PFMEA制作及修订指引办法
PFMEA制作及修订指引办法

无锡精艺达科技有限公司文件号:JYD-FM-18-04版次:A文件名称PFMEA制作及修订指引办法页次/总页次:2/106.4.l PFMEA 制做要准备以下资料:①过程流程图和产品或过程特殊特性表;②产品规格书和客户要求资料;③类似产品PFMEA 资料。
按该制程的工艺流程图所指明工序,依顺序进行,属过程或产品特殊特性的工序要在“分类”栏填写相应符号,如客户对特殊特性的标识符号无特殊要求,公司则用“△"表示。
过程特性使用“◊”飞产品特性使用“△”。
返工/修正工序需要纳入FMEA,检查工序的过程中如果辅助的检查工具对产品会有损伤的隐患,那么也要进行失效分析。
6.4.2关键日期:填写初次PFMEA预计完成的日期,该日期不能超过产品计划生产的日期。
6.4.3过程的功能分析(a)对应过程流程图确定过程编号,所用的编号、顺序、术语必须与过程流程图保持一致。
(b)尽可能简单说明过程的功能,如“下料、车加工、外观检查、包装”(c)并逐一列出该过程的要求,包括产品尺寸、外观、材质和功能。
(d)根据过程流程图的特殊特性资料,在表格的特殊特性栏标识清楚。
6.4.4潜在失效模式分析(a)在假定提供给本工序作业的物料是合格的前提下对本工序的作业内容进行潜在失效模式分析。
(b)要对具体不符要求的作业内容的描述,如“孔破”要充分考虑其可能存在的失效模式,在制程中对相关项目是否符合作业指示中相关规格加以判定。
应该用化学的、物理的、专业性的术语来描述潜在失效模式,而不同于顾客所见的现象:典型的失效模式:偏位、氧化、缺口、划伤、折痕、破裂、脏污等。
(c)潜在失效后果:失效模式会对内部(下工序或地点)或最终使用者有影响,如果该失效模式可能影响到安全或造成违法的法规,则要清楚陈述。
①对最终使用者来说,失效的后果应该用产品或系统的性能来描述,如:噪音、无信号、显示暗划或缺划、按键不入数、异昧、不稳定、外观不良、返工/返修、顾客不满意、报废等。
(参考资料)PFMEA编制实施工作指南

对于高探测度 D 风险项,如需采用防错装置,应建立《防错装置清单》 8.4、模板式 PFMEA 对于相同的工艺流程/过程和产品/过程特性(特别是其相同的产品/过程特殊特 性),可建立和制定其通用的模板式 PFMEA(如:交付工序)。模式式 PFMEA 要求 与普通 PFMEA 一致。 8.5、针对高风险项应建立《风险降低优先清单》 具体见六(二)11)。 a、行动计划应明确责任人和时间期限,并进行跟踪。 b、行动计划落实之前,应通过质量工具以确保风险得到控制(即:识别出风险 并制定措施后,在行动计划落实并得到确认之前需采取临时措施确保风险得到 控制(个人理解))。可使用的工具包括: ——检验工位对高风险问题实施双倍检查; ——对高风险问题制定作业指导书(临时)并进行培训; ——过程分层审核检查预防性控制是否符合标准化作业指导书; ——过程分层审核检查当前的控制方法是否符合检验作业指导书,等 8.6、PFMEA 应制定定期的《PFMEA 评审计划》 PFMEA 检查的频次/次数依据: ——客户期望(客户抱怨、5why 等) ——过程能力(FTQ、SPC 等) ——过程的变更(防错,2 级供应商变更等) PFMEA 检查优先级别: ——供应商新购设备、工装移动或变更中的产品; ——开发时多功能小组没有足够参与的 PFMEA;
某工位无法装配; 在顾客设施处无法附着; 在顾客设施处无法连接; 某工位时引起工具过度损耗; 导致某工位设备损坏; 在顾客设施处对操作员构成危险。
有以上情况时,只需评估制造影响,不需要做进一步分析,如果不是,则 转到 b 和 c 问题。 b、对最终顾客的影响是什么? 考虑最终顾客会觉察或经历到什么。如: 噪音; 非正常功能; 异味; 间隙性运行; 漏水; 无法调试; 控制困难; 外观不良。 c、如果影响还未涉及到最终顾客,就被发现,会怎样? 当前场所和接受场所的潜在影响也需考虑。如: 生产线关闭; 停止发运; 产品 100%报废;
制程PFMEA填写指引与制作要领

失效原因 Portential Cause Mechanism of Failure
PFMEA之输入工 具
产品特性矩阵表
PFMEA常发生的问 题是不按照流程 顺序填写制程作业 内容及目的 分析的制程作业内 容及目的决定了不 良模式.影响及其 原因的关联!!
正确的表单域定义填写
第 3 页 共 3页
1
4
28
1
2
3
4
7
5 5 5
6 6 6
8 8 8
现行管制有2种: „预防不良原因 „侦测不良项目或侦测不良原因
9 10 11 9 10 9 10
12
13
14
功能: 制程名称& 产品/制程需求
4种驱动想法: „无功能 „部份/过度功能或 长时间功能降级 必须为 „间歇性功能 动词+名词+量化 „非预期功能 值,包括特殊情 况或制约
输入内容包含: „先前/类似FMEAs „ 8D „保固索赔 „TWG „组车厂不良报告 „DPC „SPC (D)
起重器组装/选 起重器缺装 择正确的起重器 阻件并放置定位
„使用者无法更换 轮胎(7) „整修(4)
7
作业者未依程序作 业
2
后工程检出-(4) (D) „作业员训练 „作业指导书 „目视化重点标示 (P) 制程稽核-(7) (D) „作业员训练 „作业指导书 „目视化重点标示 (P)
„对已采取 的对策案与 以简要的叙 述 „重新修订 评价价值于 右侧字段, 并重新计算 RPN值
第 1 页 共 3页
制程FMEA填写指引与制作要领
产品名称Item: 次系统/名称Model:组装成品 跨功能小组: 严 零件符号 失效模式/现象(失 重 Item/Function 零件规格/性能(潜在失 效的潜在效 度 (制件功能/要求 效模式)Potential 果)Potential s Process Failure Mode Effects of Function/Requir e Failure ements) v 等 级 C l a s s 发 生 率 O c c u r 现行设计管制预防 现行设计管制检知办法 难 Current Design 检 Current Design Controls Controls Detection(现 度 Prevention(现行制程 D 行制程管制检知办法 管制预防Current Current Process e Process Controls Controls Detection) t Prevention) 关 推荐措施之负 改正后结果Action Results 键 责部门/人员 严 发 难 关 指 推荐措施 与完成日期 重 生 检 键 数 Recommended Responsibili 采取的措施 度 率 度 指 R Actions ty&Target Actions S O D 数 Completion P Taken e c e RP Date N v c t N 制程Process责任Responsibility: 工程发布尔日期 编制人Prepared By: FMEA日期Date(原始Orig.): (修定Rev.A):
PFMEA制作及修订指引办法
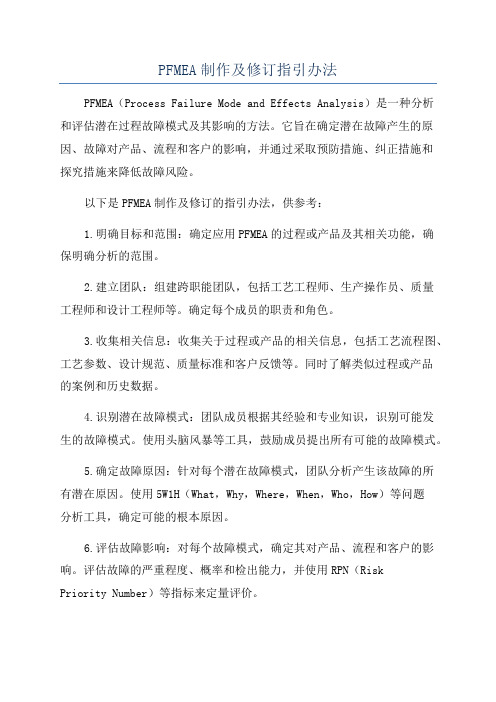
PFMEA制作及修订指引办法PFMEA(Process Failure Mode and Effects Analysis)是一种分析和评估潜在过程故障模式及其影响的方法。
它旨在确定潜在故障产生的原因、故障对产品、流程和客户的影响,并通过采取预防措施、纠正措施和探究措施来降低故障风险。
以下是PFMEA制作及修订的指引办法,供参考:1.明确目标和范围:确定应用PFMEA的过程或产品及其相关功能,确保明确分析的范围。
2.建立团队:组建跨职能团队,包括工艺工程师、生产操作员、质量工程师和设计工程师等。
确定每个成员的职责和角色。
3.收集相关信息:收集关于过程或产品的相关信息,包括工艺流程图、工艺参数、设计规范、质量标准和客户反馈等。
同时了解类似过程或产品的案例和历史数据。
4.识别潜在故障模式:团队成员根据其经验和专业知识,识别可能发生的故障模式。
使用头脑风暴等工具,鼓励成员提出所有可能的故障模式。
5.确定故障原因:针对每个潜在故障模式,团队分析产生该故障的所有潜在原因。
使用5W1H(What,Why,Where,When,Who,How)等问题分析工具,确定可能的根本原因。
6.评估故障影响:对每个故障模式,确定其对产品、流程和客户的影响。
评估故障的严重程度、概率和检出能力,并使用RPN(RiskPriority Number)等指标来定量评价。
7.制定预防措施:根据故障模式和影响评估的结果,制定预防措施来消除或减少故障的发生。
确保措施具体、可行,并与相关人员共享。
8.制定纠正措施:针对已发生的故障模式,制定纠正措施来消除或修复故障,并防止再次发生。
确保措施采取及时和有效。
9.制定探究措施:对于无法完全预测或控制的故障模式,制定探究措施来及时发现并解决问题。
例如,制定持续改进计划和故障诊断方案。
10.评估和追踪:对制定的措施进行定期评估和追踪,确保其有效性和可持续性。
根据评估结果,修订PFMEA文件并进行更新。
PFMEA编制作业指导书

PFMEA编制作业指导书PFMEA(Process Failure Mode and Effects Analysis)是一种用于根据潜在的失效模式和其对过程或产品所造成的影响的方法。
它可以帮助企业发现、评估和控制过程中的潜在问题,进而采取相应的预防措施。
以下是一份PFMEA编制作业指导书的模板,旨在帮助读者了解如何编制PFMEA。
一、背景在这一部分,首先要介绍PFMEA的目的和重要性。
重要性包括:提高产品质量、降低成本、提高生产效率、确保工艺稳定性等。
此外,还要说明编制PFMEA的前提条件,例如需要有一支专业的团队、对于所研究的过程有一定的了解等。
二、编制团队指导书需要明确编制PFMEA所需的团队成员,例如生产工程师、品质工程师、设计工程师等。
每个成员的职责应该清晰明确,确保团队协作高效。
三、编制步骤3.1 收集过程信息在这一步骤中,需要收集过程信息,包括工艺流程图、控制计划、产品规范、相关图纸等。
同时,还需要了解相关的制造工艺和设备,明确每个环节的输入和输出。
3.2 识别失效模式通过仔细分析过程信息,团队可以识别潜在的失效模式。
失效模式可能包括产品性能问题、工艺偏差、设备故障等。
每个失效模式都需要详细描述,包括其可能的原因、触发条件和影响。
3.3 评估失效影响对于每个失效模式,团队需要评估其对过程或产品的影响。
评估应该包括影响的程度、频率和持续时间。
评估的结果应该是一个科学的评分系统,能够准确反映失效的严重程度。
3.4 识别已有控制措施在这一步骤中,团队需要识别已有的控制措施,即已经采取的措施来防止或减轻失效的发生。
这些措施可以包括设计变更、工艺改进、设备维护等。
控制措施的有效性需要进行评估。
3.5 确定预防措施根据评估结果和已有的控制措施,团队需要确定额外的预防措施来防止失效的发生。
预防措施可以包括员工培训、操作规程改进、设备升级等。
预防措施需要具体、可行,并能够确保失效的概率降到最低。
3.6 确定检测措施当失效无法完全预防时,需要确定相应的检测措施,旨在尽早发现失效并采取相应的纠正措施。
PFMEA作业指导书
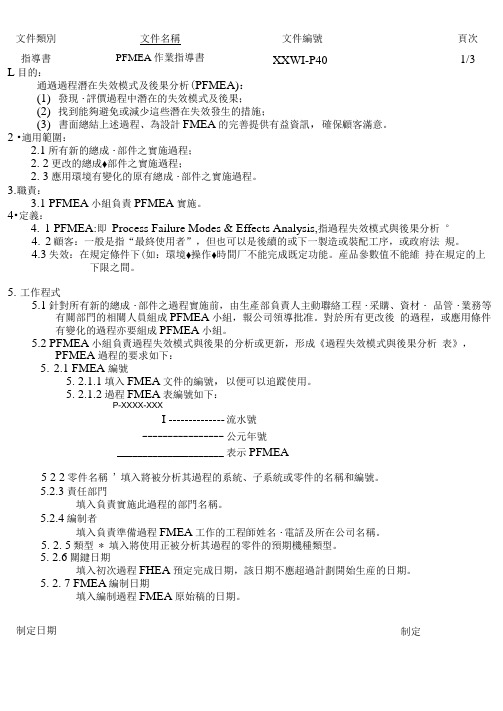
L 目的:通過過程潛在失效模式及後果分析(PFMEA): (1) 發現・評價過程中潛在的失效模式及後果;(2) 找到能夠避免或減少這些潛在失效發生的措施;(3) 書面總結上述過程、為設計FMEA 的完善提供有益資訊,確保顧客滿意。
2 •適用範圍:2.1所有新的總成・部件之實施過程; 2. 2更改的總成♦部件之實施過程;2. 3應用環境有變化的原有總成・部件之實施過程。
3.職責:3.1 PFMEA 小組負責PFMEA 實施。
4•定義:4. 1 PFMEA:即 Process Failure Modes & Effects Analysis,指過程失效模式與後果分析 ° 4. 2顧客:一般是指“最終使用者”,但也可以是後續的或下一製造或裝配工序,或政府法 規。
4.3失效:在規定條件下(如:環境♦操作♦時間厂不能完成既定功能。
産品參數值不能維 持在規定的上下限之間。
5. 工作程式5.1針對所有新的總成・部件之過程實施前,由生產部負責人主動聯絡工程・采購、資材・ 品管・業務等有關部門的相關人員組成PFMEA 小組,報公司領導批准。
對於所有更改後 的過程,或應用條件有變化的過程亦要組成PFMEA 小組。
5.2 PFMEA 小組負責過程失效模式與後果的分析或更新,形成《過程失效模式與後果分析 表》,PFMEA 過程的要求如下: 5. 2.1 FMEA 編號5. 2.1.1填入FMEA 文件的編號,以便可以追蹤使用。
5. 2.1.2過程FMEA 表編號如下:P-XXXX-XXXI -------------- 流水號---------------- 公元年號 _____________________ 表示PFMEA5 2 2零件名稱 ' 填入將被分析其過程的系統、子系統或零件的名稱和編號。
5.2.3責任部門填入負責實施此過程的部門名稱。
5.2.4編制者填入負責準備過程FMEA 工作的工程師姓名・電話及所在公司名稱。
PFMEA编制实施工作指南
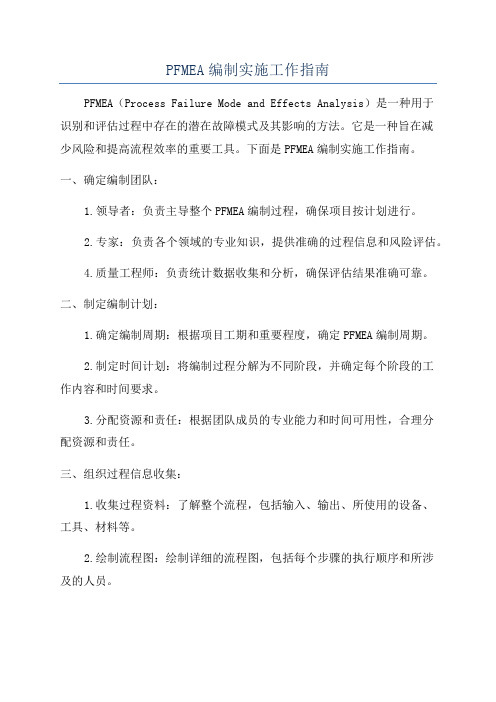
PFMEA编制实施工作指南PFMEA(Process Failure Mode and Effects Analysis)是一种用于识别和评估过程中存在的潜在故障模式及其影响的方法。
它是一种旨在减少风险和提高流程效率的重要工具。
下面是PFMEA编制实施工作指南。
一、确定编制团队:1.领导者:负责主导整个PFMEA编制过程,确保项目按计划进行。
2.专家:负责各个领域的专业知识,提供准确的过程信息和风险评估。
4.质量工程师:负责统计数据收集和分析,确保评估结果准确可靠。
二、制定编制计划:1.确定编制周期:根据项目工期和重要程度,确定PFMEA编制周期。
2.制定时间计划:将编制过程分解为不同阶段,并确定每个阶段的工作内容和时间要求。
3.分配资源和责任:根据团队成员的专业能力和时间可用性,合理分配资源和责任。
三、组织过程信息收集:1.收集过程资料:了解整个流程,包括输入、输出、所使用的设备、工具、材料等。
2.绘制流程图:绘制详细的流程图,包括每个步骤的执行顺序和所涉及的人员。
3.收集数据:收集可用的历史数据、记录和问题报告,作为评估的依据。
四、确定故障模式:1.列出所有潜在故障模式:与团队成员一起讨论,列出可能出现的故障模式。
2.评估故障模式的严重性:根据潜在故障对生产、安全和顾客满意度的影响,给每个故障模式分配一个评分。
3.选择优先级故障模式:根据评分,选择那些需要优先考虑的故障模式。
五、确定潜在故障原因:1.列出所有潜在故障原因:通过讨论和分析,列出导致故障模式发生的可能原因。
2.评估故障原因的发生概率:通过统计数据和专业判断,评估每个故障原因发生的概率。
3.选择优先级故障原因:根据发生概率和严重性,选择优先考虑的故障原因。
六、确定控制措施:1.列出所有潜在控制措施:根据潜在故障原因和从业经验,列出可能的控制措施。
2.评估控制措施的有效性:根据已有的数据和知识,评估每个控制措施的有效性。
3.选择优先级控制措施:根据有效性和成本效益,选择优先考虑的控制措施。
PFMEA制作及修订指引办法

无锡精艺达科技有限公司文件号:JYD-FM-18-04版次:A文件名称PFMEA制作及修订指引办法页次/总页次:2/10版次:A文件名称PFMEA制作及修订指引办法页次/总页次:4/10②预防控制:防止失效的起因/机理、失效模式出现或者降低其出现的机率。
如:机器维护保养、SPC 、防错、防果等。
③探测控制:探测出失效的起因/机理或者失效模式,导致采取纠正措施。
④优先运用预防控制的方法,因为其将影响最初的频度;最初的探测度将基于探测控制。
(b)探测度(D):是指在产品离开制造工序之前,采用现行过程控制方法找出失效起因/机理的可能性的评价指标,是与过程控制栏中所列的最佳探测控制相关的定级数。
为了获得一个较低的定级,通常计划的过程控制必须予以改进。
(探测度评价准则见表=)6.4.8风险评估:优先关注风险严重度S=8, 9, 10S0>35RPN: > 100风险指数(RPN):风险指数是指严重度(S)频度(0)和探测度(D)的乘积风险优化指数SO :严重度(S)和频度(0)的乘积建议措施:建议措施提出时机:依风险关注的优先顺序,当风险评估满足以上任一条件时要对设计或过程进行优化、改善,填写建议措施。
措施提出应首先针对高严重度,so值超过35及RPN值大于100的项目要强制进行预防/纠正措施的工程评价。
是否制定和采取建议措施由核心功能小组成员决定RPN值同等的情况取严重度高的,严重度也相同的情况下取频度高的,频度相同,则取探测度级别高的,如客户有特殊要求的按客户要求执行。
举例说明:依以下顺序降低其凤险级别:严重度,频度和探测度。
①一般实践中,当严重度是9或10时,必须对设计或过程进行优化、改善,填写建议措施,以确保现行的设计措施/控制或过程预防/纠正措施针对了这种凤险。
如作业员的适当防护。
8.附录附录A《流程图》XXXXXXXXXX有限公司文件号:JYD-FM-18-04版次:A。
2023修正版PFMEA范本

PFMEA范本PFMEA范本1. 引言在生产制造过程中,为了提高产品的质量和稳定性,预防潜在的质量问题和风险是至关重要的。
PFMEA(Process Flure Mode and Effects Analysis)是一种常用的质量管理工具,用于识别和评估生产过程中潜在的故障模式、影响和应对措施,以防止产品质量问题的发生。
本文档将为您提供一个PFMEA范本,以帮助您在项目中正确使用和实施PFMEA。
2. PFMEA范本2.1 PFMEA编号- 编号:[在此处填写编号]2.2 PFMEA制表信息- 制表人:[在此处填写制表人姓名]- 制表日期:[在此处填写制表日期]- 审核人:[在此处填写审核人姓名]- 审核日期:[在此处填写审核日期]2.3 产品/过程信息- 产品名称:[在此处填写产品名称]- 过程名称:[在此处填写过程名称]- 过程目标:[在此处填写过程目标,例如:确保产品装配的正确性和稳定性]2.4 意图描述- 在此处对PFMEA的目的进行描述,例如:识别和预防生产过程中可能出现的故障模式,以降低质量问题的风险和影响。
- 可以包括对故障模式的定义、对预防、检测和纠正措施的描述。
3. 评估项目在此处列出需要进行PFMEA评估的项目,包括相关的组件、过程和设备。
每个项目应包括以下信息:- 项目编号:[在此处填写项目编号]- 项目名称:[在此处填写项目名称]- 项目描述:[在此处填写项目描述]4. 评估步骤4.1 第一步:识别故障模式在此步骤中,我们将识别可能存在的故障模式。
对于每个项目,请提供以下信息:- 故障模式编号:[在此处填写故障模式编号]- 故障模式描述:[在此处填写故障模式描述]- 故障模式分类:[在此处填写故障模式分类]- 故障模式影响:[在此处填写故障模式对产品/过程的影响]4.2 第二步:评估故障严重性在此步骤中,我们将评估每个故障模式的严重性级别。
对于每个故障模式,请提供以下信息:- 故障严重性级别:[在此处填写故障严重性级别,一般使用1-10的评估等级,1代表最严重的等级]4.3 第三步:评估故障概率在此步骤中,我们将评估每个故障模式发生的概率。
PFMEA作业指导书

PFMEA作业指导书PFMEA(Process Failure Mode and Effects Analysis)作为一种流程故障模式与效果分析方法,被广泛用于各种生产过程中的质量管理和风险预防。
本文将以PFMEA作业指导书为题,介绍该指导书的内容和编写要点,以及如何有效地应用PFMEA方法。
一、PFMEA作业指导书的内容和编写要点PFMEA作业指导书是一种详细记录和指导流程故障模式与效果分析工作的文件。
编写该指导书的目的是为了帮助团队成员了解PFMEA的目标、原则和方法,并提供清晰的指导和标准化的流程。
1. 指导书的结构和组织:指导书应该清晰地描述PFMEA的编写过程,并提供详细的步骤和要求。
一般来说,可以按照以下结构组织指导书的内容:(1)前言:介绍PFMEA的背景和目的,以及指导书的使用范围和适用对象。
(2)术语和定义:解释和定义与PFMEA相关的术语,确保团队成员对这些术语的理解一致。
(3)PFMEA的流程和步骤:详细描述PFMEA的编写流程和各个步骤,包括确定流程、收集数据、分析数据、评估风险、制定改进措施等。
(4)数据收集和分析的方法:介绍PFMEA中常用的数据收集和分析方法,例如流程图分析、故障树分析等。
(5)风险评估和控制方法:说明如何评估流程中的风险,并提供一些常用的控制方法和改进措施。
(6)案例分析和实例:通过实际案例和实例,展示如何应用PFMEA方法解决流程中的问题和风险。
2. 详细描述每个步骤和要求:在指导书中,对于每个PFMEA的编写步骤和要求,都需要进行详细的描述和说明。
例如,在确定流程步骤中,应该指导团队成员如何准确描述每个流程步骤,并了解相关的输入、输出和控制要素;在收集数据步骤中,应该明确指出应该收集哪些数据和信息,以及收集的方法和工具等。
3. 强调团队合作和沟通:PFMEA是一种团队性质的工作,需要不同角色和部门的专业人员之间的合作和沟通。
指导书中应该强调团队合作的重要性,鼓励成员之间的积极交流和协作。
PFMEA编制指导书

1、目的使PFMEA的编制达到统一化、规范化;使所编制的PFMEA能更全面、更有效地对产品在过程中存在的弱点和有可能产生的缺陷,以及这些缺陷产生的后果与风险,做出更详尽的分析和更准确的评价,并在决策过程中采取措施加以控制。
2、适用范围适用于本公司产品在试生产、生产过程的PFMEA的编制。
3、定义PFMEA :即过程潜在失效模式及后果分析。
核心小组:即与“过程潜在失效模式及失效后果”相关的部门以及对此过程熟悉并有相关经验的人员组成的,参与对该过程中潜在的失效模式及失效后果进行综合分析和评价的综合小组。
核心小组由生产部根据需要进行组织(必要时邀请顾客、供应商参加)。
TGR:Thing Go Right 是指在一件事情(可以是一个项目,产品设计,过程设计,材料,人力资源管理等方面)上做的比较好,值得其他人和类似的事情借鉴的。
TGW:Thing Go Wrong 是指在一件事情上失败的地方,需要其他的人和开发类似事情的时候需要注意和考虑的地方。
4、职责5、程序细则5.1 编制PFMEA的目的:(1)发现、评价产品/过程中潜在的失效及后果;(2)确定与产品有关的过程潜在失效模式;(3)评价失效对顾客的潜在影响;(4)确定潜在制造或安装过程失效起因、机理,确定减少失效发生或找出失效条件的过程控制变量;(5)在产品/零件达到用户手中之前或零部件及总成品出厂前,提高发现缺陷的概率;(6)将分析出的制造或装配过程的失效模式及后果编制成文件;(7)为编写控制计划提供依据。
5.2 PFMEA的编制5.2.1 排列故障(1)核心小组根据研发部输出的图纸及相关的技术文件(如DFMAE、样件控制计划等)以及现有的生产过程流程,将所有有可能在过程中产生的缺陷及失效模式排列出来,并对这些缺陷/失效产生的严重度以及缺陷/失效产生的原因、机理进行分析、评定并形成记录。
(2)生产部用统一的、标准的格式(参见参考手册《潜在失效模式及后果分析》)将以上记录予以汇总整理,并使之成为文件。
第五版PFMEA编制实施指引
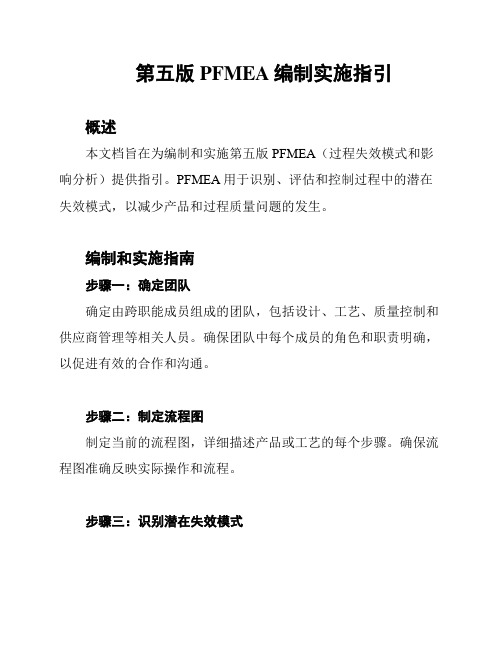
第五版PFMEA编制实施指引概述本文档旨在为编制和实施第五版PFMEA(过程失效模式和影响分析)提供指引。
PFMEA用于识别、评估和控制过程中的潜在失效模式,以减少产品和过程质量问题的发生。
编制和实施指南步骤一:确定团队确定由跨职能成员组成的团队,包括设计、工艺、质量控制和供应商管理等相关人员。
确保团队中每个成员的角色和职责明确,以促进有效的合作和沟通。
步骤二:制定流程图制定当前的流程图,详细描述产品或工艺的每个步骤。
确保流程图准确反映实际操作和流程。
步骤三:识别潜在失效模式在每个步骤中,团队成员应通过头脑风暴和经验分享等方式,识别可能存在的潜在失效模式。
例如,材料损坏、操作失误或设备故障等。
步骤四:确定失效影响对于每个潜在失效模式,团队成员应评估其可能的影响。
这包括对产品质量、工艺稳定性、安全性以及对客户满意度的影响等方面进行分析。
步骤五:确定当前控制策略审查并记录当前针对每个失效模式已经实施的控制措施。
这些控制措施可能包括工艺参数监测、工艺改进和员工培训等。
确保控制策略能够有效地预防或控制潜在失效。
步骤六:确定潜在失效的发生频率对于每个潜在失效模式,团队成员应评估其发生的频率。
这可通过分析历史数据、专家意见和实验测试等方式获取。
步骤七:计算风险优先指数 (RPN)应用以下公式计算每个潜在失效模式的风险优先指数(Risk Priority Number,RPN):RPN = 潜在失效的严重性 ×发生频率 ×发现能力步骤八:制定改进计划根据RPN评估结果,重点关注RPN较高的失效模式。
为这些失效模式制定相应的改进计划,包括控制策略的修订、工艺改进以及员工培训等。
步骤九:更新PFMEA文档根据改进计划的执行情况,及时更新PFMEA文档并进行有效的沟通和培训。
总结通过遵循以上指引,可以编制和实施一份全面有效的第五版PFMEA。
这有助于识别和控制潜在失效模式,提升产品和过程的质量,降低质量问题的发生率。
PFMEA管理办法

历史修订记录1.目的确定与产品和过程相关的潜在的失效模式和潜在制造或装配过程失效的机理/起因, 评价潜在失效对客户产生的后果和影响, 采取控制来降低失效产生频度或失效条件探测度的过程变量和能够避免或减少这些潜在失效发生的措施.2.适用范围适用于本公司所有新产品/过程或修改过的产品/过程及应用或环境发生变更的原有产品/过程的样品量试和批量生产。
3.术语及定义3.1PFMEA: 指Process Failure Mode and Effects Analysis(过程失效模式及后果分析)的英文简称. 由负责制造/装配的工程师/小组主要采用的一种分析技术, 用以最大限度地保证各种潜在的失效模式及其相关的起因/机理已得到充分的考虑和论述.3.2失效: 在规定条件下(环境、操作、时间), 不能完成既定功能或产品参数值和不能维持在规定的上下限之间, 以及在工作范围内导致零组件的破裂卡死等损坏现象.3.3严重度(S): 指一给定失效模式最严重的影响后果的级别, 是单一的FMEA范围内的相对定级结果. 严重度数值的降低只有通过设计更改或重新设计才能够实现.3.4频度(O): 指某一特定的起因/机理发生的可能发生,描述出现的可能性的级别数据有相对意义, 但不是绝对的.3.5测度(D): 指在零部件离开制造工序或装配之前, 利用第二种现行过程控制方法找出失效起因/机理过程缺陷或后序发生的失效模式的可能性的评价指标; 或者用第三种过程控制方法找出后序发生的失效模式的可能性的评价指标.3.6风险优先数 (RPN): 指严重度数(S)和频度数(O)及不易探测度数(D)三项数字之乘积.3.7客户: 一般指“最终使用者”, 但也可以是随后或下游的制造或装配工序, 维修工序或政府法规.4.职责与权限4.1技术部负责过程失效模式及后果分析(PFMEA)的制定与管理;负责主导新产品阶段过程失效模式及后果分析(PFMEA)的分析与实施;负责产品量产后的过程失效模式及后果分析(PFMEA)的更新与管理;负责返工/返修失效模式及后果分析(FMEA)的分析与实施。
PFMEA编制作业指导书 新版

的信息,商讨一个方法,同时综合按照风险顺序数,首先对级数最高和最关键的项目(例:特殊特性)采取纠正措施。
根据最新的官方FMEA参考手册第四版规定,并不强制规定使用RPN阀值来决定是否需要采取纠正措施。
如果顾客有特殊要求,明确规定以某RPN阀值来决定是否要采取纠正措施,则依照顾客要求执行展开分析。
5.4.13优先级的确定:
根据每种潜在失效模式的S、O、D的值,先对应严重度区域和探测度区域矩阵,得出严重度等级值和探测度等级;再对应优先级矩阵,得出优先级值。
优先选择prioritylevel1的top5进行风险降低行动,prioritylevel2的项目为可选项;并且编制《制造过程方案替代表》。
5.4.14建议的措施:
建议措施的主要目的是通过改进设计或过程方法,降低风险,提高顾客满意度。
据对失效模式风险评估结果,经过小组讨论,决定是否要采取措施,采取哪些措施。
应首先针对高严重度,高RPN值和小组指定的其它项目进行预防/纠正措施的工程评价。
PFMEA中的措施应主要包括制造、装配过程的措施,以及过程检验的强化措施。
采取措施的目标是降低潜在失效风险,即降低失效模式的严重度(S),频度(O)和探测度(D)。
说明:降低严重度(S),只有通过修改设计,使失效模式改变或不出现。
降低频度(O),也只有通过修改设计消除失效原因或减少其原因发生。
如改进材料的规范,通过有限元分
析改进结构,改进表面处理提高耐腐蚀性等。
降低探测度(D),应采取更有效的设计确认、验证方法。
PFMEA制作及修订指引管理办法
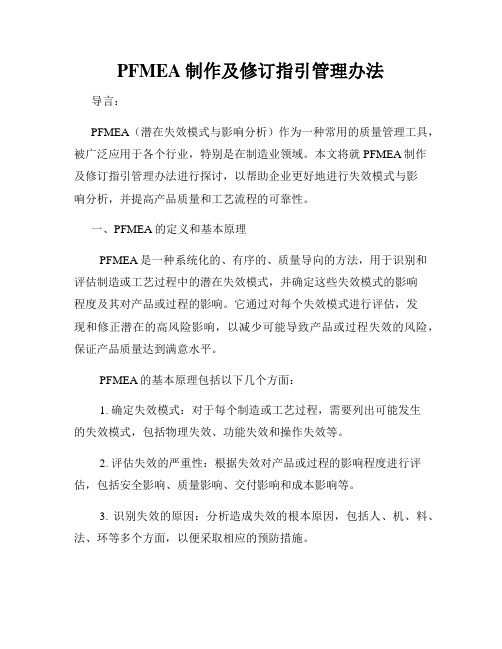
PFMEA制作及修订指引管理办法导言:PFMEA(潜在失效模式与影响分析)作为一种常用的质量管理工具,被广泛应用于各个行业,特别是在制造业领域。
本文将就PFMEA制作及修订指引管理办法进行探讨,以帮助企业更好地进行失效模式与影响分析,并提高产品质量和工艺流程的可靠性。
一、PFMEA的定义和基本原理PFMEA是一种系统化的、有序的、质量导向的方法,用于识别和评估制造或工艺过程中的潜在失效模式,并确定这些失效模式的影响程度及其对产品或过程的影响。
它通过对每个失效模式进行评估,发现和修正潜在的高风险影响,以减少可能导致产品或过程失效的风险,保证产品质量达到满意水平。
PFMEA的基本原理包括以下几个方面:1. 确定失效模式:对于每个制造或工艺过程,需要列出可能发生的失效模式,包括物理失效、功能失效和操作失效等。
2. 评估失效的严重性:根据失效对产品或过程的影响程度进行评估,包括安全影响、质量影响、交付影响和成本影响等。
3. 识别失效的原因:分析造成失效的根本原因,包括人、机、料、法、环等多个方面,以便采取相应的预防措施。
4. 确定预防控制措施:根据失效的原因,制定相应的预防控制措施,以防止失效的再次发生。
5. 跟踪和修订:对PFMEA进行定期更新和修订,确保其持续有效。
二、PFMEA的制作指引1. 确定评估对象:首先,明确需要进行PFMEA分析的制造或工艺过程,确定评估对象。
一般情况下,优先选择对产品影响最大的关键工序。
2. 组建分析团队:组建由相关人员组成的PFMEA分析团队,包括生产工程师、维修工程师、品质工程师等相关岗位人员。
团队成员应具备相关知识和经验,以便对潜在失效模式进行准确评估。
3. 收集数据:收集与评估对象相关的数据和信息,包括工艺流程图、产品设计规格、设备参数、工艺能力指数等。
4. 识别失效模式:根据收集到的数据和知识,团队成员共同识别可能发生的失效模式,并列入失效模式清单中。
5. 评估失效的严重性:对每个失效模式进行严重性评估,综合考虑安全、质量、交付和成本等方面的影响程度。
PFMEA作业指导书
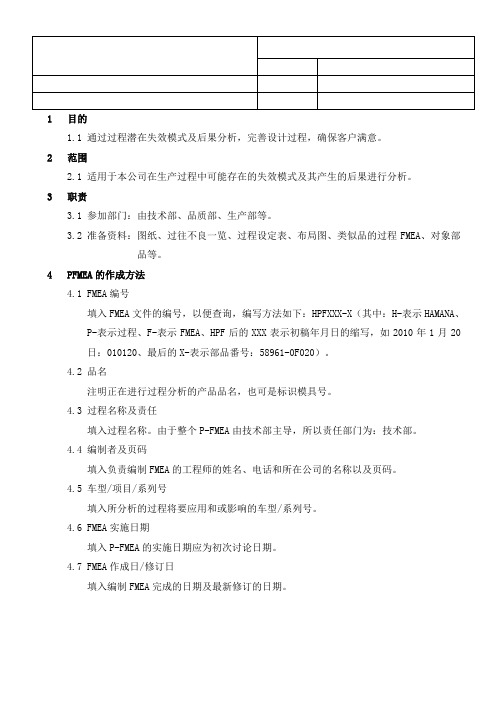
9
微小
能探测出的可能性低
×
只以目视确认进行管理
8
很小
能探测出的可能性低
×
只以双重的目视确认进行管理
7
小
能探测出
×
×
以统计性管理方法等管理图进行管理
6
中等
能探测出
×
部品离开本过程后用各样计测进行管理,部品离开本过程后用OK/NG的计测确认实施全数检查
5
中上
能充分能探测出
×Байду номын сангаас
×
②、采取预防或防错措施,来改变频度。
③、通过增加新的品质控制方法,来改变探测度。
4.21责任者&目标完成日
填入每一项建议措施的责任者以及预计完成的目标日期。
4.22实施对策
在实施了措施之后,填入实际措施的简要说明以及生效日期。
4.23对策结果
在进行预防/对策之后,重新评价所得出的严重度、频度、探测度的级别,计算风险顺序。
③、对RPN的计算结果进行排序,如针对前三项无进一步的措施,则至少应对前三项进一步采取措施
4.20建议措施
所建议的各措施的目的是在于依次降低严重度、频度、探测度的级别,必须进行改善。对涉及到给制造/组装作业者能带来危险影响的所有失效模式,需研讨/纠正措施、排除,减轻或控制起因来避免失效模式的发生。
①、通过改变设计,来改变严重度。
4.9.2尽量细分化对象过程或作业:原材料入库/出库、材料干燥、加料、拌料、上下模、成型机的周边环境、模具温度成型工艺条件、成型机状况、模具状况、治工具的影响、涂装室的环境、涂装的工艺条件、涂装设备、组装环节产品检查、成品出货等,并简单填写各过程的控制要求。(如:成型过程,其控制要求:产品尺寸、外观等)。
PFMEA制作指南
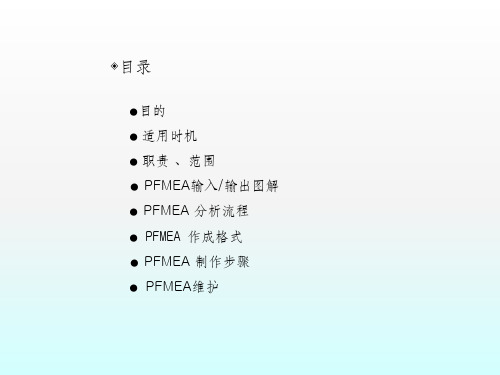
PFMEA初始日期
- 记录最初的PFMEA任务结束日
PFMEA修改日期 - 最终修订日(Revision Number)
核心小组 - 所有成员的姓名及联系方式
◈ PFMEA 作成步骤
阶段2. 记录过程/功能/要求
探测度用“1~10”表示 10分: 根据现有的管理不能检出失效原因及所伴随的失效模式. 9分:检出失效原因及所伴随的失效模式的可能性极小 8分:检出失效原因及所伴随的失效模式的可能性小 7分:检出失效原因及所伴随的失效模式的可能性非常低 6分:检出失效原因及所伴随的失效模式的可能性低 5分检出失效原因及所伴随的失效模式的可能性一般 4分:检出失效原因及所伴随的失效模式的可能性比一般要高 3分:检出失效原因及所伴随的失效模式的可能性高 2分:检出失效原因及所伴随的失效模式的可能性非常高 1分:能够检出失效原因及所伴随的失效模式
◈ PFMEA 作成步骤
阶段5.记录严重度
例子: 汽车行业 PFMEA严重度建议评价标准
◈ PFMEA 作成步骤
阶段6.记录等级或分类
●对严重度高(大于8的项目)、 或特殊过程特殊特性(关键、主 要、重要、重点特性)的识别标 识,
一般用 ▲符号或其他符号进行 标识,以引起重点关注
◈ PFMEA 作成步骤
◈ PFMEA 作成步骤
阶段11.记录探测度
例子: 汽车行业 PFMEA探测度建议评价标准
◈ PFMEA 作成步骤
阶段12.记录RPN
RPN : Risk Priority Number(风险优先指数) = 严重度×发生度×探测度
◈PFMEA 作成格式
项目名称 产品型号 核心小组
PFMEA作业指导书
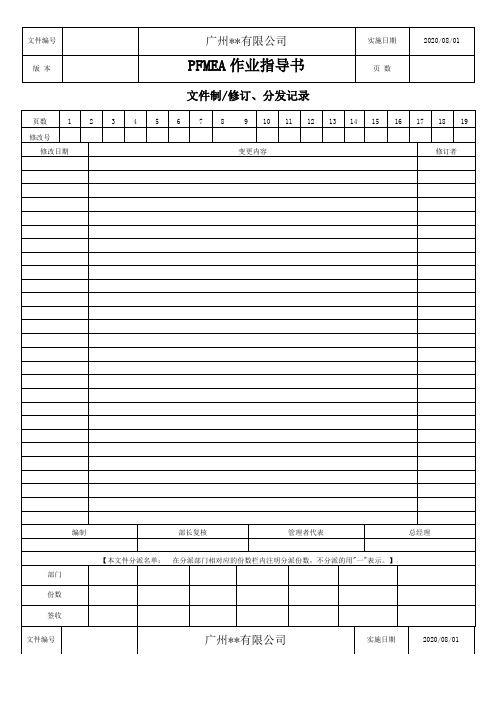
文件制/修订、分发记录1、目的为PFMEA作业提供依据2、适用范围适用于PFMEA的制作与修改3、作业步骤一、准备:由研发部准备以下资料:过往缺陷一览、过程流程图、类似品的过程FMEA、对象部品等二、PFMEA的制定,由研发部召集包括生产、品管、采购、业务、技术人员通过会议的方式完成PFMEA表格,完成内容如下所列: (1)、FMEA 编号填入FMEA文件的编号,以便查询(2)、部品名及图号注明正在进行过程分析的产品的部品名和图纸号(3)、过程责任部门填入项目工程师姓名及联系电话。
(4)、编制者信息填入负责编制FMEA的工程师的姓名、电话。
(5)、关键日期填入P-FMEA的讨论日期。
(6)、FMEA完成日/修订日填入编制FMEA完成的日期及最新修订的日期。
(7)、核心小组列出有权确定和或执行任务的部门的名称和个人的姓名及职位。
(8)、过程填入工序名称,应包括从来料到出货的所有工序;(9)、要求填入对应工序的产品质量控制要求,如“尺寸满足图纸要求”;(10)、潜在性失效模式①、在准备PFMEA作业中,假定原材料/过程均为合理,除非依据历来的数据显示进料的品质有缺点,则可纳入分析。
②、可预测到的不良:如材质不良、短料、变形、尺寸超差、碰伤、拉伤、测量的不安全、摆放的不安全等。
(11)、潜在性失效后果①、对于顾客的定义,可以是下一个制程,后续的作业或地点,经销商和或汽车车主。
当评估失效潜在效应后果时,每一个对象均应考虑到:a、对于最终使用者而言,其后果以产品或系统性能的感受,如下表所示:b、对于下一个制程或后续的作业/地点,其后果以制程/操作性能的感受,如下表所示:c、对于本部门的制程与作业,其后果以制程/可操作性为原则,考虑产品是否报废或返工等,如下表所表示:(12)、严重度①、严重度是针对失效模式中最严重的效应等级。
②、严重度等级指数可对系统、子系统或零部件的设计变更或制程之重新设计来降低。
③、失效模式后果的严重度为1分者,则不需要作进一步分析。
- 1、下载文档前请自行甄别文档内容的完整性,平台不提供额外的编辑、内容补充、找答案等附加服务。
- 2、"仅部分预览"的文档,不可在线预览部分如存在完整性等问题,可反馈申请退款(可完整预览的文档不适用该条件!)。
- 3、如文档侵犯您的权益,请联系客服反馈,我们会尽快为您处理(人工客服工作时间:9:00-18:30)。
无锡精艺达科技有限公司文件号:JYD-FM—18-04版次:A
文件名称PFMEA制作及修订指引办法页次/总页次:2/10 6。
4.l PFMEA 制做要准备以下资料:①过程流程图和产品或过程特殊特性表;
②产品规格书和客户要求资料;③类似产品PFMEA 资料。
按该制程的
工艺流程图所指明工序,依顺序进行,属过程或产品特殊特性的工序要
在“分类”栏填写相应符号,如客户对特殊特性的标识符号无特殊要求,公司则用“△"表示。
过程特性使用“◊”飞产品特性使用“△”.返
工/修正工序需要纳入FMEA,检查工序的过程中如果辅助的检查工具
对产品会有损伤的隐患,那么也要进行失效分析。
6.4。
2关键日期:填写初次PFMEA预计完成的日期,该日期不能超过产品计
划生产的日期。
6.4.3过程的功能分析
(a)对应过程流程图确定过程编号,所用的编号、顺序、术语必须与过程
流程图保持一致。
(b)尽可能简单说明过程的功能,如“下料、车加工、外观检查、包装”
(c)并逐一列出该过程的要求,包括产品尺寸、外观、材质和功能。
(d)根据过程流程图的特殊特性资料,在表格的特殊特性栏标识清楚。
6.4.4潜在失效模式分析
(a)在假定提供给本工序作业的物料是合格的前提下对本工序的作业内
容进行潜在失效模式分析。
(b)要对具体不符要求的作业内容的描述,如“孔破”要充分考虑其可
能存在的失效模式,在制程中对相关项目是否符合作业指示中相关规
格加以判定。
应该用化学的、物理的、专业性的术语来描述潜在失效
模式,而不同于顾客所见的现象:典型的失效模式:偏位、氧化、缺口、
划伤、折痕、破裂、脏污等。
(c)潜在失效后果:失效模式会对内部(下工序或地点)或最终使用者有
影响,如果该失效模式可能影响到安全或造成违法的法规,则要清楚陈
述。
①对最终使用者来说,失效的后果应该用产品或系统的性能来描述,
如:噪音、无信号、显示暗划或缺划、按键不入数、异昧、不稳定、外
观不良、返工/返修、顾客不满意、报废等.
②如果顾客是下一道工序,该后果应该以过程/作业性能来摇述,如:
无法镀铜、镀铜不良、形成开路、无法安装、无法配合、无法加工表
面或会损坏设备、导致工具过度磨损、危害操作者等。
②预防控制:防止失效的起因/机理、失效模式出现或者降低其出现的
机率。
如:机器维护保养、SPC 、防错、防果等.
③探测控制:探测出失效的起因/机理或者失效模式,导致采取纠正措施。
④优先运用预防控制的方法,因为其将影响最初的频度;最初的探测度
将基于探测控制.
(b)探测度(D):是指在产品离开制造工序之前,采用现行过程控制方法找出
失效起因/机理的可能性的评价指标,是与过程控制栏中所列的最佳
探测控制相关的定级数。
为了获得一个较低的定级,通常计划的过程控
制必须予以改进.(探测度评价准则见表=)
6。
4.8风险评估:优先关注风险严重度S=8,9, 10
S0〉35
RPN:> 100
风险指数(RPN):风险指数是指严重度(S)频度(0)和探测度(D)的乘积
风险优化指数SO : 严重度(S)和频度(0)的乘积
建议措施:
建议措施提出时机:依风险关注的优先顺序,当风险评估满足以上任一条件时要对设计或过程进行优化、改善,填写建议措施。
措施提出应首先针对高严重度,so值超过35及RPN值大于100的项目要强制进行预防/纠正措施的工程评价.是否制定和采取建议措施由核心功能小组成员决定RPN值同等的情况取严重度高的,严重度也相同的情况下取频度高的,频度相同,则取探测度级别高的,如客户有特殊要求的按客户要求执行。
举例说明:
依以下顺序降低其凤险级别:严重度,频度和探测度.
①一般实践中,当严重度是9或10时,必须对设计或过程进行优化、改
善, 填写建议措施,以确保现行的设计措施/控制或过程预防/纠正措施针对了这种凤险。
如作业员的适当防护。
XXXXXXX有限公司文件号:JYD-FM—18-04
版次:A
04
版次:A
文件名称PFMEA制作及修订指引办法页次/总页次:7/10 8。
附录
附录A《流程图》。