全员生产性维护
TPM_培训资料

TPM_培训资料TPM 培训资料一、TPM 简介TPM 即全员生产维护(Total Productive Maintenance),是一种以提高设备综合效率为目标,以全系统的预防维修为过程,全体人员参与为基础的设备保养和维修管理体系。
TPM 的核心目标是通过消除设备故障、降低维修成本、提高生产效率和产品质量,从而实现企业的可持续发展。
它强调的不仅仅是设备的维护和保养,更是一种全员参与、持续改进的管理理念。
二、TPM 的发展历程TPM 起源于 20 世纪 50 年代的美国,当时被称为“事后维修”。
到了20 世纪 60 年代,日本引进了这一理念,并结合自身的实际情况进行了改进和发展,形成了具有日本特色的 TPM 管理模式。
在 20 世纪 70 年代,TPM 开始在日本企业中广泛推广和应用,并取得了显著的成效。
随后,TPM 逐渐传播到世界各地,成为众多企业提升设备管理水平和生产效率的重要手段。
三、TPM 的八大支柱1、自主保全自主保全是指操作人员对自己操作的设备进行日常的清扫、点检、加油、紧固等保养工作。
通过自主保全,操作人员能够更加熟悉设备的性能和运行状况,及时发现并解决问题,从而提高设备的可靠性和稳定性。
2、计划保全计划保全是指由专业的维修人员根据设备的运行状况和故障规律,制定科学合理的维修计划,并按照计划进行定期的维修和保养工作。
计划保全能够有效地预防设备故障的发生,延长设备的使用寿命。
3、个别改善个别改善是指针对设备存在的问题和薄弱环节,组织专门的团队进行深入的分析和研究,制定切实可行的改善方案,并加以实施。
个别改善能够快速有效地解决设备的重大问题,提高设备的性能和效率。
4、品质保全品质保全是指通过设备的维护和保养,确保产品的质量稳定。
它要求在设备的设计、制造、安装、调试、使用和维护等各个环节,都要充分考虑到产品质量的要求,采取有效的措施防止质量问题的发生。
5、初期管理初期管理是指对设备的规划、设计、选型、购置、安装、调试等前期工作进行有效的管理。
22 现代汽车企业生产现场管理 文档:全员生产性维护

全员生产性维护1、全员生产性维修(TPM)的定义全员生产性维修(TPM)最初诞生于丰田汽车,是一套完备的全员生产性维修体系,它包括事后维修、预防维修、改善维修及维修预防。
全员生产性维修是指定义:通过在维修、生产和工程方面共享标准,最大限度利用设备、工装生产率的活动。
目的:通过提高保全意识、工作责任感及培养多能工来降低成本、安全事故,提高效率、质量。
整体开展思路是从事后维修转变到维修预防,即在设备的设计、制造源头考虑故障预防。
从TPM活动八大支柱角度理解,全员生产性维修包括了其中的两大核心支柱,即自主保全和专业保全。
2、全员生产性维修(TPM)条款全员生产性维修(TPM)包括5个条款:维修计划流程、自主保全、专业保全、维护系统有效性、备件条款1:维修计划流程主要包括5个方面:建立指标、共同验收、制定维护任务、标准化工作、应急响应流程条款2:操作人员自主保全:在设备状态劣化之前,可通过自主保全和专业保全的及时介入,提前排除设备故障或者延缓设备故障,建立操作人员自主保全制度,明确生产与维修的职责。
自主保全按照七步骤进行工作推进,共三个阶段初级阶段:主要开展清理、清扫活动中级阶段:通过培训、检查、维护提升自主保全技能高级阶段:形成一套标准化操作流程,常态化开展自主保全活动:初级阶段即步骤1-3的实施,目的是防止设备老化,使设备状态保持稳定;中级阶段的重点是执行步骤4,通过一般性检查来检测设备老化程度,为设备预防性维护提供支撑。
操作人员自主保全的核心要求有5个:设备维护任务定期执行、要有充足的维护时间、合格的设备维护技能、班组长为设备报警第一响应人、维护工作记录完整且可追溯。
条款3:维修员工专业保全专业保全是TPM八大支柱核心活动之一,是设备稳定运行的重要保障。
核心要求有5个:建立体系和标准、制定计划并实施、技能提升、过程分析、问题攻关。
条款4:设备维护系统有效性设备维护系统有效性主要是围绕过程开展,识别问题并整改,达到持续改进。
tpm管理常用手法

tpm管理常用手法
TPM(Total Productive Maintenance,全员生产维护)是一种基于集体行动和团队精神的生产维护管理方法,旨在通过最大限度地减少故障和停机时间,提高设备可靠性和生产效率。
以下是几种常用的TPM管理手法:
1.设备保养:对设备进行定期保养和检修,以确保设备的良好状态和可靠性。
包括预防性保养、周期性保养和条件监测等手段。
2.故障消除:对设备的故障进行及时排除和修复,并分析故障原因,采取措施防止再次发生相同的故障。
3.设备改进:通过改进设备的设计、工艺和操作方法等,提高设备的可靠性和效率。
包括对设备的升级、改造和优化等。
4.人员培训:为员工提供必要的技术培训和知识普及,使他们能够更好地理解和掌握设备的操作和维护方法。
5.一人多机:合理安排人员的工作任务,使其能够同时管理多台设备,提高生产效率和设备利用率。
6.标准化工作:制定标准作业流程和维护规范,确保所有操作都按照规定的标准进行,减少人为错误和设备损坏。
7.巡回检查:定期巡查设备,检查设备的运行状态和安全性,发现问题及时解决,防止设备出现故障。
8.设备管理信息系统:建立设备管理信息系统,对设备的运行状况、故障记录和维护情况进行数据收集和分析,为决策提供有力支持。
9.团队合作:建立团队合作和协作的机制,鼓励员工之间的交流和合作,共同解决设备问题,提高生产效率和质量。
10.持续改进:实施持续改进的思想和方法,不断寻求提高设备可靠性和效率的方法和措施,推动全员参与和持续改进的文化。
全员生产性维护(一)
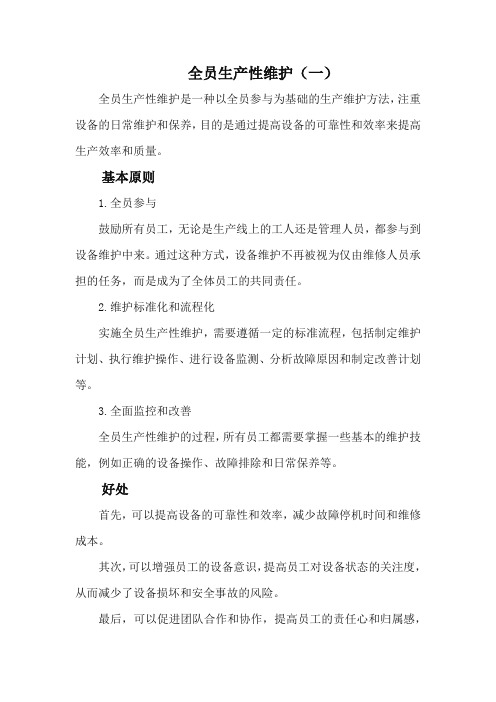
全员生产性维护(一)全员生产性维护是一种以全员参与为基础的生产维护方法,注重设备的日常维护和保养,目的是通过提高设备的可靠性和效率来提高生产效率和质量。
基本原则1.全员参与鼓励所有员工,无论是生产线上的工人还是管理人员,都参与到设备维护中来。
通过这种方式,设备维护不再被视为仅由维修人员承担的任务,而是成为了全体员工的共同责任。
2.维护标准化和流程化实施全员生产性维护,需要遵循一定的标准流程,包括制定维护计划、执行维护操作、进行设备监测、分析故障原因和制定改善计划等。
3.全面监控和改善全员生产性维护的过程,所有员工都需要掌握一些基本的维护技能,例如正确的设备操作、故障排除和日常保养等。
好处首先,可以提高设备的可靠性和效率,减少故障停机时间和维修成本。
其次,可以增强员工的设备意识,提高员工对设备状态的关注度,从而减少了设备损坏和安全事故的风险。
最后,可以促进团队合作和协作,提高员工的责任心和归属感,从而提高整个企业的生产力和竞争力。
关键因素在全员生产性维护的实施过程中,需要注意几个关键因素:第一,需要建立一个有效的维护体系,包括制定明确的维护标准和流程、培训员工掌握维护技能、建立设备档案和记录设备运行数据等。
第二,需要建立一个有效的监测机制,包括定期进行设备检查和监测、建立设备健康状况评估体系、及时发现设备故障和潜在风险等。
第三,需要制定一个有效的改善计划,包括针对设备故障原因制定相应的改善措施、推广最佳实践和经验教训等。
总而言之,全员生产性维护是一种以全员参与为基础的生产维护方法,旨在提高设备可靠性和效率、增强员工的设备意识和责任心、促进团队合作和协作等。
只有通过全体员工的共同努力和积极配合,才能够有效实施全员生产性维护,达到提高企业生产效率和质量的目标。
全员生产维护
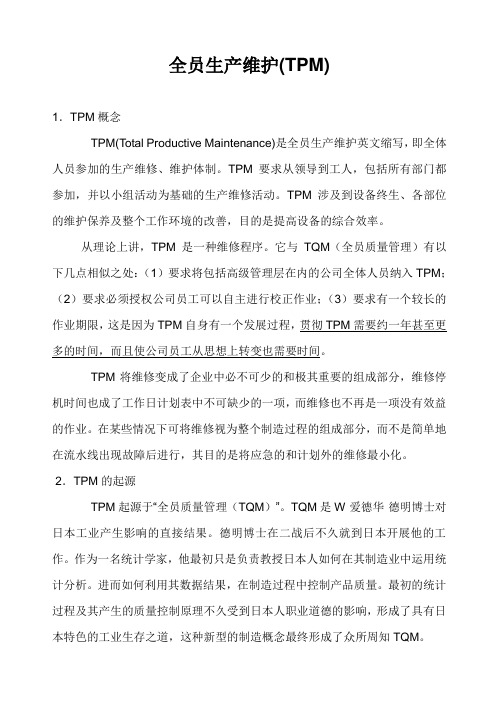
全员生产维护(TPM)1.TPM概念TPM(Total Productive Maintenance)是全员生产维护英文缩写,即全体人员参加的生产维修、维护体制。
TPM要求从领导到工人,包括所有部门都参加,并以小组活动为基础的生产维修活动。
TPM涉及到设备终生、各部位的维护保养及整个工作环境的改善,目的是提高设备的综合效率。
从理论上讲,TPM是一种维修程序。
它与TQM(全员质量管理)有以下几点相似之处:(1)要求将包括高级管理层在内的公司全体人员纳入TPM;(2)要求必须授权公司员工可以自主进行校正作业;(3)要求有一个较长的作业期限,这是因为TPM自身有一个发展过程,贯彻TPM需要约一年甚至更多的时间,而且使公司员工从思想上转变也需要时间。
TPM将维修变成了企业中必不可少的和极其重要的组成部分,维修停机时间也成了工作日计划表中不可缺少的一项,而维修也不再是一项没有效益的作业。
在某些情况下可将维修视为整个制造过程的组成部分,而不是简单地在流水线出现故障后进行,其目的是将应急的和计划外的维修最小化。
2.TPM的起源TPM起源于“全员质量管理(TQM)”。
TQM是W·爱德华·德明博士对日本工业产生影响的直接结果。
德明博士在二战后不久就到日本开展他的工作。
作为一名统计学家,他最初只是负责教授日本人如何在其制造业中运用统计分析。
进而如何利用其数据结果,在制造过程中控制产品质量。
最初的统计过程及其产生的质量控制原理不久受到日本人职业道德的影响,形成了具有日本特色的工业生存之道,这种新型的制造概念最终形成了众所周知TQM。
当TQM要求将设备维修作为其中一项检验要素时,发现TQM本身似乎并不适合维修环境。
这是由于在相当一段时间内,人们重视的是预防性维修(PM)措施,多数工厂也都采用PM,而且,通过采用PM技术制定维修计划以保持设备正常运转的技术业已成熟。
然而在需要提高或改进产量时,这种技术时常导致对设备的过度保养。
全员生产性维护
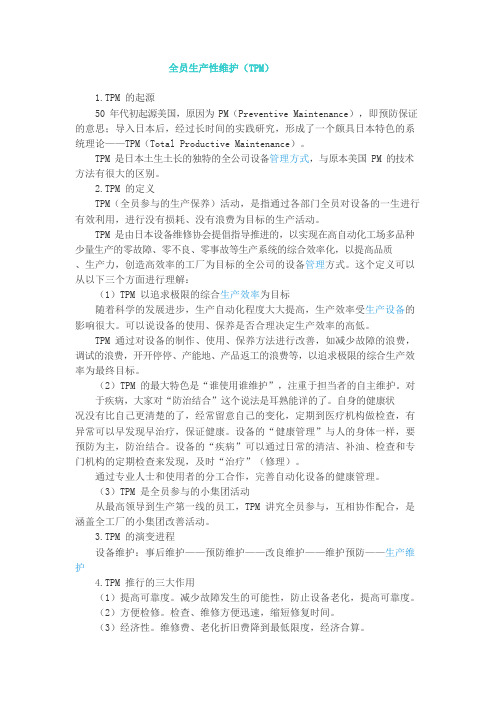
全员生产性维护(TPM)1.TPM 的起源50 年代初起源美国,原因为 PM(Preventive Maintenance),即预防保证的意思;导入日本后,经过长时间的实践研究,形成了一个颇具日本特色的系统理论——TPM(Total Productive Maintenance)。
TPM 是日本土生土长的独特的全公司设备管理方式,与原本美国 PM 的技术方法有很大的区别。
2.TPM 的定义TPM(全员参与的生产保养)活动,是指通过各部门全员对设备的一生进行有效利用,进行没有损耗、没有浪费为目标的生产活动。
TPM 是由日本设备维修协会提倡指导推进的,以实现在高自动化工场多品种少量生产的零故障、零不良、零事故等生产系统的综合效率化,以提高品质、生产力,创造高效率的工厂为目标的全公司的设备管理方式。
这个定义可以从以下三个方面进行理解:(1)TPM 以追求极限的综合生产效率为目标随着科学的发展进步,生产自动化程度大大提高,生产效率受生产设备的影响很大。
可以说设备的使用、保养是否合理决定生产效率的高低。
TPM 通过对设备的制作、使用、保养方法进行改善,如减少故障的浪费,调试的浪费,开开停停、产能地、产品返工的浪费等,以追求极限的综合生产效率为最终目标。
(2)TPM 的最大特色是“谁使用谁维护”,注重于担当者的自主维护。
对于疾病,大家对“防治结合”这个说法是耳熟能详的了。
自身的健康状况没有比自己更清楚的了,经常留意自己的变化,定期到医疗机构做检查,有异常可以早发现早治疗,保证健康。
设备的“健康管理”与人的身体一样,要预防为主,防治结合。
设备的“疾病”可以通过日常的清洁、补油、检查和专门机构的定期检查来发现,及时“治疗”(修理)。
通过专业人士和使用者的分工合作,完善自动化设备的健康管理。
(3)TPM 是全员参与的小集团活动从最高领导到生产第一线的员工,TPM 讲究全员参与,互相协作配合,是涵盖全工厂的小集团改善活动。
TPM全员生产性维护(标准模板)

3。同时通过清扫可有助于操作人员对设备产生爱护之心。
TPM
“设备的不良70%以上来自润滑与清扫的不良”
TPM
设备故障的六大原因
设备故障的六大原因
1.润滑不良 2.灰尘沾污 3.螺栓松弛; 4.受热 5.潮湿 6.保温不良
清扫、润滑
点检
TPM
进行清扫顺序
从最脏的地方开始 从设备的上面到下面 以发生源为中心向外 从上游到下游 从加工点到外观
2、“零”目标
3、全员参与
TPM
TPM的终极目标
停机为零:指计划外的设备停机时间为零。计划外的停机对生产造成 冲击相当大,使整个生产发生困难,造成资源闲置等 浪费。计划时间要有一个合理值,不能为了满足非计划停 机为零而使计划停机时间值达到很高。 废品为零:指由设备原因造成的废品为零。“完美的质量需要完善的 机器”,机器是保证产品质量的关键,而人是保证机器好 坏的关键。 事故为零:指设备运行过程中事故为零。设备事故的危害非常大,影 响生产不说,可能会造成人身伤害,严重的可能会“机毁 人亡”。 速度损失为零:指设备速度降低造成的产量损失为零。由于设备保养不好 ,设备精度降低而不能按高速度使用设备,等于降低了设备性能。
工艺的应有姿态 *现场员工所操作的所有设备是不是都按照准确的 管理基准,进行正确的管理中。
TPM
TPM 的理念
自己的设备自己管理
治疗恢复能力 维持管理能力
成为设备专家级员工
发现异常能力 设定条件能力
习惯化
•清扫,紧固、注油
因为一个企业这么大, 光靠几个几十个维修人员 维护,就算是一天8个小 时不停地巡查,也很难防 止一些显在或潜在问题发 生。
给油
发热点检
给油 清扫 母亲
TPM全员生产性维护培训讲义

TPM
TPM的发展史
1951年,美国提出了PM,日本企 业在PM基础上,经改良后,形成 了现在的TPM理论。它以与生产密 切相关的设备为切入点,通过设备, 工作环境的改善来改善人的看法, 想法,进而改善企业的体制。
TPM
TPM的发展史
50年代进行事后保全 60年代进行预防保全 70年代进行全员保全
废品/返工
准备时间
Breakdowns 16%
停机
M in o r
S t g T im e (O .E .E .) 40%
运行时间
World-Class OEE Measurements
Same equipment, 112% more capacity
重点实施事项 在全员中深入 积极开展
保全部门协力 解决发现的问 题,并简化保 全活动 记录点检结果, 并进行对策处 理
针对问题点迅 速进行改善
紧密团结,制 定目标及指标, 激动灵活地解 决问题 实施保全教育, 提高技能,积 极扩展自主保 全活动 适时审视点检 项目、基准及 要领书,并做 适当修正 推测故障点, 为降低MTTR而 实施改善
按时间计算生产量 每人的生产量 设备综合效率
备品的在库金额,在库天数的统计与管理
区分
保全作业
设备故障
保全性 人才育成
TPM目标项
项目
计划保全率 计划保全的达成率 改良设备的件数 突发设备故障的及件数 长时间设备停止的件数 关键设备的平均故障间隔 平均维修时间 个人技能的评价 取得某一资格的人数
TPM
以前一年度的实际情况为基础设定目标 以公司内同类工序的实际为基础设定目标
以同行业好的对手为基础设定目标
区分
安全 品质
全员生产维护(简称TPM Total Productive Maintenance)
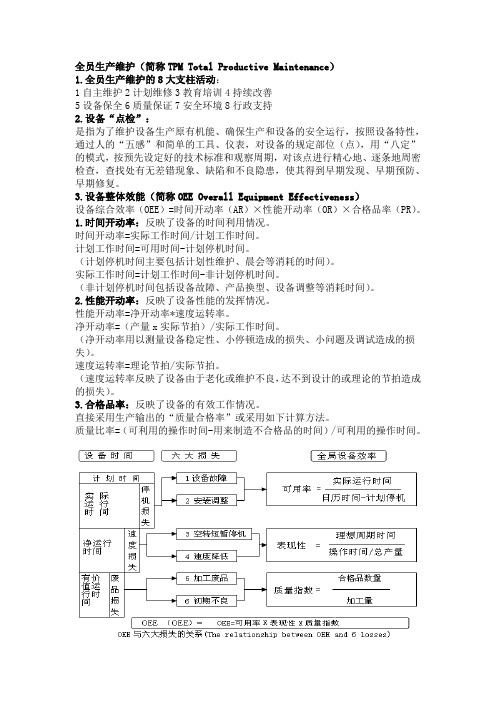
全员生产维护(简称TPM Total Productive Maintenance)1.全员生产维护的8大支柱活动:1自主维护2计划维修3教育培训4持续改善5设备保全6质量保证7安全环境8行政支持2.设备“点检”:是指为了维护设备生产原有机能、确保生产和设备的安全运行,按照设备特性,通过人的“五感”和简单的工具、仪表,对设备的规定部位(点),用“八定”的模式,按预先设定好的技术标准和观察周期,对该点进行精心地、逐条地周密检查,查找处有无差错现象、缺陷和不良隐患,使其得到早期发现、早期预防、早期修复。
3.设备整体效能(简称OEE Overall Equipment Effectiveness)设备综合效率(OEE)=时间开动率(AR)×性能开动率(OR)×合格品率(PR)。
1.时间开动率:反映了设备的时间利用情况。
时间开动率=实际工作时间/计划工作时间。
计划工作时间=可用时间-计划停机时间。
(计划停机时间主要包括计划性维护、晨会等消耗的时间)。
实际工作时间=计划工作时间-非计划停机时间。
(非计划停机时间包括设备故障、产品换型、设备调整等消耗时间)。
2.性能开动率:反映了设备性能的发挥情况。
性能开动率=净开动率*速度运转率。
净开动率=(产量x实际节拍)/实际工作时间。
(净开动率用以测量设备稳定性、小停顿造成的损失、小问题及调试造成的损失)。
速度运转率=理论节拍/实际节拍。
(速度运转率反映了设备由于老化或维护不良,达不到设计的或理论的节拍造成的损失)。
3.合格品率:反映了设备的有效工作情况。
直接采用生产输出的“质量合格率”或采用如下计算方法。
质量比率=(可利用的操作时间-用来制造不合格品的时间)/可利用的操作时间。
tpm评估
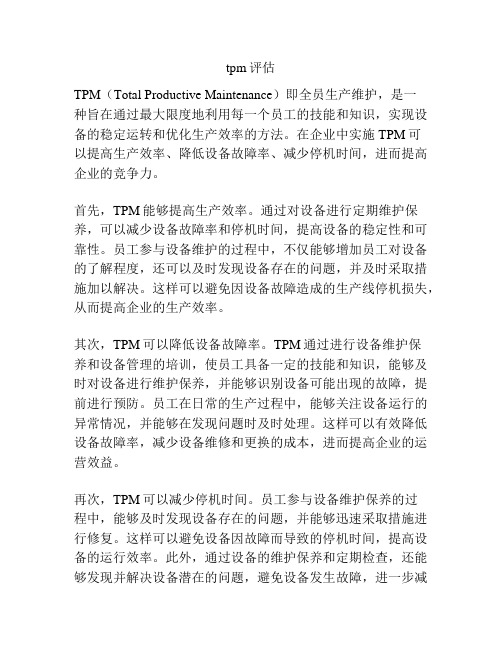
tpm评估TPM(Total Productive Maintenance)即全员生产维护,是一种旨在通过最大限度地利用每一个员工的技能和知识,实现设备的稳定运转和优化生产效率的方法。
在企业中实施TPM可以提高生产效率、降低设备故障率、减少停机时间,进而提高企业的竞争力。
首先,TPM能够提高生产效率。
通过对设备进行定期维护保养,可以减少设备故障率和停机时间,提高设备的稳定性和可靠性。
员工参与设备维护的过程中,不仅能够增加员工对设备的了解程度,还可以及时发现设备存在的问题,并及时采取措施加以解决。
这样可以避免因设备故障造成的生产线停机损失,从而提高企业的生产效率。
其次,TPM可以降低设备故障率。
TPM通过进行设备维护保养和设备管理的培训,使员工具备一定的技能和知识,能够及时对设备进行维护保养,并能够识别设备可能出现的故障,提前进行预防。
员工在日常的生产过程中,能够关注设备运行的异常情况,并能够在发现问题时及时处理。
这样可以有效降低设备故障率,减少设备维修和更换的成本,进而提高企业的运营效益。
再次,TPM可以减少停机时间。
员工参与设备维护保养的过程中,能够及时发现设备存在的问题,并能够迅速采取措施进行修复。
这样可以避免设备因故障而导致的停机时间,提高设备的运行效率。
此外,通过设备的维护保养和定期检查,还能够发现并解决设备潜在的问题,避免设备发生故障,进一步减少停机时间,提高生产效率和生产线的稳定性。
最后,TPM可以提高企业的竞争力。
通过实施TPM,企业能够提高生产效率、降低设备故障率、减少停机时间,提高产品质量和交货时间的稳定性。
这些优势可以帮助企业赢取更多的客户订单,提升企业的市场竞争力。
同时,TPM还强调员工的参与和团队合作,能够促进员工的技能提升和团队协作能力的增强,对企业文化的建设和人才培养也起到一定的促进作用。
综上所述,TPM是一种针对设备维护和生产效率优化的方法。
通过TPM的实施,可以提高生产效率、降低设备故障率、减少停机时间,进而提高企业的竞争力。
TPM定义

TPM的起源及演进发展
供应链的TPM时代
2000年开始,TPM已经跨行业国际化发展。TPM并 不是只属于日本的产业界,世界各地对TPM的关心 逐年升高。这时也不是在某个企业实施,它逐渐向 服务、流通等行业发展,逐步优化供应链系统。
TPM的起源及演进发展
改良保全时代(CM)
1957年,人们开始对原来的保养方法进行改良, 根据设备零件的使用周期定期更换零件,使设备运 转更加正常。根据零件的使用周期,在零件使用寿 命到期之前更换零件,既有效地利用了零件,又防 止了故障的发生。
TPM的起源及演进发展
保全预防时代(MP)
1960年开始,进入了保全预防时代。人们不但对 设备进行保养,而且把保养和预防结合起来。通过 对设备的运行情况进行记录,根据设备的运行情况 (比如声音、颜色的变化)可以判断设备是否正常 工作。
TPM含义及推进流程
一、TPM含义 二、TPM发展历史 三、TPM的目标 四、TPM的八大支柱 五、TPM活动的效果 六、TPM推进流程
TPM含义
一、认识TPM TPM是(Total Productive Maintenance)的英 文缩写,意为“全员生产性保全活动”(或叫全员 生产维护)。1971年首先由日本人倡导提出。它原 来的狭义定义是:全体人员,包括企业领导、生产 现场工人以及办公室人员参加的生产维修、保养体 制。TPM的目的是达到设备的最高效益,它以小组 活动为基础,涉及到设备全系统。
全员生产维修(TPM)

全员生产维修(TPM)概论TPM(Total Productive Maintenance)的意思就是是“全员生产维修”,这是日本人在70年代提出的,是一种全员参与的生产维修方式,其主要点就在“生产维修”及“全员参与”上。
通过建立一个全系统员工参与的生产维修活动,使设备性能达到最优。
什么是TPM?TPM的提出是建立在美国的生产维修体制的基础上,同时也吸收了英国设备综合工程学、中国鞍钢宪法中群众参与管理的思想。
在非日本国家,由于国情不同,对TPM的理解是:利用包括操作者在内的生产维修活动,提高设备的全面性能。
TPEM:Total Productive Equipment Management 就是全面生产设备管理。
这是一种新的维修思想,是由国际TPM协会发展出来的。
它是根据非日本文化的特点制定的。
使得在一个工厂里安装TPM活动更容易成功一些,和日本的TPM不同的是它的柔性更大一些,也就是说你可根据工厂设备的实际需求来决定开展TPM的内容,也可以说是一种动态的方法。
TPM的特点、目标、理论基础和推行要素TPM的特点:TPM的特点就是三个“全”,即全效率、全系统和全员参加。
全效率:指设备寿命周期费用评价和设备综合效率。
全系统:指生产维修系统的各个方法都要包括在内。
即是PM、MP、CM、BM等都要包含。
全员参加:指设备的计划、使用、维修等所有部门都要参加,尤其注重的是操作者的自主小组活动。
TPM的目标:TPM的目标可以概括为四个“零”,即停机为零、废品为零、事故为零、速度损失为零。
停机为零:指计划外的设备停机时间为零。
计划外的停机对生产造成冲击相当大,使整个生产品配发生困难,造成资源闲置等浪费。
计划时间要有一个合理值,不能为了满足非计划停机为零而使计划停机时间值达到很高。
废品为零:指由设备原因造成的废品为零。
“完美的质量需要完善的机器”,机器是保证产品质量的关键,而人是保证机器好坏的关键。
事故为零:指设备运行过程中事故为零。
2024年度-TPM全员生产性维护培训课件
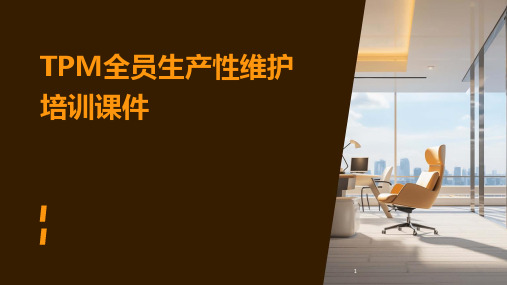
1
目 录
• TPM概述与基本原理 • 设备管理与预防性维护策略 • 自主维护与小组活动推进 • 计划性维护与专业保全实施 • 故障分析与诊断技术提升 • TPM推进策略与领导力建设 • 总结回顾与展望未来发展趋势
2
CHAPTER 01
TPM概述与基本原理
3
TPM定义及发展历程
利用人工智能、大数据等 技术,对设备运行数据进 行实时监测和分析,实现 故障预警和智能诊断。
多学科融合诊断
结合机械、电气、液压等 多学科知识,对复杂故障 进行综合诊断。
22
复杂问题解决方案探讨
跨部门协作
建立跨部门协作机制,共同解决复杂问题,提高问题解决效率。
专家团队支持
组建专家团队,对复杂问题进行深入研究和分析,提出针对性解 决方案。
提供必要的资源和支持
3
领导者应提供必要的资源,如资金、技术、人力 等,支持TPM活动的开展,确保各项计划和方案 的顺利实施。
26
跨部门协作与资源整合
加强跨部门沟通与协作
建立有效的跨部门沟通机制,促进不同部门之间的信息交 流与合作,共同解决TPM推进过程中遇到的问题。
整合内外部资源
充分利用企业内外部的资源,如专业机构、行业协会、供 应商等,为TPM推进提供有力支持。
备综合效率。
15
CHAPTER 04
计划性维护与专业保全实施
16
计划性维护流程设计
制定维护计划
维护计划审批
根据设备的重要程度、使用频率、故障历 史等数据,制定合理的维护计划,明确维 护周期、维护内容、维护人员等要素。
维护计划需要经过相关部门审批,确保计 划的合理性和可行性。
(TPM生产维护)全员生产维修(TPM)

概论TPM(Total Productive Maintenance)的意思就是是“全员生产维修”,这是日本人在70年代提出的,是一种全员参与的生产维修方式,其主要点就在“生产维修”及“全员参与”上。
通过建立一个全系统员工参与的生产维修活动,使设备性能达到最优。
什么是TPM?TPM的提出是建立在美国的生产维修体制的基础上,同时也吸收了英国设备综合工程学、中国鞍钢宪法中群众参与管理的思想。
在非日本国家,由于国情不同,对TPM的理解是:利用包括操作者在内的生产维修活动,提高设备的全面性能。
TPEM:Total Productive Equipment Management 就是全面生产设备管理。
这是一种新的维修思想,是由国际TPM协会发展出来的。
它是根据非日本文化的特点制定的。
使得在一个工厂里安装TPM活动更容易成功一些,和日本的TPM不同的是它的柔性更大一些,也就是说你可根据工厂设备的实际需求来决定开展TPM的内容,也可以说是一种动态的方法。
TPM的特点、目标、理论基础和推行要素TPM的特点:TPM的特点就是三个“全”,即全效率、全系统和全员参加。
全效率:指设备寿命周期费用评价和设备综合效率。
全系统:指生产维修系统的各个方法都要包括在内。
即是PM、MP、CM、BM等都要包含。
全员参加:指设备的计划、使用、维修等所有部门都要参加,尤其注重的是操作者的自主小组活动。
TPM的目标:TPM的目标可以概括为四个“零”,即停机为零、废品为零、事故为零、速度损失为零。
停机为零:指计划外的设备停机时间为零。
计划外的停机对生产造成冲击相当大,使整个生产品配发生困难,造成资源闲置等浪费。
计划时间要有一个合理值,不能为了满足非计划停机为零而使计划停机时间值达到很高。
废品为零:指由设备原因造成的废品为零。
“完美的质量需要完善的机器”,机器是保证产品质量的关键,而人是保证机器好坏的关键。
事故为零:指设备运行过程中事故为零。
全面生产性维护

全面生产性维护(TPM)一、TPM即全面生产性维护主要以设备为着眼点,针对设备整个生命周期中企业的综合效率进行提高。
它包括个别改善、自主保养、计划保养、教育训练、品质保养、设备初期管理、管理间接部门和安全与环境管理八大支柱。
二、大知公司认为,TPM不同于以往的传统设备管理的关键在于以下观念的转变:设备日常保养、维护甚至维修工作应该由生产部门完成。
设备自己不会发生故障,所谓故障是指人之“故”导致的设备“障”碍。
设备综合效率不高是由于存在设备的七大损耗,消除这些损耗也就意味着效率的提高。
企业所有的人,所有部门,设备的整个生命周期中的所有环节都会影响设备综合效率,全员持续不断的参与改进活动才能提高企业综合效率。
三、大知公司凭借多年来的经验,在帮助客户企业推行TPM项目时有以下特点:不同支柱的内容分阶段进行,不贪图一开始就全面铺开,首先从自主保养、计划保养、个别改善和技能教育训练开始。
根据企业特点帮助客户企业设置设备效率的衡量指标系统。
结合企业原有的持续改进系统,将大知适用于中国企业的NWG小组工作原理融入客户企业。
四、大知公司的建议TPM首先是一个系统工程,企业如果一旦决策在企业内推行TPM,就必须不遗余力的推动下去,很多企业建立了专门的TPM事务局却没有实际的权利,反而造成浪费。
TPM的发展必须根据企业实际来制定发展计划,TPM理论中的八大支柱的完善没有所谓的标准计划,譬如目前有不少企业的设备是国外原装进口,设备维护也由外国专家进行,企业内本身尚不具备维修和维护的能力,对于设备初期管理、计划保养及品质保养三个支柱就很难发挥作用;有些公司所有设备使用中的维修保养全部外包,自主保养支柱就少有用武之地。
任何时候企业在决定开展TPM活动时,都必须首先了解自己公司的5S状态和持续改进组织的状态,这是开展TPM的基础;其次要了解目前公司所运用的衡量设备效率的指标是否科学,是否能反映TPM理念,这是TPM活动开展的衡量标准;然后你要了解你的员工和技术人员的技能水平以及公司现有的管理水平,这决定了TPM项目的进度。
tpm岗位职责

tpm岗位职责TPM(Total Productive Maintenance)即全员参与的全面生产维护,是一种通过最大限度减少设备故障和损失来提高生产效率和质量的方法。
TPM岗位是企业中非常关键的职位之一,本文将着重介绍TPM岗位的职责和重要性。
一、TPM岗位职责概述TPM岗位是负责协调和推动公司内部TPM实施并确保生产过程中的设备保养和维护的职务。
该职位的主要职责包括但不限于以下几个方面:1. 制定和落实TPM计划:制定公司的TPM计划,并协调各部门的工作,确保计划的顺利实施。
2. 进行设备故障分析:及时响应设备故障,并进行详细的分析,找出故障的原因和解决方法,以减少故障频率和时间。
3. 监控设备维护和保养:负责监控设备维护和保养的执行情况,并保证按照计划进行,以确保设备处于最佳状态。
4. 培训和指导员工:组织和开展相关的培训,以提高员工的TPM 意识和技能水平,确保员工正确地进行设备维护和保养工作。
5. 改进和优化生产过程:参与生产过程的改进和优化,通过减少故障、提高效率和质量来提高生产效果。
二、TPM岗位职责的重要性1. 提高设备可靠性和稳定性:TPM的核心目标是最大限度地减少设备故障和停机时间,通过合理的维护计划和保养工作,可以提高设备的可靠性和稳定性,减少生产中的不确定因素。
2. 增加生产效率和产能:设备故障和停机时间会导致生产效率降低和产能减少,而TPM岗位的职责是及时解决设备问题,确保设备的正常运行,从而提高生产效率和产能。
3. 降低生产成本和能源消耗:设备故障和损坏会增加维修和更换的成本,而通过TPM岗位的职责,可以及时发现和解决问题,降低生产成本。
同时,合理的设备维护和保养也能够降低能源的消耗。
4. 提升产品质量和客户满意度:设备故障和不良问题会导致产品质量下降和客户满意度降低。
TPM岗位的职责是确保设备处于最佳状态,能够减少产品缺陷,提高产品质量和客户满意度。
5. 建立良好的团队合作和沟通机制:TPM的实施需要各个部门之间的紧密合作和有效沟通。
全员生产性维护(二)

全员生产性维护(二)全员生产性维护的主要目的是通过整合和利用企业内部全部资源,积极推进企业生产力提升,优化生产流程和制造工艺,降低生产成本和质量成本,提高产品质量和竞争力,增加企业收入和利润,从而实现企业的可持续发展。
全员生产性维护的意义主要有以下几个方面:1.促进企业资源的有效利用:全员生产性维护可以充分利用企业内部的全部资源,包括人力、物力、财力等,从而实现企业生产成本的有效控制和资源的最大化配置。
2.提升企业生产力水平:全员生产性维护可以通过技术革新和生产流程的优化等手段,提高企业生产力水平,同时提高产品质量和降低生产成本,从而提高企业的效益和竞争力。
3.增强员工的生产意识:全员生产性维护是一种全员参与的生产管理模式,在实践中,可以充分调动员工的工作热情和积极性,提高工作效率和质量,同时培养员工的质量观念和团队合作意识。
4.优化企业管理模式:全员生产性维护要求企业在生产管理上进行全面思考和优化调整,从而推动企业管理模式的升级和改进,提高企业的效益和市场竞争力。
全员生产性维护的步骤包括:调查问题的症状:收集关于症状的详细信息,如观察、实物证据和照片证据。
建立TPM和部门委员会。
实施计划性维护。
安排计划中的停机时间,以实施商定的修复措施。
实施修复,重新启动生产,观察修复的效果如何。
如果修复成功,则记下实施这一改变,并转到下一个停工时间的原因。
如果修复不成功,则收集更多的信息,再举行一次头脑风暴会议。
全员生产性维护的工具和方法包括:活动板:活动板是一种展示团队活动和结果的工具,可以通过它来跟踪团队成员、活动领域、理想状态描述、当前活动状态和成就、团队年度活动计划和目标等信息。
小组会议:小组会议是一种在全员生产性维护中实施的活动,通过会议讨论并解决各种问题。
简单的培训形式:简单的培训形式是一种有效的工具,可以用于提高团队成员的技能和意识。
总之,全员生产性维护是一种有效的生产管理方法,可以帮助企业提高设备维保、产品质量、成本效益、交付能力、持续改善等各方面的管理水平,为企业发展提供强劲的驱动力。
- 1、下载文档前请自行甄别文档内容的完整性,平台不提供额外的编辑、内容补充、找答案等附加服务。
- 2、"仅部分预览"的文档,不可在线预览部分如存在完整性等问题,可反馈申请退款(可完整预览的文档不适用该条件!)。
- 3、如文档侵犯您的权益,请联系客服反馈,我们会尽快为您处理(人工客服工作时间:9:00-18:30)。
全员生产性维护(TPM)
1.TPM的起源
50年代初起源美国,原因为PM(Preventive Maintenance),即预防保证的意思;导入日本后,经过长时间的实践研究,形成了一个颇具日本特色的系统理论——TPM(Total Productive Maintenance)。
TPM是日本土生土长的独特的全公司设备管理方式,与原本美国PM的技术方法有很大的区别。
2.TPM的定义
TPM(全员参与的生产保养)活动,是指通过各部门全员对设备的一生进行有效利用,进行没有损耗、没有浪费为目标的生产活动。
TPM是由日本设备维修协会提倡指导推进的,以实现在高自动化工场多品种少量生产的零故障、零不良、零事故等生产系统的综合效率化,以提高品质、生产力,创造高效率的工厂为目标的全公司的设备管理方式。
这个定义可以从以下三个方面进行理解:
(1)TPM以追求极限的综合生产效率为目标
随着科学的发展进步,生产自动化程度大大提高,生产效率受生产设备的影响很大。
可以说设备的使用、保养是否合理决定生产效率的高低。
TPM通过对设备的制作、使用、保养方法进行改善,如减少故障的浪费,调试的浪费,开开停停、产能地、产品返工的浪费等,以追求极限的综合生产效率为最终目标。
(2)TPM的最大特色是“谁使用谁维护”,注重于担当者的自主维护。
对于疾病,大家对“防治结合”这个说法是耳熟能详的了。
自身的健康状况没有比自己更清楚的了,经常留意自己的变化,定期到医疗机构做检查,有异常可以早发现早治疗,保证健康。
设备的“健康管理”与人的身体一样,要预防为主,防治结合。
设备的“疾病”可以通过日常的清洁、补油、检查和专门机构的定期检查来发现,及时“治疗”(修理)。
通过专业人士和使用者的分工合作,完善自动化设备的健康管理。
(3)TPM是全员参与的小集团活动
从最高领导到生产第一线的员工,TPM讲究全员参与,互相协作配合,是涵盖全工厂的小集团改善活动。
3.TPM的演变进程
设备维护:事后维护——预防维护——改良维护——维护预防——生产维护
4.TPM推行的三大作用
(1)提高可靠度。
减少故障发生的可能性,防止设备老化,提高可靠度。
(2)方便检修。
检查、维修方便迅速,缩短修复时间。
(3)经济性。
维修费、老化折旧费降到最低限度,经济合算。
5.TPM推进的工作分工
(1)由维护保养责任部门(一般为生产技术部门)划分对象设备。
责任部门根据对生产影响的重要程度来选择对象设备,如对生产造成重大经济损失的、仅一台的、不能用其它设备代替的、修理复杂而时间长的等等。
(2)对上述重要设备,生产技术部门要明确规定其技术参数,并指导使用人员每日进行保养和检查。
(3)专业人员则对设备实施定期检查(测试鉴定),判定设备性能是否良好。
6.TPM成功的基本要素
(1)使用者是否有彻底防止故障的意识;
(2)是否理解生产性维护需要全员参与;
(3)有无专门的推进组织;
(4)现场、生产技术部门、专业人员是否紧密配合,系统管理;
(5)小组活动和改善的活跃程度;
(6)领导的理解支持程度;
(7)全公司的推进状态。