影响塑料凹印套印的因素
塑料制品出现凹痕的原因及解决方法

塑料制品出现凹痕的原因及解决方法(时间:2007-12-21 15:55:43 共有685人次浏览)一、产生凹痕的原因1 、制品各部分厚度不同2、模具内在压力不足3、模具冷却不充分4、由于冷却时间不足而产生的变形二、相关联的知识1、在生产制品过程中,凹痕是不良现象中发生频率最高的,注入模具的塑料在冷却时发生体积收缩,早冷却部分即表面首先硬化,内部就会产生气泡,所谓凹痕,就是冷却慢的部分在气泡收缩的方向产生了显眼的凹面。
2、收缩性大的材料也容易产生凹痕。
当要改变成型条件来消除凹痕时,应该把设定条件往收缩小的方向设定。
即模温、料筒温度降低,射出压力提高,但是应该注意由此可能会引起残余内应力。
3、因为凹痕以不显眼为好,所以,如果不影响外观的时候,有故意在模具上加工成腐蚀的模样,例如纹状、粒状等。
还有,如果成型材料是HIPS时,用降低模温来降低光洁度也有效果。
但是这些方法一旦有凹痕发生,想修理磨光制品就有困难。
三、解决的方法1、即时:提高射出压力,延长射出保压时间,降低料筒温度和模具温度,在产生凹痕的地方强制冷却。
2、短期的:在产生凹痕的地方补上流边。
在产生凹痕的地方的材料通边有狭小的场所时,把这部分边厚。
3、长期的:应彻底避免设计制品厚度的差异。
容易产生凹痕的加强筋,狭长的形状应尽量短。
四.于材料的差异成型收缩性大的材料,凹痕也大。
例如PE、PP,即使只要稍微的加强筋,就会产生凹痕。
材料成型收缩率PS 0.002~0.006PP 0.01~0.02PE 0.02~0.05五、参考事项:1、当温度降低到不产生凹痕时,如果在模腔内的材料还有压力,应该考虑到不会产生凹痕了。
围绕在模具内的材料在模具内的压力即静压力,无论什么地方都是不一定的。
接近浇口部分的压力高,如果材料的通边宽,因为到各个角落的压力的传递,近浇口同远离浇口的地方的压力差跟全体的压力相比相差很小就不会产生凹痕,也就能得到不残留内部应力的制品。
凹版印刷问题

印刷师傅的操作
油墨的稀释度和干燥速度
网纹辊的网线和印版的网线是否搭配
还有就是你的印刷材质和油墨是否搭配
若想了解更清楚的话电话详谈18757540377
要把油墨粘度控制合适,浅网多墨清点好,适当加慢干,丙二醇甲醚效果最好。或是丁酯。
印刷机收料气胀轴气怎么打不饱啊?请问下什么原因?
(2)油墨黏度与刀线
印品出现刀线与油墨黏度有着直接关系。油墨的黏度越高,印刷中越容易产生刀线和干版,解决方法是向油墨中加入适量的溶剂,以降低油墨黏度,增加油墨的流动度,细小的流丝状刀线一般就会消除。
通常,印刷操作人员是用量杯来测量油墨黏度,用手工添加溶剂的方法来调整,但如此操作难以保证油墨黏度的稳定性,且降低了生产效率。因此,油墨黏度的控制技术有待
原膜死皱还调什么哦!废料了!
如果你确定印刷胶辊没问题的话,两端压力应该相等的。
气缸侧小螺丝是微调气量
你所说的如果是死皱横褶 靠调整气缸螺丝肯定不行的 你得在气压阀上调节试试 先把一边气压降到最低试下两头气压是否平衡 再看胶辊有无变形
塑料凹印如何减少油墨色差
(1)油墨黏度与色偏
根据客户样稿调准的油墨,其色相与签样基本一致。但随着印刷厂的进行,油墨中的溶剂挥发而变稠,印品颜色偏深;当操作人员向油墨中补充大量溶剂后,油墨变稀,印品颜色偏浅。如此反复会造成印刷品色偏加大。
套色精度差套色精度差套色精度差套色精度差::::
故障现象: 纵向、横向套印达不到要求或不稳定。
原因: 1、薄膜牵引时张力变动太大。
2、放卷装置的卷筒制动器调节不当。
3、卷筒料过多,收卷太松。
当一个新技术在研制并发展过程中时,它要经历很多年去寻找自己的道路以投入到商业生产应用中。例如,激光、微处理机、静电照相以及LCD都经过了大约30年时间才发展成熟。喷绘印刷的定义首先由英国的LordKelvin在19世纪60年代提出,随后德国科学家Hertz在20世纪30年代有了突破性进展。但是我们拥有的热敏和压印喷绘印刷技术是在20世纪80年代发展起来的,最
塑料凹印常见故障原因及解决办法

塑料凹印常见故障原因及解决办法在凹版印刷过程中往往会发生一些由机械、工艺原辅材料、工作环境等因素引起的印刷故障,从而影响产品质量和生产进度,现将在从事凹印工作中积累的实用经验介绍给大家,供机组及业务人员参考。
故障一:油墨印刷后外溢故障原因:(一)使用的油墨中含有水分,而油墨本身是溶剂型的;(二)印刷基材上吸附有水分;(三)印刷车间湿度太大;(四)干燥温度过低;(五)印刷车速过快,压印力太大;(六)油墨的调配过稀,粘度太小;解决方法:严格控制印刷车间温湿度,温度在18—25度,湿度在50%-60%为最佳。
防止油墨中混有水分,对吸湿性较强的基材膜进行印刷时,可以把印刷的第一色机组作为干燥单元,使这些基材膜在第一色单元的加热烘道中干燥脱水后再进行印刷;对吸湿性不强的基材膜进行印刷时,若发生油墨外溢,可通过减小压印力,提高干燥温度、加大油墨粘度或降低刷车速的办法来解决。
故障二:油墨色相不良故障原因:(一)油墨在使用过程中分离沉淀,油墨中的颜料微粒发生凝聚现象;(二)网点的再现性不良;(三)添加了不同期生产的油墨或不是同种厂家的油墨。
解决方法:首先要保证油墨的循环流动,尽量避免比重有明显差异的油墨相混合,防止混入水分,因水分会有损于油墨的流动性,严重时还会造成颜料的凝聚。
其次要严格控制印刷速度、油墨粘度等各项变化条件对中间调网点为影响,必须保持这些条件的恒定性,并用放大镜对印刷品随时检查。
另外要禁止不同期或不同厂家生产的油墨混合使用。
故障三:油墨粘着力不强故障原因:油墨粘着力不强的主要现象是印刷品上墨层达不到客户要求的厚度,严重时印刷品会脱墨或印不上。
造成这种现象的主要原因是以下几方面:(一)选用了不同期或不同厂家生产的油墨;(二)印刷用基材膜处理不当或基材膜中添加剂对印刷有影响;(三)油墨白化或变质;(四)添加溶剂过量;(五)未有充分干燥。
解决方法:应绝对不混用不同厂家或不同期生产的油墨。
对印刷基材膜事先检验其是否进行过电晕处理。
八种常见薄膜凹印故障的成因、对策

书山有路勤为径;学海无涯苦作舟
八种常见薄膜凹印故障的成因、对策
本文全面的整理了薄膜凹印过程中常见的八种故障的成因及对策,方便大家遇到问题时进行查看。
八种塑料薄膜凹版印刷故障的排除
1、套色不准
(1)薄膜张力变动,使纵向印刷套色变动。
应调整各张力控制装置,如调节放卷装置的卷筒制动器;合理设定辊筒的转速;提高辊面摩擦力;调整复卷机的卷取张力等。
(2)印刷滚筒有径差,一、二、三色印版滚筒的直径依次增粗或减细,引起纵向印刷套色变动。
应重新制版。
(3)规矩线密度不足,印刷套色纵向偏移。
应调整光电管的敏感度及排除印版的糊版故障。
专注下一代成长,为了孩子。
塑料凹印过程中的相关问题
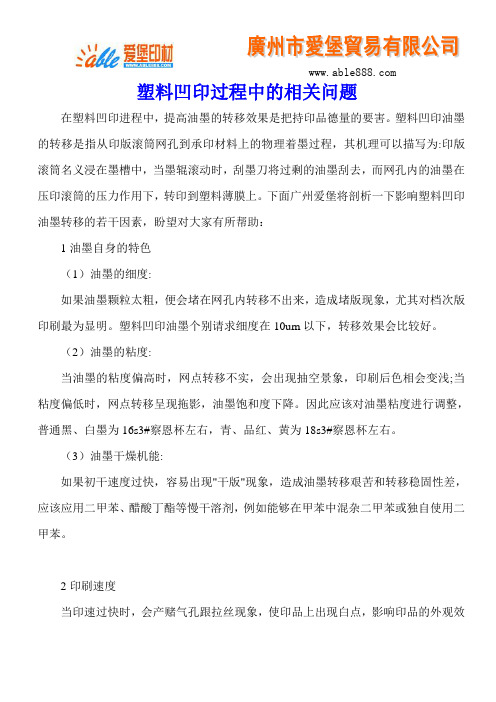
塑料凹印过程中的相关问题在塑料凹印进程中,提高油墨的转移效果是把持印品德量的要害。
塑料凹印油墨的转移是指从印版滚筒网孔到承印材料上的物理着墨过程,其机理可以描写为:印版滚筒名义浸在墨槽中,当墨辊滚动时,刮墨刀将过剩的油墨刮去,而网孔内的油墨在压印滚筒的压力作用下,转印到塑料薄膜上。
下面广州爱堡将剖析一下影响塑料凹印油墨转移的若干因素,盼望对大家有所帮助:1油墨自身的特色(1)油墨的细度:如果油墨颗粒太粗,便会堵在网孔内转移不出来,造成堵版现象,尤其对档次版印刷最为显明。
塑料凹印油墨个别请求细度在10um以下,转移效果会比较好。
(2)油墨的粘度:当油墨的粘度偏高时,网点转移不实,会出现抽空景象,印刷后色相会变浅;当粘度偏低时,网点转移呈现拖影,油墨饱和度下降。
因此应该对油墨粘度进行调整,普通黑、白墨为16s3#察恩杯左右,青、品红、黄为18s3#察恩杯左右。
(3)油墨干燥机能:如果初干速度过快,容易出现"干版"现象,造成油墨转移艰苦和转移稳固性差,应该应用二甲苯、醋酸丁酯等慢干溶剂,例如能够在甲苯中混杂二甲苯或独自使用二甲苯。
2印刷速度当印速过快时,会产赌气孔跟拉丝现象,使印品上出现白点,影响印品的外观效果;当印速过低时,油墨转移也会受到影响,表示为流平性不好,色相偏浅且不平均。
因而印刷速度应该满意承印材料的适应范畴。
3制版方面不同制版工艺发生的网孔外形、宽度和深度均会对油墨转移的效果有很大的影响。
在塑料凹印中,应该依据承印材料的性质断定版深及加网线数。
如果网穴太浅,没印多久就会被磨平,从而使网穴中的油墨量减少,影响油墨转移效果。
因此应该在保障品质的条件下,将网穴雕刻得深一些。
4刮墨刀刮墨刀的角度和品种会影响刮墨效果和印版网孔内的着墨量。
调小刮刀压力、采用软刀片、恰当减小刀的角度,均可以改良油墨的转移效果。
另外,假如刮墨刀离印版压印线较远,小网穴里的油墨轻易干结,涌现"干版"现象,因此应该将刮墨刀往前推,离压印线近些,这样有利于刮墨刀将多余油墨刮去,使网孔内的油墨很好地转移到承印资料上。
影响凹版印刷套印不准的因素

影响凹版印刷套印不准的因素对于高速的凹版印刷,大多数凹印机都采用了自动套准控制装置。
套准控制系统是凹版印刷机的重要组成部分,其主要功能是对印刷品各色组的套印情况进行实时跟踪、检测和调节。
套准控制装置主要由光电扫描器、横向套准调节机构和纵向套准调节机构等组成,对套印误差的跟踪、检测,主要由光电扫描器来完成;套印误差的调节则由横向套准调节机构和纵向套准调节机构共同来完成。
驱动电机通过控制纵向套准调节机构、驱动补偿辊来改变印刷路径的长度或改变版辊的相位,从而实现纵向套准调节。
横向调节则是根据检测的误差来调节版辊的横向相对位置。
1.设备精度因素设备本身的机械制造精度和设备所使用的计算机自动控制系统的精度是影响套准精度的决定性因素。
如:牵引辊、导辊等的加工精度。
另外,设备安装精度对印刷套准也有重要影响,如:导辊的平行度和水平度等。
所以,要获得高精度的套准,必须要首先保证印刷设备达到足够的精度,同时,还要做好设备的日常维护、保养和定期检测、检修,保证设备运转在最佳状态。
2.套准控制装置因素只有套准控制装置正常工作,才能保证印刷套准。
如果其中的任一组成部分出现故障,都会引起套印不准。
如:开关没有接通;电眼位置偏离检测位置或沾有杂物;玛克线太浅;磁性传感器有问题;套准系统存在机械故障……如果出现套印不准现象,就要对上述可能存在的故障进行逐一检查、排除。
3.承印物张力因素印刷过程中,承印物张力变化范围小,套印精度就容易控制。
反之,如果张力变化频繁,无规律可循,则会严重影响套准精度。
所以,在设定合理的张力后,还应保持最小范围的张力波动,即保持张力的稳定。
而造成张力不稳的主要因素有:自动张力控制系统的部件损坏;气压不稳;温度、湿度的变化;运行过程中速度的变化;承印物与导辊之间摩擦系数的变化;承印物厚薄的变化;接卷时引起的放卷部分的张力波动……明确了这些因素,我们就应在实际操作中尽量避免或者减少此类因素的影响,从而达到准确套印的目的。
塑料薄膜凹印套印不准问题分析
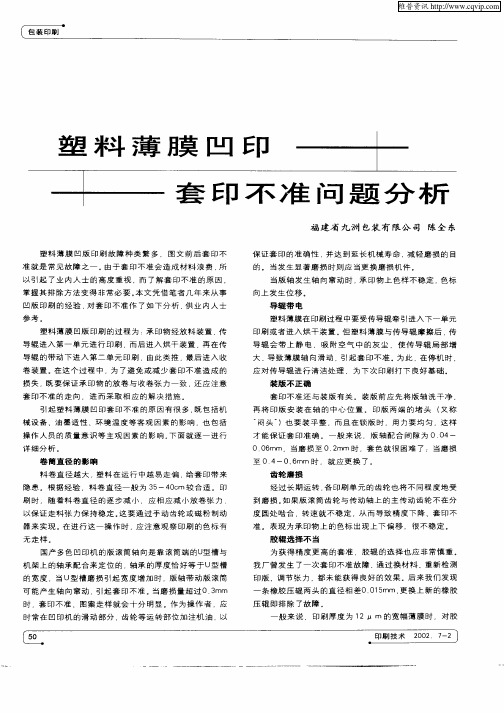
参考 。
塑 料 薄膜 凹版 印刷 的 过 程 为 : 印物 经 放 料 装置 . 承 传
印刷 或 者 进 入 烘 干装 置 。 塑料 薄 膜 与 传 导辊 摩 擦 后 . 但 传 导辊 会 带 上 静 电 .吸 附空 气 中 的 灰 尘 .使 传 导 辊 局 部 增 大 . 致 薄膜 轴 向滑 动 , 起 套 印不 准 。为此 , 导 引 在停 机 时 .
详细分析。
再将 印 版 安 装 在 轴 的 中心 位 置 。 印 版 两 端 的 堵 头 ( 称 又 闷 头 )也 要 装 平整 ,而 且 在锁 版 时 ,用 力要 均 匀 .这 样 才 能保 证 套 印准 确 。一 般 来 说 .版 轴配 合 间 隙为 0 0 ~ 4
0 06m m
可 能 产 生 轴 向 窜 动 .引 起 套 印 不 准 。当 磨 损 量 超 过 0 3 mm 时 .套 印 不 准 .图 案 走 样 就 会 十 分 明 显 。作 为 操 作 者 .应 时 常 在 凹 印 机 的 滑 动 部 分 、 轮 等 运 转 部 位 加 注 机 油 .以 齿
一
维普资讯
包 装 印 刷
塑 料 薄 膜 凹 印
—
—斗
÷
套 印 不 准 问题 分 析
福建 省 九洲 包装 有 限 公 司 陈 全 东
保 证 套 印的 准 确性 . 达 到 延长 机 械 寿 命 . 轻 磨损 的 目 并 减
的 。 当发 生 显 著 磨损 时则 应 当 更换 磨损 机 件 。
套 印 不 准 的走 向 .进 而采 取 相 应 的 解 决 措施 。
装版 不 正 确
套 印 不准 还 与 装 版 有 关 。装 版 前 应先 将 版 轴 洗 干净 .
浅谈塑料薄膜凹印套印不准问题

浅谈塑料薄膜凹印套印不准问题塑料薄膜凹版印刷故障种类繁多,图文前后套印不准就是常见故障之一。
由于套印不准会造成材料浪费。
所以引起了包装厂家的高度重视。
而了解套印不准的原因,掌握其排除方法变得非常必要。
倍特包装专注于复合包装对套印不准作了如下分析,供大家参考。
塑料薄膜凹版印刷的过程为;承印物经放料装置,传导辊进入第一单元进行印刷,而后进入烘干装置,再在传导辊的带动下进入第二单元印刷,由此类推,最后进入收卷装置。
在这个过程中,为了避免或减少套印不准造成的损失,既要保证承印物的放卷与收卷张力一致,还应注意套印不准的走向,进而采取相应的解决措施。
引起塑料薄膜凹印套印不准的原因有很多,既包括机械设备、油墨适性、环境温度等客观因素的影响,也包括操作人员的质量意识等主观因素的影响。
下面就一一进行详细谈谈。
卷筒直径的影响料卷直径越大,塑料在运行中越易走偏,给套印带来隐患。
根据经验,料卷直径一般为35-40cra较合适。
印刷时,随着料卷直径的逐步减小,应相应减小放卷张力,以保证走料张力保持稳定。
这要通过手动齿轮或磁粉制动器来实现。
在进行这一操作时,应注意观察印刷的色标有无走样。
国产多色凹印机的版滚筒轴向是靠滚筒端的U型槽与机架上的轴承配合来定位的,轴承的厚度恰好等于u型槽的宽度,当U型槽磨损引起宽度增加时,版轴带动版滚筒可能产生轴向窜动,引起套印不准。
当磨损量超过0.3mm时,套印不准、图案走样就会十分明显。
作为操作者,应时常在凹印机的滑动部分、齿轮等运转部位力口注机油,以保证套印的准确性,并达到延长机械寿命、减轻磨损的目的。
当发生显著磨损时则应当更换磨损机件。
当版轴发生轴向窜动时,承印物上色样不稳定,色标向上发生位移。
导辊带电塑料薄膜在印刷过程中要受传导辊牵引进入下一单元印刷或者进入烘干装置。
但塑料薄膜与传导辊摩擦后,传导辊会带上静电,吸附空气中的灰尘,使传导辊局部增大,导致薄膜轴向滑动,引起套印不准。
为此,在停机时,应对传导辊进行清洁处理,为下次印刷打下良好基础。
如何解决凹版印刷中套印不准的问题

如何解决凹版印刷中套印不准的问题套印不准是凹版印刷中经常遇到的问题之一,影响的主要因素有:印刷材料、印刷机性能、操作方法、印刷环境、凹版适性等,出现问题后要在各有关因素中进行排查,分别予以协调解决。
印刷机本身的精度是影响套印的一个重要因素,现在带自动套准装置的凹版印刷机精度一般在0.15mm以内,设备精度越高当然越容易克服套印偏差。
如果精度下降,首先要恢复精度,否则套印偏差较难克服。
在操作上,引起套印偏差的原因有:①刮墨刀调整不合适,光电信号端油墨脏污,电眼接受信号失真。
②凹版滚筒两端或中间积墨,影响压力及走料张力变化。
③印版安装时螺丝没拧紧.印刷时松动。
④印版制动轴心线与压滚轴心线不平行或制动轴心线不在印版本身的轴心上。
操作印刷机时,需调整好套印跟踪系统,保持电眼探头的清洁,保持压滚的清洁。
凹版印刷路线较长,承印物在运动时受印刷压力、张力拉伸以及烘干温度的作用,伴随承印物中液体物的挥发,使纤维收缩后会产生变形,超过一定量就会影响套印精度。
如果油墨的干燥时间不同,即干燥路线长短不同,纤维收缩变形的色序位置也不同,这就是为什么同一套版每次印刷套印偏差各不相同的一个原因。
此外,着墨面积越大,承印物收缩变形量也越大。
不同批次的承印物湿度不同,其套印偏差也有所不同。
带静电的承印物在印刷时会产生毛刺、木纹或飞墨等现象,也会影响印刷走料的平稳。
运动中的承印物发生静电吸附作用,会影响张力的稳定而导致套印偏差,这需要适当增加印刷环境的湿度或启用静电消除机构。
承印物本身的不平整、内部张力不均匀、边缘受潮(尤其是光电信号套色端)等,都会造成套印偏差。
印刷厂首先应确保印刷环境温湿度的稳定性;在印刷前三天将承印材料放到车间,以提高其温湿适性,防止出汗现象的产生;及时总结不同材料、不同品牌承印物和油墨的印刷适性;首次印刷需协调张力拉伸、印刷压力、刮墨刀位、油墨配比、稀料配比、油墨黏度、烘干温度以及印刷机速等。
制作凹印版滚时,在工艺条件稳定、材料收缩量基本稳定的条件下,事先给予一定的伸放量,以弥补承印材料的变形量。
凹印常见故障及解决方法
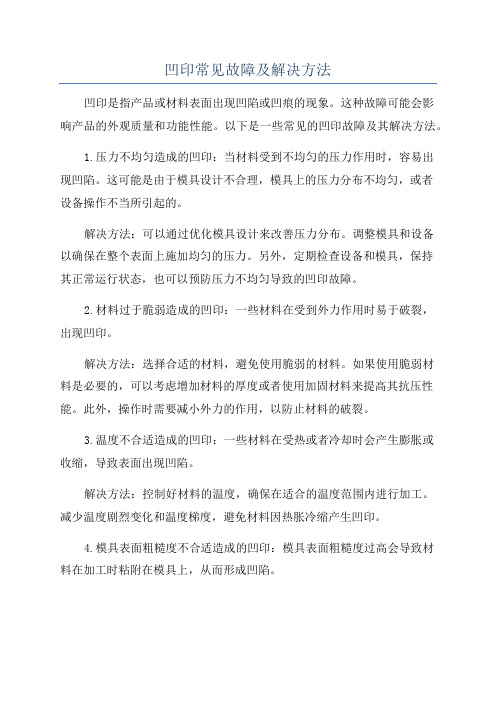
凹印常见故障及解决方法凹印是指产品或材料表面出现凹陷或凹痕的现象。
这种故障可能会影响产品的外观质量和功能性能。
以下是一些常见的凹印故障及其解决方法。
1.压力不均匀造成的凹印:当材料受到不均匀的压力作用时,容易出现凹陷。
这可能是由于模具设计不合理,模具上的压力分布不均匀,或者设备操作不当所引起的。
解决方法:可以通过优化模具设计来改善压力分布。
调整模具和设备以确保在整个表面上施加均匀的压力。
另外,定期检查设备和模具,保持其正常运行状态,也可以预防压力不均匀导致的凹印故障。
2.材料过于脆弱造成的凹印:一些材料在受到外力作用时易于破裂,出现凹印。
解决方法:选择合适的材料,避免使用脆弱的材料。
如果使用脆弱材料是必要的,可以考虑增加材料的厚度或者使用加固材料来提高其抗压性能。
此外,操作时需要减小外力的作用,以防止材料的破裂。
3.温度不合适造成的凹印:一些材料在受热或者冷却时会产生膨胀或收缩,导致表面出现凹陷。
解决方法:控制好材料的温度,确保在适合的温度范围内进行加工。
减少温度剧烈变化和温度梯度,避免材料因热胀冷缩产生凹印。
4.模具表面粗糙度不合适造成的凹印:模具表面粗糙度过高会导致材料在加工时粘附在模具上,从而形成凹陷。
解决方法:选择适合的模具材料,确保其表面粗糙度符合加工要求。
精细加工模具表面,提高其平滑度和抗粘性能。
在加工过程中,可以使用适当的润滑剂来减少材料与模具的摩擦,降低凹印发生的风险。
5.设备振动造成的凹印:在加工过程中,设备的振动会影响材料的加工质量。
解决方法:调整设备和模具的安装,确保其稳定运行。
减少设备的振动,可以增加设备的重量或者采取减振措施。
使用振动传感器和监控设备来及时检测和纠正振动问题。
综上所述,凹印故障可能由多种因素引起,包括压力不均匀、材料脆弱、温度不合适、模具表面粗糙度不合适以及设备振动等。
通过优化模具设计、调整设备和模具、选择合适的材料、控制温度、提高模具表面质量以及降低设备振动等方法,可以有效地预防和解决凹印故障,提高产品的加工质量。
影响塑料凹印套印的因素

置 主要 由光 电 扫描 器 、 向套 准 调 横
节 机 构 和 纵 向 套 准 调 节 机 构 及 对 版 仪 等 组 成 。 套 印误 差 的 跟 踪 、 对
env r m e t i on nt O pr nt n i ig
s m me d u k o l rc.
补 偿 辊 调 整 和 皈 辊 相 位 调 整 两 种
方 式 。 统 的 塑 料 软 包 装 凹 印 机 大 传
检 测 , 要 由光 电扫描器来 完成 , 主 套 印 误 差 的 调 节 则 由 横 向 套 准 调
节 机 构 和 纵 向 套 准 调 节 机 构 共 同 来完成 。
在 塑 料 _皈 印刷 过 程 中 , 印 u ] 套 不准 是 最 常 见的 印 刷故 障 之 … 。 国  ̄, GB7 0 — 7 于 印刷 套 色的 要 求 778 对 是 实 地 主 要 部 分 在0 5 mm以 内 , 层 次 主 要 部 分 在0 3 . mm以 内 。 市场 竞
维普资讯
印
刷
团
起 的 印 刷 浪 费 , 塑料 凹 印企 业 一 是 个 重 要 的 研 究 课 题 。 文 试就 其影 本 响 因 素 做 一 简 单 分 析 , 同 行 共 同 与
探讨。
环 境 等 对 印 尉 套 准 的 影
响。
Abs r t The aut or t ac : h
套 色误 差 的 起 因 和 大 小 都 是
变 化 的 , 得 要 到 较 高 的 套 色
精 度 就 必 须 在 由于薄睡的 易拉 悻殛印尉 路径鞍长 等固素 薄琪 印晨过撞 中必疆 印 刷 过 程 中 不 不断调整张力才能套准
今日印■ a , 47 嗽 3
热塑性塑料注塑件凹陷和缩痕影响因素分析
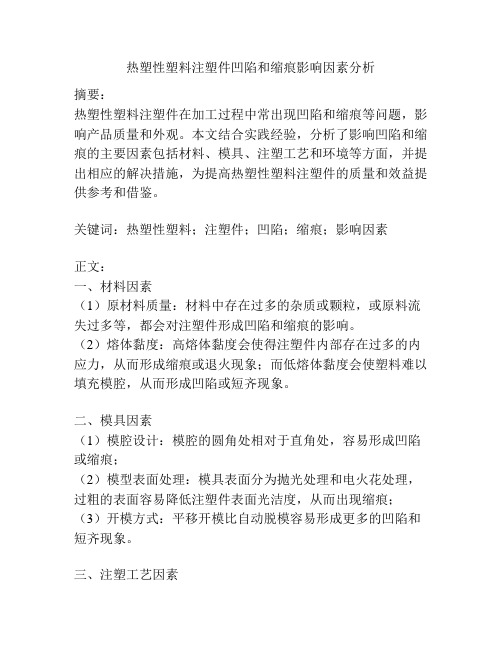
热塑性塑料注塑件凹陷和缩痕影响因素分析摘要:热塑性塑料注塑件在加工过程中常出现凹陷和缩痕等问题,影响产品质量和外观。
本文结合实践经验,分析了影响凹陷和缩痕的主要因素包括材料、模具、注塑工艺和环境等方面,并提出相应的解决措施,为提高热塑性塑料注塑件的质量和效益提供参考和借鉴。
关键词:热塑性塑料;注塑件;凹陷;缩痕;影响因素正文:一、材料因素(1)原材料质量:材料中存在过多的杂质或颗粒,或原料流失过多等,都会对注塑件形成凹陷和缩痕的影响。
(2)熔体黏度:高熔体黏度会使得注塑件内部存在过多的内应力,从而形成缩痕或退火现象;而低熔体黏度会使塑料难以填充模腔,从而形成凹陷或短齐现象。
二、模具因素(1)模腔设计:模腔的圆角处相对于直角处,容易形成凹陷或缩痕;(2)模型表面处理:模具表面分为抛光处理和电火花处理,过粗的表面容易降低注塑件表面光洁度,从而出现缩痕;(3)开模方式:平移开模比自动脱模容易形成更多的凹陷和短齐现象。
三、注塑工艺因素(1)温度控制:温度过高或过低都会影响注塑件形成的质量,应确保良好的温度平衡;(2)速度控制:注射速度过快会使得塑料温度过高,从而形成凹陷和短齐现象;(3)压力控制:压力过大会出现缩痕现象,压力过小则会出现凹陷现象。
四、环境因素(1)注塑车间的温度、湿度会对注塑件的质量产生影响,应注意是否存在温度、湿度等环境因素的变化;(2)模具的冷却时间也会对注塑件的质量产生影响。
综上所述,热塑性塑料注塑件产生凹陷和缩痕问题的原因主要包括材料、模具、注塑工艺和环境等方面,解决问题的方法包括正确的原材料选择、优化模具设计、合理的注塑工艺以及严格的环境控制等措施。
只有全面控制和改善这些因素,才能确保注塑件的高质量生产。
热塑性塑料是一种具有很高可塑性的塑料,在生产中应用广泛。
然而,热塑性塑料注塑件产生凹陷或缩痕的问题依然普遍存在,不仅影响了产品的质量和外观,还可能导致成本的增加和客户的满意度下降。
凹陷及缩痕(Sink MarK)缺陷分析及排除方法
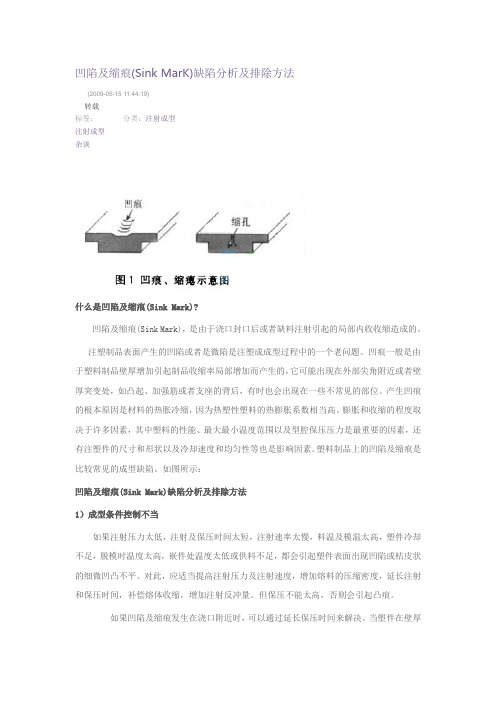
凹陷及缩痕(Sink MarK)缺陷分析及排除方法(2009-05-15 11:44:19)转载标签:分类:注射成型注射成型杂谈什么是凹陷及缩痕(Sink Mark)?凹陷及缩痕(Sink Mark),是由于浇口封口后或者缺料注射引起的局部内收收缩造成的。
注塑制品表面产生的凹陷或者是微陷是注塑成成型过程中的一个老问题。
凹痕一般是由于塑料制品壁厚增加引起制品收缩率局部增加而产生的,它可能出现在外部尖角附近或者壁厚突变处,如凸起、加强筋或者支座的背后,有时也会出现在一些不常见的部位。
产生凹痕的根本原因是材料的热胀冷缩,因为热塑性塑料的热膨胀系数相当高。
膨胀和收缩的程度取决于许多因素,其中塑料的性能、最大最小温度范围以及型腔保压压力是最重要的因素,还有注塑件的尺寸和形状以及冷却速度和均匀性等也是影响因素。
塑料制品上的凹陷及缩痕是比较常见的成型缺陷。
如图所示:凹陷及缩痕(Sink Mark)缺陷分析及排除方法1)成型条件控制不当如果注射压力太低,注射及保压时间太短,注射速率太慢,料温及模温太高,塑件冷却不足,脱模时温度太高,嵌件处温度太低或供料不足,都会引起塑件表面出现凹陷或桔皮状的细微凹凸不平。
对此,应适当提高注射压力及注射速度,增加熔料的压缩密度,延长注射和保压时间,补偿熔体收缩,增加注射反冲量。
但保压不能太高,否则会引起凸痕。
如果凹陷及缩痕发生在浇口附近时,可以通过延长保压时间来解决。
当塑件在壁厚处产生凹陷时,应适当延长塑件在模内的冷却时间。
如果嵌件周围由于熔体局部收缩引起凹陷及缩痕,这主要是由于嵌件的温度太低造成的,应设法提高嵌件温度。
如果注塑机的喷嘴孔太小或喷嘴处局部阻塞,也会因为注射压力局部损失太大引起凹陷及缩痕。
对此,应更换喷嘴或进行清理。
如果由于供料不足引起塑件表面凹陷,应增加供料量。
此外,塑件在模内的冷却必须充分。
一方面可通过调节料筒温度,适当降低熔料温度;另一方面,可采取改变模具冷却系统的设置,降低冷却水温度,或在尽量保持模具表面及各部位均匀冷却的前提下,对产生凹陷的部位适当强化冷却。
影响塑料凹印套印的因素
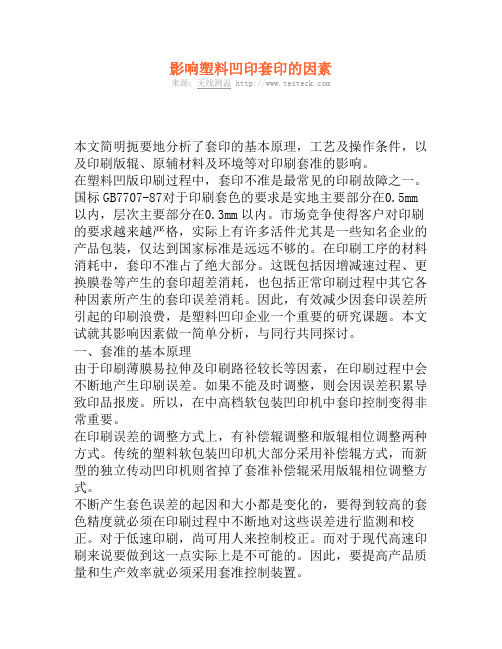
影响塑料凹印套印的因素来源:无线测温 本文简明扼要地分析了套印的基本原理,工艺及操作条件,以及印刷版辊、原辅材料及环境等对印刷套准的影响。
在塑料凹版印刷过程中,套印不准是最常见的印刷故障之一。
国标GB7707-87对于印刷套色的要求是实地主要部分在0.5mm 以内,层次主要部分在0.3mm以内。
市场竞争使得客户对印刷的要求越来越严格,实际上有许多活件尤其是一些知名企业的产品包装,仅达到国家标准是远远不够的。
在印刷工序的材料消耗中,套印不准占了绝大部分。
这既包括因增减速过程、更换膜卷等产生的套印超差消耗,也包括正常印刷过程中其它各种因素所产生的套印误差消耗。
因此,有效减少因套印误差所引起的印刷浪费,是塑料凹印企业一个重要的研究课题。
本文试就其影响因素做一简单分析,与同行共同探讨。
一、套准的基本原理由于印刷薄膜易拉伸及印刷路径较长等因素,在印刷过程中会不断地产生印刷误差。
如果不能及时调整,则会因误差积累导致印品报废。
所以,在中高档软包装凹印机中套印控制变得非常重要。
在印刷误差的调整方式上,有补偿辊调整和版辊相位调整两种方式。
传统的塑料软包装凹印机大部分采用补偿辊方式,而新型的独立传动凹印机则省掉了套准补偿辊采用版辊相位调整方式。
不断产生套色误差的起因和大小都是变化的,要得到较高的套色精度就必须在印刷过程中不断地对这些误差进行监测和校正。
对于低速印刷,尚可用人来控制校正。
而对于现代高速印刷来说要做到这一点实际上是不可能的。
因此,要提高产品质量和生产效率就必须采用套准控制装置。
套准控制系统是凹版印刷机的重要组成部分,其主要功能是对印刷品各色组的套印情况进行实时跟踪、检测和调节。
套准控制装置主要由光电扫描器、横向套准调节机构和纵向套准调节机构及对版仪等组成。
对套印误差的跟踪、检测,主要由光电扫描器来完成;套印误差的调节则由横向套准调节机构和纵向套准调节机构共同来完成。
驱动电机通过控制纵向套准调节机构、驱动补偿辊来改变印刷路径的长度或改变版辊的相位,从而实现纵套准调节。
塑胶凹痕(塌坑、瘪形)

中或热水中缓慢冷却,可以使收缩凹陷平缓又不
影响使用。四、原料方面Байду номын сангаас原料太软易发生凹陷,
有效的方法是在塑料中加入成核剂以加快结晶。
五、制品设计方面:制品
设计应使壁厚均匀,尽量避免壁厚的变化,象聚
丙烯这类收缩很大的塑料,当厚度变化超出50%时,
最好用筋条代替加厚的部位。本文由:
塑胶模具厂
塑胶厂,
递;必要时可增加点浇口数目或浇口位置以满足
实际需要;当流道长而厚时,应在流道边缘设置
排气沟槽,减少空气对料流的阻挡作用。(2)多
浇口模具要调整各浇口的
充模速度,最好对称开设浇口。(3)模具的关键
部位应有效地设置冷却水道,保证模具的冷却对
消除或减少收缩起着很好的效果。(4)整个模具
应不带毛刺且具有可靠
压时间。(2)提高注射速度可以较方便地使制件
充满并消除大部分的收缩。(3)薄壁制件应提高
模具温度,保证料流顺畅;厚壁制件应减低模温
以加速表皮的固化定型
。(4)延长制件在模内冷却停留时间,保持均匀
的生产周期,增加背压,螺杆前段保留一定的缓
冲垫等均有利于减少收缩现象。(5)低精度制品
应及早出模让其在空气
整理
或流道过狭或过浅,流道效率低、阻力大,熔料
过早冷却。浇口也不能过大,否则失去了剪切速
率,料的黏度高,同样不能使制品饱满。浇口应
开设在制品的厚壁部位。流
道中开设必要的有足够容量的冷料井可以排除冷
料进入型腔使充模持续进行。点浇口、针状浇口
的浇口长度一定要控制在1mm以下,否则塑料在
浇口凝固快,影响压力传
的合模密封性,能承受高压、高速、低黏度熔料
注塑制品有凹痕你知道怎么处理吗

注塑制品有凹痕你知道怎么处理吗
1.首先我们要知道缺陷的特征和判定的依据
凹痕多数出现在物料聚积的部位,是由于注塑件因失压而未能补偿而引起的塑料收缩痕。
2.缺陷形成的原理
在塑料的冷却过程中,由于热效应而导致塑料的自然收缩,如果这些收缩未能得到及时的补偿,在塑件的一些部位就会出现缩痕(凹痕)。
由于冷却不足,塑件表面在还未稳定的情况下被冷却时产生的内应力向内拉。
3.缺陷的可能成因
导致该缺陷的三个基本原因
1).塑料凝固速度太慢
2).有效的保压时间太短
3).由于塑料在模腔内流动的融料受到极大的阻力,或者注塑部件位置和浇口系统太狭窄,没有足够的保压压力传到模腔的某些部位。
友情提示:为了要优化保压的传送效果,注塑件的浇口应尽量设在注塑件的最大横截面上。
如果不这样做可在浇口和融料聚积位置开设一条流料加速槽,以保证保压压力的传送。
要避免浇口和系统内的流料过早固化,浇口不能过小。
4.缺陷排查步骤。
- 1、下载文档前请自行甄别文档内容的完整性,平台不提供额外的编辑、内容补充、找答案等附加服务。
- 2、"仅部分预览"的文档,不可在线预览部分如存在完整性等问题,可反馈申请退款(可完整预览的文档不适用该条件!)。
- 3、如文档侵犯您的权益,请联系客服反馈,我们会尽快为您处理(人工客服工作时间:9:00-18:30)。
定 位 和 传送 薄 膜 。 果 导 辊 运 动 精 如
度 差 , 会 导 致 薄 膜 张 力的 无 规 律 就
变 化 , 而 造 成 套 印 不 准 。 刷 设 从 印 备长时间运行时 , 由于 自身及 外 界
今1印刷 20 4 3 024 5
过 在 印 刷 中 使 用 单 倒 压 力 调 整 手
柄 , 容 易 出 现 横 向 套 色 不 稳 定 就
辊 网 眼 中的 油 墨 转 移 到 承 印 薄 膜
上 。 刷 乐 力 过 大 易 g{ £ 0 印 起 Ⅱ 折 皱、 印墨 斜 纹 及 由此 带 柬 的 套 准 问
薄 膜 起 析 等 情 况 , 获 得 良好 精 度 对
维普资讯
刷
固
点 。 管 采 用 那 种 方 式 应 注 意 以 不
下 问题 :
环 境 等 对 印 勋 套 准 的 影
7 。
A bs r t The 以ut , t ac : h一
象。 当然 也就 会 造 成 套 色 失 准 。
④ 胶 辊 轴 承 必 须 保 持 平 滑 运 转 , 印胶 辊 出现 松 动或 阻 力增 大 压 时应立即修复。 ④ 压辊 经 长 时 间 使用 ( 3 0小 0
①调 节 时 应 使 压 印滚 筒 两端
a l s sc n ie yt eb s c na y e o c s l h a i
的 力值 相 等 并 保 持 不 变 。 版 辊 在 相 对 固 定 方 式 中 , 印滚 筒 的升 落 压
由两 个 气 缸 控 制 , 印刷 压 力 的 大 小 通 过 气压 阀来 调 节 。 定 印 刷 压 力 稳 就必须保证气源的稳定 。 气缸 供 气 不 足或 气 压 不 稳 定 都 会 造 成 压 印 滚 筒 两 端 的 压 力 l 一 致 , 致 压 印 币 导 滚 筒 运 转 不 平 稳 压 印 力 分 布 不 均
c n r l gde ie . o tol n vc s i
at r &
o r i n c n to s An t e pe at o di n . d o i h s metm et eH t o n a i “ h r ~z s h n e
就 那样 使 用 那 么 该单 元的 图案 与
tee e t p it gpae h c rni lt f n
f a o l  ̄ r W ma e i l r mer l e t tra s t
以nd he nv r t e i on, t o e t pr n i g s mm e d r c i tn a l u k
引 起 的 不 平 衡 状 态 也 会 成 为 套 色
不 良的 原 因 所 以 、 辊 安 装 后 检 版
f 上期 ) 续
查 水 平是 必 要 的 。 了利 于 遗 种 操 为 作 , 可安 装 单 侧 压 力 调 整 手 柄 。
( ) 刷 压 力 2印
在 印 刷 压 力的 作 用 下 , 刷 版 印
容 易产 生 不 稳 定 。
(l 辊 3 导 凹 印 机 上 使 用 大 量 的 导 辊 来
题 ; 力过 小 , 易造 成 脱 即 缺 墨 则
及 由此 引起 的 套准 问题 。 刷 力 印
是 通 过 压 印 滚 筒 与 印 版 辊 筒 的 相
互挤 压 产 生的 。 而具 体 实 现 这 个 压 力却 有 着 不 同 的 方式 。 部 分 印 刷 大
维普资讯
因 素 的 影 响 , 辊 J 会 松 动 、 导 能 堂 形及 运 转 阻 力 发 变化 ( 含轴 承 损 坏 ) 从 而 改 变 机 组 间 的 印 刷 路 径 , 长度或者 张 力 , 由此 印刷套准 。 井 另 外 . 分 导 辊 直 接 与 印 晶 正 面接 部 触, 可能 会 囡 冷 却 不 好 致 使 导辊 粘 墨 , 样 也 会 轻 微 地 改 变 印 刷 路 径 同
的 印 刷 品 是 不利 的 。 ② 用 于塑 料 薄 膜 印 刷 的 压 辊 其 掏造多 为轻 压型 , 同时 , 虑 到 考 作 也的方便而 缺 乏耐 压性 。 以 , 所 如 果 加 L5 Ok O g以 上的 印压| 话 , 的 压 辊 就 会 发生 弯 曲 , 要 两 端 受 到 只 强压 , 中央 部 分 就 容 易 出现 脱 色现
其 它 单 元 的 图 案 相 比 宽 度 就 会 缩 小 , 会 产 生 与 过 加 压 时 相 同的 弓 就 形 状志 。 压辊表面为合成橡胶 , 由于 溶 剂 的 作 用 而 发 生 溶 胀 变 形 划 伤 等 , 需 要 经 常 研 瞻 。 磨 加 工 时 就 研 必须 注 意 防 止 压 辊 产 生 锥度 , 使 井 多 色 印刷 时 圆周 长 能 够 保 持 相 同 。 如 果 有 锥 度 , 膜 就 容 易 起 折 薄 横 向套印就 容 易产生不 稳定 。 另外 , 如 不是 同一 圆 周 长 , 纵 向 套 印就
匀 , 而 使 套 印 不 准 确 。 且 倒 压 从 而
t n f o amme d t c , e e f S I u k
syst em . & reg i eri g St n
时 左右 )后 由于 油 墨 溶 卉 的 影 响,
印刷 压 辊 的 两 端 会 发 生 膨 胀 。 果 如
lJ 跳 动 对 套 印 的 影 响 1圆
保 证 套 印玛 克 c 记 ) 位 置准 确 , 标 的 若 超 出 r可调 节 的 误 差 范 围 . 必将 会 影 响 系 统 的 自动 跟 踪 套 准 , 从而 选 到 准 确 套 印 的 F 的 。 时 , _ I 有 由 于 制 版 误 差 的 影 响 , 印 线 套 准 套 了 , 实 际上 图文部分 并 无套准 , 但 这 时 就 需 要 进行 套准 补 偿 。 f) 4版辊 的安 装 精 度 装 版 时 . 须 确 保 印 刷版 辊 筒 必 两 端 锥 7 T 固版 锥 头 清 洁 , 能 粘 Ln 不 附 油 墨或 其 它 杂 质 , 则 会 影 响 装 否 配精度 。 版完毕后 , 用手试转 , 装 应 检 查 版 辊 筒 转 动是 否 灵 活 、 否 有 是 松 动 现 象 。 刷 前 , 可 用 分 度 表 印 还 或 径 向 跳 动 仪 检 测 版 辊 筒 是 否 存 在 圆 跳 动 . 便 及 时 调 整 . 证 印 以 保