轧机工艺润滑站乳化液磁性过滤器的改进
单机架冷轧机乳化液系统的改进与应用
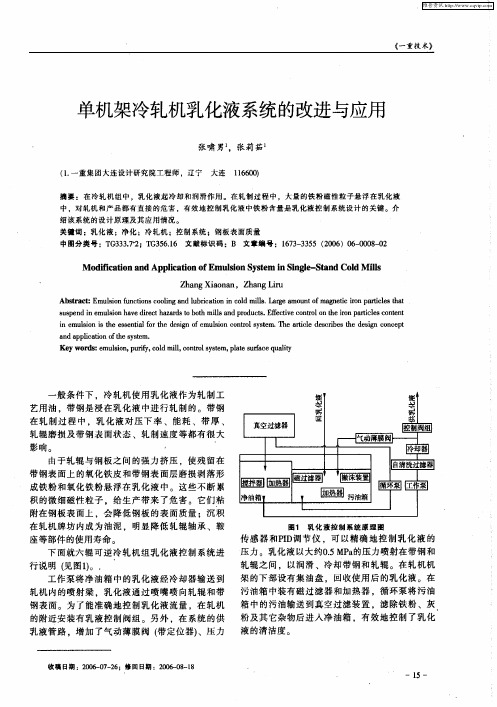
收 稿 日期 :2 0 — 7 2 ;修 回 日期 :2 0 — 8 1 060 —6 06 0 — 8
般条 件下 。冷 轧机 使 用乳 化 液作 为 轧制 工 艺 用油 。带 钢是 浸 在乳 化 液 中进 行 轧制 的。带 钢
一
在 轧 制 过程 中 。乳 化 液 对 压 下率 、能耗 、带 厚 、
轧辊 磨 损及 带钢 表 面状 态 、轧制 速 度等 都 有很 大 影 响。 一 由 于轧辊 与 钢板 之 间的 强力 挤 压 ,使 残 留在 带钢 表 面 上 的氧化 铁皮 和 带钢 表 面层磨 损 剥落 形
a da p i ai no e s se n p l t f y t m. c o h t
Ke r s e lin p r y c l l c nrl ytm, lt u a eq ai ywo d : muso , ui , odmi, o to s f l s e paes r c u  ̄ f l
s se di muso a edrc a ad ohmisa dpo u t. f ciec nrl ntei np rce o tn u p n e l nh v i t z rs ob t l n rd cs E et o t at ls ne t n i e h t l v o o h r o i c i muso ees nilfrted sg fe l o o t l ytm. h rced srb sted s n c n e t ne l ni t se t h e ino mus nc nr se T ea il e c e ei o c p i sh a o i o s t i h g
可逆冷轧机乳化液系统改造与优化

可逆冷轧机乳化液系统改造与优化摘要:近年来,我国的工业化进程有了很大进展,轧机的应用也越来越广泛。
本文基于金泰包装1200mm可逆冷轧机乳化液系统,通过对供乳方式、循环设备、加热方式及磁过滤器等设备进行改进,有效解决了薄规格边部热擦伤、乳化液寿命低、过滤精度差等问题,改善了带钢板面质量,适应了产品结构调整的需要。
关键词:冷轧;乳化液;改造引言轧机是钢板带厂的关键设备,为钢板带厂下游工序提供重要保障,签于其在钢板带生产中的重要作用,对该设备的维护、检修及故障的快速处理也显得越来越重要。
卷取机张力的稳定性直接影响带材的质量和成品率,尤其在带材被拖动动态升降速的过程中,更要保持张力的恒定以免出现断带。
所以本文着重对该轧机卷取机的张力控制系统进行简单的阐述,并对常见的张力故障加以分析、总结,以提高设备维护水平,提高产品质量和成品率。
1乳化液斑特征乳化液斑多出现在轧机的头部,也就是重卷的尾部,在重卷或平整时可清楚观察到:距尾部50m左右时开始出现(时多时少,50m只是一个大致的平均数,严重时通条都存在),起始是在带钢的边部和中部浪形区,沿带钢纵向呈条状或细长条状;随着带钢到尾部距离的缩短,斑迹的密度增大,在距尾部30m时大量出现,呈一定间距平行条状排列,有的整个区域上下表面均产生乳化液斑,斑迹的形状、大小基本一致。
斑迹大多呈黄褐色,轻者呈黄色,重者呈灰黑色,斑迹无法用擦拭物擦除。
2金泰包装 1200mm乳化液循环系统存在的问题1)乳化液箱采用老式的蒸汽盘管的加热方式,里面铺设复杂的加热蒸汽管道,容易在蒸汽管道缝隙造成油泥沉淀和板结,清理困难,蒸汽加热效率低。
2)控制温度、液位的各路控制阀门的启闭都分别需要岗位工人从轧机操作台跑到乳化液站来进行人工调节,如果指标不稳定,就会经常造成过润滑、欠润滑、乳化液浓度波动大等问题,出现薄规格产品糊边、变形区温度过高引起的粘辊或钢带断裂等事故。
3)污油箱存在着循环“死角”,容易形成大量的浮油,极大地降低了乳化液的使用寿命和质量,常时间的开启磁过滤器,不仅增加了油耗,还造成了润滑不足。
轧机乳化液系统改造
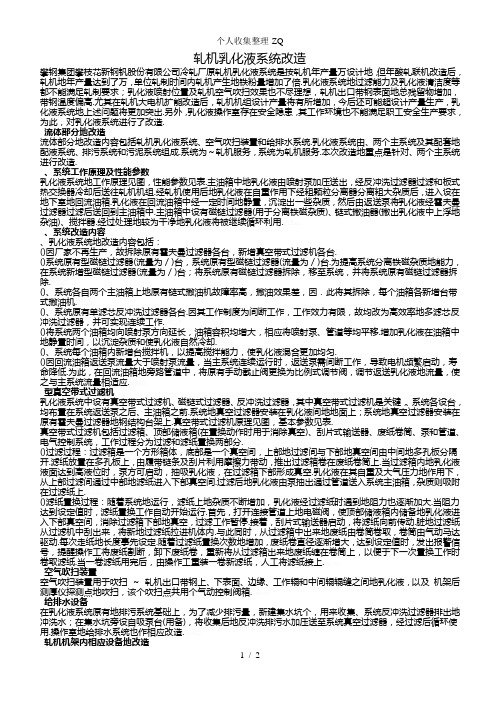
个人收集整理-ZQ轧机乳化液系统改造攀钢集团攀枝花新钢钒股份有限公司冷轧厂原轧机乳化液系统是按轧机年产量万设计地,但年酸轧联机改造后,轧机地年产量达到了万,单位轧制时间内轧机产生地铁粉量增加了倍.乳化液系统地过滤能力及乳化液清洁度等都不能满足轧制要求;乳化液喷射位置及轧机空气吹扫效果也不尽理想,轧机出口带钢表面地总残留物增加,带钢温度偏高.尤其在轧机大电机扩能改造后,轧机机组设计产量将有所增加,今后还可能超设计产量生产,乳化液系统地上述问题将更加突出.另外,乳化液操作室存在安全隐患,其工作环境也不能满足职工安全生产要求,为此,对乳化液系统进行了改造.流体部分地改造流体部分地改造内容包括轧机乳化液系统、空气吹扫装置和给排水系统.乳化液系统由、两个主系统及其配套地配液系统、排污系统和污泥系统组成.系统为~轧机服务,系统为轧机服务.本次改造地重点是针对、两个主系统进行改造.b5E2R.、系统工作原理及性能参数乳化液系统地工作原理见图,性能参数见表.主油箱中地乳化液由喷射泵加压送出,经反冲洗过滤器过滤和板式热交换器冷却后送往轧机机组.经轧机使用后地乳化液在自重作用下经粗颗粒分离器分离粗大杂质后,进入设在地下室地回流油箱.乳化液在回流油箱中经一定时间地静置,沉淀出一些杂质,然后由返送泵将乳化液经霍夫曼过滤器过滤后送回到主油箱中.主油箱中设有磁链过滤器(用于分离铁磁杂质)、链式撇油器(撇出乳化液中上浮地杂油)、搅拌器.经过处理地较为干净地乳化液将被继续循环利用.p1Ean.、系统改造内容、乳化液系统地改造内容包括:()因厂家不再生产,故拆除原有霍夫曼过滤器各台,新增真空带式过滤机各台.()系统原有型磁链过滤器(流量为/)台,系统原有型磁链过滤器(流量为/)台.为提高系统分离铁磁杂质地能力,在系统新增型磁链过滤器(流量为/)台;将系统原有磁链过滤器拆除,移至系统,并将系统原有磁链过滤器拆除.DXDiT.()、系统各自两个主油箱上地原有链式撇油机故障率高,撇油效果差,因.此将其拆除,每个油箱各新增台带式撇油机.RTCrp.()、系统原有单滤芯反冲洗过滤器各台.因其工作制度为间断工作,工作效力有限,故均改为高效率地多滤芯反冲洗过滤器,并可实现连续工作.5PCzV.()将系统两个油箱均向喷射泵方向延长,油箱容积均增大,相应将喷射泵、管道等均平移.增加乳化液在油箱中地静置时间,以沉淀杂质和使乳化液自然冷却.jLBHr.()、系统每个油箱内新增台搅拌机,以提高搅拌能力,使乳化液混合更加均匀.()因回流油箱返送泵流量大于喷射泵流量,当主系统连续运行时,返送泵需间断工作,导致电机频繁启动,寿命降低.为此,在回流油箱地旁路管道中,将原有手动截止阀更换为比例式调节阀,调节返送乳化液地流量,使之与主系统流量相适应.xHAQX.型真空带式过滤机乳化液系统中设有真空带式过滤机、磁链式过滤器、反冲洗过滤器,其中真空带式过滤机是关键,、系统各设台,均布置在系统返送泵之后、主油箱之前.系统地真空过滤器安装在乳化液间地地面上;系统地真空过滤器安装在原有霍夫曼过滤器地钢结构台架上.真空带式过滤机原理见图,基本参数见表.LDAYt.真空带式过滤机包括过滤箱、顶部储液箱(在置换动作时用于消除真空)、刮片式输送器、废纸卷筒、泵和管道、电气控制系统,工作过程分为过滤和滤纸置换两部分.Zzz6Z.()过滤过程:过滤箱是一个方形箱体,底部是一个真空间,上部地过滤间与下部地真空间由中间地多孔板分隔开.滤纸放置在多孔板上,由履带链条及刮片利用摩擦力带动,推出过滤箱卷在废纸卷筒上.当过滤箱内地乳化液液面达到高液位时,泵方可启动,抽吸乳化液,在过滤箱下部形成真空.乳化液在其自重及大气压力地作用下,从上部过滤间通过中部地滤纸进入下部真空间.过滤后地乳化液由泵抽出通过管道送入系统主油箱,杂质则吸附在过滤纸上.dvzfv.()滤纸置换过程:随着系统地运行,滤纸上地杂质不断增加,乳化液经过滤纸时遇到地阻力也逐渐加大.当阻力达到设定值时,滤纸置换工作自动开始运行.首先,打开连接管道上地电磁阀,使顶部储液箱内储备地乳化液进入下部真空间,消除过滤箱下部地真空,过滤工作暂停.接着,刮片式输送器启动,将滤纸向前传动.脏地过滤纸从过滤机中刮出来,将新地过滤纸拉进机体内.与此同时,从过滤箱中出来地废纸由卷筒卷取,卷筒由气动马达驱动.每次走纸地长度事先设定.随着过滤纸置换次数地增加,废纸卷直径逐渐增大,达到设定值时,发出报警信号,提醒操作工将废纸割断,卸下废纸卷,重新将从过滤箱出来地废纸缠在卷筒上,以便于下一次置换工作时卷取滤纸.当一卷滤纸用完后,由操作工重装一卷新滤纸,人工将滤纸接上.rqyn1.空气吹扫装置空气吹扫装置用于吹扫~轧机出口带钢上、下表面、边缘、工作辊和中间辊辊缝之间地乳化液,以及机架后测厚仪探测点地吹扫,该个吹扫点共用个气动控制阀箱.Emxvx.给排水设备在乳化液系统原有地排污系统基础上,为了减少排污量,新建集水坑个,用来收集、系统反冲洗过滤器排出地冲洗水;在集水坑旁设自吸泵台(用备),将收集后地反冲洗排污水加压送至系统真空过滤器,经过滤后循环使用.操作室地给排水系统也作相应改造.SixE2.轧机机架内相应设备地改造个人收集整理-ZQ轧机机架内地改造内容包括:()乳化液喷射粱及相应设备:在、系统压力总管中,各增设个可调式减压阀,以控制乳化液压力,满足轧机内乳化液喷嘴对压力地要求.对~机架内地乳化液喷射梁重新设计制造,包括喷嘴型号、固定方式、喷嘴数量、空间位置及流量设计等;对轧机机架内地入口导板和侧导板进行改造,以适应新地喷射梁安装位置变化.6ewMy. ()压板:拆除现有入口导板上压板、安装支架及驱动装置、侧导装置上部侧导板( 机架为侧导辊);安装新设计地入口导板上压板装置和防溅挡板,使之与改造后地入口乳化液喷射梁地安装位置相适应.新地上压板及驱动装置安装在入口导板框架内,上压板地压下和抬起由气缸驱动,并设有导向装置以保证压板地运动方向.kavU4. () 机架出口排烟罩:该排烟罩用于收集和排除从轧机区过来地乳化液烟气,以防止乳化液蒸汽冷凝后回落到带钢上而污染带钢.y6v3A.电气及自动化部分地改造乳化液系统电动机控制装置将乳化液系统电动机地控制装置全部更新,其中小容量地电动机采用抽屉式柜进行控制,大容量地电动机采用固定分隔式柜进行控制.台真空过滤泵采用变频控制,仍通过直接/与现有进行通讯.M2ub6.基础自动化乳化液系统地控制仍采用原有公司地,实施逻辑控制和状态监视.新增地真空带式过滤机、磁链过滤器和多滤芯自动清洗过滤器为机电一体化设备,自带现场控制箱,通过直接/与进行通讯.新增地带式撇油机、搅拌机和集水坑排水泵为单体设备,由原控制中心控制,并通过直接/与进行通讯.新增一个通道模拟量输入模块用于新增模拟量地通讯,其余地数字量/点全部利用旧设备.0YujC.在乳化液间重新设置一个操作室,新增一套操作站和一个操作台,乳化液系统原有和新增地电控设备均可通过该操作站完成操作、参数设定、设备状态显示、测量值显示、故障监视和报警、报表打印等.操作站与之间通过以太网进行通讯.eUts8.自动化仪表主要检测控制项目包括:系统供液主管及各机架分管地流量及压力监控、系统温度监控,乳化液站新增地检测控制信号送控制系统,操作和监控在新增地操作站上完成.现场仪表主要有温度计、电磁流量计、压力变送器和气动调节阀等.sQsAE.其他部分地改造拆除原有操作室,新增乳化液操作室,乳化液间化验室和电控室各设置柜式空调机,以消除设备发热量.结语该工程于年月启动,于年月圆满完成.通过改造,提高了乳化液系统清洁度,改善了轧制润滑效果(见表);降低了轧制过程地主电机负荷,为开发高强度和大变形量地品种创造有利条件;提高了轧后带钢板形质量和带钢表面质量;减少了轧辊地消耗,节约轧辊生产成本;随着乳化液本身地清洁性地提高,后续工序地清洗剂用量和氢气用量都会减少,降低了后工序地生产成本;重建了乳化液操作室,改善了操作人员地工作环境.GMsIa.。
冷轧厂轧机油气润滑系统优化及改进

冷轧厂轧机油气润滑系统优化及改进摘要:本文重点探讨了油气润滑的特点和工作原理,阐述了REBS油气润滑系统在某冷轧厂轧机工作辊和中间辊径向轴承润滑中的应用及优化,并简单介绍了应用中油气润滑系统存在的不足和改善措施。
关键词:油气润滑;径向轴承;原理;优化;改善措施前言油气润滑是新型的“气流两相流体”技术的典型工业应用。
油气润滑因具有润滑效果好、耗油量低、可精确计量给油、可实现高速自动控制和可使用润滑油品黏度范围大等优点,在自动化程度高的工业领域得到了广泛应用,尤其是在高温、高速、重载和使用环境恶劣的冶金领域的辊道运输线、单机架和串列机架冷轧机、线材轧机的高速转动导向装置以及连铸设备等。
1.油气润滑的工作原理1.1 油气润滑的形成和本质在一个管状的空间内,连续间断给定的润滑油被2~4bar的压缩空气从一端吹向另一端的连续作用下,润滑油在“附壁效应”的作用下从颗粒状态逐渐吹散和变薄,形成无雾化沿管壁连续流动的气动波浪油膜,即形成了“气液两相流体”中的油气。
单相流体油和单相流体压缩空气混和后就形成了两相油气混合流,两相油气混合流中油和压缩空气并不真正融合,而是在压缩空气的流动作用下,带动润滑油沿管道内壁不断地螺旋状流动并形成一层连续油膜最后以精细的连续油滴的方式喷到润滑点。
1.2 油气润滑的润滑机理沿管壁连续流动的气动波浪油膜到达润滑点后,在摩擦副表面形成油膜,隔绝相互摩擦的表面,使干摩擦状态变为液体摩擦状态或准液体摩擦状态;流动的压缩空气可以冷却摩擦副,带走热量,阻止润滑油高温碳化。
同时压缩空气使摩擦副腔内形成正压,可避免外部环境中的赃物和腐蚀流体侵入摩擦副,保证了摩擦副良好的工作环境。
2.油气润滑的特点油气润滑就是应用“气液两相流体”原理进行工作的,与传统的润滑方式(如干油、稀油和油雾润滑)相比,主要特点可归结为:(1)润滑效率高,可以大幅提高轴承的使用寿命。
由于油气润滑在供油量、轴承温度和摩擦三者间找到了最佳平衡点,即用最小的供油量达到降低轴承温度和有效润滑的最佳效果,润滑剂的利用率几乎达100%。
1550酸轧机组乳化液系统磁性过滤器的改造

I— — 气 缸 2— — f- 吲 刮 耙 3— — F 阅 刮 耙 4— — 轴 承 座 5— — 曲 机 构
改 造 J
l 磁性 过滤 器结 构示 意图
l 轴 下 轴 刮 把 下 刮把 磁棒 承 承 座
厂
/
…
…
…
黾
~
_{ =|
—
.
一
二~{ :} {
■
-
J
一/ i7,
J 鱼 …
…
。I●
。/ //
//|| | }
l㈡ ||| .
盟
I
^ .
,
I
,l1
n
|
I /¨ .
f/¨ 。 7
1— — 磁 怍 ; 2— — 七 刮 耙 ; 3— — 下 刮 耙 ; 4—— 推 中『: 5— — 挡 铁 ; 6—— 链 轮 、链 条 :7—— 齿 轮 电 机 ; 8— — 滑 块 9—— _Il1柄机 构
2 圆形刮 耙 设计 罔
3 结 语
该 设 计 简 化 了磁 性 过 滤 器 刮污 装 置 的 传 动 机构 ,使 用 更 加 简单 平 稳 。链 轮式 刮 耙 动 作平 稳 ,设 计 、安 装 与维护 具 有 极 (下转 第 62页 )
62
柳 钢 科 技
2018年第 1期
备件让步接收实践
1 前 言
该 批球 阀 阀体 的材 质 ,含 Ni质 量 分 数 为 10%。
在备件基本质量保证 的条件下 ,对备 件的 质量 缺 陷 部 分有 条 件 地接 收 ,双 方 对 备 件 降价 达 成 协 议 ,就 是 备 件 的 让 步 接 收 处 置 。 随 着柳 钢备 件 质 检 工作 的 深 入 ,购买 的 部分 备 件 没 有 达到合 同技术要求 ,但能满足使 用要求 ,经相 关部 门或使 用 单 位 同意 后 可对 该备 件 让 步接 收 , 以利 于 生 产 保 供 。本 文 总 结 柳 钢 实 施 备 件 让 步
轧机主轴承油气润滑系统分析及改进措施

关键词 : 轧机 ; 轴承 ; 油 气 润 滑
中 图分 类 号 : TG 2 4 2 文献标识码 : A
1 轴 承 润 滑 的机 理
润 滑 是 用 润 滑 剂 减 少 摩 擦 副 的摩 擦 和 降低 温
度, 或 改善 其他 形 式 的 表 面破 坏 的措施 。合 理选 择
有 实际 意义 。轧机 的轴 承润 滑大致 分 以下几 个发 展
阶段 : 一 是油脂 润 滑 阶 段 , 轧 制 过程 中 , 乳 化 液 和 碎
v =3 U _80m/ s
屑 与润 滑脂接 触 , 会降 低润 滑膜粘 着力 , 润滑 膜脱 落
后 轴承 表面 温度 会显 著提 高 , 当轧制 速度超 过 1 2 0 0
第 3 O卷第 1 期 2 0 1 4年 2月
有 色 矿 冶
N 0N — F ERR oUS MI NI NG AN D M ET A LL U RG Y
V o1 . 3 O .№ 1
Fe br ua r y 2 0 1 4
文章 编 号 : l O O 7 —9 6 7 X( 2 o 1 4 ) O l 一0 0 4 0 —0 3
粘 度≤ 7 6 0 mm。 / s ( 4 0 ℃) , 相 当于粘度 牌号 N6 8 0以
速度 , 系统 温度 不断 升高 , 随着 温度 的升 高散 热速 度 则 在不 断加 快 , 当产 热 速 度 在 某 一 时 刻等 于 系 统 的
散 热速 度 , 系统 的温 度 达 到一 个 恒 定 值 。这 个 温 度 值 是选 择润 滑 油 的关 键 , 如果 润滑 油选 择不恰 当 , 则 会 导致 润滑 油膜 破 裂 , 润滑 失 效 。 而散 热 速 度 又 与
乳化液性能参数对冷轧生产线轧制稳定性的影响
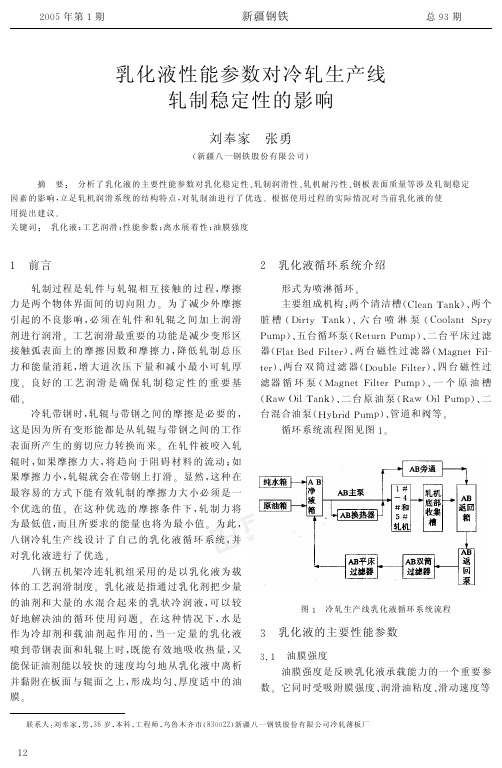
图 %! 皂化值
+ * ) -
皂化 值 是 评 价 轧 制 油 润 滑 性 能 的 重 要 指 标 " 其 反映轧制油中的动 植 物 油 脂 肪 酸 含 量 " 通常是用氢 氧化钾与轧制油浓 缩 油 进 行 皂 化 反 应 " 一克浓缩油
! &
% $ $ + 年第 ! 期
新疆钢铁
总# &期
,! 乳化液使用过程中的一些建议
%! 乳化液循环系统介绍
形式为喷淋循环 % 主要组成机构 ’ 两个清洁槽 ! # 两个 8 D E F GH F G 2" 脏槽 ! #六 台 喷 淋 泵 ! 0 I J ’ F G 2" 8 L L D F G ’M J KH ? K " # 五台循环泵 ! " # 二 台 平 床 过 滤 1 N . O E ’ N J G1 N . ? ? 器! " # 两台磁性过滤器! P D F ’: E QP I D ’ E J C F G E ’P I D R 3 " # 两台 双 筒 过 滤 器 ! " # 四台磁性过 ’ E J 0 L N S D EP I D ’ E J 滤器 循 环 泵 ! # 一个原油槽 C F G E ’P I D ’ E J1 N . 3 ?" ! # 二台原油泵! # 二 O F TU I DH F G 2" O F TU I D1 N . ?" 台混合油泵 ! " # 管道和阀等 % 7 S J I Q1 N . K ? 循环系统流程图见图 !%
新疆钢铁
总# &期
所消耗氢氧化钾的 毫 克 数 即 为 此 轧 制 油 的 皂 化 值 ! 一般认为轧制油的皂化值越高 " 其润滑效果越好 ! &" *! 铁粉含量 轧制 生 产 中 " 由于机械设备的磨损以及轧辊与 带钢的摩擦可产生 大 量 的 铁 粉 " 乳化液系统的磁性 过滤器能将这些影响产品表面质量的铁粉滤去 ! 如 果乳化液与铁粉的分离性不好 " 乳化液中铁粉多 " 容 易起浮渣 " 如轧制过程中咬入杂质 " 板面容易产生垃 圾印 ! &" )! 油膜破裂和乳化液的破坏对轧制稳定性影响 在高速轧制的过程中 " 特别是轧制薄规格时 " 压 下量达到临界值 " 因轧制力过大而产生大量的热能 " 这时 " 润滑油膜局部失调 " 平均油膜厚度小于需要的 最小值 " 轧制状态不稳定 " 产生 % 琴音 & 现象 ! 乳化液 的破坏也会造成轧 制 的 不 稳 定 " 乳化液的破坏是内 相的油从外相的水 中 分 离 " 这个分离了的油分把水 排除而附着在金 属 表 面 ! 此 现 象 称 % 离 水 展 着 性& " 它作为轧制性能的 指 标 是 极 为 重 要 的 " 在实际的轧 钢工艺中 " 乳化液在 清 洁 槽 中 通 过 搅 拌 器 的 搅 拌 是 稳定的 " 在 到 达 钢 板 表 面 时 很 快 地" 并且很均匀地 % 离水展着 & ! 乳化 液 的 破 坏 与 很 多 因 素 有 关 " 特别 是温度的影响为最大 ! 所以在生产过程中要控制乳 化液的温度 " 尽量少用强制加热 " 以免造成乳化液破 坏! 经过 对 比 分 析 " 八钢冷轧生产线采用了美国斯 图亚特公司 O 按表 L D 2 D E E G< M4% % $ $X ; 号轧制油 " ! 配置成乳化液 ! 经过使用 " 该乳化液表现出了它的主要优点 ’ ( ) 长期的乳 化 稳 定 性 好 " 随 着 轧 制 油 的 消 耗" ! 浓度降低慢 ! 且不易受铁粉影响 $ 粒径变动小 ! ( ) 轧机耐污性好 " 流动点低 " 不易产生油泥 " 对 % 轧机的污染较轻 ! ( ) 抗污染性 强 " 使 用 过 程 中" 油膜轴承漏油严 & 重" 造成乳化液的皂化值急剧下降 " 但仍表现出很好 的润滑性能 ! 乳化液的主要性能参数见表 !!
1500冷轧机组乳化液系统故障原因分析及技术改造
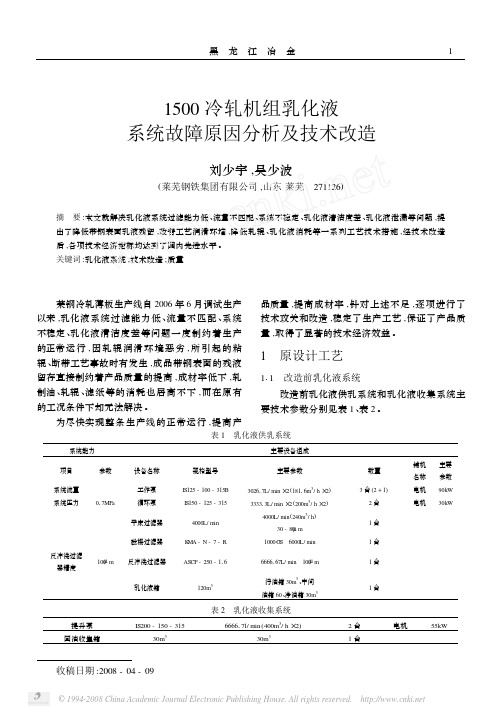
1500冷轧机组乳化液系统故障原因分析及技术改造刘少宇,吴少波(莱芜钢铁集团有限公司,山东莱芜 271126)摘 要:本文就解决乳化液系统过滤能力低、流量不匹配、系统不稳定、乳化液清洁度差、乳化液泄漏等问题,提出了降低带钢表面乳液残留,改善工艺润滑环境,降低轧辊、乳化液消耗等一系列工艺技术措施,经技术改造后,各项技术经济指标均达到了国内先进水平。
关键词:乳化液系统;技术改造;质量 莱钢冷轧薄板生产线自2006年6月调试生产以来,乳化液系统过滤能力低、流量不匹配、系统不稳定、乳化液清洁度差等问题一度制约着生产的正常运行,因轧辊润滑环境恶劣,所引起的粘辊、断带工艺事故时有发生,成品带钢表面的残液留存直接制约着产品质量的提高,成材率低下,轧制油、轧辊、滤纸等的消耗也居高不下,而在原有的工况条件下却无法解决。
为尽快实现整条生产线的正常运行,提高产品质量,提高成材率,针对上述不足,逐项进行了技术攻关和改造,稳定了生产工艺,保证了产品质量,取得了显著的技术经济效益。
1 原设计工艺111 改造前乳化液系统改造前乳化液供乳系统和乳化液收集系统主要技术参数分别见表1、表2。
表1 乳化液供乳系统系统能力主要设备组成项目参数设备名称规格型号主要参数数量辅机名称主要参数系统流量工作泵IS125-100-315B302617L/min×2(18116m3/h×2)3台(2+1)电机90kW 系统压力017MPa循环泵IS150-125-315333313L/min×2(200m3/h×2)2台电机30kW平床过滤器4000L/min 4000L/min(240m3/h)30-80μm1台磁栅过滤器K M A-N-7-R1000G S 6000L/min1台反冲洗过滤器精度100μm反冲洗过滤器ASCF-250-1166666167L/min 100μm1台乳化液箱120m3污油箱30m3、中间油箱60、净油箱30m31台表2 乳化液收集系统提升泵IS200-150-315666617l/min(400m3/h×2)2台电机55kW 回油收集箱30m330m31台1 黑 龙 江 冶 金 收稿日期:2008-04-09112 改造前工艺流程改造前工艺流程见图1。
冷轧乳化液系统使用与改进
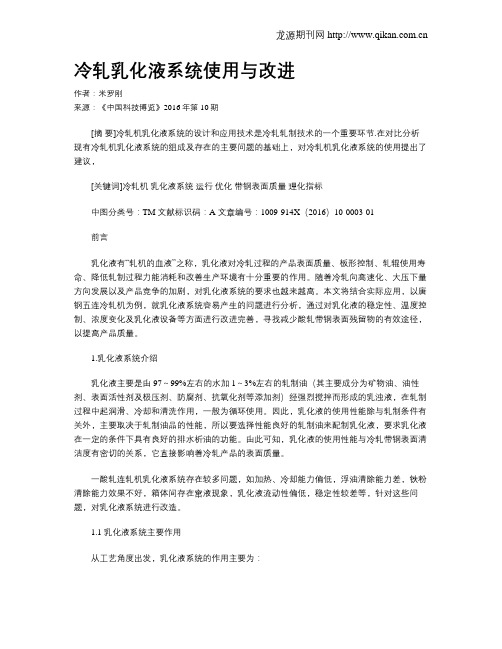
冷轧乳化液系统使用与改进作者:米罗刚来源:《中国科技博览》2016年第10期[摘要]冷轧机乳化液系统的设计和应用技术是冷轧轧制技术的一个重要环节.在对比分析现有冷轧机乳化液系统的组成及存在的主要问题的基础上,对冷轧机乳化液系统的使用提出了建议,[关键词]冷轧机乳化液系统运行优化带钢表面质量理化指标中图分类号:TM 文献标识码:A 文章编号:1009-914X(2016)10-0003-01前言乳化液有“轧机的血液”之称,乳化液对冷轧过程的产品表面质量、板形控制、轧辊使用寿命、降低轧制过程力能消耗和改善生产环境有十分重要的作用。
随着冷轧向高速化、大压下量方向发展以及产品竞争的加剧,对乳化液系统的要求也越来越高。
本文将结合实际应用,以唐钢五连冷轧机为例,就乳化液系统容易产生的问题进行分析,通过对乳化液的稳定性、温度控制、浓度变化及乳化液设备等方面进行改进完善,寻找减少酸轧带钢表面残留物的有效途径,以提高产品质量。
1.乳化液系统介绍乳化液主要是由97~99%左右的水加1~3%左右的轧制油(其主要成分为矿物油、油性剂、表面活性剂及极压剂、防腐剂、抗氧化剂等添加剂)经强烈搅拌而形成的乳浊液,在轧制过程中起润滑、冷却和清洗作用,一般为循环使用。
因此,乳化液的使用性能除与轧制条件有关外,主要取决于轧制油品的性能,所以要选择性能良好的轧制油来配制乳化液,要求乳化液在一定的条件下具有良好的排水析油的功能。
由此可知,乳化液的使用性能与冷轧带钢表面清洁度有密切的关系,它直接影响着冷轧产品的表面质量。
一酸轧连轧机乳化液系统存在较多问题,如加热、冷却能力偏低,浮油清除能力差,铁粉清除能力效果不好,箱体间存在窜液现象,乳化液流动性偏低,稳定性较差等,针对这些问题,对乳化液系统进行改造。
1.1 乳化液系统主要作用从工艺角度出发,乳化液系统的作用主要为:1)润滑:冷轧过程中,乳化液中的润滑油吸附在轧辊和带材的表面上形成一层很薄的油膜,为轧制提供必要的润滑。
单机架冷轧机工艺润滑系统改进及优化
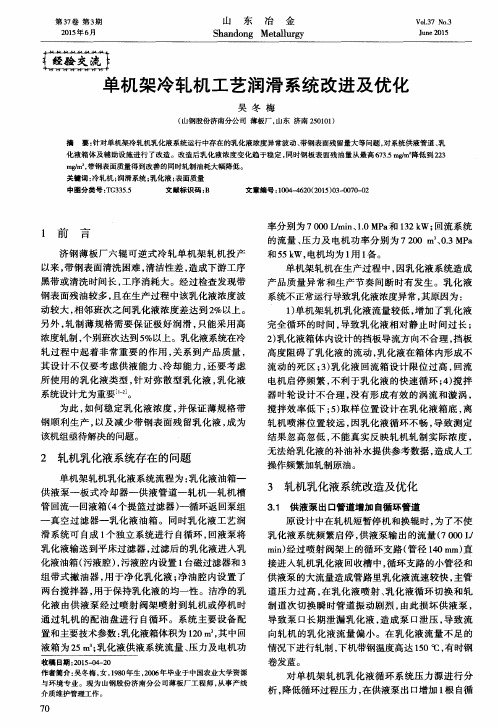
济 钢 薄板 厂六 辊 可 逆 式 冷 轧 单 机架 轧 机 投 产 以来 , 带钢 表 面清洗 困难 , 清洁 性差 , 造 成下 游 工序 黑 带或 清 洗时 间长 , 工 序 消耗 大 。经过 检查 发 现带
钢 表 面残 油较 多 , 且在 生产 过 程 中该 乳 化液 浓 度波
化液箱体 及辅助设施 进行 了改造 。改造 后乳化液浓 度变化趋 于稳定 , 同时钢板表 面残油量从 最高 6 7 3 . 5 m g / m 2 降低 到 2 2 3
m g / m  ̄ , 带钢表面质量得 到改善 的同时轧制油耗大幅降低。
关键词 : 冷轧机 ; 润滑系统 ; 乳化液 ; 表 面质量
结 果 忽 高 忽低 , 不 能 真实 反 映 轧 机轧 制 实 际 浓 度 , 无 法 给乳 化液 的补 油补 水 提供参 考 数据 , 造 成 人工 操 作频 繁加轧制 原油 。
2 轧机 乳化液 系统存 在 的问题
单 机架 轧机 乳 化液 系 统流 程为 : 乳 化 液油 箱一
供液泵一板式冷却器一供液管道一轧机一 轧机槽
动 较大 , 相 邻 班次 之 间乳化 液 浓度 差 达 到 2 %以上 。 另外 , 轧 制 薄 规 格需 要 保 证 极好 润滑 , 只 能采 用 高 浓 度轧制 , 个别班 次达 到 5 %以上。乳化 液 系统 在冷 轧 过 程 中起 着 非 常 重 要 的作 用 , 关 系 到产 品 质 量 , 其 设 计 不 仅要 考 虑 供 液 能力 、 冷 却 能力 , 还要 考 虑 所 使 用 的乳 化 液 类 型 , 针 对 弥 散 型乳 化 液 , 乳 化 液
为此 , 如何 稳 定 乳 化 液 浓度 , 并 保 证 薄规 格 带 钢顺利生产 , 以及 减 少带 钢 表 面 残 留乳 化 液 , 成 为 该机 组亟 待解决 的 问题 。
轧机工艺润滑站乳化液磁性过滤器改进

轧机工艺润滑站乳化液磁性过滤器的改进摘要:本文针对对传统轧机工艺润滑站磁性链条频繁断裂问题进行客观分析,找出造成链条断裂的各种原因,通过对磁性链条及刮铁装置的改进,成功解决了磁性链条频繁断裂的问题,减少了更换链条的次数,节约了轧钢过程中的成本,并提高了生产效率。
关键词:工艺润滑站;磁性链条;断裂;改进我公司为浙江协和薄板有限公司制作的1150六辊可逆冷轧机组在使用过程中,发现其中工艺润滑站乳化液磁性过滤器上的磁性链条断裂频繁,导致乳化液不能循环使用,需不停更换,既浪费企业资源又污染环境。
并且更换链条又比较麻烦,需要贮备大量备件,链条成本比较高,这些都造成成本增加。
一. 工艺润滑站磁性过滤器的工作原理磁性过滤器由吸铁装置、刮铁装置两部分组成:吸铁装置由上下两组材质为聚氨脂的六角链轮组和数条磁性链条缠绕在链轮上的磁性链条组成,下面那组链轮布置在乳化液收集箱箱体底部;刮铁装置主要由刮板、导向套、支架组成,它被布置在吸铁装置上下两组链轮组中间。
在工作过程中由链轮带动磁性链条循环运动,磁性链条的链节在穿过乳化液时会将乳化液从机组带来的铁屑吸在链节外圆上,将其带出乳化液,在通过刮铁装置时,刮板将铁屑从链节上刮下来,储存在支架的集屑槽中,从而净化用过的乳化液,使其能够循环使用。
二. 磁性链条频繁断裂的原因分析针对使用中出现的问题,经过仔细研究分析图纸,并观察磁性链条断裂部位并不在链节之间的铰接处,而是在链节上铰接头与不锈钢管之间的环形焊缝处,所以得出结论认为,造成磁性链条断裂的原因有两个:1. 磁性链条的链节本身焊接强度不足。
2. 刮铁装置设计不太合理,铁屑容易滑进铜刮板与链条之间的缝隙里,一旦铁屑卡住,链条将不能向下运动,而链轮在电机带动下仍要运转,从而拉裂链节。
下面是磁性链条的磁性链节图下图是刮铁装置简图具体分析如下:1. 从磁性链条链节图中可以看出在铰接头与不锈钢管之间的环形焊缝只有1.2mm,按照我们重机行业焊接方式根本就不可能焊透,只是在表面焊了一层焊肉,经机加工与不锈钢管外圆接平后,只能留下薄薄一层,作为过渡桥梁用,掩盖铰接头与钢管之间的接缝,链节在通过刮铁装置时,铜刮板不至卡接缝里,没有焊接强度,真正起连接作用、有焊接强度的只有4-φ5的塞焊孔,焊接强度比较弱。
磁性过滤机在冷轧轧机乳化液系统中的应用和改进
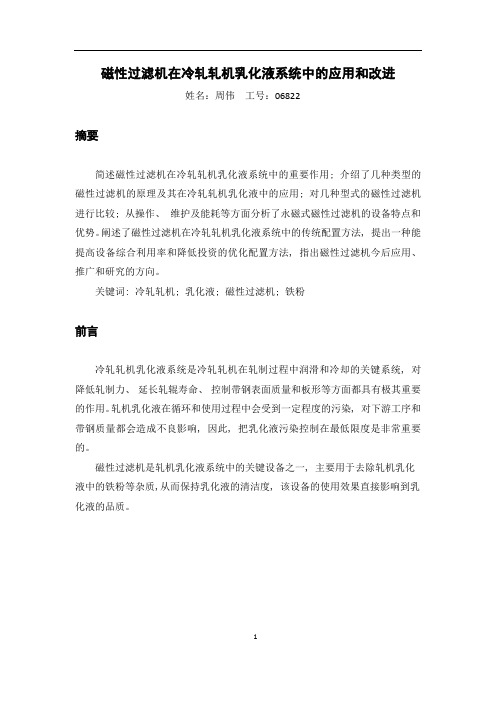
磁性过滤机在冷轧轧机乳化液系统中的应用和改进姓名:周伟工号:06822摘要简述磁性过滤机在冷轧轧机乳化液系统中的重要作用; 介绍了几种类型的磁性过滤机的原理及其在冷轧轧机乳化液中的应用; 对几种型式的磁性过滤机进行比较; 从操作、维护及能耗等方面分析了永磁式磁性过滤机的设备特点和优势。
阐述了磁性过滤机在冷轧轧机乳化液系统中的传统配置方法, 提出一种能提高设备综合利用率和降低投资的优化配置方法, 指出磁性过滤机今后应用、推广和研究的方向。
关键词: 冷轧轧机; 乳化液; 磁性过滤机; 铁粉前言冷轧轧机乳化液系统是冷轧轧机在轧制过程中润滑和冷却的关键系统, 对降低轧制力、延长轧辊寿命、控制带钢表面质量和板形等方面都具有极其重要的作用。
轧机乳化液在循环和使用过程中会受到一定程度的污染, 对下游工序和带钢质量都会造成不良影响, 因此, 把乳化液污染控制在最低限度是非常重要的。
磁性过滤机是轧机乳化液系统中的关键设备之一, 主要用于去除轧机乳化液中的铁粉等杂质,从而保持乳化液的清洁度, 该设备的使用效果直接影响到乳化液的品质。
1 磁性过滤机的分类和发展根据磁性过滤机在轧机乳化液系统中的应用, 按磁场的产生和工作原理, 磁性过滤机可分为电磁式和永磁式两类。
电磁式磁性过滤机的原理是通过过滤机自身的填充物得电, 使得填充物产生磁性和磁场, 从而吸附过滤液中的铁粉等杂质, 再在消除磁性(失电)的状态下对填充物进行冲洗, 将吸附的杂质去除。
冲洗过程也是电磁式磁性过滤机中的关键过程, 直接影响磁性过滤机的去除效果。
根据内部充填物的不同, 可将电磁式磁性过滤机分为填料式和磁球式。
填料式电磁过滤机内部设有类似于钢毛的电磁填充物, 通过得电和失电以及冲洗过程将吸附在钢毛上的铁粉分离出来。
磁球式电磁过滤机内部设置有球状填充物, 通过得电和失电使得磁球磁化和消磁。
两种型式的电磁式磁性过滤机分别在宝钢的两个冷轧分厂的轧机乳化液系统中得到应用, 磁球式电磁过滤机是在填料式(钢毛)电磁过滤机基础上的一种发展和进化。
轧机乳化液系统改造
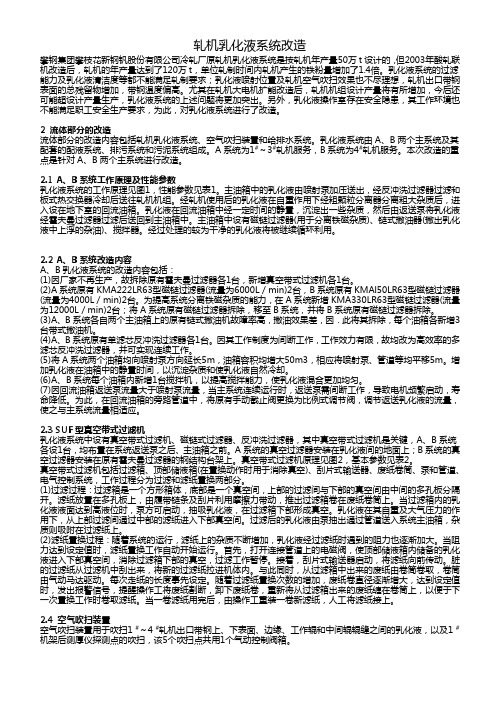
轧机乳化液系统改造攀钢集团攀枝花新钢钒股份有限公司冷轧厂原轧机乳化液系统是按轧机年产量50万t设计的,但2003年酸轧联机改造后,轧机的年产量达到了120万t,单位轧制时间内轧机产生的铁粉量增加了1.4倍。
乳化液系统的过滤能力及乳化液清洁度等都不能满足轧制要求;乳化液喷射位置及轧机空气吹扫效果也不尽理想,轧机出口带钢表面的总残留物增加,带钢温度偏高。
尤其在轧机大电机扩能改造后,轧机机组设计产量将有所增加,今后还可能超设计产量生产,乳化液系统的上述问题将更加突出。
另外,乳化液操作室存在安全隐患,其工作环境也不能满足职工安全生产要求,为此,对乳化液系统进行了改造。
2 流体部分的改造流体部分的改造内容包括轧机乳化液系统、空气吹扫装置和给排水系统。
乳化液系统由A、B两个主系统及其配套的配液系统、排污系统和污泥系统组成。
A系统为1#~3#轧机服务,B系统为4#轧机服务。
本次改造的重点是针对A、B两个主系统进行改造。
2.1 A、B系统工作原理及性能参数乳化液系统的工作原理见图1,性能参数见表1。
主油箱中的乳化液由喷射泵加压送出,经反冲洗过滤器过滤和板式热交换器冷却后送往轧机机组。
经轧机使用后的乳化液在自重作用下经粗颗粒分离器分离粗大杂质后,进入设在地下室的回流油箱。
乳化液在回流油箱中经一定时间的静置,沉淀出一些杂质,然后由返送泵将乳化液经霍夫曼过滤器过滤后送回到主油箱中。
主油箱中设有磁链过滤器(用于分离铁磁杂质)、链式撇油器(撇出乳化液中上浮的杂油)、搅拌器。
经过处理的较为干净的乳化液将被继续循环利用。
2.2 A、B系统改造内容A、B乳化液系统的改造内容包括:(1)因厂家不再生产,故拆除原有霍夫曼过滤器各1台,新增真空带式过滤机各1台。
(2)A系统原有KMA222LR63型磁链过滤器(流量为6000L/min)2台,B系统原有KMAl50LR63型磁链过滤器(流量为4000L/min)2台。
为提高系统分离铁磁杂质的能力,在A系统新增KMA330LR63型磁链过滤器(流量为12000L/min)2台;将A系统原有磁链过滤器拆除,移至B系统,并将B系统原有磁链过滤器拆除。
某钢厂HC冷轧机乳化液过滤系统研究与改进
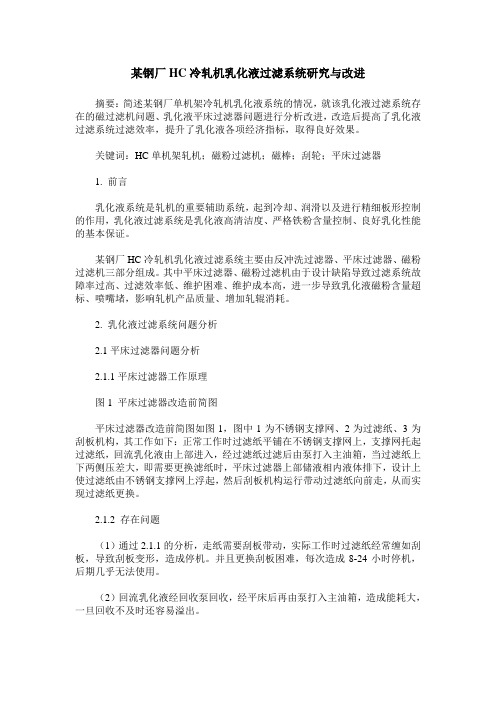
某钢厂HC冷轧机乳化液过滤系统研究与改进摘要:简述某钢厂单机架冷轧机乳化液系统的情况,就该乳化液过滤系统存在的磁过滤机问题、乳化液平床过滤器问题进行分析改进,改造后提高了乳化液过滤系统过滤效率,提升了乳化液各项经济指标,取得良好效果。
关键词:HC单机架轧机;磁粉过滤机;磁棒;刮轮;平床过滤器1. 前言乳化液系统是轧机的重要辅助系统,起到冷却、润滑以及进行精细板形控制的作用,乳化液过滤系统是乳化液高清洁度、严格铁粉含量控制、良好乳化性能的基本保证。
某钢厂HC冷轧机乳化液过滤系统主要由反冲洗过滤器、平床过滤器、磁粉过滤机三部分组成。
其中平床过滤器、磁粉过滤机由于设计缺陷导致过滤系统故障率过高、过滤效率低、维护困难、维护成本高,进一步导致乳化液磁粉含量超标、喷嘴堵,影响轧机产品质量、增加轧辊消耗。
2. 乳化液过滤系统问题分析2.1平床过滤器问题分析2.1.1平床过滤器工作原理图1 平床过滤器改造前简图平床过滤器改造前简图如图1,图中1为不锈钢支撑网、2为过滤纸、3为刮板机构,其工作如下:正常工作时过滤纸平铺在不锈钢支撑网上,支撑网托起过滤纸,回流乳化液由上部进入,经过滤纸过滤后由泵打入主油箱,当过滤纸上下两侧压差大,即需要更换滤纸时,平床过滤器上部储液相内液体排下,设计上使过滤纸由不锈钢支撑网上浮起,然后刮板机构运行带动过滤纸向前走,从而实现过滤纸更换。
2.1.2 存在问题(1)通过2.1.1的分析,走纸需要刮板带动,实际工作时过滤纸经常缠如刮板,导致刮板变形,造成停机。
并且更换刮板困难,每次造成8-24小时停机,后期几乎无法使用。
(2)回流乳化液经回收泵回收,经平床后再由泵打入主油箱,造成能耗大,一旦回收不及时还容易溢出。
2.2磁粉过滤机问题分析图2磁粉过滤机结构简图2.2.1过滤机结构原理磁粉过滤机工作原理简图见图2,过滤机传动机构通过链条带动刮磁机构前后运转,到达后限位后通过撞块与后限位的撞击使悬臂落下,刮板与磁棒接触,刮磁机构向前运行带动刮板将磁棒磁粉刮下;刮磁机构到达前限位后通过撞块与前限位的撞击使悬臂抬起,磁粉刮板与磁棒脱离,刮磁机构转向后运行,这样往复来回,达到过滤磁粉的目的。
冷轧卧式磁过滤器的改进
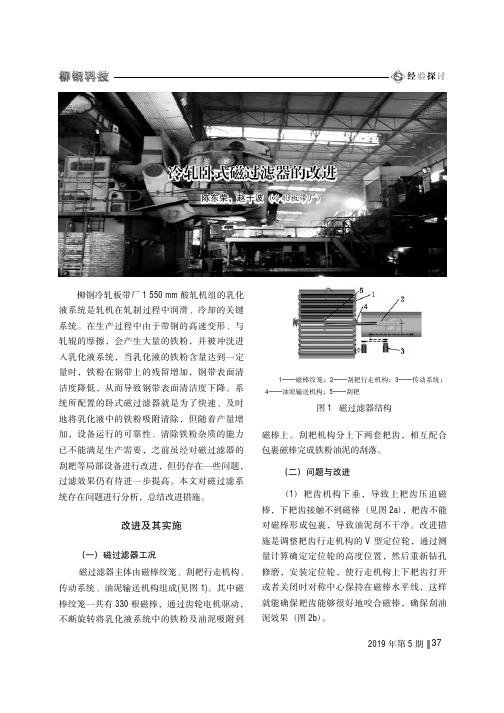
2019年第5期柳钢冷轧板带厂1550mm 酸轧机组的乳化液系统是轧机在轧制过程中润滑、冷却的关键系统。
在生产过程中由于带钢的高速变形、与轧辊的摩擦,会产生大量的铁粉,并被冲洗进入乳化液系统,当乳化液的铁粉含量达到一定量时,铁粉在钢带上的残留增加,钢带表面清洁度降低,从而导致钢带表面清洁度下降。
系统所配置的卧式磁过滤器就是为了快速、及时地将乳化液中的铁粉吸附清除,但随着产量增加,设备运行的可靠性、清除铁粉杂质的能力已不能满足生产需要,之前虽经对磁过滤器的刮耙等局部设备进行改进,但仍存在一些问题,过滤效果仍有待进一步提高。
本文对磁过滤系统存在问题进行分析,总结改进措施。
改进及其实施(一)磁过滤器工况磁过滤器主体由磁棒绞笼、刮耙行走机构、传动系统、油泥输送机构组成(见图1)。
其中磁棒绞笼一共有330根磁棒,通过齿轮电机驱动,不断旋转将乳化液系统中的铁粉及油泥吸附到磁棒上。
刮耙机构分上下两套耙齿,相互配合包裹磁棒完成铁粉油泥的刮落。
(二)问题与改进(1)耙齿机构下垂,导致上耙齿压迫磁棒,下耙齿接触不到磁棒(见图2a ),耙齿不能对磁棒形成包裹,导致油泥刮不干净。
改进措施是调整耙齿行走机构的V 型定位轮,通过测量计算确定定位轮的高度位置,然后重新钻孔修磨,安装定位轮,使行走机构上下耙齿打开或者关闭时对称中心保持在磁棒水平线,这样就能确保耙齿能够很好地咬合磁棒,确保刮油泥效果(图2b )。
冷轧卧式磁过滤器的改进陈东荣,赵干波(冷轧板带厂)图1磁过滤器结构1———磁棒绞笼;2———刮耙行走机构;3———传动系统;4———油泥输送机构;5———刮耙经验探讨372019年第5期(2)原耙齿为复合木质板材质,易磨损,使用寿命短,更换周期1个月。
经过分析对比试验,改用PPH 材质制作耙齿,耙齿的使用寿命超过半年,刮油泥效果也更加好。
(3)原耙齿齿头部为方形结构。
为确保耙齿精确咬入磁棒,要求耙齿和磁棒相对安装位置很精准,但受乳化液系统运行工况差、磁棒绞笼和刮耙行走机构的磨损等因素影响,易导致耙齿不能精确咬入磁棒而造成卡阻等故障,影响刮泥效果。
乳化液反冲洗过滤器的改进与优化

0引言河钢集团唐钢公司冷轧薄板厂一酸轧生产线采用法国VAI CLECIM 公司设计的五机架冷连轧机组,于2005年11月正式投产。
乳化液素有“轧机的血液”之称,其工艺与质量的优劣直接关系到最高允许轧制速度、轧辊的寿命、带钢表面质量等。
面对市场的严峻形势,产品质量成为重中之重,对带钢表面清洁度的要求不断提升。
在该前提下,乳化液循环净化系统中各设备的运行与维护状况便成为了重中之重。
1反冲洗过滤器存在的问题本套乳化液系统所涉及的净化设备主要有4台刮削式磁棒过滤器、3台皮带式撇渣器、1台平床真空过滤器、5台反冲洗过滤器等。
作为精过滤设备,也是通往轧机的最后一道净化设备,反冲洗过滤器的运行状况尤为关键。
本系统中反冲洗过滤器全部采用HYDAC 公司的AutoFilt ○R RF3型自动反冲洗过滤器,采用圆锥型线隙式滤芯,过滤精度为100μ。
该设备结构紧凑,过滤效率高,全自动无人值守操作,反冲洗过程中可以继续过滤供液。
但是,在现场设备维护过程中,反冲洗过滤器经常出现如下问题:①排废比较高。
乳化液粗过滤设备故障率高,导致反冲洗过滤器入口乳化液铁含量及灰分偏高,反冲洗过滤器频繁进行反冲洗操作,废液与净液的比例居高不下。
由于反冲洗废液管道直接排放进地沟,最终经排污泵输送进废液管道,频繁的反冲操作造成大量乳化液浪费。
②设备事故较频繁。
主要表现为因设备及管路振动量较大而导致管路破损漏液,过滤器滤芯在旋转过程中自身发生破裂甚至断裂,滤芯底部橡胶密封圈老化损坏等。
③设备维护周期相对固定,没有针对性。
由于定修周期较为固定,之前设备维护周期也相对固定,5台反冲洗过滤器完全按照周期轮换维护,没有针对性的制定每一台的单独维护周期。
因而,在过去的维护过程中,偶有拆解后发现设备无需维护或者设备未能及时维护的情况发生。
2分析及改进措施2.1降低排废比2.1.1加强前置净化首先从其他净化设备入手,提高反冲洗入口乳化液的洁净度。
日常点检维护工作中保障磁棒过滤器、撇渣器、平床过滤器的净化效果,降低粗滤后乳化液的铁含量及灰分。
金属轧制设备与工艺润滑的挑战与创新

润滑的历史回顾
轧制工艺始于15世纪,16世纪开始轧制窄带,用来制作货币,据说最早的轧机草图是在 D·V·Leonardo的记录中发现。1728年法国首先使用带孔型的轧辊。在约一百多年后才轧出较 规则的金属棒材。1862年连轧机开始出现在英国的曼彻斯特。18世纪中期,开始热轧较宽钢 板,而薄板热轧未采用润滑油。1892年在Teplite建成第一套带钢连轧机组。此时,还没有采用 工艺润滑,不久轧制有色金属,同时轧制的厚度范围也扩大了
热连轧机,随后鞍钢1780mm精轧机热轧生产线、珠钢CSP生产线、攀
钢1450mm生产线、宝钢梅山钢铁热轧厂以及唐钢800mm热轧带 钢等已使用了这一技术并取得了成功,获得了良好的经济效益。 经过50多年的发展,轧制工艺润滑技术已经在钢铁生产领域获 得广泛应用。
第六页,编辑于星期六:点 十七分。
1.1钢铁企业设备与工艺润滑现状与挑战
(3)节水
由于热轧过程中氧化铁皮厚度的减少,得使高压水除鳞用水水压减少,同时轧辊循环冷却水的利 用率进一步提高,而冷轧时由于能够有效地减少轧制变形区的摩擦,使得轧辊表面温升得到控制 ,轧辊冷却水用量也随之减少。
(4)酸液使用减少
热轧氧化皮厚度的降少,酸洗过程中酸洗速度可以相应提高10%~40%,酸液消耗降低
,并一直沿用到今天。由于轧制速度不断提高,因而迫切要求解决轧辊的冷却问题,于是,出现了冷却性 能良好的乳化液来润滑以代替纯油润滑。
第五页,编辑于星期六:点 十七分。
润滑的历史回顾
1968年QAUAKER-CHEMICAL的热轧润滑油在美国National钢铁公 司GREAT-LAKE分厂热连轧机组上应用并取得成功 日本应用此项技术也有35年历史,国外板带钢热连轧机的精轧机组 都已采用了工艺润滑技术。 1980年开始太钢炉卷轧机、武钢1700mm热连轧机、宝钢2050mm
轧辊磨床过滤装置的技改
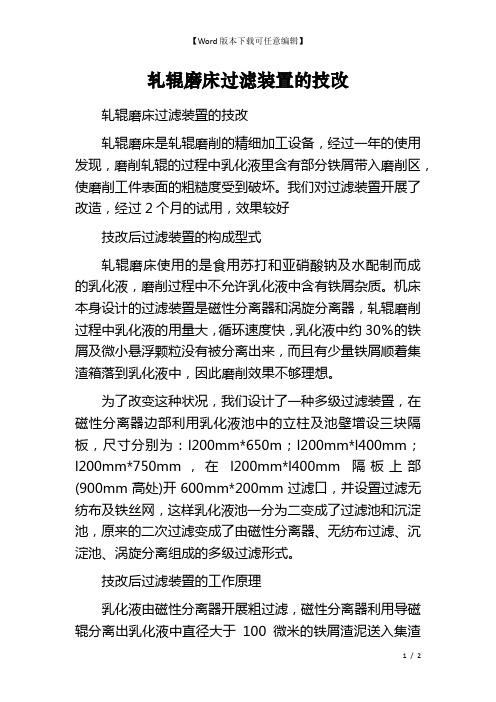
轧辊磨床过滤装置的技改轧辊磨床过滤装置的技改轧辊磨床是轧辊磨削的精细加工设备,经过一年的使用发现,磨削轧辊的过程中乳化液里含有部分铁屑带入磨削区,使磨削工件表面的粗糙度受到破坏。
我们对过滤装置开展了改造,经过2个月的试用,效果较好技改后过滤装置的构成型式轧辊磨床使用的是食用苏打和亚硝酸钠及水配制而成的乳化液,磨削过程中不允许乳化液中含有铁屑杂质。
机床本身设计的过滤装置是磁性分离器和涡旋分离器,轧辊磨削过程中乳化液的用量大,循环速度快,乳化液中约30%的铁屑及微小悬浮颗粒没有被分离出来,而且有少量铁屑顺着集渣箱落到乳化液中,因此磨削效果不够理想。
为了改变这种状况,我们设计了一种多级过滤装置,在磁性分离器边部利用乳化液池中的立柱及池壁增设三块隔板,尺寸分别为:l200mm*650m;l200mm*l400mm;l200mm*750mm,在l200mm*l400mm隔板上部(900mm高处)开600mm*200mm过滤口,并设置过滤无纺布及铁丝网,这样乳化液池一分为二变成了过滤池和沉淀池,原来的二次过滤变成了由磁性分离器、无纺布过滤、沉淀池、涡旋分离组成的多级过滤形式。
技改后过滤装置的工作原理乳化液由磁性分离器开展粗过滤,磁性分离器利用导磁辊分离出乳化液中直径大于100微米的铁屑渣泥送入集渣箱,经过磁性分离过滤后的乳化液流经隔板的过滤口上的过滤无纺布开展第二次过滤。
过滤无纺布固定在过滤口铁丝网上。
由于大部分铁屑被磁性分离器分离后送到集渣箱,无纺布在过滤过程中不易堵塞,它可以过滤非导磁性颗粒及少量浮油。
被无纺布过滤后的乳化液经过沉淀和涡旋分离,将乳化液中的杂质后除去。
技改后过滤装置的特点这种经过多级过滤装置过滤的乳化液含渣极少,提高了磨削工件的表面质量和切削率,乳化液的散热性好,保持了乳化液固有的特性,增设隔板后乳化液池一分为二,乳化液流程增加,沉淀效果明显。
因为隔板是可装拆的,所以给工人清理水箱带来了很大方便,减轻了工人的劳动强度。
- 1、下载文档前请自行甄别文档内容的完整性,平台不提供额外的编辑、内容补充、找答案等附加服务。
- 2、"仅部分预览"的文档,不可在线预览部分如存在完整性等问题,可反馈申请退款(可完整预览的文档不适用该条件!)。
- 3、如文档侵犯您的权益,请联系客服反馈,我们会尽快为您处理(人工客服工作时间:9:00-18:30)。
轧机工艺润滑站乳化液磁性过滤器的改进
摘要:本文针对对传统轧机工艺润滑站磁性链条频繁断裂问题进行客观分析,找出造成链条断裂的各种原因,通过对磁性链条及刮铁装置的改进,成功解决了磁性链条频繁断裂的问题,减少了更换链条的次数,节约了轧钢过程中的成本,并提高了生产效率。
关键词:工艺润滑站;磁性链条;断裂;改进
我公司为浙江协和薄板有限公司制作的1150六辊可逆冷轧机组在使用过程中,发现其中工艺润滑站乳化液磁性过滤器上的磁性链条断裂频繁,导致乳化液不能循环使用,需不停更换,既浪费企业资源又污染环境。
并且更换链条又比较麻烦,需要贮备大量备件,链条成本比较高,这些都造成成本增加。
一. 工艺润滑站磁性过滤器的工作原理
磁性过滤器由吸铁装置、刮铁装置两部分组成:吸铁装置由上下两组材质为聚氨脂的六角链轮组和数条磁性链条缠绕在链轮上的磁性链条组成,下面那组链轮布置在乳化液收集箱箱体底部;刮铁装置主要由刮板、导向套、支架组成,它被布置在吸铁装置上下两组链轮组中间。
在工作过程中由链轮带动磁性链条循环运动,磁性链条的链节在穿过乳化液时会将乳化液从机组带来的铁屑吸在链节外圆上,将其带出乳化液,在通过刮铁装置时,刮板将铁屑从链节上刮下来,储存在支架的集屑槽中,从而净化用过的乳化液,使其能够循环使用。
二. 磁性链条频繁断裂的原因分析
针对使用中出现的问题,经过仔细研究分析图纸,并观察磁性链条断裂部位并不在链节之间的铰接处,而是在链节上铰接头与不锈钢管之间的环形焊缝处,所以得出结论认为,造成磁性链条断裂的原因有两个:
1. 磁性链条的链节本身焊接强度不足。
2. 刮铁装置设计不太合理,铁屑容易滑进铜刮板与链条之间的缝隙里,一旦铁屑卡住,链条将不能向下运动,而链轮在电机带动下仍要运转,从而拉裂链节。
下面是磁性链条的磁性链节图
下图是刮铁装置简图
具体分析如下:
1. 从磁性链条链节图中可以看出在铰接头与不锈钢管之间的环形焊缝只有1.2mm,按照我们重机行业焊接方式根本就不可能焊透,只是在表面焊了一层焊肉,经机加工与不锈钢管外圆接平后,只能留下薄薄一层,作为过渡桥梁用,掩盖铰接头与钢管之间的接缝,链节在通过刮铁装置时,铜刮板不至卡接缝里,没有焊接强度,真正起连接作用、有焊接强度的只有4-Φ5的塞焊孔,焊接强度比较弱。
2. 从刮铁装置图可以看出,刮板内孔孔口有倒角,设计这个倒角本意是对链节起导向作用,但在实际使用中,它带来了两个弊病:(1)由于倒角的存在,刮屑部位呈钝角,影响刮屑效果;(2)它对刮掉的铁屑也起导向作用,一些铁屑会聚集在倒角里,在链条的吸附和带动下,个别小一点铁屑进入链节外圆与刮板或导向铜套内孔之间的间隙里,由于刮板、铜套与链节均是刚性材质,没有弹性,一旦铁屑卡在里面出不来,就会卡住链条使其不能运动,而链轮在电机的带动下仍在运转,从而会拉断链条。
三. 具体改进
1. 从图中可以看出增加塞焊孔或扩大塞焊孔均无空间,要增加链节强度只有在环形焊缝上想办法。
根据不锈钢管的壁厚只有2mm,以及我们的焊接手段,为保证焊缝能够焊透,我将1.2mm焊缝改为
2.5 mm,从而让环形焊缝真正起到连接作用,以增加磁性链节的焊接强度。
2. 下图是改造后的刮板图和增加的压板图。
1)将刮板改为8mm厚的夹布橡胶板,孔口不倒角,其余尺寸不变。
这样虽然由于橡胶具有弹性,即使不能将链条上的铁屑刮干净,但是由于其具有弹性,不致卡住铁屑,而且没刮下来的铁屑由于吸附在链条上,不会掉进乳化液里。
为了保证刮铁效果,需经常更换刮板,更换刮板速度快,且刮板制作方便费用低。
2)由于橡胶刮板不好固定,所以增加铜压板,将铜压板压在刮板上,用螺栓一起把合固定,铜压板为剖分式,中间有槽,便于铁屑流出。
3)将序号4铜套内孔尺寸从Φ26放大至Φ30,加大铜套与链条之间的间隙,这样,铜套仍起一定的导向作用,由于间隙增大,铁屑即使没有被刮板刮下来而进入链条与铜套之间,也不会卡住。
四. 结束语
通过以上改造后,链条再没出现过断裂现象,在协和使用良好。
乳化液磁性过滤器实现了连续工作,乳化液实现了循环利用,在保证质量的基础上大大提高了设备的效率,有效地降低了用户的使用成本;后来我公司为协和公司提供的三条冷轧线,为郑州华池钢板有限公司、江门俭美公司等提供的冷轧线均采用该方案,使用都很好,为公司带来了可观的效益。
注:文章内所有公式及图表请用PDF形式查看。