脱臭
油脂脱臭—油脂脱臭(油脂加工技术课件)

油脂脱臭是液-气传质过程,汽-液表面相接触, 水蒸汽被挥发的臭味组分所饱和,并按其分压的比率 逸出,从而达到脱除臭味组分的目的。
(1)脂肪酸和臭味组分的蒸汽压等于其在纯粹状态下的蒸汽压 乘上它在油脂中的浓度。
(2)脱臭塔的蒸发效率与设备的操作温度、压力、水蒸汽量/ 油量(S/O)三个主要参数有关: 在一定压力下,随着操作温度升高,臭味组分的蒸汽 压增大,使脱臭油中臭味组分的最终浓度降低。 固定脱臭深度,离塔脂肪酸的组分定为脱臭成品油的 质量指标,若操作温度保持不变, (S/O)将随着系统内 压力P的降低而减小,若操作压力接近真空,则水蒸汽用 量将会大幅度降低。由此,应最大限度负压操作。
当游离脂肪酸降至0.01~0.03%(过氧化值为0)时, 气味即消除。因此,脱臭的深度常用游离脂肪酸含量的降 低来衡量。 (6)油脂脱臭作用改善油脂风味,提高油脂烟点。
一、油脂脱臭理论
(一)水蒸汽蒸馏理论:
1.油脂中臭味物质的蒸汽大于甘三酯的蒸汽压
Eg:250℃,高碳链脂肪酸蒸汽压为26.66~ 2.67kPa, 高碳链脂肪酸相应的甘三脂的蒸汽压为 1.33×10-3~1.33×10-4kPa。
DEOD FLOW SHEET
连续式多容器脱臭工艺
搅拌/汽提水蒸气 加热水蒸气
真空加热容器
脱臭容器
去真空
热回收和冷却器
脂肪 物冷 凝器 脱气器
飞溅油罐
省热器
冷却器
冷却器
精过
滤机
原料
馏出物
脱臭油脂
连续式单壳体脱臭系统
加热水蒸气 搅拌/汽提水蒸气
真空加热容器
去真空
脂肪物 冷凝段 预汽提段
脱臭浅盘
油脂脱臭原理及技术详解

油脂脱臭原理及技术详解一.油脂臭味的来源(1)油料含有的类脂物等在制油过程转入油脂;(2)油脂制取、储藏过程中分解的物质;如低分子醛、酮、酸、含硫化合物等;(3)在制油和加工产生的工艺性气味:如焦糊味、溶剂味,肥皂味、漂土味、氢化异味等;(4)天然油脂中臭味组分:含量很低:为0.1-1.0%。
(5)油脂中臭味组分与游离脂肪酸含量降低相关:当游离脂肪酸降至0.01~0.03%(过氧化值为0)时,气味即消除。
因此,脱臭的深度常用游离脂肪酸含量的降低来衡量。
(6)油脂脱臭作用改善油脂风味,提高油脂烟点。
二.油脂脱臭理论(一)水蒸汽蒸馏理论1、油脂中臭味物质的蒸汽大于甘三酯的蒸汽压。
Eg:250℃,高碳链脂肪酸蒸汽压为26.66~2.67kPa,高碳链脂肪酸相应的甘三脂的蒸汽压为1.33×10-3~1.33×10-4kPa。
2、油脂中其他臭味组分的蒸汽压比脂肪酸还要高。
油脂脱臭是液-气传质过程,汽-液表面相接触,水蒸汽被挥发的臭味组分所饱和,并按其分压的比率逸出,从而达到脱除臭味组分的目的。
(1)脂肪酸和臭味组分的蒸汽压等于其在纯粹状态下的蒸汽压乘上它在油脂中的浓度。
(2)脱臭塔的蒸发效率与设备的操作温度、压力、水蒸汽量/油量(S/O)三个主要参数有关;在一定压力下,随着操作温度升高,臭味组分的蒸汽压增大,使脱臭油中臭味组分的最终浓度降低。
固定脱臭深度,离塔脂肪酸的组分定为脱臭成品油的质量指标,若操作温度保持不变,(S/O)将随着系统内压力P的降低而减小,若操作压力接近真空,则水蒸汽用量将会大幅度降低。
由此,应最大限度负压操作。
(二)脱臭损耗先进工艺及合理操作条件下,脱臭最小损耗一般为0.2~0.4%,再加上脱臭原料油中FFA 含量的1.05~1.2倍。
1、蒸馏损耗(1)易蒸馏的低分子醛、酮及游离脂肪酸;(2)少部分油脂水解生成脂肪酸;当FFA含量降低至0.015-0.03%时,游离脂肪酸的脱除速率与油脂水解生成游离脂肪酸的速率达到平衡。
洗鞋子除臭的方法

洗鞋子除臭的方法洗鞋子除臭的方法有很多种,下面我将详细介绍几种常见的方法:1. 使用醋水除臭。
醋具有很好的去除异味的作用。
将白醋与水以1:1的比例混合,用这个混合液来擦拭鞋子内外部,可以有效去除鞋子的异味。
2. 使用烤箱脱臭。
将鞋子放在预热至120C的烤箱中,保持20-30分钟。
高温可以杀死鞋子中的细菌,有效去除异味。
但要注意,这个方法适用于可以耐受高温的鞋子材料,不适用于塑料等易熔化的材质。
3. 使用小苏打粉除臭。
小苏打粉具有吸附异味的作用。
将适量小苏打粉撒在鞋子内部,并静置一整晚,第二天用吸尘器清除残留的小苏打粉即可。
4. 使用茶包除臭。
将干燥的茶包放入鞋子内部,让茶包的吸湿性去除异味。
这个方法对于异味较轻的鞋子比较有效。
5. 使用活性炭除臭。
将适量的活性炭装入透气的袜子或布袋中,然后将袜子或布袋放入鞋子内部,活性炭具有较强的吸附异味的能力,可以帮助除去鞋子的异味。
6. 使用消毒喷雾。
市面上有一些专门用于鞋子的消毒喷雾,可以杀灭鞋子上的细菌并去除异味。
使用时,按照说明使用喷雾剂喷洒鞋子内外部,然后晾干即可。
7. 定期晾晒。
鞋子在使用后可能会有一定的湿气,湿气容易滋生细菌从而产生异味。
因此,定期将鞋子晾晒在通风的地方,有助于除去湿气并减少异味。
8. 注意鞋子的保养。
定期对鞋子进行清洁和保养,可以有效延长鞋子的寿命,并减少异味。
定期擦拭鞋子,并使用合适的鞋油或鞋乳进行保养,可以使鞋子保持干燥和清洁,减少异味的发生。
最后,需要注意的是,不同的材质和鞋子类型可能需要采用不同的除臭方法,因此在选择除臭方法时要根据实际情况进行选择。
此外,除臭方法可以配合使用,以达到更好的效果。
希望以上方法可以帮到你,祝你的鞋子常保清新!。
脱臭原理与工艺

•
据研究,甘三酯的蒸汽压是很低的。不 可能构成直接的蒸馏损耗。因此,脱臭时 中性油脂的蒸馏损耗,可认为是甘三酯水 解生成的甘二酯和脂肪酸被蒸馏而损耗。
• 2、飞溅损耗 • 在许多脱臭装置中,由于汽提蒸汽的机械 作用而引起的油脂飞溅现象是构成脱臭损耗的 另一重要方面。汽提蒸汽在冲出油层到达脱臭 罐(塔)的顶部时,一般已没有足够的速度能 使相当数量的油滴带走,但当蒸汽喷入油中, 以及由油层表面冲出时,由于蒸汽体积膨胀能 产生相当大的动能,这一能量使油滴冲出档板 进入排气管道,排汽管道截面积小,该处蒸汽 流速较大,能使油滴继续被汽流带出脱臭罐 (塔)体外。
• 蒸馏塔的真空度还与油脂的水解有关联, 如果设备真空度高,就能有效地避免油脂 的水解所引起的蒸馏损耗,并保证获得低 酸值的油脂产品。
• (三)通汽速率与时间
• 在汽提脱臭过程中,汽化效率随通入 水蒸汽的速率而变化。通汽速率增大,则 汽化效率也增大。但通汽的速率必须保持 在油脂开始发生飞溅现象的限度以下。
•
•
1、蒸馏损耗
汽提脱臭过程中,低分子的醛类、酮类及 游离脂肪酸最容易蒸馏出来,随着脱臭过程的 加深,油脂内原有游离脂肪酸经脱臭后几乎完 全被除去,因此,蒸馏损耗应包括油脂脱臭前 的游离脂肪酸的含量。此外,根据反应方程可 知,汽提蒸汽不可避免地要引起部分油脂的水 解,因油脂水解所生成的这部分脂肪酸,便也 构成了蒸馏损耗。
• 此外,当压力和通汽速率固定不变时,汽 提脱臭时间与油脂中游离脂肪酸及臭味组 分的蒸汽压成反比。根据试验,当操作温 度每增加17℃时,由于游离脂肪酸及臭味 组分的蒸汽压升高,脱除它所需的时间也 将缩短一半。
• 汽提脱臭操作中,油脂与蒸汽接触的时间 直接影响到蒸发效率。因此,欲使游离脂 肪酸及臭味组分降低到产品的要求的质量 标准,就需要有一定的通汽时间。但是, 考虑到脱臭过程中发生的油脂聚合和其他 热敏性组分的热分解,在脱臭罐(塔)的 结构设计中,应考虑到使定量蒸汽与油脂 的接触时间尽可能长些,以期在最短的通 汽时间及最小的耗汽量下获得最好的脱臭 效果。
污水厂臭气处理方法

污水处理厂除臭技术污水处理厂臭味的处理方法有很多,如化学吸附法、催化剂氧化法、燃烧法、活性碳物理吸附法、废气直接通入曝气池、土壤脱臭法、臭气氧化法、填充塔式微生物法、湿式吸收氧化法、生物脱臭法、高能离子脱臭技术、天然植物提取液脱臭等。
在这些方法中化学吸附与氧化法,具有脱臭效率高的优点,但投资与运行费用高,适用于高浓度的臭气处理。
燃烧法脱臭:燃烧法可以分为直接燃烧法与辅助燃烧法。
利用风机与风道将臭气收集起来,送入焚烧炉内直接或与其它介质混合进行燃烧。
燃烧法特点:1、适用于高浓度臭气;2、适用于臭气源集中的场所;3、系统需要连续运行,需要考虑焚烧炉不运行时的处理对策;4、考虑到污水厂臭气具有腐蚀性,并且所发生的臭气浓度一般不太高但气量大、场所分散,因此投资及运行、管理费用高。
活性炭吸附法:以活性炭为原料,利用活性炭吸附功能对臭气进行处理。
活性炭除臭法特点:1、适用于低浓度臭气处理;2、方法简单,系统紧凑,占地面积较小;3、需要经常更换吸附剂,运行费用高;4产生二次污染;5由于活性炭的吸附能力极易受到臭气中的潮气、灰尘等影响而下降,因此需要增设其它附属设备,如需在系统管道上安装除尘、除湿装置,在吸附塔前面设置加热器等。
废气直接通入曝气池法:将从格栅间、沉砂池、浓缩池、污泥脱水机房收集到的废气直接通入曝气池中,有机气味物质在曝气池中被活性污泥吸收,随后被分解。
其主要优点就是方法简单,费用低,但除臭效果较差,存在过曝气的可能,曝气池中污水生化处理过程将受到一定的影响,使得曝气池成为严重的气味扩散源,因此其应用有较大的局限性。
土壤法:土壤脱臭主要可分为物理吸附与生物分解两类。
恶臭气体,如胺类、硫化氢、低级脂肪酸等水溶性臭气类,被土壤中的水分吸收去除,而非溶性臭气则被土壤表面物理吸附继而被土壤中微生物分解。
土壤除臭法特点:1、建设费用比较低,维护、管理工作量比较大;2、处理60立方米/小时的臭气量,需要3~5平方米的土地;3、不使用于降暴雨、下大雪地区;4、对于高温、高湿与水分、尘土、微尘等气体必须要进行预处理;、除臭效果类似于活性炭脱臭;6、适用于臭气浓度较低及土地充裕的地方,不适合中大型污水处理厂。
除臭技术工艺大pk各种除臭技术比较

除臭技术工艺大pk各种除臭技术比较恶臭气体主要产生在污水处理过程中的排污泵站、进水格栅、曝气沉沙池,污泥处理设施以及污泥处理过程中的污泥浓缩、脱水干化、转运、热干化、堆肥等处。
不同的处理设施及过程会产生各种不同的恶臭气体。
常见的臭气体如下所列:恶臭物质种类繁多,来源广泛,对人体呼吸、消化、心血管、内分泌及神经系统都会造成不同程度的毒害,其中芳香族化合物如苯、甲苯、苯乙烯等还能使人体产生畸变、癌变。
所以,清除恶臭气体是一项非常重要的技术。
今天小七罗列了各种除臭方法,大家看看哪种除臭技术是除臭NO.1。
一、脱臭方法:掩蔽法脱臭原理:采用更强烈的芳香气味与臭气掺和,以掩蔽臭气,使之能被人接收适用范围:适用于需立即地、暂时地消除低浓度恶臭气体影响的场合,恶臭强度2.5左右,无组织排放源优点:可尽快消除恶臭影响,灵活性大,费用低缺点:恶臭成分并没有被去除二、脱臭方法:稀释扩散法脱臭原理:将有臭味地气体通过烟囱排至大气,或用无臭空气稀释,降低恶臭物质浓度以减少臭味适用范围:适用于处理中、低浓度的有组织排放的恶臭气体优点:费用低设备简单缺点:易受气象条件限制,恶臭物质依然存在三、脱臭方法:热力燃烧法、催化燃烧法脱臭原理:在高温下恶臭物质与燃料气充分混和,实现完全燃烧适用范围:适用于处理高浓度、小气量的可燃性气体优点:净化效率高,恶臭物质被彻底氧化分解缺点:设备易腐蚀,消耗燃料,处理成本高,易形成二次污染四、脱臭方法:水吸收法脱臭原理:利用臭气中某些物质易溶于水的特性,使臭气成分直接与水接触,从而溶解于水达到脱臭目的适用范围:水溶性、有组织排放源的恶臭气体优点:工艺简单,管理方便,设备运转费用低缺点:产生二次污染,需对洗涤液进行处理;净化效率低,应与其他技术联合使用,对硫醇,脂肪酸等处理效果差五、脱臭方法:药液吸收法脱臭原理:利用臭气中某些物质和药液产生化学反应的特性,去除某些臭气成分适用范围:适用于处理大气量、高中浓度的臭气优点:能够有针对性处理某些臭气成分,工艺较成熟缺点:净化效率不高,消耗吸收剂,易形成而二次污染六、脱臭方法:吸附法脱臭原理:利用吸附剂的吸附功能使恶臭物质由气相转移至固相适用范围:适用于处理低浓度,高净化要求的恶臭气体优点:净化效率很高,可以处理多组分恶臭气体缺点:吸附剂费用昂贵,再生较困难,要求待处理的恶臭气体有较低的温度和含尘量七、脱臭方法:生物滤池式脱臭法脱臭原理:恶臭气体经过去尘增湿或降温等预处理工艺后,从滤床底部由下向上穿过由滤料组成的滤床,恶臭气体由气相转移至水—微生物混和相,通过固着于滤料上的微生物代谢作用而被分解掉适用范围:目前研究最多,工艺最成熟,在实际中也最常用的生物脱臭方法。
油脂脱臭的结果有哪些方法

油脂脱臭的结果有哪些方法油脂脱臭是指将油脂中的异味物质或挥发性有机物去除或减少,使油脂具有清香、纯净的味道。
油脂脱臭可以应用于食用油、工业油以及其他油脂产品中。
下面是一些常用的油脂脱臭方法:1. 蒸馏法:蒸馏法是通过升华和凝固的原理将挥发性物质从油脂中分离出来。
这种方法适用于高温下沸点低的物质。
蒸馏法适用于较小量的油脂脱臭,但不适用于大规模生产。
2. 催化熔体脱臭法:这种方法通过在油脂中添加一定量的吸附剂,利用吸附剂的吸附作用去除异味物质,并通过加热使吸附剂融化,从而脱除油脂中的异味。
催化熔体脱臭法适用于大规模的工业生产,可以有效去除不同类型的异味。
3. 活性炭吸附法:活性炭是一种具有极强吸附性能的材料,可以吸附油脂中的异味物质。
将活性炭添加到油脂中,搅拌均匀后过滤或离心除去,可以降低油脂的异味。
活性炭吸附法适用于小规模的油脂脱臭,但需要定期更换活性炭。
4. 超声波辅助脱臭法:超声波技术可以产生高频、高能量的声波,通过声波的作用,可以提高脱臭效果。
将油脂置于超声波水浴中,通过声波的作用使异味物质溶解在水中,从而达到脱臭的目的。
超声波辅助脱臭法适用于各种类型的油脂。
5. 溶剂萃取法:溶剂萃取法是通过将油脂溶解在适当的有机溶剂中,利用溶剂与异味物质的亲和力的差异,将异味物质从油脂中分离。
溶剂萃取法适用于特定类型的油脂,但需要注意溶剂的选择和之后的回收处理。
6. 温度脱臭法:温度脱臭法是通过加热油脂,使异味物质挥发出来,然后通过冷凝和收集处理。
这种方法适用于易挥发的异味物质,但需要控制好温度和加热的时间,以免对油脂产生不利影响。
7. 光照脱臭法:光照脱臭法是通过利用光的作用使异味物质分解或挥发出来。
将油脂置于光源下,利用光的能量使异味物质发生化学反应,从而去除异味。
光照脱臭法适用于特定类型的油脂,但需要注意光的强度和照射时间。
8. 微生物法:微生物法是通过利用某些微生物的代谢能力将异味物质分解为无害物质。
污水厂除臭技术的几种方法

污⽔⼚除臭技术的⼏种⽅法⽬前,污⽔处理⼚⼯程上常⽤恶臭⽓体处理技术有⽣物滤池、⽣物滴滤塔、⽣物滤床、植物提取液除臭、活性炭吸附、⾼能离⼦除臭、化学除臭、活性氧除臭、⼟壤脱臭法等。
⼀、⽣物滤池1.1技术原理⽣物滤池主要是利⽤微⽣物除臭,通过微⽣物的⽣理代谢将具有臭味的物质加以转化,通过专门培养在⽣物滤池内⽣物填料上的微⽣物膜对废⽓分⼦进⾏除臭的⽣物废⽓处理技术,当含有⽓、液、固三项混合的有毒、有害、有恶臭的废⽓经收集管道导⼊本系统后通过培养⽣长在⽣物填料上的⾼效微⽣物菌株形成的⽣物膜来净化和降解废⽓中的污染物。
此⽣物膜⼀⽅⾯以废⽓中的污染物为养料,进⾏⽣长繁殖;另⼀⽅⾯将废⽓中的有毒、有害恶臭物质进⾏分解,降解成⽆毒⽆害的 CO2,H2O,H2SO4,HNO3等简单⽆机物,从⽽达到除臭的⽬的。
原理图:1.2⽣物除臭⼯艺的三个阶段:1、废⽓中有毒、有害、恶臭污染物与⽔接触,溶于⽔中成为液相中的分⼦或离⼦。
2、溶液中的恶臭成分被微⽣物吸附、吸收,恶臭成分从⽔中转移⾄微⽣物体内。
3、进⼊微⽣物细胞中的有机物在各种细胞内酶的催化作⽤下,微⽣物对其进⾏氧化分解,同时进⾏合成代谢产⽣新的微⽣物细胞。
⼀部分有机物通过氧化分解最终转化为H2O,CO2等稳定的⽆机物,最终达到废⽓治理的⽬的。
1.3适⽤范围⽣物除臭⼯艺可⽤于城市污⽔站(泵站臭⽓、预处理臭⽓、污泥处理臭⽓);垃圾处理⼚(收集站臭⽓、分选车间臭⽓);涂料⼚除臭/异味;塑料、橡胶⼚⽣产废⽓;饲料加⼯废⽓;⾷品饮料⼚异味;制药企业除臭/异味等。
⼆、⽣物滴滤塔⽣物滴滤塔主体为填充塔,内有⼀层或多层填料,填料表⾯是由微⽣物区系形成的⼏毫⽶厚的⽣物膜。
含可溶性⽆机营养液的液体从塔上⽅均匀地喷洒在填料上,液体⾃上向下流动,然后由塔底排出并循环利⽤。
有机废⽓由塔底进⼊⽣物滴滤塔,在上升的过程中与润湿的⽣物膜接触⽽被净化,净化后的⽓体由塔顶排出。
⼯艺图:在欧美、⽇本等国家,⽣物滴滤塔⼯艺被⼴泛应⽤于污⽔⼚臭⽓处理⼯程中。
污水厂臭气处理方法

污水处理厂除臭技术污水处理厂臭味的处理方法有很多,如化学吸附法、催化剂氧化法、燃烧法、活性碳物理吸附法、废气直接通入曝气池、土壤脱臭法、臭气氧化法、填充塔式微生物法、湿式吸收氧化法、生物脱臭法、高能离子脱臭技术、天然植物提取液脱臭等。
在这些方法中化学吸附与氧化法,具有脱臭效率高的优点,但投资与运行费用高,适用于高浓度的臭气处理。
燃烧法脱臭:燃烧法可以分为直接燃烧法与辅助燃烧法。
利用风机与风道将臭气收集起来,送入焚烧炉内直接或与其它介质混合进行燃烧。
燃烧法特点:1、适用于高浓度臭气;2、适用于臭气源集中的场所;3、系统需要连续运行,需要考虑焚烧炉不运行时的处理对策;4、考虑到污水厂臭气具有腐蚀性,并且所发生的臭气浓度一般不太高但气量大、场所分散,因此投资及运行、管理费用高。
活性炭吸附法:以活性炭为原料,利用活性炭吸附功能对臭气进行处理。
活性炭除臭法特点:1、适用于低浓度臭气处理;2、方法简单,系统紧凑,占地面积较小;3、需要经常更换吸附剂,运行费用高;4产生二次污染;5由于活性炭的吸附能力极易受到臭气中的潮气、灰尘等影响而下降,因此需要增设其它附属设备,如需在系统管道上安装除尘、除湿装置,在吸附塔前面设置加热器等。
废气直接通入曝气池法:将从格栅间、沉砂池、浓缩池、污泥脱水机房收集到的废气直接通入曝气池中,有机气味物质在曝气池中被活性污泥吸收,随后被分解。
其主要优点就是方法简单,费用低,但除臭效果较差,存在过曝气的可能,曝气池中污水生化处理过程将受到一定的影响,使得曝气池成为严重的气味扩散源,因此其应用有较大的局限性。
土壤法:土壤脱臭主要可分为物理吸附与生物分解两类。
恶臭气体,如胺类、硫化氢、低级脂肪酸等水溶性臭气类,被土壤中的水分吸收去除,而非溶性臭气则被土壤表面物理吸附继而被土壤中微生物分解。
土壤除臭法特点:1、建设费用比较低,维护、管理工作量比较大;2、处理60立方米/小时的臭气量,需要3~5平方米的土地;3、不使用于降暴雨、下大雪地区;4、对于高温、高湿与水分、尘土、微尘等气体必须要进行预处理;、除臭效果类似于活性炭脱臭;6、适用于臭气浓度较低及土地充裕的地方,不适合中大型污水处理厂。
图解各类油脂脱臭工艺及设备

图解各类油脂脱臭工艺及设备油脂脱臭工艺及设备1、间歇式脱臭时间长(8h)、耗蒸汽量大、热能利用率低。
蒸馏釜形式,高径比为2,油层下部有直接蒸汽盘管;中央循环管,蒸汽从中央循环管上部喷出,强制循环。
2、半连续脱臭相当于多层间歇脱臭器重叠组成而成,脱臭过程被分割为若干个独立的单元,每层的液层降低。
层叠式如图6-42。
3、连续式脱臭形式很多,主要有层板式、填料式、水平浅盘式脱臭塔等。
为防止油流短路,有的采用折流隔板强制导向装置、蒙马泵等。
(一)间歇式脱臭工艺及设备图1间歇式脱臭系统图2双壳体塔半连续式脱臭系统图3单壳体塔半连续式脱臭工艺(三)连续式脱臭工艺图4连续水平式浅盘连续脱臭工艺图6带浮阀塔板的连续脱臭工艺图7连续式多容器脱臭工艺(四)填料薄膜脱臭工艺图11连续薄膜式脱臭工艺脱臭设备(一)脱臭器:多层脱臭塔、填料式脱臭塔、组合塔多层式脱臭塔A多层式脱臭塔B填料脱臭塔组合式脱臭塔(二)辅助设备1、析气器待脱臭油中,一般溶解有1/万-5/万的氧气,需在高温脱臭之前脱除。
析气器的型式有多种,70℃。
2、换热器用于冷热油热交换——热量回收、加热高温油。
利用高压蒸汽加热时,特别要注意耐高压、热补偿问题。
板式换热器热效果好,因垫片密封问题,用于低温液—液换热。
螺旋板不如板式换热效果好,可用于高温、无垫片泄露,但难以清理。
列管换热效率最低,但可拆卸头部,容易清理,常用。
3、脂肪酸捕集器采用低温(60℃)脂肪酸对高温脱臭馏出气体直接冷凝,将脂肪酸等高沸点组分冷凝回收,减少冷凝水的污染。
脂肪酸捕集器由脂肪酸喷头、旋风分离室和分离挡板组成。
4、屏蔽泵输送高温油脂的气密泵,防止空气空气对高温油脂的氧化,在高真空条件下运行。
主要特点:泵与电机为一整体结构,定子与转子都用薄金属罩密封,所有通向外界的联接处均使用密封片或O型密封环进行密封,从而有效地防止了泵运转时的空气泄漏,避免了高温油脂与氧的接触。
5、真空装置(1)水喷射真空泵、机械真空泵、汽-水串联真空泵;极限真空度较低(700mmHg),用真空度要求不高、抽气量大工序。
除臭方法

除臭方法:1.燃烧法:通过强氧化反应,降解可燃性恶臭物质。
该方法主要适用于高浓度,小气量的可燃性恶臭物质的处理。
这种方法的净化效率高,恶臭物质被彻底分解掉,但设备易腐蚀,消耗燃料,成本高,处理中可能形成二次污染物。
2.氧化法:利用氧化剂氧化恶臭物质而脱臭的方法。
此方法适用于中低浓度的恶臭物质的处理,净化效率高,但需要氧化剂,处理费用较高。
3.吸附法:此方法使用溶剂溶解臭气中的恶臭物质而脱臭。
适用于高、中浓度的恶臭物质的处理,可处理大流量的气体,工艺最成熟,但净化效率不高,消耗吸收剂,污染物仅由气相转移到液相。
4.吸附法:利用吸附剂吸附恶臭物质除臭。
该方法适用于低浓度的、高净化要求的恶臭气体的处理,净化效率很高,可处理多组分的恶臭气体,但吸附剂费用昂贵,对待处理的恶臭气体要求高,,即具有较低的湿度和含尘量。
5.中和脱臭法:使用中和脱臭剂减弱恶臭感官强度的方法。
适用于需立即地、暂时地消除低浓度恶臭气体影响的场合,可尽快地消除恶臭的影响,灵活性大,但恶臭成分并没有被去除掉,且需投加中和剂。
6.生物脱臭法:这种方法主要利用微生物降解恶臭物质而脱臭。
适用于可生物降解的水溶性的恶臭物质的处理,脱臭效率高,脱臭装置简单,处理成本低廉,运行维护容易,可避免二次污染,但不能回收利用污染物。
常见的生物脱臭法有生物过滤脱臭法和活性污泥脱臭法两种。
生物过滤脱臭法按滤料的不同,又可分为生物滤池式和生物滴滤池式脱臭法。
活性污泥法则按气液接触方式分为曝气式和洗涤式活性污泥脱臭法。
氨精制废水的处理方法:1.吹脱法除氨:当废水中含有可挥发性物质(如硫化氢、氨气等)时,可以用向废水中通入蒸汽的方法将之提取出来,这就是“吹脱”,带出来的挥发性物质可以通过适当的方法加以回收利用。
工艺流程:放空↑回收的氨氮←氨氮回收←剩余污泥→剩余污泥↑废水→加入CaO调节PH→沉淀过滤→吹←蒸汽或热空气排放→反渗透处理→脱2. 将氨氮制成硫酸铵回收利用的废水治理技术:将氨氮制成硫酸铵回收利用的废水治理技术,是向富含氨氮的废水中加入碱液,使废水中的氨以游离态的氨存在,然后采用硫酸吸收氨,以(NH4)2SO4的形式回收氨氮。
脱臭工艺流程

脱臭工艺流程脱臭是指去除物质中的异味、臭味的工艺过程。
在日常生活中,脱臭工艺被广泛应用于家庭、工业、医疗等领域,以改善空气质量和提升生活舒适度。
脱臭工艺流程包括多种方法和技术,下面将介绍其中常见的几种脱臭工艺流程。
1. 物理吸附法。
物理吸附法是一种常见的脱臭工艺流程,通过吸附剂将异味、臭味物质吸附在其表面上,从而达到脱臭的效果。
常用的吸附剂包括活性炭、分子筛等。
在工业领域,常常使用大型的吸附塔或吸附床来进行脱臭处理,通过流体的循环往复,使得异味物质被吸附在吸附剂上,从而达到脱臭的效果。
物理吸附法脱臭工艺流程简单、成本低,但对于一些特殊的异味物质可能效果不佳。
2. 化学中和法。
化学中和法是利用化学反应将异味、臭味物质转化为无害的物质,从而达到脱臭的效果。
常用的中和剂包括次氯酸钠、过氧化氢等。
在工业领域,化学中和法通常通过喷淋、喷洒等方式将中和剂喷洒到异味源上,使得异味物质被中和或转化为无害的物质。
化学中和法脱臭工艺流程效果明显,但需要谨慎选择中和剂,以免产生新的污染物。
3. 生物降解法。
生物降解法是利用微生物对异味、臭味物质进行降解,从而达到脱臭的效果。
常用的生物降解剂包括细菌、酵母等。
在工业领域,生物降解法通常通过生物反应器、生物滤池等设备进行处理,将异味源送入生物反应器中,微生物对异味物质进行降解。
生物降解法脱臭工艺流程对环境友好,但需要控制好生物反应条件,以保证降解效果。
4. 热氧化法。
热氧化法是利用高温氧化将异味、臭味物质分解为无害的物质,从而达到脱臭的效果。
常用的热氧化设备包括焚烧炉、热氧化炉等。
在工业领域,热氧化法通常通过将异味源送入热氧化设备中进行高温氧化处理,将异味物质分解为二氧化碳和水等无害物质。
热氧化法脱臭工艺流程处理效果显著,但需要耗费大量能源,且对设备要求较高。
综上所述,脱臭工艺流程包括物理吸附法、化学中和法、生物降解法和热氧化法等多种方法和技术。
不同的脱臭工艺流程适用于不同的场景和异味源,选择合适的脱臭工艺流程可以有效去除异味、臭味,改善空气质量,提升生活舒适度。
生物除臭技术

生物除臭技术第1章概述1.1生物除臭技术的发展生物除臭技术是20世纪50年代发展起来的新兴除臭技术,是利用微生物的生理代谢活动降解恶臭物质,将其氧化成无臭、无害的最终产物,达到除臭的目的。
生物除臭早在1957年就在美国获得专利,70年代后,各国开始在这一领域开展广泛的研究,其中美国、日本、德国取得的成就最为显著,主要研究内容包括除臭的基本原理和方法、装置设备及操作工艺条件等。
80年代以来,已有各类微生物除臭的装置和设备开始运用于石油、化工、屠宰、污水处理等实际中,并取得明显效果。
生物除臭技术与目前采用的物理、化学法,例如燃烧、吸附、吸收和还原等相比较。
这些物理化学方法的工艺或设备较复杂,运行费用较高;用于处理某些恶臭废气时,效果不甚理想。
生物脱臭法通过不断改进完善,克服了前述物理、化学方法的缺陷,并显示出处理效率较高、适应性较广、工艺较简单以及费用较省等优点,成为治理恶臭的一个重要发展方向。
1.2生物除臭的原理气味物质的成分大多都是低分子脂肪酸、胺类、醛类、酮类、醚类以及脂肪族的、芳香族的、杂环的氮或硫化物,带有活性基团的这些物质被液相吸收后,特别易被生物氧化,当活性基团被氧化后,恶臭气味就消失了。
臭气经不同种类的微生物分解后,产物不一样.如含氮的臭气,经微生物的氨化作用后,分解为HN3。
又通过亚硝化细菌、硝化细菌的作用,进一步氧化为稳定的硝酸态化合物;而含硫的臭气经微生物分解后产生H2S,H2S可以被硫化细菌氧化为硫酸.生物除臭工艺就是基于这一原理,所以该方法要求被去除的臭味物质有好的水溶性。
微生物除臭过程分为三个步骤:(1)臭气同水接触并溶解到水中,臭气的有机物质由气相转移到液相(或固体表面液膜)中;(2)溶于水中的臭气通过微生物的细胞壁和细胞膜被微生物吸收,不溶于水的臭气先附着在微生物体外,由微生物分泌的细胞外酶分解为可溶性物质,再渗入细胞.在液相(或固体表面液膜)中的臭气成分被微生物吸附、吸收,恶臭成分从水中转移至微生物内;(3)进入微生物细胞的恶臭成分作为营养物质被微生物所氧化分解和同化合成,产生的代谢产物一部分溶入液相,一部分作为细胞物质或细胞代谢能源,还有一部分(如CO2)则析出到空气中。
精炼:脱臭脱蜡讲解

酸值
2.5
5
10
20
30
精炼率
物理
精炼
96
92
86
75
63
(%)
碱炼
93
88
78
58
38
二种精炼方法的成本
成本
化学精炼 物理精炼
1.2
2.0
FFA%
汽提公式
假设:待脱臭油是理想溶液,臭味组分为溶质 根据拉乌尔(Lavore)定律,可推导
间歇式 ln(V1/V2)= EPvAS/PO = KPvS/ PO
蒸汽 通汽速率与时间
要使臭味降到V2,需足够蒸汽量S,理论上1/1 E=1-1/e k’Ft
蒸汽量=通汽速率×时间 通汽速率↑,E↑,以油脂不飞溅为度 时间↑,E↑,但油脂聚合、热分解↑ 脱除定量臭味所需的蒸汽量S,随臭味含量的减少而增加
在脱臭最后阶段,要有足够时间和充足蒸汽量 当压力和通汽速率固定不变时,温度↑,则PV↑,时间↓ 蒸汽占油量
脂肪酸(馏出物)捕集器
真空
脱臭气体进口
瓷圈
冷脂肪酸进口
热脂肪酸出口
第六章 冬化
一 目的和原理 二 影响冬化的因素 三 脱蜡工艺与设备
夏化
一 目的和原理
冬化 脱蜡、脱硬脂 脱蜡——从油中脱除或提取蜡质 脱硬脂—将熔点高的甘三酯组分结晶并分离
提高食用油品质 综合利用蜡、硬脂资源
蜡
熔点80℃ 40℃以上,溶于油脂,压榨还是浸出毛油,都含蜡 常温(30℃)以下,溶解度低,析出蜡的细晶粒而成为很稳定的油溶胶,
244.4 256.0
263.8 275.5
100 × 133.3 176.5
脱臭工艺流程

脱臭工艺流程脱臭工艺是去除原料中不良气味的过程,广泛应用于食品、制药、化工等领域。
以下是脱臭工艺的主要流程:1.原料接收:首先,对原料进行接收和检查,确保原料的数量、质量和品种符合工艺要求。
2.预处理:对于不同种类的原料,可能需要进行清洗、破碎、混合等预处理操作,以便更好地进行脱臭处理。
3.脱臭:这是脱臭工艺的核心步骤。
通过特定的脱臭技术,如蒸馏、吸附、萃取等,将原料中的不良气味成分去除。
这一步骤中,控制适当的温度、压力和时间是非常重要的。
4.冷却:脱臭后的产品需要进行冷却,以降低其温度并稳定其性质。
冷却的方式和温度需要根据具体的产品和工艺来确定。
5.分离:对于一些与不良气味同时存在的杂质或沉淀物,需要进行分离操作,以获得纯净的产品。
分离的方法包括过滤、沉降、离心等。
6.收集产品:经过上述步骤处理后的产品进行收集,以便进一步处理或存储。
收集过程中需要注意产品的纯净度和安全性。
7.废物处理:在脱臭过程中产生的废物,如废气、废水等,需要进行适当的处理,以避免对环境造成污染。
废物处理的方法应根据具体的废物种类和处理要求来确定。
8.质量检测:对脱臭后的产品进行质量检测,以确保其符合预定的质量标准。
质量检测的内容可以包括产品的外观、气味、成分等。
9.包装储存:经过质量检测合格的产品进行包装储存,以避免外界环境对其造成不良影响。
包装材料应具有良好的密封性、阻隔性和安全性。
10.交付运输:最后,将包装好的产品交付给客户,完成整个脱臭工艺流程。
在交付过程中,应确保产品的安全性和完整性。
以上是脱臭工艺流程的主要步骤。
在实际操作中,应根据具体的原料种类、产品要求和工艺条件进行适当的调整和优化。
同时,为确保产品的质量和安全性,每个步骤都应严格控制工艺参数并进行有效的质量控制。
脱臭工艺流程
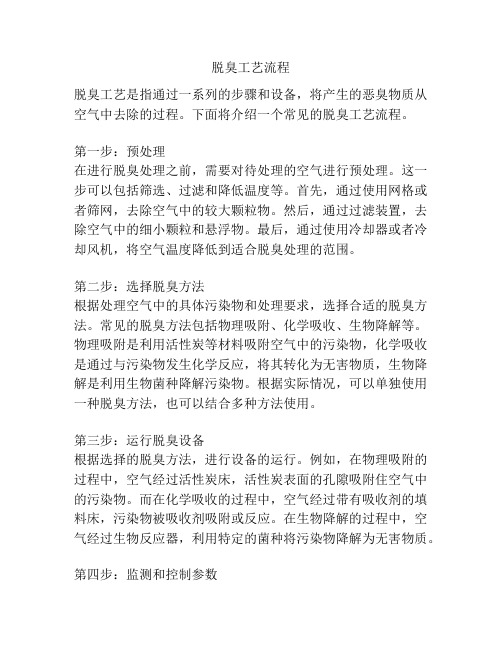
脱臭工艺流程脱臭工艺是指通过一系列的步骤和设备,将产生的恶臭物质从空气中去除的过程。
下面将介绍一个常见的脱臭工艺流程。
第一步:预处理在进行脱臭处理之前,需要对待处理的空气进行预处理。
这一步可以包括筛选、过滤和降低温度等。
首先,通过使用网格或者筛网,去除空气中的较大颗粒物。
然后,通过过滤装置,去除空气中的细小颗粒和悬浮物。
最后,通过使用冷却器或者冷却风机,将空气温度降低到适合脱臭处理的范围。
第二步:选择脱臭方法根据处理空气中的具体污染物和处理要求,选择合适的脱臭方法。
常见的脱臭方法包括物理吸附、化学吸收、生物降解等。
物理吸附是利用活性炭等材料吸附空气中的污染物,化学吸收是通过与污染物发生化学反应,将其转化为无害物质,生物降解是利用生物菌种降解污染物。
根据实际情况,可以单独使用一种脱臭方法,也可以结合多种方法使用。
第三步:运行脱臭设备根据选择的脱臭方法,进行设备的运行。
例如,在物理吸附的过程中,空气经过活性炭床,活性炭表面的孔隙吸附住空气中的污染物。
而在化学吸收的过程中,空气经过带有吸收剂的填料床,污染物被吸收剂吸附或反应。
在生物降解的过程中,空气经过生物反应器,利用特定的菌种将污染物降解为无害物质。
第四步:监测和控制参数在运行过程中,需要对脱臭设备的运行参数进行实时监测和控制。
主要监测参数包括进出口空气浓度、温度、湿度等。
通过对这些参数的监测,可以及时调整设备的运行参数,使其达到最佳处理效果。
第五步:处理副产物在脱臭过程中,会生成一些副产物。
例如,在物理吸附过程中,活性炭吸附了大量的污染物,需要定期更换或再生活性炭。
在化学吸收过程中,吸附剂也需要定期更换或再生。
这些副产物需要进行处理和处置,以防止二次污染。
第六步:排放处理后的空气经过脱臭设备处理后的空气,应符合国家和地方的排放标准。
在排放之前,需要对处理后的空气进行监测,确保其达到排放标准。
如果空气不符合排放标准,需要进行二次处理或者采用其他措施进行改善。
- 1、下载文档前请自行甄别文档内容的完整性,平台不提供额外的编辑、内容补充、找答案等附加服务。
- 2、"仅部分预览"的文档,不可在线预览部分如存在完整性等问题,可反馈申请退款(可完整预览的文档不适用该条件!)。
- 3、如文档侵犯您的权益,请联系客服反馈,我们会尽快为您处理(人工客服工作时间:9:00-18:30)。
脱臭
纯净的甘油三酯是无气味的,但用不同方法制取的天然油脂都具有不同程度的气味。
这些气味俗称为臭味。
它们有些是天然的,有些是制取加工中产生的。
油脂中的臭味物质主要是醛、酮、FFA、不饱和碳氢化合物等。
在油脂制取及加工中也会产生新的臭味,如焦糊味、溶剂味、漂土味、氢化异味等。
油脂中除FFA以外,其余臭味物质的含量很少,仅0.1%左右,但起着重要的作用。
1.脱臭目的:脱臭不仅可除去油中的臭味物质,提高烟点。
改善食用油的风味,能除去过氧化物及其分解产物,除去霉烂油料中蛋白质挥发性分解产物,除去小分子量的环芳烃及DDT等残留的农药。
同时可破坏一部分色素。
2.原理:油脂脱臭是利用油脂内臭味物质和甘三酯的挥发度有很大的差异,在高温、高真空条件下借助水蒸汽蒸馏除去臭味物质的过程。
3.影响因素:①温度:增加温度会使臭味物质蒸气压迅速增加,有利于脱臭。
同时可降低直接蒸汽的用量,但温度太高会造成油脂中较多的生育酚、甾醇等进入馏出物,会促使油脂水解而增加损耗,产生热聚合。
②真空度:减少直接蒸汽的用量,减少脱臭时间,降低油脂的水解损失,防止油脂氧化。
③通汽速度和时间
④脱臭器的结构
⑤脱臭油的成品油质量
⑥直接蒸汽质量:除氧、干燥、不夹带金属离子
4.脱臭与油脂产品品质的关系
脱臭对油脂产品的品质起着重要影响,尤其对色拉油的烟点、色泽以及少量过氧化物及其分解产物的除去具有很大的影响。
关于脱臭及脱臭过程炼
耗的讨论
•一、脱臭的原理
•二、脱臭的损耗
•三、影响脱臭及其炼耗的因素•四、我车间现在的脱臭的参数
•脱臭的原理
•脱臭是利用油脂内臭味物质和甘油三酸酯的挥发度的差异,在高温高真空条件下借助水蒸气蒸馏脱除臭味物质的工
艺过程。
•油脂中的臭味物质主要有低分子的醛、酮、游离脂肪酸、不饱和烃类等。
脱臭不仅可以除去油中的臭味物质,提高油脂
的烟点,改善食用油的风味,还能除去过氧化物及其分解产物。
•在相同温度下,各种臭味物质的蒸汽压有较大的不同,其中较难挥发的是脂肪酸和长碳链的烷烃。
但是在常压下脱出这
些臭味组分仍是不可能的,常压下游离脂肪酸的沸点一般在300℃以上,在这个温度下,油脂会发生氧化分解和热聚合,所以脱臭必须在高真空的条件下进行。
脱臭的损耗
•待脱臭的油中一般臭味物质已经很少了,一般不超过油脂量的
0.1%~0.5%,但是实际上脱臭的损耗远远高于这个数据,这其中
包括蒸馏损耗和飞溅损耗。
•蒸馏损耗
–油脂中低分子醛、酮、不饱和碳氢化合物以及游离脂肪酸等蒸馏引起的损耗。
这一部分的损耗是我们希望除去的。
当游离脂肪酸的含量降到0.015~0.03%时,油脂的水解速
度等于脂肪酸的蒸馏速度。
这一部分的损耗一般占脱臭总
损耗的20~30%。
–油脂中部分的生育酚和甾醇等不皂化物的损耗,这一部分并不是我们需要除去的,但是在脱臭的过程中是不可避免
的。
•飞溅损耗
•直接蒸汽以一定的速度喷入油中,并通过油层表面时,蒸汽本身的动能加上蒸汽在高真空状态下膨胀产生的动能,足以使相当数量的油脂液滴冲出到脱臭塔的排气管内,而且排气管的截面积小于脱臭器的截面积,使排气管内流速增加,包油脂液滴带到脱臭器外。
影响脱臭及炼耗的因素
•脱臭温度
•增加温度会使臭味物质的蒸汽压迅速升高,有利于臭味物质的挥发。
而且提高温度还有利于过氧化物和类胡萝卜素的分解,有热脱色的作用。
•温度过高也会产生不利的影响:会增加油脂的水解速度,生成的水解产物被蒸馏出去,增加蒸馏的损耗;会使较多的生育酚、甾醇等不皂化物被挥发,240℃以上有50%的生育酚被蒸馏出,280℃以上有70%被蒸馏出去,不仅增加蒸馏损耗,而且由于天然抗氧化剂的损失,降低了油脂的氧化稳定性;过高的温度还会产生热聚合,不仅降低油脂的品质,生成的聚合物还有一定的毒性。
•此外,油脂在高温条件下会发生一些副反应:酯交换作用;不饱和脂肪酸的异构化,造成反式酸及共轭酸的生成。
•一般我一车间控制的脱臭温度在245℃,便可以满足脱臭和热脱色的作用。
•脱臭的真空度
•为了防止油脂在高温的条件下氧化,脱臭操作都要求有较高的真空度,操作的压力一般在3~5mba。
真空度越高,所需的直接蒸汽量就越少,脱臭所需的时间也就越少,同时还可以有效地避免油脂水解引起的蒸馏损耗。
但是真空度过高,所需的设备成本和操作成本都会增加。
脱臭时间
•脱臭必须保证有足够的时间使热敏性色素最大限度的分解并除去。
脱臭的时间受气提水蒸气的速率、脱臭温度和脱臭真空度的影响。
气提水蒸气的速率越大、脱臭温度越高和脱臭真空度越高,脱臭所需的时间就越少。
在保证脱臭效果的前提下,脱臭的时间越短越好,时间长了会导致油脂的热聚合,同时可能增加反式酸的生成。
•脱臭的气提量
•脱臭的气提量增大,蒸汽的流速增高,有利于脱臭过程中的气、液传质过程的进行,可以减少脱臭的时间。
但是容易引起中性油的飞溅损失。
此外还要保证气提蒸汽的质量,防止蒸汽中带水,保证蒸汽干燥,不含空气。
直接蒸汽的用量一般为油重的1%左右。
•脱臭塔的结构
•脱臭塔内有防止飞溅油和蒸馏液回流结构对减少飞溅损失和保证脱臭效果有着明显的效果。
•脱臭前后油脂的质量
待脱臭油必须很好的脱胶、脱酸和脱色处理,除去胶质、色素和微量金属才能有很好的成品油。
如果成品油要求的品质很高,那么脱臭的成本和脱臭的损耗都会较大。
金属离子的影响
油脂中的金属离子主要有铁离子、铜离子、锰离子、钙镁
离子等,这些微量的金属离子是油脂氧化的催化剂,尤其在高温条件下,影响尤其特别。
可以通过添加磷酸、柠檬酸等使金属离子钝化。
一车间现阶段脱臭的参数及脱臭的损耗•现在已一车间的豆油为例说明
•脱臭温度:245℃~250℃
•脱臭时间:2小时左右
•脱臭真空度:3~5mba
•脱臭的气提压力:第一层:0.6~0.8;第二~五层:0.2~0.4;第六层:0.4~0.6层
•待脱臭油的品质要求:AV:约0.2;含磷:1~2ppm;脱色色泽视成品油的要求不同而不同;
•脱臭的损耗一般约在0.3%~0.1%
•一般脱臭馏出物的酸价和皂化值的比率应小于0.67,认为脱臭的损耗比较好,否则可以认为有较多的过量中性油混入脱臭馏出物中,损耗较大。