基于CNC齿轮测量中心的圆柱蜗杆测量研究
圆柱齿轮精度的综合检测及数据处理
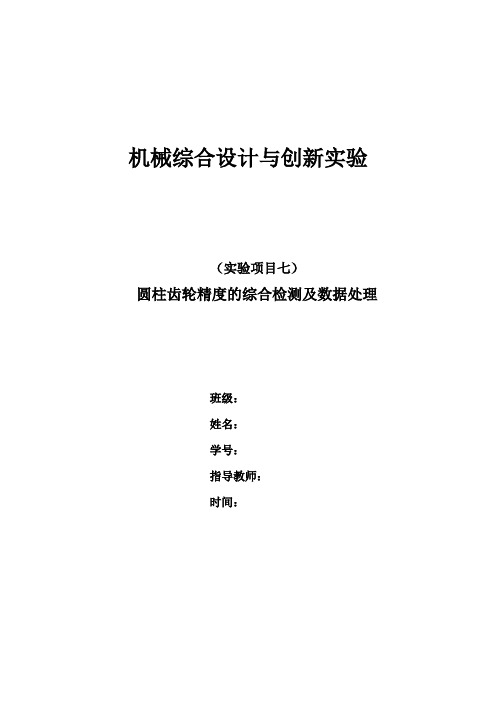
机械综合设计与创新实验(实验项目七)圆柱齿轮精度的综合检测及数据处理班级:姓名:学号:指导教师:时间:实验七圆柱齿轮精度的综合检测及数据处理一、实验意义齿轮是用来传递运动或动力的,从传递运动出发,应保证传递运动准确、平稳;从传递动力出发,则应保证传动可靠(承载能力大)和灵活(不发卡、效率高),因此,其使用要求可以归纳为以下四个方面:1.传递运动的准确性传递运动的准确性是指齿轮在一转范围内,速度变化不超过一定的限度,可用齿轮一转过程中产生的最大转角误差ΔφΣ来表示。
对齿轮的此项精度要求,称为运动精度。
2.传动的平稳性传动的平稳性是指齿轮在转一齿范围内,瞬时传动比变化不超过一定的限度。
这一变化将会引起冲击,振动和噪声,它可以用转一齿过程中的最大转角误差Δφ表示。
对齿轮的此项精度要求称为平稳性精度。
3.载荷分布的均匀性载荷分布的均匀性是要求一对齿轮啮合时,工作齿面要保证一定的接触面积,从而避免应力集中,减少齿面磨损,提高齿面强度和寿命,这一项要求可用沿轮齿齿长和齿高方向保证一定的接触区域来表示,对齿轮的此项精度要求称为接触精度。
4.齿侧间隙的合理性齿侧间隙的合理性是指一对齿轮在啮合时,在非工作齿面间存在的间隙。
这是为了使齿轮传动灵活,用以贮存润滑油、补偿齿轮的制造与安装误差以及热变形等所需的侧隙。
二、实验目的“圆柱齿轮精度的综合检测及数据处理实验课”是基于研究生对齿轮精度设计及检测内容在本科学习阶段未涉及到的背景下开设的,系统阐述齿轮精度设计和实验技术,同时加强理论和实践相结合。
通过本次实验,提高学生对齿轮精度设计所涉及到的相关理论知识以及齿轮精度检测的基本方法和相关仪器、量具的使用方法,进一步强化对理论知识的理解,提高我们的实际动手能力和分析、解决问题的能力,以适应工程实际的需要。
三、实验仪器、设备及材料1.齿轮齿距检测仪;2.双面啮合齿轮综合检测仪;3.公法线千分尺;4.齿轮齿厚游标卡尺;5.齿轮径向跳动检测仪。
互换性与技术测量-圆柱齿轮传动公差及检测
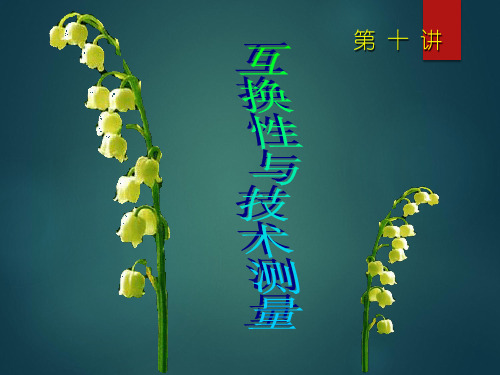
第一章回顾
1.2 公差与配合的基本术语及定义
基本尺寸&极限尺寸&最大实体尺寸&最小实体尺寸 正确理解这些概念 偏差&公差&公差带&基本偏差 能够画公差带 基孔制&基轴制 间隙配合&过盈配合&过渡配合 考点
1.3 公差与配合国家标准
计算标准公差等级的公差值或能够查表获得 轴、孔基本偏差的分布规律 计算规则及方法
高速动力齿轮用于传递大的动力,要求传动平稳,噪声及振动 小,同时对齿面接触也有较高的要求。对这类齿轮首先应根据 圆周速度以及噪声强度的要求确定第II公差组的精度等级,再 确定其它公差组精度等级。
低速动力齿轮其特点是传递功率大,速度低。主要要求是齿面 接触良好,而对运动的准确性和传动平稳性要求不高,对这类 齿轮首先根据强度和寿命要求确定第III公差组的精度等级,其 次再选择第I、II公差组的精度。
公差组 公差与极限偏差项目
对传动性能的主要影响
I F’i,Fp,Fpk,F”i,Fr,Fw
传递运动的准确性
注意:当孔直径加工成最大
实体尺寸时,轴线直线 度公差为0.01mm,当 孔直径为最小实体尺寸 时,轴线直线度公差也 为0.01mm。
3.4.2 相关原则
2 最大实体要求
注意:标识方法为在其相应的形位 公差框格内加注 M 。
要求其实际轮廓处处不能超越最大实体实效边界,当其实际尺寸偏 离最大实体尺寸时,允许其形位误差值超过图样上给定的公差值, 但要素的局部实际尺寸应界于最大实体尺寸和最小实体尺寸之间。
)2 2 lim xn
第三章回顾
3.1 概述
理想要素&实际要素&单一要素&关联要素
齿轮测量中心测量立柱的结构优化设计

齿轮测量中心测量立柱的结构优化设计摘要:齿轮测量中心的测量速度快、测量精度高,而且通过一次装夹即可自动测量完成齿轮的全部参数,是当代齿轮、齿轮刀具等回转零件测量设备的发展方向。
当前,我国齿轮测量设备在测量可靠性、测量稳定性和测量精度等方面同世界先进水平相比还有很多不足,这主要是因为对齿轮测量中心的结构优化不足。
本文选取了齿轮测量中心测量立柱的三维结构模型,并使用ANSYS软件,采用基于参数优化设计和拓扑优化设计方法对测量立柱的结构形式以及尺寸进行优化设计,从而使测量立柱获得较好的刚度/质量比,有助于提高测量中心的测量精度和测量稳定性。
关键词:齿轮测量中心;测量立柱;优化设计;拓扑优化引言齿轮测量设备的发展已经经历了将近一百年的时间,随着国民经济的快速发展和科学技术的进步,对齿轮测量技术和测量设备提出了越来越高的要求,因而出现了具有多种测量功能的齿轮测量中心。
然而,由于齿轮测量中心测头的真正位置和各个坐标轴光栅读数头的测量位置存在不重合的问题,使得每个坐标轴光栅读数头所测数值与测头的实际位移存在一些误差,这部分误差主要是机械结构弹性变形和刚体运动学误差共同导致的。
齿轮测量中心在结构上一般采用立式主轴形式,采用自下而上的结构方式按序排列切向(Y轴)、轴向(Z轴)和径向(X轴)三个直线导轨。
若测量立柱的刚度不足,将直接影响轴向和径向两个方向的测量精度。
1 测量立柱的拓扑优化设计为在保证刚度的前提下减少测量立柱的重量,获得较好的刚度/质量比,对测量立柱进行拓扑优化设计,该优化设计的主要目标是获得减重结构优化的基本形状,从而减少结构静力变形,并提高零件的固有频率。
1.1 材料参数设置、网格划分和约束条件设置测量立柱的材料为灰铸铁,材料的弹性模量设置为1.38×1011Pa,密度设置为7280kg/m3,泊松比设置为0.3。
在进行拓扑优化分析模型的建立时,单元类型选择SOLID95,测量立柱三边的外壁结构不需要进行拓扑优化,划分网格时使用单元类型2,中间区域需要进行拓扑优化使用单元类型1。
虚拟CNC的齿轮测量中心

Ke r s i u lme srme t iu le up n ;c mp tr e u rclc nrl NC) e rmes r gma hn y wo d :vr a aue n ;vr a q ime t o uei dn meia o t (C t t z o ;ga a ui c ie n
关键 词 : 虚拟测 量 ; 虚拟仪 器 ; 计算机 数 字控制 ; 齿轮 测 量 中心
中图分类号 : P 9 . T 3 19 文 献标 识码 : A 文章 编号 :01 45(070 02 — 3 10 — 5 120 )4— 03 0
Vi t lCNC - e r m e urng m ac ne r ua G a as i hi
Ab ta t h e eo me to rdt n lCNC Germe s r gma hn ( NC GMM)w sit d cd,an w cn e t sr c :T ed v lp n fta io a i — a au i c ie VC — n a nr u e o e o cp—
维普资讯
第2 4卷 第 4期
20 0 7年 4 月
机
电
工
程
Vo . 4 No 4 12 .
Ap .20 r 07
M ECH ANI CAL & ELECTRI CAL ENGI NEERI NG AGAZI M NE
虚拟 C C的齿轮测量 中心 N
虚拟 C C齿 轮测 量 中心是 传 统 的 C C齿 轮 测 N N 量 中心的机 械结 构 、 件 性 能 以及 测 量 过程 等 在 虚 工
拟环 境 中的映射 , 可 以针 对顾 客 的需 求进 行最 它 优化 的设计 , 不仅 能节 约产 品的设 计成 本 , 而且产 品 的设计 成 型时 间很快 , 主要 的特 点 是 它能 及 时 准 最 确地 根据用 户 的需 求更 改产 品 。 本 研究 介绍 虚 拟 C C齿 轮 测 量 中心 的体 系 设 N 计, 以及虚 拟 C C齿 轮 测 量 中心 的几 何 建 模( 安 工 业 大 学 机 电 工程 学 院 , 西 西 安 70 3 ) 西 陕 10 2
CNC齿轮测量中心总体设计和软件设计

图1 ·3 6 ·
分组成 (数控系统及计算机软件略) 。机械部分由切 向 ( T 轴) ③、轴向 ( Z 轴) ④和径向 ( R 轴) ⑤三个方 向的直线导轨和一个回转主轴 (θ轴) ②组成 。四个 坐标轴分别由各自的伺服电机驱动 ,通过数控系统 实现四轴联动 。三个直线导轨上分别装有长光栅 , 主轴上同轴安装有一个圆光栅 ,用来实时测量各轴 的位置 。工件安装在主轴上 ,随主轴一起转动 。测 头 (微位移传感器) ⑥安装在 R 轴滑台上 。
71 在规程的征求意见的过程中 , 有的人反映 “首次检定”“、后续检定”“、使用中检验”的概念不清
楚 。现解释如下 : 首次检定的目的是为了确定新生产的计量器具
其计量性能 ,是否符合其批准时规定的要求 。 后续检定的目的是为了确定计量器具自上次检
定 ,并在有效期内使用后 ,其计量性能是否符合所规 定的要求 。后续检定包括有效期内的检定 、周期检 定以及修理后的检定 。经安装及修理后对计量器具 计量性能有重大影响时 ,其后续检定原则上须按首 次检定进行 。
31 软件结构图 (程序代码略) CNC 齿 轮 测 量 中 心 的 软 件 开 发 采 用 面 向 对 象的 VC + + 程序设 计 语 言 , 软 件 结 构 如 图 3 所 示 。 硬件输入输出接口模块的功能是与数控系统通
讯 ,基本控制与信号处理模块库包含了运动控制 、数 据采集 、各种滤波算法 、动态补偿及设备状态的监测 与控制等模块 ,由各种测量模块调用 。其中部分功 能已经做成标准函数向用户开放 ,用户可根据需要 自行编写专用测量程序 。针对齿轮测量中心大小规 格的不同 ,测量功能的增减等硬件配置的变化 ,由硬 件配置文件来存放相应的技术参数 。测量模块作成 标准的程序模板 ,根据不同被测工件的要求 ,设计人 机界面和测量控制程序 。
CNC齿轮测量中心(开题报告)任时雨1

毕业设计(论文)开题报告题目:CNC齿轮测量机造型与结构设计院(系)机电工程学院专业工业设计班级110221姓名任时雨学号110221116导师王冠伟2015年3月15日图1.1克林格恩贝格公司CNC 1.2 格莱森公司CNC齿轮测量机由西安工业大学成功研制了我国第一台CNC齿轮测量中心(CCZ40图2.1.1 方案一图2.2.1 方案二草图方案三:如图2.3.1和2.3.2所示,此套方案吸收医院移动显示设备造型,将摆放显示器和打印机的桌子设计为一个移动支架,主体测量设备支撑柜为双曲线造型,在上方为测量仪器,线和部件放入钣金柜里,两个柜子用钣金处理方法设计纹理造型。
测量台部件为金属,与白色钣金柜,黑色大理石台,以及分型处黑色处理,形成科技感的视觉感。
例如:见图,图2.3.1 方案三图2.3.2方案三草图方案四:如图2.4.1和2.4.2所示,此套方案主要着重设备一体化设计。
在钣金支撑图2.4.1 方案四图2.4.2 方案四草图方案五:如图2.5,此套方案主要着重设备一体化设计。
在钣金支撑柜上连接移动支架,支架上连接显示器和操作手柄。
以黑白两色为主要颜色,底座套上黑色,显得具有科技感。
中部为大理石台设计,底部为钣金储物柜设计,柜子分为有四个空间放入主机、工件和打印设备。
图2.5 方案五本课题研究的重点及难点,前期以开展工作本课题研究的重点及难点产品设计要与机械装置的使用功能相结合。
才能做到结构功能合理,产品符合人们审美要求;要发现使用时和日常保养过程中产生的问题,需要对产品有一定的研究和熟悉产品结构;)要结合产品所处的工作环境来设计;)对建模软件的熟练掌握与运用。
前期开展的工作注:1、正文:宋体小四号字,行距22磅。
2、开题报告装订入毕业设计(论文)附件册。
阐述蜗杆参数的测量及应用

阐述蜗杆参数的测量及应用一、前言蜗杆和蜗轮作为蜗轮箱的关键零件,其加工和装配精度直接影响到蜗轮箱的工作性能。
蜗轮箱在平地机上是用于驱动工作装置回转,以达到调整刀板在水平面上的角度。
当平地机工作时刀板会受到地面的冲击,地面产生的冲击力将传递至蜗轮箱,由于蜗轮和蜗杆的自锁特性会使蜗轮和蜗杆承受较大冲击力,从而容易出现蜗杆等零件损坏。
因此,研发及质量部门对其加工和测量均有较高的要求。
二、测量方法目前我公司蜗轮箱产品所使用蜗杆是最常用的阿基米德圆柱蜗杆(ZA型),在生产过程中需要对其参数进行精确测量。
为了准确地测量蜗杆压力角、齿厚以及跳动等参数,检验人员曾经实验了多种的测量方法,在测量过程中使用了包括卡板、厚度卡尺、万能角度尺、偏摆仪、影像仪以及三坐标测量机等测量工具。
经过反复的测试和分析比对,最终确定利用三坐标测量机,通过编写测量程序实现了对蜗杆参数的测量。
2.1卡板法该测量方法分为两种:即多齿法和单齿法,用相应角度的齿形卡板进行直接测量,测量时可通过肉眼观察卡板测量面与齿面接触的光隙情况,作出简单的定性判断。
由于受导程角及卡板自身结构等的影响,经现场试测,其中多齿法测量基本不可靠;单齿法,对于不同的测量位置,可观察到的光隙情况也不稳定,仅能用于现场简单控制,其应用意义不大。
2.2卡尺法该方法通过使用万能角度尺及测厚卡尺等实现对压力角和齿厚的测量。
测量压力角时,使用万能角度尺的一边顺着轴截面与蜗杆面接触,保持刀口尺与齿面紧密贴合。
由于受蜗杆的导程角及曲面等因素的影响,其测量结果不稳定。
用齿厚卡尺测量蜗杆法向齿厚时,首先根据图纸要求调整卡尺的测量高度,然后用测厚卡尺在蜗杆的齿顶圆柱上沿轴向分别测量单齿和相邻两齿的长度,单齿的长度即为齿厚,再用相邻两齿轮的长度减去单齿的长度可得到齿距。
为了精确测量,建议多测几个齿,将所测得的数据计算平均值。
2.3影像法该方法通过使用影像仪将蜗杆的齿面轮廓、外圆柱边缘进行投影,利用测量软件计算出轮廓投影线与外圆柱边缘投影线的夹角,同时通过软件将轴线按分度圆半径值平行偏移构造一条虚线,该虚线与各齿的齿廓投影线相交,计算单齿两侧相交点的距离即为齿厚,进一步再计算出齿厚。
基于CNC齿轮测量中心的环面蜗杆测量研究的开题报告

基于CNC齿轮测量中心的环面蜗杆测量研究的开题报告一、选题背景与意义环面蜗杆作为一种传动装置,其在机械设备中应用非常广泛。
而环面蜗杆的制造精度对于整个机械设备的精度和稳定性都有着非常重要的影响。
因此,如何对环面蜗杆的制造精度进行可靠的测量和评估,成为了当前机械制造领域亟待解决的难题。
目前,国内外对于环面蜗杆的制造精度进行测量和评估的方法主要有以下几种:激光干涉法、光测量法、三坐标测量法以及CNC齿轮测量中心测量法等。
其中,CNC齿轮测量中心测量法具有操作简便、测量精度高、测量范围广等优点,已经成为一种广泛应用的环面蜗杆测量方法。
然而,在实际应用中,CNC齿轮测量中心测量法对于环面蜗杆的测量存在着一些问题。
例如,测量结果会受到夹持装置的影响、测量数据的处理和分析需要高水平的专业知识等。
因此,如何进一步完善和优化CNC齿轮测量中心的测量方法,提高其测量精度和可靠性,成为研究的重要内容之一。
二、研究目的和内容本研究旨在通过分析环面蜗杆传动特点和制造工艺,建立相应的数学模型,设计并制造出适用于CNC齿轮测量中心的环面蜗杆测量夹具,优化测量方法和数据处理技术,提高CNC齿轮测量中心的测量精度和可靠性。
具体内容包括:1.环面蜗杆的制造工艺及其测量要求分析;2.建立适用于CNC齿轮测量中心的环面蜗杆测量数学模型;3.设计和制造适用于CNC齿轮测量中心的环面蜗杆测量夹具,优化夹持方式;4.基于CNC齿轮测量中心的环面蜗杆测量方法及数据处理技术的优化;5.实验验证和结果分析。
三、研究方法和技术路线本研究采用理论分析和实验研究相结合的方法,具体技术路线如下:1.对环面蜗杆的制造工艺及其测量要求进行分析和研究;2.基于环面蜗杆的传动特点和制造工艺,建立适用于CNC齿轮测量中心的环面蜗杆测量数学模型;3.设计并制造出适用于CNC齿轮测量中心的环面蜗杆测量夹具,优化夹持方式;4.基于CNC齿轮测量中心的环面蜗杆测量方法及数据处理技术进行优化;5.利用实验验证所提出的优化测量方法和数据处理技术,对测量精度和可靠性进行分析和评价。
圆柱齿轮传动的精度与检测

圆柱齿轮传动的精度与检测
单个齿距精度的检测,通常用两种装置,一种是有
两个触头的齿距比较仪,另一种是只有一个触头的角度
分度仪。
由于
,所以也可用基圆齿距偏差做检测
项目。基圆齿距偏差是在沿基圆切平面上测量,因而与
齿轮轴线无关。
(1)切向综合偏差(Fi——非必检项目) 被测齿轮与测量齿轮单面啮合时,被测齿轮一转内,
齿轮分度圆上实际圆周位移与理论圆周位移的最大差值。
圆柱齿轮传动的精度与检测
圆柱齿轮传动的精度与检测
(2)齿距累积偏差(Fpk—必检项目)和齿距累积 总偏差(Fp—必检项目)
①齿距累积偏差:是指端平面上,在接近齿高中 部的一个与齿轮轴线同心的圆上,任意k个齿距的实际 弧长与理论弧长的代数差。 理论上它等于这k个齿距的 各单个齿距偏差的代数和。
a: Fpk在不大于1/8的圆周上平定; b: 通常k = z/8。 ② 齿距累积总偏差:是指齿轮同侧齿面任意弧段 内的最大齿距累积总偏差。它表现为齿距累积偏差曲线
圆柱齿轮传动的精度与检测
总值。
圆柱齿轮传动的精度与检测
圆柱齿轮传动的精度与检测
圆柱齿轮传动的精度与检测
(3)径向综合总偏差Fi” 径向综合总偏差是在径向综合检验时,产品齿轮的
1 中心距极限偏差±fa 2 轴线平行度偏差 和
与 的最大推荐值为
式中,L为轴承跨距,b为齿宽。
圆柱齿轮传动的精度与检测
圆柱齿轮传动的精度与检测
圆柱齿轮传动的精度与检测
3 接触斑点
圆柱齿轮传动的精度与检测
11.3.2 齿轮坯
圆柱齿轮传动的精度与检测
圆柱齿轮公差及检测公差与技术测量
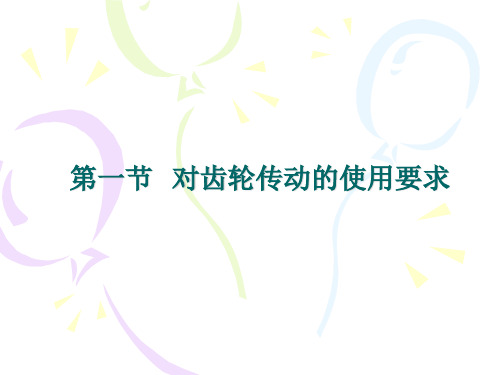
3、一齿切向综合误差Δfi´ 1)、定义:被测齿轮与理想精确的测量齿轮作 单面啮合时, 在被测齿轮一个齿距角内,它的 实际转角与理论转角之差的最大幅度值。
2)、特点:接近齿轮实际工作状态,故是评定 传动平稳性较为完善的综合误差项目,(包括 了径向、切向误差)
小结
齿轮传动的使用要求 影响使用要求的误差(或因素)
传递运动的准确性 传动的平稳性 载荷分布的均匀性
长周期误差:包括几何偏心和运动偏心分别引起 的径向和切向长周期(一转)误差。两种偏心同 时存在,可能叠加,也可能抵消。这类误差用齿 轮上的长周期偏差作为评定指标
短周期(一齿)误差:包括齿轮加工过程中的刀 具误差、机床传动链的短周期误差。这类误差用 齿轮上的短周期偏差作为评定指标
•误差评定项目和测量:
1、螺旋线偏差:实际螺旋线对理论螺旋线 的偏离量。影响齿宽方向载荷分布均匀 性。
2、齿廓偏差:影响齿高方向载荷分布均匀 性。
以上这两种偏差通常是由齿坯轴线歪斜、 机床刀架导轨误差等引起的。这类误差用轮齿 同侧齿面轴向偏差来评定
四、影响传动侧隙的误差
影响侧隙大小和侧隙不均匀的主要误差是齿厚偏差及 齿厚的变动量。
W 之差。
二、精度等级的选择:
首先,根据用途确定主要公差组的等级,然 后其它。
根据使用要求不同,各公差组可选不同的等 级,当选不同级时,其公差等级之差不能 超过一个等级,但同一公差组内各项公差 精度应相同。
三、图样上齿轮精度等级的标注 7 GB/T 10095.1
8(Fp、fpt、Fα)、7(Fβ)GB/T 10095.1
第二节 齿轮上影响四项使用要求的主要误差
CNC齿轮测量中心三维测头电路设计

CNC齿轮测量中心三维测头电路设计作者:申涛等来源:《价值工程》2012年第27期摘要:本文针对CNC齿轮测量中心,设计了一种基于USB总线的三维测头数据采集电路。
采用AD698设计了差动变压器(LVDT)传感检测电路,设计了信号调理电路,采用AD7982设计了信号A/D转换电路。
设计了ADC接口电路,中央处理电路和USB接口电路。
所设计电路以数字方式传输检测结果,能有效提高测量电路的稳定性和可靠性。
Abstract: A new three—dimensional probe data acquisition circuit is designed for CNC gear measuring center. Sensing circuit of Linear Variable Differential Transformer (LVDT) is designed based on AD698. Signal conditioning circuit and A/D transfer circuit based on AD7982 are designed. ADC interface circuit, central processing circuit and USB interface circuit also are designed. The new circuit send measuring result with digital data, thus the stability and reliability of the system are improved greatly.关键词:三维测头;差动变压器;信号调理;USB接口Key words: 3D probe;Differential Transformer;Signal Conditioning;USB interface中图分类号:TG86 文献标识码:A 文章编号:1006—4311(2012)27—0017—030 引言CNC齿轮测量中心不同于普通的三坐标测量机,它对动态测量的速度和精度要求更高,需要对电感侧头三路信号进行同步采集,测头是CNC齿轮测量中心的关键部件之一,它的精度直接影响测量中心的测量精度[1],测头的数据采样速率也是影响测量中心的速度的主要因素。
圆柱齿轮的测量

实验四圆柱齿轮的测量一、实验目的1、了解齿轮各项误差的含义、评定及其对齿轮传动性能的影响。
2、了解各种齿轮测量仪器的工作原理及其使用方法。
3、熟悉齿轮精度标准。
二、实验要求1、齿轮齿距偏差△f pt和齿距累积误差△f p的测量。
2、齿圈径向跳动的△F r测量。
3、齿轮公法线长度变动量△F w和公法线平均长度偏差△E wm的测量。
三、轮齿距偏差△f pt和齿距累积误差△f p的测量齿距偏差△f pt是指分度圆上实际齿距与公称齿距之差。
用相对量法测量时,以被测齿轮所有实际齿距的平均值作为公称齿距。
齿距累积误差△f p是指任意两同测齿廓在分度园上的实际弧长与公称弧长的最大差值(取绝对值)。
测量齿距误差的方法有绝对量法和相对量法。
对中等模数的齿轮多采用相对量法。
相对量法是在被测齿轮分度园附近的圆周上,任意取两相邻之间的实际齿距作为基准,在依次量出其余各齿距相对此基准齿距的偏差(齿距相对偏差),通过数据处理得到△f pt和△f p。
用于相对测量的常用仪器有齿距仪和万能测齿仪。
本实验采用万能测齿仪。
在万能测齿仪上测量周节的工作原理见图8—1。
被测齿轮装于心轴上,安放在仪器上下顶针之间(图中未画出顶针),在仪器的测量托架上装有与指示表图8—1万能测齿仪4相连的活动量头1合固定量头2,被测齿轮在重锤和牵引线作用下,使齿面与测量头接触进行测量。
测量前先选定任一齿距作基准,调节测量托架和固定量头2的位置,使活动量头1和固定量头2沿齿轮径向大致位于分度圆附近,将指示表4调零。
测完一齿厚,将测量托架沿径向退出,使齿轮转过一齿后再进入齿间,直到测完一周回复到基准齿距,此时指示表的指针仍应在零位。
注意:由于重锤的作用,当每次将测量托架退出时,药用首府主持轮,以免损坏测量头。
测量数据的处理。
测量数据处理有计算法和作图法两种。
现以测量模数为3mm ,齿数为12的齿轮为例说明如下:1、 计算法计算法一般均采用列表计算。
首先将实测的一系列齿距相对偏差△f pt 相对值列于表第一行(见表1),然后进行计算。
齿轮测量中心

归纳起来,应用要求可分为传动精度和齿侧间隙两个方面。
而传动精度要求按齿轮传动的作用特点,又可以分为传递运动的准确性、传递运动的平稳性和载荷分布的均匀性三个方面。
可见,齿轮转过一转的范围内,从动轮产生的最大转角误差反映齿轮副传动比变动量,即反映齿轮传动的准确性·测试与控制·收稿日期:2009-07-20作者简介:陈涛(1985-),男,陕西西安人,硕士研究生。
CNC齿轮测量中心机械结构研究陈涛,李平,王建华,赵文涛(西安工业大学机电工程学院,陕西西安710032)0引言CNC齿轮测量中心是上世纪80年代国际上迅速发展起来的机电结合的高技术量仪。
它集先进的计算机技术、微电子技术、精密机械制造技术、高精度传感技术、信息处理技术与精密测量理论于一体[1]。
CNC齿轮测量中心不限于测量齿轮,还可以测量复杂刀具、蜗轮、蜗杆、涡轮、曲轴等各种复杂工件,同时解决了许多用传统方法无法检测的技术难题。
它将代替品种繁杂的传统的齿轮检测仪器,成为检测领域的主导设备。
1总体布局的特点CNC齿轮测量中心实质上是含有一个回转角坐标的四坐标测量机———圆柱坐标测量机[2],其工作原理就是计算机根据被测工件的参数控制各坐标轴运动,使测头相对于被测工件产生所要求的测量运动,在测头沿工件表面运动的过程中,计算机不断采集测微仪的示值及同一时刻各坐标轴的实际位置,这些数据记录了被测型面的实际形状,由计算机完成与理论型面的比较,从而得出测量结果。
齿轮测量中心有两种结构布局,一种是卧式结构,一种是立式结构[3]。
一般考虑到除了测量齿轮外还可能测量其它类型的工件,故采用立式结构。
考虑到要采用的测量方法需要R、T、Z、θ四轴联动进行测量,一般测量中心由底座、测量平台、直线导轨、主轴、测头以及上顶尖柱等部分组成。
测量平台安装在底座上,其台面为设计调整的基准面,一般为了提高测量的精度床身选择大理石材质。
如图1(a)所示,比较典型的结构边缘为T向导轨;Z向导轨安装在T向滑块之上;R向导轨安装在Z向滑块之上;T向、R向、Z向滑块分别可沿其导轨运动;测头安装在R向滑块上。
蜗轮蜗杆的测绘

蜗杆传动用于交错轴间传递运动及动力,通常,交错轴Σ=90°,它的主要优点:传动比大,工作较平稳,噪声低,结构紧凑,可以自锁。
主要缺点:少头数的蜗杆传动效率较低,常需要贵重的减摩有色金属。
由于圆柱蜗杆工艺性好,尤其是阿基米德圆柱蜗杆,因此获得广泛应用。
蜗杆传动用于交错轴间传递运动及动力,通常,交错轴Σ=90°,它的主要优点:传动比大,工作较平稳,噪声低,结构紧凑,可以自锁。
主要缺点:少头数的蜗杆传动效率较低,常需要贵重的减摩有色金属。
由于圆柱蜗杆工艺性好,尤其是阿基米德圆柱蜗杆,因此获得广泛应用。
齿形标准(1)基准齿廓普通圆柱蜗杆的基准齿廓是指基准蜗杆在给定截面上的规定齿廓,见图9-24。
在蜗杆的轴平面内基准齿廓的尺寸参数(摘自GB10087-88)为: 1)齿顶高h a=m,工作齿高h''=2m,采用短齿时,h a=0.8m,h '=1.6m;2)轴向齿距p x=πm,中线上的齿厚等于齿槽:3)顶隙c=0.2m,必要时可减少到0.15m或增大到0.35m;4)齿顶可倒圆,圆角半径不大于0.2m。
5)齿顶可倒圆,圆角半径不大于0.2m。
(2)基准蜗杆的齿形角α1)阿基米德蜗杆,轴向齿形角α x=20°;2)法向直廓蜗杆,法向齿形角α n=20°;3)渐开线蜗杆,法向齿形角α n=20°;4)在动力传动中,当到成角γ》30°时,可增大齿形角,推荐用25°;在分度机构中,允许减小齿形角,推荐采用15°或12°。
蜗杆草图蜗轮草图主要几何参数蜗杆传动的主要参数为:模数m,齿形角α,蜗杆分度圆直径d1,蜗杆导程角γ,蜗杆头数z1,蜗轮齿数z2,中心距a等。
蜗杆头数z1、蜗轮齿数z2、蜗杆齿顶圆直径da1、蜗轮外圆直径de2的测量跟直齿圆柱齿轮一样,这里就不详术。
(1)模数m 在圆柱蜗杆传动中,规定通过蜗杆轴线并与蜗轮轴线垂直的中间平面作为基准平面,在该平面内,蜗轮在蜗杆传动相当于齿轮条传动,即蜗轮相当于齿轮,蜗杆相当于齿条。
齿轮及蜗轮蜗杆的测绘方法

齿轮及蜗轮蜗杆的测绘齿轮和蜗轮蜗杆结构较为复杂,因而此类零件的测绘较一般常见零件更为繁琐,是一项细致的工作。
本章主要讨论我国最常用的标准直齿圆柱齿轮、标准斜齿圆柱齿轮和标准直齿圆锥齿轮以及蜗轮蜗杆的功用与结构、测绘步骤、几何参数的测量和基本参数的确定等内容。
1 齿轮测绘概述1.1 齿轮的功用与结构齿轮是组成机器的重要传动零件,其主要功用是通过平键或花键和轴类零件连接起来形成一体,再和另一个或多个齿轮相啮合,将动力和运动从一根轴上传递到另一根轴上。
齿轮是回转零件,其结构特点是直径一般大于长度,通常由外圆柱面(圆锥面)、内孔、键槽(花键槽)、轮齿、齿槽及阶梯端面等组成,根据结构形式的不同,齿轮上常常还有轮缘、轮毂、腹板、孔板、轮辐等结构。
按结构不同齿轮可分为实心式、腹板式、孔板式、轮辐式等多种型式,如果齿轮和轴做在一起,则形成齿轮轴。
按轮齿齿形和分布形式不同,齿轮又有多种型式,常用的标准齿轮可分为直齿圆柱齿轮、斜齿圆柱齿轮、圆锥齿轮等。
1.2 齿轮的测绘步骤齿轮测绘是机械零部件测绘的重要组成部分,测绘前,首先要了解被测齿轮的应用场合、负荷大小、速度高低、润滑方式、材料与热处理工艺和齿面强化工艺等。
因为齿轮是配对使用的,因而配对齿轮要同时测量。
特别是当测绘的齿轮严重损坏时,一些参数无法直接测量得到,需要根据其啮合中心距a和齿数z,重新设计齿形及相关参数,从这个意义上讲,齿轮测绘也是齿轮设计。
齿轮测绘主要是根据齿轮及齿轮副实物进行几何要素的测量,如齿数z,齿顶圆直径da,齿根圆直径df、齿全高h、公法线长度W k、中心距a、齿宽b、分度圆弦齿厚s及固定弦齿厚sc、齿轮副法向侧隙n及螺旋角β、分锥角δ、锥距R等,经过计算和分析,推测出原设计的基本参数,如模数m、齿形角α、齿顶高系数h a*、顶隙系数C*等,并据此计算出齿轮的几何尺寸,如齿顶圆直径d a、分度圆直径d及齿根圆直径d f等,齿轮的其它部分结构尺寸按一般测绘原则进行,以达到准确地恢复齿轮原设计的目的。
- 1、下载文档前请自行甄别文档内容的完整性,平台不提供额外的编辑、内容补充、找答案等附加服务。
- 2、"仅部分预览"的文档,不可在线预览部分如存在完整性等问题,可反馈申请退款(可完整预览的文档不适用该条件!)。
- 3、如文档侵犯您的权益,请联系客服反馈,我们会尽快为您处理(人工客服工作时间:9:00-18:30)。
1)基于盘状锥面砂轮磨削加工ZK蜗杆的原理,推导了ZK蜗杆的齿廓方程,研究了ZK蜗杆轴截面齿廓的求解算法,并得到了离散化的数学模型。
2)研究了在JD系列齿轮测量中心上ZK蜗杆的测量技术。重点论述了齿廓测量的原理及其测头标定、测量运动控制、测头半径补偿等关键问题,开发了相应的蜗杆测量软件。
本文的研究实现了在齿轮测量中心上测量ZK蜗杆及其蜗轮滚刀。
测量实践表明:ZK蜗杆及其蜗轮滚刀的测量原理是可行的,已开发的测量软件运行稳定可靠。
本文链接:/Thesis_Y1676209.aspx
授权使用:黄小强(wfxadz),授权号:6e021217-ca9a-4f5f-949b-9e9a01212317
3)深入研究了ZK蜗杆的齿廓测量误差,建立了该误差的数学模型,分析了蜗杆基本参数(模数、头数和分度圆直径)对测量误差的影响规律。
4)研究了在JD系列齿轮测量中心上ZK蜗轮滚刀的测量技术。介绍了螺旋线误差和刃口齿廓误差的测量原理,分析了刃口识别、测量运动控制、误差评值等关键问题,开发了相应的滚刀测量软件。
下载时间:2011年3月2日
天津大学
硕士学位论文
基于CNC齿轮测量中心的圆柱蜗杆测量研究专业:测试计量技术及仪器
指导教师:刘书桂
20090601
基于CNC齿轮测量中心的圆柱蜗杆测量研究
作者:李俊峰
学位授予单位:天津大学
1.学位论文籍庆校ZK蜗杆及其蜗轮滚刀测量技术研究2009
蜗杆传动是机电设备中常见的一种机械传动形式,属于齿轮传动的范畴,具有传动比大、结构紧凑、工作平稳等特点,在一定条件下也具自锁性。与ZA、ZI、ZN圆柱蜗杆相比,ZK蜗杆在任意截面上的齿廓都是曲线,属于非线性曲纹蜗杆,其测量一直是个难题。