焊点的检测
焊接质量检验标准
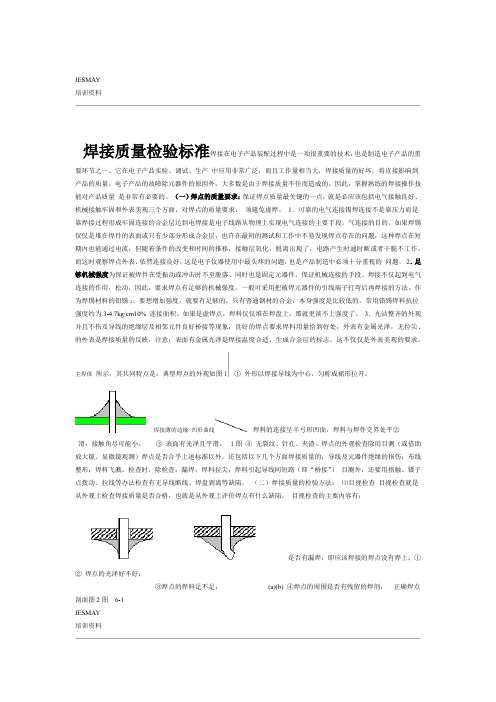
JESMAY培训资料焊接质量检验标准焊接在电子产品装配过程中是一项很重要的技术,也是制造电子产品的重要环节之一。
它在电子产品实验、调试、生产中应用非常广泛,而且工作量相当大,焊接质量的好坏,将直接影响到产品的质量。
电子产品的故障除元器件的原因外,大多数是由于焊接质量不佳而造成的。
因此,掌握熟练的焊接操作技能对产品质量是非常有必要的。
(一)焊点的质量要求:保证焊点质量最关键的一点,就是必应该包括电气接触良好、机械接触牢固和外表美观三个方面,对焊点的质量要求,须避免虚焊。
1.可靠的电气连接锡焊连接不是靠压力而是靠焊接过程形成牢固连接的合金层达到电焊接是电子线路从物理上实现电气连接的主要手段。
气连接的目的。
如果焊锡仅仅是堆在焊件的表面或只有少部分形成合金层,也许在最初的测试和工作中不易发现焊点存在的问题,这种焊点在短期内也能通过电流,但随着条件的改变和时间的推移,接触层氧化,脱离出现了,电路产生时通时断或者干脆不工作,而这时观察焊点外表,依然连接良好,这是电子仪器使用中最头疼的问题,也是产品制造中必须十分重视的问题。
2.足够机械强度为保证被焊件在受振动或冲击时不至脱落、同时也是固定元器件,保证机械连接的手段。
焊接不仅起到电气连接的作用,松动,因此,要求焊点有足够的机械强度。
一般可采用把被焊元器件的引线端子打弯后再焊接的方法。
作为焊锡材料的铅锡2。
要想增加强度,就要有足够的,只有普通钢材的合金,本身强度是比较低的,常用铅锡焊料抗拉强度约为3-4.7kg/cm10% 连接面积。
如果是虚焊点,焊料仅仅堆在焊盘上,那就更谈不上强度了。
3.光洁整齐的外观并且不伤及导线的绝缘层及相邻元件良好桥接等现象,良好的焊点要求焊料用量恰到好处,外表有金属光泽,无拉尖、的外表是焊接质量的反映,注意:表面有金属光泽是焊接温度合适、生成合金层的标志,这不仅仅是外表美观的要求。
主焊体所示,其共同特点是:典型焊点的外观如图1①外形以焊接导线为中心,匀称成裙形拉开。
SMT焊点质量检测方法

SMT焊点质量检测方法热循环为确保电子产品德量稳固性和可靠性,或对失效产品进行剖析诊断,一般需进行必要的焊点质量检测。
SM T中焊点质量检测办法很多,应当依据不同元器件、不同检测项目等选择不同的检测方法。
1 焊点质量检测方式焊点质量常用检测方法有非破坏性、破坏性和环境检测3种,见表1所示。
1.1 目视检测目视检测是最常用的一种非破坏检测方法,可用万能投影仪或10倍放大镜进行检测。
检测速度和精度与检测职员才能有关,评价可依照以下基准进行:⑴润湿状况钎料完整笼罩焊盘及引线的钎焊部位,接触角最好小于20°,通常以小于3 0°为标准,最大不超过60°。
⑵焊点外观钎料流动性好,表面完全且平滑光明,无针孔、砂粒、裂纹、桥连和拉尖等渺小缺点。
⑶钎料量钎焊引线时,钎料轮廓薄且引线轮廓显明可见。
1.2 电气检测电气检测是产品在加载条件下通电,以检测是否满足所请求的规范。
它能有效地查出目视检测所不能发明的微小裂纹和桥连等。
检测时可应用各种电气丈量仪,检测导通不良及在钎焊进程中引起的元器件热破坏。
前者是由渺小裂纹、极细丝的锡蚀和松香粘附等引起,后者是由于过热使元器件失效或助焊剂分解气体引起元器件的腐化和变质等。
1.3 X-ray 检测X-ray检测是应用X射线可穿透物资并在物质中有衰减的特征来发明缺陷,主要检测焊点内部缺陷,如BGA、CSP和FC焊点等。
目前X射线装备的X光束斑一般在1-5μm范畴内,不能用来检测亚微米规模内的焊点微小开裂。
1.4 超声波检测超声波检测利用超声波束能透进金属材料的深处,由一截面进入另一截面时,在界面边沿发生反射的特色来检测焊点的缺陷。
来自焊点表面的超声波进入金属内部,碰到缺陷及焊点底部时就会发生反射现象,将反射波束收集到荧光屏上形成脉冲波形,根据波形的特色来断定缺陷的位置、大小和性质。
超声波检验具有敏锐度高、操作便利、检验速度快、本钱低、对人体无害等长处,但是对缺陷进行定性和定量判定尚存在艰苦。
超声波测焊点的操作流程
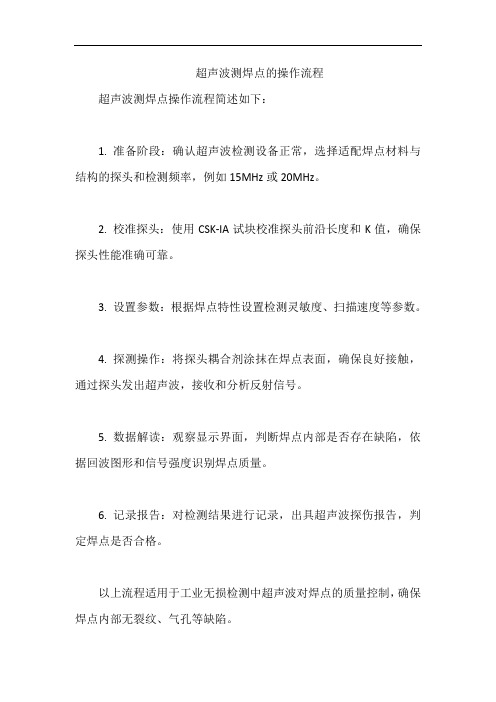
超声波测焊点的操作流程
超声波测焊点操作流程简述如下:
1. 准备阶段:确认超声波检测设备正常,选择适配焊点材料与结构的探头和检测频率,例如15MHz或20MHz。
2. 校准探头:使用CSK-IA试块校准探头前沿长度和K值,确保探头性能准确可靠。
3. 设置参数:根据焊点特性设置检测灵敏度、扫描速度等参数。
4. 探测操作:将探头耦合剂涂抹在焊点表面,确保良好接触,通过探头发出超声波,接收和分析反射信号。
5. 数据解读:观察显示界面,判断焊点内部是否存在缺陷,依据回波图形和信号强度识别焊点质量。
6. 记录报告:对检测结果进行记录,出具超声波探伤报告,判定焊点是否合格。
以上流程适用于工业无损检测中超声波对焊点的质量控制,确保焊点内部无裂纹、气孔等缺陷。
无铅焊点检验规范

机械性能检验标准
总结词
焊点的机械性能应满足一定的强度、韧性和耐久性要求。
详细描述
机械性能检验是评估无铅焊点质量的重要环节,主要测试焊点的抗拉强度、剪切 强度和疲劳寿命等指标。焊点的机械性能应满足产品使用过程中的负载要求,具 有一定的强度、韧性和耐久性,以确保电子产品的可靠性和稳定性。
化学性能检验标准
无铅焊点检验规范
目录
• 无铅焊点概述 • 无铅焊点检验标准 • 无铅焊点检验方法 • 无铅焊点检验流程 • 无铅焊点检验注意事项
01
无铅焊点概述
无铅焊点的定义
01
无铅焊点是指不含有铅元素的焊 点,主要由锡、银、铜等元素组 成,以替代传统的含铅焊点。
02
无铅焊点的出现是为了满足环保 要求,降低电子废弃物对环境的 污染。
结果记录与报告
总结词:完整性
详细描述:检验结果的记录与报告应完整、 准确、及时。结果记录应包括所有检验数据 、异常情况及处理措施等,以便对焊接质量 进行全面评估。报告应根据记录的数据进行 整理和分析,提出改进意见和建议,为后续
焊接工艺的优化提供依据。Βιβλιοθήκη 05无铅焊点检验注意事项
环境控制
温度
保持恒定的温度,避免温度波动对焊点检测的影 响。
仪器校准
1 2
校准周期
定期对检测仪器进行校准,确保其准确性和可靠 性。
校准方法
采用标准的校准方法,确保校准过程的准确性和 可重复性。
3
校准记录
对校准过程进行详细记录,以便后续追踪和审查。
人员培训与资质
培训计划
制定完善的培训计划,提高操作人员的技能和知识水 平。
资质要求
确保操作人员具备相应的资质和证书,符合国家和行 业标准要求。
焊点外观质量检验规范

文件编号WI-QC-QTS-08 版本/版次A/0 第4页,共35页8焊点外观质量检验判定标准8.1 少件--CR8.1.1 漏件8.1.1.1 定义:工艺要求贴装零件的部位SMT工序或DIP工序未进行贴装。
A图B图C图图解:A图与B图对比,B图红色框内漏件,C图上下两幅图对比为D2部位漏件。
B图和C图不允8.1.1.2 影响:影响产品功能。
8.1.1.3 纠正措施:二次补焊。
8.2 撞件8.2.1 定义:原本贴装零件的部位由于取板或放板不规范,撞击后导致零件脱落。
文件编号WI-QC-QTS-08版本/版次 A/0第5页,共35页8.2.2 影响:影响产品功能。
8.2.3 纠正措施:返修。
8.3 错件--CR8.3.1 定义:实际贴装的零件与要求贴装的零件不一致。
8.3.2 影响:影响或潜在影响产品功能。
8.3.3 纠正措施:返修。
图解:A 图与B 图对比,B 图红色框内有贴装过的痕迹,明显为撞击后导致零件脱落。
不允收。
图解:SMT :A 图与B 图对比,B 图红色框内103电阻错贴成101电阻,为错件。
不允收。
DIP :C 图中要求与实际插件不相符,不允收。
要求实际 A 图B 图C 图103103 103101文件编号WI-QC-QTS-08版本/版次 A/0第6页,共35页8.4 极反--CR8.4.1 定义:极性零件未按作业指导书或PCB 板上丝印上的极性要求进行贴装。
8.4.2 影响:烧坏元器件。
8.4.3 纠正措施:返修。
8.5 反背--MA 图解:SMT :A 图与B 图对比,B 图红色框内J106零件极反。
不允收。
C 图实际要求A 图B 图J106+901J+要求实际D 图文件编号WI-QC-QTS-08版本/版次 A/0第7页,共35页8.5.1 定义:贴装时应该向上的面被朝下贴装。
8.5.2 影响:外观或功能不良。
8.5.3 纠正措施:返修。
8.6 立碑--CR8.6.1 定义:应该两个端子均与焊盘连接的零件只有一个端子与焊盘连接,另一个端子呈悬空状态。
焊接虚焊的检测方法

焊接虚焊的检测方法
嘿,你知道焊接虚焊有多让人头疼吗?那可真是个大麻烦!咱先说说检测方法吧。
外观检查就像给焊接点做个“体检”,你瞅瞅那焊点,表面是不是光滑平整呀?要是坑坑洼洼、黑乎乎的,那十有八九有问题。
再用手轻轻掰一掰焊接点,这就好比试试它结实不结实。
如果稍微一动就松了,哎呀妈呀,那肯定是虚焊没跑了。
还有电学检测,就像给电路找“毛病”。
通上电看看电流电压正不正常,要是不对劲,嘿嘿,那可能就是虚焊在捣乱。
检测的时候安全可太重要啦!你想想,电这玩意儿多危险呀。
一定要做好防护措施,戴上手套啥的。
稳定性也不能忽视,要是检测结果一会儿一个样,那可咋整?
那这检测方法都用在啥场景呢?电子设备制造的时候,要是有虚焊,那设备还能好用吗?汽车制造也得注意呀,总不能开着开着车,零件掉了吧?优势嘛,早发现早解决,能避免好多大麻烦呢。
给你说个实际案例,有个电子厂生产手机主板,一开始总出问题,
后来一检测,好多虚焊。
修好之后,手机质量那叫一个棒。
所以呀,焊接虚焊检测方法真的很重要,大家一定要重视起来。
超声波焊点检测原理

超声波焊点检测原理
超声波焊点检测是一种非接触式检测技术,通过超声波的传播和反射来评估焊点的质量。
其原理基于超声波在不同介质(如金属和焊料)中传播速度的差异以及传播过程中遇到的界面反射(或散射)。
首先,超声波传感器将超声波信号发送到待检测的焊点上。
超声波穿过基底材料,并在焊点处发生界面反射。
接收器接收到由焊点产生的反射超声波信号。
接下来,接收器将接收到的信号转化为电信号,并进行放大和滤波处理。
处理后的信号可以显示焊点的声音特征。
根据焊点质量的不同,超声波信号会发生变化。
在良好的焊点中,超声波传播速度较高,界面反射较小。
而在焊点存在缺陷的情况下,超声波传播速度减缓,界面反射增强。
通过对比不同焊点的超声波信号,可以检测和评估焊点的质量。
除了超声波传播速度和界面反射,超声波焊点检测还可以通过分析超声波的幅度、频率、衰减等参数来评估焊点质量。
根据这些参数的变化,可以判断焊点是否存在缺陷,如气孔、裂纹、材料不均匀等。
总的来说,超声波焊点检测利用超声波传播和反射的原理,通过分析超声波信号的特征参数来评估焊点的质量和存在的缺陷。
这种非接触式的检测方法具有高效、快速、准确等优点,在焊接质量控制和产品质量检测中得到广泛应用。
pcb焊点检测算法

pcb焊点检测算法
PCB(Printed Circuit Board)焊点检测算法用于检测电子元器件焊接到PCB上的质量,确保焊接的连接可靠。
以下是一些常见的PCB 焊点检测算法:
视觉检测:使用计算机视觉技术,通过摄像头捕捉PCB 图像,然后利用图像处理算法检测焊点的位置、形状和质量。
这可能包括边缘检测、颜色分析和形状匹配等。
热成像检测:利用红外热成像技术,检测焊点周围的温度差异。
不良的焊接连接可能导致温度异常,从而通过热成像进行检测。
超声波检测:使用超声波技术检测焊点的声学特性。
这种方法可以检测焊接连接的物理性质,如焊点是否牢固。
电气测试:通过在PCB 上施加电流或电压,并测量相应的电阻、电流或电压值,来检测焊点的导通情况。
不良的焊接可能导致电气信号异常。
机器学习算法:利用机器学习技术,通过训练算法使用大量已知好坏焊接的数据,使其能够自动识别新的焊接连接是否良好。
选择适当的检测算法取决于具体的应用场景和要求。
通常,结合多种检测方法可以提高检测的准确性和可靠性。
1。
点焊检测标准

点焊检测标准.pdf范本1:点焊检测标准1. 引言本旨在规范点焊检测的工作流程和要求,确保产品质量和生产效率。
点焊作为重要的焊接工艺之一,对产品的连接质量至关重要。
通过本的指导,希翼能够提高点焊检测的准确性和可靠性,提高产品质量。
2. 术语定义2.1 点焊:将两个金属表面通过施加电流短暂加热至熔点,并施加一定压力使其熔合。
2.2 点焊电流:施加在焊点上的电流的大小。
2.3 点焊时间:施加在焊点上的电流持续的时间。
2.4 点焊电极压力:施加在焊点上的电极的压力。
2.5 焊接接触电阻:焊点所产生的电阻。
3. 点焊检测流程3.1 准备工作3.1.1 验证设备的性能和准确性。
3.1.2 确定检测样本的要求和数量。
3.1.3 准备所需的检测工具和材料。
3.2 点焊检测3.2.1 点焊电流检测3.2.2 点焊时间检测3.2.3 点焊电极压力检测3.2.4 焊接接触电阻检测4. 检测结果判定4.1 根据点焊检测标准进行判定。
4.2 如果检测结果符合标准,认定为合格;如果不符合标准,认定为不合格。
4.3 不合格产品的处理方式。
5. 附件:附件1:点焊检测报告模板附件2:点焊检测记录表6. 法律名词及注释:6.1 点焊:焊接方法的一种,用于将两个金属表面通过施加电流短暂加热至熔点,并施加一定压力使其熔合。
6.2 焊接接触电阻:焊点所产生的电阻。
范本2:点焊质量检验流程一、目的为准确判断点焊接头的质量,制定详细的点焊质量检验流程。
二、适合范围适合于点焊接头的质量检验工作。
三、术语定义3.1 点焊接头:通过点焊工艺连接的两个金属表面。
3.2 点焊电流:施加在焊点上的电流的大小。
3.3 点焊时间:施加在焊点上的电流持续的时间。
3.4 点焊电极压力:施加在焊点上的电极的压力。
3.5 点焊接头外观:点焊接头的外观形态,包括焊缺、焊渣、焊点凸起等。
四、点焊质量检验流程4.1 准备工作4.1.1 验证点焊设备的性能和准确性。
4.1.2 确定检验样本的要求和数量。
电阻焊焊点检测方法及要求

最小板厚/mm 0.60 0.70 0.75 0.80 0.85 0.90 1.00 1.20
最小焊点直径/mm 3.1 3.3 3.5 3.6 3.7 3.8 4.0 4.4
序号 9 10 11 12 13 14 15 16
最小板厚/mm 1.25 1.50 1.75 2.00 2.25 2.50 2.75 3.00
熔核直径≥最小熔核直径,焊核边 缘裂纹<100μm,熔核中心裂纹< 300μm
熔核直径≥最小熔核直径, 300μm≤熔核中心裂纹≤500μm
不合格
熔核直径<最小熔核直径,或熔核 边缘裂纹≥100μm,或熔核中心裂 纹>500μm
注:热影响区、熔核结合线上不允许出现裂纹
气孔评价说明
气孔直径<10%熔核直径,必须保证剥 离实验结果为合格。
最小焊点直径/mm 4.5 4.9 5.3 5.7 6.0 6.3 6.6 6.9
焊点质量要求
熔核尺寸 核直径只能通过测量金相试样来获得。
序号 1 2 3 4 5 6 7 8
最小板厚/mm 0.60 0.70 0.75 0.80 0.85 0.90 1.00 1.20
最小熔核直径/mm 2.7 2.9 3.0 3.1 3.2 3.3 3.5 3.8
电阻焊焊点检测方法及要求
电阻焊焊点常用检验方法 破坏性检验
非破坏性检验
剥离实验 抗剪实验 金相实验 目视检查 凿测实验 超声波检测
常用检验方法说明
目视检查
通过目视检查来初步判别,例如表面裂纹、位置偏差、边缘焊点以及漏焊等
凿测实验
是典型的非破坏性实验,通常用于检查虚焊和熔核过小的焊点,不要求通过这种方法来确定焊点尺寸。 注:凿测实验是将凿子楔入相邻焊点的板材之间(不能对准焊点进行凿测,凿子距离焊点 3~10mm) 剥离实验 是一种典型的破坏性实验,是将焊点从连接板材处分开,通过测量焊点直径大小来评价电阻点焊的质量。 注:对于焊核直径需多次测量,取平均值。 抗剪实验 确定焊点强度是否符合要求,该实验通常使用专用仪器来进行。 注:1、由于取自白车身的试样难以保证合适的装夹尺寸,因此抗剪试样多采用标准试片
焊点的质量及检查

焊点的质量及检查对焊点的质量要求, 应该包括电气接触良好、 机械接触牢固和外表美观三个方面,保证焊点质量最关键的一点,就是必须避免虚焊。
第一节虚焊产生的原因及其危害虚焊是指焊料与被焊物表面没有形成合金结构, 只是简单地依附在被焊金属的表面上,如图 3-1-1 所示。
虚焊主要是由待焊金属表面的氧化物和污垢造成的,它的焊点成为有接触电阻的连接状态, 导致电路工作不正常, 出现时好时坏的不稳定现象,噪声增加而没有规律性,给电路的调试、使用和维护带来重大隐患。
此外,也有一部分虚焊点在电路开始工作的一段较长时间内, 保持接触尚好, 因此不容易发现。
但在温度、 湿度和振动等环境条件推选用下, 接触表面逐步被氧化,接触慢慢地变得不完全起来。
虚焊点的接触电阻会引起局部发热, 局部温度升高又促使不完全接触的焊点情况进一步恶化, 最终甚至使焊点脱落, 电路完全不能正常工作。
这一过程有时可长达一、二年。
据统计数字表明,在电子整机产品故障中,有将近一半是由于焊接不良引起的, 然而,要从一台成千上万个焊点的电子设备里找出引起故障的虚焊点来, a 与引线浸润不良 b 与印制板浸润不良这并不是一件容易的事。
所以,图 3-1-1 虚焊现象虚焊是电路可靠性的一大隐患,必须严格避免。
进行手工焊接操作的时候,尤其要加以注意。
一般来说造成虚焊的主要原因为: 焊锡质量差;助焊剂的还原性不良或用量不够;被焊接处表面未预先清洁好,镀锡不牢;烙铁头的温度过高或过低,表面有氧化层;焊接时间太长或太短,掌握得不好;焊接中焊锡尚未凝固时,焊接元件松动。
第二节对焊点的要求电子产品的组装其主要任务是在印制电路板上对电子元器件进行焊锡, 焊点的个数从几十个到成千上万个, 如果有一个焊点达不到要求, 就要影响整机的质量,因此在焊接时,必须做到以下几点:1.可靠的电气连接焊接是电子线路从物理上实现电气连接的主要手段。
锡焊连接不是靠压力而是靠焊接过程形成牢固连接的合金层达到电气连接的目的。
焊点质量检测的基本要求

焊点质量检测的基本要求
1. 焊点得牢固可靠啊!就像建房子得根基稳一样,你想想看,如果焊点一掰就断,那能行吗?比如说焊接一个架子,要是焊点不牢固,那放东西上去不就散架啦!
2. 外观得规整呀!不能有乱七八糟的瑕疵。
这就好比人的脸,要是满脸麻子坑坑洼洼的,多难看呀!像焊接的电路板上,焊点要是歪七扭八的,多影响美观和性能啊!
3. 尺寸得符合标准呢!不能过大或过小。
就像穿鞋子,尺码不对怎么穿得舒服呢?比如某个零件的焊点,尺寸不合适安装都成问题。
4. 焊接的材料得选对呀!不同的材料有不同的要求。
这就跟做饭选材一样,不能乱搭配呀!如果用错了焊接材料,焊点质量能好吗?
5. 焊接的温度要适宜哟!太高或太低都会出问题。
就像烤面包,温度不合适就烤不好。
比如温度过高可能会损坏焊件,那多糟糕呀!
6. 周围环境也很重要哇!不能有灰尘、杂物干扰。
好比你在干净整洁的房间里心情好,在脏兮兮的地方心情就不好呀!要是焊接环境不干净,焊点质量肯定受影响。
7. 操作人员的技术要过硬啊!可不是随便谁都能来焊接的。
这就像开车,技术不好能安全吗?一个经验丰富的焊工才能保证焊点质量啊!
8. 要进行严格的检测呀!不检测怎么知道焊点好不好呢。
就像考试要打分一样,得知道自己做得怎么样。
对焊点进行仔细检测,才能确保质量过关嘛!
我的观点结论就是:焊点质量检测真的太重要了!每一条要求都不能马虎,只有这样才能保证焊接的质量,让我们用得放心!。
焊点质量检测方法

焊点质量检测方法1.1 目视检测目视检测时最常用的一种非破坏性检测方法,可用万能投影仪或10倍放大镜进行检测。
检测速度和精度与检测人员能力有关,评价可按照以下基准进行:(1)湿润状态钎料完全覆盖焊盘及引线的钎焊部位,接触角最好小于20°,通常以小于30°为标准,最大不超过60°。
(2)焊点外观钎料流动性好,表面完整且平滑光亮,无针孔、砂粒、裂纹、桥连和拉尖等微小缺陷。
(3)钎料量钎焊引线时,钎料轮廓薄且引线轮廓明显可见。
1.2 电气检测电气检测是产品在加载条件下通电,以检测是否满足所要求的规范。
它能有效地查出目视检测所不能发现的微小裂纹和桥连等。
检测时可使用各种电气测量仪,检测导通不良及在钎焊过程中引起的元器件热损坏。
前者是由微小裂纹、极细丝的锡蚀和松香粘附等引起,后者是由于过热使元器件失效或助焊剂分解气体引起元器件的腐蚀和变质等。
1.3 X-ray检测X-ray检测是利用X射线可穿透物质并在物质中有衰减的特性来发现缺陷,主要检测焊点内部缺陷,如BGA、CSP和FC焊点等。
目前X射线设备的X光束斑一般在1-5μm范围内,不能用来检测亚微米范围内的焊点微小开裂。
1.4 超声波检测超声波检测利用超声波束能透入金属材料的深处,由一截面进入另一截面时,在界面边缘发生反射的特点来检测焊点的缺陷。
来自焊点表面的超声波进入金属内部,遇到缺陷及焊点底部时就会发生反射现象,将反射波束收集到荧光屏上形成脉冲波形,根据波形的特点来判断缺陷的位置、大小和性质。
超声波检验具有灵敏度高、操作方便、检验速度快、成本低、对人体无害等优点,但是对缺陷进行定性和定量判定尚存在困难。
扫描超声波显微镜(C-SAM)主要利用高频超声(一般为100 MHz以上)在材料不连续的地方界面上反射产生的位相及振幅变化来成像,是用来检测元器件内部的分层、空洞和裂纹等一种有效方法。
采用微声像技术,通过超声换能器把超声脉冲发射到元件封装中,在表面和底板这一深度范围内,超声反馈回波信号以稍微不同的时间间隔到达转化器,经过处理就得到可视的内部图像,再通过选通回波信号,将成像限制在检测区域,得到缺陷图。
焊点外观检验标准
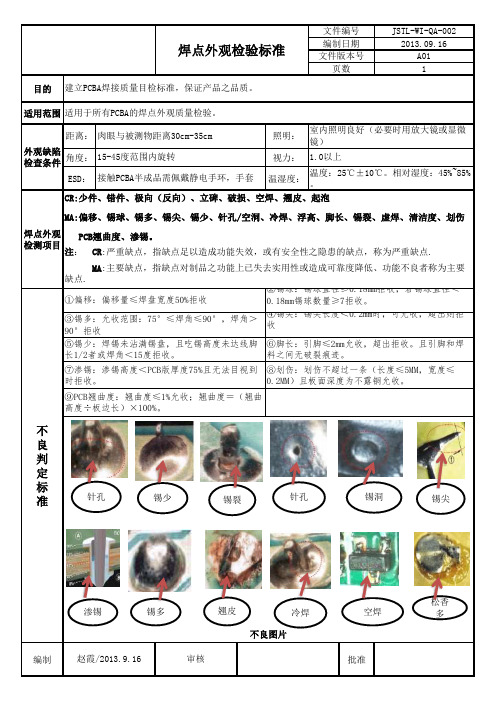
目的适用范围距离:照明:角度:视力:ESD:温湿度:编制批准焊点外观检验标准文件编号JSTL-WI-QA-002编制日期2013.09.16文件版本号A01页数1焊点外观检测项目建立PCBA焊接质量目检标准,保证产品之品质。
适用于所有PCBA的焊点外观质量检验。
外观缺陷检查条件肉眼与被测物距离30cm-35cm室内照明良好(必要时用放大镜或显微镜)15-45度范围内旋转1.0以上接触PCBA半成品需佩戴静电手环,手套温度:25℃±10℃。
相对湿度:45%~85%。
CR:少件、错件、极向(反向)、立碑、破损、空焊、翘皮、起泡MA:偏移、锡球、锡多、锡尖、锡少、针孔/空洞、冷焊、浮高、脚长、锡裂、虚焊、清洁度、划伤PCB翘曲度、渗锡。
注: CR :严重缺点,指缺点足以造成功能失效,或有安全性之隐患的缺点,称为严重缺点.MA :主要缺点,指缺点对制品之功能上已失去实用性或造成可靠度降低、功能不良者称为主要缺点.不良判定标准不良图片⑧划伤:划伤不超过一条(长度≤5MM,宽度≤0.2MM)且板面深度为不露铜允收。
⑨PCB翘曲度:翘曲度≤1%允收;翘曲度=(翘曲高度÷板边长)×100%。
赵霞/2013.9.16审核②锡球:锡球直径≥0.18mm拒收,若锡球直径<0.18mm锡球数量≥7拒收。
①偏移:偏移量≤焊盘宽度50%拒收③锡多:允收范围:75°≤焊角≤90°,焊角>90°拒收④锡尖:锡尖长度<0.2mm时,可允收,超出则拒收⑤锡少:焊锡未沾满锡盘,且吃锡高度未达线脚长1/2者或焊角<15度拒收。
⑥脚长:引脚≤2mm允收,超出拒收。
且引脚和焊料之间无破裂痕迹。
⑦渗锡:渗锡高度<PCB版厚度75%且无法目视到时拒收。
针孔锡少锡裂针孔锡洞锡尖渗锡锡多翘皮冷焊空焊松香多。
焊点检查方法

焊点检查方法1. 目测检查:对焊点进行目测检查,查看焊缝的形状,焊道的宽度和深度,焊缝表面是否平整,是否有气孔、裂纹和其他缺陷。
2. 触摸检查:用手指轻轻触摸焊点,感受其表面的凹凸不平,硬度和坚固程度,以此来初步判断焊接质量。
3. 声音检查:利用敲击焊点的方式,倾听焊点发出的声音,判断焊点的致密度和质量。
4. 温度检查:使用温度计对焊点进行温度检测,以确保焊接工艺是否符合标准要求,是否达到了正确的焊接温度。
5. 金相显微镜检查:采用金相显微镜对焊点进行放大观察,检查其金属组织、晶界和夹杂物等微观结构,以评估焊接质量。
6. X射线检查:利用X射线仪器对焊点进行检测,检查焊缝部位的结晶度、缺陷及杂质等问题。
7. 超声波检查:使用超声波探伤仪对焊点进行检测,通过声波的传播情况来评估焊接质量。
8. 磁粉探伤:对焊点表面喷洒磁粉,利用磁粉探伤设备来检测焊接部位是否存在裂纹、夹杂等缺陷。
9. 磁粉检测:在焊接区域表面喷洒磁粉,利用磁粉检测仪器观察是否有磁粉集聚,从而判断是否有裂纹或其他缺陷。
10. 高倍显微镜检查:利用高倍显微镜设备对焊点进行放大观察,检查焊接区域的细微缺陷和变形情况。
11. 发光检测:利用发光检测仪器对焊点进行检测,观察焊点会否产生辐射和发光现象,以判断焊接质量。
12. 流变学检测:通过流变学的测试方法,对焊点进行拉伸、压缩等力学性能测试,评估焊点的强度和韧性。
13. 电子探针分析:利用电子探针分析仪器,对焊点进行成分分析和元素探测,以评估焊接材料的质量和成分均匀性。
14. 硬度测试:使用硬度计对焊点进行硬度测试,评估焊接区域的硬度分布和焊接质量。
15. 电磁感应检测:利用电磁感应仪器对焊点进行检测,观察焊接区域的磁场分布情况,以判断焊点的致密性和质量。
16. 热处理检测:针对焊点进行热处理测试,检查焊接工艺是否符合热处理要求,以确保焊接质量稳定。
17. 电子束探伤:采用电子束探伤仪器,对焊接区域进行电子束探伤检测,评估焊点的结构完整性和质量。
点焊焊点检验规范
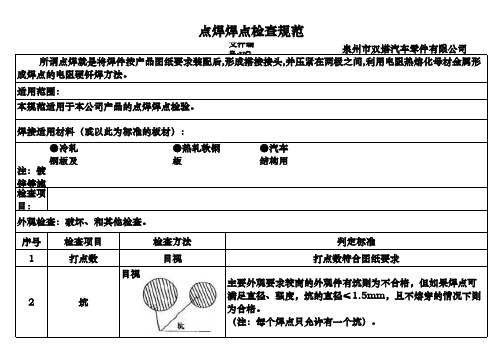
●热轧软钢 板
外观检查:破坏、和其他检查。
●汽车 结构用
序号 1
2
检查项目 打点数
目视
检查方法 目视
坑
判定标准 打点数符合图纸要求
主要外观要求较高的外观件有坑则为不合格,但如果焊点可 满足直径、强度,坑的直径≤1.5mm,且不熔穿的情况下则 为合格。 (注:每个焊点只允许有一个坑)。
目视
3
裂纹
点焊焊点检查规范
焊点表面不能有裂纹。
4 焊接部位的凹坑目视5Fra bibliotek飞溅的附着
目视
目视
6 鼓包、焊点错位
●主要外观要求较高的外观件有凹坑则为不合格; ●非外观件焊接部位的凹坑深度≤产品材料厚度的1/3,且凹 坑表面、边缘无裂纹、断裂纹则为合格。
主要外观要求较高的外观件和产品安装面有飞溅物附着则为 不合格。
●焊点的压痕偏离边缘端的为不合格; ●允许存在的“鼓包”不能超过图纸规定焊点数量的20%。 (注:边缘转角部份不能有“鼓包”)
点焊焊点检查规范
一般焊接部位及关重焊接部位的焊点直径要求要达到图纸要 求的尺寸值。
7
焊点直径
破坏检测
8
剥离强度
用凿子或锤子向着熔着 部的中心用力敲打成品
试样焊点检查应无剥落现象。
点焊焊点检查规范
9
焊接强度
编制:
审核:
批准:
点焊焊点检查规范
文件编 号:YG-
泉州市双塔汽车零件有限公司
所谓点焊就是将焊件按产品图纸要求装配后,形成搭接接头,并压紧在两极之间,利用电阻热熔化母材金属形
成焊点的电阻硬钎焊方法。
适用范围:
本规范适用于本公司产品的点焊焊点检验。
焊接适用材料(或以此为标准的板材):
焊点质量的检查方法

焊点质量的检查方法
1.外观检查法:对焊接的外观进行检查,如焊面是否平整、焊缝是否均匀、焊接是否有气孔、裂纹、夹渣等缺陷。
2.力学性能检测法:通过实验手段检测焊接件的强度、韧性等力学性能是否符合要求。
3.无损检测法:利用无损检测仪器对焊缝的内部进行检测,如X射线、超声波、磁粉、涡流等无损检测方法。
4.化学分析法:对焊接的金属组织进行化学分析,检测其化学成分是否合格。
5.金相检测法:对焊接的金属组织进行金相显微镜观察,检测其显微组织性能是否符合要求。
6.氦检测法:在氦气环境下进行检测,检测焊接焊接点部位泄气情况,检验焊点的气密性。
焊点质量检测方法

焊点质量检测方法1。
1 目视检测目视检测时最常用的一种非破坏性检测方法,可用万能投影仪或10倍放大镜进行检测。
检测速度和精度与检测人员能力有关,评价可按照以下基准进行:(1)湿润状态钎料完全覆盖焊盘及引线的钎焊部位,接触角最好小于20°,通常以小于30°为标准,最大不超过60°。
(2)焊点外观钎料流动性好,表面完整且平滑光亮,无针孔、砂粒、裂纹、桥连和拉尖等微小缺陷。
(3)钎料量钎焊引线时,钎料轮廓薄且引线轮廓明显可见.1.2 电气检测电气检测是产品在加载条件下通电,以检测是否满足所要求的规范。
它能有效地查出目视检测所不能发现的微小裂纹和桥连等.检测时可使用各种电气测量仪,检测导通不良及在钎焊过程中引起的元器件热损坏。
前者是由微小裂纹、极细丝的锡蚀和松香粘附等引起,后者是由于过热使元器件失效或助焊剂分解气体引起元器件的腐蚀和变质等。
1。
3 X-ray检测X-ray检测是利用X射线可穿透物质并在物质中有衰减的特性来发现缺陷,主要检测焊点内部缺陷,如BGA、CSP和FC焊点等。
目前X射线设备的X光束斑一般在1-5μm范围内,不能用来检测亚微米范围内的焊点微小开裂。
1.4 超声波检测超声波检测利用超声波束能透入金属材料的深处,由一截面进入另一截面时,在界面边缘发生反射的特点来检测焊点的缺陷。
来自焊点表面的超声波进入金属内部,遇到缺陷及焊点底部时就会发生反射现象,将反射波束收集到荧光屏上形成脉冲波形,根据波形的特点来判断缺陷的位置、大小和性质。
超声波检验具有灵敏度高、操作方便、检验速度快、成本低、对人体无害等优点,但是对缺陷进行定性和定量判定尚存在困难。
扫描超声波显微镜(C-SAM)主要利用高频超声(一般为100 MHz以上)在材料不连续的地方界面上反射产生的位相及振幅变化来成像,是用来检测元器件内部的分层、空洞和裂纹等一种有效方法。
采用微声像技术,通过超声换能器把超声脉冲发射到元件封装中,在表面和底板这一深度范围内,超声反馈回波信号以稍微不同的时间间隔到达转化器,经过处理就得到可视的内部图像,再通过选通回波信号,将成像限制在检测区域,得到缺陷图。
- 1、下载文档前请自行甄别文档内容的完整性,平台不提供额外的编辑、内容补充、找答案等附加服务。
- 2、"仅部分预览"的文档,不可在线预览部分如存在完整性等问题,可反馈申请退款(可完整预览的文档不适用该条件!)。
- 3、如文档侵犯您的权益,请联系客服反馈,我们会尽快为您处理(人工客服工作时间:9:00-18:30)。
1、 锡焊焊点检测 2、 PCB清洁度检测 3、 再线检测
检测技术在电子设备的制造中具有相当重要的地 位,它是实施质量检验的必要手段,没有先进的检测 技术,质量检验就无法有效的进行。 在电子设备的制造中,与装联工艺直接有关的检 测技术主要有下列几种: 可焊性检测—检查被焊材料的焊接性能,检出可 焊性不良材料; 焊点检测—检查锡焊质量,检出不良焊点;
2. 溶剂萃取法
方法:将基板浸没于测试液(由异丙醇和去
离子水混合而成)中,充分搅拌,使焊剂残渣
全部溶解于测试溶液,然后测量电路板的离
子导电率。 判断标准:参照美国MIL-P-28809标准的规 定:要求NaCI的含量 3.1g/cm2 。 该方法所使用设备的商业名称为欧米伽表 和电离图。这种方法常用来监测通孔插装基 板的清洁度,一般采用抽样检验的方法。
而在线检测仪可以在很短的时间内,以很高 的准确率发现元件安装过程引起的焊接短路、 开路以及元件插装差错、插装方向差错、元件 数值超出误差等。扩展的在线检测仪还可验证 电路的运行功能,因此具有很高的实用性,特 别适用于大规模、多品种产品的生产检测需要。
6. 在线测试仪的种类
在线检测仪有很多种类,各国对设备的分类和命 名各不相同,从应用角度出发,我们根据在线测试 仪的测量对象分为以下几类:
基板清洁度检测—检查清洗质量,防止焊接残留 物影响产品可靠性;
在线检测—检查装联质量,检出装联及元器件缺 陷。
1. 锡焊焊点检查
电子工业的整机装联是离不开锡焊的,锡焊焊
点的质量直接影响着整机的可靠性。 2. 常用检查方法
3. 焊接质量标准和常见故障的判别(P198)
1.焊接质量标准
(1)焊点表面:光滑,色泽柔和,没有砂眼,气
(1)制造缺陷分析仪(简称:MDAS ) 通常有:短路/开路测试仪、阻抗测试仪, 功能: 电路的短路/开路故障及任意两点间 的阻抗异常,有效故障检测范围约35%~65%, 优点:操作快速和价格便宜, 缺点:检测有局限性,并需要双面针床测试 夹具。随着元器件及装联质量的提高,制造缺 陷分析仪已经过时了。 。
用产品和一些要求高可靠性的电路采用高压测试。 因为高压测试不仅能够测出已经存在于光板上的 故障,而且还可以通过高压击穿清涂一些可能会
出现的故障点,诸如:毛刺和板面不洁的缺陷。。
2.PCB(载板)测试仪: (P209)
测试对象:已安装好元器件的组件级的PCB, 整机厂往往将载板称为“基板”,
整机厂应用在插件、焊接工序后,总装工序 前对基板进行自动检测的设备。
主要缺点:编程时间长。
在线检测仪与功能测试仪的比较 在线检测与功能检测仪各有长处和不足。 由于在线检测仪,可直接判断出元器件的故 障,给生产过程的维修带来很大方便,因此在 大批量生产中,在线检测仪受到很多企业的青 睐。
表面安装形式的常见不良焊点(除了与通孔插 装形式相类似的不良现象外,还有一些特殊的故 障现)
11.3 PCB清洁度检测(P202)
对PCB的清洁度检测,是整机厂为监控清洗效 果而采取的检测手段,
电子工业常用的清洁度测试方法有
目测法
溶剂萃取法
表面绝缘电阻法
1. 目测法
方法:将清洗后的基板置于放大倍数为2~10 的光学显微镜下,用肉眼检查焊剂残渣和其他 杂质, 判断标准:是在元器件下或电路板上见不到 焊剂和焊膏。 这是一种最简单的方法,这种方法的主要缺 点是必需将元器件拆卸下来,才能查出藏在大 元件下的焊剂残渣,而且肉眼只能观察出粗大 的污染物。
1.PCB(光板)检测仪 检测对象:PCB制造厂对光板(又称裸板)产品 的自动检测, 功能:主要是通过针床与对PCB的每个电路节点 的电气连通进行测试,验证PCB是否满足给定的连 通要求(开路、短路)。
这种检测仪通常又将其统称为制造缺陷分析仪。
1.方法: 低压通断测试:电压为10V左右,它主要用于 民品; 高压漏电流测试:电压为100~500V。通常军
3.表面绝缘电阻法(SIR) 方法:SMB设计时,在元器件的下方设置测试 清洁度的图形, 通常在片状电阻和电容 下用“Y形”的测试图形, 在PLCC、SOIC等大形 器件下用“梳形”的测试图形。
4. 判断标准:将清洗后的SMA置于规定的测 试条件下,用兆欧表测量图形引出端之间的绝 缘电阻,就可反映元器件下方的清洁程度。
泛应用,使在线测试技术的应用成为可能,并
研制出带有针床方式的“在线测试仪”,成为
生产过程自动检测的主要手段,用以检查基板 的装联质量。
在线测试仪在我国的应用起步比较迟,但其 发展速度却很快,随着SMT产品在我国的发展, 在元器件小型化、安装高密度的今天,传统的 通过功能检测发现故障现象,再由熟练的技术 工人找出故障原因的方法已不能满足批量生产 的需要。
消费品和工业品: 100M;
军用品或高可靠性产品: 500M。
5. 在线检测(简称:ICT)(P207) “在线测试”这个概念是1959年美国的GE公 司为检查生产的印制电路板而提出的,英文名
为
“In Circuit Testing” 是指在线路板上
测试。
80年代中期,随着微机自动控制技术的广
(2)在线检测仪(简称:ICT)
功能:是检查出基板电路的短路/开路、元器 件遗漏、插装差错、插装方向差错、元器件失效、 数值超出误差等故障,它能覆盖约90%的故障率, 并将检查结果通过打印机输出,作为维修的依据。
(3)功能测试仪
功能:检测SMA的运行功能是否正常,并以 功能是否具备而决定基板通过和不通过。 它可分为模拟电路功能检测仪和数字电路功 能检测仪两种。故障检测率在80%~98%之间。
孔、毛剌等缺陷;
(2)焊料轮廓:印制电路板焊盘与引脚间应呈弯
月面,
润湿角 15<θ <45;。
(3)焊点间:无桥接、拉丝等短路现象。
(4)焊料内部:金属没有疏松现象,焊料与焊件接
触界面上形成3μ ~10μ 的金属间化合物。
(5)表面安装良好焊点的特殊要求
2. 不良焊接现象的判别