铜铝双金属管材挤压成形工艺参数分析
挤压铸造双金属复合材料的成型工艺及微观组织研究

研究生(㈣:因丽导师(㈣黝日期可膨
武汉理工大学硕士学位论文
第1章绪论
1.1课题研究的背景
1.1.1金属基复合材料的发展背景
MMCs的研究始于20世纪60年代初期,至今已取得了很大发展。MMCs 发展的伊始是为满足航天航空等高技术部门对特殊性能结构材料的需求,因此
只要性能好,而不计成本,其研究工作大都集中于连续纤维增强的金属基复合
图41坩埚电炉表43坩埚电炉的主要性能参数型号sg21530型号ksw2d11额定电压380v50iiz额定电压220v额定温度800最高温度900最大熔铝量270kg最大功率15kw空炉升温时间2h2四柱式万能液压机图42为四柱式万能液压机适用于可塑性材料的压制工艺如冲压弯曲翻边薄板拉伸等也可以从事校正压装砂轮成形冷挤金属零件成武汉理工大学硕士学位论文形塑料制品及粉末制品的压制成形工艺以及冲裁模具和塑料模具的相关实验
挤压铸造是铸、锻结合的毛坯成形工艺,液体金属因在压力下结晶凝固,
可获得组织细密,质量好,性能高,表面光洁,机加工量少的优质零件。同时, 这种工艺一般不受合金牌号的限制,铸造或锻造合金均适用。国内对挤压铸造 工艺的研究比较少,影响挤压铸造件的因素又比较多,而且他们之间的相互关 系又非常复杂,定性的分析往往对实践的作用不大。 本文结合挤压铸造的特点,用挤压渗浸技术来对一种固态金属与另一种液
squeeze casting parts ale
so
many,and
there are interactions
among the
factors,SO
qualitative analysis Call hardly help the practical manufacture. Combining with the characteristics of squeeze casting。extrusive technology is used to compound solid metal and 1iquid metal into composites in this paper.Better performance of composites is embodied by the technics.During it,by changing the parameters,the interface structure and organizational characteristies of composites have been studied.Besides.the influence by comparing the seRing of different
挤压铸造双金属复合材料成型工艺及性能分析

世界有色金属 2023年 5月上10冶金冶炼M etallurgical smelting挤压铸造双金属复合材料成型工艺及性能分析户 芳,高秀峰,叶 云(山西晋中理工学院,山西 晋中 030600)摘 要:双金属复合材料是一种具有高利用率、综合性能优于其它金属材料的新型浇铸材料,为此,本文对挤压铸造工艺和性能进行了分析。
首先,通过对双金属复合材料的模态结构的建模、固液复合度的控制、双金属材料的包覆温度和退温成型等方面的研究,而后对其成型过程进行了分析,最后再对其导电性、轻量化等方面作了较为深入的研究。
关键词:复合材料;性能分析;挤压铸造;成型工艺中图分类号:TG249.2 文献标识码:A 文章编号:1002-5065(2023)09-0010-3Forming Technology and Performance Analysis of Squeeze Casting Bimetal CompositesHU Fang, GAO Xiu-feng, YE Yun(Shanxi Jinzhong Institute of Technology,Jinzhong 030600,China)Abstract: Bimetal composite material is a new type of casting material with high utilization rate and better comprehensive performance than other metal materials. Therefore, the squeeze casting process and performance are analyzed in this paper. First of all, through the research on the modeling of the modal structure of the bimetallic composite, the control of the solid-liquid composite, the coating temperature of the bimetallic material and the annealing molding, the molding process is analyzed, and finally, the conductivity and lightweight of the bimetallic composite are further studied.Keywords: composite materials; Performance analysis; Squeeze casting; Forming process收稿日期:2023-03作者简介:户芳,女,生于1988年,汉族,山东曹县人,硕士研究生,助教,研究方向:材料成型。
铜合金管棒材挤压过程及质量控制浅析

铜合金管棒材挤压过程及质量控制浅析摘要:铝合金挤压型材因其比强度高、耐蚀性好、导热性强、外形美观且可表面处理、易于回收再生等优点在民用建筑及交通运输等行业的应用十分广泛。
随着世界经济的发展和挤压技术的进一步改善,铝合金挤压型材的使用量和产量不断扩大。
关键词:合金型材;挤压;技术在我国铝型材挤压工业正在飞速发展,铝挤压型材的生产和消费规模达到了不可思议的程度,但是挤压模具的设计却还非常依靠模具设计师的经验,设计出的模具需要经过不断地的试模和修模来调整模具参数,这种模具设计制造模式不仅降低了企业的生产效率,大大提高模具制造成本,还使得挤压制品的均匀性存在诸多问题。
因而运用新的模具设计、制造方法已成为铝型材挤压生产行业的当务之急。
一、概述铝合金型材的挤压主要有正挤压、反挤压和混合挤压,其基本原理就是将铝合金铸锭放入容器挤压筒内,从另一端施加外力,迫使其从特定的模孔中流出,获得所需要的断面形状、尺寸及一定力学性能制品的塑性成形方法。
其原理图如图所示。
铝合金挤压加工技术是生产铝型材主要加工方法之一,与其他同类型的加工方法相比而言,挤压加工具有以下特点:(1)提高金属力学性能。
加工过程中除尺寸和形状发生改变外,金属的组织、性能得到改善和提高,尤其对于某些具有挤压效应的铝合金来说,其制品淬火时效后纵向强度远高于用其他方法加工的产品。
(2)提高金属的塑性变形能力。
挤压加工时的三向压应力比轧制或者锻造更为强烈和均匀,因此可以发挥出被加工金属的塑性潜力,使得变形量达到最大。
对于某些加工困难或不能加工的低塑性金属材料甚至脆性材料,也可以通过挤压进行加工。
(3)制品范围广、品种多。
挤压加工不但可以生产断面形状较为简单的管、棒、线材,还可以生产制品断面沿长度方向变化的变断面型材,甚至能生产尺寸超大的管材和型材,以及生产超小型精密型材。
(4)生产灵活性大。
只需在生产间隙简单的更换模具,就可以在同一台挤压设备上生产加工出不同尺寸或者不同形状的产品。
挤压铸造双金属复合材料成型工艺及性能分析

挤压铸造双金属复合材料成型工艺及性能分析摘要:挤压铸造是一种常用的制备双金属复合材料的成型工艺,其通过将两种不同材料的坯料同时加热至熔融状态,然后通过挤压成型的方式将两种材料紧密结合在一起。
本文摘要将重点关注挤压铸造双金属复合材料的成型工艺及其性能分析,并探讨相关的研究成果和结论。
通过调控挤压铸造工艺参数,如温度、压力和速度等,可以实现双金属复合材料的均匀分布和良好的界面结合。
同时,挤压铸造工艺还可以有效地消除材料之间的气孔和夹杂物,提高复合材料的密实性和力学性能。
在性能分析方面,本文将综合考虑双金属复合材料的力学性能、热性能和耐腐蚀性能等方面。
通过实验测试和数值模拟等方法,可以评估双金属复合材料的强度、硬度、热膨胀系数和耐腐蚀性等关键性能指标。
最后,本文将总结挤压铸造双金属复合材料的成型工艺及其性能分析的研究成果,并展望其在工程应用中的潜力和发展方向。
关键词:挤压铸造双金属复合材料;成型工艺;性能一、引言挤压铸造双金属复合材料是一种重要的金属复合材料制备方法,通过将两种不同金属材料在高温下进行挤压铸造,实现两种金属的结合。
该方法具有成本低、生产效率高、界面结合强度高等优点,因此在航空航天、汽车、电子等领域得到广泛应用。
然而,挤压铸造双金属复合材料的成型工艺和性能分析仍然是一个研究热点和难点。
在本文中,我们将重点关注挤压铸造双金属复合材料的成型工艺及其对材料性能的影响进行分析。
首先,我们将介绍挤压铸造双金属复合材料的基本原理和工艺流程。
然后,我们将探讨不同工艺参数对复合材料界面结合强度、力学性能和耐腐蚀性能等方面的影响。
同时,我们还将分析挤压铸造过程中可能出现的缺陷和问题,并提出相应的改进措施。
通过对挤压铸造双金属复合材料成型工艺及性能的深入研究和分析,可以为优化工艺参数、提高复合材料性能和推动其工程应用提供有益的参考和指导。
同时,对挤压铸造双金属复合材料的研究还可以为其他金属复合材料的制备方法提供借鉴和启示。
挤压成型工艺参数对铝合金塑性的影响
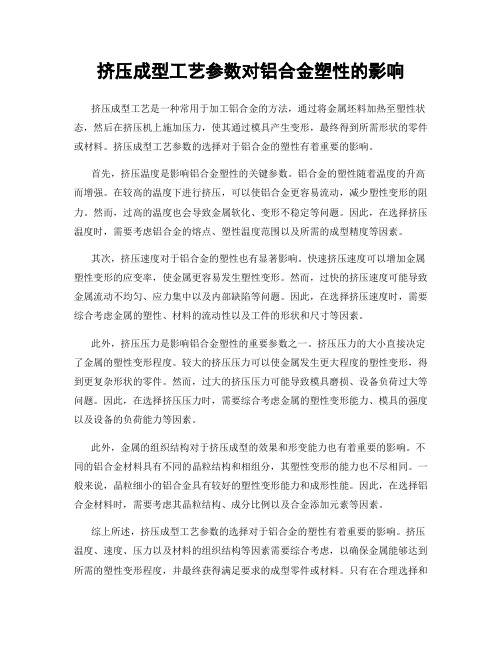
挤压成型工艺参数对铝合金塑性的影响挤压成型工艺是一种常用于加工铝合金的方法,通过将金属坯料加热至塑性状态,然后在挤压机上施加压力,使其通过模具产生变形,最终得到所需形状的零件或材料。
挤压成型工艺参数的选择对于铝合金的塑性有着重要的影响。
首先,挤压温度是影响铝合金塑性的关键参数。
铝合金的塑性随着温度的升高而增强。
在较高的温度下进行挤压,可以使铝合金更容易流动,减少塑性变形的阻力。
然而,过高的温度也会导致金属软化、变形不稳定等问题。
因此,在选择挤压温度时,需要考虑铝合金的熔点、塑性温度范围以及所需的成型精度等因素。
其次,挤压速度对于铝合金的塑性也有显著影响。
快速挤压速度可以增加金属塑性变形的应变率,使金属更容易发生塑性变形。
然而,过快的挤压速度可能导致金属流动不均匀、应力集中以及内部缺陷等问题。
因此,在选择挤压速度时,需要综合考虑金属的塑性、材料的流动性以及工件的形状和尺寸等因素。
此外,挤压压力是影响铝合金塑性的重要参数之一。
挤压压力的大小直接决定了金属的塑性变形程度。
较大的挤压压力可以使金属发生更大程度的塑性变形,得到更复杂形状的零件。
然而,过大的挤压压力可能导致模具磨损、设备负荷过大等问题。
因此,在选择挤压压力时,需要综合考虑金属的塑性变形能力、模具的强度以及设备的负荷能力等因素。
此外,金属的组织结构对于挤压成型的效果和形变能力也有着重要的影响。
不同的铝合金材料具有不同的晶粒结构和相组分,其塑性变形的能力也不尽相同。
一般来说,晶粒细小的铝合金具有较好的塑性变形能力和成形性能。
因此,在选择铝合金材料时,需要考虑其晶粒结构、成分比例以及合金添加元素等因素。
综上所述,挤压成型工艺参数的选择对于铝合金的塑性有着重要的影响。
挤压温度、速度、压力以及材料的组织结构等因素需要综合考虑,以确保金属能够达到所需的塑性变形程度,并最终获得满足要求的成型零件或材料。
只有在合理选择和控制工艺参数的情况下,挤压成型工艺才能更好地发挥其优势,实现高效的铝合金加工。
铝挤压成型的工艺特点及其优缺点分析

铝挤压成型的工艺特点及其优缺点分析首先,铝挤压成型具有高效性。
由于挤压成型是通过挤出机将铝合金材料从模具中挤压出来,整个过程可以实现自动化操作,大大提高了生产效率。
挤压成型速度快,生产速度大大加快,能够满足大批量生产的需求。
其次,铝挤压成型具有灵活性。
通过改变挤出机和模具的组合,可以制造出各种截面形状不同的铝制品。
从简单的杆状、管状产品到复杂的异型型材,挤压成型都可以实现。
这种灵活性使得铝挤压成型能够满足各种不同应用领域对铝制品的需求。
最后,铝挤压成型具有良好的可塑性。
铝合金材料在挤压过程中可以通过模具的挤压力将其塑造成各种复杂的形状。
挤压后的铝制品表面光滑,尺寸精确,质量稳定。
此外,铝合金具有良好的可加工性,可通过热处理进行强度调控,满足不同领域的使用要求。
1.低能耗:挤压成型是一种热成形加工方法,其能耗相对于其他金属加工方法较低,能够节约能源。
2.高生产效率:挤压成型能够实现大批量自动化生产,生产速度快,效率高。
3.成型精度高:挤压成型能够实现复杂形状的精确塑造,产品尺寸精度高,表面光滑。
4.良好的机械性能:挤压后的铝制品具有良好的强度和韧性,能够满足各种应用领域的需求。
5.可回收性:铝是一种可回收利用的金属材料,挤压成型过程中产生的废料可以回收再利用。
然而,铝挤压成型也存在一些缺点:1.模具制造成本较高:挤压成型需要使用专用模具,模具的制造和维护成本较高,对生产企业的投资较大。
2.适用性受限:铝挤压成型适用于中低压成型,对于高压的挤压成型需求无法满足。
3.变形控制难度较大:由于挤压成型是通过对铝合金材料施加挤压力来实现塑性变形,因此在挤压过程中控制材料的变形也是一项难度较大的工作。
总体而言,铝挤压成型具有高效性、灵活性和可塑性等显著特点,能够满足各种不同领域的需求。
随着工艺和设备的不断进步,铝挤压成型在铝制品加工领域的应用前景更加广阔。
挤压铸造双金属复合材料成型工艺及性能分析

机械加工与制造M achining and manufacturing挤压铸造双金属复合材料成型工艺及性能分析刘金龙(佳木斯大学材料科学与工程学院,黑龙江 佳木斯 154007)摘 要:双金属复合材料是一种新型的铸造材料,有着极高的利用率,且综合性能对比其他金属材料相对较好,有一定的材料使用价值。
因此,对挤压铸造双金属复合材料成型工艺及性能分析进行研究。
首先通过建立挤压铸造双金属复合材料的模型结构,控制其固液复合度,掌握挤压铸造双金属复合材料的包覆温度,以及挤压铸造双金属复合材料的退温成型,对挤压铸造双金属复合材料的成型工艺进行了一定的分析,并就其易导电性、轻量化等问题进行了全面的探讨。
关键词:复合材料;性能分析;挤压铸造;成型工艺中图分类号:TB331 文献标识码:A 文章编号:1002-5065(2021)08-0046-2Forming process and performance analysis of squeeze casting bimetal compositesLIU Jin-long(School of materials science and engineering, Jiamusi University, Jiamusi City, Heilongjiang Province,Jiamusi 154007,China)Abstract: Bimetallic composite is a new type of casting material, which has a high utilization rate, and its comprehensive performance is relatively better than other metal materials, so it has a certain material use value. Therefore, the forming process and performance analysis of squeeze casting bimetal composites were studied. Firstly, by establishing the model structure of squeeze casting bimetallic composite, controlling its solid-liquid composite degree, mastering the coating temperature of squeeze casting bimetallic composite, and the annealing forming of squeeze casting bimetallic composite, the forming process of squeeze casting bimetallic composite was analyzed, and its easy conductivity, lightweight and other issues were comprehensively discussed Discussion.Keywords: composite materials; performance analysis; squeeze casting; molding process目前,我国的金属资源是极为丰富的,被广泛应用于铸造行业,但随着行业需求的扩大,传统的单质金属逐渐不能满足铸造的要求,因此,双金属型复合材料应运而生。
挤压铸造双金属复合材料的成型工艺及微观组织研究的开题报告

挤压铸造双金属复合材料的成型工艺及微观组织研究的开
题报告
一、背景
双金属复合材料具有优异的力学性能、耐磨性和耐腐蚀性,因此在航空、汽车、电子等领域应用广泛。
挤压铸造是一种生产双金属复合材料的有效方法,可实现高效率、低成本的制造。
但目前尚缺乏对挤压铸造双金属复合材料成型工艺的细致研究。
二、研究目的
本研究旨在探索挤压铸造双金属复合材料的成型工艺,目标是实现制造高品质、高性能的复合材料。
同时,通过观察微观组织结构,研究成型工艺对双金属复合材料性能的影响。
三、研究内容
1. 设计铝/铜复合材料的化学成分和比例;
2. 设计挤压铸造的成形工艺,控制挤压、压力、温度等参数;
3. 采用金相显微镜、扫描电子显微镜等手段观察复合材料的微观组织结构,分析并比较不同成形工艺对复合材料的影响;
4. 测试复合材料的力学性能、耐磨性和耐腐蚀性等参数。
四、研究意义
挤压铸造双金属复合材料的成型工艺研究是复合材料业界的研究热点之一。
本研究将为铝/铜双金属复合材料的生产提供实用的成型工艺和制造技术。
此外,研究结果还可为其他复合材料类产品的制造提供一定的参考。
五、研究方法
本研究采用实验与理论相结合的方法,涉及挤压铸造技术、材料科学与工程、金属材料特性和力学性能等学科。
具体方法包括:实验设计、数据记录和统计、样品制备和测试、数据分析和模拟。
六、预期成果
本研究将实现以下成果:
1. 制定铝/铜双金属复合材料的制造工艺;
2. 比较不同成型工艺对复合材料性能的影响;
3. 探索德制造高品质、高性能的铝/铜双金属复合材料的最佳方法。
管材挤压工艺分析及实验研究

工 艺研 究 ・
管材 挤压 工艺分析及实验 研究
张士宏 王忠堂 , . 许沂 徐亭风 奠立华 周文龙 , , , (. 1中国科学院金属研究所 , 辽宁 沈 阳 101 ; 106
s 。d a eb e ee mn d b x ei e ti hsp p r t xr s oc d if e c p e ,h v en d tr ie y ep r n n ti a e .1 I et i fre a l n e m e ue n n nu
fc r a e aS e n su i d a t s h v lO b e t de .F o te r u t o x ei n .i i fu d ta xn s r e o rm e l e p r h s sf me t t s o n t tJi f c h e n e o h s rlt n o d fr a o trp r tr ,to u 'eam',rt f x u in.1b i n d d — a eai ,t eor t n ea eau e o l np rt e a o o t s o a i t z i e r o u rc t a a e n fr ain v l i o m t ee t o c y. Ke o d : y W r s aly .t b Xl S l.e p r n a l o u eC t li 1 x i X O e me t s y
An l ss a p rm e t S u y o b a y i nd Ex e i n t d n Tu e Ext u i n r so
铜管挤压工艺
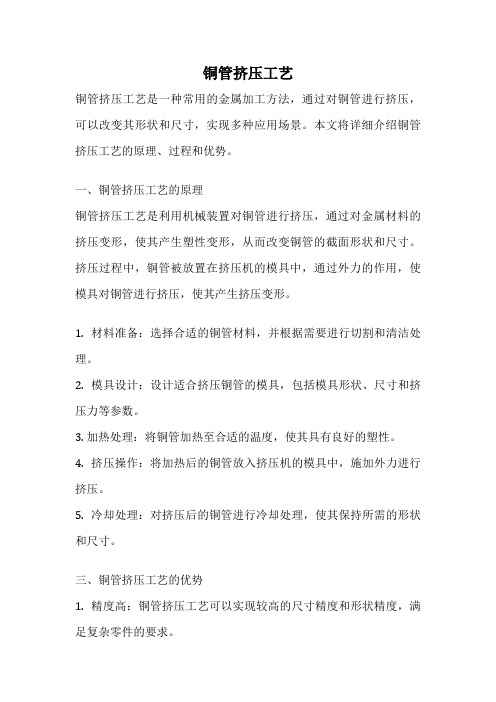
铜管挤压工艺铜管挤压工艺是一种常用的金属加工方法,通过对铜管进行挤压,可以改变其形状和尺寸,实现多种应用场景。
本文将详细介绍铜管挤压工艺的原理、过程和优势。
一、铜管挤压工艺的原理铜管挤压工艺是利用机械装置对铜管进行挤压,通过对金属材料的挤压变形,使其产生塑性变形,从而改变铜管的截面形状和尺寸。
挤压过程中,铜管被放置在挤压机的模具中,通过外力的作用,使模具对铜管进行挤压,使其产生挤压变形。
1. 材料准备:选择合适的铜管材料,并根据需要进行切割和清洁处理。
2. 模具设计:设计适合挤压铜管的模具,包括模具形状、尺寸和挤压力等参数。
3. 加热处理:将铜管加热至合适的温度,使其具有良好的塑性。
4. 挤压操作:将加热后的铜管放入挤压机的模具中,施加外力进行挤压。
5. 冷却处理:对挤压后的铜管进行冷却处理,使其保持所需的形状和尺寸。
三、铜管挤压工艺的优势1. 精度高:铜管挤压工艺可以实现较高的尺寸精度和形状精度,满足复杂零件的要求。
2. 节约材料:挤压过程中,铜管材料的利用率高,减少了材料的浪费。
3. 成本低:相比其他加工方法,铜管挤压工艺的设备和工艺成本相对较低。
4. 产品强度高:挤压后的铜管具有较高的强度和韧性,适用于各种应用场景。
5. 生产效率高:挤压工艺可以实现批量生产,提高生产效率和产能。
总结:铜管挤压工艺是一种常用的金属加工方法,通过对铜管进行挤压,可以改变其形状和尺寸。
该工艺具有精度高、节约材料、成本低、产品强度高和生产效率高等优势。
在实际应用中,铜管挤压工艺被广泛应用于航空航天、汽车制造、家具制造等领域。
通过合理设计和控制挤压工艺参数,可以实现对铜管的精确形状控制,满足各种复杂零件的需求。
《挤压铸造制备铜-铝双金属构件关键技术及组织性能研究》

《挤压铸造制备铜-铝双金属构件关键技术及组织性能研究》挤压铸造制备铜-铝双金属构件关键技术及组织性能研究一、引言随着现代工业的快速发展,对材料性能的要求日益提高,铜/铝双金属构件因其优异的导电性、导热性、轻量化和耐腐蚀性等特点,在众多领域得到广泛应用。
然而,由于铜和铝两种金属在物理性质、化学性质上的显著差异,其结合工艺一直是一个技术难题。
挤压铸造作为一种新型的制备工艺,具有制备效率高、组织结构可控等优点,被广泛应用于双金属构件的制备。
本文将就挤压铸造制备铜/铝双金属构件的关键技术及组织性能进行详细的研究和探讨。
二、挤压铸造制备铜/铝双金属构件的关键技术1. 材料选择与预处理首先,选择合适的铜、铝材料是制备铜/铝双金属构件的首要步骤。
同时,对所选材料进行预处理,如去除表面杂质、控制合金成分等,以优化其性能。
2. 模具设计与制造模具的设计与制造是挤压铸造过程中的关键环节。
模具的设计应考虑到金属的流动性、填充性以及双金属的结合性等因素。
同时,模具的制造精度和表面质量对双金属构件的最终质量有着重要的影响。
3. 挤压铸造工艺参数优化挤压铸造过程中的工艺参数包括温度、压力、速度等。
这些参数的优化对双金属构件的组织性能有着重要的影响。
通过优化这些参数,可以控制金属的流动性、填充性以及双金属的结合强度。
三、组织性能研究1. 微观组织结构分析通过金相显微镜、扫描电镜等手段,对铜/铝双金属构件的微观组织结构进行分析。
观察其晶粒大小、形状、分布等特征,以及铜、铝两相的界面结构。
2. 力学性能测试对铜/铝双金属构件进行拉伸、压缩、硬度等力学性能测试,以评估其力学性能。
同时,通过断口形貌分析,了解其断裂行为和断裂机制。
3. 物理性能分析对铜/铝双金属构件的导电性、导热性等物理性能进行分析,以评估其在实际应用中的性能表现。
四、研究结果与讨论通过上述研究,我们得出以下结论:1. 挤压铸造制备铜/铝双金属构件的关键技术包括材料选择与预处理、模具设计与制造以及工艺参数优化。
《挤压铸造制备铜-铝双金属构件关键技术及组织性能研究》

《挤压铸造制备铜-铝双金属构件关键技术及组织性能研究》篇一挤压铸造制备铜-铝双金属构件关键技术及组织性能研究一、引言随着制造业的不断发展,对于材料性能的要求也日益提高。
铜/铝双金属构件因其独特的物理和机械性能,在电子、汽车、航空航天等领域有着广泛的应用。
挤压铸造作为一种重要的制备工艺,在制备铜/铝双金属构件方面具有显著的优势。
本文旨在研究挤压铸造制备铜/铝双金属构件的关键技术及其组织性能,为相关领域的研发和应用提供理论支持。
二、挤压铸造制备铜/铝双金属构件的关键技术(一)材料选择与预处理选择合适的铜、铝材料是制备铜/铝双金属构件的基础。
在材料选择上,需考虑材料的导电性、导热性、强度等性能指标。
同时,对所选材料进行预处理,如表面清洁、除油、除锈等,以保证后续制备过程的顺利进行。
(二)模具设计与制造模具是挤压铸造的关键设备之一。
合理的模具设计能保证双金属构件的成型质量。
模具的设计应考虑金属流动的均匀性、冷却速度的控制等因素。
制造过程中需保证模具的精度和强度,以适应高温高压的铸造环境。
(三)挤压铸造工艺参数优化挤压铸造过程中,工艺参数的优化对双金属构件的性能至关重要。
主要包括压力控制、温度控制、速度控制等。
通过调整这些参数,可以控制金属的填充速度、密度和结晶组织,从而影响最终产品的性能。
(四)后处理工艺后处理工艺包括热处理、表面处理等步骤。
通过热处理可以改善材料的组织结构,提高其力学性能和耐腐蚀性能。
表面处理则可以增强材料的表面性能,如硬度、耐磨性等。
三、铜/铝双金属构件的组织性能研究(一)显微组织观察通过显微镜观察铜/铝双金属构件的显微组织,可以了解其组织结构、晶粒大小及分布等情况。
这些信息对于评估材料的性能具有重要意义。
(二)力学性能测试通过拉伸试验、硬度测试等方法,可以评估铜/铝双金属构件的力学性能,如抗拉强度、屈服强度、延伸率等。
这些性能指标对于评价材料在实际应用中的表现至关重要。
(三)耐腐蚀性能研究铝及其合金在特定环境下易发生腐蚀,因此研究铜/铝双金属构件的耐腐蚀性能具有重要意义。
铜铝双金属复合管二辊纵轧成形工艺研究

面粗糙度良好" 冷斜轧工艺适用于大复合比双金
属管材(
,%-
李明雪等
对
H[H 限动芯棒钢管连轧
过程进行 H=LD模拟分析和轧制实验" 得到钢管
外径' 轧制力等误差参数和轧辊参数对轧制效果
的影响( 目前管材轧制研究主要集中在钢管和复
合管方面" 缺乏二辊带芯棒的复合管相关连轧成
7,1)-3/)* 1@RRIL>=FBS78BSD@SR@N7KIR7RIN=LIS=78FOBNIJ 78 D@88IDK78AR7RIG7KK78ANNBDE =NLIGL7AIL=K@LN =8J =7LD@8J7K7@8ILN" Y7KE I?DIFFI8KSIDE=87D=FRL@RILK7IN" A@@J S=DE78=U7F7KO=8J NKL@8AID@8@SOQ-KKEIN=SI K7SI" =N=8 IGG7D7I8KR7RIG@LS78ASIKE@J" F@8A7KBJ78=FL@FFIJ R7RI7NNB7K=UFIG@LL@FF78A=8J G@LS78AD@RRIL> =FBS78BSD@SR@N7KIR7RINQ:8 KE7NR=RIL" KEIKEI@LIK7D=FNKBJO@GL@FF78AJIG@LS=K7@8" E@FINE=RINONKIS" L@FF78AG@LDI" IF@8A=K7@8" IKDQ" =8J KEI=8=FON7N@GG787KIIFISI8KN7SBF=K7@8 D@SR@N7KIR7RID@8K78B@BNL@FF78A G@LS78A" D@SU78IJ Y7KE I?RIL7SI8KN" KEII?RIL7SI8K=FLINBFKNNE@Y KE=KKEI788IL=8J @BKILY=FFN@GKEI D@SR@N7KIR7RI=LINS@@KE =8J JIGIDK>GLII" =8J KEISIDE=87D=FU78J78AG@LDI7N#$/# H[=" YE7DE LI=F7XIN IGGIDK7MID@SR@N7KIQ*EI=MIL=AIILL@LNUIKYII8 KEIKEI@LIK7D=F=8J SI=NBLIJ M=FBIN@GL@FF78AG@LDI" =NYIFF=N UIKYII8 KEIKEI@LIK7D=F=8J N7SBF=KIJ M=FBIN" YILI",$))j =8J "'$ZZj" LINRIDK7MIFOQ*EI=MIL=AIILL@LN UIKYII8 KEIN7SBF=KIJ =8J SI=NBLIJ M=FBIN@GD@RRILF=OIL" =FBS78BS F=OIL=8J K@K=FY=FFKE7DV8INNYILI #$Z,j" "$,#j =8J #$&%j" LINRIDK7MIFOQ*EI=MIL=AIILL@LNUIKYII8 KEIKEI@LIK7D=F=8J SI=NBLIJ M=FBIN@G IF@8A=K7@8" =NYIFF=NUIKYII8 KEIKEI@LIK7D=F=8J N7SBF=KIJ M=FBIN" YILI%$/)j =8J '$""j" LINRIDK7MIFO" YE7DE YILIY7KE78 =LI=N@8=UFIL=8AIQ*EILINBFKNMIL7GOKEI=DDBL=DO=8J LIF7=U7F7KO@GKEIKEI@LIK7D=FLINI=LDE =8J N7SBF=K7@8 =8=FON7N@GKEID@RRIL>=FBS78BSU7SIK=FF7DD@SR@N7KIKBUIL@FF78A=8J G@LS78ARL@DINNQ 8"69%-01* D@RRIL>=FBS78BSD@SR@N7KIR7RI# F@8A7KBJ78=FL@FF78AG@LS78A# IGGIDK7MID@SR@B8J78A
铝、铜材连续挤压工艺

2.7 铝、铜材连续挤压工艺2。
7。
1 铝及铝合金连续挤压工艺目前国外铝及铝合金连续挤压工艺虽然已臻成熟,但是关于生产工艺的具体报导却很少。
2。
7。
1。
1 连续挤压工艺流程铝及铝合金连续挤压工艺工艺流程如下:铝杆坯→矫直→超声波清洗→热水洗→吹干(或烘干)→连续挤压→冷却→⎭⎬⎫⎩⎨⎧→→→→盘状制品卷取张力导线直条制品矫直剪切→检验→包装入库 2。
7.1。
2 生产工艺的简要说明国产LJ300CONFORM 机工艺试验研究使用的铝及铝合金杆坯有:4.02.00.10+-φ㎜的L 2连铸连轧盘杆,每盘重约一吨。
2.02.00.10+-φ㎜的LF2和LD31铝合金挤压杆,每根长约30米。
连铸连轧盘杆的椭圆度较大,表面比较粗糙,且油污、灰尘等脏物也较严重。
挤压杆形状、尺寸均比较精确、表面洁净度也较好。
(1) 铝杆存入放线盘架后,经过多辊交叉矫直机进行矫直,使弯曲度小于2mm/m ,以便能平直、顺利地通过超声清洗装置,不致被自重度刮伤表面或卡住。
(2) 超声清洗:目的是除去铝杆表面的油污,氧化脏物等,清洗温度为65±5︒C ,超声振子频率为19±3KH 2,共20个,总功率为500~1000V A.清洗时间为2~5秒。
(3) 热水洗:目的是通过热水漂洗除去铝杆表面残留的清洗液,以免侵蚀挤压工具和带入制品内,水洗温度为65±5︒C,时间为274 2 CONFORM 技术秒左右。
(4) 吹干:目的是吹干铝杆表面的水迹,不使被带入挤压型腔内,挤入制品内产生气泡等缺陷。
(5) 连续挤压:挤压铝及铝合金时,挤压轮与挤压靴之间的间隙量调节为0。
8~1。
2mm 左右,挤压温度和挤压速度视挤压合金与挤压制品而异(见表2-2)。
(6) 冷却:制品挤压后,经水冷槽直接水冷至40︒C 左右,方可进入张力导线架送至卷取机,以免导线与卷取过程中再度产生形变。
(7) 张力导线:导线时的张力大小依冷态管、线制品的合金牌号、品种规格而异,一般控制张力使之发生1%左右的附加延伸量为宜.(8) 卷取(9) 检验(10) 包装入库2.7。
铜管挤压工艺

铜管挤压工艺铜管挤压工艺是一种常用的金属成形方法,通过对铜管施加外力,使其在模具的作用下发生塑性变形,从而得到所需的形状和尺寸。
这种工艺广泛应用于航空航天、汽车制造、建筑领域等各个行业。
本文将从铜管挤压工艺的原理、设备、优点和应用等方面进行详细介绍。
一、铜管挤压工艺的原理铜管挤压工艺是利用金属材料在受到外力作用下发生塑性变形的特性,通过挤压机将铜管放入模具中,通过模具的作用使铜管发生塑性变形,从而得到所需的形状和尺寸。
在挤压过程中,铜管受到的应力和变形主要集中在模具的凸模部分,通过凸模的形状和尺寸来控制挤压件的形状和尺寸。
挤压过程中,铜管会发生轴向缩径和周向流动,从而使铜管的截面面积减小,长度增加,形成所需的形状。
铜管挤压工艺需要使用专用的挤压机和模具。
挤压机是通过液压系统提供动力,使活塞施加外力对铜管进行挤压。
模具是根据挤压件的形状和尺寸来设计和制造的,模具的形状和尺寸决定了挤压件的形状和尺寸。
三、铜管挤压工艺的优点铜管挤压工艺具有以下几个优点:1. 高效性:铜管挤压工艺可以快速地将铜管加工成所需的形状和尺寸,生产效率高。
2. 精度高:铜管挤压工艺可以获得较高的尺寸精度和表面质量,满足各种精密要求。
3. 节省材料:铜管挤压工艺可以最大限度地利用材料,减少材料的浪费。
4. 强度高:通过挤压工艺加工的铜管具有较高的强度和硬度,可以满足各种工程要求。
四、铜管挤压工艺的应用铜管挤压工艺广泛应用于各个行业,特别是在航空航天、汽车制造和建筑领域。
在航空航天领域,铜管挤压工艺常用于制造飞机发动机燃油管、液压管等零部件。
在汽车制造领域,铜管挤压工艺常用于制造汽车制动管、冷却器管等零部件。
在建筑领域,铜管挤压工艺常用于制造建筑装饰材料,如铜管扶手、铜管栏杆等。
铜管挤压工艺是一种重要的金属成形方法,具有高效性、精度高、节省材料和强度高等优点。
它在航空航天、汽车制造和建筑领域得到广泛应用,为各个行业的发展做出了重要贡献。
《挤压铸造制备铜-铝双金属构件关键技术及组织性能研究》范文

《挤压铸造制备铜-铝双金属构件关键技术及组织性能研究》篇一挤压铸造制备铜-铝双金属构件关键技术及组织性能研究一、引言随着科技的发展,对于轻质、高强度和高导电性能的材料需求不断增加。
铜/铝双金属构件由于其优良的导电、导热及轻量化特性,在汽车、电子和航空等领域具有广泛的应用前景。
挤压铸造作为一种有效的金属成型工艺,其能高效制备铜/铝双金属构件并确保材料良好的力学性能。
本文将针对挤压铸造制备铜/铝双金属构件的关键技术以及其组织性能进行深入的研究与探讨。
二、挤压铸造制备铜/铝双金属构件的关键技术(一)工艺流程挤压铸造的工艺流程主要包括模具设计、材料准备、加热、压力铸造、冷却及后处理等步骤。
在制备铜/铝双金属构件时,需要特别注意模具的设计,以实现铜铝两种金属的准确复合。
(二)模具设计模具的设计是挤压铸造的关键环节。
在设计铜/铝双金属构件的模具时,应考虑到金属的流动性、收缩率以及两者的结合力等因素。
同时,为了确保铜铝两种金属的准确复合,模具需要具备精确的尺寸和良好的热稳定性。
(三)材料准备在挤压铸造过程中,原材料的质量直接影响到最终产品的性能。
因此,需要选用纯度高、组织均匀的铜铝合金作为原材料。
同时,为了提高两种金属的结合力,还可以添加一些合金元素或表面处理来改善界面性能。
(四)压力铸造与冷却在压力铸造过程中,需要控制好压力、温度和时间等参数,以确保铜铝两种金属能够充分融合。
冷却过程中,应控制冷却速度,以获得良好的微观组织和机械性能。
三、组织性能研究(一)微观组织观察通过金相显微镜、扫描电镜等手段,对铜/铝双金属构件的微观组织进行观察。
可以分析出两种金属的融合情况、界面结构以及晶粒大小等信息。
(二)力学性能测试对铜/铝双金属构件进行拉伸、压缩、硬度等力学性能测试,以评估其机械性能。
同时,还可以通过疲劳测试来评估其耐久性。
(三)导电与导热性能测试由于铜/铝双金属构件具有良好的导电和导热性能,因此需要对其导电和导热性能进行测试。
- 1、下载文档前请自行甄别文档内容的完整性,平台不提供额外的编辑、内容补充、找答案等附加服务。
- 2、"仅部分预览"的文档,不可在线预览部分如存在完整性等问题,可反馈申请退款(可完整预览的文档不适用该条件!)。
- 3、如文档侵犯您的权益,请联系客服反馈,我们会尽快为您处理(人工客服工作时间:9:00-18:30)。
2 1 o 3 0 2N .
重 型 机 械
・ 7・ 4
铜 铝 双金 属 管材 挤 压 成形 工 艺 参数 分 析
宋继顺 ,马静 云 ,张建民 r ,李 少光
( .天津理工大学 材料科学与工程学院 , 1 天津 重点实验 室 ,天津 30 8 ;2 0 34 .天津市光 电显示材料与器件
Pa a e e na y i fe t uso o m i r c s o r m t r a s f r a u i m ・ o e l d b m ea u l m nu c pp r c a i t lt be
n s ft b ali u i r sc n n l o ema d e sb g e a 5 n h c n s ai f n en lly r e so e w l s n fm a o e a ge ft n r l i g rt n7 。a d ti k e sr t o tr a a e u o h i h o i t x e n l a e s5 5 :3 5 T e d e s u t r a e i n d a c r i g t h x e i n e u t o e t r a y ri . l . . h i t cu e w s d sg e c o dn o t e e p r r me t s l r . Ke r s o c v i ma d il c n n l ; a u n m— o p r ca i t u e; e tu in fr n y wo d :c n a e d e; n rl; o e a g e l mi u c p e ld b mea t b l x r so o mi g
T ajn3 0 8 ini 0 3 4,C ia .Sn se l f co . t. u yn 7 0 9,C ia hn :3 io te r tr Co,Ld ,L o a g4 1 3 Re a y hn )
Ab ta t I i fu d ta h r cu e otn o c r n t ei tr a l y rme a wh n t ec n a ed e w t o e sr c : t s o n h t efa t r f c u so ne n l a e tl e o c v i i ac n t e h h h a g e a d e t so i i n r li u e o e tu e a l mi u c p e ld b mea u e A e i n l n xr i n d e w t a ma d e s s d t x r d n au n m— o p r ca i tlt b . u h n w de sr cu e t a h s a ma d e t o e a ge a d a c l d ia o c v i s p o o e h o g E s lt n t t r h t a n r l h c n n l n y i r l n a e d e i r p s d tr u h F M i a i u wi n c c mu o o xr in f mi g o i tlt e fr e t so r n fab me a b . Th tl u e d fr a in a p ai g w e h n r lSc n n l i u o u e mea b eo t m t p e rn h n t e ma d e o e a ge s o d f rn sa a y e i e om- D o t a e h o ea g eu d rte e t me c n i o n l z d b E i ee ti n lz d w t D f r 3 s f r .T e c n n l n e xr f h w h e o dt n i a ay e y F M. i s
S ONG j.h n ’, MA Jn .u Z isu igy n , HAN J n mi L h og a g G i — n , IS a —u n 。 a ( . Cl g f t i c neadE g er g i j nvrt o eho g ,Taj 034 1 oeeo e a Si c n ni e n ,Ta i U i sy f cnl y i i 308 l Ma rl e n i nn e i T o nn C ia .Taj e aoa r r hte c i Dsl aeisadD v e , h ;2 i i K yL brt yf o l tc i a M t a n ei s n nn o oP o e r p y rl c
30 8 ;3 0 34 .中钢集 团耐火材料有 限公 司 ,洛 阳 4 13 ) 70 9
摘
要 :通过对双金属管材挤压 成形 的有 限元模拟发现 :当挤压模凹模带有锥 角而芯棒为 圆柱体
时挤压铜铝 双金属管材时常 出现 内层金属断裂的现象。为了解决这个缺陷通过反向思考提 出了芯棒 带 有锥 角而凹模为直筒 的特殊的模具结构 ,并结 合有 限元 软件 D f m一3 er o D分析 了不 同芯棒锥 角下金 属
的变形情况 ,确定 了合适 的锥角大小 ,同时对 双金属管材 内外管材 的厚度 比也有限制要求 ,成功 实现
了铜铝双金 属管件 的挤压成形 。通过对挤 压过程 中的芯棒进行 强度校 核对 此挤压模 具 的结 构进 行了
设计。
关 键 词 :锥 角 ;直 筒 ;有 限 元 ;校 核 中图 分 类 号 :T 36 1 G 7 . 文 献 标 识 码 :A 文章 编 号 :10 —16 ( 02 3— 0 7— 4 0 1 9 X 2 1 )0 0 4 0