催化剂装填方式
加氢催化剂装填方案
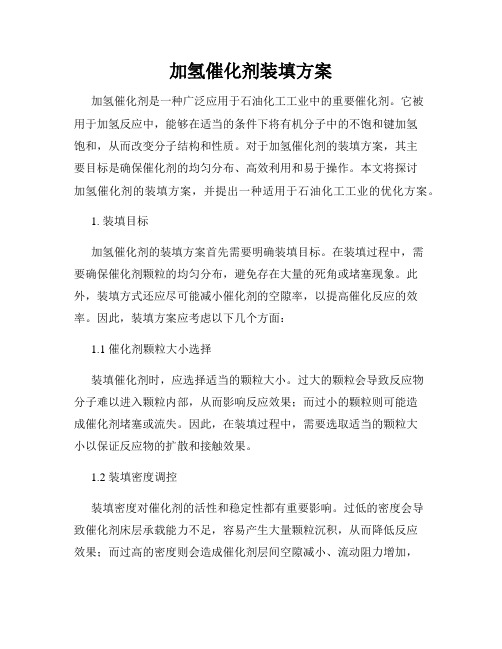
加氢催化剂装填方案加氢催化剂是一种广泛应用于石油化工工业中的重要催化剂。
它被用于加氢反应中,能够在适当的条件下将有机分子中的不饱和键加氢饱和,从而改变分子结构和性质。
对于加氢催化剂的装填方案,其主要目标是确保催化剂的均匀分布、高效利用和易于操作。
本文将探讨加氢催化剂的装填方案,并提出一种适用于石油化工工业的优化方案。
1. 装填目标加氢催化剂的装填方案首先需要明确装填目标。
在装填过程中,需要确保催化剂颗粒的均匀分布,避免存在大量的死角或堵塞现象。
此外,装填方式还应尽可能减小催化剂的空隙率,以提高催化反应的效率。
因此,装填方案应考虑以下几个方面:1.1 催化剂颗粒大小选择装填催化剂时,应选择适当的颗粒大小。
过大的颗粒会导致反应物分子难以进入颗粒内部,从而影响反应效果;而过小的颗粒则可能造成催化剂堵塞或流失。
因此,在装填过程中,需要选取适当的颗粒大小以保证反应物的扩散和接触效果。
1.2 装填密度调控装填密度对催化剂的活性和稳定性都有重要影响。
过低的密度会导致催化剂床层承载能力不足,容易产生大量颗粒沉积,从而降低反应效果;而过高的密度则会造成催化剂层间空隙减小、流动阻力增加,影响反应物的传质速率。
因此,在装填过程中,需要通过调控催化剂颗粒的大小和装填压力来实现合适的装填密度。
2. 装填方式常见的加氢催化剂装填方式包括手工装填、机械装填和液相装填等。
2.1 手工装填手工装填是一种常见的装填方式,适用于小型装置或需要更精细操作的装填场景。
装填时,操作人员需要仔细控制催化剂颗粒的均匀分布,以避免堵塞或泥饼现象的发生。
此外,在手工装填过程中,操作人员还需要注意自身的安全和防护措施,并确保装填过程中无尘、无异物等。
2.2 机械装填机械装填是一种高效、快速的装填方式,适用于大型装置或需要大量催化剂的装填场景。
机械装填通常通过输送带、振动装置等设备来实现,能够快速将催化剂颗粒均匀地装填到反应器内部。
然而,在机械装填过程中,需要注意设备的稳定性和催化剂颗粒的均匀性,以避免颗粒聚集或分布不均匀的情况发生。
催化剂装填

山东恒源石油化工股份有限公司15000NM3/h制氢装置催化剂装填量及装填方案一、催化剂装填:L Y T—701/LYT-702 加氢催化剂:催化剂装填前的准备:工作场地干燥、清洁、无杂物;检查反应器内构件是否完好,内部热电偶管和衬里有无破损;认真清扫,抹净反应器内壁、出口筛板与过滤网上的赃物;准备号筛子、加料漏斗、帆布袋和软梯等。
在反应器内壁标记号瓷球和催化剂的装填高度。
将所需瓷球洗净晾干。
在催化剂床层的下部,由向往上分别装入Φ10和Φ3毫米的普通瓷球,在催化剂床层的上部由下往上分别装入Φ3、Φ5毫米的活性瓷球,即与催化剂床层接触的都是Φ3毫米的小瓷球。
瓷球高度不小于100毫米,装瓷球的目的是防止运转过程中催化剂床层位移和下陷。
催化剂装填:催化剂是一种强吸水剂,为了避免吸潮,应选在晴天装催化剂,并连续工作装完为止。
装催化剂时用料斗和帆布袋将催化剂送入反应器,催化剂出袋后的自由自由落体高度小于1米,催化剂装填人员应使布袋口沿反应器圆周方向移动,使床层均匀上升。
每升高半米至一米,耙平一次,然后再装。
使其使床层径向温差增大。
装填催化剂时应有专人负责指挥,并认真做好现场装填记录。
精心搬运,认真记录编号及计量。
催化剂装填完毕后,要及时将反应器封好,以备装置试密。
三、LYT-701/LYT-702加氢催化剂硫化催化剂装填完毕后,将硫化流程以外的系统加盲板彻底隔离。
硫化流程采用闭路循环流程或加氢反应气出口放火炬流程。
反应系统气密合格,建立氢气-氮气循环后,进行催化剂硫化。
硫化条件:氢压,MPa 常压-5.0 MPa循环介质,% N2-H2混合气氢气含量,%(v/v) 30-50空速,h-1 200-500第一个恒温硫化阶段床层温度和时间 260℃恒温6小时第二个恒温硫化阶段床层温度和时间 300℃恒温8小时硫化剂二硫化碳或二甲基二硫理论需硫量,m%(对催化剂)约8.0实际需二硫化碳、二甲基二硫量,m%(对催化剂) 15/18硫化步骤:(1)以15~20℃/h将反应器入口温度升温至175℃恒温,启动二硫化碳泵或二甲基二硫开始注入二硫化碳或二甲基二硫,开始注入量控制反应器入口硫含量在0.5-1.5%(v/v)。
催化剂的装填..

保护剂的装填顺序是:按照床层容垢能力大小,脱金属能力由强 到弱。脱硫氮活性逐渐增加的顺序及优化比例的进行装填。
Add your company slogan
密箱装填几个最重要的参数
装填速度:通过调节喷嘴间隙大小 装填密度 装填器喷头到催化剂料面的距离
床层径向的均匀性(滴流床反应器) 装填质量 可以增加催化剂的装填量 轴向的紧密型和级配型
决定催化剂的床层的压降速度 和催化剂是否发生迁移
分级装填法
是指采用一种或数种不同尺寸大小、不同形状、不同孔容、 不同活性的高孔隙率活性和惰性瓷球、保护剂系列装填于主 催化剂床层上部,使床层从上到下颗粒逐渐变小、床层孔隙 率逐步减低的分级过渡装填方法。
催化剂装填方案
1 3 2 催化剂的装填技术 密相装填
3 4
装填步骤
各填充物料的作用
一、催化剂的装填技术
催化剂装填作业由两道工序组成: 第一道工序是把催化剂送
输送法 密相输送 第二道工序是用装填设备把催化剂装填到反应器的床层中。 普通装填(袋式装填/疏相装填)
密相装填
下 床 层
各填充物料的作用
卸料管:防止在此部分不流动的“死区”内发生化学反应和结焦。
瓷球
上部:
容纳杂质,防止和延缓运行刷造成催化剂料面的变化, 避免沟流发生中压降的上升,防止高物流冲。
下部:起到支撑催化剂床层,防止反应器中小颗粒的催化剂堵
塞出口收集器。
脱除原料中的结垢物,延缓压力上升
保护剂
密相装填优缺点
1、 反应器内可多装填催化剂,使装置总处理量增加。 2、 处理量相同时,密相装填的重量空速较小,可使催 化剂初期运转温度降低。 3、处理量相同时,密相装填的催化剂运转周期延长。 4、 催化剂床层装填均匀,紧密一致,可避免床层 陷、沟流等现象的发生,从而避免“热点”的产生。 5、 催化剂床层径向温度均匀,可以提高反应的选择性。 6、床层压降高
费托合成催化剂选择与处理—催化剂的装填与卸料(煤制油技术课件)

01
催化剂的装填
3 催化剂补充
对合成反应器内失活和流失催化剂的补充,这时合成反应器处 于正常操作阶段,合成反应器内的温度、压力都较高,催化剂的补充 加入量比较小。催化剂加入时需要注意保持合成反应器的操作平稳, 防止由于催化剂加入时产生液泛现象。在催化剂加入合成反应器前, 需要根据加入量提前将合成反应器的液位降低。保障在催化剂加入后 合成反应器操作液位的稳定。
还原反应器还原好的催化剂加入到合成反应器中,分合成反应 器开车加入和对合成反应器内流失、失活催化剂的补充两种方式。
01
催化剂的装填
2 开车加入
合成反应器内还没有催化剂,催化剂的加入需要时间较长,在 催化剂加入前,合成反应器的温度、压力维持在正常操作水平。在催 化剂全部加入结束前,需根据催化剂加入量控制进合成反应器的合成 气流量,注意保持合成反应器的操作平稳,催化剂加入速度可根据还 原反应器与合成反应器的压差调整。
02
催化剂的卸出
(1)紧急情况下还原反应器需要卸出催化剂时,首先还原反 应器系统降压,降至1.0MPa。
(2)确认渣蜡减压罐接收正常,调节压力调节阀开度,继续 给还原反应系统降压,待还原反应系统压力降到0.6~0.8MPa时, 关闭调节阀,还原反应器系统维持一定的压力。开启还原反应器卸 料口阀门,向渣蜡减压罐卸料。催化剂浆料卸出后,关闭催化剂卸 料阀。
煤间接液化 -催化剂的装填与卸出
目录
01 催化剂的装填 02 催化剂的卸出
01
催化剂的装填
费托合成采用浆态床反应器, 浆态床反应器的催化剂实行在线 补充加入,可以实现合成反应器 的连续操作运行。
01
催化剂的装填
1 催化剂装填
正常生产时,催化剂在还原反应器内还原后再补充到合成反应 器内。还原反应器催化剂装填采用程序控制加催化剂,还原反应器装 填重柴后,启动催化剂加料程序顺序控制。
催化剂装填方案
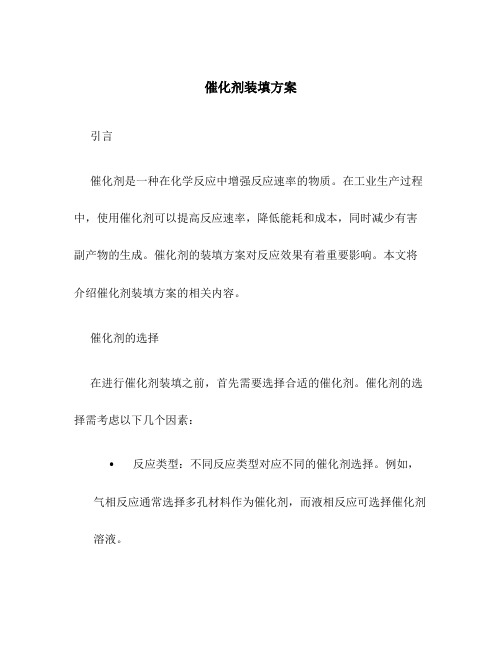
催化剂装填方案引言催化剂是一种在化学反应中增强反应速率的物质。
在工业生产过程中,使用催化剂可以提高反应速率,降低能耗和成本,同时减少有害副产物的生成。
催化剂的装填方案对反应效果有着重要影响。
本文将介绍催化剂装填方案的相关内容。
催化剂的选择在进行催化剂装填之前,首先需要选择合适的催化剂。
催化剂的选择需考虑以下几个因素:•反应类型:不同反应类型对应不同的催化剂选择。
例如,气相反应通常选择多孔材料作为催化剂,而液相反应可选择催化剂溶液。
•反应性能:催化剂对目标反应的催化活性和选择性是选择催化剂的重要指标。
一般而言,高活性和高选择性的催化剂能够提高反应效率。
•耐久性:催化剂需要具有较好的耐久性,能在长时间使用中保持相对稳定的催化性能。
•经济性:催化剂的成本也是选择催化剂的一个重要因素。
需要综合考虑催化剂的价格、使用寿命和性能等因素。
催化剂的物理形态催化剂通常以固体、液体或气体的形态存在。
下面将分别介绍这三种催化剂的装填方案。
固体催化剂的装填固体催化剂通常以颗粒、粉末或填料的形式存在。
固体催化剂的装填方式有以下几种:1.床层填料装填:将固体催化剂填充到反应器的床层中。
这种装填方式适用于颗粒或粉末状的催化剂。
填充后要保证床层的均匀性,以免发生流动不畅或堵塞等问题。
2.水平装填:将固体催化剂均匀地铺在反应器内的水平层上。
这种装填方式适用于某些对流动有一定要求的反应,如气相催化反应。
3.包埋装填:将固体催化剂填充到容器的孔隙中。
这种装填方式适用于颗粒状催化剂,使催化剂能够充分接触反应物。
液体催化剂的装填液体催化剂通常以溶液的形态存在。
装填液体催化剂时,可以采用以下方式:1.注入装填:将液体催化剂通过管道或注射器注入到反应器中。
这种装填方式适用于小型反应器或实验室规模的反应。
2.循环装填:将液体催化剂通过循环泵或搅拌器循环注入到反应器中,保持催化剂与反应物的接触。
这种装填方式适用于大规模工业生产过程。
气体催化剂的装填气体催化剂通常以气体的形态存在。
催化剂装填

催化剂装填第一节准备工作一、催化剂装填前应具备的条件1、反应系统干燥结束,反应器降至常温(任意一点反应器温度小于60℃)。
系统压缩空气置换结束,系统中氧含量>20%(v)。
2、反应系统压力降至常压,反应系统无爆炸气(爆炸气分析合格),反应器顶部大盖具备打开条件。
3、反应器安全隔离(1)按照隔离方案,反应器所有接口加盲板或者都打开,使反应器与装置其它部分完全隔离(盲板见表一、隔离见图二)。
拆掉反应器入口大盖短节以便进人,进料线盲死。
出口短节拆除,出口管线盲死,急冷氢、冲洗氢以及压降测量引线全部盲死,以防氮气或氢气从冷氢接口或压降接口泄漏至反应器中。
对不能用盲板隔离而用阀门隔离的部位,关阀后用铁丝捆绑固定,若有放空阀,开放空阀,并在上述阀门上挂上警示牌“装剂期间,禁动此阀”。
5、反应器顶部新鲜水、氮气、仪表风、工业风线等作好明显标志,防止混用。
装置仪表风和氮气相串的部位加盲板隔离。
6、电动卷扬机、抽真空器、供风用的空压机试运正常。
7、现场安装临时照明,反应器内接24V照明电,保证夜间作业。
8、催化剂装填方案置于现场,并做好看板。
(催化剂装填方案见表六)二、催化剂装填的准备工作1、催化剂装填方案和组织实施方案提前做好审批。
协调各部门做好配合,对装剂人员做好培训。
装剂现场实行看板管理。
2、装剂专用器具、器材及作业人员劳保用品准备好,见表五。
3、专人全面负责反应器的装剂工作,做好现场指挥。
4、装剂现场设立安全监护人员,重点对进入反应器作业人员的供氧、供气及通讯照明设施进行检查确认,同时检查进反应器作业票的有效性,履行作业中的安全监护职责。
气防救护车装剂期间在现场值班。
5、进入反应器前联系化验车间,按要求进行化验分析。
化验分析项目见表二。
6、检查清扫料斗、料座内干净无杂物,插板活动灵活,联接好帆布送料筒。
7、催化剂提前运至现场,按要求摆放整齐。
催化剂搬运及摆放要求如下:(1)按装填进度要求,将催化剂准时运至现场,用叉车卸车,按种类摆好并用帆布盖好。
反应器催化剂的装填注意事项以及方法
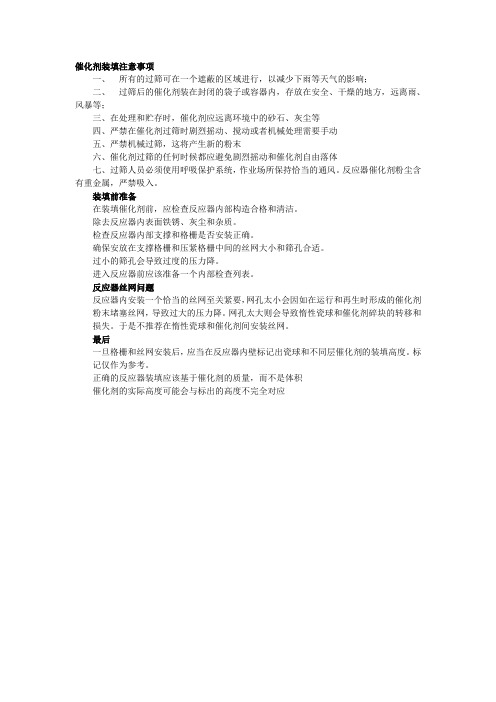
催化剂装填注意事项
一、
二、
风暴等;
三、在处理和贮存时,催化剂应远离环境中的砂石、灰尘等
四、严禁在催化剂过筛时剧烈摇动、搅动或者机械处理需要手动
五、严禁机械过筛,这将产生新的粉末
六、催化剂过筛的任何时候都应避免剧烈摇动和催化剂自由落体
七、过筛人员必须使用呼吸保护系统,作业场所保持恰当的通风。
反应器催化剂粉尘含有重金属,严禁吸入。
装填前准备
在装填催化剂前,应检查反应器内部构造合格和清洁。
除去反应器内表面铁锈、灰尘和杂质。
检查反应器内部支撑和格栅是否安装正确。
确保安放在支撑格栅和压紧格栅中间的丝网大小和筛孔合适。
过小的筛孔会导致过度的压力降。
进入反应器前应该准备一个内部检查列表。
反应器丝网问题
反应器内安装一个恰当的丝网至关紧要,网孔太小会因如在运行和再生时形成的催化剂粉末堵塞丝网,导致过大的压力降。
网孔太大则会导致惰性瓷球和催化剂碎块的转移和损失。
于是不推荐在惰性瓷球和催化剂间安装丝网。
最后
一旦格栅和丝网安装后,应当在反应器内壁标记出瓷球和不同层催化剂的装填高度。
标记仅作为参考。
正确的反应器装填应该基于催化剂的质量,而不是体积
催化剂的实际高度可能会与标出的高度不完全对应。
催化剂排列方式

催化剂的排列方式有多种不同的形式,取决于具体的反应和催化剂类型。
以下是一些常见的催化剂排列方式:
固定床催化剂:这是最常见的催化剂排列方式,催化剂通过填充在反应器中的固定床中。
反应物通过床层流过,与催化剂发生反应。
这种排列方式适用于许多气相和液相催化反应。
流化床催化剂:流化床催化剂中的催化剂以颗粒的形式悬浮在气体或液体中,形成床层。
床内的催化剂颗粒通过气体或液体的流动而保持悬浮状态。
这种排列方式适用于高速流动和快速反应的催化反应。
固定床流化床组合:这种排列方式结合了固定床和流化床的特点。
在反应器中,一部分催化剂被填充成固定床形式,而另一部分则以流化床形式存在。
这种排列方式适用于需要控制反应温度和催化剂局部浓度的反应。
催化膜:催化剂以薄膜形式涂覆在反应器的壁上或其他材料上。
反应物经过催化膜与催化剂发生反应。
这种排列方式适用于一些液相和气相反应,可以提供更高的催化活性和选择性。
以上只是一些常见的催化剂排列方式,实际应用中还可以根据具体的反应需求和催化剂特性进行特殊设计。
不同的排列方式会对催化反应的效果和性能产生不同的影响。
列管式反应器的催化剂装填方法综述
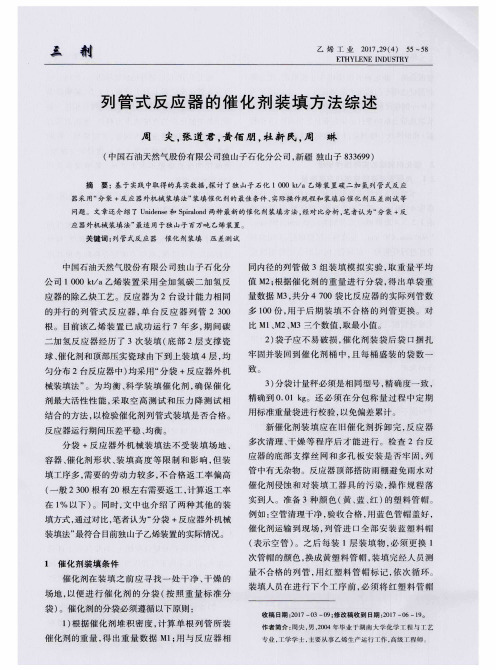
巾同石 油天然 气 股份 有 限 公 司独 山子 石化 分 公司 1 0 0 0 k t / a乙烯 装置 采 用 全 加 氢碳 二 加 氢反
同 内径 的 列管 做 3组 装 填 模 拟 实验 , 取 重量 平 均 值M 2 ; 根 据催 化 剂 的重 量 进 行 分袋 , 得 出单 袋 重
在 1 % 以下 ) 。 同时 , 文 中也 介 绍 了两 种 其 他 的装 填 方式 , 通过 对 比, 笔者认 为“ 分 袋 +反应 器外 机 械
催化 剂侵 蚀 和 对 装填 工 器 具 的 污 染 , 操 作 规 程 落
实到 人 。准备 3种 颜 色 ( 黄、 蓝、 红) 的塑 料 管 帽 。 例如 : 空 管清理 干 净 , 验收合格, 用蓝 色 管 帽盖 好 , 催化 剂运 输 到 现 场 , 列 管 进 口全 部 安 装 蓝 塑 料 帽
2 ) 袋 子应 不 易 破 损 , 催 化 剂 装 袋 后 袋 口拥 扎
牢 同并装 回到催 化 剂 桶 中 , 且 每 桶 盛 装 的 袋 数一
致。 3 ) 分 袋计量 秤 必须是 相 同型 号 , 精 确度 一致 , 精确 到 0 . O 1 k g 。还 必 须 在 分 包 称 量 过 程 巾 定 期 用标 准重 量袋进 行 校验 , 以免 偏差 累计 。
械 装填 法 ” 。 为均 衡 、 科 学 装 填催 化 剂 , 确 保 催 化
量数据 M 3 , 共分 4 7 0 0袋 比 反应 器 的 实 际列 管 数
多1 0 0份 , 用 于 后 期 装 填 不 合 格 的列 管 更 换 。 对
比 M1 、 M2 、 M3三个 数值 , 取最 小值 。
问题。文章还介 绍 了 U n i d e n s e和 S p i r a l o n d两种最新的催化剂装填方法 , 经对比分析 。 笔者认为“ 分袋 +反
药品生产技术《催化剂的装填方式》
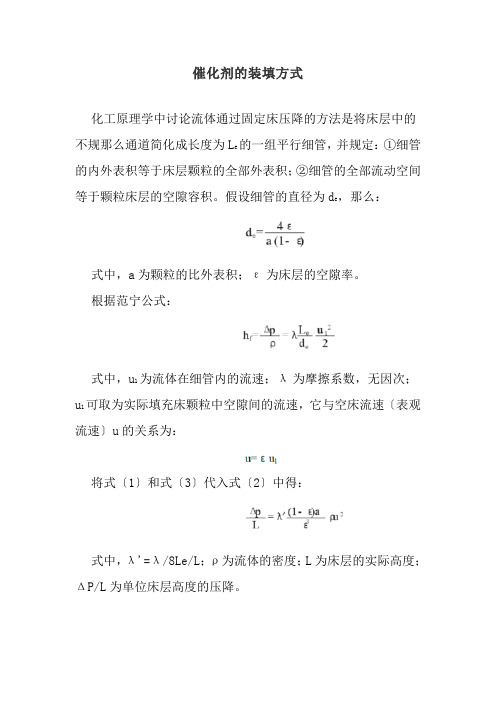
催化剂的装填方式化工原理学中讨论流体通过固定床压降的方法是将床层中的不规那么通道简化成长度为L e的一组平行细管,并规定:①细管的内外表积等于床层颗粒的全部外表积;②细管的全部流动空间等于颗粒床层的空隙容积。
假设细管的直径为d e,那么:式中,a为颗粒的比外表积;ε为床层的空隙率。
根据范宁公式:式中,u1为流体在细管内的流速;λ为摩擦系数,无因次;u1可取为实际填充床颗粒中空隙间的流速,它与空床流速〔表观流速〕u的关系为:将式〔1〕和式〔3〕代入式〔2〕中得:式中,λ'=λ/8Le/L;ρ为流体的密度;L为床层的实际高度;ΔP/L为单位床层高度的压降。
由此可以看出,影响床层压降的变量有3类:操作变量u、流体密度ρ也有人认为与流体黏度μ有关以及床层特性ε、a和L。
操作变量是指装置的加工量,它对压降的变化影响很明显。
通常我们希望装置能够满负荷运行,因此它是不变的。
对于一套确定的装置来说,ρ、a、L变化不大,对压降的变化影响也很小。
影响大同时自身变化也大的是空隙率ε。
例如,假设维持进料量不变,ε从降为,由式4不难算出,单位床层压降增加倍。
通过计算和实际经验相结合,不难看出固定床压降升高的主要原因就是床层空隙率减小。
空隙率减小的主要原因是床层杂质不断增多,堵塞了颗粒间的空隙。
要想解决这一问题,一方面要控制杂质的生成;另一方面要改变床层的颗粒分布和装填方式,增加床层的空隙率,提高床层的容垢能力。
一个好的装填方案一定使床层有较大的空隙率。
乱堆的非球形颗粒床层空隙率往往大于球形颗粒,所以固定床催化剂通常采用形状与球形相差较大的三叶草形。
此外,在催化剂上方采用除垢篮或级配剂,阻止系统杂质进入催化剂床层,引起压降增大。
除垢篮最初应用于加氢装置,后来由于它在容垢方面的显著作用而被应用到其他装置。
除垢篮一般均匀地布置在床层上外表,篮周充填适量的大颗粒瓷球。
它的主要作用就是过滤掉原料中的杂质,防止杂质进入催化剂床层。
催化剂筛分及装填方案
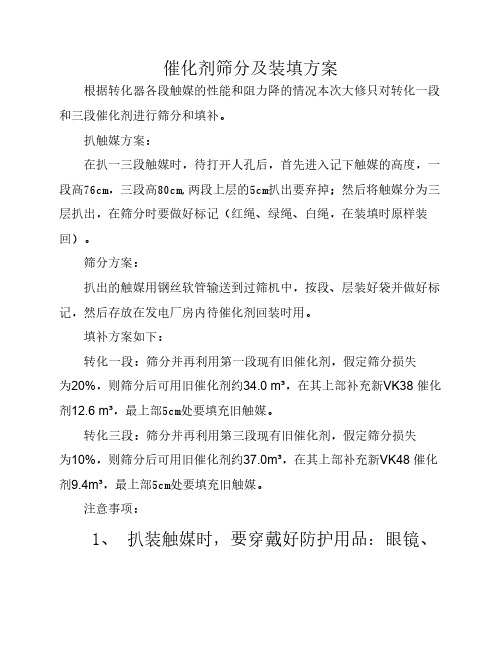
催化剂筛分及装填方案
根据转化器各段触媒的性能和阻力降的情况本次大修只对转化一段和三段催化剂进行筛分和填补。
扒触媒方案:
在扒一三段触媒时,待打开人孔后,首先进入记下触媒的高度,一段高76cm,三段高80cm,两段上层的5cm扒出要弃掉;然后将触媒分为三层扒出,在筛分时要做好标记(红绳、绿绳、白绳,在装填时原样装回)。
筛分方案:
扒出的触媒用钢丝软管输送到过筛机中,按段、层装好袋并做好标记,然后存放在发电厂房内待催化剂回装时用。
填补方案如下:
转化一段:筛分并再利用第一段现有旧催化剂,假定筛分损失
为20%,则筛分后可用旧催化剂约34.0 m³,在其上部补充新VK38 催化剂12.6 m³,最上部5cm处要填充旧触媒。
转化三段:筛分并再利用第三段现有旧催化剂,假定筛分损失
为10%,则筛分后可用旧催化剂约37.0m³,在其上部补充新VK48 催化剂9.4m³,最上部5cm处要填充旧触媒。
注意事项:
1、 扒装触媒时,要穿戴好防护用品:眼镜、
口罩、手套
2、 人员分为三帮,每帮30分钟替换
3、 在工作期间,严谨吃东西,要在充分洗干
净的基础上才允许
4、 触媒扒填要注意不能蛮干,减少触媒的破
损程度
5、 废弃的触媒,要妥善保存或厂家回收,避
免环境污染。
催化剂装填分析

山东恒源石油化工股份有限公司15000NM3/h制氢装置催化剂装填量及装填方案一、催化剂装填:L Y T—701/LYT-702 加氢催化剂:催化剂装填前的准备:工作场地干燥、清洁、无杂物;检查反应器内构件是否完好,内部热电偶管和衬里有无破损;认真清扫,抹净反应器内壁、出口筛板与过滤网上的赃物;准备号筛子、加料漏斗、帆布袋和软梯等。
在反应器内壁标记号瓷球和催化剂的装填高度。
将所需瓷球洗净晾干。
在催化剂床层的下部,由向往上分别装入Φ10和Φ3毫米的普通瓷球,在催化剂床层的上部由下往上分别装入Φ3、Φ5毫米的活性瓷球,即与催化剂床层接触的都是Φ3毫米的小瓷球。
瓷球高度不小于100毫米,装瓷球的目的是防止运转过程中催化剂床层位移和下陷。
催化剂装填:催化剂是一种强吸水剂,为了避免吸潮,应选在晴天装催化剂,并连续工作装完为止。
装催化剂时用料斗和帆布袋将催化剂送入反应器,催化剂出袋后的自由自由落体高度小于1米,催化剂装填人员应使布袋口沿反应器圆周方向移动,使床层均匀上升。
每升高半米至一米,耙平一次,然后再装。
使其使床层径向温差增大。
装填催化剂时应有专人负责指挥,并认真做好现场装填记录。
精心搬运,认真记录编号及计量。
催化剂装填完毕后,要及时将反应器封好,以备装置试密。
三、LYT-701/LYT-702加氢催化剂硫化催化剂装填完毕后,将硫化流程以外的系统加盲板彻底隔离。
硫化流程采用闭路循环流程或加氢反应气出口放火炬流程。
反应系统气密合格,建立氢气-氮气循环后,进行催化剂硫化。
硫化条件:氢压,MPa 常压-5.0 MPa循环介质,% N2-H2混合气氢气含量,%(v/v) 30-50空速,h-1 200-500第一个恒温硫化阶段床层温度和时间 260℃恒温6小时第二个恒温硫化阶段床层温度和时间 300℃恒温8小时硫化剂二硫化碳或二甲基二硫理论需硫量,m%(对催化剂)约8.0实际需二硫化碳、二甲基二硫量,m%(对催化剂) 15/18硫化步骤:(1)以15~20℃/h将反应器入口温度升温至175℃恒温,启动二硫化碳泵或二甲基二硫开始注入二硫化碳或二甲基二硫,开始注入量控制反应器入口硫含量在0.5-1.5%(v/v)。
催化剂装填.

山东恒源石油化工股份有限公司 15000NM 3/h 制氢装置催化剂装填量及装填方案 一、催化剂装填:LY T —701/LYT-702 加氢催化剂:催化剂装填前的准备:工作场地干燥、清洁、无杂物;检查反应器内构件是否完好,内部热电偶管和衬里有无破损;认真清扫,抹净反应器内壁、出口筛板与过滤网上的赃物; 准备号筛子、加料漏斗、帆布袋和软梯等。
在反应器内壁标记号瓷球和催化剂的装填高度。
将所需瓷球洗净晾干。
在催化剂床层的下部,由向往上分别装入Φ 10 和Φ 3 毫米的普通瓷球,在催化剂床层的上部由下往上分别装入Φ 3、Φ 5 毫米的活性瓷球,即与催化剂床 层接触的都是Φ 3 毫米的小瓷球。
瓷球高度不小于 100 毫米,装瓷球的目的是防止运转过程 中催化剂床层位移和下陷。
催化剂装填:催化剂是一种强吸水剂,为了避免吸潮,应选在晴天装催化剂,并连续工作装完为止。
装催化剂时用料斗和帆布袋将催化剂送入反应器,催化剂出袋后的自由自由 落体高度小于 1 米,催化剂装填人员应使布袋口沿反应器圆周方向移动,使床层均匀上升。
每升高半米至一米,耙平一次,然后再装。
使其使床层径向温差增大。
装填催化剂时应有专 人负责指挥,并认真做好现场装填记录。
精心搬运,认真记录编号及计量。
催化剂装填完毕 后,要及时将反应器封好,以备装置试密。
三、LYT-701/LYT-702 加氢催化剂硫化催化剂装填完毕后,将硫化流程以外的系统加盲板彻底隔离。
硫化流程采用闭路循环流程或加氢反应气出口放火炬流程。
反应系统气密合格,建立氢气-氮气循环后,进行催化剂硫化。
硫化条件: 氢压,MPa 常压-5.0 MPa 循环介质,% N 2-H 2 混合气 氢气含量,%(v/v ) 30-50空速,h -1200-500第一个恒温硫化阶段床层温度和时间 260℃恒温 6 小时 第二个恒温硫化阶段床层温度和时间 300℃恒温 8 小时硫化剂二硫化碳或二甲基二硫 理论需硫量,m%(对催化剂)约 8.0实际需二硫化碳、二甲基二硫量,m%(对催化剂)15/18硫化步骤:(1)以 15~20℃/h 将反应器入口温度升温至 175℃恒温,启动二硫化碳泵或二甲基二硫开始注入二硫化碳或二甲基二硫,开始注入量控制反应器入口硫含量在 0.5-1.5%(v/v )。
- 1、下载文档前请自行甄别文档内容的完整性,平台不提供额外的编辑、内容补充、找答案等附加服务。
- 2、"仅部分预览"的文档,不可在线预览部分如存在完整性等问题,可反馈申请退款(可完整预览的文档不适用该条件!)。
- 3、如文档侵犯您的权益,请联系客服反馈,我们会尽快为您处理(人工客服工作时间:9:00-18:30)。
催化剂装填方式标准化管理部编码-[99968T-6889628-J68568-1689N]
普通装填又叫疏相装填、布袋装填、稀相装填,和密相的其区别在于装填过程中有无外界推动力来提高催化剂的装填量和装填均匀性。
密相装填可以提高处理量,空速小,径向温差小,装填速度快,运行时间长。
催化剂的密相填装初始压降高,疏相填装压降低,随着装置的运行,密相填装的催化剂比后着要好
稀相装填需要人员进行耙平;密相装填借助密相装填器进行装填,不借助人力。
密相装填比稀相装填堆积密度大,装填密实,装填量多.
催化剂装填分为普通装填(疏相装填、袋式装填)和密相装填两种。
其区别在于装填过程中有无使用外界推动力来提高催化剂的装填量和装填均匀性。
普通装填方法因其多采用很长的帆布袋作为催化剂从反应器顶部向窗层料位的的输送管子而被称为布袋装填法,实际上,普通装填法中也有较多厂家不用帆布袋而改用金属舌片管来输送催化剂的。
由于普通装填法简单易行,人员上几乎不需要特别的培训,设备上不需要专利技术,因此被国内许多炼油企业所采用。
密相装填法由ARCO技术公司、法国TOTAL公司、UOP公司、Chevron公司等发明,采用密相装填法,可以将催化剂在反应器内沿半径方向呈放射性规整地排列,从而减少催化剂颗粒间的孔隙,提高催化剂的装填密度,通常,可以比普通装填法多装重量10%~25%的催化剂。
密相装填除了可以多装催化剂外,由于装填过程中催化剂颗粒在反应器横截面上规整排列,因此其沿反应器纵向、径向的装填密度也非常均匀。
密相装填与普通(稀相)装填相比,催化剂堆积密度大,反应器内装填催化剂量增大,脱硫起始温度低,脱氮相对体积活性增加7-22%。
采用密相装填时压降会相对增加,但密相装填压降升速比稀相装填要低,故在使用中期或末期压降可能比稀相装填要低。
催化剂的密相装填,可以确保物料的流量分布均匀,以最大限度地、充分地利于催化剂。
与传统的布袋装填方法相比较,催化剂的密实装填具有如下优点:
①????应器可多装填催化剂,提高加工能力或延长周期、提高产品质量;
②处理量相同时,密相装填的重量空速较小,可以使催化剂的运转温度降低;
③处理量相同时,密相装填运转周期更长;
④催化剂床层装填均匀,紧密一致,可避免床层塌陷、沟流等现象的发生,从而避免“热点”的产生;
⑤催化剂床层径向温度均匀,可以提高反应的选择性。
⑥装填时采用专门机械,连续化作业,装填速度大大提高。
也就是因为这些优点,密相装填法比袋式装填法更具有应用前景。