深孔加工动力减振镗杆的有限元分析
导致CNC加工中心镗孔加工时发生颤振因素
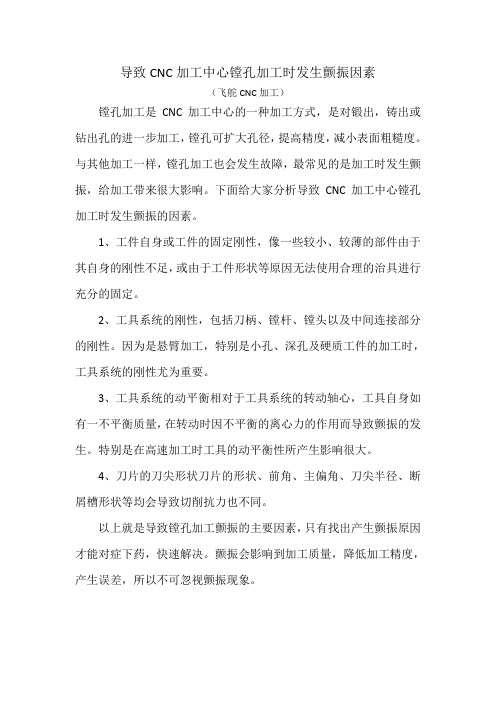
导致CNC加工中心镗孔加工时发生颤振因素
(飞舵CNC加工)
镗孔加工是CNC加工中心的一种加工方式,是对锻出,铸出或钻出孔的进一步加工,镗孔可扩大孔径,提高精度,减小表面粗糙度。
与其他加工一样,镗孔加工也会发生故障,最常见的是加工时发生颤振,给加工带来很大影响。
下面给大家分析导致CNC加工中心镗孔加工时发生颤振的因素。
1、工件自身或工件的固定刚性,像一些较小、较薄的部件由于其自身的刚性不足,或由于工件形状等原因无法使用合理的治具进行充分的固定。
2、工具系统的刚性,包括刀柄、镗杆、镗头以及中间连接部分的刚性。
因为是悬臂加工,特别是小孔、深孔及硬质工件的加工时,工具系统的刚性尤为重要。
3、工具系统的动平衡相对于工具系统的转动轴心,工具自身如有一不平衡质量,在转动时因不平衡的离心力的作用而导致颤振的发生。
特别是在高速加工时工具的动平衡性所产生影响很大。
4、刀片的刀尖形状刀片的形状、前角、主偏角、刀尖半径、断屑槽形状等均会导致切削抗力也不同。
以上就是导致镗孔加工颤振的主要因素,只有找出产生颤振原因才能对症下药,快速解决。
颤振会影响到加工质量,降低加工精度,产生误差,所以不可忽视颤振现象。
刀具减震技术:双级调谐阻尼器减振的镗刀杆结构设计
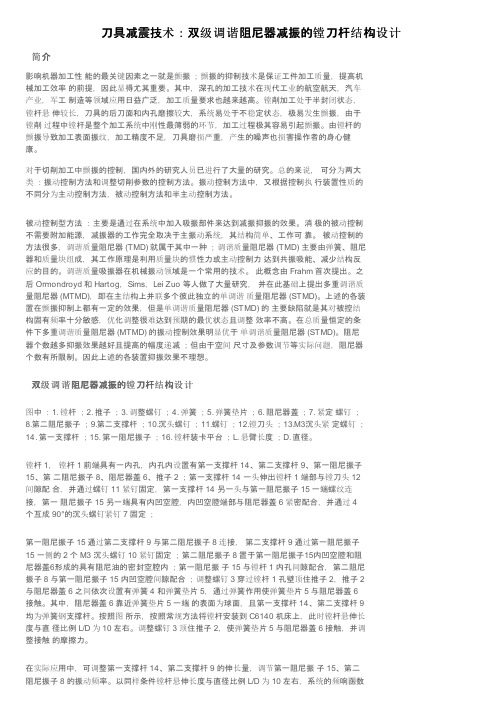
刀具减震技术:双级调谐阻尼器减振的镗刀杆结构设计简介影响机器加工性能的最关键因素之一就是颤振;颤振的抑制技术是保证工件加工质量,提高机械加工效率的前提,因此显得尤其重要。
其中,深孔的加工技术在现代工业的航空航天,汽车产业,军工制造等领域应用日益广泛,加工质量要求也越来越高。
镗削加工处于半封闭状态,镗杆悬伸较长,刀具的后刀面和内孔磨擦较大,系统易处于不稳定状态,极易发生颤振,由于镗削过程中镗杆是整个加工系统中刚性最薄弱的环节,加工过程极其容易引起颤振。
由镗杆的颤振导致加工表面振纹,加工精度不足,刀具磨损严重,产生的噪声也损害操作者的身心健康。
对于切削加工中颤振的控制,国内外的研究人员已进行了大量的研究。
总的来说,可分为两大类:振动控制方法和调整切削参数的控制方法。
振动控制方法中,又根据控制执行装置性质的不同分为主动控制方法,被动控制方法和半主动控制方法。
被动控制型方法:主要是通过在系统中加入吸振部件来达到减振抑振的效果。
消极的被动控制不需要附加能源,减振器的工作完全取决于主振动系统,其结构简单、工作可靠。
被动控制的方法很多,调谐质量阻尼器 (TMD) 就属于其中一种;调谐质量阻尼器 (TMD) 主要由弹簧、阻尼器和质量块组成,其工作原理是利用质量块的惯性力或主动控制力达到共振吸能、减少结构反应的目的。
调谐质量吸振器在机械振动领域是一个常用的技术。
此概念由 Frahm 首次提出。
之后 Ormondroyd 和 Hartog,Sims,Lei Zuo 等人做了大量研究,并在此基础上提出多重调谐质量阻尼器 (MTMD),即在主结构上并联多个彼此独立的单调谐质量阻尼器 (STMD)。
上述的各装置在颤振抑制上都有一定的效果,但是单调谐质量阻尼器 (STMD) 的主要缺陷就是其对被控结构固有频率十分敏感,优化调整很难达到预期的最优状态且调整效率不高。
在总质量恒定的条件下多重调谐质量阻尼器 (MTMD) 的振动控制效果明显优于单调谐质量阻尼器 (STMD)。
减震镗孔刀杆原理

减震镗孔刀杆原理The principle of a damping boring bar is vital in achieving smooth and accurate hole boring operations. 减震镗孔刀杆的原理对于实现平稳准确的孔加工操作至关重要。
A damping boring bar is designed to reduce vibrations and improve the surface finish of the bored holes, which is essential for achieving high-quality workpieces. 减震镗孔刀杆旨在减少振动并提高镗孔的表面光洁度,这对于获得高质量的工件至关重要。
The primary principle behind a damping boring bar lies in its abilityto absorb and dissipate the energy generated during the cutting process. 减震镗孔刀杆的主要原理在于其能够吸收和消散切削过程中产生的能量。
This is achieved through the use of damping materials, suchas rubber or composite structures, which are incorporated into the design of the boring bar. 这是通过使用减振材料,如橡胶或复合结构,将其融入到镗孔刀杆的设计中来实现的。
When the cutting forces act on the damping boring bar, the damping materials deform and absorb the energy, thereby reducing the amplitude of vibration. 当切削力作用于减震镗孔刀杆时,减震材料变形并吸收能量,从而降低振动的幅度。
减振镗刀的设计与分析
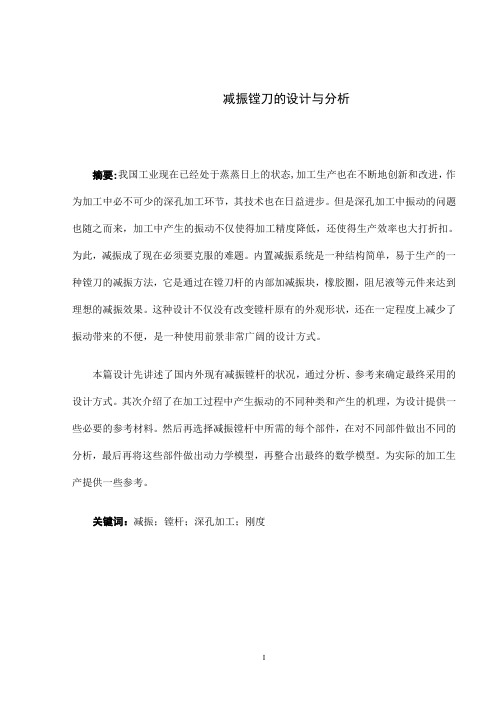
减振镗刀的设计与分析摘要:我国工业现在已经处于蒸蒸日上的状态,加工生产也在不断地创新和改进,作为加工中必不可少的深孔加工环节,其技术也在日益进步。
但是深孔加工中振动的问题也随之而来,加工中产生的振动不仅使得加工精度降低,还使得生产效率也大打折扣。
为此,减振成了现在必须要克服的难题。
内置减振系统是一种结构简单,易于生产的一种镗刀的减振方法,它是通过在镗刀杆的内部加减振块,橡胶圈,阻尼液等元件来达到理想的减振效果。
这种设计不仅没有改变镗杆原有的外观形状,还在一定程度上减少了振动带来的不便,是一种使用前景非常广阔的设计方式。
本篇设计先讲述了国内外现有减振镗杆的状况,通过分析、参考来确定最终采用的设计方式。
其次介绍了在加工过程中产生振动的不同种类和产生的机理,为设计提供一些必要的参考材料。
然后再选择减振镗杆中所需的每个部件,在对不同部件做出不同的分析,最后再将这些部件做出动力学模型,再整合出最终的数学模型。
为实际的加工生产提供一些参考。
关键词:减振;镗杆;深孔加工;刚度Design and analysis of vibration boring cutterAbstract : Now our industry is in a flourishing state, production is constantly innovating and improving, as an essential part of the processing of deep hole machining technology is also in progress. Vibration problems in the deep hole machining also come, lower vibration produced not only makes the machining accuracy in the processing, but less productive. To this end, now has to overcome the problem of vibration reduction. Built-in vibration reduction system is a simple structure, easy to produce a boring tool vibration method, it is by boring bar internal and vibration damping, and the rubber ring, the vibration damping elements such as liquid to achieve the desired effect. This design not only failed to change the boring bar is the original appearance of the shape, but also to a certain extent, reduce the inconvenience of vibration, is a very broad prospects for use of design.Absorption boring bar, through analysis, to determine the final reference design. Next introduced the vibration produced during processing of different kinds and the mechanism, is designed to provide the necessary reference materials. Then the vibration absorption boring bar for each component in different parts and different analysis, then make them dynamic model in the integration of the final model. Provide your reference for actual production.Key words : vibration; boring bars; deep holes; stiffness目录摘要 (I)Abstract (II)目录 (III)1 绪论 (1)1.1 课题背景及研究意义 (1)1.2 减振镗杆的国内外研究成果与发展的趋势 (2)1.3 国内的研究现状与发展趋势 (6)1.4 小结 (6)2 振动的机理分析和不同的减振措施 (7)2.1 切削中振动的分类及产生的原因 (7)2.2 减振的主要原则 (8)2.3 控制机械加工振动的途径 (8)2.3.1 消除或者减弱发生振动的条件 (8)2.3.2 改良工艺系统中的动态特性 (9)2.3.3 选用减振装置 (10)3 减振镗杆的结构设计 (16)3.1 减振镗刀的杆材料选择 (16)3.2 镗杆的基本结构设计 (16)3.3 冷却管的设计 (17)3.4 减振装置的组成元件 (18)3.4.1 阻尼夜的选取 (18)3.4.2 弹性元件的选择 (19)3.4.3 减振块的选择 (21)3.5 减振镗杆内部整体结构的设计 (22)3.6 刀头的设计 (23)4 动力减振系统的数学模型 (24)4.1 动力减振镗杆系统的力学模型 (24)4.2 建立动力减振系统的动力学分析模型 (27)4.3 建立动力减振镗杆的数学模型 (29)4.4 本章小结 (29)5 结论与展望 (30)5.1 全文总结 (30)5.2 展望 (30)参考文献 (32)致谢 (34)1 绪论1.1 课题背景及研究意义现今,制造业的发展已成为社会进步的标准,加工中的高速和超高速加工现已成为主流趋势,企业对加工精度的标准和要求也越来越高,在金属切削这块加工领域里,特别是在高速加工深孔的时候,由于孔的形状要求和精度要求比较高,因此刀具加工产生的振动一直是阻碍加工精度的最大障碍之一,它的产生严重影响了零件的加工精度与表面的粗糙度,阻碍了切削加工向着高速度、高精度和高强度方向的发展。
加工深孔时刀具振动现象的分析
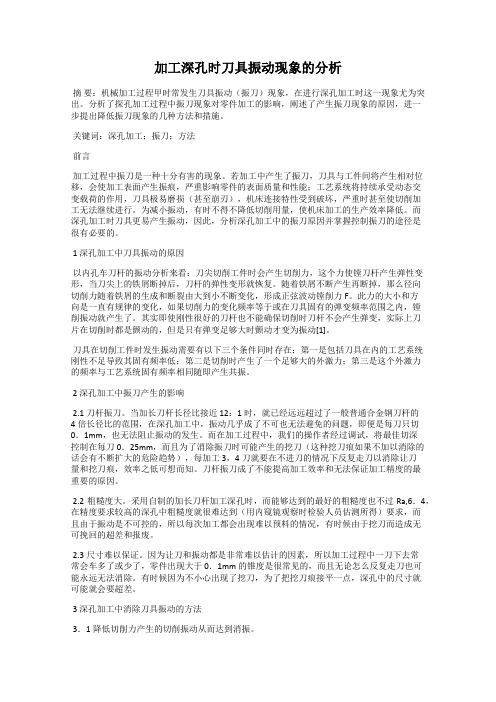
加工深孔时刀具振动现象的分析摘要:机械加工过程甲时常发生刀具振动(振刀)现象,在进行深孔加工时这一现象尤为突出。
分析了探孔加工过程中振刀现象对零件加工的影响,阐述了产生振刀现象的原因,进一步提出降低振刀现象的几种方法和措施。
关键词:深孔加工;振刀;方法前言加工过程中振刀是一种十分有害的现象。
若加工中产生了振刀,刀具与工件间将产生相对位移,会使加工表面产生振痕,严重影响零件的表面质量和性能;工艺系统将持续承受动态交变载荷的作用,刀具极易磨损(甚至崩刃),机床连接特性受到破坏,严重时甚至使切削加工无法继续进行。
为减小振动,有时不得不降低切削用量,使机床加工的生产效率降低。
而深孔加工时刀具更易产生振动,因此,分析深孔加工中的振刀原因并掌握控制振刀的途径是很有必要的。
1 深孔加工中刀具振动的原因以内孔车刀杆的振动分析来看:刀尖切削工件时会产生切削力,这个力使镗刀杆产生弹性变形,当刀尖上的铁屑断掉后,刀杆的弹性变形就恢复。
随着铁屑不断产生再断掉,那么径向切削力随着铁屑的生成和断裂由大到小不断变化,形成正弦波动镗削力F。
此力的大小和方向是一直有规律的变化,如果切削力的变化频率等于或在刀具固有的弹变频率范围之内,镗削振动就产生了。
其实即使刚性很好的刀杆也不能确保切削时刀杆不会产生弹变,实际上刀片在切削时都是颤动的,但是只有弹变足够大时颤动才变为振动[1]。
刀具在切削工件时发生振动需要有以下三个条件同时存在:第一是包括刀具在内的工艺系统刚性不足导致其固有频率低;第二是切削时产生了一个足够大的外激力;第三是这个外激力的频率与工艺系统固有频率相同随即产生共振。
2 深孔加工中振刀产生的影响2.1刀杆振刀。
当加长刀杆长径比接近12:1时,就已经远远超过了一般普通合金钢刀杆的4倍长径比的范围,在深孔加工中,振动几乎成了不可也无法避免的问题,即便是每刀只切0.1mm,也无法阻止振动的发生。
而在加工过程中,我们的操作者经过调试,将最佳切深控制在每刀0.25mm,而且为了消除振刀时可能产生的挖刀(这种挖刀痕如果不加以消除的话会有不断扩大的危险趋势),每加工3,4刀就要在不进刀的情况下反复走刀以消除让刀量和挖刀痕,效率之低可想而知。
减振镗杆的有限元分析

优秀设计目录中文摘要...................................... 错误!未定义书签。
英文摘要...................................... 错误!未定义书签。
第1章减振镗杆的国内外研究水平和发展趋势 (3)第2章颤振的机理及稳定性分析理论 (5)2.1 再生颤振的机理 (5)2.2 再生颤振系统 (6)2.3 系统切削过程动态模型 (7)2.4 镗削过程稳定性分析理论与稳定性图 (8)第3章减振镗杆的动力学模型 (13)3.1 减振镗杆的设计 (15)3.2 减振镗杆模型的分析 (17)3.3 在ANSYS程序中进行应力应变分析 (19)3.4 模型在频域内的仿真结果 (19)结论与展望 (23)致谢 (24)参考文献: (25)附件I 英文文献翻译 (26)附件II 英文文献原文 (30)减振镗杆的有限元分析摘要:介绍了深孔镗削加工过程中产生振颤的机理,建立了减振镗杆的动力学模型。
论述动力减振镗杆的工作原理,通过简化动力学模型建立微分方程。
在理论基础上通过实验分析动力减振镗杆的减振效果和动态性能,并测定其最佳状态下的性能参数。
试验结果确定了动力减振器的减振特点,为实际生产加工给出参考。
关键词:减振镗杆深孔镗削性能参数Finite element analysis of Damping Boring Bar Abstract : This paper introduced the mechanism of vibration in the process of deep hole boring , developed a dynamic modal of the damping boring bar. The working principle of a boring bar which has a dynamic vibration absorber is discussed The system’s differential equation is built according to the simple dynamical model. Based on theory,the dynamic performance of a boring bar is researched by experiment and the performance parameters at the best state are gotten. The result of experiment shows the character of dynamic vibration absorber,and gives a reference for the actual manufacture.Key words:Damping boring bar Deep hole boring Performance parameters第1章减振镗杆的国内外研究水平和发展趋势在机械生产过程当中,切削系统的加工精度及稳定性很大程度上取决与结构的刚度和切削过程中颤振对其产生的影响,刚性不足和颤振的产生不仅制约了切削系统在加工过程中的切削效率,而且还会在加工工件的表面留下振纹,影响加工精度。
重型数控机床深孔加工动力减振镗杆的设计与仿真

关键词 : 减振 ; 镗刀刀杆 ; 动刚度 ; 动力学仿真 中图分类号 : G 1 . T 73 3 文献标识 码 : 文章编 号 :10 - 6 3 20 ) 1 03 — 3 A 0 7 2 8 (06 0 — 19 0
D sg n muain o a y NC c ie To l y a c l e in a d Si lt fHe v o Ma hn o n mia D
d p oe hn igwa h ta ga dz ste d n mi s f eso e b r gb rt ein ab rw t irt n o m an v l ikn y ta g rn i h y a c t n s ft o n a o d s a i avbai t e i h i g h o a s rt n ss m eb r gb r hsat l ssa v n e ot ae ADAMSa d AN Y ul eitga- b op i y t i t o n a.T i ri eu e d a c dsf rm o e nh i c w n S St b i t ne rt o dh e ytm lt r b s do h oyo n miso l —b d ytm ,a d v iaetea c rc f h e i r d sse pa om a e nte r f f Dy a c fMut i o yS se n a d t c ua yo ed s f l h t n g o h ay N c ietosd n mia irt n a srt n b r gb rfrd e —h l rc sig h eut fs l— e v C ma hn o l y a c l b ai b o i o n a e p v o p o i o oep o esn .T ers l o i a mu t n d mo s ae a ed sg a n a c ed n mi s f eso eb r g b r e u eteq a t o da i e n t tst t e in c n e h n e t y a c t n s ft o n a ,rd c h u ni fr il o r h t h h i h i  ̄ a vb ain a d i rv es r c rc sig q ai . irt n mpo et uf ep o e s u l y o h a n t Ke r s vb ain a s rt n;b r gb r y a c s f es y a c lsmuain ywo d : irt b o i o p o o n a ;d n mi t n s ;D n mia i lt i i o
镗杆自激振动及消振实验
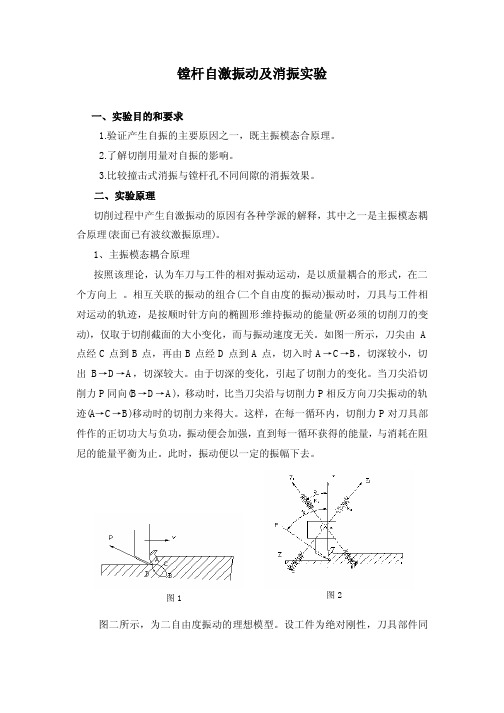
米)
振动情况
4 切削用量对自振的影响
表四
F(毫米/转)
0.1
0.21
0.42
振动情况
这样在每一循环内切削力p对刀具部件作的正切功大与负功振动便会加强直到每一循环获得的能量与消耗在阻尼的能量平衡为止
镗杆自激振动及消振实验
一、实验目的和要求 1.验证产生自振的主要原因之一,既主振模态合原理。 2.了解切削用量对自振的影响。 3.比较撞击式消振与镗杆孔不同间隙的消振效果。 二、实验原理
切削过程中产生自激振动的原因有各种学派的解释,其中之一是主振模态耦 合原理(表面已有波纹激振原理)。
三、实验设备及试件 1、机床:C6140 2、特殊刚性刀架。 3、可改变钢性主动方位的削扁镗杆。 4、消振镗杆(见图四)。 5、试件: (1)钢套 8 个:d1=90—100,d2=50mm,L1=90mm
45 钢 (2)钢套 16 个:d1=90—100,d2=50mm,L1=45mm
45 钢 (3)钢套 8 个:d1=90—100,d2=50mm,L1=60mm
4、切削用量对自振的影响
切削条件如下:
切削用量:进给量 f=0.1 毫米/转,转速 n=90 转/分,切深αР=0.2 毫米。 刀具角度:γo=5°,αo=15°,Kr=60°,Kr=45° 镗杆:圆截面镗杆。
实验时,其他条件不变,改变进给量 f,镗削后振动情况记录在附表四内。
五、拟写实验报告
1.实验名称
2、比较三种不同机构镗杆(θ=135°削扁镗杆,θ=45°削扁镗杆,圆镗
杆)的动态稳定性:
实验时,用上三种镗杆,在同一试件上各镗一段孔:比较三段加工表面振
纹。把结果记录在附表二内。
3、实验撞击块消振效果:
基于有限元的深孔镗削仿真及分析

中图分类号:TG537
文献标识码:A
文章编号:1672-545X(2019)12-0019-04
0 引言
在机械制造业中,一般将孔深超过孔径 5 倍的 圆柱孔称为深孔[1]。深孔的加工方式主要有:钻孔、扩 孔、铰孔、镗孔等。因为镗削加工具有高质高效的特 点,所以在加工大型零件的深孔时,一般都采用镗削 加工镗削。由于深孔镗削加工的轴向距离较长,刀具 磨损和崩刃的问题会严重影响加工的连续性,导致 加工表面质量不均匀,加工效率低且废品率高。通过 有限元分析,优化刀具的几何参数,可以降低切削 力,使切削过程更流畅,降低切削区域的温度,使刀 具的耐用度增强,从而提高加工效率。
19
Equipment Manufacturing Technology No.12,2019
变率;T 为工件温度,Troom 和 Tmelt 分别是室温 (20 益) 和材料的熔点。
AISI4340 材 料 的 屈 服 应 力 变 化 曲 线 如 图 1 所 示。
减振刀具系统的动力学分析说明书

1 引言1.1 课题研究背景切削颤振是金属切削过程中刀具与工件之间产生的一种十分强烈的相对振动,其产生的原因和发生、发展的规律与切削加工过程本身及金属切削系统动态特性都有着内在的本质联系,影响因素很多,是一个非常复杂的机械振动现象。
由于振动机械的各主要构造和零件要长期承受交变载荷,于是包括疲劳失效在内的各种类型的损伤和破坏就成为影响设备使用性能和使用寿命的主要因素。
现代工业对工程质量、产品精度及可靠性都提出了愈来愈高的要求,研究和解决工业工程中出现的各种振动问题已成为一项急迫的任务。
因而在研制设计中,不仅要考虑静力效应,而且还要考虑动力效应。
根据传统的基于静力准则的机械结构设计方法是无法满足现代产品的设计要求的。
对承受动载荷的结构,采用结构动态设计方法是满足现代产品设计要求的有效方法,通过动态设计达到控制机械结构的振动水平,改善产品的质量,提高它的安全可靠性等目的,即“优生”。
这也是符合国际、国内机械结构设计技术发展方向的。
本课题就是通过有限元法对减振镗刀杆系统进行动力学分析,并利用ANSYS软件对系统的关键部件进行分析和模拟仿真,获得镗刀杆系统在加工条件下的变形、应力分布等信息。
镗削是一种用刀具扩大孔或其它圆形轮廓的内径车削工艺,其应用范围一般从半粗加工到精加工,所用刀具通常为单刃镗刀(称为镗杆)。
镗刀有三个基本元件:可转位刀片、刀杆和镗座。
镗座用于夹持刀杆,夹持长度通常约为刀杆直径的4倍。
装有刀片的刀杆从镗座中伸出的长度称为悬伸量(镗刀的无支承部分)。
悬伸量决定了镗孔的最大深度,是镗刀最重要的尺寸。
悬伸量过大会造成刀杆严重挠曲,引起振颤,从而破坏工件的表面质量,还可能使刀片过早失效。
这些都会降低加工效率。
对于大多数加工应用,用户都应该选用静刚度和动刚度尽可能高的镗刀。
静刚度反映镗刀承受因切削力而产生挠曲的能力,动刚度则反映镗刀抑制振动的能力。
本文的第3部分主要分析镗刀的静刚度。
文中资料来源于作者对镗刀挠曲的研究。
数控减振镗杆设计与分析

数控减振镗杆设计与分析数控减振镗杆是一种专用工具,广泛用于车床上驱动转子加工的过程。
数控减振镗杆的目的是在机械加工过程中减少振动和刀具的磨损,增加加工效率。
设计与分析:数控减振镗杆的设计需要考虑以下方面:杆的材质和结构:镗杆要求耐磨性和抗腐蚀性,并且需要满足强度和刚度的要求。
通常采用优质钢材或铝合金制造,具有较高的刚度和强度。
中空孔的设计:杆内还设置有中空孔,以便将冷却液引入,降低温度,延长工具的寿命。
设计考虑到镗杆的外径和内径,以及孔的位置和大小。
减振结构设计:减振结构是为了降低振动的产生和传递。
现代的减振结构主要是通过在镗杆内嵌入弹性材料来实现。
当切削力作用到刀具时,弹性材料会承担部分载荷,从而减轻振动。
设计要考虑弹性材料的种类和数量,以及减振结构的形状和位置。
分析:数控减振镗杆在工业自动化生产中扮演着重要的角色,在提高工作效率的同时,也保证了产品质量。
通过减少振动和刀具的磨损,就能够减轻轴承的负担,延长机械零件的寿命,降低生产成本。
此外,在智能化制造领域,数控减振镗杆的应用也越来越广泛。
随着人们对高精度、高效率要求的提高,数控减振镗杆已经成为自动化机械加工技术不可或缺的一部分。
总结:数控减振镗杆的设计和分析是一项非常重要的工作,涉及到材料、结构和性能等方面。
随着科技的发展和工业自动化的推进,数控减振镗杆将会在更多的领域得到应用。
我们需要加强技术研发和创新,提高产品质量和性能,以满足不同领域的需求。
相关数据分析是基于所收集到的数据的信息进行评估、归纳和综合的过程,旨在为决策和规划提供更好的依据和支撑。
下面我们以某家公司的销售数据为例进行分析。
该公司的销售数据分析:销售额:销售额是一个企业的核心指标之一,能够正确地反映企业的市场表现和经营状况。
该公司最近一年的销售额为3000万元,同比增长率为10%。
这表明公司的销售业绩良好,并且有增长趋势。
销售渠道:销售渠道是指企业销售产品或服务的途径,包括线上和线下渠道。
识别动力减振镗杆主系统等效参数的数学计算方法

识别动力减振镗杆主系统等效参数的数学计算方法何苗;孙蓓蓓【摘要】采用动力减振镗杆是解决深孔加工颤振的有效技术途径,为设计减振镗杆内部吸振器的最优参数,需要识别镗杆主系统在吸振器安装位置的等效质量和等效刚度.针对采用实验和仿真的传统等效参数识别方法效率不高的问题,提出一种新的简单高效的数学计算方法:基于欧拉—伯努利梁理论和分段连续条件,将镗杆视为非等截面梁,建立主系统模态的数学模型,求解出固有频率和固有振型函数;再根据最大动能不变原则,推导出了主系统等效质量的求解公式;求解出镗杆主系统所有等效参数.数值仿真结果表明,新的数学计算方法可简便高效地计算出动力减振镗杆的主系统参数,从而提高动力减振镗杆的设计效率,同时也适用于其他不等截面梁等效动力学参数的求解.【期刊名称】《振动与冲击》【年(卷),期】2019(038)006【总页数】6页(P194-198,244)【关键词】动力减振镗杆;等效参数;数学计算方法【作者】何苗;孙蓓蓓【作者单位】东南大学机械工程学院,南京211189;东南大学机械工程学院,南京211189【正文语种】中文【中图分类】TH128深孔镗削加工时镗杆的悬伸量较大,镗杆长径比越大刚度越低,越容易产生切削颤振,所以深孔加工一直是机械加工的难题,也是国内外学者研究的热点。
动力减振镗杆是在镗杆内部空腔放置一个有阻尼动力吸振器,可以有效地减少切削颤振,提高加工精度。
为了设计减振镗杆,必须建立其动力学模型,需要识别出等效质量和等效刚度,从而把连续体实际结构等效为理想的集中参数模型。
所以镗杆主系统的等效参数准确与否,直接关系到镗杆内部的动力吸振器的动力参数设计。
目前,动力减振镗杆的研究大多集中于吸振器参数优化设计[1-5]、颤振抑制机理[6]、吸振器工程实现[7]、动力学特性[8-10]等。
Sims针对切削颤振提出一种吸振器的解析调优策略,Miguelez等基于Sims调优策略,给出了镗削过程中最佳调谐频率的新解析表达式,并提出了吸振器频率比和阻尼比的经验拟合表达式,罗红波等利用幅频响应曲线面积最小法来修正全局寻优搜索法求得的设计参数值从而得到一组最优参数值。
机械振动-精密深孔镗削中镗杆振动问题

北方工业大学科目机械振动-精密深孔镗削中镗杆振动问题学院机电工程学院专业班级机研-12学生姓名指导教师撰写日期:2012年12月12日摘要在机械制造业中,一般规定孔深L 与孔径 d 之比大于5,即L/d>5 的孔称为深孔。
深孔加工是处于封闭或半封闭状态下进行的,不能直接观察到刀具的切削情况;且受孔径尺寸限制,刀具直径小,悬伸长,刚性差;切屑不易排出,切削热不易传散,因此深孔加工一直是金属切削领域内公认的技术难题。
而对于两端孔径小,中间孔径大的瓶腔深孔加工则难度更大,除了存在上述一般深孔加工的问题外,还要求实现镗刀块的伸出、夹紧、松开、缩回等动作,且受入口直径的限制,镗杆的刚性问题及振动问题变得更加尖锐。
因此精密小深孔加工技术的研究在理论和实践上都具有重要意义。
经过深孔镗削过程中的自激振动分析、深孔镗杆进行了静力学和动力学理论分析、对深孔镗杆进行ANSYS分析、深孔镗杆的模态分析,有一些减小振动的方法可以利用,如合理选择刀具几何形状、提高工艺系统的抗振性、采用减振装置、合理调整振型的刚度比、超声波方法、镗杆结构优化、智能镗杆颤振监测实验系统、镗削振动主动控制、设计辅助结构等方法等等。
关键词:深孔;镗削;减振目录目录 (3)1机械振动概况 (4)1.1机械振动对机械加工的影响 (4)1.2深孔加工的振动问题 (4)2精密振动切削工艺中的振动问题 (4)2.1项目简介 (4)2.1.1项目中的振动 (4)2.1.2项目镗削工序的振动分析 (4)3深孔镗削过程中的振动分析 (6)3.1深孔镗削过程中的自激振动 (6)3.2深孔镗杆进行了静力学和动力学理论分析 (7)3.3对深孔镗杆进行ANSYS分析 (9)3.4深孔镗杆的模态分析 (10)4减小深孔镗削中振动的方法 (11)4.1概述 (11)4.2超声波方法 (11)4.3镗杆结构优化 (13)4.4智能镗杆颤振监测实验系统 (13)4.5镗削振动主动控制 (14)4.6深孔镗削加减振措施后效果 (15)5.总结 (15)参考文献 (16)1机械振动概况1.1机械振动对机械加工的影响在机械加工过程中,工艺系统的振动会破坏刀具与工件之间正常的运动轨迹,给机械加工带来较大的危害,具体表现在以下几个方面:①影响加工表面质量,频率低时产生波纹,频率高时产生微观不平度;②降低生产效率,加工中的振动制约了切削用量的提高,严重时甚至使切削不能正常进行;③缩短刀具、机床等的使用寿命;④振动产生的噪声污染了环境。
基于有限元分析的镗床工装优化处理
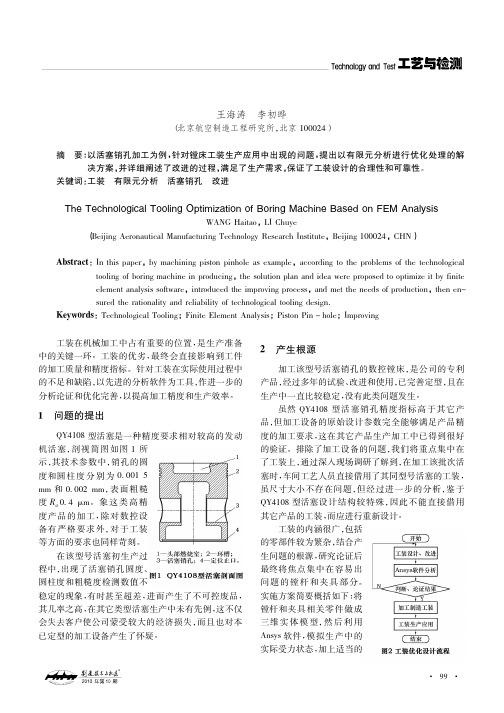
·99·基于有限元分析的镗床工装优化处理王海涛李初晔(北京航空制造工程研究所,北京100024)摘要:以活塞销孔加工为例,针对镗床工装生产应用中出现的问题,提出以有限元分析进行优化处理的解决方案,并详细阐述了改进的过程,满足了生产需求,保证了工装设计的合理性和可靠性。
关键词:工装有限元分析活塞销孔改进The Technological Tooling Optimization of Boring Machine Based on FEM AnalysisWANG Haitao ,LI Chuye(Beijing Aeronautical Manufacturing Technology Research Institute ,Beijing 100024,CHN )Abstract :In this paper ,by machining piston pinhole as example ,according to the problems of the technologicaltooling of boring machine in producing ,the solution plan and idea were proposed to optimize it by finite element analysis software ,introduced the improving process ,and met the needs of production ,then en-sured the rationality and reliability of technological tooling design.Keywords :Technological Tooling ;Finite Element Analysis ;Piston Pin -hole ;Improving 工装在机械加工中占有重要的位置,是生产准备中的关键一环。
- 1、下载文档前请自行甄别文档内容的完整性,平台不提供额外的编辑、内容补充、找答案等附加服务。
- 2、"仅部分预览"的文档,不可在线预览部分如存在完整性等问题,可反馈申请退款(可完整预览的文档不适用该条件!)。
- 3、如文档侵犯您的权益,请联系客服反馈,我们会尽快为您处理(人工客服工作时间:9:00-18:30)。
目录中文摘要 (1)英文摘要 (2)第一章绪论1.1课题研究的学术背景 (4)1.2减振镗杆的国内外研究水平和发展趋势 (5)1.3课题来源.................................................................................... (6)1.4主要研究内容、设计方法........................................................ (7)1.4.1主要研究内容 (7)1.4.2建立减振系统的数学模型 (7)第二章有限元分析软件ANSYS.2.1有限元分析软件ANSYS简介 (8)2.2 ANSYS软件的组成 (8)2.3ANSYS软件主要特点 (9)第三章减振系统结构设计与数学模型的建立3.1镗杆杆体材料的选择................................ .. (9)3.2镗杆的结构设计 (10)3.3阻尼器的设计........................................................................ . (10)3.3.1几种可选材料 (10)3.4 阻尼液的选取 (10)3.5弹簧的选择............................................................................... . (11)3.6可选材料的特性 (11)3.7弹簧材料的选取 (12)3.8减振块的设计........................................................................ . (13)3.9刀头的选择.............................................................................. .. (13)3.9.1减振系统数学模型的建立 (13)3.9.2对切削力的分析 (14)3.9.3系统运动方程的建立与求解 (14)第四章模型建立4.1多刚体动力学模型的建立.................................................. (15)4.1.1模型的坐标系统 (16)4.1.2模型的建立 (16)4.2多柔体动力学模型的建立 (16)4.2.1模态中性文件的建立 (16)4.2.2单元类型和材料参数 (17)4.2.3定义单元实常数 (18)4.3 ADAMS与ANSYS的接口 (21)第五章样机的仿真与参数化分析5.1减振系统固有频率的求取.................................................. . (22)5.2减振系统当量质量的确定 (23)5.3系统参数的确定................................................................... .. (23)5.4模型在频域内的仿真结果 (27)5.5结论.................................................................. ................... (27)5.6参数分析................................................................. .. (32)5.7设计参数变量化.................................................................. . (32)5.8定义目标函数................................................................... ....... .32 5.9分析弹簧刚度系数对刀刃跳动量的影响.. (33)5.9.1分析阻尼系数对刀刃跳动量的影响 (33)结论.............................................................................. .. (34)参考文献.............................................................................. (34)附件、外文资料 (37)深孔加工动力减振镗杆的有限元分析摘要随着金属加工行业的发展,市场竞争日益激烈,对加工质量和加工效率提出了越来越高的要求。
深孔加工由于其特殊的加工环境,使镗杆杆体的尺寸和形状都要受到一定的限制,造成了镗杆的刚度较低,特别是在镗杆的长径比比较大的情况下,镗杆的刚度会更小,这将严重影响加工质量,甚至使加工无法正常进行。
如何减小镗削过程中的振动已成为迫待解决的问题。
要研究镗杆的切削过程,就必须建立镗杆系统的动力学方程。
而用传统的方法是不可能建立一个精确的动力学方程的。
虚拟样机技术的出现提供了一个解决问题的方法。
虚拟样机技术的核心是机械系统动力学、有限元理论和控制理论等建模理论及其技术的实现。
有限元分析与机械系统仿真拥有相同的系统动力学求解基础,它们之间结合起来,可更好地实现机械系统刚柔耦合动力仿真分析研究。
利用虚拟样机技术可实现机械系统动力学方程的自动生成并精确求解,可在研究阶段预测镗杆的动力学性能,对这些性能进行优化,以达到提高产品性能、缩短开发时间、减少开发费用的目的。
本文借鉴了国外先进的镗杆制造技术,采用内置式动力减振的结构来增加镗杆的动刚度,并对动力减振镗杆进行了结构设计,建立了减振系统的数学模型。
在运动特性分析和结构优化中采用虚拟样机技术,利用ANSYS软件联合建立了减振系统的多柔体动力学模型。
以减小镗削过程中刀刃的径向跳动量为目标对动力减振镗杆虚拟样机进行仿真优化分析,得出了减振系统的最优参数。
关键词:减振器;镗孔;虚拟样机;动力学仿真;参数化分析Dynamic Simulation and Parametric Analysis of DynamicalVibration Absorption Boring Bar for Deep-Hole ProcessingAbstractWith the developmem of metal machining industry and the increasingly fierce market competition,the higher demand for machining quality and efficiency is put forward.The size and shape of the boring bar are restrictedbecause of the special machining condition in the deep —hole processing.This produces the low stiffness of the bodng bar which will become lower especially with the big length—diameter ratio ofthe b ar.Thc machining quality will be badly affected and the machining call not be on the rails due to the lower stiffness.How to reduce the vibration in the boring processing has become an urgent problem.The dynamical equation of boring bar system must be build up for studying the cutting processing of the boring bar.But all accurate dynamical equation can not be built with the traditional method.The appearance of virtual prototype technology offers a way tO solve the problem,The core of the virtual prototype technology is on the realization of modeling theories and technology,mechanical system dynamics,finite element theory and control theory,etc.The finite element analysis and mechanical system simulation,which have the same solution foundation of systematic dynamics,combine to achieve accurate simulating analysis of coupling motive between the rigid and flexible.By using virtual prototype technology,we carl realize the automatically building and accurately solving of the mechanism system dynamical equation,predict and optimize the system dynamics performance in the course of studying.11le improvement of product properties,construction period and expense reduction are achieved.Reference of the foreign advanced manufacture technology of boring bar is used in this article.We adopt a boring bar with dynamical vibration absorption system in it tO increase the stiffness of the boring bar,design its structure,set upthe mathematicaI model of the vibration absorption system.In the movement characteristic analysis and structure optimization virtual prototype technology is adopted,and multi flexible body dynamical model of the vibration absorption system are build up by using the So,ware of ADAMS and ANSYS.Aiming at reducing the radial vibrational value of the edge of knife in the boring processing,the virtual prototype of vibration absorption boring bar have been simulated,optimized and analyzed,and optimized parameter are obtained finally.The analysis skill and the conclusion,especially the building and simulation result of the vibration absorption model,providing reliable evidence for the boring bar with dynamical vibration absorption system in it,are important reference for the method of dynamical vibration absorption and the development and research of severaI of vibration absorption boring bar.Keywords vibration absorber;boring operation;virtual prototype;dynamic simulation;parametric analysis第1章绪论1.1课题研究的学术背景任何一个强大的国家都必须具有包括金属切削加工在内的强大制造业基础。