车内孔
车工工艺学-车孔

2.车孔所能达到的技术要求:
车孔是常用的孔加工方法之一,既可以作为粗加工, 也可作为精加工,加工范围很广。 (1)车孔精度可达IT7~IT8。(IT:公差等级) (2)表面粗糙度值可达Ra1.6~3.2μm,精车时可 以达到Ra0.8μm或更小。 (μm:微米, 1μm=10-6m) 此外,车孔还可以修正孔的直线度。
一、内孔车刀的种类:
车孔的方法基本上和车外圆相同,但内孔车刀和 外圆车刀相比有差别。根据不同的加工情况,内 孔车刀可分为通孔车刀和盲孔车刀两种。 1.通孔车刀 通孔车刀的几何形状基本上与75°外圆车刀相似。 为了减小径向切削力防止振动,主偏角kr应取大 值,一般取kr=60°~75°,副偏角kr′=15°~30° 常用的通孔车刀刀柄有圆刀柄和方刀柄两种。
二、车孔的技术要点
车孔的关键技术是解决内孔车刀的刚度和排屑问题。 增加内孔车刀的刚度主要采取以下两项措施: 1.尽量增加刀柄的截面积 一般的内孔车刀的刀尖位于刀柄的上面,这样车刀 有一个缺点,即刀柄的截面积小于孔截面积的1/4。 内孔车刀的后面如果刃磨成一个大后角,则刀柄的 截面积必然减小。如果刃磨成两个后角,或将后面 磨成圆弧状,则既可防止内孔车刀的后面与孔壁摩 擦,又可使刀柄的截面积增大。 2. 尽可能缩短刀柄的伸出长度 如果刀柄伸出太长,就会降低刀柄的刚度,容易引 起振动。
四、车孔方法
退刀 进刀
在粗车或精车时也要进行 试切削,其横向进给量为 径向余量的1/2。
当车刀纵向切削至2mm左右时,纵向快速退刀(横 向不动),然后停车测试,若孔的尺寸不到位,则需微 量横向进刀后再次测试,直至符合要求,方可车出整个 内孔表面。 2、车孔时的切削用量要比车外圆时适当小些,特别 是车小孔或深孔时,其切削用量应更小。
第七课 数车内孔、内腔和套类零件加工(理论讲解)
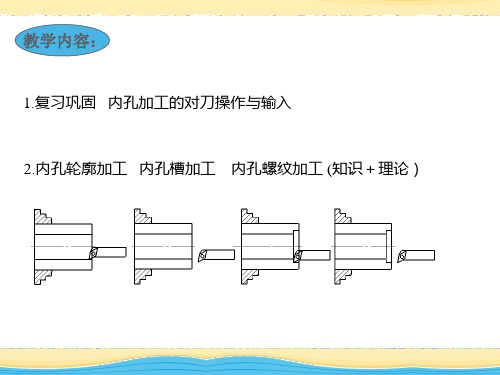
7.孔的精度 套类零件的精度有下列几个项目。
(1)孔的位置精度。 同轴度(孔之间或孔与某些表面间的尺寸精度)、平 行度、垂直度、径向圆跳动和端面圆跳动等。
铰孔是对较小和未淬火孔的精加工方法之一,在成批生
产中已被广泛采用。铰孔之前,一般先镗孔,镗孔后留些 余量,一般粗铰为0.15mm~0.3mm,精铰为0.04mm~ 0.15mm,余量大小直接影响铰孔的质量。
4.孔加工方法的选择 在车床中,孔的加工方法与孔的精度要求、孔径以及
孔的深度有很大的关系。一般来 讲,在精度等级为IT12、 IT13时,一次钻孔就可以实现。在精度等级为IT11,孔径 ≤10mm时,采用一次钻孔方式;当孔径>10~30mm时, 采用钻孔和扩孔方式;孔径>30~80mm时,采用钻孔、扩 钻、扩孔刀或车刀镗孔方式。在精度等级为ITl0、IT9,孔 径≤10mm时,采用钻孔以及铰孔方式;当孔径 >10~30mm时,采用钻孔、扩孔和铰孔方式;孔径 >30~80mm时,采用钻孔、扩孔、铰孔、或者用扩孔刀镗 孔方式。在精度等级为IT8、IT7,孔径≤10mm时,采用钻 孔及一次或二次铰孔方式;当孔径>10~30mm时,采用钻 孔、扩孔、一次或二次铰孔方式;当孔径>30~80mm时, 采用钻孔、扩钻(或者用扩孔刀镗孔)以及一次或二次铰孔 方式。
如出现Z方向的误差,则其修整办法相同。
二、内孔、内腔和套类零件(知识+理论)
课题一 盲孔零件的加工
本课题要求编程并加工如图6.1所示盲孔零件,毛 坯为φ53mm×100mm的棒料,材料为45钢。
a)零件图 b)实体图 图6.1 盲孔零件
一、基础知识 1.孔加工特点 (1)孔加工是在工件内部进行的,观察切削情况比较困 难,尤其是小孔、深孔更为突出。
数控车削内孔

参考文献:
[1]Mohan D, Singh K P, Sinha S, et. al. Removal of
pyridine derivatives from aqueous solution by activated
carbons developed from agricultural waste materials [J]
便于排屑,刃倾角 λ 取负值(后排屑)。
(3)机夹可转为内孔车刀。数控车床所采用的可转位车刀,
与通用车床相比一般无本质的区别,其基本结构、功能特点是相
同的。但数控车床的加工工序是自动完成的,因此对可转位车
刀的要求又高于通用车床所使用的刀具。
2. 内孔车刀的安装
(1)内孔车刀刀尖应与工件中心等高或稍高。
dihydropyrimidinones [J]Ultrasonics sonochemistry, 2008, 15(6),
1015
[7]Wang Q, Shao Y, Gao N, et al. Degradation kinetics
and mechanism of 2, 4-Di-tert-butylphenol with UV /
(2)内孔车刀
刀柄伸出刀架不宜过长。
(3)内孔车刀刀柄基本平行于工件轴
线。
(4)盲孔车刀装夹时,主刀刃应与孔底平成 3°-5°,在车平面
时要求横向有足够的退刀余量。
3. 刀位点和对刀
刀位点是指在加工程序编制中用以表示刀具特征的点。内
孔车刀的刀尖是刀位点。在执行加工程序前,需调整每把刀的
刀位点,使其尽量与某一理想基准点重合,这一过程称为对刀。
粗糙度和较高的几何精度,在车削安装套类零件时关键的是要
《车工》教案 项目8-2 车通孔、台阶孔

模块二车削初级工技能训练本项目参考节数:10节检查学生出勤,作好学生考勤记录。
强调课堂纪律,活跃课堂气氛。
强调实习纪律,做好安全文明生产。
【复习巩固】1.复习上次课主要学习了麻花钻的组成及主要角度;麻花钻的刃磨;麻花钻的装卸;钻孔时切削用量的选择和钻孔的方法。
播放了钻孔、锪孔、车孔和铰孔的视频。
同学们也进行了相应的练习。
通过讲解和演示及练习,使学生进一步增强对重点内容的认识和理解。
更加深了对刃磨麻花钻和钻孔的感性认识。
2.提问1)标准麻花钻由哪几部分组成?2)钻孔时的背吃刀量是什么?3)直径越小的钻头,主轴转速应如何选择?3.作业讲评作业完成情况统计表【课题导入】多媒体演示齿轮、轴承套、衬套、带轮等机器零件,使学生认识这几种机器零件。
观察它们的结构特点,并提出问题:这几种零件与我们前面学过的轴类工件有何不同之处?得到答案——它们共同的特点是比轴类工件多了内孔结构,自然引出套类工件的概念。
设置问题:同学们学习了外圆的车削,那么内孔是怎样加工出来的呢?(1)引发学生的好奇心,并给出几分种的时间让他们发挥想象,进行自由讨论。
(2)播放锪孔、车孔和铰孔的视频,通过观看,明确告诉学生内孔表面在车床上就是用这几种方法加工的,自然比较出内孔加工的4个特点(3)在分析各种加工孔的方法时指出:其中最常用的方法是——车孔,而车孔用的刃具是——内孔车刀,引入内孔车刀和车孔。
【讲授新课】(2课时)项目8 车内孔任务二车通孔、台阶孔一、内孔车刀的种类二、内孔车刀刃磨步骤1.根据刀片固定的形式分类2.根据不同的加工情况分类三、内孔车刀的装夹四、内孔的车削步骤1.通孔的车削步骤2.台阶孔的车削步骤五、测量孔径的方法【技能训练】(6小时)一、目标任务1.了解内孔车刀的种类,学会装夹内孔车刀。
2.掌握内孔车刀刃磨的角度,学会其刃磨方法。
3.学会车内孔。
4.学会用塞规测量孔径。
二、示范操作刃磨内孔车刀、装夹内孔车刀及车削和测量内孔。
床车内孔锥度计算公式

床车内孔锥度计算公式在机械加工中,床车内孔锥度的计算是非常重要的。
床车内孔锥度是指内孔壁面与内孔轴线的夹角,通常用角度或百分比来表示。
正确计算床车内孔锥度可以保证加工出来的零件符合设计要求,提高产品的质量和精度。
床车内孔锥度的计算公式可以通过几何关系和三角函数来推导得出。
在实际的加工中,我们可以根据这个公式来进行计算,从而确定加工床车内孔的角度和尺寸。
床车内孔锥度计算公式如下:tanα = (D d) / L。
其中,α表示内孔锥度的角度,D表示内孔大径,d表示内孔小径,L表示内孔长度。
根据这个公式,我们可以通过已知的内孔大径、小径和长度来计算出内孔的锥度角度。
这样就可以在加工时根据需要来确定刀具的进给量和加工速度,从而保证加工出来的内孔符合设计要求。
在实际的加工中,我们还可以根据需要对这个公式进行变形,以适应不同的加工情况。
比如,如果我们已知内孔锥度的角度和内孔大径,可以通过这个公式来计算出内孔小径,从而确定加工时需要使用的刀具尺寸和加工参数。
除了通过几何关系和三角函数来推导计算公式,我们还可以借助于计算机辅助设计软件来进行床车内孔锥度的计算。
在CAD/CAM软件中,通常会提供相应的工具来帮助我们计算内孔锥度,从而更加方便和快捷地确定加工参数。
总之,床车内孔锥度的计算是非常重要的。
通过合理的计算和确定,可以保证加工出来的内孔符合设计要求,从而提高产品的质量和精度。
我们可以通过几何关系和三角函数来推导计算公式,也可以借助于CAD/CAM软件来进行计算。
希望大家在实际的加工中能够根据这些方法来确定床车内孔的锥度,从而获得更好的加工效果。
车内孔震刀原因及解决办法【秘籍】
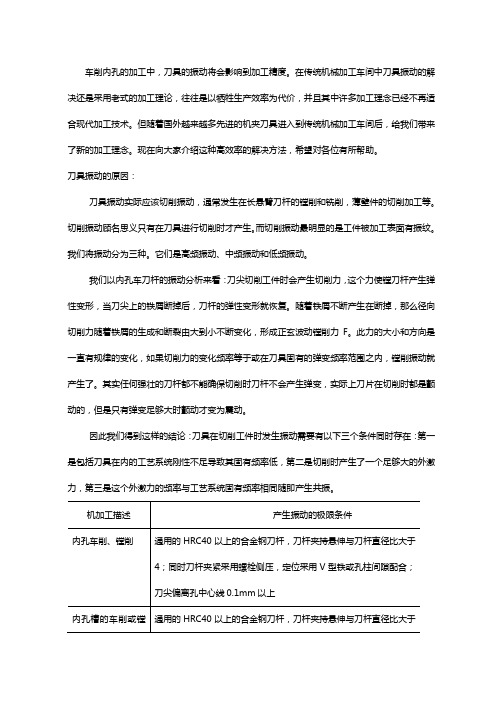
车削内孔的加工中,刀具的振动将会影响到加工精度。
在传统机械加工车间中刀具振动的解决还是采用老式的加工理论,往往是以牺牲生产效率为代价,并且其中许多加工理念已经不再适合现代加工技术。
但随着国外越来越多先进的机夹刀具进入到传统机械加工车间后,给我们带来了新的加工理念。
现在向大家介绍这种高效率的解决方法,希望对各位有所帮助。
刀具振动的原因:刀具振动实际应该切削振动,通常发生在长悬臂刀杆的镗削和铣削,薄壁件的切削加工等。
切削振动顾名思义只有在刀具进行切削时才产生。
而切削振动最明显的是工件被加工表面有振纹。
我们将振动分为三种。
它们是高频振动、中频振动和低频振动。
我们以内孔车刀杆的振动分析来看:刀尖切削工件时会产生切削力,这个力使镗刀杆产生弹性变形,当刀尖上的铁屑断掉后,刀杆的弹性变形就恢复。
随着铁屑不断产生在断掉,那么径向切削力随着铁屑的生成和断裂由大到小不断变化,形成正玄波动镗削力F。
此力的大小和方向是一直有规律的变化,如果切削力的变化频率等于或在刀具固有的弹变频率范围之内,镗削振动就产生了。
其实任何强壮的刀杆都不能确保切削时刀杆不会产生弹变,实际上刀片在切削时都是颤动的,但是只有弹变足够大时颤动才变为震动。
因此我们得到这样的结论:刀具在切削工件时发生振动需要有以下三个条件同时存在:第一是包括刀具在内的工艺系统刚性不足导致其固有频率低,第二是切削时产生了一个足够大的外激力,第三是这个外激力的频率与工艺系统固有频率相同随即产生共振。
削2;刀杆夹紧采用螺栓侧压,定位采用V型铁或孔柱间隙配合那么消除振动的方法便可根据下面三个原则:一是减小切削力至最小;二是尽量增强刀具系统或者夹具与工件的刚性;三是在刀杆内部再制造一个振动去打乱外激切削力的振频,从而消除刀具振动。
1.采用阻尼避振刀杆从而减轻振动我们虽然可通过改变刀杆的材质来达到消振的目的。
即把钢质刀杆改成整体硬质合金刀杆或重金属刀杆,它的刀杆夹持悬伸与刀杆直径避振极限比值(简称长径比)可达7-8倍。
车工实习课题五:内孔车削
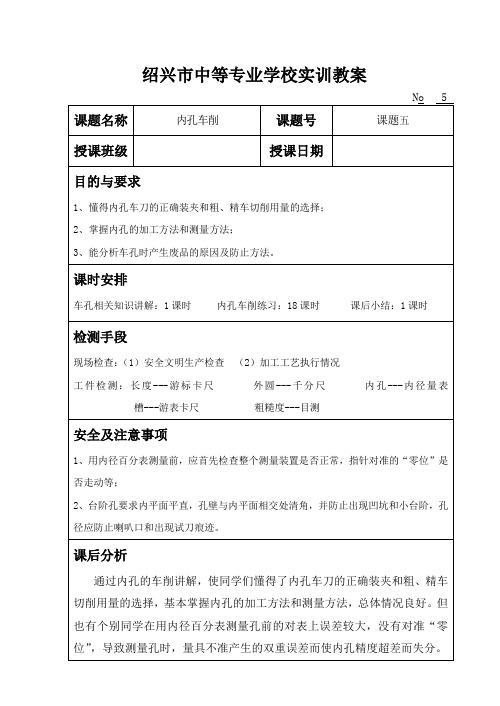
No5
课题名称
内孔车削
课题号
课题五
授课班级
授课日期
目的与要求
1、懂得内孔车刀的正确装夹和粗、精车切削用量的选择;
2、掌握内孔的加工方法和测量方法;
3、能分析车孔时产生废品的原因及防止方法。
课时安排
车孔相关知识讲解:1课时内孔车削练习:18课时课后小结:1课时
检测手段
现场检查:(1)安全文明生产检查(2)加工工艺执行情况
五、学生实训
六、巡回指导
1、指导学生如何刃磨内孔车刀;
2、指导学生如何车孔及内孔的检查方法;
七、批改工件
检测评分表(见附件2、4)
八、课后小结
通过此课讲解和训练,学生基本懂得了内孔车刀的刃磨步骤和装夹方法,掌握了内孔的加工方法,同时也学会了用内径百分表测量内孔的方法,至于内孔公差的控制,大部分学生还是可以的,但在综合课题中还得继续练习。
3.调头装夹,夹住Φ40mm外圆,长为18mm左右,车端面,控制总长,粗车Φ48mm,长18mm,粗、精车30mm,长15mm内孔,最后精车Φ48mm外圆和长度,切3X1槽(注意切槽刀与卡盘的碰撞),倒内外角去毛刺;
4.复查,打号,送检。
四、操作演示
学生分组,教师边讲解边示范,加深学生动手操作印象;
工件检测:长度---游标卡尺外圆---千分尺内孔---内径量表槽---游表卡尺粗糙度---目测
安全及注意事项
1、用内径百分表测量前,应首先检查整个测量装置是否正常,指针对准的“零位”是否走动等;
2、台阶孔要求内平面平直,孔壁与内平面相交处清角,并防止出现凹坑和小台阶,孔径应防止喇叭口和出现试刀痕迹。
(5)车削内孔时,车刀应先在内孔内行走一遍,观察其车刀与孔壁是否碰到;
车内孔教案

车内孔教案一、教学背景随着现代社会的发展,交通工具的普及和使用越来越广泛。
作为一种常见的交通工具,汽车给我们的生活带来了便利,但同时也存在一些安全隐患。
车内孔就是其中之一,也是常见的安全隐患之一。
因此,我们有必要针对车内孔的安全问题进行教育和培训,提高学生对车内孔的认知和防范意识。
二、教学目标1.了解车内孔的定义及其危害;2.掌握识别和预防车内孔的方法;3.提高学生对车内孔的防范意识和应对能力。
三、教学内容1.车内孔的定义与分类- 车内孔是指汽车内部某些部位的大孔或小孔,包括地板、座椅、仪表盘等位置的孔洞。
- 车内孔可以分为固定孔和可移动孔两种。
2.车内孔的危害- 车内孔存在抓取、摔倒、危险品漏出等安全隐患,可能对乘车人员造成伤害。
- 车内孔也可能导致物件滑入孔洞,引起汽车出现故障或损坏。
3.车内孔的识别方法- 注意观察车内环境,特别是地板、座椅和仪表盘等位置,发现可疑的孔洞。
- 通过触摸孔洞,判断是否存在锐利或突出的部位。
- 检查孔洞周围是否存在松动或破损的部分。
4.车内孔的预防方法- 提醒乘车人员保持良好的姿势和动作,避免身体过度倾斜或伸展。
- 防止物件掉落入孔洞,使用固定装置或防滑垫等辅助器材。
- 定期检查车内孔洞周围的装置和结构,确保其完好无损。
5.车内孔的应对能力培养- 学会正确的求救方式,如紧急联系车辆司机或相关人员。
- 学习基本的急救知识和技能,能够自救或互救。
四、教学方法1.讲授教学法:通过讲解、演示和示范,向学生介绍车内孔的知识和重要性。
2.情境教学法:结合生活实际,模拟车内孔发生的情境,引导学生进行思考和解决问题。
3.问题导向法:提出问题引导学生思考,培养学生的自主学习和解决问题的能力。
五、教学过程1.导入:引导学生回顾日常生活中与汽车有关的经历,引发对车内孔的思考。
2.讲解车内孔的定义与分类,通过图片和示意图向学生展示车内孔的位置和形态。
3.讨论车内孔的危害,引导学生思考车内孔可能造成的伤害和安全隐患。
关于数控车加工提高内孔表面粗糙度质量分析
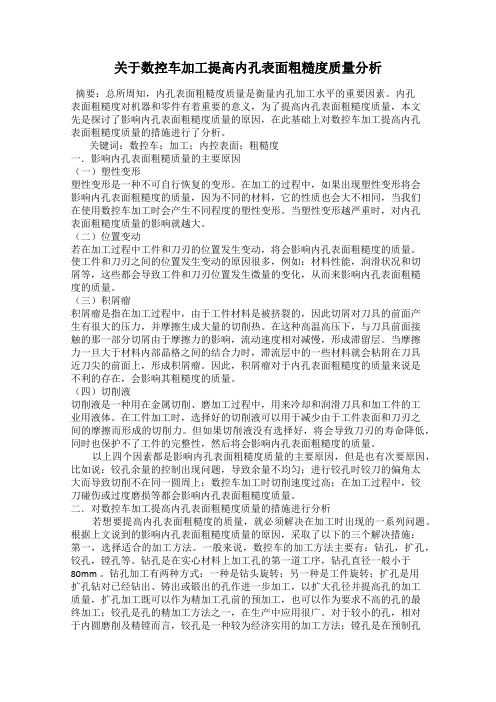
关于数控车加工提高内孔表面粗糙度质量分析摘要:总所周知,内孔表面粗糙度质量是衡量内孔加工水平的重要因素。
内孔表面粗糙度对机器和零件有着重要的意义,为了提高内孔表面粗糙度质量,本文先是探讨了影响内孔表面粗糙度质量的原因,在此基础上对数控车加工提高内孔表面粗糙度质量的措施进行了分析。
关键词:数控车;加工;内控表面;粗糙度一.影响内孔表面粗糙质量的主要原因(一)塑性变形塑性变形是一种不可自行恢复的变形。
在加工的过程中,如果出现塑性变形将会影响内孔表面粗糙度的质量,因为不同的材料,它的性质也会大不相同,当我们在使用数控车加工时会产生不同程度的塑性变形。
当塑性变形越严重时,对内孔表面粗糙度质量的影响就越大。
(二)位置变动若在加工过程中工件和刀刃的位置发生变动,将会影响内孔表面粗糙度的质量。
使工件和刀刃之间的位置发生变动的原因很多,例如:材料性能,润滑状况和切屑等,这些都会导致工件和刀刃位置发生微量的变化,从而来影响内孔表面粗糙度的质量。
(三)积屑瘤积屑瘤是指在加工过程中,由于工件材料是被挤裂的,因此切屑对刀具的前面产生有很大的压力,并摩擦生成大量的切削热。
在这种高温高压下,与刀具前面接触的那一部分切屑由于摩擦力的影响,流动速度相对减慢,形成滞留层。
当摩擦力一旦大于材料内部晶格之间的结合力时,滞流层中的一些材料就会粘附在刀具近刀尖的前面上,形成积屑瘤。
因此,积屑瘤对于内孔表面粗糙度的质量来说是不利的存在,会影响其粗糙度的质量。
(四)切削液切削液是一种用在金属切削、磨加工过程中,用来冷却和润滑刀具和加工件的工业用液体。
在工件加工时,选择好的切削液可以用于减少由于工件表面和刀刃之间的摩擦而形成的切削力。
但如果切削液没有选择好,将会导致刀刃的寿命降低,同时也保护不了工件的完整性,然后将会影响内孔表面粗糙度的质量。
以上四个因素都是影响内孔表面粗糙度质量的主要原因,但是也有次要原因,比如说:铰孔余量的控制出现问题,导致余量不均匀;进行铰孔时铰刀的偏角太大而导致切削不在同一圆周上;数控车加工时切削速度过高;在加工过程中,铰刀碰伤或过度磨损等都会影响内孔表面粗糙度质量。
车削内孔
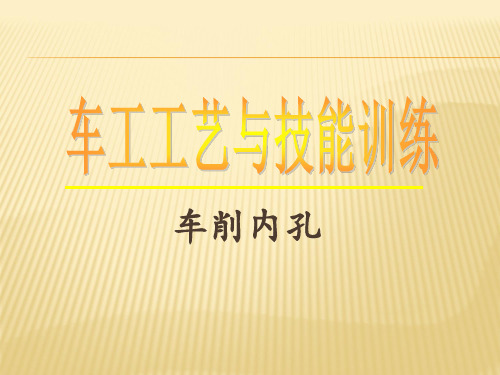
知
了解内孔车刀的种类及几何形状
识
与
掌握内孔车刀的装夹
技
能
目
学会车削内孔的方法
标
一、内孔车刀的种类及几何形状
1、内孔车刀:根据不同的加工情况,内孔车刀可分为通孔车刀。 和盲孔车刀两种。(什么叫做通孔?什么叫做盲孔?)
2.内孔车刀的几何形状
通孔车刀:几何形状基本上与外圆车刀相似
主偏角: Kr=60°~70°(减小径向切削力,防止震动)
三、车内孔的方法
(一)车孔的关键技术(★) 车孔的关键技术是解决内孔车刀的刚性和排屑问题。 1)提高内孔车刀刚性的措施 a、尽量增加刀杆的截面积。使内孔车刀的刀尖位于刀柄的
中心线上,刀柄在孔中的截面积可大大增加。 b、尽可能缩短刀柄的伸出长度,以增加车刀刀柄刚性,减
小切削过程中的震动。此外还可将刀柄上下两个平面做成 互相平行,这样就能很方便的根据孔深调整刀柄伸出的长 度。
副偏角:Kr′=15°~30°
为了防止后刀面和孔壁的摩擦又不使后角磨得太大,一
般磨双重后角α01=6°~12°α02=30°左右。
盲孔车刀:用来车盲孔
主偏角: 大于90度
Kr=92°~95°
副偏角: Kr′=6°~ 10°
后角要求和通孔车刀一样。刀尖在刀杆的最前端。刀尖
巩固练习:
1.根据的加工不同,内孔车刀分为哪几种?
2、通孔车刀的主偏角取(
),副偏角
取(
);盲孔车刀的主偏角取
(
),副偏角取(
)。
3、车内孔的关键是解决内孔车刀的( )
和(
)问题。
4、内孔车刀装夹时应注意那几点?
5、提高内孔车刀刚性的措施有?
车床加工薄壁零件内孔的方法和技巧

车床加工薄壁零件内孔的方法和技巧发布时间:2021-04-16T03:34:46.924Z 来源:《中国科技人才》2021年第6期作者:门桄1 张伟2 黄宇欢3[导读] 随着现代加工工艺的发展,薄壁零件数控加工技术愈加的精密高效,已逐渐发展成为现代高科技产业的基础,已越来越成为国家先进制造技术水平的重要衡量指标。
北方华安工业集团有限公司黑龙江 161046摘要:薄壁零件因为它具有重量轻,节约材料,结构紧凑等特点,已日益广泛地应用在各工业部门,尤其在模具、航空航天和汽车工业等领域应用更为广泛。
但薄壁零件的加工是车削中比较棘手的间题,原因是薄壁零件刚性差,强度弱,在加工中极容易变形,使零件的形位误差增大,不易保证零件的加工质量。
为此对薄壁零件的装夹,刀具的合理选用,切削用量的选择,进行了大量的试验,为今后更好地加工薄壁零件,保证质量,提供了理论依据。
关键词:车床;薄壁零件;加工随着现代加工工艺的发展,薄壁零件数控加工技术愈加的精密高效,已逐渐发展成为现代高科技产业的基础,已越来越成为国家先进制造技术水平的重要衡量指标。
薄壁零件数控加工技术在普通的数控机床实现了薄壁零件数控加工,生产出来的这些零件被广泛应用到现代工业的各个领域,包括军事、航空航天等。
在薄壁零件数控加工技术发展的过程中,计算机技术和仿真技术在这一过程中发挥了不可忽视的重要作用,高精密机床在现代加工业的运用,结合高仿真系统的分析,在数控加工前期对数控加工进行预防性仿真,利用数据来分析和减小数控零件的变形,并利用模拟平台模拟实际中的约束,建立工艺模型。
一、薄壁零件车床加工工艺薄壁零件在夹紧力、切削力的作用下,易产生变形、振动,影响工件精度。
在车削过程中,由于切削变形和切屑削、刀具、工件间的摩擦,产生大量的热,传至工件,易引起热变形,工件的尺寸不易掌握。
1、一般薄壁零件的加工装夹方法(1)一次装夹车削薄壁零件,车长度较短,直径较小的薄壁零件,毛坯预留卡盘装夹长度,粗精加工外圆、内孔、端面至要求割下;(2)用卡盘、芯轴加工,薄壁工件粗加工后,先用卡盘装夹,精车内孔,端面至要求,然后用胀力芯轴装夹工件,精车外圆、端面至要求;如图所示:(3)用花盘车削薄壁工件,直径大要求高的盘类、薄壁工件在粗加工后,磨平两端面,然后将工件装夹在花盘上,精车内孔、外圆至要求。
床车内孔锥度计算公式

床车内孔锥度计算公式在机械加工中,床车内孔锥度是一个非常重要的参数,它直接影响着零件的质量和性能。
因此,正确地计算床车内孔锥度是非常重要的。
在本文中,我们将讨论床车内孔锥度的计算公式及其应用。
床车内孔锥度的计算公式可以通过以下公式来表示:Taper = (D1 D2) / L 100%。
其中,Taper表示床车内孔的锥度,D1表示床车内孔大端的直径,D2表示床车内孔小端的直径,L表示床车内孔的长度。
这个公式非常简单,但却非常实用。
通过这个公式,我们可以快速准确地计算出床车内孔的锥度,从而为后续的加工工作提供参考。
在实际应用中,我们可以通过以下步骤来计算床车内孔的锥度:1.测量床车内孔大端和小端的直径。
这一步需要使用测量工具,如千分尺或外径千分尺,来准确地测量床车内孔的直径。
2.测量床车内孔的长度。
同样,我们需要使用测量工具来测量床车内孔的长度,以便后续的计算。
3.根据上述公式计算床车内孔的锥度。
将测量得到的床车内孔大端直径、小端直径和长度代入公式中,即可得到床车内孔的锥度。
通过上述步骤,我们可以快速准确地计算出床车内孔的锥度,为后续的加工工作提供重要的参考。
床车内孔锥度的计算公式不仅可以帮助我们快速准确地计算出床车内孔的锥度,还可以帮助我们更好地理解床车内孔的几何形状。
通过对床车内孔锥度的计算,我们可以更好地把握床车内孔的形状特征,从而更好地进行后续的加工工作。
除此之外,床车内孔锥度的计算公式还可以帮助我们更好地控制加工质量。
通过对床车内孔锥度的计算,我们可以及时发现加工中的问题,并及时调整加工工艺,从而保证加工质量。
总之,床车内孔锥度的计算公式是一个非常实用的工具,它可以帮助我们快速准确地计算出床车内孔的锥度,为后续的加工工作提供重要的参考。
同时,它还可以帮助我们更好地理解床车内孔的形状特征,并更好地控制加工质量。
因此,在实际应用中,我们应该充分利用床车内孔锥度的计算公式,以提高加工效率和加工质量。
数控车内孔加工注意事项

数控车内孔加工注意事项
1. 确保刀具刃口锐利和牢固,选择适当的加工参数,包括切削速度、进给速度和切削深度等。
2. 在加工孔时,要先进行基准定位和夹紧,以确保工件位置准确和稳定。
3. 在进行内孔加工前,要先预留出足够的余量,以便进行较大深度的加工。
4. 控制好进给速度和切削深度,保持一定的进给速度和切削深度,以确保加工精度和表面质量。
5. 选取合适的刀具进给和退刀方式,保持切削稳定,并减少振动和切屑的产生。
6. 在加工过程中,根据加工进度及时清理切屑和确保润滑液的正常供给,以保持切削效果。
7. 加工后,要对内孔的尺寸、圆度、表面质量等进行检测,以确保加工质量符合要求。
车 内 孔

车内孔内孔加工的方法很多,前面已介绍过钻孔,铰孔等加工方法。
本节介绍用车刀加工内孔的方法,通常称为镗孔。
一、常用的镗孔刀加工孔的刀具,因为刀杆的长度和粗细受到孔深和孔径的限制,不能做得太短,也不能做得太粗。
常用的镗刀有以下几种:通孔车刀、盲孔车刀通孔车刀是用来车通孔用的,切削部分的几何形状基本上与外圆车刀相似,为了减小径向切削力,防止振动,主偏角应取得较大一些,一般在60°~75°之间,副偏角为15°~30°。
盲孔车刀用来车盲孔或阶台孔,切削部分的几何形状基本上与偏刀相似。
它的主偏角大于90°。
刀尖在刀杆的最前端,刀尖与刀杆外端的距离应小于内孔半径,否则孔的底颊就无法车平。
车内孔阶台时,只要不碰内壁即可。
选择镗孔刀时应注意以下几点:第一、在保证不与孔壁相碰的情况下,尽可能选择粗壮的刀杆,也就是尽量增加刀杆的截面积,以增加其刚性和强度;第二、刀杆工作部分的长度大于孔的深度3~5mm即可,不要太长,这样可以减少振动;第三、镗孔刀的几何角度基本上和外圆车刀相同,只是后角可稍为偏大一点,后刀面均不能太高,否则会与孔壁相碰。
因此一般刀杆后面磨成圆弧形或磨成两个后角,在精加工时应选择负的刃倾角和合理的断屑槽,以控制切屑流出方向及顺利排出,使其不碰伤已加工表面。
二、车内孔的方法1、车孔刀具的安装(1)刀尖高度原则上应与工件中心对准。
但在实际工作中,粗车时可将车刀装得比工件中心线稍低一些(一般为工件直径的1%),因为这样可增大工作前角,减小切削力。
精车时,刀尖不能低于工件中心线可稍高一些,这样可以避免产生扎刀,而把内孔镗大,同时可减小后刀面与工件接触,避免摩擦,对降低工件的表面粗糙度有利。
(2)刀杆基面必须与主轴中心线平行,刀头可略向操作者偏斜一些,以免镗到一定深度时,刀杆后半部与工件表面相碰。
(3)刀杆的伸出长度应尽可能短一些,以提高其刚性。
2、工件的装夹(1)装夹有孔的毛坯工件时,必须根据外圆和内孔校正,使内、外圆的余量均匀。
车工实训指导1-2[车削内孔][1]
![车工实训指导1-2[车削内孔][1]](https://img.taocdn.com/s3/m/a2cd1587bceb19e8b8f6ba19.png)
情境四车削内圆柱面教学目的及要求1)熟习孔加工刀具的几何形状及选用及简单刃磨方法。
2)熟习内圆柱面基本车削方法。
3)会正确地选择工件的装夹方法。
4)会分析废品产生的原因和预防方法。
重点难点1)了解麻花钻的组成及几何形状;2)钻孔和扩孔的方法;3)孔加工时的切削用量及方法;4)了解内孔车刀使用与简单刃磨;5)工件及刀具的装夹;6)简单了解车孔的关键技术;7)车孔废品分析;8)内孔的测量工具及常规方法。
主要授课方法1)教师操作示范与讲解相结合;2)学生两人一组上机练习教师巡回指导相结合。
1.1、钻头1.1.1、麻花钻的组成1)柄部:是钻头的夹持部分,用于与机床主轴孔配合并传递扭矩。
2)柄部有:直柄和莫氏锥柄两种。
3)颈部:打标记、砂轮越程槽4)工作部分:包括切削部分与导向部分1.1.2、麻花钻工作部分的组成1)切削部分:由两个前刀面,两个后刀面,两条主刀刃,一条横刃组成。
2)导向部分:由两条刃带(副后刀面),两条副刀刃组成。
1.1.3、麻花钻刃磨注意事项1)钻尖的中心应予钻头的轴线一致;2)两条切削刃与轴线的夹角应相等;3)两条切削刃的长度(切削刃高度)应相等;4)横刃不得偏离轴线且相对与轴线应左右对称;5)后角应左右相等,后刀面应在同一曲面上;6)不要引起刃磨烧伤或钻尖缺损。
任务2、车孔2.1、钻中心孔及钻孔在实体材料上加工出孔的工作叫做钻孔。
(见下面图示)2.1.1、中心钻的类型A型(下图a)、B型(下图b)、C型、R型钻中心孔专用钻头。
A型与B型在日常生产中最常用2.1.2、钻中心孔的方法1)钻中心孔前将工件平面车平,中心处不许留有凸台,以利于中心钻头定心2)校正尾座中心,启动车床,使主轴带动工件回转;3)切削用量的选择和钻削钻削时应取较高的转速(一般取900~1120r/min),进给量应小而均匀(一般0.05~0.2mm/r)。
手摇尾座手轮时切勿用力过猛,并及时加注切削液冷却润滑;4)钻毕时,中心钻在孔中应稍作停留,然后退出,以修光中心孔,提高中心孔的形状精度和表面质量。
- 1、下载文档前请自行甄别文档内容的完整性,平台不提供额外的编辑、内容补充、找答案等附加服务。
- 2、"仅部分预览"的文档,不可在线预览部分如存在完整性等问题,可反馈申请退款(可完整预览的文档不适用该条件!)。
- 3、如文档侵犯您的权益,请联系客服反馈,我们会尽快为您处理(人工客服工作时间:9:00-18:30)。
b、尽可能缩短刀柄的伸出长度,以增加车刀刀柄刚性,减小切削过程中的震动。此外还可将刀柄上下两个平面做成互相平行,这样就能很方便的根据孔深调整刀柄伸出的长度。
(2)解决排屑问题
主要是控制排屑方向
a、精车时要求切屑流向待加工表面,采用正值刃倾
(2)盲孔车刀Kr=92°~95°
后角要求和通孔车刀一样不同之处是盲孔车刀夹在刀杆的最前端,刀尖到刀杆外端的距离应小于孔半径,否则无法车平孔的底面。
2.内孔车刀的刃磨步骤
粗磨前刀面——粗磨后刀面——粗磨副后刀
面——磨卷屑槽(控制前角和刃倾角)——精磨主后刀面和副后刀面——磨过渡刃
二、内孔车刀的安装要求(★)
五、车孔的方法
教学后记:
学生对这个知道比较感兴趣,积极性比较高,都能参与到课堂中来
老师讲解,学生讨论交流
课
堂
设
计
师生互动
授课内容:
概述:车孔是车削加工的主要内容之一,可作为半精加工和精加工,车孔精度可达IT7~IT8,表面粗糙度Ra可达1.6~3.2μm,精车可达Ra0.8μm。
(一)内孔车刀
1.内孔车刀的分类及主要角度
(1)通孔车刀Kr=60°~70°Kr′=15°~30°
为了防止后刀面和孔壁的摩擦又不使后角磨得太大,一般磨双重后角α01=6°~12°α02=30°左右。
(1)粗车盲孔
a、车端面、钻中心孔
b、钻底孔
c、对刀
d、用中滑板刻度控制切削深度,车削平底孔时要防止车刀与孔底面碰撞。
(2)精车盲孔
精车时用试车削的方法控制孔径尺寸。
小结:
车内孔的关键技术是什么?
作业:
习题册有关习题。
随笔
板书设计
车内孔
一、内孔车刀
二、内孔车刀的安装要求
三、工件的装夹
四、车孔的关键技术
五、车孔方法
1、车直孔.
(1)直通孔的车削基本上与车外圆相同,只是进刀和退刀的方向相反。
(2)车孔时的切削用量要比车外圆时适当减小,特别是车小孔或深孔时,其切削用量应更小。
2、车阶台孔
(1)车直径较小的阶台孔时,由于观察困难而尺寸
精度不易掌握采用粗、精车小孔再粗、精车大孔。
(2)车大的阶台孔时,视线不受影响的情况下,一般先粗车大孔和小孔,再精车小孔和大孔。
(3)车削孔径尺寸相差较大的阶台孔时,最好采用主偏角小于90°的车刀先粗车,然后用内偏刀精车。
(4)控制车孔深度的方法通常采用粗车时在刀柄上刻线作记号或安装限位铜片以及用床鞍刻线来控制等,车
时需用小滑板刻度盘或深度尺来控制
车刀刀尖必须对准工件旋转中心,否则不能将孔底车平。
车刀刀尖到刀杆外端的距离应小于内孔半径。否则端面不能车到中心。
(4)盲孔车刀装夹时内偏刀的主刀刃应与孔底平面成3°~5°角并要求横向有足够的退刀余地。
三、工件的装夹
车孔时,工件一般采用三爪卡盘安装;对于较大和较重的工件可采用四爪卡盘安装。加工直径较大、长度较短的工件,必须找正外圆和端面。
四、车孔的关键技术
车孔的关键技术是解决内孔车刀的刚性和排屑问题。
(1)提高内孔车刀刚性的措施
内孔车刀安装的正确与否,直接影响到车削情况及孔的精度,所以在安装时一定要注意:
(1)刀尖与工件中心等高或稍高。如果装的低于中心,由于切削抗力作用容易将刀柄压低而扎刀,并造成孔径扩大。
(2)刀柄伸出刀架不宜过长。一般比被加工孔长5~6mm左右.
(3)刀柄基本平行于工件轴线,否则在车削到一定深度时刀柄后半部分容易碰到工件孔口.
秭归县职教中心教师备课卡
学科:金工时间:2113年5月14日4节次:
课题
车内孔
课型
新课
教学目标
知识与技能
1、掌握内孔车刀的刃磨及安装
2、掌握内孔的车削方法
过程与方法
引导思考,知知识的探索欲望,形成自主学习的动力
教学重难点
车孔的关键技术问题,台阶孔的车削及深度控制
主导教学方法