单工序模
单工序落料模设计使用说明

冲压模具课程设计系别:模具设计与制造姓名:学号:冲压模具设计说明书目录前言 (3)设计任务书 (4)一、冲压件工艺分析 (5)二、确定冲裁工艺方案 (5)三、确定模具总体结构 (5)四、工艺尺寸计算 (6)五、冲压设备的选择 (7)六、主要零部件的设计 (8)七、模具装配图 (18)心得体会 (19)结束语 (20)前言模具课程设计是CAD/CAM专业教学计划安排的非常重要的教学实践环节,也是毕业设计的首选内容。
其目的在于巩固《模具结构及设计》所学知识,熟悉有关资料,树立正确的设计思想,掌握正确的设计方法,培养学生的实际工作能力。
通过模具结构设计,学生在工艺性分析、工艺方案论证、工艺计算、模具零件结构设计、编写说明书和查阅参考文献等方面受到一次综合的训练,增强学生的动手能力和创新设计能力。
本次设计中,本人的设计任务是根据一个座板的工件设计一副模具。
本人主要做了如下工作:1、根据座板的结构设计计算各部分尺寸;2、确定工艺方案;3、由以上数据画出装配图。
设计任务:一、冲压件工艺分析1、材料:Q235普通碳素结构钢,具有好的塑性,具有良好的冲压性能。
128、00.20-64、2、冲裁件的尺寸精度和表面粗糙度:零件的尺寸精度00.26-35、023.0-96已给公差,冲压生产出的零件精度能够符合零件精度要求。
-0.203、工件结构:结构简单,形状对称。
结论:适合冲裁二、冲压件的工艺方案确定通过以上对该零件的结构、形状及精度的分析,并结合零件的生产批量。
该零件采用落料单工序就可完成冲压加工。
三、确定模具总体结构1、模具类型的选择由冲压工艺分析可知,采用单工序模冲压,所以本套模具类型为单工序落料模。
2、定位方式的选择因为该模具采用条料,控制条料得送进方向采用导料销;控制条料的送进步距采用挡料销。
3、导柱、导套位置的选择由于落料件的结构简单,大批量生产都使用导向装置。
导向方式主要有滑动式和滚动式导柱导套结构。
单工序模工作流程

单工序模工作流程Single process mode workflow is a common method of organizing work in various industries. This workflow is characterized by the completion of one task at a time, moving sequentially from one stage to the next. In a manufacturing environment, for example, a single process mode workflow means that each product passes through a series of steps, with each step being completed before the next one begins. This ensures a consistent and controlled workflow, allowing for quality control and efficient production.单工序模式工作流程是各行各业常见的工作组织方法。
该工作流程的特点是一次只完成一个任务,按照顺序从一个阶段移动到下一个阶段。
在制造环境中,例如,单工序模式工作流程意味着每个产品都需要经过一系列步骤,每个步骤都要在下一个步骤开始之前完成。
这确保了一致而受控的工作流程,有利于质量控制和高效生产。
One of the advantages of a single process mode workflow is its simplicity. Since each task is completed before moving on to the next, there is less room for confusion or error. This makes it easier for workers to focus on their specific role and perform their dutieswithout being overwhelmed by multiple tasks at once. Additionally, the sequential nature of this workflow allows for clear accountability and tracking, as it is easy to identify which step each product is at in the process.单工序模式工作流程的一个优势是它的简单性。
冲压模具基础知识
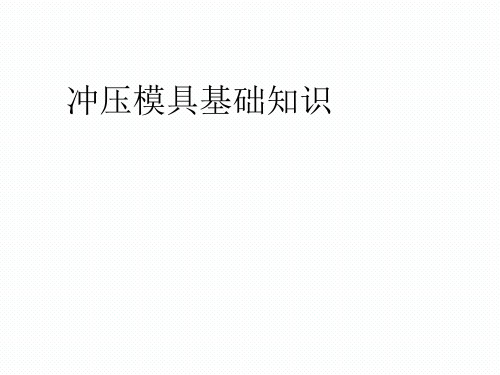
工艺性分析
OK?
N O
YES
毛坯排样
冲切刃口设计
工序优化成组
工序排样
工序排样图
工艺计算
结构概要设计
压力机
不合适 备料,毛坯粗加工
价格,周期 评测 合适
结构详细设计
零件设计
零件明细表
外购件明细 标准件明细
装配图
模具零件加工
零件图
四、冲压模具常用钢材及表面处理: Steels and surface treatment
二、冲压模具的基本结构: Basic structure
復 合 模 (彈簧脫料) 結 構 圖 例
CP
要釆用綠色彈簧
TM( 25*55)日產彈簧
PRL
所有模具必須作限位塊 以作下死點保護
要釆用紅色彈簧 TM( 25*30)日產彈簧
5 UDS 4
UBP 15
PP
23
UDP
8
16 17
USP
6
19 18
HRC62-64 HRC62-64
HRC 62-64 Nitriding >>TD Coating 渗氮甚至TD处理 HRC58-62 HRC54-58 -
Cr12/D2
Stainless steel plate 不锈钢板 Self lubricating and copper base 铜座、自给润滑 A3/45/Q235
Cr12MoV/D2/SKD11/DC53/SKH-9
Surface Treatment / HARDNESS 表面处理及硬度
HRC62-64、
Cr12MoV/D2/SKD11/DC53/SKH-9 SKD11/DC53/SKH-9 A3/45 45 D2/SKD11/DC53 D2/SKD11/DC53 Cr12MoV/D2/SKD11 45/Cr12
冲裁模的分类及导板式单工序冲裁模

模具制造难易 容易、价格低 程度及价格 生产率 生产安全性
较低 不安全
最高 比较安全
高 不安全,要有 安全装置
按模具导向方式分类
无导向的开式模、有导向的导板模、导柱模
无导向式
导柱式
其他分类方式
• 按卸料与出件方式分类
固定卸料式与弹性卸料式模具、顺出件与逆出件式模具
• 按挡料或定距方式分类
挡料销式、挡正销式、侧刃式等模具
• 按凸凹模所用材料不同分类
钢模、硬质合金模、钢带冲模、锌基合金模、橡胶冲模等
• 按自动化程度分类
手动模、半自动模和自动模
导板式单工序冲裁模
导 板 式 单 工 序 冲 裁 模
特点:上模与下模的导向是凸模与导板之间
的小间隙配合(H7/h6)实现 优点:安装调整比无导向式模具方便采用行程可调压力机,保证使用 过程中凸模与导板不脱离以保证其导向精度
谢谢观看
冲裁模的分类
——成型141-1组
按工序性质分类
落料模、冲孔模 切断模、切边模
与课本p4 表1-1 分离 工序相对应
切舌模、剖切模 整修模、精冲模
单工序模、级进模和复合模的特点比较
项目
冲压精度
单工序模
较低
级进模
复合模
较高(IT10—IT13) 高(IT8—IT11)
简单形状制件的级 进模比复合模制造 难度低,价格也较 低 复杂形状制件的复 合模比级进模制造 难度低,相对价格 低
单工序落料模
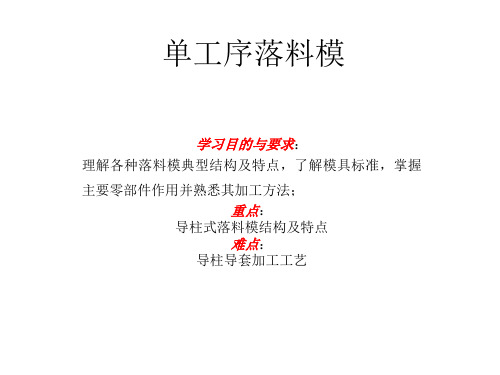
图2 导板式落料模
1-模柄 2-止动销 3-上模座 4、8-内六角螺钉 5-凸模 6-垫板 7-凸模固定板 9-导板 10-导料板 11-承料板 12-螺钉 13-凹模 14-圆柱销 15-下模座 16-固定挡料销 17-止动销 18-限位销 19-弹簧 20-始用挡料销
导板式单工序落料模
导板式单工序落料模 结构与原理
导柱导模具中起导向作用, 并保证凸模和凹模在工作时具有正确的相 对位置;保证模架的活动部分运动平稳、 无阻滞现象。 • 冷冲模标准导柱和导套如图 4
冷冲模标准导柱和导套图
图4 导柱和导套 a) 导柱 b) 导套
导柱的加工工艺路线
工序号 1 2 工序名称 下料 车端面钻中心 孔 工序内容 按尺寸¢35mm×215mm 切断 车端面保证长度 212.5mm 钻中心孔 调头车端面保证 210mm 钻中心孔 3 车外圆 车外圆至¢32.4mm 切 10mm×0.5mm 槽到尺寸 车端部 调头车外圆至¢32.4mm 车端部 4 5 6 7 8 9 检验 热处理 按热处理工艺进行,保证渗碳层深度 0.8~1.2mm,表面硬度 58~62HRC 研中心孔 研中心孔 调头研另一端中心孔 磨外圆 磨¢32h6 外圆留研磨量 0.01mm 调头磨¢32r4 外圆到尺寸 研磨 研磨外圆¢32h6 达要求 抛光圆角 检验 卧式车床 外圆磨 卧式车床 卧式车床 设备 锯床 卧式车床
单工序落料模
学习目的与要求:
理解各种落料模典型结构及特点,了解模具标准,掌握 主要零部件作用并熟悉其加工方法; 重点: 导柱式落料模结构及特点 难点: 导柱导套加工工艺
冲裁模的典型结构
一、单工序冲裁模
单工序冲裁模: 在压力机一次行程内只完成一个冲压工序的冲裁模。 .落料模 1无导向单工序落料模 2导板式单工序落料模 3导柱式单工序落料模
单工序落料模设计说明书

目录一、设计任务二。
冲压工艺分析三。
冲压工艺方案的确定四。
模具结构形式的确定.............................................5.流程规模的计算1.布局方法的确定...............................................2.与布局相关的计算.................................................3.切削刃尺寸的计算4.冲、推、卸力计算5.压机标称压力的计算6.冲裁压力中心的确定不及物动词主要部件的设计七。
模具工程图八。
冲压设备的选择九。
经验之谈十、致{\\ lang 1033 ,}XI。
参考文献一、设计任务零件名称:封面批量生产:大批量材料:Q235材料厚度:1毫米设计该零件的冲裁模。
二。
冲压件的工艺分析①材料:该冲裁件的材料Q235具有良好的冲压性能。
②零件结构:此冲裁件结构形状简单,适合冲裁。
③尺寸计算:为保证零件尺寸,应预留修边余量。
三、冲压工艺方案的确定基于以上对零件的结构、形状和精度的分析,结合零件的生产批次。
该零件可采用冲裁单工序冲压。
第四,确定模具的整体结构。
1.模具类型的选择从冲压工艺分析可知,冲压采用单工序模具,所以这套模具是单工序冲裁模。
2.定位模式的选择由于模具中使用的是条状材料,所以条状材料的进给方向由导向销控制;为了控制带状材料的进给进度,使用了止动销。
3.导柱和导套位置的选择由于冲裁件结构简单,导向装置在大批量生产中使用。
导向方式主要有滑动导向柱导向套结构和滚动导向柱导向套结构。
该部分承受的侧压力很小,为便于加工装配和易于标准化,决定采用滑动导柱导套结构。
4.滑动模板的选择由于应力和精度要求低,同时为了节约生产成本,简化模具结构,降低模具制造难度,便于安装调整,采用了背侧导柱导套模架。
模架可以从三个方向进料,操作特别方便。
5.卸载和卸料方法的选择在选择出料装置形式时,需要考虑出料方式是上出料还是下出料。
单工序模具设计说明书

课程设计说明书课程名称:冷冲压工艺及模具设计题目名称:单工序模具设计班级:20 级专业班姓名:学号:指导教师:评定成绩:教师评语:指导老师签名:20 年月日目录一、设计任务二、零件工艺性分析2.1结构与尺寸分析2.2材料分析2.3精度分析三、冲裁工艺方案的确定四、确定模具总体结构方案4.1模具类型4.2操作与定位方式4.3卸料与出件方式4.4导向方式4.5模架类型及精度五、垫片冲压工艺计算5.1排样设计与计算5.2计算冲压力5.3计算模具压力中心5.4模具刃口尺寸计算六、垫片凸模和凹模主要零件的设计计算6.1凹模设计6.2固定板6.3垫板的设计6.4卸料板的设计6.5凸模设计6.6凸模的校核6.7模架设计6.8校核模具闭合高度6.9模柄的设计七、总结八、参考文献绪论冲压是使板料经分离或成型而得到制件的加工方法。
冲压利用冲压模具对板料进行加工。
常温下进行的板料冲压加工称为冷冲压。
模具是大批生产的工具,是工业生产的主要工艺装备,模具工业是国民经济的基础工业。
模具可保证冲压的尺寸精度,使产品质量稳定,而且在加工中不破坏产吕表面。
用模具生产零部件可以采用冶金厂大量生产的廉价的轧制钢板或钢带为坯料,且在生产中不需加热,具有生产效率高、质量好、重量轻、成本低且节约能源和原材料等一系列的优点,是其它加工方法所不能比拟的,使用模具已成为工业生产的重要手段和工艺发展方向。
现代的制造工业的发展和技术水平的提高,很大程度上取决于模具工业的发展。
目前,工业生产中普遍采用模具成型工艺方法,以提高警惕产品的生产率和质量。
一般压力机加工,一台普通压力机设备每分钟可生产零件几件到几十件,高速压力机生产率已达到每分钟数百件甚至上千件。
据不完全统计,飞机、汽车、拖拉机、电机、电器、仪器、仪表等产品;有60%左右的零件是用模具加工出来的;而自行车、手表、洗衣机、电冰箱及电风扇等轻工产品,有90%左右的零件是用模具加工出来的。
显而易见,模具作为一种专用的工艺装备,在生产中的决定性作用和重要地位渐为人们所共识。
模具分类
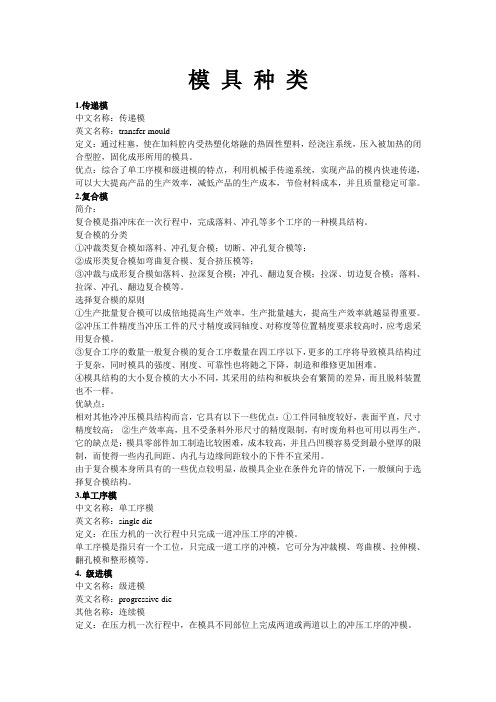
模具种类1.传递模中文名称:传递模英文名称:transfer mould定义:通过柱塞,使在加料腔内受热塑化熔融的热固性塑料,经浇注系统,压入被加热的闭合型腔,固化成形所用的模具。
优点:综合了单工序模和级进模的特点,利用机械手传递系统,实现产品的模内快速传递,可以大大提高产品的生产效率,减低产品的生产成本,节俭材料成本,并且质量稳定可靠。
2.复合模简介:复合模是指冲床在一次行程中,完成落料、冲孔等多个工序的一种模具结构。
复合模的分类①冲裁类复合模如落料、冲孔复合模;切断、冲孔复合模等;②成形类复合模如弯曲复合模、复合挤压模等;③冲裁与成形复合模如落料、拉深复合模;冲孔、翻边复合模;拉深、切边复合模;落料、拉深、冲孔、翻边复合模等。
选择复合模的原则①生产批量复合模可以成倍地提高生产效率,生产批量越大,提高生产效率就越显得重要。
②冲压工件精度当冲压工件的尺寸精度或同轴度、对称度等位置精度要求较高时,应考虑采用复合模。
③复合工序的数量一般复合模的复合工序数量在四工序以下,更多的工序将导致模具结构过于复杂,同时模具的强度、刚度、可靠性也将随之下降,制造和维修更加困难。
④模具结构的大小复合模的大小不同,其采用的结构和板块会有繁简的差异,而且脱料装置也不一样。
优缺点:相对其他冷冲压模具结构而言,它具有以下一些优点:①工件同轴度较好,表面平直,尺寸精度较高;②生产效率高,且不受条料外形尺寸的精度限制,有时废角料也可用以再生产。
它的缺点是:模具零部件加工制造比较困难,成本较高,并且凸凹模容易受到最小壁厚的限制,而使得一些内孔间距、内孔与边缘间距较小的下件不宜采用。
由于复合模本身所具有的一些优点较明显,故模具企业在条件允许的情况下,一般倾向于选择复合模结构。
3.单工序模中文名称:单工序模英文名称:single die定义:在压力机的一次行程中只完成一道冲压工序的冲模。
单工序模是指只有一个工位,只完成一道工序的冲模,它可分为冲裁模、弯曲模、拉伸模、翻孔模和整形模等。
单工序冲裁模(落料模)设计

单工序冲裁模(落料模)设计零件名称:铁芯片 材料:D21硅钢板 材料厚度:t=0.5mm1.冲压件工艺分析①材料:该冲裁件的材料硅钢板,具有较好的可冲压性能。
②零件结构:该冲裁件结构简单,形状对称,比较适合冲裁。
③尺寸精度:零件图上除30±0.17之外,其余没标尺寸的可按IT14级确定工件尺寸的公差。
按IT14级处理,并按“入体”原则标注公差。
查公差表可得各尺寸公差为:零件外形:500 -0.62mm 350 -0.62mm 150 -0.43mm 100 -0.36mm 7.50-0.36mm 补标公差后零件尺寸如右图2.冲压件的工艺方案确定通过以上对该零件的结构、形状及精度的分析,并结合零件的生产批量。
该零件采用落料单工序就可完成冲压加工。
3、工艺计算 ⑴排样设计为保证冲裁件的质量,模具寿命和操作方便,采用有搭边,单排排样,如下图所示,由表1-21得,冲裁件之间的搭边值a 1=1.5mm,冲裁件与条料件侧边之间的搭边值a=2mm 。
计算条料的宽度:b=50+2×2=54(mm) 计算条料的步距:A=35+1.5=36.5(mm)一个步距内材料的材料利用率:η=nF/bA ×100%=1x1350÷(54×36.5)×100% =68.5% 其中一个进距内的冲压数目n=1;因选用了1000mm ×2000mm 的板料,可将板料剪裁为37张条料(54mm ×1000mm ),每张条料可冲27个工件,则η总为:η总=nF 1/LB ×100%=999×1350÷(1000×2000)×100% =67.4% 冲压件面积可以简化为矩形面积50×35,减去两个槽的面积,所以:F =50×35-2(20×10)=1350(mm )⑵冲压力与压力中心的计算 ①冲压力的计算 落料力为:F 落=Lt σ b 其中:L=(50×2+35×2+20×4)=250(mm) 材料厚度t=0.5mm;材料:D21硅钢板,查表1-3,σ b =225Mpa,则: F =250×0.5×225=28(kN )根据以上模具结构类型,采用弹性卸料和漏料出件,卸料力F x =K x F,取K x =0.05,则:F x =0.05×28=1.4(kN )推件力F T =nK T F,去凹模刃壁垂直部分高度h =6mm,t =0.5mm,n =4/0.5=8;取K T =0.06,则: F T =8×0.06×28=13(kN )总冲压力F 总=F+ F x + F T =28+1.4+13=42.4(kN ) 选用的压力机公称压力P ≥(1.1~1.3) F 总取系数为1.3,则P ≥1.3F 总=1.3×42.4=55(kN )初选压力机公称吨位为63kN,型号为J23-6.3,其主要工艺参数如下:公称压力:63KN; 滑块行程:50mm;行程次数:160次∕分; 最大闭合高度:170mm; 闭合高度调节量:40mm ,(最小闭合高度:130mm ); 工作台尺寸(前后×左右):200mm ×315mm; 模柄孔尺寸:直径30mm,深度50mm; 工作垫板:厚度40mm,直径110mm 。
单工序落料模设计说明书

欢迎阅读冲压模具课程设计系别:模具设计与制造姓名:五、冲压设备的选择 (7)六、主要零部件的设计 (8)七、模具装配图 (18)心得体会 (19)结束语 (20)前言模具课程设计是CAD/CAM专业教学计划安排的非常重要的教学实践环节,也是毕业设计的首选内容。
其目的在于巩固《模具结构及设计》所学知识,熟悉有关资料,树立正确的设计思想,掌握正确的设计方法,培养学生的实际工作能力。
通过模具结构设计,学生在工艺性分析、工艺方案论证、、3、工件结构:结构简单,形状对称。
结论:适合冲裁二、冲压件的工艺方案确定通过以上对该零件的结构、形状及精度的分析,并结合零件的生产批量。
该零件采用落料单工序就可完成冲压加工。
三、确定模具总体结构1、模具类型的选择由冲压工艺分析可知,采用单工序模冲压,所以本套模具类型为单工序落料模。
2、定位方式的选择因为该模具采用条料,控制条料得送进方向采用导料销;控制条料的送进步距采用挡料销。
3、导柱、导套位置的选择由于落料件的结构简单,大批量生产都使用导向装置。
导向方式主要该冲裁件厚度t=1mm,外形由直线组成,且对称分布,在选取搭边量时可看成方形类零件。
查表p94 2—1—8(教材),工件间最小搭边值a1=1.5mm,沿边最小搭边值a=2mm,以下面排样方式中的数个零件为单位计算零件利用率。
单个零件面积A0=12288mm2。
1.排样方案的确定方案一:方案二:方案一:材料利用率=A0/A=5×12288/650×100=94.52%方案二:材料利用率=A 0/A=5×12288/490×132=94.99%比较以上两种方案,知方案二排样材料利用率最高,故采用此排样。
2、凸、凹模刃口尺寸的计算由于此工件在模具磨损后对其影响不一,所以采用配合加工的方法。
查 书本p96表2–4–14、2–4–15.m ax Z =0.13,min Z =0.10,x=0.75凹模尺寸:∆——冲裁件制造公差 x ——系数3、冲、推、卸料力的计算 (1)冲裁力F 落为: F 落=KLt 其中,L=(A+D)×2以上公式中:F ——冲裁力;K——安全系数,一般取K=1.3;L——冲裁周边长度;t——材料厚度;——材料抗拉强度MPa;则有:L=(A+D)×2=(96+128)×2=448(mm)材料厚度t=1mm;材料: Q235,参考相关资料,其抗拉强度=365Mpa, 则:则:F=0.04×181=7.24(kN)总冲压力F 总=F 落+ Fx + Ft=181+7.24+49.775=238.015(kN)4、压力机公称压力的计算选用的压力机公称压力P≥(1.3~1.5) F 总取系数为1.5,则P≥1.5F总=1.5×238.015=357.0225(kN)5、冲裁压力中心的确定由于该落料零件是为对称零件,故冲裁压力中心即为该落料件的对称中心。
项目1单工序模具设计

任务实施
1.方案分析 设计时必须根据冲压件的形状、批量及精度要求来选择是否需要导向 装置,其选用时应从以下几个方面进行综合考虑。 (1)从冲模的应用范围来看,无导向冲模主要适用于中小批量生产, 导柱模主要适用于大批量生产,而且零件精度要求较高的情况;导板 模主要适用于级进模和单工序冲模的冲裁,导板可兼作卸料板,并对
图1.3冲裁件的尺寸基准
三、制定实施计划
各小组根据下达的工作任务制定具体 的实施计划。
四、工作任务实施
学生根据小组的计划独立完成工作任务。
任务实施
1.审图 该零件尺寸齐全,材料牌号、材料厚度、生产批量均已说明,冲压件
虽未注明尺寸公差,设计时其极限偏差数值可按IT14级处理, 查参
考资料[14]知,按“入体”原则把尺寸逐个改为单向公差(目的方便 以后的刃口尺寸计算)。尺寸34、17、116属被包容尺寸,上偏差为
图1.2冲裁件的结构工艺性图
(5)冲孔时,因受凸模强度和刚度的限制,孔径不宜太小,否则容易折断或 压弯。
2)尺寸精度和粗糙度要求 (1)普通冲裁件的内外形的经济精度不高于IT11级; (2)冲孔精度(最好低于IT9级)比落料精度(最好低于IT10级)高 一级; (3)冲裁件的粗糙度Ra一般低于6.3μ m,但高于12.5μ m ; 3)冲裁材料要求 (1)对冲裁材料机械性能的要求:有一定强度和韧性,避免过硬、 过软、过脆。 (2)对材料规格的要求:材料厚度公差应符合国家标准,厚薄均匀, 避免采用边角料。 (3)冲裁件材料的选取原则:廉价代贵重,薄料代厚料,黑色代有 色金属。
1—上模座;2—卸料弹簧;3—卸料螺 钉;4—螺钉;5—模柄;6—防转销; 7—销;8—垫板;9—凸模固定板; 10—落料凸模;11—卸料板;12—落 料凹模;13—顶件板;14—下模座 ;15—顶杆;16—板;17—螺栓;18— 固定挡料销;19—导柱;20—导套; 21—螺母;22—橡皮 图 1.11 导柱式落料模
单工序冲裁模制作

阶段三:
一、爆炸图 爆炸图是对整套模 具的一个分解,可 以让我们比较明显 的看到模具中的各 个零件及其在整套 模具中的位置
二、工程图
工程图绘制 徐 周:凸模固定板 殷柏露:下模座 袁 冬:落料凹模、垫板 高暄晗:上模座 梅 杰:落料凸模
三、工程图制作方法
• 打开实体,新建工程图界面,选择合适的表
实体造型能力、组装能力、绘制工程图能力等综 合应用能力。 专题训练是重要的实践环节,可以培养运用所学 习的知识和技能从事实际工程设计和加工等一系 列工作的主要环节。通过这个环节能够得以巩固 和拓展所学习的知识,实现了专业课程之间的有 机结合,相辅相成,培养了我们面对实际问题, 思考,分析,解决问题的能力,以及表达能力。 通过对落料模各主要零件的造型,落料模零件的 组装,主要零件的工程图生成过程,使我们对 PRO/ENGINEER有了更深刻的了解。 培养小组成员团结合作能力
工作分配:
• • • •
徐 周:导套、卸料螺钉、横销、凸模、导柱 殷柏露:下模座、凸模固定板、摸柄、防转销 袁 冬:上模座、螺钉、垫板、挡料销、橡胶 高暄晗:销钉、凹模、导料销、卸料板、螺钉
实体模型主要操作步骤
• 拉伸--草绘环境--完成草绘---选择深度选项 • 旋转--截面草绘环境---完成草绘---选择深度选项, • • •
•
•
• 旋转特征:单击旋转工具进入截面草绘环境,完 • • •
成草绘,选择深度选项,输入旋转角度值,完成 旋转特征。 用螺旋扫描特征创建切削螺纹 拉伸特征:单击拉伸工具,截面草绘环境,完成 草绘,选择深度选项,输入数值,完成拉伸基础 特征。 倒圆角特征:单击倒圆角工具按钮,出现倒圆角 特征操控板,单击【设置】,选取参照曲面,输 入倒圆角半径,完成倒圆角特征 。
导柱式单工序落料模鹏飞

导柱式单工序落料模1螺帽2倒料螺钉3挡料销4弹簧5凸模固定板6销钉7模柄8垫板9止动销10卸料螺钉11上模座12凸摸13导套14导柱15卸料板16凹模17内六角螺钉18下模座工作过程:条料沿导料螺栓2送至挡料销3定位后进行落料.箍在凸摸上的边料靠弹压卸料装置进行卸料,弹压卸料装置由卸料板15,卸料螺钉10和弹簧4组成.在凸凹模进行冲裁工作之前由于弹簧力的作用,卸料板先压住条料上模继续下压是进行冲裁分离此时弹簧被压缩.上模回程时,弹簧恢复推动卸料板把箍在凸摸上边料卸下导板式单工序落料模1-模柄2-止动销3-上模座4、8-内六角螺钉5-凸模6-垫板7-凸模固定板9-导板10-导料板11-承料板12-螺钉13-凹模14-圆柱销15-下模座16-固定挡料销17-止动销18-限位销19-弹簧20-始用挡料销工作过程〔原理〕图为导板式简单落料模.其上、下模的导向是依靠导板9与凸模5的间隙配合〔一般为H7/h6〕进行的,故称导板模.冲模的工作零件为凸模5和凹模13;定位零件为导料板10和固定挡料销16、始用挡料销20;导向零件是导板9〔兼起固定卸料板作用〕;支承零件是凸模固定板7、垫板6、上模座3、模柄1、下模座15;此外还有紧固螺钉、销钉等.根据排样的需要,这副冲模的固定挡料销所设置的位置对首次冲裁起不到定位作用,为此采用了始用挡料销20.在首件冲裁之前,用手将始用挡料销压入以限定条料的位置,在以后各次冲裁中,放开始用挡料销,始用挡料销被弹簧弹出,不再起挡料作用,而靠固定挡料销对条料定位.工作过程:工作零件为凸模2和凹模5,定位零件为两个导料板4和定位板7,导料板4对条料送进起导向作用,定位板7是限制条料的送进距离;卸料零件为两个固定卸料板3;支承零件为上模座〔带模柄〕l和下模座6;此外还有紧固螺钉等.上、下模之间没有直接导向关系.分离后的冲件靠凸模直接从凹模洞口依次推出.箍在凸模上的废料由固定卸料板刮下.导柱式冲孔模1-上模座2、18-圆柱销3-导柱4-凹模5-定位圈6、7、8、15-凸模9-导套10-弹簧11-下模座12-卸料螺钉13-凸模固定板14-垫板16-模柄17-止动销19、20-内六角螺钉21-卸料板工作过程〔原理〕:送料至5定位圈,上模下行,由卸料板压紧工件凸模下行冲孔磨料从凸模下落,上模上行卸料板卸料导板式侧面冲孔模1 / 21-摇臂2-定位销3-上模座4-螺钉5-凸模6-凹模7-凹模体8-支架9-底座10-螺钉11-导板12-销钉13-压缩弹簧斜楔式水平冲孔模1-斜楔2-座板3-弹簧板4-滑块5-凸模6-凹模全长导向结构的小孔冲模1-下模座2、5-导套3-凹模4—导柱6-弹压卸料板7-凸模8—托板9-凸模护套10-扇形块11-扇形块固定板12-凸模固定板13-垫板14-弹簧15-阶梯螺钉16-上模座17-模柄超短凸模的小孔冲模1、9-定位板2、3、4-小凸模5-冲击块7-小压板8-大压板10-侧压块双侧刃定距的冲孔落料级进模1-内六角螺钉2-销钉3-模柄4-卸料螺钉5-垫板6-上模座7-凸模固定板8、9、10-凸模11-导料板12-承料板13-卸料板14-凹模15-下模座16-侧刃17-侧刃挡块工作过程〔原理〕:上下模用导板导向,冲孔凸模3与落料凸模4之间的距离就是送料步距送料时固定挡料销6进行初定位,由两个装在落料凸模上的导正销5进行精定位,导正销与落料凸模的配合为H7/r6其连接应保证在修模凸模时的装拆方便因此落料凹模安装导正销的孔是通孔,导正销的头部的形状应有利于在导正时插入已冲的孔,它与孔的配合应略有间隙.为了首件的正确定距,在带导正销的级进模中长采用始用挡料装置.它安装在导板下的导料板中间.在条料上冲制首件时,用手推始用挡料销7,使它从导料板中伸出来抵住条料的前端即可冲第一件上的两个孔.以后各次冲裁是就都由固定挡料销6控制送料步距做粗定位侧刃定距的弹压导板级进模1、10-导柱2-弹压导板3、11-导套4-导板镶块5-卸料螺钉6-凸模固定板7-凸模8-上模座9-限位柱12-导料板13-凹模14-下模座15-侧刃挡块工作过程〔原理〕:送料到侧刃进行送料定距上模座下行带动凸模下行对板料施加压力冲出工件由卸料螺钉带动弹压导板进行卸料.倒装式复合模1-下模座2-导柱3、20-弹簧4-卸料板5-活动挡料销6-导套7-上模座8-凸模固定板9-推件块10-连接推杆11-推板12-打杆13-模柄14、16-冲孔凸模15-垫板17-落料凹模18-凸凹模19-固定板21-卸料螺钉22-导料销工作过程〔原理〕:送料到定位销,上模下行,压料凸模凸模冲孔,上模上行卸料板卸料,反复循环.正装式复合模1-打杆2-模柄3-推板4-推杆5-卸料螺钉6-凸凹模7-卸料板8-落料凹模9-顶件块10-带肩顶杆11-冲孔凸模12-挡料销13-导料销2 / 2。
- 1、下载文档前请自行甄别文档内容的完整性,平台不提供额外的编辑、内容补充、找答案等附加服务。
- 2、"仅部分预览"的文档,不可在线预览部分如存在完整性等问题,可反馈申请退款(可完整预览的文档不适用该条件!)。
- 3、如文档侵犯您的权益,请联系客服反馈,我们会尽快为您处理(人工客服工作时间:9:00-18:30)。
第三章单工序冲裁模的装配工艺
一、凸模与凸模固定板的安装
1.钳工在凸模固定板上划线制作三个M6螺纹孔。
2.将一头固定凸模的孔用什锦锉扩成45度的倒角。
3.在油压机平台下放两块等高垫铁,将凸模固定板扩成45度的倒角一面向上平放在两块等高垫铁上。
4.将凸模淬火的一头用金相砂纸稍稍倒钝,用刀口角尺校正垂直的放在凸模固定板上。
5.当凸模淬火的一头的刃口完全覆盖住凸模固定板上的孔时周边再滴一两滴机油,然后开动油压机。
6.当凸模的刃口进入凸模固定板一两毫米时,停机观或测量凸模与凸模固定板两者之间是否仍然垂直?如不垂直需再次校正,定位后方可压入。
7.如仍然垂直即可缓缓压入直到凸模比凸模固定板高出0.5毫米时停止。
8.取出凸模固定板主件凸模朝下平放在两块等高垫铁上,再用榔头将凸模多出的0.5毫米部分敲打到45度倒角中去,直到填满间隙为止。
9.送到平磨磨平铆接部分,凸模与凸模固定板的安装就结束。
二、上模座与模柄的安装
1. 将模柄装夹在三爪卡盘上,将上模座旋紧在模柄上。
2. 将旋好的模柄朝下平放在两块等高垫铁上。
3. 在骑缝处按图打样冲眼,制作M6螺纹孔。
4. 将M6螺纹旋入。
三、上模部分的安装
1. 用平行夹按图将上模座、上垫板、凸模固定板的组合件夹在一起,眼睛观察
要上下左右对称、平行后再收紧平行夹中的螺杆。
2. 将两块等高垫铁放在台钻平板上,装夹好的组合件模柄朝下平放在两块等高垫铁上。
用ø5.2钻头在M6的螺孔中钻孔,要求打通孔。
3. 拆去平行夹分别将上模座、上垫板中的孔扩到ø6.5。
4. 将上模座的模柄朝上放在等高垫铁上,再扩孔ø10.5,深度只要将内六角螺
钉头埋入上模座即可。
5. 将以上所打的孔全部倒角,去毛刺。
6. 再将以上三件用M6内六角螺钉旋入上紧即可。
四、下模部分的安装
1. 将凹模套在凸模上,然后将上下模座合上,闭合高度只要凸模进入凹模口内
0.5毫米即可。
2. 将模架放在两等高垫铁上,用平行夹夹住凹模与下模座,再将上下模座分开。
3. 将两块等高垫铁放在台钻平板上,装夹好的下模座组合件平放在两块等高垫铁上。
用ø5.2钻头在M6螺孔中钻通孔。
4. 拆去平行夹分别将下模座孔扩到ø6.5。
5. 下模座背面再扩孔ø10.5,深度只要将内六角螺钉头埋入下模座即可。
6. 将以上所打的孔全部倒角,去毛刺。
7. 再将以上两件用M6内六角螺钉旋入上紧即可。
五、刀口间隙的调整
1. 将上模部分用内六角螺钉固定好,下模部分的内六角螺钉不要紧固。
2. 合上上下模座,在凸模靠近凹模时要看仔细,将凸模慢慢放进凹模口内,如
有误差应用铜棒轻敲凹模,再试着看能否进入如若不行再调,直到凸模进入凹模口内0.5毫米为止。
3. 调好以后将下模部分的内六角螺钉紧固。
4. 将上上下模座稍许分开,用纸试切一下,观察断面是否有毛边,如断面有毛
边不整齐,就要重新调整刀口,直到满意为止。
六、销钉的安装
1. 刀口间隙的调整好后就可安装销钉了,可按图钻上模和分下模部分的销钉底
孔。
2. 用铰刀分别铰出上模和下模部分的销钉孔。
七、卸料板的安装
1. 将卸料板套在凸模上,复出卸料板三螺纹孔在凸模固定板上的相对位置。
2. 拆下卸料板,用ø6.5钻头扩出三卸料螺钉过孔。
3. 在上模座顶部用扩ø10.5孔,深度只要将卸料螺钉头埋入上模座即可。
4. 将卸料板安装在上模上。
5. 将下模部分拆开,凹模套在凸模上。
6. 在钻床上复出卸料板上导向钉、定位钉孔的相对位置。
7. 将上模部分的卸料板拆开,将复出的孔位,按图纸要求钻出让位孔。
八、冲裁模的总装配
1. 分别将上下模拆开,凸模、凹模送磨床刃磨刀口。
2. 将各块模板上未倒角的孔都倒角。
3. 再将模具重新装配好,卸料板暂时不装。
4. 再用纸试切一下,看是否达标?如不达标需要再调。
5. 达标后再将卸料板装上。
6. 送压机试模。
第四章实训报告的内容格式
一、画模具装配图与零件图
1. 共四小组,每一小组画一完整的装配图,画图人签名,小组成员写上学号。
2. 小组成员每人画至少一张零件图,并签名。
3. 希望大家认真对待,这一套装配图与零件图将占50%的比分。
二、各种工艺尺寸的计算
1. 压力中心的计算
2. 凸凹模冲裁间隙的计算
3. 冲裁力、卸料力、压料力的计算
4. 计算需选用多大吨位的压力机
三、排样图及尺寸的计算
1.计算搭边值及搭边间隙
2.画出排样图。