6 Sigma项目运作实例
六西格玛经典案例

六西格玛经典案例在六西格玛质量管理方法中,通过分析和改进业务流程,以减少缺陷和提高效率,从而实现优秀质量和高度效益。
以下是三个经典的六西格玛案例。
1. Motorola的六西格玛实践Motorola是六西格玛的奠基者之一、20世纪80年代,Motorola采用六西格玛方法,以改进生产过程并提高质量。
在一个以缺陷率而不是零缺陷为标准的产业中,Motorola在一年内将缺陷率从超过三十万个降低到每百万个产品中只有5个。
六西格玛的成功引起了其他公司的注意,并成为其他公司实施质量管理的典范。
2. General Electric(GE)的六西格玛实施GE是六西格玛的早期采用者,它将六西格玛引入公司的各个部门和业务领域。
公司的首席执行官杰克·韦尔奇在1995年将六西格玛作为公司的战略重点。
GE在实施过程中的一个成功案例是其航空发动机业务部门,该部门通过六西格玛方法降低了生产过程中的缺陷率,并提高了航空发动机的性能和可靠性。
GE的成功证明了六西格玛可以在各种行业中实现卓越的结果。
3.美国政府的六西格玛应用六西格玛方法不仅在企业界取得成功,而且在政府部门中也有很好的应用。
美国政府决定在1995年引入六西格玛方法,以提高效率并减少浪费。
例如,美国联邦航空管理局(FAA)使用六西格玛方法改进了飞行管制和管理过程,减少了航班延误和事故。
美国海军也采用了六西格玛方法来改善军舰维护和修理过程,提高了战斗力和减少了成本。
以上是六西格玛的三个经典案例,它们都展示了通过六西格玛方法来实现质量改进和效益提高的潜力。
这些案例证明了六西格玛是一个非常有力的质量管理方法,可以在各个领域带来显著的结果。
无论是在制造业、服务业还是政府部门,六西格玛都能够提供一个可靠的框架来解决质量和效率方面的挑战。
6西格玛课题优秀案例

6西格玛课题优秀案例引言六西格玛(Six Sigma)是一种管理方法论,旨在通过改进过程、减少变异性,实现组织的质量提升和业绩增长。
在实施六西格玛的过程中,找到并解决关键问题是至关重要的。
本文将介绍几个成功的六西格玛课题案例,以帮助读者理解和应用这一方法。
二级标题1:提高生产效率三级标题1:问题定义某制造公司的一条生产线在生产过程中经常出现设备故障和停机现象,导致生产效率低下,成本增加。
三级标题2:数据收集和分析通过收集生产线的故障和停机数据,使用六西格玛工具进行统计和分析,发现故障率高的设备集中在一部分关键节点。
三级标题3:解决方案实施制定计划,对故障率高的设备进行维护和改善,包括增加保养频次、更换易损件等。
定期对生产线进行维护保养,并进行性能测试。
三级标题4:效果评估在实施方案后,故障率明显下降,生产效率提升,废品率减少,公司成本下降。
二级标题2:提升服务质量三级标题1:问题定义一家电信公司的客户投诉率较高,客户满意度低,需要提升服务质量。
三级标题2:数据收集和分析通过对客户投诉数据和服务流程进行分析,发现一些环节存在延迟、错误和不满足客户需求的问题。
三级标题3:解决方案实施通过重新设计服务流程、增加培训和监督措施,改进员工的服务态度和技能。
同时引入技术支持,提高服务效率。
三级标题4:效果评估客户投诉率显著下降,客户满意度得到提升,公司形象和口碑也得到了改善。
二级标题3:降低产品缺陷率三级标题1:问题定义某电子产品制造公司的产品缺陷率较高,需要降低产品缺陷率以提升产品质量。
三级标题2:数据收集和分析通过对产品缺陷数据的收集和分析,发现一些生产工艺过程存在缺陷,导致产品质量不稳定。
三级标题3:解决方案实施通过优化生产工艺,加强工艺控制和改进产品组装方式,减少产品缺陷。
同时引入质量检测和抽检机制,及时发现和解决问题。
三级标题4:效果评估产品缺陷率显著下降,客户投诉数量减少,公司产品质量得到了有效改善。
6西格玛平安案例

6西格玛平安案例案例1一个半导体簿膜设备制造商在"6-Sigma"实施前的状况是:由于设计研发周期太长,该公司老是不能及时将产品推入市场,而且由于故障率太高,致使售后效劳和维修本钱太高。
售后效劳和维修本钱包括:(1)顾客埋怨、投诉和保修本钱;(2)客户维修本钱;(3)延迟发货和停产损失。
该公司一台设备的平均单价是US$7500K。
该公司希望通过"6-Sigma"的改进运作,能使公司赶上其竞争对手,如Toshiba,Actel,Applied,Material等公司。
该公司的"6-Sigma"运作是从建立"6-Sigma"团队开始的。
核心团队由研发工程、应用工程及可靠性工程组成,其它部门(如市场、制造、财务、质量等)负责支持与协助。
公司的总裁直接领导一个"6-Sigma"负责人,该"6-Sigma"负责人是由公司的副总裁担任。
在"6-Sigma"负责人之下,是"6-Sigma"黑带委员会(包括MBB黑带师、研发总监、技术总监)、"6-Sigma"财务委员会、研发系统1#、研发系统2#、研发系统3#和两个黑带项目团队。
该公司"6-Sigma"的推进步骤如下:由管理高层确定"6-Sigma"的开展计划和管理结构,选定KPI,然后进行管理高层的培训和"6-Sigma"BB培训。
在培训过程中,BB黑带项目也要同时选定和实施,最后是项目的审核。
选定的KPI是:(1)研发周期缩短2个月;(2)生产过渡期合格率由65%提高到80%;(3)减少客户报怨和维修率80%;(4)预计财务回报:通过降低研发周期可创造亿美元(US$350KK);通过提高合格率可创造2亿美元(US$200KK);通过降低维修成本可节约4亿美元(US$400KK)。
6 Sigma项目运作实例

《6 Sigma项目运作实例》如何定义一个项目?项目定义是由冠军来完成的。
我们简单介绍以下项目是如何定义的。
1确定主要商业问题:a目标b目的c可交付使用的2对与生产来说:a循环时间b质量/缺陷水平c耗费3项目的选择a选择项目的工具a1宏观图a2 Pareto图分析a3鱼骨图a4因果矩阵图b项目的标准(评估)b1减少缺陷的70%b2第一年节省$175Kb3项目完成周期为4个月b4最少的资金总额b5黑带的第一个项目必须满足培训目标《6 Sigma项目运作实例》->《定义阶段》->我们在定义阶段做什么--------------------------------------------------------------------------------------------------- 我们在定义阶段需要做什么?1,完成项目陈述。
2,完成项目预测节省金额。
3,完成问题陈述:3.1问题是什么?3.2在哪里和什么时间发现的?3.3问题将涉及哪些工序?3.4谁将受到影响?3.5问题的严重程度是什么?3.6你是如何得知这些的?4,绘制宏观图。
5,描述项目的主线。
6,完成目标陈述。
7,组成项目小组,列出小组成员。
8,完成财务评估。
《6 Sigma项目运作实例》->《定义阶段》->如何进行项目问题陈述--------------------------------------------------------------------------------------------------- 如何进行问题陈述?分六个方面进行问题陈述:1问题是什么?2在哪里和什么时间发现的?3问题将涉及哪些工序?4谁将受到影响?5问题的严重程度是什么?6你是如何得知这些的?《6 Sigma项目运作实例》->《定义阶段》->如何绘制宏观图--------------------------------------------------------------------------------------------------- 如何绘制宏观图?绘制宏观图的顺序:供应商->输入->工序->输出->客户《6 Sigma项目运作实例》->《定义阶段》->项目的目标陈述要点--------------------------------------------------------------------------------------------------- 项目的目标陈述要点:1,目标陈述2,计算方法3,全年节省额确定Team Members成员:1,小组成员要包括技术人员2,包括维修人员(如果需要)3,包括操作者4,小组人员不超过5人(特殊情况除外)。
六西格玛案例分析
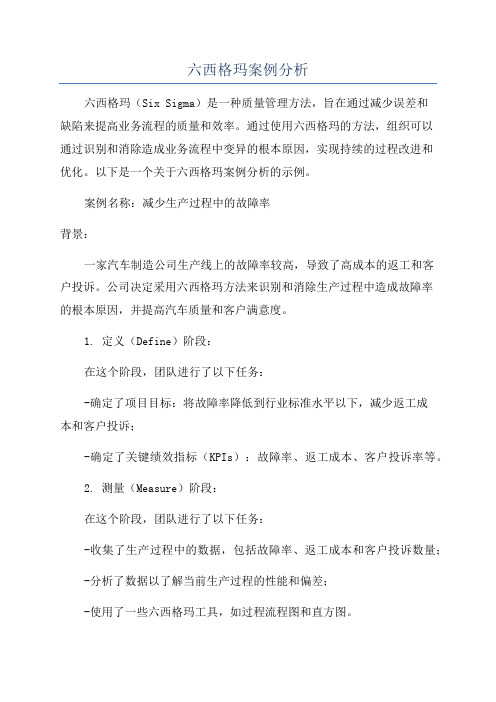
六西格玛案例分析六西格玛(Six Sigma)是一种质量管理方法,旨在通过减少误差和缺陷来提高业务流程的质量和效率。
通过使用六西格玛的方法,组织可以通过识别和消除造成业务流程中变异的根本原因,实现持续的过程改进和优化。
以下是一个关于六西格玛案例分析的示例。
案例名称:减少生产过程中的故障率背景:一家汽车制造公司生产线上的故障率较高,导致了高成本的返工和客户投诉。
公司决定采用六西格玛方法来识别和消除生产过程中造成故障率的根本原因,并提高汽车质量和客户满意度。
1. 定义(Define)阶段:在这个阶段,团队进行了以下任务:-确定了项目目标:将故障率降低到行业标准水平以下,减少返工成本和客户投诉;-确定了关键绩效指标(KPIs):故障率、返工成本、客户投诉率等。
2. 测量(Measure)阶段:在这个阶段,团队进行了以下任务:-收集了生产过程中的数据,包括故障率、返工成本和客户投诉数量;-分析了数据以了解当前生产过程的性能和偏差;-使用了一些六西格玛工具,如过程流程图和直方图。
3. 分析(Analyze)阶段:在这个阶段,团队进行了以下任务:-确定了导致故障率升高的根本原因;-使用了五力分析和鱼骨图等工具,以识别可能的原因;-根据数据和分析结果,确定了一个或多个关键影响故障率的因素。
4. 改进(Improve)阶段:在这个阶段,团队进行了以下任务:-开发了改进计划,包括减少故障率的具体措施和时间表;-实施了改进措施,并记录了结果。
5. 控制(Control)阶段:在这个阶段,团队进行了以下任务:-实施了独立检查和监控措施,以确保改善措施的可持续性;-追踪关键绩效指标,如故障率、返工成本和客户投诉;-确立了持续改进的机制,以确保过程持续优化。
通过使用六西格玛方法,该汽车制造公司成功降低了生产过程中的故障率。
在实施改进措施后,故障率从10%降低到行业标准的3%以下,成功降低了返工成本和客户投诉率。
此外,公司在生产线上建立了严格的质量控制措施和监控机制,以确保持续改进和优化。
六西格玛绿带项目案例

六西格玛绿带项目案例六西格玛(Six Sigma)是一种以数据为基础的管理方法,旨在通过减少缺陷和提高效率来改善业务流程。
在这个案例中,我们将介绍一个成功的六西格玛绿带项目,以展示这种方法如何在实际业务中取得成果。
项目背景。
这个项目发生在一家制造业公司,他们生产的产品在质量方面一直存在着一些问题。
公司决定实施六西格玛项目,以改善产品质量并提高生产效率。
为了达到这个目标,他们任命了一支由经验丰富的员工组成的团队,其中包括了一位绿带项目经理。
项目目标。
项目团队首先确定了项目的目标,他们希望通过减少产品缺陷率和提高生产效率来改善公司的整体业绩。
为了实现这一目标,他们制定了一系列的具体指标和目标,以便能够量化项目的成果。
数据收集与分析。
团队开始收集大量的数据,包括产品质量数据、生产效率数据以及生产过程中的各种参数。
通过对这些数据的分析,团队发现了一些潜在的问题,比如生产过程中的某些环节存在着不必要的浪费,以及一些常见的产品缺陷模式。
改进措施。
基于数据分析的结果,团队制定了一系列的改进措施。
他们重新设计了生产流程,优化了生产设备的配置,同时也对员工进行了培训,以提高其技能水平。
此外,团队还引入了一些先进的质量管理工具,比如故障模式和影响分析(FMEA)以及控制图等,以帮助他们更好地监控生产过程。
实施与监控。
在制定改进措施的同时,团队还制定了详细的实施计划,并建立了一套完善的监控体系。
他们定期对项目的进展进行跟踪和评估,以确保项目能够按照计划顺利进行,并且取得预期的成果。
成果与效益。
经过数月的努力,项目团队最终取得了显著的成果。
产品的缺陷率大幅下降,生产效率得到了显著提高,公司的整体业绩也得到了明显的改善。
通过这个项目,公司不仅解决了之前存在的质量问题,还为自己创造了更多的价值。
结论。
这个案例充分展示了六西格玛方法在实际业务中的应用效果。
通过对数据的深入分析和科学的改进措施,这个项目取得了令人瞩目的成果,为公司创造了实实在在的价值。
精益六西格玛案例

精益六西格玛案例
精益六西格玛是一种管理方法,它结合了精益生产和六西格玛的优点,旨在提
高效率和质量。
下面我们来看一个实际的案例,了解精益六西格玛是如何在实践中发挥作用的。
某汽车零部件制造公司在生产过程中遇到了一些问题,导致了生产效率低下和
产品质量不稳定。
经过分析,他们决定引入精益六西格玛方法来改善生产流程。
首先,他们进行价值流分析,找出了生产过程中的浪费和瓶颈。
然后,他们采
用精益工具,如5S和Kanban,对生产车间进行了重新布局和标准化。
同时,他们
还对员工进行了培训,让他们更好地理解和运用精益工具。
在改善生产流程的同时,公司还引入了六西格玛的方法,通过数据分析和流程
控制,找出了造成产品质量不稳定的根本原因,并采取了相应的改进措施。
经过一段时间的努力,公司取得了显著的成效。
生产效率得到了提高,产品质
量稳定性也得到了保障。
公司的客户满意度得到了提升,市场竞争力也得到了增强。
通过这个案例,我们可以看到精益六西格玛在实际中的应用效果。
它不仅可以
帮助企业提高效率和质量,还可以带来客户满意度和市场竞争力的提升。
综上所述,精益六西格玛是一种非常有效的管理方法,它可以帮助企业解决生
产过程中的问题,提高效率和质量,实现持续改进和持续增长。
希望更多的企业能够引入精益六西格玛,实现可持续发展。
六西格玛项目案例

六西格玛项目案例六西格玛项目是一种以改善业务流程和提高质量为目标的管理方法,它通过对现有流程进行分析和优化,以实现减少缺陷、降低成本、提高效率和客户满意度的目标。
下面我们将介绍一个六西格玛项目案例,以便更好地理解这一管理方法的具体应用。
某制造企业的生产线在生产过程中出现了频繁的故障和停机现象,导致生产效率低下,产品质量不稳定,客户投诉增加。
为了解决这一问题,该企业决定开展六西格玛项目,以改善生产线的稳定性和提高产品质量。
首先,项目团队对生产线的现状进行了全面的分析,包括生产设备、人员技能、原材料质量、生产工艺等方面的数据收集和分析。
通过对生产过程中的各个环节进行细致的观察和测量,确定了导致故障和停机的主要原因,如设备老化、操作不规范、原材料质量不稳定等。
其次,团队利用六西格玛的工具和方法,对这些问题进行了深入的分析和解决方案的制定。
针对设备老化问题,制定了定期保养和维护计划;针对操作不规范问题,进行了员工培训和技能提升;针对原材料质量不稳定问题,与供应商进行了沟通和合作,共同寻找解决方案。
在实施改进方案的过程中,团队始终保持着高度的沟通和协作,确保每一个改进措施都得到了有效的落实。
同时,团队还对改进效果进行了持续的监控和评估,以确保改进措施的有效性和可持续性。
经过几个月的努力,该企业的生产线出现故障和停机的频率显著降低,生产效率和产品质量得到了明显的提升,客户投诉也大幅减少。
这个六西格玛项目的成功实施,不仅为企业带来了经济效益,更重要的是为企业树立了良好的管理形象,提升了员工的工作积极性和创造力。
通过这个案例的介绍,我们可以看到六西格玛项目在实际应用中的重要性和价值。
它不仅可以帮助企业解决实际问题,提高经济效益,更可以促进企业内部的协作和团队精神,为企业的可持续发展奠定良好的基础。
因此,我们鼓励更多的企业和管理者,积极采用六西格玛项目的方法和理念,推动企业管理水平和竞争力的不断提升。
6西格玛课题优秀案例

6西格玛课题优秀案例
六西格玛是一种质量管理方法,旨在通过统计学的方法和工具来降低产品和服务的缺陷率,提高生产效率和降低成本。
下面是一些六西格玛课题的优秀案例:
1. LG 电子的微波炉门泄漏问题:LG 电子在制造微波炉时遇到
了门泄漏问题,这严重影响了产品质量和品牌形象。
通过使用六西格玛方法,LG 电子的团队确定了问题的根本原因,并制定了改进计划,最终成功解决了这个问题。
2. 波音公司的飞机维修成本降低:波音公司使用六西格玛方法来降低飞机的维修成本,通过分析和测量,确定了问题的的根本原因,并采取了一系列措施来减少维修成本。
这项改进不仅降低了公司的运营成本,还提高了飞机的可靠性和安全性。
3. 沃尔玛的库存管理优化:沃尔玛使用六西格玛方法来优化库存管理,通过测量和分析问题,制定了一套优化方案,成功地降低了库存成本和提高了供应链的效率。
4. 通用电气的生产效率提高:通用电气使用六西格玛方法来提高生产效率,通过分析和测量,确定了问题的根本原因,并采取了一系列措施来提高效率,最终提高了公司的盈利能力。
这些案例展示了六西格玛方法在各个领域的应用和成功的结果,不仅提高了产品或服务的质量,还降低了成本和提高了生产效率。
六西格玛绿带项目案例
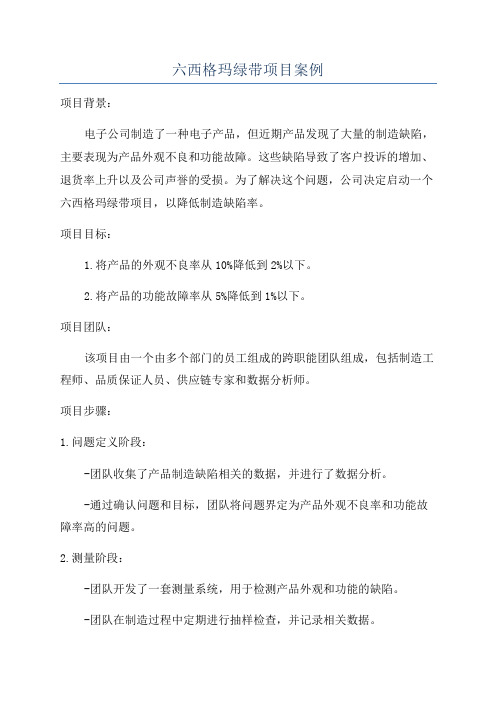
六西格玛绿带项目案例项目背景:电子公司制造了一种电子产品,但近期产品发现了大量的制造缺陷,主要表现为产品外观不良和功能故障。
这些缺陷导致了客户投诉的增加、退货率上升以及公司声誉的受损。
为了解决这个问题,公司决定启动一个六西格玛绿带项目,以降低制造缺陷率。
项目目标:1.将产品的外观不良率从10%降低到2%以下。
2.将产品的功能故障率从5%降低到1%以下。
项目团队:该项目由一个由多个部门的员工组成的跨职能团队组成,包括制造工程师、品质保证人员、供应链专家和数据分析师。
项目步骤:1.问题定义阶段:-团队收集了产品制造缺陷相关的数据,并进行了数据分析。
-通过确认问题和目标,团队将问题界定为产品外观不良率和功能故障率高的问题。
2.测量阶段:-团队开发了一套测量系统,用于检测产品外观和功能的缺陷。
-团队在制造过程中定期进行抽样检查,并记录相关数据。
3.分析阶段:-团队进行了根本原因分析,找出了导致产品缺陷的主要原因。
-通过数据分析,团队确定了关键影响外观不良率和功能故障率的因素,并进行了优先级排序。
4.改进阶段:-团队通过质量管控措施和制程改进措施降低外观不良率和功能故障率。
-团队还制定了一套培训计划,以提高员工在制造过程中的责任意识和技能水平。
5.控制阶段:-团队制定了监测和控制措施,以确保改进效果的可持续性。
-团队定期评估产品质量,并进行数据分析,以确保产品缺陷率维持在目标范围内。
项目结果:经过几个月的努力,该项目取得了显著的成果。
外观不良率从10%降低到2%以下,功能故障率从5%降低到1%以下。
产品质量得到了显著的改善,客户投诉和退货率也随之下降。
这不仅提升了产品的声誉,还为公司带来了更多的市场竞争力。
结论:通过六西格玛绿带项目的实施,该电子公司成功降低了产品制造缺陷率,改善了产品质量和客户满意度。
这个案例展示了六西格玛方法在解决制造问题和提高质量方面的有效性,并验证了该方法在减少缺陷、提高效率和降低成本方面的价值。
六西格玛管理经典案例

六西格玛管理经典案例
一、六西格玛管理经典案例之一:GE精益实施之路
GE公司,历经几个体系转变期,从企业体系和精益思想的推行,到
用六西格玛管理体系建设精益文化,大力推进GE精益实施。
在实施精益时,GE着重了解和践行客户价值,做到把握核心任务,
以及提高效率、降低成本,这是GE精益思想的本质。
GE整合了一套全面的“六西格玛管理体系”,并在全球范围内实施。
精益实施经历了6个步骤:(1)确定客户要求;(2)确定核心任务;(3)创
建团队;(4)执行;(5)实施管理系统;(6)持续改进。
另外,GE还采取了一系列有效措施来强化精益文化,如GE Vitality Index,持续改进态度等,以不断激发员工的热情,并落实精益思想。
GE精益实施的成功标志着GE有能力将精益理念扎根并落实于企业管
理实践中,让每一个员工充分意识到精益的重要性和必要性。
二、六西格玛管理经典案例之二:印度JCB公司实施精益管理
印度JCB公司是印度最大的出口制造商之一,主要生产破碎机和压路机。
由于全球化竞争日益激烈,JCB公司意识到必须推进精益制造,以提
高生产效率,提升产品质量和减少破费。
因此,JCB公司用六西格玛管理体现实施精益管理。
六西格玛项目阶段举例

六西格玛项目阶段举例引言六西格玛是一种管理方法论,旨在通过改进业务过程来提高组织的质量和效率。
在实施六西格玛项目中,通常会按照一系列阶段进行。
本文将以一个具体的项目为例,介绍六西格玛项目的六个阶段,并对每个阶段进行详细解读。
阶段一:定义阶段在定义阶段,项目团队需要明确项目的目标、范围和关键业务指标。
团队成员将收集并分析数据来确定问题的本质,并确定改进的重点。
此阶段的主要目的是确立六西格玛项目的目标和界限。
1.1 收集数据为了确保项目目标的明确性和可度量性,团队需要收集各种数据。
这些数据可以来自已有的业务过程,也可以通过调研和观察获得。
数据的收集可以通过问卷调查、面试、测量等方式进行。
1.2 确定问题在收集数据的基础上,团队需要对数据进行分析,找出其中存在的问题。
通过数据分析,团队可以识别出业务过程中存在的瓶颈、缺陷和风险,从而明确项目的改进方向。
阶段二:测量阶段测量阶段是为了评估当前业务过程的性能和稳定性。
通过测量阶段,项目团队可以了解目前的业务过程是否满足预期,并确定改进的必要性。
2.1 确定关键业务指标为了进行业务过程的测量和评估,团队需要确定一些关键业务指标。
这些指标可以是时间、成本、质量等方面的度量指标,用于度量当前的业务过程效果。
2.2 进行数据分析在测量阶段,团队需要对已有数据进行进一步分析,以便更好地了解业务过程的现状。
通过数据分析,团队可以找出业务过程中的问题,并确定可能的改进机会。
阶段三:分析阶段分析阶段的目标是深入分析当前业务过程中存在的问题,并找出产生这些问题的根本原因。
通过深入分析,团队可以确定改进措施,并制定相应的计划。
3.1 识别根本原因在分析阶段,团队需要找出产生业务问题的根本原因。
通过采用各种分析工具和技术,如因果关系图、散点图、直方图等,团队可以逐步追溯问题的根源。
3.2 开展思维导图会议为了更好地分析问题,项目团队可以组织思维导图会议。
在会议上,团队成员可以以图形化的方式展示问题和关联因素,帮助更好地理解问题的本质。
6Sigma项目运作实例(doc63)88页
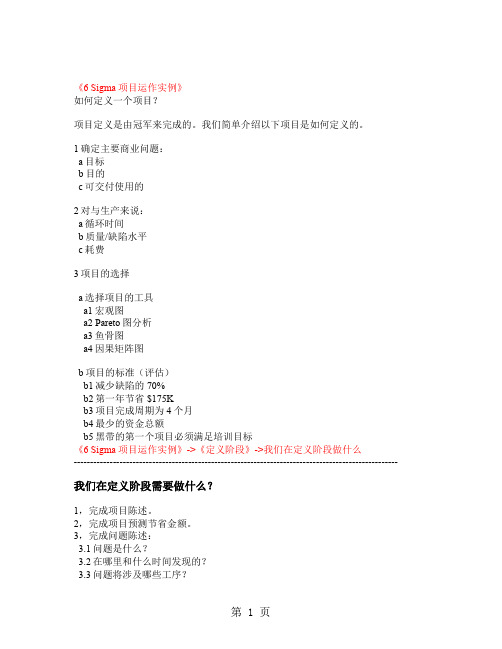
《6 Sigma项目运作实例》如何定义一个项目?项目定义是由冠军来完成的。
我们简单介绍以下项目是如何定义的。
1确定主要商业问题:a目标b目的c可交付使用的2对与生产来说:a循环时间b质量/缺陷水平c耗费3项目的选择a选择项目的工具a1宏观图a2 Pareto图分析a3鱼骨图a4因果矩阵图b项目的标准(评估)b1减少缺陷的70%b2第一年节省 $175Kb3项目完成周期为4个月b4最少的资金总额b5黑带的第一个项目必须满足培训目标《6 Sigma项目运作实例》->《定义阶段》->我们在定义阶段做什么--------------------------------------------------------------------------------------------------- 我们在定义阶段需要做什么?1,完成项目陈述。
2,完成项目预测节省金额。
3,完成问题陈述:3.1问题是什么?3.2在哪里和什么时间发现的?3.3问题将涉及哪些工序?3.4谁将受到影响?3.5问题的严重程度是什么?3.6你是如何得知这些的?4,绘制宏观图。
5,描述项目的主线。
6,完成目标陈述。
7,组成项目小组,列出小组成员。
8,完成财务评估。
《6 Sigma项目运作实例》->《定义阶段》->如何进行项目问题陈述--------------------------------------------------------------------------------------------------- 如何进行问题陈述?分六个方面进行问题陈述:1问题是什么?2在哪里和什么时间发现的?3问题将涉及哪些工序?4谁将受到影响?5问题的严重程度是什么?6你是如何得知这些的?《6 Sigma项目运作实例》->《定义阶段》->如何绘制宏观图--------------------------------------------------------------------------------------------------- 如何绘制宏观图?绘制宏观图的顺序:供应商->输入->工序->输出->客户《6 Sigma项目运作实例》->《定义阶段》->项目的目标陈述要点--------------------------------------------------------------------------------------------------- 项目的目标陈述要点:1,目标陈述2,计算方法3,全年节省额确定Team Members成员:1,小组成员要包括技术人员2,包括维修人员(如果需要)3,包括操作者4,小组人员不超过5人(特殊情况除外)。
六西格玛案例范文
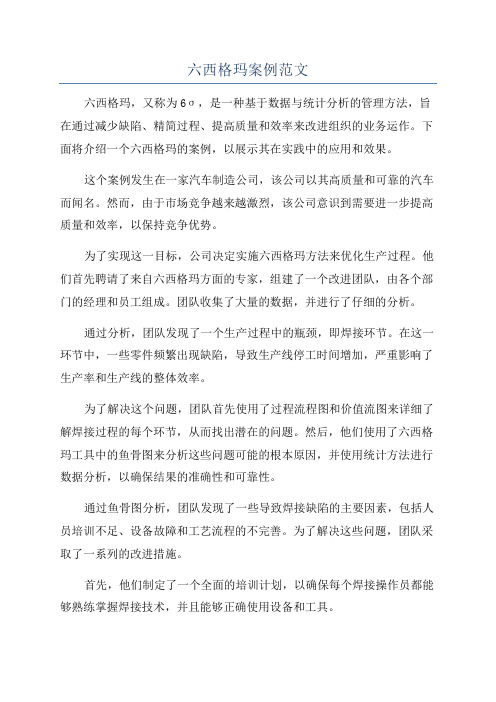
六西格玛案例范文六西格玛,又称为6σ,是一种基于数据与统计分析的管理方法,旨在通过减少缺陷、精简过程、提高质量和效率来改进组织的业务运作。
下面将介绍一个六西格玛的案例,以展示其在实践中的应用和效果。
这个案例发生在一家汽车制造公司,该公司以其高质量和可靠的汽车而闻名。
然而,由于市场竞争越来越激烈,该公司意识到需要进一步提高质量和效率,以保持竞争优势。
为了实现这一目标,公司决定实施六西格玛方法来优化生产过程。
他们首先聘请了来自六西格玛方面的专家,组建了一个改进团队,由各个部门的经理和员工组成。
团队收集了大量的数据,并进行了仔细的分析。
通过分析,团队发现了一个生产过程中的瓶颈,即焊接环节。
在这一环节中,一些零件频繁出现缺陷,导致生产线停工时间增加,严重影响了生产率和生产线的整体效率。
为了解决这个问题,团队首先使用了过程流程图和价值流图来详细了解焊接过程的每个环节,从而找出潜在的问题。
然后,他们使用了六西格玛工具中的鱼骨图来分析这些问题可能的根本原因,并使用统计方法进行数据分析,以确保结果的准确性和可靠性。
通过鱼骨图分析,团队发现了一些导致焊接缺陷的主要因素,包括人员培训不足、设备故障和工艺流程的不完善。
为了解决这些问题,团队采取了一系列的改进措施。
首先,他们制定了一个全面的培训计划,以确保每个焊接操作员都能够熟练掌握焊接技术,并且能够正确使用设备和工具。
其次,他们对焊接设备进行了全面的维护和检修,以减少设备故障和停工时间。
最后,他们重新评估了整个焊接工艺流程,并对其进行了适当的修改和优化,以确保每个环节都能够高效可靠地完成。
在几个月的改进措施下,公司观察到了显著的改进。
焊接缺陷率显著降低,生产线的停工时间大大减少,并且生产效率大幅度提高。
此外,公司还通过六西格玛方法在其他生产环节进行了类似的改进。
他们发现并解决了各种质量问题,进一步提高了产品质量和顾客满意度。
这个案例表明,六西格玛方法在管理和改进组织运作中发挥着重要的作用。
六西格玛项目案例

六西格玛项目案例六西格玛(Six Sigma)是一个以数据为基础的管理方法,旨在通过减少缺陷和提高质量来改善业务流程。
它是由美国著名的摩托罗拉公司首先引入,并在后来被通用电气公司、福特汽车公司等企业广泛应用。
六西格玛方法论通过对业务流程进行测量、分析、改进和控制,以达到减少变异、提高效率和质量的目标。
下面我们将通过一个实际的六西格玛项目案例来详细介绍这一方法的应用。
某电子制造公司的生产线上出现了一个常见问题,在组装产品时,存在着大量的次品和废品产生,导致了生产成本的增加和客户投诉的增多。
为了解决这一问题,公司决定引入六西格玛方法进行改进。
首先,团队成员收集了大量关于次品和废品产生的数据,并对生产过程进行了详细的测量和分析。
通过对数据的分析,团队发现了导致次品和废品产生的主要原因是生产线上的某个工序存在着不稳定的因素,导致产品的尺寸和质量无法得到有效控制。
接下来,团队利用六西格玛的改进工具对该工序进行了调整和优化,通过改进工艺流程和更新设备,最终成功降低了次品和废品的产生率。
随后,团队对改进后的生产流程进行了全面的控制和监测,确保改进效果的持续稳定。
他们建立了一套完善的质量管理体系,包括了定期的质量抽检、员工培训和绩效考核等措施,以确保生产质量的持续改进和稳定。
通过六西格玛项目的实施,该电子制造公司取得了显著的成效。
次品和废品的产生率明显下降,生产成本得到了有效控制,客户投诉的数量也大幅减少。
公司的生产效率和产品质量得到了显著提升,为企业的可持续发展奠定了坚实的基础。
以上就是一个典型的六西格玛项目案例。
通过对业务流程的测量、分析、改进和控制,六西格玛方法帮助企业实现了质量的持续改进和效率的提升,为企业创造了可观的经济效益和市场竞争优势。
希望这个案例能够为更多的企业和管理者提供借鉴和启示,推动六西格玛方法在各行各业的广泛应用。
六西格玛经典案例

六西格玛经典案例1. 引言六西格玛(Six Sigma)是一种质量管理方法,旨在通过降低产品和过程的变异性来提高质量和效率。
这个方法最早由日本公司Toyota引入,并于20世纪80年代由Motorola公司推广到全球。
六西格玛的核心思想是通过收集和分析数据来识别和消除导致质量问题和不必要浪费的根本原因。
在过去的几十年里,许多企业采用了六西格玛来改进其业务流程和产品质量。
本文将介绍几个六西格玛的经典案例,展示六西格玛的强大潜力和实际应用效果。
2. Motorola公司的成功案例Motorola公司在20世纪80年代是最早应用六西格玛的企业之一。
当时,该公司生产的传呼机存在严重的质量问题,导致市场份额大幅下降。
为解决这个问题,Motorola决定采用六西格玛方法来改善产品质量。
Motorola首先对传呼机生产过程进行了详细的调查和数据分析,找出了导致质量问题的根本原因。
然后,他们采取一系列措施来消除问题,如改进生产设备、培训员工和优化生产流程。
结果,Motorola成功地降低了传呼机的缺陷率,提高了产品质量,并重塑了自己在市场上的形象,重新夺回了市场份额。
这个案例显示了六西格玛的实际效果,并证明了通过数据分析和改善措施可以显著提高产品质量。
3. General Electric公司的成本降低案例General Electric(GE)是一个全球性的多元化企业,拥有众多业务部门。
在90年代初,GE公司面临着巨大的竞争压力和成本问题。
GE采用六西格玛方法来降低成本,并在其电力业务部门中开展了一项改进项目。
该项目通过分析电力设备的生产流程,并使用六西格玛工具找出了浪费和低效的环节。
随后,GE采取了一系列措施来改进生产流程,降低成本,如优化设备配置、改进工作流程和培训员工。
通过六西格玛项目的实施,GE成功地降低了电力设备生产的成本,并提高了生产效率。
这个案例证明了六西格玛可以应用于各种行业和业务部门,帮助企业降低成本、提高效率。
六西格玛的成功案例分析
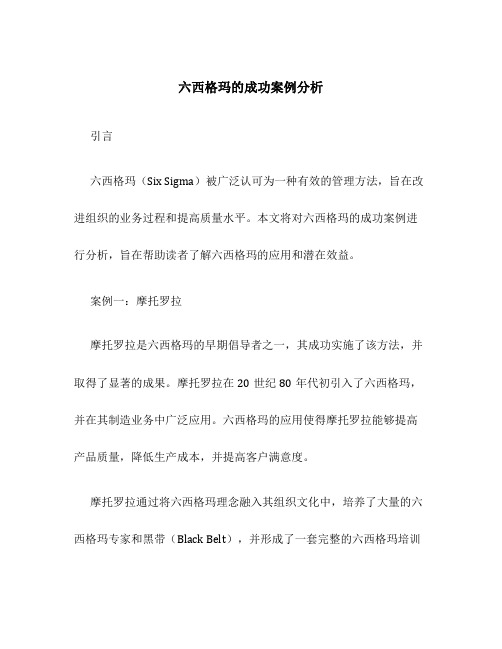
六西格玛的成功案例分析引言六西格玛(Six Sigma)被广泛认可为一种有效的管理方法,旨在改进组织的业务过程和提高质量水平。
本文将对六西格玛的成功案例进行分析,旨在帮助读者了解六西格玛的应用和潜在效益。
案例一:摩托罗拉摩托罗拉是六西格玛的早期倡导者之一,其成功实施了该方法,并取得了显著的成果。
摩托罗拉在20世纪80年代初引入了六西格玛,并在其制造业务中广泛应用。
六西格玛的应用使得摩托罗拉能够提高产品质量,降低生产成本,并提高客户满意度。
摩托罗拉通过将六西格玛理念融入其组织文化中,培养了大量的六西格玛专家和黑带(Black Belt),并形成了一套完整的六西格玛培训和认证体系。
通过推广六西格玛观念和方法,摩托罗拉实现了持续的质量改进,提高了员工的参与度和责任感。
在实施六西格玛后,摩托罗拉的产品质量得到了显著提升,不良品率大幅下降。
通过识别和解决生产过程中的潜在缺陷和变异源,摩托罗拉有效减少了质量问题,提高了产品可靠性。
同时,摩托罗拉通过引入六西格玛的方法和工具,优化了生产流程,降低了生产成本。
摩托罗拉的成功案例证明了六西格玛的有效性和可行性。
通过将六西格玛作为组织文化的一部分,并培养专业的六西格玛人才,组织可以实现质量的持续改进和业务的长期成功。
案例二:通用电气通用电气(GE)是另一个成功应用六西格玛的组织。
GE在20世纪80年代末开始采用六西格玛方法,以提高质量和降低成本。
GE通过六西格玛的实施,将质量管理融入到其核心业务流程中,并将六西格玛作为一种战略工具来推动组织的整体改进。
GE通过六西格玛的应用,实现了巨大的业绩提升。
通过减少产品缺陷和变异性,GE显著降低了质量成本,并提高了产品的可靠性和性能。
六西格玛还促使GE改进了业务流程,提高了效率和生产能力。
通过准确识别和解决问题的方法,GE加强了内部交流和团队合作,提高了员工士气和工作满意度。
GE将六西格玛作为一种战略驱动的改进方法,结合了其他管理理念和工具,如LEAN和业务流程再造。
六西格玛成功(6sigma)案例学习[优秀范文五篇]
![六西格玛成功(6sigma)案例学习[优秀范文五篇]](https://img.taocdn.com/s3/m/51b2a8e3c0c708a1284ac850ad02de80d5d80658.png)
六西格玛成功(6sigma)案例学习[优秀范文五篇]第一篇:六西格玛成功(6sigma)案例学习6sigma成功案例**电子:步伐稳健行走于6σ之路2000年12月,第十届台湾品质奖的颁奖典礼上,在评审“品质不折不扣”的理念下,**电子以多年来致力追求品质的决心与成就,脱颖而出,获得台湾品质奖。
细察**电子追求品质的努力、实践品质的过程,得以知道这个奖得来实至名归。
**电子自1994年起,就在董事长许胜雄的领导下,努力实践6σ(Six Sigma)的品质策略。
何谓6σ?σ在字面上的定义是为统计学上的标准差,简单来说,σ是一个测量品质的标准工具,它代表一种绩效目标,也是一种品质改善的观念。
达到6σ表示每百万次中只会出现3.4个错误,几乎等于零缺点。
σ曾经协助许多世界级企业展现惊人的成绩,它曾经使通用电气(GE)公司迈向营运的高峰,被杰克韦尔奇称许为通用所采用的过最重要的管理措施;也是西方企业力抗日本企业反败为胜的法宝。
提起**电子导入6 σ的原由,**电子副总经理陈乃源表示:“起源于为了满足顾客对品质的要求。
”在未实行6 σ前,**电子所生产的产品错误率颇高,无法达到客户满意,除容易引起顾客的抱怨,相对也缺乏竞争力。
为了提高竞争力,**电子决定导入6 σ。
当时**电子派遣了一批人员到美国接受6σ的训练课程,其中成员包含总经理、数位副总及相关人员,陈乃源也是其中之一。
受训回国后,陈乃源全心投入**电子执行6 σ的架构规划。
陈乃源指出:“实践6 σ的基本原则,是以顾客需求为出发点,一切改善都必须以顾客需求为主,它讲求从制造过程开始改进,而不是看产品产出最后的结果,因为产品事后的修补往往要花费更多的成本。
品质改善最重要的是要从根源做起,也就是在设计时就减少错误的机会。
尤其是在产品生命周期急速缩短的今天,已没有时间让你尝试错误了,也无法再像过去一样等生产过程结束后再统计错误,必须在设计的时候就减少错误的发生,把线上的制程能力及零件的制造能力都计算、考虑进去,让产品合于标准,将制造流程改善,一次就做好,使得后续不至于有错误发生。
6SIGMA__DMAIC方法案例

六西格玛管理法导论
鱼骨形图/因果图:CAUSE & EFFECT DIAGRAM
技术 环境
人员
协调作业技 术不成熟
公司的系统 环境不允许 公司内部网 速度太慢
软件
对软件不熟悉
没有意识到 技术的存在
企业没有利 用高科技减 少差旅费用
软件没有得到 安装和调试
六西格玛管理法导论
柏拉图法则:PARETO CHART
LSL
USL
1,000,000 100,000
-4 0 -3 0 -2 0 -1 0 0 1 0 2 0 3 0 4 0 5 0 6 0
Actual (LT) Potential (ST )
Process Demographics
Date: Re p o rte d b y: P ro je ct: De p a rtm e n t: P ro ce ss: C h a ra cte ri sti c: U n i ts: Upper Spec: 20 L o we r S p e c: -1 0 Nom inal: O p p o rtu n ity:
六西格玛管理法导论
改进路线图<DMAIC&ANOVA方差分析 • t-检验 • 流程分析
定义
• 总则 • VOC • SIPOC • CE 矩阵
测量
• 数据采集计划 • Gage R&R • 控制图表 • 性能分析
控制
• QC 图表 • 文件整理 • 监控
改善
• 确定解决方案 • 风险分析 • 试行 • 计划
找出问题的根源 与提供解决方案
分析
从这里开始
6 Tools
提炼与实施方案
成为一名合格 的黑带
- 1、下载文档前请自行甄别文档内容的完整性,平台不提供额外的编辑、内容补充、找答案等附加服务。
- 2、"仅部分预览"的文档,不可在线预览部分如存在完整性等问题,可反馈申请退款(可完整预览的文档不适用该条件!)。
- 3、如文档侵犯您的权益,请联系客服反馈,我们会尽快为您处理(人工客服工作时间:9:00-18:30)。
《6 Sigma项目运作实例》如何定义一个项目?项目定义是由冠军来完成的。
我们简单介绍以下项目是如何定义的。
1确定主要商业问题:a目标b目的c可交付使用的2对与生产来说:a循环时间b质量/缺陷水平c耗费3项目的选择a选择项目的工具a1宏观图a2 Pareto图分析a3鱼骨图a4因果矩阵图b项目的标准(评估)b1减少缺陷的70%b2第一年节省 $175Kb3项目完成周期为4个月b4最少的资金总额b5黑带的第一个项目必须满足培训目标《6 Sigma项目运作实例》->《定义阶段》->我们在定义阶段做什么--------------------------------------------------------------------------------------------------- 我们在定义阶段需要做什么?1,完成项目陈述。
2,完成项目预测节省金额。
3,完成问题陈述:3.1问题是什么?3.2在哪里和什么时间发现的?3.3问题将涉及哪些工序?3.4谁将受到影响?3.5问题的严重程度是什么?3.6你是如何得知这些的?4,绘制宏观图。
5,描述项目的主线。
6,完成目标陈述。
7,组成项目小组,列出小组成员。
8,完成财务评估。
《6 Sigma项目运作实例》->《定义阶段》->如何进行项目问题陈述--------------------------------------------------------------------------------------------------- 如何进行问题陈述?分六个方面进行问题陈述:1问题是什么?2在哪里和什么时间发现的?3问题将涉及哪些工序?4谁将受到影响?5问题的严重程度是什么?6你是如何得知这些的?《6 Sigma项目运作实例》->《定义阶段》->如何绘制宏观图--------------------------------------------------------------------------------------------------- 如何绘制宏观图?绘制宏观图的顺序:供应商->输入->工序->输出->客户《6 Sigma项目运作实例》->《定义阶段》->项目的目标陈述要点--------------------------------------------------------------------------------------------------- 项目的目标陈述要点:1,目标陈述2,计算方法3,全年节省额确定Team Members成员:1,小组成员要包括技术人员2,包括维修人员(如果需要)3,包括操作者4,小组人员不超过5人(特殊情况除外)。
《6 Sigma项目运作实例》->《测量阶段》->如何进行项目描述--------------------------------------------------------------------------------------------------- 如何进行项目描述:1,目标陈述2,Metric 图3,月节省额如何绘制工艺流程图:召集小组:流程图绘制是集体努力的结果小组包括:流程负责人:项目结果的负责人工程部门-工艺,产品,设计及设备生产部门-操作员,各班次主管,培训员,操作班长,维修技师流程图所需信息脑力风暴观察/经历操作手册工程标准,工作指示六大方面(人,机,方法,测量,材料,环境)确定工艺范围:范围至观重要越窄越好!大量工艺步骤可能表明项目定义不佳或问题源于几个项目问题藏于问题中若问题可以由粗略分析解决,管理层会去做绘制可执行的工艺图你能确认缺陷来源吗?我们能有意识地改变输入指标变量吗?有意识的改变输入指标变量能直接影响输出结果吗?工艺流程图(PFD):6 Sigma 工艺流程图的要素:所有工艺步骤包括隐形工厂数据采集点所有设备/工具各步骤表明增值性(VA)和非增值性(NVA)控制标准文件用标准符号绘制工艺流程:在Microsoft OfficeTM 等软件中可找到工艺流程图-程序:绘制工艺记载的工艺步骤包括所有检查点,测量指标和传运步骤确认所有数据采集点标示各工序标准控制文件各步骤标明为增值性(VA)或非增值性(NVA)确认各工艺步骤的 X 和 Y标明可能消除的NVA 步骤加入并标明“隐形工厂”工段标明为VA或NVA,标明可能消除的步骤标明须指定控制文件的步骤加入DUP,RTY,COPQ,循环周期等估计值标明须进行量具和工艺能力研究的步骤通过直接或秘密观察确认准确性文件记录/确认:文件记录的工艺流程首先绘制记录下来的工艺加入并标明隐形工厂步骤当所有步骤展示出来后,流程图就属于实际工艺确认流程图的准确性至关重要项目组必须花时间观察工艺秘密进行。
观察导致行为改变确认实际工艺设置与记录的设置相同跨班跨机器观察工艺如何绘制工艺流程细图:工艺流程细图:6 Sigma 工艺流程图要素:工艺或产品是输出指标Y和输入指标X标准上下限和标准控制文件所用设备/工具绘制工艺流程细图工艺流程细图必须依工艺流程图而画。
更改其一应在另一个中反映出来。
应使用最新的控制文件标明所有隐形工厂步骤的输入输出指标工艺流程细图程序:1,从流程图中列出工艺步骤2,加入下列内容输出指标输出指标标准,若存在输入指标输入指标标准,若存在工艺能力或量具能力指标所用设备3,标明隐形工厂步骤4,标明各步骤属于增值性(VA)或非增值性(NVA)5,标明各步骤属于可控性的(C)或噪音性的(N)6,确认各设备的输入指标设置7,确认流程图准确性8,必要时更改及更新流程标准限和工艺能力:工艺及产品标准加入X的工艺设置加入Y 的标准限标明未记录的Y和可控的X测量系统加入量具重复性及复验性数据标明须做测量系统分析的量具工艺能力展示RTY,DPU,CPK等的估计值标明哪些工艺步骤数据陈旧或不完整而需做工艺能力分析更改及更新:更改记住:6 Sigma 的目标之一是找出:Y=F(X)随着对工艺的深入了解,更新工艺图以反映新的信息更新项目最终成果之一是现有的工艺的流程图更新工艺图以反映任何工艺改变加入测量系统分析及工艺能力分析结果精简制造与5S:精简制造例似于日本的5S精简制造与5S:鱼骨图:鱼骨图一种系统确认所有可能导致问题(后果)产生的原因方法。
构造鱼骨图的方法:1. 陈述问题,并置于右边的方框内2. 朝方框画一水平箭头。
3. 在箭头上下写上传统因素类型名称*或你怀疑是的类型名称。
用直线连到箭头线上。
4.在各主要的类型范围内,集思广益并列出所有可能引起问题发生的因子。
5.进一步优化:对各种详细列出的因子再列出其输入变量。
*6m--man, machine ,method, measurement, mother nature (environment)(6M:人员,机器,测量方法,原材料,环境)定性测量系统研究:定性型量具 R&R -术语:检验员分数(%)-在定性型R&R检验过程中,检验员前后一致的比例定性数据--定性(合格/不合格)数据,可用来做记录和分析定性型测量系统--把每个部件与标准进行比较,从而决定部件是否符合标准的测量系统。
消费者偏见--员工倾向把合格产品判为废品有效筛选分数(%)--在定性型R&R检验过程中,所有员工本身前后一致且相互之间也一致的比例。
标准值--由一个高准确度量具所测的平均值生产者偏差--员工倾向于把不合格(有缺陷的)产品判为合格筛选--用检验方法对产品进行100%的评估筛选有效性--定性量具系统区别合格与不合格的能力使用定性型量具 R&R 的目的:工艺评估评估你的检查标准或工作质量标准与客户要求的一致性确定所有班次,机器等的检查人员是否使用相同标准来决定合格与不合格量化检查人员准确重复其检验结果的能力确定检查人员与“已知标准”的一致性及倾向于消费者偏差还是生产者偏差工艺改进发现是否需要培训,缺少工序或缺乏标准定性型量具 R&R 的方法:准备从工艺中挑选30个部件,50%合格,50%次品可能的话,挑选近乎于合格和不合格样本挑选检查人员--受过完全培训的和有资格的实施要求每一个检查人员随机地检查部件,决定合格与不合格并重复此检查评估将结果载入文件如果必要,采取适当的措施调整测量工艺重做R&R试验,核实调整后的有效性定性型量具 R&R --结论:检查员分数如果大多数员工都是100%,则培训作用极为有限筛选有效分数如果员工本身前后一致但是相互间不一致,则重新培训可帮助减少错误。
标准化分数如果员工时常与标准不一致,则需要改变测量系统(或局部标准)工艺能力分析:为何测量工艺能力?使我们根据数据分配资源!(这可不常见!)缺陷率得以量化确认可以改进机会分析工艺能力可使组织预测其所有产品和服务的真实质量水平确认工艺发生问题的本质-居中程度或分散度工艺能力研究连续数据离散数据1.确认标准限 1.确认标准限2.收集数据 2.收集数据3.确定短期偏差 3.决定:短期还是长期?4.计算工艺能力指标:(通常是长期)a.短期: 4.计算工艺能力指标:Ⅰ ZU,ZL a.长期:Ⅱ CP Ⅰ PPMⅢ CPK Ⅱ Sigma水平ZLTⅣ Sigma水平ZST Ⅲ PPKb.长期: b.短期:Ⅰ Sigma水平ZLT Ⅰ Sigma水平ZSTⅡ PPK Ⅱ CPK工艺能力计算实例一位技师负责医院设备的蒸汽杀菌过程。
其中一个关键参数是控制“暴露”阶段的温度。
设备室温度和在最小饱和蒸汽浓度的周期时间决定杀菌程度在整个设备室维持前后一致的温度范围很重要。
第一步:确认标准这一阶段常被忽视。
我们如何设定标准?设计部门-设计蓝图设计部门如何得到各项要求?工艺部门-标准由工艺以前能够做到的或开始使用时的能力定这想法有错吗?客户我们总是对客户说可以吗?对上例而言:设备室目标温度是1250C±1.50C第二步:采集数据-合理编组应采集数据获得“短期”性能,如可能,“长期”性能通过固定时间区间采集一系列快照型数据应按合理编组采集快照数据什么是合理编组?从流程连续不断产生的零件或产品中合理取样以期捕获最小工艺偏差的方法组内偏差反映一般偏差平均标准差(用一种均方差方法平均)是对工艺应有能力的良好估计第二步:采样-例子例子:技师在暴露周期从控温探针读数中选取五个数据,并从连续七个杀菌运转周期采集数据,数据列在ChamberTemp2.mtw文件的杆ChambTemp栏中第三步:确定短期偏差多数现有数据居于长期和短期之间为了估计真实短期数据:小心设计工艺能力研究方法确保编组策略合理某些工艺无法研究短期数据如低产量和长循环周期工艺采样昂贵或难以取样的工艺第三步:短期还是长期?一个指导思想:如果允许80%的输入指标在其自然范围内浮动,数据就是长期的短期及长期:组内及组间平均标准差与总标准差对各组方差取平均值可得到组内标准差的平均值总标准差由所有数据算出,不计编组平均标准差不计组间偏差,而总标准差计入组间偏差平均标准差是对组内标准差的最佳估计长期和短期指导思想短期数据在有限的周期或间隔采集数据在有限的机器和员工中采集差不多总是连续变量长期数据在很多的周期,间隔,机器和员工中采集可以是离散或连续数据离散数据几乎都是长期性的第四步:计算ZU和ZL:Z-分数提供统计数据以便用共同语言交流提供一个与标准上下限相关的工艺性能指标第四步:计算CP例子工艺平均值为325标准差为15标准上限为380,下限为270CP是多少?若平均值为 355而标准差不变CP又是多少?Cp与工艺应有能力Cp是工艺应有能力的良好指标工艺应有能力--一个工艺观察到的最好的短期性能机会--工艺长期性能与工艺应有能力间的差距Sigma项目--致力与把长期性能与工艺应有能力的差距缩短定量测量系统研究:定性型量具 R&R --模型测量系统μ总和=μ工艺+Δμ测量系统偏离度:观察值=实际真实值+测量偏移通过“校准计划” Δ测量偏移来评估真实值测量值(准确度)测量系统σ2 总合=σ2工艺+σ2测量系统偏离度:观察的偏差=工艺的偏差+测量的偏差通过“校准计划”来评估真实值测量值(准确度)测量系统的指标:量具R&R结果->量具偏差(σmeasurement system )真实值精确度(量具偏差)观察值测量系统的精确度(P):精确度包括重复性和复制性测量系统的指标-PT:精确度与公差之比--P/T代表量具偏差占公差的部分此部分通常用百分数来表示最好的情形P/T<10%--可接受的P/T<30%测量系统的测量方法--P/TV:精确度与总偏差之比代表量具偏差占据总偏差的部分此部分通常用百分率来表示最好情形<10% 量具可接受条件<30%测量系统的指标--分辨指数 :分辨指数是测量系统从工艺数据中可辨认的不同读数的数量分辨指数是一个分辨率指标分辨指数是重复性和复制性的函数最好情形:>4 ,可接受的:3-4P/T 和 P/TV 的用处:P/T (% 公差)最常用于测量系统的精确度评估将量具的精确度与公差要求进行对比如果量具用来对生产样品进行分类 P/T 还可以P/SV(%R&R)--6 Sigma 首选测量量具与量具研究偏差相比其性能如何最适合进行工艺改进的评估使用时应小心。