(工艺流程)电厂工艺流程图
火力发电厂超超临界机组四缸四排汽工艺流程图

化学水处理
3#高加
3#高加
汽车运输(综合利用、灰场)
转运站
制氢站
厂外来煤输煤皮带
出线
原煤仓
省煤器 再热器 过热器
升压站
高加给水来
汽 水 分 离 器
稀释风机
混 合 器
缓 冲 罐
蒸发器
液氨罐
7A#低加7B#低加Fra bibliotek烟气脱硝
烟 囱
给煤机
柴 油 罐
空冷凝汽器 凝结水箱 凝结水泵 黄河水
锅炉 供油泵
中 速 磨
A
除
尘
器 引风机
空气预热器 厂力输送系统
二次风机
石灰 石仓
一次风机
5#低加
干式排渣机 除氧器
1#高加
灰 库
石灰石 浆装箱
氧化风机
吸 收 塔
浆液 循环 泵
去省煤器
1#高加
化学水预处理
6#低加
补水至凝汽器 凝结 水精 处理 装置
7#低加 汽封加热器
渣 仓
脱水装置
石灰石 浆装箱
给水泵
2#高加
2#高加
脱硫石膏 汽车运输(综合利用、灰场) 汽车运输(综合利用、灰场)
火电厂生产工艺流程图

冷却塔的作用是将挟带废热的冷却水在塔内与空气进行热交换,使废热传输给空气并散人大气。
如图1 所示的火电厂为例,锅炉会将水加热成高温高压蒸汽;推动汽轮机(2)作功使发电机(3)发电。
经汽轮机作功后的乏汽排入凝汽器(4),与冷却水进行热交换凝结成水,再用水泵打回锅炉循环使用。
这一热力循环过程中;乏汽的废热在凝汽器中传给了冷却水,使水温升高.挟带废热的冷却水,在冷却塔(5)中将其热量传给空气(6),从塔筒出口排人大气。
在冷却塔内冷却过的水变为低温水,水泵将其再送入凝汽器,循环使用。
前一循环为锅炉中水的循环,后一循环为冷却水的循环。
冷却塔中水和空气的热交换方式之一是,流过水表面的空气与水直接接触,通过接触传热和蒸发散热,把水中的热量传输给空气。
用这种冷却方式的称为湿式冷却塔(简称湿塔)。
湿塔的热交换效率高,水被冷却的极限温度为空气的湿球温度。
但是,水因蒸发而造成损耗;蒸发又依循环的冷却水含盐度增加,为了稳定水质,必须排掉一部分含盐度较高的水;风吹也会造成水的损失。
这些水的亏损必须有足够的新水持续补充,因此,湿塔需要有补给水的水源。
缺水地区,补充水有困难的情况下;只能采用干式冷却塔(简称干塔或空冷塔)。
干塔中空气与水(也有空气与乏汽)的热交换;是通过由金属管组成的散热器表面传热,将管内的水或乏汽的热量传输给散热器外流动的空气。
干塔的热交换效率比湿塔低,冷却的极限温度为空气的干球温度。
2.2 蒸发耗损量当冷却回水和空气接触而产生作用,把其水温降时,部分水蒸发会引起冷却回水之损耗,而其损耗量和入塔空气的湿球温度及流量有关,以数学表达式作如下说明:令:进水温度为T1℃,出水温度为T2℃,湿球温度为Tw,则*:R=T1-T2(℃)------------(1)式中:R:冷却水的温度差,对单位水量即是冷却的热负荷或制冷量Kcal/h 对式(1)可推论出水蒸发量的估算公式*:E=(R/600)×100% ------------ (2)式中:E----当温度下降R℃时的蒸发量,以总循环水量的百分比表示%,600-----考虑了各种散热因素之后确定之常数。
火电厂脱硫工艺流程图

火电厂脱硫工艺流程图火电厂脱硫工艺流程图脱硫是火电厂废气治理的重要环节,其目的是降低废气中二氧化硫(SO2)的排放浓度,以满足环境保护标准。
下面是火电厂脱硫工艺的流程图:1. 烟气净化系统烟气净化系统是脱硫工艺的前置工序,主要用于除去烟气中的粉尘和颗粒物,以提高脱硫效果。
该系统包括除尘器和颗粒物收集设备。
2. 原料储存和输送系统原料储存和输送系统主要用于存储和输送石灰石等脱硫剂。
石灰石经破碎、筛分等工艺处理后,通过输送装置送入脱硫反应器。
3. 脱硫反应器脱硫反应器是脱硫工艺的核心设备,通过喷射剂将脱硫剂喷入烟道烟气中与SO2反应生成石膏(CaSO4·2H2O)。
该反应器内部设置了填料,增大了接触面积,提高了脱硫效率。
4. 石膏处理系统石膏处理系统用于处理脱硫反应器产生的石膏。
首先,将湿式脱硫产生的石膏通过脱水设备去除多余水分,然后进行石膏的干燥和粉碎处理,最后通过输送装置将石膏送往储存设备或外销。
5. 烟气净化系统脱硫后的烟气仍然含有少量的颗粒物和其他有害物质,需要再次经过烟气净化系统进行处理。
该系统包括除尘器、脱酸模块等设备,用于进一步净化烟气,以满足排放标准。
6. 废水处理系统脱硫过程中产生大量废水,需要进行处理以达到排放标准。
废水处理系统包括沉淀池、过滤设备、中和反应器等,通过净化工艺将含有石膏颗粒和金属离子的废水处理成符合排放标准的清水。
以上是火电厂脱硫工艺的主要流程图,通过脱硫工艺可以有效减少火电厂废气中的二氧化硫排放,保护环境,净化大气。
同时,废水处理系统的运行也能确保废水排放符合环保要求。
火电厂脱硫工艺的不断完善和改进将为环境保护事业的发展做出重要贡献。
火电厂生产工艺流程图
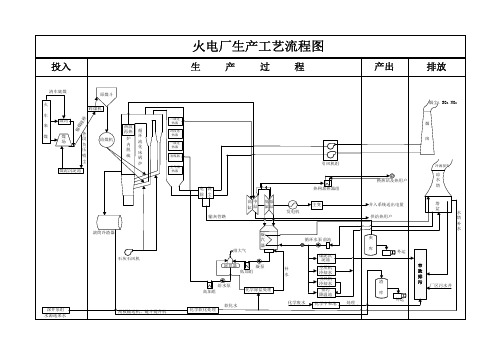
冷却塔的作用是将挟带废热的冷却水在塔内与空气进行热交换,使废热传输给空气并散人大气。
如图1 所示的火电厂为例,锅炉会将水加热成高温高压蒸汽;推动汽轮机(2)作功使发电机(3)发电。
经汽轮机作功后的乏汽排入凝汽器(4),与冷却水进行热交换凝结成水,再用水泵打回锅炉循环使用。
这一热力循环过程中;乏汽的废热在凝汽器中传给了冷却水,使水温升高.挟带废热的冷却水,在冷却塔(5)中将其热量传给空气(6),从塔筒出口排人大气。
在冷却塔内冷却过的水变为低温水,水泵将其再送入凝汽器,循环使用。
前一循环为锅炉中水的循环,后一循环为冷却水的循环。
冷却塔中水和空气的热交换方式之一是,流过水表面的空气与水直接接触,通过接触传热和蒸发散热,把水中的热量传输给空气。
用这种冷却方式的称为湿式冷却塔(简称湿塔)。
湿塔的热交换效率高,水被冷却的极限温度为空气的湿球温度。
但是,水因蒸发而造成损耗;蒸发又依循环的冷却水含盐度增加,为了稳定水质,必须排掉一部分含盐度较高的水;风吹也会造成水的损失。
这些水的亏损必须有足够的新水持续补充,因此,湿塔需要有补给水的水源。
缺水地区,补充水有困难的情况下;只能采用干式冷却塔(简称干塔或空冷塔)。
干塔中空气与水(也有空气与乏汽)的热交换;是通过由金属管组成的散热器表面传热,将管内的水或乏汽的热量传输给散热器外流动的空气。
干塔的热交换效率比湿塔低,冷却的极限温度为空气的干球温度。
2.2 蒸发耗损量当冷却回水和空气接触而产生作用,把其水温降时,部分水蒸发会引起冷却回水之损耗,而其损耗量和入塔空气的湿球温度及流量有关,以数学表达式作如下说明:令:进水温度为T1℃,出水温度为T2℃,湿球温度为Tw,则*:R=T1-T2(℃)------------(1)式中:R:冷却水的温度差,对单位水量即是冷却的热负荷或制冷量Kcal/h 对式(1)可推论出水蒸发量的估算公式*:E=(R/600)×100% ------------ (2)式中:E----当温度下降R℃时的蒸发量,以总循环水量的百分比表示%,600-----考虑了各种散热因素之后确定之常数。
沼气发电厂工艺流程图
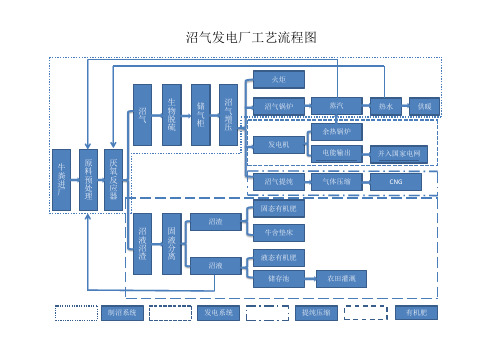
沼气发电厂工艺流程图牛粪进厂原料预处理厌氧反应器沼气沼液沼渣生物脱硫储气柜沼气增压固液分离火炬沼气锅炉发电机沼气提纯蒸汽热水余热锅炉电能输出气体压缩CNG沼渣固态有机肥牛舍垫床沼液液态有机肥储存池农田灌溉并入国家电网供暖制沼系统发电系统提纯压缩有机肥制沼系统设备1、预处理:侧式搅拌机9台,螺旋除砂机5台,立式搅拌机4台,螺旋刮砂机3台,一级提升泵2台,二级提升泵2台,切割机+凸轮泵2套,污水泵2台2、厌氧反应器:底部侧搅拌机8+8共16台,顶部破壳机16台,立式搅拌机8台,内循环泵4台,出渣泵2台,沼气在线组分分析仪2台,厌氧反应器8座,沼气气体流量计9台3、生物脱硫:一套4、双膜储气柜:双膜储气柜1套,鼓风机2台及配套控制柜1套5、沼气增压:火炬一套,冷干机一套,罗茨风机3台,沼气气体流量计3台,电动阀门若干6、沼气锅炉:蒸汽锅炉及其配套设施2套,热储罐1座,冷水罐1座,热水循环泵4台,制软水设备一套7、PLC自动化控制系统一套,通风系统发电系统发电机4台,发电机控制柜4个,余热锅炉4套,变压器4套提纯压缩脱硫塔2座,冷却系统3件,控制系统3件,MCC、防爆电机3件,系统成撬3件,螺杆压缩机及机头总成3件有机肥固液分离机4套,沼气储存池7座公共设施厂区路灯,厂区供暖系统,厂区消防系统,厂区空调系统,厂区给排水系统,厂区监控系统,厂区道路。
热电厂工艺流程
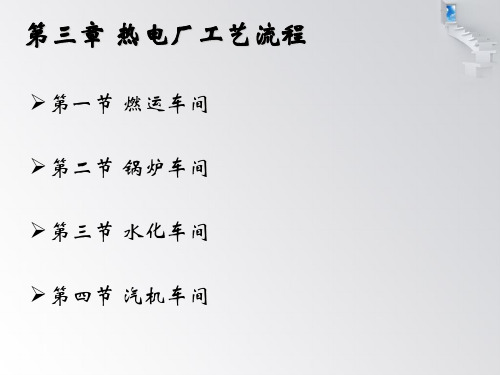
第三章第三节 水化车间
水化车间流程图如图3-2-1所示。
生产回水
回水箱
回水泵
工业水
水处理
除盐水
除盐水泵
除氧
图3-3-1 燃运车间流程图
第三章第三节 水化车间
高效过滤器: 作用: 除去来水中的泥沙、结晶等固体杂质,防 止吸附堵塞管道、锅炉壁。其结构如图3-3-2所示。
第三章第三节 水化车间
图3-3-2 过滤器组及滤芯
第三章第四节 汽机车间
图3-4-6
汽轮机
第三章第四节 汽机车间
汽轮机分类:
(1)按工作原理分类:冲动式, 反动式 (2)按热力过程特性分类: 凝汽式汽轮机、背压式汽轮机、中间再热式汽轮机、调整抽汽式 汽轮机 (3)按主蒸汽压力分类: 低压汽轮机:主蒸汽压力 < 1.47 Mpa 中压汽轮机:主蒸汽压力 1.96 ~ 3.92 Mpa 高压汽轮机:主蒸汽压力 5.88 ~ 9.8 Mpa 超高压汽轮机:主蒸汽压力 11.77 ~ 13.93 Mpa 亚临界压力汽轮机:主蒸汽压力 15.69 ~ 17.65 Mpa 超临界压力汽轮机:主蒸汽压力 > 22.15 Mpa (4)按机组轴数可分单轴和双轴汽轮机;按汽缸数目分单缸、双缸和 多缸汽轮机;等等
图3-2-5
组装中的水冷壁
第三章第二节 锅炉车间
过热器和再热器:如图3-2-6 过热器:将从汽包出来的饱和蒸汽加热成具有额定温度的过 热蒸汽。(利用高温烟气的热量加热饱和蒸汽) 再热器:将从汽轮机高压缸中膨胀做功后的蒸汽再次引入布 臵在锅炉中的再热器中受热升温,再送回汽轮机中 压缸中去做功。若采用二次再热,则再将中压缸排 汽再热后送回低压缸去做功。 作用:提高循环热效率;使汽轮机末级叶片的蒸汽湿度控 制在允许范围内。
火力发电厂亚临界生产工艺流程图
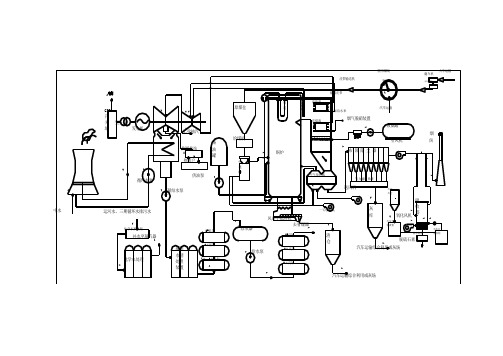
汽车运输综合利用或灰场
送风机
石灰 石仓
中水
运河水、三期循环水排污水 风冷干排渣机
化学水预处理 5#低加
一次风机 去省煤器
1#高加 6#低加
灰 库
石灰石 浆液箱
氧化风机
吸 收 塔
除氧器
补水至凝汽器 凝结 水精 处理 装置 给水泵
7#、8#低加
渣 仓
脱水装置
石灰石 浆液箱
脱硫石膏 汽车运输综合利用或灰场
2#高加
化学水处理
3#高加
圆形煤场 皮带输送机
堆取料机Biblioteka 翻车机活化给煤机火车运输
输煤皮带 屏 过
高 温 过 热 器
再热器 高加给水来 省煤器
GIS 开 关 变压器 场
原煤仓
汽车运输
烟气脱硝装置 液氨罐 引风机 烟 囱
发电机
工业抽汽 给煤机 热网首站 热用户 供油泵 柴 油 罐
中 速 磨
锅炉
布袋除尘器
空气预热器 气力输送系统
循环水泵 凝结水泵
热电厂全厂工艺流程示意图

水化车间
除盐水供水量:75~85t/h 生产回水供水量:90~100t/h 酸耗:0.334kg/t 汽 碱耗:0.129kg/t 汽 电耗:0.782KWh/t 汽 新水耗:1.1~1.15 t/t.除盐水
加热
汽机车间
凝结水泵 凝结水 2#机凝汽器 冷却水 热水 第二循环水站
高压供汽流量:90~105/h 低压供汽流量:50~70t/h 发电量:20000~25000KWh 发电汽耗:2.5~2.7kg/KWh 发电耗电:0.03~0.04KWh/KWh
汽车来煤 火车来煤
褐煤堆场 烟煤仓
干煤棚
给煤机
筛分、破碎
皮带输送
原煤仓 灰库 乏气
制粉
锅炉车间
煤粉 粉仓 冷空气 给粉机 加热 点火柴油 送风机
烟囱排空
除尘
பைடு நூலகம்
烟气 干灰
燃运车间
最大煤储量:20000t 单系统皮带运输能力:195t/h 输煤电耗:1.17kwh/t 煤 输煤柴油耗:0.099kg/t 煤
热电厂工艺流程图
2#汽轮机 1#汽轮机 低压减温减压
抽汽 背压汽
减温 减温
低压供汽
注: 4#、5#锅炉及 3#高背压机组为二期扩建
3#汽轮机 高压减温减压
背压汽
减温 高压供汽
汽车来煤干煤棚火车来煤给煤机筛分破碎皮带输送原煤仓制粉煤粉粉仓给粉机乏气工业水水处理除盐水泵生产回水除盐水回水箱回水泵2机凝汽器凝结水泵加热除氧给水泵加热2汽轮机低压减温减压高压减温减压高压供汽低压供汽除尘烟囱排空烟气送风机冷空气灰渣灰渣坝脱水仓灰渣回水第一循环水站点火柴油褐煤堆场烟煤仓锅炉给水加热1汽轮机抽汽背压汽减温第二循环水站冷却水热水凝结水新蒸汽冲渣除尘水减温3汽轮机背压汽减温注
- 1、下载文档前请自行甄别文档内容的完整性,平台不提供额外的编辑、内容补充、找答案等附加服务。
- 2、"仅部分预览"的文档,不可在线预览部分如存在完整性等问题,可反馈申请退款(可完整预览的文档不适用该条件!)。
- 3、如文档侵犯您的权益,请联系客服反馈,我们会尽快为您处理(人工客服工作时间:9:00-18:30)。
外部的煤用火车或汽车运进厂后,由螺旋卸车机(或汽车卸车机)卸入缝式煤槽,经运煤皮带送到贮煤仓,经碎煤机破碎后,再由运煤皮带机送到煤仓间,经磨煤机粉末处理后被送到锅炉燃烧,加热锅炉的水,使其变为高温高压蒸汽,之后,高温高压蒸汽被送往汽轮机膨胀做功,推动转子高速旋转,从而带动发电机发电。
从汽轮机出来的热蒸汽通过冷凝器冷却成凝结水,经处理后循环使用。
锅炉烟气经脱硝、除尘、脱硫后经烟囱排到空气中。
以下根据单元划分对各系统的工艺流程和设备布局进行详细叙述。
各种职业病危害因素标注:1煤尘、2矽尘、3石灰石尘、4石膏尘、5其它粉尘、6噪声、7高温、8辐射热、9全身振动10一氧化碳、二氧化碳、二氧化硫、一氧化氮、二氧化氮、11工频电场、12六氟化硫、13盐酸、14氨、15肼。
16硫化氢、17氢氧化钠、18硫酸、19二氧化氯、20甲酚。
2.7.1输煤系统:自备热电厂改造工程建设时,电厂燃煤厂外运输采用火车来煤与公路汽车运输相结合的方式。
拟从原有该项目铁路专用线上接出电厂运煤铁路专用线,所需燃料可方便地运送入厂。
在厂址西侧与该项目的运煤通道相连,为燃料运输车辆的出、入口。
本电厂燃用煤种为原煤。
锅炉对燃料粒度要求:粒度范围≤30mm。
输煤系统中设有三处交叉。
火车煤沟下部皮带机头部、筒仓下部皮带机头部、进煤仓间皮带机头部通过交叉均可实现带式输送机甲、乙路的切换运行。
2.7.1.1火车来煤:火车来煤由该项目内部铁路将煤运至煤场,煤受卸设施为双线缝隙式煤槽。
煤沟设计长150m,配三台螺旋卸车机将煤卸入缝式煤沟,煤沟上口宽13m,有效容量约4000t,可存放3列车的来煤量。
火车煤沟下部皮带机头部、筒仓下部皮带机头部、进煤仓间皮带机头部通过交叉均为带式输送机甲、乙路的切换运行。
2.7.1.2汽车来煤汽车来煤为与大同路相连的该项目运煤通道将煤运至煤场。
汽车来煤采用自卸或机械卸车的方式将煤卸入地下缝式煤槽,煤槽上口宽8m,长约94m,有效容量约2500t。
拟设计有3台汽车卸车机,共9个货位,另有6个自卸车货位,煤槽下带式输送机配叶轮给煤机。
2.7.1.3原煤运输工艺火车煤沟的煤通过1号带式输送机、汽车煤槽的煤通过2号带式输送机分别与3号带式输送机相连,进入全厂运煤系统。
煤(汽车来煤、火车来煤)经卸煤沟进入运煤系统。
来煤通过1号甲(乙)带式输送机、汽车煤槽的煤通过2号甲(乙)带式输送机分别与3号带式输送机相连,进入全厂运煤系统。
原煤经3号甲(乙)带式输送机的煤、经4号甲(乙)带式输送机送至5号甲甲(乙)带式输送机(犁式卸料器)和除铁器,经6号可逆配仓输送机进入筒仓。
筒仓的煤经其下部设环式叶轮给煤机,经调配送给7号甲、乙带式输送机,再通过8号甲、乙带式输送机(带有除铁器)和盘式除铁器后进入滚轴筛。
滚轴筛出来的煤如粒度如不满足要求则进入环锤式碎煤机破碎,然后进入9号甲(乙)带式输送机,如粒度满足要求的煤直接进入9号甲(乙)带式输送机,此后再依次经10号甲(乙)带式输送机、11号甲(乙)带式输送机、犁煤卸料器(乙)进入原煤仓。
输煤工艺流程图见图2-3。
2.7.1.4输煤主要设备a.输煤设备:厂内运煤系统均由固定带式输送机组成。
带式输送机由二种带宽规格组成,煤沟至筒仓的1号~6号带式输送机,其胶带宽B=1200mm;筒仓下7号带式输送机至煤仓间9号带式输送机,其胶带宽B=1000mm。
b.输煤系统设三级除铁设施,除铁设备采用二级永磁带式除铁器,一级盘式除铁器。
带式除铁器安装在5号转运站及碎煤机室内,盘式除铁器安装在8号皮带机中部采光间内。
c.本工程输煤系统在9号带式输送机上的电子皮带秤计量装置。
d.筛分设备采用一级筛分一级破碎方案,选用滚轴筛,滚轴筛通过能力为600t/h,破碎设备选用环锤式碎煤机,碎煤机出力为400t/h,入料粒度≤350mm,出料粒度≤30mm。
当来煤粒度不需要破碎时,可经过旁路直接进入系统。
筛碎设备双路布置,一路运行,一路备用。
e.设置6个储煤筒仓,筒仓直径¢22m,每个筒仓容量为1×104t,可满足本期2×1080t/h锅炉最大连续蒸发量时燃用约9天。
筒仓下部向带式输送机配煤采用环式叶轮给煤机。
带式输送机向原煤仓配煤采用固定式双(单)侧可变槽角犁式卸料器完成。
输煤主要设备及布局见表2-11 。
2.7.2 燃烧系统破碎至≤30mm的煤由运输皮带输送至原煤仓内,经由连接在给煤机将原煤送入落煤管。
在混煤箱里,煤经过热风预干燥后,再由螺旋输送器送入磨煤机内,然后经旋转筒体内钢球的连续运动研磨成粉。
然后由给煤机将煤直接送入锅炉内。
锅炉所需的空气由送风机提供,锅炉燃烧所需的一次风、二次风均采用独立系统。
由一次风机提供并经空气预热器加热后的正压热一次风在磨煤机前下部的进风口与正压冷一次风混合进入磨煤机。
一次风与煤粉组成风粉混合物,经燃烧器喷入炉膛燃烧。
二次风系统的送风机采用室内、外吸风方式。
送风机出口的空气进入空气预热器加热,空气预热器出口的热风接至锅炉两侧的二次风大风箱进入燃烧器的各个二次风口,作为主要的助燃风。
锅炉燃烧产生的烟气,从炉膛出口出来后依次通过省煤器、脱硝系统和空气预热器后进入双室五电场除尘器,再由引风机引入锅炉脱硫系统脱硫后由烟囱排入大气。
锅炉产生的蒸汽一部分送入汽轮机发电,一部分送入热网系统供热,锅炉产生的灰渣进入锅炉除灰渣系统处理。
本工程设烟气脱硝系统。
烟气从炉膛出口通过尾部受热面,在省煤器出口烟气分两路进入SCR脱硝装置进行脱硝,脱硝后的烟气再分别进三分仓空气预热器,然后通过烟道进入电气除尘器,再可调吸风机经烟囱排至大气。
本期工程二台炉合用一座高210m钢筋混凝土烟囱。
燃烧工艺流程图见图2-4。
燃烧系统主要设备:每台锅炉设置3台双进双出钢球磨煤机,6台电子秤给煤机、6只圆筒钢结构原煤斗。
采用5台运行、1台备用的运行方式;每炉配2台单速离心式风机,配2台可调轴流式送风机、2台离心式密封风机。
配置2套双室五电场除尘器。
两台锅炉共用一座高210m的烟囱。
燃烧系统主要设备及布局见表2-12。
2.7.3 热力系统锅炉产生的高压蒸汽通过主蒸汽管道,到汽轮机前再分两根分别接到汽轮机高压缸左右侧主汽门的管道,蒸汽输入汽轮机高压缸内做功,推动汽轮机转子高速运转,带动发电机发电。
做功后的蒸汽通过冷再热蒸汽管道进入再热器再加热,再通过热再热蒸汽管道回到汽轮机中压缸做功。
从汽轮机低压缸排出的蒸汽,经排汽装置通过1根的管道,流向空冷凝汽器,凝结水经排汽装置联箱收集于凝结水箱中,通过凝结水泵送入中压精处理装置处理后送入轴封加热器、各级低压加热器,最后至除氧器。
凝结水再循环管道由轴封加热器后引出至排汽装置。
高压加热器疏水串联疏水至除氧器,低压加热器疏水串联疏水至排汽装置。
热力工艺流程见图2-5。
热力系统主要设备:热力系统按7级抽汽回热系统设计,配3台低压加热器,3台高压加热器,1台除氧器;每台机组配3台50%容量的电动调速给水泵,2台运行,1台备用。
给水泵出口都单独接至除氧器给水箱。
3台高压加热器和3台低压加热器正常疏水都采用逐级回流以利用疏水热量。
高压加热器疏水串联疏水至除氧器,低压加热器疏水串联疏水至排汽装置。
轴封加热器疏水单独回流入排汽装置,疏水管路设置多级水封。
真空系统中设置3台水环式真空泵用以抽取空冷凝汽器内不凝结而分离出的气体。
每台机组均设置高、低压两个辅助蒸汽联箱向机组提供在启动、停机、正常运行和甩负荷等工况下符合参数要求的蒸汽。
其汽源来自老厂高压辅助蒸汽联箱、四段抽汽、冷再热蒸汽。
热力系统设备布局见表2-13 。
2.7.4热网站工艺本工程冬季是以供热为主、发电为辅的热电厂,本次在电厂内建热网首站,利用汽机抽汽加热外网供热热水。
本工程热网站为独立建筑,热网系统采用一级换热闭式循环、间接供热方式,以水为热媒。
热网循环水经热网循环水泵升压后,进入基加吸热,水温由60℃升至110℃,然后进入供热管网供给热用户。
本系统设有1台低压除氧器,由化学软化水箱来的补充水经软化水泵后进入低压除氧器,除氧水经热网补水泵进入热网循环泵入口的热网回水管道中循环。
热网疏水系统设有基加疏水泵,正常情况下,基加疏水返回到本机回热系统。
本次拟采用4台基本热网加热器设5台热网循环泵,其中一台备用,供水温度110℃,回水温度60℃,热网循环水量为8600t/h。
设有1台低压除氧器。
热网站生产工艺流程见图2-6。
2.7.5电气系统本工程两台机组,分别采用发电机-变压器-线路组接入厂外接入距电厂1km和2km的220kV新总降和九降压。
采用两台370MVA、220kV三相主变压器,主变高压侧经绝缘母线套筒接入厂内220kV GIS,低压侧通过离相封母接发电机出线套管。
高压侧采用全链式分相封闭母线,由发电机出线分支引出;低压侧采用共箱封闭母线,分别接入每台机组设置的两段6kV母线。
每台机组低压工作厂用电动力配电中心(PC)分别按汽机和锅炉配置。
高压侧经绝缘母线套筒接入厂内110kV GIS接入老厂的110kV 母线上,低压侧采用共箱封闭母线,分别“T”接接入两台机组的两段6kV母线。
电气及发电系统生产工艺流程见图2-7。
电气及发电系统主要设备及布局,见表2-14 。
2.7.6直接空冷系统采用直接空冷系统,单排管空冷凝汽器设计。
汽轮机排出的乏汽经由主排汽管道引出汽机房“A”列外,垂直上升至一定高度后,水平分管,再从水平分管分出支管,垂直上升,引至空冷凝汽器顶部。
蒸汽从空冷凝汽器上部联箱进入,与空气进行表面换热后冷凝。
进入空冷凝汽器的乏汽在轴流风机的作用下冷却成凝结水。
凝结水经空冷凝汽器下部的各单元凝结水管汇集至凝结水竖直总管,接至布置在汽机房内的排汽装置下部凝结水箱内。
通过凝结水泵打入凝结水凝结水精处理装置进行处理。
排汽主管道内的疏水通过疏水管道排至排汽装置下部的凝结水箱内。
直接空冷系统的风机均采用大直径的采用变频调速轴流风机。
每个空冷凝汽器单元拟配置一台轴流式风机,变频调速,每台机组共配置30台风机;两台机组共设清洗水泵一台。
本工程空冷凝汽器由顺流管束和逆流管束两部分组成。
按单排管空冷凝汽器进行设计,30个空冷凝汽器单元分6列垂直于A列布置,每列有5个空冷凝汽器单元,其中4个为顺流,1个为逆流,逆流空冷凝汽器放置在单元中部。
每台300MW机组共有300个管束。
直接空冷系统工艺流程见图2-8。
2.7.7 除灰渣系统2.7.7.1 除灰系统除灰系统拟采用正压浓相气力输送系统。
其工艺流程如下:在省煤器排灰斗、静电除尘器每个灰斗下设置一台输灰器,灰斗的排灰经输灰器由压缩空气通过管道输送至灰库。
灰库设有干灰分选系统。
灰库分选系统采用闭式循环,原状灰经给料机进入气灰混合器,与管内负压气流混合后进入分选机,分离出的粗灰经下部给料机落入粗灰库,细灰则随负压气流经旋风分离器后排入细灰库。