5why分析法
5Why问题分析法

➢新入员工发6双棉袜,收取半价 ➢每双袜子颜色不同,每天统一穿 一种颜色 ➢每天洗脚换袜子,宿监监督员工 ➢周日全体员工将工鞋带回家清洗
推导的同时进行验证
异常的发生
为什么? (原因/后果 关系)
CCCC
直接原因
为什么? (原因/后果 关系)
总结
5why的作用、用途 5why的步骤 5why分析法的注意事项
CCC C
为什么? 原因x
(原因/后果 关系)
CCC
原因xx
为什么? (原因/后果 关系)
CCC
原因xxx
为什么? (原因/后果 关系)
CCC
根本原因
“因此” 测试
注意-避免不自然的推论
WHY?
千万不能用类似借口的内容回答所提出的为什么
没有修理设备
设备全负荷运作
生产量多
作业方法没有明确 没有及时进行仪器矫正
LOGO
经理级技能提升培训之二
5Why问题分析法
故事的启示:袋鼠的篱笆
5WHY起源
丰田生产方式创始人大野耐一总是爱在车间 走来走去,停下来向工人发问。他反复地就一个 问题,问“为什么”,直到回答令他满意,被他 问到的人也心里明白为止——这就是后来著名的 “五个为什么”。
5WHY起源——
起源于日本丰田公司,当有人问丰田公司的总裁成功 的秘诀,他就说了这么一句话:碰到问题至少问五个 为什么。因此在日本流行开来,随著丰田的成功, 5WHY也流行到世界各地。
案例2 为什么杰弗逊纪念馆大厦墙壁受腐蚀
1.)为什么大厦表面班驳陈旧? 2.)为什么经常清洗呢?
专家发现,冲洗墙壁所用的清洁剂 对建筑物有腐蚀作用,该大厦墙壁 每年被冲洗的次数大大多余其他建 筑,腐蚀自然更加严重。
5Why分析法
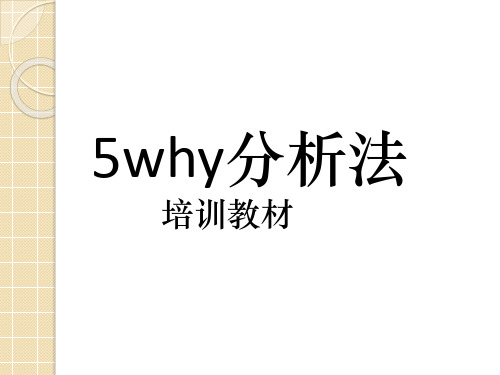
六.思考题:下列的5Why分析为什么失败?
X公司的产品质量做得不好,要是问生产:为什 么做不好?生产会说:材料不好。 于是问采购:为什么买的材料不好?现在收的货 款少,资金紧张。 问业务:为什么货款少?业务答:经济危机订单 量减少了,采购一般会答:财务不让我们买贵的材 料。 于是问财务:为什么要购买便宜的材料?财务答: 老板不给钱让我们去发展新业务…………
备注:一个不合格或潜在不合格可以有若干个原因
四. 纠正.纠正措施.预防措施的区别
1. 纠正和纠正措施 共同点: .都是措施; .都针对已发现的不合格的情况; 不同点: .纠正的目的是消除这次已发现的不合格,但 不能够避免下次再次发生; .纠正措施是针对已发现不合格的根本原因, 所以起到预防再次发生的目的。
2. 纠正措施和预防措施 共同点: .都是措施; .都起到预防的作用. 不同点: .预防措施在没有发生不合格前提下(往往从数据 分析得到这种预见和趋势),纠正措施在已发生不 合格情况下; .纠正措施的作用是预防不合格再次发生,而预防 措施的作用是预防不合格的发生.
五.纠正.纠正措施和预防措施案例(一) A商家的玻璃门被撞破了。 于是, A商家将撞破了的地方换上一块玻 璃——纠正; A商家为了不再发生撞玻璃事件,在新的玻璃 上用颜色笔画了一只眼睛,防止别人误撞— —纠正措施。 对面的B商家看到了,也在自己的玻璃上用颜 色笔写上“当心玻璃”,防止别人误撞—— 预防措施。
二. 5Why分析法案例(一)
问题 回答 回答 回答 一名工人,正将铁屑洒在机器之间的通道地面上 因为地面有点滑,不安全 因为那儿有油渍 因为机器在滴油
第一个为什么 为何你将铁屑洒在地面上
第二个为什么 为什么滑,不安全
第三个为什么 为什么会有油渍
5Why分析法

一、5W分析法 5Why应用步骤: 准确的认识问题,是解决问题的前提。
我们失败的原因多半是因为尝试用正确的方法解决错误的问题。 —— 阿可夫
一、5W分析法 5Why应用步骤:
千万别忽视第一步:
要向有关人员清晰陈述所发生的问题和相关信息,做到让所有相关人员都了 解要分析问题是什么,即使是不熟悉该类问题的人员。
一、5W分析法
找原因要找可控的原因,基于组织内部,要找内部的原因,而不能去找不可控的(比如顾客的原因)。 1.为什么滑倒了 因为没看到地上有水
2.为什么没看到地上有水
仰头走路,没有防范意识 3、为源自么仰头走路,没有防范意识? .... 思维方式的差异,有些喜欢找借口,这些借口就是那些不可控的原因。 1、问到第二个W时,可以采取纠正措施了,将水清除。 2、第一个至第四个W的潜在因子都存在摔跤者“大意摔跤”,如果他走路小心点,既使地面滑、既使地面有水, 只要他小心一点,他完全可以一步跨过或者绕道走。 3、第五个W的回答存在逻辑错误。 A、纸杯掉地上一定是因为没有杯托吗?
跟踪并核实结果。
问: • 解决方案有效吗? • 我如何确认?
• 使用5Why分析法检查清单
一、5W分析法
2、5Why注意点 1) 5W分析是指不能凭随便想象来考虑现象所产生的主要原因 而是要有规则、有顺序、毫无遗漏地来分析 用原理和原则核实的同时,从理论上来查明。
什么是5Why分析法?(附案例)
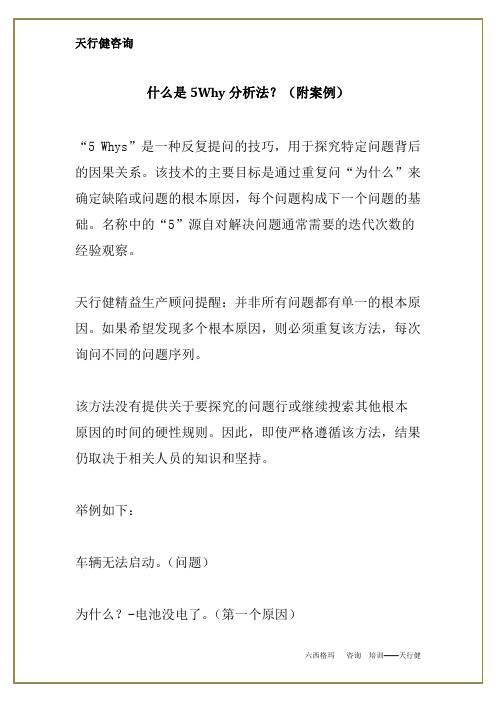
什么是5Why分析法?(附案例)
“5 Whys”是一种反复提问的技巧,用于探究特定问题背后的因果关系。
该技术的主要目标是通过重复问“为什么”来确定缺陷或问题的根本原因,每个问题构成下一个问题的基础。
名称中的“5”源自对解决问题通常需要的迭代次数的经验观察。
天行健精益生产顾问提醒:并非所有问题都有单一的根本原因。
如果希望发现多个根本原因,则必须重复该方法,每次询问不同的问题序列。
该方法没有提供关于要探究的问题行或继续搜索其他根本原因的时间的硬性规则。
因此,即使严格遵循该方法,结果仍取决于相关人员的知识和坚持。
举例如下:
车辆无法启动。
(问题)
为什么?-电池没电了。
(第一个原因)
为什么?-交流发电机不工作。
(第二个原因)
为什么?-交流发电机皮带断裂。
(第三个原因)
为什么?-交流发电机皮带已超过其使用寿命,未更换。
(第四个原因)
为什么?-车辆没有按照推荐的保养计划进行保养。
(第五个原因,根本原因)
这个例子的问题可以进一步深入到第六、第七或更高的层次,但五次反复询问原因通常足以找到根本原因。
关键是鼓励问题解决者避免假设和逻辑陷阱,而是以直接递增的方式追踪因果关系链,从效果到任何抽象层,再到与原始问题仍有一定联系的根本原因。
请注意,在本例中,第五个原因表明了一个中断的过程或一个可改变的行为,这表明达到了根本原因级别。
此外,在每个级别执行必要性和充分性的逻辑测试可以帮助避免选择虚假原因,并促进对多个根本原因的考虑。
改善工具-5why分析法
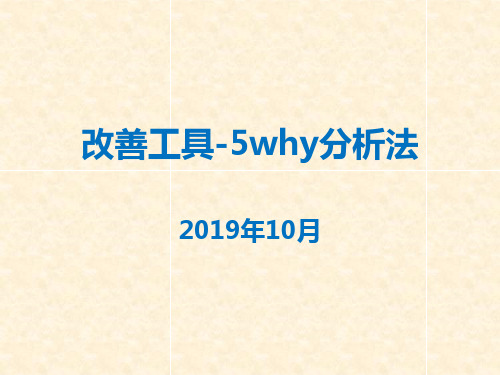
为什么?3 原因
为什么?4 原因
为什么?5
问题纠正
根本原因 对策/纠正措施
FMEA 预防措施
评估对策成效 流程标准化/吸取教训
基本情况调查 问题发生在哪块? “去看“问题
5wHY 根本原因调查分析
了解情况 抓住形势
原因调查
问题纠正 预防措施
解决问题 5why
为什么会发生 (失效链/技术层面)
5why分析法的应用原则
五个为什么
问五次为什么
5
5why分析法的应用要点
1.注意-避免不自然的推论 千万不能用类似借口的内容回答所提出的为什么: 没有修理设备 设备全负荷运作 生产量多 接了很多定单
作业方法没有明确
很少进行该作业
没有及时进行仪器矫正
要做的事情太多了
铅笔芯断了
用的是2B的铅笔
公司要赚钱
• 为什么要学习和使用5why:问题冰山
表面问题 潜在原因
现象(可感觉,可衡量) 问题表象
一次因(近因)
直接原因
中间原因
N次因(根因)
根本原因
• 为什么要学习和使用5why
顾客需求
格式易懂
1.对已确定的问题 根源做清晰的沟通
2.对缺乏的能力作 出说明以便发现问 题
3 .重视潜在的系统 性问题
1 . 5why图表会把 因果路径简单地呈 现出来
5why分析法的关键
多问几次”为什么”
鼓励解决问题的人要努力避开主观或自负的假设和逻辑陷阱, 从结果着手,沿着因果关系链条,顺藤摸瓜,穿越不同的抽象层面, 直至找出原有问题的根本原因。
保证非专业人员也能轻松看懂分析报告,明白根本原因。
5why分析法的应用
5WHY分析法:一个问题分析与解决的工具
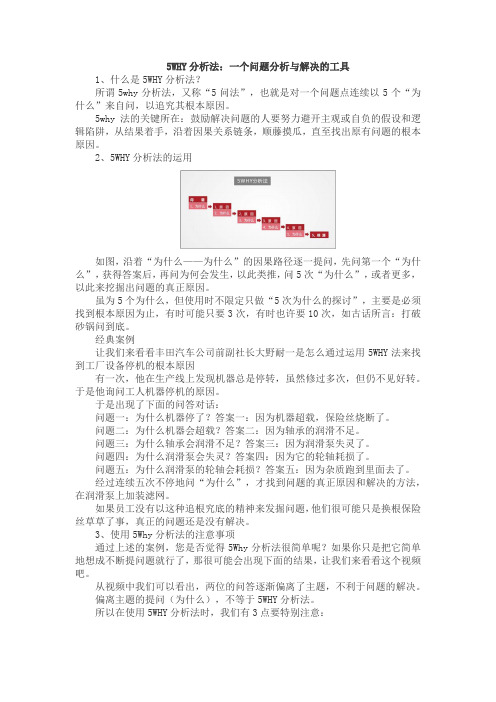
5WHY分析法:一个问题分析与解决的工具1、什么是5WHY分析法?所谓5why分析法,又称“5问法”,也就是对一个问题点连续以5个“为什么”来自问,以追究其根本原因。
5why法的关键所在:鼓励解决问题的人要努力避开主观或自负的假设和逻辑陷阱,从结果着手,沿着因果关系链条,顺藤摸瓜,直至找出原有问题的根本原因。
2、5WHY分析法的运用如图,沿着“为什么——为什么”的因果路径逐一提问,先问第一个“为什么”,获得答案后,再问为何会发生,以此类推,问5次“为什么”,或者更多,以此来挖掘出问题的真正原因。
虽为5个为什么,但使用时不限定只做“5次为什么的探讨”,主要是必须找到根本原因为止,有时可能只要3次,有时也许要10次,如古话所言:打破砂锅问到底。
经典案例让我们来看看丰田汽车公司前副社长大野耐一是怎么通过运用5WHY法来找到工厂设备停机的根本原因有一次,他在生产线上发现机器总是停转,虽然修过多次,但仍不见好转。
于是他询问工人机器停机的原因。
于是出现了下面的问答对话:问题一:为什么机器停了?答案一:因为机器超载,保险丝烧断了。
问题二:为什么机器会超载?答案二:因为轴承的润滑不足。
问题三:为什么轴承会润滑不足?答案三:因为润滑泵失灵了。
问题四:为什么润滑泵会失灵?答案四:因为它的轮轴耗损了。
问题五:为什么润滑泵的轮轴会耗损?答案五:因为杂质跑到里面去了。
经过连续五次不停地问“为什么”,才找到问题的真正原因和解决的方法,在润滑泵上加装滤网。
如果员工没有以这种追根究底的精神来发掘问题,他们很可能只是换根保险丝草草了事,真正的问题还是没有解决。
3、使用5Why分析法的注意事项通过上述的案例,您是否觉得5Why分析法很简单呢?如果你只是把它简单地想成不断提问题就行了,那很可能会出现下面的结果,让我们来看看这个视频吧。
从视频中我们可以看出,两位的问答逐渐偏离了主题,不利于问题的解决。
偏离主题的提问(为什么),不等于5WHY分析法。
5Why分析法

应用高级工具
•7
5WHY定义及由来
•8
什么是5WHY分析 5个WHY分析,又称“为什么-为什么”分析。是一
种探索问题原因的方法。 对一个问题连续发问5次,每一个“原因”都会紧
跟着另外一个“为什么?”直到问题的根源
被确定下来。
–为什么?”
–为什么?”
–为什么?”
–为什么?” –为什么?”
•9
5WHY分析法的由来
5个Why分析又称5问法,最初由丰田公司提出幷在丰田公司广泛 采用,因此也被称为丰田5问法。
5个Why报告在日系企业利用的很多,其首创是丰田公司的大野奈一,来源于 一次新闻发布会,有人问,丰田公司的汽车质量怎么会这么好?他回答说:我碰 到问题至少要问5个为什么。
大野耐一总是爱在车间走来走去,停下来向工人发问。他反复地就一个问 题,问“为什么”,直到回答令他满意,被他问到的人也心里明白为止——这就是 后来著名的“五个为什么”。
2、对缺乏的能力 作出说明以便发现 问题
3、重视潜在的系 统性问题
格式易懂
1、5Why图表会把 因果路径简单地呈 现出来
2、因果会被概括 成摘要而不需要技 术细节
大众语言
1、不是所有人都 十分精通6个西格 码术语 2、使将来的参考 书和问题指南更容 易理解 3、既考虑顾客的 满意度又兼顾厂商 的发展
系统的问题解决方法和传统的质量控制工具均有助于改
善业绩,但并非唯一的途径。
问题比率
100
➢ 5why ➢ 3 C(问题/原因 /对策)
经验证明,多数工作 问题可用简单的方法 予以解决。关键在于
纪律性和实施。
➢ 系统的问题解决方法 ➢ 传统的质量控制工具
50
➢ 试验设计 ➢ 田口法
5Why问题分析法完整版

•2W
•为什么sb?
•sc引起
•3W
•为什么sc?
•sd引起
•4W
•为什么sd?
•se引起
•5W
•为什么se?
•Root case 真因引起
•S真因3纠正措施:
5Why解决问题方式:透过5M1E作系统分析 •人、机、料 •为什么该特定问题会发生?
•方法 •为什么该问题没有被检查、检验到?
•环境 •为什么管理体系、流程会允许该问题发生?
掉。 问: • 临时措施会遏止问题直到永久解决措施能被实施吗?
通过不断提问为什么前一个事件会发生,直到回答“没 有好的理由”或直到一个新的故障模式被发现时才停止提问。 解决根本原因以防止问题重演。文件中所有带有“为什么” 的语句都会定义真正的根源(通常需要至少5个“为什么”, 但5个Why不是说一定就是5个,可能是1个,也可能是连问10鼓励解决问题的人要努力避开主观或自负的假设和逻辑 陷阱,从结果着手,沿着因果关系链条,顺藤摸瓜,穿越不 同的抽象层面,直至找出原有问题的根本原因。
5Why简介:
用中国古代的成语来说就是:“打破沙锅问到底”的习 惯,包含了锲而不舍、不断探索、追本溯源的精神。
5Why的应用:
5Why分析有助于解决零星的品质缺陷引发的问题。 5Why分析被用作一个解决实际问题过程的一部分,即根本 原因分析和调查。
5Why应用步骤: 准确的认识问题,是解决问题的前提。
我们失败的原因多半是因为尝试用正确的方法 解决错误的问题。
—— 阿可夫
5Why应用步骤:
千万别忽视第一步: 要向有关人员清晰陈述所发生的问题和相关信息,做到
让所有相关人员都了解要分析问题是什么,即使是不熟悉该 类问题的人员。
- 1、下载文档前请自行甄别文档内容的完整性,平台不提供额外的编辑、内容补充、找答案等附加服务。
- 2、"仅部分预览"的文档,不可在线预览部分如存在完整性等问题,可反馈申请退款(可完整预览的文档不适用该条件!)。
- 3、如文档侵犯您的权益,请联系客服反馈,我们会尽快为您处理(人工客服工作时间:9:00-18:30)。
Make by品质部:LIAO SHU ZHI Date :2018年6月27日
• 简介 • 这种方法最初是由丰田佐吉提出的;后来,丰田汽 车公司在发展完善其制造方法学的过程之中也采用 了这一方法。作为丰田生产系统(Toyota Production System)的入门课程的组成部分,这种方法成为其 中问题求解培训的一项关键内容。丰田生产系统的 设计师大野耐一曾经将五问法描述为:“……丰田科 学方法的基础……重复五次,问题的本质及其解决办 法随即显而易见。”目前,该方法在丰田之外已经得 到了广泛采用,并且现在持续改善法(Kaizen), 精益生产法(lean manufacturing)以及六西格玛法 之中也得到了采用。
• 现在,焦点集中在查找问题原因的实际要点上。你需要追溯来了 解第一手的原因要点。问: • 我需要去哪里? • 我需要看什么? • 谁可能掌握有关问题的信息? • ★步骤5:把握问题的倾向 • 要把握问题的倾向,问: • 谁? • 哪个? • 什么时间? • 多少频次? • 多大量? • 在问为什么之前,问这些问题是很重要的。 • 第二部分: 原因调查 • ★步骤6:识别并确认异常现象的直接原因。 • 如果原因是可见的,验证它。如果原因是不可见的,考虑潜在原 因并核实最可能的原因。依据事实确认直接原因。问:
• • • • • •
• • • • • • • • •
这个问题为什么发生? 我能看见问题的直接原因吗? 如果不能,我怀疑什么是潜在原因呢? 我怎么核实最可能的潜在原因呢? 我怎么确认直接原因? ★步骤7:使用“5个为什么”调查方法来建立一个通向根本原因的 原因/效果关系链。 问:处理直接原因会防止再发生吗? 如果不能,我能发现下一级原因吗? 如果不能,我怀疑什么是下一级原因呢? 我怎么才能核实和确认下一级有原因呢? 处理这一级原因会防止再发生吗? 如果不能,继续问“为什么”直到找到根本原因。在必须处理以防 止再发生的原因处停止,问: 我已经找到问题的根本原因了吗? 我能通过处理这个原因来防止再发生吗? 这个原因能通过以事实为依据的原因/效果关系链与问题联系起来 吗?
谢谢
• • • • •
实施方法 5WHY从三个层面来实施: 一、为什么会发生?从“制造”的角度。 二、为什么没有发现?从“检验”的角度。 三、为什么没有从系统上预防事故?从“体系” 或“流程”的角度。 • 每个层面连续5次或N次的询问,得出最终结论。 只有以上三个层面的问题都探寻出来,才能发 现根本问题,并寻求解决。
• 经典案例 • 丰田汽车公司前副社长大野耐一曾举了一个例子来找出停机的真 正原因 • ★问题一:为什么机器停了? • 答案一:因为机器超载,保险丝烧断了。 • ★问题二:为什么机器会超载? • 答案二:因为轴承的润滑不足。 • ★问题三:为什么轴承会润滑不足? • 答案三:因为润滑泵失灵了。 • ★问题四:为什么润滑泵会失灵? • 答案四:因为它的轮轴耗损了。 • ★问题五:为什么润滑泵的轮轴会耗损? • • 答案五:因为杂质跑到里面去了。 • 经过连续五次不停地问“为什么”,才找到问题的真正原因和解决 的方法,在润滑泵上加装滤网。 • 如果员工没有以这种追根究底的精神来发掘问题,他们很可能只 是换根保险丝草草了事,真正的问题还是没有解决。
• • • • • • • • • • • • • • • •
这个链通过了“因此”检验了吗? 如果我再问“为什么”会进入另一个问题吗? 确认你已经使用“5个为什么”调查方法来回答这些问题。 为什么我们有了这个问题? 为什么问题会到达顾客处? 为什么我们的系统允许问题发生? ★步骤8:采取明确的措施来处理问题 使用临时措施来去除异常现象直到根本原因能够被处理掉。问: 临时措施会遏止问题直到永久解决措施能被实施吗? 实施纠正措施来处理根本原因以防止再发生。问: 纠正措施会防止问题发生吗? 跟踪并核实结果。问: 解决方案有效吗? 我如何确认? 为什么一为什么分析法检查清单 为确认你已经按照问题解决模型操作,当你完成问题解决过程时, 使用这个检查清单。
5WHY分析法询问与回答技巧
• 通常情况下,在询问为什么的时候,因为是发散性思维,很难 把握询问和回答者的在受控范围内。 • 比如:这个工件为什么尺寸不合格?因为装夹松动; • 为什么装夹松动?因为操作工没装好; • 为什么操作工没装好?因为操作工技能不足; • 为什么技能不足?因为人事没有考评 • 类似这样的情况,在5Why分析中,经常发现。 • 所以,我们在利用5Why进行根本原因分析时,一定要把握好一 些基本原则: • 1)回答的理由是受控的; • 2)询问和回答是在限定的一定的流程范围内; • 3)从回答的结果中,我们能够找到行动的方向。 •
ห้องสมุดไป่ตู้
5why分析法解决问题的基本步骤
• 第一部分:把握现状 • ★步骤1:识别问题 • 在方法的第一步中,你开始了解一个可能大、模糊或复杂的问题。你 掌握一些信息,但一定没有掌握详细事实。 • 问:我知道什么? • ★步骤2:澄清问题 • 方法中接下来的步骤是澄清问题。为得到更清楚的理解,问: • 实际发生了什么? • 应该发生什么? • ★步骤3:分解问题 • 在这一步,如果必要,需要向相关人员调查,将问题分解为小的、独 立的元素。 • 关于这个问题我还知道什么? • 还有其他子问题吗? • ★步骤4:查找原因要点(PoC)