Honeywell+8cal+电弧服技术信息
honeywell新一代压力无关线型温度调节阀介绍

23
HONEYWELL - CONFIDENTIAL
Kombi-8 系列 最大流量预设定
•可以很方便的在超级电动执 行器内根据被调对象需要对 最大流量进行预设定 •设定范围为(60%~100%)
最大流量 调节范围
轴向长 L(mm) 160
轴上高度 H(mm) 273 273 280 280
DN32
DN40 DN50
6.0
9.6 16.1
60% ~ 100%
±4%
168 182 205
5
HONEYWELL - CONFIDENTIAL
ML-SBE系列超级电动执行器组件
ML-SBE系列超级电动执行器组件由超级电动执行器、前置感应器、采样直 管和专用排气阀等构成。
环境 温度
储藏 温度
相对 湿度
IP54
12 VA
38 mm
1800 N
175S
-10 ~ 50℃
-40 ~ 70℃
5%~ 95%
ML7421B1023-SBE150
DN150
10
HONEYWELL - CONFIDENTIAL
Kombi-8 系列 工作原理
1.当水从前置感应器流入调节阀时,前置感应器感受采 样信号,经采样直管、专用排气阀和采样软管进入超级 电动执行器的采样传感组件,然后输送到超级电动执行 器; 2. 超级电动执行器内含被调对象的特征数据库和压力无 关数据库; 3.超级电动执行器接受来自楼宇控制系统或现场控制器 的标准控制信号及采样传感组件的信号,并对选定的被 调对象特征值及压力无关数据进行处理,输出信号改变 调节阀的开度; 4.通过以上实现对被调对象区域温度的高精度压力无关 线型温度调节。
11
电弧防护服燃烧性能分析

电弧防护服燃烧性能分析ASTMF1506纺织材料的标准性能规范:针对会暴露在瞬间电弧和其他热危害中的电力工作人员的服装所用的阻燃纺织材料,ASTMF1506制定了性能规范。
ASTMF1506防护的相关要求包括垂直燃烧法(新材料在水洗之后)和电弧级定。
另外,该标准要求织物不易被点燃或点燃后能遏制燃烧并自行熄灭。
阻燃性能通过FTM5903.1垂直燃烧法(暴露在火焰中2秒后最大损毁长度约为15厘米)测试。
电弧级定通过ASTMF1959测试后用ATPV值或EBT值评定。
ASTMF1891防电弧阻燃雨衣的标准规范:这个标准适用于雨衣的阻燃防水材料,可以利用阻燃的涂层或层压织物来生产服装。
其阻燃性能通过ASTMD-6413垂直燃烧法的测定,ATPV值也需要记录。
通过ASTMF1959电弧热性能测试法测定5次并选取最小的EBT值来记录。
为了更适用于涂层织物,目前该标准正在修订,以便增加织物燃烧性测试法。
NFPA70E工作环境中电力安全要求标准:在2004年美国国家消防协会公布的最新版本的NFPA70E标准包含各行业工作环境中的各方面安全用电规则。
NFPA70E建议,在有电弧产生的情况下,电弧防护、阻燃的个人装备,在使用时必须达到ASTMF1506、ASTMF1891和ASTMF2178的性能标准,且重新修订的版本要求企业要预先进行电弧危险分析来判定电弧安全界限。
该标准为了保护在电弧安全界限内的员工而设定,通过使用相应的危险风险分类的ATPV值的防护服装来保护员工。
ATPV值的单位是cal/cm2,代表电弧热防护值,用来反映电弧防护材料特别是电弧防护服的最大防护性能。
NFPA70E为工作在带电设备附近的工作人员设定安全用电标准,规范并设计出必要的步骤来防止在电弧事故中造成的严重伤害。
按照NFPA70E规定,每个在电弧安全界限(此范围内释放能量大于1.2cal/cm2)内工作的人员必须能够胜任并穿着适当的阻燃防电弧服。
Honeywell North RU8800 半面罩说明书

For more informationTechnical Service: 800.873.5242 Honeywell Industrial Safety 900 Douglas Pike Smithfield, RI 02917 USA Phone: 800.430.5490 Fax: 800.322.1330 CANADAPhone: 888.212.7233 Fax: 888.667.8477Honeywell North ® RU8800 Series Half MasksThe Honeywell North RU8800 Series is a silicone half mask compatible with the Honeywell North N-Series cartridges and filters. The half mask has a triple flange that provides three sealing surfaces between the mask and face for additional layers of protection against seal leaks. The RU8800 comes in two sizes: small (RU88001S) and medium/ large (RU88001ML). Due to its unique design, the RU8800 fits a wide variety of facial types.Protection TypeWhen used with the appropriate filters, cartridges orfilter/cartridge combinations, the Honeywell North RU8800 is an air-purifying respirator for protection from particulates, gases or vapors, or any combination of particulates, gases and vapors.Do not use the RU8800 respirator in environments that are Immediately Dangerous to Life or Health (IDLH) or where the oxygen level is less than 19.5% volume at sea level.CertificationsThe Honeywell North RU8800 is currently NIOSH approved as an air-purifying respirator (APR). It is also NIOSH approved with the North Backpack Adapter (BP1002).Assigned Protection Factors In APR mode 10Major Components Cartridge ConnectionsThe RU8800 includes two cartridge connections, one on each side. The threaded cartridge connections are compatible with all Honeywell North N-Series cartridges and filters.Ordering InformationDescription Packaging MASKSRU88001S Triple flange silicone half mask, size small EachRU88001ML Triple flange silicone half mask, size medium/large Each CARTRIDGESN75001L Organicvaporcartridges PairN75002L Acid gas (chlorine, hydrogen chloride, sulfur dioxide, hydrogen fluoride, chlorine dioxide) and formaldehyde cartridgesPairN75003L Organic vapor and acid gas (chlorine, hydrogen chloride, sulfur dioxide, hydrogen fluoride,chlorine dioxide) CartridgesPairN75004L Ammonia and methylamine cartridges PairN750052L Mercury vapor and chlorine cartridges with End-of-Service-Life Indicator (ESLI) for mercuryvaporPair75SCL Defender®: Organic vapor, acid gas (chlorine, hydrogen chloride, sulfur dioxide, hydrogensulfide, hydrogen fluoride, chlorine dioxide), ammonia, methylamine and formaldehyde cartridgePairCOMBINATION CARTRIDGES AND FILTERS7581P100L Organic vapor and P100 cartridge/filter combination Pair7582P100L Acid gas (chlorine, hydrogen chloride, sulfur dioxide, hydrogen fluoride, chlorine dioxide), formaldehyde and P100 cartridge/filter combinationPair7583P100L Organic vapor, acid gas (chlorine, hydrogen chloride, sulfur dioxide, hydrogen fluoride, chlorine dioxide) and P100 cartridge/filter combinationPair7584P100L Ammonia, methylamine and P100 cartridge/filter combination Pair75852P100L Mercury vapor, chlorine and P100 cartridge/filter combination with End-of-Service-Life Indicator (ESLI) for mercury vaporPair75SCP100L Defender®: Organic vapor, acid gas (chlorine, hydrogen chloride, sulfur dioxide, hydrogensulfide, hydrogen fluoride, chlorine dioxide), ammonia, methylamine, formaldehyde and P100 cartridge/filter combinationPairFILTERS7580P100 P100 Filter for protection from all particulates Pair75FFP100 Flexible P100 Filter for protection from all particulates 50 Pairs/Bx75FFP100NL Flexible P100 Filter for protection from all particulates, with odor relief from nuisance levels ofOrganic Vapors, Acid Gases and ozone10/Pk7506N95 N95 filters for protection from particulates where no oil based aerosols are present 10/Pk 7506N99 N99 filters for protection from particulates where no oil based aerosols are present 10/Pk 7506R95 R95 filters for protection from particulates including where oil based aerosols may be present 10/Pk ACCESSORIESN750029 Shower Cap for 7580P100 and gas/vapor P100 cartridge/filter combinations. Protects filtersfrom water spray during abatement and decontamination; plus sparks and slag during weldingand grinding operationsEachN750035 Adapter for 75FFP100 and 75FFP100NL filters; attaches filter for gas and vapor cartridges EachN750036 Filter Retainer for 7506N95, 7506N99 and 7506R95 filters when used with gas and vaporcartridgesPairN750037 Filter Retainer for 7506N95, 7506N99 and 7506R95 filters when filters are attached directly on facepiecePair7003 Respirator refresher wipe pads, with alcohol. 5” x 7” towelettes 100/Bx 7003A Respirator refresher wipe pads, alcohol free. 5” x 7” towelettes 100/Bx140082 Respirator refresher wipe pads, with alcohol, dispenser canister 200 wipes per canister80095 Cleaner and disinfectant for respirator facepieces; 10 oz. bottle (not available in Canada) Each 770021 Fit test adapter for quantitative fit testing PairReplacement PartsProduct Weights & DimensionsEach unit contains one (1) mask, user instructions, resealable bag Part Number Length Width Height Weight RU88001S 8.00” (20.32 cm) 4.00” (10.16 cm) 11.75” (29.84 cm) .72 lb (.33 kg) RU88001ML 8.00” (20.32 cm) 4.50” (11.43 cm) 11.75” (29.84 cm) .79 lb (.36 kg)Shipping Weights & Dimensions Shipping carton includes 12 units. Part Number Length Width Height Weight RU88001S 19.5” (49.50 cm) 8.81” (22.40 cm) 11.88” (30 cm) 9.40 lb (4.26 kg) RU88001ML 19.5” (49.50 cm) 8.81” (22.40 cm) 11.88” (30 cm) 9.84 lb (4.46 kg)ITEM NO.PART NUMBERDESCRIPTION 1 RP88001S SKIRT, SMALL (US) 1 RP88001ML SKIRT, MEDIUM/LARGE (US) 2 RP88001YS YOKE, SMALL 2 RP88001YML YOKE, MEDIUM/LARGE 3 770016 INHALATION CARTRIDGECONNECTOR4 770017 INHALATION VALVE FLAP5 770019 EXHALATION VALVE SEAT6 770018 EXHALATION VALVE FLAP7 770020 EXHALATION VALVE GUARD8 RP8801HS HEADBAND HOOK SIDEASSEMBLY9 RP8801RS HEADBAND RING SIDEASSEMBLY10 RP8801CA HEADBAND CRADLEASSEMBLYCountry of OriginMexicoLimited WarrantyHoneywell Industrial Safety warrants the RU8800 Series Half Mask to the original owner to be free from defects in materials and workmanship for a period of one (1) year from the date of original shipment from Honeywell’s factory. Honeywell’s obligation under this limited warranty will be, at Honeywell’s option, to repair or replace without charge the RU8800 Series Half Mask or any of its components found by Honeywell to have been defective during the limited warranty period, under the following terms:1. The warranty claim is made (i) by the owner who purchased the RU8800 Series Half Mask new from Honeywell or an authorized Honeywell Distributor, and (ii) not more than three (3) months after the end of the limited warranty period.2. The RU8800 Series Half Mask or component is found by Honeywell to have been defective in normal use and service during the limited warranty period of one (1) year from the date of purchase by the original owner.3. The RU8800 Series Half Mask or component is returned freight prepaid to Honeywell, either to its factory or to a Honeywell authorized service center, and is thereafter returned to the owner freight collect.4. This limited warranty does not apply to (i) any RU8800 Series Half Mask or component found by Honeywell to have become defective as a result of any accident, alteration, misuse, abuse, or servicing with parts not approved by Honeywell; (ii) deterioration or aging of any component made of rubber or other elastomer since such components can be adversely affected by undue exposure to heat, sun, water, chemicals, ozone or other deteriorating elements; or (iii) facepiece lens, compressed-air cylinders and parts that become defective through normal use. The decision as to what constitutes normal use shall be made solely by HONEYWELL SAFETY PRODUCTS.5. To maintain this limited warranty, the purchaser must perform maintenance and inspections as set forth in the Operating and Maintenance Instruction Manual for this product which shall include prompt replacement or repair of defective parts, and replacement of parts per the maintenance schedule as set forth in such instructions.。
honeywell介绍

详细资料请查看:世界500强跨国集团ૠปᆊऑႊࡼ಼ဥ1885年,Al Butz 开发了熔炉控制系统,将此系统作为产品成立公司 1886年,发明世界上第一个温控器,成立Butz 电子温度调节器公司 1893年, 更名为电子供热调节器公司(HER) 1906年,马克 · 霍尼韦尔的年轻人创立了霍尼韦尔特种加热器公司 1921年,EHR公司更名为明尼艾普利斯公斯供热调节器公司(MHR) 1927年,MHR公司和霍尼韦尔特种加热器公司合并,组成明尼艾普利斯。
霍尼韦尔 调节器公司 从此开始了在控制领域购并企业及在全球扩展业务 调节器公司,从此开始了在控制领域购并企业及在全球扩展业务 1929年,公司公司股票上市 1963年,公司正式更名为霍尼韦尔公司 1969年,霍尼韦尔的仪表帮助美国宇航员首次成功登月 1974年,霍尼韦尔研制开发了世界上第一套集散控制系统(DCS), 并成为一种 规范沿用至今 1998年,霍尼韦尔营业收入达到84亿美元 1999年,霍尼韦尔与美国联合信号公司合并,合并后公司仍称为霍尼韦尔 年 霍尼韦尔与美国联合信号公司合并 合并后公司仍称为霍尼韦尔ሚᏴࡼૠปᆊऑႊ///全球 100个国家拥有12万员工, 总部设在美国新泽西州莫里斯镇 年销售额超过346亿美元 著名 30 家道琼斯股指公司之一,“标准普尔 家道琼斯股指公司之 “标准普尔500指数”的组成部分 排列《财富》杂志前50位 被《财富》杂志(1999)评为“工作最适” Best to Work For 公司 被《工业周刊》(1999) 评为 “最佳管理公司” 最佳管理公司 Best Managed Companies, 被 《福布斯》评为 “世界第一多元化公司”●●●●●●全球超过1亿的家庭或大楼使用霍尼韦尔的楼宇控制产品 全球第一流的专利拥有者 全球第 流的专利拥有者●ጓᇗஉ৩特种材料 航空航天自动化与控制 交通与动力非常宽的、多元化的业务、技术和产品ੋహੋᄖݝDŽAerospaceDž主要产品:涡轮发动机 空中管理系统 发电系统 飞机安全系 涡轮发动机,空中管理系统,发电系统, 统,通信产品,商业数据与处理,飞机内外照明 航天 飞机导航 航 与控制系统 飞机导航,航空与控制系统,全球定位系统等。
电弧防护服标准

电弧防护服标准
电弧防护服的标准主要有以下几个:
1. NFPA 70E:这个标准是由美国国家消防协会制定的,用于指导和保护职业工作者在电弧灾害中的安全工作。
它规定了电弧防护服的设计要求、性能要求以及使用和维护要求。
2. EN ISO 11612:这个标准是欧洲标准化组织制定的电弧防护服的欧洲标准。
它对电弧防护服的燃烧性能、热传导性能、热辐射热防护性能、电弧抗击穿强度等方面进行了要求。
3. ASTM F1506:这个标准是美国材料和试验协会制定的电弧防护服的标准。
它要求电弧防护服材料具有一定的防火性能和电弧抗击穿能力,保护工人免受电弧灾害的伤害。
4. IEC 61482-1-1:这个标准是国际电工委员会制定的电弧防护服的国际标准。
它规定了电弧防护服的设计要求、材料要求、测试方法等,以确保工作人员在电弧灾害中获得足够的保护。
5. 由国家应急管理部提出并归口防护服标准:《GB 8965.4-2022 防护服装防电弧服新标》已于2022年12月29日发布,将于2024年1月1日起实施
这些标准旨在确保电弧防护服具有足够的耐火性能、电弧抗击穿能力以及热辐射热防护性能,以保护工人免受电弧灾害的伤害。
根据不同国家和地区的要求,电弧防护服可能需要符合其中一个或多个标准。
Honeywell压力开关产品介绍及特点说明书
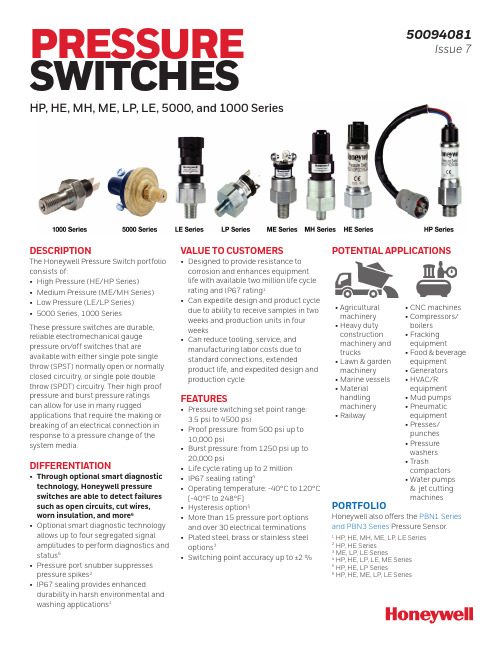
DESCRIPTIONThe Honeywell Pressure Switch portfolio consists of:• High Pressure (HE/HP Series)• Medium Pressure (ME/MH Series)• Low Pressure (LE/LP Series)• 5000 Series, 1000 SeriesThese pressure switches are durable, reliable electromechanical gauge pressure on/off switches that are available with either single pole single throw (SPST) normally open or normally closed circuitry, or single pole double throw (SPDT) circuitry. Their high proof pressure and burst pressure ratingscan allow for use in many rugged applications that require the making or breaking of an electrical connection in response to a pressure change of the system media.DIFFERENTIATION• Through optional smart diagnostic technology, Honeywell pressure switches are able to detect failures such as open circuits, cut wires, worn insulation, and more6• Optional smart diagnostic technology allows up to four segregated signal amplitudes to perform diagnostics and status6• Pressure port snubber suppresses pressure spikes2• IP67 sealing provides enhanced durability in harsh environmental and washing applications1POTENTIAL APPLICATIONS • Agriculturalmachinery• Heavy dutyconstructionmachinery andtrucks• Lawn & gardenmachinery• Marine vessels• Materialhandlingmachinery• Railway• CNC machines• Compressors/boilers• Frackingequipment• Food & beverageequipment• Generators• HVAC/Requipment• Mud pumps• Pneumaticequipment• Presses/punches• Pressurewashers• Trashcompactors• Water pumps& jet cuttingmachines PORTFOLIOHoneywell also offers the PBN1 Series and PBN3 Series Pressure Sensor.1 HP, HE, MH, ME, LP, LE Series2 HP, HE Series3 ME, LP, LE Series4 HP, HE, LP, LE, ME Series5 HP, HE, LP Series6 HP, HE, ME, LP, LE SeriesPRESSURE SWITCHES HP, HE, MH, ME, LP, LE, 5000, and 1000 Series 50094081Issue 7VALUE TO CUSTOMERS• Designed to provide resistance to corrosion and enhances equipment life with available two million life cycle rating and IP67 rating1• Can expedite design and product cycle due to ability to receive samples in two weeks and production units in four weeks• Can reduce tooling, service, and manufacturing labor costs due to standard connections, extended product life, and expedited design and production cycleFEATURES• Pressure switching set point range: 3.5 psi to 4500 psi• Proof pressure: from 500 psi up to 10,000 psi• Burst pressure: from 1250 psi up to 20,000 psi• Life cycle rating up to 2 million• IP67 sealing rating4• Operating temperature: -40°C to 120°C [-40°F to 248°F]• Hysteresis option5• More than 15 pressure port options and over 30 electrical terminations • Plated steel, brass or stainless steel options3• Switching point accuracy up to ±2 %8Port Style C: Switches less than 975 psi will use Base Style B; switches greater than 975 psi will use Base Style A.Port Styles F and G: Switches less than 350 psi will use Base Style B; switches greater than 350 psi will use Base Style A. Port Styles A, B, E, M, P, T, and Y will use Base Style B.Switches less than 150 psi will only use Base Style B.2 /ast2Operating pressure: Maximum normal system operating pressure3Proof pressure: Maximum pressure that the switch can handle while it maintains set point accuracy. Intermittent spikes to this level are acceptable. 4Burst pressure: Point of complete switch failure5SPST: Single pole, single throw. SPDT: Single pole, double throw. NO: Normally open. NC: Normally closed. 6Field adjustability only available with AA, BA, CA, and DA (SPST only) terminations.7IP00 for AA and BA terminations.Honeywell Advanced Sensing Technologies 3*These connectors are designed for dual circuit (SPDT) by default. They can be used for single-circuit applications (SPNC/SPNO) by making suit-able connections. Refer to wiring diagram.4 /astHoneywell Advanced Sensing Technologies 5DIMENSIONS - HIGH PRESSURE: HP SERIES (BASE STYLE A), HE SERIESBase Style A key specifications • Life: 2 million (HP), 1 million (HE); Burst pressure: 20,000 psiFigure 1. AMP Superseal 1.5(top view)Female Connector Part Number (included): C-282105Male Mating Connector (customer provided): C-282087IP Rating: IP67(top view)Female Connector Part Number (included): DT04-3P Male Mating Connector (customer provided): DT06-3S IP Rating: IP67(top view)27 mm [1.063] hex A/F(top view)IP Rating: IP676 /astDIMENSIONS - HIGH PRESSURE: HP SERIES (BASE STYLE B)Base Style B key specifications • Life: 1 million; Burst pressure: 9,000 psi1Port Style C: Switches less than 975 psi will use Base Style B; switches greater than 975 psi will use Base Style A.2Port Styles F and G: Switches less than 350 psi will use Base Style B; switches greater than 350 psi will use Base Style A. Switches less than 150 psi will use only Base Style B.Figure 6. HP Series Base Style Bfor all base ports.Honeywell Advanced Sensing Technologies 7DIMENSIONS - MEDIUM PRESSURE: MH SERIESFigure 13. MH Series Pressure Port DimensionsFigure 8. AMP Superseal 1.5Figure 12. Screw terminal8 /astDIMENSIONS - MEDIUM PRESSURE: ME SERIESFigure 20. ME Series Pressure Port DimensionsMale mating connector (customer provided): C-282087IP rating: IP67Female connector part number (included): DT04-3P Male mating connector (customer provided): DT06-3S IP rating:IP67Figure 17. Wire outMale mating connector (customer provided): DT06-2S IP rating:IP67Honeywell Advanced Sensing Technologies 9DIMENSIONS - LOW PRESSURE: LP SERIES, LE SERIESFigure 24. Wire outFigure 27. LP/LE Series Pressure Port Dimensions10 /astDIMENSIONS - 1000 SERIES, 5000 SERIESFigure 28. 1000 Series Dimensions[0.39 in]Figure 29. 5000 Series DimensionsTHoneywell Advanced Sensing Technologies 11NOMENCLATURE: HIGH PRESSUREHPSeriesSet PointRPressure UnitPHP Series HE Series (100 psi to 4500 psi),High Pressure SwitchFPort TypePressure Set Point05500NOutputBaseSPActuation/ApplicationOptionsAAAConnector TypePackaging Options01They can be used for single-circuit applications (SPNC/SPNO) by making suitable connections. Refer to wiring diagram.For example, HPR05500PFNSPAAA01 defines a high pressure switch, rising factory set, non-adjustable set point, 550 psi set point, psig, sealed gage pressure unit, M14 x 1.5 port type, SPST-NO silver contacts output, cold-rolled steel base, glycol-based fluid (EPDM) actuation/application, spade terminal connectors, standard switch, individually boxed units.12 /astNOMENCLATURE: MEDIUM PRESSURE, HIGH BURSTMHSeriesSet PointRPressure UnitPMedium PressureSwitchAPort TypePressure Set Point01500POutputBaseNMActuation/ApplicationOptionsAAAConnector TypeThey can be used for single-circuit applications (SPNC/SPNO) by making suitable connections. Refer to wiring diagram.Packaging Options01For example, MHR01500PFPNMAAA01 defines a medium pressure, high burst switch, rising factory set, non-adjustable set point, 150 psi set point, psig, sealed gage pressure unit, 1/4-18 NPT port type, SPST-NO contacts output, plated steel base, LTNB diaphragm, and spade terminal connectors.Honeywell Advanced Sensing Technologies 13NOMENCLATURE: MEDIUM PRESSUREMESeriesSet PointRPressure UnitPMedium PressureSwitchFPort TypePressure Set Point01500POutputBaseVKActuation/ApplicationOptionsAPackaging Options01AAConnector TypeThey can be used for single-circuit applications (SPNC/SPNO) by making suitable connections. Refer to wiring diagram.For example, MER01500PFPVKAAA01 defines a medium pressure switch, rising factory set, non-adjustable set point, 55 psi set point, psig, sealed gage pressure unit, M14 x 1.5 port type, SPST-NO gold-plated contacts output, stainless steel base, Kapton ® diaphragm (Teflon ® coated), Nitrile O-ring actuation/application, spade terminal connectors, standard switch, individually boxed units.14 /astNOMENCLATURE: LOW PRESSURELPSeriesSet PointRPressure UnitPLowPressureSwitchFPort TypePressure Set Point00550POutputBaseVKActuation/ApplicationOptionsAPackaging Options01AAConnector TypeThey can be used for single-circuit applications (SPNC/SPNO) by making suitable connections. Refer to wiring diagram.**For electrical termination with SPST option, only SPNOconfiguration is available. SPNC configuration cannot be provided.For example, LPR00550PFPVKAAA01 defines a low pressure switch, rising factory set, non-adjustable set point, 55 psi set point, psig, sealed gage pressure unit, M14 x 1.5 port type, SPST-NO gold-plated contacts output, stainless steel base, Kapton ® diaphragm (Teflon ® coated), Nitrile O-ring actuation/application, spade terminal connectors, standard switch, individually boxed units.® DuPont™, Teflon ®, Tefzel ®, and Kapton ® are trademarks or reg-istered trademarks of E.I. du Pont de Nemours and Company50094081-7-EN | 7 | 04/21© 2021 Honeywell International Inc.WARRANTY/REMEDYHoneywell warrants goods of its manu-facture as being free of defective materi-als and faulty workmanship during the applicable warranty period. Honeywell’s standard product warranty applies un-less agreed to otherwise by Honeywell in writing; please refer to your order ac-knowledgment or consult your local sales office for specific warranty details. If war-ranted goods are returned to Honeywell during the period of coverage, Honeywell will repair or replace, at its option, without charge those items that Honeywell, in its sole discretion, finds defective. The foregoing is buyer’s sole remedy and is in lieu of all other warranties, expressed or implied, including those of merchantability and fitness for a particular purpose. In no event shall Honeywell be liable for consequential, special, or indirect damages.While Honeywell may provide applica-tion assistance personally, through our literature and the Honeywell web site, it is buyer’s sole responsibility to determine the suitability of the product in the ap-plication.Specifications may change without notice. The information we supply isbelieved to be accurate and reliable as of this writing. However, Honeywell assumes no responsibility for its use.m WARNINGPERSONAL INJURYDO NOT USE these products as safety or emergency stop devices or in any other application where failure of the product could result in personal injury.Failure to comply with theseinstructions could result in death or serious injury.m WARNINGMISUSE OFDOCUMENTATION•The information presented in this product sheet is for reference only. Do not use this document as a product installation guide.•Complete installation, operation, and maintenance information is provided in the instructions supplied with each product.Failure to comply with theseinstructions could result in death or serious injury.HoneywellAdvanced Sensing Technologies 830 East Arapaho Road Richardson, TX /astFOR MORE INFORMATIONHoneywell Advanced SensingTechnologies services its customers through a worldwide network of sales offices and distributors. For application assistance, current specifications, pricing, or the nearest AuthorizedDistributor, visit /ast or call:USA/Canada +302 613 4491Latin America +1 305 805 8188Europe +44 1344 238258Japan +81 (0) 3-6730-7152Singapore +65 6355 2828Greater China+86 4006396841。
霍尼韦尔燃烧产品手册

霍尼韦尔燃烧控制产品手册燃烧安全控制器燃气阀门组7800 系列燃烧安全控制器Satronic 系列燃烧安全控制器Honeywell 锅炉及燃烧器控制产品目录7800 - 系列燃烧程序控制器 (5)EC7800 / R M7800 - 燃烧程序控制器..........................................................................................5Q7800 - 通用接线座...............................................................................................................5S7800A - 吹扫时间定时卡......................................................................................................5S7800 - 工作状态显示板.........................................................................................................5S7810 - 数据通讯板..................................................................................................................5S7820A - 远端复位板...............................................................................................................5R7800 - 火焰信号放大器............................................................................................................5其它常用燃烧程序控制器 (6)R4343D/E - 火焰开关型控制器......... ................................................................................................6FC1000A/B-火焰开关型控制器...................................................................................................6RA890F/G - 基本型燃烧安全控制器.......................................................................................6火焰探测器 (7)C7015A - 红外滤波型火焰探测器.............................................................................................7C7027A - 一体化紫外型火焰探测器.............................................................................................7C7035A - 紫外型火焰探测器(紫外探测管可更换)........................................................................7C7061A/F-紫外,自检型火焰探测器................................................................................................7C7012A/C/E/F - 紫外型火焰探测器(可带探头自检及防爆)...............................................................7Satronic 燃烧安全控制器 (8)数字微处理器型燃油燃烧程序控制器.......................................................................................8数字微处理器型燃气燃烧程序控制器..........................................................................................8模拟型燃油燃烧程序控制器................................................................................................8模拟型燃气燃烧程序控制器...................................................................................................8点火变压器..................................................................................................................8火焰探测器.........................................................................................................8风门执行器 (9)MT4000 - 中小型燃烧机用风门或蝶阀执行器..............................................................................9LKS - 系列风门执行器...............................................................................................................9MODUTROL I V - 大中型燃烧器用风门执行器..............................................................................9MODUTROL I V - 系列执行器通用配件.......................................................................................9压力开关及压力控制器............................................................................................................10 L404-锅炉压力控制开关 (10)L91B - 锅炉蒸汽压力控制器...................................................................................................10P7800 - 锅炉蒸汽压力控制器................................................................................................10C6097A - 燃气、空气压力开关.............................................................................................10燃气电磁阀(UGV系列) (11)VE400AA - 系列点火电磁阀 (11)VE4000A1 -无流量调节功能,通断,常闭,快开螺纹连接电磁阀 (11)VE4000B1 -具有流量调节功能,通断,常闭,快开螺纹连接电磁阀 (11)VE 4000B3 -具有流量调节功能,通断,常闭,快开法兰连接电磁阀 (12)VE4000 C1- 具有流量调节和缓慢开启功能的通断常闭阀 (12)VE5000及V5055 -系列电液执行器型电动阀 (12)VQ400 -系列 “A”级 组合电磁阀 (13)VR400 -系列组合“A”级电磁阀 (14)VQ465、VQ480 -系列大口径组合电磁阀 (15)VG400、VG4000 -系列手动复位“A”级电磁阀 (16)BT-BC -系列大口径电磁阀 (16)VF 5000 - 系列燃气调节蝶阀 (17)HUPF -带过滤器的调压器,HUF -过滤器 (17)HUPF- 带过滤器的调压器 (17)HUF -过滤器 (17)HUG -燃气连接软管 (18)A4021A -燃气阀门泄漏检测器 (18)小型家用及商业用燃气电磁阀及控制器 (19)CVI 控制系统 (19)VR4605AB/CB 系列电磁阀及 S4560 系列控制器 (20)阀门流量曲线图 (21)VE400及VE4000 - 系列电磁阀流量曲线图 (21)VE4000及VE5000 -系列电磁阀流量曲线图......................................................... (22)VQ400 -系列组合电磁阀流量曲线图 (22)VQ465/VQ480 - 系列电磁阀流量曲线图 (23)VF5000A -系列蝶阀流量曲线图 (24)HUPF -系列调压器流量曲线图 (25)HUF -系列过滤器流量曲线图 (25)产品型号索引 (26)本产品手册如与出厂资料不同,请以出厂资料为准。
林肯电气兰格8型切割机操作手册说明书

RANGER ™8OPERATOR’S MANUALFor Machines with Code Numbers 10908, 10935, 10998IM752-AJanuary, 2003Copyright © 2003 Lincoln Global Inc.This manual covers equipment which is nolonger in production by The Lincoln Electric Co. Speci cations and availability of optional features may have changed.Mar ‘95for selecting a QUALITY product by Lincoln Electric. We want you to take pride in operating this Lincoln Electric Company product ••• as much pride as we have in bringing this product to you!Read this Operators Manual completely before attempting to use this equipment. Save this manual and keep it handy for quick reference. Pay particular attention to the safety instructions we have provided for your protection.The level of seriousness to be applied to each is explained below:vvAC STICK / TIG (CC) OUTPUTOUTPUT AMPSO U T P U T V O L T S AC (R M S )50100150200250010203040607080DC STICK / TIG (CC) OUTPUTOUTPUT AMPSO U T P U T V O L T S D C (R M S )5010015020025030035001020304050607080CV OUTPUT RANGE50100150200250300OUTPUT AMPS3500510152025303540DC WIRE FEED (CV) OUTPUTO U T P U T V O L T S D C (R M S )SPECIFICATIONSInternal combustion engines are designed to run in a level condition which is where the optimum perfor-mance is achieved. The maximum angle of operation for the engine is 15 degrees from horizontal in any direction. If the engine is to be operated at an angle,provisions must be made for checking and maintain-ing the oil at the normal (F ULL) oil capacity in the crankcase in a level condition.When operating at an angle, the effective fuel capaci-ty will be slightly less than the specified 9 gallons.HIGH ALTITUDE OPERATIONIf the Ranger 8 will be consistently operated at alti-tudes above 5000 ft, a carburetor jet designed for high altitudes should be installed. This will result in better fuel economy, cleaner exhaust, and longer spark plug life. It will not give increased power which is decreased at higher altitudes. Engine horsepower is reduced by 3.5% per 1000 feet for altitudes above 377 feet.Do not operate a Ranger 8 with a high altitude jet installed at altitudes below 5000 ft. This will result in the engine running too lean and result in higher engine operating temperatures which can shorten engine life.Contact your local Onan, Kohler or Honda Authorized Dealer for high altitude jet kits that are available from the engine manufacturer.Muffler Relocation Shut off welder and allowmuffler to cool before touching muffler.The Ranger 8 is shipped with the exhaust coming out on the left side. The exhaust can be changed to the opposite side by removing the two screws that hold the exhaust port cover in place and installing the cover on the opposite side. (Operating the Ranger 8without the cover in place will result in a higher noise level and no increase in machine output.)The welder should be located to provide an unrestrict-ed flow of clean, cool air to the cooling air inlets and to avoid heated air coming out of the welder recirculating back to the cooling air inlet. Also, locate the welder so that engine exhaust fumes are properly vented to an outside area.CONNECTION OF LINCOLN ELECTRIC WIRE FEEDERSShut off welder before making any electrical connections.WIRE FEED (CONSTANT VOLTAGE)CONNECTION OF THE LN-25 TO THE RANGER 8•Shut the welder off.•Connect the electrode cable from the LN-25 to the“ELECTRODE” terminal of the welder. Connect the work cable to the “TO WORK” terminal of the welder.•Position the welder “Polarity” switch to the desired polarity, either DC (-) or DC (+).•Position the “RANGE” switch to the “WIRE FEED”position.•Attach the single lead from the LN-25 control box to the work using the spring clip on the end of thelead - it carries no welding current.•Place the idler switch in the “AUTO” position.•Adjust wire feed speed at the LN-25 and adjust the welding voltage with the output “CONTROL”at the welder.NOTE:The welding electrode is energized at all times, unless an LN-25 with built-in contactor is used.If the output “CONTROL” is set below “3”, the LN-25contactor may not pull in.•Connect the LN-7 and the K240 contactor kit per instructions on the connection diagram S17742(can be found in the back of this manual).•Place the “RANGE” switch to the “WIRE FEED”position and the “POLARITY” switch to thedesired polarity.•Place the “IDLER” switch in the “HIGH” idle position. The engine idling device may notfunction when welding in the “WIRE FEED” mode.•Adjust wire feed speed at the LN-7 and adjust the welding voltage with the output “CONTROL” atthe welder.NOTE:If the output “CONTROL” is set below “3” the K240 contactor may not pull in.CONNECTION OF K930-[ ] TIG MODULE TO THE RANGER 8.The TIG Module is an accessory that provides high frequency and shielding gas control for AC and DC GTAW (TIG) welding. See IM528 supplied with the TIG Module for installation instructions.Note: The TIG Module does not require the use of a high frequency bypass capacitor. However, if the Ranger 8 is used with any other high frequency equip-ment, the bypass capacitor must be installed - order kit T12246.INSTRUCTIONSADDITIONAL SAFETY PRECAUTIONSAlways operate the welder with the roof and case sides in place as this provides maximum protection from moving parts and assures proper cooling air flow.Read and understand all Safety Precautions before operating this machine. Always follow these and any other safety procedures included in this manual and inthe Engine Owner’s Manual.TABLE lllELECTRICAL DEVICE USE WITH THE RANGER 8.Type Common Electrical Devices Possible ConcernsResistive Heaters, toasters, incandescent NONElight bulbs, electric range, hotpan, skillet, coffee maker.Capacitive TV sets, radios, microwaves, Voltage spikes or high voltageappliances with electrical control.regulation can cause the capac-itative elements to fail. Surgeprotection, transient protection,and additional loading is recom-mended for 100% fail-safeoperation. DO NOT RUNTHESE DEVICES WITHOUTADDITIONAL RESISTIVE TYPELOADS.Inductive Single-phase induction motors, These devices require largedrills, well pumps, grinders, small current inrush for starting.refrigerators, weed and hedge Some synchronous motors maytrimmers be frequency sensitive to attainmaximum output torque, butthey SHOULD BE SAFE fromany frequency induced failures. Capacitive/Inductive Computers, high resolution TV sets,An inductive type line condition-complicated electrical equipment. er along with transient andsurge protection is required,and liabilities still exist. DONOT USE THESE DEVICESWITH A RANGER 8The Lincoln Electric Company is not responsible for any damage to electrical components improperly connect-ed to the RANGER 8.1.Install a double pole, double throw switch betweenthe power company meter and the premisesdisconnect.Switch rating must be the same or greater thanthe customer’s premises disconnect and serviceovercurrent protection.2.Take necessary steps to assure load is limited tothe capacity of the Ranger 8 by installing a 35 amp 230V double pole circuit breaker. Maximumrated load for the 230V auxiliary is 35 amperes.Loading above 35 amperes will reduce outputvoltage below the allowable -10% of ratedvoltage which may damage appliances or othermotor-driven equipment.3.Install a 50 amp 115/230V plug (NEMA type 14-50)to the Double Pole Circuit Breaker using No. 8,4 conductor cable of the desired length. (The50 amp 115/230V plug is available in theoptional plug kit.)4.Plug this cable into the 50 amp 115/230Vreceptacle on the Ranger 8 case front.LOAD NATIONAL ELECTRICAL CODE FOR ALTERNATE WIRESIZE RECOMMENDATIONS.“ CONTROL” SWITCHProvides a fine welding current adjustment within the Range Switch settings in the STICK/TIG mode and welding voltage control with the Range switch set in the wire feed mode.“IDLER” SWITCHThe idler switch has two positions, “HIGH” and “AUTO”.When in “HIGH” ( ) position, the engine will run continuously at high idle.When in “AUTO” ( / ) idle position, the idler operates as follows:•WeldingWhen the electrode touches the work, the welding arc is initiated and the engine accelerates to fullspeed.After welding ceases (and no auxiliary power isbeing drawn), the engine will return to low idleafter approximately 10 to 14 seconds.•Auxiliary PowerWith the engine running at low idle and auxiliarypower for lights or tools is drawn (approximately100-150 watts or greater) from the receptacles,the engine will accelerate to high speed. If nopower is being drawn from the receptacles (andnot welding) for 10-14 seconds, the idler reducesthe engine speed to low idle.SUMMARY OF WELDING PROCESSESThis Troubleshooting Guide is provided to help you locate and repair possible machine malfunctions.Simply follow the three-step procedure listed below.Step 1.LOCATE PROBLEM (SYMPTOM).Look under the column labeled “PROBLEM (SYMP-TOMS)”. This column describes possible symptoms that the machine may exhibit. Find the listing that best describes the symptom that the machine isexhibiting.Step 2.POSSIBLE CAUSE.The second column labeled “POSSIBLE CAUSE ” lists the obvious external possibilities that may contribute to the machine symptom.Step 3.RECOMMENDED COURSE OF ACTIONThis column provides a course of action for the Possible Cause, generally it states to contact your local Lincoln Authorized Field Service Facility.If you do not understand or are unable to perform the Recommended Course of Action safely, contact your local Lincoln Authorized Field Service Facility.HOW TO USE TROUBLESHOOTING GUIDEService and Repair should only be performed by Lincoln Electric Factory Trained Personnel.Unauthorized repairs performed on this equipment may result in danger to the technician and machine operator and will invalidate your factory warranty. For your safety and to avoid Electrical Shock, please observe all safety notes and precautions detailed throughout this manual.__________________________________________________________________________R A N G E R 8 H O N D A W I R I N G D I A G R A M F O R C O D E 10998G 4375N O T E : T h i s d i a g r a m i s f o r r e f e r e n c e o n l y . I t m a y n o t b e a c c u r a t e f o r a l l m a c h i n e s c o v e r e d b y t h i s m a n u a l . T h e s p e c i f i c d i a g r a m f o r a p a r t i c u l a r c o d e i s p a s t e d i n s i d e t h e m a c h i n e o n o n e o f t h e e n c l o s u r e p a n e l s . I f t h e d i a g r a m i s i l l e g i b l e , w r i t e t o t h e S e r v i c e D e p a r t m e n t f o r a r e p l a c e m e n t . G i v e t h e e q u i p m e n t c o d e n u m b e r ..JapaneseChineseKoreanArabicREAD AND UNDERSTAND THE MANUFACTURER’S INSTRUCTION FOR THIS EQUIPMENT AND THE CONSUMABLES TO BE USED AND FOLLOW YOUR EMPLOYER’S SAFETY PRACTICES.SE RECOMIENDA LEER Y ENTENDER LAS INSTRUCCIONES DEL FABRICANTE PARA EL USO DE ESTE EQUIPO Y LOS CONSUMIBLES QUE VA A UTILIZAR, SIGA LAS MEDIDAS DE SEGURIDAD DE SU SUPERVISOR.LISEZ ET COMPRENEZ LES INSTRUCTIONS DU FABRICANT EN CE QUI REGARDE CET EQUIPMENT ET LES PRODUITS A ETRE EMPLOYES ET SUIVEZ LES PROCEDURES DE SECURITE DE VOTRE EMPLOYEUR.LESEN SIE UND BEFOLGEN SIE DIE BETRIEBSANLEITUNG DER ANLAGE UND DEN ELEKTRODENEINSATZ DES HER-STELLERS. DIE UNFALLVERHÜTUNGSVORSCHRIFTEN DES ARBEITGEBERS SIND EBENFALLS ZU BEACHTEN.JapaneseChineseKoreanArabicLEIA E COMPREENDA AS INSTRUÇÕES DO FABRICANTE PARA ESTE EQUIPAMENTO E AS PARTES DE USO, E SIGA AS PRÁTICAS DE SEGURANÇA DO EMPREGADOR.。
Honeywell 低功耗开关技术简介说明书

LOW ENERGY SWITCHINGGeneral Technical Bulletin #13 - Low Energy Switching2 Honeywell Sensing and Controle of ContentsPageINTRODUCTION (3)LOW ENERGY SWITCHING (3)MECHANICAL PERFORMANCE (4)Plunger Movement Characteristics (4)Plunger Force vs. Plunger Position................................................................. 5 Circuit Terminology (5)ELECTRICAL PERFORMANCE (6)Insulation Resistance..................................................................................... 6 Dielectric Strength......................................................................................... 6 Switch Resistance......................................................................................... 6 Contact Resistance....................................................................................... 7 Load Resistance........................................................................................... 7 Measurement of Switch Resistance................................................................ 7 Switch Resistance in Application................................................................... 8 Role of Contamination in Switch Resistance................................................... 9 Common Contact Materials..........................................................................10 Common Contact Configurations...................................................................11 Switch Life (12)GENERAL APPLICATION GUIDELINES .....................................................13 Storage, Installation, and Maintenance...........................................................13 Design..........................................................................................................14 Environment.. (15)SUMMARY (15)General Technical Bulletin #13 - Low Energy SwitchingFor application help: call 1-800-537-6945 Honeywell Sensing and Control 3INTRODUCTIONIn today’s age of low energy control, electromechanical switches are more frequently interfacing directly with computers and other low energy driven hardware. Switching low energy loads presents a unique challenge as compared to switching higher energy loads and at times requires an alternative switch design.The purpose of this bulletin is to provide general information about mechanical and electrical performance of electromechanical switches, along with application guidelines for using electromechanical switches in low energy applications.LOW ENERGY SWITCHINGLow energy switching can be described as using a switch to control any component(s) of a circuit where the load that the contacts will switch will not cause an arc to form between the contacts. Common names for these types of circuits are thermocouple load, dry circuit, logic level, etc.The primary concern in the area of low energy switching is contact contamination. Since low energy loads do not arc or burn the contact surface, they also do not arc or burn off the contaminants that may reside on the contact surface. These contaminants may cause erratic switch resistance and can stop current flow. Pay special attention to the General Application Guidelines if the switch is to be used in a low energy application.General Technical Bulletin #13 - Low Energy Switching4 For application help: call 1-800-537-6945 Honeywell Sensing and ControlMECHANICAL PERFORMANCEPlunger Movement Characteristics of a Basic SwitchFree Position: Switch plunger is fully released and common contact is against normally closed contact.Pretravel: Distance from free position to operating point.Operating Point: Common contact transfers from normally closed contact to normally open contact.Overtravel : Distance plunger travels past operating point.Full Overtravel Point : Point at which further plunger depression is prevented by switch mechanism.Release Point: Common contact transfers from normally open contact to normally closed contact.Differential Travel: Distance between operating point and release point.Operating Force: Force required to depress switch plunger to operating point.Full Overtravel Force: Force required to depress switch plunger to full overtravel point.Release force: Force required to allow the plunger to return to release point.The movement of the switch plunger from the free position through the release point is considered one cycle of switch operation.General Technical Bulletin #13 - Low Energy SwitchingFor application help: call 1-800-537-6945 Honeywell Sensing and Control 5Plunger Force vs. Plunger PositionThe graph at the right represents the relationship between plunger travel and plunger force and is of interest when the mechanism used to operate the switch is a force-sensitive device such as a dead weight, a thermostatic bimetal or a gas-filled bellows.For data on a specific switch type, contact the- MICRO SWITCH Application Center at 1-800-537-6945.Circuitry TerminologyPole : The number of completely separate circuits that can pass through the switch at one time.Throw: The number of different circuits that each pole can control.Break: The number of pairs of separated contacts the switch introduces into each circuit it opens.General Technical Bulletin #13 - Low Energy Switching6 For application help: call 1-800-537-6945 Honeywell Sensing and ControlELECTRICAL PERFORMANCEInsulation Resistance Applied voltage divided by the current is the electrical resistance of the insulation. For new switches at commonly used voltages, insulation resistance usually exceeds 100,000 megohms between non-connected terminals and between terminals and switch housing. The voltage does put an electrical stress on the material but does not damage it unless the potential exceeds the dielectric strength of the switch.Dielectric Strength Dielectric strength is the highest electrical potential that an insulating material can withstand without breaking down, i.e., dielectric breakdown. New switches usually have dielectric strength of over 1000 volts with leakage current less than 500 microamps. When the voltage exceeds the dielectric strength, the insulating material is permanently damaged.Insulation Resistance and Dielectric StrengthSwitch Resistance Switch Resistance is the total resistance of the conducting path between the wiringterminals of the switch.Sources of Switch ResistanceGeneral Technical Bulletin #13 - Low Energy SwitchingFor application help: call 1-800-537-6945 Honeywell Sensing and Control 7Typical Pattern of Switch Resistance versus Plunger Position at 6 Volts DC, 0.1 AmpereContact Resistance : The resistance between a pair of closed contacts.Load Resistance : Load resistance affects contact resistance in the following way; if the circuit voltageexceeds the softening or melting voltage of the contact material, the material softens or melts due to I 2R heating. See table below for softening and melting voltage of silver and gold.MaterialApproximateSoftening VoltageApproximate Melting VoltageSilver .09 Volt .37 Volt Gold.08 Volt.43 VoltIf the metal at the contact interface softens or melts, the cross-sectional area of the conducting path between the contacts will depend upon the current. The size of this cross-sectional area determines contact resistance. The higher the current, the greater the cross-sectional area of the bridge and the lower its resistance. If the softening voltage is not reached, the contact resistance is independent of current.Measurement ofSwitch Resistance: Switch resistance should be measured by voltage drop using the same voltage andcurrent as in the circuit in which the switch is to be used. This can be accomplished by connecting the switch in a series circuit consisting of a power supply of the specified voltage, a variable resistor and ammeter.General Technical Bulletin #13 - Low Energy SwitchingConnections for Measurement of Switch ResistanceSwitch Resistancein Application: In the application of snap-acting switches, if the source voltage is at least .5 volts, contact material almost always softens, or melts slightly, at the interface, and switch resistance becomes afunction of current. This leads to the following practical consequences:1. In low current circuits, switch resistance tends to be relatively high. However, low current circuitsusually have high resistance load components. The resistance of the switch usually is such a smallpart of the total resistance of the circuit that switch resistance is not a problem.2. High current circuits usually have low-resistance load components. In high current circuitshowever, switch resistance tends to be low. Again, the resistance is such a small part of the totalresistance of the circuit that switch resistance is not a problem.At source voltages of 0.5 volt or greater, the resistance of a switch during its life will rarely exceed1% of the load resistance. If source voltage is less than 0.5 volt, switch resistance may or may notbe a function of current, depending upon the amount of the source voltage that appears across thecontacts.In general, the maximum allowable switch resistance of a specific application can be defined asfollows: For DC circuits, the maximum allowable switch resistance equals the line voltage divided by the minimum allowable current, minus the load resistance. For AC circuits, the maximum allowable switch resistance equals the line voltage divided by minimum allowable current, multiplied by thepower factor and minus the load resistance.8 For application help: call 1-800-537-6945 Honeywell Sensing and ControlGeneral Technical Bulletin #13 - Low Energy SwitchingFor example, consider a switch in series with a relay coil:• 24 VDC, 5000 ohm coil, operate .004 amp, release .0025 amp.• Without the switch in the circuit, I=.0048• With the switch in circuit, coil will operate at I=.004. Switch resistance will do no harm if it does not reduce the .0048 amp to less than .004 amp• Total resistance that will allow .004 amp flow = R = V/I = 24 volts/.004 amp = 6000 ohms• Therefore, maximum allowable switch resistance = 6000 ohms - 5000 ohms or 1000 ohmsRole ofContamination inSwitch Resistance:There are two general classifications for switch contaminants, particles and films. Particles can becrushed solids that enter the switch during application or assembly. Particles deposit on the contact surface, are crushed between the contacts and can become embedded in the contact material due to contact force. Particles can cause erratic contact during wipe and roll of contacts and, if large orextensive enough, can stop current flow.Films are the second type of switch contaminant, which can be broken into two parts, organic andinorganic. Inorganic films, such as silver oxides or silver sulfides, do not typically cause switchresistance problems at the contacts. Silver oxide is conductive, so it does not represent a problem.Silver sulfide films are brittle and are punctured mechanically due to contact force and wiping action.There are several types of contaminants that can create organic films and cause resistance problems.The most common are flux, organic vapors, and silicones. Flux enters the switch cavity by vapor or is carried into the switch cavity by a cleaning solvent. Flux will increase switch resistance and can stop current flow. To avoid flux contamination: avoid use of activated flux; use flux sparingly; use flux core solder; do not allow liquid flux or flux vapor to enter the switch; use a soldering temperature ofapproximately 550° F (288° C); and, do not use solvents on or near switches - they carry flux residue and other contaminants into the switch. It is not necessary to remove flux residue from terminals.Organic materials, especially organic vapors, can decompose in the arc or I2R heating of the material at the interface between the closed contacts. Carbonaceous deposits can build up over time on thecontact surface and increase the switch resistance.For application help: call 1-800-537-6945 Honeywell Sensing and Control 9General Technical Bulletin #13 - Low Energy SwitchingSilicon is an inorganic element found in many materials. Silicone is an organic material commonlyfound in oils, greases, mold release, cleaning sprays, and potting material. Silica (SiO2), commonly referred to as glass, is transformed from silicone in the presence of electrical energy. Silicones enter the switch as vapor and over time, based on load, rate of actuation, and amount of silicone present, transform into silica. These silica deposits can raise switch resistance and stop current flow. Everyprecaution should be taken in the application to prevent silicone from coming in contact with the inner switch cavity.Common ContactMaterials:• Fine silver. 1.6 ohms/cm, low cost, if kept clean, there is no lower load limit.• 24 karat gold.2.36 ohm/cm, high cost, limited to use in applications with little or no arc energy because of its ductility.• Gold Alloys.Different properties depending on the alloy.• Gold clad over silver.If the load is low energy, it is carried through gold. If the load is arcing, it burns away the gold and is carried through silver contacts. However, a switch that has seen anarcing load should not be used for a low energy load.• Silver Cadmium Oxide.Designed for use in power loads, not recommended for use in loads less than .5 amp and/or 12 volts.The following graph can be used as a general guide for the selection of contact material. The graph indicates 1st choice, 2nd choice, etc. for each current range. Note, the current represented on the X axis is steady-state. Inrush currents from motor loads and lamp loads can be 6 to 10 times steadystate current.General Guide to the Selection of Contact Material10 For application help: call 1-800-537-6945 Honeywell Sensing and ControlFor application help: call 1-800-537-6945 Honeywell Sensing and Control 11 Common ContactConfigurations:Smooth contact. Common contact configurationSerrated contact. The top surface of the contact can be serrated toprovide a series of peaks and valleys. When the switch is operated theraised areas (peaks) tend to scruff or scrape over the mating contactsurface. This self-cleaning discourage buildups of films or particulate foreignmaterial on the raised areas. Even when the minute particles are not totallyremoved, they tend to drop into the valleys where they are less likely tocontaminate the contact interface. Serrated contacts have been effective inimproving electrical continuity in applications ranging from power duty loadsto low current requirements.Bifurcated contacts. The most effective system developed to date.Bifurcated contacts offer some of the same benefits as described forserrated contacts in addition to providing parallel redundancy.Redundancy can also be provided by connecting two or more switches inparallel and actuating them at the same time.NOTE : Not all contact configurations are available on all switch types.For more information regarding the availability of different contactconfigurations on specific switch types, contact the HONEYWELLApplication Center at 1-800-537-6945.12 For application help: call 1-800-537-6945 Honeywell Sensing and ControlSwitch Life: Mechanical life: The life of a switch with no electrical load present.Electrical life: The life of a switch when switching an electrical load.The following graph demonstrates the life of switch at different electrical loads. Switch life depends on such criteria as electrical load, environment, switch mechanism, and other factors particular to the application. As electrical load increases, switch life decreases. Below 1 amp, the electrical life approaches the mechanical life of the switch. For available test data, contact the HONEYWELL Application Center at 1-800-537-6945.GENERAL APPLICATION GUIDELINESStorage, Installation,and Maintenance• Store switch in a clean, reasonably dry environment that does not exceed the rated temperature of the switch.• Install the switch carefully:♦ Do not drill, sand or otherwise modify the switch.♦ Do not overtighten mounting screws. Review packing sheet instructions carefully.♦ If mounting the switch with an adhesive, use extreme care to avoid contaminating the switch interior.♦ Avoid the use of silicone materials to prevent silicone from coming in contact with the interior of the switch. If this is not possible, in low energy applications, use a sealed switch.♦ When soldering leads to terminals, use non-activated flux core solder and a soldering temperature of about 550° F (288° C).♦ Do not use solvents on switches.♦ Do not use commercial contact cleaners on snap-action switches.♦ Do not paint over switch after installation.♦ Do not connect opposite polarity between normally open and closed terminals. When this is done, and when the arc persists after the contacts are fully apart, a short circuit is establishedthrough the arc and hence through the switch.• Chemicals used during maintenance cleaning can degrade switch materials. If the switch cannot be easily removed prior to cleaning and the types of chemicals used for cleaning are known,contact the HONEYWELL Application Center at 1-800- 537-6945 fo r fluid compatibilitydata.For application help: call 1-800-537-6945 Honeywell Sensing and Control 13Design• For advice regarding the choice of a switch for a specific application, contact the HONEYWELL Application Center at 1-800-537-6945.• If low price is an important factor, silver contacts may help reach the objective.• All snap acting electromechanical switches have contact bounce. When the contact closes it bounces, causing the switch to open and close for a period of microseconds before stayingclosed. If contact bounce will be a problem, the circuit must be buffered. The circuit can bebuffered with additional electronic circuitry or with software.• If the load is below melting voltage, gold or gold alloys can be used for an added measure of safety.• Actuate the switch as closely as possible to the extremes of its plunger travel without applying excess force that might damage the switch. For force data, contact theHONEYWELLApplication Center, 1-800-537-6945.• Decide, based on accurate technical information, whether a switch resistance specification is needed and whether its additional cost is justified. If so, on the basis of end use, specify: thevoltage, current, plunger position, sequence of actuation, and measurement, and maximumallowable switch resistance.• When to give switch resistance special attention:♦ When the switch controls a circuit at less than 0.5 volts.♦ When several switches must be connected in series.♦ When a switch is likely to be exposed to contaminating particles or fumes.♦ When an occasional switch closure with the switch resistance exceeding 1% of the load resistance will have negative consequences.• Design the circuit so the switch sees voltage well above the softening voltage of the contact material, e.g., 0.08 volt for gold, 0.09 volt for silver.• Design low voltage circuits with a minimum number of switches in series.• Design the switch circuit to be as insensitive to normal variations of switch resistance as possible.14 For application help: call 1-800-537-6945 Honeywell Sensing and ControlIf additional assurance of low and stable resistance is desired, use bifurcated contacts or connect two or more switches in parallel and actuate them at the same time.Customers should test the switch under conditions simulating end use to verify that it performs asrequired in the application.Environment• Protect unsealed switches from contamination by particles and fumes.• Switches can be sealed to help prevent contamination from entering them. Some common levels of sealing are: dust resistant, drip-proof, water resistant, resilient, and hermetic. In general, themore critical the application and the harsher the environment, the more stringent the sealrequirements.• If the switch is unsealed and a low energy load is involved, a thorough understanding of the environment is required to choose the correct contact material and configuration. Contact theHONEYWELL Application Center at 1-800-537-6945, for help in choosing the propermaterial• If the environment of an unsealed switch contains a significant amount of sulfides (such as decaying organic matter, cardboard, or vulcanized rubber) and moisture, gold or gold-plated contacts canhelp.• If an alien film contaminant (such as paint spray or oil mist) can reach the contacts, gold won't help. Use a sealed switch.SUMMARYContact material, contact configuration, and the degree of environmental protection are importantconsiderations when low energy switching is required. They must be considered, along with otherapplication variables, to determine the proper switch for the application. The most reliable and cost-effective solution to any switch application results from a partnership between the user andHoneywell’s Sensing and Control Division.For further technical information and assistance in determining your total switching requirements,contact HONEYWELL:1-800-537-6945 USA1-800-737-3360 Canada1-815-235-6847 InternationalFAX1-815-235-6545 USAINTERNET********************.comFor application help: call 1-800-537-6945 Honeywell • MICRO SWITCH Sensing and Control 15Helping You Control Your World Honeywell Inc.11 West Spring StreetFreeport, Illinois 61032001008-3-EN IL50 GLO 797 Printed in USA。
高压电弧抗点燃指数

高压电弧抗点燃指数
高压电弧抗点燃指数(Arc Rating)是用来衡量防护服物料对电弧热能的防护能力的指标。
它以cal/cm²(卡/平方厘米)为单位表示。
高压电弧抗点燃指数是通过进行实验测试得出的,测试方法根据ASTM标准F1959进行。
在测试中,将样品暴露在电弧能量下,然后根据样品对热能的防护能力来评估抗点燃性能。
电弧时产生的热辐射能量可以通过高压电弧抗点燃指数来进行衡量,指数越高代表物料对电弧热能的防护能力越强。
高压电弧抗点燃指数通常用于评估防护服的选择,以确保工作人员在电弧发生时能够得到足够的防护,从而预防热能引起的烧伤。
需要注意的是,不同的工作环境和操作条件可能需要不同的高压电弧抗点燃指数等级。
因此,在选择防护服时,应根据具体工作条件和要求来确定所需的高压电弧抗点燃指数等级。
Honeywell变压器产品参数手册说明书

PA/V A SOLUTIONSVARIODYN D1Digital Public Address andVoice Alarm System2 | Voice Alarm is increasingly important in the safe management of buildings. A voice message informs occupants exactly what to do in an emergency and it is a long established fact that people respond more quickly and are more likely to take the correct action during an evacuation if voice messages are used instead of tone sounders.THE ROLE OF VOICE ALARM• Clear directions to people in the building• Live messages giving exactinstructions to people whoare not familiar with the surroundings • Customised pre-recordedmessages (available inmultiple languages)• Up to 20 minutes shorter response time to fire alarm• Serial Interface toHoneywell fire panels for EVAC guidance and time-controlled evacuation • High-end non-emergency features such asequalizing, automatic volume control and multi-channel announcements as well as backgroundmusic • Alarm cancellation and manual evacuation override controlBENEFITS | 3PUBLIC ADDRESS -MORE THAN VOICE ALARMVoice Alarm systems are more frequently used as public address and entertainment systems than only as automatic evacuation system inpublic buildings with a high number of visitors.• Paging and evacuation with zone-dependent messages • Integration with airport/train station managementsystems• Multiple channel/zone music broadcasting • Sport/concert hall and stadium sound systemintegration • Time-scheduled announcements• Touch screen operation panels• Operation from intuitive computer management systems • High quality background music for high class shopping experienceFEATURES PUBLIC ADDRESS PROVIDES ADDITIONALL Y:4 |Selecting, designing and commissioning a PA/VA system can be challenging. At Honeywell we have a team of experts that will help you build the most suitable system for your building.The first step is to decide exactly what type of PA/VA system you will need. This will largely depend on the size and functional complexity of your building.The following two types of systems are available that start from small ‘Compact Solution’ packages suitable for single storey buildings such as shops and offices and move up to a custommade ‘Modular System’ that will consist of a number of distributed systems linked together for large structures such as exhibition fairgrounds and airports.VOICE ALARMCOMPETENCE FOR YOU• Controlling and indicating equipment certified to EN 54-16 and EN 54-4• Complete range of EN 54-24 certified loudspeakers • Flexible systems that supports both simple and the most complex communication needs • High quality digital audio matrix• Intuitive touchscreen Graphical User Interface that manages the entire system • Phased evacuation scenarios • Situation, location & evacuation phasedependent voice messages • Exact guidance regarding evacuation routes• Freely configurableevacuation scenarios with logical dependencies • Dedicated Honeywelldesign and project supportSYSTEMS KEY FEATURES |5 LEISURE COMPLEXES SCHOOLS SMALL HOTELS OFFICESTHE COMPACT SOLUTION:COMPRIO D1An easy-to-install PA/VA system.Suitable for small to medium buildingswith up to 24 loudspeaker zones.APPLICATIONS• Leisure complexes• Supermarkets• Schools• Hotels• OfficesBENEFITS• Amplifier with build-in PSU available• ‘Off the Shelf’ Package• Installation within two hours• Only 8 HU rack space incl. amplifier,charger and batteries• Ensured compliance to ENstandards• Complete solution for up to 24zones• max. 2000 W output powerexpandable with additional DOM/AMPs6 | Our PA/VA systems can be distributed and networked together to deliver the most comprehensive and powerful solution for a wide range of applications. Suitable for mid to large and complex sites.THE MODULAR SOLUTION V ARIODYN D1• Industrial facilities • Universities• Airports and transport hubs • Stadiums• Exhibition halls and fairgrounds • Mega Shopping Malls • Large Office buildingsAPPLICATIONS• Scalable and modular to adapt to constant changes and demands• Supports a large number of evacuation and/or paging zones • Manages complicated evacuation strategies in the event of an emergency • IP connectivity tolink multiple nodes (VARIODYN D1 DOM)BENEFITS• Up to 120 announcements at the same time• Pre-recording and playbackof messages• Secured data link to various Honeywell Fire Alarm Systems• Decentralized and redundant system architecture• Interface to BuildingManagement Systems (e.g. Honeywell EBI)• Redundant network and Call Stations linksComputer Management Station (PAMMI)Decentralized | 7STADIUMS AIRPORTS SHOPPING MALLS RAILWAY STATIONSCUSTOMISED CONTROLThe PAMMI (Public Announcement Man Machine Interface) software provides monitoring and control of the Honeywell Voice Alarm System via a graphical user interface on a Microsoft Windows® based personal computer.PERFECT SYMBIOSIS VOICE ALARM AND FIRE ALARMAREA BY AREA, TARGETED AND ORDERL Y:EVACUATION PROCEDURE EXAMPLE AT THE AIRPORT• There is a short-circuit in the baggage sortingarea on the 1st sub-level,section B of the airport. • The fire detector detects the formation of smokeand transmits theinformation to the firealarm control panel.• The fire alarm system simultaneously initiatesalarms to the securityservices and the voicealarm system.• The security inspectorassesses the situation viathe video camera installedon-site and then activatesa stored a nnouncementto the personnel with thepush of a button.• Due to the increasingformation of smoke,the fire alarm systemautomatically closes thefire door in the affectedarea.Synergies arise through digital coupling of the fire alarm system with the voice alarm system, thus facilitating an orderly, area-specific evacuation during emergencies: If a fire is detected by the connected fire detectors and then received by the fire alarm control panel, this automatically activates the voice alarm system. The endangered areas are then selected automatically and informed via the PA/VA system, while at the same time the fire alarm control panel activates fire protection systems, for example, fire doors, air-conditioning and ventilating systems, elevator controls or smoke dampers.The combination of voice alarm and fire alarm technology not only offers functional advantages, there are economical advantages as well: PA/VA reduces the total EVAC time significantly, a PA/VA system is not much more expensive than standard sounders, while it adds valuable support by increasing productivity of building occupants.8 | | 9VARIODYN D1 AND COMPRIO PA/VA SYSTEM DIAGRAM Thanks to its modular construction and the varioussystem components, the VARIODYN D1 system can easily DCS Digital Call Station DSCF DSC for Firefighter Fire Alarm Control PanelInterfaceDOMAMP PSUDCSF 1/12Configuration via LaptopCD playerETCSDCS PlusCentral Operating Terminal(PAMMI, WINMAG, Honeywell EBI etc)Loop Isolator ModuleAdvanced,Automatic Volume Control10 | WINMAGPLUSONE MANAGEMENT SYSTEM FOR ALLPERFORMANCE FEATURES OF THE VARIODYN D1 INTERFACE WINMAGPLUS DRIVER• System configuration readout of a VARIODYN D1 network to take it over via import files to WINMAGplus application.• Fault and status indication of the VARIODYN D1 system components: • DOM, SCU, DAL bus devices like DCS and • UIM, Amplifiers (each channel)• Audio and control contact inputs and outputsThe WINMAGplus hazard management system lets you create a scalable software solution with superb levels of integration with different sub-systems.In case of Voice Alarm system, VARIODYN D1 is connected via Ethernet/RJ45 to the same network as the WINMAGplus server. This enables the VARIODYN D1 integration with systems such as: fire alarm, fire extinguishing, smoke and heat control, escape routes, CCTV, access control, intrusion detection, emergency lighting as well as BMS and others via open protocols.• Call station function: • Microphone switched to pre-selectable or fixed targets for live-spoken announcements• Playback of pre-recorded announcements onselectable or fixed targets• Display, update and controlof: • Volume• Volume presettings (min., max., alarm)• Audio signal levels • Control contacts | 11Client Ma chinesHazardManagementVideo SystemsIntrusion Detection SystemsAccess ControlPublic Address & Voice AlarmFire AlarmFireExtinguishingFireControlsEmergency LightingBuildingManagement Systems12 | CHALLENGING PROJECTS REQUIRE BEST DESIGN AND EXPERTISEBY CEN/TS 54-32 EUROPEAN STANDARD VA SYSTEM CAN BE DESIGNED IN 2 WAYS TO ACHIEVE REQUIRED INTELLIGIBILITY: 1. Simplified, prescriptive method, requiring loudspeakers mounted every 6 meters or less.2. Detailed method, requiring in practice acoustics simulations as VA system design base regarding spacing, location, type selection, audio equalizing and proper orientation of loudspeakers.Acoustic simulations are paramount for a proper PA/VA system design in complex, tough and large areas. EN 50489 and CEN/TS 54-32 require minimum intelligibility level from installed VA systems. Installing and planning VA systems bears a risk of failure during intelligibily measurements in the handover phase. Toprevent such critical situations and underbudgeting of VA systems acoustic simulations are the only guarantee. |13EXAMPLE OF THE ACOUSTIC SIMULATION OF AN AUDITORIUM Acoustic simulation software provides to precisely and reliably assess sound pressure level (dB) and intelligibility level (STI/CIS). The software calculates the simulatedroom as a space map in 3D, enabling the user to verify the selected type, location and setting of loudspeakers.Voice Alarm system design for acoustically challenging areas must be based on professional, quality simulations,prepared by experienced acoustic experts.Our Technical Support Team provides expertise, experience, tools and wide portfolio of certified VA loudspeakers to assure our partners and system designers that Variodyn D1 system designs will pass acceptance tests.14 | VARIODYN D1 PRODUCT FAMIL YAll of the components of the VARIODYN D1 product family are compatible, interchangeable and optimally adapted to the customers growing needs. As varied as the requirements may be, all of the components are modular designed andcan be combined with each other quick and easy.ComprioComprio is a voice alarm system optimised for small and medium-size facilities such as schools,hotels, leisure centres and offices. It's characterised by its compact design, wide performance range and its flexibility.Digital Output Module (DOM)The Digital Output Module (DOM) is the heart of the Honeywell Voice Alarm and Public Address system. Managing either 8 or 24 zones the DOM routes up to 4 channels of audio from amplifiers to any individual zone or group of zones.Class D Power AmplifiersCombining the latest in digitalaudio technology with the integrity necessary for emergency Voice Alarm systems to satisfy the requirements of EN54 part 16.Direct Drive Power Amplifier4-channel Direct Drive Amplifier 4 x 300 W or 4 x 500 W power outputs or unit providing 4 x 125 W or 4 x 250 W power outputs with integral EN 54-4 certified battery charger.Paging Microphone DCSPlus The paging microphone allows for the selection of loudspeakerzones, and the transmission of voice announcements via programmable buttons.Ethernet Touch Call Station (ETCS)This EN 54-16 certified touch screen call station provides a user friendly, multilingual and multi-user interface support with high failure safety due to redundant transmission routes via Ethernet (PoE possible). It includes audio memory up to 27 hour and a USB stick can be connected to play audio files as well.Universal Interface Module (UIM)Interface module enables audio or control connection to third party systems such as CD players, security systems and other PA/VA or building management control systems.System Communication Unit (SCU)The System Communication Unit (SCU) is an integrated digital audio memory source able to simultaneously record and play back multiple audio data streams.PAMMI PublicAnnouncement User Interface The PAMMI software provides connection and control of the Honeywell Voice Alarm System via a graphical user interface on a Microsoft Windows ® based PC.Emergency Microphones Emergency Microphone used to select and broadcast pre-programmed alarm messages and live voice announcements during emergency situations by security operator or fire brigade commander. | 15LOUDSPEAKERSHoneywell offers loudspeakers, specially designed to meet various requirements and specifications in many project types e.g.Excellent acoustic performance to realize clear, understandable voice announcements or high quality background music.• Cost-effective types• Well designed, modern appearance• Easy for installation to reduce time, efforts and costs • Robust material to offer long lifetime•Models with ceramic terminal block and thermofuseCeiling Loudspeaker• Metal or plastic ceilingloudspeakers• Several power tappings withsimple setting• Partly dual-cone speaker toensure best audio performance • Appropriate for indoorapplications such as offices, warehouses, schools etcHorn Speaker• Clear voice messagereproduction for open and outside areas• Offers a high sound pressureand long-lasting weather resistanceSound Projector• Wide frequency response range,low distortion• Robust aluminum housing • IP65 rating• Best option for applicationssuch as corridors and railway platformsColumn Loudspeaker • Flat, directed soundpropagation, minimized reverberation• Intelligible voice and superiorsound reproduction • IP65 rating• Great choice for theme parks ,exhibition halls and any open, high-volume rooms with high reverberation time.Cabinet Loudspeaker• Simple power setting and easyinstallation• Practicable for wall mountapplication• Plastic, MDF or metal vandal-proof cabinetSpherical Loudspeaker• Where wall mount or ceilingmounting is not possible • Variable hanging height • 360° sound propagationSpecial Loudspeaker for tunnels• Specially designed and EN 54-24certified for tunnel applications • Boundary effect and loudspeakerphasing for best intelligibility inextremely difficult tunnel projectsEXTRACT FROM OUR EXTENSIVE PRODUCT OFFERINGS:00-0000 | DI | 01/ 21© 2021 Honeywell International Inc.Honeywell Building Technologies 715 Peachtree St. NE Atlanta, GA 。
世伟洛克高性能焊头8HPH系列说明书

轨道焊接系统高性能焊头8HPH 系列■ 适应外径范围从 1/8 到 1/2 in. 和 3 到 12 mm■ 台面安装夹具■ 光学速度控制 — 不需要转速计或校准■ 循环寿命:对于直径 1/4 in. 的焊接,平均维护时间间隔 (MTTM) 为焊接 10 000 道焊缝,对于直径 1/2 in. 的焊接,MTTM 为焊接 3000 道焊缝■ 焊接能力:对于 1/4 in. 直径,每小时焊接 60 道焊缝;对于 1/2 in. 直径,每小时焊接 30 道焊缝■ 包含可调的中心规■ 提供集成工作支持系统2 轨道焊接系统—高性能焊头夹具成套件夹具成套件可用于外径为 1/8 到 1/2 in. 和 3 到 12 mm 的尺寸范围。
■ 每个夹具套件包含一个固定板、两个可拆卸板和一个中心规。
■ 每个高性能焊头均随附了一个夹具成套件。
要订购其他夹具成套件,请从下表中选择成套件订购号。
技术数据➀ 基于焊接 1/4 × 0.035 in. 316L 卡套管。
➁ 基于焊接 1/2 × 0.049 in. 316L 卡套管。
高性能焊头 — 8HPH 系列 订购信息高性能焊头世伟洛克® 8HPH 系列高性能焊头配有夹具成套件、工具包、钨棒、12.5 ft 延长电缆线和用户手册。
欲订购世伟洛克 8HPH 系列焊头,请在基本订购号 SWS-8HPH- 中添加一个夹具尺寸代号。
示例:SWS-8HPH-02尺寸尺寸以英寸(毫米)为单位表示,仅供参考,可能有变动。
右侧正面左侧轨道焊接系统—高性能焊头 3附件中心规焊头中心规使操作员可以确保焊接元件在夹具中对中。
根据指定的夹具尺寸,每个高性能焊头均随附了一个中心规。
要订购其他中心规,请从右侧表中选择订购号。
钨电极世伟洛克钨棒可以提供一致、可重复的焊接。
■ 这种钨棒含 2 % 铈钨,轴向接地,符合严格的规范。
■ 钨棒要与氩气保护气体一起使用。
其他保护气体混合物可能需要使用钨棒头部直径为 0.012 in. (0.30 mm) 以外的尺寸。
奥马尔-281997D自动暗晕焊电 helmet产品说明说明书

TABLE OF CONTENTS...... SECTION 1 − WELDING HELMET SAFETY PRECAUTIONS −READ BEFORE USING1.............................................................1-1.Symbol Usage1.......................................................1-2.Arc Welding Hazards1 1-3.Proposition 65 Warnings2.....................................................................................................1-4.Lens Shade Selection T able3..................................................1-5.Principal Safety Standards3..................................................... SECTION 2 − SPECIFICATIONS4.......................................... SECTION 3 − OPERATING INSTRUCTIONS5...........................................................3-1.Helmet Controls5.......................................................3-2.Low Battery Indicator5.........................................................3-3.Lens Delay Control6 3-4.Variable Shade Control (No. 9–13)6......................................................................................................3-5.Sensitivity Control7 3-6.Weld/Grind Mode Switch8.................................................................................................................3-7.Power Modes8.............................................. SECTION 4 − ADJUSTING HEADGEAR9 SECTION 5 − REPLACING THE LENS COVERS10...................................................................................5-1.Replacing Outside Lens Cover10................................................5-2.Replacing Inside Lens Cover11.......................................... SECTION 6 − REPLACING THE BATTERY12.......................... SECTION 7 − INSTALLING OPTIONAL MAGNIFYING LENS13...................................... SECTION 8 − MAINTENANCE AND STORAGE13................................................ SECTION 9 − TROUBLESHOOTING14....................................................... SECTION 10 − PARTS LIST15............................................... SECTION 11 − LIMITED WARRANTY16OM-281997 Page 1SECTION 1 − WELDING HELMET SAFETY PRECAUTIONS −READ BEFORE USINGProtect yourself and others from injury — read, follow, and save these important safetyprecautions and operating instructions.This group of symbols means Warning! Watch Out! ELECTRIC SHOCK, MOVING PARTS,and HOT PARTS hazards. Consult symbols and related instructions below for necessary actions to avoid the hazards..Indicates special instructions.DANGER! − Indicates a hazardous situation which, if not avoided, will result in death or serious injury. The possible hazards are shown in the adjoining symbols or explained inthe text.Indicates a hazardous situation which, if not avoided, could result in death or serious injury. The possible hazards are shown in the adjoiningsymbols or explained in the text.NOTICE − Indicates statements not related topersonal injury.Only qualified persons should install, operate, maintain, and repair this equipment. A qualified person is defined as one who, by possession of a recognized degree, certificate,or professional standing, or who by extensive knowledge, training and experience, has successfully demonstrated ability to solve or resolve problems relating to the subject matter, the work, or the project and has received safety training to recognize and avoid the hazards involved.D Wear a welding helmet fitted with a proper shade of filter to protect your face and eyes when welding or watching (see ANSI Z49.1 and Z87.1 listed in Safety Standards). Refer to Lens Shade Selection table in Section 1-4.D Wear approved safety glasses with side shields under your helmet.D Use protective screens or barriers to protect others from flash, glare, and sparks; warn others not to watch the arc.D Wear body protection made from durable, flame −resistant material (leather, heavy cotton,wool). Body protection includes oil-free clothing such as leather gloves, heavy shirt, cuffless trousers, high shoes, and a cap.•Before welding, adjust the auto-darkening lens sensitivity setting to meet the application.•Stop welding immediately if the auto-darkening lens does not darken when the arc is struck.OM-281997 Page 2D Use helmet for welding/cutting applications only. Do not use helmet for laser welding/cutting.D Use impact resistant safety spectacles or goggles and ear protection at all times when using this welding helmet.D Do not use this helmet while working with or around explosives or corrosive liquids.D This helmet is not rated for overhead welding. Do not weld in the direct overhead position while using this helmet unless additional precautions are taken to protect yourself from arc rays, spatter, and other hazards.D Inspect the auto-lens frequently. Immediately replace any scratched, cracked, or pitted cover lenses or auto-lenses.D Lens and retention components must be installed as instructed in this manual to ensurecompliance with ANSI Z87.1 protection standards.D Use only genuine replacement parts from the manufacturer.D Perform installation, maintenance, and service according to the Owner’s Manuals, industrystandards, and national, state, and local codes.D Ventilate the work area and/or use local forced ventilation at the arc to remove welding fumes and gases. The recommended way to determine adequate ventilation is to sample for the com-position and quantity of fumes and gases to which personnel are exposed.D If ventilation is poor, wear an approved air-supplied respirator.D Read and understand the Safety Data Sheets (SDSs) and the manufacturer’s instructions for adhesives, coatings, cleaners, consumables, coolants, degreasers, fluxes, and metals.D Work in a confined space only if it is well ventilated, or while wearing an air-supplied respirator.Always have a trained watchperson nearby. Welding fumes and gases can displace air and lower the oxygen level causing injury or death. Be sure the breathing air is safe.D Do not weld in locations near degreasing, cleaning, or spraying operations. The heat and rays of the arc can react with vapors to form highly toxic and irritating gases.D Do not weld on coated metals, such as galvanized, lead, or cadmium plated steel, unless the coating is removed from the weld area, the area is well ventilated, and while wearing an air-supplied respirator. The coatings and any metals containing these elements can give off toxic fumes if welded.WARNING: Cancer and Reproductive Harm − www.P65W OM-281997 Page 3ProcessElectrode Size in. (mm)Arc Currentin AmperesMinimum Protective Shade No.Suggested Shade No.(Comfort)*Shielded Metal Arc Welding (SMAW)Less than 3/32 (2.4)3/32−5/32 (2.4−4.0)5/32−1/4 (4.0−6.4)More than 1/4 (6.4)Less than 6060−160160−250250−550781011−−101214Gas Metal Arc Welding (GMAW)Flux Cored Arc Welding (FCAW)Less than 6060−160160−250250−5007101010−−111214Gas Tungsten Arc Welding (TIG)Less than 5050−150150−5008810101214Air CarbonArc Cutting (CAC-A)Light HeavyLess than 500500−100010111214Plasma Arc Cutting (PAC)Less than 2020−4040−6060−8080−300300−400400−80045688910456891214Plasma Arc Welding(PAW)Less than 2020−100100−400400−8006810116−8101214Reference: ANSI Z49.1:2012*Start with a shade that is too dark to see the weld zone. Then, go to a lighter shade which gives a sufficient view of the weld zone without going below the minimum.Safety in Welding, Cutting, and Allied Processes, ANSI Standard Z49.1, is available as a free down-load from the American Welding Society at or purchased from Global Engineering Documents (phone: 1-877-413-5184, website: www ).Safe Practice For Occupational And Educational Eye And Face Protection, ANSI Standard Z87.1,from American National Standards Institute, 25 West 43rd Street, New York, NY 10036 (phone:212-642-4900, website: ).Industrial Head Protection, ANSI/ISEA Standard Z89.1, from American National Standards Institute,25 West 43rd Street, New York, NY 10036 (phone: 212-642-4900, website: ).SECTION 2 − SPECIFICATIONSViewing Field 3.94 x 2.36 in. (100 x 60 mm)Reaction Time0.00004 sec (1/25,000 sec)Available Shades Darkened State: No. 9–13/Light State: No. 3Provides Continuous UV And IR Protection (DIN 15) Grind Mode YesSensitivity Control Lo-Hi Adjustment For Varying Ambient Light AndWelding ArcDelay Control Min-Max Adjustment Slows Lens Dark-T o-Light StateBetween 0.1 And 0.9 SecondsPower Auto-On/Auto-OffLow Battery Indicator Red LED Light Illuminates T o Indicate 2−3 DaysRemaining Battery LifePower Supply Solar Cell And Two Replaceable CR2450 LithiumBatteriesSensors Independent/Redundant (Four)Operating T emperature14_F to 149_F / −10_C to +65_C.When stored in extremely cold temperatures, warmhelmet to ambient temperature before welding.T otal Weight19.7 oz (560 g)Standards ANSI Z87.1-2015, CE EN379, CSA Z94.3-15 Warranty Two Years From Date Of Purchase (see Section 11) NotesOM-281997 Page 4SECTION 3 − OPERATING INSTRUCTIONS3-1.Helmet Controls3-2.Low Battery IndicatorOM-281997 Page 53-4.Variable Shade Control (No. 9–13)OM-281997 Page 6Recommended Sensitivity SettingsStick Electrode Mid-RangeShort Circuiting (MIG)Low/Mid-RangePulsed And Spray (MIG)Mid-RangeGas Tungsten Arc (TIG)Mid/High-RangePlasma Arc Cutting/Welding Low/Mid-RangeGrinding Place Weld/Grind Mode Switch In Grind PositionOM-281997 Page 73-6.Weld/Grind Mode Switch3-7.Power ModesOM-281997 Page 8SECTION 4 − ADJUSTING HEADGEAROM-281997 Page 9SECTION 5 − REPLACING THE LENS COVERS 5-1.Replacing Outside Lens CoverOM-281997 Page 105-2.Replacing Inside Lens CoverOM-281997 Page 11SECTION 6 − REPLACING THE BATTERYOM-281997 Page 12Do not use solvents or abrasive cleaning detergents to clean the helmet. Do not immerse the lens assembly in water.Keep helmet dry; do not expose helmet to rain or snow. Keep helmet away from fire and other sources of heat.The auto-darkening lens uses sensitive electronics. Do not drop helmet or handle it in a rough man-ner.The helmet requires little maintenance. However, for best performance clean helmet after each use. Using a soft cloth dampened with a mild soap and water solution, wipe the cover lenses clean. Allow to air dry. Occasionally, the filter lens and sensors should be cleaned by gently wiping with a soft, dry cloth.Store helmet in a clean, dry, cool place free of solvent−based vapors. T o prevent battery from losing power, store helmet in helmet bag or in a dark location. Remove battery(s) if helmet will be stored longer than six months.End Of Useful LifeThe welding helmet has no expiration date, and with proper care and maintenance it can provide many years of eye and face protection. The helmet can continue to be used, provided that the helmet shell/shroud is undamaged (no cracks, gaps, or holes) and the lens functions normally (switches from a light state to a dark state.)helm main 2019-05OM-281997 Page 13SECTION 9 −TROUBLESHOOTING Trouble RemedyNot switching – auto-lens stays light and will not darken when welding.Stop welding immediately. If power is on, review the sensitivity recommendations and adjust sensitivity. Make sure helmet is not in Grind mode. Clean lens cover and sensors of any obstructions. Make sure the sensors are facing the arc; angles of 45_ or more may not allow the arc light to reach the sensors.Check batteries and verify they are in good condition and installed properly. Also, check battery surfaces and contacts, and clean if necessary. Check batteries for proper contact and gently adjust contact points if necessary. This is particularly important if the helmet has been dropped.Not Switching – auto-lens stays dark after the weld arc is extinguished, or the auto-lens stays dark when no arc is present.Fine-tune the sensitivity setting by making small adjustments to the control by turning it toward the LO setting. In extreme light conditions, it may be necessary to reduce the surrounding light levels.Sections of the auto-lens are not going dark, distinct lines separate the light and dark areas.Stop welding immediately: The auto-lens may be cracked which can be caused by the impact of dropping the helmet. Weld spatter on the auto lens may also cause cracking. (The lens may need to be replaced; most cracked lenses are not covered by warranty).Switching or Flickering –the auto-lens darkens then lightens while the welding arc is present.Review the sensitivity setting recommendations and increase the sensitivity if possible. Be sure the arc sensors are not being blocked from direct access to the arc light. Check the lens cover for dirt and spatter that may be blocking the arc sensors. Increas-ing Lens Delay slightly may also reduce switching.Inconsistent or lighter auto-lens shading in the dark-state, noticeable on the outside edges and corners.Referred to as an angle of view effect, auto-darkening lenses have an optimum viewing angle. The optimum viewing angle is perpendicular or 90_ to the surface of the auto-lens. When that angle of view varies in the dark-state, welders may notice slightly lighter areas at the outside edges and the corners of the lens. This is normal and does not represent any health or safety hazard. This effect may also be more noticeable in applications where magnifying lenses are used.OM-281997 Page 14SECTION 10 − PARTS LISTFigure 10-1. Inventor Series Auto-Darkening Welding HelmetOM-281997 Page 15OM-281997 Page 16Description Part No.Item No.QuantityFigure 10-1. Inventor Series Auto-Darkening Welding Helmet1770847Headgear 1..........................................................216714Label, Warning, Helmet EN/SP/FR 1.......................................2♦770274Diopter Lens 150X 1................................................♦770276Diopter Lens 200X 1..................................................♦770277Diopter Lens 250X 1..................................................3770846Auto-Darkening Lens 1................................................770284Battery, CR24502......................................................4770883Frame, Lens Replacement 1...........................................5770858Kit, Clear Protective Lens 1............................................♦ OptionalSECTION 11 − LIMITED WARRANTYNotessafely. Read thesafety rules atthe beginningof this manual.Miller Electric Mfg. LLCAn Illinois T ool Works Company1635 West Spencer StreetAppleton, WI 54914 USAPhone: 800-332-3281Visit our website atORIGINAL INSTRUCTIONS − PRINTED IN USA© 2019 Miller Electric Mfg. LLC 2019-01。
Honeywell CPS新一代线缆拉动安全开关说明书

• Safety Products for Machine Safeguarding •1© Honeywell International Inc. - April 2003N e wCPS SeriesCable Pull Safety SwitchFEATURES••2CPS: 2NO/2NC, 1NO/3NC or 4NC contact configurations1CPS: 1NO/1NC, 2NO/2NC, 1NO/3NC or4NC contact configurations• Typical cable span of 76 m (250 ft) in an environment with a temperature changeof ±17°C (±30 °F). Longer spans are possible depending upon temperature change and installation(ref. note on page 6 for more details or Application note - Effect of Temperature on Cable Pull Switch Operation)• Choice of three actuator configurations (2CPS)• Removable contact block version available (2CPS)• Large wiring cavity with straight-through wiring• 24 Vdc or 120 Vac bright, multicluster LED status indicator light available on 2CPS. Single high intensity LED on 1CPS • Gold-plated contacts are standard on 2CPS, available on 1CPS • Die-cast zinc housing• Optional hardware packs availableTYPICAL APPLICATIONS•Long conveyor systems found in warehouses and distribution centers • Conveyor systems having a high amount of vibration• Conveyor systems that experience wide temperature swings• Long conveyor systems where easy through wiring, or highly visible trip status is required•Hose down conditions •Packaging equipment •Assembly linesCPS Series Cable Pull Safety Switches provide a readily accessible emergency stop signal. This is a cost-effective means compared to using multiple emergency stop push-buttons. (Cable Pull Safety Switches are not, however, to be used as a means of personnel safeguarding. They may be used to prevent further injury or damage to equipment when used for emergency stop signaling.)The CPS Series Cable Pull Safety switch is designed to provide emergency stop protection for exposed conveyor and assembly lines. The internal mechanism latches on both slackened cable (push) and pulled cable. This capability also en-hances productivity by eliminating nuisance stops due to variations in temperature,stretch of cable over time, and other application variables.The 1CPS is intended for use in applications where the cable span is 76 m (250 ft)or shorter. It is an economical solution for shorter runs or zone protection typical to automated systems. The 2CPS series is intended for use in very long cable runs of 152 m (500 ft) or shorter, such as long conveyor lines found in warehouses.A line in the midpoint of the cable tension window indicates proper cable tension,providing easy set-up. The direct opening switch contacts are held closed when the actuating cable is under proper tension and the reset knob is set to RUN. When the actuating cable is pulled, slackened or broken, a cam positively opens the NC (Nor-mally Closed) switch contacts. The snap action, trip operation causes the switch contacts to change state and mechanically latch almost simultaneously when the cable is pulled, slackened or broken. The NC switch contacts remain open until the CPS is reset by properly tensioning the cable and manually rotating the reset knob.When the direct opening switch contacts open, the auxiliary contacts also actuate (open contacts close and closed contacts open). The auxiliary contacts are electri-cally isolated from the direct opening switch contacts. These NO (Normally Open)contacts may be used for monitoring or signaling.The CPS complies with: Low Voltage Directive 73/23/EEC, as amended by directive 93/68/EEC; Machinery Directive 98/37/EEC only as the directives relate to the components being used in a safety function; IEC/EN 60947-1; IEC/EN 60947-5-1;IEC/EN 60947-5-5.BG(Applied for)2• Safety Products for Machine Safeguarding •© Honeywell International Inc. - April 20031CPSCable Pull Safety SwitchTechnical DataMechanical 1 000 000 operationslife Degree of IP 67protection NEMA 1, 4, 12, 13Temperature Operating:range-25 °C to +80 °C /-13 °F to +176 °F without condensation ApprovalsIEC/EN 60947-1IEC/EN 60947-5-1IEC/EN 60947-5-5AC15 A300DC13 Q300UL & CSA BG Applied for Vibration 10 Hz - 500 Hz, 5 g Shock 15 gContact Silver standard material Gold plated optional Included NoneaccessoriesConduit ThreadContact closed A Left switch B Right switch C Slackened cable D Proper cable tension E Pulled cableF Cable tension = 111 N (25 lb)G Cable tension = 133 N (30 lb)H Cable tension = 178 N (40 lb)IGround screw• Safety Products for Machine Safeguarding •3© Honeywell International Inc. - April 20034• Safety Products for Machine Safeguarding •© Honeywell International Inc. - April 20032CPSCable Pull Safety SwitchTechnical DataMechanical 1 000 000 operations life Degree of IP 67protection NEMA 1, 4, 12, 13Temperature Operating:range-40 °C to +80 °C /-40 °F to +176 °F without condensation ApprovalsIEC/EN 60947-1IEC/EN 60947-5-1IEC/EN 60947-5-5AC15 A300DC13 Q300UL & CSA BGVibration 10 Hz - 500 Hz, 5 g Shock 15 g Contact Gold plate material over silver Included Turnbuckle(s)accessoriesContact blocks mounted to housing• Safety Products for Machine Safeguarding •5© Honeywell International Inc. - April 20036• Safety Products for Machine Safeguarding • © Honeywell International Inc. - April 2003Temperature-Span Distance Application InformationCable Pull Switches featuring broken cable detection require pre-tensioning in order to enable the RUN condition.The relative expansion or contraction of the steel actuating cable when the ambient temperature increases or decreases must be taken into account when pre-tensioning a cable pull switch.The change in cable length with change in temperature can cause significant nuisance shut downs on longer runs.Install the system when the temperature is at the mid point of the extremes. If a warehouse has a low temperature of 15,6 °C (60 °F) and a high of 32,2 °C (90 °F), set up the system at the midpoint 23,9 °C (75 °F).Use an endspring or another CPS at the opposite end of the cable span to double the temperature tolerance and to meet the requirements of EN 418.0 m [0 ft]0 ˚C [0 ˚F]22,9 m [75 ft]45,7 m [150 ft]114,3 m [375 ft]228,6 m [750 ft]-27,8 ˚C [-50 ˚F]+27,8 ˚C [+50 ˚F]76,2 m [250 ft]+16,7 ˚C [+30 ˚F]+8,3 ˚C [+15 ˚F]-16,7 ˚C [-30 ˚F]-8,3 ˚C [-15 ˚F]137,2 m [450 ft]160,0 m [525 ft]205,7 m [675 ft]68,8 m [225 ft]182,9 m [600 ft]A =Total temperature variationB =Setup point - Ideally at middle of temperature extremesC =Cable Pull Switch usable temperature span without endspring or second CPSD =Cable Pull Switch usable temperature span with endspring or second CPSE =Cable span distance• Safety Products for Machine Safeguarding •7© Honeywell International Inc. - April 2003Application information1CPS8• Safety Products for Machine Safeguarding • © Honeywell International Inc. - April 2003Hardware packets (available separately)ListingAccessoryCLSZC1Cable - 7,6 m (25 ft) length CLSZC2Cable - 15,2 m (50 ft) length CLSZC3Cable - 30,5 m (100 ft) length CLSZC4Cable - 45,7 m (150 ft) length CLSZC5Cable - 61 m (200 ft) length CLSZC7Cable - 76,2 m (250 ft) length CLSZTC (2) Thimbles(2) Low-profile Duplex Cable ClampsCPSZ1S (1) Draw-bar EndspringCPSZK1(1) J-hook Turnbuckle with Lock Nuts (2) Thimbles(2) Low-profile Duplex Cable Clamps(16) Sets of Cable Supports ((16) 1/4-20 Eye Bolts, (32) 1/4-20 Nuts,(32) Flat Washers, (16) Lock Washers)CPSLED24Multicluster LED Accessory - 24 Vdc (conduit mount)CPSLED120Multicluster LED Accessory - 120 Vdc (conduit mount)CPS-BRACKET Mounting bracket (to be used with 1CPS or 2CPS)CPSZTBJ-hook turnbuckle with lock nuts (included with 2CPS)CPSLEDA Multi-LED red pilot lightB 1/2-14 NPom ThreadC 18 AWG red PVC insulation D18 AWG black PVC insulationCPS-BRACKET• Safety Products for Machine Safeguarding •9© Honeywell International Inc. - April 2003Mounting dimensions (mm/in)1CPS2CPSWarranty and remedyHoneywell warrants goods of its manufacture as being free of defective materials and faulty workmanship. Contact your local sales office for war-ranty information. If warranted goods are returned to Honeywell during the period of coverage, Honeywell will repair or replace without charge those items it finds defective. The foregoing is Buyer ’s sole remedy and is in lieu of all other warranties, expressed or implied, including those of merchantability and fitness for a particular purpose.While we provide application assistance, personally, through our literature and the Honeywell web site, it is up to the customer to determine thesuitability of the product in the application.HoneywellNewhouse Industrial Estate Motherwell ML1 5SBLanarkshire, Scotland, U.K.Honeywell21 Chemin du Vieux Chêne 38240 Meylan Cedex FranceThis publication does not constitute a contract between Honeywell and its customers. The contents may be changed at any time without notice. It is the customer's responsibility to ensure safe installation and operation of the products. Detailed mounting drawings of all products illustrated are available on request. © 2003 Honeywell International Inc. All rights reserved.Specifications may change at any time without notice. The information we supply is believed to be accurate and reliable as of this printing. However,we assume no responsibility for its use.Sales and ServiceHoneywell serves its customers through a worldwide network of sales offices and distributors. For application assistance,current specifications,pricing or name of the nearest Authorised Distributor, contact a nearby sales office or:INTERNET: /sensing E-mail:*********************/sensingASIA PACIFICControl Products Asia Pacific HeadquartersPhone: +(65) 6355-2828FAX: +(65) 6445-3033AustraliaHoneywell LimitedPhone: +(61) 2-9370-4500FAX: +(61) 2-9370-4525Toll Free 1300-36-39-36Toll Free Fax 1300-36-04-70China - PRC - Beijing Honeywell (Tianjin) Ltd.Phone: +(86-10) 8458-3280FAX: +(86-10) 8458-3102China - PRC - Shanghai Honeywell China Inc.Phone: +(86-21) 6237-0237FAX: +(86-21) 6237-1237China - Hong Kong SAR Honeywell Ltd.Phone: +(852) 2953-6412FAX: +(852) 2953-6767IndiaTata Honeywell LtdPhone: +(91) 20 687 0445/0446FAX: +(91) 20 681 2243/687 5992IndonesiaHoneywell Indonesia Pte Ltd Phone: +(62-21) 535-8833FAX: +(62-21) 5367 1008JapanHoneywell IncPhone: +(81) 3 5440 1425FAX: +(81) 3 5440 1368South KoreaHoneywell Korea Co. Ltd Phone: +(822) 799-6167FAX: +(822) 792-9013MalaysiaHoneywell Engineering Sdn Bdh Phone: +(60-3) 7958-4988FAX: +(60-3) 7958-8922New Zealand Honeywell LimitedPhone: +(64-9) 623-5050FAX: +(64-9) 623-5060Toll Free (0800) 202-088PhilippinesHoneywell Systems (Philippines) Inc.Phone: +(63-2) 636-1661/1662FAX: +(63-2) 638-4013SingaporeHoneywell South East Asia Phone: +(65) 6355-2828FAX: +(65) 6445-3033Taiwan R.O.C.Honeywell Taiwan Ltd.Phone: +(886-2) 2245-1000FAX: +(886-2) 2245 3242ThailandHoneywell Systems Ltd.Phone: +(662) 693 3099FAX: +(662) 693 3085NORTH AMERICA CanadaHoneywell LTDPhone: 1-800-737-3360FAX: 1-800-565-4130USAControl Products,International Headquarters Phone:1-800-537-69451-815-235-6847FAX: 1-815-235-6545E-mail:*********************EUROPEAustriaHoneywell Austria GmbHPhone: +(43) 1 727 80 366/246FAX: +(43) 1 727 80 337BelgiumHoneywell SA/NVPhone: +(32) 2 728 2522FAX: +(32) 2 728 2502BulgariaHoneywell EOODPhone: +(359) 2 79 40 27FAX: +(359) 2 79 40 90RomaniaHoneywell Bucharest Phone: +(40) 1 2110076FAX: +(40) 1 2103375Commonwealth of Indepen-dent States (CIS )ZAO HoneywellPhone: +(7 095) 796 98 36FAX: +(7 095) 796 98 93Slovak Republic Honeywell s.r.o.Phone: +(421 7) 58247403/400FAX: +(421 7) 58247 415South Africa (Republic of)Honeywell Southern Africa Honeywell S.A. Pty. Ltd Phone: +(27) 11 695 8000FAX +(27) 11 805 1504SpainHoneywell S.A.Phone: +(34) 91 313 6100FAX: +(34) 91 313 6129Sweden Honeywell ABPhone: +(46) 8 775 55 00FAX: +(46) 8 775 56 00Switzerland Honeywell AGPhone: +(41) 1 855 24 40FAX: +(41) 1 855 24 45TurkeyHoneywell Turkey A.S.Phone: +(90) 216 575 6620FAX: +(90) 216 575 6637United KingdomHoneywell Control Systems Ltd Phone: +(44) 1698 481 481FAX: +(44) 1698 481 276Mediterranean & African Distributors Honeywell SpAPhone: +(39) 2 921 46 232FAX: +(39) 2 921 46 233Middle East Headquarters Honeywell Middle East Ltd.Phone: +(9712) 443 2119FAX +(9712) 443 2536Czech Republic Honeywell spol. s.r.o.Phone:+(420) 2 6112 3469/3424FAX: +(420) 2 6112 3461Denmark Honeywell A/SPhone: +(45) 39 55 55 55FAX: +(45) 39 55 55 58Finland Honeywell OYPhone: +(358) 9 3480101FAX: +(358) 9 34801375FranceHoneywell SAPhone: +(33) 1 60 19 80 40FAX: +(33) 1 60 19 81 73Germany Honeywell AGPhone: +(49) 69 8064 444FAX: +(49) 69 8064 442HungaryHoneywell Kft.Phone: +(36 1) 451 4300FAX: +(36 1) 451 4343ItalyHoneywell S.p.A.Phone: +(39) 02 92146 450/456FAX: +(39) 02 92146 490The Netherlands Honeywell B.V.Phone: +(31) 20 565 69 11FAX: +(31) 20 565 66 00NorwayHoneywell A/SPhone: +(47) 66 76 20 00FAX: +(47) 66 76 20 90PolandHoneywell Sp. zo.oPhone: +(48) 22 606 0900FAX: +(48) 22 606 0901PortugalHoneywell Portugal LdaPhone: +(351 21) 424 50 00FAX: +(351 21) 424 50 99LATIN AMERICAArgentinaHoneywell S.A.I.C.Phone: +(54-11) 4383-3637FAX: +(54-11) 4325-6470BrazilHoneywell do Brasil & Cia Phone: +(55-11) 7266 1900FAX: +(55-11) 7266 1905ChileHoneywell Chile, S.A.Phone: +(56-2) 233-0688FAX: +(56-2) 231-6679ColumbiaHoneywell Columbia, S.A.Phone: +(57-1) 623-3239/3051FAX: +(57-1) 623-3395EcuadorHoneywell S.A.Phone: +(593-2) 981-560/1FAX: +(593-2) 981-562MexicoHoneywell S.A. de C.V.Phone: +(52) 55 5259-1966FAX: +(52) 55 5570-2985PeruHoneywell PeruPhone: +(511) 445-2136-1891FAX: +(511) 348-3552Puerto Rico Honeywell Inc.Phone: +(809) 792-7075FAX: +(809) 792-0053TrinidadHoneywell Inc.Phone: +(868) 624-3964FAX: +(868) 624-3969Venezuela Honeywell CAPhone: +(58-2) 238-0211FAX: +(58-2) 238-3391Honeywell11 West Spring Street Freeport, Illinois 61032USA107122-02-EN FR26 GLO 403 Printed in France。
赫伐利顿制造公司 Lighting Management Systems 产品说明书

Leviton Mfg. co., Inc. Lighting Management Systems20497 SW Teton Avenue, Portland, OR 97062 1-800-736-6682 Tech Line: 1-800-959-6004 Fax: 503-404-5594 /lms© 2008 Leviton Manufacturing Co., Inc. All rights reserved. Subject to change without notice.FeatureS• Local creation of new presets with the integral scene master set up/preset storage control feature• Direct Manual or preset recall control allows for an infinite selection of different lighting looks• Simple, powerful local preset storage and recall of 4 or 8 scenes with programmable fade times when used with an i Series e or i Series Quad dimmer rack• Virtually limitless DIMMER channel capacity • Multiple stations may be installed allowing control from several locations• Control stations can act independently of each other, together or as a group • Take control feature• Selectable emergency power up mode feature - Preset 1 active or all off active when power is applied to control station • Selectable multiple record mode lockout • Discrete digital control of 4 or 8 presets and/ or multiple overlapping submaster scenes • Direct integration capability withRemembrance Analog and Digital Control Stations and i Series e control electronicsNormal Loads1-Alpha 1898/12& Belden 9829Control Cable120 VAC i Series e or i Series Quad Dimmer RackAlpha 1898/8to Remote Analog StationsNormal PowerAlpha 1898/12to Remote Preset StationsInnovator Consoleremembrance dMX512r e m e m b r a n c e d M X 512 d i g i t a l p r e s e t c o n t r o l S t a t i o nHeight4.50 [11.43]4.50 [11.43]4.50 [11.43]product dataLeviton Manufacturing co., Inc. Lighting Management Systems20497 SW Teton Avenue, Portland, OR 97062Telephone: 1-800-736-6682 • FAX: 503-404-5594 • Tech Line (6:00AM-4:00PM P.S.T. Monday-Friday): 1-800-959-6004Leviton Manufacturing of canada, Ltd.165 Hymus Boulevard, Pointe Claire, Quebec H9R 1E9 • Telephone: 1-800-469-7890 • FAX: 1-800-563-1853Leviton S. de r.L. de c.V.Lago Tana 43, Mexico DF, Mexico CP 11290 • Tel. (+52) 55-5082-1040 • FAX: (+52) 5386-1797 • .mxVisit our Website at: /lms© 2008 Leviton Manufacturing Co., Inc. All rights reserved. Subject to change without notice.MecHanIcaL• The control faceplate shall be constructed of formed steel painted white.• Silkscreen legends on faceplate shall be black. Preset and Manual selection buttons shall be black with green LED indicators. Off preset button shall contain a bi-colored LED for indicating various operating modes. Channel sliders shall have graduated silkscreen scales fitted with professional grade fader knobs.• The 4 slider with master control station and presets is 12” wide by 4-1/2” tall. The station mounts in a NEMA 6 gang 3-12/” deep back box. Contact the factory for recommended back box suppliers.• The 8 slider with master control station and presets is 15-5/8” wide by 4-12/” tall. The station mounts in a NEMA 8 gang 3-1/2” deep back box. Contact the factory for recommended back box suppliers.eLectrIcaL• push buttons. Control station shall contain 4 or 8 presetbuttons with an integral green LED, and a separate OFF button with an integral bi-colored LED. Manual push button shall be distinctively different to distinguish between manual and preset modes. Control Stations can be wired to act independently of each other, or together as a group.• Slide controllers. Control stations shall contain 4 or 8 slider channels with a master. All potentiometers shall have at least a 2” travel and shall be capable of providing live, instantaneous control of the associated dimmers. The channel fader shall have the capacity of operating as an overlapping submaster for all dimmers within the control system. Channel sliders must be configured by a DMX512 control source.• Wiring. The control station requires power from a 10VAC @ 5V A transformer. The control station requires a DMX512 con-trol signal into the station. The 4 preset control station wiring requires an Alpha 1898/8 or equivalent and a Belden 9829 or equivalent connected between the i Series e or i Series Quad dimmer racks and the control station. The 8 preset controlstation wiring requires an Alpha 1898/12 or equivalent and a Belden 9829 or equivalent connected between the i Series e or the i Series Quad dimmer racks and the control station.operatIonaL• recall. The Control Station shall have the ability to activate a timed preset, manually mix a scene, or enable both simultane-ously at the press of a single button. The corresponding LED on the button will illuminate.• Slider record. Sliders shall be configured by capturing the DMX512 control signal into the unit. When enabled, the capture sequence is activated by pressing and holding the manual button in the ON mode with all sliders down for at least five seconds, then sliding up the master and channel slider up where the scene is to be stored. The manual button must be pressed throughout the record sequence and held for an additional 3 seconds after the sliders have been raised. Slider record mode may be de-activated independently of the preset record mode. When active, slider scenes pile onto or generate a DMX512 signal. Slider scenes are stored in non-volatile memory.• preset record. When connected to an i Series e or i Series Quad, the control station shall have the ability to store active DMX scene simply by pressing and holding the OFF button until the active scene lighting levels dip by 50%, and then while still holding the OFF button, pressing the preset button where the scene is to be stored. Preset record may be de-activated independently of slider record mode. Presets shall be stored in non-volatile memory.• capacity. The control station shall have the ability to control a virtually limitless number of dimmer channels when used in conjunction with i Series e or i Series Quad, or Remembrance Control Stations.• record Lockout. The control station can be configured to disable slider record mode, preset record mode, or both simultaneously.• power up State. The control station can be configured to active Preset 1 on power up, or activate OFF on power up.512G-7933/B8-ak。
俄罗斯防电弧服的市场准入标准

这些市场准入标准可能由俄罗斯相关机构或行业协会制定和发布。供应商应该了解并遵守 适用的标准,并确保其产品符合相关要求。为了获得更具体和最新的信息,建议与俄罗斯的 认证机构、行业协会或当地的法规机构进行联系和咨询。
3. 材料和构造:防电弧服的材料和构造应该能够提供良。
俄罗斯防电弧服的市场准入标准
4. 尺寸和适配性:防电弧服应该适合穿戴者的身材,并提供足够的舒适性和灵活性。市场 准入标准可能对尺寸范围、调整方式和人体工程学要求等进行规定。
俄罗斯防电弧服的市场准入标准
俄罗斯防电弧服的市场准入标准可能涉及以下方面:
1. 防火性能:防电弧服必须符合俄罗斯相关标准对防火性能的要求。这包括材料的阻燃性 能、耐热性能、耐磨性能等。
2. 电弧等级:防电弧服应该能够提供足够的保护,以抵御不同电弧等级下的热能辐射和热 传导。俄罗斯可能有特定的电弧等级要求,供应商需要确保其产品符合这些要求。
- 1、下载文档前请自行甄别文档内容的完整性,平台不提供额外的编辑、内容补充、找答案等附加服务。
- 2、"仅部分预览"的文档,不可在线预览部分如存在完整性等问题,可反馈申请退款(可完整预览的文档不适用该条件!)。
- 3、如文档侵犯您的权益,请联系客服反馈,我们会尽快为您处理(人工客服工作时间:9:00-18:30)。
Salisbury 8cal防电弧服技术信息
产品描述:
Salisbury防电弧服采用永久阻燃面料;面料融合Lenzing FR®与Taparan®/Tametan®芳纶科技: (1) 面料绿色环保部分可降解,无污染;(2) 面料永久阻燃,无熔融、滴落,不支持燃烧,阻燃防护性能不会因为水洗(超过100次)或使用而降低和消失;(3) 面料柔软、透气排汗性能优异,可贴皮肤穿着,舒适不过敏;(4) 面料具有良好的耐磨性,抗撕裂/断裂性能优异;(5) 水洗超过100次,不缩水、不退色,防护性能优异。
产品技术性能:
服装的热防护性能(服装面料克重:270g/m2)
∙服装面料电弧热防护性能值ATPV超过8cal/cm2
∙服装面料破裂阈能E BT超过20 cal/cm2
服装阻燃及耐高温性能
∙续燃时间:无续燃,无熔融滴落现象
∙损毁长度:水洗前经/纬向小于80mm;水洗100次之后经/纬向小于85mm(标准要求小于150mm)
∙面料高温稳定性:经纬向小于3%(标准要求小于10%)
∙缝纫线:均采用进口阻燃的缝纫线,耐260o C高温
∙纽扣:阻燃耐高温纽扣,耐260o C高温
∙拉链:进口黑色YKK树脂耐高温拉链,耐260o C高温
服装物理性能
∙服装面料耐磨性能:达到ASTM3884标准3级要求,无破损
∙服装面料断裂强力:经纬向大于800N(标准要求大于450N)
∙服装面料撕裂强力:经向大于80N,纬向大于50N(标准要求经纬向大于40N)∙服装面料水洗尺寸稳定性:经向收缩率小于3.5%,纬向收缩率小于1.5%(标准要求小于5%)
∙服装面料水洗色牢度:4-5级
∙服装面料耐水洗次数:超过100次
产品设计与款式
∙上身:夹克设计;下身:罩裤设计。
所有面料均采用纯天然的、永久阻燃纤维素纤维的制成
∙所有辅件(纽扣、拉链、缝纫线),均使用阻燃耐高温材料
∙上衣胸口暗袋、下方反插口袋设计,手臂上方工具袋设计
∙电网、卡数刺绣设计可选
其他
∙尺码:S,M,L,XL,XXL
∙颜色:卡其色(另有藏青、宝蓝、灰色可选)
∙符合标准:DL/T 320-2010
∙认证检测机构:苏州热工研究院
附表:8cal电弧服尺码对照表。