车身冲焊件孔位设计规范
汽车焊接要求

汽车焊接要求一、焊接方法的应用1.点焊1)实现点焊的空间要求:⏹焊接面尽可能是平面;⏹有足够的焊钳进出零件的空间;⏹能够实现点焊面与焊钳极臂垂直;⏹有电极焊接时的运动空间;⏹有足够的可视空间,至少能看见一个极臂与板件的接触点;⏹零件不能与焊钳钳身、悬挂钢缆、焊钳转盘相干涉。
2)板厚的要求在产品设计过程中,多使用两层板点焊,减少三层板焊接,杜绝三层以上板件搭接点焊,对于点焊搭接料厚要求如下:≥440MPa高强度钢板以双面镀锌钢板计,超出以上范围的钢板搭接,要求采用固定点焊或弧焊连接实现。
3)三层板点焊搭接顺序要求:考虑到三层板点焊过程中焊核偏移对焊接质量的影响,在设计中尽量采用搭接形式1。
当镀锌刚板或高强刚板与低碳钢板混合焊接时,尽可能使镀锌钢板或高强钢板夹在低碳钢板之间,以增强可焊性,减少锌层对电极的污损和粘连。
4)搭接料厚一致性建议在同道工序,能够使用同一型号焊钳焊接的焊点,焊接料厚尽可能接近,以便于参数的统一。
5)搭接宽度要求搭接边大小应大于12mm,料厚大于等于3mm情况下,搭接边宽度应达到16mm,焊接料厚越大,搭接宽度越宽。
6)焊点间距要求长、直焊缝焊点间距要求一般在50~80mm之间,局部强度要求较低的位置,如车门外板加强板与门外板的搭接点焊,距离可增大至100mm;螺母板及部分小件需要在较小的平面内达到连接强度要求,焊点可依实际情况增加,点距相应缩短。
7)焊点排布要求相同位置第一道焊点与第二道叠加的焊点在位置上要求尽可能均匀交错,避免在同一位置、或距离较近位置第一道、第二道焊点叠加,影响焊接强度。
弧焊亦如此。
尽可能避免在同道工序内,点焊、弧焊等各种焊接方式反复交叉,尽可能实现弧焊工序、螺柱焊工图○1 图○2 图○4 图○3 序的集中,减少焊接弧光的干扰,并利于生产线的编排和生产组织。
8) 焊点数量要求焊点数量以满足强度要求为准,过多、过密的焊点只能增加焊接的成本,同时过密的焊点由于焊接分流的加大,焊接强度降低。
(完整)焊装车身定位要求

SE分析手册编号:SE—BP—#—003类别:定位第 1 页共 4 页名称:焊装车身定位要求目的:规范车身定位孔孔径、位置,适应平台化及生产线柔性要求内容:1。
定位孔孔径设置原则➢优先选择原有共线生产车型的定位孔径(参考车身主定位孔数据库);➢新生产线车身主定位孔可在Φ30、Φ25、Φ20三种孔径中选择,优先选择顺序为Φ30(为焊、涂、总共用的吊装孔)、Φ25、Φ20,如无法实现,不得小于Φ16;➢前后主定位孔共四个,建议孔径尽可能选择一致;➢前定位孔使用圆孔,后定位孔使用长圆孔,长圆孔方向沿X轴方向,相应规格为30×36、25×31、20×26、16×20;➢主定位孔采用翻边孔,以保证强度,Φ30孔翻边高度为6~6.5mm,其它翻边孔直边长度大于3mm,对于板材强度较弱的孔,要考虑结构加强;➢主定位孔中心线方向需与Z向一致;➢翻边孔要考虑料厚方向,保证内径与孔径规范相一致。
2. 采用锁紧销的定位孔空径和纵梁宽度的关系➢光孔——单勾销(COMAU标准)因车身主定位孔在主焊线上需使用勾销进行定位(如右图),针对勾销对定位孔及纵梁宽度提出如下要求:No.定位孔径D 孔径范围纵梁槽底宽度L1¢20¢20-23≥16。
5mm×22¢25¢24-28≥18mm×23¢30¢29—32≥21mm×24——¢33-40≥25mm×2※纵梁槽底宽度指直线宽度(不含R角).➢翻边孔——双钩销(SMC标准)⏹当C=30时(即采用¢30定位销时),要求B≤40,A≥53;⏹翻边总高度D≤9,翻边孔半径E≤R3。
5;⏹纵梁内部距纵梁底部40mm空间无其它零件遮挡,以满足定位销的伸入空间;D LSE分析手册3。
定位孔位置➢优先选择原有共线生产车型的定位位置;➢主定位孔要设置在车身结构不易变形位置(包括冲击变形和热变形),如前舱前定位孔较后定位孔位置上更容易变形;➢主定位孔优先选择前后纵梁的主定位孔;➢左右对应定位孔间距要超过700mm,以满足机械化传送的需求.➢所选择的主定位孔能在单件及分总成上实现基准传递;前后主定位孔中心高差不要超过300mm,防止车身下落时车身的前后摆动对先接触到的定位孔产生过大的冲击,引起精度偏差;SE分析手册编号:SE—BP—#-003类别:定位第 3 页共 4 页➢ 通常车身主定位孔选择前舱后部定位孔、后地板后部定位孔作为车身的主定位孔(如下图);➢ 带独立车架的SUV ,车身主定位孔的选择通常在车身与车架的最前和最末安装点附近;➢ 左前定位孔为车身定位的主定位孔,优先选择左侧定位(即采用左侧两定位孔实现定位,右侧定位孔辅助定位)。
车身孔位设计经验

⑴ 过孔(图1-2-1)凸焊螺母:d2= d1+2mm,如果有第三层或第四层依次类推,特殊情况可调整;凸焊螺栓:d2= d1+2mm,如果有第三层或第四层依次类推,特殊情况可调整;⑵ 卡扣孔⑶ 焊装定位孔⑷ 涂装工艺孔d1=d(螺母公称直径)+0.5mm;如果有两层或两层以上的钣金,则第二层钣金件的孔直径为:根据电器和内外饰的卡扣规格,卡扣孔分圆孔、方孔和腰形孔三种:公差:-0.2~+0.2M10和M10以下的凸焊螺母在白车身上对应的孔直径(d1)为:d1=d(螺母公称直径)+1mm;M10以上的凸焊螺母在白车身上对应的孔直径(d1)为:如果有两层或两层以上的钣金,则第二层钣金件的孔直径(d2)为:d1=d(螺母公称直径)+2mm;凸焊螺栓在白车身上对应的孔直径(d1)为:公差:0~+0.2地板漏液孔取φ32、φ35、φ50三种规格的孔,根据车型尺寸选取;涂装夹持孔取φ30(0~+0.2),3.2㎜的翻边;其他部件的涂装工艺孔,根据实际状态确定。
公差:0~+0.2、±0.4,当涂装工艺孔用作焊接工艺孔时公差取0~+0.2,其他取±0.4 。
a 卡扣用的圆孔孔径有以下几种:Φ5、 Φ6.5、Φ7、Φ8、Φ8.5、Φ9、Φ10;公差:±0.2。
公差:±0.2。
公差:±0.2、±0.4,根据安装件的装配精度要求选择公差。
c 卡扣用的腰形孔规格有以下几种:φ5×7、Φ5×8、φ6×8、φ6×11、φ7×10、φ7×11、φ7×12、φ9×14;公差:-0.2~+0.2b 卡扣用的方孔规格有以下几种:L7×7方形孔、L8×8方形孔、L8.5×8.5方形孔、L5×21矩形孔、L5×30矩形孔、L6×11矩形孔、L6×20矩形孔、L6×21矩形孔、L8×13矩形孔、L8×25矩形孔、L10×12矩形孔;焊接定位孔借用其他孔时,孔径即为该孔孔径;当该孔仅为焊接定位用时,根据孔的位置和结构,孔径选取φ6、φ8、φ10、φ12、φ16、φ20、φ26、φ32、φ40的尺寸;⑸ 线束过孔⑹ 自攻螺钉孔根据线束形状和护套尺寸,线束过孔的形状分圆孔和腰形孔两种。
定位基准设计规范

的布置,便于夹具设计; 13、基准的选择应具有连续性和关联性。
3.4.2 考虑可重复性和重复操作性 1、基准特征自身必须在制造过程中保持尺寸稳定; 2、基准特征必须具有可重复性,不会因装配等而变化; 3、基准应该对各种误差不敏感; 4、基准可以选择在装配孔、焊接面、压合面、粘接面等装配面上。
3.3定位系统设计原则
3.3.1遵循3-2-1定位准则 1、在刚体面积最大的投影面上布置不在同一直线上的三个定位基准; 2、在面积次大的投影面上布置两个定位基准; 3、在面积最小的投影面上布置一个定位基准; 4、为了保证定位稳定,这些点之间的距离应尽可能大,以占据长度方向2/3至5/6为佳。
3.3.2网格平行性准则 基准系统要求建立起零件自身的坐标系--零件坐标系,并以此作为基础。零件坐标系 是以整车坐标系为基础建立起来的,有下面两种建立方式:
图3
3、4 定位系统设计所考虑的因素
3.4.1 考虑功能性 1、基准应该考虑选择在零件装配的配合面上; 2、基准是车身制造和检验的基础,基准本身的精度要求要高; 3、选择基准应该考虑使其装配误差最小化; 4、零件的基准应该能够代表实际零件的某些特征关系; 5、选择基准应考虑与装配工艺相适应; 6、基准应选择在尺寸相对稳定的功能区域上; 7、基准所在的平面应尽可能覆盖整个零件; 8、再小的零件选择基准也要尽可能考虑定位孔; 9、考虑钣金件易变形特性,选则基准时要考虑选择防止变形的夹持点与支撑点,原则是300mm距离左
3.4.3 考虑一致性和继承性 1、设计基准与制造基准统一; 2、单件装配、总成装配的定位基准统一; 3、建立的基准体系应该在零件的制造、检测和装配过程中共用且一致; 4、零件在冲压过程中的基准、零件检具基准、工装基准必须一致,定位基准信息; 5、要与设计,冲压,焊装,总装以及质量部门共享; 6、选择基准不仅要考虑单件焊接加工要求,而且还要考虑后续装配过程要求; 7、焊装后的总成应尽可能采用组成零件的部分基准点作为总成的基准点,
车身焊接信息规范设计指南

焊接信息规范设计指南主要讲述了车身在设计过程中所用到的焊接方式,焊接过程中的主要参数以及注意事项。
并以图例的形式表示了这些参数。
本指南着重讲解了焊接过程中需要关注的内容。
1点焊焊接信息规范设计1.1设计原则⑴应选择具有良好焊接性的母材;⑵焊接件应保证足够的强度、刚度和使用寿命焊接接头的强度校核可按公式σ≤(σ’)来计算;式中:σ为焊接接头静载强度计算值σ’为焊接接头许用应力⑶焊接工作量应最少;⑷易于操作,应为焊接创造良好的操作条件;⑸尽量采用实用技术,机械化或自动化焊接。
焊点布置规则应在保证强度的前提下,焊点数量应最少,点焊件应尽量采用带弯边的开敞板件。
例如下面两种设计方法中,图1-1-1是合理的,图1-1-2图1-1-1合理图1-1-2不合理1.2设计参数⑴边距边距是焊点到搭接面边缘的距离.如图1-2-1中AB段所示:AB图1-2-1焊点边距⑵搭接量搭接量是搭接面的宽度,通常是边距的两倍.如图1-2-2所示的线段CD的距离。
图1-2-2焊接搭接量搭接量是边距的两倍,推荐的最小搭接量见下表1-2-1:表1-2-1接头的最小搭接量⑶点距点距是两个焊点之间的距离如下图1-2-3中线段EF 所示:图1-2-3焊点点距点距即相邻两点的中心距,其最小值与被焊金属的厚度、导电率、表面清洁度、以及熔核的直径有关。
下表1-2-2为推荐的最小点距。
表1-2-2焊点的最小点距1.3点焊接头规范⑴点焊接头的尺寸点焊通常采用搭接接头和折边接头。
接头可以由两个或两个以上等厚度或不等厚度的工件组成。
在设计点焊结构时,必须考虑电极的可达性,即电极必须能方便地抵达构件的焊接部位。
同时还应考虑诸如边距、搭接量、点距、装配间隙和焊点强度诸因素。
边距的最小值取决于被焊金属的种类、厚度和焊接条件。
对于屈服强度高的金属、薄件或采用强条件时可取较小的边距值。
点焊接头的尺寸应符合下表1-3-1的标准表1-3-1点焊接头的尺寸图1-3-1距离示意图图1-3-2间距注 a.不同板厚零件焊接时,尺寸C 按薄件选取b .三板焊时尺寸a 和d 应增加15%-20%c .当R >δ时,尺寸a 应适当放宽⑵点焊应用与焊点设计如表1-3-2所示:表1-3-2点焊应用与焊点设计注:a.最小板厚0.1mmb.两板厚比小于3⑶注意事项最后一个焊点到非焊接边的距离不得大于12mm 。
汽车焊接夹具定位设计规范化

汽车焊接夹具定位设计规范化陈岩(广东福迪汽车有限公司)摘要:从“N-2-1”定位原理、基准统一、定位结构等各方面论述汽车焊接夹具定位设计贵规范化。
重点描述定位结构规范化,制定非标设计设计规范,缩短汽车焊接夹具设计周期,降低设计成本。
主题词:汽车焊接夹具基准定位设计结构规范化Auto Welding Jigs Design of Orientation standardizationChen yan(Guangdong Fudi Automobile Co.,Ltd)Abstract: Discuss on auto welding jigs design of orientation from “N-2-1”principle of orientation、benchmark unite、structure of orientation. Especially for describing structure of orientation standardization, establish nonstandard of design into standardization, in order to shorten period of auto welding jigs design, reduce design cost.Key words: Auto welding jigs, Benchmark,Orientation of design, Structure of standardization1 前言国内汽车行业近几年的快速增长,带动了国内汽车焊接夹具制造业的快速成长。
基本每个新车型投产,均需要投入相应的焊接夹具。
按目前市场情况看,从新车型开发到推进市场,要求周期短,进而对焊接夹具设计、制造、调试提出更高的要求。
汽车焊接夹具的功能是为了实现车身零件的正确装配,保证零件正确搭配和完成焊接。
车身焊接工艺标准及参数设置

•
• 焊接时间 见初选工艺规范表 • 预热电流预热时间 对于淬透性较大,电导率、热导率较高的、较厚 板材,可通过调整电流缓升或缓降以达到预热或缓冷的目的.一般 5~15周波 • 冷却保持时间 对于1~3mm的钢板,其冷却结晶时间一般为5~20周 波 • 休止时间 休止时间为电极开始提起到电极第二次开始下降的时间, 休止时间的长短影响连续打点的速度。一般5~8周波
4、焊点间距的一般要求 1)焊点的点距应在保证焊缝强度和技术要求的前提下点距尽可能大些,焊大 件和组合件时,点距可以适当大些,一般不小于35~40mm,(推荐一般受力 部件50~60),在一些非受力部件还可加大到70~80mm ,生产中可根据产品 的保安和重要性具体确定点距值。后面的章节有专门针对产品的保安和重要 性在焊接质量的讨论。 2)焊点间距e应均匀,允差为emax/emin≤1.5。焊点间距 不能小于表中的最 小间距,以免产生分流; 对于多层焊,焊点距增(20~25)% 3)焊接构钢时的点距: 焊件厚度mm 1 2 25 3 30 4 40 6 60
• • • b = 4δ+8 (当δ1<δ2 时,按δ2计算 ) 其中 b ——搭边宽度,mm δ——板厚,mm
3、点焊接头的最小搭边宽度和焊点的最小点距
点焊接头的最小搭边宽度和焊点的最小点距 单位:mm 项目 参数值 最薄板件厚度 0.5 0.8 1.0 1.2 1.5 2.0 2.3 3.2 单排焊点最小搭边宽度 11 11 12 14 16 18 20 22 双排焊点最小搭边宽度 22 22 24 28 32 36 40 42 焊点的最小距 9 12 18 20 27 35 40 50
氩弧焊身及分总成
其中电阻点焊因为对低碳钢薄板适焊性强,在汽车车身制造 过程中被广泛应用; 下面针对这一典型工艺进行深入地讨论:
汽车车身板件焊接操作技术解析——以对接焊、填孔焊为例

随着汽车技术的不断发展,小型客车车身的结构由车架式车身逐步转变到整体式车身结构,整个车身形状都是由薄钢板冲压制成,再通过各种连接方式形成一个整体。
在车身材料的选择方面,20世纪70年代中期以后,高强度低合金材料、超高强度材料、铝合金材料及镀层材料逐渐代替了原有的低碳钢板材质。
钢材的厚度也发生了很大的变化,外板材零件的厚度由0.9 mm 下降到0.7 mm, 结构零件的板材从3 mm 下降到1.2 mm ~2 mm 。
以一台后部发生撞击的事故轿车为例,后翼子板(厚度通常为0.7 m m )发生严重变形,需要重新更换该零件,车身的整个侧围是一个整体,整体更换侧围工时和成本均较高,因此,维修改事故车采用切割更换的方式,在后翼子板的C 柱上端位置和车门槛和后尾灯等位置需要切割变形零件,新的零件采用气体保护焊对接焊及填孔焊完成焊接作业,本文对气体保护焊对接焊、填孔焊操作技术进行解析。
1 焊接种类及其在车身维修中的应用汽车车身板件维修应用焊接时,根据焊接接头所处的状态不同,可分为压焊、熔化焊和钎焊。
(1)压焊。
先对金属施加压力使其压紧,同时通过大电流形成的电阻热将被焊金属熔化形成焊点。
压焊焊接时,从操作方式来说,加热和加压并存。
在各种压焊方法中,电阻点焊(压焊中的一种)是汽车制造业不可缺少的焊接方法,在汽车修理业中应用也较为广泛。
(2)熔化焊。
将金属件加热到熔点,形成熔池,然后冷却结晶,形成焊点。
实施熔化焊时,只需将金属加热形成熔池,不需要加压。
目前,在车身维修作业中,气体保护焊(熔化焊中的一种)应用最为广泛。
(3)钎焊。
在需要焊接的板件上,将熔点比它低的焊料熔化(被焊板件不需熔化),而使被焊板件形成连接。
根据钎焊材料的温度,可分为软钎焊和硬钎焊。
汽车车身维修中,应用的主要是铜焊,用于车身零件接口处密封,可防止水分和灰尘渗入,使用黄铜焊条作为焊料,属于硬钎焊。
2 焊接在车身零件连接中的优缺点(1)由于焊接的形状不受限制,它适合于连接整体式车身结构,焊接后仍保持车体的完整性。
车身结构设计规范

车身结构设计规范1.范围本规范归纳了白车身结构设计的一些基本方法和注意事项。
2. 规范性引用文件下列文件对于本文件的应用是必不可少的。
凡是注日期的引用文件,仅注日期的版本适用于本文件。
凡是不注日期的引用文件,其最新版本(包括所有的修改单)适用于本文本。
GB 20182 商用车驾驶室外部突出物GB 15741 汽车和挂车号牌板(架)及其位置,汽车罩(盖)锁系统GB 11568 汽车罩(盖)锁系统3.工艺要求:3.1、冲压工艺要求3.1.1 在设计钣金件时,应使钣金件有拔模角度,最小3度。
如果拉延深度越大拔模角度需要越大,如果有负角的话,就必须增加一道整形工序,大大增加成本。
3.1.2在设计钣金件时,对于影响拉延成型的圆角要尽可能放大,原则上内角R≥5,以利于拉延成型;对于折弯成型的圆角可以适当放小,原则上R≈3即可,以减小折弯后的回弹。
3.1.3在设计钣金件时,考虑防止成型时起皱,应在适当的地方(如材料聚集处)布置工艺缺口,或布置工艺凸台、筋。
3.1.4孔与孔,孔与边界距离应大于2t(t=钣金料厚),若在圆角处冲孔,孔与翻边的距离应大于R+2t。
开孔时尽量不要开在倒角面上,以避免模具刃口早期磨损。
3.1.5 三面或多面交汇的尖角处在倒圆时应尽量倒成球形。
3.2 焊接工艺要求3.2.1 焊接搭接边重叠部分的宽度一般在14—16mm为佳,最小不小于12mm;3.2.2考虑焊接时应考虑焊接工具的接近性。
3.2.3对于无法焊接的内板,可以考虑开焊接工艺过孔,一般要求Φ30以上;3.2.4焊点的距离一般是60-80mm,2.2.5 如果焊接处对于防水、隔音、隔热等性能要求较高时,焊接处需要涂焊接结构胶3.3 涂装工艺要求I3.3.1考虑在侧围下部和车门最下部开漏液孔;2.3.2考虑在地板总成低洼处布置漏液孔。
3.4 装配工艺要求3.4.1考虑零部件装配时装配工具的接近性3.4.2考虑零部件自身安装或拆卸的方便性;3.4.3对于安装工艺过孔,应考虑做成翻边孔,以增加零件本身的刚度,以及不伤手和工具4. 性能要求4.1 车身作为整车的基础结构,给各个功能件提供安装和固定的位置,并具有足够的刚度和强度,以保证所有部件相互位置的正确与稳定。
车身冲焊件孔位设计规范

车身冲焊件孔位设计规范车身冲焊件孔位设计规范1范围本规范规定了长安公司车身冲焊件孔位的设计方法、参数及质量保证等。
本规范适用于长安公司车身冲焊件孔位的设计。
2 车身冲焊件孔位概述2.1 车身冲焊件孔分类2.1.1 按照用途分类:定位孔、功能孔(结构安装孔,装配过孔,焊接过孔,涂装工艺孔-电泳工艺孔、排水工艺孔、排气工艺孔、注蜡工艺孔,减重孔)2.1.2 按照加工精度分类:A级——为联结而设计的孔径尺寸(如连接板上的螺钉过孔、销孔、铆钉孔、装配件的螺母孔和螺钉过孔、夹具定位孔等)。
B级——次要孔径尺寸(如缆索、线束过孔、焊接电极让位孔、排水孔、减重孔等)。
2.2 冲压件孔形分类2.2.1 冲压件圆孔(等级A和B)冲压件圆孔型式和尺寸公差见图1和表1的规定。
图1表12.2.2 冲压件长圆孔(等级A和B)冲压件长孔型式和尺寸公差见图2和表2的规定。
图2表22.2.3 冲压件带缺口的圆孔 (仅当定义了一个公差等级时)冲压件带缺口的圆孔型式和尺寸公差见图3和表3的规定。
图3 表32.2.4 冲压件矩形孔 (等级A 和B )冲压件矩形孔型式和尺寸公差见图4和表4的规定。
图42.2.5 冲压件正多边形孔(仅当定义了一个公差等级时)冲压件正多边形孔型式和尺寸公差见图5和表5的规定。
图53 设计准则3.1坐标尽量取整原则:冲焊件的尺寸标注一般从坐标系的原点开始,带有公差的形状尺寸和功能尺寸,必须总是与坐标系的原点具有某种关系。
为了方便测量和质量控制,孔径形状及位置尺寸应圆整,孔径应符合优先系列数值。
3.2符合工艺性原则:设计各种孔要考虑孔的冲压方向,尽量将孔位都设计在同一冲压方向上。
3.3定位基准统一原则:a)设计基准与工艺基准统一;b)冲压、检测、装配焊接(即通常说的模、检、夹具)定位基准统一;c)单件装配与总成装配的定位基准统一:组装后的总成应尽可能采用组成零件已有基准点中的部分基准点作为总成的基准点,即基准点的继承性。
浅谈车身冲焊件定位基准设计

124AUTO TIMEAUTOMOBILE DESIGN | 汽车设计浅谈车身冲焊件定位基准设计王国鹏 蒋伟光 黄建茌上汽通用五菱汽车股份有限公司 广西柳州市 545000摘 要:车身是汽车的重要组成部分,所有零部件均是以车身为载体进行装配的,其尺寸精度将影响功能部件的性能发挥、外观是否均匀、是否有异响等。
车身一般由400-600个冲压件通过夹具定位,从分总成到总成、再到总拼焊接而成,夹具设计则是根据给定的MCP/MCS 图或定位基准进行的,基准体系可以控制单件、分总成、总成、装配及检测过程中基准位置一致,状态稳定,从而保证有功能要求的安装孔、安装面、切边等尺寸受控,定位基准设计的好坏会直接影响车身尺寸精度。
本文简要介绍冲焊件定位基准设计相关依据和方法,为工程技术人员在项目开发中提供参考。
关键词:车身 冲焊件 定位基准 规范1 引言近年经济快速发展促进生活水平不断提高,汽车作为一种消费品在普通家庭中开始大规模普及,并且保有量在不断加大。
所有零部件均是以车身为载体进行装配的,其尺寸精度好坏直接影响产品品质,而夹具定位又是车身尺寸控制的关键环节。
夹具设计时根据给定的MCP/MCS 图或定位基准开展的,基准体系可以控制单件、分总成、总成、装配及检测过程中基准位置一致,状态稳定,从而保证有功能要求的安装孔、安装面、切边等尺寸受控,定位基准设计的好坏会直接影响车身尺寸精度。
本文将简要探讨车身冲焊件定位基准的设计方法,便于在新项目开发中提供相关参考。
2 冲焊件定位基准设计规范3-2-1定位原则介绍一个刚性体零件在空间坐标系中存在六个方向自由度,分别朝X 轴、Y 轴、Z 轴的平移运动,绕X 轴、Y 轴、Z 轴的旋转运动,可以通过基准定位实现零件六个自由度的限制,第一基准规定方向,3点或面接触控制3个自由度(如Z1、Z2、Z3限制Z 轴的平移,X/Y 两轴的旋转),第二基准用作定位,2点或线接触控制2个自由度(如Y1、Y2限制Y 轴的平移,Z 轴的旋转),第三基准用来固定,控制零件的旋转,1点控制1个自由度(如X1限制X 轴的平移),如图1所示,该套基准限制了零件的6个自由度,因此叫3-2-1定位原则。
车身典型孔设计规范

序号类别标准件公称直径孔直径孔径公差备注凸焊螺栓底
孔凸焊螺母底
孔过孔一般安装孔φ1=d+0.2
圆孔:φ2=d+0.2
长圆孔:
宽值=d+0.2,
长值取样件测量值
圆整.d 圆孔公差:长圆孔公差:宽值长值加油口座铆接孔加油口盖铰链孔示意断面车身典型孔设计规范
d φ=d+0.51d 圆孔:φ值取样件测量值圆整长圆孔:长值和宽
值取样件测量值圆
整φ=d+1.0英制安全带7/16凸焊螺母底孔为¢13;孔径公差为圆孔:φ值取样件测量值圆整长圆孔:长值和宽
值取样件测量值圆
整圆孔:φ=d。
长圆孔:宽值=d。
,长值取样件测量值
圆整.圆孔公差:长圆孔公差:宽值长值车门铰链车门侧安装孔,机舱锁安装孔,机舱铰链安装孔。
d 圆孔:φ=d+0.2长圆孔:宽值=d+0.2,
长值取样件测量值
圆整.圆孔公差:长圆孔公差:宽值长值翼子板安装定位孔,前保险杠安装支架定位孔,玻璃升降器安装定位孔,车门限位器安
装定位孔。
45d 凸肩直径d。
d d 一般定位安
装孔7带凸肩的螺
栓定位孔铆钉孔6235
.00
+5.00+2.00+2.00+5.00+2.00+2.00+5
.00+2.00+2.00+2.00+5
.00+5.00+5.00+5.00
+5.00
+。
车身开孔设计规范
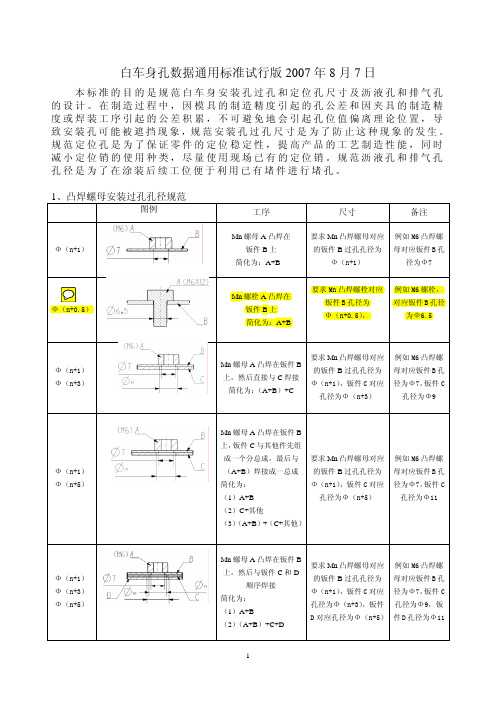
白车身孔数据通用标准试行版2007年8月7日本标准的目的是规范白车身安装孔过孔和定位孔尺寸及沥液孔和排气孔的设计。
在制造过程中,因模具的制造精度引起的孔公差和因夹具的制造精度或焊装工序引起的公差积累,不可避免地会引起孔位值偏离理论位置,导致安装孔可能被遮挡现象,规范安装孔过孔尺寸是为了防止这种现象的发生。
规范定位孔是为了保证零件的定位稳定性,提高产品的工艺制造性能,同时减小定位销的使用种类,尽量使用现场已有的定位销。
规范沥液孔和排气孔孔径是为了在涂装后续工位便于利用已有堵件进行堵孔。
Ф(n+1) Ф(n+5) Ф(n+5)Mn 螺母A 凸焊在钣件B A+成 其D 对应孔径为Ф(n+5) 件D 孔径为Ф11上,然后钣件C 与钣件D 及其他件焊接,最后与B 组成一总简化为: (1)A+B (2)C+D+其他 (3)(A+B )+(C+D+他)要求Mn 凸焊螺母对应的钣件B 过孔孔径为Ф(n+1),钣件C 对应孔径为Ф(n+5),钣件例如M6凸焊螺母对应钣件B 孔径为Ф7,钣件C 孔径为Ф11,钣上述描述的是安装面与如果安装面与该钣件的定位要求Mn 母对应Ф(n+1),钣件C 对应孔径为Ф(n+5)为Ф7,钣件C 孔径为Ф11定位面一致的情况,孔面有一定的角度凸焊螺的钣件B 过孔孔径为例如零件B 的定位孔面与安装面成90度角,则M6凸焊螺母对应钣件B 孔径Ф(n+5)Ф(n+1) * 7/16英寸凸焊螺母对应钣件孔径为Ф12mm,其相邻钣件孔径尺寸格内要求执行。
、对于其他安装孔的过孔也参考上述表格内容,一些特殊的安装孔(例如:铰链安装孔,翼子板安装孔等)可根据调整需要来制定径大小,调整方向做长圆孔。
3、定位孔的标准(1)在精度要求比较高的位置设定定位孔,以保证最终的定位精度(2防止因定位引起钣件变形,如果料太ood 内板和尽量与冲压方向一致。
度15º角以内,以种类,对定位孔尺寸做如下规范要求按上述表也可根据; 2孔)定位孔之间的距离应大于工件尺寸的三分之二;(3)定位孔设定在强度比较好的地方,薄,可做翻边处理;(4)零件定位孔一般需要两个,建议采用两个圆孔,两定位孔面尽量与主平面平行,如果设计不能满足要求,请与工艺人员商讨决定;h tailgate 内板可根据包边需要听取冲压部门人员意见,如果钣件刚性较好,也可使用一个圆孔和一个长圆孔定位,要求长圆孔长方向与两定位孔中心连线方向一致,如设计有困难,则要求在保证定位精度;(5)根据公司现有的定位销工艺孔孔径大小定位孔Φ32、Φ□30、Φ□25、Φ□20、Φ□16、Φ14、Φ□12、 Φ□10、Φ□8、Φ6、Φ5定位孔径按照上述孔径来选择,优选方长圆孔Φ32×38 Φ30×36 Φ25×31 Φ20×26 Φ16×20Φ12×16 Φ10×14 Φ6×10 Φ5×9框内数据8×12 Φ(6)定位孔避让过孔孔径要比定位孔孔径至少大2mm,可根据需要增大孔径。
车身冲焊件孔位设计规范要点
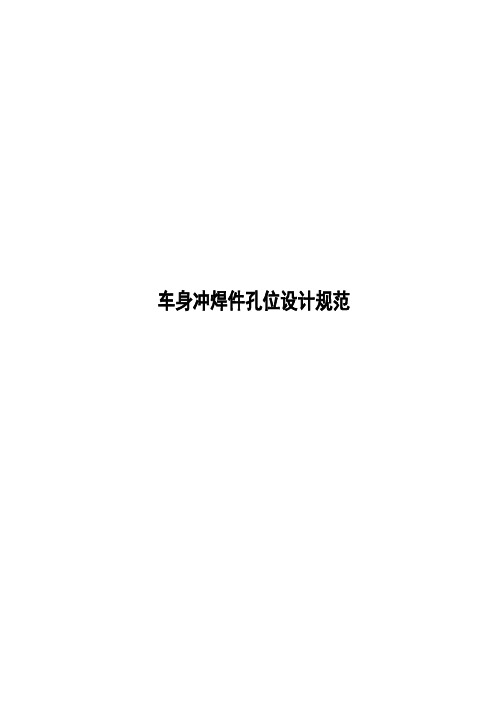
车身冲焊件孔位设计规范车身冲焊件孔位设计规范1范围本规范规定了长安公司车身冲焊件孔位的设计方法、参数及质量保证等。
本规范适用于长安公司车身冲焊件孔位的设计。
2 车身冲焊件孔位概述2.1 车身冲焊件孔分类2.1.1 按照用途分类:定位孔、功能孔(结构安装孔,装配过孔,焊接过孔,涂装工艺孔-电泳工艺孔、排水工艺孔、排气工艺孔、注蜡工艺孔,减重孔)2.1.2 按照加工精度分类:A级——为联结而设计的孔径尺寸(如连接板上的螺钉过孔、销孔、铆钉孔、装配件的螺母孔和螺钉过孔、夹具定位孔等)。
B级——次要孔径尺寸(如缆索、线束过孔、焊接电极让位孔、排水孔、减重孔等)。
2.2 冲压件孔形分类2.2.1 冲压件圆孔(等级A和B)冲压件圆孔型式和尺寸公差见图1和表1的规定。
图1表12.2.2 冲压件长圆孔(等级A和B)冲压件长孔型式和尺寸公差见图2和表2的规定。
图2表22.2.3 冲压件带缺口的圆孔 (仅当定义了一个公差等级时)冲压件带缺口的圆孔型式和尺寸公差见图3和表3的规定。
图3 表32.2.4 冲压件矩形孔 (等级A 和B )冲压件矩形孔型式和尺寸公差见图4和表4的规定。
图42.2.5 冲压件正多边形孔(仅当定义了一个公差等级时)冲压件正多边形孔型式和尺寸公差见图5和表5的规定。
图53 设计准则3.1坐标尽量取整原则:冲焊件的尺寸标注一般从坐标系的原点开始,带有公差的形状尺寸和功能尺寸,必须总是与坐标系的原点具有某种关系。
为了方便测量和质量控制,孔径形状及位置尺寸应圆整,孔径应符合优先系列数值。
3.2符合工艺性原则:设计各种孔要考虑孔的冲压方向,尽量将孔位都设计在同一冲压方向上。
3.3定位基准统一原则:a)设计基准与工艺基准统一;b)冲压、检测、装配焊接(即通常说的模、检、夹具)定位基准统一;c)单件装配与总成装配的定位基准统一:组装后的总成应尽可能采用组成零件已有基准点中的部分基准点作为总成的基准点,即基准点的继承性。
汽车车身装焊工艺

焊接机器人
2 装焊基础
(一)、焊接基础
1.含义:焊接是利用加热或加压或两者并用的方法,使焊 件达到原子结合的一种加工方法。其实质是使两个分 离金属通过原子或分子间的相互扩散与结合而形成一 个不可拆卸的整体的过程,并且连接后不能再拆卸。
焊缝 熔合区
热影响区
主焊线点定自动焊钳
2.过程特点:钢材材料的熔化焊一般经历几个过程: 加热—熔化—冶金反应—结晶—固态相变—形成接头。 经历焊接热过程、化学冶金过程、金属结晶过程和相变 过程。
10
5000--8000
0.6—1.00 14000--18000
4.0
11
6000--9000
0.8—1.2 15000--20000
5.0
13
8000--10000
0.9—1.5 17000--24000
6.0
15
1000--14000 1.2—2.00 20000--26000
2.缝焊
❖ 焊件装配成搭接或对接接头并置于两滚轮电极之间, 滚轮加压焊件并转动,连续或断续送电,形成一条连 续焊缝的电阻焊方法。
b) 焊接时间——焊接电流通过工件并产生熔核的时间。 c) 维持时间——焊接电流切断以后,电极压力继续保持的时 间。
点焊和凸焊一样,其焊接循环有四个基本阶段组成。
d)休止时间——由电极开始提起到电极再次开始下降,准 备在下一个待焊点压紧工件的时间。
点焊工艺参数参考表
板厚(mm 电极直径(mm) 焊接压力(N) )
加压结束时间滞后于通电结束时间! 目的:保证在压力作用下结晶。
放电时间过早
预压未稳定时就已先放电,由于放电时接 触不稳,会将焊件烧穿。
T1
汽车钣金冲压 焊接 涂装设计规范
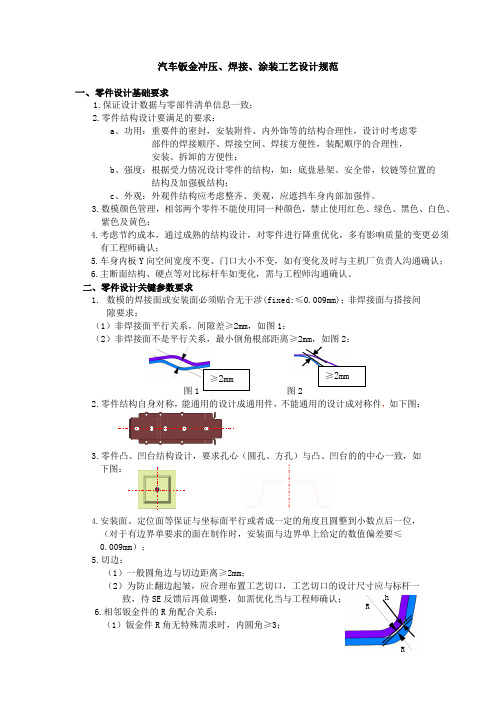
汽车钣金冲压、焊接、涂装工艺设计规范一、零件设计基础要求1.保证设计数据与零部件清单信息一致;2.零件结构设计要满足的要求:a 、功用:重要件的密封,安装附件、内外饰等的结构合理性,设计时考虑零 部件的焊接顺序、焊接空间、焊接方便性,装配顺序的合理性, 安装、拆卸的方便性;b 、强度:根据受力情况设计零件的结构,如:底盘悬架、安全带,铰链等位置的 结构及加强板结构;c 、外观:外观件结构应考虑整齐、美观,应遮挡车身内部加强件。
3.数模颜色管理,相邻两个零件不能使用同一种颜色,禁止使用红色、绿色、黑色、白色、 紫色及黄色;4.考虑节约成本,通过成熟的结构设计,对零件进行降重优化,多有影响质量的变更必须有工程师确认;5.车身内板Y 向空间宽度不变、门口大小不变,如有变化及时与主机厂负责人沟通确认;6.主断面结构、硬点等对比标杆车如变化,需与工程师沟通确认。
二、零件设计关键参数要求1. 数模的焊接面或安装面必须贴合无干涉(fixed:≤0.009mm);非焊接面与搭接间隙要求:(1)非焊接面平行关系,间隙差≥2mm ,如图1;(2)非焊接面不是平行关系,最小倒角根部距离≥2mm ,如图2:图1 图2.零件结构自身对称,能通用的设计成通用件,不能通用的设计成对称件,如下图:3.零件凸、凹台结构设计,要求孔心(圆孔、方孔)与凸、凹台的的中心一致,如下图:4.安装面、定位面等保证与坐标面平行或者成一定的角度且圆整到小数点后一位,(对于有边界单要求的面在制作时,安装面与边界单上给定的数值偏差要≤0.009mm ); 5.切边:(1)一般圆角边与切边距离≥2mm ;(2)为防止翻边起皱,应合理布置工艺切口,工艺切口的设计尺寸应与标杆一致,待SE 反馈后再做调整,如需优化当与工程师确认; 6.相邻钣金件的R 角配合关系:(1)钣金件R 角无特殊需求时,内圆角≥3;RRh ≥2mm≥2mm(2)如图:①R1>R2,当R2≥5mm 时,R1-R2≥3;②当R2<5mm 时, R1-R2≥2;③不影响焊接边h 值尽可能的加大距离。
车身焊装规范(定位点及夹持点)

焊接SE分析规范
定 位 点 及 夹 持 点
3-1定位点及夹持点标准
3-2MCP
3-3MLP
3-4螺母孔
共 1 页第 1 页圆管型零件的定位方式如下:
圆管型零件
900
“V”型块
MLP
共 2 页
第 1 页
A —A
- 0.15
- 0.5
- 0.15
定位销公差
A
A
定位销
MLP 一般要求:
1.MLP 小总成与大总成定位方式要求一致;见下图。
共 2 页
第 2 页
MLP
定位销公差
A
A
定位销
- 0.2
- 0.5
- 0.2
A —A
MLP共 1 页第 1 页定位孔选取方向尽量与装件和取件方向一致;
门盖内蒙皮定位孔方向
扣合方向
共 1 页
第 1 页
MLP
定位孔选取方向尽量与装件和取件方向一致;
A ——A
装件和取件方向
A
A
定位销
共 1 页
第 1 页
MLP
在制定总成MLP 时要考虑过定位的问题,通过过定位来校正因焊接变形、零件自身刚度不够等引起的偏差,以上图作为示意说明:
图1中零件在分总成夹具上组焊后,在A 区域会出现因为碰撞横梁内板回弹造成的变形,如果把该总成作为一个刚体看待,采用常规的夹具定位措施,那么就无法控制图2中B 区域的精度,解决这种问题有效的措施是在B 区域增加一个过定位。
A
B
图1
图2
回弹变形方向。
轿车整车通用设计规范..

白车身设计规范一、冲压件设计规范1.孔1.1钣金上的冲孔设计要与钣金冲压方向一致。
1.2孔的公差表示方法1.3过线孔1.3.1过线孔翻边1.3.1.1过线孔翻边至少要3mm高。
此翻边对钣金起加强作用,防止在安装过程中产生变形,从而影响此孔的密封性。
1.3.1.2如果通过过线孔的零件是面积≤6的固体,或者钣金足够厚,使其在不借助翻边时也能够承受住过线孔安装时的压力,那么此过线孔可以不翻边。
1.3.2过线孔所在平面尺寸1.3.2.1过线孔为圆孔(半径设为Rmm)时,孔周圈的平面半径应为(R+6)mm1.3.2.2过线孔为方孔时,孔周边的平面尺寸应比孔各边尺寸大6mm。
1.4法兰孔1.4.11.5排水孔1.5.1排水孔设计在车身内部空腔的最低处,其直径一般为6.5mm。
1.5.2对于车身内部加固的防撞梁,应同样在其空腔的最低处布置排水孔。
1.5.3在车身结构件的空腔及凹陷处必须布置排水孔。
1.6空调管路过孔1.7螺栓过孔1.8管道贯通孔2.圆角2.1对于在同一个件上喷涂两种不同颜色的零件,要设计分界特征,并且最小特征圆角为1.5mm。
3.边3.1密封边3.1.1行李箱下端3.1.1.1.为了使水排出止口,如图所示需要留出3.0mm的间隙。
3.1.1.2安装用止口应该具备恒定的高度和厚度(用于弯角的凸缘除外)。
3.1.1.3车门开口周围的止口厚度变化,包括制造变差的范围通常在1.8mm至6.0mm之间。
厚度的极端值会产生较高的插入作用力和密封条稳定性等问题。
3.1.1.4止口厚度的变化在任何位置不得超过一个金属板的厚度。
如果可能,仅可以使垂直的止口产生厚度变化,绝对不要使弯角半径产生厚度变化。
止口厚度的阶段变化会使密封条托架中的水渗漏。
3.1.1.5应该避免带有焊点的止口出现燃油和其它润滑油,这些物质会降低稳定性。
3.1.1.6止口结构类型及其优缺点3.1.2行李箱上端为了防止水从密封条止口泄漏并且进入行李舱,可按下面结构进行设计:3.1.2.1支架内的胶黏料或可发泡的热熔胶需符合漏水防止设计手册。
- 1、下载文档前请自行甄别文档内容的完整性,平台不提供额外的编辑、内容补充、找答案等附加服务。
- 2、"仅部分预览"的文档,不可在线预览部分如存在完整性等问题,可反馈申请退款(可完整预览的文档不适用该条件!)。
- 3、如文档侵犯您的权益,请联系客服反馈,我们会尽快为您处理(人工客服工作时间:9:00-18:30)。
车身冲焊件孔位设计规范1范围本规范规定了长安公司车身冲焊件孔位的设计方法、参数及质量保证等。
本规范适用于长安公司车身冲焊件孔位的设计。
2车身冲焊件孔位概述2.1车身冲焊件孔分类2.1.1按照用途分类:定位孔、功能孔(结构安装孔,装配过孔,焊接过孔,涂装工艺孔-电泳工艺孔、排水工艺孔、排气工艺孔、注蜡工艺孔,减重孔)2.1.2按照加工精度分类:A级一一为联结而设计的孔径尺寸(如连接板上的螺钉过孔、销孔、铆钉孔、装配件的螺母孔和螺钉过孔、夹具定位孔等)。
B级一一次要孔径尺寸(如缆索、线束过孔、焊接电极让位孔、排水孔、减重孔等)。
2.2冲压件孔形分类■卫・1222 冲压件长圆孔(等级A和B)图2表2223 冲压件带缺口的圆孔(仅当定义了一个公差等级时)冲压件带缺口的圆孔型式和尺寸公差见图3和表3的规定.b 图4表4225 冲压件正多边形孔(仅当定义了一个公差等级时)冲压件正多边形孔型式和尺寸公差见图5和表5的规定图5表53设计准则3.1坐标尽量取整原则:冲焊件的尺寸标注一般从坐标系的原点开始,带有公差的形状尺寸和功能尺寸,必须总是与坐标系的原点具有某种关系。
为了方便测量和质量控制,孔径形状及位置尺寸应圆整,孔径应符合优先系列数值。
3.2符合工艺性原则:设计各种孔要考虑孔的冲压方向,尽量将孔位都设计在同一冲压方向上。
3.3定位基准统一原则:a)设计基准与工艺基准统一;b)冲压、检测、装配焊接(即通常说的模、检、夹具)定位基准统一;c )单件装配与总成装配的定位基准统一:组装后的总成应尽可能采用组成零件已有基准点中的部分基准点作为总成的基准点,即基准点的继承性。
3.4对一些装配、工艺过孔,可根据车间实际工艺精度适当增大孔径,以降低零部件的装配难度。
4 典型孔位设计要求4.1定位孔的设计一般零件都设计 2 个定位孔,对于回弹较大的零件或尺寸较大的零件,需要设计成2个以上定位孔,使其更有效定位,如地板等大件。
也有一些零件一个孔定位,其它以型面定位。
有功能尺寸要求的安装孔按重要程度可优先定为定位孔,也可设计专用定位孔,如两个定位孔则必需明确主孔与辅孔。
一般为一圆孔,另一为长圆孔。
设计要求如下:a)为了降低制造成本,定位基准要设置在稳定面(不易变形)上;b)定位孔选取方向尽量与装件和取件方向一致,要求定位孔的冲孔方向与所在面尽量垂直,公差在 3 度之内;c)定位孔之间的距离至少达到零件最大尺寸的2/3,以保证有效定位;d)两个定位孔最好在同一方向上,方便取件,降低检、夹具成本;e)定位孔尺寸要求,见图6:——圆孔(hole )和长圆孔(slot )圆弧部位的直径大小一般要求一致;定位孔一般要求© 8〜© 12,最小不得小于© 6,直径公差+0.2,辅定位孔位置公差± 0.3;对一些尺寸较大的零部件,考虑到零部件的定位可靠性,需设计较大的定位销,故定位孔可在一般要求的基础上适当增大。
这种情况需设计与工艺协商决定。
长圆孔(slot )型式和尺寸公差见图6和表6的规定6d D d w 10 d+2 10v d w 20 d+4 d > 20d+6f ) 简单螺母板等零件可选择螺母孔为定位孔;g ) 强度不够的定位孔可设计成翻边为 3〜5mm 勺翻边孔4.2 功能孔的设计功能孔常有结构安装孔和一些为焊接, 总装,涂装而设的工艺孔,工艺孔一般有装配件的螺钉过孔、线束过孔、总装件过孔等,孔位按照结构需要布置。
4.2.1 所有孔需满足的冲压工艺及相关孔径的尺寸要求 4.2.1.1 冲压工艺要求4.2.1.1.1孔间距与孔边距:孔与孔之间或孔与边缘之间的距离a ,受模具强度和冲裁件质量的限制,其值不能过小宜取 a >2t ,并不得小于3〜4mm 必要时 可取a=(1〜1.5)t (当t<1mmP 寸按t=1mm 计算),但模具寿命会因此降低或结构复 杂程度增加(t 为材料厚度),见下图7。
另,需要凸焊螺母,则a >9。
4_丿—图7421.1.2在弯曲件或拉伸件上的冲孔:在弯曲件或拉伸件上冲孔时,其孔与工件直壁之间的距离L1> R+0.5t,L2 > R+0.5t,见图8。
图8 (t为材料厚度)4.2.1.2孔翻边的工艺性孔翻边时的毛坯和零件的形状与尺寸如图9所示,此时零件的形状和尺寸有如下要求:十图9 (t为材料厚度)a)翻边零件竖立边缘与平面之间的圆角半径为:--- 厚度为2mm以下的板料r= (4〜5)t;--- 厚度为2mn以上的板料r= (2〜3)t。
b)翻边厚度为H> 1.5r ;c)翻边凸缘宽度为B> H。
421.3 相关孔径的尺寸设计要求42131 冲孔极限尺寸:冲孔时,应受到冲头强度的限制,冲孔的尺寸不能太小,否则容易损坏冲头。
最小冲孔直径及最小边长见表7。
表74.2.1.3.2常用螺栓螺钉通孔尺寸要求,见表8表84.2.1.3.3螺母孔:过孔直径数值与相应焊接螺母过孔直径设计值见表9表94.2.1.3.4多层零件过孔:如果螺母板外部为2层板(后加强板和薄外板),其中螺母板孔© 1尺寸见表1,加强板孔© 2为© 1+2,外板孔© 3为© 2+2 (厚),若外板件与安装孔不易对中或装配接触面相对较大时,外板孔© 3可为© 2+4或© 2+6。
见图10。
如地板上的安装座椅,后围板上安装的后保骨架的螺母过孔等42135 方孔:方孔边长b < 10的,R 为0.5, b > 10,则R 为2。
见图114.2.2 装配件上螺栓过孔的形状与尺寸设计 4.2.2.1根据不同情况装配件上螺栓过孔的形状与尺寸列出几种见表10表10两个安装过孔的零件 三个安装过孔的零件1一个小孔,一个长圆孔:可调整量很小, 精确装配使用一个小孔,一个长圆孔,一个大孔:可调 整量很小,精确装配使用2 一个小孔,一个大孔:可调整量较小,精 确装配使用一个小孔,两个大孔:可调整量很小,精 确装配使用3两个大孔:可调整量大,用于装配位置需 根据实际情况调节的情况三个大孔:可调整量大,用于装配位置需 根据实际情况调节的情况4两个长圆孔:可调整量较大,特殊时使用注:1、小孔孔径为螺栓公称直径d+(0.5〜1);大孔为d+(2〜4)2 、根据实际需要确定长圆孔的R 尺寸。
4.2.2.2 焊接工艺孔是为满足焊接的通过性而设计的通孔,一般应在零件上加 带翻边3〜5mm 勺凸台孔,孔的大小需根据焊点位置及焊枪规格来确定。
4.2.2.3焊钳通过孔要求大于© 45,随着H 的大小越大,孔径就越大,具体大 小需要大于焊钳的规格尺寸,见图12。
03图10图11图12423 涂装工艺孔的位置和大小的设计涂装工艺孔的位置和大小的设计是评价涂装质量防腐性好坏的关键。
4.2.3.1 电泳工艺孔是为保证车体内部电泳漆性而设置的。
根据质量标准书要求,车身不同部位电泳膜厚要求不一致,比如裙边内腔膜厚要求在6卩10卩m, 门内腔膜厚大于16卩m等等,因此不同部位通电工艺孔位置、大小、数量要求不一致。
孔位设置原则如下:a)考虑到车体的通电方式以及不同部位的结构、位置等,要求设置的孔在电泳漆及电场最容易浸透的地方。
b)孔的大小和间距以电泳工艺孔设置说明为标准进行设置例如:――孔大小及位置标准:大梁,加强横梁,门槛侧一孔之间的间距200mm 直径大于20mm—— A B C立柱—孔之间的间距200mm 直径30〜50mn;――引擎盖,行李箱盖,后门的加强件一孔之间的间距200mm直径25mr〜80mm423.2排水工艺孔:在设计中必须注意设计涂装过程的工艺排水孔,因为在涂装前处理工艺中白车身一般要有10道左右的工序需在槽液中进行,上道工序的槽液应在规定的节拍内完成工艺内容,并基本倒完槽液后流入下道工序,上道工序槽液,原则上不应带入下道工序中,排水孔就是为达到这一工艺要求设计的。
孔位设置原则如下:a)地板总成应在前、中地板、后地板上各设直径30mm左右的排水孔2〜4 个;b)门槛梁、车架纵梁A.B.C立柱及各圭寸闭梁等应设计15mm〜25mn排水孔;c)车门与盖的内板靠下部低端应设计 6 mm排水孔2个;d)设计排水孔应同时选择或设计堵盖,在总装时堵塞。
423.3排气工艺孔是为防止气泡而设置的。
一般设计位置见表11表11排气孔车体顶棚、门上沿4.2.3.4注腊孔是在汽车板材间的贴合部位及车体底部等易潮部位和会反复进水并蓄水的部位,仅用电泳漆膜(裙边、大梁等部件内部由于结构及强度要求,无法开足够多的电泳孔,从而使内部电泳膜厚只有6-8微米)是无法确保防腐效果(水浸透后会产生锈蚀).所以要采用注蜡进行隔离而设计的工艺孔。
般孔位设置原则如下:a)设置在易于注蜡的部位,必须开在平面上,便于用孔盖密封,考虑注蜡作业喷枪喷头的大小及类型,尺寸大于注蜡枪头2-4mm孔尺寸:直径〉10mm排气结构图例在板面及厢式结构的最高点设计排气孔(必须轮毂、裙边)如果上沿有缝隙可以不开排气孔后轮鼓排气孔前防撞横梁上沿排气孔设置鼓包排气孔外蒙皮b)根据经验需注蜡的部位一般是前后门、背门,轮毂、前后大梁等易积水、泥沙或结露的部位,但这些部位一般都可以利用焊接及总装工艺孔进行注蜡。
优先考虑利用设置的其他工艺孔(电泳、排水孔及焊接、总装工艺孔等)。
4.2.4减重孔的设计减重孔是车身轻量化工程里最简单普遍的方式,开孔要满足冲压工艺性,装配可行性,同时要满足性能要求-NVH安全、耐久、腐蚀。
5设计评价(自查项目)5.1是否满足功能要求:a)定位孔的位置是否准确,能否保证零件定位稳定,是否符合基准统一原则;b)零件安装孔的开孔大小和位置是否符合安装件的要求(如螺母孔和螺钉过孔的大小,形状);c)焊接工艺孔是否满足焊钳的通过性;d)涂装工艺孔的位置和大小的设计是否能保证涂装的质量;e)总装工艺孔是否考虑了装配,安装调试,维修的可行性,经济性和方便性。
5.2冲压工艺性是否良好:a)孔径大小是否为优先数值,孔位坐标是否圆整;b)孔间距和孔边距,翻边孔是否符合要求;5.3是否影响性能要求-NVH安全、耐久、腐蚀。