12、13多头与蜗杆
第五讲蜗杆传动
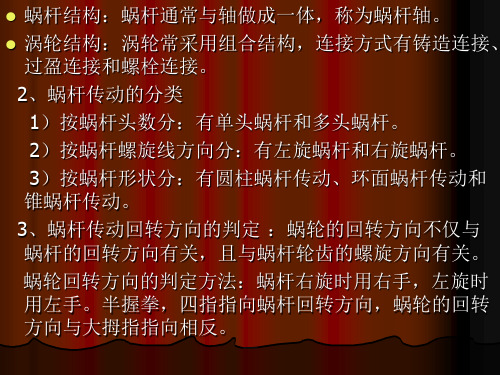
二、蜗杆传动的类型
根据蜗杆的形状可分为:圆柱蜗杆传动和环面蜗杆传动。圆柱 蜗杆按螺旋面形状的不同可分为渐开线蜗杆和阿基米德蜗杆。由 于阿基米德蜗杆加工方便,所以应用广泛。
三、蜗杆传动的特点和用途
1.传动比大。
i=10--40,最大可达80。 若只传递运动,传动比可达1000。
2.传动平稳、噪声小。 3.可制成具有自锁性的蜗杆。 4.效率较低。η=0.7——0.8。 5.蜗轮造价较高。
mt2、αt2分别为蜗轮的端面模数和端面压力角; γ为蜗杆的导程角; β为蜗轮的螺旋角。
2.蜗杆传动的失效形式 由于蜗轮材料的强度往往低于蜗杆材料的强度,
所以失效大多发生在蜗轮轮齿上。蜗杆传动的失效 形式有点蚀、胶合、磨损和折断。蜗杆传动在工作 时,齿面间相对滑动速度大,摩擦和发热严重,所 以主要失效形式为齿面胶合、磨损和齿面点蚀。实 践表明,在闭式传动中,蜗轮的失效形式主要是胶 合与点蚀;在开式传动中,失效形式主要是磨损; 当过载时,会发生轮齿折断现象。
1.蜗杆传动的基本参数 (1)模数和压力角 如图所示,在中间平面内,蜗杆和
蜗轮的啮合就相当于渐开线齿轮与齿条的啮合。为加工方
便,规定在中间平面内的几何参数应是标准值。所以,蜗
杆的轴向模数和蜗轮的端面模数应相等,并为标准值,分 别用mx1和mt2表示,即mx1=mt2=m。同时,蜗杆的压 力角αx1,等于蜗轮的端面压力角αt2,并为标准值,即 αx1=αt2=α=20°。
3).蜗杆头数、蜗轮齿数和传动比 一般推荐z1=1~4,最多为6。单头蜗杆容易切
削,导程角小,自锁性好,效率低。蜗杆头数越多, 加工越困难,分度误差越大。在传动中,蜗轮齿数 不宜过多,否则将使结构不紧凑。对于动力传动, 一般推荐z2=29~70,为了避免根切现象,取 z2≥27,通常蜗轮齿数按传动比来确定,z2=iz1。
机械基础第五章
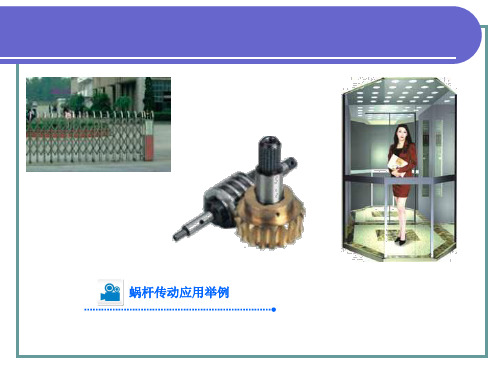
一、蜗杆传动的主要参数
1.模数m、齿形角α 2.蜗杆分度圆导程角γ 3.蜗杆分度圆直径d1和蜗杆直径系数q 4.蜗杆头数z1和蜗轮齿数z2
1.模数m、齿形角α
蜗杆的轴面模数mx1和蜗轮的端面模数mt2相等,且 为标准值。
蜗杆的轴面齿形角αx1和蜗轮的端面齿形角αt2相等, 且为标准值。
二、蜗杆传动的正确啮合条件
1.在中间平面内,蜗杆的轴面模数mx1和蜗轮的端 面模数mt2相等。即: mx1=mt2
2.在中间平面内,蜗杆的轴面齿形角αx1和蜗轮的 端面齿形角αt2相等。即:αx1=αt2
3.蜗杆分度圆导程角γ1和蜗轮分度圆柱面螺旋角β2 相等,且旋向一致。即:γ1=β2
§5-3 蜗杆传动的应用特点
件)。 2.蜗杆传动的类型和应用特点。 3.蜗轮回转方向的判定方法。 4.蜗轮蜗杆传动的主要参数:模数m、齿形角α、蜗杆
直径系数q、蜗杆导程角γ、蜗杆头数z1、蜗轮齿数z2及蜗轮 螺旋角β2。
5.蜗杆传动的正确啮合杆用左手,右 旋蜗杆用右手,用四指弯 曲表示蜗杆的回转方向, 拇指伸直代表蜗杆轴线, 则拇指所指方向的相反方 向即为蜗轮上啮合点的线 速度方向。
§5-2 蜗杆传动的主要参数和啮合条件
在蜗杆传动中,其几何参数及尺寸计算均 以中间平面为准。通过蜗杆轴线并与蜗轮轴线 垂直的平面称为中间平面。
按蜗杆形状
圆柱蜗杆传动 环面蜗杆传动 锥蜗杆传动
按蜗杆螺旋线方向
左旋蜗杆 右旋蜗杆
按蜗杆头数
单头蜗杆 多头蜗杆
三、蜗轮回转方向的判定
1.判断蜗杆或蜗轮的旋向
右手法则:
手心对着自己,四指顺 着蜗杆或蜗轮轴线方向摆正, 若齿向与右手拇指指向一致, 则该蜗杆或蜗轮为右旋,反 之则为左旋。
多头螺纹和多头蜗杆

2020年12月9日星期三
多头螺纹和多头蜗杆
3.车削多头蜗杆的步骤
1)粗车
粗车主要作用是车出梯形槽,以去除大量余量,有以下两种 方法。
(1)是利用小滑板刻度分线并车削.具体可考虑参 考双线梯形螺纹分线Байду номын сангаас方法;
(2)是将小滑板对零位.然后按多头蜗杆的齿距进 行分线,同时用三角螺纹车刀在蜗杆外圆上刻出 粗车时齿顶宽(Sa按0.843ms+0.5m掌握),以蜗 杆粗车刀在齿槽的刻线范围进行左右车削(不能 超越齿顶宽刻线)。粗车时,为防止切屑黏附在 车刀上或形成积屑瘤,可采用30#机油加适量红丹 粉作切削液.进行冷润滑。
2020年12月9日星期三
多头螺纹和多头蜗杆
3)削过程中开合螺母抬起。 预防方法: (1)在工件上先车出一条很浅的螺旋线,测量螺距
(周节)是否正确; (2)调整好主轴和丝杆的轴向窜动量,开全螺母间隙; (3)将溜板箱手轮拉出出使之与传动轴脱开或加装平
衡块使之平衡; (4)用重物挂在开合螺母手柄上防止其中途抬起。
(3)用百分表和量块确定小滑板的移动量,如图8-26, 这种方法分线的精度较高,也适宜加工导程较大的多 线螺纹,在车削过程中应经常找正百分表的零位。
2020年12月9日星期三
多头螺纹和多头蜗杆
图8-25 用百分表进行分线
图8-26 用百分表和量线进行分线 1-挡板;2-量块;3百分表
2020年12月9日星期三
2020年12月9日星期三
多头螺纹和多头蜗杆
预防方法: (1)用高速钢车刀切削时,应降低切削速度,并加切
削液; (2)增加刀杆截面积,并减小伸出长度; (3)减小车刀纵向前角,调整中滑板丝杆螺母间隙; (4)高速切削螺纹时,最后一刀的切削厚度,一般要
蜗杆传动是用来传递空间交错轴之间的运动和动力最常用
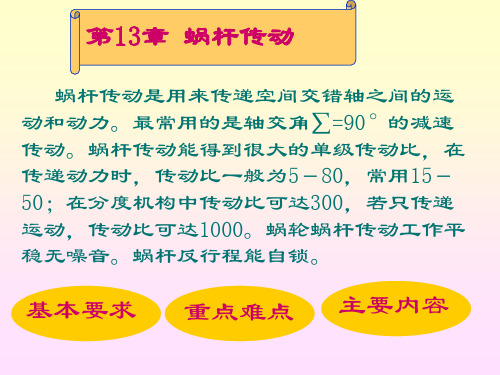
Fn2
Ft2
coscosn
13.5.2 效率
123
式中 1 啮合效率;
2-油的搅动和 时飞 的溅 效损 2率 0耗 ; .99
3-轴承 ;3效 0.98 ~ 率 0.99
主要影响因素:啮合效率
1
tan tan(v)
蜗杆主动
1
tan(v) tan
蜗轮主动
啮合效率的主要影响因素:
(1)当量摩 v;(2 擦 )导角 程 角
式中 I-蜗杆轴中间截面的惯性矩 L—两支承间距离;
I d14
64
[]许用最大挠度;杆淬取 0火 .00蜗 m 4,
调质蜗0.杆 01m取 ,m-模数;
13.8 温度计算
13.8.1 润滑油工作温度
闭式传动需进行温度计算
温度计算的原因:
效率低→产生较多热量→寿命降低,甚至胶合
到达热平衡时: 1P 0 1 ( 1 0 ) w 0 A ( t 1 t 0 )
1)变位的主要目的是配凑中心距和凑传 动比,使之符合标准或推荐值。 2)为保持加工蜗轮时的滚刀尺寸不变, 蜗杆是不变位的。 3) 当配凑中心距时:齿数不变,正变位 x2=(a'-a)/m; 凑传动比:中心距不变,齿数变化, x=1/2(z2-z2/)
正确啮合条件:
mx1 mt2 m
x1 t2 2,旋向相同
[F]
[F]SFFmlimin
(13.24)
SFmi n1.4
13.7 蜗杆轴挠度计算
必要性:
蜗杆轴啮合部位受力后→轴产生挠曲→影响啮
合→局部偏载、干涉
,
蜗杆轴挠曲
主要由圆周力和径向力造成的,轴向力可以忽略
不计。
挠度计算:设轴为自由支承
蜗杆传动

蜗杆传动蜗杆传动由蜗杆和蜗轮组成,一般蜗杆为主动件。
蜗杆和螺纹一样有右旋和左旋之分蜗杆传动,分别称为右旋蜗杆和左旋蜗杆。
蜗杆上只有一条螺旋线的称为单头蜗杆,即蜗杆转一周,蜗轮转过一齿,若蜗杆上有两条螺旋线,就称为双头蜗杆,即蜗杆转一周,蜗轮转过两个齿。
由蜗杆与蜗轮互相啮合组成的交错轴间的齿轮传动(图1)。
通常两轴的交错角为90°。
一般蜗杆为主动件,蜗轮为从动件。
蜗杆传动的传动比大,工作平稳,噪声小,结构紧凑,可以实现自锁。
但一般的蜗杆传动效率较低,蜗轮常须用较贵的有色金属(如青铜)制造。
蜗杆传动广泛用于分度机构和中小功率的传动系统。
单级蜗杆传动的传动比常用 8~80。
在分度机构或手动机构中蜗杆传动的传动比可达300,用于传递运动时可达到1500。
蜗杆传动-类型蜗杆传动有多种类型,如表所示。
蜗杆传动圆柱蜗杆传动是蜗杆分度曲面为圆柱面的蜗杆传动。
其中常用的有阿基米德圆柱蜗杆传动和圆弧齿圆柱蜗杆传动(图2)。
①阿基米德蜗杆的端面齿廓为阿基米德螺旋线,其轴面齿廓为直线。
阿基米德蜗杆可以在车床上用梯形车刀加工,所以制造简单,但难以磨削,故精度不高。
在阿基米德圆柱蜗杆传动中,蜗杆与蜗轮齿面的接触线与相对滑动速度之间的夹角很小,不易形成润滑油膜,故承载能力较低。
②弧齿圆柱蜗杆传动是一种蜗杆轴面(或法面)齿廓为凹圆弧和蜗轮齿廓为凸圆弧的蜗杆传动。
在这种传动中,接触线与相对滑动速度之间的夹角较大,故易于形成润滑油膜,而且凸凹齿廓相啮合,接触线上齿廓当量曲率半径较大,接触应力较低,因而其承载能力和效率均较其他圆柱蜗杆传动为高。
蜗杆传动-主要参数各类圆柱蜗杆传动的参数和几何尺寸基本相同。
图3为阿基米德圆柱蜗杆传动的主要参数。
通过蜗杆轴线并垂直于蜗轮轴线的平面,称为中间平面。
在中间平面上,蜗杆的齿廓为直线,蜗轮的齿廓为渐开线,蜗杆和蜗轮的啮合相当于齿条和渐开线齿轮的啮合。
因此,蜗杆传动的参数和几何尺寸计算大致与齿轮传动相同,并且在设计和制造中皆以中间平面上的参数和尺寸为基准。
9.2多线螺纹和多线蜗杆的分线方法

概念 分线:
多线螺纹(蜗杆)的各螺旋槽在轴向是等距离分布的,在端面上螺旋线 的起点是等角分布的,而进行等距分布(或等角度分布)的操作叫分线。
多线螺纹(蜗杆)与单线的不同之处 :
车多线螺纹(蜗杆)与车单线螺纹(蜗杆)的不同之处是:按导程计算 交换齿轮,按螺纹(蜗杆)线数分线。
利用交换齿轮分线:当车床交换齿轮Z的齿数是螺纹线数(或蜗杆头数) 的整数倍时,就可以在交换齿轮上进行分线。
圆周分线法
例: 车削三头蜗ຫໍສະໝຸດ ,可按以下步骤进行: 车好第一条螺旋后,停机,在交换齿轮Z1上用粉笔做好三等分(设主轴 到Z1的传动比为1)记号1、2、3。随后把Z2齿轮与 Z1齿轮脱开,用手 转动卡盘,使记号2的一个齿转到原来3的位置上,并与 Z2记号4处啮合, 就可以车削第二条螺旋槽。第三条螺旋槽用同样方法进行。 用交换齿轮分线的优点是分线精度高,但比较麻烦。
解:
轴向分线法
利用百分表和量块分线
把百分表固定在刀架上,并在床鞍上装一固定挡块。当车第一条螺旋槽 时,在挡块与百分表之间放入厚度等于两倍轴向齿距(2p )的量块,并 移动小滑板,使百分表触头接触量块,并调整百分表指针至零位,当车 好第一条螺旋槽后,调一块厚度为一个轴向齿距p的量块,移动小滑板, 使百分表触头接触量块至指针零位,即可车削第二条螺旋槽。
圆周分线法
当车好第一条螺旋槽后,使工件与滑板之间的传动链分离,并 把工件转过α=360 /n角度,再接通传动链车另一条螺旋槽的方 法,称为圆周分线法。
利用卡盘卡爪分线:当工件在两顶尖装夹时,可用四爪单动卡盘或三爪 自定心卡盘的卡爪对二、三、四头的蜗杆或螺纹进行分线。分线时只需 要把顶尖松开,把工件连同夹头转动一个角度,由卡盘上另一卡爪拨动, 顶好顶尖后,即可车削另一条螺旋槽。 这种分线方法较简单,但精度不高,适用于齿面还需磨削的多线螺纹 (蜗杆)。
《机械设计基础》第12章 蜗杆传动

3、摩擦磨损问题突出,磨损是主要 的失效形式。为了减摩耐磨,蜗轮齿圈常需用青铜制造,成本较高;
4、传动效率低,具有自锁性时,效率低于50%。
由于上述特点,蜗杆传动主要用于传递运动,而在动力传输中的应用受到限制。
其齿面一般是在车床上用直线刀刃的 车刀切制而成,车刀安装位置不同, 加工出的蜗杆齿面的齿廓形状不同。
γ
β
γ=β (蜗轮、蜗杆同旋向)
一、蜗杆传动的主要参数及其选择
1、模数m和压力角α
§12-2 蜗杆传动的参数分析及几何计算
ma1= mt2= m αa1=αt2 =α=20°
在蜗杆蜗轮传动中,规定中间平面上的模数和压力角为标准值,即:
模数m按表12-1选取,压力角取α=20° (ZA型αa=20º;ZI型αn=20º) 。
阿基米德蜗杆(ZA蜗杆) 渐开线蜗杆(ZI蜗杆)
圆柱蜗杆传动
环面蜗杆传动
锥蜗杆传动
其蜗杆体在轴向的外形是以凹弧面为母线所形成的旋转曲面,这种蜗杆同时啮合齿数多,传动平稳;齿面利于润滑油膜形成,传动效率较高。
同时啮合齿数多,重合度大;传动比范围大(10~360);承载能力和效率较高。
三、分类
在轴剖面上齿廓为直线,在垂直于蜗 杆轴线的截面上为阿基米德螺旋线。
§12-5 圆柱蜗杆传动的强度计算
一、蜗轮齿面接触疲劳强度的计算
1、校核公式:
2、设计公式:
式中:a—中心距,mm;T2 —作用在蜗轮上的转矩,T2 = T1 iη; zE—材料综合弹性系数,钢与铸锡青铜配对时,取zE=150;钢与铝青铜或灰铸铁配对时, 取zE=160。 zρ—接触系数,由d1/a查图12-11,一般d1/a=0.3~0.5。取小值时,导程角大,故效率高,但蜗杆刚性较小。 kA —使用系数,kA =1.1~1.4。有冲击载荷、环境温度高(t>35oC)、速度较高时,取大值。
圆柱蜗杆传动主要参数及几何计算
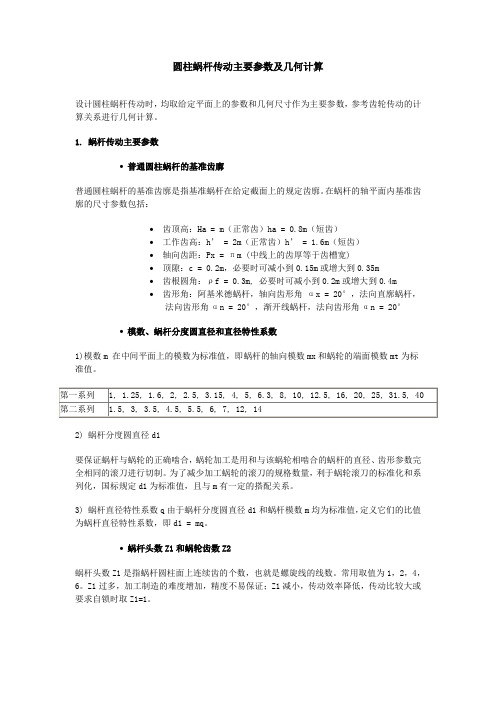
圆柱蜗杆传动主要参数及几何计算设计圆柱蜗杆传动时,均取给定平面上的参数和几何尺寸作为主要参数,参考齿轮传动的计算关系进行几何计算。
1. 蜗杆传动主要参数∙普通圆柱蜗杆的基准齿廓普通圆柱蜗杆的基准齿廓是指基准蜗杆在给定截面上的规定齿廓。
在蜗杆的轴平面内基准齿廓的尺寸参数包括:∙齿顶高:Ha = m(正常齿)ha = 0.8m(短齿)∙工作齿高:h’ = 2m(正常齿)h’ = 1.6m(短齿)∙轴向齿距:Px = πm (中线上的齿厚等于齿槽宽)∙顶隙:c = 0.2m,必要时可减小到0.15m或增大到0.35m∙齿根圆角:ρf = 0.3m, 必要时可减小到0.2m或增大到0.4m∙齿形角:阿基米德蜗杆,轴向齿形角αx = 20°,法向直廓蜗杆,法向齿形角αn = 20°,渐开线蜗杆,法向齿形角αn = 20°∙模数、蜗杆分度圆直径和直径特性系数1)模数m 在中间平面上的模数为标准值,即蜗杆的轴向模数mx和蜗轮的端面模数mt为标准值。
2) 蜗杆分度圆直径d1要保证蜗杆与蜗轮的正确啮合,蜗轮加工是用和与该蜗轮相啮合的蜗杆的直径、齿形参数完全相同的滚刀进行切制。
为了减少加工蜗轮的滚刀的规格数量,利于蜗轮滚刀的标准化和系列化,国标规定d1为标准值,且与m有一定的搭配关系。
3) 蜗杆直径特性系数q由于蜗杆分度圆直径d1和蜗杆模数m均为标准值,定义它们的比值为蜗杆直径特性系数,即d1 = mq。
∙蜗杆头数Z1和蜗轮齿数Z2蜗杆头数Z1是指蜗杆圆柱面上连续齿的个数,也就是螺旋线的线数。
常用取值为1,2,4,6。
Z1过多,加工制造的难度增加,精度不易保证;Z1减小,传动效率降低,传动比较大或要求自锁时取Z1=1。
蜗轮齿数Z2根据传动比i和Z1确定。
Z2 = i Z1。
为避免蜗轮轮齿发生根切和保证传动的平稳性,一般取蜗轮齿数Z2>27;同时为避免结构尺寸一定时,模数过小而导致弯曲强度不足或模数一定时,蜗轮直径过大而导致蜗杆轴支撑跨距过大从而刚度降低,蜗轮齿数也不宜过大,一般取Z2<80。
多头蜗杆工艺分析及快捷车削法
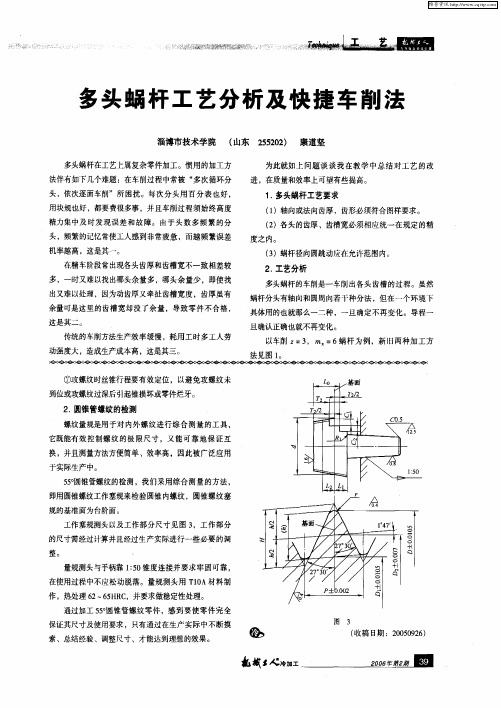
疆 礴 0
一
多头蜗 杆 工 艺分 析及 快 捷 车 削 法
淄博市技术学院 ( 山东 250 ) 康道坚 52 2
多头蜗杆在工艺上属复杂零件加工。惯用的加工方 法伴有如下几个难题:在车削过程中常被 “ 多次循环分 头, 依次逐面车削”所困扰。每次分头用百分表也好, 用块规也好 , 都要费很多事, 并且车削过程须始终高度 精力集中及时发现误差和故障。由于头数多频繁的分 头,频繁的记忆常使工人感到非常疲惫,而越频繁误差 为此就如上问题谈谈我在教学 中总结对工艺的改 进, 在质量和效率上可望有些提高。
1 多头蜗杆工艺要求 .
()轴向或法向齿厚 , 1 齿形必须符合图样要求。 ()各头的齿厚 、 2 齿槽宽必须相应统一在规定的精
度 之内。
机率越高, 这是其一。
在精车阶段常出现各头齿厚和齿槽宽不一致相差较
()蜗杆径向圆跳动应在允许范围内。 3
2 工艺分析 .
多头蜗杆的车削是一车削出各头齿槽的过程。虽然 蜗杆分头有轴向和圆周向若干种分法,但在一个环境下 具体用的也就那么一二种 ,一旦确定不再变化。导程一 旦确认正确也就不再变化。 以车削 =3 蜗杆为例,新旧两种加工方 ,m =6 法见图 1 。
2圆 . 锥管螺纹的检测
螺纹量规是用于对内外螺纹进行综合测量的工具, 它既能有效控制螺纹的极限尺寸,又能可靠地保证互
换, 并且测量方法方便简单、效率高,因此被广泛应用
于实 际生产 中。
5o 5圆锥管螺纹的检测, 我们采用综合测量的方法, 即用圆锥螺纹工作塞规来检验圆锥内螺纹,圆锥螺纹塞 规的基准面为台阶面。 工作塞规测头以及工作部分尺寸见图 3 ,工作部分 的尺寸需经过计算并且经过生产实际进行一些必要的调
机械设计--12 蜗杆传动
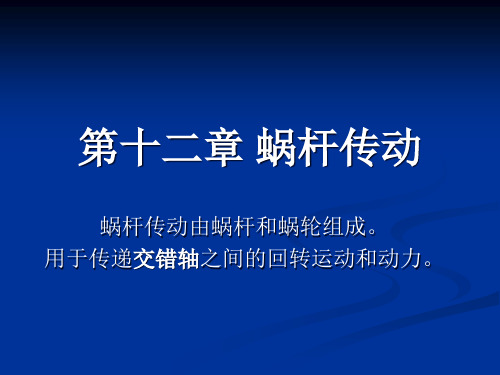
m
1
1.25
1.6
2
mm
d1
18
mm
20 20.4 20 28 (18)
31.25 35 51.2 72 89.6 112
71.68
142
m
2.5
3.15
4
mm
d1 (22.4) 28 (28) 35.5 (45) 56 mm (35.5) 45
度增加,导致蜗杆刚度降低,影响啮合精度。) 传动比:
蜗杆头数与蜗轮齿数的荐用值
传动比 i 蜗杆头数z1 蜗轮齿数z2
7~13 4
28~52
14~27 2
28~54
28~40 >40 2、1 1 28~80 >40
3 、蜗杆直径系数q和导程角γ
蜗杆的分度圆直径以d1表示。 蜗轮分度圆直径以d2表示。 蜗杆直径系数q :是蜗杆分度圆直径与模数的比值,
三、蜗杆的刚度计算
蜗杆在圆周力和径向力的作用下产生的挠度分别为:
Yt1
Ft1l 3 48EI
Yr1
Fr1l 3 48EI
总挠度为:
E---材料弹性模量;对钢E=2.06×105 MPa; I---危险截面惯性矩,I=(πd14)/64 ; L---蜗杆支点跨距,初算取l=0.9d2 ; [Y]=d1/1000
5、可以实现自锁; '
6、传动效率低,通常为70%~80%,成本较高。
12.1.2 蜗杆传动的类型
一、根据蜗杆形状的不同,蜗杆传动分为: 圆柱蜗杆传动; 环面蜗杆传动; 锥蜗杆传动三大类。
圆柱、环面及锥蜗杆传动
圆柱蜗杆传动
环面蜗杆传动
锥蜗杆传动
二、普通圆柱蜗杆{根据刀具加工位置的不 同,即垂直于蜗杆轴线的剖面(横截面)的 齿廓形状的不同}按螺旋面的形状分为:
蜗杆传动

第8章蜗杆传动(书13)本章主要学习阿基米德圆柱蜗杆传动的设计。
掌握阿基米德圆柱蜗杆传动的基本参数的意义及选择、受力分析和效率计算、蜗杆传动的失效形式、强度计算、温度计算;了解蜗杆传动的蜗杆轴挠度计算、润滑油粘度及润滑方式的选择,了解提高圆柱蜗杆传动承载能力的措施、蜗杆传动的分类、特点、应用、精度选择以及蜗杆和蜗轮的结构。
一、知识点分析:按蜗杆头数分:单头、多头(双头、四头等);按旋向分:左旋、右旋。
2、蜗杆的旋向与蜗轮的旋向一致。
3、单头蜗杆主要应用于传动比较大、功率小的场合,要求自锁的传动必须采用单头蜗杆;多头蜗杆主要用于传动比不大、功率较大、要求效率较高的场合。
4、阿基米德蜗杆(ZA)和蜗轮在中间平面上是直齿条和渐开线齿轮的啮合,端面齿廓是阿基米德螺线;渐开线蜗杆(ZI)的端面齿廓是渐开线,与基圆柱相切的截面,齿廓是直线。
5、蜗杆传动的正确啮合条件是:m x1=m t2=m;αx1=αt2;γ=β2(旋向相同)6、与齿轮传动相比,蜗杆传动的失效形式有以下异同特点:与齿轮传动相似,有点蚀、胶合、磨损、轮齿折断等;但蜗杆传动更易产生磨损和胶合,一般情况下,失效总是发生在蜗轮轮齿上。
7、啮合效率的主要影响因素:(1)、当量摩擦角:与蜗杆副的材料、表面润滑状况、润滑油的种类、啮合角、滑动速度v s有关。
(2)、导程角:z1越大,导程角越大,啮合效率越高;z1越小,导程角越小,效率越低。
此外:还有滑动速度v s、表面粗糙度、润滑油粘度等,其中导程角的大小起主导作用。
8、闭式蜗杆传动要进行温度计算是为了防止蜗杆传动发生胶合失效。
9、进行蜗杆传动的温度计算时,如果温度不符合要求,可以采取以下措施:(1)、增大散热面积(采用散热筋);(2)、增大散热能力(蜗杆轴端装风扇、外冷却器冷却、内水管冷却)10、蜗杆传动的传动比不等于蜗轮、蜗杆分度圆直径之比。
11、蜗杆应首先采用硬面蜗杆。
12、蜗杆传动的基本参数及选择:二、思考题1、蜗杆传动有何优缺点(和齿轮传动比)?2、蜗杆传动是如何分类的?依据蜗杆的硬度、头数、旋向、加工蜗轮时刀具的加工位置各分为哪几种传动?3、对蜗轮的材料有何要求?常选哪几种?各有何特点?4、对蜗杆的材料有何要求?常选哪几种?各有何特点?5、加工ZA、ZI、ZN、ZC蜗轮时,刀具的加工位置如何?6、要求自锁的蜗杆传动为什么必须采用单头蜗杆?而传递较大功率时,又必须采用多头蜗杆?7、蜗杆传动的精度等级分几级?如何确定?8、蜗杆传动的参数:m、m n、α0、d1、q 、a、i12、z1、z2中,哪些应取标准值?哪些应取推荐值?哪些应取整数?哪些应取准确值?9、蜗杆传动的正确啮合条件是什么?10、与齿轮传动相比,蜗杆传动的失效形式有何特点?11、为什么说[d1/ a]是蜗杆传动的重要参数?12、评价蜗杆传动工作性能的指标有哪些?13、为什么说中心距a是蜗杆传动的最基本尺寸?14、滑动速度v s和哪些参数有关?15、蜗杆传动的啮合效率受哪些因素影响?主要影响因素是什么?为什么传动大功率时很少用蜗杆传动?16、为什么闭式蜗杆传动要进行温度计算?如果温度不符合要求,可以采取哪些措施?为什么?17、在蜗杆传动中,为什么只验算蜗轮的强度,而不验算蜗杆的强度?18、蜗杆传动变位的目的是什么?19、蜗杆传动的传动比是否等于蜗轮与蜗杆的分度圆直径之比?为什么?20、蜗杆轴系应如何固定?21、如何提高圆柱蜗杆传动的承载能力?三、作业与练习1、蜗杆传动的类型有哪些?各有何特点?3、为什么闭式蜗杆传动要进行温度计算?若温度计算不合要求时,应采取哪些措施?4、影响蜗杆传动效率的主要因素和参数有哪些?5、在蜗杆传动中,为什么只验算蜗轮的强度,而不验算蜗杆的强度?6、蜗杆传动变位的目的是什么?变位蜗杆传动中蜗杆、蜗轮的哪些尺寸发生了变化?哪些尺寸没有变化?为什么?7、蜗杆传动的传动比是否等于蜗轮、蜗杆分度圆直径之比?为什么?中,哪些应取标准值?哪些应取推荐值?为什么?8、蜗杆传动的参数:i,z,,,,a,zddm12219、与齿轮传动相比,蜗杆传动有何特点?常用于什么场合?10、为什么传递大功率时很少用蜗杆传动?11、若已知蜗杆传动要传递的功率、主动轮的转速和传动比,设计蜗杆传动时要确定哪些主要参数?12、蜗杆和蜗轮的螺旋角之间有什么关系?如何求得蜗杆的导程角?13、蜗杆传动的精度分几级?应如何选择?14、蜗杆传动的自锁条件是什么?是否可以靠其自锁性能,采用蜗杆传动作为实现电梯在各楼层停止的机构?为什么?正确的结构是什么?15、蜗杆传动用于增速的应用实例你是否见过或听到过?其效率应如何计算?16、蜗杆传动减速器中(两轴都处于水平位置),蜗杆在蜗轮的上面还是在下面?应如何选择?17、题17图所示的ZA型蜗杆传动装置中,蜗轮为主动件,蜗杆输出功率P=0.1KW,蜗轮转速n2=50r/min,蜗杆头数z1=2,蜗轮齿数z2=47,模数m=1.6mm,蜗杆分度圆直径d2=20mm,当量摩擦系数μV=0.07.要求计算:Array(1)、蜗杆导程角,当量摩擦角,此蜗杆传动能否自锁?(2)、蜗杆转向(标在图上).(3)、蜗轮受力的大小,方向(标在图上).(4)、传动效率,蜗轮输入功率.18、题18图所示,为一提升机构的传动示意图,重物G悬挂在钢丝绳上,钢丝绳绕在直径D=200mm的卷筒上,卷筒与蜗轮联接为一体,转动手柄可以提升重物G,G=20KN,斜齿圆柱齿轮的齿数z1=20,z2=60,m n=3,蜗杆头数z3=1,蜗轮齿数z4=60,蜗轮分度圆直径d4=240mm,蜗杆传动压力角α=20°,不变位,系统总效率η=0.35,蜗杆传动的效率η1=0.4。
蜗轮蜗杆轮系介绍

蜗轮的转向
2
v2
1
左右手法:
左旋左手,右旋右手,四指转
向1,拇指反向;即为v2。
课堂练习
1、右旋蜗杆转动,蜗轮如何动? 2、左旋蜗杆转动,蜗轮如何动? 3、蜗轮转动,右旋蜗杆如何动?
4、判断蜗杆旋向。
5、蜗轮转动,左旋蜗杆如何动? 6、判断蜗杆旋向。
5、蜗杆传动的特点:
1)传动比大,一般 i =10~80,最大可达1000;
一 轮系的类型
定义:由齿轮组成的传动系统-简称轮系 定轴轮系(轴线固定) 轮系分类 周转轮系(轴有公转) 复合轮系(两者混合)) 本节要解决的问题: 1.轮系传动比 i 的计算; 平面定轴轮系 空间定轴轮系 差动轮系
行星轮系
2.从动轮转向的判断。
知识链接
齿轮在轴上的固定方式
齿轮与轴之间的关系
固定(齿轮与轴固定为一体, 齿轮与轴一同转动,齿轮不能 沿轴向移动) 结构简图 单一齿轮 双联齿轮
蜗杆蜗轮传动
1、用于降速传递交错轴蜗杆有左旋、右旋之 分,蜗轮的旋向与配对的 蜗杆相同。
旋向判别:以轴心线为界, 螺旋线相对轴线往左上升 为左旋;往右上升为右旋。
蜗杆分左旋和右旋
蜗杆还有单头和多头之分
左 旋
右 旋
3、蜗杆传动比: i=n1/n2=z2/z1 4、回转方向的判定: 右旋右手、左旋左手。 四指指向蜗杆回转 方向,蜗轮的回转方向 与大拇指指向相反。
n 1 至 轮 k 间 所 有 从 动 轮 齿 数 的 连 乘 积 1 轮 i 1 k n 1 至 轮 k 间 所 有 主 动 轮 齿 数 的 连 乘 积 k 轮
惰轮(Z4)只改变齿轮副中从动轮回转方向,不影响齿轮副传动比大小的齿轮。
蜗轮蜗杆(常见普通)规格及尺寸

常见普通蜗轮蜗杆的规格及尺寸例:蜗杆传动,已知模数m=4.蜗杆头数z1=1,蜗轮齿数z2=50,特性系数q=10。
求传动中心距a=?0时:中心距a=(+蜗轮)/2=(特性系数q*m+蜗轮齿数Z2*模数m)/2=(10*4+50*4)/2=120特性系数:蜗杆的与模数的比值称为蜗杆特性系数。
加工蜗轮时,因为是直径和形状与蜗杆相同的滚刀来切制,由上式可看出,在同一下由于Z1和λ0的变化,将有很多不同的蜗杆直径,也就是说需要配备很多加工蜗轮的滚刀。
为了减少滚刀的数目,便于刀具标准化,不但要规定标准模数,同时还必须规定对应于一定模数的Z1/tgλ0值,这个值用q表示,称之为蜗杆特性系数。
圆柱蜗轮、蜗杆设计参数选择 蜗轮和蜗杆通常用于垂直交叉的两轴之间的传动(图1)。
蜗轮和蜗杆的齿向是螺旋形的,蜗轮的轮齿顶面常制成环面。
在蜗轮蜗杆传动中,蜗杆是主动件,蜗轮是从动件。
蜗杆轴向剖面类是梯形螺纹的轴向剖面,有单头和多头之分。
若为单头,则蜗杆转一圈蜗轮只转一个齿,因此可以得到较高速比。
计算速比(i )的公式如下:i=蜗杆转速n1蜗轮转速n2 =蜗轮齿数z2蜗杆头数z11、 蜗轮蜗杆主要参数与尺寸计算主要参数有:模数(m )、蜗杆分度圆直径(d1)、导程角(r )、中心距(a )、蜗杆头数(或线数z1)、蜗轮齿数(z2)等,根据上述参数可决定蜗杆与蜗轮的基本尺寸,其中z1、z2由传动要求选定。
(1) 模数m 为设计和加工方便,规定以蜗杆轴项目数mx 和蜗轮的断面模数mt 为标准模数。
对啮合的蜗轮蜗杆,其模数应相等,及标准模数m=mx=mt 。
标准模数可有表A 查的,需要注意的是,蜗轮蜗杆的标准模数值与齿轮的标准模数值并不相同。
表A 模数m 分度圆直径 d 1蜗杆直径系数 q 1.25 20 1622.4 17.921.6 20 12.5图1 图2(2) 蜗杆分度圆直径d1 再制造蜗轮时,最理想的是用尺寸、形状与蜗杆完全相同的蜗轮滚刀来进行切削加工。
蜗轮蜗杆传动

目,国家标准对每一标准模数规定了一定数目的标准蜗杆分度圆直径d1(参见 表12-1)。 直径d1与模数m的比值称为蜗杆的直径系数q。即:
1. 模数m和压力角α 中间平面:通过蜗杆轴线并与蜗轮轴线垂直的平面。
主平面
β1 γ=β
第十二章 蜗杆传动
第二节圆柱蜗杆传动的主要参数和几何尺寸
中间平面:通过蜗杆轴线并与蜗轮轴线垂直的平面。 是蜗杆的轴面 是蜗轮的端面
v 蜗杆、蜗轮的参数和尺寸大多在中间平面(主平面)内确定。
v 由于蜗轮是用与蜗杆形状相仿的滚刀,按范成原理切制轮齿
由于蜗杆齿是连续的螺旋,其材料的强度又很高,因而失效总是出 现在蜗轮上,所以蜗杆传动只需对蜗轮轮齿进行强度计算。
第十二章 蜗杆传动
第五节圆柱蜗杆传动的强度计算
1. 蜗轮齿面接触疲劳强度计算
目的:防止“点蚀”和“胶合”失效。 强度条件:σH≤[σH] 以蜗杆蜗轮节点为计算点,计算齿面接触应力 σH 。 校核公式:
轴),当蜗杆的直径较大时,可以将轴与蜗杆分开制作。
无退刀槽,加工螺旋部分时只能用铣制的办法。
有退刀槽,螺旋部分可用车制,也可用铣制加工,但该结构 的刚度 较前一种差。
第十二章 蜗杆传动
第三节蜗杆传动的失效形式、材料和结构
为了减摩的需要,蜗轮通常要用青铜制作。为了节省铜材,当蜗轮直径较大时 ,采用组合式蜗轮结构,齿圈用青铜,轮芯用铸铁或碳素钢。常用蜗轮的结构 形式如下:
=2/10=0.2
γ =11.3099°(11°18‘36“)
(3) 传动中心距 a =0.5(q + z2 )
机械设计基础复习精要:第12章 蜗杆传动

154第12章 蜗杆传动12.1 考点提要12.1.1 重要的术语和概念蜗杆的传动特点和分类、蜗杆的效率、蜗杆的头数、导程角、直径系数、12.1.2蜗杆传动的滑动速度和效率蜗杆主动时的机构效率为:)(v tg tg ϕγγη+-=)96.095.0( (12-1) 蜗杆的功率损耗一般由啮合摩擦,轴承损耗及零件搅油和飞溅损耗。
计算效率时,需要用到当量摩擦角v ϕ,其数值可通过arctgf v =ϕ算出,再结合相对滑动速度查表确定。
增加蜗杆的头数会使导程角增大,从而使效率增大,同时滑动速度也增大;如果增大蜗杆的分度圆直径将使导程角减小,从而使效率下降,而蜗杆的刚度提高。
蜗轮主动的效率为)(’v tg tg ϕγγη-= (12-2) 显然若v ϕγ≤,则0≤‘η,机构自锁,显然,如果反行程(蜗轮主动)自锁,正行程的效率(蜗杆主动)一定不大于50O O /。
蜗杆机构总的效率为啮合效率与轴承效率及搅油效率的乘积。
在设计之初,为近似求出蜗轮的转矩2T ,η数值可按表14-1数值估计。
表14-1 效率与蜗杆头数关系1Z 12 3 4 总效率0.7 0.8 0.85 0.9 影响蜗杆传动啮合效率的几何因素有:蜗杆的头数Z1,蜗杆的直径系数q﹑蜗杆分度圆直径〔或模数﹑Z1﹑q〕。
由于传动多是减速传动,所以蜗杆多处于高速级。
当蜗杆头数较少时,反行程效率低,机构自锁。
只有蜗杆头数多时才有较高的效率,反行程不自锁(可以蜗轮为主动件),但蜗轮和蜗杆的滑动速度过大,对材料要求很高,易出现磨损和胶合,因此很少采用。
12.1.3普通圆柱蜗杆传动的主要参数和几何尺寸计算蜗杆蜗轮的正确啮合条件有:1)蜗杆的轴向模数ma1=蜗轮的端面模数mt2且等于标准模数;2)杆的轴向压力角αa1=蜗轮的端面压力角αt2且等于标准压力角;3)蜗杆的导程角γ=蜗轮的螺旋角β且均可用γ表示,蜗轮与蜗轮的螺旋线方向相同。
通过蜗杆轴线并与涡轮端面垂直的平面称中间平面。
蜗杆传动的几何参数和尺寸计算
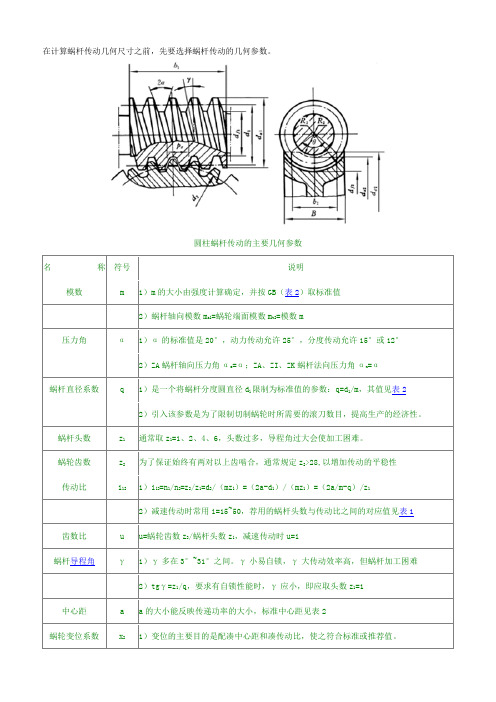
径d1/mm
m2d1/mm3
蜗杆头数z1
直径系数q
蜗杆分度圆导程角γ
蜗轮齿数z2
蜗轮变位系数x2
40
1
18
18
1
18.00
3°10′47″
62
0
50
82
0
40
1.25
20
31.25
1
16.00
3°34′35″
49
-0.500
50
22.4
35
17.92
3°11′38″
62
0.040
63
62
0.440
-0.1
≥(10.5+ )m
0.5
≥(12.5+0.1 )m
1.0
≥(13+0.1 )m
表1蜗杆头数z1与蜗轮齿数z2的荐用值
i=z2/z1
z1
z2
5
6
29~31
7~15
4
29~61
14~30
2
29~61
29~82
1
29~82
往上
表2普通圆柱蜗杆基本尺寸和参数及其与蜗轮参数的匹配
中心距a/mm
模数m/mm
传动比
i12
1)i12=n1/n2=z2/z1=d2/(mz1)=(2a-d1)/(mz1)=(2a/m-q)/z1
2)减速传动时常用i=15~50,荐用的蜗杆头数与传动比之间的对应值见表1
齿数比
u
u=蜗轮齿数z2/蜗杆头数z1,减速传动时u=i
蜗杆导程角
γ
1)γ多在3°~31°之间。γ小易自锁,γ大传动效率高,但蜗杆加工困难
(-0.100)
蜗轮蜗杆头数与效率的关系
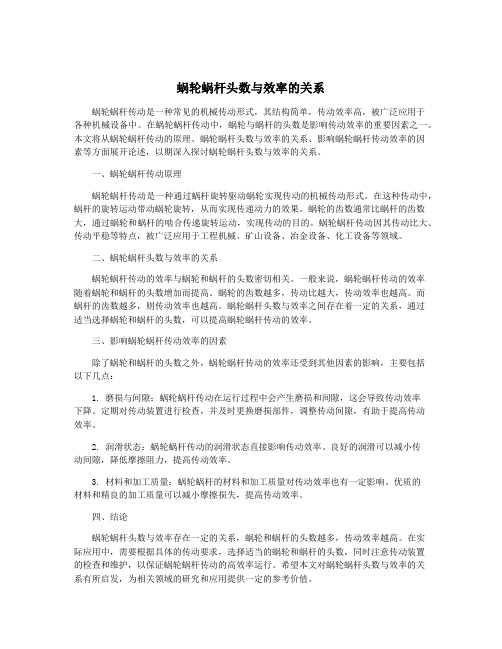
蜗轮蜗杆头数与效率的关系蜗轮蜗杆传动是一种常见的机械传动形式,其结构简单,传动效率高,被广泛应用于各种机械设备中。
在蜗轮蜗杆传动中,蜗轮与蜗杆的头数是影响传动效率的重要因素之一。
本文将从蜗轮蜗杆传动的原理、蜗轮蜗杆头数与效率的关系、影响蜗轮蜗杆传动效率的因素等方面展开论述,以期深入探讨蜗轮蜗杆头数与效率的关系。
一、蜗轮蜗杆传动原理蜗轮蜗杆传动是一种通过蜗杆旋转驱动蜗轮实现传动的机械传动形式。
在这种传动中,蜗杆的旋转运动带动蜗轮旋转,从而实现传递动力的效果。
蜗轮的齿数通常比蜗杆的齿数大,通过蜗轮和蜗杆的啮合传递旋转运动,实现传动的目的。
蜗轮蜗杆传动因其传动比大、传动平稳等特点,被广泛应用于工程机械、矿山设备、冶金设备、化工设备等领域。
二、蜗轮蜗杆头数与效率的关系蜗轮蜗杆传动的效率与蜗轮和蜗杆的头数密切相关。
一般来说,蜗轮蜗杆传动的效率随着蜗轮和蜗杆的头数增加而提高。
蜗轮的齿数越多,传动比越大,传动效率也越高。
而蜗杆的齿数越多,则传动效率也越高。
蜗轮蜗杆头数与效率之间存在着一定的关系,通过适当选择蜗轮和蜗杆的头数,可以提高蜗轮蜗杆传动的效率。
三、影响蜗轮蜗杆传动效率的因素除了蜗轮和蜗杆的头数之外,蜗轮蜗杆传动的效率还受到其他因素的影响,主要包括以下几点:1. 磨损与间隙:蜗轮蜗杆传动在运行过程中会产生磨损和间隙,这会导致传动效率下降。
定期对传动装置进行检查,并及时更换磨损部件,调整传动间隙,有助于提高传动效率。
2. 润滑状态:蜗轮蜗杆传动的润滑状态直接影响传动效率。
良好的润滑可以减小传动间隙,降低摩擦阻力,提高传动效率。
3. 材料和加工质量:蜗轮蜗杆的材料和加工质量对传动效率也有一定影响。
优质的材料和精良的加工质量可以减小摩擦损失,提高传动效率。
四、结论蜗轮蜗杆头数与效率存在一定的关系,蜗轮和蜗杆的头数越多,传动效率越高。
在实际应用中,需要根据具体的传动要求,选择适当的蜗轮和蜗杆的头数,同时注意传动装置的检查和维护,以保证蜗轮蜗杆传动的高效率运行。
蜗轮蜗杆测绘、设计计算及图纸标注

蜗轮蜗杆的测绘
一、蜗轮、蜗杆齿轮的功用与结构
蜗轮、蜗杆的功用主要用于传递交错轴间运动和动力,通常,轴交角∑=90°。其优点是传动 比大,工作较平稳,噪声低,结构紧凑,可以自锁;缺点是当蜗杆头数较少时,传动效率低,常需 要采用贵重的减摩有色金属材料,制造成本高。 蜗轮是回转形零件,蜗轮的结构特点和齿轮基本相似,直径一般大于长度,通常由外圆柱面、 内环面、内孔、键槽(花键槽) 、轮齿、齿槽等组成。根据结构形式的不同,齿轮上常常还有轮缘、 轮毂、腹板(孔板) 、轮辐等结构。按结构不同蜗轮可分为实心式、腹板式、孔板式、轮辐式等多种 型式。 蜗杆的结构和轴相似,其结构特点是长度一般大于直径,通常由外圆柱面、圆锥面、螺纹及阶 梯端面等所组成。蜗杆上啮合部分的轮齿呈螺旋状,有单头和多头之分, 单头蜗杆的自锁性能好、 易加工,但传动效率低。 由于圆柱蜗杆工艺性好,尤其是阿基米德圆杆蜗杆,因此,圆柱蜗杆获得了广泛应用。
3.537 3.625 4 4.043 4.233 4.500 4.548 5
33.340 34.930 35.470 36.510 37.700 38.100 39.900 41.270
10.612 11.117 11.289 11.622 12 12.127 12.700 13.138
如图 8-17 所示,用游标卡尺的深度尺或其他测量工具直接量得 h,则 ma 即可算出。 ③ 根据计算公式 da2 = mt (z2+2) ,则
12. 13. 14. 15.
- 1、下载文档前请自行甄别文档内容的完整性,平台不提供额外的编辑、内容补充、找答案等附加服务。
- 2、"仅部分预览"的文档,不可在线预览部分如存在完整性等问题,可反馈申请退款(可完整预览的文档不适用该条件!)。
- 3、如文档侵犯您的权益,请联系客服反馈,我们会尽快为您处理(人工客服工作时间:9:00-18:30)。
A:组织教学:
a: 考勤。
检查学生出勤情况。
b: 维护课堂秩序。
c: 检查工奘。
检查学生工作衣帽穿戴是否规范。
d: 宣布授课内容及目的要求。
B: 入门指导:
a: 复习引导:
以前车削单头螺纹时的方法是什么?梯形螺纹怎样测量?
b: 讲解新课
多线螺纹的车削
螺纹有单线和多线之分,沿一条螺旋线所形成的螺纹称为单线螺纹,沿两条或两条以上螺旋线所形成的螺纹,该螺旋线在轴向等距分布称之为多线螺纹。
它常用于需快速移动的机构中。
判定头数时,可从螺纹端面上的痕迹来判定。
一、表示代号
1.普通多线三角螺纹,如:M48x3/
2.
2.梯形多线螺纹,如:Tr40x12(P6).
二、各部位尺寸计算方法和单头螺纹相同,只是要用导程代替螺距。
三、分线方法
1.技术要求
⑴多线螺纹的螺距必须相等;
⑵每条螺纹的小径要相等;
⑶每条螺纹的牙型角要相等。
车削多线螺纹主要是考虑分线方法和车削步骤的协调。
它的各螺旋槽在轴向是等距离分布的,在端面上螺旋线的起点是等角度分布的,而进行等距分布的操作就叫分线。
若出现分线误差,使得螺距不等,则会直接影响内外螺纹的配合性能,增加不必要的磨损,降低使用寿命。
因此必须掌握分线方法,控制分线精度。
根据多线螺纹在轴向和圆周上等距分布的特点,分线方法有轴向分线法和圆周分线法两种。
结合我校实际情况,常用轴向分线法的其中一种――小滑板分线法。
2.轴向分线法(以双头梯形螺纹为例)
⑴当粗车好第一条螺旋槽之后,把刀轴向移动一个螺距,然后用中滑板将第二个螺旋槽也车至同样深度,两侧留同样余量。
⑵精车时,可按下图所示步骤进行加工:
再将3面车光后,也车至1、2面的中滑板刻度,然后将小滑板右移一个螺距,利用中滑板将4面车至1、2、3面的中滑板刻度,从而完成右侧的分线。
最后,要用尺厚卡尺测量,保证A=B且a=b,若不等,应分析是a大还是b 大,确定好后,是加工左侧面还是右侧面,还要看A和B的大、小情况来定。
四、注意事项
1.多线螺纹导程大,走刀速度快,车削时要防止碰撞,特别是小滑板不要退得太靠后。
2.由于螺纹升角大,车刀后角要相应增减。
3.小滑板的间隙要调整适当,摇动时注意空行程的影响,要与轴线平行,否则会造成分线误差。
4.精车时要多次循环分线,以矫正赶刀或粗车时所产生的误差。
蜗杆的加工
一、蜗杆的基本知识
蜗杆蜗轮组成的运动副常用于减速传动机构中,以传递两轴在空间垂直交错且减速比较大的运动。
蜗杆与蜗轮传动的基本要求是:蜗杆的周节必须等于蜗轮的周节。
蜗杆的齿形与梯形螺纹很相似,其轴向剖面形状为梯形。
常用的蜗杆有公制(齿形角40°)和英制(齿形角29°)两种。
我们主要介绍公制蜗杆。
二、蜗杆的主要参数
1、轴向模数(m x):为规定的基本参数
2、齿距(周节)(P):P=πm x
3、导程(L):L=ZP=Zπm x Z为线数(头数)
4、分度圆直径(d1):d1=qm x(q为直径系数,由强度条件决定)
5、齿顶宽(f):法向f n=0.843m x cosγ
6、法向齿厚(s):s n=(πm x/2)cosγ=(P/2)cosγ
三、蜗杆的测量方法
1、齿顶圆直径可用千分尺或游标卡尺测量;齿根圆直径一般采用控制齿深的办法保证。
2、分度圆直径可用三针方法与测量梯形螺纹相同。
三针测量时M值的计算公式:M=d1+3.924d D-4.316m x
其中:d1为分度圆直径,d1=d a-2m x;d D为量针直径,其简化计算公式为:d D=2.446m x(最大值);1.675m x(最佳值);1.61m x (最小值);通常我们把d D的最佳值代入公式进行计算M值。
3、齿厚一般用齿厚游标卡尺进行测量。
齿厚游标卡尺由相互垂直的齿高卡尺和齿厚卡尺组成(其刻线原理和读数方法与游标卡尺相同)。
测量时,将齿高卡尺读数调整到1个实际齿顶高(必须排除齿顶圆直径误差的影响),使卡脚在法向卡入齿廓,并作微量往复转动,直到卡脚与蜗杆齿侧平行(此时尺杆与蜗杆轴线的夹角恰为导程角)。
特别注意在做往复运动的时候,不能摆动太大,否则会损坏齿厚游标卡尺。
在这种状态下,齿厚卡尺的最小读数即是蜗杆分度圆上的法向齿厚s n。
但图样上一般标注的是轴向齿厚,所以测出的法向齿厚s n应换算为轴向齿厚s x来检验是否符合图纸要
求。
轴向齿厚与法向齿厚的换算关系为:
s n= s x cosγ=(πm x/2)cosγ
四、车削蜗杆的方法
1、蜗杆车刀
(1)材料一般用高速钢,分粗车刀和精车刀。
(2)粗车刀:左右刀刃之间的夹角应略小于齿形角;刀头宽度应略小于齿根槽宽以保证精加工余量;应有较大的前角;刀尖适当倒圆。
(3)精车刀:刀刃夹角应等于齿形角,并且要有较好的对称度,切削刃直线度要好,表面粗糙度要小;应磨有较大的前角的卷屑槽以保证切削顺利。
这种车刀的前端刀刃不能进行切削,只能依靠两侧面刀刃精车两侧齿面。
2、车刀安装
工业上用的公制蜗杆按齿形可分为轴向直廓蜗杆(阿基米德蜗杆ZH)和法向直廓蜗杆(延长渐开线蜗杆ZN),我们经常用到的是轴向直廓蜗杆。
车削轴向直廓蜗杆时,应采用水平装刀法,即应使车刀两侧刃组成的平面处于水平状态且与蜗杆轴线等高。
车削法向直廓蜗杆时,应采用垂直装刀法。
安装模数较小的蜗杆车刀时,可用样板找正,模数较大时通常用万能角度尺找正,其方法与梯形螺纹安装车刀相似。
3、车削方法
蜗杆车削方法与梯形螺纹相似,先根据蜗杆导程(单线蜗杆为周节),在操作的车床进给箱铭牌上找到相应的数据,来调节各有关手柄的位置。
由于蜗杆导程大、齿槽深、切削面积大,车削比梯形螺纹困难,故常选用较低的切削速度,采用倒顺车的方法进行车削,以防止乱牙。
粗车时,通常用分层切削法粗车。
粗车完成后,用精车刀修整牙形,在安装车刀的时候,使车床主轴停转,摇动小拖板使车刀切削刃正好对准已粗车的螺旋槽中,摇动中拖板使车刀前端切削刃与槽底接触,此时记下中拖板刻度,将中拖板刻度调至零位,并退回车刀,然后开动车床,依次进行精车左右侧面。
精车时,逐步摇动小拖板使车刀左切削刃与左侧面接触后退回起始位置,中拖板此时摇至与零位相差半格处,然后以纵向切削深度为0.05~0.01mm逐次减精车左侧面。
左侧面表面粗糙度达到要求以后,开始精车右侧面,精车右侧面与精车左侧面类似。
逐渐将右侧面车至满足图纸要求的法向齿厚尺寸。
多线蜗杆的车削应遵循多线梯形螺纹加工时的分头和粗精车方法进行。
4、注意事项:
(1)开始车削时,应先检查周节是否正确。
(2)由于蜗杆导程角较大,车刀的两侧后角应适当增减。
(3)应尽量提高装夹刚性,避免工件移位。
(4)每次切入深度要适量,同时经常测量法向齿厚,控制精车余量。
(5)精车时应注意工件的同轴度。
车刀前角应小些,刀口要平直、锋利。
车削时采用低速,并加注充分切削液。
(6)中拖板手动时给时,要防止多摇一圈,以免发生撞刀现象。
c、示范操作
一、装卡工件和车刀。
二、根据图样调整工件和机床。
三、按前述方法将工件分粗、精车进行完毕。
四、精车时,用移动小滑板法进行双头梯形螺纹的分线[Tr40x12(P6)]。
d: 实习分配
1.实习分配见分配表。
2.实习内容见练习图。
C、巡回指导
1.车床的调整。
2.测量时分线精度不准确的分析。
3.操作时学生和设备的安全。
还要观察每位同学的加工方法和步骤及操作姿势是否正确,切削用量选择是否合理,发现问题及时纠正。
对个别差生作重点辅导,对普遍问题进行集中讲解指导。
D、结束指导
总结、评比当日的加工练习中表现出的正确现象和不正确现象,对较好的同学进行表扬,对操作中出现的问题分析原因并提出解决办法。