机加工检验记录表
施工现场施工机具(挖掘机)检查验收记录表

使用地点
设备型号
验收日期
验收项目
验收内容及要求
验收结果
外观验收灯光、仪表正Fra bibliotek,齐全有效轮胎螺丝紧固无缺少、传动螺丝紧固无缺少
方向机横、竖杆无松动
无漏油、漏气、漏水
全车各部位无变形
检查油位水
位
水箱水位正常、机油油位正常、方向机机油油位、刹车机动油正常变速箱油位正常、液压油位正常、各齿轮油位正常、电瓶水位正常
发动机部分
机油压力怠速时不少于1.5kg/cm2、水温正常
发动机运转正常无异响、各辅助机构工作正常
液压传动部
分
液压泵压力正常、行走系统正常、液压油温无异常
举臂油缸、转斗油缸起升正常
底盘部分
液压耦合器、变速箱正常,刹车系统、各操控、行走系统正常
安全防护
操作人员持证上岗
验收结论:
CNC首尾件检验记录表

编号:
□不合格,重新调机 □不合格,重新调机 □合格,正常生产 □合格,正常生产 □特采,QE______ □特采,QE______
□NG;物料隔离返修 □OK;物料正常流通
检 验
备注:1.同一台机床在工装、工艺、产品没有变更的情况下15天有效,15天后重新首检; 2.三次首检不合格需要部门主管签字确认,并指导调机,调机品不允许超过5件; 3.出现批量质量事故(不良率超过10%,批量不良数量超过20件)需要重新调机首检.
CNC首/尾件检验记录表
日
调机开始
单件加工
期 产 品 机 台
时间:
产品图号
产品批号
调机员
时长:
班次
版本
序 号
ห้องสมุดไป่ตู้
检验项目
□第一次
检验结果
□第二次
□第三次
末件检验
1
2
3
4
5
6
7
8
9
10
11
12
13
14
15
16
17
18
19
20
调机送检时间
检验完成时间
结果判定
□不合格,重新调 机 □合格,正常生产 □特采,QE______
立式加工中心精度检测记录表

9
主轴端面轴向跳动
B:
10
主轴端锥孔径向跳动
C:
11
主轴偏差(摆差)(主轴与主轴锥孔中心线的同轴度)
将检验棒插入主轴端锥孔内,将千分表分别打至检验棒外圆顶端与靠近主轴之根部,转动主轴,读取跳动数值之最大差为测量值。
A:
B:
12
主轴中心线与
Z轴方
向运动的平行度
X
Z
将检验棒插入主轴端锥孔内,将千分表打至检验棒外圆,并沿Z轴方向移动主轴,读取检验棒顶端与靠近主轴根部之跳动数值最大差为测量值。
Per 300
6
Z轴方
向运动与工作台面的垂直度
X
Z
将工作台移至X轴方向运动全程之中央,将角尺置于工作台上,再将固定于主轴头上之千分表与之接触,并沿Z轴方向移动主轴头,以千分表读数之最大差为测量值。
Per 300பைடு நூலகம்
Y
Z
将固定于主轴上之千分表与置于工作台上之角尺接触,并沿Z轴方向移动主轴,以千分表读数之最大差为测量值。
Per 300
7
主轴中心线与工作台面的垂直度
X
Z
将固定于主轴头之千分表与工作台顶面接触,并予以转动,以千分表读数之最大差为测量值。
旋径 300
Y
Z
旋径 300
8
主轴端外圆径向跳动
将千分表表座固定于工作台面或主轴座上,将千分表表针分别打至主轴端外圆、主轴端端面、主轴端锥孔壁,转动主轴,测量跳动数值差。
Per 300
4
X轴方向运动与工作台基准T形槽侧面的平行度
将直规之凸边与工作台基准T形槽侧面依靠,在其垂直面将固定于主轴头之千分表与之接触,并沿X轴方向移动工作台连同直规,以全程距离内千分表读数之最大差为测量值。
机加工制程检验记录表
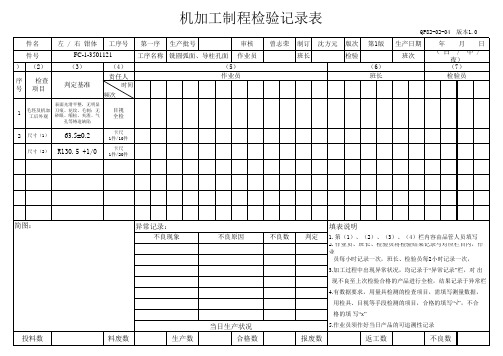
件名
左 / 右 钳体 工序号 第一序 生产批号
审核
(1 件号 ) (2)
序 检查 号 项目
FC-1-3501121
工序名称 铣圆弧面、导柱孔面 作业员
(3) 判定基准
(4) 责任人
时间
(5) 作业员
频次
表面光滑平整,无明显
1
毛坯及机加 刀痕、花纹、毛刺;无 工后外观 砂眼、缩松、夹渣、气
生产数
不良原因
当日生产状况 合格数
不良数
判定
填表说明
1.第(1)、(2)、(3)、(4)栏内容由品管人员填写 2.作业员、班长、检验员将检验结果记录与对应栏目内,作 业
员每小时记录一次,班长、检验员每2小时记录一次,
3.加工过程中出现异常状况,均记录于“异常记录”栏,对 出
现不良至上次检验合格的产品进行全检,结果记录于异常栏
孔等铸造缺陷
目视 全检
2 尺寸(1) 63.5±0.2 尺寸(2) R130.5 +1/0
卡尺 1件/10件
卡尺 1件/20件
曾志荣 制长
QP82-02-04 版本1.0
生产日期 班次
年月日 (白 / 中/
夜) (7)
检验员
简图: 投料数
异常记录: 不良现象
料废数
4.有数据要求,用量具检测的检查项目,需填写测量数据, 用检具、目视等手段检测的项目,合格的填写“√”,不合 格的填 写“х”
5.作业员须作好当日产品的可追溯性记录
报废数
返工数
不良数
过程检验记录表
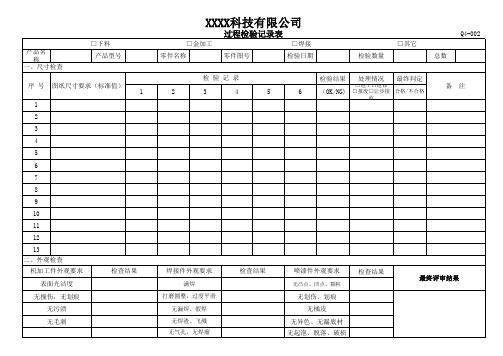
Q4-002 □焊接 □其它 检验数量 检验结果 处理情况
□返工□返修 收
□金加工 零件名称 零件图号
产品型号
检验日期
总数 最பைடு நூலகம்判定 备 注
图纸尺寸要求(标准值)
1
2
3
4
5
6
(OK/NG) □报废□让步接 合格/不合格
检查结果
喷漆件外观要求
无凸点、凹点、颗粒
检查结果
最终评审结果
无划伤、划痕 无橘皮 无异色、无漏底材 无起泡、脱落、破损
XXXX科技有限公司
过程检验记录表
□下料 产品名称 一、尺寸检查 检 验 记 录 序 号 1 2 3 4 5 6 7 8 9 10 11 12 13 二、外观检查 机加工件外观要求 表面光洁度 无撞伤,无划痕 无污渍 无毛刺 检查结果 焊接件外观要求
满焊 打磨圆整,过度平滑 无漏焊、假焊 无焊渣、飞溅 无气孔,无焊瘤
机加工过程检验流程
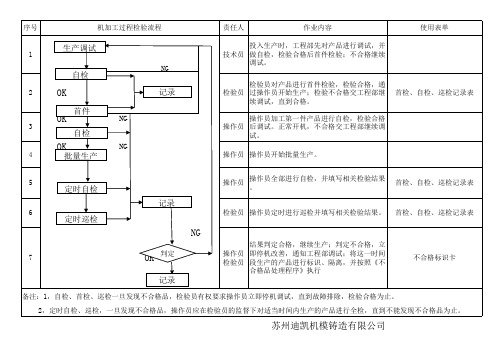
序号
机加工过程检验流程
责任人
作业内容
使用表单
1
生产调试 自检
NG
投入生产时,工程部先对产品进行调试,并 技术员 做自检,检验合格后首件检验;不合格继续 调试。 检验员对产品进行首件检验,检验合格,通 检验员 过操作员开始生产;检验不合格交工程部继 续调试,直到合格。 操作员加工第一件产品进行自检,检验合格 操作员 后调试。正常开机,不合格交工程部继续调 试。 操作员 操作员开始批量生产。 操作员全部进行自检,并填写相关检验结果 。
不合格标识卡
记录
备注:1,自检、首检、巡检一旦发现不合格品,检验员有权要求操作员立即停机调试,直到故障排除,检验合格为止。 2,定时自检、巡检,一旦发现不合格品,操作员应在检验员的监督下对适当时间内生产的产品进行全检,直到不能发现不合格品为止。
苏州迪凯机模铸造有限公司
2
OK OK OK
批量生产
首件
记录 NG NG
首检、自检、巡检记录表
3
自检
4ቤተ መጻሕፍቲ ባይዱ
5
定时自检
记录
操作员
首检、自检、巡检记录表
6
定时巡检
检验员 操作员定时进行巡检并填写相关检验结果。
首检、自检、巡检记录表
NG
7
OK
判定
结果判定合格,继续生产;判定不合格,立 操作员 即停机改善,通知工程部调试;将这一时间 检验员 段生产的产品进行标识、隔离,并按照《不 合格品处理程序》执行
CNC加工中心检查表

5.根据指导书检查物料料号,材料是否合 格、材料是否摆放整齐。
1.刀具的规格型号: B.刀具 2.使用的刀具是否与产品、机床要求相
检查 符 3.刀具是否松动
工序
检验项目
结论
检查内容
6.是否已阅读并清楚作业指导书要求
7.产品是否装夹到位或是否有间隙; 8.检验指导书是否受控,手改是否有人签字, 文件、图纸是否正确、版本是否最新。 9.检验工具、量具、检具是否满足需求。 C加工中心控制系统周围是否有妨碍物 11.是否有人在机械危险区内
结论
4.刀具有无磨损、破损,
5.刀具已使用:
H
时间段
品名 首件
14:00 16:00 18:00
产品有无披锋、毛刺,刮伤、夹伤、碰伤、缺料。
C. 外观检 粗糙度是否符合要求、产品加工位置有无台阶
验
齿面是否损伤,有无砂眼。
D.尺寸
抽检记 录/不 合格事 项
异常处 理措施
责 任 人
备注: 1.QC依本表进行巡检,正常打√;异常打×,每2小时巡一次.尺寸标准依据要求填写,测量异常的填写真实数据(正常的用符号标示即可) 2.QC巡检到异常时,将异常状况填入不合格事项,请责任人签名确认;并给出异常处理措施及改善对策. 3.有本表未列入的项目,写其它。
姓名: 品名 规格/图号
CNC加工过程检查表
材料
规格
批次
班别:白班 数量
返修数
精加工 工废
时间: 年 月 日
料废
备注
设检查内容 1.润滑油箱,水箱等的油水量是否充 足,气压压力是否正确
2.各控制系统、控制开关状况是否良好
机加工审核检查表

21 管理层
与最高管理层交流,了解组织对内外环境的分析,相关方对企业的期望或 要求,为完成质量环境安全方针、目标采取的措施,以及在持续改进方面 所做的工作,管理评审
GB/T19001-2016 5.2.2,7.3 7.4 5.3 7.2,7.1.2
7.1.3 7.1.4
对应条款 GB/T24001-2016
11
现场观察操作人员是否按规定进行首检、互检与专检,并做好检验记录 (记住本批产品及原材料)
12
现场观察操作人员是否按规定做好产品的防护、以及合格品、不合格品、 废的消防器材是否按期进行检查,讯问操作人员如何使用消防器 材?是否进行培训,并根据需要查询记录
根据操作人员使用的原材料,到仓库检查此原材料是否贯彻了先入先出的 14 原则?并同时现场观察物料的管理水平,如帐卡物是否一致?物料标示、
18 根据销售合同,查研发设计部的研发设计条款及设计变更,并查看是否考 研发部 虑了从生命周期的不同阶段考虑了环境、安全因素
19 质量部
根据操作者及使用的测量工具,到质量部查工具台帐及检测报告及周期内 的质量绩效情况(是否有改进),产品放行情况,让步接受情况(降 低),并同时检查环境、安全因素,内部质量审核
7.2,8.1,8.2 6.1,8.5.2,8.5.3,8.5.4
8.4,9.1.3
8.1
8.2,8.3,8.5.4,8.5.5 9.1.2,9.1.3
8.1
8.3,8.5.6
8.1
7.1.5,8.6,8.7 9.1.1,9.1.3,9.2,10.2,10.3
8.1
4.4.2,4.4.6,4.4.7 4.4.6 4.4.6 4.4.6 4.4.6
20 到操作工为例,人事部门查岗位职责、年度培训的编制情况,人员能力的 人事部 确认情况,培训效果的验证情况,关键岗位人员的流失情况
机加工自检记录单
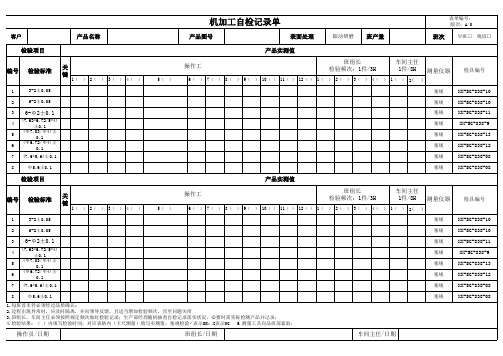
塞规
检具编号 XX-SG-838-10
2
6-2±0.05
塞规
XX-SG-838-10
3 6-Φ2±0.1
4
(7.63*6.72/5*4) ±0.1
5
(Φ7.03/Φ4)± 0.1
6
(Φ6.72/Φ4)± 0.1
7 (7.6*5.6)±0.1
塞规
XX-SG-838-11
塞规
XX-SG-838-9
塞规
XX-SG-838-13
客户
产品名称Biblioteka 机加工自检记录单产品图号
表面处理
振动研磨 班产量
表单编号: 版次:A/0
班次
早班□ 晚班□
检验项目
产品实测值
编号 检验标准
1
3-2±0.05
关
键
1( ) 2( ) 3( ) 4( )
5( )
操作工
班组长 检验频次:1件/3H
车间主任 1件/8H 测量仪器
6( ) 7( ) 8( ) 9( ) 10( ) 11( ) 12( ) 1( ) 2( ) 3( ) 4( ) 1( ) 2( )
塞规
检具编号 XX-SG-838-10
2
6-2±0.05
塞规
XX-SG-838-10
3 6-Φ2±0.1
4
(7.63*6.72/5*4) ±0.1
5
(Φ7.03/Φ4)± 0.1
6
(Φ6.72/Φ4)± 0.1
7 (7.6*5.6)±0.1
塞规
XX-SG-838-11
塞规
XX-SG-838-9
塞规
XX-SG-838-13
塞规
XX-SG-838-12
机加工记录表格

合同更改内容:
合同更改需通知部门人:
填写人
批准
日期
合同修改通知单
序号:XB-C-63
合同编号
更改原因
合同更改内容:
合同更改需通知部门人:
填写人
批准
日期
销售合同台帐(加工件)
序号:XB-C-62
月日
名称
工作号
规格
材质
数量
单重
工序
工料
交货期
订货单位
车
铣
刨
镗
锯
钳
供方评定记录
XB-C-23
序
号
供方名称
联系人
受审核部门
审核日期
审核依据
审核员
不合格事实描述:
不符合GB/T
机加工首件检验记录表

总结
最终判定结果
□合格 □不合格
是否同意量产: □是 □否
检验员签名:
注意事 1、所有项目均需连续检查最少2件。 项 2、根据质量统计的不良项目进行持续跟进。
1、产品新开机生产时,由最终工序准备好2个样件置于待检区,并通知检验员,检查判定合格后生产。
填写 2、检验员判定合格后从样品中随机挑选1个样件,进行首件标识。并连同巡检记录表一起置于产线最终检查工位。 说明 3、适用范围:产品新开机、变更工艺/参数、变更材料等均需要进行首件检查。
4、检查结果:合格项目打“√”,不合格项目打“×”,无此检查项目打“0”;本表单保留一年。
机加工首件检验记录表
编号: 版本:A/0
零件号
首件 信息 □开机首检
□其他:
产品名称 □生产参数变更 □材料变更
项目
检验标准
12原料来自机台编号生产日期检验依据
□工程图纸 □标准样件 □产品标准 □其它
实测值
3
4
5
判定
检验时间
时 分
备注
检查 尺寸 记录
外观
□变形 □孔毛刺 □飞边毛刺 □划伤 □疤瘤 □烧穿 □未焊透
机械加工检验记录表常用
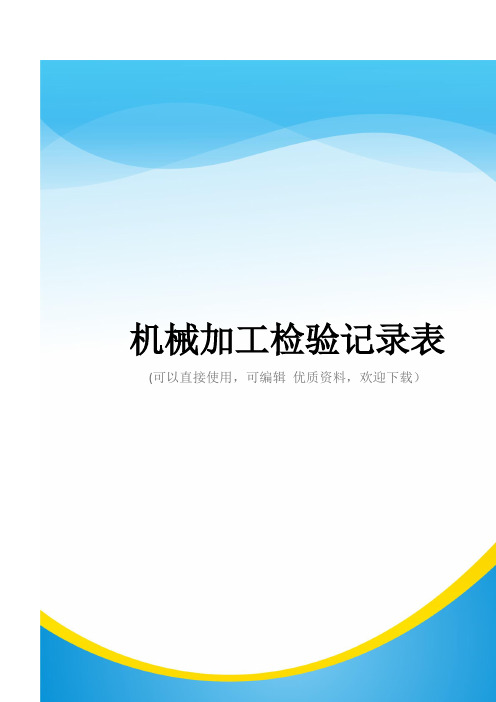
机械加工检验记录表(可以直接使用,可编辑优质资料,欢迎下载)编号:CHME/JL-ZJ-03岗位安全职责总经理1.工作内容及要求1.1总经理对本公司生产指挥和经营管理工作统一领导,全面负责。
1.2负责贯彻执行国家有关质量的法律、法规及方针政策,制定、发布质量方针并组织实施。
1.3批准并建立和完善与质量体系相适应的组织机构,明确职责、权限及相互关系,负责管理评审和内部质量审核及签署报告。
1.4决定重大质量决策,对公司的工作质量、产品质量和服务质量负全责。
1.5充分调动公司各方面的积极因素,发挥副经理及各职能部门的作用,确保公司质量方针目标的实现。
1.6负责职工的思想、文化、业务教育,组织职工进行技术创新,支持合理化建议活动。
2.责任与权限2.1总经理有企业经营管理工作的决策权和生产指挥权。
2.2总经理负责主持经理办公会议,研究解决生产经营和行政管理中的决策问题,对经营管理中的重大问题,意见不一致时,经理有权作出决定。
3.检查与考核3.1总经理的工作由董事会负责检查和考核。
3.2总经理应严以律己,自觉接受董事会的监督、检查。
管理者代表1.作内容及要求1.1管理者代表在公司总经理领导下工作。
1.2负责公司质量管理和质量保证等工作的组织和协调。
1.3负责建立、实施并保持质量体系的正常运行。
1.4负责组织内部质量体系审核,并将年度审核结果报告给总经理。
1.5协助总经理做好管理评审工作。
1.6负责质量体系文件的修改工作。
1.7负责对员工进行质量意识教育。
1.8按时完成领导交办的各项工作、任务。
2.责任与权限2.1对总经理负责,执行总经理决定,有权对总经理的工作提出建议。
2.2对保证公司质量体系有效运行负责,有权下达质量管理工作指令,并监督实施。
3.检查与考核3.1由总经理负责检查与考核。
3.2按对公司质量管理和质量保证工作的贡献和失误,由总经理视其情况,给予奖罚。
销售主管1.工作内容及要求1.1销售经理在总经理直接领导下,负责销售部的各项工作。
数控检验单

数 控 检 验 记 录 表
项目 检验时间 件号 检验员 工程别 加工内容 机台
合格√不合格×无关/
操作者
检验 结果 复检 结果
检验项目
底面/座面 部分
检 验 内 容
平面加工精度是否良好 U沟加工是否良好 快速定位加工是够良好 定位键槽加工是否良好 刀块定点加工是否良好 导柱孔/导套孔加工是否良好 导板背托面/承面加工是否良好 导滑面加工是否良好 型面轮廓加工是否良好 型面是否存在加工错误 角度头加工型面轮廓是否良好 分模线加工是否良好 刃口逃料加工是否良好 型面是否存在加工遗漏 衬套孔加工是否良好 止转销加工是否良好 侧销孔加工是否良好 左右件记号孔加工是否良好 到底记号孔加工是否良好 CH孔加工是否良好 弹簧孔加工是否良好 修模孔加工是否良好 吊挂孔加工是否良好 逃料孔加工是否良好 角度头加工孔是否良好 躲避孔加工是否良好 弹簧孔加工是否良好 定位销孔加工是否良好 弹簧座面加工是否良好 平面是否存在加工错误 素材定位器平面加工是否良好 平面是否存在加工遗漏 能够测量的平面尺寸是否良好 起吊/翻转平台加工是否良好 夹持块是否加工 对应标记平台加工是否良好 斜楔加工是否良好 是否存在加工遗漏 机加部:
检 验 记 录
导向部分
型面/轮廓 部分
孔部分
平面部分
斜楔部分 其他部分