不合格镀层的退除配方
PCB电镀镍工艺及故障原因与排除
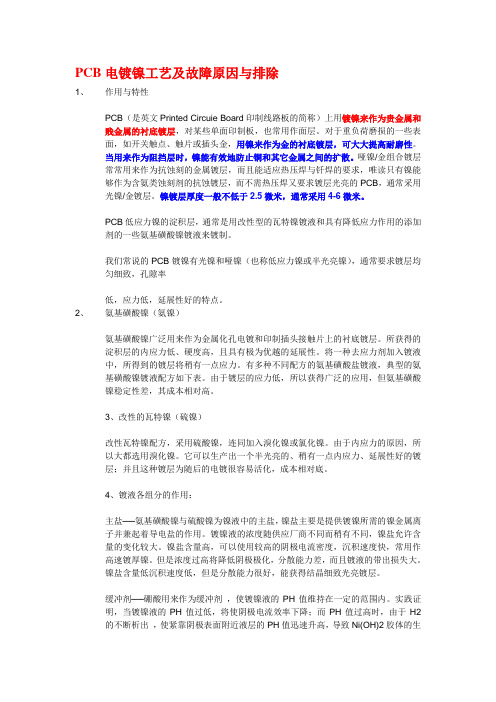
PCB电镀镍工艺及故障原因与排除1、作用与特性PCB(是英文Printed Circuie Board印制线路板的简称)上用镀镍来作为贵金属和贱金属的衬底镀层,对某些单面印制板,也常用作面层。
对于重负荷磨损的一些表面,如开关触点、触片或插头金,用镍来作为金的衬底镀层,可大大提高耐磨性。
当用来作为阻挡层时,镍能有效地防止铜和其它金属之间的扩散。
哑镍/金组合镀层常常用来作为抗蚀刻的金属镀层,而且能适应热压焊与钎焊的要求,唯读只有镍能够作为含氨类蚀刻剂的抗蚀镀层,而不需热压焊又要求镀层光亮的PCB,通常采用光镍/金镀层。
镍镀层厚度一般不低于2.5微米,通常采用4-6微米。
PCB低应力镍的淀积层,通常是用改性型的瓦特镍镀液和具有降低应力作用的添加剂的一些氨基磺酸镍镀液来镀制。
我们常说的PCB镀镍有光镍和哑镍(也称低应力镍或半光亮镍),通常要求镀层均匀细致,孔隙率低,应力低,延展性好的特点。
2、氨基磺酸镍(氨镍)氨基磺酸镍广泛用来作为金属化孔电镀和印制插头接触片上的衬底镀层。
所获得的淀积层的内应力低、硬度高,且具有极为优越的延展性。
将一种去应力剂加入镀液中,所得到的镀层将稍有一点应力。
有多种不同配方的氨基磺酸盐镀液,典型的氨基磺酸镍镀液配方如下表。
由于镀层的应力低,所以获得广泛的应用,但氨基磺酸镍稳定性差,其成本相对高。
3、改性的瓦特镍(硫镍)改性瓦特镍配方,采用硫酸镍,连同加入溴化镍或氯化镍。
由于内应力的原因,所以大都选用溴化镍。
它可以生产出一个半光亮的、稍有一点内应力、延展性好的镀层;并且这种镀层为随后的电镀很容易活化,成本相对底。
4、镀液各组分的作用:主盐──氨基磺酸镍与硫酸镍为镍液中的主盐,镍盐主要是提供镀镍所需的镍金属离子并兼起着导电盐的作用。
镀镍液的浓度随供应厂商不同而稍有不同,镍盐允许含量的变化较大。
镍盐含量高,可以使用较高的阴极电流密度,沉积速度快,常用作高速镀厚镍。
但是浓度过高将降低阴极极化,分散能力差,而且镀液的带出损失大。
镀金工艺

B。金缸
(1)PH值升高,可提高电流效率和有利于镀层合金成份的电 沉积。 PH值降低,镀层为应力降低,硬度降低。 (2)T T升高可提高电流效率和镀金层中合金铖份的含量。 T降低内应力降低,硬度降低,合金含量降低。 (3)电流浓度 电流浓度升高,电流效率升高,太高会烧焦。
C。药水开缸及控制范围
开缸加药量 条件 开缸 氨基磺酸镍(g/e) 400L 氯化镍(g/e) 1.70kg 硼酸(g/e) 17kg 阳极活化剂(ml/e) 17L ACR3010 Di水 50L MP7100 DI水 360L 金盐 45kg
机理: + H3BO3 H + H2BO3 2+ H2BO3 H + HBO2 + 23HBO3 H + BO3 除缓冲作用以外,还能提高阴极板化,改善 镀液性能,在高电流密度条件下,使镀层结 晶细致,不易烧焦。 (4)光剂 可使镀层晶粒减小,具有一定光泽,芳香 族 含苯环有机物。光剂过高会给镀层压应力。
。 (2)氯化镍 阳极活化剂,但其浓度不能超过30g/l,因氯 离子太高会增加镀层应力。 阳极钝化有以下表现: 1)电流升不上去,槽电压高,可达6V以上。 2)阳极上气泡较多,有时会有刺激气味, 甚至阳极表面褐色。 (3)硼酸 镀液PH值缓冲剂,缓冲范围PH值 4-5。有资 料建议40~45g/l。
药水的控制范围
缸名
镀镍缸
名称
Ni NICL3 H3 BO 3 ACR3010 PH Au S.G PH
WI范围
140~160g/e 5~15g/e 25~35g/e 20~30ml/e 3.8~4.4 2~5g/e 0.063~1.200 4.2~4.6
镀金缸
药水的控制范围
表面处理后不良品处理流程

1 . 0 目的:为使产品退镀、重镀质量能够有效掌控,使不合格品(料)的退镀、重镀管制及处理流程清晰明了,杜绝品质问题发生或再发生,减少返工造成的报废,特制定本流程。
2 . 0 范围:机电事业部内部及所有表面处理供应商各阶段所产生的不合格品,需退镀、重镀均适用。
3 . 0 权责:生产:不合格品的提报与协助处理、矫正及预防措施的执行。
供应商:不合格品的提报与协助处理、矫正及预防措施的执行。
品管:产品的检验及区分和预防措施执行效果跟进确认。
4 . 0 定义:4 . 1不合格之阳极氧化和电镀需退镀、重镀:凡本事业部之物料、在制程及仓储半成品/成品或委外加工有不符合本事业部规定要求或不能满足客户需求者。
4 . 2阳极氧化与尺寸变化:阳极氧化是铝及其合金在相应的电解液和特定的工艺条件下,在铝制品(阳极)上形成一层氧化膜的过程。
阳极氧化如果没有特别指明,通常是指硫酸阳极氧化。
外形尺寸阳极后单边变小约-0.005mm至-0.010mm,内径尺寸阳极后单边变大约+0.005mm至+0.010mm;硬质阳极有0.060mm至0.20mm变化(一般根据膜厚要求加工);4 . 3化学电镀与尺寸变化:当将某种镀件放入金属盐与可溶性还原剂共存的溶液中时,通过还原剂的氧化,其所释放出的电子转移到金属离子上,从而在镀件表面上析出金属而形成金属皮膜,这种不需要通入电流而是基于化学上的还原作用而实现的电镀,通常称为化学电镀(亦称为无电解电镀)。
电镀层比较均匀,从增厚几个微米到几十个微米不等。
5 . 0 作业程序:5 . 1 表面处理后不合格品处理流程:5.1.1 经检验判定为不合格品,应按其不良性质区分:①贴示黄色“不合格”标签,区分供应商不良及内部不良和不良项目。
②放置在相应胶箱后放入“不合格区”作为识别,内部不良开出《物料异常处理单》处理,供应商不良超出不良比例应开出SCAR反馈供应商改善。
5.1.2 退镀重镀品处理:直接退供应商退镀后重镀。
氰化仿金电镀工艺

氰化仿金电镀工艺(一)铜锌合金仿金电镀铜锌合金的仿金镀层很薄,一般只有0.3~1μm,其中含有铜70%~80%、锌约20%~30%。
为了防变色并效果好,还可以添加少量其他一元金属。
仿金镀层的颜色不仅与铜和锌的含量及比例有关,而且与镀液的成分及工艺条件有着密切关系。
镀铜锌合金仿金镀层溶液配方及工艺条件如下:氰化亚铜(CuCN) 75g/L 溶液温度20~22℃氰化锌[Zn(CN)2] 9g/L 电流密度2~10A/dm2氰化钠(总量,NaCN) 55g/L 阳极材料铜(70%)、锌(30%)氰化钠(游离,NaCN) 15~25g/L合金板碳酸钠(Na2CO3)6~25g/L电镀时间视镀层厚度而定氟化钠2~5g/L仿金镀层出镀后,对空气和水中的杂质极其敏感,因此必须用纯净水或无离子水清洗最后一道工序,同时必须马上进行钝化处理。
钝化处理的溶液配方如下:铬酐(Cr03) 2~5g/L 氧化锌(ZnO) 0.8g/L销酸(HN03) 1mL/L 阴离子表面活性剂0.2mL/L所得的钝化膜是一层看不见、透明的薄膜,它不仅可以增加耐蚀性,在存放时可抗色变,同时还可以增加仿金镀层与最后涂刷清漆层之间的附着力。
仿金镀层钝化后必须迅速干燥,最后一次也应用无离子水清洗。
用木屑烘干是一种有效的干燥方法,能够可靠地防止干燥后出现的斑点。
仿金镀层干燥后应马上涂透明清漆,以便隔绝镀层与氧接触,避免由于氧化而颜色变暗的情况出现。
6~12μm的环氧基罩光漆或清漆效果较好,环氧基罩光漆的耐磨性能较好,产品在使用过程中不会变色,漆膜不易破损。
漆膜涂覆后在30~40min内硬化,但要在90~100℃下干燥24h。
这种仿金镀层有沉积速度快、镀层厚度只有0.3~1.0μm、复杂零件上的仿金镀层色泽基本均匀一致而操作简便等特点。
(二)铜锡合金仿金电镀铜锡基合金仿金电镀效果也很好,其溶液的基本配方及工艺条件如下:氰化亚铜(CuCN) 30g/L 氰化钾(总,KCN) 40g/L锡酸钠(Na2Sn03) 15g/L 氰化镍钾[KzNi(CN)4] 5g/L氨基磺酸钠[Na2(NH2S03)2] 10g/L 溶液温度20~30℃氨基磺酸铟[In(NH2S03)2] 6g/L 电流密度3A/din2酒石酸钾钠[NaKC4H46] 20g/L如果在溶液中再添加2g/L苹果酸或柠檬酸,可获得良好的黄铜色泽;若添加10g/L柠檬酸,可得到18K金色;把柠檬酸的含量提高到20g/L时,可以镀得玫瑰金色泽。
第6章电镀镍(2)解析

0.2g/l时,阴极电流效率显 步降低到0.2A/dm2,将NO3-还原为铵根至溶
著下降,镀层呈黑色
液正常为止
有机 杂质
镀层发脆,发黑或发亮,产 生条纹,针孔等
定期加双氧水,活性炭联合处理
第三节 光亮镀镍
光亮镀镍镀液在目前镀镍工艺中应用最普遍、最广泛。它的特点是依 靠不同光亮剂的良好配合,能够在镀液中直接获得全光亮并具有一定整平 性的镀层,现代光亮镀镍工艺,绝大多数是在瓦茨型镀镍液中加入光亮剂 而获得的。
2.5 工艺维护
(1)使用合格的硫酸镍 尤其注意锌杂质的含量,应先化验再使用,含 锌量高,低电流密度区发黑,难处理;
(2)阳极可使用电解镍板或镍块(需用阳极套); (3)经常测定并调整溶液的pH值; (4)杂质的影响和去除方法(见下表)
杂质 危害含量 种类 (g/l)
Fe2+
0.030.05
表6-3 杂质的影响和去除方法
当阳极电流密度过高,镀液中又缺乏阳极活化剂时,将会发生阳极钝 化,并有析出氧气的副反应:
2H2O - 4e = O2↑+4H+ 加入C1-离子可以防止阳极钝化,但也可能发生析出氯气的副反应:
2C1- - 2e = Cl2 ↑
2.4 镀液中主要成分的作用及操作条件对镀层性能的影响
(1)硫酸镍 是镀液的主要成分,是镍离子的来源,在暗镍镀液中,一 般含量是150g/L~300g/L。硫酸镍含量低,镀液分散能力好,镀层结晶细 致,易抛光,但阴极电流效率和极限电流密度低,沉积速度慢,硫酸镍
1.5 镀镍的类型
以镀液种类来分,有硫酸盐、硫酸盐一氯化物、全氯化物、氨磺酸盐、 柠檬酸盐、焦磷酸盐和氟硼性盐等镀镍。由于镍在电化学反应中的交换 电流密度(i0)比较小,在单盐镀液中,就有较大的电化学极化。
深镀能力研究
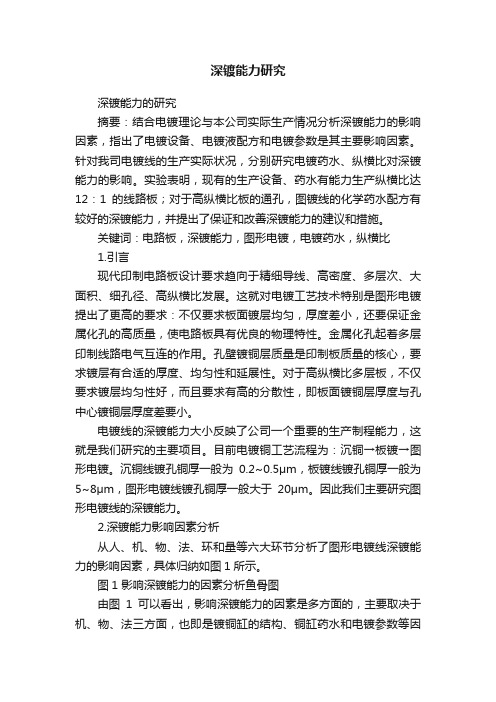
深镀能力研究深镀能力的研究摘要:结合电镀理论与本公司实际生产情况分析深镀能力的影响因素,指出了电镀设备、电镀液配方和电镀参数是其主要影响因素。
针对我司电镀线的生产实际状况,分别研究电镀药水、纵横比对深镀能力的影响。
实验表明,现有的生产设备、药水有能力生产纵横比达12:1的线路板;对于高纵横比板的通孔,图镀线的化学药水配方有较好的深镀能力,并提出了保证和改善深镀能力的建议和措施。
关键词:电路板,深镀能力,图形电镀,电镀药水,纵横比1.引言现代印制电路板设计要求趋向于精细导线、高密度、多层次、大面积、细孔径、高纵横比发展。
这就对电镀工艺技术特别是图形电镀提出了更高的要求:不仅要求板面镀层均匀,厚度差小,还要保证金属化孔的高质量,使电路板具有优良的物理特性。
金属化孔起着多层印制线路电气互连的作用。
孔壁镀铜层质量是印制板质量的核心,要求镀层有合适的厚度、均匀性和延展性。
对于高纵横比多层板,不仅要求镀层均匀性好,而且要求有高的分散性,即板面镀铜层厚度与孔中心镀铜层厚度差要小。
电镀线的深镀能力大小反映了公司一个重要的生产制程能力,这就是我们研究的主要项目。
目前电镀铜工艺流程为:沉铜→板镀→图形电镀。
沉铜线镀孔铜厚一般为0.2~0.5μm,板镀线镀孔铜厚一般为5~8μm,图形电镀线镀孔铜厚一般大于20μm。
因此我们主要研究图形电镀线的深镀能力。
2.深镀能力影响因素分析从人、机、物、法、环和量等六大环节分析了图形电镀线深镀能力的影响因素,具体归纳如图1所示。
图1 影响深镀能力的因素分析鱼骨图由图1可以看出,影响深镀能力的因素是多方面的,主要取决于机、物、法三方面,也即是镀铜缸的结构、铜缸药水和电镀参数等因素。
(1)镀铜缸结构的影响铜缸的结构设计决定了电力线的宏观分布,而电流的分布情况又是影响深镀能力的最根本因素。
因此,只有当镀铜缸的结构设计合理时,才能得到良好的深镀能力。
镀铜缸的结构设计包括:缸体的大小,阴、阳极之间的距离及面积比,挂架上的夹具分布、夹具的良好等,阴极移动的频率和振幅、震动、打气、循环过滤等各方面,如图2所示。
弹簧弹片检验标准

弹簧/弹片检验标准1 目的适应本公司金属弹簧、弹片及其电镀件物料检验的需要。
2 适用范围本公司IQC所有金属弹簧、弹片及其电镀件来料。
3 引用文件《物料认可书》、BOM、ECO。
4 定义4.1 CRI(致命缺陷):违反相关安规标准,对安全有影响者。
4.2 MAJ(主要缺陷):属功能性缺陷,影响使用或装配。
4.3 MIN(次要缺陷):属外观、包装轻微缺陷,不影响使用或装配。
5 抽样方案5.1依据MIL-STD-105E II 一般检查,从不同的包装箱(包)内随机抽取来料,其中外观项6.2.3.4和功能测试项抽样数、判定按测试项说明。
5.2 AQL取值(抽样有特殊规定的除外):CRI(致命缺陷)=0;MAJ(主要缺陷)=0.65;MIN(次要缺陷)=2.5。
5.3 检验抽样方案转换原则(针对同一供应商同一型号的部品):5.3.1 正常检查到加严检查的条件:①连续5批中有2批(包括检验不到5批已发现2批)检验不合格;②主管者认为有必要。
以上两个条件必须同时满足。
5.3.2 加严检查到正常检查的条件:连续5批合格。
5.3.3 正常检查到放宽检查的条件:①连续10批检验合格;②10批中不合格品(或缺陷)总数在界限个数以下;③生产正常;④主管者认为有必要。
以上四个条件必须同时满足。
5.3.4 放宽检查到正常检查的条件:①1批检验不合格;②生产不正常;③主管者认为有必要。
只要满足以上三条件之一。
5.3.5 加严检查到暂停检查的条件:具体依质量预警处理。
5.4 抽样开箱(包)率要求:当同种物料来料>5箱(包)时检验开箱(包)率必须达到80%且不能小于5箱(包);当同种物料来料≤5箱(包)时检验开箱(包)率必须达到100%。
6 检验步骤:6.1 外包装检验:6.1.1 货品检验单:要求货品检验单上的供应商、送检单号、来货数量、物料编码、物料名称等与实物相符。
6.1.2 物料的包装:要求箱(包)内、外无异物、水、灰尘、破裂等情况。
达克罗涂层的检测方法的详细介绍

达克罗(涂层)防腐新技术沈志明(国营黄河机器制造厂,陕西西安710043)摘要:介绍了达克罗涂层新技术,它是解决铁基材料防腐的新材料、新技术,是一种远离酸、碱、无氢脆、无污染的绿色工艺。
关键词:达克罗涂层;防腐;新材料;绿色工艺1达克罗涂层技术的开发背景达克罗涂层技术在日本称Dacromet,在美国和欧洲则称为锌铬涂层技术。
达克罗涂层技术最早产生于20世纪60年代后期的美国,其最初是为解决汽车底盘零件遇含盐份的雨雪易发生锈蚀,威胁车辆运行安全而发明的一种防护技术。
70年代欧洲的法国、德国、意大利等国和80年代的日本先后引进了该项技术。
该项技术的成功应用大大提高了铁基材料的防腐性能。
90年代由国内某空降设备厂首家引进,在一项与德国合作的产品上成功的应用了此项涂层技术。
近五、六年国内陆续有22条生产线被引进,使达克罗涂层技术得到推广,呈燎原之势。
2引进达克罗涂层技术的目的2.1提高产品质量达克罗涂层技术与镀锌技术比较,是一项耐蚀性好、无氢脆、无污梁的绿色工艺,1987年10月美国军方颁布了以《浸入锌片/铬酸盐分散涂层》冠名的军标《MIL-C-87115A》。
使此项技术在陆、海、空军装备上广泛应用。
然而,产品锈蚀却是长期困扰国内很多企业的难题。
产品尚未出厂,经过淋雨试验后螺钉就锈得不像样,必须换新后才能出厂。
即便后来改成不锈钢螺钉也没从根本上解决问题。
当前装备部已指示各级部队着手解决装备严重锈蚀的课题。
2.2 解决钢结构件点焊并镀锌后出现的焊点锈蚀问题引进达克罗技术前,组合结构件采用点焊工艺和镀锌防护,表面质量与产品防护性皆差。
先点焊后镀锌,在组合件夹层间由于酸液清洗不干净,造成出厂后产品锈蚀。
若先镀锌后点焊则焊点处锌层破坏,外观质量不保。
工艺部门左右为难。
采用了达克罗技术后,因达克罗涂层技术远离酸、碱(镀液),避免了腐蚀问题。
更令人高兴的是涂达克罗零件点焊后焊点涂层完好,且无灼色。
至此,一切迎刃而解。
不合格品(HSF)处理流程图
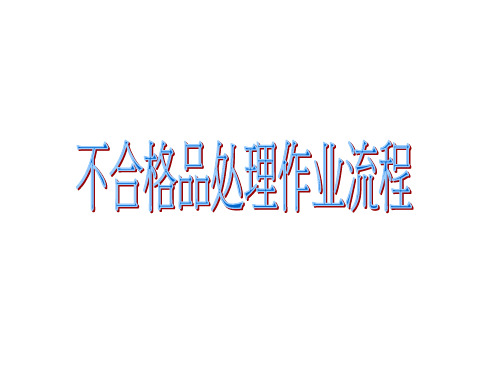
• 6.5.4 资材单位负责对于久存成品及半成品﹙确 定已无可出售机会、逾保存期限或无法重工利用 者﹚,经判定不良需报废时,依流程报废处理。
• 6.5.5 客供品若有质量异常状况发生时,发现单 位须立即以「纠正及预防措施单」反应;业务单 位负责人员则主导通知客户,并告知相关单位客 户允收与否之判定结果或后续应急处理之要求。
• 6.2.3.1不合格品召回的评审和处置
• 1)产品召回时机:
• 当公司存在不合格产品及影响批次产品已经不在公司控制 下时(如已经交付)必须启动召回流程,包括但不限于如 下情形都可能涉及召回产品,触发召回流程:
• a 客户的投诉
• b 主管部门检查发现的不合格品
• c 公司内部检查发现受不合格品影响的批次产品已交付
发生异常
原材料或部件中含 有禁止使用物质 异常连络书的发行
★报告品保部经理/总经理 ★与客户进行联络并报告 ★处理时需注意模向展开其 它料号与追踪上一批物料质 量状况
原因调查
工厂内部混入
纠正预防措施单的发行
供应商
异常工序
不合格对策处理确认会议 ◇库存品处理的确认 ◇防止再次发生的确认 ◇向其它部门或工序的水平推广
• 6.7.2 制造单位作业 • 6.7.2.1 制程重工、制程中产生之不合格品需维
修重工时,依〈制程检验管制程序〉执行。 • 6.7.2.2 需重工时,由生管人员开立 「生产重工
单」客户退回或已入库品因ECR变更经MRB判定, 依IE制定的〈重工SOP〉实施重工作业。 • 6.7.3 重工后产品,需依制程管制流程经品管检 验﹙IPQC、FQC、OQC﹚合格后,方可办理入库作 业。 • 6.8 特采作业流程 • 6.8.1特采之提出与管制 • 6.8.1.1申请特采作业时填写「特采申请单」;特 采案件成立后,于「特采管制表」中登录管制。
达克罗涂层的检测方法的详细介绍

达克罗涂层的检测方法的详细介绍根据2002年国家质量监督检验检疫总局发布了"锌铬涂层技术条件"的中华人民共和国国家标准,标准号为GB/T18684-2002,对达克罗涂层的检测主要有以下五项:一、外观:在自然折射光下,用肉眼进行观察。
锌铬涂层的基本色调应呈银灰色,经改性也可以获得其他颜色,如黑色等。
锌铬涂层应连续,无漏涂、气泡、剥落、裂纹、麻点、夹杂物等缺陷。
涂层应基本均匀,无明显的局部过厚现象。
涂层不应变色,但是允许有小黄色斑点存在。
二、涂敷量和涂层厚度的检测:标准对不同等级涂层的涂敷量或涂层厚度分为四个等级,可以采用二种方法进行检测:1,溶解称重法:重量大于50g试样,采用精度为1mg的天平称得原始质量W1(mg),将试样放入70℃~80℃的20%NaOH水溶液中,浸泡10min,使锌铬涂层全部溶解。
取出试样,充分水洗后立即烘干,在称取涂层溶解后的试样质量W2(mg)。
量取并计算出工件的表面积S (dm2 ),按下列公式计算出涂层的涂覆量W(mg/dm2):W=(W1-W2)/S2,金相显微镜法:按GB/T6462要求,采用金相显微镜法检测涂层的厚度。
三、附着强度试验:采用胶带试验方法,检测锌铬涂层与基体的附着强度,胶带试验按GB/T5270-1985第1.4要求进行。
要求试验后涂层不得从基体上剥落或露底,但允许胶带变色和粘着锌、铝粉粒。
耐水性能试验:把试样浸入40℃±1℃的去离子水中,连续浸泡240h,将试样取出后在室温下干燥,再进行附着强度试验,试验结果应达到附着强度试验的要求。
附着强度试验应在试样从去离子水中取出后的2h之内进行。
进行耐水性试验后,涂层不得从基体上剥落或露底。
四、耐盐雾性能试验:耐盐雾性能试验按GB/T10125-1997第3.2.1要求进行。
涂层经盐雾试验后,按涂层上出现红锈的时间从120小时到1000小时,分为四个等级。
五、湿热试验:湿热试验在湿热试验箱中进行,湿热试验箱应能调整和控制温度和湿度。
表面处理技术要求规范
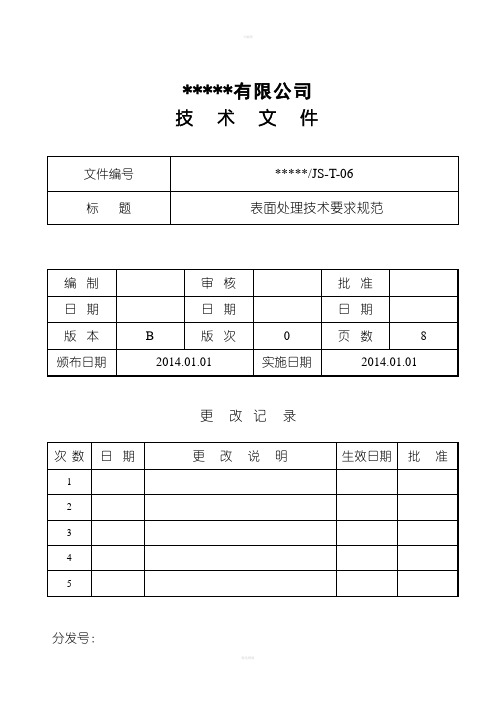
*****有限公司技术文件更改记录分发号:/JS-T-06目次一.镀NiP工艺规范二. 发黑工艺规范三. 磷化工艺规范/JS-T-06一镀NiP工艺规程1.主题内容和适用范围本规程规定了对产品部件进行化学镍磷的一般要求。
2.一般要求2.1 所有要求表面镀镍磷的工件,均须严格按照本规程规定的工艺控制程序进行金属表面的处理准备2.2每一控制程序操作完,均须由质检员对部件表面处理情况进行检查,达到控制要求后方可转入下一程序;2.3化学镀镍磷的厚度一般要求在0.01mm,由检验员检验测定,符合要求的部件才可办理入库手续、3.控制程序3.1除油待处理部件首先要除去表面油污。
除油效果以破水检查合格的为准。
3.2水洗将经除油处理后的表面用水冲洗干净;3.3除锈除油水洗之后的表面要进行除锈处理。
局部较厚的氧化膜,可用钢丝刷除去。
除锈后金属部件表面要露出金属光泽;3.4水洗用清水冲掉经除锈处理的表面锈尘;3.5电解除油严格按照电解除没的工艺要求对部件进行电解除油,以除去不良性组织层及前序未除去的金属粉尘,为后序提供一微观粗糙表面。
电解除油后的表面严禁用手触摸。
3.6表面活化处理严格按照活化处理工艺对电解除油后的部件表面进行活化处理,以除去电解处理后部件表面的钝化膜,生成新的表面,活化处理后用白布擦抹,无黑灰方合格。
4.检验要求4.1外观:镀层色泽要均匀,表面光滑;4.2尺寸:对重要配合尺寸,对镀层部位的镀后总尺寸进行检验,符合要求。
/JS-T-06二发黑工艺规范1主题内容与适用范围本规程规定了常发黑操作程序及要点。
本规程适用于钢、铁、铸铁件的常温表面发黑处理。
2准备2.1 检查待发黑工件的质量2.1.1 工件表面不得有裂纹、磕伤、漆膜和金属镀层。
2.1.2 表面不得有严重锈蚀难以去掉的厚氧化皮。
2.1.3 工件有装饰性要求时,表面粗糙度应达到,一般应达到。
2.1.4 准备好工具、料框及起吊用具、发黑盆或桶等。
2.1.5 配制后除锈酸液,一般用10%~15%盐酸水溶液。
不合格镀层的退除配方
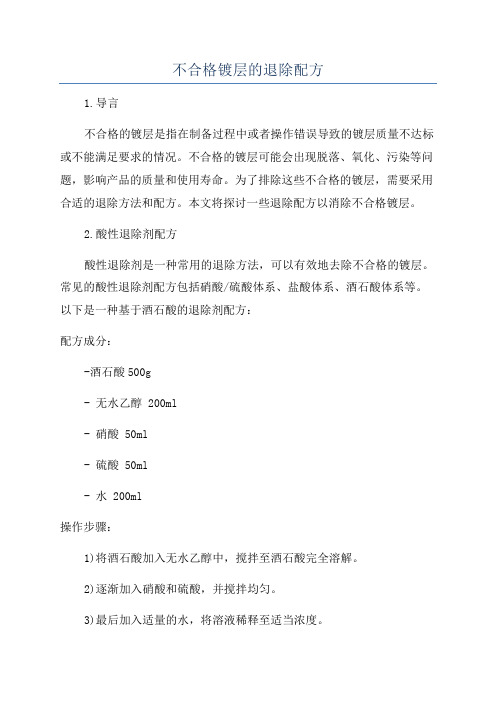
不合格镀层的退除配方1.导言不合格的镀层是指在制备过程中或者操作错误导致的镀层质量不达标或不能满足要求的情况。
不合格的镀层可能会出现脱落、氧化、污染等问题,影响产品的质量和使用寿命。
为了排除这些不合格的镀层,需要采用合适的退除方法和配方。
本文将探讨一些退除配方以消除不合格镀层。
2.酸性退除剂配方酸性退除剂是一种常用的退除方法,可以有效地去除不合格的镀层。
常见的酸性退除剂配方包括硝酸/硫酸体系、盐酸体系、酒石酸体系等。
以下是一种基于酒石酸的退除剂配方:配方成分:-酒石酸500g- 无水乙醇 200ml- 硝酸 50ml- 硫酸 50ml- 水 200ml操作步骤:1)将酒石酸加入无水乙醇中,搅拌至酒石酸完全溶解。
2)逐渐加入硝酸和硫酸,并搅拌均匀。
3)最后加入适量的水,将溶液稀释至适当浓度。
使用方法:1)将退除剂溶液倒入适当大小的容器中。
2)将待处理的不合格镀层浸泡在退除剂中,时间根据实际情况决定。
3)定期检查不合格镀层的退除情况,并根据需要调整浸泡时间。
4)镀层完全退除后,用水冲洗并进行干燥处理。
3.碱性退除剂配方碱性退除剂可以快速有效地去除一些不合格的镀层,特别是一些有机物的污染物。
常见的碱性退除剂配方包括氢氧化钠、氢氧化钾等。
以下是一种基于氢氧化钠的退除剂配方:配方成分:-氢氧化钠1000g- 纯水 1000ml操作步骤:1)将适量的纯水加入容器中,并加热至60-70℃。
2)逐渐加入氢氧化钠,并充分搅拌均匀。
3)搅拌至溶液完全溶解,并冷却至室温。
使用方法:1)将退除剂溶液倒入适当大小的容器中。
2)将待处理的不合格镀层浸泡在退除剂中,时间根据实际情况决定。
3)定期检查不合格镀层的退除情况,并根据需要调整浸泡时间。
4)镀层完全退除后,用水冲洗并进行干燥处理。
4.机械研磨配方对于一些比较厚重的不合格镀层,可以采用机械研磨的方法进行退除。
机械研磨可以通过研磨材料的硬度和研磨方法的控制,去除不合格镀层而不会对基材造成损伤。
电镀工艺的基本要求
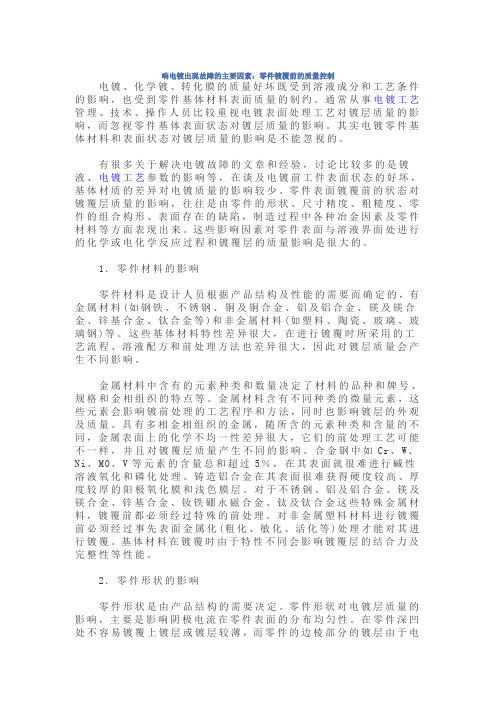
响电镀出现故障的主要因素:零件镀覆前的质量控制电镀、化学镀、转化膜的质量好坏既受到溶液成分和工艺条件的影响,也受到零件基体材料表面质量的制约。
通常从事电镀工艺管理、技术、操作人员比较重视电镀表面处理工艺对镀层质量的影响,而忽视零件基体表面状态对镀层质量的影响。
其实电镀零件基体材料和表面状态对镀层质量的影响是不能忽视的。
有很多关于解决电镀故障的文章和经验,讨论比较多的是镀液、电镀工艺参数的影响等,在谈及电镀前工件表面状态的好坏,基体材质的差异对电镀质量的影响较少。
零件表面镀覆前的状态对镀覆层质量的影响,往往是由零件的形状、尺寸精度、粗糙度、零件的组合构形、表面存在的缺陷,制造过程中各种冶金因素及零件材料等方面表现出来。
这些影响因素对零件表面与溶液界面处进行的化学或电化学反应过程和镀覆层的质量影响是很大的。
1.零件材料的影响零件材料是设计人员根据产品结构及性能的需要而确定的,有金属材料(如钢铁、不锈钢、铜及铜合金、铝及铝合金、镁及镁合金、锌基合金、钛合金等)和非金属材料(如塑料、陶瓷、玻璃、玻璃钢)等。
这些基体材料特性差异很大,在进行镀覆时所采用的工艺流程、溶液配方和前处理方法也差异很大,因此对镀层质量会产生不同影响。
金属材料中含有的元素种类和数量决定了材料的品种和牌号、规格和金相组织的特点等。
金属材料含有不同种类的微量元素,这些元素会影响镀前处理的工艺程序和方法,同时也影响镀层的外观及质量。
具有多相金相组织的金属,随所含的元素种类和含量的不同,金属表面上的化学不均一性差异很大,它们的前处理工艺可能不一样,并且对镀覆层质量产生不同的影响。
合金钢中如Cr、W、N i、M0、V等元素的含量总和超过5%,在其表面就很难进行碱性溶液氧化和磷化处理。
铸造铝合金在其表面很难获得硬度较高、厚度较厚的阳极氧化膜和浅色膜层。
对于不锈钢、铝及铝合金、镁及镁合金、锌基合金、钕铁硼永磁合金、钛及钛合金这些特殊金属材料,镀覆前都必须经过特殊的前处理。
- 1、下载文档前请自行甄别文档内容的完整性,平台不提供额外的编辑、内容补充、找答案等附加服务。
- 2、"仅部分预览"的文档,不可在线预览部分如存在完整性等问题,可反馈申请退款(可完整预览的文档不适用该条件!)。
- 3、如文档侵犯您的权益,请联系客服反馈,我们会尽快为您处理(人工客服工作时间:9:00-18:30)。
不合格镀层的退除配方
配方1钢铁基体上镍电镀层的退除(一)
间硝基苯磺酸钠70-80g/L
氢氧化钠025g/L
氰化钠70-80g/L
水加至1L
描述工艺条件:处理温度为6070℃
配方2钢铁基体上镍电镀层的退除(二)
铬酐250300g/L
硼酸25-30g/L
水加至1L
描述工艺条件:电流密度57A/dm2,温度为室温,阴极为铅板。
配方3钢、铜、黄铜及锌压铸件镍镀层的退除
硫酸50%-60%
乙二醇3%
水37%-47%
描述工艺条件:温度为室温,电压3-6V,电流密度6-20A/dm2,阴极为铅板。
配方4铜基体上镍镀层的退除(化学法)
硫酸100.0-120.Og/L
间硝基苯磺酸钠60.070.Og/L
硫氰酸钾0.5-l.Og/L
水加至1.01
描述将要退镀的工件浸入退镀液中,退至表面为深棕色,清洗后用细纱布抛光去膜即可。
配方5钢基体上镍镀层的退除(电解法)
氯化钠130-150g/L
盐酸20-30g/L
磷酸1-3g/L
水加至1L
描述将工件浸入电解液,工作电压为15-20V,相对运动速度为
15m/min,电源极性反接。
配方6带有黄铜件或铜件的钢零件上镍镀层的退除
间硝基苯磺酸钠40.0-70.Og/L
硫酸60.0-70.OmL/L
硫氰酸钠0.1-l.Og/L
水加至1.01
描述处理温度为8090℃,时间以表面由黑色变为深棕色为准。
配方7铜及铜合金基体上化学镀镍层的退除
乙二胺50-lOOmL/L
间硝基苯磺酸钠25-50g/L
乙二胺四醋酸1020g/L
硫脲1-5g/L
描述处理液的温度为50-80。
C,pH值(用醋酸调整)为7.5-8.O。
配制时以水为溶剂。
配方8钢铁基体上镍铁合金镀层的退除(一)
间硝基苯磺酸钠80-lOOg
焦磷酸钾120-160g
乙二胺120-160mL
水加至1L
描述本处理液的pH值(用醋酸调整)为8.0~9.5,温度为80100℃。
配方9钢铁基体上镍铁合金镀层的退除(二)
硫酸(工业级)300-400mL
六亚甲基四胺(工业级)2535g
水加至1L
描述工艺条件:阴阳极面积比2:1,电流密度1030A/dm2,温度为室温至65℃。
配方10钢铁基体上镍铁合金镀层的退除(三)
硝酸铵240g/L
硫氰酸铵lg/L
溴化钠6g/L
葡萄糖酸钠lOg/L
水加至1L
描述工艺条件:pH值(用稀硝酸调整)5.5;温度20-300C;电流密度10A/dm2;退除速度,不搅拌时2μm/min,搅拌时2.5μm/min。
配方11不合格镍铁合金镀层的退除
浓硝酸1000mL
氯化钠15g/L
描述处理温度为室温,处理时间退完为止。
镍铁合金镀层的合格率可达
95%一98%。
对于镀层不亮、局部发花和毛刺的镀件不必全退,可以
稍作处理后重镀薄层低铁合金,再套铬。
如已套铬件用1:1的盐酸退铬
后进行修复。
零件要干燥入槽,否则易发生过腐蚀。
实际生产中根据不
同的要求常采用单层或多层镍铁合金体系。
采用多层合金时,零件上先
镀一层高铁合金(含铁250-/0-35%),再镀一层低铁合金
(10%-15%)。
配方12钢铁基体上不良铜层的退除(化学法)
铬酐400g/L
硫酸50g/L
水加至1L
描述本配方适用于化学法退除钢铁基体上的不良铜层。
配方13钢铁基体上不良铜层的退除(电解法)
铬酐250g/L
硼酸25g/L
碳酸钡3-5g/L
水加至IL
描述本配方适用于电解法退除不良铜层。
工作电压为10-15V,操作
温度为室温。
配方14H202/H2S04法溶解不锈钢铜包套
过氧化氢(30%)200-400mL/L
浓硫酸(98%)100-120mUL
BS稳定剂(西北有色金属研究院)7-lOg/L
水加至1L
描述先加入配方总量1/3的蒸馏水或母液,再在搅拌下缓慢加入硫酸,当温度回落至40-50CC时加入稳定剂,最后加入过氧化氢。
溶解不锈
钢铜包套是不锈钢精加工过程中一个重要步骤,本工艺避开了硝酸法,
成本低、环境污染小,并可以得到纯度较高的副产品硫酸铜。
配方15不合格镀铅层的去除(化学法)
醋酸(96%-980-/0)1L
过氧化氢(30%)30-lOOmL
描述将镀件置于溶液中,用棉花擦拭,到镀层退净为止。
配方16不合格镀铅层的去除(电解法)
氢氧化钠10%
水90%
描述在1O%碱溶液中,于温度60-70℃、阳极电流密度13A/dm2的情况下进行电解,至镀层退净为止。
配方17镀锌层的退除(化学法)
氢氧化钠200-300g/L
亚硝酸钠1OO-200g/L
水加至1L
描述本剂用化学法退除弹性零件、高强度零件以及质量要求高的零件表
面上的不合格锌镀层。
处理温度为100℃,时间以退净为止。
配方18镀锌层的退除(电解法)
柠檬酸钠208.Og/L
柠檬酸56.Og/L
氟硼酸2.lg/L
水加至1.01
描述本剂适用于电化学法退除锌层。
工作电压为15-20V,相对运动
速度为6-15m/min,电源极性反接,温度为20-35℃,pH值为4.8。
配方19金属锡镀层去除剂
盐酸(37%)80mL
硫酸铜150g
三氯化铁150g
水加至1000mL
描述将各组分溶于水,搅匀即成。
本剂用于零件或制品表面不合格或在
使用过程中受损坏要进行返修时使用。
适用于除去铜基材料上锡镀层,
可在室温进行。
配方20化学法退锡
氢氧化钠80-lOOg/L
间硝基苯磺酸钠7090g/L
水加至IL
描述本剂用于退除不合格的镀锡层,处理温度800C至沸腾,处理时间以退净为止,退除过程中注意翻动零件。
配方21电化学法退锡
氢氧化钠150一200g/L
氯化钠10-15g/L
水加至1L
描述本法用于退除不合格的镀锡层。
温度80-1OO℃,阳极电流密度5A/dm2,阴极为不锈钢板,时间退净为止。
配方22多种镀层的化学去除剂
氟硼酸(40%)125mL
过氧化氢(30%)38mL
水加至1000mL
描述本品适用于钢铁基体和铜基体上的镀锡层、镀铅层、镀铅锡合金层的去除,可在室温条件下使用。
配方23不合格镀镉层的去除(一)
铬酐140-250g/L
硫酸3-4g/L
水加至1L
描述处理温度为室温,处理时间以退净为止。
配方24不合格镀镉层的去除(二)
硝酸铵200-250g/L
水加至1L
描述处理温度为18-25℃,处理时间以退净为止。
本配方既适用于化学溶解,也适用于电化学溶解。
电化学溶解时,温度为40-60℃,阳极电流密度为5-10A/dm2,零件挂在阳极上,阴极为铁板。
配方25不合格镀镉层的去除(三)
盐酸50-lOOg/L
水加至lL
描述处理温度为室温,处理时间以退净为止。
本配方适用于退除铜件上的镀镉层。
配方26退镀液
硝酸100.Og/L
盐酸50.Og/L
过氧化氢15.Og/L
六亚甲基四胺1.0-1.5g/L
水加至1.01
配方27常用塑料制品镀层退除工艺
方法1
盐酸lOOmL/L
过氧化氢(30%)80-lOOmUL
水加至1L
描述处理温度≤800C,处理时间以退净为止。
方法2
三氯化铁l00-300g/L
盐酸60-80mL/L
水加至IL
描述处理温度40-50C,处理时间以退净为止。