基于PLC的原煤采样控制系统
基于PLC控制的燃煤全自动采样装置故障分析与优化

基于 PLC 控制的燃煤全自动采样装置故障分析与优化摘要:当前,PLC程序控制被广泛应用于工业领域,并为检修人员的故障分析与排查工作提供了较大便利。
某电厂燃料输煤系统中的全自动采样装置为德博利恩公司产品,使用了S7-200系列PLC进行控制,本文主要结合该电厂采样装置样品收集器中卸料阀发生故障未能及时停机与报警的案例,对基于PLC控制的输煤采样电气设备的故障分析、处理以及程序的完善过程进行阐述,可供使用同类设备的火电企业参考。
关键词:输煤系统全自动采样装置PLC设备故障引言大多数火力发电厂燃煤成本都占企业经营成本的70%以上,燃煤是否质价相符一直是火力发电企业关注的重点。
而入厂煤的采样装置一旦发生故障,轻则使得船舶接卸过程中的燃煤无法正常采集,导致卸煤过程中断,延长船舶接卸时间,重则发生采集样品混合,导致燃煤化验结果失准,给企业带来经济损失,所以我们燃料生产检修人员在日常工作中首先要保证的就是采制样装置的可靠投运。
下面,本人将结合某电厂新投运的全自动采样装置,在煤样正常采集时发生的煤样装罐暂存至集中卸料过程中,卸料阀发生故障,但设备未停机且无报警输出的故障案例,进行分析与阐述。
1.设备简介某电厂全自动采样装置属于输煤皮带中部采样设备,由触摸屏结合西门子S7-200系列PLC进行控制,分为手动与自动控制模式两种,其工作流程大致为:初级采样头采样、破碎机碎煤、缩分得到样品、样品装罐暂存、按采集批次输送至制样机进行化验样品制备。
发生故障的样品收集器组成如(图1)所示,共由6个集样罐组成,入料口与放料口位置相距180°,卸料阀位于放料口上部,通过气动执行装置下压带动集样罐仓门打开,气动执行装置上部设有一原位检测传感器,负责检测气动执行装置是否缩回到位。
样品收集工作流程:在采样开始前,空样品罐转入进料口下方准备接料,终端控制系统根据输煤批次自动生成采样编码写入对应集样罐。
开始采集后,输煤皮带上采集的煤样从入料口进入,储存在集样罐中,采集到设定值14个点位后,集样罐在中部选择电机的带动下旋转,由空余无采集点数的集样罐继续进行样品收集工作。
基于plc的输煤控制系统
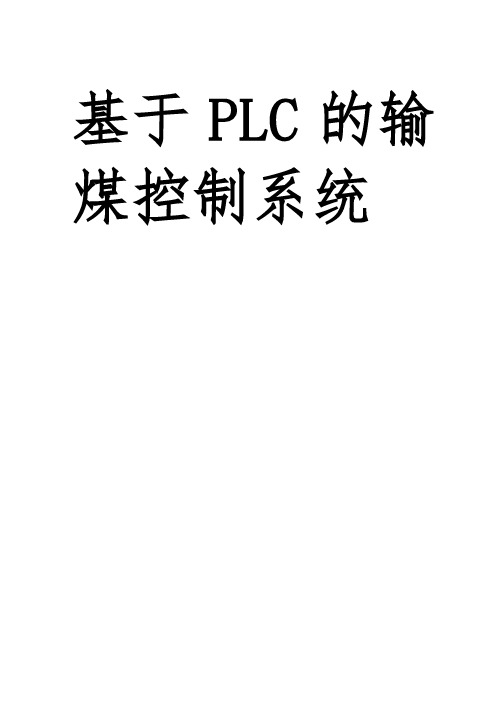
这种方式是通过安装在带式输送机侧的机旁操作箱来控制带式输送机的运行停止,这种工作方式既可以通过手动开关控制所有带式输送机按照预先规定好的顺序联动,也可以只让某条带式输送机单独运动,以检测单条带式输送机是否有故障。
1.2
传统的发电厂输煤系统是一种基于继电接触器和人工手动方式的半自动化系统,现场环境十分恶劣,工人们通过开动承前启后的皮带运输机及取煤机向锅炉前的储煤仓输煤,经常有皮带跑偏、皮带撕裂和落煤管堵塞等。但对发电厂而言,蒸汽工序的炉膛是不允许断煤的:于是,蒸汽机前通常有一个很大的储煤仓。输煤系统工作时尽量将煤装满储煤仓,不仅可以保证输煤系统故障时,工人们有足够的时间排除故障,也可以保证输煤设备有充分的时间检修。随着发电厂规模的迅速扩大,输煤系统的作用日益突出,而传统的输煤系统己无法满足发电厂的需要,因此需要对传统的发电厂输煤系统进行改造。
利用PLC可以把整条运输线集中到一个控制系统中,可以方便地实现机旁连锁就地控制、中控室PLC集中连锁控制等多种控制方式,在运输线的终端和火电厂控制室都可以对运输线的各种保护传感器等进行有效地监测。以某火电厂为例,介绍系统的结构组成、控制系统具备的功能等。
关键词输煤,PLC,带式输送机,
Abstract1.3.2来自火力发电厂的输煤程控系统,它和相应的发电机组配套承担着发电厂的燃煤输送任务,是电厂内工作环境差,劳动强度大的一个系统,有效地提高输煤系统的自动控制和管理水平是国内众多火电厂急待解决的问题。煤是火电厂发电的重要燃料,燃煤合理充分的利用直接决定了电厂的发电量。因此,在发电过程中,高效率的、稳定的、合理的运输,堆取,配煤成为电厂控制系统中十分重要的部分。
正如前面所说,大型火电厂燃料输煤系统设备种类繁多,分布较为分散一般都分布在几公里范围内,由于其实时性要求不高,不是24小时都需要运行,所以其在电厂的被重视程度往往不如主机系统,导致其生产管理及设备自动化水平相对滞后,而不得不使用较多的人力物力,有的电厂甚至出现燃料运行人员超过主机运行人员的现象。
基于PLC的输煤系统自动化控制设计原理

基于PLC的输煤系统自动化控制设计原理随着现代工业的发展,自动化控制系统在各个领域得到了广泛的应用。
在输煤系统中,自动化控制技术的应用不仅可以提高生产效率,降低人工成本,还能保障生产安全。
本文将介绍基于PLC的输煤系统自动化控制设计原理。
一、PLC概述PLC(ProgrammableLogicController,可编程逻辑控制器)是一种广泛应用于工业自动化领域的数字运算控制器。
它通过编程存储器执行用户编写的程序,对输入/输出信号进行逻辑、定时、计数和算术运算等处理,并通过数字或模拟输出信号控制外部设备的工作。
PLC 具有可靠性高、抗干扰能力强、易于扩展和维护等优点。
二、输煤系统简介输煤系统主要用于将煤炭从原料仓输送到锅炉,主要包括原煤仓、输送带、破碎机、筛选机、煤仓等设备。
输煤系统的稳定运行对锅炉的燃烧效果和生产安全具有重要意义。
三、基于PLC的输煤系统自动化控制设计原理1.输入/输出信号采集PLC需要实时采集输煤系统中的各种输入/输出信号,包括设备运行状态、故障报警、物料浓度、输送带速度等。
这些信号通过传感器、开关等设备传输给PLC,为后续控制提供数据基础。
2.控制逻辑设计根据输煤系统的工艺要求,设计合适的控制逻辑。
以输送带为例,当原煤仓中的煤炭达到一定高度时,PLC会输出信号控制输送带启动,将煤炭输送到煤仓。
同时,PLC会监测输送带运行状态,如发生故障,立即输出报警信号并停止输送带运行,确保生产安全。
3.定时/计数功能PLC具有定时和计数功能,可用于输煤系统中的设备运行时间、物料计数等。
例如,PLC可以监测破碎机的运行时间,当达到设定的运行时间后,自动启动筛选机,实现煤炭的筛选作业。
4.模拟量处理输煤系统中涉及到的物料浓度、输送带速度等参数为模拟量信号,PLC可以通过模拟量输入模块进行采集,并进行相应的处理和控制。
例如,PLC可以根据物料浓度实时调整输送带的速度,保证煤炭的正常输送。
5.通信功能现代PLC具有强大的通信功能,可用于实现输煤系统各设备之间的数据交换和远程监控。
基于PLC技术的煤层气井生产监控系统智能排采功能的设计与实现

基于PLC技术的煤层气井生产监控系统智能排采功能的设计与实现1. 引言1.1 背景介绍在当今社会,煤层气资源的开发利用已成为国家能源战略的重要组成部分。
由于传统的煤层气井生产监控系统存在监控数据不准确、排采操作不及时等问题,导致煤层气资源的开采效率和安全性受到极大影响。
为解决这一问题,基于PLC技术的煤层气井生产监控系统智能排采功能的设计与实现显得尤为重要。
随着科技的不断进步,PLC技术在工业自动化领域发挥着越来越重要的作用。
其稳定性、可靠性和灵活性使其成为煤层气井生产监控系统的理想选择。
通过引入智能排采算法,可以实现对煤层气井生产过程的自动化监控和优化调控,提高煤层气资源的开采效率和安全性。
本文将深入探讨基于PLC技术的煤层气井生产监控系统智能排采功能的设计与实现,旨在为煤层气资源的高效开发提供技术支持和科学依据。
通过系统架构设计、功能模块设计、智能排采算法设计等方面的研究,将为煤层气井生产监控系统的升级改造和智能化发展提供重要参考。
1.2 研究目的本研究的目的是设计与实现基于PLC技术的煤层气井生产监控系统智能排采功能,旨在提高煤层气井的生产效率和安全性。
通过对煤层气井生产过程进行监控和控制,实现对煤层气井排采过程的智能化管理。
具体目的包括:一是优化煤层气井的生产操作流程,提高煤层气井的产量和采收率;二是提高煤层气井的安全性和稳定性,减少煤层气井的事故风险;三是降低煤层气开采成本,提高经济效益;四是为煤层气井的远程监控和智能化管理打下技术基础。
通过本研究,将为煤层气井生产监控系统的智能排采功能的设计与实现提供理论和实践参考,为我国煤层气资源的高效开发利用做出贡献。
1.3 意义和价值煤层气井生产监控系统是煤层气田开发中的关键技术之一,可以实现对井下生产参数的实时监测、数据采集和分析,为生产管理提供科学依据。
智能排采功能作为煤层气井生产监控系统的重要组成部分,能够根据井下数据实时调整采气参数,提高煤层气井生产效率和安全性。
基于PLC技术的煤层气井生产监控系统智能排采功能的设计与实现

基于PLC技术的煤层气井生产监控系统智能排采功能的设计与实现摘要:随着煤层气的开发利用,煤层气井生产监控系统的发展日益受到重视。
本文基于PLC技术,设计了一种智能排采功能,并实现了在煤层气井生产监控系统中的应用。
通过对智能排采功能的相关原理和设计方法的分析,以及实际案例的应用验证,表明了该设计与实现的可行性和有效性。
关键词:煤层气井;生产监控系统;智能排采;PLC技术1.引言煤层气是一种被广泛开发利用的可再生能源,其开发利用对于我国能源结构的调整和碳排放的减少具有重要意义。
随着煤层气资源的不断开发,煤层气井生产监控系统成为煤层气开发利用过程中的重要组成部分。
煤层气井生产监控系统能够实时监测井下各种参数,对煤层气开采工艺进行管控,提高生产效率,降低安全风险。
在煤层气井生产监控系统中,智能排采是一个重要的功能,能够实现对井下排采设备的自动化控制和智能化管理,为煤层气开采提供技术支持和保障。
2.煤层气井生产监控系统中的智能排采功能设计2.1 智能排采功能原理智能排采功能是指利用先进的控制技术,自动控制和调节井下排采设备的工作状态,保证排采过程的高效稳定进行。
在煤层气井生产监控系统中,智能排采功能可以根据井下各种传感器的实时数据,进行智能化决策和控制,实现对排采设备的自动化管理。
通过智能排采功能,可以有效提高生产效率,降低运行成本,保障生产安全。
2.2 智能排采功能设计方法在煤层气井生产监控系统中,智能排采功能的设计方法是基于PLC技术的。
PLC (Programmable Logic Controller,可编程逻辑控制器)是一种专门用于工业自动化控制的计算机,具有可编程性、稳定性和灵活性等特点。
利用PLC技术,可以实现对排采设备的精准控制和智能化管理。
智能排采功能的设计方法包括传感器数据采集、数据处理和控制指令输出等环节,其中传感器数据采集是指对井下各种参数进行实时监测和采集;数据处理是指对采集到的数据进行处理和分析,形成决策依据;控制指令输出是指根据数据处理结果,对排采设备进行控制指令的输出,实现自动化控制。
基于PLC的选煤厂集控系统的设计与应用

赵伟①Z a i黄文娟②Hu n nu n; h oWe; a gWej a 陈玉 良①C e l n h nYui g a
( ①河北理工大学轻工学院, 唐山 0 30 ; 6 09②唐山职业技术学院, 唐山 0 30 ) 604 ( )oeeo L h Id sy H bi o tcnc n esyTnsa 60 9C ia ( Cl g i tnut , eeP leh iU i rt,aghn0 30 ,hn ;  ̄ l f g r y v i @Tnsa oaoa adT cn aC lg ,aghn030 , h a ag nV ctnl n eh i l oeeTnsa 60 4 C i ) h i c l n
摘 要 : 绍 了基 于 P C的选 煤生 产 集控 系统组 成 结构 、 介 L 系统 功 能及 实现 方法 , 讨论 了 P C在 该 系统 中 的应 用、 L 各控 制模 块 的功 能 以及通 信 网络等部分的设计方法。实际应用表明该系统在节能降耗 、 安全生产等方面取得了良好的效果。
Absr c :Th o o ig u cin a d raiain meh d fc nr l e o to y t m n c a r p rto ln s d o LC a e ito u e n ta t e c mp sn ,f n t n e l to t o so e tai d c nr ls se i o lp e aain pa tbae n P r nr d c d i o z z t i p r hspa e .Th p lc to LC,f n t n o to d l n sg t o so hec mmu iain newok ae ds u s d.I h sb e h wn t t ea p iain o P f u ci so c nr lmo esa d dein meh d ft o o f nc t t r r ic s e t a e n s o ha o t eg o e ut a ebe n o t ie n te e e g a ig a d s f r d to . h o d r s lsh v e b an d i h n r ys vn n ae p o ucin
基于PLC的选煤厂控制系统的应用分析

基于PLC的选煤厂控制系统的应用分析摘要:随着社会经济的发展,选煤厂自动化水平也在不断提高,可编程控制在选煤厂的广泛应用,给我国煤炭企业工作人员带来了福音。
本文主要从选煤厂集中控制新技术切入,着重分析了基于PLC的选煤厂控制系统的具体应用情况,希望能够对相关工作人员起到借鉴与参考的作用。
关键词:选煤厂;PLC;控制系统;应用前言近年来,国内外精煤市场对于精煤的需求日益提高,在这样的背景下,选煤厂为了提高精煤产量,需要不断革新自身选煤技术,才能够充分满足日益增长的市场需求。
选煤厂实现集中控制需要遵循三项基本原则,即在保证选煤质量的基础上提升选煤效率、在保证选煤质量和选煤效率的基础上降低选煤成本、在保证选煤质量、效率、成本的基础上提高系统运行的安全性与连续性。
基于PLC的选煤厂控制系统的应用,取得了极为显著的成效,不仅提高了选煤厂的选煤质量,而且还在很大程度上提升了选煤效率,保证了选煤系统的连续性与安全性,具有极高的推广价值。
一、概述(一)概念PLC又称PC,是可编程序控制器的简称,其在结合计算机技术与继电器逻辑控制技术的基础上,进行合理的改进和发展,最终成为新一代工业控制器。
可编程序控制器具有可靠性高、适应能力强、设备齐全及编程简单的特征,被广泛应用于我国各行业和领域。
选煤厂采用PLC对全厂设备进行控制,是实现选煤厂计算机集中控制的重要条件。
(二)工艺系统我选煤厂年处理能力约为3100万吨,控制系统主要包括产品装车系统、原煤系统及重介系统等。
二、系统配置及功能设置(一)系统配置选煤厂控制系统主要是由PLC、模拟屏、控制台和电源柜共同组成,其中,PLC作为选煤厂集中控制的核心部分,采用了美国罗克韦尔公司生产的AB型PLC,Logix5000系列。
ControlLogix系统与传统的PLC系统不同,具备更为先进的系统构建理念,其硬件性能高且软件功能强大,能实现多种性质的控制任务,属于复杂多任务控制平台。
PLC在选煤厂集控系统改造中的应用

PLC在选煤厂集控系统改造中的应用随着工业自动化技术的不断发展,PLC(可编程逻辑控制器)已经成为各种工业控制系统中最重要的组成部分之一。
在煤炭行业中,选煤厂是一个重要的环节,其集控系统需要不断更新改造以适应市场需求和技术发展。
本文将重点介绍PLC在选煤厂集控系统改造中的应用。
一、选煤厂集控系统的基本组成选煤厂是煤炭深加工的重要环节,主要任务是从原始煤炭中分离出质量更好的洗煤产品。
传统的选煤厂集控系统是由人工操作和一些简单的控制设备组成,其控制效率和精度有限。
随着自动化技术的不断进步,现代选煤厂集控系统一般由PLC控制器、人机界面、传感器、执行机构等多个部分组成,通过这些部分的紧密配合,实现对选煤过程的全方位监控和控制。
1. 数据采集和传输在选煤厂的集控系统中,各种传感器和执行机构都需要与PLC进行数据交换,PLC作为控制中心,负责采集和处理各种传感器传来的数据,并根据预设的算法和逻辑进行控制指令的生成。
通过PLC的串口通信功能,可以方便地与其他设备进行数据交换和传输,确保各个部件之间的协调和一致性。
2. 控制逻辑的编程3. 人机界面的设计PLC系统中的人机界面是与操作人员进行交互的重要部分,通过人机界面,操作人员可以直观地看到选煤过程中各个部件的状态和参数,并且可以进行操作指令的下达和系统的监控。
PLC系统一般与触摸屏等设备配合使用,通过触摸屏,操作人员可以方便地对系统进行各种操作,大大提高了操作的便捷性和效率。
4. 系统的故障检测和诊断在选煤过程中,各种设备和传感器可能会出现故障或者异常,这些故障情况需要及时检测和诊断,以避免对选煤过程的影响。
PLC系统可以通过实时监测各个部件的状态和参数,及时发现故障情况,并通过程序设定的逻辑进行相应的处理和报警,保证选煤过程的稳定和安全。
5. 数据记录和报表生成PLC系统可以对选煤过程中的各种数据进行记录和存储,通过数据记录功能,可以方便地进行数据的分析和统计,为生产管理和质量控制提供重要的数据支持。
PLC在选煤厂集中控制系统的应用

PLC在选煤厂集中控制系统的应用随着煤矿行业的不断发展,选煤技术也在不断的更新,自动化水平的不断提高,可编程序控制器在选煤行业中的应用日渐增多。
本文主要从PLC控制系统的工艺流程及其控制结构,分析了PLC程序设计的可行性。
阐述了控制系统的设备配置、功能设置和选煤厂对PLC的干扰以及处理措施,对选煤厂集中控制系统的设计具有一定的借鉴作用。
标签:集中控制PLC 功能特点编程软件通讯干扰0 引言众所周知,随着科学技术的不断发展,可编程序控制器(简称PLC或PC)逐渐走向市场,逐渐被广大企业所接受和应用,PLC是结合了继电逻辑控制与IT 技术,它是一种新型的工业控制器,PLC技术具有很多优点,比如可靠性高,灵活性好,编程简单实用,而且硬件配备齐全等,当前情况下,目前,可编程序控制器已经被大多数工业控制企业所应用,并且逐渐向其他领域发展。
选煤厂采用以PLC技术为核心,从而实现对整个企业的生产设备进行有效集中控制,这是选煤厂能够实现计算机自动化控制的前提和基础,与此同时,还能够让我们实现对新式集中控制系统的进一步研究和探讨。
1 工艺系统选煤厂的组成工艺系统选煤厂由原煤系统、重介系统、浮选系统、产品装车系统四部分组成。
其生产系统规模大,设备多,工艺流程复杂。
2 配置方案功能设置2.1 系统配置该PLC控制系统只要由以下几个部分组成,即可编程序控制器PLC、控制台、以及模拟屏和电源等部分。
与此同时,对该PLC控制器要配置六台具有大屏幕的彩色显示器,从而这样可以组成工控机的监控系统,因此这样可以对选煤厂的全体设备实现集中控制。
2.2 功能设置根据工艺特点,设计的控制系统具有顺煤流停车、逆煤流起车的顺序控制功能,部分过程控制功能,设备运行状态的监视、故障报警、急停,且能保证在发生故障的情况下不堆煤、不堵塞。
这样可以对生产系统的相关工艺流程实现实时的、全面的、直观的监视各生产系统的设备运行情况。
上位机接受操作人员发出的控制指令,通过PLC实施对选煤厂各环节的生产设备进行控制。
基于PLC的选煤厂集控系统设计与功能分析

基于 P L C 的选 煤 厂 集控 系 统设 计 与功能 分析
纪洪 准 刘 倩
( 平 顶 山中选 自控 系统有 限公 司 , 河 南 平 顶山 4 6 7 0 0 0 )
摘
要: 首先 指 出了选煤 厂生 产工 艺对 集控 的要求 , 然 后重 点研究 了基 于 P L C的集 控系统 相关设 计 , 最 后介 绍 了集控 系统 的功 能 。生
统 一。
4 结 语
随着社会的发展和科技 的进 步 , 人们 了解了越来越 多的绿 色技术相关知识 , 越来越 重视节约 能源以及保护环 境, 因此 , 更 加注重将绿色技术应用 到冶金机械 的设 计 、 制造 和生产 中。可
冶金机械在工作一定时间后要进行保养 与维修 , 这必然 要 耗费大量的人力 、 物力 和财力 。而且 大部 分冶金企 业对机械 的
3 . 5 提 高故 障 诊 断技 术 水 平
2 . 1 P L C 系统 检 测 控 制 的 重 点
( 1 )原煤储 煤仓及 各产 品仓 的煤 位。 ( 2 )设 备 的运行 信 号、 停止信号 、 集控 信号 以及就地信 号 。系统可 实时 收集生 产 不污染 环境 的前提下 , 充分体 现人一机一环境 系统的真正 和谐
冶金, 2 0 1 0 ( 3 )
就 白白浪费 了资源 ; 再加 上冶金机械设备 的性能要经过 一定的 磨合期后才能达到最好的状态[ 2 ] , 所以有必要加强对设备检测和
诊 断技 术 的研 究 , 并 在设 计 中加 以 体 现 , 使 得 相 关 人 员 在 维 修 之
前就能了解到设备的运行状态, 从 而将维修成本降到最低 。
基于plc的选煤生产连续控制

基于plc的选煤生产连续控制摘要:本文主要诠释了PLC优势,并从在选煤生产当中PLC控制方式与基本原理、生产连续性控制系统设计、生产连续性控制系统的部件选型方面入手,对plc选煤生产的连续控制,开展了深度地分析与研究。
从而能够充分发挥PLC的功能优势,进行选煤生产的连续控制系统优化设计,以更好地实现选煤生产综合化的连续控制,为我国煤矿事业的长期发展提供保障。
关键词:plc;选煤;生产;连续控制;前言Plc(Programmable Logic Controller),中文全称为PLC的控制系统或可编程的逻辑性控制器,是工业控制最为核心的部分。
通过Plc在煤矿的选煤生产当中有效性的应用,大大提升了选煤生产的自动化水平,为煤矿业提供了发展性动力。
为了能够更加充分地发挥Plc各项功能优势,就对Plc进行更为深度的研究,并对Plc控制系统下选煤生产的连续性控制系统,进行科学地、合理地优化设计,以将Plc各项功能优势均充分运用至选煤生产当中,以将选煤生产的自动化水平提升到新的高度,为我国煤矿事业的可持续性发展奠定重要基础。
1、PLC优势PLC,它可针对于不同的机械化生产过程,运用模拟化输入/出、数字等来实施系统控制。
它主要是由电源、存储器、中央的处理单元、输入/输出的接口电路、通信模块、功能模块等所组成。
中央的处理单元,为PLC控制系统核心,主要负责检查及诊断警戒的定时器、存储器、电源等系统程序实际运行状态。
煤矿选煤实际生产期间,PLC所组成的系统编程与应用极具灵活性,且极易扩展,可更好地适应较为恶劣的煤矿工作环境,可靠性与抗干扰性均较强。
在一定程度上,PLC它主要以开关量控制为主,还可在生产连续期间的PID回路性控制组成极具复杂性的一个控制系统。
基于语言编程仅需利用简单的语句表与逻辑图等即可完成编程,程序修改期间无需更改方案。
因而,PLC更易于现场调试,可让煤矿实际生产期间实现综合的自动化控制。
2、在选煤生产当中PLC控制方式与基本原理2.1 PLC控制方式PLC,它在煤矿实际选煤生产期间主要控制方式分为分布式控制与集中式控制。
PLC电气控制系统在煤炭开采中的应用分析

PLC电气控制系统在煤炭开采中的应用分析随着科技的飞速发展,煤炭开采行业也迎来了前所未有的技术革新。
其中,PLC电气控制系统作为一种新型的自动化控制技术,正逐渐在煤炭开采领域崭露头角。
本文将从多个角度对PLC 电气控制系统在煤炭开采中的应用进行分析,以期为煤炭行业的可持续发展提供有益的参考。
首先,PLC电气控制系统在煤炭开采中的应用,如同给矿工们装上了一双“千里眼”。
传统的煤炭开采方式往往依赖于人工观察和经验判断,不仅效率低下,而且存在极大的安全隐患。
而PLC电气控制系统通过实时监测和数据分析,能够精准掌握矿井内的各项参数,如温度、湿度、瓦斯浓度等,从而确保矿工们在一个相对安全的环境中进行作业。
这种“千里眼”般的功能,无疑为煤炭开采提供了更为可靠的保障。
其次,PLC电气控制系统在煤炭开采中的应用,犹如给矿井装上了一颗“智能心脏”。
PLC系统具有强大的数据处理能力和灵活的控制策略,能够根据实际需求自动调整设备的运行状态,实现煤矿生产的智能化和自动化。
这不仅大大提高了煤炭开采的效率,还降低了能耗和成本,为企业创造了更多的经济效益。
这颗“智能心脏”的跳动,为煤炭行业的未来发展注入了新的活力。
然而,我们也必须看到PLC电气控制系统在煤炭开采中应用所面临的挑战。
一方面,煤炭开采环境的复杂性和多变性要求PLC系统具备更高的稳定性和可靠性;另一方面,随着煤炭资源的逐渐枯竭,如何进一步提高PLC系统的能效比和适应性,成为了亟待解决的问题。
这些问题的解决,需要我们在技术创新和人才培养上下更大的功夫。
此外,我们还应该关注PLC电气控制系统在煤炭开采中的环保效益。
传统的煤炭开采方式往往伴随着大量的废弃物排放和环境污染问题。
而PLC系统的引入,可以通过精确控制和优化工艺流程,减少废弃物的产生和排放,降低对环境的影响。
这种“绿色开采”的理念,正是煤炭行业转型升级的重要方向。
综上所述,PLC电气控制系统在煤炭开采中的应用具有显著的优势和潜力。
基于PLC技术的采煤机控制系统分析

基于PLC技术的采煤机控制系统分析作者:张瑞阳来源:《科技与创新》 2015年第22期张瑞阳(吉林省机械装备制造有限责任公司,吉林辽源 136200)摘要:PLC 技术的控制能力比较好,可以快速适应采煤机的控制需求,提供可靠的技术控制,保障采煤机控制的准确性。
重点分析了PLC 技术在采煤机控制系统中的应用。
关键词:PLC 技术;采煤机;控制系统;程序设计中图分类号:TD421.6 文献标识码:A DOI:10.15913/ki.kjycx.2015.22.154文章编号:2095-6835(2015)22-0154-01煤炭是我国的重要资源,采煤机是煤炭开采中的主要设备。
采煤机的运行效率直接关系到煤矿开采的效益,所以要积极提高采煤机的工作效率。
为了保障采煤机的安全运行,提高其工作效率,同时优化采煤机的运行环境,降低采煤机的开采难度,可在采煤机的控制系统中引入PLC 技术。
1 采煤机控制系统分析采煤机是煤矿作业中的重要设备,一般呈现往复式的运行方式,这是因为煤层并不是出于同一个表层,当高度发生变化时,采煤机控制系统需要采取一定的措施。
为了保障采煤机控制系统的灵活性和准确性,需要引进PLC 技术,积极控制采煤机控制系统的运行,为采煤机控制系统提供精准的操作方式,使采煤机处于高效的运行状态,防止采煤机控制系统出现安全问题。
目前,采煤机控制系统中的PLC 技术正朝着成熟化的方向发展,其改善了煤矿开采的环境,为煤矿提供了稳定的采煤方式,体现了PLC 技术在采煤机控制系统中的实践价值。
2 基于PLC 技术的采煤机控制系统PLC 技术是采煤机控制系统中的关键部分,利用可编程控制器能完成对采煤机系统的硬件控制。
结合采煤机控制系统的应用,分析PLC 技术的设计。
2.1 PLC 技术分析PLC 技术在采煤机控制系统中利用可编程程序专门控制采煤机的硬件部分,并按照程序设计改变采煤机控制系统的运行方式。
PLC 技术简化了采煤机控制系统的设计,能利用集成电路全面控制采煤机的运行。
基于S7-1200PLC煤矿监测系统的多点采集系统

办公自动化杂志基金项目:2019年内蒙古自治区高等学校科学研究项目:基于无线网络的集群智能控制技术在煤矿安检系统中的应用(项目编号NJZY19303);包头职业技术学院2017科研创新团队工业智能控制技术支撑论文。
0引言煤矿安检系统主要以自动化技术和计算机网络技术相结合,实现了煤炭生产过程中智能识别安全隐患的工作方式。
在矿下区域中主要是瓦斯气体最容易爆炸出现危险,瓦斯爆炸具备一定浓度、高温火源以及氧气,因此,瓦斯监测是安检系统核心部分。
本文采用集群智能控制技术,控制由多个智能个体耦合而成的多智能体系统经由相互的分布式协调合作机制可实现对复杂控制,实现系统准确、稳定的监测和控制。
1系统组成1.1总体设计利用西门子S7-12001212C PLC 主控制器输入至按键电路,输出至步进电机驱动器使其控制步进电机的脉冲及方向,来进行主动防护控制,当步进电机工作触碰到限位开关时停止运行。
各器件的动作情况会通过指示灯反应,同时接入智能触摸屏,方便控制,如图1所示。
图1总体设计原理图基于S7-1200PLC 煤矿监测系统的多点采集系统王政1李松2(包头职业技术学院电气工程系包头014030)1(内蒙古北方重工业集团有限公司电气维修公司包头014030)2摘要:煤矿安检系统中数据采集是一个重要组成部分。
矿下安全隐患都是根据各类传感器实时监测,当出现异常信息时,系统能够“主动”监测并执行安全防范措施。
本文根据系统的技术要求,提出了多点采集系统的总体设计方案,工业计算机选用了S7-1200PLC,将S7-1200PLC 与上位机(西门子MP277触摸屏)相连接,实现触摸屏数据控制及系统运行状态。
关键词:监测;智能传感器;S7-1200;多点采集中图分类号:TP274+.2;TD712文献标识码:A 文章编号:7752Design of the Multi-point Acquisition System for Coal MineMonitoring System Based on S7-1200PLCWANG Zheng 1LI Song 2(Departmentof Electrical Engineering,Baotou Vocational and Technical College Baotou014030)1(Electric Maintenance Company,Inner Mongolia North HeavyIndustry Group Co.,Ltd.Baotou 014030)2Abstract :Data acquisition is an important part of coal mine safety inspection system.The hidden danger of undergroundmine is real-time monitored by various sensors.When abnormal information appears,the system can "actively"monitor and implement safety precautions.According to the technical requirements of the system,this paper puts forward the overall design scheme of multi-point acquisition system.The industrial computer selects S7-1200PLC and connects S7-1200PLC with upper computer (SIEMENS MP277touch screen)to realize touch screen data control and system op-eration status.Keywords :monitoring;intelligent sensor;S7-1200;multi-point acquisition**总第440期202121Collection of Translations6··办公自动化杂志1.2硬件搭建1.2.1西门子S-71200PLCS7-1200是一款紧凑型、模块化的PLC,可完成简单逻辑控制、高级逻辑控制、HMI 和网络通信等任务。
基于PLC程控输煤系统的设计与控制

本科毕业设计(论文) 题目:基于PLC程控输煤系统的设计与控制本科毕业设计(论文) 题目:基于PLC程控输煤系统的设计与控制基于PLC程控输煤系统的设计与控制摘要火力发电厂燃煤输送系统是保证电厂锅炉安全可靠运行的十分重要的支持系统,主要负责对发电机组燃煤的卸载、储存和上煤。
如何保证设备运行的可靠性、减少操作人员与维护人员劳动强度、提高经济效益,成为一个值得研究的课题。
可编程逻辑控制器(PLC)是近年来发展极为迅速,应用面极广,以微处理器为核心,集微机技术、自动化技术、通信技术于一体的通用工业控制装置。
它具有功能齐全、使用方便、维护容易、通用性强、可靠性高、性能价格比高等优点,已在工业控制的各个领域得到了极为广泛的应用,成为实现工业自动化的一种强有力工具。
本文基于西门子公司的S7-200型PLC,设计了程控输煤系统。
各设备之间均实现了安全联锁保护控制功能:系统中的输煤电机启停是有着严格的控制顺序。
起动时,为了避免在前段运输皮带上因煤料堆积而造成事故,系统要求逆煤料的流动方向按一定时间间隔顺序起动。
停止时为了不使运输皮带上因残留煤料而造成事故,系统要求顺煤料流动方向按一定时间间隔顺序停止。
PLC控制系统硬件设计布局合理,工作可靠,操作、维护方便,工作良好。
用 PLC程控输煤程控系统,不但实现了设备运行的自动化管理和监控,提高了系统的可靠性和安全性,而且改善了工作环境,提高了企业经济效益和工作效率。
因此PLC程控输煤系统具有一定的工程应用和推广价值。
关键词:锅炉;输煤系统;皮带运输机;可编程逻辑控制器;梯形图;Based On PLC,Program-controlled Coal Conveying SystemAbstractThermal power plant coal conveying system is the guarantee of safe and reliable operation of the power plant boiler is very important support system, is mainly responsible for generating sets of coal unloading, storage and coal. How to ensure the reliability of equipment operation, reduce the operating and maintenance personnel the labor strength, improve the economic benefit, has become a topic worth studying. Programmable logic controller (PLC) is developing very rapidly in recent years, a wide application, microprocessor as the core, integrating microcomputer technology, automation technology and communication technology in the integration of general industrial control device. It has complete functions, convenient use, easy maintenance, strong commonality, high reliability, high ratio of performance to price, has been in the areas of industrial control is widely used and become a powerful tool to realize industrial automation.This article is based on Siemens S7-200 PLC, program-controlled coal conveying system is designed. Between various devices are realized safety interlock protection control function: the coal conveying system motor start-stop is fairly strict control sequence. When starting, in order to avoid in front transport belt accident caused by the accumulation of coal material, system requirements inverse coal material flow direction in a certain time interval starting sequence. Stops in order not to make the transport belt accident, caused by residual coal feeding system requirements along the coal flow direction in a certain time interval sequence stops. PLC control system hardware design layout is reasonable, reliable work, convenient operation and maintenance, good work. With PLC program-controlled coal SPC system, not only has realized the automation of the equipment operation management and monitoring, to improve the reliability and security of the system, and improve the working environment, improve the enterprise economic benefit and work efficiency. So the PLC program-controlled coal conveying system has a certain value for engineering application and promotion.Key Words: Boiler;Coal conveying system;Belt conveyor;Programmable logic controller;Ladder diagram;目录中文摘要 (I)英文摘要 (II)1 绪论 (1)1.1课题背景 (1)1.2设计任务 (2)1.3本文主要研究内容 (2)1.4本文研究的目的及意义 (3)2 可编程逻辑控制器PLC概况 (4)2.1plc的概念及发展 (4)2.1.1可编程序控制器的历史 (4)2.2可编程序控制器的硬件及工作原理 (5)2.2.1可编程序控制器的基本结构 (5)2.2.2可编程序控制器的物理结构 (6)3 系统的硬件设计 (7)3.1PLC机型选择 (7)3.2电动机的选型 (9)3.3电机主电路图设计 (10)4 S7-200PLC及其开发环境介绍 (11)4.1S7-200PLC介绍 (11)4.2Microwin32介绍 (15)5 系统的软件设计 (22)5.1系统软件控制 (22)5.2程控输煤系统启动部分控制 (25)5.3程控输煤系统停止部分控制 (26)5.4程控输煤系统紧急停止和故障停止部分控制 (27)5.4.1紧急停止部分控制 (27)5.4.2故障停止部分控制 (27)6 上位机(触摸屏)的设计 (38)6.1触摸屏机型选择 (38)6.2起始画面的设计 (38)6.3一二号系统画面的设计 (39)6.4传感器监测画面的设计 (40)6.5报警画面的设计 (41)6.6趋势画面的设计 (42)7结论 (45)参考文献 (46)致谢.......................................... 错误!未定义书签。
基于PLC技术的煤层气井生产监控系统智能排采功能的设计与实现

基于PLC技术的煤层气井生产监控系统智能排采功能的设计与实现1. 引言1.1 背景介绍煤层气是一种天然气,存在于煤层中。
随着能源需求的不断增长和环境保护意识的提高,煤层气已成为重要的替代能源之一。
煤层气井生产监控系统是煤层气开采过程中的关键设备,可以实时监测煤层气井的生产情况,确保生产稳定和安全。
随着科技的不断发展,PLC 技术被广泛应用于煤层气井生产监控中,极大地提高了系统的稳定性和可靠性。
传统的煤层气井生产监控系统仅能实现简单的监测和控制功能,对于煤层气井的智能排采功能还有待提升。
本文旨在利用PLC技术,设计并实现一种具有智能排采功能的煤层气井生产监控系统,以提高煤层气井的排采效率和安全性。
本文将从煤层气井生产监控系统的概述入手,阐述PLC技术在煤层气井生产监控中的应用,详细设计智能排采功能,并描述系统的实现过程。
通过系统性能评估,验证设计的可行性和效果。
1.2 研究意义研究将针对煤层气井生产监控系统的概述及PLC技术在其中的应用,提出一套完整的监控方案。
借助PLC技术,可以实现对煤层气生产过程的自动化监控,提高生产效率和安全性。
通过智能排采功能的设计,可以更加精准地控制煤层气井的生产过程,提高排采效率和减少排采损失。
这对于提高煤层气生产效率具有重要意义。
本研究的实施将为煤层气井生产监控系统的智能化和自动化提供一种新的思路和方法,对于我国的煤层气产业发展具有积极的推动作用。
1.3 研究内容研究内容包括对煤层气井生产监控系统智能排采功能的设计和实现。
具体而言,研究将围绕如何通过PLC技术实现对煤层气井生产过程的实时监控和智能化排采进行探讨。
将对煤层气井生产监控系统的概念和功能进行详细介绍,包括系统的组成结构和监控对象。
将详细阐述PLC技术在煤层气井生产监控中的应用,包括PLC在数据采集、处理和控制方面的作用和优势。
接着,将重点讨论智能排采功能的设计原理和方法,包括如何利用传感器数据和PLC系统实现对煤层气井生产参数的智能监测和控制。
基于PLC的输煤控制系统的设计

基于 PLC的输煤控制系统的设计摘要:火电厂的输煤系统是保证火电厂平稳运行的关键。
基于火电厂输煤工序噪声、粉尘等有害因素较多,危害职工生命健康,本文设计了一套基于PLC控制的输煤智慧监盘系统,实现了输煤过程中的现场无人值守。
关键字:PLC控制、输煤、无人值守。
火电厂的输煤系统工序存在噪声污染、粉尘、机械伤害等有害因素,会造成耳鸣、尘肺病等职业病,直接损害现场巡检人员的身体健康。
基于“以人为本”的发展理念,设计了一套现场无人值守的输煤智慧监盘系统,可有效地避免员工与有害因素的直接接触。
本套系统利用除铁器除去煤料中的铁块、碎钉等,可有效的防止皮带的划伤,利用传感器可以精准测量皮带是否跑偏、有无撕裂、料仓是否满位、犁煤器的动作是否到位等一系列的问题。
再结合PLC控制系统即可实现输煤过程中现场的无人值守。
1 系统总体设计本文以陕西金泰氯碱化工有限公司的输煤系统为原型,设计了一套自动化输煤系统。
该系统采用西门子S7-1500 PLC控制系统,硬件系统配置图如下:本系统共有西门子S7-1500 PLC 系统模块21块,共六种,现将各模块的功能简介如下:1.1系统电源(PS)系统电源(PS)通过U行连接器连接到背板总线,并专门为背板总线提供内部所需的系统电源,这种系统电源可为模块电子元件和LED指示灯供电。
当CPU 模块、PROFIBUS通讯模块、Ethernet通讯模块以及接口模块等模块,没有连接到DC24V电源上,系统电源可以为这些模块供电。
1.2 CPU模块CPU 模块为PLC系统中央控制处理单元,PLC系统的核心组成部分,用于存储和执行用户应用程序。
1.3数字量输入(DI)模块数字量输入(DI)模块将现场的数字量信号转换成CPU可接收信号,SIMATIC S7-1500 PLC 的DI有直流16点、直流32点以及交流16点。
数字量输入(DI)模块主要接收现场泵类的启停指令、反馈、故障信号,阀门的开关指令、反馈、故障信号等。
- 1、下载文档前请自行甄别文档内容的完整性,平台不提供额外的编辑、内容补充、找答案等附加服务。
- 2、"仅部分预览"的文档,不可在线预览部分如存在完整性等问题,可反馈申请退款(可完整预览的文档不适用该条件!)。
- 3、如文档侵犯您的权益,请联系客服反馈,我们会尽快为您处理(人工客服工作时间:9:00-18:30)。
河南工程学院毕业设计基于PLC的原煤采样控制系统学生姓名王红晓系(部)机械工程系专业机电一体化指导教师李振杰2010年05月25日摘要我国煤炭储存丰富,是煤炭资源的产、销大国。
针对当前煤炭行业发展中对原煤质量的要求不断提高,原煤采样技术在当今选煤行业也发挥着越来越重要的作用。
本设计就是为中小洗煤厂设计的工业生产流水线的自动控制系统。
在控制系统中采用的PLC技术,系统安全性能好,所采煤样代表性高,维护简单,不需人员看守,采样结果能正确指导选煤厂生产,提高工作效率和操作精度,也就保证正常工业生产中的最大产量和最佳产品质量。
物流配送是物流中一个重要的环节,对于一个大规模的物流集团来说,集约化的发展要使多个仓库、多个配送点(往往达到数以千计的规模)综合实行配送优化成为可能。
关键词:可编程控制器,原煤采样,控制流程图,传感器2ABSTRACTChina's coal stockpiles are rich in coal resources production, marketing power. In view of the current development of the coal industry on the quality of coal rising coal sampling technology in the coal preparation industry today is also playing an increasingly important role. The design is designed for small and medium-sized coal washer of industrial production pipeline Control System. In the control system we use the PLC technology, better security system, the coal-like representation, maintaining simple, PLC no security guards, sampling results will correct meaning to different plant production. Improve efficiency and accuracy of operation. Also ensure normal industrial production was the largest yield of the best quality products.To a scaled logistic company,assigning is an important part of logistic,and further development will make the optimized assigning of warehouse and multi—task possible .KEY WORDS:program logic controller, coal sampling ,control flow chart ,ladder graphics,censors3目录前言 (1)1背景简介 (1)2 系统概述 (1)第1章工艺流程 (2)§1.1初级采样机 (2)§1.2 一次给料胶带 (3)§1.3 破碎机 (3)§1.4 二次给料胶带 (4)§1.5 缩分器 (4)§1.6 样品收集器 (4)§1.7 斗提机 (4)第2章原煤采样控制系统 (5)§2.1控制系统分析 (5)§2.1.1运行过程 (5)§2.1.2控制系统功能 (5)§2.2系统硬件分析...................................... ..6§2.2.1控制单元 (6)§2.2.2 PLC简介 (7)§2.3系统软件分析 (8)§2.3.1系统状态流程图设计 (8)§2.3.2 PLC的I/O点地址分配及PLC选型 (8)§2.3.3 I/O接点电气连接图 (9)§2.4 PLC梯形图程序设计部分 (10)4第3章系统干扰措施 (12)§3.1.抗电源干扰 (12)§3.1.1隔离变压器 (12)§3.1.2滤波器 (12)§3.1.3 分离供电系统 (12)§3.2控制系统接地 (12)§3.3防I/O信号干扰 (12)第4章系统的不足之处及改善方法 (14)结论 (15)参考文献 (16)致谢 (17)附录 (18)561前言1背景简介我国煤炭储存丰富,是煤炭资源的产、销大国,整个煤炭工业在中国的经济发展中发挥了重要的基础和支柱作用。
针对当前煤炭行业发展中对原煤质量的要求不断提高,原煤采样技术在当今选煤行业也发挥着越来越重要的作用,为了进一步了解原煤采样的过程,更好的提高所学专业知识在实际工业现场中的实际运用情况,结合了当前选煤领域广泛采用的原煤采样的控制技术,我选取了本设计题目,采用PLC来实现对原煤采样环节的控制。
希望通过此次设计可以真正把所学知识运用到实际工业现场,为将来参加工作做好铺垫。
我国是煤炭大国,但人均占有量都非常贫乏。
随着经济的飞速增长,冶金、化工、电力等行业对煤炭的需求越来越大,而我国的工业基础却相对比较薄弱。
就煤炭工业而言,只有一些大的企业才实现了原煤采样生产过程中的全部自动化。
一些中小企业,尤其是年产小于30万吨的小企业,却还使用着与时代技术不相称的老的生产方式。
这种生产方式不仅劳动是巨大的,对工人身体上有一定的危害性,而且产品的生产功耗大,生产成本高。
2 系统概述本次设计内容为基于PLC控制的原煤采样系统。
主要控制要求是利用可编程控制器控制各个部分的运行。
其主要设备有初级采样机,一次给料胶带,破碎机,二次给料胶带,缩分器,样品收集器,弃料提升机。
本系统的控制方面可分为自动和手动两种工作方式,就是通常我们所说的集中控制和就地控制两种方式。
选择集中控制方式操作人员可以在控制台上实现系统的正常开停;选择就地控制方式检修人员可在现场实现单机的检修和试运。
就自动工作方式来说,输入量有启动和停止两个开关,输入量主要是采样设备的电动机起停及继电器开关和电磁阀的开关。
正常工作后采用连续运行方式,采样机和胶带运输机连锁运行,对应的时间间隔、数量、缩分质量等参数有计算机输入,然后由PLC控制系统运行,人为干扰很难,采用全封闭共同监管,安全性好。
可编程控制器(PLC)是具有高可靠性的工业自动化产品,作为监控系统的一种现场设备,有出色的数据采集和可编程控制能力。
第1章工艺流程本系统的工艺流程图如下图所示:图1-1原煤采样系统流程图§1.1 初级采样机作用是负责进行运煤带上的初级采样,选用带式输送机煤流采样的刮臂式采样机,刮臂的动作是横向扫过带式输送机的全宽刮出子样,子样的质量取决于胶带上负荷和采样铲的宽度和形状。
刮臂式采样机示意图如下图所示:2图1-2刮臂式采样机示意图1—停止开关;2—蜗轮蜗杆减速机;3—电机;4—运输带;5—接样溜槽;6—取样机联杆刮臂;7—采样铲;8.—皮带托辊§1.2 一次给料胶带作用是从初级采样机输出的煤均匀的撒到一次给料胶带上,运送到下一级,即破碎机。
胶带运输机的长短与现场工艺有关。
§1.3 破碎机滚筒破碎机又叫选择性破碎机,是利用煤和矸石在同一冲击破碎环境中,根据其可碎性的差异,把夹在煤中的矸石解离出来。
滚筒是靠拉轮和滚筒之间的摩擦力而转动。
在滚筒的一端,由给料溜槽给入一级的煤块,随着滚筒的旋转,给入的煤快被提升机顶起,转到一定高度后,煤块就顺着提升机从高出自由落下,由于滚筒的不断转动,煤快反复地被提起和落下。
在次过程中煤受到冲击而破碎,并透过筛孔排出,未被破碎的大块矸石、金属杂物和木块经筛子排矸槽排出,进入二次给料胶带。
3§1.4 二次给料胶带其作用和上面一次给料胶带相同。
§1.5 缩分器缩分是指在煤样制备中,将试样分成具有代表性的几部分,一份或多份留下来的过程,目的在于从大量煤样中取出一部分煤样。
缩分器应尽量减少缩分误差,并能使保留煤样量尽量少。
在这里我们选用旋转式缩分器,示意图如下所示:图1-3旋转式缩分器示意图§1.6 样品收集器作用是将已经缩分好的煤样采集,送到实验室进一步制成分析所用煤样。
§1.7 斗提机斗提机又称为弃料提升机,因经过上述一系列生产过程中,设备的高度一级级降低,所以斗提机的作用就是把经过缩分剩余的余煤将通过斗提机送回到原煤输送带上。
4第2章原煤采样控制系统§2.1 控制系统分析这章我们将对这次设计的控制系统进行详细的分析。
§2.1.1 运行过程原煤采样系统启动后要求整个运行过程能自动运行,并在某一设备故障时能及时发出报警提示。
下面根据原煤采样系统流程图简述系统运行过程。
⑴启动过程:按下启动按钮,受控设备按逆煤流方向依次起车,即由后向前启动。
在这里斗提机最先启动,其次为样品收集器、缩分器、二次给料胶带、破碎机、一次给料胶带,最后为初级采样机。
各个设备之间的启动间隔时间可以自己设定,这里设定为10秒。
系统停止时,与启动相反的方向顺序停止。
⑵初级采样机工作:启动过程完成后,初级采样机开始进行采集煤样并送入一次给料胶带。
此时,初级采样机完成一次采样后将处于保持状态,等待整个原煤采样过程结束后,进行下一次采样过程。
⑶破碎煤快:一次给料胶带把初级采样机采的煤样运送入破碎机。
破碎机的作用是把较大的煤块进行破碎,以便下一级使用。
破碎后的煤样落到二次给料胶带。
⑷缩分:在二次给料胶带上有个缩分器设备,胶带上的煤样有一部分落入缩分器进行缩分,所谓缩分通俗的讲就是把煤样再次破碎到的供检验用的合适的大小。
缩分器缩分次数可以自己设定。
⑸样品收集:由缩分器缩分的煤样已经达到煤样采集的标准,可以直接落入样品收集器,作为检验这批原煤参数的标准。
⑹弃料返回:由于缩分器缩分只用到很少一部分原煤,所以剩余的煤样要返送回原煤运输带,这就用到斗提机。
二次给料胶带把剩余的煤样送入斗提机,通过斗提机把余料送回原煤运输带。
到这步算一个工作过程完成,若按下连续工作开关,系统将连续工作处于自动运行状态。
如果不按下连续工作按钮,各个设备将都将处于待命状态。
§2.1.2 控制系统功能⑴原煤采样装置的控制有两种控制方式,即“自动”控制与“手动”控制。