石墨化炉节能增产改进技术方案
提高窑产量,降低煤电耗的几项优化措施

公司是2003年由天津院设计的一条5000t∕d熟料生产线,并配套了9Mw纯低温余热发电项目。
石灰石采用两套锤式破碎机,生料粉磨是两条。
4.6mX(10+3.5)m中卸式烘干磨,烧成系统是。
4.8mX72m窑外预热分解系统,煤粉制备采用ZGM立磨系统。
这几年来,公司通过采取精细化管理,重点攻关技术瓶颈,优化完善工艺操作,设备维护全员化,找差距、定目标、寻方法、细管理,经过多年的努力,熟料产量提升了约500t∕d,煤耗下降了约8kg∕t,综合电耗下降了约8kWh∕t,各项指标取得了一定进步。
1、提升窑产量和寻找经济产量生产线是天津院5000t∕d窑型第一代产品,设计时产量富余能力不强,只有在窑产量有了提升空间,才能摸索到最经济产量,才是煤电消耗降低的基础和前提,紧紧围绕这个主线并落实到整个工作始终,原来产量在58001/d左右,优化后现产量能稳定达到6300t∕d左右,最高时能达到6500t∕d,经济运行产量是6100~6300t/d.具体措施是:(1)通过篦冷机用风系统调整,重点增加固定板和一室的面积,对一段风机部分进行调整,主要是增加风量,风压略为提高,来为窑提产提供煤粉燃烧充足的氧气。
(2)调整窑尾烟室相关尺寸。
通过2014年及2015年对预热器进行升级改造,重点是对后窑口、烟室拱形、烟室缩口尺寸进行放大(放大后分别是3.7m、2.44m、2.55m),确保了炉内供氧充足,并做到低阻供氧,同时延长气体停留时间,确保提产后入窑物料分解率达到95%以上。
(3)2014年通过对分解炉加高一钵和2015年对三次风管双进风改成单进风,将分解炉喷煤管位置降低到分解炉锥部,增加气体和物料在炉风停留时间,确保了炉内风煤料最佳配合,分解炉和C5,出口温度分布更趋合理。
(4)在满足了窑、炉供氧需求,同时对预热器各级旋风筒进风蜗壳加大面积,降低系统阻力,使系统内各处风速达到合理匹配,并为提高窑系统产量所需总风量创造了条件。
如何更好的降低电炉电极消耗、改进石墨电极质量?
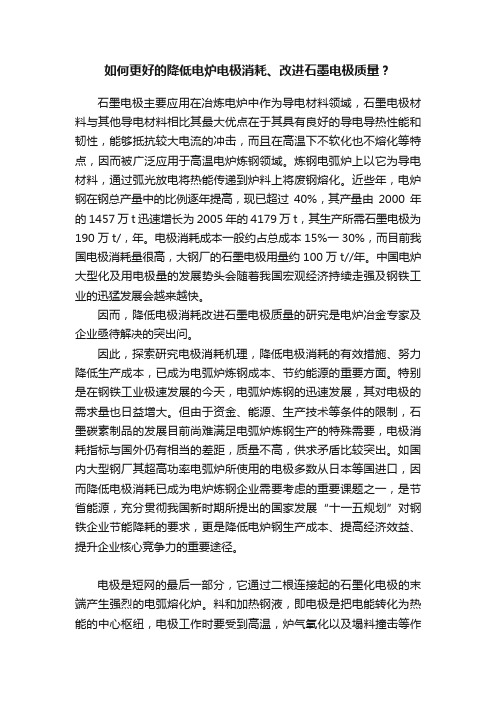
如何更好的降低电炉电极消耗、改进石墨电极质量?石墨电极主要应用在冶炼电炉中作为导电材料领域,石墨电极材料与其他导电材料相比其最大优点在于其具有良好的导电导热性能和韧性,能够抵抗较大电流的冲击,而且在高温下不软化也不熔化等特点,因而被广泛应用于高温电炉炼钢领域。
炼钢电弧炉上以它为导电材料,通过弧光放电将热能传递到炉料上将废钢熔化。
近些年,电炉钢在钢总产量中的比例逐年提高,现已超过40%,其产量由2000年的1457万t迅速增长为2005年的4179万t,其生产所需石墨电极为190万t/,年。
电极消耗成本一般约占总成本15%一30%,而目前我国电极消耗量很高,大钢厂的石墨电极用量约100万t//年。
中国电炉大型化及用电极量的发展势头会随着我国宏观经济持续走强及钢铁工业的迅猛发展会越来越快。
因而,降低电极消耗改进石墨电极质量的研究是电炉冶金专家及企业亟待解决的突出问。
因此,探索研究电极消耗机理,降低电极消耗的有效措施、努力降低生产成本,已成为电弧炉炼钢成本、节约能源的重要方面。
特别是在钢铁工业极速发展的今天,电弧炉炼钢的迅速发展,其对电极的需求量也日益增大。
但由于资金、能源、生产技术等条件的限制,石墨碳素制品的发展目前尚难满足电弧炉炼钢生产的特殊需要,电极消耗指标与国外仍有相当的差距,质量不高,供求矛盾比较突出。
如国内大型钢厂其超高功率电弧炉所使用的电极多数从日本等国进口,因而降低电极消耗已成为电炉炼钢企业需要考虑的重要课题之一,是节省能源,充分贯彻我国新时期所提出的国家发展“十一五规划”对钢铁企业节能降耗的要求,更是降低电炉钢生产成本、提高经济效益、提升企业核心竞争力的重要途径。
电极是短网的最后一部分,它通过二根连接起的石墨化电极的末端产生强烈的电弧熔化炉。
料和加热钢液,即电极是把电能转化为热能的中心枢纽,电极工作时要受到高温,炉气氧化以及塌料撞击等作用,尤其是两根电极连接处,要比其它地方电阻大、导电系数低,易脱扣、氧化、脱落、折断,因而造成电极的极大消耗,而且延长了冶炼时间,降低了生产率。
负极材料石墨化技术要点及改善方向
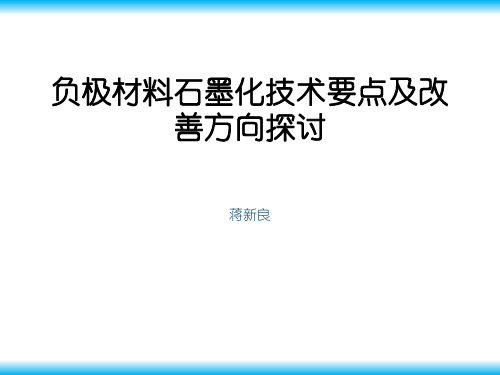
负极材料石墨化工艺不足及改善方向
改善方向及建议:
4、箱体炉兼具艾奇逊炉与内串炉的优点又规避了缺点,推荐 箱体炉作为未来负极材料石墨化的主要炉型,但须对其品 质不稳定的缺点加以关注并重点研究,建议炉型设计小型 化,变压器选取15000KVA~17000KVA,寻求石墨化品质 与石墨化效率的最佳契合点。
三种石墨化方式的特点及不足:
1、艾奇逊炉生产周期长,冷却慢,效率不高; 2、艾奇逊炉平均每1吨主料需要约3~4吨辅料进行生产,这些
辅料多为煅后石油焦,出炉后作为增碳剂售出,另一部分 返炉使用,然而增碳剂的市场增量无法跟上锂电池市场的 飞速发展,增碳剂市场趋于饱和时,辅料处理将变成一大 难题;
3、内串炉生产周期短,电能利用率高,但是装炉量小,坩埚 成本高;
送电——功率曲线的选择
要求: ①根据炉内主/辅料、坩埚的不同选取不同升温曲线; ②炉内主/辅料挥发分较高时,选取较慢的升温曲线; ③炉内主料/辅料灰分较高时,须延长高功率时长。
高效快捷安全
电能充分利用
炉内物料从室温逐步升温至 石墨化温度,且高温区 扩散至全炉需要一定的 时间,如何让送电功率 曲线匹配这个升温曲线, 这是一个永恒的行业研 究方向。
冷却出炉——表皮料处理
由于表皮料在指标上与合格的负极材料相差太大(粒度、振实、 比表、形貌、成分等差异显著),为确保负极材料品质, 可在出炉后出粉前,打掉1~5公分直至物料表面光滑,取 出的表皮料另行处理。
目录
1. 前言
2. 装炉
3. 送电
4.冷却出炉
5.不足及改善方向
6.结束语
28
负极材料石墨化工艺不足及改善方向
但块料由于形状各异,堆积摆放方 式也不同,给炉阻和炉温带来 了不稳定的因素,因此艾奇逊 炉需要注意装块料的方式和位 置(装在高温区)。
卧式高温石墨化炉的设计方案
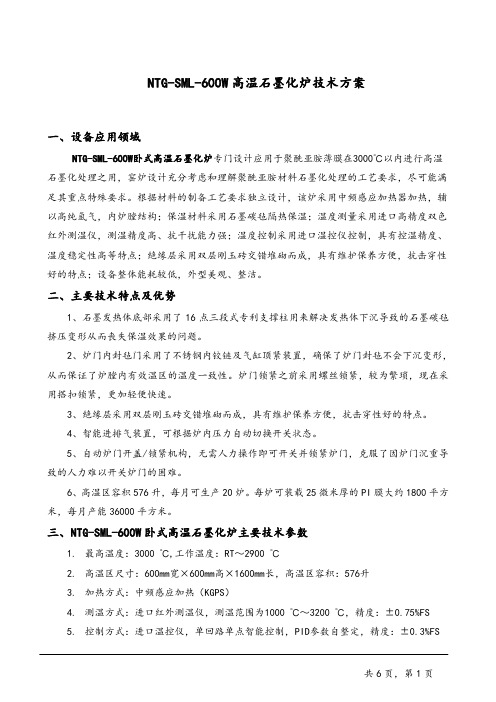
中频感应加热。发热体为卧式整体石墨件,考虑到石墨碳毡经过多次使用会有损耗、下 沉等问题,石墨发热体底部采用了 16 点三段式专利支撑柱用来解决发热体下沉导致的石墨碳
福禄克 endurance
套
1
7
控温仪表
FP93-4I-90-0050
套
1
真空泵
2X-70A
台
1
真空阀
GI-80
只
2
8
真空 系统
进排气阀 破空阀 安全装置
GM-10 GM-10 DN100-0.004MPa
只
4
只
2
套
2
真空计
绝压变送器 KD41
只
2
真空波纹管 DN80
9
炉体 L
DN1830
套
2
台
2
10
三、NTG-SML-600W 卧式高温石墨化炉主要技术参数
1. 最高温度:3000 ℃,工作温度:RT~2900 ℃ 2. 高温区尺寸:600mm宽×600mm高×1600mm长,高温区容积:576升 3. 加热方式:中频感应加热(KGPS) 4. 测温方式:进口红外测温仪,测温范围为1000 ℃~3200 ℃,精度:±0.75%FS 5. 控制方式:进口温控仪,单回路单点智能控制,PID参数自整定,精度:±0.3%FS
测温元件采用高性能双色红外测温仪。温度控制采用独立控制柜,所有控制均位于同一 面板上,操作方便,并配有中文标识。
4.4、冷却系统介绍: NTG-SML-600W卧式高温石墨化炉在系统设计时充分考虑了设备的可靠性和连续长时间运
箱式炉石墨化技术原理
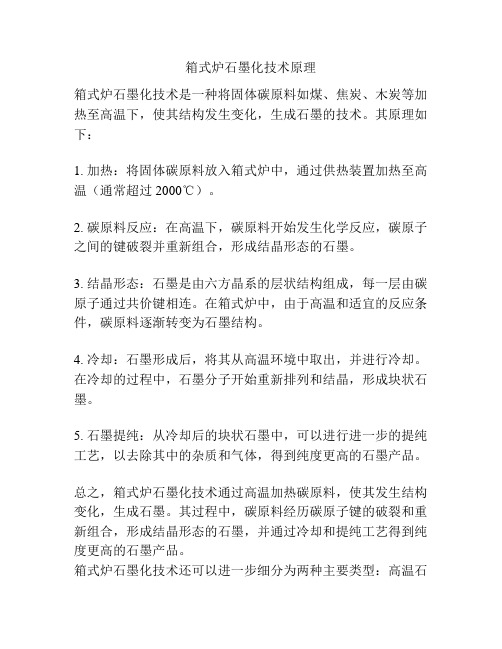
箱式炉石墨化技术原理箱式炉石墨化技术是一种将固体碳原料如煤、焦炭、木炭等加热至高温下,使其结构发生变化,生成石墨的技术。
其原理如下:1. 加热:将固体碳原料放入箱式炉中,通过供热装置加热至高温(通常超过2000℃)。
2. 碳原料反应:在高温下,碳原料开始发生化学反应,碳原子之间的键破裂并重新组合,形成结晶形态的石墨。
3. 结晶形态:石墨是由六方晶系的层状结构组成,每一层由碳原子通过共价键相连。
在箱式炉中,由于高温和适宜的反应条件,碳原料逐渐转变为石墨结构。
4. 冷却:石墨形成后,将其从高温环境中取出,并进行冷却。
在冷却的过程中,石墨分子开始重新排列和结晶,形成块状石墨。
5. 石墨提纯:从冷却后的块状石墨中,可以进行进一步的提纯工艺,以去除其中的杂质和气体,得到纯度更高的石墨产品。
总之,箱式炉石墨化技术通过高温加热碳原料,使其发生结构变化,生成石墨。
其过程中,碳原料经历碳原子键的破裂和重新组合,形成结晶形态的石墨,并通过冷却和提纯工艺得到纯度更高的石墨产品。
箱式炉石墨化技术还可以进一步细分为两种主要类型:高温石墨化和超高温石墨化。
1. 高温石墨化:高温石墨化技术通常在1500℃到3000℃的温度范围内进行。
在高温环境下,碳原料发生结构变化,形成石墨。
这种技术适用于冶金、电力、化工等行业,用于生产高纯度石墨、石墨电极、石墨粉等产品。
2. 超高温石墨化:超高温石墨化技术在3000℃以上的超高温环境下进行。
超高温可以加速碳原料的结构变化和石墨化过程,从而获得高品质的石墨产品。
这种技术适用于航空航天、核能等高端领域,用于制造石墨陶瓷、石墨碳化物等高性能材料。
箱式炉石墨化技术具有以下优点:1. 温度控制精准:箱式炉设备通常配备先进的温度控制系统,能够精确控制炉膛温度,保证石墨化过程的稳定性和高品质。
2. 环境友好:箱式炉石墨化技术采用封闭式加热环境,减少了碳原料的氧化和损失,同时也减少了环境污染。
3. 生产效率高:箱式炉设备结构简单,易于维护和操作。
提高加热炉热效率的两项技改措施

二 、技改措施
11 耐火纤维喷涂的应用
当前 ,耐火纤维以其密度低 、导热系数小 、热稳定性好 、抗热
振性强等优良特性 ,已广泛应用于冶金 、石油 、化工 、机械 、电子 、
建筑 、轻工等行业 ,是耐火 、保温 、隔热 、隔音 、防火的优选材料 。
目前 ,国内耐火纤维的应用是将其二次制品 ,如毡 、毯 、预制
能涂料 ,是近几年应用较广的一种新型节能材料 ,其主要成分见
表 3 。可应用于加热炉炉窑内衬耐火砖和耐火纤维隔热材料的
表面上 ,具有抗热振和抗剥落 、增强炉壁抗气流冲刷性能 ,和延
长炉衬寿命 、提高热效率 、降低单位产品能耗的特性及作用 。其
主要技术指标见表 4 。
表 3 涂料组分 (按重量计)
%
从表 6 中可以看出 ,喷涂 HT - 1 涂料后 ,在处理量 、加热介 质相同的情况下 ,炉膛平均温度下降了 20 ℃,从而降低了燃料 消耗 ,达到了节能目的 。另外 ,从喷涂前后的平均单耗也可以看 出其节能效果 ,见表 7 。根据表 7 可知月平均单耗由 29187kg(标 油)Πt 下降到 28184kg(标油)Πt ,下降了 1103kg (标油)Πt ,下降幅度 为 314 %。如果装置处理量按 80 万 tΠa 考虑 (因有二台炉子并联 运行 ,故单台炉子的处理量为 40 万 tΠa) ,燃料价格按 400 元Πt 计 算 ,这台炉子每年可节约 16148 万元 ,减去 51544 万元的投资 ,一 年可产生 101936 万元的经济效益 ,相当可观 。
量 ,炉膛中氧含量从
炉墙外壁检测点 温度 ℃
12 %降至目前的6 %以
破损处
200
下 ,炉膛明亮 ,燃烧情况 改造前
最高处
高产汽率副产蒸汽石墨二合一合成炉的应用与改进

。
一 业的发展 。其后五十年代法国更将 HC1合成一 冷却一 8月在滨化一次点火成功 ,11小时蒸汽压 力 O.3MPa,
# I
吸收三台设备合并成一台设备 (我 国称三合一炉 ), 考核时 到 0.5MPa,后 因现场需 要改 副产热 水 ,该 炉
更大大精减 了流程 ,而且可以不输入吸收水 ,仅完成 是 由石 墨炉筒上的石墨换热块 段取热副产蒸汽 ,为国
但 实际生 产 中因合 成气 中所 含水份 冷凝 并生 成盐 酸 蒸汽三合一炉 ,由下段钢 管炉筒段取热副产蒸汽 ,可
后会 腐蚀钢炉筒 使寿 命减短 ,因而 1942年美 国开发 产 出 0.8~ 1.5MPa蒸 汽 。国产首 台副 产蒸汽 二 合一
了耐 盐酸 卓越 的石 墨 HC1合成 炉后 ,促进 了盐酸 工 炉 (下点 火炉 )由 山剑石 墨公 司设 、制 ,于 2002年
< 0.5MPa的水 蒸汽 ,不但 实现 了余热 回收利用 ,而 容易被 冷凝酸 腐蚀 ,故使用寿命普 遍偏短 ;
且节省 了冷 却水 的消耗。其后 德 国 SGL公司开发 了
(2)采用下 点火 结构时 ,除 山剑开发 的二合一
石墨冷却换热块在上 ,石墨 合成炉 筒在 下的下点火二 炉外 ,其余在合成炉筒上的石墨换热块 ,都在 中心部
锄 籀 赢 ≮瀚 漱 黪 辐 赫 赫 镳
赫 嘲 黪 蕊 蠢 褥 臻 套 沌 懑
搬
}
0
}
}
附表 典 型两段 取热 副产蒸汽二合一炉截 面产 能、产 汽 率
力 。也欢迎需要此压力蒸汽的用户与我们共同开发 ; (2) 已研 发 了可 副 产 两 个压 力级 别 蒸 汽 (如
艾奇逊石墨化炉的节能
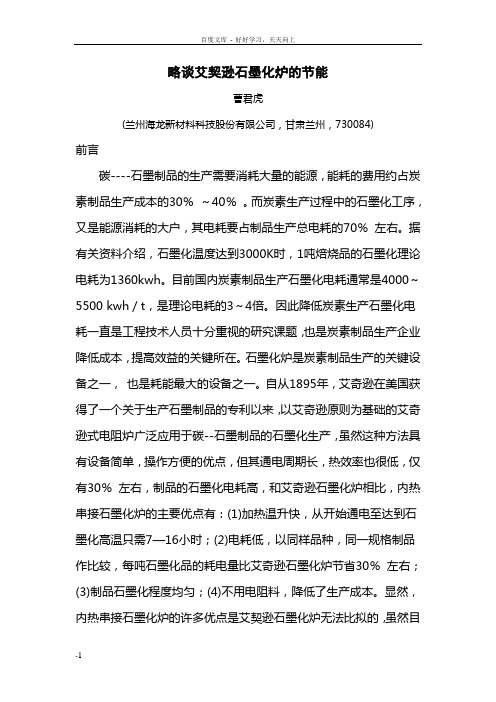
略谈艾契逊石墨化炉的节能曹君虎(兰州海龙新材料科技股份有限公司,甘肃兰州,730084)前言碳----石墨制品的生产需要消耗大量的能源,能耗的费用约占炭素制品生产成本的30%~40%。
而炭素生产过程中的石墨化工序,又是能源消耗的大户,其电耗要占制品生产总电耗的70%左右。
据有关资料介绍,石墨化温度达到3000K时,1吨焙烧品的石墨化理论电耗为1360kwh。
目前国内炭素制品生产石墨化电耗通常是4000~5500 kwh/t,是理论电耗的3~4倍。
因此降低炭素生产石墨化电耗一直是工程技术人员十分重视的研究课题,也是炭素制品生产企业降低成本,提高效益的关键所在。
石墨化炉是炭素制品生产的关键设备之一,也是耗能最大的设备之一。
自从1895年,艾奇逊在美国获得了一个关于生产石墨制品的专利以来,以艾奇逊原则为基础的艾奇逊式电阻炉广泛应用于碳--石墨制品的石墨化生产,虽然这种方法具有设备简单,操作方便的优点,但其通电周期长,热效率也很低,仅有30%左右,制品的石墨化电耗高,和艾奇逊石墨化炉相比,内热串接石墨化炉的主要优点有:(1)加热温升快,从开始通电至达到石墨化高温只需7—16小时;(2)电耗低,以同样品种,同一规格制品作比较,每吨石墨化品的耗电量比艾奇逊石墨化炉节省30%左右;(3)制品石墨化程度均匀;(4)不用电阻料,降低了生产成本。
显然,内热串接石墨化炉的许多优点是艾契逊石墨化炉无法比拟的,虽然目前国内也有企业采用内热串接石墨化工艺生产碳一石墨制品,但内热串接石墨化炉现在还不能完全取代艾契逊石墨化炉,艾奇逊石墨化炉仍然是碳---石墨制品生产的主要热工设备之一。
因此,充分发挥艾奇逊石墨化炉的潜力,降低其石墨化生产过程中的能源消耗,对于炭素制品生产企业来说,也是降低生产成本,提高经济效益的有效手段之一。
1 艾奇逊石墨化炉的能量平衡由于奇契逊石墨化炉是现行炭素工业石墨化生产的主要炉型,弄清楚艾契逊石墨化炉的电热效率和能量平衡,对于碳一石墨制品的石墨化生产和石墨化炉的节能有着十分重要的作用。
石墨化炉窑的节能分析及措施
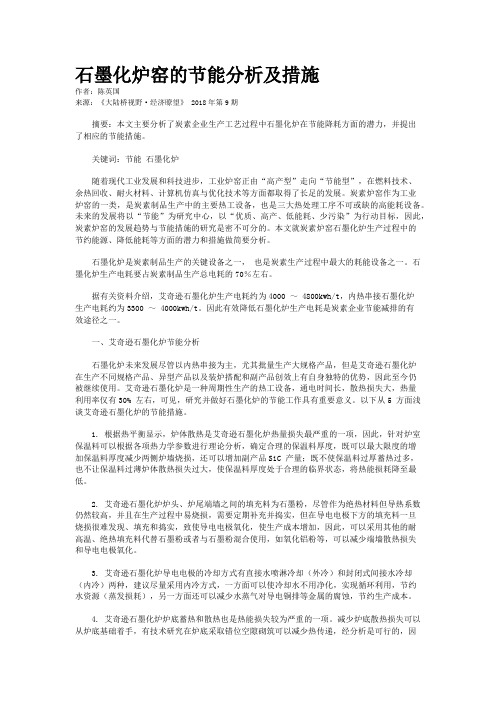
石墨化炉窑的节能分析及措施作者:陈英国来源:《大陆桥视野·经济瞭望》 2018年第9期摘要:本文主要分析了炭素企业生产工艺过程中石墨化炉在节能降耗方面的潜力,并提出了相应的节能措施。
关键词:节能石墨化炉随着现代工业发展和科技进步,工业炉窑正由“高产型”走向“节能型”,在燃料技术、余热回收、耐火材料、计算机仿真与优化技术等方面都取得了长足的发展。
炭素炉窑作为工业炉窑的一类,是炭素制品生产中的主要热工设备,也是三大热处理工序不可或缺的高能耗设备。
未来的发展将以“节能”为研究中心,以“优质、高产、低能耗、少污染”为行动目标,因此,炭素炉窑的发展趋势与节能措施的研究是密不可分的。
本文就炭素炉窑石墨化炉生产过程中的节约能源、降低能耗等方面的潜力和措施做简要分析。
石墨化炉是炭素制品生产的关键设备之一,也是炭素生产过程中最大的耗能设备之一。
石墨化炉生产电耗要占炭素制品生产总电耗的70%左右。
据有关资料介绍,艾奇逊石墨化炉生产电耗约为4000 ~ 4800kwh/t,内热串接石墨化炉生产电耗约为3300 ~ 4000kwh/t。
因此有效降低石墨化炉生产电耗是炭素企业节能减排的有效途径之一。
一、艾奇逊石墨化炉节能分析石墨化炉未来发展尽管以内热串接为主,尤其批量生产大规格产品,但是艾奇逊石墨化炉在生产不同规格产品、异型产品以及装炉搭配和副产品创效上有自身独特的优势,因此至今仍被继续使用。
艾奇逊石墨化炉是一种周期性生产的热工设备,通电时间长,散热损失大,热量利用率仅有30% 左右,可见,研究并做好石墨化炉的节能工作具有重要意义。
以下从5 方面浅谈艾奇逊石墨化炉的节能措施。
1. 根据热平衡显示,炉体散热是艾奇逊石墨化炉热量损失最严重的一项,因此,针对炉室保温料可以根据各项热力学参数进行理论分析,确定合理的保温料厚度,既可以最大限度的增加保温料厚度减少两侧炉墙烧损,还可以增加副产品SiC 产量;既不使保温料过厚蓄热过多,也不让保温料过薄炉体散热损失过大,使保温料厚度处于合理的临界状态,将热能损耗降至最低。
艾奇逊石墨化炉裂纹废品产生原因分析及改进措施

#$%&’( )*#+(,-.*/ 炭 素 技 术
01125 3 ・ !" 6789 04・
艾奇逊石墨化炉裂纹废品产生原因分析及改进措施
张向军
(晋能集团大同能源发展有限公司炭素分公司, 山西 大同 &)*&&%)
摘 要:主要介绍了大同能源发展有限公司炭素分公司针对 %&&+ 年艾奇逊石墨化炉发生的一系列裂纹废品事故所进行的有 关调查分析及采取的改进措施, 并以 %&&# 年的运行结果对所采取措施进行了验证。 关键词: 艾奇逊石墨化炉; 裂纹; 原因分析; 改进措施 中图分类号: ,-!%*. ! / ! 文献标识码: 0 (%&&$) 文章编号: !&&!1)*(! (+1&)
!
制定措施
针对调查发现的情况,攻关小组经过研究讨
论, 制定了如下措施并认真进行了实施: M 1 N 随时与变电站沟通,尽量保证送电过程的 前 (’ L 不停电;一旦发生送电过程的前 (’ L 停电 事件, 在恢复送电时, 根据停电时间的长短, 以合理
第%期
张向军
艾奇逊石墨化炉裂纹废品产生原因分析及改进措施
表$ 电阻率统计 $%%& 年焙烧品体积密度、 23456. *8389789:7 <;= =679783E:6 3EA A6E798C ;< I=3@L986 656:8=;A6 43>9EI @;AB:87 9E .’’& 品种规格 ! "" #$ ! %&’ #$ ! (’’ )$ ! %&’ )$ ! (&’ *)$ !%&’ *)$ !(’’ *)$ !(&’ *)$ !&’’ *)$ !&&’ +)$ !%&’ +)$ !(’’ +)$ !(&’ +)$ !&’’ +)$ !&&’ 体积密度 ! I・ :" O % 最高 1G -1G -1G /% 1G /% 1G /1G /1G /% 1G /% 1G /% 1G /& 1G /& 1G /( 1G /& 1G // 1G /最低 1G -% 1G -% 1G /’ 1G /’ 1G /% 1G /% 1G /’ 1G /1 1G /’ 1G /. 1G /. 1G /’ 1G /. 1G /% 1G /. 电阻率 ! !"・ " 最高 &’G && (,G ,(’G &. (%G /0 (%G &1 ((G .% (&G .1 (.G && (’G ’1 (.G -1 (’G 0, (&G .. (1G 0& (%G .% ((G %, 最低 (/G ’. (&G %( %-G 0, (’G 11 (’G ’1 %,G -0 (’G ’, %,G ,(.G %& (’G (( %,G 11 (%G ’1 (’G 1. (’G -& (1G %1
石墨化产能节能措施

石墨化产能节能措施引言石墨化材料是一种具有优异导电、导热和机械性能的特种材料,在众多领域中有广泛的应用。
然而,随着石墨化产能的增加,能源消耗和环境污染也日益严重。
因此,采取节能措施是十分必要的。
本文将讨论石墨化产能的节能措施。
1. 原材料优化利用石墨化的主要原材料是石墨矿石和焦炭。
在石墨化过程中,对原材料进行优化利用是节能的关键。
可以通过以下方式实现原材料的优化利用:•优选原材料:选择具有低杂质含量和高固定碳含量的石墨矿石和焦炭,以提高石墨化的效率。
•增加焦炭利用率:在石墨化过程中,控制焦炭的用量和燃烧方式,以提高焦炭的利用率,并降低能耗。
•粉煤气替代焦炭:考虑使用粉煤气替代部分焦炭,以减少对焦炭的需求,降低能源消耗。
2. 工艺优化对石墨化的工艺进行优化也是降低能耗的重要手段。
下面是一些常见的工艺优化措施:•控制石墨炉温度:合理控制石墨炉的温度,以提高石墨化反应的效率,并减少能源的浪费。
•减少石墨炉停机次数:通过优化石墨炉的操作和维护,减少因炉体损坏或故障导致的停机次数,提高产能利用率,降低能耗。
•循环利用废热:利用石墨炉产生的余热,进行废热回收,用于其他生产过程,以提高能源利用效率。
3. 节能设备的应用采用节能设备也是石墨化产能节能的重要手段。
以下是一些常见的节能设备的应用:•高效石墨炉:采用高效石墨炉可以提高石墨化反应的效率,减少能源的浪费。
•余热回收装置:通过安装余热回收装置,对石墨炉产生的余热进行回收利用,以减少能源的消耗。
•高效过滤装置:在石墨化过程中,采用高效过滤装置可以减少颗粒物的排放,降低环境污染,并提高设备的利用效率。
4. 人员培训和技术支持为了实施上述的节能措施,人员培训和技术支持也是必不可少的。
公司应该加强对员工的培训,使他们了解石墨化产能节能的重要性和具体操作方法。
此外,还可以与节能技术公司合作,获得相关技术的支持和指导。
结论石墨化产能的节能措施可以降低能源消耗,减少环境污染,并提高企业的经济效益。
锂电池负极石墨化炉技术现状与发展方向

锂电池负极石墨化炉技术现状与发展方向《锂电池负极石墨化炉技术现状与发展方向》摘要:锂电池作为一种重要的新能源电池,正逐渐取代传统的铅酸电池和镍氢电池,成为高能量密度和长循环寿命的理想选择。
石墨是锂电池负极材料的主要成分,而石墨的石墨化程度直接影响电池的性能。
因此,开发锂电池负极石墨化炉技术具有重大意义。
本文主要介绍了锂电池负极石墨化炉技术的现状和发展方向。
一、现状目前,锂电池负极石墨化炉技术主要分为高温石墨化法和化学还原法两种。
高温石墨化法通过在高温下将石墨形态从非结晶转变为结晶,实现石墨化过程。
化学还原法则是通过还原剂将石墨表面的氧化物还原,生成纯净的石墨材料。
高温石墨化法由于其高炉温、长炉期以及环境污染等问题,限制了其在工业中的应用。
而化学还原法由于操作简便、能耗低以及产能高等优势,在实际应用中得到了广泛推广。
二、发展方向为了满足锂电池市场的需求,锂电池负极石墨化炉技术需要在以下几个方面进行发展:1. 提高产能:目前锂电池市场需求急剧增长,加速生产和提高产能已经成为了关键。
石墨化炉技术需要研发高效、高产能的石墨化炉设备,以满足市场需求。
2. 降低能耗:锂电池负极石墨化炉技术在石墨化过程中需要消耗大量电能。
因此,降低能耗是石墨化炉技术发展的重要方向。
可以通过改进反应体系、优化操作流程和引入新型高效节能设备来实现能耗的降低。
3. 提高石墨化质量:石墨化质量是决定锂电池性能的关键因素之一。
石墨化炉技术需要进一步提高石墨化的均匀性和完整性,降低松散度,增强石墨颗粒的结晶度和导电性。
4. 提高设备自动化程度:锂电池负极石墨化炉技术需要进一步提高设备的自动化程度,降低人工干预,提高生产效率与质量的稳定性。
可以引入自动化装置和采用智能控制系统,实现设备的自动化操作和监控。
结论:锂电池负极石墨化炉技术作为锂电池生产的关键环节,其发展方向与现状紧密相关。
随着锂电池市场需求的增加,石墨化炉技术需要在提高产能、降低能耗、提高石墨化质量和提高设备自动化程度等方面不断创新发展,以满足市场需求,并为锂电池产业的持续发展做出贡献。
如何改善加热炉的操作以实现节能增效
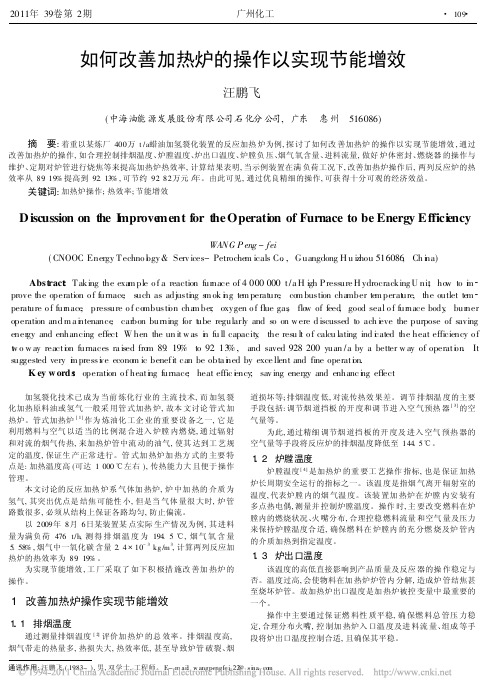
如何改善加热炉的操作以实现节能增效汪鹏飞(中海油能源发展股份有限公司石化分公司,广东 惠州 516086)摘 要:着重以某炼厂400万t /a 蜡油加氢裂化装置的反应加热炉为例,探讨了如何改善加热炉的操作以实现节能增效,通过改善加热炉的操作,如合理控制排烟温度、炉膛温度、炉出口温度、炉膛负压、烟气氧含量、进料流量,做好炉体密封、燃烧器的操作与维护、定期对炉管进行烧焦等来提高加热炉热效率,计算结果表明,当示例装置在满负荷工况下,改善加热炉操作后,两列反应炉的热效率从89.19%提高到92.13%,可节约92.82万元/年。
由此可见,通过优良精细的操作,可获得十分可观的经济效益。
关键词:加热炉操作;热效率;节能增效D iscussion on the I mprove ment for the Operati on of Furnace to be EnergyE ffici encyWANG P eng -fei(CNOOC Energy Techno l o gy &Serv ices-Petroche m icals Co .,Guangdong H u izhou 516086,Ch i n a)Abst ract :Taking the exa m ple o f a reaction fur nace of 4000000t/a H igh Pressure H ydrocracking U ni,t ho w to i mprove the operation o f furnace ,such as adjusti n g s m ok i n g te m perature ,co m bustion cha mber te m perat u re ,the outlet te m perature o f fur nace ,pressure o f co mbusti o n cha m ber ,oxygen o f flue gas ,flo w of feed ,good seal o f fur nace body ,bur ner operation and m a i n tenance ,car bon burning for t u be regularly and so on w ere d iscussed to ach i e ve the purpose of saving ener gy and enhancing effec.t W hen the un it w as i n fu ll capacity ,the resu lt o f calcu lating ind i c ated the heat efficiency o f t w o w ay reacti o n furnaces ra ised fro m 89.19%to 92.13%,and saved 928200yuan /a by a better w ay of operati o n .It suggested very i m pressi v e econo m ic benefit can be obta i n ed by exce llent and fine operati o n.K ey w ords :operation o f heati n g furnace ;heat effic i e ncy ;sav ing energy and enhanc i n g effect通讯作用:汪鹏飞(1983-),男,双学士,工程师。
电石矿热炉产能及产量提升设计方案与电极入炉插入深度控制措施及方法

电石矿热炉产能提升设计方案与电极入炉深度控制措施及方法一、电石矿热炉产能提升:XXX电石厂有12台电石炉,每台电石炉用三台单相变压器供电,单台变压器容量为9000KVA,共9000×3=27000KVA;总负荷为27000KVA×12=324000KVA。
电石炉用电由220KV两台主变供电,每台变压器接带6台电石炉负荷,每台主变压器额定38.5KV电压时负荷为180000KVA,两台变压器38.5KV电压时总负荷为360000KVA,35KV电压时为163800×2=327600KVA, 12台电石炉额定总需求负荷为27000KVA×12=324000KVA。
按照表1设计要求电石炉变压器制造时可超额定负荷20%长期运行,但是实际运行时,电石炉总负荷324000KVA超20%为388800KVA,已经超过变压器的额定负荷,显然主变压器设计时未考虑电石炉变压器设计负荷要求,在原设计中,电石炉总负荷限制在额定负荷324000KVA以下。
表1、主变分支回路的实际参数和目前的运行参数单台变压器额定负荷9000KVA(超额定负荷20%能长期运行),一次电流257A(相电流),角接运行时额定线电流为257×1.732=445A,三台电石炉满负荷电流为445×3=1335A,从上表中可以看出,分支电流报警值为1300A,额定电流为1350A。
三台电石炉满负荷运行时电流1335A大于供电分支设定报警值1300A,小于设计电流值1350A。
受供电设备额定负荷的影响,实际运行中,每台电石炉只能运行在27000KVA以下,考虑到电石炉操作电流引起的三相不平衡,电石炉负荷实际达不到额定的27000KVA。
主变的限制,已成为电石炉负荷提升的一个制约点;另外一点,电石炉变压器运行时功率因数0.95,档位达到3档甚至2档运行,变压器在负荷不超27000KVA,有功功率最高可提高到25650KW,这时,变压器已基本达到上限,这是制约电石炉负荷提升的另一个原因,两方面制约了电石炉负荷的进一步提升。
大型高电阻石墨化炉节能降碳关键技术及应用

大型高电阻石墨化炉节能降碳关键技术及应用下载提示:该文档是本店铺精心编制而成的,希望大家下载后,能够帮助大家解决实际问题。
文档下载后可定制修改,请根据实际需要进行调整和使用,谢谢!本店铺为大家提供各种类型的实用资料,如教育随笔、日记赏析、句子摘抄、古诗大全、经典美文、话题作文、工作总结、词语解析、文案摘录、其他资料等等,想了解不同资料格式和写法,敬请关注!Download tips: This document is carefully compiled by this editor. I hope that after you download it, it can help you solve practical problems. The document can be customized and modified after downloading, please adjust and use it according to actual needs, thank you! In addition, this shop provides you with various types of practical materials, such as educational essays, diary appreciation, sentence excerpts, ancient poems, classic articles, topic composition, work summary, word parsing, copy excerpts, other materials and so on, want to know different data formats and writing methods, please pay attention!1. 研究背景。
随着全球环保意识的不断提高,节能降碳已经成为了一个全球性的关注点。
石墨设备改造及目前生产状况分析和意见
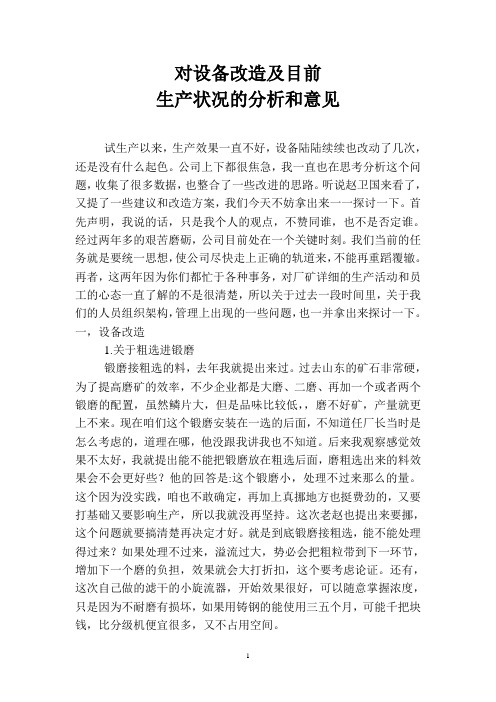
对设备改造及目前生产状况的分析和意见试生产以来,生产效果一直不好,设备陆陆续续也改动了几次,还是没有什么起色。
公司上下都很焦急,我一直也在思考分析这个问题,收集了很多数据,也整合了一些改进的思路。
听说赵卫国来看了,又提了一些建议和改造方案,我们今天不妨拿出来一一探讨一下。
首先声明,我说的话,只是我个人的观点,不赞同谁,也不是否定谁。
经过两年多的艰苦磨砺,公司目前处在一个关键时刻。
我们当前的任务就是要统一思想,使公司尽快走上正确的轨道来,不能再重蹈覆辙。
再者,这两年因为你们都忙于各种事务,对厂矿详细的生产活动和员工的心态一直了解的不是很清楚,所以关于过去一段时间里,关于我们的人员组织架构,管理上出现的一些问题,也一并拿出来探讨一下。
一,设备改造1.关于粗选进锻磨锻磨接粗选的料,去年我就提出来过。
过去山东的矿石非常硬,为了提高磨矿的效率,不少企业都是大磨、二磨、再加一个或者两个锻磨的配置,虽然鳞片大,但是品味比较低,,磨不好矿,产量就更上不来。
现在咱们这个锻磨安装在一选的后面,不知道任厂长当时是怎么考虑的,道理在哪,他没跟我讲我也不知道。
后来我观察感觉效果不太好,我就提出能不能把锻磨放在粗选后面,磨粗选出来的料效果会不会更好些?他的回答是:这个锻磨小,处理不过来那么的量。
这个因为没实践,咱也不敢确定,再加上真挪地方也挺费劲的,又要打基础又要影响生产,所以我就没再坚持。
这次老赵也提出来要挪,这个问题就要搞清楚再决定才好。
就是到底锻磨接粗选,能不能处理得过来?如果处理不过来,溢流过大,势必会把粗粒带到下一环节,增加下一个磨的负担,效果就会大打折扣,这个要考虑论证。
还有,这次自己做的滤干的小旋流器,开始效果很好,可以随意掌握浓度,只是因为不耐磨有损坏,如果用铸钢的能使用三五个月,可能千把块钱,比分级机便宜很多,又不占用空间。
2.关于二磨和尾沙跑粗我们知道,所有的球磨都是为了充分的磨矿解离,以便逐级提碳,提高回收率。
论炭素石墨化炉循环水系统节能设计
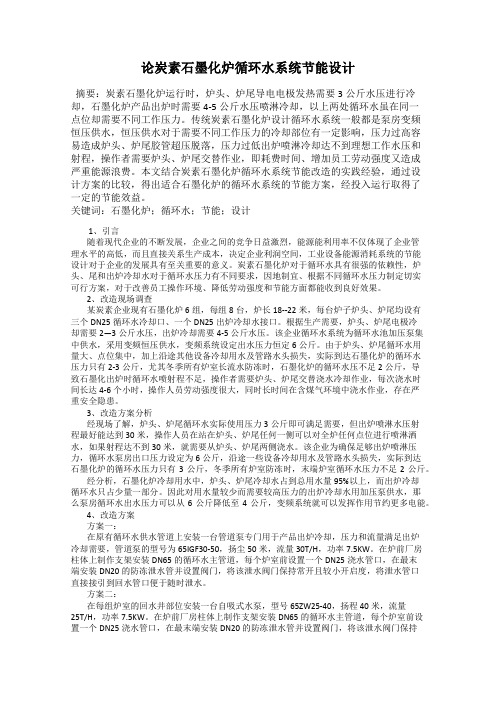
论炭素石墨化炉循环水系统节能设计摘要:炭素石墨化炉运行时,炉头、炉尾导电电极发热需要3公斤水压进行冷却,石墨化炉产品出炉时需要4-5公斤水压喷淋冷却,以上两处循环水虽在同一点位却需要不同工作压力。
传统炭素石墨化炉设计循环水系统一般都是泵房变频恒压供水,恒压供水对于需要不同工作压力的冷却部位有一定影响,压力过高容易造成炉头、炉尾胶管超压脱落,压力过低出炉喷淋冷却达不到理想工作水压和射程,操作者需要炉头、炉尾交替作业,即耗费时间、增加员工劳动强度又造成严重能源浪费。
本文结合炭素石墨化炉循环水系统节能改造的实践经验,通过设计方案的比较,得出适合石墨化炉的循环水系统的节能方案,经投入运行取得了一定的节能效益。
关键词:石墨化炉;循环水;节能;设计1、引言随着现代企业的不断发展,企业之间的竞争日益激烈,能源能利用率不仅体现了企业管理水平的高低,而且直接关系生产成本,决定企业利润空间,工业设备能源消耗系统的节能设计对于企业的发展具有至关重要的意义。
炭素石墨化炉对于循环水具有很强的依赖性,炉头、尾和出炉冷却水对于循环水压力有不同要求,因地制宜、根据不同循环水压力制定切实可行方案,对于改善员工操作环境、降低劳动强度和节能方面都能收到良好效果。
2、改造现场调查某炭素企业现有石墨化炉6组,每组8台,炉长18--22米,每台炉子炉头、炉尾均设有三个DN25循环水冷却口、一个DN25出炉冷却水接口。
根据生产需要,炉头、炉尾电极冷却需要2—3公斤水压,出炉冷却需要4-5公斤水压。
该企业循环水系统为循环水池加压泵集中供水,采用变频恒压供水,变频系统设定出水压力恒定6公斤。
由于炉头、炉尾循环水用量大、点位集中,加上沿途其他设备冷却用水及管路水头损失,实际到达石墨化炉的循环水压力只有2-3公斤,尤其冬季所有炉室长流水防冻时,石墨化炉的循环水压不足2公斤,导致石墨化出炉时循环水喷射程不足,操作者需要炉头、炉尾交替浇水冷却作业,每次浇水时间长达4-6个小时,操作人员劳动强度很大,同时长时间在含煤气环境中浇水作业,存在严重安全隐患。