尾轴镗孔工艺
镗孔技术
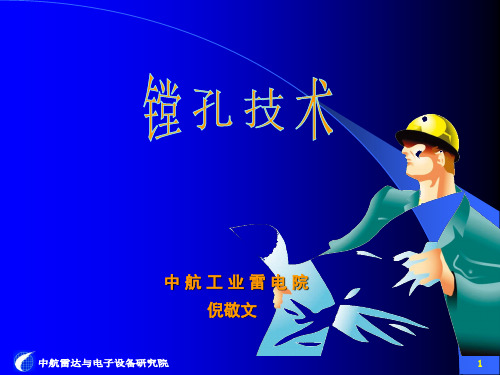
11
四、镗孔步骤及注意事项
镗刀安装
安装镗刀工作部是非常重要 的,特别是针对采用偏心原 理的工作调整,安装镗孔刀 后一定要注意观察镗刀的主 刀刃上平面,是否与镗刀头 的进给方向在同一水平面上? 安装在同一水平面上才能保 证几个切屑刃是在正常的加 工切削角度。
注意:检查刀片安装时导向槽贴合及后刀面高度检查
28
六、镗削加工影响因素
卧加悬伸镗孔
卧加悬伸镗孔采用主轴送进镗 削时,镗刀杆随主轴送进而不断悬 伸,刀杆系统因自重变化产生的绕 度不同,在加工较长内孔时,加工 孔的轴线易产生弯曲;由于悬伸长 度不断增加,刀杆系统的刚性不断 变差,在切削力的作用下,系统弹 性变形逐渐增大,影响镗孔精度, 使被加工孔的表面质量和圆柱度产 生偏差。 合理降低切削速度(转速及进给量)
5
二、镗孔概述
镗孔加工标准
加工精度高。 精镗孔的尺寸精度可达IT8 ~IT7,可将孔径控制 在0.01MM精度以内。若为精细镗孔,加工的精度可达 IT7 ~ IT6; 表面质量好。 一般的镗孔,表面精糙度Ra值1.6 ~ 0.8μm。若为 精细镗孔,表面粗糙度值为Ra0.4 ~ 0.05μm。 孔位纠偏。
七、镗孔量具使用方法
测微量具原理
主标尺标定为0.5mm测 量精度范围
主标尺
微分筒标尺
微分筒标尺标定为 0.005mm~0.5mm测量 精度范围
测微量具主要应用螺旋副传动,将微分筒的转动变为测微螺杆的移 动。一般测微螺杆的螺距为0.5mm,微分同与测微螺杆连成一体, 上刻有50条等分刻线。当微分同旋转一圈时测微螺杆轴向移动 0.5mm;而当微分筒转过一格时测微螺杆轴向移动0.5/50=0.01mm 。
镗孔工艺介绍

3.镗刀
按不同结构,镗刀可分为单刃镗刀和双刃镗刀。
孔的尺寸是由操作者调整镗 刀头位置保证的。
孔的尺寸精度靠镗 刀本身的尺铰工艺相比,孔径尺寸不受刀 具尺寸的限制,且镗孔具有较强的误差修正能力, 可通过多次走刀来修正原孔轴线偏斜误差,而且能 使所镗孔与定位表面保持较高的位置精度。
三、镗孔
镗孔是在预制孔上用切削刀具使之扩 大的一种加工方法,镗孔工作既可以在 镗床上进行,也可以在车床上进行。
1.镗孔方式 镗孔有三种不同的加工方式。
1.镗孔方式 (1)工件旋转,刀具作进给运动
➢工艺特点:加工后孔的轴心线与工件的回转轴线一致,孔 的圆度主要取决于机床主轴回转精度,孔的轴向几何形状误 差主要取决于刀具进给方向相对于工件回转轴线的位置精度。
为3.2~0.8μm。
➢镗孔可以在镗床、车床、铣床等机床上进行,具 有机动灵活的有点。应用十分广泛。 ➢在大批大量生产中,为提高孔效率,常使用镗模。
镗孔和车外圆相比,由于刀杆系统的刚性差、 变形大,散热排屑条件不好,工件和刀具的热变形 比较大,因此,镗孔的加工质量和生产效率都不如 车外圆高。
4.镗孔的工艺特点及应用范围
镗孔的加工范围广,可加工各种不同尺寸和不 同精度等级的孔。 ➢对于孔径较大、尺寸和位置精度要求较高的孔和 孔系,镗孔几乎是唯一的加工方法。 ➢镗孔的加工精度为IT9 ~ IT7级,表面粗糙度Ra
适于加工与外圆表面有同轴度要求的孔。
(2)刀具旋转,工件作进给运动
➢工艺特点:镗杆的悬伸长度L一定,镗杆变形对孔的轴向形 状精度无影响。但工作台进给方向的偏斜会使孔中心线产生 位置误差。镗深孔或离主轴端面较远的孔时,为提高镗杆刚 度和镗孔质量,镗杆由主轴前端锥孔和镗床后立柱上的尾架 孔支承。
镗孔加工工艺介绍

镗孔
镗孔是对锻出,铸出或钻出孔的进一步加工,镗孔可扩大孔径,提高精度,减小表面粗糙度,还可以较好地纠正原来孔轴线的偏斜。
镗孔可以分为粗镗、半精镗和精镗。
精镗孔的尺寸精度可达IT8~IT7,表面粗糙度Ra值1.6~0.8μm。
镗孔分为一般镗孔和深孔镗孔,一般镗孔在普通车床就可以,把镗刀固定在车床尾座或者固定在小刀架上都可以。
深孔镗孔需要专用的深孔钻镗床,镗刀要加上镗秆,还要加上液压泵站利用冷却液把铁屑排除。
一、常用镗刀
1.通孔镗刀镗通孔用的普通镗刀,为减小径向切削分力,以减小刀杆弯曲变形,一般主偏角为45°~75°,常取60°~70°.
2.不通孔镗刀镗台阶孔和不通孔用的镗刀,其主偏角大于90°,一般取95~100°,刀头处宽度应小于孔的半径。
二、镗刀的安装
1.刀杆伸出刀架处的长度应尽可能短,以增加刚性,避免因刀杆弯曲变形,而使孔产生锥形误差。
2.刀尖应略高于工件旋转中心,以减小振动和扎刀现象,防止镗刀下部碰坏孔壁,影响加工精度。
3.刀杆要装正,不能歪斜,以防止刀杆碰坏已加工表面。
镗孔工艺流程及工艺要求
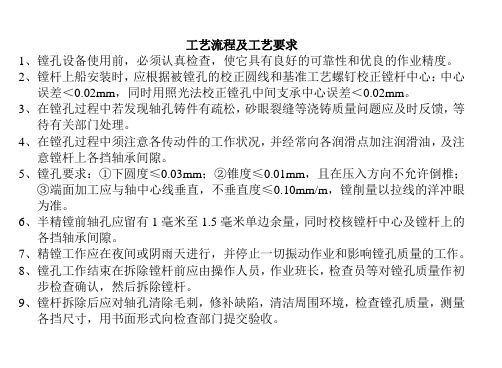
工艺流程及工艺要求
1、镗孔设备使用前,必须认真检查,使它具有良好的可靠性和优良的作业精度。
2、镗杆上船安装时,应根据被镗孔的校正圆线和基准工艺螺钉校正镗杆中心:中心
误差<0.02mm,同时用照光法校正镗孔中间支承中心误差<0.02mm。
3、在镗孔过程中若发现轴孔铸件有疏松,砂眼裂缝等浇铸质量问题应及时反馈,等
待有关部门处理。
4、在镗孔过程中须注意各传动件的工作状况,并经常向各润滑点加注润滑油,及注
意镗杆上各挡轴承间隙。
5、镗孔要求:①下圆度≤0.03mm;②锥度≤0.01mm,且在压入方向不允许倒椎;
③端面加工应与轴中心线垂直,不垂直度≤0.10mm/m,镗削量以拉线的洋冲眼
为准。
6、半精镗前轴孔应留有1毫米至1.5毫米单边余量,同时校核镗杆中心及镗杆上的
各挡轴承间隙。
7、精镗工作应在夜间或阴雨天进行,并停止一切振动作业和影响镗孔质量的工作。
8、镗孔工作结束在拆除镗杆前应由操作人员,作业班长,检查员等对镗孔质量作初
步检查确认,然后拆除镗杆。
9、镗杆拆除后应对轴孔清除毛刺,修补缺陷,清洁周围环境,检查镗孔质量,测量
各挡尺寸,用书面形式向检查部门提交验收。
艉轴管镗孔工艺、流程
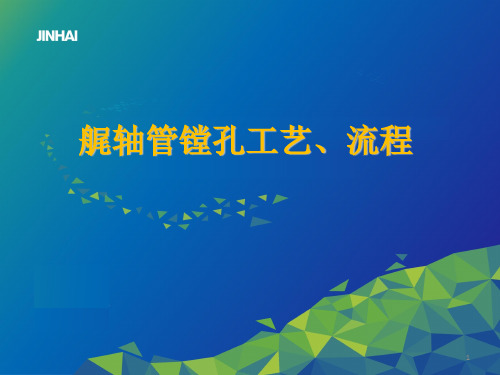
3
4.人员 4.1 操作人员和检验人员应具备专业知识,并经过相关专业培训,考试或考 核取得合格证书,方可上岗操作。 4.2 操作人员和检验人员应熟悉本规范要求并严格遵守工艺纪律和现场安全 操作规程。 5.工艺要求 5.1 镗孔的圆度、圆柱度公差符合表1要求。
10
8.检验流程表
编 号
项目
13 镗排检验 14 按工艺要求搭排 15 校中镗排,确认直线度 16 粗镗孔 17 光刀前同心度检查 18 光刀 19 光刀后同心度检查 20 镗孔后粗糙度检验
≤0.08mm
≤0.08mm 按图纸要求
21 与压配有关的圆角检验(R0.2~0.5)
22 镗孔数据报验(测三次,取平均值)
5
6.3 用照光时预置的基准点(调整螺钉)校直。
7
6.3 镗杆调整后应进行无负荷动车,加注润滑油脂,检查支架各连接点螺 栓松紧情况。 6.4 粗镗加工 6.4.1 依据施工图,将各阶梯孔直径尺寸、长度等全部加工到半精镗前状态, 各阶梯孔应留有1~1.5mm加工余量。 6.4.2 切削深度不大于4mm、进给量0.6mm/r、镗杆转速10r/min;要求粗糙 度达到 。 6.4.3 工作中如发现较大面积砂眼、裂缝等铸件缺陷应及时反馈。 6.4.4 粗加工结束后,通过检验圆复测镗杆中心与轴心的同心度。 6.5 半精镗加工 6.5.1 提高同轴度精度,各档孔径应留有0.5mm加工余量。 6.5.2 切削深度不大于0.80mm、进给量0.30mm/r、镗杆转速10r/min,要 求粗糙度不小于 6.5.3 工作中应在孔径表面喷注由植物油70%和煤油30%组成的混合冷却油。
艉轴管分段预镗孔工艺的应用

\ 6 0 1 P / S 6 0 2 P , S
——J — — —
— — ~
段与 主船 体 H 0 1环 段 、 E 0 2 P / S分 段 及 挂 舵 臂 1 1 1 分段 的焊 接 、 控 制达 到 整 个船 体 总 组 合拢 的精 度 要
求 。在 总段合 拢前需 对各个 区域 的状 态进行 测量 与
标 记 出来 , 留待大 合 拢 时定 位所 用 。整 个 E 0 1总段
调整后 的水平 度控 制在 ± 4 m m, 主机 面板 机 座 水平 度控制 在 ± 2 . 5 m m之 内 。
1 . 2 货舱 区船体 的状态 要 求
测量货 舱 区 H 0 1环 段 与 机 舱 E 0 1总 段 合 拢 口
3 7
基 准靶 所 确 定 的直 线 上 。确 定 B、 C、 D 3个 投 影 靶
肌舱下平 台——T]0 、\ l
\ 3 0 2 P / s /3 O 1 P, S
.
_
.
.
2 1 .
. \
调整 。
5
I 陆 , m o 昕 r n 距 8 帮 , n 4 。
图1 合 拢 区域 分 段 划 分 图
1 .Байду номын сангаас1 机舱 区船体 的状态 要求
轴管照光 、 镗孔及机舱分段镗孔后的总段合拢 、 焊接和轴舵 系照光工艺过程 。首 先对机舱 区与货舱 区船体状 态 进行测量与调整以达到整个船体 总组合拢精度要求 , 接着进行 轴系预照光 、 总段合 拢定位 以及 总段 合拢焊接 , 最 后对轴系 、 舵 系进行正式照光 。此工艺的应用 , 使得机舱分段建造完成后即可进行艉轴 管的镗孔 工艺 , 缩 短 了船
项目-船舶轴系安装,镗孔
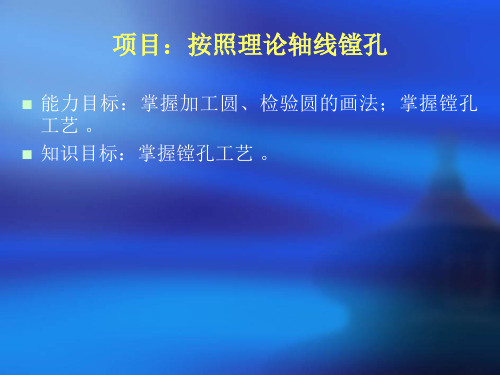
㈡镗孔技术要求
⑴镗削后,孔与检验圆线中心的偏差≯ 0.10mm; ⑵尾柱(或人字架)轴毂孔和尾隔舱孔的同轴度误差≯
0.10mm;舵系各舵承孔同轴度误差≯ 0.20mm; ⑶孔端面与孔轴中心线的垂直度误差≯0.15mm/m;
镗排装置示意图
1-进给箱 ;2-传动机构;3-止推轴承;4- 轴承;5,6-支架; 7-蜗轮、蜗杆;8-刀架;9-镗杆;10-尾隔舱壁;11-电动机; 12-皮带轮
⒉镗排在船上的安装、校中镗杆
镗排在船上的安装,主要工作是校中镗杆。 镗杆的校中就是使镗杆的轴线与轴系理论中 心线相重合。将轴承与镗杆在镗杆轴承架上 安装好后,可以通过调整镗杆轴承的位置, 使镗杆对中。校中镗杆的方法有以下几种:
⑷孔的圆度与圆柱度误差不得超过下表的规定;
表3—1轴系各孔的圆度、圆柱度允差(位:mm)毂孔直径 <80
80~ 120
120~ 180
180~ 260
260~ 360
360~ 500
500~ 700
规定值 0.04 0.05 0.06 0.07 0.08 0.09 0.10
⑸加工后的内孔配合面处以及端面的粗糙度RA值分别不得 超过3.2µm和12.5µm;
⑵用加工圆线和检验圆线校中镗杆
根据轴毂端面的加工圆线和检验圆线,用独脚卡钳或者划针 盘校中调整镗杆的位置,使其找正。
图3—3依据加工圆线和检验圆线使用划针盘或独脚卡钳校中镗杆 1-划针盘;2-镗杆;3-检验圆线
加工圆线和检验圆线的划法
加工圆线和检验圆线同心,加工圆是为了镗孔时确 定其加工线,以便于达到所规定的尺寸要求。检验 圆线比加工圆直径稍大,它是作为镗孔和船帕大修 检验轴系理论中线用。加工圆线和检验圆线的划法 如下:
浅析艉轴管镗孔精度控制
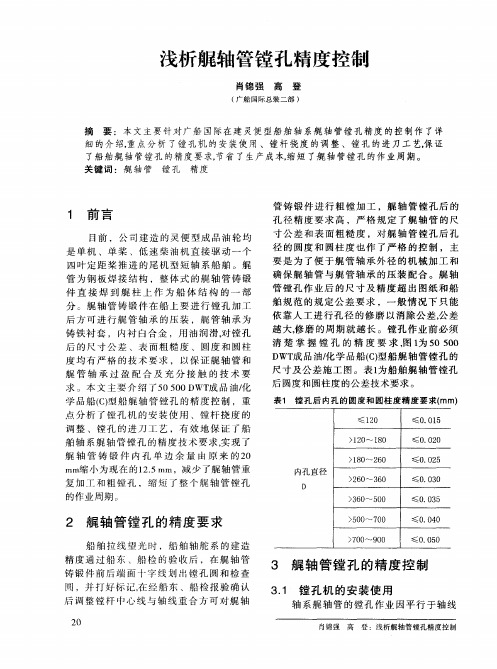
肖锦 强 高 登
( 船 国 际总 装 二部 ) 广
摘 要 :本 文 主要 针对 广 船 国 际在 建 灵便 型 船舶 轴 系艉 轴 管镗 孔精 度 的控 制 作 了详 细 的介 绍, 点分 析 了镗 孔 机 的 安装 使 用 、镗 杆 挠 度 的调 整 、镗 孔 的进 刀 工 艺, 证 重 保 了船 舶艉 轴 管镗孔 的精度 要求, 节省 了生产 成本。 缩短 了艉 轴 管镗 孔 的作 业周 期。 关 键词 :艉 轴管 镗 孔 精度
学 品船 f) 船 艉 轴 管 镗 孔 的精 度 控 制 ,重 c型
点 分 析 了镗 孑 机 的安 装 使 用 、镗 杆 挠 度 的 L 调 整 、镗 孔 的进 刀 工 艺 ,有 效 地 保 证 了船
舶 轴 系 艉 轴 管镗 孔 的精 度 技 术要 求 , 现 了 实 艉 轴 管 铸 锻 件 内 孔 单 边 余 量 由 原 来 的2 0 mm 小为现 在 的1 . n 缩 25 l m,减 少 了艉轴 管 重 复 加 _ 粗 镗 孔 ,缩 短 了整 个艉 轴 管镗 孔 T和 的作 业周期 。
1 前 言
目前 ,公 司建 造 的灵 便 型成 品 油 轮 均 是 单 机 、单 桨 、低 速 柴 油 机 直 接 驱 动 一 个 四 叶定 距 桨 推 进 的尾 机 型 短 轴 系 船 舶 。 艉 管 为钢 板 焊 接 结 构 ,整 体 式 的 艉 轴 管 铸 锻 件 直 接 焊 到 艉 柱 上 作 为 船 体 结 构 的 一 部 分 。艉 轴 管 铸 锻 件 在 船 上 要 进 行 镗孔 加 工 后 方 可 进 行 艉 管 轴 承 的 压 装 ,艉 管轴 承为 铸 铁衬 套 ,内衬 白合 金 ,用 油 润 滑, 镗 孑 对 L 后 的尺 寸 公 差 、表 面粗 糙 度 、圆度 和 圆柱 度 均 有严 格 的 技 术要 求 ,以保 证 艉 轴 管 和 艉 管 轴 承 过 盈 配 合 及 充 分 接 触 的 技 术 要
镗孔的加工工艺及夹具设计
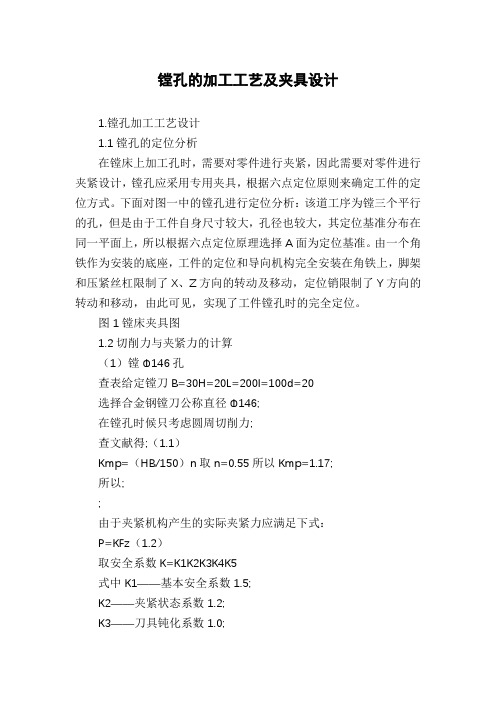
镗孔的加工工艺及夹具设计1.镗孔加工工艺设计1.1镗孔的定位分析在镗床上加工孔时,需要对零件进行夹紧,因此需要对零件进行夹紧设计,镗孔应采用专用夹具,根据六点定位原则来确定工件的定位方式。
下面对图一中的镗孔进行定位分析:该道工序为镗三个平行的孔,但是由于工件自身尺寸较大,孔径也较大,其定位基准分布在同一平面上,所以根据六点定位原理选择A面为定位基准。
由一个角铁作为安装的底座,工件的定位和导向机构完全安装在角铁上,脚架和压紧丝杠限制了X、Z方向的转动及移动,定位销限制了Y方向的转动和移动,由此可见,实现了工件镗孔时的完全定位。
图1镗床夹具图1.2切削力与夹紧力的计算(1)镗Φ146孔查表给定镗刀B=30H=20L=200I=100d=20选择合金钢镗刀公称直径Φ146;在镗孔时候只考虑圆周切削力;查文献得;(1.1)Kmp=(HB/150)n取n=0.55所以Kmp=1.17;所以;;由于夹紧机构产生的实际夹紧力应满足下式:P=KFz(1.2)取安全系数K=K1K2K3K4K5式中K1——基本安全系数1.5;K2——夹紧状态系数1.2;K3——刀具钝化系数1.0;K4——考虑夹紧动力稳定性系数1.0;K5——尽在有力矩企图使用回转时开考虑支撑面接触情况的系数1.0;所以得到K=K1K2K3K4K5=1.9,得到P=KFz=1.9X365.18=693.88N (2)镗Φ48孔选择高速钢镗刀公称直径Φ48;查表给定镗刀B=25H=30L=170I=80d=15在镗孔时候只考虑圆周切削力;查文献得;Kmp=(HB/150)n取n=0.55所以Kmp=1.17;所以;;由于夹紧机构产生的实际夹紧力应满足下式:P=KFz取安全系数K=K1K2K3K4K5式中K1——基本安全系数1.5;K2——夹紧状态系数1.2;K3——刀具钝化系数1.0;K4——考虑夹紧动力稳定性系数1.0;K5——尽在有力矩企图使用回转时开考虑支撑面接触情况的系数1.0;所以得到K=K1K2K3K4K5=1.9,得到P=KFz=1.9X223.2=424.08N <ol> 镗Φ80孔</ol>镗Φ80孔的计算过程与上边量孔的方法是一样的,就是选择高速钢镗刀公称直径Φ80的镗刀,最后计算结果为P=KFz=569.23N 根据上边的计算夹紧力不是很大,且夹具选择的种类为组合夹具,所以动力选择手动夹紧。
镗孔工艺

第五章加工工艺培训
第四节镗孔加工事项
一、操作
1.镗刀分粗、精镗,使用前根据镗削余量,选择刀具类型,镗刀长度尽量短
2.镗孔冷却方式采用切削液冷却。
3.镗孔指令为G85、G76
3.1粗镗G85格式:
G85 X0. Y0. Z-100. R1. F100;
镗孔指令孔坐标孔深度起始加工高度进给速度
3.2精镗G76格式:
G76 X0. Y0. Z-100. R1. I1. JI. F100;
镗孔指令孔坐标孔深度起始加工高度退刀点进给速度
说明:
使用G76镗孔,精镗刀只能有1个切削刃,镗刀装主轴后,执行主轴定位,确认刀尖方向,然后修改程序中I、J退刀值,I代表X方向、J代表Y方向(也可只选用一个方向),I、J数值移动方向必须与刀尖方向相反,否则会产生撞刀,损坏机床、工件、刀具现象,切记!!
执行G76指令具体动作为:
主轴移动到孔坐标位置,开始镗削,Z值到设定的深度后,主轴定位,执行I、J值刀尖偏离工件,主轴以快速进给速度抬起到R点,主轴按先前速度旋转,X、Y轴移至孔坐标位置。
4.孔径测量采用内径量表,先调整量表,如Φ25孔先将内径表调整在25,测量时将触头放如孔内,读表数值。
二、工艺流程:
1)钻底孔,底孔直径应比实际直径小3~5mm,选用U钻加工。
2)粗镗,粗镗后留1mm余量。
3)中镗,中镗留0.1mm余量,采用对刀仪测量镗刀直径。
4)精镗,精镗刀直径调整前确认每小格调整量,注意调整量是直径调整。
5)检验,内径量表,如不合格根据偏差量调整镗刀直径。
6)镗孔加工参数可在MJNCSVR\\刀具信息\\刀具切削参数表2004-8-11查询。
镗孔工艺

6.7 镗孔工艺、编程6.7.1 镗孔加工概述1.镗孔加工要求镗孔是加工中心的主要加工内容之一,它能精确地保证孔系的尺寸精度和形位精度,并纠正上道工序的误差。
通过镗削上加工的圆柱孔,大多数是机器零件中的主要配合孔或支承孔,所以有较高的尺寸精度要求。
一般配合孔的尺寸精度要求控制在IT7~IT8,机床主轴箱体孔的尺寸精度为IT6,精度要求较低的孔一般控制在IT11。
对于精度要求较高的支架类、套类零件的孔以及箱体类零件的重要孔,其形状精度应控制在孔径公差的1/2~1/3。
镗孔的孔距间误差一般控制在±0.025~0.06 mm,两孔轴心线平行度误差控制在0.03~0.10 mm。
镗削表面粗糙度,一般是Ra1.6~0.4 μm。
2.镗孔加工方法孔的镗削加工往往要经过粗镗、半精镗、精镗工序的过程。
粗镗、半精镗、精镗工序的选择,决定于所镗孔的精度要求、工件的材质及工件的具体结构等因素。
⑴粗镗粗镗是圆柱孔镗削加工的重要工艺过程,它主要是对工件的毛坯孔(铸、锻孔)或对钻、扩后的孔进行预加工,为下一步半精镗、精镗加工达到要求奠定基础,并能及时发现毛坯的缺陷(裂纹、夹砂、砂眼等)。
粗镗后一般留单边2~3 mm作为半精镗和精镗的余量。
对于精密的箱体类工件,一般粗镗后还应安排回火或时效处理,以消除粗镗时所产生的内应力,最后再进行精镗。
由于在粗镗中采用较大的切削用量,故在粗镗中产生的切削力大、切削温度高,刀具磨损严重。
为了保证粗镗的生产率及一定的镗削精度,因此要求粗镗刀应有足够的强度,能承受较大的切削力,并有良好的抗冲击性能;粗镗要求镗刀有合适的几何角度,以减小切削力,并有利于镗刀的散热。
⑵半精镗半精镗是精镗的预备工序,主要是解决粗镗时残留下来的余量不均部分。
对精度要求高的孔,半精镗一般分两次进行:第一次主要是去掉粗镗时留下的余量不均匀的部分;第二次是镗削余下的余量,以提高孔的尺寸精度、形状精度及减小表面粗糙度。
400000DWTVLOC艉管镗孔及尾轴承安装关键技术

400 000DWT VLOC尾管镗孔及尾轴承安装关键技术摘要:本文针对公司在建400 000DWT VLOC 的尾管镗孔及尾轴承安装的关键技术进行了详细介绍,重点分析了镗排的选用、镗排中心调节方法、精细镗孔关键技术以及尾轴承的安装等关键技术应用,确保了尾管镗孔和轴承安装的高质量要求。
关键词:超大型矿砂船;尾管镗孔;尾轴承安装;关键技术1 前言400 000DWT VLO(是由一台B&W MAN 7G80G9.5 低速柴油机驱动一只大直径定距桨推进的船舶,也是到目前为止最大的矿砂运输船。
尾管为焊接结构,尾管两端的铸钢件焊接在101 分段上作为船体结构的一部分,需在照光后对此铸钢件进行镗孔方可进行尾轴承的压装。
本文主要介绍了400 000DWT VLOC尾管镗孔过程中镗排的选用、镗排中心的调节方法、精细镗孔的关键技术以及尾轴承的安装等关键技术,确保了尾管镗孔和轴承安装的高精度要求,节省了生产成本,缩短了作业周期。
2 400 000DWT VLO啲尾管介绍2.1 尾管布置图本船的艉管布置图如下:2.2 镗孔的精度要求轴系望光报检后,我们会在艉管铸钢件前后端面划镗孔圆和检验圆并作标记。
通常在经船东和船级社确认后调整镗排中心线与轴系中心线重合,然后开始对艉管铸钢件进行镗孔加工。
艉管镗孔后的内孔精度要求高,对艉管尺寸公差和表面粗糙度、艉管镗孔后内孔的圆度、圆柱度以及前后轴承的同心度也作了严格的规定,目的是为了方便艉管轴承外径的机械加工尺寸匹配,确保艉管与艉管轴承的压装配合质量。
艉管镗孔作业后的尺寸及精度超出图纸和规范的公差要求,将带来无法预期的后果,严重的会造成昂贵的轴承报废,带来成本和时间的极大浪费。
3 镗孔精度的控制3.1 镗排的选用为保证艉管镗孔的精度,须考虑镗排自身重量而产生的挠度影响。
以前的镗排由于使用时间长,两端的支撑轴承磨损严重,轴承间隙过大,镗排跳动大,且动力系统一般采用普通电机通过皮带来带动蜗杆蜗轮传动,精度较低,容易出现打滑、蹦刀等情况发生,镗孔后的圆度和圆柱度等难以保证,会严重影响到整个镗孔的作业周期。
项目-船舶轴系安装,镗孔
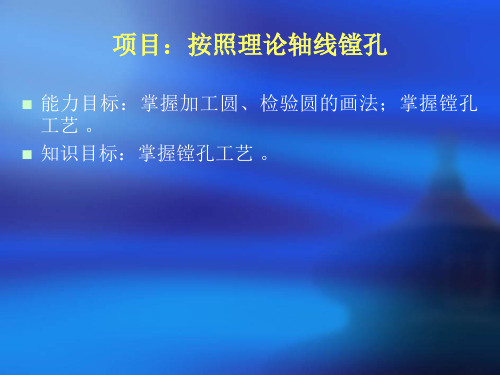
㈡镗孔技术要求
⑴镗削后,孔与检验圆线中心的偏差≯ 0.10mm; ⑵尾柱(或人字架)轴毂孔和尾隔舱孔的同轴度误差≯
0.10mm;舵系各舵承孔同轴度误差≯ 0.20mm; ⑶孔端面与孔轴中心线的垂直度误差≯0.15mm/m;
项目:按照理论轴线镗孔
能力目标:掌握加工圆、检验圆的画法;掌握镗孔 工艺 。
知识目标:掌握镗孔工艺 。
㈠镗孔目的和技术要求
人字架轴毂、尾柱轴毂、尾隔舱壁座板法兰或尾 轴管等,都是通过精确定位将其装焊在船体上的, 并且在装焊过程中采取了相应的控制焊接变形的 措施。但是在装焊完成之后,这些焊接件相对于 船体的定位及其本身的形状仍然会发生变化,使 其内孔中心线与轴系理论中心线不重合。为了解 决这个问题,目前船厂普遍采用的工艺方法就是 镗孔。
因此在设计和选用镗杆时应该尽量加大镗杆直径。
⑵镗杆轴承支架
应该尽可能加大镗杆轴承支架的刚性;并且轴承支 架应该尽量安装在船体强结构处,并予以可靠固定; 尽量减小镗杆轴承支架之间的距离以减轻镗杆变形 等等。
当镗杆跨度较长时可以考虑在镗杆上增加一个中间 轴承,如图3-6 所示。在轴系拉线、望光前,根据 镗杆的长度和轴承的位置,先在车间对镗杆进行挠 度测量,然后将测量的数据进行统计分析, 经综合 考虑计算后得到镗杆中间轴承部位的实际挠度,安 装镗杆时按该数值进行调整。
⑷孔的圆度与圆柱度误差不得超过下表的规定;
表3—1轴系各孔的圆度、圆柱度允差(单位:mm)
毂孔直径 <80
80~ 120
120~ 180
180~ 260
260~ 360
360~ 500
艉轴管分段镗孔及定位技术的应用
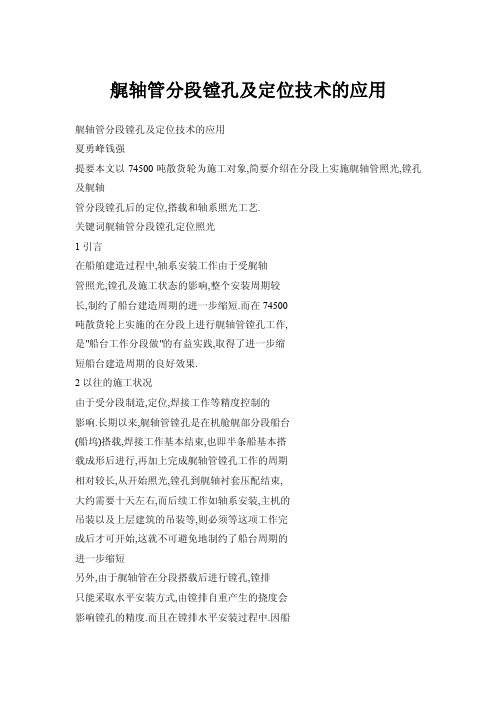
艉轴管分段镗孔及定位技术的应用艉轴管分段镗孔及定位技术的应用夏勇峰钱强提要本文以74500吨散货轮为施工对象,简要介绍在分段上实施艉轴管照光,镗孔及艉轴管分段镗孔后的定位,搭载和轴系照光工艺.关键词艉轴管分段镗孔定位照光1引言在船舶建造过程中,轴系安装工作由于受艉轴管照光,镗孔及施工状态的影响,整个安装周期较长,制约了船台建造周期的进一步缩短.而在74500吨散货轮上实施的在分段上进行艉轴管镗孔工作,是"船台工作分段做"的有益实践,取得了进一步缩短船台建造周期的良好效果.2以往的施工状况由于受分段制造,定位,焊接工作等精度控制的影响.长期以来,艉轴管镗孔是在机舱艉部分段船台(船坞)搭载,焊接工作基本结束,也即半条船基本搭载成形后进行,再加上完成艉轴管镗孔工作的周期相对较长,从开始照光,镗孔到艉轴衬套压配结束,大约需要十天左右,而后续工作如轴系安装,主机的吊装以及上层建筑的吊装等,则必须等这项工作完成后才可开始,这就不可避免地制约了船台周期的进一步缩短另外,由于艉轴管在分段搭载后进行镗孔,镗排只能采取水平安装方式,由镗排自重产生的挠度会影响镗孔的精度.而且在镗排水平安装过程中.因船上场地狭小,船台旁的高吊难以全过程发挥作用,须用手动葫芦配合吊装到位,工人的劳动强度大,危险系数高,容易造成人员和设备的伤害事故.3改进方案随着公司对船体精度控制水平的不断提高及74500吨散货轮的批量建造.为艉轴管在分段上进行照光,镗孔工作提供了可能.艉轴管分段镗孔时,如原先船台照光时用作基准的船体基线,基准肋骨在分段上都难以找到,因此需要重新设定基准:在轴系高度方向,不再以船体基线为基准.而是将艉轴管理论中心移植到分段胎架上,并以此中心为基准,确定镗孔的加工圆及检验圆; 艏艉方向.以分段横舱壁FR11#船体肋位为基准,测量艉轴管前端面到11#肋位的距离及艉轴管毛坯长度,参照艉轴管理论长度确定艉轴管端面加工余量. 在艉轴管分段(AB02分段)镗孔结束后,通过对该分段定位精度和焊接顺序的控制来保证轴系中心线的偏差.在分段总组定位时,在艉轴管后面和32#肋位处根据理论轴系高度竖立艉靶和艏靶,同时在艉轴管前后端面放置照光靶,用拉钢丝的方法找出艉轴管中心线,通过放置于尾部的激光仪找出轴系理论中心线.调整AB02分段,使艉轴管实际中心线与由艏,艉靶确定的理论中心线重合(偏差≤1mm),达到要求后进行焊接,并在焊接过程中根据实际情况调整焊接顺序,保证焊接后艉轴管实际中心线与理论中心线最终偏差~<4mm.艉轴管分段镗孔,定位的流程如图1所示.图1艉轴管分段镗孔,定位流程图334实施情况4.1分段照光,划线确定改进方案后,我们首先在74500吨散货船上实施.首先,在胎架上标出AB02分段的理论中心.并将此中心移植到地面上,以FR11样横舱壁为基面完成AB02分段的制造工作,并保证分段处于水平状态.然后根据分段的理论中心,在艉轴管前,后端面放置十字照光靶,利用重锤并调整照光靶使靶心与分段理论中心重合,如图2.以调整后的靶心为基准划出镗孔加工圆及检验圆.艉靶见图4.由图4数据可以看出,镗孔后的圆度基本控制在O.05mln的范围内,达到了预定的加工精度要求.4.3分段总组定位在机舱三甲板以下区域分段合拢后,对艉轴管分段进行定位,总组.按图5所示,设置A,B,C,D,F五只照光靶,利用拉钢丝的方法找出艉轴管镗孔后的中心线,通过置于尾部平台的照光仪,调整艉轴管分段使艉轴管两端的B靶,c靶与A靶,D靶的中心线处于同一直线上(左右定位偏差≤1mm.高度定位偏差≤2mm,且C靶要比B靶高1-2mm).测量艉轴管后端面到F靶(19#肋位)的距离,调整艉轴图2AB02分段照光,划线测量艉轴管长度:实际长度(L):3324mm理论长度(L):3290mm测量艉轴管前端面距FR11样肋骨长度:实际长度(A):262mm理论长度(A):250mm由上述尺寸得出:艉轴管前端面加工余量12mm,艉轴管后端面加工余量22mm.4.2分段镗孔镗排呈竖直状态进行安装(如图3),在镗孔过程中由于镗排的运转产生一定的振动,将影响镗孔的精度.为减小振动保证镗孔质量,需对分段的胎架进行必要的加强,并对镗孔进刀量进行适当控制,每次进刀量不宜超过3mm.镗孔结束后进行艉轴管加工尺寸的测量,数据34管分段前后位置并进行分段的定位.4.4分段焊接为了控制分段的焊接变形量,要求分段装配间隙控制在3~5mm,并采用CO:半自动单面焊工艺. 焊接时安排双数焊工对称同时施焊,要求焊接顺序, 焊缝层数,焊缝长度,焊接规范等都相同,每层焊缝厚度控制在3-4mm,并制定了专门的焊接工艺.在焊接过程中,利用照光仪(如图6),每隔1~2小时记录下理论轴线和实际轴线的偏差,并及时调整焊接顺序.使偏差值始终处在允许范围之内.焊接结束后,测量艉管后端面到F靶的长度及艉管实际中心线与船体基线的偏差.4.5轴,舵系照光A向\lr]/IIl_/llI一7300~300X6400nn,,/镗排t分-ID段UC-镗排托架|IlI【胎架地面—\,,图3搭排示意图pA向T.l,.''B标准尺寸中7oo中628中626中626中628中700序号l2345678910ll12l314T—B+o.2O-0.13-0.15-0.16-0.9l-0.94-0.93-0.90-0.87-0.B5-0.43-0.43-0.4l+o.13 P—S+o.19-0.1l-0.14-0.15-0.88-0.89-0.92-0.94.93-0.90-0.48-0.46-0.43+o.1O 图4艉轴管分段镗孔后测量数据∥F靶D靶EG3\\E632P!,S.'_]]门'延\照光仪{\fI3ES43P/Sl钔II'~EBOI下EB02EB03L一图5AB02分段定位示意图35艉部BS图6AB02分段总组时的焊接过程艏部图7照光时艉轴管测量数据在机舱38#肋位以后分段搭载结束后.进行轴舵系的照光工作并提交船东.在艉轴管的前,后端面安装照光靶,通过调整使其靶心与艉轴管实际中心重合,调整照光望远镜使其同艉轴管实际中心线在同一直线上.通过对比艏,艉基准靶,检查轴线理论中心线和实际中心线的偏差.测量数据如图7所示:分段艉部向下偏4ram.向左偏1mm;分段艏部向下偏3mm,向右偏0.5mm.测量艉轴管后端面至F 靶长度为9437mm,比理论值短了3mm.轴,舵系两中心线的偏差为1.2mm.与船体基线的偏差为3 mm.因此分段定位,焊接后的状态达到了预先设定的精度要求,新工艺的尝试取得初步成功.5结论新工艺的实施,省去了船台镗孑L时间,使得分段搭载完毕后即可进行艉轴管衬套的压配.至少可以使船台周期缩短一周左右;同时由于是在分段上进行镗孔,以前影响镗孔质量的因素得到控制,使得艉轴管的镗孔质量有所提高;最重要的一点在于:新的工艺大大减轻了施工劳动强度,由于是竖直搭排,使得镗排的吊装变得非常简单.分段镗孔,工人可以不必像以前那样需在船体尾部和机舱之间爬进爬出,而只需借助梯子在地面和上部平台之间就可施工,变船台施工为地面施工,使得安全系数也大大提高.同时镗孔施工人数也可由原来的三人减少为两人,节省了人工成本.当然,由于艉轴管是在分段阶段就镗孔结束,为保证后续轴系安装工作的顺利进行,对艉轴管分段与机舱分段的定位,搭载的精度提出很高要求,增加了这一部分的施工难度,但是该工艺的较多优点,使它所带来的好处大大超过其造成的困难,通过不断地应用,总结及改进,艉轴管分段镗孔必将成为一个成熟的工艺而得到推广应用.。
尾轴镗孔工艺

1. 镗孔前的要求及准备工作Requirement and preparation before boring.1)孔的中心线己确定并提交船东船检认可,同时尾部的所有振动工作应停止。
Center line confirmed and approved by owner and inspector, and stop allvibration at after.2)检查在尾轴孔端面的加工圆及检验圆是否己标记。
Check marked for machining circle and check circle at stern tube.3) 检查尾管铸件是否符合图纸尺寸要求,确认后方可塞镗排进行镗孔。
Check the size of stern tube casting, ensure the size as same as the sizeof shaft arrangement drawing , after being confirmed, take the boringspindle into stern tube2. 镗排在船上的安装Installation boring spindle on board.1)将专用镗排用滑车及手拉葫芦慢慢装入尾轴孔内并在适当的位置用专用轴承支承。
(见图①)Fix special boring spindle slowly into stern tube by tackle and hand gourdand support by special bearing where necessary (See fig. ①).2)在镗排的两端近尾轴孔的两端面固定两根划针,(见图①所示)慢慢转动镗杆根据尾轴孔两端的检验圆进行校核镗杆,直至镗杆与尾管两端的检验圆同心,将镗孔上各调整轴承固定并将传动装置安装到位,这样可以开始进行尾轴孔的切削。
Fix two needle at boring spindle both ends near stern tube both ends(showed in fig. ①), slowly rotate boring spindle according to stern tubeboth ends check circle until boring spindle is concentric with check circleat stern tube both ends, fix adjustment bearing on boring hole and installpower unit, so can begin stern tube hole cutting.3. 尾管的镗孔Boring for stern tube1)根据图纸要求见尾轴尾管总图加工达到图纸的要求,见图②,镗孔必须分粗镗和精镗两阶级,粗加工后须要据检验圆校核镗杆位置有无移动,经检验无误或经调整后方可进行精镗,具体的加工切削用量如下表。
船舶艉轴管镗孔工装架设工艺
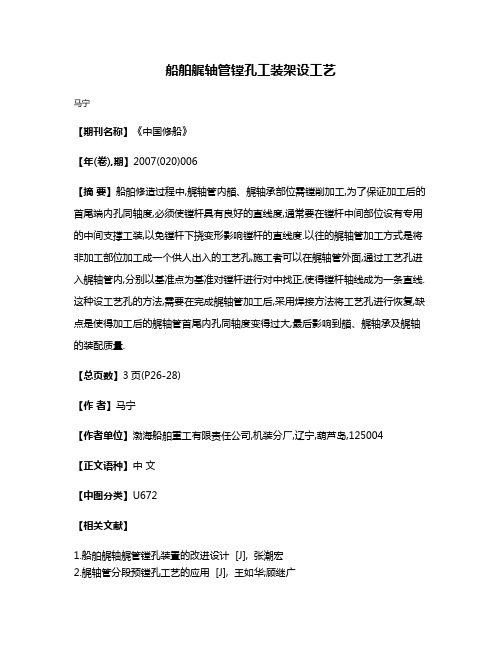
船舶艉轴管镗孔工装架设工艺
马宁
【期刊名称】《中国修船》
【年(卷),期】2007(020)006
【摘要】船舶修造过程中,艉轴管内艏、艉轴承部位需镗削加工,为了保证加工后的首尾端内孔同轴度,必须使镗杆具有良好的直线度,通常要在镗杆中间部位设有专用的中间支撑工装,以免镗杆下挠变形影响镗杆的直线度.以往的艉轴管加工方式是将非加工部位加工成一个供人出入的工艺孔,施工者可以在艉轴管外面,通过工艺孔进入艉轴管内,分别以基准点为基准对镗杆进行对中找正,使得镗杆轴线成为一条直线.这种设工艺孔的方法,需要在完成艉轴管加工后,采用焊接方法将工艺孔进行恢复,缺点是使得加工后的艉轴管首尾内孔同轴度变得过大,最后影响到艏、艉轴承及艉轴的装配质量.
【总页数】3页(P26-28)
【作者】马宁
【作者单位】渤海船舶重工有限责任公司,机装分厂,辽宁,葫芦岛,125004
【正文语种】中文
【中图分类】U672
【相关文献】
1.船舶艉轴艉管镗孔装置的改进设计 [J], 张潮宏
2.艉轴管分段预镗孔工艺的应用 [J], 王如华;顾继广
3.湘岳24车渡船艉轴管无镗孔安装工艺 [J], 李新平
4.长艉轴管镗孔新工艺 [J], 刘一燕
5.长艉轴管镗孔新工艺 [J], 刘一燕
因版权原因,仅展示原文概要,查看原文内容请购买。
- 1、下载文档前请自行甄别文档内容的完整性,平台不提供额外的编辑、内容补充、找答案等附加服务。
- 2、"仅部分预览"的文档,不可在线预览部分如存在完整性等问题,可反馈申请退款(可完整预览的文档不适用该条件!)。
- 3、如文档侵犯您的权益,请联系客服反馈,我们会尽快为您处理(人工客服工作时间:9:00-18:30)。
1.镗孔前的要求及准备工作
Requirement and preparation before boring.
1)孔的中心线己确定并提交船东船检认可,同时尾部的所有振动工作应停止。
Center line confirmed and approved by owner and inspector, and stop
all vibration at after.
2)检查在尾轴孔端面的加工圆及检验圆是否己标记。
Check marked for machining circle and check circle at stern tube.
3)检查尾管铸件是否符合图纸尺寸要求,确认后方可塞镗排进行镗孔。
Check the size of stern tube casting, ensure the size as same as the size
of shaft arrangement drawing, after being confirmed, take the boring
spindle into stern tube
4)对镗排应进行严格的检查休整,确保镗孔所需各种工具到位。
2.镗排在船上的安装
Installation boring spindle on board.
1)将专用镗排用滑车及手拉葫芦慢慢装入尾轴孔内并在适当的位置用专用轴承支承。
(见图①)
Fix special boring spindle slowly into stern tube by tackle and hand
gourd and support by special bearing where necessary (See fig. ①).
2)在镗排的两端近尾轴孔的两端面固定两根划针,(见图①所示)慢慢转动镗杆根据尾轴孔两端的检验圆进行校核镗杆,直至镗杆与尾管两端的检验圆同心,将
镗孔上各调整轴承固定并将传动装置安装到位,这样可以开始进行尾轴孔的切
削。
Fix two needle at boring spindle both ends near stern tube both ends
(showed in fig. ①), slowly rotate boring spindle according to stern tube
both ends check circle until boring spindle is concentric with check
circle at stern tube both ends, fix adjustment bearing on boring hole
and install power unit, so can begin stern tube hole cutting.
3.尾管的镗孔
Boring for stern tube
1)根据图纸要求见尾轴尾管总图加工达到图纸的要求,见图②,镗孔须分粗镗、半精镗、精镗三阶级,每阶段加工后须要据检验圆校核镗杆位置有无移动,经
检验无误或经调整后方可进行下阶段,具体各阶段的加工切削用量如下表。
According to drawing requirement seeing stern tube general drawing,
see fig. ②, boring must be divided into three stages of heavy boring 、
half finally boring and finally boring, must check whether boring
spindle position is moved as check circle after rough machining, finally
boring can be carry out after having checked right or adjusted, actual
machining cutting value as follows table.
为了避免因温度的变化而引起的尾管变形,尾管的精镗最后刀应在阴雨天或夜
间一次连续完成,最后一刀的走刀方向最好与轴承压入的方向一致。
To avoid stern tube’s deformation due to temperature alternate, last
feed of stern tube finally boring should finish continuously at a time in
cloudy rainy day or at night, last feed cutting direction accord with
that of bearing press-in best.
2)尾轴孔加工完毕经检验合格后,加工两面端面。
Finish stern tube hole and check carry out, then machining two ends
surface.
3)检验人员测量时应测量艉管现场的温度,然后把测量的数据记录在附表中,测量完毕后把数据提供给相关部门计算艉管轴承加工尺寸。
We should measure the temperature of the stern tube when starting
measurement, then record the measurement value at attached sheet
and afford the value to design department to decide the machining size
of stern tube.
4.镗孔质量的检验及要求
Check and requirement for boring quality
1)尾管孔表面的检验,可采用专用工具对加工表面检测,对于与轴承配合的表面的粗糙度控制在3.2um以内,对于非配合表面粗糙度控制在6.4u m以内。
Check stern tube hole surface, can adopt special tool to check finish
surface, roughness for surface fit with bearing should be within 3.2um,
and roughness for no fit surface should be within 6.4um.
2)镗削后的孔的同轴度的检验,在镗杆的两端安装两只百分表(见图③),慢慢转动镗杆确保同轴度误差不超过0.05mm.
check hole coaxiality after boring, mount two dial gauge at the both
ends of boring spindle (see fig ③), and slowly turn boring spindle to ensure no coaxiality not exceeding 0.05mm.
3)艉管内镗孔尺寸的检验,镗孔加工允许(相对于某一纵截面)椭圆度为0.02mm,圆柱度为0.01/200mm。
Check stern tube hole size, we allow the ellipse defection of stern tube boring is 0.02mm, column deflection 0.01/200mm.
4)镗孔结束后,根据镗孔尺寸确定艉管轴承加工的尺寸,在加工过程中金加工应全程监控,确保尺寸的准确性。
(为了保证艉轴轴承加工尺寸的准确度,建议从艉轴轴承到货就检查其原始尺寸,包括内外径。
After boring, according to the size of boring to decide the size of stern tube bearing. The worker of the machinery workshop should attend checking the size of stern tube bearing ensure the size veracity.。