空分设备冷箱内管道断裂事故分析及处理
空分主冷事故

空分膨胀机工作原理?空分的一些事故分析及操作注意2009年12月06日:先容10000m3/h空分设备按计划进行检修,在打开底部两个人孔排珠光砂时发生了喷砂事故,造成1人死亡、1人受伤。
阐发了事故发生的原因,并提出了防范办法。
:1事故经过及征象四川威远钢铁有限公司动力厂制氧车间按照川威集团中修计划,在2007年1月24日15∶15召开了10000m3/h空分设备冷箱扒珠光砂的筹办会。
随落伍行了扒砂前的筹办事情:拆掉喷射蒸发器到排液总管之间的管道(便于扒砂);顶部人孔全数大开;15m平台的人孔紧固好并关闭珠1、事故经过1996年7月18日,哈尔滨气化厂空分分厂当班人员听见一声闷响,接着主冷凝器(以下略称"主冷")液位全无、下塔液位上涨,氧、氮不及格,现场有少量珠光砂从冷箱里泄了出来。
断定为主冷爆炸。
后经主冷出产厂家切开主冷发明上塔塔板全数变型,主冷四个单位中有1个单位局部烧熔,爆炸切口有煤黑,另外1个单位发生轻细爆炸,下塔有一块塔板变型。
二、有关情况该套空分设备1993年投入出产,产量和纯度都达到要求。
该套设备是接纳全低压板式换热器净化流程,没液空、液氧吸附器。
爆炸前工艺指标未发明异常,主冷液位控制在2500~2900mm,主冷处于全浸操作,当时气相色谱阐发仪带病运行,每周阐发1次。
造气、净化、甲醇三个分厂距离空分较近,化验阐发碳氢化物超过标准3倍多,有电石气出现。
3、事故阐发1.空气污染空气分厂与造气、甲醇、净化分厂较近,这三个分厂不没事了排放对空分出产造成为了威吓。
主冷液氧中碳氢化物超过标准时有发生。
在爆炸前几天风向和气压都对空分出产不利,造成原料空气碳氢化物含量上涨。
2.碳氢化物在主冷中积累碳氢化物经过液空吸附器和液氧吸附器吸附后,部门被排除,另外一部门在液氧中积聚,使其在液氧中液体浓度升高。
电石气在液氧中局部浓缩而析出危险的固体电石气,吸附器倒换周期长,液氧泵时开时停,导致碳氢化物不能被实时排出,又未采纳大量排液手眼,导致超过标准。
空分事故分析

一、事故经过1996年7月18日,哈尔滨气化厂空分分厂当班人员听到一声闷响,接着主冷凝器(以下简称“主冷”)液位全无、下塔液位上升,氧、氮不合格,现场有少量珠光砂从冷箱里泄了出来。
断定为主冷爆炸。
后经主冷生产厂家切开主冷发现上塔塔板全部变形,主冷四个单元中有一个单元局部烧熔,爆炸切口有碳黑,另一个单元发生轻微爆炸,下塔有一块塔板变形。
二、有关情况该套空分设备1993年投入生产,产量和纯度都达到要求。
该套设备是采用全低压板式换热器净化流程,没液空、液氧吸附器。
爆炸前工艺指标未发现异常,主冷液位控制在2500~2900mm,主冷处于全浸操作,当时气相色谱分析仪带病运行,每周分析1次。
造气、净化、甲醇三个分厂距离空分较近,化验分析碳氢化合物超标3倍多,有乙炔出现。
三、事故分析1.空气污染空气分厂与造气、甲醇、净化分厂较近,这三个分厂不正常排放对空分生产造成了威胁。
主冷液氧中碳氢化合物超标时有发生。
在爆炸前几天风向和气压都对空分生产不利,造成原料空气碳氢化合物含量上升。
2.碳氢化合物在主冷中积累碳氢化合物经过液空吸附器和液氧吸附器吸附后,部分被排除,另一部分在液氧中积聚,使其在液氧中浓度升高。
乙炔在液氧中局部浓缩而析出危险的固体乙炔,吸附器倒换周期长,液氧泵时开时停,导致碳氢化合物不能被及时排出,又未采取大量排液手段,导致超标。
3.操作不当在吸附器操作过程中,不按规程精心操作导致硅胶破碎,致使硅胶粉末进入主冷。
4.液氧中硅胶和二氧化碳颗粒随液体运动产生静电,是乙炔起爆的点火源。
四、教训和建议1.空分设备吸风口应该远离碳氢化合物杂质散发源,加强对空气监测。
2.防止硅胶和二氧化碳进入分馏塔,加强操作管理,缩短吸附器倒换周期,液氧泵24小时运行,增大膨胀量集中排放大量液氧。
3.空分设备运行12个月,停车全面加温,彻底清除碳氢化合物和油脂。
4.对设备进行及时维护修理,防止带病运行。
5.加强分析管理,严格控制碳氢化合物不超标。
空分装置冷箱内爆炸事故
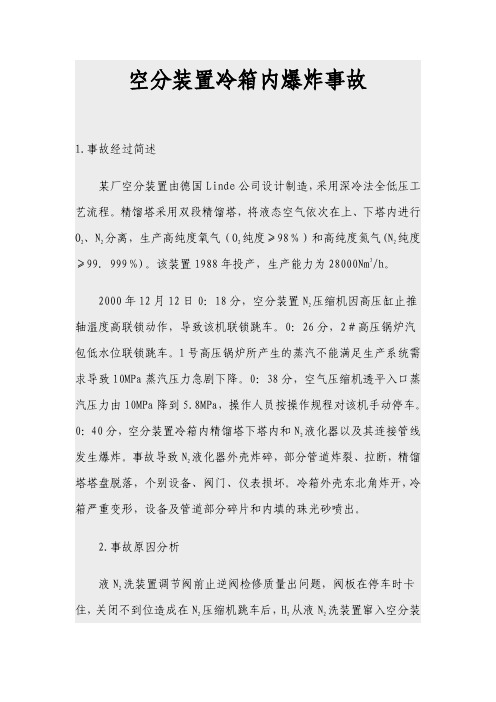
1.事故经过简述
某厂空分装置由德国 Linde 公司设计制造,采用深冷法全低压工 艺流程。精馏塔采用双段精馏塔,将液态空气依次在上、下塔内进行 O2、N2 分离,生产高纯度氧气(O2 纯度≥98%)和高纯度氮气(N2 纯度 ≥99.999%)。该装置 1988 年投产,生产能力为 28000Nm3/h。
2000 年 12 月 12 日 0:18 分,空分装置 N2 压缩机因高压缸止推 轴温度高联锁动作,导致该机联锁跳车。0:26 分,2#高压锅炉汽 包低水位联锁跳车。1 号高压锅炉所产生的蒸汽不能满足生产系统需 求导致 10MPa 蒸汽压力急剧下降。0:38 分,空气压缩机透平入口蒸 汽压力由 10MPa 降到 5.8MPa,操作人员按操作规程对该机手动停车。 0:40 分,空分装置冷箱内精馏塔下塔内和 N2 液化器以及其连接管线 发生爆炸。事故导致 N2 液化器外壳炸碎,部分管道炸裂、拉断,精馏 塔塔盘脱落,个别设备、阀门、仪表损坏。冷箱外壳东北角炸开,冷 箱严重变形,设备及管道部分碎片和内填的珠光砂喷出。
2.事故原因分析
液 N2 洗装置调节阀前止逆阀检修质量出问题,阀板在停车时卡 住,关闭不到位造成在 N2 压缩机跳车后,H2 从液 N2 洗装置窜入空分装
置冷箱内,为爆炸提供了物质条件。当 N2 压缩机跳车后。操作工在 14min 后才按下液 N2 洗系统的停车总联锁,造成液 N2 洗装置阀不能及 时关闭,H2 穿过止逆阀到调节阀大约 6min,在操作工手动关闭阀以后 才切断 H2 源。
N2 压缩机联锁误动作跳车导致空分装置系统内工况变化,为 H2 向该系统反窜提供了机会。事故状态下,蒸汽系统失控,造成空气压 缩机停车,使空分装置系统工况紊乱。造成精馏塔底的富 O2 液空气上 窜,同已进入精馏塔、低压 N2 以及其它设备中的 H2 汇集混合,达到 爆炸极限,在气流的作用下产生静电引爆。
空分装置冷箱管系变形及焊缝开裂的原因分析

阀 出 、 1 管 线 1 4 人 2 I 1 mm/ 5 mm 和  ̄ 6 mm/  ̄3 18
 ̄3 5 mm 大小 头 的  ̄ 3 5 mm 侧 焊缝 热影 响 区处 , 裂
0 MP ,外 直 径 1 4 m,壁 厚 6 m,总 长 .5 a 1r a a r
2 . 0m 。 9 7
在 设计 温 度 下 若 管 线 和设 备 能 自 由冷 缩 变
形 , 产生 的位 移量 可 由式 ( ) 所 1 计算 [ : 2 ]
A 一 L 1 AT () 1
油 天 然气 股 份 有 限公 司 大 庆 石 化 分 公 司水 气 厂 从 事 设 备 管
理 工作 。
维普资讯
第 2 8卷 第 5期
刘 秀英 等 .空 分 装 置 冷 箱 管 系变 形及 焊 缝 开 裂 的原 因分 析
下发 生 了 塑性 变 形 : a点 弯 头 扭 曲变 形 , b点 管 线
纹 环形 长度 7 mm( 图 2 。冷箱 壁低 温脆 裂 , 0 见 ) 阀
作 者 简 介 : 秀 英 ( 9 6 ) 女 , 龙 江 大 庆 人 。 20 刘 17 一 , 黑 0 0年 毕
门支撑 架 、 出人 口管线支 架底 座开 裂 , 门支 架 固 阀
定 箍撕脱 。
业 于 大 庆 石 油学 院 化 工 与 石 油 机 械 工 程 专 业 。现 在 中 国石
束, 限制 了管道 的 自由伸缩 。这样一 来 , 产 生 了 便
热应 力 。如果 应力 越 过 了强 度 极 限 , 管道 便 会 变 形 、 生 断裂 。 发 中 国石油 天然气 股份 有 限公 司大庆石 化分 公 司水 气厂林 德 “ 0 0 ” 分 装 置 全套 设 备 从 德 国 100 空 林德 公 司 引进 , 全 低压 分 子筛 、 为 空气 膨 胀 、 高 双 产 品外 部 压 缩 的 流程 , 装 置 于 1 8 该 9 5年 建 成 投 产 。2 0 0 4年装 置大检 修 后 , 7月 4 日 1 :O开 于 53
空分装置预冷系统事故原因分析及对策
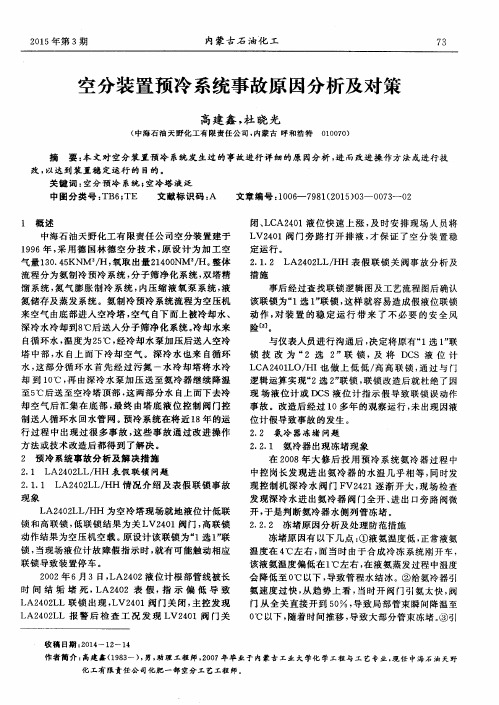
闭、 L C A2 4 O 1液 位 快 速 上 涨 , 及 时安 排 现场 人 员 将 L V2 4 0 1阀 门旁 路 打 开 排 液 , 才 保 证 了空 分 装 置 稳
定 运行 。
中海 石油 天野 化 工有 限责 任 公 司空 分装 置建 于 1 9 9 6年 , 采用德国林德空分技术 , 原 设 计 为 加 工 空 气量1 3 0 . 4 5 KNM。 / H, 氧取 出量 2 1 4 0 0 NM。 / H。 整 体 流程 分为 氨制 冷 预冷 系统 , 分 子 筛净 化 系统 , 双塔 精 馏 系统 , 氮 气 膨胀 制 冷 系 统 , 内压 缩 液 氧 泵 系 统 , 液
2 0 1 5 年第 3 期
内蒙 古石 油化 工 7 3 空分装 置预冷 系统事故原 因分 析及对策
高建鑫 , 杜 晓 光
( 中海 石 油 天 野 化 工 有 限责 任 公 司 , 内蒙 古 呼 和 浩 特 0 1 0 0 7 0 )
摘
要: 本 文 对空 分装 置预 冷 系统 发 生过 的事 故进行 详 细的原 因分析 , 进 而改进操 作 方法或进 行技
逻 辑运算 实 现“ 2 选2 ” 联锁 , 联 锁改 造后 就杜 绝 了因 现 场 液 位计 或 D C S液 位 计 指 示 假导 致 联 锁误 动作 事 故 。改 造 后经 过 1 O多 年 的观 察运 行 , 未 出现 因液
制 送人 循 环水 回水 管 网 。 预冷 系统 在 将 近 1 8年 的运 行 过 程 中 出现 过 很 多 事 故 , 这 些 事故 通 过改 进 操 作
2 . 2 . 2 冻 堵 原 因分析 及 处理 防 范措施
冻堵原 因有以下几点 : ①液氨温度低, 正常液氨
空分车间事故分析

空分车间事故分析一、背景介绍空分车间是一种重要的工业生产设施,用于将混合气体中的不同成分分离出来。
然而,由于操作不当、设备故障或其他原因,空分车间事故时有发生。
为了确保工作场所的安全和员工的健康,对空分车间事故进行详细分析是非常重要的。
二、事故概述在本次事故中,发生了一起空分车间的爆炸事故。
据初步调查,事故发生时车间内正常运行,突然发生爆炸,导致多名员工受伤。
事故发生后,紧急救援人员迅速赶到现场进行救援,并将伤员送往医院进行治疗。
现场安全人员立即启动应急预案,将事故区域进行封锁,并进行初步的事故调查。
三、事故原因分析1. 设备故障:初步调查发现,事故可能与空分车间内的某个设备发生故障有关。
这可能包括管道破裂、阀门失灵或压力异常等。
详细的设备检查和测试将有助于确定具体的故障原因。
2. 操作失误:操作人员在使用空分车间时可能存在操作失误,如操作不当、违反操作规程或忽视安全警示。
这可能导致事故的发生和扩大。
通过调查操作记录和访谈相关人员,可以进一步确定是否存在操作失误。
3. 安全管理不到位:事故的发生也可能与安全管理不到位有关。
例如,缺乏必要的安全培训、缺乏安全操作程序、缺乏紧急救援设备等。
对安全管理制度进行全面评估和审查,可以帮助找出管理不到位的问题。
四、事故影响分析1. 人员伤亡:事故导致多名员工受伤,其中一些可能伤势较重。
对受伤员工的伤情评估和治疗情况进行跟踪,以确保他们得到及时的医疗照顾和康复。
2. 生产中断:事故导致空分车间无法正常运行,进而导致生产中断。
对生产损失进行评估,估计损失的时间和成本,并采取相应措施尽快恢复生产。
3. 环境污染:爆炸可能导致有害物质泄漏,对周围环境造成污染。
进行环境监测和污染防控,确保及时清理和修复受影响的区域。
五、事故防范措施1. 设备维护:定期进行设备的维护和检修,确保其正常运行。
对关键设备进行全面的检查和测试,及时发现并解决潜在问题。
2. 操作培训:加强操作人员的培训,提高他们的操作技能和安全意识。
空分车间事故分析

空分车间事故分析一、事故概述空分车间是化工企业中的重要部门之一,主要负责气体的分离和纯化工作。
然而,由于操作不当、设备故障或其他原因,空分车间事故时有发生,给生产安全和环境保护带来严重威胁。
为了深入分析空分车间事故的原因和影响,本文将对一起空分车间事故进行详细分析。
二、事故背景1. 事故地点:某化工企业空分车间2. 事故时间:2021年5月10日上午10点3. 事故类型:化学品泄漏事故三、事故过程1. 事故起因根据调查和现场勘查,事故起因为空分车间中的一台冷凝器发生了泄漏。
冷凝器是空分车间中的重要设备,用于冷却和凝结气体。
泄漏原因初步判断为设备老化和维护不当导致的管道腐蚀。
2. 事故发展冷凝器泄漏导致大量的气体泄漏到空气中,形成可燃气体云。
由于空分车间存在较高的温度和湿度,加上未及时发现和处理,可燃气体云逐渐扩散,并与空气中的氧气形成可燃混合物。
3. 事故后果可燃混合物在空分车间内遇到明火引发爆炸,造成车间内部设备严重损坏,导致火势蔓延。
同时,爆炸产生的冲击波和火焰造成多名工人受伤,其中两人伤势严重,送往医院救治。
事故还引发了一定的环境污染,有毒气体进入大气中,对周边地区的环境造成一定影响。
四、事故原因分析1. 设备老化和维护不当冷凝器作为空分车间的核心设备之一,长期使用后容易出现老化和腐蚀现象。
此次事故中,冷凝器泄漏的原因初步判断为设备老化和维护不当导致的管道腐蚀,需要加强设备的定期检修和维护工作。
2. 操作人员疏忽事故发生时,操作人员未能及时发现冷凝器泄漏,并采取相应的措施进行处理。
操作人员在日常工作中应该加强对设备的巡检和监控,及时发现异常情况并采取相应的应急措施。
3. 应急预案不完善事故发生后,由于应急预案不完善,导致事故处理不及时、不得当。
企业应该建立健全的应急预案,明确责任分工和处置流程,提高应对突发事件的能力。
五、事故教训与改进措施1. 加强设备维护管理企业应加强空分车间设备的定期检修和维护工作,及时发现和处理设备的老化和腐蚀问题,确保设备的正常运行和安全性。
发生空分设备事故原因分析与管控措施
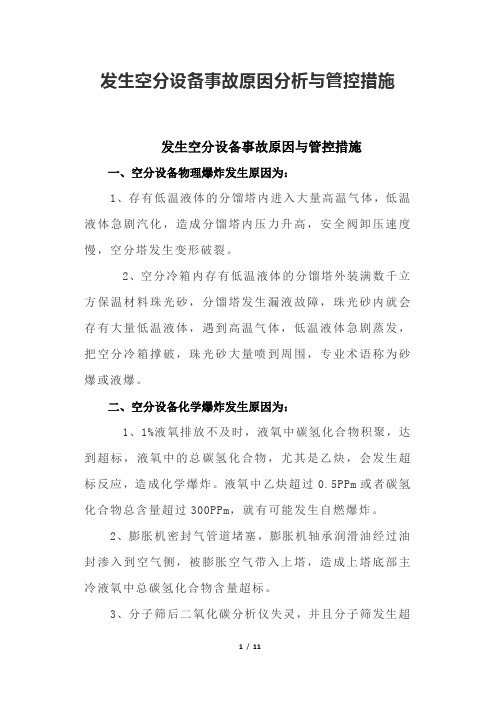
发生空分设备事故原因分析与管控措施发生空分设备事故原因与管控措施一、空分设备物理爆炸发生原因为:1、存有低温液体的分馏塔内进入大量高温气体,低温液体急剧汽化,造成分馏塔内压力升高,安全阀卸压速度慢,空分塔发生变形破裂。
2、空分冷箱内存有低温液体的分馏塔外装满数千立方保温材料珠光砂,分馏塔发生漏液故障,珠光砂内就会存有大量低温液体,遇到高温气体,低温液体急剧蒸发,把空分冷箱撑破,珠光砂大量喷到周围,专业术语称为砂爆或液爆。
二、空分设备化学爆炸发生原因为:1、1%液氧排放不及时,液氧中碳氢化合物积聚,达到超标,液氧中的总碳氢化合物,尤其是乙炔,会发生超标反应,造成化学爆炸。
液氧中乙炔超过0.5PPm或者碳氢化合物总含量超过300PPm,就有可能发生自燃爆炸。
2、膨胀机密封气管道堵塞,膨胀机轴承润滑油经过油封渗入到空气侧,被膨胀空气带入上塔,造成上塔底部主冷液氧中总碳氢化合物含量超标。
3、分子筛后二氧化碳分析仪失灵,并且分子筛发生超期使用,超温使用,再生不足,进入游离水,进油中毒等原因,不能完全吸附二氧化碳、总碳氢化合物等,碳氢化合物穿过分子筛进入分馏塔内,造成下塔底部液空和上塔底部主冷液氧总碳氢化合物含量超标。
4、对于自由端轴承在吸风管内的空压机来说,自由端轴承密封气管断开或堵塞,吸风管内产生的负压会把轴承内的、润滑油吸入空气中,造成分子筛中毒,空气中的总碳氢化合物会穿过分子筛,进入分馏塔内,造成下塔底部液空和上塔底部主冷液氧总碳氢化合物含量超标。
5、由于化工厂或化工车辆放散口在空压机吸风口附近放散杂环烃1#、杂环烃2#、粗酚、轻粗苯、硫磺、硫酸铵等化产气体,空气含有大量的总碳氢化合物。
空压机吸入总碳氢化合物含量高的空气,会造成总碳氢化合物会穿过分子筛,进入分馏塔内,造成下塔底部液空和上塔底部主冷液氧总碳氢化合物含量超标。
三、针对以上各种危险因素,制氧应制定相应的管控措施:1、操作空分塔进塔阀门必须缓慢,热空气进塔速度根据压力变化逐步调整。
空分设备冷箱内脚手架造成低温管道断裂的事故分析

Ac i e ta ay i fa r p u eo o t mp r t r i ei ed e cd n n l sso u t r fl w e e a u ep p l u n
t h c fo d i o d b x o i e a a i n u i o t e s a f l n c l o far s p r to n t
中原大 化集 团有 限责 任公 司为煤 化工 项 目配套
Байду номын сангаас
用 ,避免 类似 事故 的再 次发生 。
的 5 00 / 2 0 m0 h空 分 设 备 , 由杭 州 杭 氧 股 份 有 限公
司制造 ,采 用分 子筛 吸附 净化 、增 压膨胀 制冷 、双 泵 内 压 缩 和 全 精 馏 无 氢 制 氩 流 程 ,设 计 氧 产 量 5 00 0h 2 0 m / 、纯度 9 .4 O ,氮 产量6 6 0 / 、 97 % z 0 0 m0h 纯度 1 0× 1 O, 0 ,氩 产 量 为 1 0 m h 纯 度 60 / 、
He a n n。P.R .C ia) hn
Ab t a t Fo h c n e inc f sr c : r t e o v n e e o mant n n e, s i eac ome s af l we e r ti d n od o fe h la g c fods r e ane i c l b x a t r t e e ka e
Ca n —a o Ho g to
( aii t n a d Ai Sp rt n Pa t h n y a a u o p C . t ,P y n 5 0 4, G s c i n r e a ai ln ,Z o g u nD h a Gru o ,L d. u a g 4 7 0 fao o
一起氨制冷系统管道断裂事故的原因分析

一起氨制冷系统管道断裂事故的原因分析熊从贵【摘要】制冷系统的库房回气管道发生了断裂失效,断裂位置在环焊缝中心且断口平整,焊缝存在未焊透缺陷。
管道采用管束整体发泡保温,增加了管道的刚性,不利于管道的位移补偿。
通过对管道材质进行分析,化学成分和力学性能符合设计要求。
对管道受力状态进行分析并进行应力计算,结果表明,管道焊接接头未焊透,削弱了焊接接头的承载能力。
管道在“冷缩”时不能补偿而产生较大的拉应力,导致在管道强度薄弱的焊接接头处发生断裂失效。
%The fracture failure occurred in the suction pipe of the cold store refrigeration system ,the fracture position was in the center of the circular weld ,the fracture surface was smooth and there existed defects of not welded thoroughly .Pipe bun-dle heat insulation used overall foam ,the rigidity of the pipeline was increased ,but not conducive to the displacement com-pensation of the pipeline .Through the analysis of the material of the pipe ,chemical composition and mechanical properties met the design requirements .The stress state of the pipeline was analyzed and the stress calculated .The results showed that the pipe welding joint was not welded thoroughly ,and the weakened of the welded joint was weakened .When the pipelinewas‘cold shrinkage’ ,it wouldn’t compensate and lead to te nsilestress ,fracture failure occurred at the weld joint where the strength of the pipeline was weak .【期刊名称】《工业安全与环保》【年(卷),期】2017(043)001【总页数】3页(P75-77)【关键词】制冷系统;低温管道;整体发泡保温;未焊透;收缩;断裂;自然补偿【作者】熊从贵【作者单位】台州龙江化工机械科技有限公司浙江温岭317500【正文语种】中文2015年9月,某冷库在正常运行过程中发生氨泄漏,泄漏点位于开放式的货品挑选场所,7名员工轻度氨中毒,无较大经济损失。
空分车间事故分析
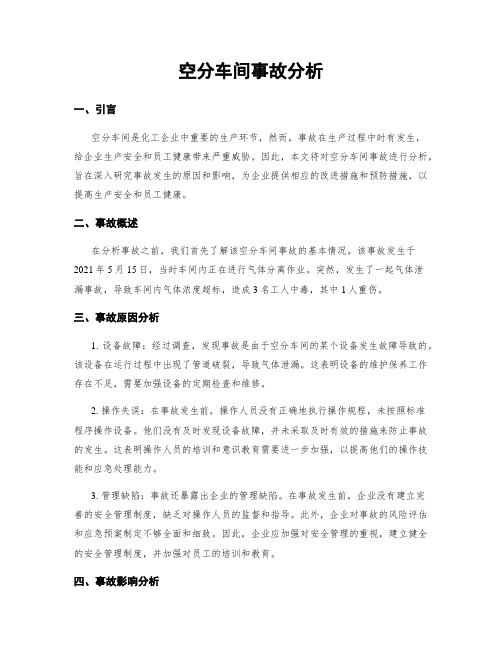
空分车间事故分析一、引言空分车间是化工企业中重要的生产环节,然而,事故在生产过程中时有发生,给企业生产安全和员工健康带来严重威胁。
因此,本文将对空分车间事故进行分析,旨在深入研究事故发生的原因和影响,为企业提供相应的改进措施和预防措施,以提高生产安全和员工健康。
二、事故概述在分析事故之前,我们首先了解该空分车间事故的基本情况。
该事故发生于2021年5月15日,当时车间内正在进行气体分离作业。
突然,发生了一起气体泄漏事故,导致车间内气体浓度超标,造成3名工人中毒,其中1人重伤。
三、事故原因分析1. 设备故障:经过调查,发现事故是由于空分车间的某个设备发生故障导致的。
该设备在运行过程中出现了管道破裂,导致气体泄漏。
这表明设备的维护保养工作存在不足,需要加强设备的定期检查和维修。
2. 操作失误:在事故发生前,操作人员没有正确地执行操作规程,未按照标准程序操作设备。
他们没有及时发现设备故障,并未采取及时有效的措施来防止事故的发生。
这表明操作人员的培训和意识教育需要进一步加强,以提高他们的操作技能和应急处理能力。
3. 管理缺陷:事故还暴露出企业的管理缺陷。
在事故发生前,企业没有建立完善的安全管理制度,缺乏对操作人员的监督和指导。
此外,企业对事故的风险评估和应急预案制定不够全面和细致。
因此,企业应加强对安全管理的重视,建立健全的安全管理制度,并加强对员工的培训和教育。
四、事故影响分析1. 生产损失:事故发生后,空分车间的生产受到了严重影响。
车间停工进行事故处理和设备维修,造成了生产线的停产,导致了生产损失。
此外,事故还给企业的声誉带来了负面影响,可能导致客户的流失和订单的减少。
2. 人员伤亡:事故导致了3名工人中毒,其中1人重伤。
这不仅对受伤工人本人造成了严重的身体和心理伤害,还给其家庭带来了沉重的负担。
此外,事故还对其他员工的身心健康造成了一定的影响,增加了企业的人力成本和风险。
3. 环境污染:气体泄漏事故导致了大量有害气体的释放,对周围的环境造成了污染。
10000m 3/h空分设备冷箱内管道焊缝开裂分析

Jy a 5 6 0,He a iu n 4 4 5 n n,P. R.C ia) hn
1 0 0m3h空 分设 备 冷 箱 内管道 焊 缝 开 裂 分析 0 0 /
吴 魏 国 ,赵 军 虎 。 翟 艳 飞
( 南 豫 光 金 铅 股 份 有 限 公 司 项 目部 ,河南 省济 源市 荆 梁 南 街 1 河 号 445 ) 56 0
摘要 :由于安装人 员将 粗 氩塔 进 液 阀 v 3的 固定 支架和 活动 支架 的位 置装 反 ,导 致投 运 制氩 系统 时 V 3阀进 口管线 焊缝 开裂 ,制氩 系统不 能成功投 入运 行 。 文章介 绍 了故 障 经过 、原 因分析
a g n t we n r v re p sto r o o r i e e s d o iin, t l o V3 he we d f vav i lt i ei e c a ks t o m iso i g o t a g n l e n e p p ln r c a c m si n n f he r o ge e a ig s se a d i u n r s ls i ns c e s u o m iso n ft e a g n g ne a i g s se . H e e,t e n r tn y t m n n t r e u t n u u c sf lc m s inig o h r o e r tn y t m r h p r iua so h r u e a d t a a fc l o n h o r e a ay i o s r re e a tc lr ft e to bl n he d m geo o d b x a d t e c u s n l ss c ure a e b if d,a d fn l h n i al t e y m e s r s t p i iet e p p l n i et e c l o nd p e e i em e s r st v i e c u r n eo hesm i r a u e o o tm z h i ei i sd h od b x a r v ntv a u e o a o d r o c r e c ft i l ne a
空分设备冷损分析与对策

1的
翻妞机百年华祝.气体总月技术交浪会论文集(?.003.4)
启定荣:空分设备冷狈分析及对策
安 装 运 转
(1) 时 冷 箱内进行充氮,并保持一定压力_ 一 般充人的氮气 为空分生产的干燥 氮气,压力在
(100一200)M MHz0(表压),并保证始终为正压, 以使冷箱外含湿空气无法进人冷箱内〔含湿空气进
.月 , ,
户
16 1
(2) 在 工 作中谨懊操作,杜绝超压现象。如容 器的预冷、积液、切换等,要缓慢 调阀的调节尤 其是中低压相连的阀门.调节操作时更要缓慢。超
庄很容易引起泄漏,带道、弃器、阀门等都有一定 的工作压力,一几超J,11- 容易使其变形或使材料内 部压力发生变化而受损伤,严重的会直接导致破裂 而造成重大泄漏.R至停产,这是绝对要预防的
②换热器设计、制造及组成的材质 。也是很重要的 方面。但运行操作中对此是无法有控侧的。 12 跑冷损失
跑冷 损 失 主要是由环境介质传人热皿而引起的 冷量损失,主要有两个方面:①热传导,热且通过 接触面 (或层)进行传递,这与接触面 (或层)的 材料有很大关系;②泄踢,主要是气和液的泄砚,
这与设备的材质、检修质t.调节操作等方面有 关。因此.减少跑冷损失要从多方面若手,针对引 起跑冷损失的主要因素采取措施。 1.3 液体产品排出带来冷f扭失
的论文,获得了物理学博士学位〕该透平后被英国氧气公 司采用并进行了深一步研制,用在 LEM 系列液氮机上、该 技术现己为林德公司拥有
195 9年 妙 伯特加盟美1g国家标准局低退部.在那里他 研制出小型笼透平脚胀机。1963年他到牛津大学工程科学 系工作,从事氮气体轴承压缩机研究工作。他于 1981年退 休,但又在美国新罕布什尔州 Came公司里研制微型低温 透平机械,它将用于哈勃 (Huwe)太空望远镜上。在该太 空望远镜上关链仪表组件是近红外扳像机和多目标摄谱仪 它们是低泥冷却的检测仪,原采用固氮冷却。由于消耗比 预期快、摄谱仪信号终止。199,年 〔:reare公司受命建造逆 布雷顿 (Br sytai)低m制冷机来恢复供冷。建造的徽型透 平机械展动可忽略不计,不会影响望远镜的定向精度。该 低沮制冷机装有一台徽型离心式压缩机,一台微型透平发 生器和一台徽型循环器将检测仪的热盆传至低沮制冷机 该低沮制冷机设计、建造和调试总共用了不到十 FL个月的 时间。1998年 10月航天飞机 “发理号”将制冷机带上太空 试验 证实该机性能良好。该制冷机还要进行进一步的严
空分工段事故案例分析及处理经验交流--续一

空分工段事故案例分析及处理经验交流续一一、某空分装置冷箱炸裂喷砂事故分析1、问题描述2011年2月24日,某系统操作人员1:00发现冷箱压力出现明显上升,正常指标为0.00Kpa或0.01KPA,发现时为0.04KPA,当时总控人员立即通知现场人员到现场检查充气阀是否开得过大,现场是否有误喷砂情况,没有发现异常,认为是仪表只是有问题,通知仪表人员查看了冷箱压力变送器。
冷箱基础温度未发生任何变化。
2:00现场操作人员发现冷箱北侧约20米高度污氮管道连接处有珠光砂喷出。
立即通知化验室人员对冷箱下部外冒气体用测氧仪监测,东侧、南侧不报警,西侧报警,手动分析结果冷箱西氧含量36﹪,冷箱南侧31﹪.检查过程中2:30听见钢板破裂的声音,返回检查发现在冷箱南侧约18米高度,距离上塔安全阀40cm距离处出现裂缝,并有液体流出。
空分立即停止冷箱进气,上下塔排液,打开一个冷箱珠光砂卸料口和中部珠光砂口以及顶部的排气口,冷箱上下部压力回复正常数值。
从先现象判断冷箱漏液,无法直接判断原因,必须扒砂处理。
2、原因分析﹙1﹚根据化验室分析结果,冷箱西氧含量为36﹪、冷箱南氧含量为31﹪,从而判断漏液不是液氧,成份与液空含量近似,可能是液空管道泄漏。
﹙2﹚管道支撑不合适,原来检查冷箱内管道时,此管道的支撑抱箍断,厂家施工人员对管道支撑进行处理后,原来的废旧支撑应该去掉,但是没有去除,管道和旧支撑磨损造成管道漏液。
漏液之后,由于富氧液空在冷箱内部气化,造成冷箱的密封气压力高,高到一定程度时,由于冷箱无法承受住压力高,造成冷箱破裂。
3、处理措施及建议﹙1﹚、扒砂后去掉废旧支撑,更换此段管道。
对冷箱破裂处进行焊接。
﹙2﹚、冷箱内每次扒砂都应该检查支撑是否变形,是否合适,管道是否变形,焊缝是否开焊,并且安排专人负责检查﹙3﹚、如果防止这种现象的发生:总控人员应该注意冷箱的密封气压力是不是有较大的变化,如果有变化看情况处理。
二、某空分装置氧气放空阀及放空管线爆炸事故分析【简要经过】2010年11月1日,事发前3号空分装置冷箱高压液氧A泵正在运行;B泵检修后试运行,准备投备用。
空分事故案例概念

空分事故案例概念安阳钢铁集团公司制氧厂,河南安阳梅东路,455004"g(u(-N/I6c:v2m3某+N)l3G%M!某(~2A【摘要】一起空分开车冰堵事故的判断与处理6b:q%V1i)L+1o6w+r&a%_5]-%_'c#8R5f-g]#E某[(W+W--------------------------------------------------------------------------------&m6g5B1\6m(^0安阳钢铁集团公司信阳钢铁公司KDON—1500/1500—型制氧机系90年代初产品,为切换板翅式换热器流程,上、下塔分开,主冷在下塔顶部,靠液氧泵与上塔联接。
该制氧机配置一套加温系统,大加温时由两只干燥器产生的干净空气通过罗茨风机加压后送人空分系统进行加温,在整个大加温过程中,两只干燥器需相继投入使用。
8f8P.L;J'`#Q8L&F/|1j1事故经过#E6b(l:L某v4\)h|1a2000年6月底以来,该制氧机运行很不正常,现象是冷损增大,经常靠两台膨胀机运行来维持冷量平衡,氧产量大幅度下降。
根据有关现象怀疑液空吸附器泄漏,停车检查,发现两个硅胶排放口法兰漏,处理好后,进行大加温,然后重新启动。
某`+B(a!F,yM启动后运行至第二阶段时,发现氧液化器阻力增大,有冻堵的现象,随即板翅式换热器氧通道也被冻堵。
于是停车后对氧液化器和板翅式换热器进行单体加温。
吹通后,继续开车。
下塔产生液空,液空节流进上塔,上塔底部液面至1.6米时,启动液氧泵,主冷开始工作,空气大量进塔,下塔阻力由4kPa增至lOkPa,但上塔底部阻力一直满表(大于25kPa),主冷氧侧压力达0.07MPa,居高不下,不久上塔底部液位急剧下降,只得开大旁通阀,加大回流量,以维持液氧泵运转。
此时,主冷氧侧压力降至0.03kPa,下塔阻力降至4kPa,进塔空气量减少,主冷停止工作,上塔阻力仍满表,再过不久,上塔底部液位又涨高,主冷恢复工作,但不久主冷又停止工作,约4分钟波动一次,这是典型的上塔液悬现象,因处于开车阶段,主冷液位低,所以对下塔工况影响较大。
空分车间事故分析

空分车间事故分析一、背景介绍空分车间是一个重要的工业生产环节,主要用于将混合气体分离成不同组分。
然而,由于操作不当、设备故障或其他原因,空分车间事故时有发生,给工人的生命安全和生产环境带来了严重威胁。
因此,对空分车间事故进行详细分析,找出事故原因和改进措施,对确保工人安全和生产环境的稳定具有重要意义。
二、事故概述在XX年XX月XX日,位于某工业园区的空分车间发生了一起事故。
事故发生时,车间内有10名工人正在进行日常操作。
事故导致3名工人受伤,其中1人伤势严重,送往医院进行治疗。
事故发生后,工作人员立即采取应急措施,将事故区域封锁,并通知相关部门进行调查。
三、事故原因分析1. 设备故障:经初步调查,事故的起因是空分车间的某台设备发生故障。
该设备在运行过程中出现异常震动,导致部分管道连接松动,从而引发泄漏。
2. 人为操作不当:在事故发生前,工人没有按照操作规程进行操作,未及时发现设备故障的迹象,并未采取相应的措施进行处理。
这种操作不当增加了事故发生的风险。
四、事故影响分析1. 人员伤亡:事故导致3名工人受伤,其中1人伤势严重。
伤员的治疗费用和工伤赔偿将成为企业的负担,同时也对受伤工人的家庭造成了不可挽回的损失。
2. 生产中断:事故发生后,空分车间被迫停产,导致生产计划无法正常进行。
这将给企业带来直接的经济损失,并可能影响客户的信任和订单的延误。
五、事故防范措施1. 设备维护与检修:加强对空分车间设备的定期维护和检修工作,及时发现和处理设备故障,确保设备运行的稳定和安全。
2. 操作规程培训:加强对工人的操作规程培训,确保他们了解并严格按照规程进行操作。
提高工人对设备异常情况的敏感性,及时发现和处理潜在的安全隐患。
3. 应急预案制定:制定完善的应急预案,明确各级人员的职责和应急处置流程。
定期组织演练,提高员工的应急处理能力和反应速度。
4. 安全意识培养:通过开展安全培训和宣传活动,提高员工的安全意识和风险防范意识。
空分车间事故分析

空分车间事故分析一、概述空分车间是化工生产过程中的重要环节,但在操作过程中可能发生事故。
本文将对空分车间事故进行分析,包括事故原因、事故后果以及事故防控措施等方面的内容。
二、事故原因分析1. 设备故障:空分车间的设备故障可能导致事故发生,如压力容器爆炸、管道泄漏等。
这可能是由于设备老化、维护不当或者操作错误等原因引起的。
2. 人为因素:人为因素是导致事故的重要原因之一。
操作人员的疏忽大意、操作不规范、缺乏安全意识等都可能导致事故的发生。
此外,人为因素还包括管理层的不合理决策、缺乏有效的培训和监督等方面。
3. 环境因素:环境因素也可能对空分车间事故产生影响。
例如,恶劣的天气条件、地震等自然灾害可能导致车间设备损坏,从而引发事故。
三、事故后果分析1. 人员伤亡:空分车间事故可能导致操作人员和周围人员的伤亡。
这可能包括轻伤、重伤甚至死亡。
人员伤亡不仅对个人和家庭造成了巨大的伤害,也对企业的声誉和经济利益造成了严重影响。
2. 环境污染:事故可能导致有害物质的泄漏,对周围环境造成污染。
这对生态环境和人类健康都带来了潜在的危害。
3. 经济损失:事故造成的设备损坏、停产停工等都会给企业带来巨大的经济损失。
此外,事故还可能引发相关法律诉讼和赔偿,进一步加大了企业的经济负担。
四、事故防控措施1. 加强设备维护:定期对空分车间的设备进行检修和维护,确保设备的正常运行。
特别是对于老化设备,应及时进行更换或升级,避免设备故障引发事故。
2. 强化安全培训:对操作人员进行定期的安全培训,提高他们的安全意识和操作技能。
培训内容可以包括操作规程、紧急救援措施等方面。
3. 建立安全管理体系:企业应建立完善的安全管理体系,包括制定安全操作规程、设立安全责任岗位、建立安全检查制度等。
通过规范管理和监督,提高事故防控能力。
4. 应急预案制定:针对可能发生的事故情况,制定相应的应急预案。
预案应包括事故报告流程、应急救援措施、事故调查和处理等内容,以便在事故发生时能够迅速有效地应对。
空分车间事故分析

空分车间事故分析一、事故背景空分车间是化工企业生产过程中的关键环节之一,主要负责将混合气体分离成不同成分的气体。
然而,由于操作不当、设备故障或其他原因,空分车间事故时有发生,给企业生产和员工安全带来严重威胁。
因此,本文将对空分车间事故进行详细分析,以期找出事故发生的原因,并提出相应的预防措施,以确保空分车间的安全运行。
二、事故概述在2019年5月15日的上午10点,某化工企业的空分车间发生了一起严重事故。
事故发生时,空分车间正处于正常运行状态,突然发生了一次爆炸,造成了严重的人员伤亡和设备损坏。
事故导致3名员工死亡,10名员工受伤,其中2人伤势严重。
此外,空分车间的主要设备也受到了严重破坏,导致车间停产。
三、事故原因分析1. 设备故障:经初步调查,事故的起因是空分车间中的一台冷凝器发生了故障。
冷凝器是空分车间的核心设备之一,用于冷却和液化气体。
由于长时间运行和缺乏定期维护,冷凝器内部的管道堵塞,导致压力升高,最终引发爆炸。
2. 操作失误:事故发生前,空分车间的操作人员未能及时发现冷凝器的异常情况,并未采取相应的措施进行处理。
操作人员对设备的运行状态和维护要求了解不足,缺乏对潜在故障的判断能力和处理经验,从而未能及时发现和解决问题。
3. 安全管理不到位:企业在空分车间的安全管理方面存在一定的问题。
缺乏完善的安全制度和操作规程,没有进行定期的设备检查和维护,对操作人员的安全培训和技能提升也不够重视。
此外,企业对于事故隐患的排查和处理不够及时和彻底,导致事故的发生。
四、事故影响分析1. 人员伤亡:事故造成了3名员工死亡,10名员工受伤,其中2人伤势严重。
这不仅对受伤员工及其家属造成了巨大的伤痛,也给企业员工的安全意识和士气带来了负面影响。
2. 设备损坏:事故导致空分车间的冷凝器和其他相关设备受到严重破坏,需要进行大规模的维修和更换。
这不仅给企业带来了巨大的经济损失,还导致了车间的停产,影响了企业的正常生产。
空分事故案例分析 (1)
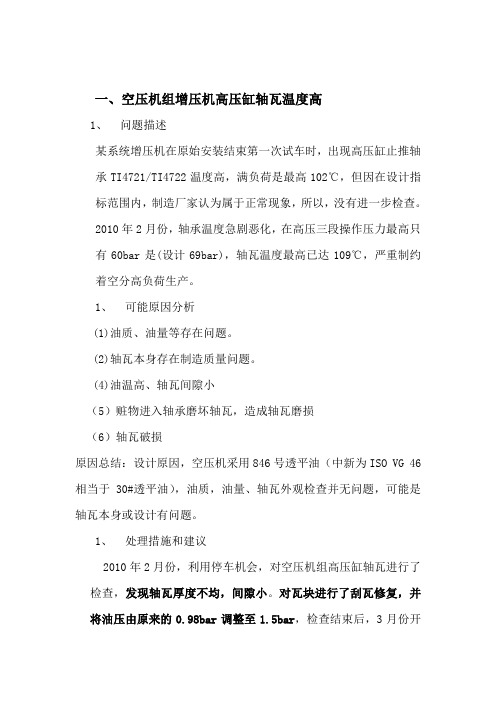
一、空压机组增压机高压缸轴瓦温度高1、问题描述某系统增压机在原始安装结束第一次试车时,出现高压缸止推轴承TI4721/TI4722温度高,满负荷是最高102℃,但因在设计指标范围内,制造厂家认为属于正常现象,所以,没有进一步检查。
2010年2月份,轴承温度急剧恶化,在高压三段操作压力最高只有60bar是(设计69bar),轴瓦温度最高已达109℃,严重制约着空分高负荷生产。
1、可能原因分析(1)油质、油量等存在问题。
(2)轴瓦本身存在制造质量问题。
(4)油温高、轴瓦间隙小(5)赃物进入轴承磨坏轴瓦,造成轴瓦磨损(6)轴瓦破损原因总结:设计原因,空压机采用846号透平油(中新为ISO VG 46相当于30#透平油),油质,油量、轴瓦外观检查并无问题,可能是轴瓦本身或设计有问题。
1、处理措施和建议2010年2月份,利用停车机会,对空压机组高压缸轴瓦进行了检查,发现轴瓦厚度不均,间隙小。
对瓦块进行了刮瓦修复,并将油压由原来的0.98bar调整至1.5bar,检查结束后,3月份开车,在90%生产负荷下,轴瓦温度最高76℃,取得了不错的效果。
沈鼓制造的压缩机普通存在轴瓦温度有一个偏高,建议对机组油质,油压,轴瓦进行检查,若以上没有问题,联系厂家解决。
二、分子筛蒸汽加热器泄漏1、问题描述2009年1月31号上午,某系统操作人员发现在分子筛蒸汽加热器E4201的底部水侧管子与壳体的间隙有水流出,为进一步确认,将蒸汽加热器底部保温全部拆除,打开蒸汽加热器底部壳侧盲法兰处有大量空气排出,而且还随着所加工空气的流量变化而变化,由此判断,蒸汽加热器管侧有漏点。
2、可能原因分析(1)分子筛蒸汽系统超压,超出材料承受范围。
(2)运行中,蒸汽加热器管壳侧温差过大,产生应力。
(3)蒸汽加热器后汽水分离器无液位,产生水击。
(4)冬季停车期间,防冻不彻底,冻坏设备。
最终原因:在装置运行期间,严格控制蒸汽加热器的操作压力和温度,分离器液位控制在250mm以上,没有发生过水击现象。
- 1、下载文档前请自行甄别文档内容的完整性,平台不提供额外的编辑、内容补充、找答案等附加服务。
- 2、"仅部分预览"的文档,不可在线预览部分如存在完整性等问题,可反馈申请退款(可完整预览的文档不适用该条件!)。
- 3、如文档侵犯您的权益,请联系客服反馈,我们会尽快为您处理(人工客服工作时间:9:00-18:30)。
八 钢 公 司制 氧 K DO N A r 一 2 0 0 ( 】 0 / 2 0 0 0 0 / 7 5 0型 l
点 进入 珠光 砂 。 设备 厂 家人 员于 2 0 0 9 2月 3日 到达 现场 ,对 漏液 点 及冷箱 内 气体纯 度进 行综 合分
号空 分设 备 , 采用 分子 筛 吸附净 化 , 增 压透 平膨 胀机 制 冷 ,膨胀 空 气送 上塔 和全 精馏 无 氢制氩 外压 缩流
位汁 f 取 压 管 线 在 设 备 部 位焊 缝 热 影 响 f ) £ 上 部 开
影响区上部开裂, 管道表面无硬伤原因同上。
2 . 2 . 2 珠光 砂水 分 含量超 标较 大 f } 1 于珠 光 砂 本身 较 干燥 , 含水 约 在 0 . 2 %, 当与 空气 接触 时空 气 中的水 分就会 吸 附到 内部 ,本 次装 入 的珠光 砂抽 检 含水 为 0 . 8 % 。( 杭 氧标 准 l %标 准
裂, 仪表管 向下弯曲; 粗氩 Ⅱ 塔液位计上取压管线在 设 箭 部位 焊缝 热影 响 f ) ( 断裂, 管 道无 明显 变形 ; 塔 内
还 - - 一些 小 直径管 道 及仪表 取 压管道 变形 。
号H T 7 0 1 2 — 8 2 、 林德标准号 L s l 5 2 — 4 , 据杭氧专家现 场告 知新 标 准 为 0 . 5 %) , 由于扒砂 是 在 3月 , 天气 潮
的运行状况 ,设备厂家建议对该套冷箱系统做彻底 的检修 ,以保证该设备能长期稳定运行 。2 0 0 9 年2
月 l 0 b l 1 号2 0 0 0 0 m / h空分 机组 进行 年修计 划 。 空 分冷 箱扒砂 完 成后 ,检 查发 现主 冷液 氧液 位计下 阀 有 砂 眼 ,空分 本体在 二周 内检 修 完成 。按 照年休 计
An a l y s i s t h e Ac c i d e n t o f F r a c t u r e d Pi p e l i n e i n Co l d Bo x o f AS U & I t s Tr e a t me n t
LI Ga n g
( E n e r g y C e n t r e, B a y i I r o n& S l e d C o . , B a o s l e e l ( ; n i l I j ) )
Ab s t r ac t : r r hi s pa p e r a na l y z e d t he a r ( ‘ i ‘ l e nt o f f r a ( q l l r e  ̄ I pi pe l i ne i n t ( l b o x of " 2 000 0Nm3 / h 、I : S f M’ i n g r I I I mi r i g. t i n ’ o ug h o pl i mi z i n g t m ̄ e r( 1 e l a r i d 1 t t mi r i l l g t he d a ma g e d J r e a e he d I h e de s i g n p a r a l n e l e r .AUS r I i nn i l / g i n g o o d( ' 0 I l l l i l i o n. Ke y wor ds :p e r ] i | e;l e a k a g e;s t r e s s ;e o mp e , ns a t i o n;r e i n f o r ( ! e n l e n [ ;e & l } 1 ( ’ x ( ‘ O I ’ l l i n g( , 1 1 .Ti l f ‘O p e l a l l ot I a l l l e [ i 、 l s v
为了避免产生更大损失 , 停运 了空分设备并排液 , 使 其 自然升温 , 精馏塔内通入气体保持正压, 保证泄漏
联 系人 : 乍H 4 , , 3 9岁. 火学 , 机做 没汁圳造及 I I 动化 - u I 师, 屿伫术齐( 8 : , 0 0 2 2 ) 宝钢 集圳八钢公 司能源 ・ f 『 . 、 删 钣分厂
点较远 ,上部安装保护架后与之同定导致 自由端较
短 ,设 备投 用后 的仪 表管线 吹 除温度 降 低 、补偿 不 足, 导致 在设 备部 位焊 缝热 影响 区断 裂 , 致使粗 氩 Ⅱ 塔 带压 产生 假液 位 ( 此时 液位计 上 管 m于断 裂处 于 大 气 压 环境 , 液 位 计 下 管 与塔 体 压 力约 5 k P a , 折 合 液 位约 3 0 0 mm, 与假液 位数 值吻 合 ) 。 综 合现 场情 况和 同类 事故 案例 ,参 与事 故处
1 事故过程简述
2 0 0 9年 1月 2 9日 l 6 : 3 0发现 正 在运 行 的 1 号
2 0 0 0 0 m 3 / h空 分 机组 下 塔 液氮 回流 阀 结 霜部 位 有 冷 气 冒} } I , 且 还 有 少量 珠光 砂排 , 2小 时后 下 塔液 氮 回流 阀 V 4阀下 方 结 霜 部 位有 微 量 的 液体 外 流 , 起 初 以 为是 阀 门泄 漏 ,当将 V 4阀下 方 的大 块结 霜 清 除 后发 现 冷箱板 冻 裂 。l 号2 0 0 0 0 N I T I / h机组 冷箱 北 侧冻裂, 有 少量 低温 液体 通过 裂缝 夹带珠 光 砂流 ,
1 . 液氩计量罐进液管断裂 ; ! . 粗 氩 液 空 回 流 管 变形 严 重 ;
的技术 人 员… 一 致 认 为 两 项原 闪是 造成 此 次事 ^ 史 的
主要原 冈 。管道 的应 力不 足是 次: 要原 因 。
3 . 粗氩 I 1 塔 底部液位计 负压 室仪表 管断 裂; 4精氩塔底部 液
充 过程 中 , 在倾倒 珠 光砂 时 口袋 内膜 翻 撕烂 , 后 续 的珠 光砂 进 人形 成 小包 装 口袋通 过 格 网进 人 冷 箱 。 精 氩塔 蒸发 器液 位计 上取 压管 线在设 备 部位 焊缝 热
却精氩塔 , 1 9 : 4 2 精氩塔蒸发器底部 现液体 ,精氩 纯度合格准备充灌 ,但是巡检人员发现 V 4阀上 阀 大 面积结 霜 , 冷箱 板有 裂 口 , 且 有 液 体流 , 冷箱 面 板东侧阀箱下部约 1 . 5 m范围内冷箱面板开裂。 扒砂 后 发 现精 氩塔 液 氩 m 口至 液氲 计 量罐 阀后管 道 ( ‘ | ) 3 0 a r m)与液氩计量罐连接处焊缝热影响区上部 开裂, 闷 . 此 管道 严重 向下弯 曲变形 ; 精 氩塔 蒸发 器液
2 0 1 3 年第 1 期
新 疆 钢 铁
总1 2 5 期
空分设 备冷箱 内管道 断裂事 故分析及处理
李 刚
( 宝钢集 I  ̄ : I A钢公 司能源巾心制氧分厂 ) 摘 要: 针对 2 0 0 0 0 mV h 分机组仵运行 中j { { 现冷箱板结霜冻裂事故进行 r 分析 ? 迎过埘上 } } 内缺陷锊路优化
位计上 阀仪表 管断裂, 及塔 内部 分仪 表管变形 严重
图 1 空 分 机 组 冷箱 冻 裂 后塔 内设 备损 坏 情 况 的 示 意 图
3 对 损坏 设 备 的 处 理
3 . 1 断裂管 路 处理措 施
2 - 2 现场管路损坏情况分析 2 . 2 . 1 块状软物体进入冷箱使管道受损 精氚塔液氩 f _ J 阀, 根据
现场 漏液 情况 判断 为液 空节 流 阀冷箱 下部 附近 的液 氧管 道漏 液 , 冷箱 板冻 裂 的面积 约为 2 m 。根据设 备
程, 上塔 、 粗氚塔和精氩塔采用规整填料塔 , 下塔采 用筛板塔。 空分塔因设备故障造成塔内泄漏 , 经过分 析找到造成泄漏的原因, 并进行了优化 , 机组启动后 运 行 正常 , 各项 参数 均 达到 没 汁要 求 。
焊 缝热 影 u 向 上部 开裂 ,检查 管 道弯 『 抖 1 变 肜 可以 发
( 1 ) 全 面检查仪 表管 线及 小 径 ( 中5 5 m m 以下 ) 管路 , 找f f I 断裂 位置 , 切 除断裂 位置 的焊 缝及 热影 响 I , 重新 焊接 ; 对 变形 较大 的管 道校形 或 更换 。 ( 2 ) 对 冷箱 内变形 严重 的管 道或 弯头 进行 更换 处理 ,并 根 据 现场 情况 增加 补偿 和进 行改 路 处理 。 ( 3 ) 对冷 箱 上 的 所有 阀 门 、管道 支 架进 行俭 及增 补部 分 同定 支架 , ( 4 ) 检 查冷箱 内 艺管道 液封 及气 封 , 对不 合 理 的地方进 行 优化 ( 5 ) 检查 冷箱 『 大 J 所有 液位 汁的配
标 。3月 2 5日 l 8 : 3 0进 行投用 粗 氩系 统并 调整粗 氩 纯度 , 4月 4日粗 氩 系统 投 运 正 常 ,T 艺 氩纯 度 达 1 . 5 2×l 0 。 粗 氩系 统 T况正 常 。 4月 4日 1 7 : 0 0点 冷
珠光砂 中发现异物进行判断 : ( 1 ) 在检修完成加砂的 过 程 中提升 机 曾m现 多 次故障 停运 现象 ,在维 修 提 升机过程中发现提升机部分附件丢失 ( 在扒 f } J 的珠 光砂中曾发现其附件 ) ; ( 2 ) 在装砂的过程中发现有残 存 的珠光砂 口袋内膜 ,认为这种物体可能是盛装有 珠 光砂 口袋 内膜 残片 包裹珠 光砂 形成 的 ,珠光 砂填
管 道局 部 弯 曲 , 产生 应 力集 中 , 损 坏 了 管道 薄 弱 处 ,
检修 中更换的精氩去储槽 、 粗氩液空同上塔管道及 粗氲 流量计 仪 表保 护 支架 的变形 状况可 以证 明。
2 . 2 3 管 道应 力补偿 不 够 南于 粗氚 Ⅱ塔 液位计 上 取 压管线距 离 冷箱 同定
划 ,辅助设备和空分本体于 3 月 3日完成。 3 月8 日冷箱装填珠光砂 , 2 4小时作业 ,且此时天气状况
较差 ; 装砂 过程 中提 升机 } } I 现故 障 , 发 生 滑 轮掉 落 、