T6145镗床主轴套筒加工工艺设计
机械加工工艺卡片
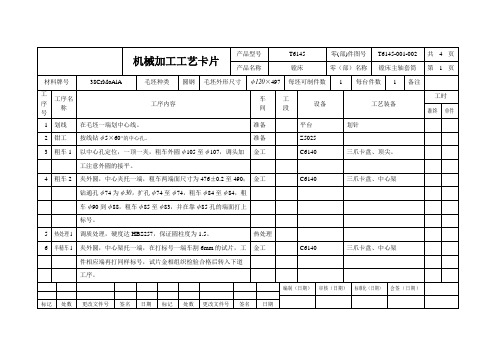
倒角定位,粗磨外圆,槽内肩面磨出即可,磨,工步内容工艺φ84至φ84,φ90至φ88,φ85至φ83,并在此端打标号。
工步内容工艺车φ至φ,车1:10锥面工步内容工艺装1 车两端尺寸为476±0.2至476.3±0.2,2 切6×φ96槽,3 车孔φ至φ,4 车60○内锥面。
5 切6×φ94槽,6 车孔φ至φ,工步内容工艺装7车孔φ85至φ,8 车60○内锥面工步内容工艺装粗铣齿条精铣齿条工步内容工粗磨外圆至,Ra0.63。
工步内容工艺粗磨φ至φ,带磨槽内肩面,60○倒角内锥面粗磨φ至φ粗磨φ85至φ,带磨槽内肩面60○倒角内锥面工工步内容工艺装步号1 粗磨齿条,齿面Ra1.25。
工工步内容工艺装备步号1 在两端划各孔的中心线,2 按划线在左端面钻1×60○中心孔3 钻φ3.3孔六个4 攻M4的螺纹5 按划线在右端面钻1×60○中心孔6 钻φ3.3孔六个工工步内容工艺装备步号7 钻φ3孔两个8 攻M4的螺纹9铰2×φ的孔工步内容精磨外圆至,Ra0.32。
工步内容工磨外圆至Ra0.16。
工步内容工磨两端面尺寸476±0.2。
至φ,带磨槽内肩面。
至图样尺寸,至,带磨槽内肩面。
工工步内容工艺装备步号1 精磨齿条至图样要求。
工步内容工研磨外圆φ至图样要求。
工步内容工艺研磨φ至图样要求研磨φ至图样要求。
高精度薄壁套简类零件车削工艺
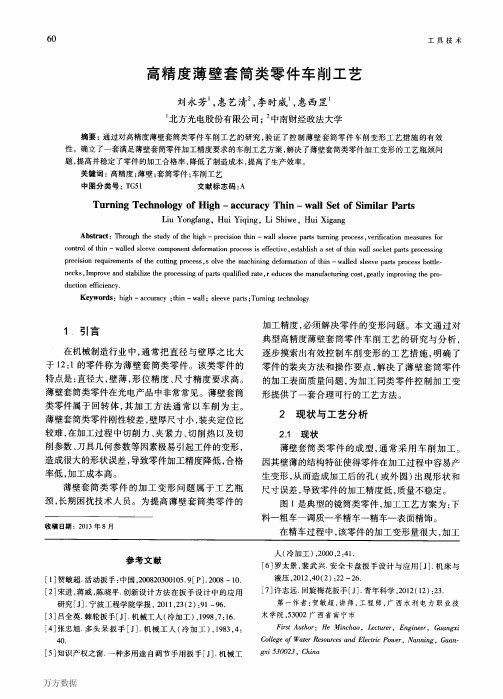
零件的装夹方法和操作要点,解决了薄壁套筒零件
的加工表面质量问题,为加工同类零件控制加工变 形提供了一套合理可行的工艺方法。
2现状与工艺分析
2_1
现状
削参数、刀具几何参数等因素极易引起工件的变形, 造成很大的形状误差,导致零件加工精度降低,合格 率低,加工成本高。 薄壁套筒类零件的加工变形问题属于工艺瓶
∽.ol,镗孔咖107p 035,保证尺寸215p 05,车外圆 曲113:::筘,倒角l×45。;去掉中心架,装螺纹堵头,
顶起车外园西109、西l 10如图7工序简图所示。
(1)三爪夹持外园西113.6,先镗基准孔 咖64p 035,用可换刀片镗刀直接加工,如图4所示。
该镗刀强度高,操作快捷方便,提高了加工表面的质
precision requirements
a
set of
thin wall socket parts processing
of the cutting pmcess,s olve the machining deformation of thin—walled sleeve pans process bottle—
(3)调头以咖64p 035孔及左端面作定位基准, 其中左端面为主要定位基准面,自制心轴与基准孔 采用间隙配合(间隙在o.01mm以内),找正咖110.20_。, 外圆保证跳动在o.005mm以内,再在西86孔内用专
用压板,将端面压紧,如图6装夹示意图所示。车外 圆咖110、咖113.21005,车外圆咖109.20-0l,长30(支 中心架用);然后,装中心架(注意孔内用塑料减震 泡沫填充防止共振,在架中心架时注意用千分表架 在已加工面上,校正跳动在0.005mm,防止架中心
套筒零件的机械加工工艺规程及夹具设计(含全套CAD图纸)

算; 4)、夹具总装图绘制。
9、刀具、量具没计。(绘制刀具量具工作图)
10、某工序数控编程程序设计。
四、上交资料(除资料 2 使用标准 A3 手写外,其余电子文稿指导教师审核后,打印上交)
1、零件机械加工工艺规程制订设计说明书一份;(按统一格式撰写)
2、工艺文件一套(含工艺过程卡片、每一道工序的工序卡片,工序附图);
第五章 第 30、35、65、70 号工序数控编程设计说明书 ........................... 23 1.数控加工工艺性分析.................................................... 23
2.走刀路线的确定........................................................ 23 3.刀具及切削用量确定.................................................... 23 4.编程原点的确定及数值计算.............................................. 24 5.程序编写及说明........................................................ 25 第六章 毕业设计体会........................................................ 29 第七章 参考资料............................................................ 30 致 谢....................................................................... 31
钻床主轴套筒零件的加工工艺规程和滚齿用夹具设计

XXXX毕业设计(论文)毕业设计题目钻床主轴套筒零件的机械加工工艺规程设计和滚齿用夹具设计学院 XXXXXX专业_ 机械设计制造及自动化姓名____ XXXX_______ __学号__ XXX_ __指导老师______XXX_____ __日期__ XXXXX机械制造工业是为现代化建设提供各种机械装备的部门,在国民经济的发展中具有十分重要的地位。
本文针对钻床主轴套筒的机械加工工艺规程分析和滚齿用夹具设计,进行了零件图分析、毛坯选择、基准的选择、工艺路线的确定、工序尺寸的确定、选择机械加工工艺设备、填写了机械加工工艺过程卡片和指定工序机械加工工序卡片,进行了滚齿夹具设计,并进行了定位误差分析等。
关键词:钻床套筒设计、加工工艺、滚齿夹具中文摘要 (2)1. 引言 (4)2. 计算生产纲领,确定生产类型 (4)3. 零件的分析 (4)4. 选择毛坯 (5)5. 工艺规程设计 (5)5.1 定位基准选择 (5)5.2零件的加工方法的选择 (5)5.3定制工艺路线 (6)5.4确定机械加工的余量及毛坯尺寸,设计毛坯——零件综合图 (7)6. 工序设计 (8)6.1选择加工设备工艺装备 (8)6.2工序尺寸的确定及计算 (9)6.3选择切削用量、确定时间定额 (10)7. 滚齿用夹具设计 (11)7.1拟定滚齿夹具的结构方案 (11)7.2确定刀具的导向方式或对刀装置 (12)7.3夹具精度的计 (12)7.4夹具总图 (13)7.5夹具零件图 (14)8. 课题总结 (14)参考文献 (15)附表 (16)机械制造工业是为现代化建设提供各种机械装备的部门。
在国民经济的发展中具有十分重要的地位。
机械制造工业的发展规模和水平,是反映国民经济实力和科学技术水平的重要标志。
本次毕业设计题目是钻床主轴套筒零件的工艺规程设计和滚齿用夹具设计,我认为好的工艺规程可以保证和提高产品质量;提高劳动生产率;提高经济效益。
镗孔的加工工艺及夹具设计
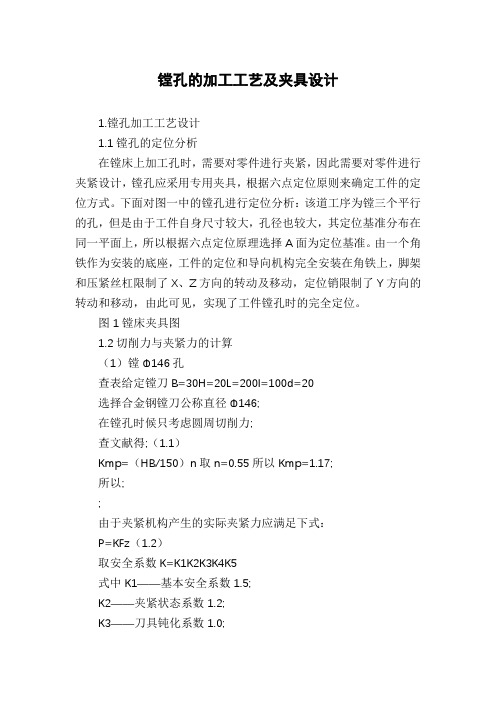
镗孔的加工工艺及夹具设计1.镗孔加工工艺设计1.1镗孔的定位分析在镗床上加工孔时,需要对零件进行夹紧,因此需要对零件进行夹紧设计,镗孔应采用专用夹具,根据六点定位原则来确定工件的定位方式。
下面对图一中的镗孔进行定位分析:该道工序为镗三个平行的孔,但是由于工件自身尺寸较大,孔径也较大,其定位基准分布在同一平面上,所以根据六点定位原理选择A面为定位基准。
由一个角铁作为安装的底座,工件的定位和导向机构完全安装在角铁上,脚架和压紧丝杠限制了X、Z方向的转动及移动,定位销限制了Y方向的转动和移动,由此可见,实现了工件镗孔时的完全定位。
图1镗床夹具图1.2切削力与夹紧力的计算(1)镗Φ146孔查表给定镗刀B=30H=20L=200I=100d=20选择合金钢镗刀公称直径Φ146;在镗孔时候只考虑圆周切削力;查文献得;(1.1)Kmp=(HB/150)n取n=0.55所以Kmp=1.17;所以;;由于夹紧机构产生的实际夹紧力应满足下式:P=KFz(1.2)取安全系数K=K1K2K3K4K5式中K1——基本安全系数1.5;K2——夹紧状态系数1.2;K3——刀具钝化系数1.0;K4——考虑夹紧动力稳定性系数1.0;K5——尽在有力矩企图使用回转时开考虑支撑面接触情况的系数1.0;所以得到K=K1K2K3K4K5=1.9,得到P=KFz=1.9X365.18=693.88N (2)镗Φ48孔选择高速钢镗刀公称直径Φ48;查表给定镗刀B=25H=30L=170I=80d=15在镗孔时候只考虑圆周切削力;查文献得;Kmp=(HB/150)n取n=0.55所以Kmp=1.17;所以;;由于夹紧机构产生的实际夹紧力应满足下式:P=KFz取安全系数K=K1K2K3K4K5式中K1——基本安全系数1.5;K2——夹紧状态系数1.2;K3——刀具钝化系数1.0;K4——考虑夹紧动力稳定性系数1.0;K5——尽在有力矩企图使用回转时开考虑支撑面接触情况的系数1.0;所以得到K=K1K2K3K4K5=1.9,得到P=KFz=1.9X223.2=424.08N <ol> 镗Φ80孔</ol>镗Φ80孔的计算过程与上边量孔的方法是一样的,就是选择高速钢镗刀公称直径Φ80的镗刀,最后计算结果为P=KFz=569.23N 根据上边的计算夹紧力不是很大,且夹具选择的种类为组合夹具,所以动力选择手动夹紧。
车床套筒工艺规程设计

车床尾座套筒是车床的主要零件,其结构合理与否、质量的好坏对加工过程、加工精度等有很大的影响,因此,在机床零件设计的过程中为主要考虑对象。
车床尾座在轴类工件的加工、端面钻孔等工序中经常应用,其工作状况好坏对工件加工质量有着较大的影响。
车床尾座的主要作用是为轴类零件定心,同时具有辅助支撑和夹紧的功能。
尾座顶尖的定位精度直接影响机床加工工件的径向尺寸精度,以及圆度、圆柱度、同轴度等形位精度。
而套筒是直接用来装夹顶尖的,由此可见,车床套筒的加工质量将直接影响到机床的工作精度和使用寿命。
所以,研究车床套筒的成形工艺是非常重要的。
此篇课程设计主要内容是对套筒零件的材料选用以及成形方法的研究及设计。
首先,简述了车床套筒的作用与工艺分析,然后对成形工艺作了详细的研究与设计。
这其中包括如何选材及热处理要求,分析了毛坯的制造方案与选用原则,分析了基准面的选取,叙述了切削用量对加工精度的影响以及如何选用。
在此基础上,制定了加工工艺路线与工艺规程设计,进行了各道工序的加工方法,机床、刀具、夹具、辅具、量具的选择,最后编制了机械加工工艺过程卡片与典型的工序卡片。
由于能力所限,经验不足,设计中还有许多不足之处,希望各位老师多加指导。
第一章机械制造工艺学课程设计任务书 (4)第二章零件分析 (5)第三章工艺规程设计 (9)3.1 选择毛坯 (9)3.2 基准的毛坯 (9)3.3 零件加工方法的选择 (10)3.4 确定工艺路线 (11)3.5 工艺分析 (14)第四章工序设计 (16)4.1 确定加工余量、工序尺寸及公差 (16)4.2 工艺装备选择 (19)4.3 确定各工序的切削余量 (23)第五章机械加工工艺过程卡 (35)第六章机械加工工序卡片 (36)第七章收获及心得体会 (37)致谢 (39)参考文献 (40)第一章机械制造工艺学课程设计任务书第二章零件分析2.1 计算生产纲领,明确生产类型生产纲领是企业在计划期内应当生产的产品产量和进度计划。
CA6140主轴零件加工工艺、工装设计

CA6140主轴零件加工工艺、工装设计攀枝花学院本科毕业设计(论文)如有需要全套夹具设计的请联系QQ:718384168 [CA6140主轴零件加工工艺、工装设计]学生姓名:学生学号:院(系):年级专业:指导教师:助理指导教师:二〇一四年五月摘要在机械领域中,车床是应用最为广泛、使用最为频繁的一种机床,特别是CA车床,它的应用非常的普遍。
所以它的加工精度就极其的重要,工件能否6140达到加工要求就取决于车床本身的精度,而决定6140CA车床加工质量的就是它的主轴。
6140CA车床主轴是把旋转运动及扭矩通过主轴端部的夹具传递给工件和刀具,要求有很高的强度及回转精度。
6140CA车床主轴设计为空心阶梯轴,外圆表面设有花键、垫键等功能槽及螺纹。
此论文详细计算了加工余量、切削用量、尺寸公差并阐述了6140CA主轴的加工工艺过程以及生产中所涉及的重要夹具设计方法。
经设计的6140CA主轴较其传统的车床主轴有更高的强度和回转精度。
关键词车床,主轴,加工工艺,夹具ABSTRACTIn machinery field, the lather is the most extensively and frequently used machine. Easpecially the CA6140 lather, its application is very widespread. So its processing accuracy is very important. Whether the work piece can reach the accuracy required is decided by the lather. While, the part deciding the processing quality of CA6140 lather is its mainshaft. The mainshaft of the CA6140 lather is to transmit the rovolve motion and the torque to the workpiece and cutting-tool through the fixture on the end of mainshaft, in which high strengh and rotating accuracy are required.In this design, my job contains the things as below. Mainshaft is a hollow stepped shaft. There are functional slots and thread, such as spline, pad key and so on. In the paper, allowance, cutting consumption and tolerance are calculated. Also elaborates the craft processes of the mainshaft of CA6140 lather, and the design of important fixture. After being designed, compared with traditional lather, the strength and rotating accuracy are enhanced.Key words Lather,Mainshaft,Processing technic,Fixture 目录摘要 .......................................................................................................................... .. (I)ABSTRACT ..................................................................................................................................... I I1 零件的分析 (1)1.1 零件的作用 (1)1.2 零件的工艺分析 (1)1.2.1 主轴的主要技术要求 (1)1.2.2 加工阶段的划分 (1)1.2.3 工序顺序安排 (2)2 工艺规程的设计 (3)2.1 毛坯的制造形式 (3)2.2 基准的选择 (3)2.3 主要加工表面工序安排 (4)2.4 制定工艺路线 (5)2.5 机械加工余量、工序尺寸及毛坯尺寸的确定 (7)2.5.1 毛坯的制造分析 (7)2.5.2 确定各加工表面的加工余量、工序尺寸及毛坯尺寸 (7)2.6 确定切削用量及基本工时 (9)3 磨床夹具设计 (38)3.1 问题的提出 (38)3.2 夹具设计 (38)3.2.1 定位分析 (38)3.2.2 定位基准的选择 (38)3.2.3 选择定位元件 (38)3.2.4 磨削力的计算 (38)3.2.5 定位误差的分析 (39)3.2.6 夹紧装置及夹具体设计 (39)4 钻床夹具设计 (41)4.1 钻床夹具的作用及类型 (41)4.1.1 钻床夹具的作用 (41)4.1.2 钻床夹具的类型 (41)4.2 夹具设计 (41)4.2.1 问题的提出 (41)4.2.2 定位分析 (42)4.2.3 定位基准的选择 (42)4.2.4 选择定位元件 (42)4.2.5 定位误差分析 (42)4.2.6 切削力与夹紧力分析 (42)4.3 钻模板、钻套、衬套选择设计 (43)4.3.1 钻模板选择 (43)4.3.2 钻套选择 (43)4.3.3 衬套选择 (44)4.4 夹紧装置及夹具体设计 (45)5 结论 (47)参考文献 (48)附录 (49)致谢 (50)1 零件的分析1.1 零件的作用本次设计所给定的零件是6140CA主轴零件图。
套筒加工工艺规程设计
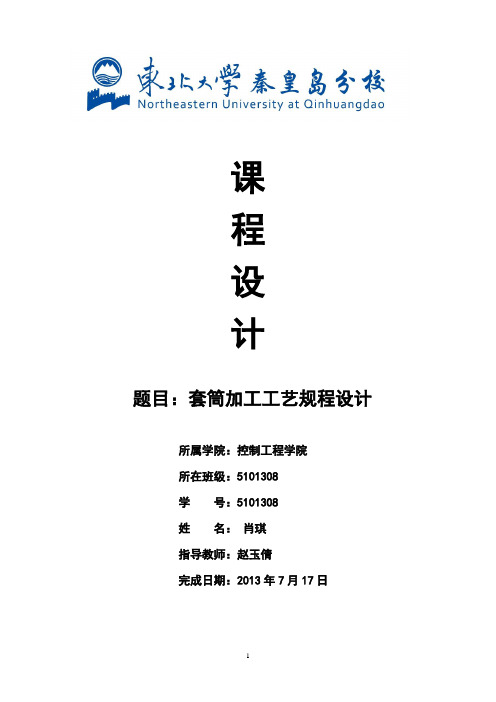
课程设计题目:套筒加工工艺规程设计所属学院:控制工程学院所在班级:5101308学号:*******姓名:肖琪指导教师:***完成日期:2013年7月17日目录课程设计要求 (3)一、零件分析 (4)二、产品类型确定 (4)三、确定毛坯 (4)四、确定各加工表面的加工、定位及方案加紧 (6)五、安排工艺过程 (8)六、工序设计 (9)(一)绘制工序图,选择机床、工艺装备 (9)(二)确定工序尺寸 (10)(三)切削用量的制定 (13)七、课程设计总结 (16)套筒零件机械加工工艺过程卡 (17)套筒零件机械加工工序卡(一) (18)套筒零件机械加工工序卡(二) (19)附录 (20)设计题目:套筒的机械加工工艺规程设计设计参数:下图示为套筒,材料45#钢,是某产品上的一个零件。
该产品年生产4000台,产品零件备品率4%,机加工废品率1%。
编制其机械加工规程。
设计任务:1)被加工零件的零件图和三维仿真图;2)零件毛坯二维图;3)机械加工工艺过程卡片和机械加工工序卡片;4)编写课程设计说明书。
一、零件分析该零件结构简单明了,结构工艺性好,无不方便加工之处。
φ60外圆、3×1凹槽尺寸精度均为11级,φ20+00.033孔、φ25+00.033孔、φ40-00.039外圆尺寸精度均为准公差8级,表面粗糙度要求最高是Ra≤1.6um,未标注形位公差,无热处理要求,是一个加工要求中等的零件。
但是轴向尺寸20-00.2和65-00.2不便直接测量,如何保证其精度是该零件加工和检测的一个重点。
二、确定生产类型1、生产纲领:根据以知数据可求得该零件的年生产纲领。
N=Qm(1+a%+b%)=4000×1×(1+4%+1%)=4200(件/年)2、生产类型的划分:查表1-1可得确定该零件生产类型为中批生产类型。
表1-1机械加工零件生产类型划分三、确定毛坯根据该零件的材料、生产类型、结构形状、尺寸大小、技术要求等的因其选用棒料。
车床主轴的零件机械加工工艺规程设计
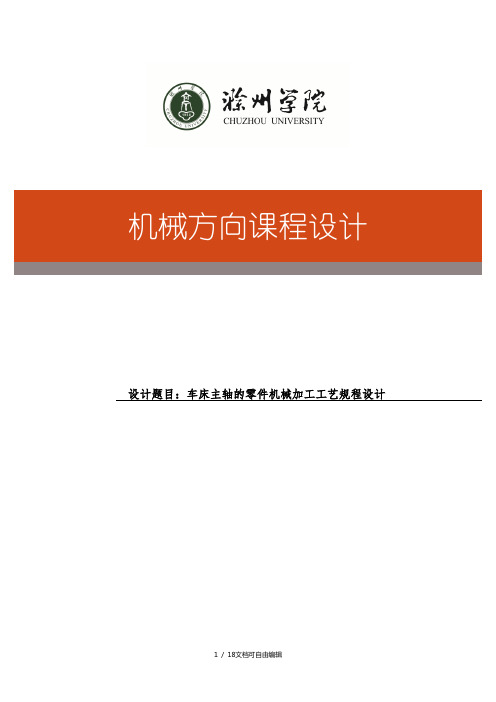
机械方向课程设计设计题目:车床主轴的零件机械加工工艺规程设计目录目录 (2)1、课题 (3)1.1、原始资料 (3)1.2、设计要求 (4)2、有关零件的分析 (4)2.1、零件的结构特点 (4)2.2、加工工艺性 (5)2.3、确定零件毛胚 (5)3、基准的选择 (5)3.1、有关基准的选择说明 (5)3.1.1、粗基准的选用原则 (5)3.1.2、精基准的选用原则 (5)3.2、确定零件的定位基准 (6)4、轴类零件的材料、毛坯及热处理 (6)4.1、轴类零件的材料 (6)4.2、轴类毛坯 (7)4.3、轴类零件的热处理 (7)5、制定加工工艺路线 (7)5.1、主轴加工工艺过程分析 (7)5.2、工艺路线的拟定 (8)5.3、车床主轴机械加工工艺过程卡 (13)5.4、加工余量的确定 (15)6、轴类零件的检验 (15)6.1、加工中的检验 (15)6.2、加工后的检验 (15)7、总结 (16)参考文献 (17)1、课题车床主轴是车床的主要零件,它的头端装有夹具、工件或刀具,工作时要承受扭曲和弯矩,所以要求有足够的刚性、耐磨性和抗振性,并要求很高的回转精度。
所以主轴的加工质量对机床的工作精度和使用寿命有很大的影响。
1.1、原始资料:零件材料:45钢技术要求:1、莫氏锥度及1:12锥面用涂色法检查,接触率为大于等于70% ;2、莫氏6号锥孔对主轴端面的位移为+2 ;3、用环规紧贴C面,环规端面与D端面的间隙为0.05~0.1 ;4、花键不等分积累误差和键对定心直径中心的偏移为0.02 。
生产批量:中等批量零件数据:(见零件图,在说明书最后一页)1.2、设计要求要求编制一个车床主轴零件的机械加工工艺规程,并编写设计说明书,具体内容如下:1.选择毛胚的制造方法,指定毛胚的技术要求;2.拟定车床主轴的机械加工工艺过程;3.合理选择各工序的定位定位基准与各工序所用的加工设备;4.确定一个加工表面的工序余量和总余量;5.确定一个工序的切削用量;6.确定工序尺寸,正确拟定工序技术要求;7.计算一个工件的单件工时;8.编写工艺文件;9.编写设计说明书。
固定套筒零件机械加工工艺规程与机床夹具设计(参考Word)

摘要套筒零件是一种常用零件,研究套筒零件的加工工艺和夹具生产技术,可以改进套筒零件的生产方法,提高工厂的生产效率,降低生产成本,提高零件的精度,对实际生产具有重要意义。
固定套筒零件加工工艺及钻床夹具设计是包括零件加工的工艺设计、工序设计以及专用夹具的设计三部分。
在工艺设计中要首先对零件进行分析,了解零件的工艺再设计出毛坯的结构,并选择好零件的加工基准,设计出零件的工艺路线;接着对零件各个工步的工序进行尺寸计算,关键是决定出各个工序的工艺装备及切削用量;然后进行专用夹具的设计,选择设计出夹具的各个组成部件,如定位元件、夹紧元件、引导元件、夹具体与机床的连接部件以及其它部件;计算出夹具定位时产生的定位误差,分析夹具结构的合理性与不足之处,并在以后设计中注意改进。
本次设计的套筒主要起到连接作用,且结构简单,便于加工,可以进行大量的投入生产,这对机械制造业具有一定的应用价值。
关键词:工艺;工序;切削用量;夹紧;定位;误差The Design of Fixed sleeve parts machining process planning andFixtureStudent:QING Zhi-bin Teacher:LING Ming-taoAbstract:Sleeve parts is a common part,process research and fixture sleeve parts production technology,we can improve the production process of the sleeve part,improve plant productivity, reduce production costs, improve the accuracy of parts,important for practical production.Set of parts machining technology and the design of drilling jig design, including design process is machining process design and the three part special fixture. In the process of design should first of all parts to analyze, understand parts of the process and then design a blank structure, and choose the good parts machining datum, designs the process routes of the parts; then the parts of each step process dimension calculation, the key is to determine the process equipment and cutting the amount of each working procedure; design then a special fixture, fixture for the various components of the design, such as the connecting part positioning device, clamping device, a guide element, clamp and the machine tool and other components; the positioning error generated when calculate fixture positioning, analysis of the rationality and deficiency of fixture structure, pay attention to improving and will design in.The sleeve is designed to connect major role to play,simple structure and ease of processing,they can put a lot of production,this has some value for machinery manufacturing.Keywords: process;process;cutting parameters;clamping目次摘要 (I)ABSTRACT (II)1 引言 (1)1.1课题研究的背景和意义 (1)1.2国内外发展现状 (1)1.3课题研究的主要内容 (2)2 工艺规程设计 (3)2.1零件的分析 (3)2.2确定毛坯的制造形式 (4)2.3基面的选择 (4)2.4制定工艺路线 (5)2.5选择加工设备和工艺装备 (5)2.5.1 机床选用 (5)2.5.2 选择刀具 (5)2.5.3 选择量具 (6)2.6确定切削用量及基本工时 (6)2.6.1 工序30 (6)2.6.2 工序40 (8)2.6.3 工序50 (8)2.6.4 工序60 (9)2.6.5工序120 (11)3钻孔夹具设计 (13)3.1研究原始质料 (13)3.2机床夹具定位元件 (13)3.3定位、夹紧方案的选择 (13)3.4切削力及夹紧力的计算 (14)3.5误差分析与计算 (15)3.6钻套、钻模板设计与选用 (16)3.7对夹具体的设计的基本要求 (18)3.8夹具设计及操作的简要说明 (18)4总结 (20)致谢 (21)参考文献 (22)附录1 固定套筒零件机械加工工艺卡 (23)附录2 本次设计相关图纸 (33)1引言1.1 课题研究的背景和意义本次我选定的题目固定套筒零件机械加工工艺规程与机床夹具设计,这属于机械制造业的内容。
机械加工工艺卡片
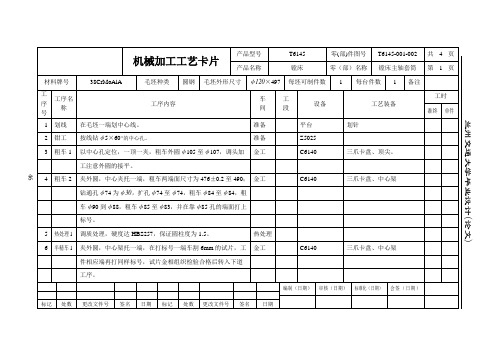
产品名称
镗床
零(部)名称
镗床主轴套筒
第1页
车间
工序号
工序名称
材料牌号
金工
7
半精车2
38CrMoAlA
毛坯种类
毛坯外形尺寸
每坯可制件数
每台件数
圆钢
φ120×497
1
1
设备名称
设备型号
设备编号
同时加工件数
普通车床
C6140
1
夹具编号
夹具名称
切削液
三爪卡盘、中心架
工位器具编号
工位器具名称
工序工时
准终
第1页
车间
工序号
工序名称
材料牌号
金工
3
粗车1
38CrMoAlA
毛坯种类
毛坯外形尺寸
每坯可制件数
每台件数
圆钢
φ120×497
1
1
设备名称
设备型号
设备编号
同时加工件数
普通车床
C6140
1
夹具编号
夹具名称
切削液
三爪卡盘、顶尖
工位器具编号
工位器具名称
工序工时
准终
单件
三爪卡盘
工
步
号
工步内容
工艺装备
主轴
转速(r/min)
机械加工工艺卡片
产品型号
T6145
零(部)件图号
T6145-001-002
共4页
产品名称
镗床
零(部)名称
镗床主轴套筒
第1页
材料牌号
38CrMoAlA
毛坯种类
圆钢
毛坯外形尺寸
φ120×497
每坯可制件数
轴承套工艺设计说明书-第5组标准版
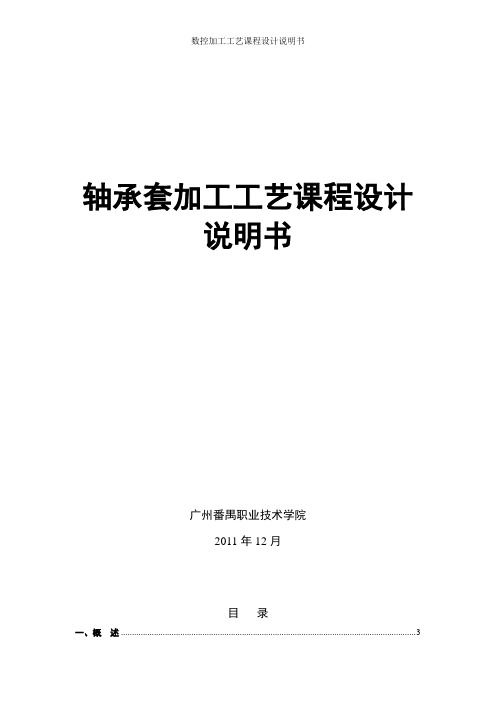
轴承套加工工艺课程设计说明书广州番禺职业技术学院2011年12月目录一、概述 (3)二、零件工艺分析 (5)三、确定毛坯 (6)轴承套的工艺路线如下:下料→车两端面→粗车各外圆→精车各外圆,车槽,倒角→检验77.1 工序设计 (11)7.2 机床选择 (11)参考文献 (14)一、概述套筒类零件的加工工艺根据其功用、结构形状、材料和热处理以及尺寸大小的不同而异。
就其结构形状来划分,大体可以分为短套筒和长套筒两大类。
一般套筒类零件在机械加工中的主要工艺问题是保证内外圆的相互位置精度(即保证内、外圆表面的同轴度以及轴线与端面的垂直度要求)和防止变形。
套筒类零件的外圆表面多以过盈或过渡配合与机架或箱体孔相配合起支承作用。
内孔主要起导向作用或支承作用,常与运动轴、主轴、活塞、滑阀相配合。
有些套筒的端面或凸缘端面有定位或承受载荷的作用。
套筒类零件虽然形状结构不一,但仍有共同特点和技术要求,根据使用情况可对套筒类零件的外圆与内孔提出如下要求1)内孔与外圆的精度要求外圆直径精度通常为IT5~IT7,表面粗糙度Ra 为5~0.63um,要求较高的可达0.04 um;内孔作为套类零件支承或导向的主要表面,要求内孔尺寸精度一般为IT6~117,为保证其耐磨性要求,对表面粗糙度要求较高(Ra=2.5~0.16 um)。
有的精密套筒及阀套的内孔尺寸精度要求为IT4~II5,也有的套筒(如油缸、气缸缸筒)由于与其相配的活塞上有密封圈,故对尺寸精度要求较低,一般为II'8—ITc),但对表面粗糙度要求较高,Ra一般为2.5~1.6um。
2)几何形状精度要求通常将外圆与内孔的几何形状精度控制在直径公差以内即可;对精密轴套有时控制在孔径公差的1/2~1/3,甚至更严。
对较长套筒除圆度有要求以外,还应有孔的圆柱度要求。
为提高耐磨性,有的内孔表面粗糙度要求为Ral.6-0.1 um,有的高达Ra0.025um。
套筒类零件外圆形状精度一般应在外径公差内,表面粗糙度Ra为3.2~0.4um。
机械工艺课程设计-钻床主轴套筒
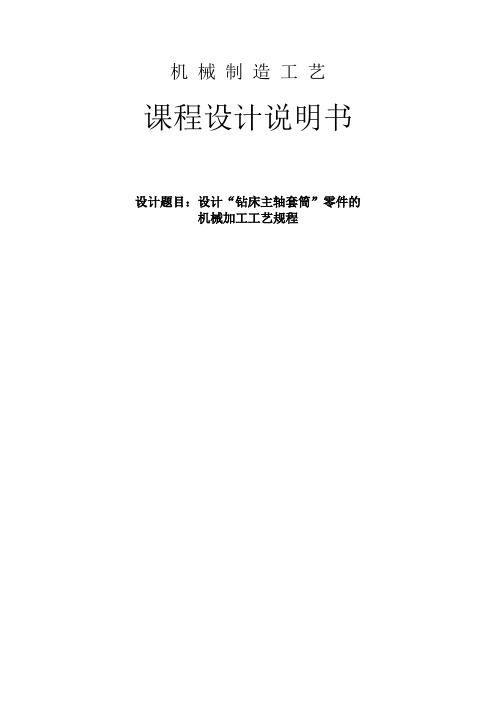
机械制造工艺课程设计说明书设计题目:设计“钻床主轴套筒”零件的机械加工工艺规程机械制造工艺课程设计任务书题目:设计“钻床主轴套筒”零件的机械加工工艺规程内容:1、零件图2、毛坯图3、机械加工工艺规程4、课程设计说明书前言机械制造工艺学课程设计是我们对所学课程的一次深入的综合性的复习,也是一次理论联系实际的训练,因此,它在我们大学四年生活中占有重要的地位。
我们希望能通过这次课程设计对自己未来将从事的工作进行一次适应性训练,从中培养自己分析问题、解决问题及与团队合作的能力,另外,这也是对自身意志力的一次很好的磨练机会。
由于能力所限,本设计中尚难免有许多不足之处,恳请各位老师、同学不吝给予批评和指教。
一、零件的分析(一)、零件的作用题目中所给定的零件是钻床主轴套筒(见附图)。
钻床主轴套筒是钻床主轴实现轴向进给运动的传动元件,主要作用一是传递钻孔所需的旋转运动, 带动主轴的上下移动;二是承受并传递钻孔时的作用力;三是安装定位钻套。
(二)、零件的工艺分析钻床主轴套筒可以按装夹方式分成两组加工表面。
下面分述如下:1.装夹外圆时这时可以加工的表面包括两端面,Φ24mm的孔,Φ42mm的孔,两个Φ40mm的孔及其中一个孔的端面,Φ28mm的孔,尺寸为Φ46mm×2mm的内槽,尺寸为M45×1的内螺纹,Φ31mm的孔及其端面。
其中两Φ42mm孔应保证0.01mm的圆柱度公差。
2.两端顶尖装夹时这时可以加工的表面包括外圆Φ50mm,模数为2、齿数为18、压力角为20°的齿,尺寸为8mm×1.5mm 的两处外槽。
其中应保证齿槽底面与Φ50mm轴的垂直度公差0.025mm。
这两组加工表面之间有着一定的位置要求,主要是1)孔Φ28mm对Φ50mm轴的基准轴线的圆跳动公差为0.01mm;2)孔Φ31mm对Φ50mm轴的基准轴线的圆跳动公差为0.01mm;3)两Φ40mm的孔对Φ50mm轴的基准轴线的同轴度公差为0.012mm。
镗床变速箱壳体机械加工工艺设计
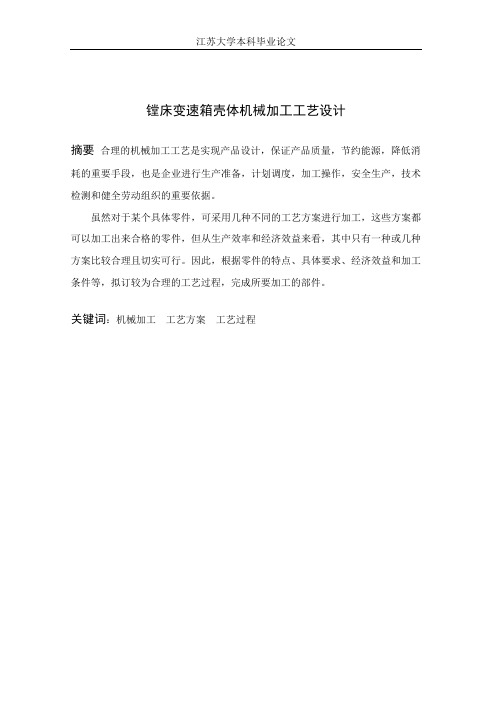
江苏大学本科毕业论文镗床变速箱壳体机械加工工艺设计摘要合理的机械加工工艺是实现产品设计,保证产品质量,节约能源,降低消耗的重要手段,也是企业进行生产准备,计划调度,加工操作,安全生产,技术检测和健全劳动组织的重要依据。
虽然对于某个具体零件,可采用几种不同的工艺方案进行加工,这些方案都可以加工出来合格的零件,但从生产效率和经济效益来看,其中只有一种或几种方案比较合理且切实可行。
因此,根据零件的特点、具体要求、经济效益和加工条件等,拟订较为合理的工艺过程,完成所要加工的部件。
关键词:机械加工工艺方案工艺过程Boring transmission case machining process designAbstract Reasonable machining process is to achieve product design, ensure product quality, Energy conservation, an important means to reduce consumption but also enterprises in the production preparation, planning and scheduling, processing operations, safety, technical testing and an important basis for sound labor organization.Although a specific part, the process can be used several different programs for processing, these options are passing out of the parts can be processed, but the production efficiency and cost effectiveness, of which only one or a few more reasonable and practical solution feasible. Thus, according to the characteristics of parts, and specific requirements, cost and processing conditions, develop a more rational process, to complete the processing of parts.Keywords: Machining Technology solutions Process引言箱体类是机器或部件的基础零件,它将机器或部件中的轴、套、齿轮等有关零件组装成一个整体,使它们之间保持正确的相互位置,并按照一定的传动关系协调地传递运动或动力。
- 1、下载文档前请自行甄别文档内容的完整性,平台不提供额外的编辑、内容补充、找答案等附加服务。
- 2、"仅部分预览"的文档,不可在线预览部分如存在完整性等问题,可反馈申请退款(可完整预览的文档不适用该条件!)。
- 3、如文档侵犯您的权益,请联系客服反馈,我们会尽快为您处理(人工客服工作时间:9:00-18:30)。
T6145镗床主轴套筒加工工艺设计第一节零件图分析一、结构特点主轴套筒是镗床的关键零件之一,它的质量直接影响机床的精度和镗床对工件的加工质量和精度,所以它的精度要求较高,尤其尺寸精度、形位精度和表面粗糙度等。
图1为镗床主轴套筒零件图图1为镗床主轴套筒零件图。
其结构特点如下:主轴套筒中间安装镗床主轴,在两端φ90mm 与φ85mm孔内安装轴承,轴承内孔与主轴轴颈相配合用来支承主轴并保证主轴的精度;在套筒的圆表面上铣出齿条与主轴箱中的齿轮相啮合,由齿轮带动齿条,使主轴套筒与主轴实现进给运动;主轴套筒外圆与抽轴承相配合,要求主轴套筒既能在横向运动时无阻滞,以要求在主轴旋转时不产生晃动,以保证主轴的回转精度。
所以φ90mm与φ85mm孔和φ105mm 的外圆是该零件的主要加工的表面。
此外,该零件全长476mm,两端内孔的形状和位置公差是不易掌握的,并且其最薄处仅有 4.5mm,工序安排不易会产生变形,将直接影响到零件的加工精度,套筒的主要面的粗糙度Ra数值是0.01和0.02,加工表面全部需要磨削,并在磨削前必须要安排合理的热处理,总之该零件的主要加工表面必须经过多道加工,才能逐步提高精度以达到要求。
2、技术要求分析1.φ105+0.013+0.023mm外圆表面的轴线是设计基准,其尺寸公差等级很高为IT4级,表面粗糙度为Ra0.04μm,这些技术条件都是为了保证与抽轴承的配合精度和运动的平稳。
2.两端φ90−0.009+0.001mm和φ85−0.009+0.001mm内孔表面对φ105+0.013+0.023 mm外圆轴线的径向圆跳动公差为0.002mm,圆柱度为0.002mm,其表面粗糙度值为Ra0.32mm,这些技术条件都是为了满足与轴承配合的要求,以保证主轴的回转精度;φ90−0.009+0.001mm 和φ85−0.009+0.001mm孔的内端面对φ90−0.009+0.001mm和φ85−0.009+0.001mm内孔的公共轴线端面圆跳动公差为0.002mm,这是因为这两处端面都是推力轴承的安装基准,它的精度直接影响轴向窜动。
3.中间的60○倒角是工艺基准,专为精磨φ105+0.013+0.023mm外圆时用顶尖式心轴而设计的,以保证两端内孔与外圆有很高的同轴度。
4.齿条齿形中心平面对φ105+0.013+0.023mm外圆轴线的垂直度公差为0.02mm,这项技术条件是保证齿轮与齿条啮合时接触良好,传动平稳。
3、生产类型的确定生产类型是企业生产专业化程度的分类,一般分为大量生产、成批生产和单件生产,其中成批生产又分为小批生产、中批生产和大批生产。
由于该T6145镗床主轴套筒的年产量定为5件/年,该生产类型属于小批生产小批量生产纲领的工艺特点如下:1.毛坯的制造方法及加工余量:自由锻、木模手工造型;毛坯精度低余量大。
2.机床设备及机床布置:通用机床按机群式排列;部分采用数控机床及柔性制造单元。
3.夹具及尺寸保证:通用夹具、标准附件或组合夹具;划线试切保证尺寸。
4.刀具及量具:通用刀具,标准量具。
5.零件互换性:配对制造,互换性低,多采用钳工修配。
6.工序集中成度:工序集中,加工工序少,每工序加工内容多。
7.工艺文件的要求:编制简单的工艺过程卡片。
8.生产率:用传统加工方法,生产率低,用数控机床可提高生产率。
9.成本:较高。
10.对工人的技术要求:需要技术熟练地工人。
11.发展趋势:采用成组工艺、数控机床、加工中心及柔性制造系统第三节毛坯的选择T6145镗床主轴套筒的材料为38CrMoAlA,所以选择毛坯类型为圆钢,成品外形尺寸为φ105mm×476mm,所以参考外圆表面加工余量表,T6145镗床主轴套筒选择毛坯尺寸为φ120mm×497mm。
第四节选择定位基准一、选择精基准和确定夹紧方案φ105+0.013+0.023的轴线是该零件的设计基准,根据精基准的选择原则,T6145镗床主轴套筒加工时的精基准具体选择如下:1.以60○倒角内锥面作为车削或磨削φ105+0.013+0.023外圆表面的精基准,如图2.2;图外圆表面加工精基准2.以φ105+0.013+0.023作为车削或磨削各内孔的精基准,如图2.3;图3内孔精基准3.以φ105+0.013+0.023外圆表面和端面作为铣削或磨削齿条的精基准,如图2.4。
图4 齿条加工精基准二、选择粗基准和确定夹紧方案根据粗基准的选择原则,T6145镗床主轴套筒加工时以φ105+0.013+0.023外圆表面为粗基准,如图2.5。
主轴套筒加工粗基准第五节拟定套筒的工艺路线一、加工阶段的划分T6145镗床主轴套筒主要表面精度很高(最高精度为IT4),表面粗糙度值很小(最小为0.002),是高精度零件,所以加工阶段化分除了一般的粗加工阶段、半精加工阶段和精加工阶段外,还要安排精整和光整加工阶段。
各阶段的主要任务如下:1.粗加工阶段在该阶段高效地切除加工表面的大部分余量,使毛坯形状和尺寸上接近成品套筒,主要加工完成粗车外圆和各个孔。
2.半精加工阶段切除粗加工后留下的误差,使被加工工件达到一定精度,为精加工做准备,并完成一些次要表的加工。
3.精加工阶段保证各主要表面达到零件规定的加工质量和要求,主要有粗磨外圆面、内孔和齿条。
4.精整和光整加工阶段对高精度的φ105+0.013+0.023外圆表面,φ90−0.009+0.001和85−0.009+0.001的孔表面进行研磨,使其达到图样要求。
三、加工顺序安排根据机械加工的安排原则,先安排基准和主要表面的粗加工,然后再安排基准和主要表面的精加工。
首先以φ105mm外圆表面作为粗基准来加工中心孔,然后中心孔为基准来加工外圆表面,再以φ105mm外圆表面为精基准来粗加工各个孔和60○倒角内锥面(精基准),最后以φ105mm外圆表面和60○倒角内锥面互为精基准来完成零件外圆和内孔的加工;以φ105mm外圆表面和端面为基准完成齿条的加工。
四、热处理工序及表面处理工序的安排在镗床主轴套筒的机械加工工艺过程中,为了改善工件的切削性能、消除工件内应力、改善工件材料的力学性能和提高工件表面性能等,必须要严格安排合理正确的热处理工序。
1.为了细化零件晶粒,使镗床主轴套筒获得高的韧性和足够的强度,使其具有良好的综合机械性能,在粗车工序以后安排调质处理。
调质外理的过程是将淬火钢件加热到500~600℃再进行高温回火。
2.镗床主轴套筒经过调质工序以后,虽然能够获得高的韧性和足够的强度,良好的综合机械性能,但调质过程中在淬火后组织不太稳定,虽然高温回火,消除部分的淬火应力,但仍有保留下来的,在这以后还有可能会引起尺寸的微小变形。
这对普通零件影响不大,但对高精度的镗床主轴套筒零件是不允许的。
那么只要还存在淬火应力及粗加工切削应力,是无法达到图纸要求的。
而经过高温时效,可以消除残余应力,使镗床主轴套筒的尺寸稳定下来。
38CrMoAlA的镗床主轴套筒零件氮化(是将氮原子渗入钢件表层的化学热处理)后;表面硬度可以保证达到技术要求HV900,和较高的疲劳强度、较高的抗蚀性和较高的抗咬合性能。
氮化工序中零件的渗氮层薄而脆,其渗氮工件不可能承受太大的接触压力和冲击。
渗氮后所允许磨削余量较小,因此氮化工序要安排在精磨工序以前、粗磨工序以后即可。
3.镗床主轴套筒在氮化后安排定性外理,垂直吊挂,油炉定性工作,并且不许人为较真,从而保证工件表面机械性能良好,消除机械加工累积的应力集中,稳定尺寸精度,从而提高镗床主轴套筒在实际使用中的寿命。
五、其他工序的安排1.在完成外圆和内孔的半精加工后、铣齿前,对工件安排磁粉探伤,这能够及时发现工件的表面与近表面是否有裂纹和夹渣等缺陷,保证工件合格的进入下道工序。
磁粉探伤完成后要对套筒进行去磁。
2.为了使镗床主轴套筒上非渗氮面得到防护,提高零件的使用价值,在工件进行渗氮工序前安排一道钳工,及取螺钉旋入套筒两端孔内。
六、工序过程安排根据以上的分析,初步拟订机械加工工艺过程如下:1 划线在毛坯一端划中心线。
2 钳工按线钻φ5×60○的中心孔。
3 粗车1 粗车外加圆,留余量,调头加工注意外圆的接平。
4 粗车2 粗车两端面,留余量;钻通孔φ74,扩孔φ74,粗车孔φ84、φ90,、φ85,均留余量;并在靠φ85孔的端面打上标号。
5 热处理1 调质处理,硬度达HBS257。
6 半精车1 在打标号一端车割6mm的试片,工件相应端再打同样标号,试片金相组织检验合格后转入下道工序。
7 半精车2 车外圆φ105+0.013+0.023,调头加工要保持接刃平整,留余量;车1:10锥面。
8 半精车3 车两端面,车孔φ90−0.009+0.001、φ760 +0.046 、φ85,均留余量;切6×φ96,6×φ94槽,车倒角60○。
9 粗磨1 粗磨外圆φ105+0.013+0.023,留余量。
10 探伤磁粉探伤。
11 铣粗、精铣齿条,中径留磨量。
12 热处理2 高温时效(不准使用工具校正)。
13 粗磨2 粗磨外圆105+0.013+0.023 ,留余量。
14 粗磨3 粗磨孔φ90−0.009+0.001、φ760 +0.046 、φ85,槽内肩面磨出即可,磨60○倒角内锥面。
15 磨齿1 粗磨齿条,中径留磨量。
16 钳工两端面上钻孔,攻6×M4-6H深10的螺纹,铰2×φ30+0.01深6的孔,锉刀修齿顶棱角倒圆为R0.5,其余棱角倒角0.3×45○。
17 精磨1 精磨外圆105+0.013+0.023至105.01−0.0220,18 钳工两端螺纹孔旋入M4的螺钉,待氮化后取出。
19 热处理3 氮化处理,硬度达HV900,渗层深为0.5,试片随工件氮化。
20 热处理4 定性处理,垂直吊挂,油炉定性。
21 精磨2 磨外圆105+0.013+0.023,留余量。
22 精磨3 外圆面定位,精磨φ90−0.009+0.001、φ85−0.009+0.001均留余量;磨φ760 +0.046和φ85+0.036+0.090至图样尺寸,磨两端尺寸为476±0.2至476±0.2。
23 磨齿2 精磨齿条至图样要求。
24 研磨研磨外圆105+0.013+0.023至图样要求。
研磨φ90−0.009+0.001至图样要求,研磨φ85−0.009+0.001至图样要求。
25 检验按图样对零件各项技术要求检验。
26 入库上油、包装、入库。
综上所述为镗床主轴套筒加工工艺。