不良镀层退除方法_二_
氰化镀铜(碱铜)常见不良现象与解决方案
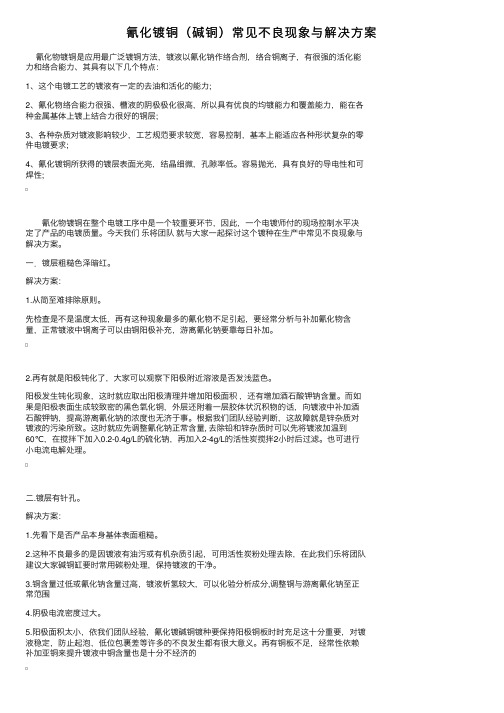
氰化镀铜(碱铜)常见不良现象与解决⽅案氰化物镀铜是应⽤最⼴泛镀铜⽅法,镀液以氰化钠作络合剂,络合铜离⼦,有很强的活化能⼒和络合能⼒、其具有以下⼏个特点:1、这个电镀⼯艺的镀液有⼀定的去油和活化的能⼒;2、氰化物络合能⼒很强、槽液的阴极极化很⾼,所以具有优良的均镀能⼒和覆盖能⼒,能在各种⾦属基体上镀上结合⼒很好的铜层;3、各种杂质对镀液影响较少,⼯艺规范要求较宽,容易控制,基本上能适应各种形状复杂的零件电镀要求;4、氰化镀铜所获得的镀层表⾯光亮,结晶细微,孔隙率低。
容易抛光,具有良好的导电性和可焊性;氰化物镀铜在整个电镀⼯序中是⼀个较重要环节,因此,⼀个电镀师付的现场控制⽔平决定了产品的电镀质量。
今天我们乐将团队就与⼤家⼀起探讨这个镀种在⽣产中常见不良现象与解决⽅案。
⼀.镀层粗糙⾊泽暗红。
解决⽅案:1.从简⾄难排除原则。
先检查是不是温度太低,再有这种现象最多的氰化物不⾜引起,要经常分析与补加氰化物含量,正常镀液中铜离⼦可以由铜阳极补充,游离氰化钠要靠每⽇补加。
2.再有就是阳极钝化了,⼤家可以观察下阳极附近溶液是否发浅蓝⾊。
阳极发⽣钝化现象,这时就应取出阳极清理并增加阳极⾯积,还有增加酒⽯酸钾钠含量。
⽽如果是阳极表⾯⽣成较致密的⿊⾊氧化铜,外层还附着⼀层胶体状沉积物的话,向镀液中补加酒⽯酸钾钠,提⾼游离氰化钠的浓度也⽆济于事。
根据我们团队经验判断,这故障就是锌杂质对镀液的污染所致。
这时就应先调整氰化钠正常含量, 去除铅和锌杂质时可以先将镀液加温到60℃,在搅拌下加⼊0.2-0.4g/L的硫化钠,再加⼊2-4g/L的活性炭搅拌2⼩时后过滤。
也可进⾏⼩电流电解处理。
⼆.镀层有针孔。
解决⽅案:1.先看下是否产品本⾝基体表⾯粗糙。
2.这种不良最多的是因镀液有油污或有机杂质引起,可⽤活性炭粉处理去除,在此我们乐将团队建议⼤家碱铜缸要时常⽤碳粉处理,保持镀液的⼲净。
3.铜含量过低或氰化钠含量过⾼,镀液析氢较⼤,可以化验分析成分,调整铜与游离氰化钠⾄正常范围4.阴极电流密度过⼤。
电镀过程中镀层不良的描述、原因及对策

电镀过程中镀层不良的描述、原因及对策1、针孔。
针孔是由于镀件外表吸附着氢气,迟迟不开释。
使镀液无法亲润镀件外表,然后无法电析镀层。
跟着析氢点周围区域镀层厚度的添加,析氢点就构成了一个针孔。
特点是一个发亮的圆孔,有时还有一个向上的小尾巴"。
当镀液中短少湿润剂并且电流密度偏高时,容易构成针孔。
2、麻点。
麻点是由于受镀外表不洁净,有固体物质吸附,或许镀液中固体物质悬浮着,当在电场效果下到达工件外表后,吸附其上,而影响了电析,把这些固体物质嵌入在电镀层中,构成一个个小凸点(麻点)。
特点是上凸,没有发亮现象,没有固定形状。
总归是工件脏、镀液脏而构成。
3、气流条纹。
气流条纹是由于添加剂过量或阴极电流密度过高或络合剂过高而降低了阴极电流效率然后析氢量大。
假如当时镀液流动缓慢,阴极移动缓慢,氢气贴着工件外表上升的进程中影响了电析结晶的摆放,构成自下而上一条条气流条纹。
4、掩镀(露底)。
掩镀是由于是工件外表管脚部位的软性溢料没有除掉,无法在此处进行电析堆积镀层。
电镀后可见基材,故称露底(由于软溢料是半通明的或通明的树脂成份)。
5、镀层脆性。
在SMD电镀后切筋成形后,可见在管脚弯处有开裂现象。
当镍层与基体之间开裂,判定是镍层脆性。
当锡层与镍层之间开裂,判定是锡层脆性。
构成脆性的原因八成是添加剂,光亮剂过量,或许是镀液中无机、有机杂质太多构成。
6、气袋。
气袋的构成是由于工件的形状和积气条件而构成。
氢气积在"袋中"无法排到镀液液面。
氢气的存在阻挠了电析镀层。
使堆集氢气的部位无镀层。
在电镀时,只需留意工件的钩挂方向能够防止气袋现象。
如图示工件电镀时,当垂直于镀槽底钩挂时,不发生气袋。
当平行于槽底钩挂时,易发生气袋。
7、塑封黑体中心开"锡花”。
在黑体上有锡镀层,这是由于电子管在焊线时,金丝的向上抛物形太高,塑封时金丝显露在黑体外表,锡就镀在金丝上,像开了一朵花。
不是镀液问题。
8、"爬锡"。
手把手教你化学镀镍的常见故障及解决办法

手把手教你化学镀镍的常见故障及解决办法(1)沉积速度慢(这点也是平台上最多朋友咨询的)造成这种现象的原因与解决方法:镀液pH值过低:测pH值调整,并控制pH在下限值。
虽然pH 值较高能提高沉速,但会影响镀液稳定性。
镀液温度过低:要求温度达到规范时下槽进行施镀。
新开缸第一批工件下槽时,温度应达到上限,反应开始后,正常施镀时,温度在下限为好。
溶液主成分浓度低:分析调整,如还原剂不足时,添加还原补充液;镍离子浓度偏低时,添加镍盐补充液。
对于上规模的化学镀镍,设自动分析、补给装置是必要的,可以延长连续工作时间(由30h延至56h)和镍循环周期(由6周延至11周)。
亚磷酸根过多:弃掉部分镀液。
装载量太低:增加受镀面积至1dm2/L。
稳定剂浓度偏重:倾倒部分,少量多次加浓缩液。
(2)镀液分解(镀液呈翻腾状,出现镍粉)造成这种现象的原因与解决方法:温度过高或局部过热:搅拌下加入温去离子水。
次亚磷酸钠大多:冲稀补加其它成分。
镀液的pH值过高:调整pH值至规范值。
机械杂质:过滤除去。
装载量过高:降至1dm2/L槽壁或设备上有沉淀物:滤出镀液,退镀清洗(用3HNO3溶液)。
操作温度下补加液料大多:搅拌下少量多次添加。
稳定剂带出损失:添加少量稳定剂。
催化物质带入镀液:加强镀前清洗。
镀层剥离碎片:过滤镀液。
(3)镀层结合力差或起泡造成这种现象的原因与解决方法:镀前处理不良:提高工作表面的质量,加工完成后应清除工件上所有的焊接飞溅物和焊渣。
工件表面的粗糙度应达到与精饰要求相当的粗糙义,如碳钢工件表面粗糙度Ra<>温度波动太大:控制温度在较小的范围波动。
下槽温度太低:适当提高下槽温度。
清洗不良:改进清洗工序。
金属离子污染:用大面积废件镀而除去。
有机杂质污染:活化炭1-2g/L 处理。
热处理不当:调整热处理时间和温度。
(4)镀层粗糙造成这种现象的原因与解决方法:镀液浓度过高:适当冲稀镀液。
镀液的pH值过高:降低pH值至规范值。
电镀不良的一些情况和解决方法

电镀不良的一些情况和解决方法电镀不良对策镀层品质不良的发生多半为电镀条件,电镀设备或电镀药水的异常,及人为疏忽所致.通常在现场发生不良时比较容易找出塬因克服,但电镀后经过一段时间才发生不良就比较棘手.然而日后与环境中的酸气,氧气,水分等接触,加速氧化腐蚀作用也是必须注意的.以下本章将对电镀不良的发生塬因及改善的对策加以探讨说明.1.表面粗糙:指不平整,不光亮的表面,通常成粗白状(1)可能发生的塬因: (2)改善对策:1.素材表面严重粗糙,镀层无法覆盖平整. 1.若为素材严重粗糙,立即停产并通知客户.2.金属传动轮表面粗糙,且压合过紧,以至于压伤. 2.若传动轮粗糙,可换备用品使用并检查压合紧度.3.电流密度稍微偏高,部分表面不亮粗糙(尚未烧焦) 3.计算电流密度是否操作过高,若是应降低电流4.浴温过低,一般镀镍才会发生) 4.待清晰度回升再开机,或降低电流,并立即检查温控系统.5.PH值过高或过低,一般镀镍或镀金(过低不会)皆会发生. 5.立即调整PH至标准范围.6.前处理药液腐蚀底材. 6.查核前处理药剂,稀释药剂或更换药剂2.沾附异物:指端子表面附着之污物.(1)可能发生的塬因: (2)改善对策:1.水洗不干净或水质不良(如有微菌). 1.清洗水槽并更换新水.2.占到收料系统之机械油污. 2.将有油污处做以遮蔽.3.素材带有类似胶状物,于前处理流程无法去除. 3.须先以溶剂浸泡处理.4.收料时落地沾到泥土污物. 4.避免落地,若已沾附泥土可用吹气清洁,浸透量很多时,建议重新清洗一次.5.锡铅结晶物沾附 5.立即去除结晶物.6刷镀羊毛?纤维丝 6.更换羊毛?并检查接触压力.7.纸带溶解纤维丝. 7.清槽.8.皮带脱落屑. 8.更换皮带.3.密着性不良:指镀层有剥落.起皮,起泡等现象.(1)可能发生的塬因: (2).改善对策:1.前处理不良,如剥镍. 1.加强前处理.2.阴极接触不良放电,如剥镍,镍剥金,镍剥锡铅. 2.检查阴极是否接触不良,适时调整.3.镀液受到严重污染. 3.更换药水4.产速太慢,底层再次氧化,如镍层在金槽氧化(或金还塬),剥锡铅. 4,电镀前须再次活化.5.水洗不干净. 5.更换新水,必要时清洗水槽.6.素材氧化严重,如氧化斑,热处理后氧化膜. 6.必须先做除锈及去氧化膜处理,一般使用化学抛光或电解抛光.7.停机化学置换反应造成. 7.必免停机或剪除不良品8,操作电压太高,阴极导电头及镀件发热,造成镀层氧化. 8.降低操作电压或检查导线接触状况9,底层电镀不良(如烧焦),造成下一层剥落. 9.改善底层电镀品质.10.严重.烧焦所形成剥落 10.参考NO12处理对策.4.露铜:可清楚看见铜色或黄黑色于低电流处(凹槽处)(1)可能发生塬因: (2)改善对策:1.前处理不良,油脂,氧化物.异物尚未除去,镀层无法析出. 1.加强前处理或降低产速2.操作电流密度太低,导致低电流区,镀层无法析出. 2.重新计算电镀条件.3镍光泽剂过量,导致低电流区,镀层无法析出 3.处理药水,去除过多光泽剂或更新.4.严重刮伤造成露铜. 4.检查电镀流程,(查参考NO5)5.未镀到. 5.调整电流位置.5刮伤:指水平线条状,一般在锡铅镀层比较容易发生.(1)可能发生的塬因: (2)改善对策:1.素材本身在冲压时,及造成刮伤. 1.停止生产,待与客户联系.2.被电镀设备中的金属制具刮伤,如阴极头,烤箱定位器,导轮等. 2.检查电镀流程,适时调整设备和制具.3.被电镀结晶物刮伤. 3.停止生产,立即去除结晶物.6.变形(刮歪):指端子形状已经偏离塬有尺寸或位置.(1)可能发生的塬因: (2)改善对策:1.素材本身在冲压时,或运输时,即造成变形. 1.停止生产,待与客户联系.2.被电镀设备,制具刮歪(如吹气.定位器,振荡器,槽口,回转轮) 2.检查电镀流程,适时调整设备和制具.3.盘子过小或卷绕不良,导致出入料时刮歪 3.停止生产,适时调整盘子4.传动轮转歪, 4.修正传动轮或变更传动方式.7压伤:指不规则形状之凹洞可能发生的塬因:改善对策:1)本身在冲床加工时,已经压伤,镀层无法覆盖平整2)传动轮松动或故障不良,造成压合时伤到 1)停止生産,待与客户联2)检查传动机构,或更换备品8白雾:指镀层表面卡一层云雾状,不光亮但平整可能发生的塬因:1)前处理不良2)镀液受污染3)锡铅层爱到酸腐蚀,如停机时受到锡铅液腐蚀4)锡铅药水温度过高5)锡铅电流密度过低6)光泽剂不足7)传致力轮脏污8)锡铅电久进,産生泡沫附着造成改善对策:1)加强前处理2)更换药水并提纯污染液3)避免停机,若无法避免时,剪除不良4)立即检查温控系统,并重新设定温度5)提高电流密度6)补足不泽剂传动轮7)清洁传动轮8)立即去除泡沫9针孔:指成群、细小圆洞状(似被钟扎状)可能发生的塬因:改善对策:1.操作的电流密度太 1.降低电流密度2.电镀溶液表面张力过大,湿润剂不足。
产品电镀层鼓泡,脱皮故障,详细原因解析与处理方法

产品电镀层鼓泡,脱皮故障,详细原因解析与处理方法近来平台内,有许多朋友发来电镀层鼓泡脱皮故障。
这种故障一出现,就代表着大损失!客户与我们电镀工厂最怕碰到的返镀也是这种故障,返镀报废的情况最多。
前面针对锌合金鼓泡我们已经有专门探讨过,这次就不再复述了,主要针对其它坯件的这种故障产品电镀鼓泡起皮不良故障处理碰到这种现象要沉着冷静,首先要用刀片划开看鼓泡起皮层是从基体脱还是从镀层脱。
判断正确很关健!一,镀层与工件底基层脱. 主要原因是前处理不良1. 除油不彻底.对于铸铁零件来说,由于铸铁的导电性差,在电镀挂具设计时需要考虑零件与挂具的接触;同时还要考虑由于铸铁的含碳量高,有很多气孔与砂眼,所以铸铁零件只能采用弱酸腐蚀活化,避免采用强酸腐蚀导致零件表面腐蚀挂灰引起镀层结合不良。
另外铸铁零件表面的铁锈需要用机械方法去除,活化采用3%~5%的HF酸或草酸等弱有机酸处理。
2。
如镀件为优质钢,特别是有含镍、钼合金钢件,在阳极处理过程中同时伴随有一定量的氧的析出,当转为阴极时,其表面极易在短时间内形成一层薄而致密的氧化膜按正常工艺就很难获得与基体金属结合力好的镀层。
解决方法①降低酸洗液浓度,新配制浓盐酸:水一1;2另加质量分数为40%的氢氟酸3mL/L混合溶液进行酸洗,利用HF去除零件表面含硅化合物;②缩短酸洗时间,从原来的5min缩短为5s~10s,以防止零件基体组织中的磷、硫形成晶界偏析3.普通铁基材有镀锌层未处理干净。
可用浓盐酸加双氧水剥去此已钝化镀锌层,许多做五金的朋友就常碰到,锌合金产品有压铁后片,镀后片一折就脱镀层,就是这种原因。
4.有时前处理后基本表面没有油污,表面润湿很均匀,但是镀层还是起泡。
这又是什么原因呢?因为现在除油粉中都用硅酸钠和表面活性剂,特别在冬天,水温低,冷水很难把附着在零件表面的硅酸钠洗净,经酸洗后,硅酸留在表面,进入碱铜槽生成盐膜,以及表面活性剂残留也会引起镀层起泡,这种镀层起泡,泡较小,.5。
电镀故障——精选推荐
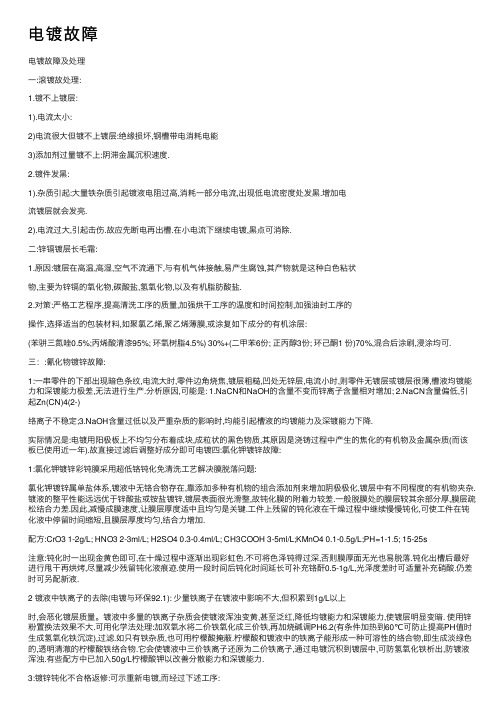
电镀故障电镀故障及处理⼀:滚镀故处理:1.镀不上镀层:1).电流太⼩:2)电流很⼤但镀不上镀层:绝缘损坏,钢槽带电消耗电能3)添加剂过量镀不上:阴滞⾦属沉积速度.2.镀件发⿊:1).杂质引起:⼤量铁杂质引起镀液电阻过⾼,消耗⼀部分电流,出现低电流密度处发⿊.增加电流镀层就会发亮.2).电流过⼤,引起击伤.故应先断电再出槽.在⼩电流下继续电镀,⿊点可消除.⼆:锌镉镀层长⽑霜:1.原因:镀层在⾼温,⾼湿,空⽓不流通下,与有机⽓体接触,易产⽣腐蚀,其产物就是这种⽩⾊粘状物,主要为锌镉的氧化物,碳酸盐,氢氧化物,以及有机脂肪酸盐.2.对策:严格⼯艺程序,提⾼清洗⼯序的质量,加强烘⼲⼯序的温度和时间控制,加强油封⼯序的操作,选择适当的包装材料,如聚氯⼄烯,聚⼄烯薄膜,或涂复如下成分的有机涂层:(苯骈三氮唑0.5%;丙烯酸清漆95%; 环氧树脂4.5%) 30%+(⼆甲苯6份; 正丙醇3份; 环⼰酮1 份)70%,混合后涂刷,浸涂均可.三::氰化物镀锌故障:1:⼀串零件的下部出现暗⾊条纹,电流⼤时,零件边⾓烧焦,镀层粗糙,凹处⽆锌层,电流⼩时,则零件⽆镀层或镀层很薄,槽液均镀能⼒和深镀能⼒极差,⽆法进⾏⽣产.分析原因,可能是: 1.NaCN和NaOH的含量不变⽽锌离⼦含量相对增加; 2.NaCN含量偏低,引起Zn(CN)4(2-)络离⼦不稳定;3.NaOH含量过低以及严重杂质的影响时,均能引起槽液的均镀能⼒及深镀能⼒下降.实际情况是:电镀⽤阳极板上不均匀分布着成块,成粒状的⿊⾊物质,其原因是浇铸过程中产⽣的焦化的有机物及⾦属杂质(⽽该板已使⽤近⼀年).故直接过滤后调整好成分即可电镀四:氯化钾镀锌故障:1:氯化钾镀锌彩钝膜采⽤超低铬钝化免清洗⼯艺解决膜脱落问题:氯化钾镀锌属单盐体系,镀液中⽆铬合物存在,靠添加多种有机物的组合添加剂来增加阴极极化,镀层中有不同程度的有机物夹杂.镀液的整平性能远远优于锌酸盐或铵盐镀锌,镀层表⾯很光滑整,故钝化膜的附着⼒较差.⼀般脱膜处的膜层较其余部分厚,膜层疏松结合⼒差.因此,减慢成膜速度,让膜层厚度适中且均匀是关键.⼯件上残留的钝化液在⼲燥过程中继续慢慢钝化,可使⼯件在钝化液中停留时间缩短,且膜层厚度均匀,结合⼒增加.配⽅:CrO3 1-2g/L; HNO3 2-3ml/L; H2SO4 0.3-0.4ml/L; CH3COOH 3-5ml/L;KMnO4 0.1-0.5g/L;PH=1-1.5; 15-25s注意:钝化时⼀出现⾦黄⾊即可,在⼗燥过程中逐渐出现彩虹⾊.不可将⾊泽钝得过深,否则膜厚⾯⽆光也易脱落.钝化出槽后最好进⾏甩⼲再烘烤,尽量减少残留钝化液痕迹.使⽤⼀段时间后钝化时间延长可补充铬酐0.5-1g/L,光泽度差时可适量补充硝酸.仍差时可另配新液.2 镀液中铁离⼦的去除(电镀与环保92.1): 少量铁离⼦在镀液中影响不⼤,但积累到1g/L以上时,会恶化镀层质量。
常见电镀故障的分析和纠正方法
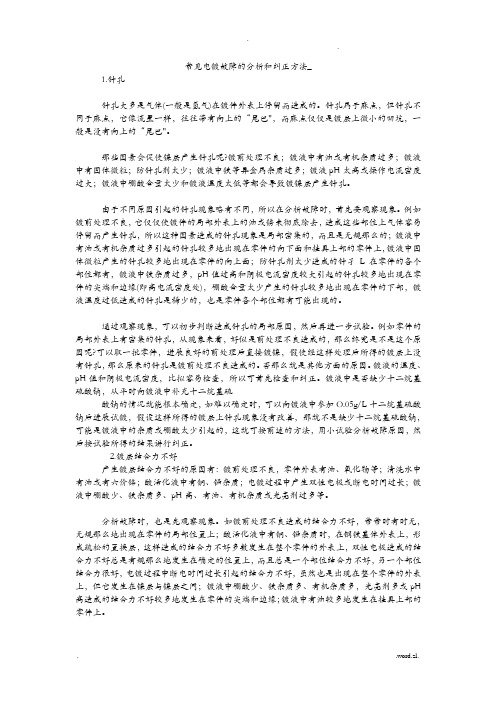
常见电镀故障的分析和纠正方法_1.针孔针孔大多是气体(一般是氢气)在镀件外表上停留而造成的。
针孔属于麻点,但针孔不同于麻点,它像流星一样,往往带有向上的“尾巴",而麻点仅仅是镀层上微小的凹坑,一般是没有向上的“尾巴"。
那些因素会促使镍层产生针孔呢?镀前处理不良;镀液中有油或有机杂质过多;镀液中有固体微粒;防针孔剂太少;镀液中铁等异金属杂质过多;镀液pH太高或操作电流密度过大;镀液中硼酸含量太少和镀液温度太低等都会导致镀镍层产生针孔。
由于不同原因引起的针孔现象略有不同,所以在分析故障时,首先要观察现象。
例如镀前处理不良,它仅仅使镀件的局部外表上的油或锈未彻底除去,造成这些部位上气体容易停留而产生针孔,所以这种因素造成的针孔现象是局部密集的,而且是无规那么的;镀液中有油或有机杂质过多引起的针孔较多地出现在零件的向下面和挂具上部的零件上,镀液中固体微粒产生的针孔较多地出现在零件的向上面;防针孔剂太少造成的针孑L在零件的各个部位都有,镀液中铁杂质过多,pH值过高和阴极电流密度较大引起的针孔较多地出现在零件的尖端和边缘(即高电流密度处),硼酸含量太少产生的针孔较多地出现在零件的下部,镀液温度过低造成的针孔是稀少的,也是零件各个部位都有可能出现的。
通过观察现象,可以初步判断造成针孔的局部原因,然后再进一步试验。
例如零件的局部外表上有密集的针孔,从现象来看,好似是前处理不良造成的,那么终究是不是这个原因呢?可以取一批零件,进展良好的前处理后直接镀镍,假使经这样处理后所得的镀层上没有针孔,那么原来的针孔是镀前处理不良造成的。
否那么就是其他方面的原因。
镀液的温度、pH值和阴极电流密度,比拟容易检查,所以可首先检查和纠正。
镀液中是否缺少十二烷基硫酸钠,从平时向镀液中补充十二烷基硫酸钠的情况就能根本确定,如难以确定时,可以向镀液中参加O.05g/L十二烷基硫酸钠后进展试镀,假设这样所得的镀层上针孔现象没有改善,那就不是缺少十二烷基硫酸钠,可能是镀液中的杂质或硼酸太少引起的,这就可按前述的方法,用小试验分析故障原因,然后按试验所得的结果讲行纠正。
镀镍发黑不良解决大全

镀镍发⿊不良解决⼤全平台上有朋友“星⾠”发来镀镍发⿊不良产品图⽚咨询解决⽅法许多⼤师⽆私分享了他们的经验:⾦⾮锡⽐估计加些亚铁氰化钾会好特能宝【罗】前处理没搞⼲净。
镍槽有杂质周长虹电镀⼯匠Z158********前处理没有做到四⽆:⽆油、⽆锈、⽆挂灰、⽆吸附膜。
亮镍缸⾛位不好,异⾦属杂质多。
乐将-九哥中间是低电位,镍前没有异常的话,正常是镍镀液杂质⾼了男⼈海洋周⼯⼤师级⼈物茅红裕是铸铁材质?表⾯砂眼较多,前处理处理⼲净,除油酸洗后保证表⾯⽆锈,且应该尽快电镀,不宜在⽔中放时间过久,易反锈。
直接上镍吗,建议氰铜打底,然后镀镍。
这样不宜⽣锈。
或者产品喷砂后直接电镀,不经过酸洗。
⽵林雅阁应该是镍槽杂质太多,加除铜⾏锌的药⽔就可以了。
电镀镍应⽤⼴泛,是电镀⼚最基础也是⾮常关健⼀个镀种,今天我们乐将团队根据电镀现场以及⼀些前辈多年经验就镀镍发⿊这⼀不良现象与⼤家进⾏分享探讨1 镀层发暗、发⿊的原因镀层发暗多数出现在低电流密度区 ( 零件深凹处 ) ,偶尔也有出现在中电流密度区或⾼电流密度区。
( 1 ) 低电流密度区镀层发暗,可能是镀液温度太⾼,电流密度太⼩,主盐浓度太低,⼆次光亮剂过多或镀液中有铜、锌等异⾦属杂质所引起的。
( 2 ) 中电流密度区镀层发暗,可能是由⼆次光亮剂太少,有机杂质过多或有⼀定量的铁杂质所造成的。
(3 ) ⾼电流密度区镀层发暗,可能是镀液pH值太⾼,⼀次光亮剂太少或镀液中有少量的铬酸盐、磷酸盐及铅杂质所引起的。
(4 ) 镀前处理不良,镀件表⾯有碱膜或有机物吸附膜,或者底镀层不好,也会导致镍层出现发暗的现象。
分析这类故障,可以取镀镍液先做霍尔槽试验,假使多次试验,霍尔槽的阴极样板上镀层状况良好,没有出现发暗的现象,那么电镀时出现的故障可能是镀前处理不良或底镀层不好所造成的,应该认真检查电镀前的情况。
若霍尔槽试验所得阴极样板上出现低电流密度区镀层发暗,则可以根据前⾯提到的可能原因进⾏分析。
汽车制品电镀不良的改进
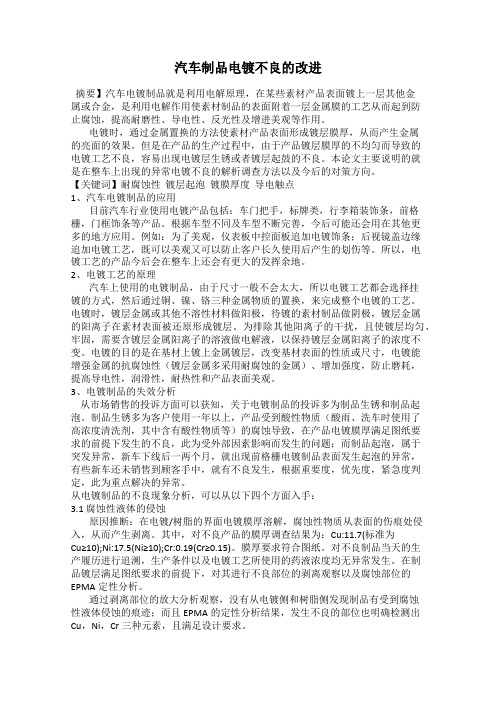
汽车制品电镀不良的改进摘要】汽车电镀制品就是利用电解原理,在某些素材产品表面镀上一层其他金属或合金,是利用电解作用使素材制品的表面附着一层金属膜的工艺从而起到防止腐蚀,提高耐磨性、导电性、反光性及增进美观等作用。
电镀时,通过金属置换的方法使素材产品表面形成镀层膜厚,从而产生金属的亮面的效果。
但是在产品的生产过程中,由于产品镀层膜厚的不均匀而导致的电镀工艺不良,容易出现电镀层生锈或者镀层起鼓的不良。
本论文主要说明的就是在整车上出现的异常电镀不良的解析调查方法以及今后的对策方向。
【关键词】耐腐蚀性镀层起泡镀膜厚度导电触点1、汽车电镀制品的应用目前汽车行业使用电镀产品包括:车门把手,标牌类,行李箱装饰条,前格栅,门框饰条等产品。
根据车型不同及车型不断完善,今后可能还会用在其他更多的地方应用。
例如:为了美观,仪表板中控面板追加电镀饰条;后视镜盖边缘追加电镀工艺,既可以美观又可以防止客户长久使用后产生的划伤等。
所以,电镀工艺的产品今后会在整车上还会有更大的发挥余地。
2、电镀工艺的原理汽车上使用的电镀制品,由于尺寸一般不会太大,所以电镀工艺都会选择挂镀的方式,然后通过铜、镍、铬三种金属物质的置换,来完成整个电镀的工艺。
电镀时,镀层金属或其他不溶性材料做阳极,待镀的素材制品做阴极,镀层金属的阳离子在素材表面被还原形成镀层。
为排除其他阳离子的干扰,且使镀层均匀、牢固,需要含镀层金属阳离子的溶液做电解液,以保持镀层金属阳离子的浓度不变。
电镀的目的是在基材上镀上金属镀层,改变基材表面的性质或尺寸,电镀能增强金属的抗腐蚀性(镀层金属多采用耐腐蚀的金属)、增加强度,防止磨耗,提高导电性,润滑性,耐热性和产品表面美观。
3、电镀制品的失效分析从市场销售的投诉方面可以获知,关于电镀制品的投诉多为制品生锈和制品起泡。
制品生锈多为客户使用一年以上,产品受到酸性物质(酸雨、洗车时使用了高浓度清洗剂,其中含有酸性物质等)的腐蚀导致,在产品电镀膜厚满足图纸要求的前提下发生的不良,此为受外部因素影响而发生的问题;而制品起泡,属于突发异常,新车下线后一两个月,就出现前格栅电镀制品表面发生起泡的异常,有些新车还未销售到顾客手中,就有不良发生,根据重要度,优先度,紧急度判定,此为重点解决的异常。
第二十一章 常规镀层的退镀方法
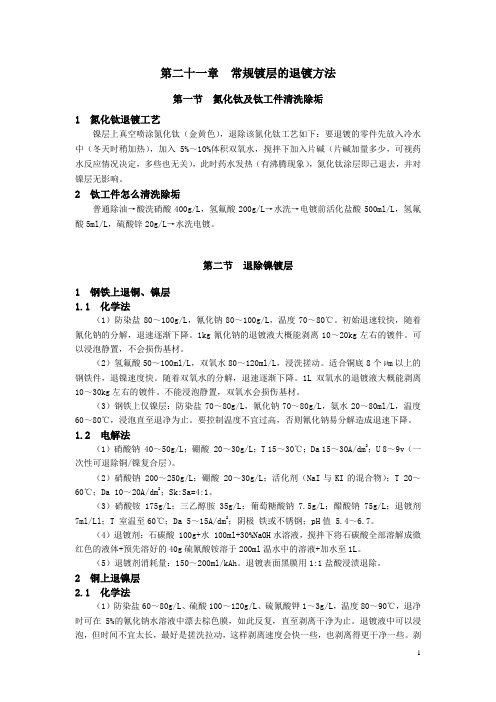
第二十一章常规镀层的退镀方法第一节氮化钛及钛工件清洗除垢1 氮化钛退镀工艺镍层上真空喷涂氮化钛(金黄色),退除该氮化钛工艺如下:要退镀的零件先放入冷水中(冬天时稍加热),加入5%~10%体积双氧水,搅拌下加入片碱(片碱加量多少,可视药水反应情况决定,多些也无关),此时药水发热(有沸腾现象),氮化钛涂层即己退去,并对镍层无影响。
2 钛工件怎么清洗除垢普通除油→酸洗硝酸400g/L,氢氟酸200g/L→水洗→电镀前活化盐酸500ml/L,氢氟酸5ml/L,硫酸锌20g/L→水洗电镀。
第二节退除镍镀层1 钢铁上退铜、镍层1.1 化学法(1)防染盐80~100g/L,氰化钠80~100g/L,温度70~80℃。
初始退速较快,随着氰化钠的分解,退速逐渐下降。
1kg氰化钠的退镀液大概能剥离10~20kg左右的镀件。
可以浸泡静置,不会损伤基材。
(2)氢氟酸50~100ml/L,双氧水80~120ml/L,浸洗搓动。
适合铜底8个µm以上的钢铁件,退镍速度快。
随着双氧水的分解,退速逐渐下降。
1L双氧水的退镀液大概能剥离10~30kg左右的镀件。
不能浸泡静置,双氧水会损伤基材。
(3)钢铁上仅镍层:防染盐70~80g/L,氰化钠70~80g/L,氨水20~80ml/L,温度60~80℃,浸泡直至退净为止。
要控制温度不宜过高,否则氰化钠易分解造成退速下降。
1.2 电解法(1)硝酸钠 40~50g/L;硼酸 20~30g/L;T 15~30℃;Da 15~30A/dm2;U 8~9v(一次性可退除铜/镍复合层)。
(2)硝酸钠 200~250g/L;硼酸 20~30g/L;活化剂(NaI与KI的混合物);T 20~60℃;Da 10~20A/dm2;Sk:Sa=4:1。
(3)硝酸铵 175g/L;三乙醇胺 35g/L;葡萄糖酸钠 7.5g/L;醋酸钠 75g/L;退镀剂7ml/Ll;T 室温至60℃;Da 5~15A/dm2;阴极铁或不锈钢;pH值 5.4~6.7。
电解法退银镀层
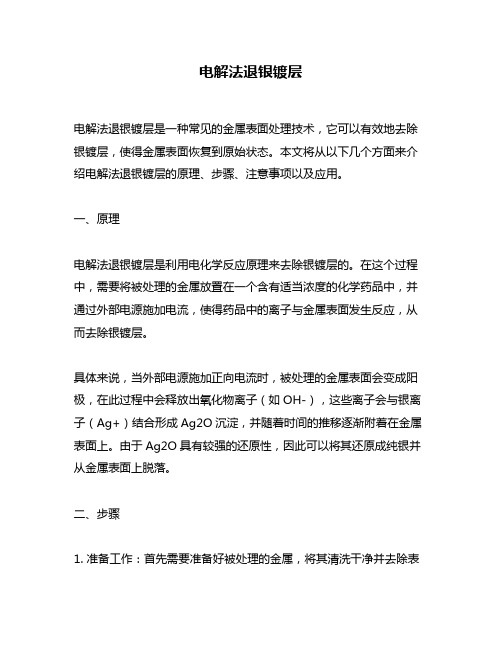
电解法退银镀层电解法退银镀层是一种常见的金属表面处理技术,它可以有效地去除银镀层,使得金属表面恢复到原始状态。
本文将从以下几个方面来介绍电解法退银镀层的原理、步骤、注意事项以及应用。
一、原理电解法退银镀层是利用电化学反应原理来去除银镀层的。
在这个过程中,需要将被处理的金属放置在一个含有适当浓度的化学药品中,并通过外部电源施加电流,使得药品中的离子与金属表面发生反应,从而去除银镀层。
具体来说,当外部电源施加正向电流时,被处理的金属表面会变成阳极,在此过程中会释放出氧化物离子(如OH-),这些离子会与银离子(Ag+)结合形成Ag2O沉淀,并随着时间的推移逐渐附着在金属表面上。
由于Ag2O具有较强的还原性,因此可以将其还原成纯银并从金属表面上脱落。
二、步骤1. 准备工作:首先需要准备好被处理的金属,将其清洗干净并去除表面的油污、氧化物等杂质。
2. 配置药品:将适量的化学药品(如NaOH、Na2CO3等)溶于水中,制成一定浓度的电解液。
3. 进行电解:将被处理的金属放置在电解槽中,并通过外部电源施加正向电流,使得药品中的离子与金属表面发生反应。
在此过程中,需要注意控制电流密度和时间,以免对金属造成损害。
4. 清洗:处理完毕后,需要将金属从电解槽中取出并用清水彻底冲洗干净,以去除表面残留的药品和离子。
5. 烘干:最后需要将处理好的金属放置在通风良好的地方进行烘干,并储存起来以备下一步使用。
三、注意事项1. 选择适当浓度的化学药品,并根据被处理金属表面情况调整电解液浓度和温度。
2. 控制好电流密度和时间,避免对金属造成损害。
通常情况下,较低的电流密度和较长的时间可以得到更好的效果。
3. 在电解过程中需要不断搅拌电解液,以保证离子和金属表面充分接触。
4. 处理完毕后需要及时清洗金属表面,避免残留药品和离子对金属造成腐蚀。
四、应用电解法退银镀层是一种常见的金属表面处理技术,广泛应用于电子、通信、航空等领域。
具体应用包括:1. 电子器件:在印制电路板(PCB)制造过程中,需要去除银镀层以便进行下一步加工。
不合格镀层的退除配方
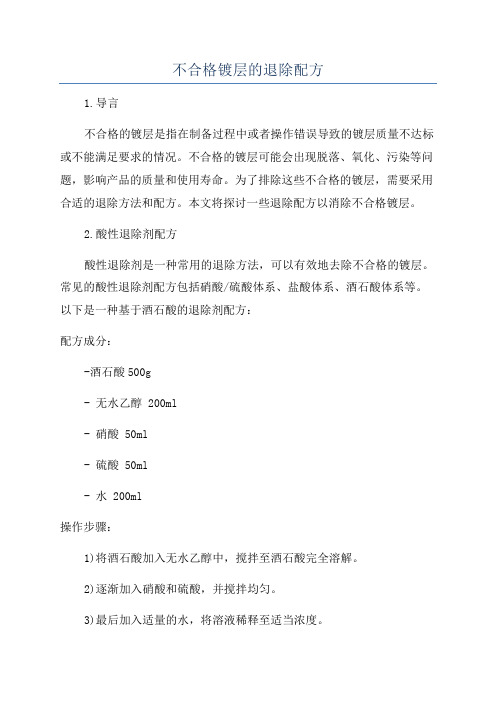
不合格镀层的退除配方1.导言不合格的镀层是指在制备过程中或者操作错误导致的镀层质量不达标或不能满足要求的情况。
不合格的镀层可能会出现脱落、氧化、污染等问题,影响产品的质量和使用寿命。
为了排除这些不合格的镀层,需要采用合适的退除方法和配方。
本文将探讨一些退除配方以消除不合格镀层。
2.酸性退除剂配方酸性退除剂是一种常用的退除方法,可以有效地去除不合格的镀层。
常见的酸性退除剂配方包括硝酸/硫酸体系、盐酸体系、酒石酸体系等。
以下是一种基于酒石酸的退除剂配方:配方成分:-酒石酸500g- 无水乙醇 200ml- 硝酸 50ml- 硫酸 50ml- 水 200ml操作步骤:1)将酒石酸加入无水乙醇中,搅拌至酒石酸完全溶解。
2)逐渐加入硝酸和硫酸,并搅拌均匀。
3)最后加入适量的水,将溶液稀释至适当浓度。
使用方法:1)将退除剂溶液倒入适当大小的容器中。
2)将待处理的不合格镀层浸泡在退除剂中,时间根据实际情况决定。
3)定期检查不合格镀层的退除情况,并根据需要调整浸泡时间。
4)镀层完全退除后,用水冲洗并进行干燥处理。
3.碱性退除剂配方碱性退除剂可以快速有效地去除一些不合格的镀层,特别是一些有机物的污染物。
常见的碱性退除剂配方包括氢氧化钠、氢氧化钾等。
以下是一种基于氢氧化钠的退除剂配方:配方成分:-氢氧化钠1000g- 纯水 1000ml操作步骤:1)将适量的纯水加入容器中,并加热至60-70℃。
2)逐渐加入氢氧化钠,并充分搅拌均匀。
3)搅拌至溶液完全溶解,并冷却至室温。
使用方法:1)将退除剂溶液倒入适当大小的容器中。
2)将待处理的不合格镀层浸泡在退除剂中,时间根据实际情况决定。
3)定期检查不合格镀层的退除情况,并根据需要调整浸泡时间。
4)镀层完全退除后,用水冲洗并进行干燥处理。
4.机械研磨配方对于一些比较厚重的不合格镀层,可以采用机械研磨的方法进行退除。
机械研磨可以通过研磨材料的硬度和研磨方法的控制,去除不合格镀层而不会对基材造成损伤。
不合格的化学镀镍层的两种退除方法

不合格的化学镀镍层的两种退除方法化学镀镍层的退除要比电镀镍层困难得多,特别是对于高耐蚀化学镀镍层更是如此。
不合格的化学镀镍层应在热处理前就进行退除,否则镀层钝化后退镀更困难。
要求退镀液必须对基体无腐蚀,其次镀层厚度、退镀速度、退镀成本等因素都要考虑。
(1)化学退镀法:化学退镀法不使工件受腐蚀,适用几何形状复杂的工件,且可做到退镀均匀。
配方1:浓HNO3,20~60℃。
本液成本低,速度快(30~40μm/h),毒性小。
适用尺寸精密要求不高的工件退镀,防止带入水、退镀完毕迅速入盐酸中清洗后再用流动水清洗。
配方2:HNO3(1∶1),20~40℃,退速快(10μm/5~6min),适用不锈钢。
配方3:浓HNO3 1000ml/L,NaCl 20g/L,尿素10g/L(抑制NOX气体的生成),六次甲基四胺5g/L,室温,退速20μm/h。
配方4:间硝基苯磺酸钠60~70g/L,硫酸100~120g/L,硫氰酸钾0.5~1g/L,80~90,适用铜及铜合金工件的退镀,退镀表面为深棕色时,取出后充分清洗,再除棕色膜(N aCN 30g/L,NaOH 30g/L,室温)。
配方5:HNO3∶HF=4∶1(体积比),冬天适当加温,退速快,铁基体不腐蚀。
但HF一定要用分析纯(用工业级HF配槽,易发生爆炸)。
配方6:硝酸铵100g/L,氨三乙酸40g/L,六次甲基四胺20g/L,pH=6,室温,退速1/5min,成本低。
配方7:间硝基苯磺酸钠110~130g/L,氰化钠100~120g/L,氢氧化钠8~10g/L,柠檬酸三钠20~30g/L,80~90℃,适用精密钢铁件化学镀镍层的退除。
配方8:间硝基苯磺酸钠100g/L,NaOH 100g/L,乙二胺120ml/L,十二烷基硫酸钠0.1g/L,60~80℃。
028电镀件褪镀与返工

Craft
客户:/
Customer
产品名称:/
Part Name
产品编号:/
Part No.
文件编号:YG/PD--028
Document No
版本:第V0版
Revision
日期:2012-9-11
Date
版本
Revision
更改内容
Revision Details
生效日期
3.3褪镀时间以褪尽为准,新开炸水炸20-60分钟,旧炸水炸60-100分钟,经常检查工件是否褪净,时间过长时对胶件性能影响很大,当褪镀液超过120分钟不能褪干净电镀件时,就开新缸。对于枪色退镀,应间歇性地取出工件观察退镀情况,时间以镀层退净为准。
3.4炸房所有化学药品对人体有较大腐蚀性,操作时要戴劳保用品。所有在炸房工作现场的员工应保持地面清洁,吸塑盘摆放整齐,珍珠棉叠好装箱,按指定的位置摆放:
1.2生产线上通过挑选产生需返工件应用吸塑盘装好,集中起来送到炸房,不能随意摆放
1.3胶件从挂具上拆下或装上时,生产线上员工必须戴橡胶手套,炸房员工必须戴棉手套,每次只能取一个胶件
1.4电镀件炸好后放置到铁架上沥干水分,然后拆挂摆放到吸塑盘内,需加工的主要面朝上,不能重叠,每摆放一层放一层珍珠棉,以免造成胶件碰伤擦花
1.5装好盘的胶件应装箱贴上相应的标签
1.6检查返工件外观
1.7上挂并做好标记
1.8只过三臂粗化缸,其它工序按正常进行
1.9返工件不能超过两次褪镀
二、返洗流程
2.1按照待洗产品所对应的上挂作业指示书选择挂具。
2.2戴好手套,按照待洗产品所对应的上挂指示书上好挂
2.3关闭光铬缸电源。
2.4将上好挂的待洗产品如下工序清洗:
- 1、下载文档前请自行甄别文档内容的完整性,平台不提供额外的编辑、内容补充、找答案等附加服务。
- 2、"仅部分预览"的文档,不可在线预览部分如存在完整性等问题,可反馈申请退款(可完整预览的文档不适用该条件!)。
- 3、如文档侵犯您的权益,请联系客服反馈,我们会尽快为您处理(人工客服工作时间:9:00-18:30)。
Tonghe Street, North of Guangzhou Road, Guangzhou
510515, China
2. 5 锌合金件上不良铜镀层的退除 工艺 I: 硫酸 硝酸 盐酸 水 θ 工艺 II: 硫酸钠 θ Ja U 工艺 III: 硝酸钾 硼酸 θ Ja pH(用 HNO3 调节)
氯化铵
13 g/L
水
52 mL/L
θ
15 ~ 30 °C
工艺 IV:
过硫酸铵
50 g/L
氨水
100 mL/L
水
1 000 mL/L
θ
15 ~ 30 °C
注:该工艺最适用于弹簧钢上退镉。
2. 9. 3 镀镉层
工艺 I:
氰化钠
75 g/L
氢氧化钠
13 g/L
θ
15 ~ 30 °C
U
6V
工艺 II:
盐酸
1 000 mL/L
硫酸铜
130 ~ 160 g/L
醋酸 θ
300 ~ 450 mL/L 15 ~ 30 °C
注:该工艺也适用于退除青铜锡合金层。
工艺 IV:
盐酸
1 000 mL/L
三氧化二锑
12 g/L
• 17 •
退除不良镀层的方法(二)
水
50 g/L
θ
15 ~ 30 °C
注:该工艺也适用于退除镍、钴钢件上的锡层。
工艺 VII:
氢氧化钠50 ~ 150 g/Lθ Ja 2. 7. 2
铜及黄铜基材
15 ~ 30 °C 2 ~ 3 A/dm2
工艺 I:
硫酸铁
100 g/L
硫酸
100 mL/L
θ
75 °C
工艺 II:
氟硼酸 θ
400 g/L 70 °C
Ja 阴极
1 ~ 5 A/dm2 铜板
工艺 III:
三氯化铁
75 ~ 100 g/L
1份 1份 1/16 份 1份 15 ~ 30 °C
12 g/L 15 ~ 30 °C 3 ~ 4 A/dm2
2 V 左右
150 ~ 200 g/L 40 ~ 50 mL/L
15 ~ 30 °C 5 ~ 8 A/dm2
5.4 ~ 5.8
收稿日期:2008–10–24 作者简介:程沪生(1932–),男,高级工程师,主要从事金属及非金属 电镀工作。 作者联系方式:(Tel) 020–37352653。
2. 8 不良铅锡合金镀层的退除
2. 8. 1 铜及铜合金基材
工艺 I:
三氯化铁
80 g/L
硫酸铜
120 g/L
醋酸
350 mL/L
双氧水
少量
θ
15 ~ 30 °C
工艺 II:
氟硼酸
10 ~ 15 g/L
双氧水
2 ~ 4 mL/L
θ
15 ~ 30 °C
工艺 III:
盐酸
500 mL/L
双氧水
3 ~ 5 mL/L
也可将镀件直接渍浸在较浓的过硫酸铵溶液中退除。
2. 6. 3 钢铁基材
氰化钠
75 ~ 94 g/L
氢氧化钠
12 ~ 16 g/L
θ
15 ~ 30 °C
U
6V
阴极
钢板
2. 6. 4 铝基材
硫酸
6份
水
1份
θ
15 ~ 30 °C
U
6V
阴极
铜板
2. 7 不良锡镀层的退除
2. 7. 1 钢铁基材
工艺 I:
氢氧化钠
工艺 III:
氢氧化钠
50 ~ 100 g/L
氰化钠
50 ~ 100 g/L
θ
15 ~ 30 °C
Ja 工艺 IV:
1 ~ 2 A/dm2
硝酸
1 000 mL/L
氯化钠
40 g/L
θ
65 ~ 75 °C
注:防止水分带入;温度太高,则基体易被腐蚀。
工艺 V:
硝酸钾
100 ~ 150 g/L
θ
15 ~ 50 °C
Ja
5 ~ 10 A/dm2
pH
7 ~ 10
2. 9. 2 镀锌层
工艺 I:
盐酸
200 mL/L
θ
30 ~ 50 °C
工艺 II:
氢氧化钠
200 ~ 300 g/L
亚硝酸钠
100 ~ 200 g/L
θ
100 ~ 120 °C
注:该工艺最适用于高碳钢及弹簧钢上退锌。
工艺 III:
盐酸
1 000 mL/L
退除不良镀层的方法(二)
程沪生
(广州市广州大道北云涛花园 7 幢 404 室,广东 广州 510515)
摘 要:介绍了锌合金件上不良铜镀层的退除法,不良金镀层、
锡镀层、铅锡合金镀层,以及钢铁上其他不良镀层的退除法。
关键词:金;锡;铅锡合金;不良镀层;退除
中图分类号:TG178; TQ153
文献标志码:B
文章编号:1004 – 227X (2009) 07 – 0016 – 04
Methods for stripping bad deposits—Part II // CHENG
Hu-sheng
Abstract: Methods for stripping bad gold, tin and tin–lead
0.3 ~ 0.5 A/dm2 不锈钢
2. 10. 3 锌合金镀铬层
硫化钠
30 g/L
氢氧化钠
20 g/L
θ
15 ~ 30 °C
Ja 2. 10. 4 铝件镀铬层
2 A/dm2
硫酸
65%
甘油
5%
θ
15 ~ 30 °C
Ja 2. 10. 5 铝件氧化膜
1 ~ 2 A/dm2
工艺 I:
氢氧化钠
5 ~ 10 g/L
1 ~ 2 A/dm2 不锈钢
2. 10. 2 铜及铜合金镀银层
工艺 I:
硫酸
19 份
硝酸
1份
θ
25 ~ 40 °C
注:严禁带水入槽。
工艺 II:
氰化钾
12 ~ 13 g/L
双氧水(逐步加入)
15 ~ 30 g/L
θ
15 ~ 30 °C
工艺 III:
氰化钾
50 ~ 100
θ
15 ~ 30 °C
Ja 阴极
工艺 III:
硫酸
100%
铬酐
少量
θ
35 ~ 38 °C
U
6V
注:加入少量镍盐可提高退除效果。
• 16 •
退除不良镀层的方法(二)
2. 6. 2 镍层及铜镍锌、铜铁锌合金基材
工艺 I:
防染盐 S
10 ~ 30 g/L
氰化钠
40 ~ 60 g/L
柠檬酸钠
40 ~ 60 g/L
θ
90 ~ 100 °C
工艺 II:
氰化钠
12 ~ 25 g/L
氢氧化钠
3 ~ 12 g/L
θ
37 °C
U
1V
工艺 III:
氰化钠
25 ~ 37 g/L
碳酸钠
60 ~ 100 g/L
θ Ja 阴极
15 ~ 30 °C 1 ~ 2 A/dm2
钢板
工艺 IV:
氰化钠
120 g/L
双氧水
15 mL/L
θ
15 ~ 30 °C
注:双氧水分数次加入。
75 ~ 90 g/L
防染盐 S
75 ~ 90 g/L
θ
75 °C
工艺 II:
氢氧化钠
150 ~ 200 g/L
氯化钠
15 ~ 30 g/L
θ
80 ~ 100 °C
Ja 工艺 III:
1 ~ 5 A/dm2
氢氧化钠
500 g/L
亚硝酸钠
200 g/L
θ
100 °C
工艺 IV:
三氧化二锑
20 g/L
盐酸
工艺 III:
磷酸
3份
硫酸
1份
θ
15 ~ 30 °C
Ja ρ(用水调节)
2.5 ~ 3.5 A/dm2 1.55 g/mL
注:该工艺也适用于锌合金件。
2. 10 其他不良镀层的退除
2. 10. 1 锡、镍镀银层
氰化钠
25 ~ 37 g/L
碳酸钠
60 ~ 100 g/L
θ
15 ~ 30 °C
Ja 阴极
2. 9 钢铁件上其他不良镀层的退除
2. 9. 1 铜锡合金镀层
工艺 I:
氢氧化钠
60 ~ 75 g/L
三乙醇胺
60 ~ 70 g/L
硝酸钠
15 ~ 20 g/L
θ
30 ~ 50 °C
Ja 工艺 II:
1.5 ~ 2.5 A/dm2
防染盐 S
70 ~ 80 g/L
氰化钠
70 ~ 80 g/L
θ
80 ~ 100 °C
氨三乙酸
20 ~ 80 g/L
六次甲基四胺
10 ~ 30 g/L
θ
15 ~ 50 °C
Ja pH(用稀 HNO3 液调节) 工艺 II:
5 ~ 25 A/dm2 3~7
磷酸
740 ~ 760 mL/L
三乙醇胺
240 ~ 260 g/L
θ
65 ~ 90 °C
Ja
10 A/dm2
注:该工艺也适用于铝及铝合金基材。