减少设备故障率、改善设备维修计划和提高设备操作者的技能水平为目标,可以有效地提高设备可用率。
设备生产率表示设备在正常运行时间内所生产的实际产量与理论产量的比例。
设备生产率的改善可以通过减少停机时间、提高设备运行速度、优化生产计划等手段来实现。
通过有效地调整生产节奏、加强设备维护和保养以及改善生产工艺流程,可以提高设备生产率,从而提高整体生产效率。
合格品率是指产品符合标准要求的比例。
合格品率的提高可以通过优化生产工艺、加强品质检验和控制,以及改善设备操作者的技能和培训来实现。
通过减少生产过程中的缺陷和废品产生,可以提高产品品质,提高整体生产效能。
OEE的计算公式为:OEE = 设备可用率× 设备生产率× 合格品率。
这个公式将设备可用率、设备生产率和合格品率三个指标综合起来,以综合反映生产系统的效能。
OEE不仅是一个衡量生产效率的指标,也是一个改善生产管理的工具。
通过实时监控和分析OEE,生产企业可以了解设备的真实运行情况,找出潜在的问题,并制定相应的改善措施。
例如,设备可用率低可能是由于设备老化、备件缺失或维修不及时等问题导致的,可以通过设备更新、备件管理和维修计划的优化来提高可用率;设备生产率低可能是由于操作不规范、产品切换时间长或生产节奏不合理等问题导致的,可以通过设备操作培训、生产计划调整和工艺流程优化来提高生产率;合格品率低可能是由于原材料质量不稳定、生产工艺参数设置错误或操作者技能不足等问题导致的,可以通过原材料筛选、工艺参数优化和操作者培训来提高合格品率。
认识OEE整体设备效能

认识OEE(整体设备效能)训培文件2012年8月15日•OEE 代表整体效能(设备Overall Equipment Effectiveness)•是一格的机器体性能的衡量手段,揭示浪存在于里这种严总时间费哪•各浪目的在于改统计种时间费实现进OEE 是什么?失总时间损生产转换故障停机效率衡量方式传统只算了部分计时间失损OEE 所涵盖的其他失时间损外停机计划速度慢缓坏设备损坏的部件损OEE用在何时?针对业务标实OEE用于以明确目的有性地支持目的施–限制足客需求的价造流程能力的机器满户值创实现瓶颈设备–利用率必提高的(如注模、和冲须昂贵设备设备压铸设备压设备)河水与暗礁的比喻为什么在衡量OEE ?精益生的目的是要降低存(河水水位),指出生生停的潜在产库产产顿原因(暗礁),除之使企能以更强的力即更低水位作清业竞争运高损坏率计划外停机产品质量低下运行缓慢频繁故障产品生产线换线时间长库存水平通使企的存强制少到过业库减某定目,企可以降低个既标业水位,主使暗礁浮出水面,动而可以除礁石或降低暗礁从清高度OEE衡量的是礁石的大小,明先暗礁着手说应该从哪块处理六重大种OEE 失损机器故障换线外停计划机速度下降量缺陷质坏损OEE 失分时间损为6大类操作(停工时间时间失)损机器故障换线可用 时间= (可使用工总时) - (工失窝时间损)(可使用工总时)增值(缺陷失)损坏损量缺陷质量 质= (加工品量) 产数- (缺陷量数) (加工品量产数)OEE 算 计– 模型可使用工总时停工计划内*机器运转时间(速度失)损外停工计划速度降低生率劳动产* = (操作时间) - (速度失损)(作运时间)总体设备效能(OEE ) = 可用时间 x 生产效率 x 质量一班工作总时六重大失降低机器效能明种损说OEE 算 计– 例举可使用工总时168 - 7*1 = 161停工 计划内= 1 小时/天每周工作总时间7*24 hours = 168机器故障 = 11.3 小时换线= 80.5 小时可得的作 获运时间= (161) - (91.8) = 43%(161)操作时间161 - 91.8= 69.2外停工 计划= 27.4 小时速度降低 = 12.9 小时生率劳动产* = (69.2) - (40.3) = 42%(69.2)机器运转时间69.2 - 40.3 = 28.9量 质= (28.9) - (9.7) = 66%(28.9)量缺陷 质= 9.4 小时增值时间28.9 - 9.7 = 19.2坏 损= 0.3 小 时航天企例业举在生中量产实践测OEE量方法具体情而明实际现场测应视况详细说例举•在本例中,OEE 量同通直接测时过PLC 和手工方法行量,可以算出未的停工记录记录两种进测这测记录时间并设法降低工。
OEE:设备整体效能概述

OEE:设备整体效能概述首先,设备的稼动率是指设备实际运行时间与计划运行时间的比值。
一个设备的稼动率越高,就表示设备的运行时间越充分利用,生产效率也就越高。
其次,生产良率是指设备生产的合格产品数量与总产量的比例。
高生产良率意味着设备的生产质量良好,低废品率,提高了整体效能。
最后,运行速度是指设备在运行时的实际产量与理论产量之比。
高运行速度可以提高设备的生产效率,降低生产成本。
通过综合考量稼动率、生产良率和运行速度,可以全面地评估设备的整体效能。
OEE的计算可以帮助企业发现设备运行中的瓶颈和问题,提高设备的生产效率和质量。
因此,OEE是企业评估设备效能的重要工具,也是提高生产效率和降低生产成本的关键指标。
综上所述,OEE是一个综合考量设备稼动率、生产良率和运行速度的关键性能指标,可以帮助企业全面评估设备的整体效能,发现问题并提高生产效率。
因此,企业应该重视OEE的计算与分析,以不断优化生产流程,提高设备的整体效能。
OEE(Overall Equipment Effectiveness)是一个关键性能指标,用于评估设备在生产过程中的效率和效能。
它是通过对设备的稼动率、生产良率和运行速度进行综合评估,从而全面衡量设备的整体效能。
OEE的计算可以帮助企业发现和解决设备运行中的瓶颈和问题,提高设备的生产效率和质量。
因此,OEE被广泛应用于制造业和生产领域,成为了衡量设备效能和生产效率的重要指标。
首先,设备稼动率是指设备实际运行时间与计划运行时间的比值。
通过计算稼动率,企业可以了解设备的利用率如何,识别出设备运行中的浪费时间和停机时间,从而采取相应措施来减少这些时间,提高设备的利用率。
比如,通过实施预防性维护、加强设备操作培训、优化生产排程等方式,来提高设备的稼动率。
其次,生产良率是指设备生产的合格产品数量与总产量的比例。
高生产良率意味着设备的生产质量良好,低废品率,能够提高产品的一次性合格率和降低生产成本。
OEE:设备整体效能概述

OEE:设备整体效能的基本原理马志军宋文渊摘要:设备整体效能(OEE)是一种有效的分析方法,在目前世界级的一些大公司内已经得到广泛应用,但很遗憾,在今天许多维修部门仍没有得到有效的使用。
主要原因在于人们对于OEE的基本原理并不理解。
文章从OEE的定义入手,分别就OEE的基本原理、OEE作用、OEE的实施策略以及维修与设备操作人员的关系作了简要分析介绍。
关键词:维修管理;OEE;可用度;性能比;优质率1.引入Mike(最佳作业方式的倡导者与作者)认为:“尽管许多人都知道RCA和它的应用,但很少人使用它。
原因是没有足够多的、适当的人相信它,并愿意在自己的工作中尝试着去使用它,且坚持下去。
”与根源分析方法的应用相似,成功实施OEE的主要障碍在于人们没有人真正的了解它,认认真真地去尝试并坚持。
作者认为,OEE 比其它的分析工具如RCA或故障树分析(FTA)的应用范围更广,这可能是由于设备整体效能(OEE),不仅是一个分析工具而且是一个基准设计工具。
为了促使更多的人使用OEE并从中获益,文章将简单介绍什么是OEE,为什么要使用OEE和如何使用OEE。
2. OEE的定义:设备整体效能可用度设备整体效能,英文全称是:Overall Equipment Effectiveness,简称OEE。
它由可用度、性能比、优质率三个要素构成,单一设备甚至整个工厂的运行都受到OEE 这三个要素累积效果的影响。
OEE是这三个要素百分数的乘积,其结果可用于生产分析和基准设计。
即:OEE=可用度×生产率×优质率可用度——生产计划内产品正常使用的百分比(用于评估可靠性)或可使用时间占日历时间(天/周/年)的百分比(用于度量装备的利用率),即设备能够工作的概率。
注:设备可使用时间的百分比(常常以天/周/年的总时间来计算)是按设备能否正常工作的时间(或实际产量)来计算的。
性能比――单位时间内原始设备制造商(OEM)以最大额定生产速度生产产品部件的百分比。
- 1、下载文档前请自行甄别文档内容的完整性,平台不提供额外的编辑、内容补充、找答案等附加服务。
- 2、"仅部分预览"的文档,不可在线预览部分如存在完整性等问题,可反馈申请退款(可完整预览的文档不适用该条件!)。
- 3、如文档侵犯您的权益,请联系客服反馈,我们会尽快为您处理(人工客服工作时间:9:00-18:30)。
OEE:设备整体效能概述(doc 4页)
部门: xxx
时间: xxx
制作人:xxx
整理范文,仅供参考,勿作商业用途
OEE:设备整体效能的基本原理
马志军宋文渊
摘要:设备整体效能(OEE)是一种有效的分析方
法,在目前世界级的一些大公司内已经得到广泛应
用,但很遗憾,在今天许多维修部门仍没有得到有效
的使用。
主要原因在于人们对于OEE的基本原理并不
理解。
文章从OEE的定义入手,分别就OEE的基本原
理、OEE作用、OEE的实施策略以及维修与设备操作人
员的关系作了简要分析介绍。
关键词:维修管理;OEE;可用度;性能比;优质率
1.引入
Mike(最佳作业方式的倡导者与作者)认为:“尽管许多人都知道RCA和它的应用,但很少人使用它。
原因是没有足够多的、适当的人相信它,并愿意在自己的工作中尝试着去使用它,且坚持下去。
”与根源分析方法的应用相似,成功实施OEE的主要障碍在于人们没有人真正的了解它,认认真真地去尝试并坚持。
作者认为,OEE比其它的分析工具如RCA或故障树分析(FTA)的应用范围更广,这可能是由于设备整体效能(OEE),不仅是一个分析工具而且是一个基准设计工具。
为了促使更多的人使用OEE并从中获益,文章将简单介绍什么是OEE,为什么要使用OEE和如何使用OEE。
2. OEE的定义:设备整体效能可用度
设备整体效能,英文全称是:Overall Equipment Effectiveness,简称OEE。
它由可用度、性能比、优质率三个要素构成,单一设备甚至整个工厂的运行都受到OEE这三个要素累积效果的影响。
OEE是这三个要素百分数的乘积,其结果可用于生产分析和基准设计。
即:OEE=可用度×生产率×优质率
可用度——生产计划内产品正常使用的百分比(用于评估可靠性)或可使用时间占日历时间(天/周/年)的百分比(用于度量装备的利用率),即设备能够工作的概率。
注:设备可使用时间的百分比(常常以天/周/年的总时间来计算)是按设备能否正常工作的时间(或实际产量)来计算的。
性能比――单位时间内原始设备制造商(OEM)以最大额定生产速度生产产品部件的百分比。
如得不到该数据,则可用产品生产率代替。
注:生产效率是设备以理论速度进行单件生产时有效时间的百分比,它可以度量速度的损失。
(如:低效率计量,机械障碍)。
优质率――单位时间生产的适于销售的产品占总产品的百分比。
注:用于确定所有优质产品的百分比(例如:所有产品包括生产、工程、再生产及废料)
例:50%可用度(0.5)×70%生产率(0.7)×20%劣质率(80%(0.8)优质率)=28%OEE
3. OEE的作用
设备整体效能(OEE)分析可以帮助公司减少不适当的消费,改进机械设备和工厂固定资产的运行效率。
它还可用于发现公司中最需要改进的地方,从这里开始进行改进,可以获得最大的投资回报。
OEE公式可以体现生产设备和方法、产品质量、机器可靠性改进、持续工作能力及其它方面的改进,并将最终影响公司的成本底线。
OEE公式虽然简单,却是一个极好的基准设计工具,可以使公司设备具有世界上一流的生产力。
OEE公式中的百分数很容易理解,可在设备操作员能看到它的地方显示这些数据,以更大的激励操作人员进行更好的生产。
让你的职工更容易的看到他们所做的工作是如何影响到整体设备的使用、生产率和产品质量,他们会更加努力取得到一个更好的效果。
在公司使用带有液晶显示器的自动设备监控系统,显示设备各个不同部分的OEE,对于各个不同工作环节的操作人员来说,就像汽车上的速度表一样可以随时了解自己的工作情况。
需要指出的是显示器显示的机器运行速度,只是设备整体效能的一部分而不是全部。
4. OEE的使用
同一设备的OEE公式可以采用多种形式,它可以作为基准设计和分析工具用于可靠性分析、设备使用效率分析或两方面都用。
如果需要可以从小处开始。
选择你生产流程的瓶颈处使用OEE。
一旦你发现它是一个多么有价值的工具,你就会逐渐的将它用于你设备的其它方面。
如果是在制造业工作,就必须走进车间,对OEE进行粗略的度量。
当监控每一个设备的OEE时不能仅着眼于设备自身,否则除非原因是明显的,它可能不能提供造成损失的主要的真实原因。
例如OEE似乎能够通过一些改进措施而得到提高,如:购买超大型设备,提供多余的支持系统,和增加检查的频率。
作为决策工具,将OEE与TDC合并。
前期:将TDC与你的数据收集结合在一起。
后期:通过向你的软件供应商索取软件报告,将TDC与你的软件结合。
总的来说,不应仅计算设备的OEE,也应计算生产线的OEE,对于公司而言,还应计算所有设备的OEE。
对制造工厂,现在也开始将OEE与自动生产车间自动生成的报告相结合。
也有一些公司,他们专门提供车间数据,并且很容易的自动读到OEE报告。
5.操作人员能否实施维修
当一个组织决定他们需要提高维修操作(包括把维修资源纳入操作人员管理范围)时,他们将会采取一些常用的措施(外部采购除外)。
然而有些组织为了进行维修作业改进而采取了一些其它措施,主要如下:
·维修人员将在设备操作领域获得更多的自主权。
·维修人员与操作人员联系得更加密切。
·维修不需要太多的管理人员,以便减少维修费用。
这些现象是常见的。
但也可以通过一些措施来减少费用。
首先:如果基本的维修作业(计划和时间安排,预防性维修,存储,技术数据基础)没有像日常生活方式那样建立起来,就不要采取这些措施,否则它将导致许多低劣的维修作业组织。
这样即使有几个没有经验的维修管理员去执行或改进这些维修数据基础,也会由于缺乏维修管理知识,企业会在六到九个月之内发生时间、利益、主动性或一下几项问题:
·更多的维修人员轮流当值,因为这样它可以感觉更安全。
其后果是操作人员会要求设备具有更高的工作效能以获得更多的利润。
·更多的维修人员将配置在一些可能或将要发生问题的领域。
这样可实现对问题更快的维修。
·工作请求将不再被输入计算机中,因为召唤人更加容易和
方便。
·为了对故障进行修复而在不同部门之间调动人员将会变得更困难。
·由于有更多的人在岗,加班时间和承包人的工时将会增加。
·订货将会增加。
·设备可靠性开始降低。
从而导致整个的维修成本上升,但管理人员可能看不到所有的这一切。
这将导致一些典型的意外现象发生,而且还时常不采取相关措施来改进这种状况。
原因是这些问题是由管理人员引起的,从而不愿看到或容对它进行改动。
这样做是错误的。
一些专业人士已多次提醒有关公司,使之认识到维修已经超出了控制范围,需要改进,相信问题会得到改善。
这种现象通常会经历大约三年左右的时间才会发生。
从调查数据上看,许多组织在十到十五年之间要重复上面的循环许多次。
作者不赞成将维修挪到生产操作领域。
这是因为我已经看到过太多的像上述的例子,并且没有一个通过将维修挪到操作领域而取得一个可以承受的改进。
同样的,如果你已经建立起了集中的或分散组织的基础维修数据库,且与操作有非常密切的联系,也没有必要去改变组织。
下图显示了一个实际的三年案例,它研究了一个组织为了降低维修费用,而将维修挪到操作领域。
将维修资源划归设备操作人员并减少员
工总数后变化百分比。
2002年9月数开1年后 2年后
——员工总
数
——承包商
第一年技术人员的数量降低了14.3%,而一年后又招回了6%,在同期,承包商的费用上涨了88%。
总的维修时间包括加班时间,承包人时间和house hours上升了10.5%,并且当然的总的维修代价上升了29.2%。
除此之外,可靠性和生产下降了6%。
这个工厂正准备雇用并训练更多的维修人员,执行丢掉的维修活动并将所有的维修资源归专业维修管理。