生产精益管理原则及技巧
精益管理方式方法及工作思路

精益管理方式方法及工作思路精益管理方式及工作思路精益管理(Lean Management)是一种以流程优化、资源最大化利用和持续改善为核心的管理方法。
它的目标是通过消除浪费、提高效率和质量,实现企业的持续改善和卓越竞争力。
本文将介绍精益管理的基本原则、常用工具和实施步骤,以及在工作中如何应用精益管理的思路。
一、精益管理的基本原则精益管理的核心原则是以客户价值为导向,通过持续的改进来满足客户的需求。
以下是精益管理的基本原则:1. 价值流分析:通过理解价值流,即产品或服务从原材料采购到最终交付给客户的全过程,识别和分析其中的浪费,并持续改善流程,以提高价值创造能力和降低成本。
2. 浪费消除:浪费指的是任何不增加产品或服务价值的活动、物料或信息。
精益管理强调对浪费的彻底消除,包括运输、库存、运动、等待、过程中的不良品和不必要的加工等。
3. 价值流平衡:通过优化生产或服务过程中的各个环节,确保每个环节的节拍和产能相匹配,以避免过度生产或产能不足的情况。
4. 强调标准化工作:通过建立标准化工作程序和规范,确保工作的一致性和高质量,同时提供员工培训和支持,以便他们能够充分掌握和理解标准化工作的重要性和益处。
二、精益管理常用工具在实施精益管理时,常用的工具和技术有:1. 价值流图(Value Stream Mapping):价值流图是用于分析和改善价值流的工具,通过绘制价值流程图,可以清晰地展现原料采购、生产过程和交付给客户的全过程,进而找出其中的瓶颈和浪费,提出改善方案。
2. 5S方法:5S是一套整理、整顿、清扫、清洁和素养的方法,通过规范工作环境和操作规程,提高工作效率和质量,减少浪费。
3. Kaizen活动:Kaizen是指持续改善的活动,通过团队合作和日常小改进,不断优化工作流程,提高效率,降低成本。
4. 柏拉图图(Pareto Chart):柏拉图图用于分析问题的主要原因,帮助管理者更好地分配资源和制定改善计划。
精益管理五个原则

精益管理五个原则精益管理是一种以提高效率和质量为目标的管理方法,它包含了五个重要的原则,即价值流映射、流程改进、拉动生产、持续改进和尊重人。
这五个原则有助于企业实现更高效的生产流程和更高质量的产品,提升竞争力。
价值流映射是精益管理的核心原则之一。
它通过绘制整个生产流程,识别出价值创造的关键环节和非价值创造的浪费环节。
通过分析和改进这些浪费环节,企业可以优化生产流程,提高生产效率和质量。
流程改进是精益管理的重要手段之一。
它强调通过消除浪费和提高流程效率来改进生产流程。
流程改进可以通过标准化工作流程、优化物料流动、改进设备布局等方式来实现。
通过持续地优化流程,企业可以降低生产成本,提高产品质量。
第三,拉动生产是精益管理的核心原则之一。
传统的生产方式是按计划生产,即按照预测的需求量来生产产品。
而拉动生产则是根据实际需求来生产产品,以避免库存积压和产能浪费。
拉动生产需要企业与供应商建立紧密的合作关系,实现供应链的高效运作。
第四,持续改进是精益管理的核心原则之一。
它强调通过不断的改进来提高生产效率和质量。
持续改进可以通过设立目标、收集数据、分析数据、制定改进计划和实施改进措施等步骤来实现。
通过持续改进,企业可以不断提高自身的竞争力和适应市场的变化。
尊重人是精益管理的核心原则之一。
它强调员工的参与和尊重,认为员工是企业最重要的资产。
尊重人可以通过提供培训机会、激励员工、建立良好的工作环境等方式来实现。
尊重人可以激发员工的创造力和积极性,提高员工的工作质量和效率。
精益管理的五个原则可以帮助企业提高生产效率和质量,提升竞争力。
企业可以通过价值流映射、流程改进、拉动生产、持续改进和尊重人这五个原则来优化生产流程,降低成本,提高产品质量,并不断适应市场的变化。
只有不断地改进和创新,企业才能在激烈的市场竞争中立于不败之地。
实现精益生产的14项管理原则
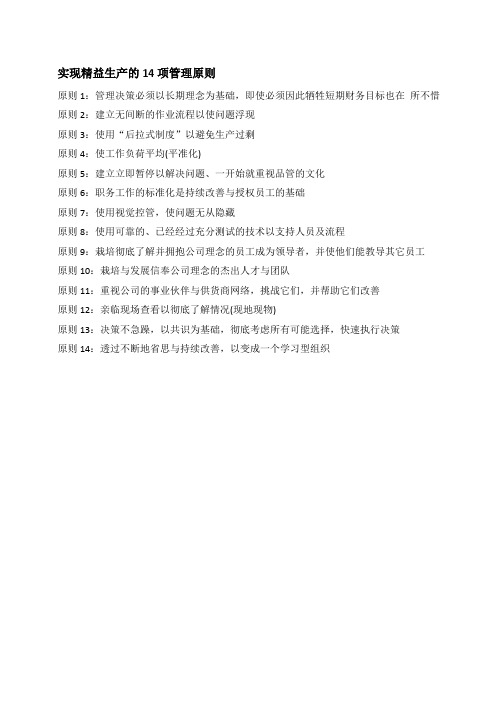
实现精益生产的14项管理原则
原则1:管理决策必须以长期理念为基础,即使必须因此牺牲短期财务目标也在所不惜原则2:建立无间断的作业流程以使问题浮现
原则3:使用“后拉式制度”以避免生产过剩
原则4:使工作负荷平均(平准化)
原则5:建立立即暂停以解决问题、一开始就重视品管的文化
原则6:职务工作的标准化是持续改善与授权员工的基础
原则7:使用视觉控管,使问题无从隐藏
原则8:使用可靠的、已经经过充分测试的技术以支持人员及流程
原则9:栽培彻底了解并拥抱公司理念的员工成为领导者,并使他们能教导其它员工
原则10:栽培与发展信奉公司理念的杰出人才与团队
原则11:重视公司的事业伙伴与供货商网络,挑战它们,并帮助它们改善
原则12:亲临现场查看以彻底了解情况(现地现物)
原则13:决策不急躁,以共识为基础,彻底考虑所有可能选择,快速执行决策
原则14:透过不断地省思与持续改善,以变成一个学习型组织。
精益生产管理的核心及五个原则

精益生产管理的核心及五个原则
随着市场经济发发展,企业竞争激烈,精益生产管理已经成为众多企业必不可少的管理方式,便于企业更好的推行精益生产管理。
下面就和小编一起来了解下,精益生产管理的核心及五个原则吧。
一、精益生产管理的核心
精益生产管理的核心是通过持续不断滴排除浪费来赢得利润、创造价值。
二、精益思想五个原则
1.流动——使价值不间断地流动。
2.尽善尽美——永远追求尽善尽美。
3.价值——精确地确定特定产品的价值。
4.拉动——让用户从生产者方面拉动价值。
5.价值流——识别出每种产品的价值流。
精益生产管理是一种以客户需求为拉动,以消除浪费和不断改善为核心,使企业以最少的投入获取成本和运作效益显着改善的一种全新的生产管理模式。
精益生产管理手册
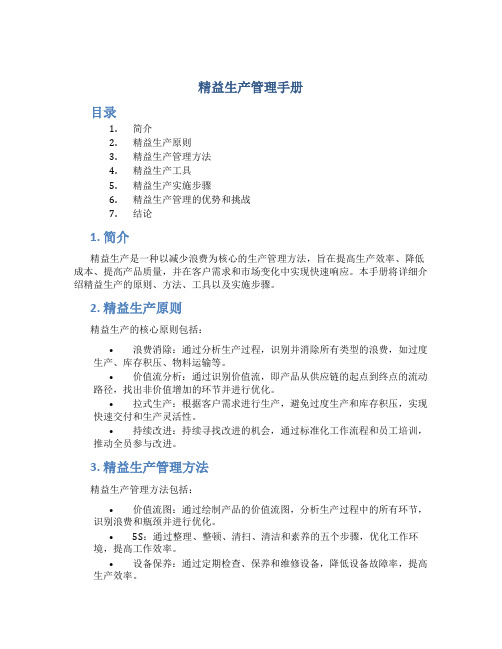
精益生产管理手册目录1.简介2.精益生产原则3.精益生产管理方法4.精益生产工具5.精益生产实施步骤6.精益生产管理的优势和挑战7.结论1. 简介精益生产是一种以减少浪费为核心的生产管理方法,旨在提高生产效率、降低成本、提高产品质量,并在客户需求和市场变化中实现快速响应。
本手册将详细介绍精益生产的原则、方法、工具以及实施步骤。
2. 精益生产原则精益生产的核心原则包括:•浪费消除:通过分析生产过程,识别并消除所有类型的浪费,如过度生产、库存积压、物料运输等。
•价值流分析:通过识别价值流,即产品从供应链的起点到终点的流动路径,找出非价值增加的环节并进行优化。
•拉式生产:根据客户需求进行生产,避免过度生产和库存积压,实现快速交付和生产灵活性。
•持续改进:持续寻找改进的机会,通过标准化工作流程和员工培训,推动全员参与改进。
3. 精益生产管理方法精益生产管理方法包括:•价值流图:通过绘制产品的价值流图,分析生产过程中的所有环节,识别浪费和瓶颈并进行优化。
•5S:通过整理、整顿、清扫、清洁和素养的五个步骤,优化工作环境,提高工作效率。
•设备保养:通过定期检查、保养和维修设备,降低设备故障率,提高生产效率。
•产能平衡:根据市场需求和生产能力,调整生产线的平衡,提高生产效率和产品质量。
•Just-In-Time (JIT) 生产:根据客户需求精确控制物料、零部件和成品的库存,避免过度生产和库存积压。
•持续改进:通过持续的改进活动,提高工作流程、生产效率和产品质量。
4. 精益生产工具精益生产使用多种工具来支持管理和改进活动,包括:•流程图:用于描述生产过程中的各个步骤和环节。
•Gantt 图:用于规划和跟踪项目进度。
•帕累托图:用于识别主要问题和优先解决。
•5W1H 分析:通过回答问题谁、何时、何地、为什么、如何和多少来分析问题的根本原因。
•根本原因分析:通过追溯问题的根本原因,找到解决问题的有效措施。
•PDCA 循环:通过计划、执行、检查和行动的循环,持续改进工作流程和活动。
精益生产十大原则
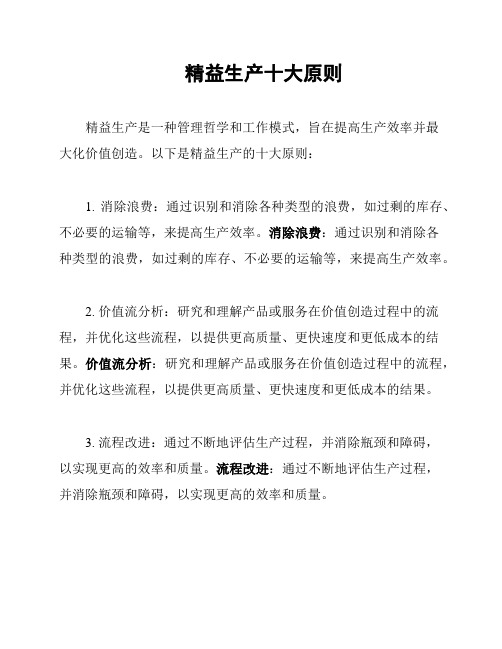
精益生产十大原则精益生产是一种管理哲学和工作模式,旨在提高生产效率并最大化价值创造。
以下是精益生产的十大原则:1. 消除浪费:通过识别和消除各种类型的浪费,如过剩的库存、不必要的运输等,来提高生产效率。
消除浪费:通过识别和消除各种类型的浪费,如过剩的库存、不必要的运输等,来提高生产效率。
2. 价值流分析:研究和理解产品或服务在价值创造过程中的流程,并优化这些流程,以提供更高质量、更快速度和更低成本的结果。
价值流分析:研究和理解产品或服务在价值创造过程中的流程,并优化这些流程,以提供更高质量、更快速度和更低成本的结果。
3. 流程改进:通过不断地评估生产过程,并消除瓶颈和障碍,以实现更高的效率和质量。
流程改进:通过不断地评估生产过程,并消除瓶颈和障碍,以实现更高的效率和质量。
4. 标准化工作:确保每个工作岗位都有明确的工作标准和操作方法,以提高工作质量和一致性。
标准化工作:确保每个工作岗位都有明确的工作标准和操作方法,以提高工作质量和一致性。
5. 持续改进:通过鼓励员工提出改进建议并实施这些建议,不断地改进生产过程和工作方法。
持续改进:通过鼓励员工提出改进建议并实施这些建议,不断地改进生产过程和工作方法。
6. 团队合作:建立一个积极的团队合作环境,鼓励员工之间的互相支持和协作。
团队合作:建立一个积极的团队合作环境,鼓励员工之间的互相支持和协作。
7. 可视化管理:使用可视化工具和技术,如看板、图表等,帮助员工和管理层更好地了解生产状况和问题,并及时做出调整。
可视化管理:使用可视化工具和技术,如看板、图表等,帮助员工和管理层更好地了解生产状况和问题,并及时做出调整。
8. 质量优先:将质量放在首位,确保产品和服务符合客户的期望,并尽量减少缺陷和错误。
质量优先:将质量放在首位,确保产品和服务符合客户的期望,并尽量减少缺陷和错误。
9. 减少变动:尽量避免频繁的变动和调整,以保持生产过程的稳定性和可控性。
减少变动:尽量避免频繁的变动和调整,以保持生产过程的稳定性和可控性。
精益生产之目视化管理
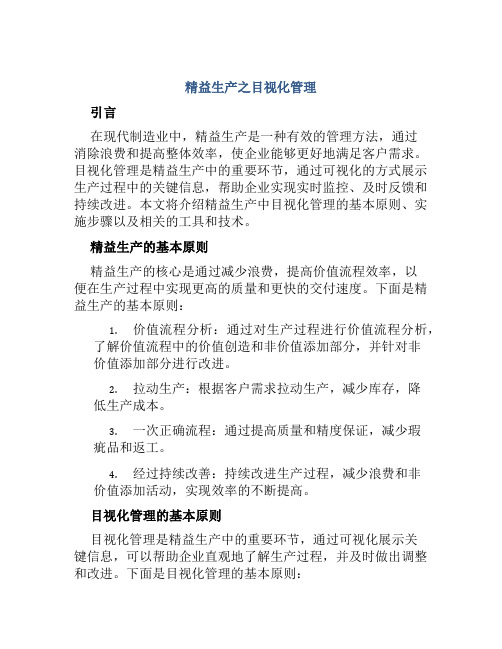
精益生产之目视化管理引言在现代制造业中,精益生产是一种有效的管理方法,通过消除浪费和提高整体效率,使企业能够更好地满足客户需求。
目视化管理是精益生产中的重要环节,通过可视化的方式展示生产过程中的关键信息,帮助企业实现实时监控、及时反馈和持续改进。
本文将介绍精益生产中目视化管理的基本原则、实施步骤以及相关的工具和技术。
精益生产的基本原则精益生产的核心是通过减少浪费,提高价值流程效率,以便在生产过程中实现更高的质量和更快的交付速度。
下面是精益生产的基本原则:1.价值流程分析:通过对生产过程进行价值流程分析,了解价值流程中的价值创造和非价值添加部分,并针对非价值添加部分进行改进。
2.拉动生产:根据客户需求拉动生产,减少库存,降低生产成本。
3.一次正确流程:通过提高质量和精度保证,减少瑕疵品和返工。
4.经过持续改善:持续改进生产过程,减少浪费和非价值添加活动,实现效率的不断提高。
目视化管理的基本原则目视化管理是精益生产中的重要环节,通过可视化展示关键信息,可以帮助企业直观地了解生产过程,并及时做出调整和改进。
下面是目视化管理的基本原则:1.明确目标:明确管理的目标和关键指标,确定需要可视化的内容。
2.突出重点:将关键信息突出显示,以便工作人员可以迅速识别和解读。
3.统一标准:制定统一的标准和规范,使所有人都能理解并采用相同的信息展示方式。
4.及时反馈:将实时数据及时反馈给相关人员,以便他们能够及时采取措施并做出决策。
5.持续改进:根据可视化信息的反馈和结果,持续改进生产过程和管理方式。
目视化管理的实施步骤实施目视化管理需要经过一系列的步骤,下面是目视化管理的实施步骤:1.分析流程:分析生产流程,确定关键节点和关键信息。
2.设计和安装可视化工具:根据生产流程和关键信息,设计并安装可视化工具,如看板、指示灯等。
3.收集和整理数据:收集生产过程中的关键数据,并进行整理和归类。
4.设定目标和指标:根据管理的目标,设定关键指标,并确定目标值和标准。
精益质量管理的方法和原则
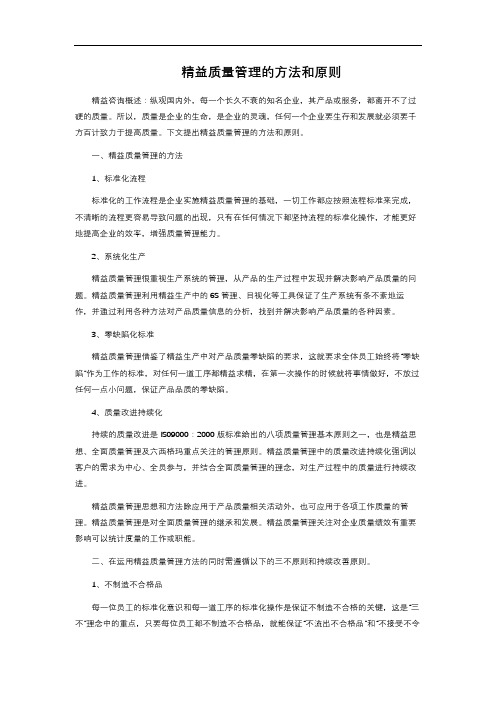
精益质量管理的方法和原则精益咨询概述:纵观国内外,每一个长久不衰的知名企业,其产品或服务,都离开不了过硬的质量。
所以,质量是企业的生命,是企业的灵魂,任何一个企业要生存和发展就必须要千方百计致力于提高质量。
下文提出精益质量管理的方法和原则。
一、精益质量管理的方法1、标准化流程标准化的工作流程是企业实施精益质量管理的基础,一切工作都应按照流程标准来完成,不清晰的流程更容易导致问题的出现,只有在任何情况下都坚持流程的标准化操作,才能更好地提高企业的效率,增强质量管理能力。
2、系统化生产精益质量管理很重视生产系统的管理,从产品的生产过程中发现并解决影响产品质量的问题。
精益质量管理利用精益生产中的6S管理、目视化等工具保证了生产系统有条不紊地运作,并通过利用各种方法对产品质量信息的分析,找到并解决影响产品质量的各种因素。
3、零缺陷化标准精益质量管理借鉴了精益生产中对产品质量零缺陷的要求,这就要求全体员工始终将“零缺陷”作为工作的标准,对任何一道工序都精益求精,在第一次操作的时候就将事情做好,不放过任何一点小问题,保证产品品质的零缺陷。
4、质量改进持续化持续的质量改进是IS09000:2000版标准给出的八项质量管理基本原则之一,也是精益思想、全面质量管理及六西格玛重点关注的管理原则。
精益质量管理中的质量改进持续化强调以客户的需求为中心、全员参与,并结合全面质量管理的理念,对生产过程中的质量进行持续改进。
精益质量管理思想和方法除应用于产品质量相关活动外,也可应用于各项工作质量的管理。
精益质量管理是对全面质量管理的继承和发展。
精益质量管理关注对企业质量绩效有重要影响可以统计度量的工作或职能。
二、在运用精益质量管理方法的同时需遵循以下的三不原则和持续改善原则。
1、不制造不合格品每一位员工的标准化意识和每一道工序的标准化操作是保证不制造不合格的关键,这是“三不”理念中的重点,只要每位员工都不制造不合格品,就能保证“不流出不合格品”和“不接受不令格品”的执行。
精益管理5个基本原则

精益管理5个基本原则精益管理是一种管理方法论,旨在通过简化流程、减少浪费、提高效率和质量,从而提高组织的竞争力和盈利能力。
它基于5个基本原则,分别是价值、价值流、流动、拉动和迭代学习。
本文将依次介绍这5个基本原则,并说明它们的重要性和应用方法。
第一个基本原则是价值。
精益管理强调将价值观念贯穿于整个组织的运作中。
价值是指顾客愿意为之付费的产品或服务。
在精益管理中,组织需要明确了解顾客的需求和期望,以便为顾客创造价值。
要实现这一点,组织需要建立有效的沟通渠道,与顾客保持密切联系,并根据顾客的反馈不断改进产品和服务。
第二个基本原则是价值流。
价值流是指将原材料转化为最终产品或服务的所有步骤和活动。
精益管理强调要理解和优化价值流,以便消除浪费和提高效率。
为了实现这一点,组织需要进行价值流分析,识别出不必要的环节和步骤,并采取措施进行改进。
例如,可以通过流程重组、设备自动化和员工培训等方式来简化流程和提高生产效率。
第三个基本原则是流动。
流动是指产品或服务在价值流中的连续流动,以最大程度地减少等待时间和库存。
精益管理强调要实现流动生产,避免批量生产和存货积压。
为了实现这一点,组织需要优化生产线布局,减少生产环节之间的物料传递时间,同时采取合理的生产节奏和灵活的生产调度。
第四个基本原则是拉动。
拉动是指根据顾客需求来进行生产,而不是按照计划或预测来进行生产。
精益管理强调要实现拉动生产,避免过度生产和库存积压。
为了实现这一点,组织需要建立有效的供应链管理系统,及时获取顾客需求信息,并根据需求进行生产和供应。
第五个基本原则是迭代学习。
迭代学习是指不断试验、学习和改进的过程。
精益管理强调要持续改进和学习,以适应市场和顾客的变化。
为了实现这一点,组织需要建立学习型组织文化,鼓励员工不断尝试新方法和想法,并及时反馈和总结经验教训。
精益管理的5个基本原则是价值、价值流、流动、拉动和迭代学习。
这些原则强调了价值创造、流程优化、资源精益利用和持续改进的重要性。
精益生产的定义及基本原则
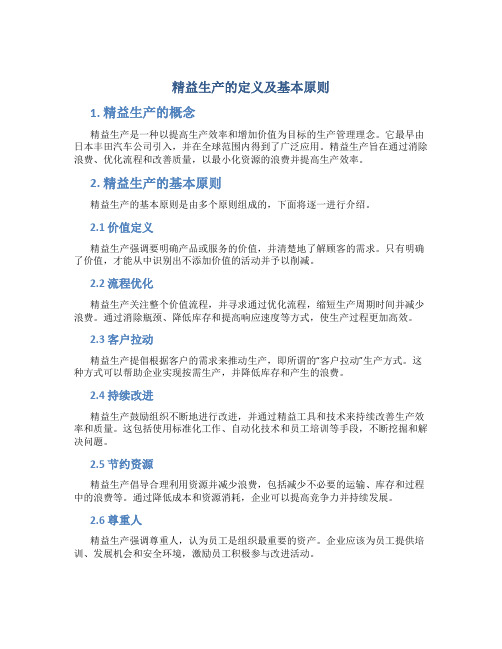
精益生产的定义及基本原则1. 精益生产的概念精益生产是一种以提高生产效率和增加价值为目标的生产管理理念。
它最早由日本丰田汽车公司引入,并在全球范围内得到了广泛应用。
精益生产旨在通过消除浪费、优化流程和改善质量,以最小化资源的浪费并提高生产效率。
2. 精益生产的基本原则精益生产的基本原则是由多个原则组成的,下面将逐一进行介绍。
2.1 价值定义精益生产强调要明确产品或服务的价值,并清楚地了解顾客的需求。
只有明确了价值,才能从中识别出不添加价值的活动并予以削减。
2.2 流程优化精益生产关注整个价值流程,并寻求通过优化流程,缩短生产周期时间并减少浪费。
通过消除瓶颈、降低库存和提高响应速度等方式,使生产过程更加高效。
2.3 客户拉动精益生产提倡根据客户的需求来推动生产,即所谓的“客户拉动”生产方式。
这种方式可以帮助企业实现按需生产,并降低库存和产生的浪费。
2.4 持续改进精益生产鼓励组织不断地进行改进,并通过精益工具和技术来持续改善生产效率和质量。
这包括使用标准化工作、自动化技术和员工培训等手段,不断挖掘和解决问题。
2.5 节约资源精益生产倡导合理利用资源并减少浪费,包括减少不必要的运输、库存和过程中的浪费等。
通过降低成本和资源消耗,企业可以提高竞争力并持续发展。
2.6 尊重人精益生产强调尊重人,认为员工是组织最重要的资产。
企业应该为员工提供培训、发展机会和安全环境,激励员工积极参与改进活动。
3. 精益生产的实施步骤实施精益生产需要经过一系列的步骤,下面将进行简要介绍。
3.1 确定目标首先,组织需要明确实施精益生产的目标,并将其与组织的战略目标进行对齐。
明确的目标可以帮助组织在实施过程中保持目标导向性。
3.2 培训和教育实施精益生产需要员工具备相应的知识和技能。
因此,组织需要为员工提供相关的培训和教育,使其了解精益生产的原理和方法。
3.3 流程改善精益生产强调流程的优化,因此,组织需要对现有的生产流程进行分析和评估,找出其中的问题和瓶颈,并采取相应的改进措施。
什么是精益管理?

什么是精益管理?精益管理是现代制造业和服务业中使用最广泛的管理方法之一,它的目的是最大化价值,最小化浪费,以提高企业的效率和竞争力。
那么,什么是精益管理,其核心原则是什么,它的优势和不足是什么呢?本文将为大家详细介绍。
1. 什么是精益管理?精益管理是一种以客户为导向,通过流程改进来缩短生产周期,降低成本,提高质量的管理方法。
它的核心是以流程为中心,通过不断优化生产流程来减少浪费,提高效率。
精益管理来源于丰田生产系统,以及日本的“精益生产”和“精益服务”思想,现在已成为了全球制造业和服务业中使用最广泛的管理方法之一。
2. 精益管理的核心原则(1) 价值流分析精益管理的核心原则是价值流分析,即从产品或服务的角度,分析整个价值链并将非价值活动的流程优化,以最大化价值流,最小化浪费。
将所有的流程分为价值增加和非价值增加的,然后通过改善流程来减少浪费、纠正错误和提高质量。
(2) 创建流程标准化创建流程标准化是精益管理中另一个重要原则,其目的在于制定出一套标准化的工作流程,以使团队成员能够立即发现错误和问题,并且能够快速解决。
流程标准化能够帮助每个团队成员了解和掌握自己的职责以及如何完成任务。
同时,流程标准化也能够保证所有的工作都是按照预定的流程进行的,从而降低误操作和生产错误率。
(3) 持续改进持续改进是精益管理又一个非常重要的原则,其目的是通过不断地改进流程来提高效率,减少浪费和错误。
持续改进需要在整个流程中形成一种改善文化,让每个人都能够积极参与到改进中来。
只有通过大家的努力,才能够实现长期的改进和增长。
3. 精益管理的优势和不足优势(1) 提高效率精益管理可以帮助企业降低生产成本和缩短生产周期,从而提高生产效率和利润。
(2) 提高质量精益管理可以通过从处理问题的角度而不是找问题的责任人的角度来提高质量。
它可以让员工更好地感知问题发生的原因,并且更容易找到解决问题的方法。
这有助于避免类似问题再次发生,并提高产品和服务的质量。
精益生产现场管理和改善的5个要点

精益生产管理的目标是不断改善员工的工作效率和工作方法。
这里的改善仅靠精益管理工具是远远不够的。
以下是精益生产现场管理与改善的重点:1.精益生产现场管理与改进的四个原则①重要管理的时间管理原则。
② 标准化原则。
改进的第一步是标准化。
没有标准,就没有进步。
③ 追查原因中的“五五法”原则是通过五个为什么找出问题的原因。
④ 现场原则。
所有工作应在现场解决,我们的主管和工程师应在现场。
改进应遵循场景、客体和现实三个原则。
2. 根据实际需要进行改进不需要的不改进。
在实际工作中,把它们放在次要的时间并不紧迫,工作中需要的东西需要立即改进。
3. 不要轻视琐碎的改进活动精益生产现场管理和改进中总会出现一些不显眼、不合理的现象或工作方法。
而一些重大事故往往来自这些通常被忽视的环节。
因此,我们应该关注那些看似意义重大的改进活动,但不能轻视“小改进”。
4. 能忍受失败不可能事事成功。
失败本身就意味着进步。
精益生产现场管理和改进中的每一个失败案例都能为我们提供改进的机会和思路,防止再次发生。
失败并不重要,但重要的是不要让同样的错误再次发生。
失败经常发生,当事人往往很难告诉老板。
既然下属有勇气说出自己的失败,领导就应该表扬和鼓励他们继续改进。
5. 改善无止境生产现场不是一成不变的,改进工作也不是一蹴而就的。
在过去的改进中,我们可能会发现一些不完善的地方,我们可能会找到更好的改进方法。
随着人们能力的不断提高和新知识、新技术的出现,人们不会也不应该满足于或停留在现有的改进成果上。
企业的环境在不断变化,客户的需求也在不断丰富。
因此,生产现场不仅能保持原样。
改进的过程是一个上升的螺旋过程,精益生产现场的管理和改进永无止境。
车间精益化生产管理
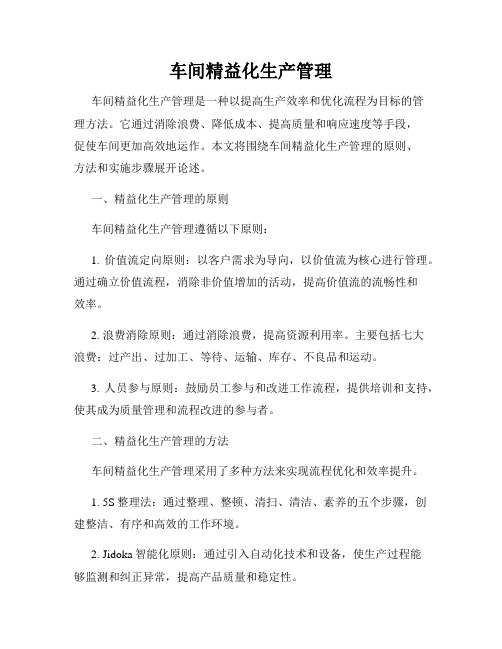
车间精益化生产管理车间精益化生产管理是一种以提高生产效率和优化流程为目标的管理方法。
它通过消除浪费、降低成本、提高质量和响应速度等手段,促使车间更加高效地运作。
本文将围绕车间精益化生产管理的原则、方法和实施步骤展开论述。
一、精益化生产管理的原则车间精益化生产管理遵循以下原则:1. 价值流定向原则:以客户需求为导向,以价值流为核心进行管理。
通过确立价值流程,消除非价值增加的活动,提高价值流的流畅性和效率。
2. 浪费消除原则:通过消除浪费,提高资源利用率。
主要包括七大浪费:过产出、过加工、等待、运输、库存、不良品和运动。
3. 人员参与原则:鼓励员工参与和改进工作流程,提供培训和支持,使其成为质量管理和流程改进的参与者。
二、精益化生产管理的方法车间精益化生产管理采用了多种方法来实现流程优化和效率提升。
1. 5S整理法:通过整理、整顿、清扫、清洁、素养的五个步骤,创建整洁、有序和高效的工作环境。
2. Jidoka智能化原则:通过引入自动化技术和设备,使生产过程能够监测和纠正异常,提高产品质量和稳定性。
3. Kaizen持续改进:通过不断地小步优化,改善工作流程和生产效率。
包括5W1H分析法、PDCA循环、流程图等工具的应用。
4. Kanban看板系统:通过可视化管理,控制生产和物流流程。
通过看板、标识和信号,及时传递信息,避免过程中的延误和浪费。
5. 拉动生产模式:通过根据客户需求进行生产,减少库存和库位占用,并实现按需交付。
三、精益化生产管理的实施步骤实施车间精益化生产管理需要有一个系统性和渐进性的过程。
1. 了解和分析:了解车间现状和问题。
通过价值流图绘制、现场观察、数据分析等方式,识别瓶颈、浪费和改进机会。
2. 设计和规划:根据分析结果,制定改进计划。
确定目标、确定改进方法和工具,建立改进团队。
3. 实施和改进:按照计划逐步实施改进方案,分级推进。
通过PDCA循环,及时调整和改进。
4. 持续改进:建立持续改进机制和文化,鼓励员工提出改进建议和解决方案。
14-34. 精益生产管理的四大原则

34.精益生产管理的四大原则
精益生产管理强调在企业管理注意对细节的观察和掌握,制定到具体详细的执行方案。
精益生产管理要求企业运用“精益思想”。
“精益思想”的核心就是以小资源投入,包括人力、设备、资金、时刻和空间,创造出尽可能多的价值,为顾客供给新产品和及时的服务。
“精”——少投入、少耗费资源、少花时间,减少不能再生资源的投入和浪费,高质量。
“益”——多产出经济效益,完成企业升级的方针。
更加,精雕细镂。
精益生产管理的方针能够概括为:企业在为顾客供给满意的产品与服务的同时,把浪费降到最低程度。
要实现精益生产管理必须遵循的四大原则:
1、数据化原则
用数据说话、用数据分析、用数据要求、用数据检验。
2、交点原则
管理中存在交点问题,精益化管理要用沟通,责任确立等方式解决交点问题。
3、操作性原则
管理规则具有可操作性,考虑的方面更细,同时去掉那些不能操作、又容易产生责任推诿的表述。
4、底线原则
在细的程度上要把握两点:一是可不可以再细分,二是需不需要再细分。
精益生产管理的十四个基本原则

精益生产管理的十四个基本原则一、管理决策以长期理念为基础,即使因此牺牲短期财务目标也在所不惜。
企业要有一个优先于任何短期决策的目的理念,使整个企业的运作与发展能配合着朝向这个比赚钱更重要的共同目的一一长期稳固的发展。
长期理念和历史地位的起始点应该是为客户、为社会、为企业的收益创造价值。
精益生产管理要求要每一个员工都有责任。
二、建立无间断流程以使问题浮现要求重新设计流程,使流程不仅仅是工作过程的描述。
一定要建立快速输送材料与信息的流程,使流程与员工的行为动作紧密地联结在一起。
要使整个企业文化重视流程,这是促成真正的持续改进流程及员工发展的关键。
三、实施拉式生产制度以避免生产过剩在你生产流程下游的客户有需求的时候,供应给他们正确数量的正确东西。
使在制品及库存减至最少,每项产品只维持少量存货,根据向客户实际交付的数量,经常补充存货。
按客户的需求每天进行调整在制品和存货量,而不是依靠计算机的时间表与系统来追踪已经成为浪费的存货。
四、使工作负荷水准稳定(生产均衡化),工作应该象龟兔赛跑中的乌龟一样杜绝浪费只是实现精益生产所必须做的工作的1/3o避免员工与设备的负荷过重,以避免生产安排的不均匀,也同等重要。
尽量使所有制造与服务流程的工作负荷平均化,以取代大多数公司实行的批量生产方法中经常启动、停止、启动的做法。
五、建立立即暂停以解决问题,从一开始就重视品质管理的文化为顾客提供的品质决定着你的定价。
你要想收益高,首先需要品质好。
为了提高品质,应该使用所有能够确保产品品质的现代方法。
想一想,我们的方法是不是能够确保产品品质?使生产设备具有发现问题及一发现问题就停止生产的能力。
在企业中设立支持快速解决问题的制度和监督检测。
在企业文化中融入发生问题时立即暂停或减缓速度、就地改进质量以提升长期生产力的概念。
在工作场所中的任何地方都使用稳定、可重复的方法,以维持流程的可预测性、规律的运作时间,以及规律的产出。
到一定时间时, 应该汲取对流程的累积学习心得,把“现在”的最佳实务进行标准化,让员工对于标准提出有创意的改进意见,把这些见解纳入精益生产管理新标准中。
精益生产的五大基本原则
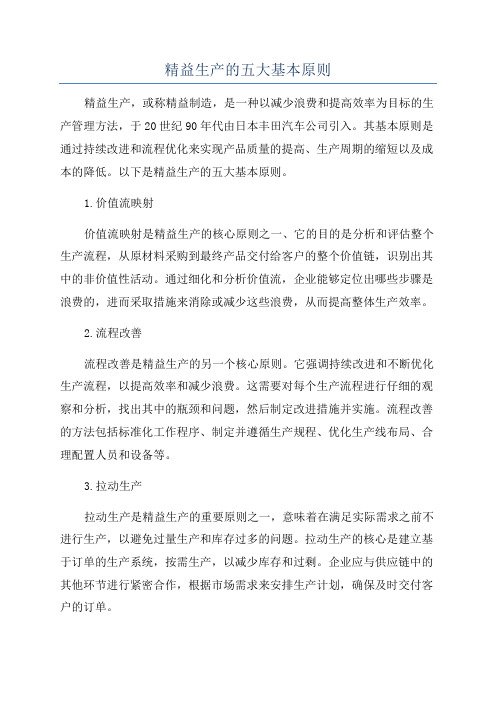
精益生产的五大基本原则精益生产,或称精益制造,是一种以减少浪费和提高效率为目标的生产管理方法,于20世纪90年代由日本丰田汽车公司引入。
其基本原则是通过持续改进和流程优化来实现产品质量的提高、生产周期的缩短以及成本的降低。
以下是精益生产的五大基本原则。
1.价值流映射价值流映射是精益生产的核心原则之一、它的目的是分析和评估整个生产流程,从原材料采购到最终产品交付给客户的整个价值链,识别出其中的非价值性活动。
通过细化和分析价值流,企业能够定位出哪些步骤是浪费的,进而采取措施来消除或减少这些浪费,从而提高整体生产效率。
2.流程改善流程改善是精益生产的另一个核心原则。
它强调持续改进和不断优化生产流程,以提高效率和减少浪费。
这需要对每个生产流程进行仔细的观察和分析,找出其中的瓶颈和问题,然后制定改进措施并实施。
流程改善的方法包括标准化工作程序、制定并遵循生产规程、优化生产线布局、合理配置人员和设备等。
3.拉动生产拉动生产是精益生产的重要原则之一,意味着在满足实际需求之前不进行生产,以避免过量生产和库存过多的问题。
拉动生产的核心是建立基于订单的生产系统,按需生产,以减少库存和过剩。
企业应与供应链中的其他环节进行紧密合作,根据市场需求来安排生产计划,确保及时交付客户的订单。
4.全员参与全员参与是精益生产一个重要的原则。
它强调每个员工都是企业改进的推动者。
全员参与的核心是培养员工的意识和责任感,使他们参与到生产过程的改进中去。
为此,企业应提供员工培训、绩效激励和奖励机制,鼓励员工提出改进建议,并积极地实施和推广这些改进措施。
5.长期关系长期关系是精益生产的最后一个原则。
它强调与供应链中的每个环节建立稳定的长期关系,包括供应商、合作伙伴和客户。
这种长期关系能够增强合作伙伴的互信和相互间的合作,实现更高效的生产和供应。
总结起来,精益生产的五大基本原则包括价值流映射、流程改善、拉动生产、全员参与和长期关系。
这些原则的目标是通过减少浪费和提高效率来实现产品质量的提高、生产周期的缩短和成本的降低。
精益生产管理的核心及五个原则

精益生产管理的核心及五个原则
精益生产管理的核心及五个原则
随着市场经济发发展,企业竞争激烈,精益生产管理已经成为众多企业必不可少的管理方式,便于企业更好的推行精益生产管理。
下面就和小编一起来了解下,精益生产管理的核心及五个原则吧。
一、精益生产管理的核心
精益生产管理的核心是通过持续不断滴排除浪费来赢得利润、创造价值。
二、精益思想五个原则
1.流动——使价值不间断地流动。
2.尽善尽美——永远追求尽善尽美。
3.价值——精确地确定特定产品的价值。
4.拉动——让用户从生产者方面拉动价值。
5.价值流——识别出每种产品的价值流。
精益生产管理是一种以客户需求为拉动,以消除浪费和不断改善为核心,使企业以最少的投入获取成本和运作效益显着改善的一种全新的生产管理模式。
精益管理总结

精益管理总结近年来,精益管理作为一种管理方法在企业界广泛应用,并取得了显著的成果。
它通过深入了解客户需求、精简生产过程、最大化价值流动等手段,帮助企业实现高效运营和持续改进。
在本文中,将对精益管理进行总结和探讨。
一、精益管理的核心思想精益管理的核心思想是通过消除浪费来提高效率。
它强调从价值流的角度来审视企业的运营过程,以便找出其中的浪费。
通过消除这些浪费,企业可以更快、更准确地满足客户需求,从而提高竞争力。
二、精益管理的关键原则1. 客户导向:精益管理倡导将客户需求置于核心位置,将企业的所有决策和活动都与客户价值相关联。
只有深入了解客户需求,并将其转化为产品或服务的要求,企业才能在市场上立足。
2. 流程优化:精益管理注重将整个价值流程流畅化,消除不必要的环节和步骤。
这需要对生产过程进行深入的分析,并找出其中的瓶颈和浪费。
通过精细规划和调整,不仅可以减少生产周期,还可以提高产品质量。
3. 持续改进:精益管理强调持续改进的重要性。
它认为没有最好,只有更好。
企业应该建立学习型组织,通过培养员工的改进意识和能力,促进每个人不断地寻找和解决问题,并改善工作流程和产品质量。
三、精益管理的实践技巧1. 价值流分析:通过绘制价值流图,我们可以清楚地看到整个流程中的每个环节,并发现其中的浪费。
价值流分析的目的是为了消除这些浪费,从而提高生产效率。
2. 小批量生产:精益管理提倡小批量生产,这样可以减少库存,并缩短生产周期。
而大规模生产往往会导致过剩和低效。
3. 5S管理:5S管理是精益管理中常用的工具之一。
它通过整理、整顿、清扫、标准化和自律五个步骤,帮助企业营造整洁、有序的工作环境,提高工作效率和质量。
四、精益管理的优势1. 提升效率:精益管理通过消除浪费和优化生产过程,可以大幅提升企业的生产效率。
这不仅意味着更短的生产周期和更快的交付速度,还意味着更高的产品质量和更低的成本。
2. 增强竞争力:在激烈的市场竞争中,企业必须不断提高效率和质量,才能保持竞争优势。
- 1、下载文档前请自行甄别文档内容的完整性,平台不提供额外的编辑、内容补充、找答案等附加服务。
- 2、"仅部分预览"的文档,不可在线预览部分如存在完整性等问题,可反馈申请退款(可完整预览的文档不适用该条件!)。
- 3、如文档侵犯您的权益,请联系客服反馈,我们会尽快为您处理(人工客服工作时间:9:00-18:30)。
生产精益管理的原则与技巧
建立稳定的流程,运用不断改进的工具以找出导致缺乏效率的根本原因,并采取有效的对策,把最佳实务标准化,以促进学习,而不是在每个新计划及每位新经理人上台后,又重新发明新方法。
一、生产精益管理的原则
1、建立无间断流程以使问题浮现。
要求重新设计流程,使流程不仅仅是工
作过程的描述。
一定要建立快速输送材料与信息的流程,使流程与员工的行为动作紧密地联结在一起。
要使整个企业文化重视流程,这是促成真正的持续改进流程及员工发展的关键。
2、实施拉式生产制度以避免生产过剩
在你生产流程下游的客户有需求的时候,供应给他们正确数量的正确东西。
使在制品及库存减至最少,每项产品只维持少量存货,根据向客户实际交付的数量,经常补充存货。
按客户的需求每天进行调整在制品和存货量,而不是依靠计算机的时间表与系统来追踪已经成为浪费的存货。
3、建立立即暂停以解决问题,从一开始就重视品质管理的文化
为顾客提供的品质决定着你的定价。
你要想收益高,首先需要品质好。
为了提高品质,应该使用所有能够确保产品品质的现代方法。
想一想,我们的方法是不是能够确保产品品质?使生产设备具有发现问题及一发现问题就停止生产的能力。
在企业中设立支持快速解决问题的制度和监督检测。
在企业文化中融入发生问题时立即暂停或减缓速度、就地改进质量以提升长期生产力的概念。
4、工作的标准化是持续改进与授权员工的基础
在工作场所中的任何地方都使用稳定、可重复的方法,以维持流程的可预测性、规律的运作时间,以及规律的产出。
到一定时间时,应该汲取对流程的累积学习心得,把“现在”的最佳实务进行标准化,让员工对于标准提出有创意的改进意见,把这些见解纳入新标准中。
5、使工作负荷水准稳定(生产均衡化),工作应象龟兔赛跑中的乌龟一样
杜绝浪费只是实现精益所必须做的工作的1/3。
避免员工与设备的负荷过重,以避免生产安排的不均匀,也同等重要。
尽量使所有制造与服务流程的工作负荷平均化,以取代大多数公司实行的批量生产方法中经常启动、停止、启动的做法。
6、使用可靠的、已经充分测试的技术以协助员工及生产流程
许多时候,最好的方法是让技术支持流程之前,先以人工方式证实流程切实可行。
技术应该是用来支持员工,而不是取代员工。
新技术往往不可靠而且难以标准化,因此会危害到流程。
让检验过的流程正常运转的重要性要优于未经充分测试的新技术。
在企业流程、制造系统或产品中采用新技术之前,必须先经过实际测试。
与企业文化有冲突,或可能会损及稳定性、可靠性与可预测性的技术,必须予以修正或干脆舍弃。
不过,在寻求新的工作方法时,必须鼓励员工考虑新技术。
若一项适合的技术已经过充分测试,且能改进你的流程,就应该快速实施。
7、运用视觉管理使问题无处隐藏
使用简单的视觉指示,以帮助员工立即确定它们是否出于标准状况下,抑或状况是否发生变异。
避免因使用计算机屏幕而使员工的注意力从工作场所移开。
设计简单的视觉系统,安装在执行工作的场所,以支持“一个流”与拉式制度。
尽可能把报告缩减为一页,即使是最重要的财务决策报告也是如此。
8、把彻底了解且拥护公司理念的员工培养成为领导者,使他们能教导其他员工。
尽量从企业内部栽培领导者,来代替完全从企业外招聘。
不要把领导者的职责视为只是完成工作和具备良好的人际关系技巧。
一位优秀的领导者必须对日常工作有事无巨细的了解,方能成为公司理念的最佳教导者。
9、亲临现场察看以彻底了解情况(现地现物)
精益生产强调:解决问题与改进流程必须追溯源头、亲自观察,然后验证所得数据,而不是根据他人所言及计算机屏幕所显示的东西来理论化。
根据亲自验证的资料来思考与叙述。
即使是高层经理与主管,也应该亲自察看情况,才不会对实际情况只有肤浅的表面了解。
10、培养与发展信奉公司理念的杰出人才与团队
一个公司应该创造坚实稳固的文化,使公司的价值观与信念普及并延续多年,而不是只关注产品的结果。
企业要有一批训练有素的杰出的个人与一支杰出团队,来实现公司理念,这才能使公司获得杰出成果,而这支团队应该非常努力的持续强化公司文化,这样才能使公司成为一个坚实的不可摧毁的整体。
要学会运用跨部门团队,来提高品质与生产效率,解决有难度的技术性问题,来改进流程。
公司应该持续努力教导员工如何以团队合作方式实现共同目标。
团队合作是员工务必学习的东西。
11、重视事业伙伴与供货商网络,激励并助其改进
精益企业要使自己的精益目标达成并保持,很重要的一点就是重视你的事业伙伴与供货商,把他们视为你事业的延伸。
激励你的外部事业伙伴,要求他们成长与发展。
12、不急于作决策,以共识为基础,彻底考虑所有可能的选择,并快速执行决策
在还没有周全考虑所有其它选择之前,不要武断的选定一个方向而一路走下去,一旦经过周全考虑而选定途径后,就要快速而谨慎的采取行动。
领导人在做重要决定时,必须设法将所有成员的意见都统一起来。
13、通过不断省思(反省)与持续改进以变成一个学习型组织
企业要有一个优先于任何短期决策的目的理念,使整个企业的运作与发展能配合着朝向这个比赚钱更重要的共同目的——长期稳固的发展。
长期理念和历史地位的起始点应该是为客户、为社会、为企业的收益创造价值。
二、生产精益管理的技巧
工作做到位的前提是摆正自己的职场位置。
员工应当做建筑师而不是小时工,要以老板的眼光审视工作成果;领导者应该做规划师而不是建筑工,在宏观上把控企业发展的方向,把企业资源合理配置,做幕后的推手。
到位的工作便是各司其职,在分内做到极致。
1、汇报工作说结果
请不要告诉老板工作过程多艰辛,你多么不容易!老板不傻,否则做不到今天。
老板最喜欢举重若轻的人,一定要把结果给老板,结果思维是第一思维。
2、请示工作说方案
不要让老板做问答题,而是要让老板做选择题。
请示工作至少保证给老板两个方案,并表达自己的看法。
3、总结工作说流程
做工作总结要描述流程,不只是先后顺序逻辑清楚,还要找出流程中的关键点、失误点、反思点。
4、布置工作说标准
工作有布置就有考核,考核就要建立工作标准,否则下属不知道如何做,做到什么程度才是最合适的。
标准既确立了规范,又划定了工作的边界。
5、关心下级问过程
关心下级就是关心细节,明确让下级感动的点和面。
关心下属要注意聆听他们的问题,让其阐述越详细越好。
6、交接工作讲道德
让员工把工作中形成的经验教训毫不保留的交接给继任者,把完成的与未竟的工作分类逐一交接,不要设置任何障碍,使其迅速进入工作角色。
7、回忆工作说感受
交流多说自己工作中的感悟,哪些是学到的,哪些是悟到的,哪些是反思的,哪些是努力的。
当你此刻很忙的时候就问问自己:
1、我在忙什么?
2、我忙的事有多大价值?
3、我做的事别人会不会做?
4、我为什么会这么忙?。