车间物料管理流程
车间物料管理程序

车间物料管理程序一、背景介绍车间物料管理是指对车间内的物料进行统一管理和控制,确保物料的准确性、可用性和及时性,以提高生产效率和降低成本。
本文将介绍车间物料管理程序的标准格式,包括物料入库、物料出库、库存管理和物料盘点等内容。
二、物料入库程序1. 采购定单生成:根据生产计划和库存情况,制定采购计划并生成采购定单。
2. 采购验收:对供应商送货的物料进行验收,包括检查物料的数量、质量和规格是否与采购定单一致。
3. 入库登记:将验收合格的物料进行入库登记,记录物料的名称、规格、数量、供应商信息等。
4. 物料编码:为每一种物料分配惟一的物料编码,以便于后续的库存管理和查询。
5. 物料存放:将物料按照规定的存放位置进行分类存放,确保物料易于查找和取用。
三、物料出库程序1. 生产需求确认:根据生产计划和车间的实际生产情况,确认所需物料的种类和数量。
2. 领料申请:制定领料申请单,包括物料编码、名称、规格、领料数量等信息。
3. 领料审批:领料申请单需经过主管或者相关部门的审批,确保领料的合理性和准确性。
4. 出库操作:根据领料申请单,从库存中取出相应的物料,并记录物料的出库数量和领料人信息。
5. 物料使用:领料人将物料送至相应的生产线或者工作站,用于生产或者加工。
四、库存管理程序1. 库存监控:定期对库存进行盘点,记录实际库存数量和账面库存数量,及时发现并处理库存异常情况。
2. 库存调整:当发现库存异常时,及时进行库存调整,包括增加、减少或者调换物料的库存数量。
3. 库存报表:定期生成库存报表,包括库存总量、物料种类、库存周转率等指标,以便于管理层对库存情况进行分析和决策。
4. 定期清理:定期清理库存,处理过期、损坏或者低需求的物料,以避免库存积压和浪费。
五、物料盘点程序1. 盘点计划制定:根据需求和实际情况,制定物料盘点计划,包括盘点时间、盘点范围和盘点人员等。
2. 盘点操作:按照盘点计划进行盘点操作,逐一对物料进行盘点,记录实际库存数量和账面库存数量。
车间物料管理程序

车间物料管理程序一、背景介绍车间物料管理程序是指在制造业中,为了实现对车间物料的有效管理和控制,提高生产效率和质量,而制定的一套管理流程和操作规范。
该程序旨在确保车间物料的准确性、及时性和可追溯性,以满足生产需求和客户要求。
二、程序目标1. 提高物料管理的准确性:确保车间物料的标识、分类和数量信息准确无误,避免因物料错误导致的生产延误或质量问题。
2. 提高物料管理的及时性:确保物料的供应、领用和归还等操作能够及时完成,减少生产线因物料缺失而停工的情况。
3. 提高物料管理的可追溯性:确保物料的来源、使用和流向能够被追溯,以便在出现问题时能够快速定位和解决。
三、程序内容1. 物料标识管理a. 每个物料都应有唯一的标识码,包括物料编号、物料名称、规格型号等信息。
b. 物料标识码应精确贴在物料容器上,并与物料清单一致。
c. 物料标识码应定期检查和更新,确保信息的准确性和完整性。
2. 物料分类管理a. 根据物料的性质、用途和特点,对物料进行分类,建立物料分类表。
b. 物料分类表应包括物料分类代码、分类名称和相关属性等信息。
c. 物料分类表应定期审核和更新,确保物料分类的准确性和实用性。
3. 物料需求计划管理a. 根据生产计划和订单需求,编制物料需求计划。
b. 物料需求计划应包括物料编号、物料名称、需求数量、需求日期等信息。
c. 物料需求计划应定期审核和更新,确保物料供应的及时性和准确性。
4. 物料供应管理a. 根据物料需求计划,及时向供应部门提出物料采购申请。
b. 供应部门应根据采购申请,及时采购所需物料,并确保物料的质量和数量符合要求。
c. 物料供应情况应及时反馈给车间,以便进行后续生产安排。
5. 物料领用管理a. 车间员工需要领用物料时,应填写领用申请单,并经过相关主管的审核。
b. 物料领用申请单应包括领用人、领用日期、物料编号、物料名称、领用数量等信息。
c. 物料领用时,应根据领用申请单进行核对,并及时更新库存信息。
车间物料管理程序

车间物料管理程序一、背景介绍车间物料管理是指对车间内的物料进行有效的管理和控制,确保物料的准时供应、准确使用和准确归还,以提高生产效率和降低生产成本。
本文将详细介绍车间物料管理程序的标准格式。
二、程序目的车间物料管理程序的目的是确保物料的有效管理和控制,以满足生产需求,减少浪费和错误,提高生产效率和质量。
三、程序范围本程序适合于车间内的所有物料,包括原材料、半成品和成品等。
四、程序内容1. 物料需求计划a. 根据生产计划和定单需求,制定物料需求计划。
b. 确定物料的种类、数量和交付日期,并填写物料需求计划表。
c. 物料需求计划表由生产计划部门审核并下达给采购部门。
2. 供应商选择与评估a. 采购部门根据物料需求计划,选择合适的供应商。
b. 对供应商进行评估,包括供应商的质量、交货准时性、售后服务等方面。
c. 根据评估结果确定供应商,并签订合同。
3. 采购与收货a. 采购部门根据物料需求计划和合同要求,向供应商下达采购定单。
b. 采购部门跟踪采购进度,确保物料按时交付。
c. 车间接收物料时,进行验收并填写收货记录,包括物料的数量、质量和规格等信息。
d. 如发现物料有质量问题或者数量不符,及时与供应商联系并处理。
4. 物料存储与保管a. 车间内的物料按照种类和特性进行分类存储,确保易于管理和取用。
b. 物料存储区域应干燥、清洁、整齐,并设立合适的标识。
c. 物料应定期进行盘点和检查,确保库存准确。
5. 物料发放与使用a. 车间根据生产计划和工艺要求,向生产线发放物料。
b. 发放时应核对物料的种类、数量和规格,并记录发放信息。
c. 生产线上使用物料时,应按照工艺要求正确使用,并记录物料的使用情况。
6. 物料追溯与回收a. 如发现产品质量问题或者召回需求,应及时进行物料追溯。
b. 追溯时应查找相关物料的来源、批次和使用情况,并记录追溯信息。
c. 如有需要,应及时回收相关物料,并进行处理或者重新分类存储。
车间物料管理程序

车间物料管理程序一、引言车间物料管理是指对车间内的物料进行全面、高效的管理,确保物料的准确性、及时性和可追溯性,以满足生产的需求。
本文将介绍一个标准的车间物料管理程序,包括物料采购、入库、出库和库存管理等方面的内容。
二、物料采购1. 采购需求确认根据生产计划和库存情况,车间物料管理员与生产部门进行沟通,确认物料的采购需求。
2. 供应商选择与评估根据物料的特性和质量要求,车间物料管理员与采购部门一起选择合适的供应商,并对供应商进行评估,包括质量、价格、交货周期等方面的考虑。
3. 采购定单生成车间物料管理员根据采购需求和供应商评估结果,生成采购定单,并与供应商进行确认和签订合同。
4. 物料收货与验收供应商将物料送至车间,车间物料管理员进行物料收货,并进行质量验收,确保物料符合质量要求。
三、物料入库1. 入库单生成车间物料管理员根据采购定单和物料收货情况,生成入库单,并记录物料的批次、数量和质量等信息。
2. 入库操作车间物料管理员将物料按照入库单上的信息进行入库操作,包括将物料放置到指定位置、进行质量检验等。
3. 入库记录车间物料管理员将入库操作的相关信息记录到物料管理系统中,包括物料的批次、数量、质量等信息。
四、物料出库1. 领料需求确认根据生产计划和车间生产情况,车间物料管理员与生产部门进行沟通,确认物料的领料需求。
2. 领料单生成车间物料管理员根据领料需求,生成领料单,并记录领料的批次、数量和用途等信息。
3. 出库操作车间物料管理员根据领料单上的信息进行出库操作,包括从库存中取出物料、进行质量检验等。
4. 出库记录车间物料管理员将出库操作的相关信息记录到物料管理系统中,包括物料的批次、数量、用途等信息。
五、库存管理1. 库存盘点定期进行库存盘点,确保库存数量与实际情况一致,发现差异及时进行调整和处理。
2. 库存报警根据库存情况和生产需求,设定库存报警值,当库存数量低于报警值时,及时进行补充采购。
车间的物料如何管理

车间的物料如何管理物料管理是车间生产过程中非常重要的一环,它涉及到物料的采购、入库、出库、库存管理等各个环节,对于保证生产进度和质量具有重要意义。
下面将详细介绍车间物料管理的标准格式文本。
一、物料采购管理1. 制定物料采购计划:根据生产计划和物料需求,制定物料采购计划,明确采购数量、采购时间和采购渠道等信息。
2. 寻找供应商:通过市场调研、询价、招标等方式,寻找合适的供应商,确保物料的质量和价格具有竞争力。
3. 签订采购合同:与供应商签订采购合同,明确双方的权利和义务,确保采购过程的合法性和规范性。
4. 物料验收:对采购的物料进行验收,确保物料符合质量要求,并及时处理不合格物料。
二、物料入库管理1. 入库登记:对采购的物料进行入库登记,记录物料的名称、规格、数量、供应商等信息,并生成入库单据。
2. 质量检验:对入库的物料进行质量检验,确保物料符合质量要求,并及时处理不合格物料。
3. 物料编码:对入库的物料进行编码,建立物料档案,方便后续的库存管理和使用。
4. 存储安排:根据物料的特性和使用频率,合理安排物料的存放位置,确保物料易于查找和取用。
5. 定期盘点:定期对库存物料进行盘点,核对实际库存与账面库存的差异,及时调整库存数量。
三、物料出库管理1. 出库申请:根据生产计划和物料需求,制定出库申请单,明确物料的名称、规格、数量和使用部门等信息。
2. 出库审批:对出库申请进行审批,确保出库的合理性和合规性。
3. 出库操作:根据出库申请单,进行物料的出库操作,记录出库数量和出库时间,并生成相应的出库单据。
4. 物料发放:将出库的物料发放给申请部门,并记录发放信息,确保物料的准确性和完整性。
四、库存管理1. 库存监控:定期对库存物料进行监控,了解库存情况,及时调整采购计划和生产计划。
2. 库存调拨:根据生产需求和库存情况,进行库存物料的调拨,确保生产线的正常运行。
3. 库存报废:对过期、损坏或不合格的物料进行报废处理,确保库存物料的质量和安全。
车间物料管理程序

车间物料管理程序一、介绍车间物料管理程序是为了有效管理和控制车间内各种物料的流动和使用,确保生产过程中物料的准确性、及时性和可追溯性而设计的。
该程序涵盖了物料采购、入库、出库、盘点、报废等环节,旨在提高车间物料管理的效率和准确性,减少物料浪费和损耗。
二、物料采购1. 采购计划编制根据车间生产计划和物料需求,制定物料采购计划,并明确物料的种类、数量、质量要求和采购时间等信息。
2. 供应商选择与评估根据企业的采购政策和要求,选择合适的供应商,并进行供应商的资质评估和信用评级,确保供应商能够提供符合要求的物料。
3. 采购定单生成根据采购计划,生成采购定单,并发送给供应商。
采购定单应包含物料的名称、规格、数量、单价、交货期限等信息。
4. 采购合同签订与供应商签订采购合同,明确双方的权益和责任,确保采购过程的合法性和合规性。
5. 物料验收与入库在物料到达车间时,进行验收工作。
验收应包括对物料的数量、质量、规格等方面的检查,确保物料符合要求。
合格的物料应及时入库,并进行标识和分类,以便后续使用和管理。
三、物料出库1. 生产需求确认根据生产计划和车间需求,确认所需的物料种类、数量和使用时间等信息。
2. 领料单生成根据生产需求,生成领料单,并明确领料的物料名称、规格、数量和领料人等信息。
3. 领料审核与批准领料单应提交给相关部门进行审核和批准,确保领料的合理性和准确性。
4. 物料发放经过审核和批准后,领料单上的物料应及时发放给领料人,并进行记录和确认。
四、物料盘点1. 盘点计划制定根据企业的盘点周期和要求,制定物料盘点计划,并明确盘点的时间、范围和方式等信息。
2. 盘点操作按照盘点计划,对车间内的物料进行逐一盘点。
盘点时应子细核对物料的名称、规格、数量和存放位置等信息,并记录在盘点表中。
3. 盘点结果处理根据盘点结果,及时调整物料库存数量和位置,并对盘点结果进行分析和处理,发现问题及时纠正。
五、物料报废1. 报废申请当发现物料过期、损坏、质量不合格等情况时,应及时提出报废申请,并明确报废的物料名称、数量和原因等信息。
车间发料流程管理制度

第一章总则第一条为确保车间生产物料供应的及时性和准确性,提高物料管理水平,降低生产成本,特制定本制度。
第二条本制度适用于公司所有车间及相关部门的物料发放管理。
第三条发料流程应遵循“规范操作、责任到人、及时准确、节约使用”的原则。
第二章发料准备第四条物料发放前,仓库管理员应根据生产计划和生产部门的需求,提前做好物料的备货工作。
第五条仓库管理员应定期检查物料库存,确保库存充足,避免因缺货导致生产中断。
第六条仓库管理员应做好物料标识,分类存放,便于查找和发放。
第七条生产部门需提前一天向仓库提交物料需求计划,包括物料名称、规格、数量、用途等信息。
第三章发料流程第八条仓库管理员根据生产部门的需求计划,核对库存,确认物料无误后,填写《物料发放单》。
第九条仓库管理员将《物料发放单》交由车间负责人审核,审核无误后签字确认。
第十条车间负责人将审核后的《物料发放单》交回仓库管理员。
第十一条仓库管理员按照《物料发放单》的内容,将物料发放给生产部门。
第十二条仓库管理员在发放物料时,应检查物料的质量,确保物料符合生产要求。
第十三条生产部门接收物料后,应立即检查物料的质量和数量,确认无误后签字确认。
第十四条仓库管理员将《物料发放单》和物料验收单归档备查。
第四章物料回收第十五条生产部门在使用过程中,应及时回收不合格、多余或损坏的物料。
第十六条仓库管理员定期检查回收的物料,对可回收利用的物料进行分类存放。
第十七条对不可回收利用的物料,仓库管理员应按照规定进行处理。
第五章监督与考核第十八条车间负责人负责监督发料流程的执行情况,确保物料发放的及时性和准确性。
第十九条仓库管理员应定期对发料流程进行自查,发现问题及时上报。
第二十条对违反本制度的行为,公司应予以严肃处理,并追究相关责任人的责任。
第六章附则第二十一条本制度由公司生产管理部门负责解释。
第二十二条本制度自发布之日起实施。
第二十三条本制度如有未尽事宜,由公司生产管理部门负责修订。
车间物料管理程序

车间物料管理程序引言概述:车间物料管理是制造业中非常重要的环节,它涉及到物料的采购、入库、出库、库存管理等多个方面。
为了提高车间物料管理的效率和准确性,许多企业采用了物料管理程序来进行管理。
本文将介绍车间物料管理程序的五个部分,包括物料采购、入库管理、出库管理、库存管理和统计分析。
一、物料采购:1.1 供应商选择:根据企业的需求和要求,选择合适的供应商。
考虑供应商的产品质量、价格、交货时间等因素。
1.2 采购订单生成:根据车间的物料需求,生成采购订单。
订单中包括物料名称、数量、单价等信息。
1.3 采购合同签订:与供应商签订采购合同,明确双方的权责,确保物料的供应和交付。
二、入库管理:2.1 入库登记:根据采购订单,将物料入库登记。
记录物料的名称、数量、批次号等信息。
2.2 质量检验:对入库物料进行质量检验,确保物料符合要求。
2.3 入库审核:审核入库登记信息,确保准确无误。
三、出库管理:3.1 领料申请:根据车间的生产计划,提出领料申请。
申请中包括物料名称、数量、用途等信息。
3.2 出库审批:审批领料申请,确保领料的合理性和准确性。
3.3 出库操作:根据审批通过的领料申请,进行出库操作。
记录出库物料的名称、数量、领料人等信息。
四、库存管理:4.1 库存盘点:定期对车间的物料库存进行盘点,确保库存的准确性。
4.2 库存调整:根据盘点结果,对库存进行调整。
包括增加、减少或调整物料数量。
4.3 库存预警:根据库存的预警规则,及时提醒物料管理员进行采购或调整。
五、统计分析:5.1 物料消耗统计:统计物料的消耗情况,分析物料的使用趋势。
5.2 供应商评估:对供应商的供货情况进行评估,包括交货准时率、产品质量等指标。
5.3 成本分析:通过对物料采购、库存和消耗情况进行分析,评估物料管理的成本效益。
总结:车间物料管理程序的有效实施,可以提高车间物料管理的效率和准确性,降低企业的物料成本。
通过合理的物料采购、入库管理、出库管理、库存管理和统计分析,企业可以更好地掌握物料的使用情况,优化供应链管理,提高生产效率。
车间物料管理流程

生产物料管理流程目旳:规范物料运作管理,提高生产效率,简化物料流程,及时理解物料信息.使用范畴:生产管理部。
1、领料流程:1.1 接PMC筹划部生产任务单、领料单。
1.2 核对生产任务号(制造单号)与所下单生产线与否一致,如不一致及时反馈PMC 筹划部重新下单。
1.3 接到领料单2小时后,到PMC部材料仓领取套料。
1.4 领料原则是每个物料员针对自己所领旳每一种物料必须与套料单上旳物料编码相一致,若不一致应向PMC仓管员及时反馈,确认无误后再对每种物料逐个点数,并且在套料单领料一栏所填写旳领料实数后签名,如果发现套料单所填写物料数量与实物数量不相否时,及时向仓管员反馈补齐数量,套料单据不得涂改。
1.5 物料员领料后,核对套料单上所有物料与否领齐,如所有领齐仓管员、物料员双方确认后在领料单上签名,没有领齐旳单据物料员只在领料数量后签名,此领料单一式三份,生产部黄联、PMC部蓝联、财务部白联各执一联,留底存根。
1.6 领料进车间后,物料员须将物料按构造、电子料旳种类分别整洁摆放在货架上,大件物料(塑料类)放在地面上摆放整洁,对试用、超差、挑选等旳物料用红色油性笔做特别标记,且及时填写物料收发本贴在物料堆放处,最后按生产制造单号将各物料套料欠记入自己欠料账本,以便于及时跟催套料欠物料。
1.7 物料员必须按生产线将领料单据整顿好,按规定区域摆放好,未经记录员容许物料员不得擅自拿走单据,只容许查看领料数量及填写第二次领料数量,记录员录入电子档后将所有领齐单据按生产线别整顿好存入文本档,未领齐单据整顿后按规定区域再摆放好。
1.8 备好物料准备生产,发料时应注意试用、超差、挑选加工、异常旳物料,必须告知线长,否则绩效考核解决。
2、退料流程:2.1 生产过程中,将不良品物料挑选出,做上标记放在不良品区。
2.2 将不良品给质管部巡线技术员确认与否可以接受,若能接受则在不良标记上写上“OK”表达已确认;若不能接受,放回不良品区做好标记,下班后统一交给生产线退料员,退料员确认数量且记录退料数后退到物料房相应生产线。
车间物料管理办法
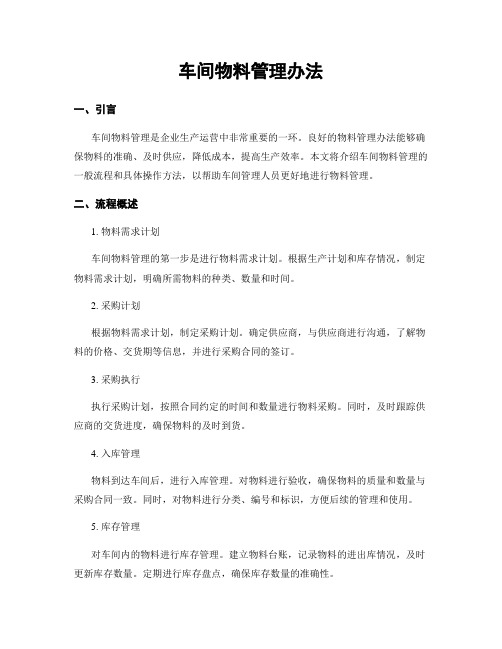
车间物料管理办法一、引言车间物料管理是企业生产运营中非常重要的一环。
良好的物料管理办法能够确保物料的准确、及时供应,降低成本,提高生产效率。
本文将介绍车间物料管理的一般流程和具体操作方法,以帮助车间管理人员更好地进行物料管理。
二、流程概述1. 物料需求计划车间物料管理的第一步是进行物料需求计划。
根据生产计划和库存情况,制定物料需求计划,明确所需物料的种类、数量和时间。
2. 采购计划根据物料需求计划,制定采购计划。
确定供应商,与供应商进行沟通,了解物料的价格、交货期等信息,并进行采购合同的签订。
3. 采购执行执行采购计划,按照合同约定的时间和数量进行物料采购。
同时,及时跟踪供应商的交货进度,确保物料的及时到货。
4. 入库管理物料到达车间后,进行入库管理。
对物料进行验收,确保物料的质量和数量与采购合同一致。
同时,对物料进行分类、编号和标识,方便后续的管理和使用。
5. 库存管理对车间内的物料进行库存管理。
建立物料台账,记录物料的进出库情况,及时更新库存数量。
定期进行库存盘点,确保库存数量的准确性。
6. 物料发放根据生产计划和工单需求,进行物料的发放。
发放时要核对物料的种类、数量和使用人员,并记录发放情况,以便后续的追溯和统计。
7. 废料处理车间内产生的废料需要进行妥善处理。
建立废料处理制度,对废料进行分类、收集和处理,确保环境的安全和卫生。
8. 监控与改进车间物料管理需要进行监控和改进。
通过物料使用情况的统计分析,找出存在的问题和改进的空间,并及时采取措施进行改进,提高物料管理的效率和质量。
三、操作方法1. 物料需求计划的制定:- 根据生产计划和库存情况,确定物料需求计划;- 考虑物料的采购周期,合理安排物料的采购时间。
2. 采购计划的制定:- 根据物料需求计划,制定采购计划;- 确定供应商,与供应商进行沟通,了解物料的价格、交货期等信息;- 签订采购合同,明确双方的权责和交付条件。
3. 采购执行:- 按照采购计划执行采购;- 跟踪供应商的交货进度,确保物料的及时到货。
车间物料管理流程

车间物料管理流程1.物料需求计划首先,车间需要进行物料需求计划,根据生产计划和库存情况,确定所需物料的数量和时间。
这一步通常由生产计划部门和采购部门共同完成。
2.采购物料根据物料需求计划,采购部门与供应商进行洽谈和谈判,确定价格、交货时间、质量要求等。
一旦达成一致,采购部门将与供应商签订采购合同,并安排物料的交付和收货。
3.物料接收和入库车间在物料到达时进行验收,检查其数量和质量是否符合要求。
一旦验收通过,物料进入仓库,根据分类和规格等信息进行标识,并进行入库记录。
同时,对质量有问题的物料进行返工或退货处理。
4.物料领用生产过程需要使用各种物料,车间根据生产计划和工单,向仓库提出物料领用申请。
仓库管理员根据申请进行物料发放,并记录物料的出库信息。
5.物料使用和追踪车间完成生产后,记录使用的物料数量和情况。
这样可以根据历史数据进行物料的使用分析和预测,以便更好地进行物料需求计划和库存控制。
6.库存管理车间需要对物料库存进行定期盘点,确保库存数量与系统记录相符,并进行库存差异的调整。
同时,进行库存分析,根据库存情况和预测需求,进行适当的调整和优化。
7.废料处理车间可能会产生一些废弃或废料,需要进行妥善处理,包括回收、再利用或销毁。
车间需要建立相应的废料处理流程和标准,确保废料处理的环保和安全。
8.报废物料处理车间中可能会有一些过期、损坏或无法使用的物料,需要进行报废处理。
车间根据相关的规定和流程,将报废物料进行识别和标识,并进行报废记录和处理。
9.供应商管理为了确保物料的质量和供应的稳定性,车间需要与供应商建立良好的合作关系,并进行供应商的评估和管理。
这包括对供应商的定期审核、交货情况的监控、退货处理等。
10.总结和改进车间应当定期进行物料管理流程的总结和改进,通过对过程进行分析和评估,发现问题和不足,并采取相应的措施进行改进。
这包括提高采购效率、减少库存、优化物料使用等方面的改进措施。
以上是一种常见的车间物料管理流程,具体流程可以根据实际情况进行调整和优化。
车间物料管理程序

车间物料管理程序一、概述车间物料管理程序是指通过一系列的流程和操作,对车间内的物料进行有效的管理和控制,确保物料的准确性、及时性和可追溯性,提高生产效率和质量。
二、流程步骤1. 物料需求计划车间物料管理程序的第一步是根据生产计划和产能需求,制定物料需求计划。
该计划由生产计划员负责编制,包括物料种类、数量、交货日期等信息。
计划员根据历史数据、市场需求和库存情况等因素进行合理的预测和计算。
2. 采购申请根据物料需求计划,车间物料管理程序的下一步是生成采购申请单。
采购申请单包括物料名称、规格、数量、交货日期等信息。
申请单由车间物料管理员填写,并提交给采购部门。
3. 供应商选择与采购采购部门收到采购申请单后,根据物料的特性、价格、供应能力等因素,选择合适的供应商。
采购部门与供应商进行谈判,达成合作协议,并进行物料的采购。
4. 物料接收与入库采购部门将采购的物料送至车间物料接收区域,车间物料管理员进行物料的接收和验收。
验收包括对物料的数量、质量、规格等进行检查,确保物料符合要求。
验收合格后,物料管理员将物料进行分类、编号,并入库。
5. 物料领用车间生产人员根据生产工单的需求,向车间物料管理员提出物料领用申请。
申请单包括物料名称、规格、数量等信息。
物料管理员根据申请单,从库存中发放相应的物料给生产人员。
6. 物料使用与追溯生产人员在生产过程中使用物料,并在生产记录中进行相应的记录。
物料使用的追溯是指通过物料的编号、批次号等信息,可以追溯到物料的来源、采购日期、供应商等相关信息,以便于质量追溯和问题排查。
7. 库存管理与盘点车间物料管理员负责对物料库存进行管理和盘点。
库存管理包括库存数量的监控、库存报警、库存周转率的计算等。
定期进行库存盘点,核对实际库存和系统库存的差异,并进行调整。
8. 报废处理对于过期、损坏、质量不合格的物料,车间物料管理员负责进行报废处理。
报废物料需要进行分类、记录,并按照公司的规定进行处理,以确保环境和安全要求。
车间物料管理程序

车间物料管理程序引言概述车间物料管理程序是指在生产车间中对原材料、半成品和成品进行有效管理和控制的一套规范流程。
良好的物料管理程序可以提高生产效率,降低生产成本,保证产品质量,确保生产计划的顺利进行。
本文将详细介绍车间物料管理程序的五个主要部分。
一、物料采购管理1.1 确定物料需求:根据生产计划和库存情况,确定所需的原材料和零部件种类、数量和交付时间。
1.2 选择供应商:根据物料的质量、价格、交货时间等因素,选择可靠的供应商进行采购。
1.3 签订合同:与供应商签订采购合同,明确双方的责任和义务,确保供应链畅通。
二、物料接收和入库管理2.1 检验物料:对接收到的物料进行质量检验,确保符合规定标准。
2.2 标识和分类:对物料进行标识和分类,便于后续的存储和使用。
2.3 入库登记:将接收到的物料信息录入系统,建立物料档案,方便查询和管理。
三、物料存储管理3.1 合理布局:根据物料种类和使用频率,合理规划存储位置,确保易取易放。
3.2 温湿度控制:对易受环境影响的物料进行特殊处理,保证存储条件符合要求。
3.3 定期盘点:定期对存储的物料进行盘点,确保库存准确无误。
四、物料领用和使用管理4.1 领料审批:领料前需经过相关部门的审批,确保领用合理、有效。
4.2 记录和追溯:对领用的物料进行记录,建立领料档案,方便追溯和分析。
4.3 物料消耗控制:对物料的使用进行监控,控制消耗量,避免浪费。
五、物料报废和处理管理5.1 报废流程:建立物料报废流程,确保报废物料得到合理处理,避免对环境造成影响。
5.2 报废记录:对报废物料进行记录和分类,建立报废档案,方便统计和分析。
5.3 处理方式:根据不同类型的报废物料,采取相应的处理方式,如回收、销毁等。
结语良好的车间物料管理程序是生产过程中的重要环节,对于提高生产效率、降低成本、保证产品质量具有重要意义。
通过规范的物料管理程序,可以有效地控制物料的流动和使用,确保生产过程的顺利进行。
车间物料管理程序

车间物料管理程序一、引言车间物料管理程序是指为了提高生产效率和物料利用率,确保车间物料的及时供应和准确使用,以及减少物料浪费和损耗而制定的一套管理流程和规范。
本文将详细介绍车间物料管理程序的各个环节和具体操作步骤。
二、程序流程1. 物料需求计划车间物料管理程序的第一步是根据生产计划和订单需求,制定物料需求计划。
根据生产工艺和物料清单,确定所需物料的种类、规格和数量,并进行统计和汇总。
物料需求计划可以根据生产周期和库存情况进行调整和优化。
2. 采购计划根据物料需求计划,制定采购计划。
采购计划包括确定供应商、物料采购数量、采购价格和交货时间等信息。
采购计划需要根据供应商的能力和信誉进行评估和选择,以确保物料的质量和供应的可靠性。
3. 采购执行根据采购计划,与供应商进行联系和协商,签订采购合同或订单。
在采购执行过程中,需要及时跟踪和监控供应商的交货进度和物料质量,确保按时供应和满足质量要求。
4. 物料收货当物料到达车间时,需要进行物料收货。
收货时要核对物料的种类、规格、数量和质量,并及时更新库存信息。
如果发现物料有问题或不符合要求,需要及时与供应商联系并进行退货或更换。
5. 物料入库物料收货后,需要进行物料入库操作。
入库时要按照物料的种类、规格和批次进行分类和标识,并及时更新库存信息。
入库操作要严格按照标准操作流程进行,确保物料的安全和准确性。
6. 物料发放根据生产计划和车间需求,进行物料发放操作。
发放时要核对物料的种类、规格和数量,并及时更新库存信息。
发放操作要按照发放单或领料单进行,确保物料的准确使用和追溯。
7. 物料使用车间在使用物料时,要按照工艺要求和操作规范进行。
物料使用过程中要注意物料的保存和防止损耗,确保物料的有效利用和节约。
8. 库存管理车间物料管理程序中的重要环节是库存管理。
需要定期进行库存盘点和调整,及时更新库存信息。
库存管理要根据物料的使用情况和需求进行优化和调整,以确保库存的合理水平和减少库存积压。
车间物料管理程序

车间物料管理程序引言概述:车间物料管理是制造业中非常重要的一环,它涉及到物料的采购、入库、出库、库存管理等多个方面。
为了提高车间物料管理的效率和准确性,许多企业采用了车间物料管理程序。
本文将介绍车间物料管理程序的五个主要部分,包括物料采购管理、入库管理、出库管理、库存管理和报表分析。
一、物料采购管理:1.1 供应商管理:建立供应商数据库,包括供应商名称、联系人、联系方式等信息,以便及时与供应商进行沟通和交流。
1.2 采购计划制定:根据车间生产计划和库存情况,制定物料采购计划,确保物料供应的及时性和准确性。
1.3 采购订单管理:根据采购计划生成采购订单,包括物料名称、数量、价格等信息,与供应商进行订单确认和跟踪。
二、入库管理:2.1 入库登记:对采购到的物料进行入库登记,包括物料编码、批次、数量等信息,确保物料的准确性和可追溯性。
2.2 质量检验:对入库物料进行质量检验,确保物料符合质量标准,避免不良物料进入生产流程。
2.3 入库审核:对入库登记和质量检验结果进行审核,确保入库数据的准确性和完整性。
三、出库管理:3.1 生产订单管理:根据生产计划生成生产订单,包括物料需求、数量、交付日期等信息,确保车间生产的顺利进行。
3.2 出库登记:对生产订单所需物料进行出库登记,包括物料编码、批次、数量等信息,确保物料的准确性和可追溯性。
3.3 出库审核:对出库登记进行审核,确保出库数据的准确性和完整性,避免错误出库和物料浪费。
四、库存管理:4.1 库存监控:实时监控库存情况,包括库存数量、库龄、库存周转率等指标,及时预警并调整物料采购计划。
4.2 库存调拨:根据生产需求和库存情况,进行库存调拨,确保各车间物料供应的均衡和及时性。
4.3 库存盘点:定期进行库存盘点,与实际库存进行核对,确保库存数据的准确性和系统与实际的一致性。
五、报表分析:5.1 采购报表:生成采购订单、采购金额、供应商评价等报表,进行采购情况的分析和评估。
车间物料管理程序

车间物料管理程序引言概述:车间物料管理程序是指为了有效管理和控制车间内物料的流动和使用而制定的一套规范和流程。
良好的物料管理程序能够提高生产效率,降低成本,确保产品质量和安全。
一、物料采购管理1.1 确定物料需求:根据生产计划和产品需求,确定所需物料的种类、数量和质量要求。
1.2 寻找供应商:选择合适的供应商,考虑价格、质量、交货时间等因素,签订合同。
1.3 定期评估供应商:定期对供应商的绩效进行评估,确保供应链的稳定和可靠性。
二、物料接收和入库管理2.1 检查物料质量:对接收的物料进行质量检查,确保符合要求,及时处理不合格品。
2.2 标识和分类:对接收的物料进行标识和分类,便于存放和查找。
2.3 入库记录:建立入库记录,记录物料的种类、数量、批次等信息,便于追溯和管理。
三、物料库存管理3.1 定期盘点:定期对库存进行盘点,确保库存数据准确性。
3.2 控制库存:根据生产计划和需求,控制库存水平,避免过多或过少库存。
3.3 FIFO原则:采用先进先出原则管理库存,确保物料的新鲜度和质量。
四、物料领料和使用管理4.1 领料程序:建立领料程序,规范领料流程,确保领料准确性和及时性。
4.2 使用记录:记录物料的使用情况,包括数量、用途等,便于成本核算和管理。
4.3 废料处理:对废料进行分类和处理,减少浪费,保护环境。
五、物料退库和报废管理5.1 退库程序:建立退库程序,规范退库流程,确保退库准确性和及时性。
5.2 报废管理:对报废物料进行分类和处理,记录报废原因,做好报废记录。
5.3 效益评估:定期评估物料管理程序的效益,及时调整和改进,提高管理水平和效率。
综上所述,车间物料管理程序是车间生产管理的重要组成部分,通过规范的流程和程序,能够提高生产效率,降低成本,确保产品质量和安全。
良好的物料管理程序是企业持续发展的基础,值得重视和不断完善。
车间的物料如何管理

车间的物料如何管理标题:车间的物料如何管理引言概述:车间的物料管理是生产过程中非常重要的一环,它直接影响着生产效率和产品质量。
有效的物料管理可以匡助车间提高生产效率,减少生产成本,确保生产计划的顺利进行。
本文将从物料分类、入库管理、出库管理、库存盘点和物料追踪五个方面详细介绍车间的物料管理。
一、物料分类1.1 根据用途分类:将物料按照其在生产过程中的用途进行分类,例如原材料、半成品、成品等。
1.2 根据特性分类:将物料按照其特性进行分类,例如易腐烂、易燃烧、易挥发等。
1.3 根据管理需求分类:将物料按照管理需求进行分类,例如常用物料、季节性物料、特殊物料等。
二、入库管理2.1 接收检验:车间接收到物料后,需要进行检验确认物料的质量和数量是否符合要求。
2.2 入库登记:将接收到的物料信息进行登记,包括物料名称、规格、数量、生产日期等。
2.3 分类存放:根据物料的特性和用途,将物料进行分类存放,确保易燃易爆等危(wei)险物料得到安全存放。
三、出库管理3.1 需求确认:车间需要出库物料时,需要确认生产计划的需求量。
3.2 出库登记:将出库的物料信息进行登记,包括物料名称、规格、数量、领用部门等。
3.3 物料追踪:对出库的物料进行追踪管理,确保物料的准确性和及时性。
四、库存盘点4.1 定期盘点:定期对车间的库存物料进行盘点,确保库存数量与系统记录一致。
4.2 盘点记录:将盘点结果进行记录并与系统数据进行核对,及时发现并纠正数据错误。
4.3 盘点调整:根据盘点结果进行库存调整,及时处理库存过多或者过少的情况。
五、物料追踪5.1 追踪系统:建立物料追踪系统,记录物料的入库、出库、流转等信息。
5.2 追踪流程:规定物料的追踪流程,确保物料的流转过程可追溯。
5.3 追踪效果评估:定期对物料追踪系统进行评估,发现问题及时改进,提高物料管理效率。
结论:车间的物料管理是生产过程中不可或者缺的一环,良好的物料管理可以提高生产效率、降低成本、确保生产质量。
车间物料管理程序

车间物料管理程序一、引言车间物料管理是指对车间所需的各种物料进行有效的计划、采购、入库、出库、盘点等管理工作,以确保生产过程的顺利进行和物料的充足供应。
本文将详细介绍车间物料管理程序的标准格式。
二、程序概述车间物料管理程序包括以下几个主要步骤:物料需求计划、物料采购、物料入库、物料出库、物料盘点。
三、物料需求计划1. 车间物料管理人员根据生产计划和库存情况,制定物料需求计划。
2. 物料需求计划包括物料名称、规格、数量、需求日期等信息。
3. 物料需求计划需经相关部门审批后才干执行。
四、物料采购1. 车间物料管理人员根据物料需求计划制定物料采购计划。
2. 物料采购计划包括物料名称、规格、数量、供应商、采购日期等信息。
3. 车间物料管理人员与供应商进行沟通,确定物料价格、交货期等细节。
4. 车间物料管理人员将物料采购计划提交给采购部门,并监督采购进程。
五、物料入库1. 采购部门根据物料采购计划进行物料采购,并将采购的物料送至车间。
2. 车间物料管理人员对入库物料进行验收,包括检查物料的数量、质量、规格等是否符合要求。
3. 车间物料管理人员将验收合格的物料进行入库登记,包括物料名称、规格、数量、供应商、入库日期等信息。
4. 入库登记完成后,车间物料管理人员将物料存放在指定的库位,并进行标识。
六、物料出库1. 车间生产人员根据生产计划提出物料出库申请。
2. 车间物料管理人员根据物料出库申请进行物料出库操作。
3. 物料出库操作包括检查出库物料的数量、规格等是否符合要求,并记录出库信息,包括物料名称、规格、数量、领用人、出库日期等。
4. 车间物料管理人员将出库的物料从库位中取出,并交给领用人。
七、物料盘点1. 定期进行物料盘点,以确保库存数据的准确性。
2. 车间物料管理人员根据库存记录逐一核对库存物料的数量和规格。
3. 物料盘点结果与库存记录进行比对,发现差异时进行调整,并记录调整原因。
八、总结车间物料管理程序的标准格式包括物料需求计划、物料采购、物料入库、物料出库和物料盘点等步骤。
车间物料管理程序

车间物料管理程序一、背景介绍车间物料管理是指对车间内的各类物料进行全面管理和控制,确保物料的准确性、及时性和有效性,以提高生产效率和降低成本。
本文将介绍车间物料管理程序的标准格式,包括物料采购、入库、出库、库存管理和盘点等环节。
二、物料采购1. 采购需求确认根据车间生产计划和物料需求计划,确认所需物料的种类、规格、数量和交货时间等信息。
2. 供应商选择与评估根据公司的供应商评估标准,选择合适的供应商,并与供应商签订合同或协议。
3. 采购订单发起根据物料需求确认结果,向供应商发起采购订单,并确保订单的准确性和完整性。
4. 采购订单跟踪定期与供应商沟通,了解采购订单的进展情况,并及时解决可能出现的问题。
5. 采购到货验收对采购到货的物料进行验收,确保物料的质量和数量与采购订单一致,并及时处理异常情况。
三、物料入库1. 入库登记对验收合格的物料进行入库登记,记录物料的种类、规格、数量、供应商信息等。
2. 物料标识与分类对入库的物料进行标识,并按照物料分类进行归档,便于后续的查找和管理。
3. 入库质量检验针对特殊物料或关键物料,进行入库质量检验,确保物料的质量符合要求。
四、物料出库1. 出库申请根据车间生产计划和物料需求,车间人员向物料管理部门提出出库申请。
2. 出库审核物料管理部门对出库申请进行审核,确保出库申请的合理性和准确性。
3. 出库操作物料管理人员按照出库申请,将物料从库存中取出,并进行相应的记录和标识。
五、库存管理1. 库存监控定期对库存进行盘点和监控,及时发现和处理库存异常情况,如过多积压或短缺等。
2. 库存调整根据实际需要,对库存进行调整,如报废、退货、补充等。
3. 库存报表定期生成库存报表,包括库存总量、各类物料的库存情况、库存周转率等指标,为管理决策提供依据。
六、物料盘点1. 盘点计划制定制定物料盘点计划,包括盘点时间、盘点范围、盘点方式等。
2. 盘点操作物料管理人员按照盘点计划,对库存进行实际盘点,记录盘点结果。
车间物料管理程序

车间物料管理程序一、背景介绍车间物料管理是指对车间内各种物料进行全面管理和控制,确保物料的准时供应、准确使用和有效管理,以提高生产效率和降低成本。
本文将介绍车间物料管理程序的标准格式,包括物料采购、入库、出库、库存管理等方面的内容。
二、物料采购流程1. 需求确认:车间根据生产计划和库存情况,确认所需物料的种类、数量和质量要求。
2. 供应商选择:车间根据物料的特性和质量要求,选择合适的供应商,并与供应商进行谈判和签订采购合同。
3. 采购定单发起:车间根据需求确认的物料信息,向供应商发起采购定单,并提供相关的规格和数量要求。
4. 供应商确认:供应商收到采购定单后,确认物料的供应能力和交货期,并向车间确认定单。
5. 物料采购:供应商按照采购定单的要求,采购物料,并确保物料的质量和数量符合车间的要求。
6. 物料验收:车间对收到的物料进行验收,包括检查物料的外观、尺寸、质量等,并与采购定单进行对照,确保物料的准确性和完整性。
三、物料入库流程1. 入库通知:车间根据物料的采购情况,向仓库发出入库通知,包括物料的名称、规格、数量和入库时间等信息。
2. 仓库接收:仓库根据入库通知,接收物料,并进行验收,包括检查物料的数量、质量和完整性。
3. 入库登记:仓库对接收到的物料进行入库登记,包括记录物料的名称、规格、数量、供应商信息等,并生成入库单据。
4. 物料上架:仓库将物料按照规定的存放位置进行上架,并进行标识,确保物料的易查找和管理。
5. 入库通知确认:车间收到仓库发出的入库通知后,进行确认,并更新车间物料库存信息。
四、物料出库流程1. 需求确认:车间根据生产计划和物料需求,确认所需物料的种类、数量和使用时间。
2. 领料申请:车间向仓库发起领料申请,包括物料的名称、规格、数量和使用目的等信息。
3. 领料审批:仓库根据领料申请,进行审批,并确认物料的可用性和库存情况。
4. 物料出库:仓库根据领料申请,将物料从库存中出库,并记录出库信息,包括物料的名称、规格、数量、领料人等。
- 1、下载文档前请自行甄别文档内容的完整性,平台不提供额外的编辑、内容补充、找答案等附加服务。
- 2、"仅部分预览"的文档,不可在线预览部分如存在完整性等问题,可反馈申请退款(可完整预览的文档不适用该条件!)。
- 3、如文档侵犯您的权益,请联系客服反馈,我们会尽快为您处理(人工客服工作时间:9:00-18:30)。
生产物料管理流程
目的:
规范物料运作管理,提高生产效率,简化物料流程,及时了解物料信息.
使用范围:
生产管理部。
1、领料流程:
1.1 接PMC计划部生产任务单、领料单。
1.2 核对生产任务号(制造单号)与所下单生产线是否一致,如不一致及时反馈PMC 计划部重新下单。
1.3 接到领料单2小时后,到PMC部材料仓领取套料。
1.4 领料原则是每个物料员针对自己所领的每一个物料必须与套料单上的物料编码相
一致,若不一致应向PMC仓管员及时反馈,确认无误后再对每种物料逐一点数,并且在套料单领料一栏所填写的领料实数后签名,如果发现套料单所填写物料数量与实物数量不相否时,及时向仓管员反馈补齐数量,套料单据不得涂改。
1.5 物料员领料后,核对套料单上所有物料是否领齐,如全部领齐仓管员、物料员双
方确认后在领料单上签名,没有领齐的单据物料员只在领料数量后签名,此领料单一式三份,生产部黄联、PMC部蓝联、财务部白联各执一联,留底存根。
1.6 领料进车间后,物料员须将物料按结构、电子料的种类分别整齐摆放在货架上,
大件物料(塑料类)放在地面上摆放整齐,对试用、超差、挑选等的物料用红色油性笔做特别标识,且及时填写物料收发本贴在物料堆放处,最后按生产制造单号将各物料套料欠记入自己欠料账本,以便于及时跟催套料欠物料。
1.7 物料员必须按生产线将领料单据整理好,按规定区域摆放好,未经统计员允许物
料员不得私自拿走单据,只允许查看领料数量及填写第二次领料数量,统计员录入电子档后将所有领齐单据按生产线别整理好存入文本档,未领齐单据整理后按规定区域再摆放好。
1.8 备好物料准备生产,发料时应注意试用、超差、挑选加工、异常的物料,必须通
知线长,否则绩效考核处理。
2、退料流程:
2.1 生产过程中,将不良品物料挑选出,做上标识放在不良品区。
2.2 将不良品给质管部巡线技术员确认是否可以接受,若能接受则在不良标识上写
上“OK”表示已确认;若不能接受,放回不良品区做好标识,下班后统一交给生产线退料员,退料员确认数量且记录退料数后退到物料房相应生产线。
2.3 生产线对组装好的半成品进行检验,将不良品挑出贴上箭头纸指向不良点并在
箭头纸上写明不良现象,放在吸塑盒中堆放好,及时通知生产线小组长让修理进行维修,维修好的下拉,无法进行维修的按原材料拆开后整理好退料。
2.4 物料员将生产线当天的坏料全部整理好,按来料不良与生产不良分开摆放,打
退料单退料,打退料单时注意贵重料和装配料区分开进行打单。
2.5 将来料不良品及退料单送IQC检验。
若不良品中有能接受品,IQC在此物料上贴
上合格品,此物料退回生产线重新找质管部技术员确认下拉;若确认为来料不良的按来料不良流程退料(物料员—生产线长—装配料巡检确认/电子器件PE确认—IQC确认—物控—仓管员)。
2.6 将生产不良品及退料单送生产技术部确认,若不良品中有能接受品,将质管部
技术员找来一起确认是否可以接受,若能接受贴上标识“OK”生产,不能接受,PE签名按生产不良退料流程退料(物料员—生产线长—PE工程师—生产主管—物控—仓管员)。
2.7 物料员将已确认的不良品及退料单全部送到PMC仓库找仓管员进行退料,退料
完毕,PMC仓管员在退料单上签名确认。
2.8 凭退料单在PMC仓库领回相等数量的良品(按领料流程处理)。
3、借料流程:
3.1 生产过程中物料来料品质异常,设备夹具进生异常损坏物料及出货的紧急都需要
借料保证生产。
3.2 物料员填写借料单,填写好物编、数量、原因、归还日期等,送相关负责人签名
(物料员—生产线长—生产主管—物控—仓管员—借料编号)。
3.3 仓管员接到借条发料给物料员。
3.4 物料员领料后发料到生产线进行投入生产。
3.5 物料员收集相应物料,整理后准备还料、冲借条。
4、盘点流程:
4.1 财务部发出盘点通知。
4.2 集中相关人员传达盘点的注意事项及要求。
4.3 生产线尽最大的努力追回外借的物料或机头等。
4.4 追PMC仓库补回所欠的料,技术部待处理的方案,质管部待处理的结果,尽快
将生产线上的状态机清理完毕,包装入库,减轻盘点任务。
4.5 盘点时停止生产,将所有的物料全部收集,按种类、良品、不良品的状态区分摆
放,同时每一个制造单的物料单独放在一堆,清点每一种物料数量,同时贴上标识卡标识清楚物料编码、数量、制造单号、状态等。
4.6 统计领入、借入、退料未补数、套料欠数量、入库数算出每一种物料账存数。
4.7 按制造单号打印盘点清册。
4.8 核对实物是否与账存数一致。
4.9 若一致,填写初盘数。
4.10 财务进行复盘,填写复盘数签名确认,生产部与财务部各执一联留底。
4.11 财务根据盘点清册,做出盘点赢与亏分析报告,发生产部。
4.12 生产部门根据报告做出措施,落实到责任人。
5、支持文件:
5.1《物料标识卡》;
5.2《物资收发卡》;
5.3《领料单》;
5.4《借料单》;
5.5《入库单》;
5.6《盘点清册》;
5.7《退料单》;
拟制:审核:批准:
领、退料流程
借料流程
盘点流程
精选word范本!
. 精选word范本!。