过程潜在失效模式及后果分析(PFMEA)样板
过程失效模式及后果分析(PFMEA)

XXX汽车技术股份有限公司潜在失效模式及影响分析 PFMEA螺纹孔内无铝屑,机加工面边缘毛刺清理干净;螺纹孔内有铝屑,机加工面边缘未清理干净影响客户装配,客户抱怨61.丝锥损坏2.夹具松动3.切削液未正确喷淋,铝屑未吹掉31.首检记录表2.巡检记录表354None5XΦ0.341±0.01深0.55(英制)尺寸超差 1.毛坯不合格或尺寸变化大4XΦ0.232±0.01深0.5(英制)尺寸超差 2.夹具松动;3.程序错误2XΦ0.232±0.01深0.5(英制)尺寸超差 4.装夹失误2X4.34±0.02(英制)尺寸超差 1.毛坯不合格或尺寸变化大27.19±0.02(英制)尺寸超差 2.夹具松动;3.程序错误2X7.05±0.02(英制)尺寸超差 4.装夹失误2X11.72±0.02(英制)尺寸超差1.毛坯不合格或尺寸变化大1.25±0.02(英制)尺寸超差2.夹具松动;3.程序错误2.38±0.02(英制)尺寸超差 4.装夹失误1.56±0.02(英制)尺寸超差 1.毛坯不合格或尺寸变化大2.44±0.02(英制)尺寸超差 2.夹具松动;3.程序错误8XΦ0.118±0.01(英制)尺寸超差 4.装夹失误尺寸超差1.毛坯不合格或尺寸变化大2X45°±0.5°尺寸超差2.夹具松动;None3影响装配和功能7631.首检记录表2.巡检记录表3★3影响装配和功能7★31.首检记录表2.巡检记录表363NoneNone63影响装配和功能7★31.首检记录表2.巡检记录表3影响装配和功能7★31.首检记录表2.巡检记录表None影响装配和功能7★31.首检记录表2.巡检记录表36363None。
过程潜在失效模式及后果分析(PFMEA)已填写

半成品未做标示
使用统一的周转箱存放半成品 3
检查周转箱内的标示
3 45
热处理8.8级 130 热处理
工件表面处理未达到技术 要求
导致产品机械性能不合格
7
零件不得混淆
产品混杂
用户抱怨
3
热处理未按工艺严格执行
供应商定期评审
盛器未清理干净
1.定期评审; 2.定期对供应商质量考核。
2
1.核对供方检验报告; 2.抽检。
4
1.下单错误; 2.领料计数偏差过大。
1.生产部核对领料单; 2.领料员复验领料数量.
4 车间主任核对
4 64
原材料正确堆放
原材料损坏,变形
1.损坏材料无法使用; 2.缺陷材料造成零件不良
4
原材料搬运、存放过程中碰伤 1.按要求搬运;
、变形。
2.做防护措施。
5
1.工人作业时自检; 2.检验员巡检。
2.检测工具失效.
2.检具定期校正.
6
1.按培训计划执行; 2.量检具检测报告
3 72
半成品按规定堆放、
90 搬至搓牙机床
移动
半成品按规定放置并
做标识
半成品损坏,变形 半成品混淆
无法使用
5
需要挑选半成品,浪费时 间和人力
5
产品搬运过程中碰伤,掉落 使用统一的周转箱和手推车 3 在下道工序生产时目视检验 3 45
零件/系统名称及编号: 车型年/车辆类型 核心小组
过程潜在失效模式及后果分析(PFMEA)
过程责任: 关键日期
工
序 号
过程描述
No.
要求
半成品按规定堆放、
140 搬至待待检区
注塑件过程失效模式及后果分析表模板(PFMEA)

6
包装破损
零件污染,客户投 诉
5
产品碰伤砸伤 客户投诉
6
装箱时确认不足 货物堆积过高
搬运不规范
2
无
3
试验后制定合理堆 积标准
2
无
100目测 100目测 100目测
5 60 5 75 4 48
标签贴错 发错货,客户投诉 5
标签与实物未核对 2
无
100目测
4 40
产品数量不正确
客户投诉
6
80-出货检验
关键尺寸超差
第 1 页,共 2 页
注塑件过程失效模式及后果分析表模板(PFMEA)
零件号
设计责任部门
FMEA 编号
零件名称
关键日期
编制人
车型/年份
系统/子系统/部件
编制日期
核心小组
序号
过程
潜在的失效模式
严 潜在的失效后果 重
度
级 别
潜在的失效原因/机理
频 度 数
现行预防性设计控 制
现行探测性设计控 制
探 测 度
5 60 5 75
建议措施
责任人和目标 完成日期
无
采取的措施
严频探 R 重度测 P 度数度 N
无
无
无
无
不同产品分区放置, 并做好标识
6
2 5 60
无
对纸箱进行固定 6 2 5 60
无
无
无
无
无
不同产品分区放置, 并做好标识
6
2 5 60
无
对纸箱进行固定 6 2 5 60
无
40-原材料烘料
烘料时间不对 烘料温度不对
表面料花 色差
PFMEA范本

要求 进料检
过验程/IQC 功能
潜在 失效模式
潜在 失效后果
严 重分 度类 S
潜在失效 起因/机理
频现 行
度预 防
O过
现行探测 过程控制
探 风险 测 系数 度 D RPN
作业员技能不 足
漏判,误判
5
作业员不熟悉检验标准, 理解错误
3
新员工入司后,必须进行培训并考 核,在考核合格后方能上岗。
3
45
检验仪器设备 误差过大
物料数量 不对
影响产能
5
1、发料员不清楚所需数量 2
5 2、发料员疏忽
4
核对、与套料单/BOM/ECN一致 发料后实行两人确认
3 30 3 60
ESD设施 静电敏感器件被
失效
击穿,功能丢失 7
ESD设施的安装或保护或
实施不规范
2
每日对各ESD点进行点检
5 70
作业指导书不 不按标准/流程 3
全
作业,流出不良 3
4
IQC合理安排检验工作,急料先检 。
4
48
及时制作并不断完善检验标准,按
标准制作不完善
3
检验标准或参考物料规格书实施检 3 45
验
标准制订不合理
3
由IQC工程师及以上人员制订标 准,并根据实际状况修订标准。
3 45
第1页,共9页
建议措施
责任及 目标完成
日期
措施结果
采取的
R
措施 S O D P
N
FORM NO: SST-PFMEA-001
3 36 3 54
黄胶过稀
2 黄胶流到其它元 件上,影响外观
2
PFMEA范本
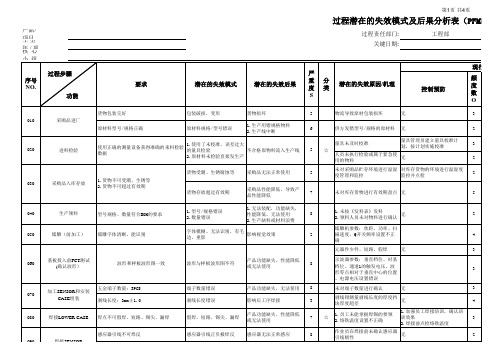
5
75
物料发运现场前,确认是否有IQC 检验标识
2
20
每月盘点货物的受损情况
2
20
每月对库存货物进行有效期盘
点,超出有效期的货物,由IQC检 2
70
验合格后重新张贴检验标识。
领料员对照《发料表》对物料规
格/型号/数量进行确认
5
80
镭雕字体外观全检 FCT测试,确认波形
5
40
4
96
在测试前对示波器参数点检
量具管理员建立量具校准计 划,按计划实施校准
☆
人员未执行检验或属于紧急使 用的物料
无
3 2
030
采购品入库存放
1.货物不可受潮、生锈等 2.货物不可超过有效期
货物受潮、生锈腐蚀等
采购品无法正常使用
5
货物存放超过有效期
采购品性能降低,导致产 品性能降低
7
未对采购品贮存环境进行温湿 对库存货物的环境进行温湿度
090
过程步骤
功能
焊接SENSOR
100
注胶前FCT测试 (调试波形)
110
基板焊接点检查
120
感应距离测试
130
注胶
140
注胶后测试波形
150 160
编制:
成品检验 包装
第2页 共4页
过程潜在的失效模式及后果分析表(PFMEA)
过程责任部门: 关键日期:
工程部
要求
潜在的失效模式
潜在的失效后果
严 重分 度类
度管理和监控
监控并点检
2
未对库存货物进行有效期盘点 无
5
040
生产领料
型号规格、数量符合BOM的要求
PFMEA过程失效模式及后果分析报告

科技股份有限公司作业文件文件编号:XXXX-XXXX.XX 版号:A/0(PFMEA)过程失效模式及后果分析作业指导书批准:审核:编制:受控状态:分发号:2016年01月15日发布2016年01月15日实施过程潜在失效模式及后果分析作业指导书(PFMEA)XXXX-XXXX.XX1目的过程潜在失效模式及后果分析,简称PFMEA。
是一种信赖度分析的工具,可以描述为一组系统化的活动,是对确定产品/过程必须做哪些事情才能使顾客满意这一过程的补充。
其目的是:(a)并评价产品/过程中的潜在失效以及该失效的后果;(b)确定能够消除或减少潜在失效发生机会的措施;(c)将全部过程形成文件。
2 范围:适用于公司用于零组件的所有新产品/过程的样品试制和批量生产。
适用于过程设计的风险性及后果的分析;适用于过程重复,周期性永不间断的改进分析。
3 术语和定义:1)PFMEA:指Process Failure Mode and Effects Analysis(过程失效模式及后果分析)的英文简称。
由负责制造/装配的工程师/小组主要采用的一种分析技术,用以最大限度地保证各种潜在的失效模式及其相关的起因/机理已得到充分的考虑和论述。
2)失效:在规定条件下(环境、操作、时间),不能完成既定功能或产品参数值和不能维持在规定的上下限之间,以及在工作范围内导致零组件的破裂卡死等损坏现象。
3)严重度(S):指一给定失效模式最严重的影响后果的级别,是单一的PFMEA范围内的相对定级结果。
严重度数值的降低只有通过设计更改或重新设计才能够实现。
4)频度(O):指某一特定的起因/机理发生的可能发生,描述出现的可能性的级别数具有相对意义,但不是绝对的。
5)探测度(D):指在零部件离开制造工序或装配之前,利用第二种现行过程控制方法找出失效起因/机理过程缺陷或后序发生的失效模式的可能性的评价指标;或者用第三种过程控制方法找出后序发生的失效模式的可能性的评价指标。
产品潜在失效模式及后果分析(PFEMA)--报告模板

5
90
第 5 页,共 228 页
潜在失效模式及后果分析
GLP1007 ◎首次提交 ○OTS提交更新 ○PPAP提交更新 ○生产更新
版本号:5
○DFMEA ◎PFMEA
供应商代码/名称 100036
编号:
零件号码:01727609
零件名称:GPS主机-MP5
核心小组:PE-毛积钧、唐庆姚、廖正江 、黄业旺 SQE - 吴冲 ,ME - 郭业亮 ,新进-梁 小华,叶振超 PM -温闻,田梦棠
潜在失效模式及后果分析
GLP1007 ◎首次提交 ○OTS提交更新 ○PPAP提交更新 ○生产更新
版本号:5
○DFMEA ◎PFMEA
供应商代码/名称 100036
编号:
零件号码:01727609
零件名称:GPS主机-MP5
核心小组:PE-毛积钧、唐庆姚、廖正江 、黄业旺 SQE - 吴冲 ,ME - 郭业亮 ,新进-梁 小华,叶振超 PM -温闻,田梦棠
编制人:毛积钧
编制日期:2014-04-15
设计项目或过程功 能要求
潜在失效模式
失效的潜在后果
S
特性分 类
失效的潜在起因
○
现有设计或过程控制
D RPN
二维条形码贴装
条形码纸翘起或是中间 凸起
外观不良
3
条形码纸贴装完后没 有用手抹平贴纸
3
条形码纸贴装完用手指将胶 纸抹平贴紧.
8
72
Z刮浆
拉尖、锡孔、短路、少 丝印不良,回流焊接后产生
设计项目或过程功 能要求
潜在失效模式
失效的潜在后果
S
特性分 类
失效的潜在起因
○
现有设计或过程控制
潜在失效模式分析(PFMEA)样板-1
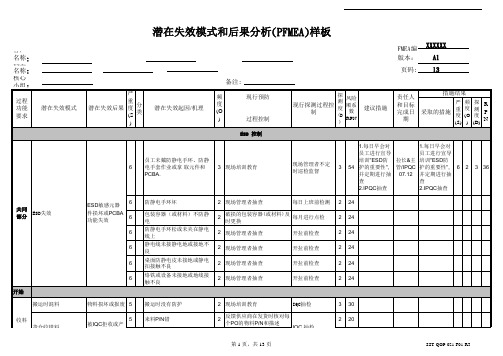
1.不同的Model 之间有相似 的的钢网设计 2.钢网上的P/N标示错误或没 标示 1.印刷速度或刮刀压力设置 不当 2.钢网孔堵塞或漏开孔 3.刮刀两边红胶收拢不及时 4.PCB板表面清洁度不够 5.红胶开封时间太长或过期 1.印刷速度或刮刀压力设置 不当 2.红胶开封时间太长或过期 3.印刷偏移位 1.钢网孔偏位 2.程序设定偏位
1.定期培训员 工"电子元件 基础知识"并 实践考核 2.每站物料上 6 线时依BOM 描述需要测量 其阻容值并记 PIE 录 /操作员 3.开线换线后 Dec-07 由技术员确认 所有方向性器 件的"方向标 示"并贴装首 6 件确认 4.换料时由两 人互检确认 5.IPQC 抽验
2
3 36
2
3 36
2
3 36
共同 ESD失效 部分
ESD敏感元器 件损坏或PCBA 功能失效
6 6 6 6 6 6
防静电手环坏 包装容器(或材料)不防静 电 防静电手环松或未夹在静电 线上 静电线未接静电地或接地不 良 桌面防静电皮未接地或静电 扣接触不良 烙铁或设备未接地或地线接 触不良
2 现场管理者抽查 2
每日上班前检测
潜在失效模式和后果分析(PFMEA)样板 样板 潜在失效模式和后果分析
FMEA编号: XXXXXX 客户名称: 机型名称: 核心小组:
严 重 分 潜在失效后果 度 类 (S ) 频 度 (O )
XXXXXX XXXXXX
过程责任部门:SMT&MI&TEST
编制者:
版本: 页码:
A1 13
备注:
现行预防
2 2 2 2 2 2
破损的包装容器(或材料)及 每月进行点检 时更换 开拉前检查
潜在失效模式及后果分析PFMEA

Part name:Proces TechnicalPrepared By:Approval By:零件名称:过程责技术部编制:批准:Part number:KeyDateFMEA Date(Orig):FMEA Date(Rev.):Rev.A/0零件号:关键日FMEA 日期(编制):FMEA 日期(修订):版本:A/0Core Team:general manager :主要参加人:总经理:, 技术部: , 销preservation溶解,保温Part name:Proces TechnicalPrepared By:Approval By:零件名称:过程责技术部编制:批准:Part number:KeyDateFMEA Date(Orig):FMEA Date(Rev.):Rev.A/0零件号:关键日FMEA 日期(编制):FMEA 日期(修订):版本:A/0Core Team:general manager :主要参加人:总经理:, 技术部: , 销Part name:Proces TechnicalPrepared By:Approval By:零件名称:过程责技术部编制:批准:Part number:KeyDateFMEA Date(Orig):FMEA Date(Rev.):Rev.A/0零件号:关键日FMEA 日期(编制):FMEA 日期(修订):版本:A/0Core Team:general manager :主要参加人:总经理:, 技术部: , 销Part name:Proces TechnicalPrepared By:Approval By:零件名称:过程责技术部编制:批准:Part number:KeyDateFMEA Date(Orig):FMEA Date(Rev.):Rev.A/0零件号:关键日FMEA 日期(编制):FMEA 日期(修订):版本:A/0Core Team:general manager :主要参加人:总经理:, 技术部: , 销Part name:Proces TechnicalPrepared By:Approval By:零件名称:过程责技术部编制:批准:Part number:KeyDateFMEA Date(Orig):FMEA Date(Rev.):Rev.A/0零件号:关键日FMEA 日期(编制):FMEA 日期(修订):版本:A/0Core Team:general manager :主要参加人:总经理:, 技术部: , 销Part name:Proces TechnicalPrepared By:Approval By:零件名称:过程责技术部编制:批准:Part number:KeyDateFMEA Date(Orig):FMEA Date(Rev.):Rev.A/0零件号:关键日FMEA 日期(编制):FMEA 日期(修订):版本:A/0Core Team:general manager :主要参加人:总经理:, 技术部: , 销。
2018.6.14潜在失效模式及后果分析(PFMEA)

模式及后果分析
FMEA号码: 联系电话: 最新修改日期:
称:
寇卫平
建议的措施
负责人/部门/ 计划完成日期
采取的措施
S
O
D
RPN
无 无 无 无 每年不定期抽样进行第三方检测 无 无 定人进行领料,领料时双方100%核对 生产部 按烘料作业指导书设定烘料时间和温 生产部 度 无 1以生产样件工艺参数为准,更 1锁定生产样件成型工艺参数,2操作 技术部/生产部/ 新工艺参数表,且锁定。2操作 员100%检查,3巡检每2H一次进行抽查 品质部 员100%检查,3巡检每2H一次进 行抽查 1以生产样件工艺参数为准,更 1锁定生产样件成型工艺参数,2操作 技术部/生产部/ 新工艺参数表,且锁定。2操作 员100%检查,3巡检每2H一次进行抽查 品质部 员100%检查,3巡检每2H一次进 行抽查 1以生产样件工艺参数为准,更 1锁定生产样件成型工艺参数,2操作 技术部/生产部/ 新工艺参数表,且锁定。2操作 员100%检查,3巡检每2H一次进行抽查 品质部 员100%检查,3巡检每2H一次进 行抽查 定人进行领料,领料时双方 100%核对 实施烘料记录 2 6 1 1 2 3 4 18 质量部 每年不定期抽样进行第三方检测 7 2 2 28
胶口设计不合理 冷却时间不够 浇口设计不合理 顶出受力不平衡 胶口设计不合理 注射压力偏小 顶出受力不平衡 注塑压力过大 保压压力过大 C 注射时间过长 C 注射时间不足 检验标准认识不足 未检验 检验标准认识不足 未检验 B 成型工艺参数未调试好 C 成型工艺参数未调试好 B 操作工漏装
4
对模具做模流分析,选择合适位置、形状、大小 的胶口
6
2
3
30
仓库实行严格先进先出管理 做限高标识限高 必须持证上岗 制定新的库位标识 更换新的库位标识 无 增加检验人员 无 增加检验人员 无 生产部
PFMEA过程失效模式及后果分析

□ 样件 □ Prototype
□ 试生产 □ Pre-Launch
System系统
Subsystem子 系统
Component零 部件 Model Year(s)/Vehic le(s)车型年/ Core Team核 心小组成员
Recommended Action(s) 建议措施
Responsibility&
Action Results措施结果
Target
Completion Date 责任和目
标完成日期
Actions Taken 采取的措施
Sev 严 重 度
Oc c 频 度
De t探 测 度
Rpn 风险
度
Se v. 严 重 度
CL AS S级 别
Potential Cause (s) / Mechanism(s) of Failure
潜在失效的起因/机理
Occ r.频 度
Current Process Control 现行控制过程
预防 Prevention(P)
探测 Detect(D)
FMEA Numbn
body/车身 floor/地板
BV61-A045B30-AA
过程失效模式及后果分析
Design Responsibility 设计责任
Key Date 关键日期
Item / Function项目/
功能
Potential Faisure Mode 潜在失效模式
Potential Effect(s) of Failure潜在失效后果
Se v. 严 重 度
潜在的失效模式及后果分析(PFMEA)-63210118
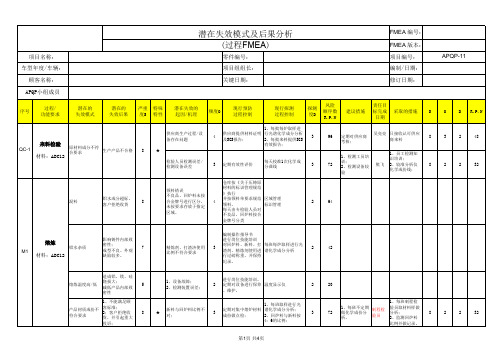
S
O
D R.P.N
气密测试 不符合IP66标准 影响产品功能 M8
水压测试 漏气,密封失效 影响产品功能
8
1、产品平面度超 ★ 差;
2、检测装置误差;
6
1、制作专用测试工 1、检验人员对产品
装;
100%做气密性测试;
2
1、产品平面度超
8
★
差; 2、打密封胶不均
匀;
3
1、使用打胶机均匀 打胶,保证打胶连贯 性;
1、检验人员对产品 100%做气密性测试;
2
1、产品加工时
96
保证产品平面 度; 2、变形产品作
蔡建华 持续
1、对不合格品 检查漏气位置后 做返工处理。
8
2
2
32
较形返工;
48
1、监测产品平 面度; 2、使用自动打 胶机;
1、产品平面度 检测; 蔡建华 2、螺丝拧入时 采用对角平衡方 式;
8
1
2
16
潭熙存
1、设计制作专 用加工夹具。
8
2
3
48
42
24 30 30 54
45 54 48
第3页 共4页
序号
过程/ 功能要求
潜在的 失效模式
潜在的 失效后果
严重 特殊 度S 特性
潜在失效的 起因/机理
频度O
现行预防 过程控制
现行探测 过程控制
探测 度D
风险 顺序数 R.P.N
建议措施
责任目 标完成 采取的措施
8
1、压铸机台参数 由压铸领班铱工艺 要求设定; 2、规范员工操作 规程; 3、模具易损件作 抛光并加硬回火处 理;
1、首件确认并对 比前次生产未件; 2、压铸工艺参数 记录表; 3、工序检验记录 表; 4、生产自检;
过程失效模式及后果分析模板(PFMEA)

潜在失效模式
严
潜在失效后果
重 度
级 别
S
潜在失效原因机理
频 度 O
现行控制
探 测 度 D
R P N
建议采取的措施
责任人 完成日期
措施结果 验证 S O D RPN
长度超出上限 下限 报废
4
员工计算失误
4
员工计算失误
6 首件检验 2 首件检验
板材开裂
2
折弯
外型扭曲
报废 报废
4
周转/搬运碰到
XXX 2019/3/2 XXX 2019/3/2 XXX 2019/3/2 XXX 2019/3/2 XXX 2019/3/6 XXX 2019/3/6 XXX 2019/3/6 XXX 2019/3/6 XXX 2019/3/6 XXX 2019/3/7 XXX 2019/3/7 XXX 2019/3/9 XXX 2019/3/9 XXX 2019/3/9
4
周转/搬运碰到
4 巡检 1次/2hr 2 巡检 1次/2hr
孔径规格不符 影响装配
8
钻孔设备精度不够 2 巡检 1次/2hr
3
钻孔 尺寸超差
影响装配
7
钻头定位不准
2 首件检验
位置不对中心 影响装配
7
钻头定位不准
2 首件检验
焊渣飞溅
影响外观
设备调试不良
3 巡检 1次/2hr
3
毛刺未及时磨掉
4 巡检 1次/2hr
过程失效模式及后果分析(PFMEA)
Process Failure Modes and Effects Analysis
产品名称: XXXXXXXXXXXXXXX 小组成员: XXX(开发)、XXX(生产)、XX(品质)、XXX(技术)…
PFMEA潜在失效模式及后果影响分析 案例

带 ★ 风险 的 探測性 顺 序 正 D 数RPN 在 改 进
建议的措施
尺寸超出要求範圍 組立空間不足 尺寸低於要求範圍 穿線空間不足
4
IQC依通常检验水准 供應商來料不符合要求 II級 AQL:0.4 進行檢
驗
3
使用精密影像 測繪儀檢驗
3
36
5
IQC依通常检验水准 供應商來料不符合要求 II級 AQL:0.5 進行檢
20.1
依要求配比黑膠 未依要求配比黑膠 黑膠無法固化
20.灌膠
20.2
依要求進行灌膠作業 未依要求進行灌膠 灌膠過多或過少
5
作業員未依要求作業
4
作業員未依要求作業
1、作業規定 2、IPQC抽檢
1、幹部確認 2、IPQC抽檢
1、首件確認 2、IPQC抽檢
3
使用耐壓測試 仪
4
48
使用直流電源
3
、示波器、電 子負載、萬用
鐵芯穿線空間不 足
4
供應商來料不符合要求
IQC依特殊检验水准S1級AQL:4.0進行檢驗
4
使用微米千分 尺檢驗
3
48
2.2
線徑尺寸符合要求
線徑尺寸低於要求
半成品測試電阻 不良
5
供應商來料不符合要求
IQC依特殊检验水准S1級AQL:4.0進行檢驗
3
使用微米千分 尺檢驗
4
60
2.3 2.漆包線
外觀符合要求
1、作業規定
2
、IPQC巡查
3
使用樣品比對
3
36
14.2
14.基板視 檢驗焊接后元件接觸
檢
是否良好
元件焊接不良 電氣檢驗結果NG
潜在失效模式及后果分析PFMEA(案例)

3
42
无
2
押出
铜丝拉细
导体电阻过大
7
▲
放线张力过大
2
操作员用OD表首检铜丝线径
4
56
无
热收缩不良
使用时绝缘收缩严重使端部导体外露
6
未过预热器
2
操作员每换规格目测检查是否过预热器
7
84
无
潜在失效模式及后果分析
(过程FMEA)
FMEA编号:PF001第3页,共4页
2
检验员目测全检线材标识
7
70
无
PE膜包覆不完全
线材局部裸露,运输过程中使线材表面擦伤,顾客不满意
5
操作员因疏忽而导致包装不完全
2
检验员目测全检线材包装
7
70
无
频度O
现行过程控制预防
现行过程控制探测
探测度
R
P
N
建议措施
责任及目标完成日期
措施结果
采取的措施
S
O
D
R
P
1
束绞
铜丝跳股
引起成品线材表面有股纹、起包,火花电压测试通不过
7
绞线机内导轮不灵活
2
每班开始时手感检查导轮是否灵活
操作工每两小时目测一次。检验员每两小时目测检查,查看是否有跳股
7
98
无
7
放线张力不同
7
98
无
线材偏心
最小点厚度小于规定值,导致绝缘电阻过低使漏电流过大,引起仪表指示不灵敏
7
▲
模具未调好
2
检验员投影仪首检、每两小时目测检查,查看是否偏心,操作工每小时目测一次。