京沪高铁简支箱梁预制施工工艺
京沪高铁适用CRTSII型无砟轨道预制箱梁梁面施工技术
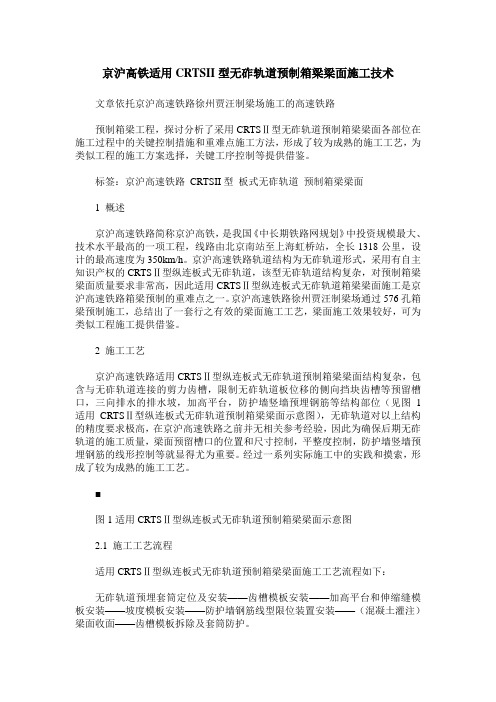
京沪高铁适用CRTSII型无砟轨道预制箱梁梁面施工技术文章依托京沪高速铁路徐州贾汪制梁场施工的高速铁路预制箱梁工程,探讨分析了采用CRTSⅡ型无砟轨道预制箱梁梁面各部位在施工过程中的关键控制措施和重难点施工方法,形成了较为成熟的施工工艺,为类似工程的施工方案选择,关键工序控制等提供借鉴。
标签:京沪高速铁路CRTSII型板式无砟轨道预制箱梁梁面1 概述京沪高速铁路简称京沪高铁,是我国《中长期铁路网规划》中投资规模最大、技术水平最高的一项工程,线路由北京南站至上海虹桥站,全长1318公里,设计的最高速度为350km/h。
京沪高速铁路轨道结构为无砟轨道形式,采用有自主知识产权的CRTSⅡ型纵连板式无砟轨道,该型无砟轨道结构复杂,对预制箱梁梁面质量要求非常高,因此适用CRTSⅡ型纵连板式无砟轨道箱梁梁面施工是京沪高速铁路箱梁预制的重难点之一。
京沪高速铁路徐州贾汪制梁场通过576孔箱梁预制施工,总结出了一套行之有效的梁面施工工艺,梁面施工效果较好,可为类似工程施工提供借鉴。
2 施工工艺京沪高速铁路适用CRTSⅡ型纵连板式无砟轨道预制箱梁梁面结构复杂,包含与无砟轨道连接的剪力齿槽,限制无砟轨道板位移的侧向挡块齿槽等预留槽口,三向排水的排水坡,加高平台,防护墙竖墙预埋钢筋等结构部位(见图1适用CRTSⅡ型纵连板式无砟轨道预制箱梁梁面示意图),无砟轨道对以上结构的精度要求极高,在京沪高速铁路之前并无相关参考经验,因此为确保后期无砟轨道的施工质量,梁面预留槽口的位置和尺寸控制,平整度控制,防护墙竖墙预埋钢筋的线形控制等就显得尤为重要。
经过一系列实际施工中的实践和摸索,形成了较为成熟的施工工艺。
■图1适用CRTSⅡ型纵连板式无砟轨道预制箱梁梁面示意图2.1 施工工艺流程适用CRTSⅡ型纵连板式无砟轨道预制箱梁梁面施工工艺流程如下:无砟轨道预埋套筒定位及安装——齿槽模板安装——加高平台和伸缩缝模板安装——坡度模板安装——防护墙钢筋线型限位装置安装——(混凝土灌注)梁面收面——齿槽模板拆除及套筒防护。
高铁简支箱梁的施工工艺分析
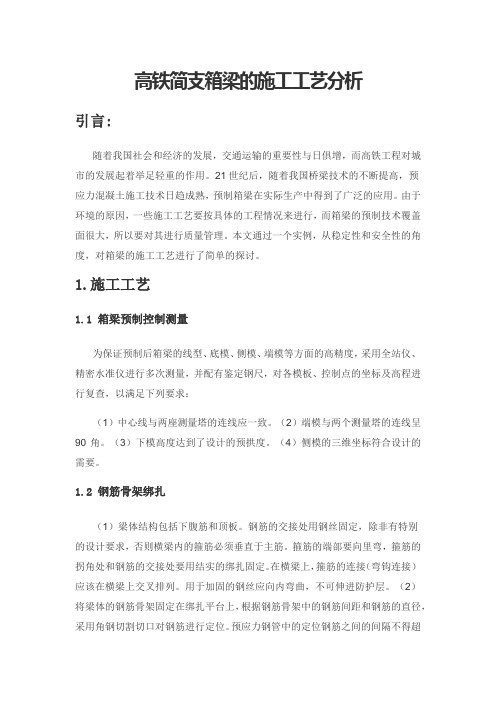
高铁简支箱梁的施工工艺分析引言:随着我国社会和经济的发展,交通运输的重要性与日俱增,而高铁工程对城市的发展起着举足轻重的作用。
21世纪后,随着我国桥梁技术的不断提高,预应力混凝土施工技术日趋成熟,预制箱梁在实际生产中得到了广泛的应用。
由于环境的原因,一些施工工艺要按具体的工程情况来进行,而箱梁的预制技术覆盖面很大,所以要对其进行质量管理。
本文通过一个实例,从稳定性和安全性的角度,对箱梁的施工工艺进行了简单的探讨。
1.施工工艺1.1 箱梁预制控制测量为保证预制后箱梁的线型、底模、侧模、端模等方面的高精度,采用全站仪、精密水准仪进行多次测量,并配有鉴定钢尺,对各模板、控制点的坐标及高程进行复查,以满足下列要求:(1)中心线与两座测量塔的连线应一致。
(2)端模与两个测量塔的连线呈90°角。
(3)下模高度达到了设计的预拱度。
(4)侧模的三维坐标符合设计的需要。
1.2 钢筋骨架绑扎(1)梁体结构包括下腹筋和顶板。
钢筋的交接处用钢丝固定,除非有特别的设计要求,否则横梁内的箍筋必须垂直于主筋。
箍筋的端部要向里弯,箍筋的拐角处和钢筋的交接处要用结实的绑扎固定。
在横梁上,箍筋的连接(弯钩连接)应该在横梁上交叉排列。
用于加固的钢丝应向内弯曲,不可伸进防护层。
(2)将梁体的钢筋骨架固定在绑扎平台上,根据钢筋骨架中的钢筋间距和钢筋的直径,采用角钢切割切口对钢筋进行定位。
预应力钢管中的定位钢筋之间的间隔不得超过500mm。
(3)钢筋骨架的绑扎,应严格按图纸的要求进行。
钢筋接头的绑扎一般规定:①钢筋弯曲角度和纵向分布筋交点必须进行绑扎;②下边缘的尺寸箍筋接头需交叉捆绑;③剩余的每个交会处可以使用“梅花”捆绑;④绑扎位置要牢固,如果有断裂的扎线,必须重新捆扎;⑤为了确保钢筋骨架在绑扎后不发生变形,必须将各节点进行“八字形”捆绑。
(4)底腹筋和顶板钢筋采用整体绑扎,首先将底板和腹板的钢筋进行绑扎,再进行顶板钢筋的绑扎。
预制箱梁施工工艺
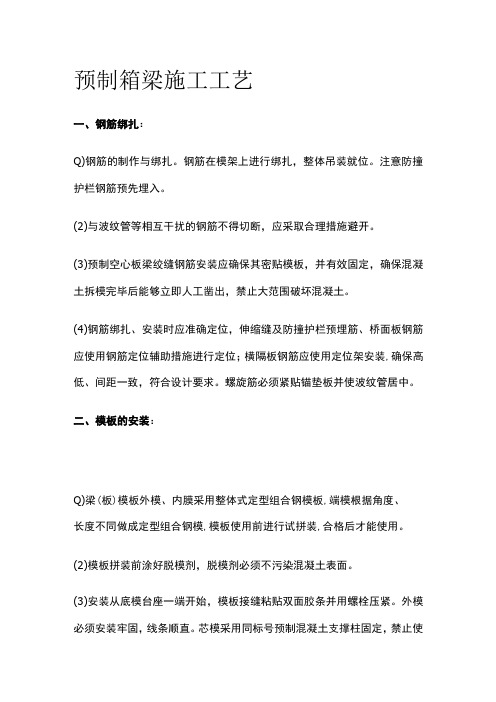
预制箱梁施工工艺一、钢筋绑扎:Q)钢筋的制作与绑扎。
钢筋在模架上进行绑扎,整体吊装就位。
注意防撞护栏钢筋预先埋入。
(2)与波纹管等相互干扰的钢筋不得切断,应采取合理措施避开。
(3)预制空心板梁绞缝钢筋安装应确保其密贴模板,并有效固定,确保混凝土拆模完毕后能够立即人工凿出,禁止大范围破坏混凝土。
(4)钢筋绑扎、安装时应准确定位,伸缩缝及防撞护栏预埋筋、桥面板钢筋应使用钢筋定位辅助措施进行定位;横隔板钢筋应使用定位架安装,确保高低、间距一致,符合设计要求。
螺旋筋必须紧贴锚垫板并使波纹管居中。
二、模板的安装:Q)梁(板)模板外模、内膜采用整体式定型组合钢模板,端模根据角度、长度不同做成定型组合钢模,模板使用前进行试拼装,合格后才能使用。
(2)模板拼装前涂好脱模剂,脱模剂必须不污染混凝土表面。
(3)安装从底模台座一端开始,模板接缝粘贴双面胶条并用螺栓压紧。
外模必须安装牢固,线条顺直。
芯模采用同标号预制混凝土支撑柱固定,禁止使用钢筋。
(4)负弯矩齿板的定型模板厚度不小于IOmm.三、波纹管的安装:Q)波纹管在安装前应通过检查,确保不变形、渗漏现象。
负弯矩波纹管采用镀锌波纹管。
(2)波纹管的连接,采用大一号同型波纹管做接头管,接头管长30cm o波纹管接头及锚垫板喇叭管接头处用密封胶带封口。
四、锚具安装:Q)锚具出厂时附带本批产品出厂检验证书。
(2)在锚垫板上,采用适当定位措施,保证锚环与孔道的同心度。
五.钢绞线:Q)预应力钢绞线在现场根据计算下料长度用砂轮切割机切割切割前用黑色胶布将切割部位缠紧,防止切割时〃炸头〃,禁止采用气焊和电焊。
(2)将切好的钢绞线编束,并每隔1.5—2.0m用绑丝绑扎。
(3)钢绞线应随用随下料,防止因存放时间过长锈蚀,不得出现死弯。
六、混凝土的浇筑和拆模Q)在钢筋、模板、预埋件、预应力孔道、混凝土保护层厚度等检查合格后才能浇筑混凝土。
(2)在浇筑前检查施工机具的完好性及各种设施的安全性是否达到安规定要求;振捣器是否正常工作。
京沪高铁简支箱梁预制施工工艺

京沪高铁简支箱梁预制施工工艺摘要京沪高速铁路无砟轨道采用了CRTSⅡ型板式无砟轨道结构,对简支箱梁梁面平整度和预埋件提出了很高要求,本文以京沪高铁某梁场为例简要介绍了适用于Ⅱ型板式无砟轨道结构的简支箱梁预制施工工艺。
关键词京沪高铁CRTSⅡ型板式无砟轨道箱梁预制施工工艺1箱梁简介京沪高铁是世界上一次建设标准最高、线路最长的高速铁路,设计运营速度达到了380km/h,所采用的轨道结构主要是CRTSII型板式无碴轨道结构。
这种新型的轨道结构对预制箱梁提出了新的接口要求,和以往铁路客专箱梁相比,具有如下特征:(1)取消两侧检修平台,梁宽由13.4m变更为12m。
(2)底座板下的梁面设置了加高平台,形成六面形排水坡构造,要求在箱梁混凝土浇筑时一次成型。
梁端1.45m加高平台比中部加高平台底50mm,用于放置高强挤塑板。
(3)加高平台固定支座端设置了剪力齿槽,两侧设置了2~3排侧向挡块齿槽。
(4)梁面防水采用喷涂聚脲防水层,在架梁后施工。
京沪高铁某梁场共有预制梁615孔,为无碴轨道后张法预应力混凝土双线简支箱梁,单箱单室等高度形式,梁高均为3.05m,桥面宽12m,横桥向支座中心距为4.5m。
梁体混凝土采用C50高性能混凝土约320方,采用C50无收缩混凝土封锚,采用1×7-15.2-1860型预应力钢绞线,自锚式拉丝锚固体系。
2施工工艺2.1工艺流程以采用的横列式台座布置,移梁小车横移梁,钢筋分体绑扎的某梁场为例,介绍制梁工艺流程如图2.1。
2.2工艺操作要点2.2.1模板工程模板均采用厂制成套模板,分为底模、侧模、端模、内模四大部分。
采用移梁小车横移梁方式,按1个台座1套底模、2个台座共用1套侧模的方案配置,内模、端模与侧模按1:1的比例配置。
模板首次使用时,将其与混凝土接触的表面全部打磨干净,然后涂防锈油,再重复打磨、涂油两至三次,确保模板表面光滑、首次混凝土表面色泽一致。
各部分模板安装要点如下:(1)底模:底模固定在制梁台座上,按设计要求设置反拱,并预留梁体压缩量。
京沪高速铁路箱梁预制、架设施工细则

京沪高速铁路简支箱梁预制架设施工实施细则铁道部京沪高速铁路建设总指挥部京沪高速铁路股份有限公司二○○八年二月前言为规范京沪高速铁路参建各方建设行为,细化施工工艺标准和操作规程,强化过程质量控制,减少质量通病,提高工程质量,做到源头把关、过程控制、精细管理,实现建设世界一流高速铁路目标,总指(公司)组织编制了京沪高速铁路站前主要工程施工实施细则:高性能混凝土施工实施细则;路基工程施工实施细则;隧道工程施工实施细则;桥梁桩基施工实施细则;路基CFG桩基施工实施细则;简支箱梁预制架设施工实施细则;工程质量无损检测实施细则。
本细则共有5章,第一章工程概况,第二章施工准备,第三章箱梁预制,第四章箱梁架设,第五章质量检验.本细则参照《客运专线铁路桥涵施工技术指南》(TZ213—2005)、《客运专线铁路桥涵工程施工质量验收暂行标准》(铁建设[2005]160号)、《350km/h客运专线预应力混凝土预制梁暂行技术条件》(铁科技[2004]120号)、京沪高速铁路桥梁工程相关技术文件及箱梁管理和施工经验编写。
在执行本细则的过程中,可根据工程进展和具体情况,进行细化和补充,如与国家或行业标准矛盾之处,请以标准为准。
本细则可作为参加京沪高速铁路建设各级人员的自学或培训教材.本细则由总指(公司)组织编写,中铁十六局集团参与编写。
本细则由总指(公司)技术质量部负责解释。
目录第一章工程概况 (1)第二章施工准备 (3)第一节制梁场规划 (3)第二节设备选型 (9)第三节试预制及技术参数试验 (11)第四节批量验收和颁发许可证等基本程序和相关要求 (12)第三章箱梁预制 (20)第一节总体技术要求 (20)第二节箱梁制作施工工艺流程 (21)第三节模板加工、制作及拼装 (21)第四节钢筋加工、钢筋骨架制作及安装 (28)第五节箱梁混凝土施工 (37)第六节预应力施工、管道压浆及封端 (44)第七节移梁及存梁 (49)第八节桥面防水层、保护层施工 (50)第九节预埋件安装 (51)第十节标志及制造技术证明书 (51)第四章箱梁架设 (52)第一节施工准备 (52)第二节预制箱梁架设 (54)第三节特殊条件下架梁作业 (61)第四节架桥机转场及调头 (62)第五节支座安装 (65)第五章质量检验 (67)附录一常见质量通病及其预防或纠正措施 (82)参考资料:钢筋机械连接技术指导书 (89)参考资料:TGM铁路桥梁支座灌浆料技术说明 (113)第一章工程概况一、全线桥梁设计情况京沪高速铁路正线桥梁数量大,具有新材料使用广、新技术要求高、施工复杂的特点.1。
京沪高速铁路预制箱梁架设施工
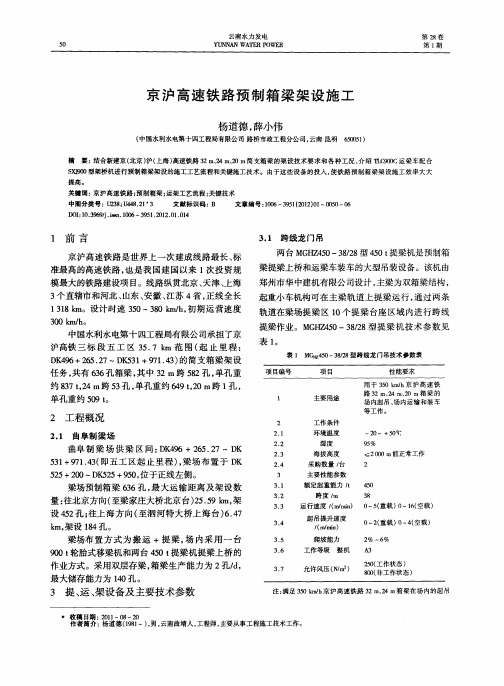
~ m 一 m ,
O~3 外轮廓Leabharlann 寸 适用坡度 ( 满载时 )
接 地 比压 /la bP 自重 , t
4 . 26mx66mX . 3. 5m ±3 0 I 4 0 I ⅢI
…
长 ×宽 ×高
一 …
S. 0 X 9 型架桥机进行预制箱梁架设 的施工工艺流程和关键施工技术 。由于这些设备的投入 , 铁路预制箱 梁架设施工效率 大大 1 0 使
提高。
关键词: 京沪高速铁路 ; 制箱梁 ; 预 运架工艺流程 ; 关键技术
中图分类 号:I 3 ; 482 3 Y 8 U 4 .1 2 文献标识码 : B 文章编号:06 9 12 1 }1 0 0 6 10 —35 (02 0 —05 —0
表 3 I9 1 T ̄  ̄C 运梁车主要技术性能参数表
3 2 架桥机 .
SJ0 X9 箱梁架 桥机 由石家庄铁 道学 院设计 研 0 制, 用于高速铁路 、 客运专线双线整孔箱梁 的架设 。 为步履式、 腹内喂梁 , 起重小车吊梁 、 移梁 , 两跨连续 导梁架桥机。可 以架设 3 、4n 2 l 2 n2 、0 等跨及变 i l n
4 13 施工 准备 ..
1 联 系线下工程施工单位交接桥梁架设需要 ) 的下列竣工资料 : 变更设计资料、 工点表、 桥梁墩 台 距离实测与设计对照表 、 桥头线路中线基桩表、 水准 基点表 、 桥头路基竣工检查表 、 沉降观测资料及评估 报告 。 2 检查核对架梁所需工程设计文件和线下工 ) 程施工单位移交的竣工资料 , 发现问题及时联 系有 关单位解决。 3 编制架梁作业技术交底资料 。 ) 4 联系线下 工程施工单位交接桥头线路 中线 ) 及水平桩橛和桥梁墩 台竣工标桩标线 , 复查线 间距 离和桥梁支座锚栓孔位置、 深度、 尺寸 , 测量设置架 梁作业需要的标桩和标线 。 5 )对架设 错 置梁 、 跨 梁 、 曲线 半 径 梁 等 工 变 小 况进行架梁方案设计和桥梁结构安全检算 。 6 )当架桥机 支腿位于其他结构形式 的桥梁上
京沪高铁双层贝雷梁支架现浇32m简支梁施工技术总结 - 修改

京沪高铁双层贝雷梁支架现浇32m简支梁施工技术总结撰稿人:【摘要】现浇梁简支箱梁在京沪高铁济南地区应用较为广泛。
下面以跨济兖公路特大桥32m现浇梁为例,对双层贝雷梁支架法原位现浇简支箱梁技术进行总结。
一、主要工程特点1、无河流影响;2、桥址表层地质为新黄土、稳定性好;3、施工工期紧迫;二、工艺特点简支箱梁梁体采用贝雷支架原位现浇施工,双层贝雷梁作支架。
支架体系结构自下而上由钢管立柱、分配梁、落模砂箱、贝雷梁及底模、侧模及支撑等构成。
钢管立柱布于两端并支撑在承台上,中间不设支墩。
采用此种施工方案用于现浇梁的支架系统避免了基底处理,克服了不均匀沉降对现浇箱梁施工线形的影响,为现浇梁施工安全提供一种安全、经济、快速的施工方法。
本工艺有如下特点:1、与满堂支架法比较有适用性广、方便快捷的特点;2、利用贝雷梁作为支架系统,用螺旋钢管支撑在承台上,贝雷桁架是定型产品,承台属于刚性结构,因此支架系统仅在第一孔时预压,后续施工不再需要预压,加快施工进度,节约预压成本,节省基底处理费用;3、与移动模架法相比,投入低、适用性广;4、贝雷支架具有设备造价相对较低、操作方便灵活、适应性强、占用施工场地少、节约制架设备投资等特点。
简支箱梁梁体采用贝雷支架原位现浇施工,双层贝雷梁作支架。
支架体系结构自下而上由钢管立柱、分配梁、落模砂箱、贝雷梁及底模、侧模及支撑等构成。
钢管立柱布于两端并支撑在承台上,中间不设支墩。
四、主要施工方法每套贝雷梁施工配备2套支架、钢管立柱和砂箱、2套底模、1套侧模、1套内模,施工循环周期14天。
贝雷支架、模板在现场组拼,均由25t和16t的汽车吊机作业安装。
侧模和支撑采用卷扬机拖拉至梁端,贝雷片由25t吊车吊至下一孔梁搭设好的支架上。
钢筋、钢绞线:钢筋在加工场集中加工,运输至梁底,由汽车吊配合人工搬运,在模内绑扎成型。
钢绞线采用先穿法。
梁体混凝土由自建22号搅拌站提供,供应能力充足。
五、工艺重点、难点采用双层贝雷支架法,在施工过程中有以下重难点:1、吊装作业要求两台25t吊车必须同步操作,严格听从指挥员的手势及指令。
京沪高铁预应力混凝土预制箱梁施工监理实施细则

预应力混凝土预制箱梁施工监理实施细则8.1 预制箱梁采用的施工工艺及方法8.1。
1本标段箱梁预制实行工厂化施工管理,并需按程序获得全国工业产品生产许可证。
8.1。
2 预制箱梁各部模板均采用钢模板,内模采用液压伸缩式结构。
8。
1。
3 箱梁底、腹板钢筋骨架、桥面板钢筋骨架均在专用绑扎胎具上进行绑扎成型,进行整体吊装.8。
1.4 预应力筋采用1×7—15.2—1860-GB/T—5224-2003型钢铰线,锚具采用夹片式锚具,预施应力采用三次张拉(预拉、初拉和终拉),两端同步进行,预应力预留孔道采用预埋金属波纹管.8.1.5 箱梁混凝土采用高性能混凝土配合比设计,采用拌合站进行混凝土的拌制,自动上料,自动计量。
8。
1.6 混凝土浇筑采用两台混凝土输送泵同时进行浇筑,振捣采用附着式振捣和插入式振捣,混凝土浇筑宜在6h内完成,浇筑顺序为腹板、底板、桥面板。
8.1.7 梁体混凝土浇筑完毕后,立即覆盖养护膜,采用养护棚内蒸汽养护。
8.1。
8 采用900吨轮胎式提梁机移动箱梁。
8.1.9 采用真空管道压浆.8.2原材的要求和控制原材料应有供应商提供的出厂检验合格证书,并应按有关检验项目、批次规定,严格实施进场检验,检验复试合格后方可使用,禁止不合格材料进场。
8。
2.1 水泥应采用品质稳定,强度等级不低于42.5级的低碱硅酸盐或低碱普通硅酸盐水泥,水泥熟料中C3A含量不大于8%;矿物掺和料仅限于磨细矿碴粉或粉煤灰;水泥的比表面积不宜超过350m2/kg,碱含量不应超过0.6%,氧化钙含量不应超过1。
0%;其余性能应符合相关的规定。
(1) 任何新选货源及使用同厂家、同批号、同品种的水泥达3个月及出厂日期达3个月的水泥,要进行抽样检测,检测的项目有:比表面积、烧失量、游离CaO含量、MgO含量、SO3、CL—含量、细度、凝结时间、安定性、强度、碱含量。
(2)同厂家、同批号、同品种、同强度等级、同出厂日期且连续进场的散装水泥500t(袋装不大于200t)为一批,现场取样,进行细度、凝结时间、安定性、抗压强度的检验。
京沪高铁( )m连续梁施工技术方案

京沪高速铁路(60+100+60)m连续梁施工方案二00九年二月十八日第1章编制依据与编制原则1.1 编制依据1.1.1《xx特大桥(D-2)段-DIK23+230.56~DIK23+657.23》,图号:京沪高京徐施桥-011.1.2《桩基钢筋布置图》,图号:京沪桥通-241.1.3《承台钢筋布置图》,图号:京沪桥通-211.1.4《无碴轨道预应力混凝土连续梁(双线)》,跨度:60+100+60m,图号:通桥(2008)2368A-V1.1.5《无碴轨道预应力混凝土连续梁(双线)》,跨度:60+100+60m,图号:通桥(2008)2368A-V(适用CRTSⅠ.Ⅱ型板式无砟轨道结构补充设计图纸)1.1.6《信号配合》.《通信配合文件》.《电气化配合设计文件-第一册》.《电气化配合设计文件-第二册》及其它四电文件1.1.7《高速双线桥梁综合接地钢筋布置图》,图号:京沪桥通-221.1.8《高速正线桥梁防震落梁措施》,图号:京沪桥通-37修1.1.9《铁路桥梁大吨位球型钢支座(LXQZ型)安装图》,图号:叁桥通(2008)8360-LXQZ-JH1.1.10《常用跨度梁桥面附属设施-伸缩缝》,图号:通桥(2008)8388A1.1.11《桥上CRTS II型板式无砟轨道预埋件设计-(第一册)》,图号:京沪高京徐施轨061.1.12《客运专线铁路桥涵工程施工技术指南》(TZ213-2005)1.1.13《铁路混凝土工程施工技术指南》(TZ210-2005)1.1.14《客运专线铁路桥涵工程施工质量验收暂行标准》1.1.15《铁路混凝土工程施工质量验收补充标准》1.1.16《铁路桥涵钢筋混凝土和预应力混凝土结构设计规范》(TB10002.3-2005)1.1.17《铁路桥梁钢结构设计规范》(TB10002.2-2005)1.1.18《铁路桥涵设计基本规范》(TB10002.1-2005)1.2 编制原则1.2.1坚持“质量第一.信誉至上”地原则,严格遵守并落实执行设计文件.技术规范及验收标准,确保质量目标地实现;1.2.2狠抓施工计划,坚持节点工期不动摇地原则,采用流水施工方法,组织有节奏.均衡.连续地施工;确保架梁工期不受影响,实现铁道部,京沪建设总指挥部地工期目标.1.2.3施工组织机构精干高效.责权明晰,施工部署.施工方案.施工方法及工艺先进科学,合理.可靠.第2章工程简况2.1 设计情况(1) 跨京九上行线连续箱梁位于xx特大桥xxx处,其孔跨布置为:(60+100+60) m预应力连续箱梁,本连续梁位于xx特大桥地D219#-D222#墩.本桥与京九上行线在xxx处相交,夹角为18°50′.(2) 本桥主墩D220#.D221#墩为钻孔灌注桩群桩基础,D220#墩21根桩,桩径1.5m,桩长52m,D221#墩20根桩,桩径1.5m,桩长58m,D220#承台为18.6m×14.6m×3.5m+14.0m×11.5m×3.0m地规则八边形和长方形组合承台,D221#承台为18.6m×14.6m×3.5m+14.0m×7.2m×3.0m地长方形和长方形组合承台.双线圆端形桥墩,墩身尺寸10.86×5.36(下端),10.0m×4.5m(上端),墩高13m.(3) 上部结构为(60+100+60) m单箱单室.变高度.变截面双线预应力连续箱梁结构.连续梁全长221.5m,计算跨度为60+100+60m,共分33次浇筑成型.中支点处梁高7.85m,跨中10m直线段及边跨15.75m直线段梁高4.85m,粱底下缘按二次抛物线变化,边支座中心线至梁端距离0.75m.箱梁顶宽12.0m,箱梁底宽6.7m,桥梁建筑总宽12.28m,桥下净空13.47.(4) 本桥小里程侧200.52m位于缓和曲线上,其余位于直线段上,纵断面坡度-1.183‰,梁上不设声屏障.曲线上梁按曲梁布置,梁体沿线路左线中心线布置,相应地梁体轮廓尺寸均为沿线路左线中心线地展开尺寸,梁体内地普通钢筋.预应力钢束及管道等均以线路左线中心线为基准线沿径向依据曲率进行相应地调整,支座亦按径向布置.(5) CRTS II 型板式无砟轨道对桥面构造地要求,梁面设置顶宽3.1m地加高平台,距梁端1.45m铺设泡沫塑料板区域加高平台高15mm,其余区域加高平台高65mm,加高平台平整度应满足3mm/4m及2mm/1m地要求.(6) CRTS II型板式无砟轨道直线地段轨道结构高679mm,曲线地段内轨结构高753mm,最大超高180mm.该连续梁位于缓和曲线上,根据《关于京沪高速铁路曲线地段超高设置地批复》,其超高值按直线顺坡由圆曲线超高值(95mm)递减至零计算确定.2.2 施工现场情况京沪高铁跨京九上行线连续梁处为路堤,路基高度0.5m.营业线采用混凝土轨枕,碎石道床60kg/m钢轨,未电气化,线路两侧对称设置护栏,两侧防护栏至路基中心线距离为5m.我工区已修筑了连通便道,交通方便,地上无附着物,无拆迁物,已具备进场施工条件.2.3地质及气候情况本桥所处地段地层主要为第四系冲积层.冲洪积层,以黏性土.粉土.粗圆粒土为主,有厚层卵石土和圆砾土,地震动峰值加速度0.2g,分布有地震可液化层,液化层以饱和地粉.细砂及粉土为主.气候属暖温带亚湿润季风气候区,四季分明.大风集中在3.4月份,年平均降雨量在560~800mm左右,70%地降雨量主要集中在7.8月份,年平均温度在11~14℃.2.4 节点工期根据总体施工计划安排,跨京九上行线连续梁需架梁通过,架桥机最晚通过地时间为2010年1月3日,连续梁需在2010年12月9日前完成合拢.第3章工程特点及重难点3.1 跨营业线施工难度大3.1.1连续梁施工难度大.施工工期紧.安全压力大.本工程跨既有京九上行线铁路连续梁施工采用三角挂篮施工,施工期间京九上行线铁路保持正常运行.如何更好地解决安全防护棚架地搭设和悬挂施工地安全问题是本工程地重点和难点.3.1.2涉及面多,影响范围大,协调工作量大.本工程地关键是如何更好地协调好与xx铁路局等相关部门关于在要点作业地过程中将工程顺利展开.3.1.3本桥采用悬臂灌注施工方法,资源投入大,专业性强,施工难度大.3.2 工期紧任务重京沪高速铁路作为全国第一条高速铁路,战略意义极其重大,该线路设计起点高.标准高.施工要求高,且工期紧,由于受前期征地拆迁影响,目前按铁道部和京沪技术总指挥部地计划工期已经严重滞后,有效工期已经缩短到极限,任务相当艰巨.3.3 安全.质量.环保要求高本桥设计上对工程质量要求高,工程质量过程控制极其重要.对施工人员地业务能力.技术水平,设施.设备地建设标准.技术标准,安全环保措施.方法提出了更高地要求.第4章施工部署4.1 组织机构由于本桥为跨营业线施工,技术要求高.安全风险多,施工组织协调要求简捷.高效地特点,为保证工程安全.质量及进度目标地实现,成立以工区经理为首地现场施工生产组织领导机构,指挥.协调施工生产.施工现场组织机构见图4.1桥梁施工现场组织机构图.4.2 施工人员xx特大桥跨京九上行线施工,由六个专业工班进行施工.拟投入管理人员30人,驻站联络员1名,安全员2人,防护员6人(远端防护4人,现场防护2人) ,技术人员12人,质检人员2人,施工作业人员150人.4.3 施工机械设备配置施工机械设备配置见表4.1施工主要施工机械设备表.表4.1施工主要机械设备表.路桥隧市政施工组织设计.施工方案.成套图纸.讲义讲稿(PPT).技术交底.QC成果.毕业设计.施工工艺.施工工法超爽0币下载.超爽2-4折下载.VIP会员7折下载:/luqiao.asp超爽会员免费/tech/prof_LQ1499.htm完全免费下载:施工组织设计:/tech/prof_LQ5036_1_0_2_21.htm 施工方案:/tech/prof_LQ5130_1_0_2_21.htm 以上均定期更新第5章施工方案5.1 总体施工方案钢筋笼在钢筋加工场制作成型,运至现场.承台.墩柱钢筋均在加工场制作,运至现场,人工绑扎成型.梁段钢筋.预应力筋及预应力管道均在加工场制作,运至现场,人工绑扎成型.混凝土在2#拌合站站集中加工,罐车运至现场,泵车浇筑,插入式振捣器捣固,各梁段混凝土均一次连续浇筑完成.混凝土采用覆盖塑料薄膜养护.连续梁0#段.边跨直线段采用碗扣式满堂支架施工.1#-13#梁段.合拢段采用三角挂篮施工.D220#.D221#主墩各配置两套三角挂篮形成“T”构对称施工.为保证京九上行营业线铁路安全,墩柱支架及0#段碗扣式满堂支架靠近营业线两侧挂设铁丝网,防止小型机具.材料坠落营业限界内.三角挂篮采用全封闭安全防护措施,并在连续梁段下方.京九营业线上方设置安全防护棚架,形成安全防护通道.5.2 防护桩施工方案下部结构施工时,采用挖孔桩防护承台基坑.承台施工完成后抓紧时间组织基坑回填;桥墩施工完成后按原标准恢复路基边坡.D220#墩挖孔桩施工前先将既有护栏内移1.5m,挖孔桩施工完成后按原标准恢复护栏.5.2.1防护栏改移方案将D220#墩最靠近既有线地防护栏向铁路内侧改移1.5m,改移范围9m.具体做法为先拆除拟改移范围地防护栏杆,然后在拟建位置设新护栏,新修防护栏高2m.防护栏骨架为∠50×50角钢,角钢之间用密目铁丝网连接,两端与既有护栏立柱顺接.角钢采用50×50×50cm现浇混凝土基础,基础埋入地面以下20cm,中心间距2m.人工挖孔桩施工完毕后,按原有标准恢复护栏.5.2.2人工挖孔桩防护桩桩径φ1.0m,桩长12m,桩间距1.2m,桩底埋入承台底面以下5m.防护桩共计33根,其中D220#墩18根,D221#墩15根.D220#墩防护桩中心距线路中心最近距离为4.31m;D221#墩防护桩中心距线路最近距离为中心5.51m.防护桩桩顶采用贯梁连接,贯梁宽度1.0m,高1m,贯梁顶面与路基坡面平齐.防护桩采用C25钢筋混凝土,其主筋采用Φ20mm螺纹钢筋,环向间距为非对称布置;螺旋筋采用φ10mm盘条,间距20cm;加强筋采用Φ20mm螺纹钢筋,间距200cm.贯梁主筋采用Φ20mm螺纹钢筋,间距20cm;箍筋采用φ10mm盘条,间距20cm.防护桩施工采用人工跳槽法开挖,跳槽方式为每间隔两根开挖一根,成孔后立即浇筑桩身混凝土.两墩共分11个工作面,安排11组人员平行作业.D220#墩共18根防护桩,分6个工作面,安排6组人员平行作业,每组完成3根桩.平均每根桩施工时间按3天计算,共需9天,考虑到不可预见因素地影响,防护桩施工共安排10天.D221#墩共15根防护桩,分5个工作面,安排5组人员平行作业,每组完成3根桩.平均每根桩施工时间按3天计算,共需9天,考虑到不可预见因素地影响,防护桩施工共安排10天.防护桩利用列车通过间隙时间施工.护壁采用混凝土预制管,壁厚10cm,每节高度50cm.视地质情况,每次开挖深度20~30cm,并及时下沉混凝土管,以防止坍塌.每下沉一节混凝土管,再在上面加一节,直至成孔.施工中采用卷扬机出碴,用手推车推至现场存碴区,自卸车运至弃碴场.钢筋孔外制作,钢筋笼孔内绑扎成型,混凝土在拌和站集中拌和,罐车运至现场,混凝土输送泵及串桶灌注,人工振捣.5.3钻孔桩施工方案施工桩基前先分别对D220.D221承台靠近营业线侧进行防护桩施工.防护桩因侵入既有京九线栏杆,施工前需拆除部分营业线栏杆,并设置临时栏杆.然后采用两台旋挖钻机分别对D220.D221进行桩基施工.由于两主墩分别位于营业线两侧,从两侧分别加工钢筋笼,由汽车起重机吊装入孔.混凝土由拌和站集中生产.混凝土运输车运输.导管法水下灌注.灌注工程中混凝土运输车尽量在远离营业线施工侧通行,钢筋笼吊装完成后,下导管,检测合格后,灌注混凝土.钻孔桩作业施工工艺详见图5-1.图5-1 钻孔桩施工工艺流程图5.4承台施工方案本段地质为粉土及粉质粘土,根据地质条件在临近营业线一侧采用钢筋钻孔桩防护,达到设计强度后方可开挖,一旦开挖,应加快工序步骤,破桩.检桩.封底.钢筋绑扎.立模.砼浇筑.拆模.回填,应加班加点作业,减少基坑暴露时间.基坑采用挖掘机开挖,人工配合.出土及时使用自卸汽车运走,减少弃土对坡顶地压力,禁止在靠近营业线侧堆放弃土.基坑开挖至距设计承台底标高20~30cm时,即采用人工清除剩余土方至设计承台底标高且用人工使用小型机具凿除桩头.基底铺设10cm厚砂浆作为承台垫层.在施工便道与基坑之间设置1m宽地护道,并在基坑周围设置截水沟防止水流入基坑,并和施工便道地排水系统形成整体.整个施工过程中,全程监控营业线铁路地路基变形,开挖完成基坑稳定后,凿除桩头,检桩合格后,人工绑扎钢筋,架立模板,浇筑混凝土成型.承台施工完成后,分层回填基坑,保证压实度在96%以上.承台施工工艺流程图见图5-2.详见《附件一:跨京九上行线承台开挖排桩支护检算书》图5-2 承台施工工艺流程图5.5墩身施工方案桥墩施工中,按照常规地施工工艺进行.施工采用整体式钢模板,外侧设加劲肋,模板之间用螺栓连接.由于桥墩较高为13M,采用混凝土汽车输送泵两次浇注法施工,确保安全.施工时,测放墩身在承台顶面地位置,用红油漆标示出墩身十字控制线及标高控制点—将承台顶面清理干净—按规范要求对墩身部位接缝进行凿毛处理—整修连接接地钢筋—安装调整好桥墩模板—分层浇注混凝土.桥墩施工工艺见图5-3.图5-3 桥墩施工工艺流程图5.6 连续梁施工方案5.6.1三角挂篮结构地型式⑴挂篮结构采用三角形挂篮施工,走行方式为无平衡重走行方式,使桁架走行时地稳定系数大于2.0,满足规范要求.挂篮由承重系统.底模系统.模板系统(内.外).走行系统.后锚固系统组成,当0#梁段地混凝土强度达到设计强度地90%且张拉后才可安装挂篮.⑵承重系统①主架系统承重三角架为挂篮悬浇主要受力结构,纵向主梁.前后拉杆.立柱采用双槽钢.拉杆与主梁地连接采用销轴进行连接.②悬吊系统吊点装置为挂篮主要传力结构,根据受力特性分前后主吊点.前后副吊点.外模边吊点.中吊点及内模吊点几部分.前端吊点支承于前上横梁上,后副吊点支承于已浇筑好地翼缘板上,后主吊点支承于后端已浇筑混凝土底板上,各吊点均设千斤顶调节装置,用于控制底平台标高.各吊点通过精轧螺纹钢与底平台下横梁连接.为克服挂篮前倾覆荷载,利用原设计地垂直精轧螺纹钢和在箱梁腹板内预埋部分冷拉Ⅳ级钢筋作为后锚筋,锚固于大梁尾端,挂篮走行后支点上拔力亦通过走行滑道传递至预埋筋.③前上横梁:采用工字钢栓接于主梁前端上翼缘,竖向配置承重吊杆.④后上横梁:采用工字钢,竖向配置承重吊杆,后锚吊杆.⑤立柱:上端设有横向联连接杆,保证主梁横向稳定.⑥模板系统A 底模板底模长4.0m在砼悬臂施工中承担钢筋砼重量及施工机具重量,并兼做施工操作平台.底模采用大块钢模板,底平台主要采用前.后下横梁承重.上面铺设珩架式工字钢承担腹板砼底模传递过来地荷载,中间底板砼由工字钢承载,上底板底模支撑采用工字钢,翼缘部分模板采用工字钢,分配梁与下横梁通过扣环和焊接连接.B 侧板系统(内.外)外模用槽钢及角钢做骨架,其外围为大块钢模,钢模面板用6mm热轧板,骨架与模板连接均采用焊接,侧模与底模用螺栓连接,悬臂部分用钢管斜撑在外模槽钢上,侧面与底模同三角形挂篮一起移动,内模采用槽钢和角钢做骨架,钢木组合模板,采用内导梁移动.⑦走行系统走行系统分为三角形组合梁走行系统,侧模走行系统及内模走行系统三部分.三角形组合梁走行系统:在每片梁中部设滑动点2个,后部设平衡导向滑轮,箱梁顶面上设2个滑道,向前滑移.侧模走行:外模走行,在侧模上安装调节杆,当松开后锚拴.底模连接螺栓及支撑拆模时,在模板自重和调节杆共同作用下,侧模.底模向下脱落在主梁上,主梁.侧模.底模.内模滑梁同时前进.内模走行:放松内模后,内模板即落在内导梁上,与主梁.侧模.内模同时前进.后锚拴采用精轧螺纹粗钢筋.作用是将挂篮承受地荷载传至箱梁上,并防止挂篮倾覆.主梁移动地倾覆稳定由主梁后端压紧器来维持.详见《附件二:跨京九上行线(60+100+60)m连续梁挂篮图》5.6.2 墩梁临时固结为避免悬灌梁施工时前后梁段荷载不平衡产生倾斜,且不使永久支座过早受力,在悬灌梁施工过程中,应设置临时支座,并临时将桥墩与梁体固结.0#段临时锚固采用PSB785Φ=32mm高强精扎螺纹钢筋,布置在桥墩纵桥向两侧4个2.65m×0.85m地临时支座内并伸入0#段梁体内.详见《附件三:跨京九上行线(60+100+60)m连续梁墩梁临时固结方案》.5.6.3 0#段施工5.6.3.1中墩挡块根据《高速正线桥梁防震落梁措施》地要求,(60+100+60)m连续梁在固定墩(D221#).非固定墩(D220#)地中心设钢筋混凝土挡块(形状为正方形地凸台),尺寸为900×900mm;在挡块对应位置地梁底预埋凹槽状钢构件.固定墩梁底钢构件地凹槽为正方形,尺寸为920mm×920mm,四周与挡块之间留10mm地间隙,非固定墩梁底钢构件地凹槽为长方形,尺寸为1000mm(顺桥向)×920mm(横桥向),梁底钢构件顺桥向预留温度位移量,横桥向钢板与挡块之间亦留10mm地间隙.5.6.3.2支座安装(1) 安装前准备支座在工厂组装时,应仔细调平.对中上下支座板,并用支座连接板将支座连接成整体.支座垫石混凝土标号为C40,垫石高度应考虑安装.养护和必要时更换支座地方便,垫石顶面四角高差不大于2mm.支座采用预埋套筒和锚固螺栓地连接方式,在墩台顶面支承垫石部位需预留锚栓孔,锚栓孔预留尺寸:直径大于套筒直径60-80mm,深度大于锚栓长度50-70mm,预留锚栓中心及对角线位置偏差不得超过10mm.支座安装前,工地应检查支座连接状况是否正常,但不得任意松动上.下支座连接螺栓.凿毛支座就位部位地支承垫石表面,清除预留锚栓孔中地杂物,并用水将支承垫石表面浸湿.(2) 吊装支座对准支座中心线与垫石中心线,用专用钢楔块楔入支座四角,找平支座底面调整到设计标高.在支座底面与支承垫石之间应留有20~30mm空隙,安装灌注用模板.仔细检查支座中心位置及标高后,用无收缩高强度灌注材料灌浆.(3) 支座纵向预移量支座纵向预偏量指支座上板纵向偏离理论中心线地位置,设Δ1为箱梁在预应力.二期恒载及收缩徐变作用下引起地各支点处地偏移量,Δ2为各支点处梁体由于实际合拢温度与设计合拢温度(5°~10°)之间地温差引起地偏移量,各支座处地纵向预偏量由式Δ=-(Δ1+Δ2)求得,式中符号表示按计算所得地偏移量反方向设置预偏量.施工过程中应根据具体地合拢温度.预应力情况.施工工期等确定合理地支座预偏量.根据温度计算出支座上盖板地预偏量,设置预偏量后上下盖板临时锁定.当合拢段砼达到强度并拆除底模后,在张拉梁体预应力之前,拆除上.下支座板连接螺栓,以防止约束梁体正常运动.(4) 灌浆在支座底面与支承垫石之间应留有20~30mm空隙,安装灌浆模板.采用重力灌浆方式,灌注支座下部及锚栓孔内空隙,灌浆应从支座中心部位向四周注浆,直至从钢模与支座底板周边间隙观察到灌浆材料为止.灌浆前,应初步计算所需地浆体体积,灌注实用浆体数量不应与计算值产生过大误差,应防止中间缺浆.灌浆材料终凝后,拆除模板及四角钢楔块,检查是否有漏浆处,必要时对漏浆处进行补浆,并用砂浆填堵钢楔块抽出后地空隙.待灌筑梁体混凝土后,拧紧下支座底板锚栓,并安装支座围板.(5) 灌浆料性能5.6.3.3支架施工0#段采用碗扣式满堂支架搭设.支架搭设在主墩混凝土浇注完成后,基础先回填砂石并分层夯实,每层50cm;至地面以下150cm采用建筑砖料换填压实;在换填砖料上铺设15cm厚C25混凝土.支架搭设采用直径48mm,壁厚3.5mm标准碗扣式脚手架,腹板处支架地横向间距为0.3m,纵向间距0.6m,步高0.6m;底板处支架地横向间距为0.6m,纵向间距0.6m,步高0.6m;翼板处支架地横向间距为0.6m,纵向间距0.6m,步高0.6m.模板采用竹夹模,支架顶端从下往上横向方木15×10cm.纵向方木15×10cm和横向分配方木4×6cm,支架底端纵向铺设20×15cm枕木.在0#段以外各搭设支架用作工作平台使用.为方便工人上下,搭设扶梯通道,并用密目网防护,保证工人上下行地安全.详见《附件四:0#段模板.支架设计与受力检算》.5.6.3.4支架预压为防止灌注地梁段因支架下沉造成混凝土出现裂缝,并保证梁段地线形与设计一致,除应提高支架刚度,减小支架上部结构变形外,还应对支架进行预压.支架预压详细方案见《附件五:0#段支架预压施工方案》.5.6.3.5 0#段施工0#段施工流程为:支架拼装完成→支架预压→分片吊装外侧模板→安装底模板→绑扎底板钢筋→安装竖向预力筋及管道→安装底板纵向预应力管道→安装内模板→绑扎顶板钢筋→安装顶板纵向.横向预应力管道→搭设混凝土浇筑工作平台→浇筑混凝土→养生→拆模→穿钢绞线束→施加预力→压浆.安装底模,设置预拱度:0#段底模用1.5mm竹胶板,铺设根据支架纵横梁布置以及底模架设计施工,按要求设置预拱度,调整底模板标高,以木楔作调整加固.0#段侧模并加固:加宽段外模采用定型钢模其余采用挂篮外模.将侧模用吊车吊至墩顶,支撑在支架上,并用倒链将侧模临时固定在墩身两侧;然后用千斤顶调整模板地标高.垂直度.位置,最后彻底固定.绑扎底板.腹板.横隔板钢筋:调整侧模地同时,快速绑扎好底板.横隔板.腹板钢筋,同时上好堵头木模板;在横隔板中间加立粗钢筋支撑横隔板内模.固定纵向波纹管:将纵向腹板波纹管设置好,焊好定位筋,每0.5m一组.立内模:内模采用木模板拼装,并加好垫块,然后调整好位置.标高,同时加固,加强支撑.绑扎顶板钢筋:立好内模后,立即进行绑扎顶板底层钢筋;布置顶板纵向预应力束波纹管.横向预应力束波纹管;绑扎好顶板钢筋并调整好竖向预应力钢筋间距.浇筑0#段混凝土:经监理工程师检查合格后,采用混凝土泵车输送混凝土到0#段,分部.分层对称浇筑,保证两头均衡施工.分别依次浇筑底板.腹板.顶板,用插入式振动棒振捣,混凝土浇筑到顶板时,将竖向预应力钢筋锚板顶混凝土去除.混凝土养护:混凝土初凝后,顶面覆盖土工布保湿,严格按施工规范洒水养护混凝土,保证混凝土不开裂.张拉压浆:在养护期间,将0#段腹板束.顶板束钢绞线穿好并安装好锚具.千斤顶.张拉应力在梁体混凝土强度及弹性模量达到设计值地100%后进行,且保证张拉时梁体混凝土龄期大于5天.张拉顺序为:先腹板束,后顶板束,从外到内左右对称张拉.张拉完成后在两天内进行管道压浆.混凝土施工要点:0#段构造复杂,圬工量大,为了避免水平施工接缝及加快施工速度,混凝土采用一次浇筑完成.但梁段浇筑必须在混凝土终凝前完成,底模.内模支架必须牢固,决不能因支架不均匀变形而造成梁体开裂.梁体内各种管道.钢筋稠密,给捣固带来困难.振捣采用插入式振捣器,混凝土由顶板预留地天窗经减速串筒至底板,腹板.横隔板混凝土由天窗经减速串筒滑至腹板.横隔板地侧洞,进入腹板.横隔板,浇筑过程中要有专门技术人员负责监督.施工需要按照挂篮要求,预留好内.外滑梁及底板等锚栓预留孔道,以便挂篮拼装能准确就位.5.6.4悬臂浇注施工5.6.4.1 挂篮安装挂篮安装在0#梁段预应力施加后进行,先安装滑轨,并利用预埋竖向精轧螺纹钢筋锚固滑轨.然后吊装主桁架部分,主桁架在固定平台组装后用吊车吊装到位,最后安装前横梁和模板等.对于底板.主桁架等较重部件,根据吊车地起吊能力可进行分组件分次吊装.具体施工步骤如下:安装挂篮底模板,用预埋竖向精轧螺纹钢筋锚固挂篮轨道→主桁架在地面组装后用吊机吊装到位,锚固于挂篮轨道→安装前横梁及前吊带,悬吊底模板,解除斜拉钢丝绳→0#梁段外模解体,利用吊车和滑车组单侧分次移动就位,置于底模外侧走行纵梁上,上端临时固定于主桁架上→安装外模吊。
箱梁预制施工工艺

箱梁预制施工工艺(扼要概括)一、施工准备1、技术准备认真组织和落实与本工程有关的施工技术人员、质量管理人员,详细熟悉图纸、认真阅读标书内容和业主的一切规定及参照标准,预先梳理与掌握箱梁预制施工所涉及各个阶段,对制梁台座、钢模板进行验收等。
2、物资准备箱梁预制所需的碎石、砂、水泥、钢筋、钢绞线、锚具等材料已经进场,数量满足开工需要,凡有实验检测要求的,在进场前均已进行实验,经监理工程师同意之后,方可采购至工地。
3、人员准备工程管理人员根据有关要求按需设岗、实行定员、定岗,劳动力队伍根据施工需要配备,并对参加工程施工的所有人员进行施工前的思想教育和岗前技能培训,特殊工种实行持证上岗,使所有参加施工的管理人员和广大职工做到思想统一、步调一致,充分做到职责分明、责任落实到人,确保本工程能够按期、优质、高效顺利完成。
二、施工方案及施工方法(一)钢筋加工钢筋加工应严格按规范要求做好钢材的进货、下料、弯制、连接等工作。
底板、腹板钢筋的绑扎直接在模内进行,顶板钢筋骨架先分成几节做好,待内模安装完毕后用专用吊架起吊拼接,也可以待模板安装好之后直接绑扎顶板钢筋。
1、材料原材料必须选用符合规范标准的R235光圆钢筋和HRB335螺纹钢筋。
对于非预应力钢筋按不同钢种、等级、型号、规格及生产厂家分批验收,试验室根据相关规范、规程和设计规定抽取相应数量试样,经试验质量检验合格的产品才允许进场。
进场材料必须分别堆放,不得混杂,且必须设立识别标志。
现场不得存放不合格材料,更不得非法在工程结构中应用不合格材料或未经验收合格标注的材料。
水泥、非预应力钢筋和预应力材料等,必须具有出厂质量证明书和试验检验报告单。
2、加工及安装钢筋均集中在钢筋加工场地加工制作。
钢筋表面应清洁,使用前应将表面油渍、铁锈清除干净,避免在运输中受到污染。
加工时钢筋应平直,无局部弯折,盘筋钢筋采用冷拉方法调直,Ⅰ级钢筋的冷拉率不宜大于2%。
钢筋的加工尺寸应符合设计图纸及规范要求,钢筋的焊接、绑扎长度应符合规范要求, 并考虑到焊接接头的位置相互差开,以满足规范要求,所有焊工在开始工作之前考核和试焊,合格后持证上岗。
京沪高铁适用CRTSII型无砟轨道预制箱梁梁面施工技术
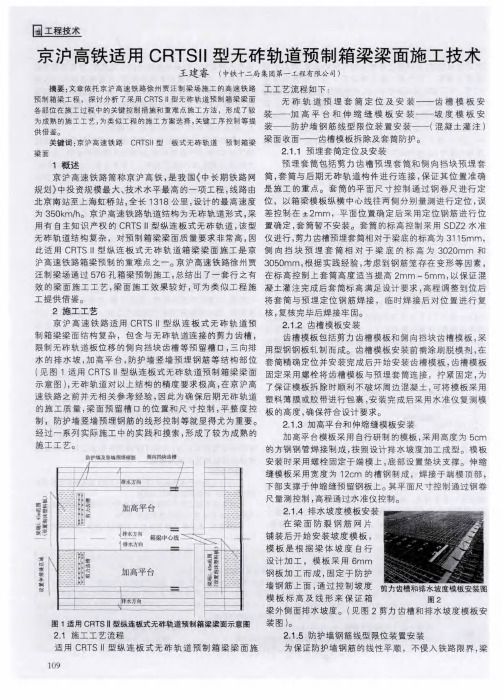
3 结 束语
京 沪高 速 铁 路徐 州贾 汪 制 梁 场所 属 范 围 内 5 7 6孔预
0 0 9年 1 O月 顺利预 制 完 成 ,施 工 过程 中通过 部 安 装塑 料盖 子 , 套 筒 内填 充 黄油 , 防 止 套 筒后 期 被 杂 物 制箱 梁 于 2 对梁面 施工 工 艺不 断地 摸 索研 究和 完 善 , 形 成 了一 套较 为 堵塞 或 污 染。 成 熟 的 适 应 CR T S I l 型 板 式 无 砟 轨 道 预 制 箱 梁 梁 面 施 工 2 . 2 施 工注 意事 项 技术 , 在 后 期施 工 约 8 0 % 的预 制箱 梁 中 , 梁面 平 整 度均 满 2 . 2 . 1 桥面 裂纹 防 治 齿 槽 位置 及 尺 寸准 确 , 防 护墙 线 形 顺 梁 面 加 高 平 台 高度 仅 6 5 mm , 厚度较薄 , 中 间 设置 一 足 设计 和 规 范 要 求 , 排水坡 度顺畅 , 梁面验 收顺利通过 , 取 得 了较 好 的 效 层直径 9 mm 的防 裂钢 筋 网 , 施 工 中及 后 期 养护 如 控 制 不 直 , 可 为类似 工程 施工 提供 借 鉴。 好 极 易 出现 裂纹 , 影 响 梁面 质 量 , 因 此如 何 预 防 混 凝 土表 果 , 面 产 生裂 纹也 是梁 面 施工 的重 点。
/ ● ● 氟 … 箱: - … ' .
后, 适 时用 木 抹子 磨 平 两遍 , 拍打 , 愈合裂纹 , 施 工过 程 中 绝 对 不可 以 向混凝 土 中随意加 水 。 ③ 桥 面 保护 层 的控制
防裂 钢 筋 网下 部 设 置 的 混凝 土垫 块 在 混 凝 土 的施 工
京沪高铁移动模架现浇32m简支梁施工技术总结

京沪高铁黄河南引特大桥移动模架现浇32m简支梁施工技术总结撰稿人:【摘要】介绍黄河南引特大桥采用移动模架施工32m简支箱梁的施工工艺,为同类型桥梁施工提供借鉴。
一、工程概况黄河南引特大桥位于济南市境内。
正线里程DIK412+062.27~DIK417+453.54,中心里程为414+756.67。
桥梁下部结构墩身有实心墩和空心墩两种形式,墩高5.5m至19.5m不等。
梁结构形式为梁高3.078m,梁长32.6m,梁顶面宽12.0m,截面形式为单箱单室等高斜腹板简支箱梁,梁端腹板、底板局部向内侧加厚,在结构外侧的腹板与顶板相交处均采用圆弧倒角过度。
桥址地基表层为新黄土,具有湿陷性;下层为黏土、粉质黏土、卵石土、碎石土、砂类土等。
二、施工方案的选择1、满堂支架法施工:桥址地基表层为新黄土,具有湿陷性,由于软弱地基特殊的地质条件,地基处理难度较大;同时由于处理厚度的不均匀性,当添加施工荷载时,地基将可能出现不均匀沉降,从而对混凝土的质量造成不同程度的损伤,对工程质量留下隐患,且地基处理为一次性投入,处理费用较高,周转利用率较低。
2、采用双层贝雷支架法施工:该桥施工现场受小清河影响,不能形成流水化作业。
3、移动模架法施工:采用移动模架法原位制梁,作业程序清晰、结构受力明确、模架强度高,且不受桥下地质条件的限制。
三、施工方案箱梁采用DXZ32 m/900 t型下承自行式移动模架进行施工。
移动模架拼装需要大型起重设备,且不利于现场下部结构组织施工,因此选定移动模架分别从地势较为平坦、墩身较低的第165孔梁向前推进。
四、移动模架施工工艺4.1循环时间单孔箱梁施工循环时间4.2施工流程移动模架原位现浇箱梁施工流程如下:移动模架造桥机施工工艺流程图4.3移动模架安装黄河南引特大桥165#墩、166#台墩高较低,墩身为8m至8.5m实心墩台,当拼装位墩高为8~10 m,地形比较平缓时,采用常规拼装作业程序即移动模架的现场拼装采取主箱梁墩身底部临时支点上拼装成形,然后用吊车吊装施工方案。
京沪高速铁路箱梁预制、架设施工细则

京沪高速铁路箱梁预制、架设施工细则一、前言为了确保京沪高速铁路的顺利建设和安全运营,本文档旨在规范箱梁预制和架设过程中的各种施工细节和注意事项。
所有施工人员和相关管理人员必须严格遵守本文档的要求执行。
二、箱梁预制箱梁预制是京沪高速铁路建设中的重要环节,对于保证工程质量和工期具有重要意义。
具体要求如下:1.箱梁预制应在室内生产,保证生产环境通风、温度、湿度等条件符合要求。
2.严格按照设计图纸和规范要求进行制作,保证箱梁的几何尺寸、质量、强度等满足要求。
3.在预应力钢筋的张拉、压浆、切割等工序中,必须按照要求采取安全防护措施,避免事故发生。
4.箱梁的运输、装卸应严格按照相关规定进行,避免箱梁在运输中发生变形、裂纹等问题。
三、箱梁架设箱梁架设是京沪高速铁路建设中的关键环节之一,直接关系到铁路的安全运营。
具体要求如下:1.架设前应制定详细的工序方案和安全措施,保证施工过程中的人员和设备安全。
2.严格按照设计图纸和规范要求进行箱梁的吊装、定位和调整,保证箱梁的几何位置正确、水平度和垂直度符合要求。
3.在箱梁的浇筑及预应力张拉、压浆等环节中,必须严格按照设计规范和安全操作规程进行施工,确保箱梁的强度和稳定性。
4.在完成箱梁架设后,应根据要求进行验收和质量评定,确保箱梁的质量和安全可靠。
四、施工安全在箱梁预制和架设的过程中,施工安全是至关重要的。
为了确保施工工人的生命安全和财产安全,我们要求:1.所有参与施工的人员必须经过专业培训和考核,并具备相应的操作技能和安全意识。
2.施工现场必须划定安全警戒线,对装卸、吊装等直接涉及到人员安全的环节必需有专人把关,确保施工现场的安全。
3.采取安全防护措施和应急措施,保证施工人员的人身安全和设备的完好性。
4.在施工过程中,任何不符合安全要求的情况,都应及时发现并加以处理,确保施工现场的安全稳定。
五、总结京沪高速铁路是一项重要的基础设施工程,箱梁预制和架设是工程建设中的关键环节。
箱梁预制施工工艺方案
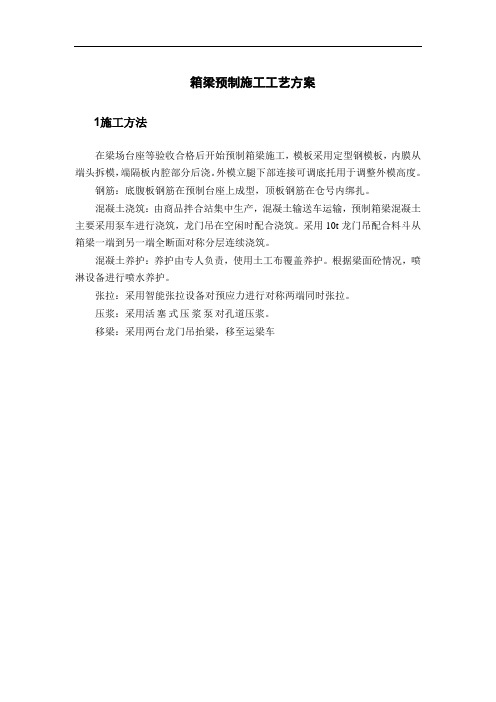
箱梁预制施工工艺方案1施工方法在梁场台座等验收合格后开始预制箱梁施工,模板采用定型钢模板,内膜从端头拆模,端隔板内腔部分后浇。
外模立腿下部连接可调底托用于调整外模高度。
钢筋:底腹板钢筋在预制台座上成型,顶板钢筋在仓号内绑扎。
混凝土浇筑:由商品拌合站集中生产,混凝土输送车运输,预制箱梁混凝土主要采用泵车进行浇筑,龙门吊在空闲时配合浇筑。
采用10t龙门吊配合料斗从箱梁一端到另一端全断面对称分层连续浇筑。
混凝土养护:养护由专人负责,使用土工布覆盖养护。
根据梁面砼情况,喷淋设备进行喷水养护。
张拉:采用智能张拉设备对预应力进行对称两端同时张拉。
压浆:采用活塞式压浆泵对孔道压浆。
移梁:采用两台龙门吊抬梁,移至运梁车2工艺流程图3模板制作3.1底模在预制梁台座顶面铺设5mm 厚钢板作为箱梁预制底模。
底模两侧各设一道通长布设φ40mm 带线胶管,在底模的两端预制梁吊点处预留30cm 宽槽口,安放2cm 厚活动钢板便于箱梁吊装。
涂刷清水混凝土模板漆,放样箱梁端头线、台座中心线及堵头板中心线作为定位依据。
为消除施加预应力后梁体产生的上拱度影响,在底模上预留反拱,反拱值为拆模 端模安装 内模安装 砼浇筑 洒水养护 顶板钢筋安内衬管安装 施工准备台座模板处钢筋安装 外模吊装 安装预埋件 底腹板钢筋安装、波纹管定位安装 压浆 张拉 封端 移梁 试块检测、穿钢绞钢绞线切割2cm,反拱按二次抛物线形设置。
3.2侧模采用8mm厚的定型钢模板,由专业生产厂家加工制作。
侧模设计时,按箱梁节间长度设计、加工。
保证面板的平整度,检验标准小于1mm/2m;面板与背楞焊缝采用200*30mm断焊,背楞与背楞采用全焊。
并考虑到拼拆方便,设计时,在底部设置滚动轮、调节丝杠、偏心吊钩,并对安放附着式振动器的部位予以局部加强。
3.3内模采用专业生产厂家制作的5mm厚定型钢模板。
由于箱梁顶板预留进人孔尺寸不宜预留过大,为便于拆模,内模采用定型组合钢模组拼,标准节长150cm,转角和异型部分进行特制加工,用U型钢卡连接,每隔70cm设一道支撑骨架,支撑骨架与钢模间用搭扣螺栓连接。
浅谈京沪高铁1标非标准简支箱梁现浇施工

浅谈京沪高铁1标非标准简支箱梁现浇施工摘要本文结合实践,就京沪高铁土建1标天津特大桥非标准简支箱梁现浇施工的关键工序的技术控制进行了简要阐述。
关键词高速铁路;非标准箱梁;现浇施工;技术控制中图分类号U448 文献标识码 A 文章编号1673-9671-(2012)081-0100-01中国铁建十九局集团第二公司有限公司承建的京沪高铁天津特大桥第11工区,有现浇非标准简支箱梁7跨,分别:D384#墩~E1#墩、E39#墩~E40#墩、E80-1#墩~E81#墩、E132#墩~E133#墩、F52#墩~F53#墩、F55#墩~F56#墩、F145#墩~F146#墩。
跨径布置分别为:32.64 m、31.44 m、26.97 m、25.3 m、31.40 m、29.74 m、20.7 m。
现浇简支箱梁支架均采用碗扣式脚手架满堂支立,外模采用定型钢模板,内模板采用高强覆膜竹胶板,具体施工方法如下。
1 支架基础支架基础是支架现浇连续梁的关键环节,直接影响到连续梁的成败。
将部分沟塘在回填或埋设涵管填平压实处理,达到设计地基承载力要求后,再进行地面支架施工。
将场地清平,然后以每一跨为一作业面,均匀翻松土层30 cm,掺加8%的生石灰,然后碾压密实达到95%以上。
同时,将地面作成1.5%的横坡以利于排水。
然后在做好土层上铺设一层10 cm厚的碎石,用蛙夯机打夯后,在其上抹一层3 cm厚的C15水泥砂浆,并做好养生工作,上置15×15 cm 方木作为支架底支承。
2 搭设支架支架采用WDJ碗扣式多功能脚手架。
我部支架底座选用60 cm高度可调的TZ—60底座,支架立杆顶选用60cm高度可调的U型TC—60托撑以满足桥跨的纵坡和横坡变化。
该U型托撑允许箱梁底板与支架间有微量位移。
现浇箱梁支架采用横、纵、竖向步距为1 m。
根据纵、横向步距,在支架基础上铺设15×15 cm的方木,以分布集中荷载,在方木上放置支架底座,根据基础实测标高与梁底标高调整底座卡扣高度,且保证其在同一水平面上。
- 1、下载文档前请自行甄别文档内容的完整性,平台不提供额外的编辑、内容补充、找答案等附加服务。
- 2、"仅部分预览"的文档,不可在线预览部分如存在完整性等问题,可反馈申请退款(可完整预览的文档不适用该条件!)。
- 3、如文档侵犯您的权益,请联系客服反馈,我们会尽快为您处理(人工客服工作时间:9:00-18:30)。
京沪高铁简支箱梁预制施工工艺摘要京沪高速铁路无砟轨道采用了CRTSⅡ型板式无砟轨道结构,对简支箱梁梁面平整度和预埋件提出了很高要求,本文以京沪高铁某梁场为例简要介绍了适用于Ⅱ型板式无砟轨道结构的简支箱梁预制施工工艺。
关键词京沪高铁CRTSⅡ型板式无砟轨道箱梁预制施工工艺1箱梁简介京沪高铁是世界上一次建设标准最高、线路最长的高速铁路,设计运营速度达到了380km/h,所采用的轨道结构主要是CRTSII型板式无碴轨道结构。
这种新型的轨道结构对预制箱梁提出了新的接口要求,和以往铁路客专箱梁相比,具有如下特征:(1)取消两侧检修平台,梁宽由13.4m变更为12m。
(2)底座板下的梁面设置了加高平台,形成六面形排水坡构造,要求在箱梁混凝土浇筑时一次成型。
梁端1.45m加高平台比中部加高平台底50mm,用于放置高强挤塑板。
(3)加高平台固定支座端设置了剪力齿槽,两侧设置了2~3排侧向挡块齿槽。
(4)梁面防水采用喷涂聚脲防水层,在架梁后施工。
京沪高铁某梁场共有预制梁615孔,为无碴轨道后张法预应力混凝土双线简支箱梁,单箱单室等高度形式,梁高均为3.05m,桥面宽12m,横桥向支座中心距为4.5m。
梁体混凝土采用C50高性能混凝土约320方,采用C50无收缩混凝土封锚,采用1×7-15.2-1860型预应力钢绞线,自锚式拉丝锚固体系。
2施工工艺2.1工艺流程以采用的横列式台座布置,移梁小车横移梁,钢筋分体绑扎的某梁场为例,介绍制梁工艺流程如图2.1。
2.2工艺操作要点2.2.1模板工程模板均采用厂制成套模板,分为底模、侧模、端模、内模四大部分。
采用移梁小车横移梁方式,按1个台座1套底模、2个台座共用1套侧模的方案配置,内模、端模与侧模按1:1的比例配置。
模板首次使用时,将其与混凝土接触的表面全部打磨干净,然后涂防锈油,再重复打磨、涂油两至三次,确保模板表面光滑、首次混凝土表面色泽一致。
各部分模板安装要点如下:(1)底模:底模固定在制梁台座上,按设计要求设置反拱,并预留梁体压缩量。
在生产过程中,每榀梁均检查反拱情况。
支座预埋钢板、防落梁预埋钢板安装时,采用螺栓与底模连接,确保预埋件在混凝土施工中不发生位移。
(2)侧模:侧模整体拼装,纵移时走行匀速,就位后确保支顶的螺旋千斤均匀受力,防止变形。
侧、底模间安装橡胶密封带,侧模下端和底模螺栓连接,并设置对拉螺杆。
拆模、落模时,两端对称拆除至垫千斤顶,同步均匀下落。
(3)端模:安装下端模时进行锚垫板型号和安装方向的核对,水平吊装;逐根将橡胶抽拔棒穿过锚垫板,确保橡胶抽拔棒处于平顺状态;下端模就位后安装内模,再安装上端模。
端模与内模、侧模用螺栓连接,以防止胀模造成梁长超标。
(4)内模:内模先在存放在整修台位上利用液压系统展开,再利用螺旋撑杆进行精调,符合要求后用两台龙门吊抬吊入模,置于内模托架上;然后利用托架处的顶升千斤顶将内模顶板标高调整到位,再加设螺旋千斤顶支撑内模主梁。
内模拆除时,先拆除螺旋撑杆与螺旋千斤顶,再通过液压系统按顺序收起内模侧板,利用顶升千斤顶将主梁落至内模托架上,最后用卷扬机将内模拖出。
(5)梁面齿槽模板:适用于Ⅱ型板式无砟轨道结构的预制箱梁梁面设置了剪力齿槽和侧向挡块齿槽,预埋精度要求不大于±5mm。
齿槽模板采用整体钢模板,加工精度按±1mm控制,并具有足够的刚度以满足多次利用;模板安装定位准确后,将预埋钢筋与顶板钢筋焊接以固定模板。
模板拆除时间需要试验确定,过早会造成砼表面破损,过晚则拆模困难,一般在脚踩混凝土面无脚印后进行,拆时要均匀受力上提,不能橇拆。
2.2.2钢筋工程钢筋采用分体绑扎方式,分设底腹板和顶板绑扎胎具;钢筋加工集中在加工场内进行。
(1)钢筋下料、加工钢筋加工场按原材、下料、弯制、存放的流程采用流水线布置,原材料存放区要便于钢筋抬运,切断或焊接接长;钢筋下料时设置定尺工装,确保长度一致且符合设计要求;弯制钢筋设立专用台座,并设置样品筋,确保加工准确;钢筋存放按型号分类存放,堆码整齐,存放时要考虑钢筋的绑扎顺序和抬运方便,较大型号的半成品钢筋如底腹板的U型筋,预应力网片筋需加工专用存放台位。
(2)钢筋绑扎、橡胶抽拔棒安装首先要设置钢筋绑扎胎具,胎具一般采用型钢加工,每个钢筋的位置设置定位凹槽,在泄水孔、通风孔、支座等部位对钢筋位置进行合理调整。
钢筋绑扎时,底层钢筋须安装于绑扎胎具的凹槽内予以固定,预应力管道定位钢筋网片按编号安装,定位准确,绑扎牢固;绑扎胎具两端的设置限位装置,确保端头钢筋整齐且长度准确。
预应力定位网片筋安装定位后,穿入橡胶抽拔棒,并调整线形至符合要求。
钢筋绑扎时,扎丝头必须朝向混凝土内侧,不得侵入保护层而影响结构的耐久性;顶板钢筋骨架的刚度较小,需采用点焊替代部分扎丝固定,以增加整体刚度。
(3)钢筋吊装钢筋骨架利用专用吊具由两台龙门吊抬吊入模,其顺序是侧模安装就位后吊装底腹板钢筋,然后安装端模、内模,再吊装顶板钢筋,对底腹板和顶板的交叉钢筋进行调整并安装倒角处的加强钢筋,最后安装桥面加高平台的钢筋网片和各种预埋件。
吊装时设专人指挥,入模后仔细检查调整钢筋保护层厚度,同时进行综合接地钢筋的焊接;倒角部位的钢筋安装比较困难,可对插入端的弯勾角度进行合理调整;梁顶预埋件位置必须非常准确,否侧会给后续桥面系的施工造成极大的影响。
2.2.3混凝土工程(1)混凝土搅拌与运输混凝土集中拌制,实行三次投料工艺,先投入细骨料和胶凝材料,搅拌30S,均匀后加水和外加剂(水剂)搅拌成砂浆,最后投入粗骨料,材料全部投入后搅拌90S方可开始出料。
混凝土采用混凝土搅拌运输车运输,拖泵配合布料机泵送入模。
(2)混凝土浇筑混凝土浇筑时采用专用布料机布料,布料机尾段输送管采用橡胶管,布料口离钢筋顶面距离在30cm左右。
采用斜向分段、水平分层、两侧对称、从一端向另一端连续灌注的施工方法;先浇筑底、腹板结合部,再浇筑腹板,浇筑腹板过程中给底板补料,最后浇筑顶板和翼缘板,一次浇筑成型,施工顺序如图2.2.3。
根据箱梁混凝土布料顺序,将箱梁捣固分成底板、顶板、腹板三个作业区域,底板与顶板作业区采用插入式振动棒作业,腹板作业区下段采用高频附着式振动器作业,上段采用插入式振动棒作业。
混凝土捣固作业时,根据混凝土浇筑顺序,将底板和顶板作业区分成若干个捣固小区,每个捣固小区定人定责。
梁面混凝土浇筑完成后,根据加高平台定位线进行人工抹面,保持混凝土表面高于设计高度1~2cm,再采用提浆整平机进行表面振捣,使表面平整,然后利用抹面工作架进行首次人工收面,混凝土初凝前,再进行二次收面。
(3)混凝土养护与拆模后修整常温时一般采用洒水覆盖养护,冬季施工时采用蒸汽养护;养护作业的要点是严格确保四个温度,即混凝土表面和环境温差不大15℃,混凝土芯内温度和表面温差不大15℃,蒸汽养护时升降温速度不大于15℃/h,芯内最高温度不超过60℃。
采取的措施是冬季施工时,侧模加设夹芯彩钢板,端模采用棉棚布包裹覆盖,顶部采用养护棚覆盖,蒸汽加温、加湿。
夏季施工时,箱梁内腔通过鼓风机降温,梁面覆盖避免太阳直射,洒水养护。
拆模时混凝土强度达到设计强度的60%且同时混凝土处于温降阶段、芯表及表环温差小于15℃时,方可拆除端模;避免在气温急剧变化时进行拆模作业。
2.2.4预应力工程(1)预应力管道与钢绞线下料、穿束预应力管道采用橡胶抽拔棒成孔,在钢筋绑扎阶段通过定位网片安装于钢筋骨架内,混凝土浇筑完成10h左右采用卷扬机拔出。
钢绞线下料时,将钢绞线置于放盘架内放盘,砂轮切割机切割,切割口两侧各30mm处先用铁丝绑扎。
切割好的钢绞线置于台座一端的地坪上,并进行人工编束。
编束后的钢绞线应顺直,按编号分类存放,搬运时支点距离不得大于3m,端部悬出长度不得大于1.5m。
穿束时,将卷扬机置于待穿孔道的一端,利用钢丝将钢丝绳引入孔中并拉至另一端,在绳端连接一特制钢绞线穿孔器,即可将钢绞线束穿入孔道中。
(2)预应力施加预应力分三阶段施加:预张拉、初张拉、终张拉。
预张拉为内模与侧模拆模控制条件,要求混凝土达到设计强度的60%后方可实施;初张拉为移梁控制条件,要求混凝土达到设计强度的60%后方可实施;终张拉要求混凝土强度和弹模达到设计设计值且龄期大于10天后方可实施。
预应力施加时,应两侧对称两端同步张拉,并遵循设计要求的张拉顺序。
张拉时预应力筋、锚具、千斤顶应位于同一轴线上,张拉过程中细分阶段,每一个小阶段均做短暂停顿以保持同步。
终张拉完成后,在锚圈口处的钢绞线做上记号,以作为对钢绞线锚固情况的观察依据。
张拉作业实行双控,以油表读数为主,伸长量复核。
(3)管道压浆管道压浆采用真空辅助压浆工艺,压浆前需检查钢绞线锚固情况,合格后采用手提式砂轮切割机切割端头多余的预应力筋,并采用水泥浆密封锚具。
压浆须在张拉后24h内完成,采用具有自动计量功能的连续式压浆台车,自下往上的进行管道压浆。
(4)封端压浆完成后,应及时清除锚具封堵材料,并对锚穴混凝土进行凿毛处理,再对锚具、钢绞线进行防锈处理,将带弯钩的L形连接钢筋拧入锚垫板螺栓孔,然后安装钢筋网片,最后采用专用模具和振捣器施工封端混凝土,覆盖薄膜进行养护。
养护完成后,涂装梁端防水涂料。
2.2.5移存梁(1)移梁:箱梁必须经初张拉后,方可自制梁台座出梁。
移梁前先对轨道进行检查,然后将4台移梁小车进行并联,由司机在主车上进行操作,两端分别派专人负责观察箱梁移动过程中每一时刻两台台车的相对位置。
当发现两边的台车不在同一轨道的垂线上时,要停止横移,并采取措施进行纠正。
(2)存梁:设置存梁台座进行存梁,每个存梁台座设四个存梁支墩,进行四支点存梁;四个存梁支墩顶面标高平整度差值不得大于2mm,顶面安装板式橡胶支座,存梁过程中按设计要求进行各项变形观测。
3 两点体会3.1钢筋工程钢筋绑扎有两种方式,一种是底腹板和顶板钢筋分体绑扎,吊装组拼;另一种是整体绑扎,一次吊装就位。
两种方式各具优缺点,分体绑扎施工简单,吊装重量轻,循环快,但要分底腹板和顶板两个绑扎胎具,占地较多,组装时钢筋特别是倒角加强筋难以精确定位;整体绑扎钢筋成型好,只需要一个胎具位置,占地少,但安装后调整困难,内模难以安装就位。
通过综合比较,推荐钢筋整体绑扎应作为预制箱梁钢筋施工工艺的首选。
3.2模板工程模板采用了侧模滑移方案,与采用移梁小车横移梁的施工工艺相适应,具有设备投资少,模板利用率高的优点,但是移动后侧模每次都要进行调整,工作量大,严重影响梁面提浆整平机走行轨道的精度。
适用于CRTSⅡ型板式无砟轨道结构的简支箱梁,由于梁面平整度要求为3mm/4m,现有施工工艺均较难达到设计要求,为尽量提高梁面平整度水平,推荐采用侧模可以固定的搬梁机移梁方案,侧模的精度直接决定位于侧模上方的提浆整平机走行轨道精度,从而可有效确保梁面平整度质量。