丰田汽车模具制造技术1(1)
快速成型之FDM 应用及实例

熔融挤出成型(FDM)工艺的材料一般是热塑性材料,如蜡、ABS、PC、尼龙等,以丝状供料。
材料在喷头内被加热熔化。
喷头沿零件截面轮廓和填充轨迹运动,同时将熔化的材料挤出,材料迅速固化,并与周围的材料粘结。
每一个层片都是在上一层上堆积而成,上一层对当前层起到定位和支撑的作用。
随着高度的增加,层片轮廓的面积和形状都会发生变化,当形状发生较大的变化时,上层轮廓就不能给当前层提供充分的定位和支撑作用,这就需要设计一些辅助结构-“支撑”,对后续层提供定位和支撑,以保证成形过程的顺利实现。
快速模具制造(Rapid Tooling,RT)是快速成型技术的重要应用方向。
RT可分为直接法和间接法两种。
快速成型能容易地直接得到立体实物的特点使得一步成型模具的直接法更为现实,基于SLS工艺的RT技术已经可以一步到位地得到所设计的模具。
间接法则利用快速成型系统制造出母模,再用传统方法通过一次或多次翻模来得到最终的模具。
FDM在快速经济制模领域中可用间接法得到注塑模和铸造模。
首先用FDM制造母模,然后浇注硅橡胶、环氧树脂、聚氨酯等材料或低熔点合金材料,固化后取出母模即可得到软性的注塑模或低熔点合金铸模。
这种模具的寿命通常只有数件至数百件。
如果利用母模或这种模具浇注(涂覆)石膏、陶瓷、金属构成硬模具,其寿命可达数千件。
用铸造石蜡为原料,可直接得到用于熔模铸造的母模。
日本丰田公司利用FDM技术在汽车设计制造中获得了巨大收益。
Avalon汽车是丰田公司应用FDM工艺重新设计的第一个项目计划。
由于是首次应用,计划用FDM制造的零件只有35种。
FDM制造出的Avalon原型零件使设计者捕捉到了不少缺陷,例如通过对后视镜原型件的分析,发现如果采用原来的设计,零件与模具将很难分离,于是做了相应的改动,节省了后期更改所需的大量费用。
Avalon汽车的左侧后视镜是用最终使用的材料制成的,用来做振动试验,右侧后视镜则用FDM完成,仅此一项就为丰田公司节省了20万美元。
丰田术语及缩写的注释

SPTT: GA GW JA JW 1W、1A 1A后半 KA 量确 品确 号试 号口 SOP L/O SPO 本型 本工程 W部品 A部品 C/F HVPT 流用品 新规部品 新规供应商 T0品 T1品 生准场所:CC JC JJ 设变 supply global global parts tracking team 零部件供应商跟踪小组 全球试生产的总装 全球试生产的焊装 日本试生产的总装 日本试生产的焊装 assemble welding
量产用的正式模具 量产用的正式工序 Welding Part Assemble Part check fixture 焊接用部品 组装用部品 检具、测量设备 大量生产试作
High volume production try
以前生产过同样的部品,不需要进行新的生产准备 新增加/新设的,需要进行新生准的部品 首次与GTMC有贸易往来的供应商 模具制作完成后,没有经过修整生产出来的产品 经过第一次修整模具后生产出来的产品 中系供应商在中国制造模具 日系供应商在中国制造模具 日系供应商在日本制造模具 设计变更
部分术语/缩写的注释(2 / 2)
英中对照: 1 TMC(Toyota Motor Co.,Ltd):丰田汽车公司。 2 GTMC(GAC, Toyota Motor Co.,Ltd):广汽丰田汽车有限公司。
3 RDDP(Request for Design & Development of Parts):外协零件设计申请单。 4 DPS(Design Planning Sheet):设计计划书。 5 ASA(Application Sheet for Approval):批准申请单。 6 RAD(Receipt of Approval Drawing):承认图出图通知。 7 TS(Toyota Engineering Standards):丰田技术标准。 8 TIS(Technical Instruction Sheet):技术指示书。 9 ECI(Engineering Change Instructions):设变切换依赖书。 10 ECR(Engineering Change Reqபைடு நூலகம்est):设计变更检讨依赖书。 11 SE(Simultaneous Engineering)图:同步工程图。 12 SPRL(Service Parts Routing List):服务零件工序清单。 13 丰田图:丰田设计、制作的图纸。 14 承认图:供应商受丰田委托而制作的用于丰田设计的车辆零件的图纸。 英日对照: 1 TMC(Toyota Motor Co.,Ltd):トヨタ自動車株式会社。 2 GTMC(GAC, Toyota Motor Co.,Ltd):広汽トヨタ自動車有限会社。 3 RDDP (Request for Design & Development of Parts) :外注部品設計申請書。 4 DPS (Design Planning Sheet) :設計計画書。 5 ASA (Application Sheet for Approval) :批准申請書。 6 RAD (Receipt of Approval Drawing) :承認図出図通知。 7 TS (Toyota Standard) :トヨタ技術標準。 8 TIS (Technical Instruction Sheet):技術指示書。 9 ECI (Engineering Change Instructions) :設変切替依頼書。 10 ECR(Engineering Change Request):設変検討依頼書。 11 SE (Simultaneous Engineering) 図:SE図。 12 SPRL (Service Parts Routing List):サービスパーツ手順リスト 13 トヨタ図:トヨタが設計し、作成した図面 14 承認図:仕入先がトヨタに委託され、作成し、トヨタ設計部が承認した部品の図面。
浅谈我国汽车模具业的制造技术及其改进方向

丰田供应链的基本构造

丰田供应链的基本构造众所周知TOYOTA能够以其产品的高品质、低成本、低油耗打进美国等发达国家的市场,而且形成了相当大的竞争优势,主要不在于它采用的生产制造技术,而是由于在生产组织和管理上采取了一系列先进的生产经营理念、管理模式、组织体系、管理技术和方法以及推行了良好的企业文化,被世人称为“丰田生产方式(TPS,TOYOTA Production System)”又被称作“精益生产(LPS)”,还被称为“准时生产制(JIT)”。
仅仅从这些名称上就不难看出,车辆生产管理与零件的采购是其中起到最关键作用的一环。
它是实体工厂生产的前工程,是降低汽车生产成本的捷径。
首先从整体上看,车辆生产与零部件采购的基本状况如图1。
在整体的需求链中,可以分为车辆的需求链与零件的需求链。
从整体着眼的目的是使具体的环节更容易理解,下面开始分块介绍。
车辆需求链——车辆生产计划制定1)从车辆销售到生产计划按需生产、“0”库存丰田的4S店遍布全国,处在这个遍布全国的销售网络的顶端的则是丰田汽车的销售公司(FTXS)。
各4S店每销售或预定一辆车都会将详细的购车信息登记到管理系统中,这些信息通过网络传送到FTXS,FTXS再将全国各地的信息进行汇总、整理、计算,并将与制定生产计划有关的信息传送到生产工厂——丰田对应的现地工厂(简称FTXD)。
这些信息由FTXD中负责生产管理、计划制定、物流采购的生产管理部接受。
生产管理部的生产管理科是负责生产计划制定、新车新推进和通关等工作的部门。
其中的生产计划组使用着与FTXS的管理系统相连接的G-PPS系统。
G-PPS是丰田的全球使用系统。
2)G-PPS的主要机能G-PPS的主要职能有2个,分别是制定生产计划和计算零部件的必要数量。
①制定生产计划G-PPS根据FTXS发来的信息,结合安排生产所必需的“平准化”等条件,制定工厂的月生产计划。
它可以制定出“未来5个月的生产台数”、“未来三个月的细分到等级和颜色的生产计划”、“未来1个月每天的生产计划”。
模具制造技术概述

1 模具与模具工业概述
• 模具是当今工业生产中使用的极其广泛的主要工艺设备,是最重要的 工业生产手段和工艺发展方向。一个国家工业水平的高低爱很大程度 上取决于模具工业的发展水平,模具工业的发展水平是一个国家工业 水平的重要标志之一。鉴于此,模具工业也被称之为“黄金工业”。
• 国民经济的5大支柱产业机械、电子、汽车、石化、建筑,都要求模 具工业的发展与之相适应,模具是“效应放大器”,用模具生产的最 终产品价值,往往是模具自身价值的几十倍、上百倍,模具生产水平 的高低,已经成为衡量一个国家制造业水平高低的重要的标志,也在 很大程度上决定产品的质量、效益和新产品的开发能力。因此,振兴 和发展我国的模具工业,日益受到人们关注和重视。
3.工艺装备水平
模具加工设备与国外相比有很大差距
2.3 我国模具技术的发展趋势
1.模具产品的大型化和精密化
模具产品成型零件的日趋大型化,以及由于高效率生产要求的 一模多腔,使模具日趋大型化。
随着零件微型化和模具模具结构发展的要求(如多工位级进模工 位数的增加,其步距精度的提高),精密模具精度已由原来的5μm提 高到2~3μm,今后有些模具的加工精度公差要求在1μm以下,这就要求 发展超精工加工。
CAD (Computer Aided Design )计算机辅助设计 CAE (Computer Aided Engineering )计算机辅助工程 CAM (Computer Aided Menufacturing )计算机辅助制造
1.冲模(汽车覆盖件)
2.塑料模
3.压铸模
4.快速经济制模技术
(3)仿真技术(检测数控加工NC程序,减少加工失误)
(4)网络技术(实现异地同步通信,及时解决问题)
2.2 我国模具技术与国外的差距
准时化生产方式的技术(JIT)1.doc

准时化生产方式的技术(JIT)1 目录:1.准时化生产方式的技术支撑体系2.集成JIT和MRP3.流程分析与优化重组技术准时化生产方式的技术支撑体系丰田公司的“准时化生产方式(JIT)”技术支撑体系,特别着重分析了构成这一技术支撑体系的每一个技法的特殊作用,以及各个技法间的相互关系,以便使我们更好地理解丰田生产体系,并为实施准时化生产奠定理论基础。
关键词:丰田生产体系、准时化生产1.引言准时化生产方式(Just-in-time,JIT)是日本丰田汽车公司创立的一种独具特色的现代化生产方式。
它顺应时代的发展和市场的变化,经历了20多年的探索和完善,逐渐形成和发展成为今天这样的包括经营理念、生产组织、物流控制、质量管理、成本控制、库存管理、现场管理和现场改善等在内的较为完整的生产管理技术与方法体系。
准时化生产方式诞生在丰田公司,但它并不是仅适用于汽车生产。
事实上,准时化生产方式作为一种彻底追求生产过程合理性、高效性和灵活性的生产管理技术,它已被应用于日本的许多行业和众多企业之中。
同样,它的基本思想、基本原理和基本枝法对我国企业的生产方式和管理方法的现代化具有重要的借鉴意义和参考价值。
实际上,早在80年代初,丰田准时化生产方式就被介绍到了我国。
遗憾的是,当时我们误认为准时化生产方式就是“看板管理(Kanban)”。
我们的一些企业曾简单地模仿传递看板,但并未见到成效,于是就草率地把它否定了。
实践表明,如果没有生产经营观念的彻底转变和管理意识的彻底更新,没有对准时化生产方式进行系统性研究,而仅仅是模仿某个单项技法,准时化生产是不可能实现的。
因此,在借鉴丰田生产方式时,我们首先对其进行系统性的研究是极为重要和必要的。
2.准时化生产方式的真缔日本筑波大学的门田安弘教授曾指出:“丰田生产方式是一个完整的生产技术综合体,而者板管理仅仅是实现准时化生产的工具之一。
把看板管理等同于丰田生产方式是一种非常错误的认识。
”丰田的准时化生产方式通过看板管理,成功地制止了过量生产,实现了“在必要的时刻生产必要数量的必要产品(或零部件)”,从而彻底消除在制品过量的浪费,以及由之衍生出来的种种间接浪费。
模具制造工艺 项目一 认识现代模具制造技术概况

●模具寿命
压注模 塑模
冷冲模 锻模
项目 锌、锡压注模 铝压注模 铜压铸膜 黑色金属压注模 非淬火钢模 淬火钢模 合金钢制模 硬质合金制模 刃磨 普通锻模 精锻模 玻璃模
国外 100-300万次 100万次以上
10万次 0.8-2万次 10-60万次 100-300万次 500-1000万次
2亿次 500-1000万次刃磨1次
调研综述:
文本资源
上一页 下一页
首页
项目一
四、知识、能力测试
本项目学习过程中直到结束,应与配套教材的学习光盘结合, 并进行测试,检验学习效果。
上一页 下一页
首页
认识现代模具制造技术概况
单元1: 模具制造特点及现代制造技术流程
项目一
单元1
模具制造特点及现代制造技术流程
1.模具制造的特点
(1) 单件、多品种生产 (2) 生产周期短 (3) 要求成套性生产 (4) 模具要求高精度和低表面粗糙度。 (5) 要求模具寿命高,以降低制造成本。 (6) 模具制造具有经验性的特点,模具制造装配、调试是非常 重要的,也是影响制造周期的重要因素。
上一页 下一页
首页
模具制造特点与流程
项目导入 项目分析 项目实施 知识、能力测试
项目一
上一页 下一页
首页
1.模具
一、项目导入
项目一
座椅摇臂零件产品 模具设计
模具制造
上一页 下一页
首页
二、项目分析
2.模具制造流程
项目一
模具是一种专用工具, 用于成形( 型) 各种金属或非金属材料所需要零件的形状 制品,这种专用工具统称模具。
(2)现代制模则通过计算机数据模拟和仿真技术来 完善模具结构,返修少,成本低。
汽车模具基本知识讲义(1)

• 翻边模:是将半成品工件的一部分材料相对另一部分材料 产生翻转的制件。
• 整形模:将半成品调整尺寸轮廓以提高尺寸精度和表面光 洁度的冲模。
汽车模具基本知识讲义(1)
பைடு நூலகம்
第二节 冷冲模的成形特点
一、冷冲模的定义 在常温下,把金属或非金属板料放入模具内,通过压
汽车模具基本知识讲义(1)
二、模具的分类
冷冲模 注塑模
模
热压模
具
发泡模
热锻模
橡胶模
成形模 冷冲模
修冲模
拉延模 翻边模 整形模 冲孔模 修边模
汽车模具基本知识讲义(1)
• 拉延模:保证制成合格覆盖件的最主要的装备,其作用是 将平板状毛料经拉延工序使之成为主体空间工件,分正装 和倒装两种形式。
• 修边模:用于将拉延件的工艺补充部分和压料凸缘多余部 分切除,为翻边和整形准备条件,在小批量生产时,可以 用手工或其它简单设备代替,修边模往往兼冲孔。
汽车模具基本知识讲义(1)
第一节 模具的定义和分类
一、模具的定义 模具,是以特定的结构形式通过一定方式使
材料成型的一种工业产品,同时也是能成批生产 出具有一定形状和尺寸要求的工业产品零部件的 一种生产工具。
大到飞机、汽车,小到茶杯、钉子,几乎所 有的工业产品都必须依靠模具成型。用模具生产 制件所具备的高精度、高一致性、高生产率是任 何其它加工方法所不能比拟的。模具在很大程度 上决定着产品的质量、效益和新产品开发能力, 所以模具又有“工业之母”的荣誉称号。
冲压工艺是通过模具对毛坯施加外力,使之产生塑性 变形或分离,从而获得一定尺寸、形状和性能的工件的加 工方法。冲压工艺的应用范围十分广泛,既可以加工金属 板料、棒料,也可以加工多种非金属材料。由于加工通常 是在常温下进行的,故又称为冷冲压。而冲压工艺分析是 通过各个方面的参数综合确定最佳的冲压工艺。
《模具制造技术》课程标准

《模具制造技术》课程标准《模具制造技术》课程教学标准课程编码:30103003 课程类别:专业素质课适⽤专业: 2009级模具设计与制造专业课程管理单位:汽车⼯程系学时:116课时学分: 5 制定⽇期:2010年8⽉1、课程概述1. 1课程性质本课程性质是“理论+实践”课程,是模具设计与制造专业的⼀门综合性、实践性很强的专业课程,它承担模具专业学⽣的模具制造与装配知识、技能的培养任务。
针对模具专业⾼技能⼈才培养⽬标和模具制造中级⼯国家职业标准所涵盖的相关⼯作岗位所需要的知识与能⼒,对课程设置、教学内容、教学⽅法与教学⼿段等⽅⾯都进⾏了较⼤⼒度的改⾰,以模具制造为对象,“项⽬引领,任务驱动,案例分析”,综合学习⼑具、机床选择、数控铣镗程序编制、电加⼯线切割程序编制,加⼯⼯艺⽅案制订、装配⼯艺⽅案制订。
1.2课程的定位本课程是在已经学习完成了模具设计与制造专业群基础技术平台课程后,以模具为对象,综合应⽤⼑具、机床、加⼯⼯艺、设备操作相关知识的⼀门专业核⼼课。
课程是针对模具制造企业⽣产的产品特点和就业岗位特点设置。
本课程的前导课程为:机械制图、机械设计基础、计算机绘图、模具设计、机加⼯实训、钳⼯实训;后续课程为:顶岗实习、毕业设计。
1.3修读条件全⽇制模具专业⾼职学⽣。
2、课程⽬标2.1知识⽬标:掌握模具零件的⼀般机械加⼯⽅法、模具典型零件加⼯⼯艺分析与⼯艺规程的编制、了解模具的电加⼯⽅法与特种加⼯⽅法;掌握模具的装配⼯艺;掌握各类机床夹具的选择;掌握模具材料与热处理⽅法的选择;了解国内外先进的制模技术。
2.2技能⽬标:在设计、制造、装配模具时,能够根据实际情况,充分考虑各种制造⽅法的特点,从⽽选⽤最佳的⼯艺⽅案:具有分析模具结构⼯艺性的能⼒,具备设计出⼯艺性能良好的模具结构的能⼒;具备⼯艺设计过程中的计算能⼒;具备相关⼿册的查阅能⼒与新知识的检索能⼒。
2.3情感与态度⽬标:培养达到从事本专业的基本职业素质:纪律性强、能遵守学校的教学规章制度;具有团结协作、积极向上、刻苦学习的现代⼤学⽣风貌;养成⼀丝不苟的⼯作态度、良好的职业道德,以及团结协作、不怕困难、勇于创新的精神。
冲压工艺基础知识

2010-112010-11-29
10
Chery automobile Co., Ltd.
一、工艺知识----冲压工艺编制
直冲孔
整形
侧冲孔
如果轮 如果轮罩处有向内的翻边 有向内的翻边 需要研讨 工序 需要研讨5工序
侧冲孔
翻边
确认孔与孔的加工方式是否有干 如干涉 涉,如干涉就要分序 ≒45 2010-112010-11-29
2010-112010-11-29
25
Chery automobile Co., Ltd.
二、模具知识----概述
概述 模具是冲压生产的基础,也是一种成本很高的工装, 车型开发费用的五分之一会投在模具开发上;模具的制 造水平直接影响到了产品的质量和企业的经济效益。
2010-112010-11-29
Chery automobile Co., Ltd.
二、模具知识----模具结构
模具结构 一般模具的组成 6、紧固零件 包括内六角螺钉、卸料螺钉等零件。 7、缓冲零件 包括卸料弹簧、聚氨脂橡胶和氮气缸等。 8、安全零件及其它辅助零件 主要有安全侧销、安全螺钉、工作限制器、存放限制器、 上下料架、废料滑槽、起重棒、吊耳等。
Chery automobile Co., Ltd.
一、工艺知识----模具重量的预估
模具重量 是模具发 包估算价 格的重要 依据。 依据。
模具重量 = L ・ W ・ H ・ 比重 ・ K
备注: 备注:L/W/H单位要统一且为国际制单位
2010-112010-11-29 21
Chery automobile Co., Ltd.
一、工艺知识----拉延工艺
2.1 拉延:利用模具使平面毛坯变成为开口的空心零件 的冲压工艺方法。
丰田汽车案例
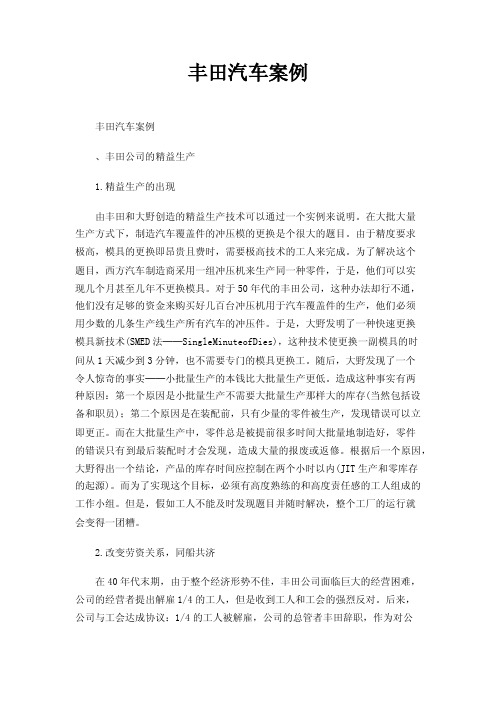
丰田汽车案例丰田汽车案例、丰田公司的精益生产1.精益生产的出现由丰田和大野创造的精益生产技术可以通过一个实例来说明。
在大批大量生产方式下,制造汽车覆盖件的冲压模的更换是个很大的题目。
由于精度要求极高,模具的更换即昂贵且费时,需要极高技术的工人来完成。
为了解决这个题目,西方汽车制造商采用一组冲压机来生产同一种零件,于是,他们可以实现几个月甚至几年不更换模具。
对于50年代的丰田公司,这种办法却行不通,他们没有足够的资金来购买好几百台冲压机用于汽车覆盖件的生产,他们必须用少数的几条生产线生产所有汽车的冲压件。
于是,大野发明了一种快速更换模具新技术(SMED法──SingleMinuteofDies),这种技术使更换一副模具的时间从1天减少到3分钟,也不需要专门的模具更换工。
随后,大野发现了一个令人惊奇的事实──小批量生产的本钱比大批量生产更低。
造成这种事实有两种原因:第一个原因是小批量生产不需要大批量生产那样大的库存(当然包括设备和职员);第二个原因是在装配前,只有少量的零件被生产,发现错误可以立即更正。
而在大批量生产中,零件总是被提前很多时间大批量地制造好,零件的错误只有到最后装配时才会发现,造成大量的报废或返修。
根据后一个原因,大野得出一个结论,产品的库存时间应控制在两个小时以内(JIT生产和零库存的起源)。
而为了实现这个目标,必须有高度熟练的和高度责任感的工人组成的工作小组。
但是,假如工人不能及时发现题目并随时解决,整个工厂的运行就会变得一团糟。
2.改变劳资关系,同船共济在40年代末期,由于整个经济形势不佳,丰田公司面临巨大的经营困难,公司的经营者提出解雇1/4的工人,但是收到工人和工会的强烈反对。
后来,公司与工会达成协议:1/4的工人被解雇,公司的总管者丰田辞职,作为对公司经营失败的惩罚;其余的工人则得到双倍的保证,一个是终身雇用,另一个是工资随在公司的工作年限同步增长而不与工种挂钩。
换言之,工人成为公司的一员,享受公司的一切福利。
TPS丰田生产方式的技术支撑体系

丰田生产方式的技术支撑体系1.引言丰田生产方式(Toyota Production System,TPS)是日本丰田汽车公司创立的一种独具特色的现代化生产方式。
它顺应时代的发展和市场的变化,经历了20多年的探索和完善,逐渐形成和发展成为今天这样的包括经营理念、生产组织、物流控制、质量管理、成本控制、库存管理、现场管理和现场改善等在内的较为完整的生产管理技术与方法体系。
丰田生产方式诞生在丰田公司,但它并不是仅适用于汽车生产。
事实上,丰田生产方式作为一种彻底追求生产过程合理性、高效性和灵活性的生产管理技术,它已被应用于日本的许多行业和众多企业之中。
同样,它的基本思想、基本原理和基本技法对我国企业的生产方式和管理方法的现代化具有重要的借鉴意义和参考价值。
实际上,早在80年代初,丰田生产方式就被介绍到了我国。
遗憾的是,当时我们误认为丰田生产方式就是“看板管理(Kanban)”。
我们的一些企业曾简单地模仿传递看板,但并未见到成效,于是就草率地把它否定了。
实践表明,如果没有生产经营观念的彻底转变和管理意识的彻底更新,没有对丰田生产方式进行系统性研究,而仅仅是模仿某个单项技法,丰田生产是不可能实现的。
因此,在借鉴丰田生产方式时,我们首先对其进行系统性的研究是极为重要和必要的。
2.丰田生产方式的真缔日本筑波大学的门田安弘教授曾指出:“丰田生产方式是一个完整的生产技术综合体系,而看板管理仅仅是实现丰田生产的工具之一。
把看板管理等同于丰田生产方式是一种非常错误的认识。
”丰田生产方式通过看板管理,成功地制止了过量生产,实现了“在必要的时刻生产必要数量的必要产品(或零部件)”,从而彻底消除在制品过量的浪费,以及由之衍生出来的种种间接浪费。
因此,每当人们说起丰田生产方式,往往容易只会想到看板管理和减少在制品库存。
事实上,丰田公司以看板管理为手段,制止过量生产,减少在制品,从而使产生次品的原因和隐藏在生产过程中的种种问题及不合理成份充分暴露出来,然后通过旨在解决这些问题的改善活动,彻底消除引起成本增加的种种浪费,实现生产过程的合理性、高效性和灵活性。
汽车制造IMD工艺介绍

INS 模内嵌件技术S
1.能够制作弯曲深度相对较大的表面 装饰(立体成型高度可达40mm); 2.适合小批量、多品种生产。
薄膜剖面图
成型后剥离
薄膜层 离型层
耐磨层 印刷层 粘结层 树脂层
INS薄膜剖面图
薄膜层 印刷层 粘结层 树脂层
公司名称
日本
NISSHA 三井
主要配套厂家 青岛海泰科、深圳华益盛、
天津丰田合成
上海通领
备注 ———— ————
德国 KURZ
深圳华益盛、威海海创
合肥有生产基地
韩国 LG
上海爱卓
————
结论:目前膜片开发的核心技术由国外少数公司掌握,故膜片只能依 靠国外采购进口(膜片开发技术难点1.高温高压下,保护层(薄膜层) 与油墨层的分离;2.高温高压下,油墨层与产品基材完整粘结。)
汽车制造IMD工艺介绍
目录
1 工艺分析及发展趋势 2 基础规划及投资分析 3 下一步计划
一、工艺分析
IMD/INS工艺流程图
INS
精密模具
IMD
精密模具
高压成型
冲切成型
送膜过程
IMD注塑
IMD工艺介绍
IMD工艺视频
GWM-PPT V2012.2
INS注塑
包装全检
出货
包装全检
一、工艺分析
IMD 模内转印
一、工艺分析
工艺性能对比
关键性能 IMD/INS 喷漆
制造成本
高
中等
装饰效果
好
差
图案种类
多
中等
电镀
中等 好 少
制造模式部分答案

制造模式1、简述丰田公司实施精益生产方式的主要做法.答:(1)拉动式的准时生产方式,杜绝一切超前、超量制造;采用快换工装模具新技术;把单一品种生产线改成多品种混流生产线,把小批次大批量轮番生产改变为多批次小批量生产,最大限度地降低在制品储备,提高适应市场的能力。
(2)“零缺陷”工作目标和发现问题随时修改。
追求目标是:“零缺陷”,即最低的成本、最好的质量、无废品、零库存与产品的多样性。
发现问题可以随时让组装线停下来。
(3)以“精简”为主要手段。
在组织机构方面,去掉一切多余的环节和人员。
在生产过程中,采用先进的柔性加工设备,减少非直接生产方式工人的数量,使每个工人都真正对产品实现增值。
此外,减少产品复杂性的同时,提供多样化的产品。
(4)在生产组织结构和协作关系上,丰田生产方式一反大量生产方式追求纵向一体化的做法,把70%左右的汽车零部件的设计和制造委托给协作厂进行,主机厂只完成约占整车30%的设计和制造任务。
(5)采用多功能作业小组和并行设计方式进行新产品开发。
工作小组由企业各部门专业人员组成,全面负责一个产品型号的开发和生产,并格局实际情况调整原有的设计和计划。
产品设计采用并行工程方法,克服了大量生产方式中由于分工过细所造成的那些信息传递慢、协调工作难、开发周期城等缺陷。
(6)与用户保持密切联系,将用户纳入产品开发过程。
不仅向用户提供周到的服务,而且洞悉用户的思想和要求,以生产出适销对路的产品。
(7)改变劳资关系,强调人的作用。
人是企业一切活动的主体。
劳动力和机器一样,不仅从短期看是企业的不变成本,而且从长远看是更重要的固定成本。
丰田公司采用终身雇佣制,工资按资历分级,奖金与公司盈利挂钩。
充分发挥一线职工的积极性和创造性,使他们积极为改进产品的质量献计献策,使一线工人真正成为“零缺陷”生产的主力军。
下放部分权力,使人人有权、有责任、有义务随时解决碰到的问题。
形成独特的、具有竞争意识的企业文化。
2、制造企业的浪费现象主要有哪些?可以采取哪些方法消除?答:浪费,(1)超量生产造成的无效劳动。
汽车冲压模具设计

上模
压料
下模
2024/6/23
51
冲模工作的基本原理
• 4) 整形:校正制件成准确的形状和尺寸 的成型模。
• 一端压料,材料不流动。间隙大于0.8料厚 ,下面有模具,为整形
上模
压料
下模
下模
2024/6/23
52
冲模工作的基本原理
2024/6/23
35
油箱盖总成
2024/6/23
36
四。覆盖件的分组——总成
白车身
发动机舱总成 发动机罩总成
侧围总成(2个) 车门总成(4个) 后围总成 后背门总成 地板总成 顶盖横梁总成
2024/6/23
37
什么是A级表面
• 什么是A级表面(Class A Surface? • A级表面实际上并非是曲面质量的度量而是
2024/6/23
11
行李箱内板
2024/6/23
12
前门外板(左、右)
2024/6/23
13
前门内板(左、右)
2024/6/23
14
后门外板(左、右)
2024/6/23
15
后门内板(左、右)
2024/6/23
16
顶盖
2024/6/23
17
二.车身内板件
焊接白车身总成(除了外板的侧围、顶盖)
、制造成本)
• 用户生产条件和习惯及用户特殊性要求——用
户会签 2024/6/23
69
实型制造
• 数控编程 • 准备坯料 • 数控加工 • 粘贴整理 • 检查、研讨
2024/6/23
70
FDM(熔融沉积制造)

精品课件
(3)FDM在Mizunos公司的应用
Mizuno是世界上最大的综合性体育用品制造公司。1997年1月,Mizuno 美国公司开发一套新的高尔夫球杆,通常需要13个月的时间。FDM的应用大大缩 短了这个过程,设计出的新高尔夫球头用FDM制作后,可以迅速地得到反馈意见 并进行修改,大大加快了造型阶段的设计验证,一旦设计定型,FDM最后制造出 的ABS原型就可以作为加工基准在CNC机床上进行钢制母模的加工。新的高尔夫球 杆整个开发周期在7个月内就全部完成,缩短了40%的时间。目前,FDM快速原型 技术已成为Mizuno美国公司在产品开发过程中起决定性作用的组成部分。
精品课件
四、熔融沉积快速成型技术的应用
FDM快速成型技术已被广泛应用于汽车、机械、航空航天、家电、通讯、电 子、建筑、医学、玩具等产品的设计开发过程,如产品外观评估、方案选择、装 配检查、功能测试、用户看样订货、塑料件开模前校验设计以及少量产品制造等, 也应用于政府、大学及研究所等机构。用传统方法须几个星期、几个月才能制造 的复杂产品原型,用FDM成型法无需任何刀具和模具,瞬间便可完成。
精品课件
一、熔融沉积工艺的基本原理
熔融沉积又叫熔丝沉积,它 是将丝状的热熔性材料加热熔化, 通过带有一个微细喷嘴的喷头挤 喷出来。喷头可沿着X轴方向移动, 而工作台则沿Y轴方向移动。如果 热熔性材料的温度始终稍高于固 化温度,而成型部分的温度稍低 于固化温度,就能保证热熔性材 料挤喷出喷嘴后,随即与前一层 面熔结在一起。一个层面沉积完 成后,工作台按预定的增量下降 一个层的厚度,再继续熔喷沉积, 直至完成整个实体造型。熔融沉 积制造工艺的具体过程如下:
电动工具
精品课件
抗冲精品击课件构件
丰田汽车的生产方式

丰田生产方式日本丰田汽车工业公司副总经理大野耐一第一章出自需要为石油冲击所唤醒昭和四十八年(一九七三年)秋天发生石油冲击以后,社会上好像开始强烈地关心起丰田生产方式来。
无论怎么说,石油冲击对于政府、企业和个人生活全都产生了巨大影响。
第二年,日本经济下降到无增长的状态,整个产业界陷入了恐怖的深渊。
就在各家公司由于萧条而非常苦恼的时候,丰田虽然收益有所减少,确保住了其他大公司的盈利,因此引起了社会上的注意,人们说,丰田这家企业在用着足以对付冲击的生产办法……。
我在石油冲击以前很早的时候,每遇到人,就打算介绍什么是丰田式的制造技术,什么是丰田的生产方式。
可是,当时人们对此不太感兴趣。
石油冲击以后,经过昭和五十年(一九七五年)、五十一年(一九七六年)、五十二年(一九七七年),丰田的盈利与日俱增,拉大了同其它公司的距离,于是丰田生产方式开始受到重视了。
在昭和四十八年(一九七三年)以前,日本经济一直保持高速度的增长。
在那个年代,企业可以在用美国的生产方式。
但是,高速度增长一停止,增长率一降低,美国式的有计划大量生产方式就行不通了。
日本的工业,譬如设备、工厂设计,全都是一致效仿美国的。
偶然也有过两位数的增长率。
那时候采用有计划大量生产是非常合适的。
但是到了高数增长停止并减产的时候,采用历来的大量生产方式不合算,这一点显著的表现出来了。
战后的昭和二十五年(一九五零)、二十六(一九五一)年,我们想也没想过汽车的数量会象现在这样多起来。
在那以前很久,在美国,汽车种类少,便发明了大量生产的方法来降低成本。
这种方法渐渐成了美国的一个特点。
可是,日本并非如此。
当时我们的课题是,怎样才能创造出多品种、少量生产的办法来降低成本。
从昭和三十四年(一九五九)、三十五(一九六零)年起的十五年里,日本在经济方面实现了速度非常快的增长,因此,采用和美国一样的做法,也在各方面表现出大量生产得相当好的效果。
但是,我们从昭和二十五年(一九五零)、二十六(一九五一)年起就开始认识到,不加取舍的单纯模仿美国式的大量生产方式是危险的。
丰田生产方式-华制国际
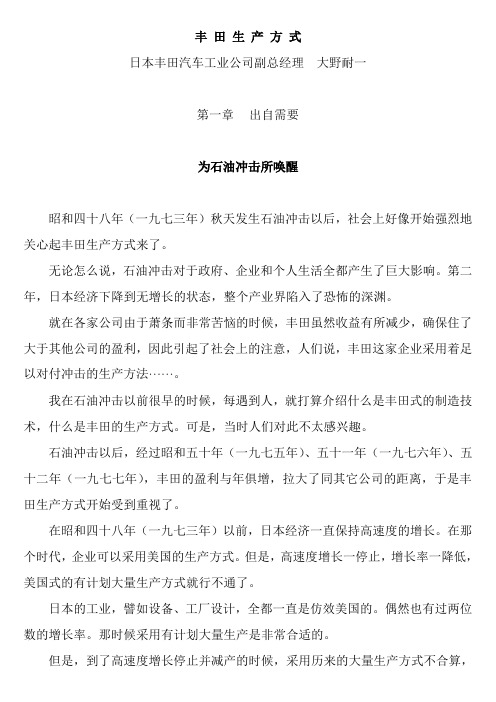
丰田生产方式日本丰田汽车工业公司副总经理大野耐一第一章出自需要为石油冲击所唤醒昭和四十八年(一九七三年)秋天发生石油冲击以后,社会上好像开始强烈地关心起丰田生产方式来了。
无论怎么说,石油冲击对于政府、企业和个人生活全都产生了巨大影响。
第二年,日本经济下降到无增长的状态,整个产业界陷入了恐怖的深渊。
就在各家公司由于萧条而非常苦恼的时候,丰田虽然收益有所减少,确保住了大于其他公司的盈利,因此引起了社会上的注意,人们说,丰田这家企业采用着足以对付冲击的生产方法……。
我在石油冲击以前很早的时候,每遇到人,就打算介绍什么是丰田式的制造技术,什么是丰田的生产方式。
可是,当时人们对此不太感兴趣。
石油冲击以后,经过昭和五十年(一九七五年)、五十一年(一九七六年)、五十二年(一九七七年),丰田的盈利与年俱增,拉大了同其它公司的距离,于是丰田生产方式开始受到重视了。
在昭和四十八年(一九七三年)以前,日本经济一直保持高速度的增长。
在那个时代,企业可以采用美国的生产方式。
但是,高速度增长一停止,增长率一降低,美国式的有计划大量生产方式就行不通了。
日本的工业,譬如设备、工厂设计,全都一直是仿效美国的。
偶然也有过两位数的增长率。
那时候采用有计划大量生产是非常合适的。
但是,到了高速度增长停止并减产的时候,采用历来的大量生产方式不合算,这一点显著的表现出来了。
战后的昭和二十五年(一九五零)、二十六(一九五一)年,我们想也没想过汽车的数量会象现在这样的多起来。
在那以前很久,在美国,汽车种类少,便发明了大量生产的方法来降低成本。
这种方法渐渐地成了美国的一个特点。
可是,日本并非如此。
当时我们的课题是,怎样才能够创造出多品种、少量生产的方法来降低成本。
从昭和三十四年(一九五九)、三十五(一九六零)年起的十五年里,日本在经济方面实现了速度非常快的增长,因此,采用和美国一样的做法,也在各个方面表现出大量生产的相当好的效果。
但是,我们从昭和二十五年(一九五零)、二十六(一九五一)年起就开始认识到,不加取舍地单纯模仿美国式的大量生产方式是危险的。
- 1、下载文档前请自行甄别文档内容的完整性,平台不提供额外的编辑、内容补充、找答案等附加服务。
- 2、"仅部分预览"的文档,不可在线预览部分如存在完整性等问题,可反馈申请退款(可完整预览的文档不适用该条件!)。
- 3、如文档侵犯您的权益,请联系客服反馈,我们会尽快为您处理(人工客服工作时间:9:00-18:30)。
丰田汽车模具制造技术一、丰田模具设计与制造部门概况丰田汽车公司中与冲压模具设计制造有关的部门主要有两个,其中负责模具设计的是第八生产技术部,负责模具制造的是ST部(ST为冲模的英文缩写)。
它们都直属于总公司,生产技术1-8部属于生产准备部门,冲模部(ST部)属于工机制造部门。
1、第8生产技术部其主要职责是模具设计和冲压设备准备,加上它所属的计划、生产准备、部属等科室共有将近350人。
其中与模具设计有关的技术室有三个,它们是由从事的产品制件的类型来划分的:部门职责人员一室车身周边件模具设计(车门、机盖、后行李厢盖)约70人二室主车身件模具设计(侧围、翼子板、顶盖等)约75人三室底板、梁架件模具设计(地板、发动机舱等)约30人每个室又分为冲压工艺与模具结构设计两个组。
专业化分工是丰田模具设计部门工作的特点:a.模具设计内容细分丰田把模具设计分成三个工序:工序设计、模面设计和结构设计,分工明确,分别由专门人员负责。
工序设计主要完成工序草图、dl图设计、作详细的模具设计任务书、模面构想等,模具设计的主要创造性劳动都在这一步靠人脑完成。
模面设计几乎是单纯的曲面造型,结构设计的重点在于模具结构的具体实现。
b.人员专业化分工细微各个室只负责一类产品件,每个人在一定时间内负责同一个件,甚至是同一类模具。
由于丰田每年开发的新车可达十种,这就是说,可能有的人在一年内画十套非常相似的前车门外板拉延模,其专业化程度可想而知。
c. 模具的社会大分工日本的模具制造专业性分工很强,丰田虽然自己的模具制造能力很强,但它并不是什么模具都干。
比如,整车所有件的冲压工艺和模具的整车协调,都由他自己负责,但模具设计和制造他只干车身内外覆盖件,地板和梁架件全部到定点厂家外协。
不但丰田如此,国外的大汽车公司所属模具厂无不如此,比如日本大发公司模具厂,甚至只做侧围、翼子板、顶盖等有限的几种外覆盖件。
这可以看作是一种发展趋势,在韩国、台湾甚至是专业模具厂家也是向只做几种件的更专业方向发展。
2、模具制造部(ST部)丰田ST部负责模具制造和新车整车模具的协调,并一直到大批量生产之前的冲压生产准备。
ST部构成:科室责任人员技术室生产技术开发、生产计划生产准备、设备计划 89人NC课 NC编程、检查 175人实型课验具、实型制造 142人机械课机械加工 173人钳工课钳工、装配 237人调试课试模、调试 204人总共 :1020人主要数控加工设备:构造面加工数控铣床 39 台型面加工高速、五轴五面铣 15 台新型一体化加工设备 6 台其他小件加工设备 31 台3 、丰田的模具设计和制造能力模具设计与制造能力:每年大约可开发10个轿车整车模具;模具产量(标准套)约2000套/年;内制率60%(外协40%);主要产品中:模具占80%;验具占7%;其他占13%;全年完成模具制造成本预算近200亿日元。
人均模具产量 2 标准套/人。
年模具制造成本(不含设计)约600万日元/套工时成本(平均)约1万日元/小时整车模具设计制造周期 12个月(由车身设计完成至新车批量生产)其中包括整车全部模具设计周期 5个月制造周期 5个月调试周期 6个月由此可见,丰田一年的轿车生产能力大约500万辆(日本国内部分约占50%),是中国大陆轿车产量的十倍,而模具设计制造能力也超过我们全国汽车模具生产能力的数倍。
丰田的整车模具制造周期,远远短于我们的一般单套模具制造周期,它的标准单套模具制造周期为三至四个月,在我们看来还是一个梦想。
我们的模具质量水平与丰田相比相差更远。
3、丰田一般模具制造周期丰田把模具的制造计划形成了标准化,根据模具的复杂程度可分为短周期、标准周期和长周期三种。
现以单套模具的设计制造周期(拉延模,标准周期)为例:冲压工艺20天模具设计20天模面设计 8天NC编程 15天实型制作 7天铸造12天机加工 9天钳工装配 7天单套拉延模总周期62天,其中制造周期52天以上周期包括模具的设计、制造直至模具初次试模完成为止。
如果再考虑产品件各序模具的总周期,单个制件各序模具的总周期,要在拉延模的基础上再加22天(包括模具调试,但不包括整车调试),总共84天。
以上天数均为工作日(节假日除外),换算为日历日大约为20天等于一个月,也就是单套模具制造周期三至四个月。
丰田的模具制造也是按照准时化生产方式进行的,全部倒排计划,计划到每一个工作日,不提前投产,避免增加在产模具。
我们的倒排计划往往是为赶工期,人为的压缩工期。
而丰田的倒排计划,是为了在必要的时候生产出必要的产品,避免提前投产造成生产过剩的浪费。
二、丰田模具制造技术近十年来本人曾在日本多家模具制造厂进行过较为深入的学习和考察,先后累计时间达6个多月。
对比以后发现,丰田的模具技术在日本的模具厂家中也是十分突出的,无论是能力、效率及技术都不愧为世界一流水平。
通过对丰田的了解我们可以看到,世界汽车模具制造技术正在向这些方向发展:计算机前的操作逐步代替现场操作,以高精度加工代替人的手工劳动,模具的设计、制造高度标准化,单件生产方式向流水线式生产方式发展等等。
结合我们国内的模具制造情况,丰田在以下一些地方与我们有很大的不同,值得我们很好的借鉴。
1、冲压工艺设计a、精细模面设计我们常说的模具设计实际上分为三个部分:冲压工艺设计、模面设计和结构设计。
这三种设计的内容和侧重点是完全不同的,丰田的工作流程为先有冲压工艺设计然后指导模面设计和模具结构设计,分别由不同的人来做,专业分工很明确。
传统的冲压工艺设计采用工序图或是DL图,它的模面设计是非常粗略的,以这样的图纸指导下的工艺造型,必须在后序靠人工修整、制造工艺祢补,造成模具制造的人工钳修量很大、周期延长。
丰田在设计阶段通过计算机的曲面造型,完成模面的精细设计。
比如:针对进料量不同设计各种拉延筋,同一套模不同部位的拉延筋截面不同,防回弹、过拉延处理,最小压料面设计,凸凹模不等间隙设计等等。
精细模面设计的结果,可以极大的减少型面加工,减少钳修,减少试模工时,它的作用非同小可。
对比之下,国内的模具设计还停留在结构设计阶段,模面设计没有受到很好的重视,模面实际上是靠后天完成,模具设计的落后造成了制造的落后,也就毫不奇怪了。
b、板料成型分析技术应用情况丰田公司从5-6年前,开始应用有限元法做计算机模拟板料成型分析,主要应用的解算软件为美国的dyna3d,他们经过了近三年的努力才达到实用水平。
目前,丰田建立了一个整车身各种典型件的分析结果库。
对一个新车型的件,如果成型性没有太大的变化,只是参考原工艺不做分析,只有特殊的新造型才做板料成型分析。
丰田的新车要做样车,对造型特殊的件除了做板料成型分析外一般还要做简易模进行验证。
因此,丰田人认为目前板料成型分析还不是一件必需的、简单的事,无论是周期还是成本都有很大代价。
本人认为,丰田的车型开发量很大,车型之间变化不大、类似件很多,又积累了丰富的人的经验,板料成型分析确实用武之地不多,建立一个分析结果库是一个好方法(日本富士模具公司也是这么做的)。
反观国内现状,一方面模具厂专业分工很低,各种件都会遇到,难有现成经验,似乎更需要板料成型技术。
另一方面,技术水平低支持环境差(如:板料参数、摩擦系数等难掌握),模具厂应用起来,要达到实用(不讲效果、不计代价的研究不算)也是非常困难的。
即使是成立专业分析公司,考虑用户数量、周期、价格等因素,恐怕也难成立。
目前,这项技术在国内的实际应用效果还难有定论。
c、模面设计经验积累机制丰田的设计部门除手工勾画草图以外,设计已全部计算机化,一般设计人员除一台工作站外还有一台笔记本电脑。
但,真正创造性的设计还是靠人脑,特别是靠人的经验积累。
丰田特别强调经验积累机制:只有集体的经验不能有只属于个人的经验,比如:资料的统一管理,草图设计的小组讨论,图纸的多部门集体审核,设计标准、规范的经常性增改等等。
经验积累机制是丰田能够不断提高模面精细设计的主要手段。
比如:模具加工完成之后,一般模具型面不用研合,刃口不必对间隙,钳工只负责安装,在初次试模时也不能随便修调模具,调试模具有模面设计人员在场,初次试模缺陷需要记录下来。
最后的休整结果,像拉延筋、拉延圆角变动、对称件的不对称现象等,还要进行现场测量。
这些资料的积累、整理、分析、存档,都是模面设计的经验积累,并随时加入到下一次的设计中去。
丰田的模具设计和调试过程,真正做到了是一个闭环制造系统,借助于这种自我完善的经验积累机制,模具的设计越来越精细,越来越准确。
d、间隙图设计在丰田,模面设计实际上是由曲面造型和NC编程两部分共同完成的,为了传达和描述模面设计思想,就产生了除DL图、模具图之外的第三种图---间隙图也叫质量保证图。
间隙图本人在以前还没有见识过,这可能是丰田的一种创造。
模具的设计不是单纯为了设计出一种机器,能够完成它一定的动作就完了(这只能叫作结构设计),模具设计的最终目的是为了保证它所压出的产品件是合格的高质量的,间隙图就是这样一种专为保证产品件质量的图。
质量保证图中,主要包括这样几项内容:模具实际符型面区域、各个符型区域的间隙值、工艺要求的模面变化情况、拉延圆角的变化、各种模面的挖空等等。
凡是无法通过曲面造型实现的模面设计,都通过间隙图的传达,依靠NC编程的设计来实现,在这里NC编程也不再是单纯的实现模具结构的加工,它实际上也参与到模面设计中来了。
因此,间隙图的应用也是精细模面设计的一种必然。
e、大规模生产对模具的影响丰田的生产规模是世界一流的,它在模具设计如何适应大规模生产的要求方面具有丰富的经验。
提高材料利用率:对于大批量汽车生产来说,提高板料的利用率是模具设计的第一大事。
只要把材料利用率提高几个百分点,模具的成本就可乎略不计了。
如果一套模具40万人民币,只相当于100吨钢板的价格,以寿命50万件计算,平均每件节约0.2Kg钢板,就足可节约出这套模具费用了。
减少冲压工序:模具设计的趋势是,零件的合并,左右对称件合模,前后顺序件合模等等,原来几个件合成一个件,不同的件合在一套模,模具越来越大,单件工序大大减少,整车模具数量越来越少,这对降低冲压的成本起关键作用。
例如:丰田把整车制件的模具系数,由过去的3点几降到2左右。
冲压自动化:为适应冲压线完全自动化,模具必须考虑机械手上下料,废料的自动排出,气动、自动和传感装置普遍采用等等。
模具的快速装换:冲压线的换模时间,也成为一个模具设计必须考虑的问题。
如:拉延模完全以单动代替双动,模具自动卡紧,换模不换气顶杆等等。
2、模具结构的设计和加工设计有两种目的:一个是面向设计本身,一个是面向制造。
设计者在画图过程中逐步完善自己的设计思路,图画完了,自己也清楚了,因此图纸首先要设计者自己看得方便,并使设计的工作效率高。