丰田式生产方式PPT课件
合集下载
丰田式生产方式(TPS)讲义PPT(65张)

・信息的确定(1个月前)
・材料的订购、各工序的人員、设备负荷、计划
③・日程计划
・平均化计划
・确定每生产品种、生产順序
12
(2)・每天必要生产数量和节拍
・每天的必要数量= 1个月的必要数量 一个月运转天数
・节拍 =
每天的运转时间 × 运转率 每天的必要数量
・是决定用几分钟、几秒生产一个部件、或是1台份的时间长短值。
4
準时化生产方式
基本原則
方法策略
・从后工序取件
J ・必要的数量
I
决定生产节拍
T
・工序的流程化 ・小批量生產
・平均化生产 ・看板方式 ・按生产顺序取件
・决定日生产量 ・彻底贯彻标准作业
・防止制造过多(减少库存) ・(物)同步化、(人)多技能工化
・改善准备工序作业
5
自動化
自動化(JIDOUKA):异常的情况下设备停止 • 在豐田生產方式中,始終強調必須是帶人字旁的“自動
8
豐田生產方式的手法
・经常观察现场
5・进一步改善 1・了解所有工序
4・找出浪费 排除浪费
2・目视化管理
・工厂4S ・标准作业 ・定位置停止作业 ・生产线停止显示板 ・库存管理(最小ー最大)
・全員参加 ・毅力和努力
3・节拍生产
・平均化生产 ・防止多余、过多生产
9
平均化生產
• 在生产多种类产品的情况下 ① 保证每天的生产量一定; ② 将「种类」「数量」进行平均化生产。
变化(质量劣化)
6. 動作上的無效勞動--不产生附加值的动作(歩行、取件、放置) 7. 制造出次品所形成的無效勞動和浪費--原材料、工时、
• 豐田生產方式的基本思想:
徹底杜絕無效勞動和浪費(改善產品制造方法)。
・材料的订购、各工序的人員、设备负荷、计划
③・日程计划
・平均化计划
・确定每生产品种、生产順序
12
(2)・每天必要生产数量和节拍
・每天的必要数量= 1个月的必要数量 一个月运转天数
・节拍 =
每天的运转时间 × 运转率 每天的必要数量
・是决定用几分钟、几秒生产一个部件、或是1台份的时间长短值。
4
準时化生产方式
基本原則
方法策略
・从后工序取件
J ・必要的数量
I
决定生产节拍
T
・工序的流程化 ・小批量生產
・平均化生产 ・看板方式 ・按生产顺序取件
・决定日生产量 ・彻底贯彻标准作业
・防止制造过多(减少库存) ・(物)同步化、(人)多技能工化
・改善准备工序作业
5
自動化
自動化(JIDOUKA):异常的情况下设备停止 • 在豐田生產方式中,始終強調必須是帶人字旁的“自動
8
豐田生產方式的手法
・经常观察现场
5・进一步改善 1・了解所有工序
4・找出浪费 排除浪费
2・目视化管理
・工厂4S ・标准作业 ・定位置停止作业 ・生产线停止显示板 ・库存管理(最小ー最大)
・全員参加 ・毅力和努力
3・节拍生产
・平均化生产 ・防止多余、过多生产
9
平均化生產
• 在生产多种类产品的情况下 ① 保证每天的生产量一定; ② 将「种类」「数量」进行平均化生产。
变化(质量劣化)
6. 動作上的無效勞動--不产生附加值的动作(歩行、取件、放置) 7. 制造出次品所形成的無效勞動和浪費--原材料、工时、
• 豐田生產方式的基本思想:
徹底杜絕無效勞動和浪費(改善產品制造方法)。
丰田式生产方式培训课件
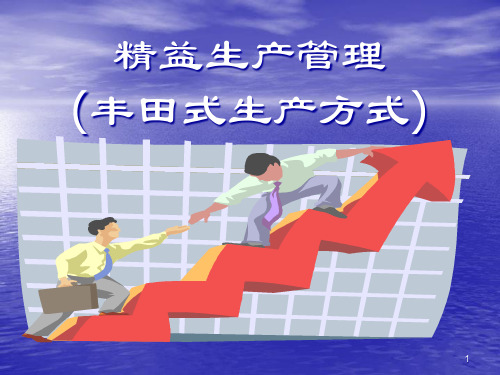
20 22
设备名称 数量
调正,不是按类型而是按工序形成相互 衔接的生产线(U形、T形等)
13
一个流生产的要点
1. 单件流动: 避免以批量为单位加工,应
逐个完成相关工序加工
2. 按工序排列设备布置流水线 3. 按节拍进行生产,按看板和用户需求适
时、适量、适物连续流动
4. 站立式走动作业 5. 培养多能工,一人多机(工序)操作 6. 设备小型化,排列U、L、三角形等 7. 作业标准化
1. 为什么会过剩是平衡生产和次废品需求,
过剩生产说明由于人员和设备过多。
2. 表面效率和实际效率
原来某工序生产100个,现通过努力增 产到120个,表面效率得到提高,但实 际祗需求(或生产线工艺节拍)100个, 这就是浪费。实际效率没提高,所以整 体效率重于个人效率
16
缩短作业切换时间
调正、试加 工 50%
箱内数量:100 看板编号:2/5
使用工序 总装1-3 入口位置
POS.12-8
12
均衡化同步同节拍生产
• 同步化节拍生产是按照生产工艺规定和
物流顺序确定生产提前期条件下和产品 总装配线保持同步地进行生产
• 一个流的生产,前工序加工一结束即立
即转到下一工序,尽量使工序间在制品 接近于零
• 一个流的生产,必须将设备的布局进行
• 缺乏改善意识的企业属于此类型,
市场好时有较高的利润,市场差时 大幅度下降
4
利润中心型
• 在供应>销量时,以利润为中心,
当市场售价降低时,成本也必须下 降以获得的利润 (目标利润 ) 不 会减少
• 其公式为: • 成本 = 售价- 利润
5
减少浪费 --降低成本的主要手段
丰田生产方式PPT(共40页)
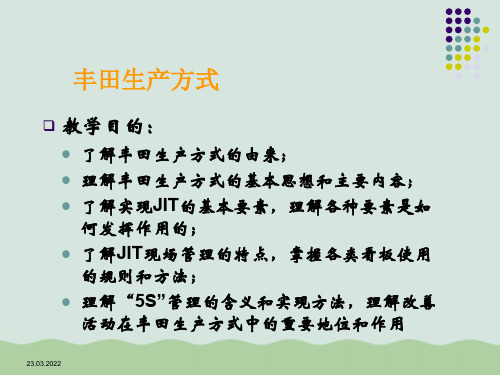
23.03.2022
12.2.3 全面质量管理
全面质量管理Total quality management (TQM)是丰 田生产方式的支柱之一。
TPS与TQM是同根、同源、同目标、同方法。
TQM的三全:全员、全过程、全方位。
JIT不允许将有问题的产品转移到下一道工序。
在出现质量问题时,工人有权停止生产线的流动。
设备1
工 人 1 工人1
设备9
设备2
工 人 2
设备8
设备3
工人2
工人3
设备4
设备7
设备6
设备5
在制造单元内,加工同一零件族的不同设备集中在一起 布置,组成柔性生产线。
工作流沿同一方向通过单元
可以通过改变工人数量和看管设备路线调整生产节拍。
可以采用联合U型生产线,以更充分利用人力资源。范例 13-1。 Return
“少人化” 为了适合需求的变化,弹性 改变各工序的作业人员人数
扩大或缩小各工作人员 的作业范围
“少人化” 减少工序的作业
人员人数
连接 U 字型生产 线的设备布置
23.03.2022
多能工
工作岗位轮 换制
修订标准作业组合票 工序的改善
作业改善
设备改善 (“自动化”)
实现“少人化”的因素
Return
12.2.2 制造单元
丰田选择了看似不符合规模经济的独特的生产模式, 经过20多年的努力,丰田人成功了。
丰田的成功也引来了日本的其它汽车公司的效仿, 他们也成功了。TPS成为了日本的汽车生产模式。
23.03.2022
12.1.2 TPS的由来
丰田公司与通用的业绩比较
23.03.2022
12.1.2 TPS的由来
12.2.3 全面质量管理
全面质量管理Total quality management (TQM)是丰 田生产方式的支柱之一。
TPS与TQM是同根、同源、同目标、同方法。
TQM的三全:全员、全过程、全方位。
JIT不允许将有问题的产品转移到下一道工序。
在出现质量问题时,工人有权停止生产线的流动。
设备1
工 人 1 工人1
设备9
设备2
工 人 2
设备8
设备3
工人2
工人3
设备4
设备7
设备6
设备5
在制造单元内,加工同一零件族的不同设备集中在一起 布置,组成柔性生产线。
工作流沿同一方向通过单元
可以通过改变工人数量和看管设备路线调整生产节拍。
可以采用联合U型生产线,以更充分利用人力资源。范例 13-1。 Return
“少人化” 为了适合需求的变化,弹性 改变各工序的作业人员人数
扩大或缩小各工作人员 的作业范围
“少人化” 减少工序的作业
人员人数
连接 U 字型生产 线的设备布置
23.03.2022
多能工
工作岗位轮 换制
修订标准作业组合票 工序的改善
作业改善
设备改善 (“自动化”)
实现“少人化”的因素
Return
12.2.2 制造单元
丰田选择了看似不符合规模经济的独特的生产模式, 经过20多年的努力,丰田人成功了。
丰田的成功也引来了日本的其它汽车公司的效仿, 他们也成功了。TPS成为了日本的汽车生产模式。
23.03.2022
12.1.2 TPS的由来
丰田公司与通用的业绩比较
23.03.2022
12.1.2 TPS的由来
《丰田看板拉动方式》课件
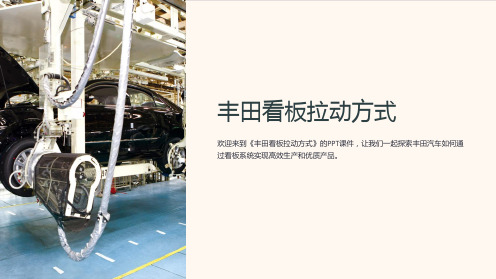
丰田看板拉动方式
欢迎来到《丰田看板拉动方式》的PPT课件,让我们一起探索丰田汽车如何通 过看板系统实现高效生产和优质产品。
什么是看板系统
看板系统是一个源自日本的生产管理方法,用于控制生产速度和库存量。 它通过可视化工作流程,帮助企业实现精益生产和及时交付。
丰田看板拉动方式
1
丰田看板拉动方式介绍
2
生产拉动看板用于控制生产线 上物料的供应和运输,确保按 需生产。
物流拉动看板
物流拉动看板用于控制供应链 中物流环节的运输和库存,确 保产品及时交付。
库存拉动看板
库存拉动看板用于控制仓库中 的原材料和成品库存,避免过 多库存和缺货情况。
看板系统的应用
1 看板系统与供应链的关系
看板系统帮助企业优化供应链流程,提高供应链的可视性和响应速度。
丰田看板拉动方式是丰田生产方式的核
心,它通过按需生产和减少库存浪费,
提高生产效率和灵活性。
3
丰田生产方式概述
丰田生产方式是丰田汽车在20世纪50年 代开创的一种以拉动方式运作的生产管 理方法。
丰田看板拉动方式的优点
丰田看板拉动方式可以避免过度生产和 库存积压,降低成本和提高产品质量。
看板的种类
生产拉动看板
看板系统的维护
保持看板系统的准确性和可读性 非常重要,需要定期更新信息和 检查看板系统的使用情况。
看板系统的改进
看板系统应该不断改进和优化, 以适应不断变化的生产需求和市 场需求。
2 看板系பைடு நூலகம்在物流管理中的应用
看板系统能够提高物流运作的效率和准确性,降低运输成本和提高订单交付率。
3 看板系统在生产管理中的应用
看板系统可以减少生产过程中的浪费和等待时间,提高生产线的效率和质量。
欢迎来到《丰田看板拉动方式》的PPT课件,让我们一起探索丰田汽车如何通 过看板系统实现高效生产和优质产品。
什么是看板系统
看板系统是一个源自日本的生产管理方法,用于控制生产速度和库存量。 它通过可视化工作流程,帮助企业实现精益生产和及时交付。
丰田看板拉动方式
1
丰田看板拉动方式介绍
2
生产拉动看板用于控制生产线 上物料的供应和运输,确保按 需生产。
物流拉动看板
物流拉动看板用于控制供应链 中物流环节的运输和库存,确 保产品及时交付。
库存拉动看板
库存拉动看板用于控制仓库中 的原材料和成品库存,避免过 多库存和缺货情况。
看板系统的应用
1 看板系统与供应链的关系
看板系统帮助企业优化供应链流程,提高供应链的可视性和响应速度。
丰田看板拉动方式是丰田生产方式的核
心,它通过按需生产和减少库存浪费,
提高生产效率和灵活性。
3
丰田生产方式概述
丰田生产方式是丰田汽车在20世纪50年 代开创的一种以拉动方式运作的生产管 理方法。
丰田看板拉动方式的优点
丰田看板拉动方式可以避免过度生产和 库存积压,降低成本和提高产品质量。
看板的种类
生产拉动看板
看板系统的维护
保持看板系统的准确性和可读性 非常重要,需要定期更新信息和 检查看板系统的使用情况。
看板系统的改进
看板系统应该不断改进和优化, 以适应不断变化的生产需求和市 场需求。
2 看板系பைடு நூலகம்在物流管理中的应用
看板系统能够提高物流运作的效率和准确性,降低运输成本和提高订单交付率。
3 看板系统在生产管理中的应用
看板系统可以减少生产过程中的浪费和等待时间,提高生产线的效率和质量。
《丰田模式14项原则》PPT课件

小区,同时也为美国人创造高薪资的制造业工作.
编辑ppt
8
原则1:管理决策以长期理念为基础 即使因此牺牲短期财务目标也在所不惜
别让决策伤害到信任与相互尊重
✓ 丰田公司认识到,维持员工的饭碗是它对小区与社会的责任之一. ✓ 丰田并非以季度预算来衡量此投资,而是从使顾客及员工持续尊
敬丰田公司及其产品的角度来考虑的.丰田知道这个工厂熟练且 努力的员工必定能应用丰田生产方式持续地改进质量,去除浪费. 丰田相信这才是带动长期获利的主要因素.
量管理的文化(自动化) • 工作的标准化是持续改进与授权员工的基础 • 运用视觉管理使问题无处隐藏 • 使用可靠的,已经过充分测试的技术以协助员
工及生产流程
理念 (着眼于长期的理念)
编辑ppt
13
原则2:建立无间断的操作流程以使问题浮现
在“一个流”的制造方法中,若有问题发生,整条生产 线都会暂停.就此看来,这是一种糟糕的生产制度.可是, 当生产停止时,每个人都被迫要立刻解决问题.于是,大 家都被迫去思考解决之道,通过彻底思考,团队成员因 而成长,变得更加胜任.
比赚钱更重要的使命
✓ 丰田公司经营企业的起点是为顾客,社会与经济创造 更高价值
编辑ppt
6
原则1:管理决策以长期理念为基础 即使因此牺牲短期财务目标也在所不惜
做有益于顾客的事
✓ 丰田公司在1971年的“尼克松冲击”中坚持做有益于顾客的事. 虽然公司发生了很大的损失,但也使得顾客满意,并赢得长期顾 客关系.
编辑ppt
2
目录
第三类原则 发展员工与事业伙伴,为组织创造价值
原则9: 把彻底了解且拥护公司理念的员工培养成为领导者,使他们能 教导其他员工
原则10: 培养与发展信奉公司理念的杰出人才与团队 原则11: 重视事业伙伴与供货商网络,激励并助其改进
编辑ppt
8
原则1:管理决策以长期理念为基础 即使因此牺牲短期财务目标也在所不惜
别让决策伤害到信任与相互尊重
✓ 丰田公司认识到,维持员工的饭碗是它对小区与社会的责任之一. ✓ 丰田并非以季度预算来衡量此投资,而是从使顾客及员工持续尊
敬丰田公司及其产品的角度来考虑的.丰田知道这个工厂熟练且 努力的员工必定能应用丰田生产方式持续地改进质量,去除浪费. 丰田相信这才是带动长期获利的主要因素.
量管理的文化(自动化) • 工作的标准化是持续改进与授权员工的基础 • 运用视觉管理使问题无处隐藏 • 使用可靠的,已经过充分测试的技术以协助员
工及生产流程
理念 (着眼于长期的理念)
编辑ppt
13
原则2:建立无间断的操作流程以使问题浮现
在“一个流”的制造方法中,若有问题发生,整条生产 线都会暂停.就此看来,这是一种糟糕的生产制度.可是, 当生产停止时,每个人都被迫要立刻解决问题.于是,大 家都被迫去思考解决之道,通过彻底思考,团队成员因 而成长,变得更加胜任.
比赚钱更重要的使命
✓ 丰田公司经营企业的起点是为顾客,社会与经济创造 更高价值
编辑ppt
6
原则1:管理决策以长期理念为基础 即使因此牺牲短期财务目标也在所不惜
做有益于顾客的事
✓ 丰田公司在1971年的“尼克松冲击”中坚持做有益于顾客的事. 虽然公司发生了很大的损失,但也使得顾客满意,并赢得长期顾 客关系.
编辑ppt
2
目录
第三类原则 发展员工与事业伙伴,为组织创造价值
原则9: 把彻底了解且拥护公司理念的员工培养成为领导者,使他们能 教导其他员工
原则10: 培养与发展信奉公司理念的杰出人才与团队 原则11: 重视事业伙伴与供货商网络,激励并助其改进
图解丰田生产方式讲解
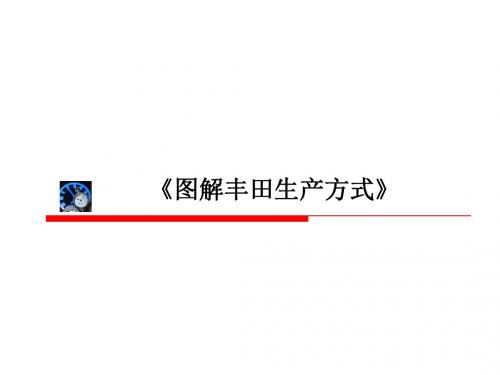
• 顾客需要的产品数量为100,现有10个人生产100个
产品,则效率:10个/人, • 若用10个人生产了120个产品,效率为12个/人,此 时提升的效率为表面的效率; • 若用8个人生产了100个产品,则效率为12.5个/人, 提升的效率为真正的效率。
10
假效率与真效率
例:市场需求100件/天 10个人1天 生产 100件产品 10个人1天 生产 120件产品
13
个别效率与整体效率(水桶效应)
例
能力需求:100件/H
项 能
目 力
工序1 100件/H 100% 标准产量奖金 个别效率合格
工序2 125件/H 125% 125%奖金 个别效率高 14
工序3 80件/H 80% 0 个别效率低
工序4 100件/H 80% 0 个别效率低
达成率 奖 效 金 率
11
8个人1天 生产 100件产品
假效率 真效率
假效率
固定的人员
真效率
最少的人员
生产出仅需的产品
生产出更多的产品
12
能力提升是效率的基础。 但效率建立在有效需求的基础 上,以【是否创造利润】为标 准;如果不创造效益甚至造成 在库,则此种效率是假效率。
假效率 能力 提升
真效率
【效率建立在有效需求的基础上】 能力提升是效率提升的基础。但有时能力 提升会造成效率提升的假象。 管理者的责任就是在能力提升的基础上, 将假效率转化成真效率。 所以,“省人化”是效率的关键。 省人化的两种形式: ☆ 正式工 + 季节工 / 临时工(变动用工) ☆ 固定人员 + 公用人员(弹性作业人员)
18
(2)制造不良品的浪费
(3)停工等活的浪费 (4)动作上的浪费 (5)搬运的浪费 (6)加工本身的浪费
产品,则效率:10个/人, • 若用10个人生产了120个产品,效率为12个/人,此 时提升的效率为表面的效率; • 若用8个人生产了100个产品,则效率为12.5个/人, 提升的效率为真正的效率。
10
假效率与真效率
例:市场需求100件/天 10个人1天 生产 100件产品 10个人1天 生产 120件产品
13
个别效率与整体效率(水桶效应)
例
能力需求:100件/H
项 能
目 力
工序1 100件/H 100% 标准产量奖金 个别效率合格
工序2 125件/H 125% 125%奖金 个别效率高 14
工序3 80件/H 80% 0 个别效率低
工序4 100件/H 80% 0 个别效率低
达成率 奖 效 金 率
11
8个人1天 生产 100件产品
假效率 真效率
假效率
固定的人员
真效率
最少的人员
生产出仅需的产品
生产出更多的产品
12
能力提升是效率的基础。 但效率建立在有效需求的基础 上,以【是否创造利润】为标 准;如果不创造效益甚至造成 在库,则此种效率是假效率。
假效率 能力 提升
真效率
【效率建立在有效需求的基础上】 能力提升是效率提升的基础。但有时能力 提升会造成效率提升的假象。 管理者的责任就是在能力提升的基础上, 将假效率转化成真效率。 所以,“省人化”是效率的关键。 省人化的两种形式: ☆ 正式工 + 季节工 / 临时工(变动用工) ☆ 固定人员 + 公用人员(弹性作业人员)
18
(2)制造不良品的浪费
(3)停工等活的浪费 (4)动作上的浪费 (5)搬运的浪费 (6)加工本身的浪费
讲座ppt-丰田模式_图文

最让美国三大车商(通用、福特、戴姆勒-克莱斯勒)汗颜 的是,2004年丰田净利润达到102亿美元,超过三家利润 总和。
当这样的老大滋味不好受。“我们早已处于劣势。在我心里 ,丰田是第一,我们是第二。”通用汽车一位高级副总裁袒 露心声。
战后丰田公司到美国取经
1800’s 晚期
20世纪20年代
精益生产的优点
所需人力资源方面,与大量生产方式下的工厂相比 ,均能减至1/2; 新产品开发周期—可减至l/2或2/3; 生产过程的在制品库存可减至大量生产方式下一般 水平的1/10; 工厂占用空间—可减至采用大量生产方式工厂的1/2; 成品库存—可减至大量生产方式工厂平均库存水平 的1/4; 产品质量可提高3倍。
生产过程中的七大浪费 ----制造过剩的浪费
制造过多的浪費是指在一个工序到一个工序的 中间准备了过多的量.
1973年石油危机确立了大野耐一 的超市式生产方式。
开始时遭到了大多数人的反对
(员工,供应商)
生产过程中的七大浪费 ----不良品的浪费
及早的发现不良品。 每增加一道工序,损失就会增加一倍。
持续改进的主要方法:PDCA循环
持续改善的方法:PDCA循环
计划(plan) 它包括分析现状;找出存在问
题;分析产生问题的原因;找出 其中主要原因;拟订措施计划, 预计效果五个步骤。
实施(do),执行计划。
检查(check),执行结果与预定目 标进行对比,检查执行情况
处理(action),巩固成绩,把 成功经验纳入标注化程序,遗留 问题进入下个循环。
准时化生产
“只在需要的时候,按需要的量生产所需的 产品”.
通过生产的计划和控制及库存的管理,追求 一种无库存,或库存达到最小的生产系统。 准时生产方式的核心是追求一种无库存的生 产系统,或使库存达到最小的生产系统。
当这样的老大滋味不好受。“我们早已处于劣势。在我心里 ,丰田是第一,我们是第二。”通用汽车一位高级副总裁袒 露心声。
战后丰田公司到美国取经
1800’s 晚期
20世纪20年代
精益生产的优点
所需人力资源方面,与大量生产方式下的工厂相比 ,均能减至1/2; 新产品开发周期—可减至l/2或2/3; 生产过程的在制品库存可减至大量生产方式下一般 水平的1/10; 工厂占用空间—可减至采用大量生产方式工厂的1/2; 成品库存—可减至大量生产方式工厂平均库存水平 的1/4; 产品质量可提高3倍。
生产过程中的七大浪费 ----制造过剩的浪费
制造过多的浪費是指在一个工序到一个工序的 中间准备了过多的量.
1973年石油危机确立了大野耐一 的超市式生产方式。
开始时遭到了大多数人的反对
(员工,供应商)
生产过程中的七大浪费 ----不良品的浪费
及早的发现不良品。 每增加一道工序,损失就会增加一倍。
持续改进的主要方法:PDCA循环
持续改善的方法:PDCA循环
计划(plan) 它包括分析现状;找出存在问
题;分析产生问题的原因;找出 其中主要原因;拟订措施计划, 预计效果五个步骤。
实施(do),执行计划。
检查(check),执行结果与预定目 标进行对比,检查执行情况
处理(action),巩固成绩,把 成功经验纳入标注化程序,遗留 问题进入下个循环。
准时化生产
“只在需要的时候,按需要的量生产所需的 产品”.
通过生产的计划和控制及库存的管理,追求 一种无库存,或库存达到最小的生产系统。 准时生产方式的核心是追求一种无库存的生 产系统,或使库存达到最小的生产系统。
丰田模式PPT课件

.
14
现地、现物、现认在丰田又被称“三现”主义,它 是突出现场确认的务实的管理精神。
现地——发生问题的地点
现物——对发生问题的对象进行确认
现认——摈弃完全凭经验和感觉进行判断的习惯,注 意数据和事实,对问题进行分析,找出真正原因。
.
15
1、说明问题并描述相关信息 2、问“为什么”直接找出根本原因 3、制定对策并执行 4、执行后,验证有效性; 如有效进行定置/标准化/经验总结
【固有定义】清扫(擦拭再打扫)。 【丰田的定义】(清扫+清洁的工作环境) 首先确认每个人环境美化的能力并制定目标
.
8
标准化及训练
【固有定义】做到持续(美→保持行为的优美,外表+心灵)
【丰田的定义】(制定基准,以基准制定标准化,训练达到标
准化)
设定标准化项目及其法律 管理者要率先遵守标准化得行为准则,并设定其为公司的法
整顿——目视化管理,创造对问题一目了然的工作
环境
清洁——创建安全·健康的作业环境
清扫——工作环境的美化
素养——标准化及其训练
.
3
分离必需品及不需要品,坚决不生产不必要品
【固有定义】在生产过程中产生的边角材料,切割粉末,捆 包材料,粉尘,垃圾作为废品去处理,但是可以再利用的 边角料留下后用。
【丰田的定义】(固有理念当然合理,但关键在于不生产不 需要的商品) 区分的概念由各自(经理、部长、班组长…)来决定并且 一定要制定出统一的标准。
创造利润的劳动。除此之外其他劳动
都属于浪费!
.
10
(d)现在的 条件下不可消
除的浪费 改变条件后可
消除的浪费
(c)马上可 以消除的浪
费
《丰田式生产方式》课件

均衡各生产环节产能,有效消除浪费,提升生 产效率。
快速工业化
不断迭代改良生产方式,加速生产流程,以适 应日益竞争的市场环境。
丰田生产方式的优势
1
降低成本
2
节约生产资源,避免过度生产和库存积
压等浪费现象。
3
促进管理
4
丰富员工的培训内容,引导员工参与管 理和流程优化的行动。
提升效率
通过流程改进和质量优先的方式提高生 产效率。
公司名称 丰田汽车 华为 拜耳
成功经验
在世界范围内推广丰田式生产方式,成为行业标 准。
推行“质量第一”的管理理念,运用丰田式生产方 式提升产品品质。
针对差别化的市场需求,推行量身定制的丰田式 生产方式。
局限性及未来发展趋势
1 部分流程与政策冲突 2 出现质量问题
丰田式生产方式目前无法 完全适应所有市场和行业。
智能化制造、大数据和物联网。
工具
Kaizen
持续改进的方法论, 强调日常改进和逐步 完善。
5S
用5S的方法管理生产 现场,达到现场整顿、 清理和总结。
Jidoka
自动化的一种应用, 可以通过检测设备的 异常状况来支持质量 管理和流程控制。
Andon
自动化提示设备,可 以支持快速反应生产 线的异常情况。
丰田式生产方式的成功案例
提高品质
追求着眼于细节的品质标准,通过团队 人员共同努力提高产品的品质。
丰田式生产方式的核心活动
拉动式生产
依赖市场需求,避免过量生产或积压库存。
平衡式生产
均衡各生产环节产能,消除浪费,提升生产效率。
精益制造
集成全员态度,关注生产环节的每个细节,追求精 益求精的品质标准。
快速工业化
不断迭代改良生产方式,加速生产流程,以适 应日益竞争的市场环境。
丰田生产方式的优势
1
降低成本
2
节约生产资源,避免过度生产和库存积
压等浪费现象。
3
促进管理
4
丰富员工的培训内容,引导员工参与管 理和流程优化的行动。
提升效率
通过流程改进和质量优先的方式提高生 产效率。
公司名称 丰田汽车 华为 拜耳
成功经验
在世界范围内推广丰田式生产方式,成为行业标 准。
推行“质量第一”的管理理念,运用丰田式生产方 式提升产品品质。
针对差别化的市场需求,推行量身定制的丰田式 生产方式。
局限性及未来发展趋势
1 部分流程与政策冲突 2 出现质量问题
丰田式生产方式目前无法 完全适应所有市场和行业。
智能化制造、大数据和物联网。
工具
Kaizen
持续改进的方法论, 强调日常改进和逐步 完善。
5S
用5S的方法管理生产 现场,达到现场整顿、 清理和总结。
Jidoka
自动化的一种应用, 可以通过检测设备的 异常状况来支持质量 管理和流程控制。
Andon
自动化提示设备,可 以支持快速反应生产 线的异常情况。
丰田式生产方式的成功案例
提高品质
追求着眼于细节的品质标准,通过团队 人员共同努力提高产品的品质。
丰田式生产方式的核心活动
拉动式生产
依赖市场需求,避免过量生产或积压库存。
平衡式生产
均衡各生产环节产能,消除浪费,提升生产效率。
精益制造
集成全员态度,关注生产环节的每个细节,追求精 益求精的品质标准。
相关主题
- 1、下载文档前请自行甄别文档内容的完整性,平台不提供额外的编辑、内容补充、找答案等附加服务。
- 2、"仅部分预览"的文档,不可在线预览部分如存在完整性等问题,可反馈申请退款(可完整预览的文档不适用该条件!)。
- 3、如文档侵犯您的权益,请联系客服反馈,我们会尽快为您处理(人工客服工作时间:9:00-18:30)。
庫存的增加, 使問題掩蓋無 從改善
若容忍生產過剩就會產生新的浪費
‧料架、置場、料箱、運搬車、堆高機、增建 倉庫等
產生新的 浪費
.
無法 降低 成本
11
豐田生產方式 ( TOYOTA Production System )
(一) 豐田生產方式的基本想法
7. 表面效率和實際效率是不一樣的
表面效率
實際效率
,讓生產是依後工程所需的T/T而形成節拍。
节拍时间 ( T/T ):指一個部品需用多少時間生產的時間值 每班的稼動時間 ( 定時 )
T/T=每班生產必要數
.
16
豐田生產方式 ( TOYOTA Production System )
1.Just In Time
基本原則
后工程向前工程引取……所有生產都是由後工程向前工程發起, 後工程在必要的時候,向前工程引取必 要的東西及必要的量,前工程再依被拿 走的量而生產。 所以各工程後均須建立完成品店面。
.
8
豐田生產方式 ( TOYOTA Production System )
(一) 豐田生產方式的基本想法
5. 浪費的種類(七大類)
等待的浪費
浪費!!
運搬的浪費
加工本身的浪費
製造過剩的浪費
.
9
豐田生產方式 ( TOYOTA Production System )
七大浪費
1. 等待的浪費……………設備稼動利用率差 2. 運搬的浪費……………設備原價 ( 搬運者、堆高機等 ) 不必要的增加 3. 加工本身的浪費………不當的設計衍生出不必要的動作浪費 4. 在庫的浪費……………營運成本的增加、廠房SPACE浪費 5. 不良品修整的浪費……額外人員的增加 6. 動作的浪費……………人員工時、作業疲勞度浪費 7. 製造過剩的浪費………將問題 ( 改善的必要性 ) 掩蓋
.
10
豐田生產方式 ( TOYOTA Production System )
(一) 豐田生產方式的基本想法
6. 最嚴重的浪費(生產過剩)
將生產過剩視為浪費
多餘的人員、設 備,超量生產
為何麼會生產出多於銷售量的產品?
‧擁有過多的人員及設備
為何麼會想要生產過剩?
‧害怕設備故障、不良品、人員欠勤等安心量
『 將必要的東西在必要的時候只生產或運搬必要的量 』
‧用最少的資金、最小的空間、最少的人力、
最便宜的設備,去生產種類繁多且量少的產品 。 不 该 来 的 请 不 要 来
.
15
豐田生產方式 ( TOYOTA Production System )
1.Just In Time
基本原則
生產節拍的形成……讓生產是循環性的而且進度是可目視掌握的
(四) TPS的一大基础是:改善
3
豐田生產方式 ( TOYOTA Production System )
(一) 豐田生產方式的基本想法
◎豐田式生產方式: 是一種徹底排除浪費及追求製造方法合理性
的思想。
◎徹底排除浪費以降低成本
.
4
豐田生產方式 ( TOYOTA Production System )
10人每天生產 ( 100件 ) 10人每天生產 ( 120件 )
需要量
100
件/日
10人每天生產 ( 120件 )
=20件過 剩 9人每天生產 ( 100件 )
= 改善
.
12
豐田生產方式 ( TOYOTA Production System )
(一) 豐田生產方式的基本想法
8.增加勞動和提高能率是不一樣的
.
7
豐田生產方式 ( TOYOTA Production System )
(一) 豐田生產方式的基本想法
4. 減少浪費
『分析作業者的動作內容』
A 浪費
有附加價 值作業
C 作業者 動作 B
無附加價 值作業
A 浪費:
作業上所有不必要的動作
B 無附加價值作業:
現狀作業條件下不得不做
C 有附加價值作業:
對產品有實質效益的作業
2.自働化 生產
基本原則
自働化 與 自動化 的差異
自働化
‧異常時: 機械可自動判斷、自動停止
‧不產出不良 製程或機械本身能自動檢測不良 異常的原因能容易且快速掌握 可再發防止
不是现场 的管理大
看板
看板是後補充系統所使用的一種管理道具
.
17
看板
看板是实施JIT生产的管理道具,是引取 顺序或加工顺序的一张指示牌(情报);
.
18
看板
看板是实施JIT生产的管理道具,是引取 顺序或加工顺序的一张指示牌(情报);
.
19
豐田生產方式 ( TOYOTA Production System )
(一) 豐田生產方式的基本想法
1. 企業的目的
過更加文明、更加富裕的生活 透過公司促進地區的活性化 穩定員工的生活基礎
因此,企業 首先必須提高獲利,才能確保企業的永續生存
.
5
豐田生產方式 ( TOYOTA Production System )
豐田生產方式的基本想法: 提高利潤
(不降低成本就無法提高利潤)
增加勞動
提高能率
作業
動作
浪費
作業
動作
浪費
不實施改善;只是一味地加重 作業者的勞動強度
作業
動作
浪費
作業
動作 浪費
改善 將無意義的浪費改善成;
有效的正味作業
再加 50斤
.
13
豐田生產方式 ( TOYOTA Production System )
(二) 豐田生產方式两大支柱 1. JIT:及時化生產
2.自働化:生產製程的自働化改善
提高售價
利潤 成本
售價
降低成本
利潤 成本
售價
售價是由顧客決定的
.
6
豐田生產方式 ( TOYOTA Production System )
(一) 豐田生產方式的基本想法
3. 降低成本
成本結構
能源
材料費
製造(人事、在庫)
‧製造方法的不同將決定成本的差異,因此製程中的 『消除浪費』;將是降低成本的第一要務。
豐田生產方式( TOYOTA Production System )
.
1
豐田生產方式 TOYOTA
Production
System
.
2
豐田生產方式 ( TOYOTA Production System )
(一) 豐田生產方式的基本想法
(二) 豐田生產方式两大支柱: 1. JIT: 2.自働化:
(三).TPS评价的三大指标:品质● 生产性●在库
豐田式生產方式;是一種徹底排除浪費及追求製造 方法合理性的思想。 其貫穿整個系統的兩大支柱: 1. Just In Time (及時化生產)……徹底排除浪費 2. 生產的 自働化 ……杜絕不良品的產出
.
14
豐田生產方式 ( TOYOTA Production System )
1.Just In Time