品质异常停线处理作业办法
品质异常停线处理作业办法

探探修订履历※探Revision HistoryCatalogue1 目的(Purpose)制定合理的生产停线和停止出货的基准,确保不良品得到有效管控制。
2 适用范围(Scope)此档应用於IPPD印表机产品。
3 定义(Define )无4 职责(Responsibility )4.1 制造:负责将待CSA抽检的印表机移交给CSA及QC抽检等。
4.2 QC:负责制程品质检测和判定,及责任部门改善效果确认。
4.3 PE:负责印表机产品不良异常分析处理。
4.4 EE:负责处理电子元器件/元件不良分析。
4.5 TE: 负责分析测试程式引起的所有异常分析处理。
NPI: 负责协助相关部门工程人员分析异常和提供有效建议。
5 过程描述 ( Process Description ) 5.1当产线出现以下品质异常时,要求品质部门提出停线或停止出货:5.1.6 客户抱怨和 RMA 问题4.6 4.7SQE/IQC: 负责处理来料不良异常处理。
4.8 ME:负责制造生产或检测设备仪器异常处理。
4.9I E :负责主持重工会议且负责制定临时重工 SOP 。
4.10 维修 :负责协助经工程人员分析後非重工作业处理的不良进行修复。
4.11IT:负责SFC 系统管控和日常维护。
产品生产操作无生产作业指导书,作业员无相关机种/相关站别的上岗证,产线不按正常生产流程生5.1.15.1.2 产,私自变更工位。
产线生产时,工治具设备发现异常、测试程式错误、版本错误、参数设定错误等。
产线生产之机种混料使用(非替代料),生产用错料,使用超过保质期的物料生产。
5.1.3 首件不良为批量性不良生产时,或使用不符合 RoHS 或非安规认证物料等环保要求物料。
5.1.4CSA 测试工站发现异常:5.1.55.1.4.1 5.1.4.2 5.1.4.3 5.1.4.4 SOR SOR SOR SOR 之前: 之前: 之後: 之後: 产线不良品:5.1.5.1 如每条线每班发现 如每条线每班发现 如每条线每班发现 如每条线每班发现 生产线材料、制程作业不良率达到台功能不良时或发现 3 台相同的功能不良时停线。
停线管理规定
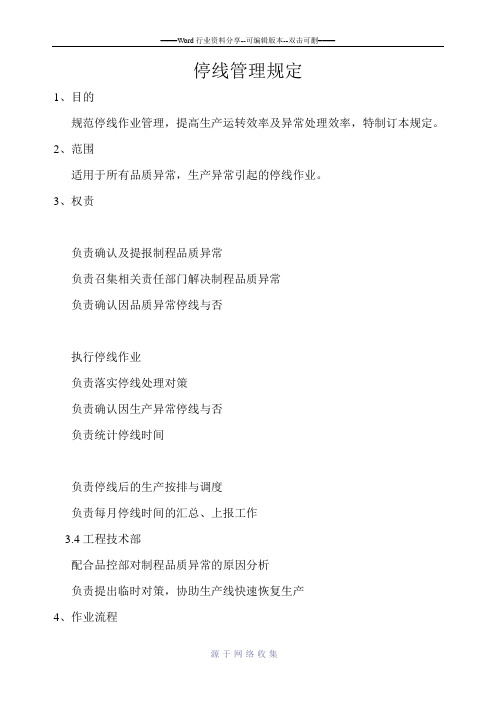
停线管理规定1、目的规范停线作业管理,提高生产运转效率及异常处理效率,特制订本规定。
2、范围适用于所有品质异常,生产异常引起的停线作业。
3、权责负责确认及提报制程品质异常负责召集相关责任部门解决制程品质异常负责确认因品质异常停线与否执行停线作业负责落实停线处理对策负责确认因生产异常停线与否负责统计停线时间负责停线后的生产按排与调度负责每月停线时间的汇总、上报工作3.4工程技术部配合品控部对制程品质异常的原因分析负责提出临时对策,协助生产线快速恢复生产4、作业流程IPQC发现制程品质异常时,应立即提报科长确认,填写《内部不良情况联络票》交品控部部长审核,当异常较为严重时,品控部长开具《停线通知单》交生产车间及生产计划部,并上报执行总经理。
生产过程发现物料异常时(缺料、错料等),线长应立即提报车间主任确认,填写《内部不良情况联络票》交生产部长,当异常较为严重时,生产部长开具《停线通知单》交生产车间及生产计划部,并上报执行总经理。
4.3《停线通知单》由相应的部门提出,部门主管确认后,经生产最高领导批准生效,特殊情况下最高领导可授权批准,《停线通知单》由生产计划部保存。
4.4《停线通知单》发出后,生产部,品控部应主导各相关责任部门对造成停线的异常原因进行分析,并提出可减少或防堵异常的临时对策,临时对策经确认有效则进入开线作业流程。
4.5生产线开线后,依据《停线通知单》的临时对策确认改善效果,如执行对策后,同类不良仍然存在而比例较高时,则再次提报《停线通知单》,执行第二次停线作业。
5、停线时机出现以下异常应提报停线5.1生产资料不齐全,BOM表有误时,5.2首检有重大异常:有致命缺陷或批量性功能不良时5.3生产设备、工装出现异常,足以影响生产和品质时6、停线考核生产计划部每月停线进行统计和分析,界定每批停线的责任单位根据公司的相管理规定进行追溯,对责任单位予以追究。
7、本规定自颁布之日执行。
批准:编制:。
生产线异常停线管理规定

e)刀具未保养/维护;
f)制程(含物料)不良率超过2%,或报废率超过给定的指标。
4.2停线的报告与通知
当生产中发生停线的情况,生产现场人员应立即予以解决;不能立即解决时,现场质量主管可以开出《生产异常停线通知单》。
现场质量主管开出停线通知后,经现场生产主管(或经理)签名,报品质总监签批,发行给现场生产主管(或经理)。
停线权授予生产现场的质量检验人员,品质主管确认、品质总监批准停线。
事业部负责人召集有关的工艺人员和技术人员、设备工装模具人员解决问题。
4.作业程序Байду номын сангаас
4.1需要停线的情况
当下列质量问题被发现时,生产作业人员可以停线、或质量人员告知生产作业人员停线:
1)冲压生产:
a)检验尺寸不合格;
b)外观变形、压伤、有铜丝,外形与图纸不符合;
有限公司
质量管理体系文件
版次
修订页次
实施日期
修改简记
制定
日期
审核
日期
批准
日期
1.目的和范围
本文件规定了为解决生产中的质量问题而停止生产的权限及反应要求,促进聚集有关力量以快速解决生产中的质量问题。
本文件适用于公司全部产品。
2.定义
停线:正在进行的批量生产因质量问题需要立即解决而停止生产。
3.主要职责
c)镀层脱落;
d)制程不良率超过2%,或报废率超过给定的指标。
2)注塑生产:
a)检验尺寸不合格;
b)零件缺损;
c)零件起泡;
d)耐热测试不合格;
e)混料或错料;
f)制程不良率超过2%,或报废率超过给定的指标。
3)组装生产:
异常处理及停线作业办法[参照材料]
![异常处理及停线作业办法[参照材料]](https://img.taocdn.com/s3/m/d04523cb960590c69ec376da.png)
文件編號:SCTQC-版本: 1.0發行日期:2012.05.21機密等級:一般核准: 審核: 制定: 賈友艷1.0 目的为控制因异常而造成质量,交期问题,将损失降低至最小程度,确保满足客户的质量和交期。
2.0 範圍适用于本厂工序异常或出货检测异常的控制。
3.0 定义3.1异常:符合以下条件之一的称之为异常,导致停线的异常有:3.1.1 影响生产绩效导致延误客户交期;3.1.2 重大品质问题;3.1.3 不良率在3%以上;3.2停线:由于异常的发生需要停止生产进行改善的作业,符合以下条件之一者3.2.1由3.1判定需要停止生产的;3.2.2 FAI不过;3.2.3 材料不正确;3.2.4 ECN变更未执行4.0 程序流程5.0程序内容5.1 生产停线的异常规定5.1.1印刷5.1.1.1当IPQC首件测试电阻变化率时如发现1PCS附着性,硬度和绝缘不良时,则立即停线。
5.1.1.2当3PCS电阻超出规格,且后续生产无法调试在规格内,或呈现不稳定状态时,立即停线。
5.1.1.3当IPQC巡检发现同一处外观不良超过15PCS时,经生产改善后仍有同样异常立即停线。
5.1.2冲贴发现同一类型不良连续10PCS(含)以上时,经改善后仍有同样异常则立即停线。
5.1.3冲形站检查时,外形及尺寸有1PCS外形与样品不符或连续4PCS尺寸超出公差时,立即停线。
5.1.4ATE测试,三片测试5.1.4.1 IPQC抽检已测之半成品,若发现功能不良1PCS(含)以上时,经重新测试后抽检仍发现有不良时立即停线;5.1.4.2 IPQC巡检发现机器参数不对时,经改善后仍发现有同类异常时立即停线。
5.1.5其它必须停线的异常有:FAI不过,材料不正确,ECN变更未执行,影响生产绩效导致延误客户交期,重大质量问题,不良率3%以上。
5.2异常的处理5.2.1相关部门发生异常时填写《品质异常处理报告》(品管部由检验员以上填写,生产部由组长以上填写),生产发生异常时生产部组长必须马上将异常状况通知IPQC 或OQC,由IPQC或OQC作重点检查,必要时进行100%检查或对样检查。
OQC异常及停复线处理程序

OQC异常及停复线处理程序1.目的:为建立一个完善的OQC异常及停复线处理流程,按照正确的路径作业,使之合理化、统一化、规范化及促进异常处理作业的有序进行.2.范围:本标准适用于OQC3.相关资料:3.1 不合格品管制办法3.2 矫正预防措施管理办法3.3 OQC抽样计划3.4 OQC检验规范3.5 AQ单处理流程作业规范3.6 Error code 不良代码4.定义:4.1 AQ(Abnormal Quality)单: 质量异常单电子化窗体4.2 Error Code:不良代码4.3 PCR: 制程变更需求4.4 PCN: 制程变更通知5.作业程序与权责:5.1 权责5.1.1 发生单位(OQC):异常处理,召集各单位参加会议,并追踪异常直至结案5.1.2 技术单位(硬件工程,软件工程,机构工程,工业工程):5.1.2.1 找出异常的初步原因, 并定义电测不良机台Sorting 方式5.1.2.2 根据责任单位给出的短期及预防对策进行评估.5.1.2.3 对于原材不良,送厂分析厂商回复NTF部分,技术单位应对其进行判断是否合理,并找出异常真因.5.1.2.4 计算Sorting和停线工时及费用.5.1.2.5 PCN/PCR导入时修正SOP.5.1.3 制造单位配合执行异常会议之相关决议.5.1.4 生管单位:5.1.4.1 停线或复线后,生产排程因应的调节与安排。
5.1.4.2 不良影响到成品出货时,生管确认订单出货时间及订单的出货调整5.1.4.3 不良重工及Sorting的安排5.1.5 责任单位:异常及停线原因的追查以及对策实施5.1.6 品保单位(PQA&QSM)5.1.6.1 发现异常时,PQA做系统Rework5.1.6.2 对策导入设计到制程变更时,PQA开PCN导入会议5.1.6.3 异常或停复线需Highlight客户时,QSM将异常或停复线讯息反馈给客户5.1.7 FPM若不良机台未下对策,但客人由于其他原因同意特采出货时,FPM开立特单5.2 作业程序:5.2.1 异常处理程序5.2.1.1 OQC发现异常, 立即记录不良发生的相关信息,并通知相关单位确认不良5.2.1.2 相关单位一起将不良回流产线,确认产线是否可以卡下不良5.2.1.3 OQC将不良机台贴上OQC Reject单,并召开一次会议5.2.1.4 依抽样计划要求制造Sorting b台(b=i/3)机台, Sorting无不良则依异常处理流程处理,Sorting 发现≧2台不良时,立即停线处理5.2.1.5 Sorting过程中发现1pcs同现象不良,则扩大Sorting i台, Sorting无不良则依异常处理流程处理,若Sorting过程中发现≧1台同现象不良时,立即停线处理5.2.1.6 技术单位在未拆机台30分钟或拆机台60分钟内给出短期对策(分析出人为或原材造成不良).并在3~4小时内分析出问题真因,并发出分析报告.5.2.1.7 经分析涉及到主板时,必须回流SMT看是否可以将不良卡下.5.2.1.8 OQC根据工程分析的真因确定不良影响范围并召开二次异常会议5.2.1.9 经分析为人为原因造成时,责任单位在30分钟之内给出短期对策.5.2.1.10 经分析为原材时不良,请MQC到现场确认,MQC请厂商进厂确认,厂商3hs内到厂,3天内回复初步分析报告,7天回复最终报告.5.2.1.11 MC确认是否有替代料及替代料库存是否满足产线需求,若替代料可满足产线需求则换替代料上线5.2.1.12 若无替代,则MQC 找厂商进厂Sorting原材上线, WIP工程单位提供短期预防对策5.2.1.13 若异常涉及停线及影响出货时, 需通知生管做相应处理,OQC对成品进行机台Hold,并在适当时机解除Hold.5.2.1.14 不良机台经维修解碼回流产线后,必须经OQC复判方可入库. 5.2.1.15 若对策需长期导入时,PQA开PCN/PCR导入会议.5.2.1.16 OQC开出AQ单电子文件.追踪责任单位AQ单回复状况,并确认对策有效性.5.2.5停线处理程序:5.2.5.1 OQC 12小时内抽检到两台以上(含两台)同机种同现象异常时,立刻纪录不良发生的相关讯息,产线立即停线,并通知相关部门参加会议.5.2.5.2 发生1pcs烧板,烧机或safety问题时,产线立即停线.5.2.5.3 抽到1pcs异常,Sorting b台(b=i/3)时发现≧2台同现象不良时,产线立即停线5.2.5.4 抽到1pcs异常,Sorting b台时发现1pcs不良,追加sorting i台时发现≧1同一不良时,产线立即停线.5.2.5.5 抽到1pcs HSF超标时,产线立即停线.5.2.5.6 停线发生时, OQC召开停线会议,相关单位需于5mins内到会议区参加会议,停线0.5hr需通知到厂级主管,1hr需通知到客户. 5.3 OQC异常处理流程图(见第5页):5.4 OQC停复线处理流程上述内容,如客户有特别要求,则根据客户要求进行相应的调整和修改6.附件6.1 OQC Reject单6.2 OQC品质异常通知单品质异常处理单TO:□生产部□工程部□品质部□PMC □仓库□其它。
品质问题停线和恢复程序
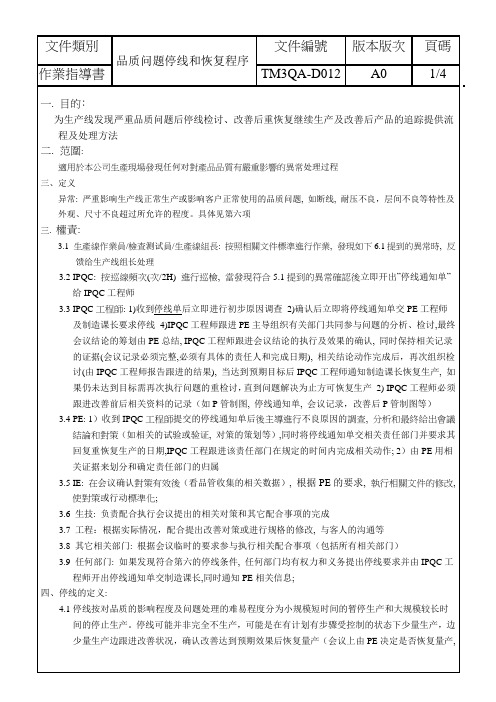
一. 目的﹕为生产线发现严重品质问题后停线检讨、改善后重恢复继续生产及改善后产品的追踪提供流程及处理方法二. 范圍:適用於本公司生產現場發現任何对對產品品質有嚴重影響的異常处理过程三、定义异常: 严重影响生产线正常生产或影响客户正常使用的品质问题, 如断线, 耐压不良,层间不良等特性及外观、尺寸不良超过所允许的程度。
具体见第六项三. 權責:3.1 生產線作業員/檢查测试員/生產線組長: 按照相關文件標準進行作業,發現如下6.1提到的異常時,反馈给生产线组长处理3.2 IPQC:按巡線頻次(次/2H)進行巡檢,當發現符合5.1提到的異常確認後立即开出”停线通知单”给IPQC工程师3.3 IPQC工程師: 1)收到停线单后立即进行初步原因调查2)确认后立即将停线通知单交PE工程师及制造课长要求停线4)IPQC工程师跟进PE主导组织有关部门共同参与问题的分析、检讨,最终会议结论的筹划由PE总结, IPQC工程师跟进会议结论的执行及效果的确认, 同时保持相关记录的证据(会议记录必须完整,必须有具体的责任人和完成日期), 相关结论动作完成后,再次组织检讨(由IPQC工程师报告跟进的结果), 当达到预期目标后IPQC工程师通知制造课长恢复生产, 如果仍未达到目标需再次执行问题的重检讨,直到问题解决为止方可恢复生产2) IPQC工程师必须跟进改善前后相关资料的记录(如P管制图, 停线通知单, 会议记录,改善后P管制图等)3.4 PE: 1)收到IPQC工程師提交的停线通知单后後主導進行不良原因的調查,分析和最終給出會議結論和對策(如相关的试验或验证, 对策的策划等),同时将停线通知单交相关责任部门并要求其回复重恢复生产的日期,IPQC工程跟进该责任部门在规定的时间内完成相关动作; 2)由PE用相关证据来划分和确定责任部门的归属3.5 IE: 在会议确认對策有效後(看品管收集的相关数据),根据PE的要求, 執行相關文件的修改,使對策或行动標準化;3.6 生技: 负责配合执行会议提出的相关对策和其它配合事项的完成3.7 工程:根据实际情况,配合提出改善对策或进行规格的修改, 与客人的沟通等3.8 其它相关部门: 根据会议临时的要求参与执行相关配合事项(包括所有相关部门)3.9 任何部门: 如果发现符合第六的停线条件, 任何部门均有权力和义务提出停线要求并由IPQC工程师开出停线通知单交制造课长,同时通知PE相关信息;四、停线的定义:4.1停线按对品质的影响程度及问题处理的难易程度分为小规模短时间的暂停生产和大规模较长时间的停止生产。
制程品质异常和停线管理规范

首件有重大异常,有严重功能不良或致命缺陷;
品质部 《品质异常单》 品质主管 生产部 《品质异常单》 品质主管 品质部 《品质异常单》 品质主管
停线
单项外观不良,发生5台以上同类不良; 单项功能不良,发生3台以上同类不良;
生产部 《品质异常单》 品质主管 生产部 《品质异常单》 品质主管
制程品质异常和停线管理规定
序 号
类别
1)为制程品质异常提供处理依据;
内容
一 目的 2)提高制程品质异常处理的质量和效率,保证生产中品质异常能得到及时有效的处理;
3)规范停线作业管理,提高生产线运转效率及异常处理效率。
文件编号: 版本:A0
二 适用范围 所有品质事故引起的异常和停线作业均可适用。
三 定义 异常停线:超出质量制程要求范围的行为动作。
处理时效 4H以内 4H以内 4H以内 4H以内
2H以内
2H以内 2H以内 2H以内
停线
品质检验连续2台以上同类不良; 制程品质异常提报后,对策无效或新的不良产生; 有重大品质隐患(不受发生数量限制)。
品质部 《品质异常单》 品质主管 生产部 《品质异常单》 品质主管 生产/品质 《品质异常单》 总经办
1)品质部:负责确认制程品质异常,召集相关责任部门解决制程品质异常,确认停线处理对策的有效性;
2)生产部:执行停线作业,负责落实停线处理对策,负责统计停线时间; 四 权限职责
3)工程部:负责制程品质异常的原因分析,负责提出临时对策,协助生产线快速恢复生产作业;
4)PMC部:负责生产停线、转线、开线的生产进度安排。
类别
异常/停线提报时机
提报部门 输出表单
品质异常停线处理作业办法
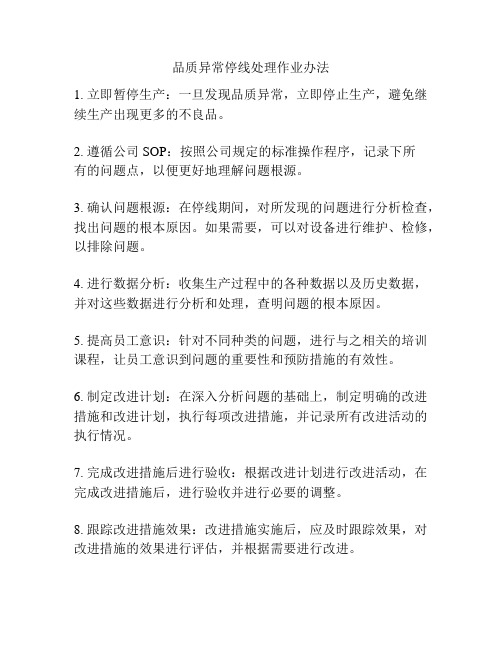
品质异常停线处理作业办法
1. 立即暂停生产:一旦发现品质异常,立即停止生产,避免继续生产出现更多的不良品。
2. 遵循公司SOP:按照公司规定的标准操作程序,记录下所
有的问题点,以便更好地理解问题根源。
3. 确认问题根源:在停线期间,对所发现的问题进行分析检查,找出问题的根本原因。
如果需要,可以对设备进行维护、检修,以排除问题。
4. 进行数据分析:收集生产过程中的各种数据以及历史数据,并对这些数据进行分析和处理,查明问题的根本原因。
5. 提高员工意识:针对不同种类的问题,进行与之相关的培训课程,让员工意识到问题的重要性和预防措施的有效性。
6. 制定改进计划:在深入分析问题的基础上,制定明确的改进措施和改进计划,执行每项改进措施,并记录所有改进活动的执行情况。
7. 完成改进措施后进行验收:根据改进计划进行改进活动,在完成改进措施后,进行验收并进行必要的调整。
8. 跟踪改进措施效果:改进措施实施后,应及时跟踪效果,对改进措施的效果进行评估,并根据需要进行改进。
- 1、下载文档前请自行甄别文档内容的完整性,平台不提供额外的编辑、内容补充、找答案等附加服务。
- 2、"仅部分预览"的文档,不可在线预览部分如存在完整性等问题,可反馈申请退款(可完整预览的文档不适用该条件!)。
- 3、如文档侵犯您的权益,请联系客服反馈,我们会尽快为您处理(人工客服工作时间:9:00-18:30)。
探探修訂履歷※探Revision HistoryCatalogue1 目的(Purpose)制定合理的生產停線和停止出貨的基準,確保不良品得到有效管控制。
2 適用範圍(Scope)此檔應用於IPPD印表機產品。
3 定義(Define )無八、、4 職責(Responsibility )4.1 製造:負責將待CSA抽檢的印表機移交給CSA及QC抽檢等。
4.2 QC:負責制程品質檢測和判定,及責任部門改善效果確認。
4.3 PE:負責印表機產品不良異常分析處理。
4.4 EE:負責處理電子元器件/元件不良分析。
4.5 TE: 負責分析測試程式引起的所有異常分析處理。
4.6 NPI: 負責協助相關部門工程人員分析異常和提供有效建議。
4.7 SQE/IQC: 負責處理來料不良異常處理。
4.8 ME: 負責制造生產或檢測設備儀器異常處理。
4.9 IE :負責主持重工會議且負責制定臨時重工SOP 。
4.10 維修 :負責協助經工程人員分析後非重工作業處理的不良進行修復。
4.11 IT:負責SFC 系統管控和日常維護。
5過程描述 ( Process Description ) 5.1當產線出現以下品質異常時,要求品質部門提出停線或停止出貨: 5.1.1產品生產操作無生產作業指導書,作業員無相關機種 /相關站別的上崗證,產線不按正常生產流程生產,私自變更工位。
5.1.1 產線生產時,工治具設備發現異常、測試程式錯誤、版本錯誤、參數設定錯誤等。
5.1.2 產線生產之機種混料使用(非替代料),生產用錯料,使用超過保質期的物料生產。
5.1.3 首件不良為批量性不良生產時,或使用不符合 RoHS 或非安規認證物料等環保要求物料。
5.1.4CSA 測試工站發現異常:5.1.5.2 功能測試站測試不良達到 5%(每 1 小時統計資料)。
5.1.5.3 當某一生產線不良品 1 小時內累積達到 15 台時,或連續出現 5台同一功能不良品時。
5.1.5.4 SPC 設置的控制圖顯示異常時。
5.1.6客戶抱怨和 RMA 問題5.1.6.1 當客戶有抱怨時,工廠沒有有效的糾正措施,要求停產。
5.1.4.1 SOR 之前:如每條線每班發現 5.1.4.2 SOR 之前:如每條線每班發現 5.1.4.3 SOR 之後:如每條線每班發現 5.1.4.4 SOR 之後:如每條線每班發現 5.1.5產線不良品:5.1.5.1 生產線材料、制程作業不良率達到4 台功能不良時或發現 3 台相同的功能不良時停線。
2 台 Workmanship 要求產線停線 10 分鐘教育。
3 台功能不良時或發現 2 台相同的功能不良時停線。
1 台 Workmanship 要求產線停線 10 分鐘教育。
8% 時(每 1 小時統計資料)。
5.1.6.2 當RMA 品經海外FAE 等回饋分析顯示事先風險係數RPN 偏大超過100 ,無及時有效的臨時對策時。
5.1.7 CSA按系統要求抽檢不合格時而再次追加抽檢N ( N=不良數*15 )台時,仍然有不良時需要停線整頓、改善。
5.1.8 PPPL(MAVS+PPP)測試不合格,客戶要求方面要求停線改善整頓時。
5.2 出貨停止5.2.1 產品在出貨時因搬運和堆疊造成產品不良時。
5.2.2 在包裝時使用錯誤物料和方式等。
5.2.3 產品在儲存時有受潮和發霉等現象。
5.2.4 在客戶、用戶端、檢測中心顯示環保管控有害物質檢測、安規檢測失效。
5.2.5 在客戶對工廠進行過程審核、產品審核失效時,有要求停產改善整頓。
5.2.6 當發生停線處理異常時,SFC 自動提示或品保、客戶要求停止出貨時。
5.2.7 當SOR 試產階段到大批量生產前各個部門彙集問題點無法解決,且得不到客戶認可時。
5.2.8 制程不良發生未按公司不良或疑似不良品批重工處置且重檢合格時,及不良品流到成品倉庫時,倉庫應根據SFC 系統提示或QC 要求實施擋貨,停止出貨。
5.2.9 判定其他任何重大品質問題時。
5.3 停線或停止出貨實施時,QC 首先發出《停線或停止出貨通知單》,如一般停線(指各別線體停線)要第一時間匯報到品保主管(專理或以上)級,如全面停線則要第一時間通知到品保最高主管(協理或以上)級,並聯絡相關責任部門(MFG、ENG、IQC、PP、TQM )一起會議檢討對策,再由TQM通知HP客戶。
《停線或停止出貨通知單》由各部門會簽確認後由QC 保管。
5.4 所有停線或停止出貨異常,必需進行不良、異常原因分析及改善報告,並進行效果確認,直至改善OK。
5.4.1 製造部門違反作業流程規定作業等,由製造自身檢討,回復負責不良原因分析、制定改善措施,在提岀有效的應急臨時對策後方可恢復生產。
在24小時內回復QC開岀“ PDCS ”《製成品質異常回饋單》,QC收到製造回復的制程異常糾正預防措施單後,會同QC工程師一起確認改善對策實施效果,決定是否關閉該異常問題點。
5.4.2 制程不良由PE負責不良原因分析並提岀改善措施建議,或者根據初步分析結果要求做更深一步分EE/SQE/TE析,QC 根據工程人員最終分析報告判定責任單位。
責任部門必需針對具體品質異常制定並實施有效改善措施。
在責任單位提出有效的應急臨時對策後方可恢復生產。
收到QC 開出“PDCS ”《製成品質異常回饋單》,後必需在24 小時內回復,並定期向產品專案組人員和隨線工程人員報告改善進度和措施實施效果。
QC 接收到責任單位回復的制程異常糾正預防措施單後,會同QC工程師一起確認改善對策實施效果,決定是否關閉該異常問題點。
5.4.3 測試軟體問題、燒錄程式問題引起不良由TE 負責不良原因分析並提出重工、改善措施建議,QC根據分析報告判定責任單位,責任部門負責針對具體品質異常制定並實施有效改善措施,收到QC開出“ PDCS ”《製成品質異常回饋單》,後必需在24 小時內回復,並定期向產品專案組人員和隨線工程人員報告改善進度和措施實施效果。
QC接收到責任單位回復的制程異常糾正預防措施單後,會同QC工程師一起確認改善對策實施效果,決定是否關閉該異常問題點。
5.4.4 來料不良、或不符合RoHS 等環保、安規要求時,由SQE 聯絡、要求供應商進行不良原因分析和提出並實施有效改善對策,並定時向工廠內部相關部門報告異常處理進度及效果。
在必要時要求供應商或IQC 進行選別來救濟生產。
5.4.5 生產工治具、設備、參數設定錯誤或運行異常或導致不良產生時,由ME 負責異常原因分析,並針對具體異常制定並實施有效改善措施,收到QC開岀“ PDCS ”《製成品質異常回饋單》,後必需在24小時內回復,並定期向產品專案組人員和隨線工程人員報告改善進度和措施實施效果。
QC接收到ME回復的制程異常糾正預防措施單後,會同QC工程師一起確認改善對策實施效果,決定是否關閉該異常問題點。
546 在SOR試產階段直至大批量生產期間,NPI負責協助相關部門進行不良原因分析,提岀改善措施建議,必要時經公司高層同意後聯絡客戶請求支援改善方案,如在產品設計進行改善或產品要求方面進行調整。
5.5 恢復生產和恢復岀貨5.5.1 製造部門停線整頓期間在QC確認改善對策有效、可行後,提交《產線恢復生產/岀貨恢復申請》。
QC 工程師收到後會同其他工程人員實施評估,在品保專理/製造專理/工程專理/人員會簽同意恢復生產,製造將批准後的《產線恢復生產/岀貨恢復申請》,複印發放給QC等相關部門。
製造部門即可正式恢復生產。
5.6 產線在製品和倉庫庫存需要重工處理時,必需遵守執行以下:5.6.1 由責任部門通知所有相關人員岀席重工會議。
5.6.2 由IE負責主持重工會議且負責制定臨時重工SOP。
5.6.3 分析工程人員在會議上提岀重工流程和注意事項。
5.6.5 製造部門負責實施重工作業,重工完成後通知QC 人員再次檢測。
5.6.6 QC 負責對製造重工完成品進行抽檢或全檢和判定,並記錄相關檢測結果。
5.7 改善對策有效行確認:5.6.4 QC 工程師與其他工程人員一起審核重工流程和提出注意事項或要求。
5.7.1 改善對策效果確認範圍/期限:在改善對策提出、實施後生產的3lots/ 實施4個星期。
5.7.2 有效性標準:由QC工程師評估的事先風險係數RPN在改善對策實施明顯下降。
5.7.3 不能出現同一不良原因引起的其他不良或同一類不良現象再次發生。
否則判定對策無效或需要組建改善專案組通過QCC 或6Sigma ( DAMIC )活動來加以持續改進。
6 記錄的保存(Records Retention)本作業文件長期有效直到產品生命週期終結, 檢查報告及相關記錄最少要保留三個月.7 參考文件Reference7.1 《RoHS 實施管理辦法》7.2 《产品重工及特殊作业办法》8 附件及附表Attachment8.1 產線異常處理流程圖Flow Chart8.2 《停線或停止出貨通知單》附件一:品質异常停线处理流程图厂因品质异常造成停线 /停、 止出货发生QC 首先发出《停线或 停止出货通知单》同时第一时间向上级 汇报停线或异常情况品保部门负责联络召集相关 责任部门(MFG 、ENG 、IQC 、PP 、TQM )一起会议 检讨对策如一般停线(指各别线体停 线)要第一时间汇报到品保主 管(专理或以上)一级各责任部门问题点总结, 避免类似问题发生否《重 否是如需重工作业参照《重工作 业处理流程》实施如需重工作业参照 工作业处理流程》实施如全面停线则要第一时间通知 到品保最高主管(协理或以 上)一级MF 依据临时对策恢 品常*由ENG 部门分析原因并给出 ”临时有效的改善措施要求ENGI 新 对策保根据ENGB 口EL策评估判定能否 部门提出的临时对策判 生产是品保根据EN 部门扌的临时对策评估判定能门提岀的临时对责任部门给出有效的改善 对策并回复PDC 单品保判疋改善 措施是否有效退件要求重 新对策由TQM 通知HP 客户 ,反馈异常状况。