品质问题停线和恢复程序
OCAP品质异常处理流程图-经典

1、生产部开始转入正常的《生产制作流 程》; 2、品质部负责《品质异常联络单》上传 、归档。
流程结束。
异常原因分析 及确认
4
产线开始
5
试做或返工
不合格品
6
继续生产 7
8
生产制作流程
9
NG 确认对策 是否有效
OK
品质异常 联络单
结束
技术部
OCAP工作流程图
开发部
采购部
分析造成异 常現象的原
因
分析造成异 常現象的 原
因
拟定临时对策
拟定永久对策
理
总经理核 准
作业指导
1、生产部门主导品质异常的提出; 2、品质部判定异常是否正确,NG继续生 产,OK进入第2段落; 3、异常标准: 1h内同种不良超10﹪;
4异常原因分析及确认拟定临时对策产线开始试做或返工不合格品供应商改善对策5拟定永久对策ngng确认对策是否有效1技术部负责对责任部门拟定临时改善对策进行纠正措施包含原材料在制品成品等的处理方式
段落
1 2 3
生产部
品质异常联 络单
停线并开出
品质部
判定是否
开异常单 NG
OK
OK
判定是否
停线
NG QE主导异常会议
1、品质部判定异常是否要停线,OK则停线进入第 3段落,NG由QE主导品质异常的处理; 2、停线标准: 见《LED生产车间质量问题停线制度》
1、品质部书面通知生产部停线; 2、QE负责主导品质异常会议的召开 及 组织品质异常的评审;
1、QE进行品质异常原因分析并作进一步的确认, OK进入第5段落; 2、如涉及生产工艺、产品结构、电路设计等问题 则转技术部、开发部协助分析(物随单走); 3、异常分析为原材料原因进入供应商改善第5段 落,如是设计不良、生产作业问题则逐级返回技 术部;
不合格品控制程序及处理流程

不合格品控制程序及处理流程文件编号:1.目的:对不合格品加以标识、隔离、风险评估、重新处理,以防止非预期的使用或流入客户手中。
为对品质异常能及时反应处理、预防消除异常原因,以维持品质系统正常运作。
2.范围:针对来料、在制品及包装出货等各个阶段的不合格品。
3.定义:不合格品:不符合产品标准、技术规范或合同要求的产品。
返工:为使不合格品符合要求而对其采取的措施。
返修:为使不合格品满足预期用途而对其采取的措施。
挑选:对不合格品加以挑选,以区别等级。
报废:无法挑选处理并不可能进行返工或返修的不良品及维修成本高于制作制作成本的不良品。
退货:质量部检验材料、半成品、成品等有品质异常不满足需求状况时,将产品整批退还给供应商或制造单位,并要求处理的情形。
特采:于进检、生产过程或最终成品发现不合格品,因客户生产需求急迫,客户担当或业务部代表征得客户同意,或投入后不影响产品功能、构造能力、特殊外观要求及应用功能性,不造成人身安全,可满足最终客户使用品质的不合格品,做特殊接收标识,等同让步接收。
降级降档:因产品检验不符合标注定义要求,而采取更低标准确认接收、降级处理的状况。
4.职责:4.1生产部4.1.1负责对生产过程不合格品隔离作业及相应的标识。
4.1.2执行对品质异常发生时不合格品的应急处理要求。
4.1.3按照技术及质量提供的方案执行不合格品的返工、返修、挑选等作业。
4.1.4负责生产原因及品质异常之分析改善。
4.2质量部4.2.1负责对不合格品处置的协调,包含来料不合格、制程不合格、客户反馈不合格等。
4.2.2定义不合格品的区分、隔离及标识方式。
4.2.3评估定义不合格品的挑选方式及标准。
4.2.4品质异常发生时,不合格品紧急处理方式要求。
4.2.5对品质异常的分析与改善要求。
4.3技术部4.3.1品质异常发生时的应急处理方案拟定。
4.3.2对品质异常的分析与改善要求。
4.3.3对返工、返修作业方式的定义。
4.4其他部门4.4.1其他部门负责履行本部门的职责予以协助。
生产线异常停线管理规定

e)刀具未保养/维护;
f)制程(含物料)不良率超过2%,或报废率超过给定的指标。
4.2停线的报告与通知
当生产中发生停线的情况,生产现场人员应立即予以解决;不能立即解决时,现场质量主管可以开出《生产异常停线通知单》。
现场质量主管开出停线通知后,经现场生产主管(或经理)签名,报品质总监签批,发行给现场生产主管(或经理)。
停线权授予生产现场的质量检验人员,品质主管确认、品质总监批准停线。
事业部负责人召集有关的工艺人员和技术人员、设备工装模具人员解决问题。
4.作业程序Байду номын сангаас
4.1需要停线的情况
当下列质量问题被发现时,生产作业人员可以停线、或质量人员告知生产作业人员停线:
1)冲压生产:
a)检验尺寸不合格;
b)外观变形、压伤、有铜丝,外形与图纸不符合;
有限公司
质量管理体系文件
版次
修订页次
实施日期
修改简记
制定
日期
审核
日期
批准
日期
1.目的和范围
本文件规定了为解决生产中的质量问题而停止生产的权限及反应要求,促进聚集有关力量以快速解决生产中的质量问题。
本文件适用于公司全部产品。
2.定义
停线:正在进行的批量生产因质量问题需要立即解决而停止生产。
3.主要职责
c)镀层脱落;
d)制程不良率超过2%,或报废率超过给定的指标。
2)注塑生产:
a)检验尺寸不合格;
b)零件缺损;
c)零件起泡;
d)耐热测试不合格;
e)混料或错料;
f)制程不良率超过2%,或报废率超过给定的指标。
3)组装生产:
OCAP品质异常处理流程图-经典

分析造成异 常現象的 原
因
拟定临时对策
拟定永久对策
NG
供应 商改 善对 策
总经理
总经理核 准
作业指导
1、生产部门主导品质异常的提出; 2、品质部判定异常是否正确,NG继续生 产,OK进入第2段落; 3、异常标准: 1h内同种不良超10﹪;
1、品质部判定异常是否要停线,OK则停线进入第 3段落,NG由QE主导品质异常的处理; 2、停线标准: 见《LED生产车间质量问题停线制度》
段落
1 2 3
生产部
品质异常联 络单
停线并开出
品质部
判定是否
开异常单 NG
OK
OK
判定是否
停线
NG QE主导异常会议
异常原因分析 及确认
4
产线开始
5
试做或返工
不合格品
6
继续生产 7
8
生产制作流程
9
NG 确认对策 是否有效
OK
品质异常 联络单
结束
技术部
OCAP工作流程图
开发部
采购部
分析造成异 常現象的原
1、总经理负责改善对策的核准; 2、生产部按有效的改善对策继续生产, 停线通知废除;
1、生产部开始转入正常的《生产制作流 程》; 2、品质部负责《品质异常联络单》上传 、归档。
流程结束。
1、技术部负责对责任部门拟定临时改善 对策进行纠正,措施包含原材料、在制品 、成品等的处理方式; 2、如是原材料问题导致品质异常,采购 部负责落实供应商改善对策及改善效果追 踪; 3、技术部负责对责任部门拟定永久改善 对策进行预防,措施包含原材料、在制品 、成品等的处理方策是否有效,验证OK进入第7段落, NG则逐级返回第5段落重新拟定临时/永 久对策;
停线作业流程

停线作业流程下面是对停线作业流程的更口语化表述:第一步:发现问题,马上行动看到不对劲:只要产线上的工友发现产品有问题、机器不正常、原料不够用或者其他可能导致产品出状况的事儿,就得马上告诉大家。
紧急刹车:要是发现情况严重,操作员或者领班得赶紧按下那个“紧急停机”的按钮,或者按照规定做别的动作,让生产线赶快停下来。
第二步:现场保护与初步了解挂警示牌:在机器控制面板或者显眼的地方挂个“机器停了,别乱动”的牌子,免得有人误操作。
断电处理:按照规矩,可能得把电源关掉,特别是修机器或者有电风险的时候。
简单调查:相关的同事(比如质量检查员、操作员、领班)赶快去看看现场,记下出了多少坏产品、具体啥情况、可能为啥,做个初步的记录。
第三步:通知大家,组织起来告诉大家:马上告诉质量部、工程部、生产部还有管物料的人,说清楚为啥停线,目前是个啥情况。
开紧急会:一般是由质量部门主持,叫上这些部门的代表,甚至有时候高层也要来,一起讨论这个事儿。
第四步:现场查问题,找出原因技术大神来帮忙:质量检查员、工程师这些懂行的人赶紧来现场,仔仔细细地检查那些坏产品,看看机器参数、对比标准操作步骤,找出问题到底出在哪儿。
问题分类:看看是原料有问题、电子零件坏了、设计不合理还是工人操作不当,搞清楚是谁的责任。
第五步:想应急办法,恢复计划临时解决方案:工程师要在两小时内拿出个对付这个问题的临时办法,比如换批原料、调调机器、修个小故障,总之得尽快恢复生产。
分工合作:得把每个人该干啥都说清楚,要是工程师搞不定,还得找高层商量。
第六步:动手修,验证效果动手修:按照临时方案去现场整改,比如换零件、调机器、教工人怎么操作。
小规模试验:修完后先试着生产一小批,让质量检查员严格检查,看看问题是不是真的解决了。
第七步:恢复正常,持续关注正式复工:确定一切都OK,没啥问题了,就可以摘掉警示牌,按照规矩把电送上,启动生产线。
保持警惕:复工后一段时间,得多留意生产过程,确保问题不会再犯。
品质异常停线处理作业办法
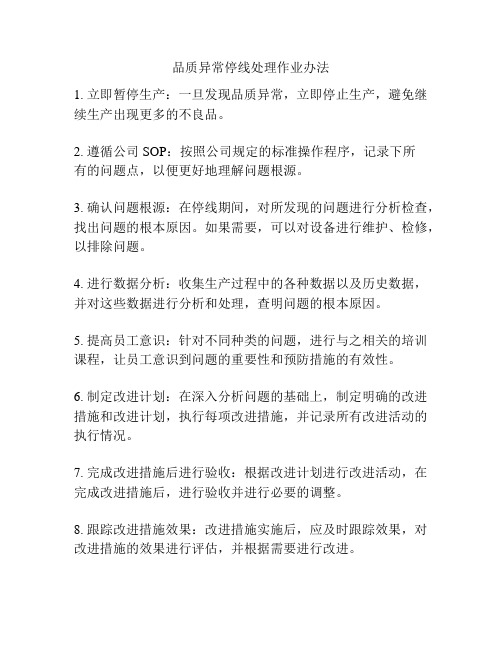
品质异常停线处理作业办法
1. 立即暂停生产:一旦发现品质异常,立即停止生产,避免继续生产出现更多的不良品。
2. 遵循公司SOP:按照公司规定的标准操作程序,记录下所
有的问题点,以便更好地理解问题根源。
3. 确认问题根源:在停线期间,对所发现的问题进行分析检查,找出问题的根本原因。
如果需要,可以对设备进行维护、检修,以排除问题。
4. 进行数据分析:收集生产过程中的各种数据以及历史数据,并对这些数据进行分析和处理,查明问题的根本原因。
5. 提高员工意识:针对不同种类的问题,进行与之相关的培训课程,让员工意识到问题的重要性和预防措施的有效性。
6. 制定改进计划:在深入分析问题的基础上,制定明确的改进措施和改进计划,执行每项改进措施,并记录所有改进活动的执行情况。
7. 完成改进措施后进行验收:根据改进计划进行改进活动,在完成改进措施后,进行验收并进行必要的调整。
8. 跟踪改进措施效果:改进措施实施后,应及时跟踪效果,对改进措施的效果进行评估,并根据需要进行改进。
生产停线管理程序

生产质量、停线管理程序1.目的:为了明确因生产中发现不良而造成停线的条件和责任者,使厂内机制更加完善特建立此ABL机制程序. 2.适用范围:本程序适用于泰汇公司所有的生产线,设备及测定器出现不良现象时,采取的报警,圈定风险批,停线等处理办法.3.权责:3. 1 生产部:负责对产品直接缺陷的发掘及发现,报警,拦截等动作,并反馈相应信息。
3. 2 品管部:负责对生产过程中所有影响产品质量的相关信息的监督及发掘,报警及拦截并将信息反馈给相关人员及单位.3. 3 品质工程师:负责对产品生产过程中各类异常情况的确认及分析,并提供改善方案.当发生重大缺陷异常时,负责主导召集相关单位召开QIP品质检讨会议.3. 4 现场管理:负责报警,拦截,停复线指令的下达及改善措施的实施.3. 5 工程部:负责停线后各类异常的解析及处理.4.名词解析:4. 1 主缺陷:直接影响产品性能的缺陷(如:尺寸不良,漏工序不良,严重变形压伤毛边毛刺不良)4. 2 模具异常:当模具产生变异时对产品及模具本生所造成的不良(如:模具缺料,模具刀口间隙不均,模具冲子或入子断裂,模具定位松动,模具磁性过大,模具打爆等)以上异常都会使产品产生主缺陷的不良.4. 3 设备管理值超差:即检查设备的调试状态是否按照设备管理规定值设定的,当设备当前设定值跟规定值有差异时,需立即报告上级确认,并立即停止生产。
4. 4 A .B . L定义:英文缩写:Alarm Block Linestop.中文定义:生产报警,圈定风险批,停线 .7.程序:7.1作业员发现及实行ABL机制7.1.1 生产中,作业员按照生产设备作业指导书对设备进行自检,按照ABL内相关标准进行,若有发现设备出现异常,作业员需立即上报生产组长及以上人员,并由现场管理人员作立即停线处理。
7.1.2 对特殊工序的设备,也必须按照ABL标准实行,如生产中若有发现各项工艺参数偏离《控制计划》标准时,须报备组长及以上人员,如直接对产品产生主缺陷时,须立即停线处理。
不合格品控制程序及处理流程
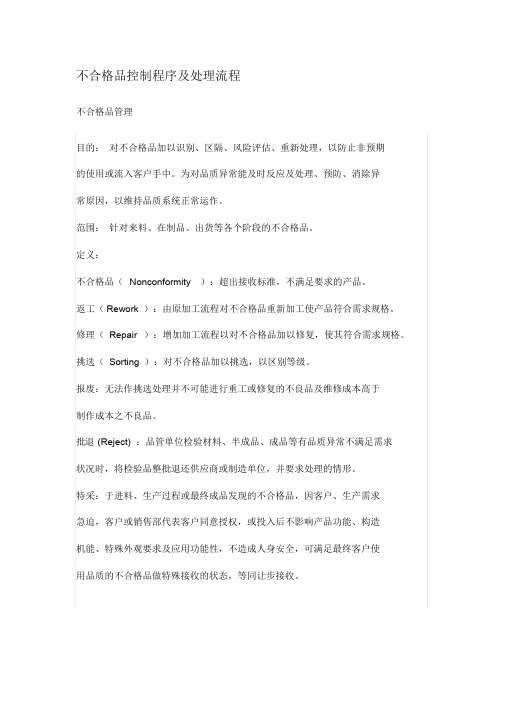
不合格品控制程序及处理流程不合格品管理目的:对不合格品加以识别、区隔、风险评估、重新处理,以防止非预期的使用或流入客户手中。
为对品质异常能及时反应及处理、预防、消除异常原因,以维持品质系统正常运作。
范围:针对来料、在制品、出货等各个阶段的不合格品。
定义:不合格品(Nonconformity ):超出接收标准,不满足要求的产品。
返工(Rework ):由原加工流程对不合格品重新加工使产品符合需求规格。
修理(Repair ):增加加工流程以对不合格品加以修复,使其符合需求规格。
挑选(Sorting ):对不合格品加以挑选,以区别等级。
报废:无法作挑选处理并不可能进行重工或修复的不良品及维修成本高于制作成本之不良品。
批退(Reject) :品管单位检验材料、半成品、成品等有品质异常不满足需求状况时,将检验品整批退还供应商或制造单位,并要求处理的情形。
特采:于进料、生产过程或最终成品发现的不合格品,因客户、生产需求急迫,客户或销售部代表客户同意授权,或投入后不影响产品功能、构造机能、特殊外观要求及应用功能性,不造成人身安全,可满足最终客户使用品质的不合格品做特殊接收的状态,等同让步接收。
降级、降档:因产品检验不符合定义标准要求,而采用更低标准确认接收、降级处理的状况。
各部门职责一. 质量部负责不合格品处置活动之协调,包含来料不合格、生产中不合格、顾客反馈不合格等。
定义不合格品的区分、隔离及标示方式;评估定义不合格品的挑选方式及标准;品质异常发生时,不合格品紧急处理方式要求;二. 生产部负责对生产过程不合格品区隔作业及相应的标识。
执行对品质异常发生时不合格品的应急处理要求;按照工艺及质量提供的方案执行不合格品品的返工、修理、挑选等作业负责生产原因造成品质异常之分析与改善;三. 工艺部品质异常发生时之应急处理方案拟定。
对过程品质异常之分析与改善要求。
对修理、返工作业方式定义。
其他部门负责履行本部门的职责予以协助。
- 1、下载文档前请自行甄别文档内容的完整性,平台不提供额外的编辑、内容补充、找答案等附加服务。
- 2、"仅部分预览"的文档,不可在线预览部分如存在完整性等问题,可反馈申请退款(可完整预览的文档不适用该条件!)。
- 3、如文档侵犯您的权益,请联系客服反馈,我们会尽快为您处理(人工客服工作时间:9:00-18:30)。
一. 目的﹕
为生产线发现严重品质问题后停线检讨、改善后重恢复继续生产及改善后产品的追踪提供流程及处理方法
二. 范圍:
適用於本公司生產現場發現任何对對產品品質有嚴重影響的異常处理过程
三、定义
异常: 严重影响生产线正常生产或影响客户正常使用的品质问题, 如断线, 耐压不良,层间不良等特性及外观、尺寸不良超过所允许的程度。
具体见第六项
三. 權責:
3.1 生產線作業員/檢查测试員/生產線組長: 按照相關文件標準進行作業,發現如下6.1提到的異常時,反
馈给生产线组长处理
3.2 IPQC:按巡線頻次(次/2H)進行巡檢,當發現符合5.1提到的異常確認後立即开出”停线通知单”
给IPQC工程师
3.3 IPQC工程師: 1)收到停线单后立即进行初步原因调查2)确认后立即将停线通知单交PE工程师
及制造课长要求停线4)IPQC工程师跟进PE主导组织有关部门共同参与问题的分析、检讨,最终会议结论的筹划由PE总结, IPQC工程师跟进会议结论的执行及效果的确认, 同时保持相关记录的证据(会议记录必须完整,必须有具体的责任人和完成日期), 相关结论动作完成后,再次组织检讨(由IPQC工程师报告跟进的结果), 当达到预期目标后IPQC工程师通知制造课长恢复生产, 如果仍未达到目标需再次执行问题的重检讨,直到问题解决为止方可恢复生产2) IPQC工程师必须跟进改善前后相关资料的记录(如P管制图, 停线通知单, 会议记录,改善后P管制图等)
3.4 PE: 1)收到IPQC工程師提交的停线通知单后後主導進行不良原因的調查,分析和最終給出會議
結論和對策(如相关的试验或验证, 对策的策划等),同时将停线通知单交相关责任部门并要求其回复重恢复生产的日期,IPQC工程跟进该责任部门在规定的时间内完成相关动作; 2)由PE用相关证据来划分和确定责任部门的归属
3.5 IE: 在会议确认對策有效後(看品管收集的相关数据),根据PE的要求, 執行相關文件的修改,
使對策或行动標準化;
3.6 生技: 负责配合执行会议提出的相关对策和其它配合事项的完成
3.7 工程:根据实际情况,配合提出改善对策或进行规格的修改, 与客人的沟通等
3.8 其它相关部门: 根据会议临时的要求参与执行相关配合事项(包括所有相关部门)
3.9 任何部门: 如果发现符合第六的停线条件, 任何部门均有权力和义务提出停线要求并由IPQC工
程师开出停线通知单交制造课长,同时通知PE相关信息;
四、停线的定义:
4.1停线按对品质的影响程度及问题处理的难易程度分为小规模短时间的暂停生产和大规模较长时
间的停止生产。
停线可能并非完全不生产,可能是在有计划有步骤受控制的状态下少量生产,边少量生产边跟进改善状况,确认改善达到预期效果后恢复量产(会议上由PE决定是否恢复量产,
品管需提供相关数据)
4.2 小规模的暂停生产后恢复:指明确的知道问题产生的位置和原因,并很清楚知道如何解决的暂
时停止生产,经过短时间的修整后即可进行量产的。
IPQC工程师需跟进其改善效果并保持记录。
比如相关人员经过短时间的培训和教育后立即可纠正和跟进的; 设备不稳定或设定错误可以马
上纠正的(纯粹为作业员不懂标准,作业手法明显不正确, 作业动作明显不规范等原因造成的人为原因, 经过短暂的停止作业, 培训后即可达到要求的或设备或仪器校正后立即可正常的)
4.3 大规模长时间的停止生产后恢复: 指严重品质不良或不良率已高过设定的目标,凭借单个部门的
力量无法立即确定问题产生的原因和解决的。
因为问题的严重性及解决问题的速度需要较长时
间,所以它需要较长时间的停止,经研究试验等,最终找出问题解决办法后再次恢复生产。
它主要通过所有相关部门(工作团队)共同配合来完成
4.4 停线的目的是为了避免生产出更多不良品,减少不良品或杜绝有不良隐患的产品流入下一站,从
而降低生产成本、品质成本及品质风险。
五、停线后的应对行动
接到停线通知单后所有相关部门的负责人员必须立即行动,积极投入到问题的分析和解决之中,以期以最快的速度解决问题后恢复生产。
不允许任何人有怠慢和推卸责任的作法,一切以解决问题恢复生产为优先。
最后问题责任人提供停线通知单及检讨报告交品管部存档。
六、停线条件,停线时机和再次恢复生产的条件
6.1 以下情况必须立即停线并及时检讨、纠正后方可进行生产:
6.1.1 经确认材料用错
6.1.2 经确认作业方法错
6.1.3 经确认仪器或设备有问题(如设定的条件错,设备不稳定, 设备不能正常运转等)
6.1.4 有高品质隐患的动作(如产品严重堆积,摆放散乱, 用牙签或刀片重工细线位置/覆盖细线的
胶等动作)
6.1.5 严重品质不良(高风险品质问题)和高不良率需要停线,依会议要求进行配合试产,找到最终
方法后, 方可大量生产, 否则不允许量产(看6.4表内的不良数量或PPM)
6.2停线时机:
6.2.1无论谁发现不良品数量达到6.4表内的条件或6.1的条件时
6.2.2品管每两小时统计发现时不良达到6.4表内的条件时
6.3停线后的恢复条件:
6.3.1已完全找到根本原因并确认此行动有效(以品管提供的数据来证明),经实验此行动后不良率控
制到期望范围内(有数据及不良率改善记录可追查)
6.3.1经开会讨论,鉴于目前的技术条件或迫于出货的要求必须边生产边改善的,此种情况必须要有品
管经理或以上级别的人员批准并留记录于停线通知单内,生产线方可恢复量产(由会议组织者向品管经理或以上级请示)
七. 作業流程(见附表7.1)。