生产综合效率及MTBF指标计算基准
MTBF指标和计算方法

MTBF指标和计算方法MTBF指标和计算方法1)一般常用单位计算在单位时间内(一般以年为单位),产品的故障总数与运行的产品总量之比叫―故障率‖(Failure rate),常用λ表示。
例如网上运行了100 台某设备,一年之内出了2次故障,则该设备的故障率为0.02次/年。
当产品的寿命服从指数分布时,其故障率的倒数就叫做平均故障间隔时间(Mean Time Between Failures),简称MTBF。
即:MTBF=1/λ例如某型号YY产品的MTBF时间高达16万小时。
16万小时约为18年,并不是说YY产品每台均能工作18年不出故障。
由MTBF=1/λ可知λ=1/MTBF=1/18年(假如YY产品的寿命服从指数分布),即YY产品平均年故障率约为5.5%,一年内,平均1000台设备有55台会出故障。
整机可靠性指标用平均故障间隔时间表示:MTBF=(T1+T2+…Tn)/ rn式中:MTBF——整机的平均故障间隔时间,h;Ti——第i台被试整机的累计工作时间,h;rn——被试整机在试验期间内出现的故障总数。
字串82)通信上通过单个模块计算总值MTBF-平均无故障时间,是指两次故障之间所经历的时间,是一种统计平均值,MTBF值的确定,通常采用两种方式:1) 理论统计法:根据器件、组件及约束条件的实际情况,累计平均得到的。
2) 经验统计法:根据工厂或实验室破坏性记录,累计平均得到的数据。
1+0单机系统MTBF统计值根据1+0单机系统的组成框图,总的MTBF统计值由以下公式给出:1/MTBF总=1/MTBF发高频+1/MTBF收高频+1/MTBF调制+1/MTBF基带+1/MTBF 电源3)通信网络中串并联部件所导致的MTBF不同λ=1/MTBF (h)如果两个部件串联工作,其中一个发生失效,整个功能就失效了,串联结构的:λ总=λ1+λ2或MTBF总=1/(λ1+λ2)对于并联或冗余的结构,虽然一个部件失效,但仍然维持功能的完整性(100%);1/λ总=(1/λ1)+(1/λ2)+(1/(λ1+λ2))或MTBF总=(λ21 + λ1λ2 +λ22)/(λ21λ2 +λ1λ22)字串44)一般产品的MTBF计算平均失效(故障)前时间(MTTF)设N0个不可修复的产品在同样条件下进行试验,测得其全部失效时间为T1,T2,……TN0。
MTBF指标和计算方法
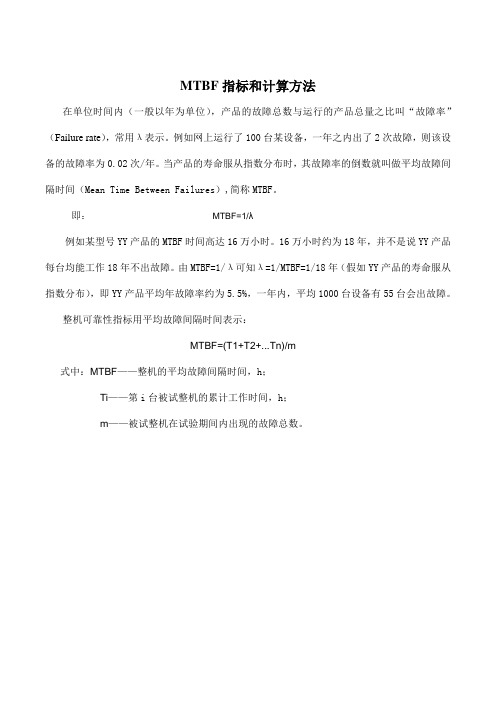
MTBF指标和计算方法
在单位时间内(一般以年为单位),产品的故障总数与运行的产品总量之比叫“故障率”(Failure rate),常用λ表示。
例如网上运行了100台某设备,一年之内出了2次故障,则该设备的故障率为0.02次/年。
当产品的寿命服从指数分布时,其故障率的倒数就叫做平均故障间隔时间(Mean Time Between Failures),简称MTBF。
即:MTBF=1/λ
例如某型号YY产品的MTBF时间高达16万小时。
16万小时约为18年,并不是说YY产品每台均能工作18年不出故障。
由MTBF=1/λ可知λ=1/MTBF=1/18年(假如YY产品的寿命服从指数分布),即YY产品平均年故障率约为5.5%,一年内,平均1000台设备有55台会出故障。
整机可靠性指标用平均故障间隔时间表示:
MTBF=(T1+T2+...Tn)/m
式中:MTBF——整机的平均故障间隔时间,h;
Ti——第i台被试整机的累计工作时间,h;
m——被试整机在试验期间内出现的故障总数。
MTBF指标和计算方法

MTBF指标和计算方法1〕一般常用单位计算在单位时间内〔一般以年为单位〕,产品的故障总数与运行的产品总量之比叫"故障率"〔Failure rate〕,常用λ表示.例如网上运行了100 台某设备,一年之内出了2次故障,则该设备的故障率为0.02次/年.当产品的寿命服从指数分布时,其故障率的倒数就叫做平均故障间隔时间〔Mean Time Between Failures〕,简称MTBF.即:MTBF=1/λ例如某型号YY产品的MTBF时间高达16万小时.16万小时约为18年,并不是说YY产品每台均能工作18年不出故障.由MTBF=1/λ可知λ=1/MTBF=1/18年〔假如YY产品的寿命服从指数分布〕,即YY产品平均年故障率约为5.5%,一年内,平均1000台设备有55台会出故障.整机可靠性指标用平均故障间隔时间表示:MTBF=〔T1+T2+…Tn〕/ rn式中:MTBF——整机的平均故障间隔时间,h;Ti——第i台被试整机的累计工作时间,h;rn——被试整机在试验期间内出现的故障总数. 字串82〕通信上通过单个模块计算总值MTBF-平均无故障时间,是指两次故障之间所经历的时间,是一种统计平均值,MTBF值的确定,通常采用两种方式:1> 理论统计法:根据器件、组件与约束条件的实际情况,累计平均得到的.2> 经验统计法:根据工厂或实验室破坏性记录,累计平均得到的数据.1+0单机系统MTBF统计值根据1+0单机系统的组成框图,总的MTBF统计值由以下公式给出:1/MTBF总=1/MTBF发高频+1/MTBF收高频+1/MTBF调制+1/MTBF基带+1/MTBF 电源3〕通信网络中串并联部件所导致的MTBF不同λ=1/MTBF <h>如果两个部件串联工作,其中一个发生失效,整个功能就失效了,串联结构的:λ总=λ1+λ2或MTBF总=1/〔λ1+λ2〕对于并联或冗余的结构,虽然一个部件失效,但仍然维持功能的完整性<100%>;1/λ总=〔1/λ1〕+〔1/λ2〕+〔1/〔λ1+λ2〕〕或MTBF总=〔λ21 + λ1λ2 +λ22〕/〔λ21λ2 +λ1λ22〕字串44〕一般产品的MTBF计算平均失效〔故障〕前时间<MTTF>设N0个不可修复的产品在同样条件下进行试验,测得其全部失效时间为T1,T2,……TN0.其平均失效前时间<MTTF>为:MTTF = <T1+T2+…Tn>/N0由于对不可修复的产品,失效时间即是产品的寿命,故MTTF也即为平均寿命.当产品的寿命服从指数分布时,MTTF=1/λ平均故障间隔时间〔MTBF〕一个可修复产品在使用过程中发生了N0次故障,每次故障修复后又重新投入使用,测得其每次工作持续时间为T1,T2,……TN0,其平均故障间隔时间MTBF 为:MTBF=T/N0其中,T为产品总的工作时间.对于完全修复的产品,因修复后的状态与新产品一样,一个产品发生了N0次故障相当于N0个新产品工作到首次故障.因此:MTBF=MTTF当产品的寿命服从指数分布时,产品的故障率为常数λ,则MTBF=MTTF=1/λ.平均修复时间<MTTR>其观测值是修复时间t的总和与修复次数之比:MTTR=<T1+T2+…Tn>/n 字串9式中:ti——第i次修复时间;n——修复次数.5〕简单计算〔通过温度系数〕MTBF = Total Test Time*Acceleration Factor/Coefficient <refer to the table>Total Test Time = <sample size>*<test days>*<power on hour/day>Acceleration Factor = e <E/K> <1/Tn-1/Ta>Ta = Burn – in Room Test TemperatureTn = Normal TemperatureCoefficientConfidenceLevel Numbers of Failure <n>0 1 2 3 4 5 6 7 8 9Mn<90%> 2.30 3.89 5.32 6.68 7.99 9.27 10.53 11.77 12.99 14.20字串6Acceleration Factor = e <E/K> <1/Tn-1/Ta> 此加速模型即为阿列纽斯加速模型。
MTBF是什么和MTBF计算的方法(转载)
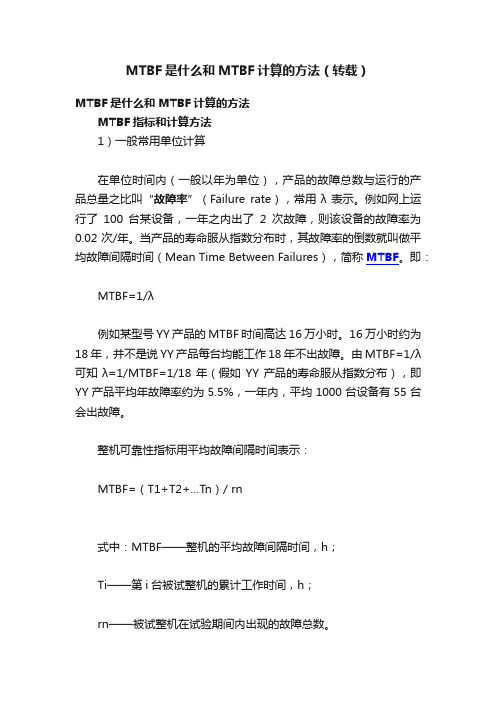
MTBF是什么和MTBF计算的方法(转载)MTBF是什么和MTBF计算的方法MTBF指标和计算方法1)一般常用单位计算在单位时间内(一般以年为单位),产品的故障总数与运行的产品总量之比叫“故障率”(Failure rate),常用λ表示。
例如网上运行了100 台某设备,一年之内出了2次故障,则该设备的故障率为0.02次/年。
当产品的寿命服从指数分布时,其故障率的倒数就叫做平均故障间隔时间(Mean Time Between Failures),简称MTBF。
即:MTBF=1/λ例如某型号YY产品的MTBF时间高达16万小时。
16万小时约为18年,并不是说YY产品每台均能工作18年不出故障。
由MTBF=1/λ可知λ=1/MTBF=1/18年(假如YY产品的寿命服从指数分布),即YY产品平均年故障率约为5.5%,一年内,平均1000台设备有55台会出故障。
整机可靠性指标用平均故障间隔时间表示:MTBF=(T1+T2+…Tn)/ rn式中:MTBF——整机的平均故障间隔时间,h;Ti——第i台被试整机的累计工作时间,h;rn——被试整机在试验期间内出现的故障总数。
2)通信上通过单个模块计算总值MTBF-平均无故障时间,是指两次故障之间所经历的时间,是一种统计平均值,MTBF值的确定,通常采用两种方式:1) 理论统计法:根据器件、组件及约束条件的实际情况,累计平均得到的。
2) 经验统计法:根据工厂或实验室破坏性记录,累计平均得到的数据。
1+0单机系统MTBF统计值根据1+0单机系统的组成框图,总的MTBF统计值由以下公式给出:1/MTBF总=1/MTBF发高频 +1/MTBF收高频 +1/MTBF调制+1/MTBF基带 +1/MTBF电源3)通信网络中串并联部件所导致的MTBF不同λ=1/MTBF (h)如果两个部件串联工作,其中一个发生失效,整个功能就失效了,串联结构的:λ总=λ1+λ2或MTBF总=1/(λ1+λ2)对于并联或冗余的结构,虽然一个部件失效,但仍然维持功能的完整性(100%);1/λ总=(1/λ1)+(1/λ2)+(1/(λ1+λ2))或 MTBF总=(λ21 + λ1λ2 +λ22)/(λ21λ2 +λ1λ22)4)一般产品的MTBF计算平均失效(故障)前时间(MTTF)设N0个不可修复的产品在同样条件下进行试验,测得其全部失效时间为T1,T2,……TN0。
生产综合效率指标诸基准.pptx
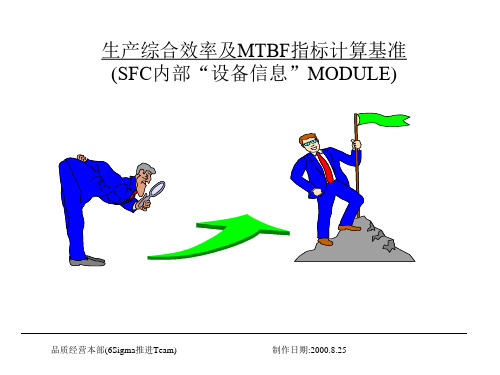
大分类
中分类
计划LOSS 交班时间/就餐/休息/生产中断/计划保全
停止LOSS 设备故障/动力事故/JOB CHANGE/流量不足 流量调节/资材短缺/品质问题
性能LOSS 大分类瞬间停止/速度降低/空转
不良LOSS 不良/再作业
对中分类的小分类是各事业Team内部的现象, 具体内容参考后面说明的定义
N
各LINE 详细内容
E
单
位
事业场/LINE 日推移
事业场/LINE 月推移
输入非稼动LOSS 基准情报
全工程MTBF现况
工
程
各工程LINE别 MTBF现况
单
位
日 MTBF现况
月 工程MTBF现况
*兰色:目前是从WEB提供,以后使用ESFC时 需附加的事项
3/16
3. 指标计算基准
3-1 生产综合效率:与CAPA对比,生产的良品比率.
10/12
指标计算基准
3-3-4.LOSS用语பைடு நூலகம்义
[计划LOSS] (1)接班时间:交班之间为了交班发生的设备不运转时间 (2)就餐/休息:工作中为了就餐/休息发生的设备不运转时间 (3)生产中断:计划的工作时间中根据发生的紧急情况计划性
地中断生产的时间。 (4)计划保全:工作之中为了设备预防保全停止设备的时间 (5)PIOLT:工作之中开发及品质关系实施的设备运转时间,
7/12
指标计算基准
3-3.有关指标计算参考资料(用语及)计算公式
3-3-1.交率用语及计算公式
(1)生产综合效率:工作时间中为产出良品消耗的时间比率 (价值运转时间工作时间)×100 OR(负荷率×时间运转率×性能运转率×良品率)
OEE﹑MTBF﹑MTTR定定义及计算方法
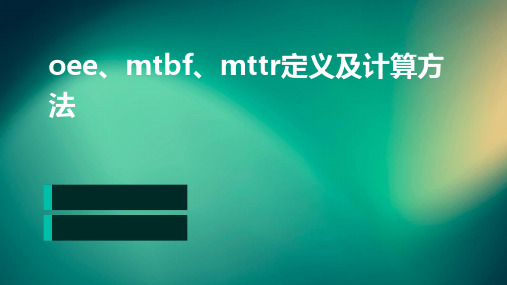
的维修时间,减少停机时间。
降低生产成本
优化生产流程
通过分析OEE、MTBF和MTTR数据,发现生产流程中的瓶颈和 浪费,改进生产工艺和布局,降低生产成本。
提高资源利用率
合理安排生产计划,均衡设备负载,减少设备空转和闲置时间, 提高资源利用率。
减少维修费用
通过降低设备故障率和缩短维修时间,减少维修成本和外委维修 费用。
直接法
通过统计设备故障次数和总运行时间来计算 MTBF。这种方法需要详细的设备故障记录和运 行时间记录。
寿命试验法
通过加速寿命试验来推算设备的MTBF。这种方 法需要在设备上施加高于正常工作条件的应力, 以加速设备的失效。
维修性参数法
通过设备的维修性参数来计算MTBF。这种方法 需要考虑设备的维修策略、维修时间和维修效果 等因素。
它综合考虑了设备的可用性、性能和 效率,是衡量设备整体性能的重要指 标。
OEE计算方法
OEE = 实际产量 / 理论产量 × 100%
其中,实际产量是指设备在一定时间内实际生产的合格产品数量,理论产 量则是设备在理想状态下能够生产的最大合格产品数量。
通过比较实际产量和理论产量,可以评估设备的性能表现,并找出设备性 能不佳的原因。
提高设备效率
设备综合效率(OEE)
01
通过监测设备的运行状态和性能,分析设备效率低下的原因,
采取措施提高设备的运行效率。
平均故障间隔时间(MTBF)
02
通过预测设备故障周期,合理安排维护和检修计划,延长设备
使用寿命,提高设备可靠性。
平均修复时间(MTTR)
03
优化设备维修流程,提高维修人员技能水平,缩短设备故障后
03 MTTR定义及计算方法
MTBF指标和计算方法
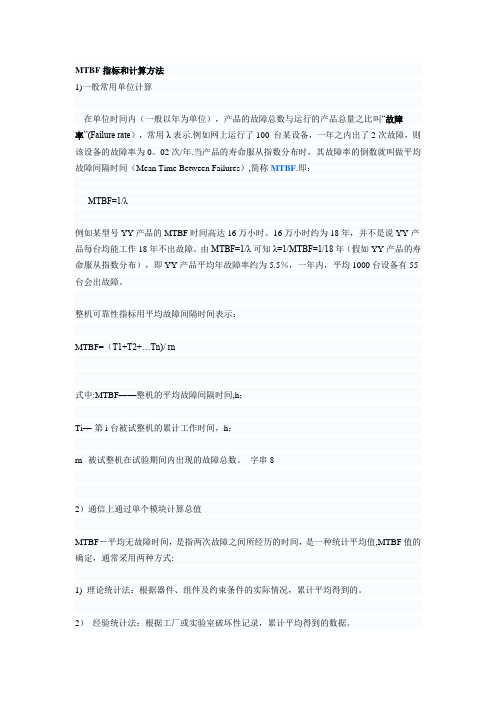
MTBF指标和计算方法1)一般常用单位计算在单位时间内(一般以年为单位),产品的故障总数与运行的产品总量之比叫“故障率”(Failure rate),常用λ表示.例如网上运行了100 台某设备,一年之内出了2次故障,则该设备的故障率为0。
02次/年.当产品的寿命服从指数分布时,其故障率的倒数就叫做平均故障间隔时间(Mean Time Between Failures),简称MTBF.即:MTBF=1/λ例如某型号YY产品的MTBF时间高达16万小时。
16万小时约为18年,并不是说YY产品每台均能工作18年不出故障。
由MTBF=1/λ可知λ=1/MTBF=1/18年(假如YY产品的寿命服从指数分布),即YY产品平均年故障率约为5.5%,一年内,平均1000台设备有55台会出故障。
整机可靠性指标用平均故障间隔时间表示:MTBF=(T1+T2+…Tn)/ rn式中:MTBF——整机的平均故障间隔时间,h;Ti—-第i台被试整机的累计工作时间,h;rn--被试整机在试验期间内出现的故障总数。
字串82)通信上通过单个模块计算总值MTBF-平均无故障时间,是指两次故障之间所经历的时间,是一种统计平均值,MTBF值的确定,通常采用两种方式:1) 理论统计法:根据器件、组件及约束条件的实际情况,累计平均得到的。
2)经验统计法:根据工厂或实验室破坏性记录,累计平均得到的数据。
1+0单机系统MTBF统计值根据1+0单机系统的组成框图,总的MTBF统计值由以下公式给出:1/MTBF总=1/MTBF发高频+1/MTBF收高频+1/MTBF调制+1/MTBF基带+1/MTBF 电源3)通信网络中串并联部件所导致的MTBF不同λ=1/MTBF (h)如果两个部件串联工作,其中一个发生失效,整个功能就失效了,串联结构的:λ总=λ1+λ2或MTBF总=1/(λ1+λ2)对于并联或冗余的结构,虽然一个部件失效,但仍然维持功能的完整性(100%);1/λ总=(1/λ1)+(1/λ2)+(1/(λ1+λ2))或MTBF总=(λ21 + λ1λ2 +λ22)/(λ21λ2 +λ1λ22)字串44)一般产品的MTBF计算平均失效(故障)前时间(MTTF)设N0个不可修复的产品在同样条件下进行试验,测得其全部失效时间为T1,T2,……TN0.其平均失效前时间(MTTF)为:MTTF = (T1+T2+…Tn)/N0由于对不可修复的产品,失效时间即是产品的寿命,故MTTF也即为平均寿命。
生产综合效率指标计算基准

生产综合效率指标计算基准在现代企业管理中,生产综合效率是一个重要的指标,用于衡量企业在生产过程中所创造的价值和资源利用的效率。
本文将介绍生产综合效率指标的计算基准,以及在实际应用中的意义和影响。
一、生产综合效率的定义生产综合效率是指企业在生产过程中所实现的成本、时间、质量等方面的综合表现。
它可以通过以下指标来衡量:单位产出成本、生产周期、产品质量、资源利用率等。
生产综合效率越高,说明企业在资源利用和生产管理方面取得了良好的结果,能够以较低的成本和较高的质量满足市场需求。
二、生产综合效率指标的计算基准计算生产综合效率指标的基准是基于企业所经营的具体行业和市场环境而定。
以下是一般情况下用于计算生产综合效率指标的基本公式:1. 单位产出成本 = 生产成本 / 产量单位产出成本指标可以评估企业生产过程的经济效益,提高该指标有助于减少生产成本,提高企业的盈利能力。
2. 生产周期 = 完成日期 - 开始日期生产周期指标可以衡量企业完成生产任务所需的时间,缩短生产周期对于满足客户需求、提高企业竞争力非常重要。
3. 产品质量 = 合格数量 / 总数量产品质量指标是衡量产品合格率的指标,合格率高意味着产品质量稳定可靠,有助于提升客户满意度和企业声誉。
4. 资源利用率 = 实际产量 / 理论产量资源利用率指标可以评估企业在生产过程中是否充分利用了设备、材料等资源,提高资源利用率有助于减少资源浪费,提高生产效率。
三、生产综合效率指标的意义和影响生产综合效率指标的提高对企业的意义和影响非常重大。
以下是几个方面的具体示例:1. 成本控制:通过降低单位产出成本,企业可以实现成本的控制和降低,从而提高盈利能力。
2. 速度和效率:缩短生产周期可以提高企业的响应速度和生产效率,加强企业对市场变化的适应能力。
3. 品质保证:通过提高产品质量,企业可以获得客户的信任和认可,提升市场竞争力。
4. 资源利用:提高资源利用率可以减少资源浪费,降低企业对环境的影响,增加可持续发展的机会。
OEE﹑MTBF﹑MTTR定定义及计算方法
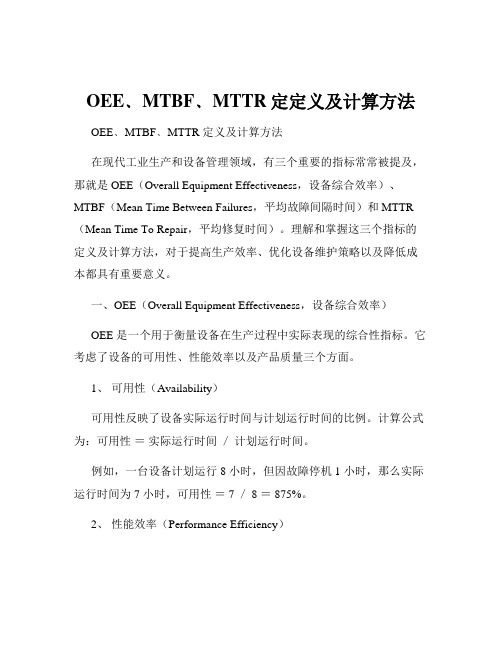
OEE﹑MTBF﹑MTTR定定义及计算方法OEE﹑MTBF﹑MTTR 定义及计算方法在现代工业生产和设备管理领域,有三个重要的指标常常被提及,那就是 OEE(Overall Equipment Effectiveness,设备综合效率)、MTBF(Mean Time Between Failures,平均故障间隔时间)和 MTTR (Mean Time To Repair,平均修复时间)。
理解和掌握这三个指标的定义及计算方法,对于提高生产效率、优化设备维护策略以及降低成本都具有重要意义。
一、OEE(Overall Equipment Effectiveness,设备综合效率)OEE 是一个用于衡量设备在生产过程中实际表现的综合性指标。
它考虑了设备的可用性、性能效率以及产品质量三个方面。
1、可用性(Availability)可用性反映了设备实际运行时间与计划运行时间的比例。
计算公式为:可用性=实际运行时间/计划运行时间。
例如,一台设备计划运行 8 小时,但因故障停机 1 小时,那么实际运行时间为 7 小时,可用性= 7 / 8 = 875%。
2、性能效率(Performance Efficiency)性能效率衡量的是设备在运行过程中,实际产出与理论最大产出的比例。
计算公式为:性能效率=实际产量 ×理论生产节拍/实际运行时间。
假设设备理论生产节拍为每分钟 10 个产品,实际运行 7 小时(420 分钟),实际生产 3500 个产品,那么性能效率= 3500 × 10 / 420 =833%。
3、质量合格率(Quality Rate)质量合格率指的是合格产品数量与总生产数量的比例。
计算公式为:质量合格率=合格产品数量/总生产数量。
如果总生产数量为 4000 个,其中合格产品数量为 3800 个,质量合格率= 3800 / 4000 = 95%。
OEE 的计算公式为:OEE =可用性 ×性能效率 ×质量合格率以上面的例子为例,OEE =875% × 833% × 95% ≈ 694%通过计算 OEE,我们可以清晰地了解设备在生产过程中的效率损失情况,从而有针对性地采取措施进行改进。
生产综合效率及MTBF指标计算基准
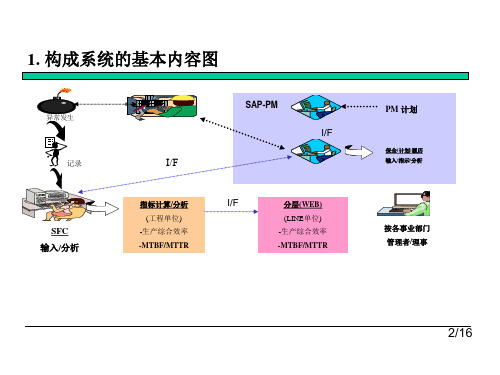
日 MTBF现况
月 工程MTBF现况
*兰色:目前是从WEB提供,以后使用ESFC时 需附加的事项
3/16
3. 指标计算基准
3-1 生产综合效率:与CAPA对比,生产的良品比率.
工作时间 负荷时间 稼动时间 性能稼动时间
计划 停止 性能
价值稼动时间
不良
负荷率
时间稼动率 性能稼动率
良品率
-单位工程:相关工程良品数/相关工程CAPA -以LINE单位:外装良品数/BM生产CAPA *生产综合效率=负荷率X时间稼动率X性能稼动时间X良品率
4/16
指标计算基准
3-1-2.LOSS的分类
大分类
中分类
计划LOSS 交班时间/就餐/休息/生产中断/计划保全
停止LOSS 设备故障/动力事故/JOB CHANGE/流量不足 流量调节/资材短缺/品质问题
性能LOSS 大分类瞬间停止/速度降低/空转
不良LOSS 不良/再作业
对中分类的小分类是各事业Team内部的现象, 具体内容参考后面说明的定义
1. 构成系统的基本内容图
异常发生
记录
SFC 输入/分析
I/F
指标计算/分析 (工程单位)
-生产综合效率 -MTBF/MTTR
SAP-PM
I/F
I/F
分层(WEB)
(LINE单位)
-生产综合效率
-MTBF/MTTR
PM 计划
保全(计划)履历 输入/指示/分析
按各事业部门 管理者/理事
2/16
2. 主要构成内容
7/12
指标计算基准
3-3.有关指标计算参考资料(用语及)计算公式
3-3-1.交率用语及计算公式
OEE﹑MTBF﹑MTTR定定义及计算方法
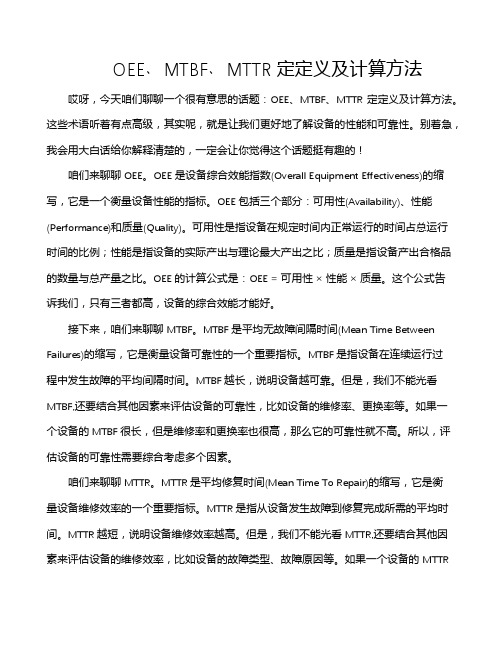
OEE﹑MTBF﹑MTTR定定义及计算方法哎呀,今天咱们聊聊一个很有意思的话题:OEE、MTBF、MTTR定定义及计算方法。
这些术语听着有点高级,其实呢,就是让我们更好地了解设备的性能和可靠性。
别着急,我会用大白话给你解释清楚的,一定会让你觉得这个话题挺有趣的!咱们来聊聊OEE。
OEE是设备综合效能指数(Overall Equipment Effectiveness)的缩写,它是一个衡量设备性能的指标。
OEE包括三个部分:可用性(Availability)、性能(Performance)和质量(Quality)。
可用性是指设备在规定时间内正常运行的时间占总运行时间的比例;性能是指设备的实际产出与理论最大产出之比;质量是指设备产出合格品的数量与总产量之比。
OEE的计算公式是:OEE = 可用性× 性能× 质量。
这个公式告诉我们,只有三者都高,设备的综合效能才能好。
接下来,咱们来聊聊MTBF。
MTBF是平均无故障间隔时间(Mean Time Between Failures)的缩写,它是衡量设备可靠性的一个重要指标。
MTBF是指设备在连续运行过程中发生故障的平均间隔时间。
MTBF越长,说明设备越可靠。
但是,我们不能光看MTBF,还要结合其他因素来评估设备的可靠性,比如设备的维修率、更换率等。
如果一个设备的MTBF很长,但是维修率和更换率也很高,那么它的可靠性就不高。
所以,评估设备的可靠性需要综合考虑多个因素。
咱们来聊聊MTTR。
MTTR是平均修复时间(Mean Time To Repair)的缩写,它是衡量设备维修效率的一个重要指标。
MTTR是指从设备发生故障到修复完成所需的平均时间。
MTTR越短,说明设备维修效率越高。
但是,我们不能光看MTTR,还要结合其他因素来评估设备的维修效率,比如设备的故障类型、故障原因等。
如果一个设备的MTTR很短,但是故障类型和故障原因很多,那么它的维修效率就不高。
OEE,MTBF,MTTR
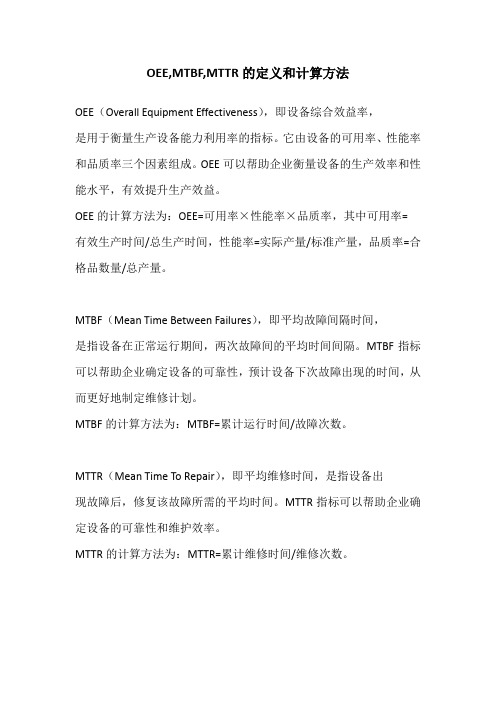
OEE,MTBF,MTTR的定义和计算方法
OEE(Overall Equipment Effectiveness),即设备综合效益率,
是用于衡量生产设备能力利用率的指标。
它由设备的可用率、性能率和品质率三个因素组成。
OEE可以帮助企业衡量设备的生产效率和性能水平,有效提升生产效益。
OEE的计算方法为:OEE=可用率×性能率×品质率,其中可用率=
有效生产时间/总生产时间,性能率=实际产量/标准产量,品质率=合格品数量/总产量。
MTBF(Mean Time Between Failures),即平均故障间隔时间,
是指设备在正常运行期间,两次故障间的平均时间间隔。
MTBF指标可以帮助企业确定设备的可靠性,预计设备下次故障出现的时间,从而更好地制定维修计划。
MTBF的计算方法为:MTBF=累计运行时间/故障次数。
MTTR(Mean Time To Repair),即平均维修时间,是指设备出
现故障后,修复该故障所需的平均时间。
MTTR指标可以帮助企业确定设备的可靠性和维护效率。
MTTR的计算方法为:MTTR=累计维修时间/维修次数。
OEE﹑MTBF﹑MTTR定定义及计算方法
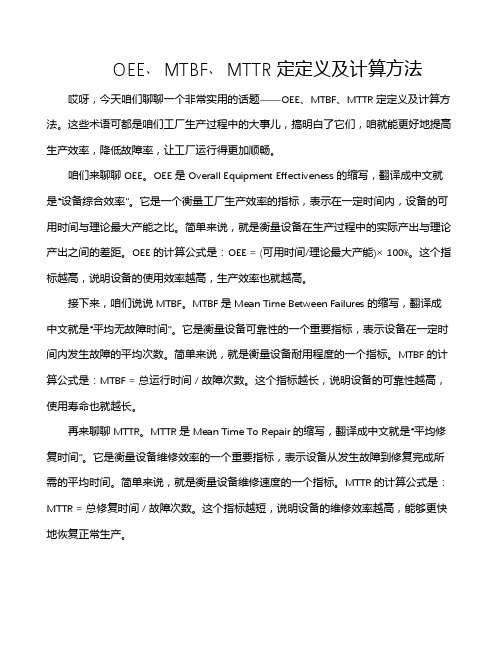
OEE﹑MTBF﹑MTTR定定义及计算方法哎呀,今天咱们聊聊一个非常实用的话题——OEE、MTBF、MTTR定定义及计算方法。
这些术语可都是咱们工厂生产过程中的大事儿,搞明白了它们,咱就能更好地提高生产效率,降低故障率,让工厂运行得更加顺畅。
咱们来聊聊OEE。
OEE是Overall Equipment Effectiveness的缩写,翻译成中文就是“设备综合效率”。
它是一个衡量工厂生产效率的指标,表示在一定时间内,设备的可用时间与理论最大产能之比。
简单来说,就是衡量设备在生产过程中的实际产出与理论产出之间的差距。
OEE的计算公式是:OEE = (可用时间/理论最大产能)× 100%。
这个指标越高,说明设备的使用效率越高,生产效率也就越高。
接下来,咱们说说MTBF。
MTBF是Mean Time Between Failures的缩写,翻译成中文就是“平均无故障时间”。
它是衡量设备可靠性的一个重要指标,表示设备在一定时间内发生故障的平均次数。
简单来说,就是衡量设备耐用程度的一个指标。
MTBF的计算公式是:MTBF = 总运行时间 / 故障次数。
这个指标越长,说明设备的可靠性越高,使用寿命也就越长。
再来聊聊MTTR。
MTTR是Mean Time To Repair的缩写,翻译成中文就是“平均修复时间”。
它是衡量设备维修效率的一个重要指标,表示设备从发生故障到修复完成所需的平均时间。
简单来说,就是衡量设备维修速度的一个指标。
MTTR的计算公式是:MTTR = 总修复时间 / 故障次数。
这个指标越短,说明设备的维修效率越高,能够更快地恢复正常生产。
那么,如何才能提高这三个指标呢?其实,从某种程度上说,这三个指标是相互关联的。
提高OEE,就需要减少故障次数;提高MTBF,就需要减少维修时间;提高MTTR,就需要减少总修复时间。
所以,咱们可以从以下几个方面入手:1. 提高设备的使用效率:这需要咱们合理安排生产计划,避免过度生产导致设备过载;还要定期对设备进行维护保养,确保设备的正常运行。
生产综合效率及MTBF指标计算资料

(工作时间—计划LOSS时间) (3)稼动时间:负荷时间减去停止时间
(负荷时间—停止时间) (4)性能稼动时间:稼动时间—性能LOSS时间
(稼动时间减去性能LOSS时间OR(作业数 X 理论INDEX)) (5)实际稼动时间:在稼动时间中实际为生产消耗的时间
5/16
指标计算基准 3-1-3.用语定义
计划LOSS:是工作时间中公司认定的流失, 停止设备时间或发生LOSS时间
停止LOSS:被负荷时间中的故障,J/CHANGE设备停止的时间 性能LOSS:稼动时间是被速度降低,瞬间停止,空车运转等
发生的时间 不良LOSS:性能稼动时间中造成不良发生的LOSS时间
10/12
指标计算基准
3-3-4.LOSS用语定义
[计划LOSS] (1)接班时间:交班之间为了交班发生的设备不运转时间 (2)就餐/休息:工作中为了就餐/休息发生的设备不运转时间 (3)生产中断:计划的工作时间中根据发生的紧急情况计划性
地中断生产的时间。 (4)计划保全:工作之中为了设备预防保全停止设备的时间 (5)PIOLT:工作之中开发及品质关系实施的设备运转时间,
4/16
指标计算基准ຫໍສະໝຸດ 3-1-2.LOSS的分类
大分类
中分类
计划LOSS 交班时间/就餐/休息/生产中断/计划保全
停止LOSS 设备故障/动力事故/JOB CHANGE/流量不足 流量调节/资材短缺/品质问题
性能LOSS 大分类瞬间停止/速度降低/空转
不良LOSS 不良/再作业
对中分类的小分类是各事业Team内部的现象, 具体内容参考后面说明的定义
生产综合效率指标计算基准
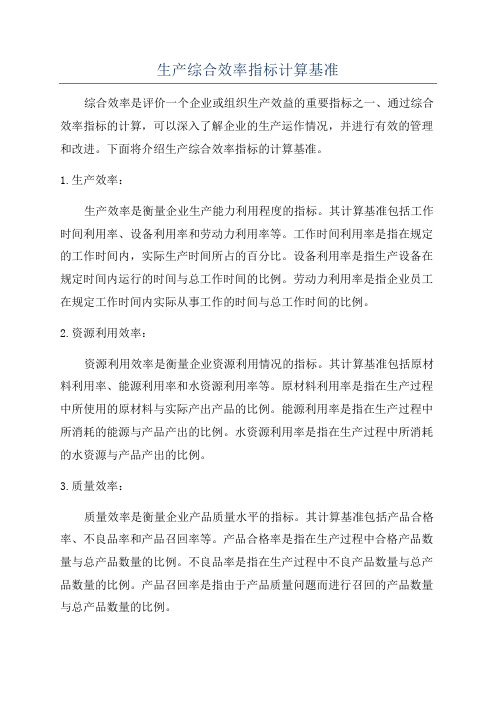
生产综合效率指标计算基准综合效率是评价一个企业或组织生产效益的重要指标之一、通过综合效率指标的计算,可以深入了解企业的生产运作情况,并进行有效的管理和改进。
下面将介绍生产综合效率指标的计算基准。
1.生产效率:生产效率是衡量企业生产能力利用程度的指标。
其计算基准包括工作时间利用率、设备利用率和劳动力利用率等。
工作时间利用率是指在规定的工作时间内,实际生产时间所占的百分比。
设备利用率是指生产设备在规定时间内运行的时间与总工作时间的比例。
劳动力利用率是指企业员工在规定工作时间内实际从事工作的时间与总工作时间的比例。
2.资源利用效率:资源利用效率是衡量企业资源利用情况的指标。
其计算基准包括原材料利用率、能源利用率和水资源利用率等。
原材料利用率是指在生产过程中所使用的原材料与实际产出产品的比例。
能源利用率是指在生产过程中所消耗的能源与产品产出的比例。
水资源利用率是指在生产过程中所消耗的水资源与产品产出的比例。
3.质量效率:质量效率是衡量企业产品质量水平的指标。
其计算基准包括产品合格率、不良品率和产品召回率等。
产品合格率是指在生产过程中合格产品数量与总产品数量的比例。
不良品率是指在生产过程中不良产品数量与总产品数量的比例。
产品召回率是指由于产品质量问题而进行召回的产品数量与总产品数量的比例。
4.成本效率:成本效率是衡量企业生产成本控制水平的指标。
其计算基准包括人工成本占比、能源成本占比和原材料成本占比等。
人工成本占比是指企业在生产过程中的人工成本与总成本的比例。
能源成本占比是指企业在生产过程中的能源成本与总成本的比例。
原材料成本占比是指企业在生产过程中的原材料成本与总成本的比例。
综合效率指标的计算基准可以根据企业的具体情况进行调整和衡量。
一般来说,高效率的企业在生产过程中能够更好地利用时间、资源和成本,提高产品质量,降低生产成本。
因此,通过对综合效率指标的计算和分析,企业可以得出一系列改进措施,提高生产效率和质量,降低生产成本,从而提升企业的竞争力和盈利能力。
MTBF指标和计算方法

MTBF指标和计算方法1)一般常用单位计算在单位时间内(一般以年为单位),产品的故障总数与运行的产品总量之比叫“故障率”(Failure rate),常用λ表示。
例如网上运行了100 台某设备,一年之内出了2次故障,则该设备的故障率为0.02次/年.当产品的寿命服从指数分布时,其故障率的倒数就叫做平均故障间隔时间(Mean Time Between Failures),简称MTBF。
即:MTBF=1/λ例如某型号YY产品的MTBF时间高达16万小时。
16万小时约为18年,并不是说YY产品每台均能工作18年不出故障。
由MTBF=1/λ可知λ=1/MTBF=1/18年(假如YY产品的寿命服从指数分布),即YY产品平均年故障率约为5.5%,一年内,平均1000台设备有55台会出故障。
整机可靠性指标用平均故障间隔时间表示:MTBF=(T1+T2+…Tn)/ rn式中:MTBF—-整机的平均故障间隔时间,h;Ti—-第i台被试整机的累计工作时间,h;rn--被试整机在试验期间内出现的故障总数。
字串82)通信上通过单个模块计算总值MTBF-平均无故障时间,是指两次故障之间所经历的时间,是一种统计平均值,MTBF值的确定,通常采用两种方式:1) 理论统计法:根据器件、组件及约束条件的实际情况,累计平均得到的.2) 经验统计法:根据工厂或实验室破坏性记录,累计平均得到的数据。
1+0单机系统MTBF统计值根据1+0单机系统的组成框图,总的MTBF统计值由以下公式给出:1/MTBF总=1/MTBF发高频+1/MTBF收高频+1/MTBF调制+1/MTBF基带+1/MTBF 电源3)通信网络中串并联部件所导致的MTBF不同λ=1/MTBF (h)如果两个部件串联工作,其中一个发生失效,整个功能就失效了,串联结构的:λ总=λ1+λ2或MTBF总=1/(λ1+λ2)对于并联或冗余的结构,虽然一个部件失效,但仍然维持功能的完整性(100%);1/λ总=(1/λ1)+(1/λ2)+(1/(λ1+λ2))或MTBF总=(λ21 + λ1λ2 +λ22)/(λ21λ2 +λ1λ22)字串44)一般产品的MTBF计算平均失效(故障)前时间(MTTF)设N0个不可修复的产品在同样条件下进行试验,测得其全部失效时间为T1,T2,……TN0.其平均失效前时间(MTTF)为:MTTF = (T1+T2+…Tn)/N0由于对不可修复的产品,失效时间即是产品的寿命,故MTTF也即为平均寿命.当产品的寿命服从指数分布时,MTTF=1/λ平均故障间隔时间(MTBF)一个可修复产品在使用过程中发生了N0次故障,每次故障修复后又重新投入使用,测得其每次工作持续时间为T1,T2,……TN0,其平均故障间隔时间MTBF为:MTBF=T/N0其中,T为产品总的工作时间.对于完全修复的产品,因修复后的状态与新产品一样,一个产品发生了N0次故障相当于N0个新产品工作到首次故障。
- 1、下载文档前请自行甄别文档内容的完整性,平台不提供额外的编辑、内容补充、找答案等附加服务。
- 2、"仅部分预览"的文档,不可在线预览部分如存在完整性等问题,可反馈申请退款(可完整预览的文档不适用该条件!)。
- 3、如文档侵犯您的权益,请联系客服反馈,我们会尽快为您处理(人工客服工作时间:9:00-18:30)。
4/16
中国工业工程管理咨询网收集整理
指标计算基准
3-1-2.LOSS的分类
大分类
中分类
计划LOSS 交班时间/就餐/休息/生产中断/计划保全
停止LOSS 设备故障/动力事故/JOB CHANGE/流量不足 流量调节/资材短缺/品质问题
性能LOSS 大分类瞬间停止/速度降低/空转
3/16
中国工业工程管理咨询网收集整理
3. 指标计算基准
3-1 生产综合效率:与CAPA对比,生产的良品比率.
工作时间 负荷时间 稼动时间 性能稼动时间 价值稼动时间
计划 停止 性能 不良
负荷率
时间稼动率 性能稼动率
良品率
-单位工程:相关工程良品数/相关工程CAPA -以LINE单位:外装良品数/BM生产CAPA *生产综合效率=负荷率X时间稼动率X性能稼动时间X良品率
指标计算基准
3-3-2.时间用语及计算公式 (1)工作时间:正常出勤日出勤时间 (2)负荷时间:工作时间减去计划LOSS时间
(工作时间—计划LOSS时间) (3)稼动时间:负荷时间减去停止时间
(负荷时间—停止时间) (4)性能稼动时间:稼动时间—性能LOSS时间
(稼动时间减去性能LOSS时间OR(作业数 X 理论INDEX)) (5)实际稼动时间:在稼动时间中实际为生产消耗的时间
中国工业工程管理咨询网收集整理
生产综合效率及MTBF指标计算基准 (SFC内部“设备信息”MODULE)
中国工业工程管理咨询网收集整理
1. 构成系统的基本内容图
异常发生 记录
SFC 输入/分析
I/F
指标计算/分析 (工程单位)
-生产综合效率 -MTBF/MTTR
7/12
中国工业工程管理咨询网收集整理
指标计算基准
3-3.有关指标计算参考资料(用语及)计算公式
3-3-1.交率用语及计算公式
(1)生产综合效率:工作时间中为产出良品消耗的时间比率 (价值运转时间÷工作时间)×100 OR(负荷率×时间运转率×性能运转率×良品率)
(2)负荷率:工作时间中运转设备的时间比率 (负荷时间÷工作时间)×100
(作业数X实际INDEX) (6)价值稼动时间:在性能稼动时间中为生产良品消耗的时间
(良品数 X 理论INDEX) (7)理论INDEX:表示制作设备时的SPEC CYCLE TIME,也可作为目标TIME (8)实际INDEX:在现有制造现场/设备状态/产品特性上,可稼动的终C/TIME.
9/12
MTBF
稼动日报
L
事业场/LINE (S/C)
I
N
各LINE 详细内容
E
单
位
事业场/LINE 日推移
事业场/LINE 月推移
输入非稼动LOSS
基准情报
全工程MTBF现况
工
程
各工程LINE别 MTBF现况
单
位 日 MTBF现况
月 工程MTBF现况
*兰色:目前是从WEB提供,以后使用ESFC时 需附加的事项
发生的时间 f不良LOSS:性能稼动时间中造成不良发生的LOSS时间
6/16
中国工业工程管理咨询网收集整理
指标计算基准
3-2.MTBF(Mean Time Between Failures):平均停止间隔时间(或称为平均 无故障工作时间)
-单位工程:相关工程(实)运转时间/相关工程停止件数 -Line单位(SCREEN) :BM工程(实)运转时间/SCREEN工程停止件数合计
事业场/LINE 每日推移 事业场/LINE 每月推移
工程单位
综合情报现况
全工程设备综合效率现况
各工程LINE别 LOSS现况(率)
各工程LINE别 LOSS现况(数量)
各工程LINE别 日推移 各工程LINE别 月推移
LOSS详细现况 LOSS详细内容
WORST-10设备(件数) WORST-10设备(时间)
10/12
中国工业工程管理咨询网收集整理
指标计算基准
3-3-4.LOSS用语定义
[计划LOSS] (1)接班时间:交班之间为了交班发生的设备不运转时间 (2)就餐/休息:工作中为了就餐/休息发生的设备不运转时间 (3)生产中断:计划的工作时间中根据发生的紧急情况计划性
地中断生产的时间。 (4)计划保全:工作之中为了设备预防保全停止设备的时间 (5)PIOLT:工作之中开发及品质关系实施的设备运转时间,
不良LOSS 不良/再作业
对中分类的小分类是各事业Team内部的现象, 具体内容参考后面说明的定义
5/16
中国工业工程管理咨询网收集整理
指标计算基准 3-1-3.用语定义
c计划LOSS:是工作时间中公司认定的流失, 停止设备时间或发生LOSS时间
d停止LOSS:被负荷时间中的故障,J/CHANGE设备停止的时间 e性能LOSS:稼动时间是被速度降低,瞬间停止,空车运转等
11/12
中国工业工程管理咨询网收集整理
指标计算基准
(4)物流不足:被前工程的问题生产中断或生产损失的数量 (5)物流调节:被后工程问题生产中断或LOSS数量 (6)资材品质:被使用资材的短缺生产中断的时间 (7)品质问题:被品质问题停止设备时间或LOSS数量 [性能LOSS] (1)降低速度:比理论INDEX慢发生的LOSS (2)瞬间停止:不是意图性的停止或空转是被设备、人、资材、 作业方法暂时的停止状态,并且没有保全部门的协助自己能改善 的水准的设备停止 *瞬间停止每1件反映为30秒,可以计算停止时间时计算实际停止时间 (3)空转:以被工程上问题或CAPA UNBANCE/物流关系未生产的时间。
从正规MODEL生产中断起始到PIOLT生产完了 后正规MODEL起始点为止的时间 [停止LOSS] (1)设备故障:运转中的设备以停止丧失本来的机能总5分钟以上的停 止,受保全人员的支援采取措施的设备停止时间。 *故障发生时故障LOSS没有发生统计为故障时间 (2)动力事故:被电、Air、Gass、水等问题生产中断的期间 (3)JOB CHANG:是指同一生产线上更换MODEL的情况,从现在生产 中的MODEL完了的起始点上到下次MODEL良品生产起始点为止消耗的时间
SAP-PM
I/F
I/F
分层(WEB)
(LINE单位)
-生产综合效率
-MTBF/MTTR
PM 计划
保全(计划)履历 输入/指示管理咨询网收集整理
2. 主要构成内容
生产综合效率
LINE单位
事业场/LINE 综合效率
各LINE PITCHDIAGRAM
(3)时间运转率:负荷时间中设备不停止运转的比率 (运转时间÷负荷时间)×100
(4)性能运转率:运转时间中设备设计时的性能发挥程度比率 (性能运转时间÷运转时间)×100 (5)良品率:生产的作业数中良品占有率 (良品数÷作业数)×100 OR(价值运转时间÷性能运转时间) ×100
8/12
中国工业工程管理咨询网收集整理
c (实)运转时间=负荷时间-(停止时间+瞬间停止时间+PILOT时间) d停止件数=故障停止件数+瞬间停止件数 [故障停止]5分钟以上丧失规定设备机能停止时 [瞬间停止]被设备、人、资材、作业方法停止时。 [MTBF意义的再规定] 表示设备信赖性的指标,是以设备的故障为基准“平均故障停止间隔时间, 在公司意味着为提高生产设备的信赖性及运转率,以设备停止为基准的 “平均停止间隔时间”
中国工业工程管理咨询网收集整理
指标计算基准
3-3-3 LOSS率计算公式 (1) 计划LOSS率=(LOSS时间÷工作时间)×100% (2) 停止LOSS率=(LOSS时间÷工作时间)×100%
故障停止LOSS率=(故障时间÷工作时间)×100% Job change LOSS率= =(Job change时间÷工作时间)×100% etc (3) 性能LOSS率=(LOSS时间÷工作时间)×100% 瞬间停止LOSS时间=(瞬间停止时间÷工作时间)×100% 空运行LOSS率=(稼动时间-瞬间停止时间-实际稼动时间) ÷工作时间×100% (4)不良LOSS率=【(性能稼动时间-价值稼动时间) ÷工作时间】×100%