北京科技大学材料成形自动控制基础复习要点
北京科技大学材料成型自动控制基础书本重点 chenyang

材料成形自动控制理论基础总结版1.自动控制是采用自动检测、信号调节、电动执行等自动化装置组成的闭环控制系统,它使各种被控变量保持在所要求的给定值上。
2.过程自动化是指在生产过程中,由多个自动控制系统组合成的复杂过程控制系统。
3.生产过程实现自动化的目的是:保证生产过程安全稳定;维持工序质量,用有限资源制造持久耐用的精美产品;在人力不能胜任的复杂快速工作场合中实现自动操作;把人从繁重枯燥的体力劳动中解放出来;不轻易受人的情绪和技术水平影响,按要求控制生产过程。
4.轧制生产过程的特点:(1)需要模型计算。
(2)控制项目众多。
(3)调节速度快。
(4)参数之间相互耦合影响。
(5) 控制结果综合性强。
5.轧制过程技术现状:(1) 轧钢生产日益连续化。
(2)轧制速度不断提高。
(3)生产过程计算机控制。
(4) 产品质量和精度高标准交货。
(5)操作者具有较高技术水平。
6.轧制自动化目前可以分为对过程的自动控制和对工艺过程的计算机系统控制两部分。
7.计算机控制内容又分为计算机配置方式、信息跟踪方式和动态在线控制算法以及分布计算机通讯网络四大部分。
8.中国冶金自动化的发展:(1) 在基础控制方面,以PLC、DCS、工业控制计算机为代表的计算机控制取代了常规模拟控制。
(2)在控制算法上,重要回路控制一般采用PID算法。
(3)在电气传动方面,用于节能的交流变频技术普遍采用;国产大功率交直流传动装置在轧线上得到成功应用。
(4)在过程控制方面,计算机过程控制系统普及率有较大幅度提高。
9.自动控制是利用控制系统使被控对象或是生产过程自动按照预定的目标运转所进行的控制活动。
10.开环控制系统:输出量不会返回影响过程的直接控制系统。
11.闭环控制系统:将输出量反馈回来影响输人量的控制系统,或称为反馈控制系统。
12.自动控制系统:如果将自动检测信号与设定值进行比较,得到与目标信号的偏差,再利用运算控制器自动完成偏差信号调节和控制信号输出,最后由电动执行器完成调节任务,使偏差得到消除,就成为自动控制系统。
材料成型技术基础-总复习-知识点归纳

二、铸造1.零件结构分析:筒壁过厚;圆角过渡,易产生应力集中。
2.铸造方法:砂型铸造(手工造型)及两箱造型。
3.选择浇注位置和分型面4.确定工艺参数(1) 铸件尺寸公差:因精度要求不高,故取CT15(2) 要求的机械加工余量(RMA ):余量等级取H 级。
参考表2-6,余量值取5mm ,标注为GB/T 6414-CT15-RMA5(H)(3) 铸件线收缩率:因是灰铸铁件及受阻收缩,取0.8%(4) 起模斜度:因铸件凸缘端为机加工面,增加壁厚式,斜度值1°(5) 不铸出的孔:该铸件6个φ18孔均不铸出(6) 芯头形式:参考图2-39,采用水平芯头零件结构的铸造工艺性:1、基本原则:1) 铸件的结构形状应便于造型、制芯和清理2) 铸件的结构形状应利于减少铸造缺陷3) 对铸造性能差的合金其铸件结构应从严要求2、铸造性能要求:1) 铸件壁厚应均匀、合理(外壁>内壁>肋(筋))2) 铸件壁的连接(圆角过渡、避免交叉和锐角、避免壁厚突变 )3) 防止铸件变形(结构尽量对称)4) 避免较大而薄的水平面5) 减少轮形铸件的内应力 (避免受阻收缩)3、铸造工艺要求:1)外形铸件外形分型面应尽量少而平;避免局部凸起或凹下侧凹和凸台不应妨碍起模;垂直于分型面的非加工面应具有结构斜度2)内腔尽量采用开放式、半开放式结构;应利于型芯的固定、排气和清理3)大件和形状复杂件可采用组合结构三、塑性成形金属塑性成形的方法:锻造、冲压、挤压、轧制、拉拔自由锻1、零件结构分析2、绘制锻件图 (余块、余量、公差)3、确定变形工序(镦粗、冲孔、芯轴、拔长、弯曲、切肩、锻台阶)4、计算坯料质量(mo= (md+mc+mq) (1+δ))和尺寸 (首工序镦粗:D0≥0.8 拔长:D0≥ 零件结构的自由锻工艺性1)应避免锥形或楔形,尽量采用圆柱面和平行面,以利于锻造2)各表面交接处应避免弧线和曲线,尽量采用直线或圆,以利于锻制3)应避免肋板或凸台,以利于减少余块和简化锻造工艺4)大件和形状复杂的锻件,可采用锻—焊,锻—螺纹联接等组合结构模锻1、零件结构分析(分模面、结构斜度、圆角过渡、腹板厚度)2、绘制锻件图(余块、机械加工余量、锻件公差、模锻斜度、模锻圆角)3、确定变形工步(镦粗、拔长、滚压、弯曲、预锻、终锻)4、修整工序选择(切边、冲连皮、校正、热处理(正火或退火)、清理) 30V max Dy零件结构的模锻工艺性1)应有合理的分模面,以保证锻件从模膛中取出又利于金属填充、减少余块和易于制模2)与分模面垂直的非加工面应有结构斜度,以利于从模膛中取出锻件(圆角过渡,利金属流动,防应力集中)3)应避免肋的设置过密或高宽比过大,利于金属充填模膛4)应避免腹板过薄,以减小变形抗力以及利于金属填充模膛5)应尽量避免深孔或多孔结构,以利于制模和减少余块6)形状复杂性件宜采用锻—焊、锻—螺纹联接等组合结构,以利于模具和减少余块冲压(冲裁、弯曲、拉深、缩口、起伏和翻孔)冲裁:落料模:D凹≈(Dmin)D凸≈(D凹-Zmin)冲孔模:d凸≈(dmax)d凹≈(d凸+Zmin)弯曲:工件内侧圆角半径≥凸模圆角半径、弯曲件毛坯长度拉伸:拉深间隙、拉伸模尺寸、毛坯直径、拉深次数冲压工序:1)带孔平板件:单工序:先落料后冲孔,连续模:先冲孔后落料2)带孔的弯曲件或拉深件:热处理、拉深/弯曲、冲孔3)形状复杂的弯曲件:先弯两端、两侧,后弯中间模具:单工序模、复合模、连续模1、零件结构分析:孔边距过小,宜加大2、冲裁间隙:取大间隙Z/2=(10%~12.5%)δ故Z=0.30~0.38mm模具刃口尺寸:落料模:D凹≈(Dmin)=33.2 D凸≈(D凹-Zmin)=32.9冲孔模:d凸≈(dmax)=26.7 d凹≈(d凸+Zmin)=273、冲压工序选择工序类型:平板件,冲孔和落料工序工序顺序:大批量,先冲孔后落料4、模具类型:精度要求不高且为大批量生产,采用连续模零件结构的冲压工艺性1)材料:尽量选用价格较低的材料2)精度和表面质量:3)冲压件的形状和尺寸1)冲裁件:①形状尽可能简单、对称②圆弧过渡、避免锐角③注意孔形、孔径、孔位2)弯曲件:①形状②h、a、c≥2δ、l≥r+(1~2)δ、R/r≥0.5δ③冲孔槽防止孔变形④位置3)拉深件:①形状②转角l≥R/r+0.5δ、R≥2~4δ、r≥2δ③位置④组合工艺、切口工艺四、连接成形焊接头力学性能:相变重结晶区、焊缝金属区、母材、不完全重结晶区、熔合区、过热区焊接残余应力:调节1)设:减少焊缝的数量和尺寸并避免焊缝密集和交叉;采用刚性较小的接头2)工:合理的焊接顺序(先内后外、先短后长、交叉处不起头收尾)、降低焊接接头的刚性、加热减应区、锤击焊缝、预热和后热2、消除:1)去应力退火2)机械拉伸法3)温差拉伸法4)振动法3、焊接残余变形控制和矫正:(收缩变形、角变形、弯曲变形、扭曲变形、失稳变形)1)设:尽量减少焊缝的数量和尺寸,合理选用焊缝的截面形状2、合理安排焊缝位置2)工:反变形法、刚性固定法、合理选用焊接方法和焊接规范、选用合理的装配焊接顺序材料的焊接性:(材料的化学成分、焊接方法、焊接材料、焊件结构类型、服役要求)焊接性评价:碳当量、冷裂纹敏感系数公式金属材料的焊接:1、碳钢:(①淬硬组织、裂纹;②预热和后热;③低氢型焊条、碱度较高的焊剂;④去应力退火或高温回火)1)低碳钢、强度低的低合金结构钢:各种方法,无需采用任何工艺措施方便施焊2)中碳钢:①易②③④小电流、低焊速和多层焊。
《材料成形技术基础》复习要点 (2)
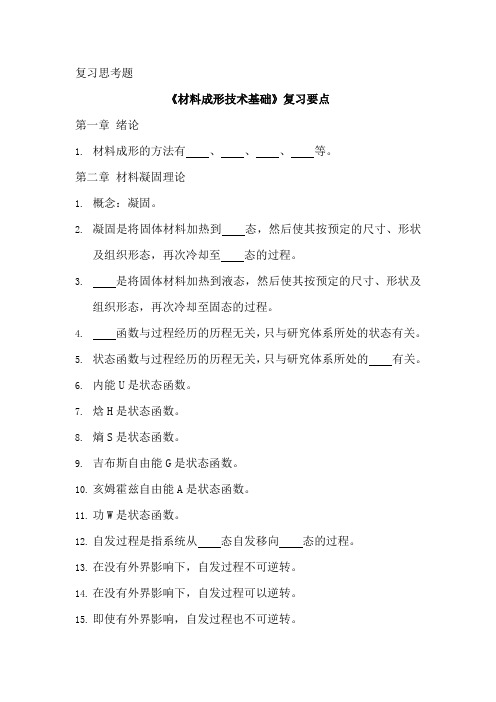
复习思考题《材料成形技术基础》复习要点第一章绪论1.材料成形的方法有、、、等。
第二章材料凝固理论1.概念:凝固。
2.凝固是将固体材料加热到态,然后使其按预定的尺寸、形状及组织形态,再次冷却至态的过程。
3.是将固体材料加热到液态,然后使其按预定的尺寸、形状及组织形态,再次冷却至固态的过程。
4.函数与过程经历的历程无关,只与研究体系所处的状态有关。
5.状态函数与过程经历的历程无关,只与研究体系所处的有关。
6.内能U是状态函数。
7.焓H是状态函数。
8.熵S是状态函数。
9.吉布斯自由能G是状态函数。
10.亥姆霍兹自由能A是状态函数。
11.功W是状态函数。
12.自发过程是指系统从态自发移向态的过程。
13.在没有外界影响下,自发过程不可逆转。
14.在没有外界影响下,自发过程可以逆转。
15.即使有外界影响,自发过程也不可逆转。
16. 有外界影响时,自发过程可以逆转。
17. 自发过程两个判据是 和 。
18. 自由能最低原理指 条件下,体系的自由能永不增大,自发过程的方向力图 体系的自由能,平衡的标志是体系的自由能 。
19. 吉布斯自由能判据(自由焓判据)指 条件下,一个只做体积功的体系,其自由焓永不 ,自发过程的方向是使体系自由焓 ,当自由焓减到 时,体系达到平衡。
20. 概念:自发过程;自由能最低原理。
21. 如图示,a )-d)分别处于什么润湿状态?22. 根据杨氏方程LGLS SG σσσθ-=cos ,说明当LG LS SG σσσ、、满足什么条件时,接触界面表现为润湿(不润湿)。
23. 由于自发形核是自行发生的形核,因此比非自发形核容易。
24. 非自发形核依靠外来质点形核,比自发形核容易。
25. 由于非自发形核依靠外来质点形核,因此没有自发形核容易进行。
26. 形核剂应具备的基本条件是 、 、 、 。
27. 凝固时,形核剂应具备的基本条件是什么?28. 粗糙界面的晶体生长要比光滑界面容易。
29. 光滑界面的晶体生长要比粗糙界面容易。
材料成型复习提纲(完整版)
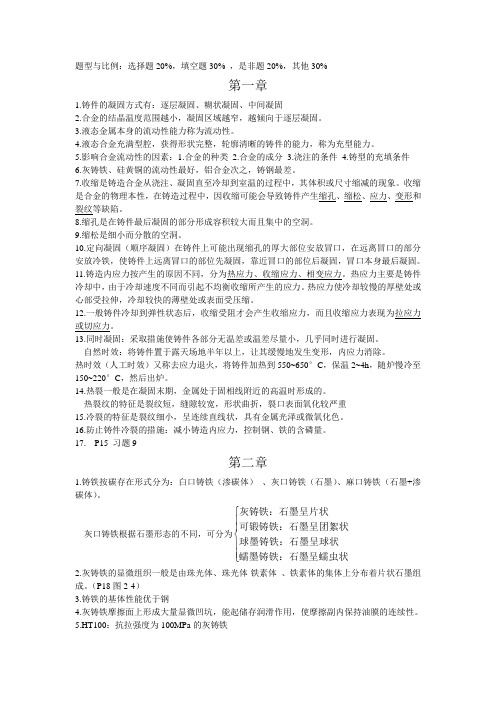
题型与比例:选择题20%,填空题30% ,是非题20%,其他30%第一章1.铸件的凝固方式有:逐层凝固、糊状凝固、中间凝固2.合金的结晶温度范围越小,凝固区域越窄,越倾向于逐层凝固。
3.液态金属本身的流动性能力称为流动性。
4.液态合金充满型腔,获得形状完整,轮廓清晰的铸件的能力,称为充型能力。
5.影响合金流动性的因素:1.合金的种类2.合金的成分3.浇注的条件4.铸型的充填条件6.灰铸铁、硅黄铜的流动性最好,铝合金次之,铸钢最差。
7.收缩是铸造合金从浇注、凝固直至冷却到室温的过程中,其体积或尺寸缩减的现象。
收缩是合金的物理本性,在铸造过程中,因收缩可能会导致铸件产生缩孔、缩松、应力、变形和裂纹等缺陷。
8.缩孔是在铸件最后凝固的部分形成容积较大而且集中的空洞。
9.缩松是细小而分散的空洞。
10.定向凝固(顺序凝固)在铸件上可能出现缩孔的厚大部位安放冒口,在远离冒口的部分安放冷铁,使铸件上远离冒口的部位先凝固,靠近冒口的部位后凝固,冒口本身最后凝固。
11.铸造内应力按产生的原因不同,分为热应力、收缩应力、相变应力。
热应力主要是铸件冷却中,由于冷却速度不同而引起不均衡收缩所产生的应力。
热应力使冷却较慢的厚壁处或心部受拉伸,冷却较快的薄壁处或表面受压缩。
12.一般铸件冷却到弹性状态后,收缩受阻才会产生收缩应力,而且收缩应力表现为拉应力或切应力。
13.同时凝固:采取措施使铸件各部分无温差或温差尽量小,几乎同时进行凝固。
自然时效:将铸件置于露天场地半年以上,让其缓慢地发生变形,内应力消除。
热时效(人工时效)又称去应力退火,将铸件加热到550~650°C,保温2~4h,随炉慢冷至150~220°C,然后出炉。
14.热裂一般是在凝固末期,金属处于固相线附近的高温时形成的。
热裂纹的特征是裂纹短,缝隙较宽,形状曲折,裂口表面氧化较严重15.冷裂的特征是裂纹细小,呈连续直线状,具有金属光泽或微氧化色。
材料成型及控制相关知识
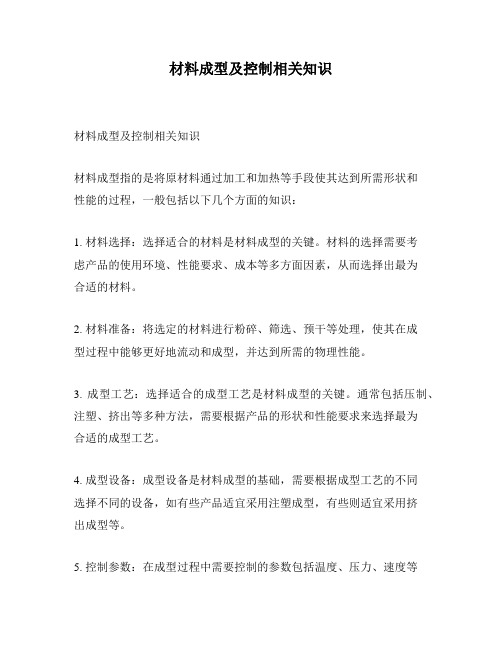
材料成型及控制相关知识
材料成型及控制相关知识
材料成型指的是将原材料通过加工和加热等手段使其达到所需形状和
性能的过程,一般包括以下几个方面的知识:
1. 材料选择:选择适合的材料是材料成型的关键。
材料的选择需要考
虑产品的使用环境、性能要求、成本等多方面因素,从而选择出最为
合适的材料。
2. 材料准备:将选定的材料进行粉碎、筛选、预干等处理,使其在成
型过程中能够更好地流动和成型,并达到所需的物理性能。
3. 成型工艺:选择适合的成型工艺是材料成型的关键。
通常包括压制、注塑、挤出等多种方法,需要根据产品的形状和性能要求来选择最为
合适的成型工艺。
4. 成型设备:成型设备是材料成型的基础,需要根据成型工艺的不同
选择不同的设备,如有些产品适宜采用注塑成型,有些则适宜采用挤
出成型等。
5. 控制参数:在成型过程中需要控制的参数包括温度、压力、速度等
多个方面,需要根据产品的要求进行相应的调整和控制,以保证产品的质量达到所需标准。
6. 检测和修整:成型后的材料需要进行检测和修整,以保证其符合产品的要求,这需要根据产品的不同进行相应的检测方法和技术,如力学性能测试、X射线检测等。
总之,材料成型及控制相关知识是非常广泛和复杂的一个领域,需要掌握和应用多方面的技术和知识,以保证成型后的产品质量和性能达到所需标准。
材料成型控制工程基础考试重点
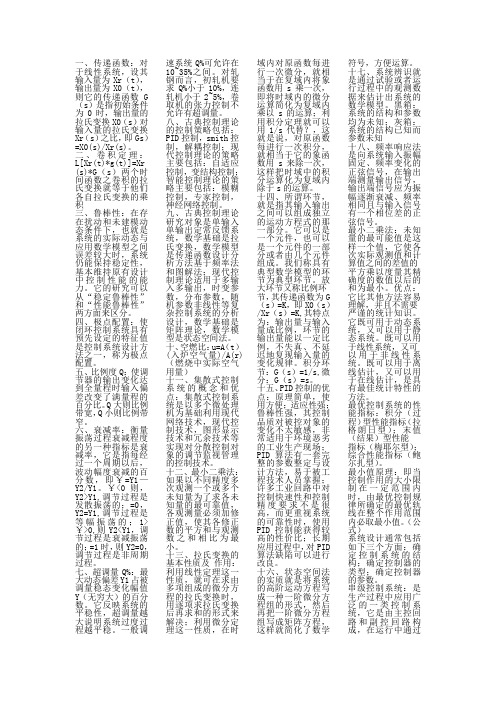
一、传递函数:对于线性系统,设其输入量为Xr(t),输出量为X0(t),则它的传递函数G (s)是指初始条件为0时,输出量的拉氏变换X0(s)对输入量的拉氏变换Xr(s)之比,即Gs)=X0(s)/Xr(s)。
二、卷积定理:L[Xr(t)*g(t)]=Xr (s)*G(s)两个时间函数之卷积的拉氏变换就等于他们各自拉氏变换的乘积三、鲁棒性:在存在扰动和未建模动态条件下,也就是系统的实际动态与应用数学模型之间误差较大时,系统仍能保持稳定性,基本维持原有设计中控制性能的能力。
它的研究可以从“稳定鲁棒性”和“性能鲁棒性”两方面来区分。
四、极点配置:使闭环控制系统具有预先设定的特征值是控制系统设计方法之一,称为极点配置。
五、比例度Q:使调节器的输出变化达到全量程时输入偏差改变了满量程的百分比。
Q大则比例带宽,Q小则比例带窄。
六、衰减率:衡量振荡过程衰减程度的另一种指标是衰减率,它是指每经过一个周期以后,波动幅度衰减的百分数,即¥=Y1—Y2/Y1。
¥<0则,Y2>Y1,调节过程是发散振荡的;=0,Y2=Y1,调节过程是等幅振荡的;1>¥>0,则Y2<Y1,调节过程是衰减振荡的;=1时,则Y2=0,调节过程是非周期过程。
七、超调量Q%:最大动态偏差Y1占被调量稳态变化幅值Y(无穷大)的百分数。
它反映系统的平稳性,超调量越大说明系统过度过程越平稳。
一般调速系统Q%可允许在10~35%之间。
对轧钢而言,初轧机要求Q%小于10%,连轧机小于2~5%,卷取机的张力控制不允许有超调量。
八、古典控制理论的控制策略包括:PID控制,smith控制,解耦控制;现代控制理论的策略主要包括:自适应控制,变结构控制;智能控制理论的策略主要包括:模糊控制,专家控制,神经网络控制。
九、古典控制理论研究对象是单输入单输出定常反馈系统,数学基础是拉氏变换,数学模型是传递函数设计分析方法基于频率法和图解法;现代控制理论适用于多输入多输出,时变参数,分布参数,随机参数非线性等复杂控制系统的分析设计,数学基础是矩阵理论,数学模型是状态空间法。
北京科技大学材科基第二学期复习重点(共21张PPT)

• 临界晶核半径、临界形核功、形核率 • 晶核长大
• 液固界面结构(光滑、粗糙) • 晶核长大方式
• 固溶体的结晶
• 平衡凝固、非平衡凝固 • 平衡分配系数、Scheil方程、成分过冷
• 共晶凝固和包晶凝固
共二十一页
第十一章 凝固(nínggù)
• 相关公式
CLC0fLk01
共二十一页
8. (本题20分) 用成分-自由能曲线表述二元过饱和固溶体脱溶驱动力和 形核驱动力。说明脱溶可能的贯序,解释产生这些贯序可能的原因。 下图为铝铜合金不同过渡相的转变曲线图,回答以下问题:①合金
经固溶处理后,在室温放置多少时间才开始出现G.P.区?②在什么 温度G.P.区出现最快?需要多少时间?③G.P.区能出现的最高温 度是多少?④q’’相出现的最高温度是多少?⑤在130 C时效
• 奇异晶界、邻位晶界 • 小角晶界和大角晶界:能量、偏析、迁移 • 取向差 • 相界—共格、半共格、非共格 • 体缺陷
共二十一页
第八章 固体中原子的扩散
• 扩散机制—间隙、空位、换位
• 扩散系数—微观意义、影响因素 • 扩散激活能 • 扩散方程的解
•误差函数解、高斯解、三角函数解、数值(shùzí)解、平方根关系
C S k 0 C 01 fSk 0 1
mLC01k0 GL DL k0 v
共二十一页
第十二章 固态转变
• 合金脱溶 • 脱溶贯序
• 时效 • 共析转变、块状转变
• 连续型转变—调幅分解、无序—有序转变 • 无扩散型相变 • 回复和再结晶
• 组织、性能变化、驱动力 • 再结晶基本规律、动力学及影响因素(yīn sù)
高;Σ3孪晶界是共格的,很稳定,能量很低,甚至低于小角晶界;杂质偏析少,迁移率
材料制备加工理论题复习提纲(北科大)

材料制备加⼯理论题复习提纲(北科⼤)材料制备加⼯(宋⽼师上课部分)第⼀章材料加⼯成形的⽅法1.概述:根据化学成分和显微结构分为:⾦属材料、⽆机粉⾦属材料、⾼分⼦材料、复合材料成形。
2.⾦属材料的精确成形包括:铸造、塑性成形、焊接。
3.⾦属塑性成形:利⽤⾦属在外⼒作⽤下所产⽣的塑性形变来获得具有⼀定形状、尺⼨和⼒学性能的材料。
(⼀般作⽤⼒有冲击⼒和压⼒)4.⾦属塑性成形包括:轧制:⾦属坯料在两个回转轧辊之间受压变形⽽形成各种产品的成形⼯艺。
挤压:⾦属坯料在挤压模内被挤出模孔⽽变形的成形⼯艺。
拉拔:将⾦属坯料拉过拉拔模的模孔⽽变形的成形⼯艺。
锻压:⾦属坯料在上下砥铁间受冲击⼒或压⼒⽽变形的成形⼯艺称为⾃由锻,坯料在⼀定形状的锻模模膛内受冲击⼒或挤压⼒⽽变形的成形⼯艺称模锻,⾦属板料在冲模之间受压产⽣分离或变形的成形⼯艺称冲压。
5.焊接与其他连接⽅法的重要区别是通过原⼦之间的结合⽽实现连接。
6.材料成形加⼯技术的发展趋势:精密成形-材料制备与成形⼀体化-复合成型-数字化成形-材料成形⾃动化-绿⾊清洁⽣产。
第⼆章钢铁材料⽣产⼯艺1.炼铁:矿⽯到钢材可分为两个流程:(长流程)⾼炉-转炉-轧机流程;(短流程)直接还原或熔融还原-电炉-轧机流程。
2.设备:⾼炉本体和五个辅助设备系统3.原料:铁矿⽯和熔剂(作⽤:1.使还原出来的铁与脉⽯和⽯灰⽯实现良好分离,并顺利从炉缸中流出,即渣铁分离。
2.使⼀定数量和⼀定物理、化学性能的炉渣去除有害杂质硫,确保⽣铁质量。
)、⾼炉燃料(焦炭:在风⼝前燃烧,提供冶炼所需热量;固体碳及其氧化物co充当还原剂;在⾼温区焦炭作为⽀撑料柱⾻架,同时保证⽓路流通;铁⽔渗碳。
、煤粉)4.铁矿粉造块⽅法:烧结法和球团法。
5.⾼炉冶炼原理:⽤CO和H2还原铁氧化物(间接还原)T<570℃时,CO作还原剂:3Fe2O3+CO=2Fe3O4+CO2Fe3O4+CO=3FeO+CO2FeO+CO=Fe+CO2当温度⼤于570℃时,⽤H2作还原剂3Fe2O3+H2=2Fe3O4+H2OFe3O4+H2=3FeO+H2OFeO+H2=Fe+H2O间接还原时⽤⽓体作为还原剂,可逆反应,还原剂不能充分利⽤,需要⼀定过量的还原剂。
- 1、下载文档前请自行甄别文档内容的完整性,平台不提供额外的编辑、内容补充、找答案等附加服务。
- 2、"仅部分预览"的文档,不可在线预览部分如存在完整性等问题,可反馈申请退款(可完整预览的文档不适用该条件!)。
- 3、如文档侵犯您的权益,请联系客服反馈,我们会尽快为您处理(人工客服工作时间:9:00-18:30)。
第一、二章1.系统定义:由相互作用和相互依赖的若干组成部分结合成的具有特定功能的有机整体。
(1) 包含若干部分(2) 各个部分之间存在某种联系(3) 具有特定的功能。
控制对象:泛指任何被控物体(不含控制器)。
控制:使某个控制对象中一个或多个输出量随着时间的推移按照某种预期的方式进行变化。
实现:靠控制系统去完成。
开环系统:不存在稳定性问题,控制精度无法保证。
闭环系统:可实现高精度控制,但稳定性是系统设计的一个主要问题。
2.实现闭环控制的三个步骤一是对被控量(即实际轧出厚度或压下位置)的正确测量与及时报告;二是将实际测量的被控量与希望保持的给定值进行比较、PID计算和控制方向的判断;三是根据比较计算的结果,发出执行控制的命令,使被控量恢复到所希望保持的数值上。
闭环控制系统的基本组成和要求(1)被控对象(2)被控量(3)干扰量(或叫扰动量)(4)自动检测装置(或叫自动检测环节) (5)给定量(或叫给定值)(6)比较环节(7)调节器(8)执行控制器古典控制策略主要包括:PID控制、Smith控制和解耦控制。
古典控制策略的应用要满足下面几个条件:(1) 系统应为线性定常系统;(2)系统的数学模型应比较精确;(3) 系统的运行环境应比较稳定。
PID算法的特点PID算法综合了系统动态过程中的过去、现在以及将来的信息PID算法适应性好,有较强的鲁棒性PID算法有一套完整的参数设计与整定方法PID控制能获得较高的性价比对PID算法的缺陷进行了许多改良形成具有实用价值的复合控制策略PID控制的显著缺点是不适于具有大时滞的被控系统( G(s)e- s )变参数及变结构的被控系统系统复杂、环境复杂、控制性能要求高的场合3.PID控制完全依靠偏差信号调节会带来很大调节延迟。
对偏差信号进行比例、积分和微分调节运算称为PID控制,它可以提高控制品质。
这是将偏差放大或通过微分给与短时间的强烈输出,加快启动,减少死区。
积分是将偏差累积起来,进行调整,达到消除静差的目的。
减少比例放大或增加对象变动的阻尼可以减少震荡幅度,但也降低系统响应频率。
自适应控制基本思想:在控制系统的闭环回路之外建立一个由参考模型和自适应机构组成的附加调节回路。
系统用参考模型的输出代表系统的理想输出,当系统运行过程中发生参数或特性的变化时,输出与期望输出之间的误差进入自适应机构,由自适应机构进行运算后,制订出改变控制器参数的策略,或对控制对象产生等效的附加控制,使输出与期望输出趋于一致。
变结构控制变结构控制策略与其它控制策略的根本区别在于:控制器的结构是不固定的,可根据控制对象所处的状态改变。
神经网络控制的特点(1)具有对大量信息的分布存贮能力和并行处理能力;(2)具有对多种形式信息(如图像、语音、数字等)的处理和利用能力;(3)具有很强的处理非线性问题的能力;(4)具有对不确定问题的自适应和自学习能力。
神经网络控制应用方式基本分为两类:单神经元和神经网络。
4.自动控制自动控制是采用自动检测、信号调节(包括数字调节器、计算机)、电动执行等自动化装置,组成的闭环控制系统,它使各种被控变量(如流量、温度、张力、轧机辊缝和轧机转速等)保持在所要求的给定值上。
过程自动化是指在生产过程中,由多个自动控制系统组合的复杂过程控制系统。
5.自动控制目的生产过程实现自动化的目的是:提高工序质量,用有限资源,制造持久耐用的精美产品;在人力不能胜任的复杂快速工作场合中实现自动操作;把人从繁重枯燥的体力劳动中解放出来;不轻易受人的情绪和技术水平的影响,稳定工序质量。
实现自动化大批量生产,提供质量好、性能稳定、价格具有竞争力的产品,为企业生存发展提供更大的空间。
6.现代钢铁生产过程的特点控制项目众多、调节速度快、参数之间相互耦合影响、控制结果综合性强。
7.轧制过程技术现状与自动化发展:轧钢生产日益连续化、轧制速度的不断提高、生产过程计算机控制、产品质量和精度高标准交货、操作者具有高度水平。
8.中国冶金自动化的发展在基础控制方面,以PLC,DCS,工业控制计算机为代表的计算机控制取代了常规模拟控制,在冶金企业全面普及。
近年来发展起来的现场总线、工业以太网等技术逐步在冶金自动化系统中应用,分布控制系统结构替代集中控制成为主流。
在控制算法上,重要回路控制一般采用PID算法,智能控制、先进控制在电炉电极升降控制、连铸结晶器液位控制,加热炉燃烧控制,轧机轧制力控制等方面有了初步应用,取得一定成果。
在电气传动方面,用于节能的交流变频技术普遍采用;国产大功率交直流传动装置在轧线上得到成功应用。
在过程控制方面,计算机过程控制系统普及率有较大幅度提高。
第三章轧制控制计算机系统的数学模型数学模型是计算机自动控制系统设定计算的工具。
与先进工艺、精良设备、精心保养、严格原料等因素一道,成为轧制自动化控制系统的基础。
其合理与否、对生产过程产量的高低、产品质量的优劣和生产事故的多少等均有重要的影响。
轧制数学模型的基本特点1.生产过程由多个环节组成,初始环节偏差影响后续环节2.由于轧制过程表面摩擦、前后张力随机变化,模型参数不可能跟踪变化,这样即便静态模型准确,使用也不很准确。
3.随着通讯、微电子、自动化等高新技术不断发展,以及高新技术进一步应用于冶金工业去创造新工艺、开发新产品,计算机技术支持下的建模和模拟都是经常使用的有效手段。
数学模型的分类1)确定性模型和随机性模型2) 静态模型和动态模型,3)线性模型和非线性模型4) 耦合模型5)离散模型和连续模型,模型的自学习也叫作模型的自适应修正。
进行模型自学习的目的是为了消除和减弱一些变化或干扰因素造成的模型误差,保持和提高数学模型的计算精度。
1.BP网络:其基本思想是,学习过程由信号的正向传播与误差的反向传播两个过程组成。
正向传播时,输入样本从输入层传入,经隐层逐层处理后传向输出层。
若输出层的实际输出与期望输出(教师信号)不符,则转向误差的反向传播阶段。
误差的反向传播是将输出误差以某种形式通过隐层向输入层逐层反传,并将误差分摊给各层的所有单元,从而获得各层单元的误差信号,此误差信号即作为修正各单元权值的依据。
这种信号正向传播与误差反向传播的各层权值调整过程是周而复始地进行。
权值不断调整的过程,也就是网络的学习训练过程。
此过程一直进行到网络输出的误差减少到可以接受的程度,或进行到预先设定的学习次数为止。
BP神经网络包含输入层、输出层和一个隐层2.为什么要预测轧制压力和变形抗力:热轧轧制压力的预报计算计算是个老问题。
在热轧生产中,如何准确地预测在具体生产条件下的轧制压力重要,如果轧制压力太大,会导致轧辊的断裂甚至电机的烧毁;如果轧制压力太小,会导致轧制能力的浪费。
通过准确地预报轧制力可使工厂的技术人员确定合适的轧制工艺。
金属塑性变形抗力是表征钢材压力加工性能的一个基本量,正确确定不同变形条件下金属的变形抗力,是制定合理的轧制工艺规程的必要条件。
3.自学习的流程1) 采集实际数据(1)同时数据。
在同一时刻采集所有机架的有关数据(2)同点数据。
在轧件同一点上采集所有机架的有关数据2) 检查实际测量数据检查各种实测数据的合理性,对实际数据进行极限值检查,判断设定值与实际值的偏差是否超过了给定的限制值。
如果数据异常时,就输出报警,对本块钢不再进行数学模型的自学习,以避免由于测量数据的异常而造成的错误自学习。
主要检查的数据有:PDI数据、带坯的厚度、宽度、温度、精轧温度、轧制力、轧制功率、轧机速度、电流、电压等3) 计算实际测量数据的平均值采用如下算法对实际数据计算平均值即去掉一个最大值,去掉一个最小值,然后取其平均值。
4) 更新自学习系数首先计算各个自学习项目的“瞬时值”,然后进行指数平滑法的修正,最后更新自学习系数。
即把新的自学习系数存储到学习文件中,供下次轧制时使用。
4常用数学模型:初等模型、简单的优化模型、数学规划模型、微分方程模型、差分方程模型、统计回归模型。
第四章轧制过程计算机控制系统轧制过程计算机控制的发展(1)系统结构逐步分散化(2)控制功能不断完善(3)控制范围不断扩大(4)控制速度不断提高工业控制计算机特点(1)可靠性高(2)有开放式的总线结构(3)软件采用组态软件(4)采用专用键盘和面板PLC的主要模块1)CPU模块2)信号模块3)特殊功能模块4)接口模块5)电源模块6)编程设备L0级也称数字传动级,它包括各种DDC/PLC控制的执行设备,这些执行设备本身成为各自独立又有通讯的闭环自动控制系统,可以对调节器进行比例、积分、微分等各种算法设置L1级是SCC操作过程控制级,主要是在程序控制下,进行轧制过程如AGC/AFC等具体控制,即所有相关设备工作的状态控制。
人工操作也可进行干预。
L2 级称为模型控制级(Pattern Integraded Calculation),主要按照产品要求和原料情况,制定压下规程,并按照各工艺环节的数学模型进行预报运算,包括各架辊缝、转速设定,厚度AGC、板形AFC等计算比较。
同时接受L1级控制的结果,进行轧件跟踪、滤波辨识、自学习修正模型系数,特别是控制轧制节奏。
L3级(Procdut Control System)生产控制级,它主要进行全系统生产的计划和调度,安排L2级和L1级进行工作。
这一级又可以按企业的规模和管理范围的大小,分成几级,例如分成车间管理、工厂管理和公司管理级。
PCS级的计算机都是通讯能力强大的通用计算机,要求数据处理和内外存的容量大。
L3级还完成资源调度,质量控制,材料设计、合同跟踪等相应功能,以实现整个热轧生产线的生产控制、调度与管理。
L4级是公司管理级,主要完成合同跟踪、成本核算、生产计划编制、各生产部门协调安排,作业计划的下发(L3 级),跟踪生产情况和质量情况等。
第五章连续铸钢生产过程控制1.实现连铸生产过程自动化的意义:(1)提高产品的质量(2)提高生产率(3)减少人为干扰因素(4)实现现代化管理(5)改善工作环境、降低劳动强度。
2.连铸机的主要装置:(1)结晶器:钢水→铸坯外壳(2)结晶器振动装置:防止坯壳与结晶器粘结,改善铸坯表面质量(3)二次冷却装置:铸坯加速凝固(4)拉坯矫直装置:克服结晶器与二冷区的阻力,拉出铸坯;调节拉速;保证铸坯质量。
3. 连续铸钢检测技术:(1)钢包钢水温度检测(2)浸入式水口混入钢渣检测(3)无氧化浇注的微气量检测(4)结晶器钢水液面检测(5)坯壳与结晶器壁间摩擦力检(6)铸坯拉漏检测(7)铸坯短边凹度检测(8)铸坯凝固外壳厚度检测(9)铸坯表面缺陷检测(10)拉矫辊检测。
4.连续铸钢自动控制:(1)钢包钢水脱氧自动控制(2)保护渣自动加入控制(3)结晶器锥度及宽度自动控制(4)全自动浇注系统①中间罐液位控制②结晶器液位控制③拉速控制(5)火焰切割毛刺自动清理系(6)自动打印装置(7)钢坯搬运吊车的自动化。