公司内部存在的七种浪费
企业管理七大浪费

企业管理七大浪费浪费 1:管理工作“等”等待上级的指示:上级不安排工作下级就坐等,上级不指示下级就不执行,上级不询问下级就不汇报,上级不检查下级就拖着办。
多干事情多吃亏,出了问题怎么办?听从指示没有错,再大责任可分担。
很多工作是在多次检查和催办下才完成的,造成极大的浪费。
等待下级的汇报:任务虽已布置,但是没有检查、监督。
不主动深入调查情况,掌握第一手资料,只是被动地听下级汇报,不做核实就做决定或者向上级汇报,出了问题,责任还可以往下级身上推。
等待对方的回复:已与对方联系过,什么时候得到回复我无法决定,延误工作的责任应该由对方负责,我只能等。
追究责任也不怕,我某月某日把这份文件送给对方,这里记录得很清楚,对方不回复我能怎么办?你还是和对方联系一下吧,以免耽误工作。
等待生产现场的联系:职能部门不主动去为现场提供服务,而是坐等现场的联系,有时还很不耐烦,认为多等一会有什么了不起,却没有设身处地去为现场着想,严重地影响了生产现场问题的及时解决。
浪费 2:管理工作无序职责不清造成的无序:由于制度、管理等方面的原因,造成某项工作好像两个部门都管,却纠缠不休,整天扯皮,使原来的有序反而变成无序,造成极大浪费。
某个部门某个人,当看到一项工作比较紧急,如果不做就会影响到公司利益时,进行了补位。
这时就出现了一种怪现象:那么,今后这项工作就由你们来做吧,责任部门反而放任不管了,这也是一种无序。
业务能力低下造成的无序:素质低下、能力不能满足工作需要,都会造成了工作的无序。
应该承担某项工作的部门和人员,因能力不够而导致工作混乱无序;当出现部门和人员变更时,工作交接不力,协作不到位,原来形成的工作流程经常被推翻,人为增加了从“无序”恢复到“有序”的时间。
一个有效的管理者应该是一个规范化的高手,能把复杂无序的工作标准化、规范化、简单化,从而使普通员工可以完成原本无法完成的工作。
有章不循造成的无序:随心所欲,把公司的规章制度当成他人的守则,没有自律,不以身作则,不按制度进行管理考核,造成无章无序的管理,影响员工的积极性和创造性,影响部门的整体工作效率和质量。
精益生产之七大浪费

精益生产之七大浪费精益生产是一种以最小化浪费为目标,通过优化流程和提高效率来提高产品质量和客户满意度的管理方法。
在精益生产中,有七大浪费被认为是造成资源浪费和低效率的主要原因,它们是:过产、等待、运输、不合格、运动、库存和过程错误。
1. 过产(Overproduction):过产是指在没有实际需求的情况下进行生产活动,导致产品过度积压和资源浪费。
这不仅会给企业带来高成本,还会增加库存量和缩短产品寿命。
2. 等待(Waiting):等待是指生产过程中出现的不必要的停顿和延迟。
这可能是由于设备故障、物料不足、工人缺席等原因导致的。
等待会降低生产效率,增加生产周期,延迟产品交付。
3. 运输(Transportation):运输是指不必要的材料和产品的长距离运输。
这使得运输成为了一个独立的过程,需要额外的时间和资源。
这些额外的步骤可能会导致物料的损坏、遗失和延迟,进一步增加了生产成本。
4. 不合格(Defects):不合格是指生产中出现的错误、缺陷和质量问题。
不合格的产品需要进行修正、重新制造或报废,这增加了不必要的时间和资源。
这不仅会导致生产延误,还会降低产品质量和客户满意度。
5. 运动(Motion):运动是指工人在生产过程中进行不必要的移动和动作。
这可能是由于生产线布局不合理、工具和设备摆放不当等原因导致的。
这增加了工人的体力消耗,降低了生产效率,也增加了人为错误的可能性。
6. 库存(Inventory):库存是指未经加工的原材料和半成品的储存量。
过多的库存可能会导致资金占用、过期损失、储存空间浪费等问题。
此外,库存过多也会隐藏潜在的问题,如质量问题和需求变化的风险。
7. 过程错误(Processing):过程错误是指生产过程中出现的不必要的重复、增补和调整。
这可能是由于不合理的工艺流程、工具和设备的不良设计等原因导致的。
这会增加生产成本和时间,降低生产效率和产品质量。
有效管理和消除以上七大浪费是精益生产的关键。
企业管理中的七大浪费现象

企业管理中的七大浪费现象2019-12-12 16:34在我们的现实生活中存在的浪费现象,有生活中的,有企业管理中的,这些浪费,都是横亘在我们面前的敌人,我们只有对它了解的越多,将来获得的利益也越多。
对此,企业管理中又存在着哪些浪费现象呢?下面请和九脑汇学院一起来看看吧。
浪费一:管理工作“等”在管理工作中,等待的浪费主要表现在以下几方面:1、等待上级的指示上级不安排工作下级就坐等,上级不指示下级就不执行,上级不询问下级就不汇报,上级不检查下级就拖着办。
多干事情多吃亏,出了问题怎么办?听从指示没有错,再大责任可分担。
很多工作是在多次检查和催办下才完成的,造成极大的浪费。
2、等待下级的汇报任务虽已布置,但是没有检查、监督。
不主动深入调查情况,掌握第一手资料,只是被动地听下级汇报,不做核实就做决定或者向上级汇报,出了问题,责任还可以往下级身上推。
3、等待对方的回复我已与对方联系过,什么时候得到回复我无法决定,延误工作的责任应该由对方负责,我只能等。
追究责任也不怕,我某月某日把这份文件送给对方,这里记录得很清楚,对方不回复我能怎么办?你还是和对方联系一下吧,以免耽误工作。
4、等待生产现场的联系职能部门不主动去为现场提供服务,而是坐等现场的联系,有时还很不耐烦,认为多等一会有什么了不起,却没有设身处地去为现场着想,严重地影响了生产现场问题的及时解决。
这些“等待”在工作中是大量存在的,主要是中层管理人员缺乏责任心和主动精神,不愿意承担责任。
对于这种浪费,九脑汇学院认为,根据不同企业的文化氛围,如果不能用Y理论激励员工去消除等待的浪费,就需要用X理论去加强管理。
浪费二:管理工作无序“没有规矩,不成方圆”,这句古语说明了秩序的重要性。
缺乏明确的规章、制度、流程,工作中容易产生混乱,这是众所周知的。
但如果有令不行、有章不循,按个人意愿行事造成的无序浪费,更是非常糟糕的事。
1、职责不清造成的无序由于制度、管理等方面的原因,造成某项工作好像两个部门都管,却纠缠不休,整天扯皮,使原来的有序反而变成无序,造成极大浪费。
每个公司都存在这7大浪费【会计实务经验之谈】

每个公司都存在这7大浪费【会计实务经验之谈】「1」过量生产是一种时间匹配上的不合理,当生产多余或快于下道工序所需或下游客户所需时,就是过量生产。
简单的说就是生产的太多了,生产的太快了。
这种过量生产的浪费往往是制造工厂中最常见也是最严重的浪费。
特征如下:(1)物料堆积如山,一时用不上;(2)设备闲置用不上;(3)人员雇佣过多;(4)生产空间闲置用不上「2」过量库存「3」搬运与运输工作:不符合精益生产的一切物料搬运活动都是多余的、浪费的。
(1)多余的叉车、货车;(2)多余的搬运工;(3)零件、产品的磕碰、划伤、损坏;(4)重复的放置;(5)重复的堆放;(6)重复的移动;(7)重复的排列;「4」加工浪费与返修工作:(1)返修工作的产生原因是:①工人操作不当;②员工工作能力不足;③公司对员工的培训不够「5」内部管理不当工作「6」多余动作任何不增加产品或服务价值的人员动作和设备动作叫多余动作。
特征有(1)两手空闲;(2)单手空闲;(3)动作太大;(4)转身角度太大;(5)重复动作;(6)不明等待。
等待动作:当两个关联要素之间未能完全同步时所产生的空闲时间叫等待。
特征有:(1)人员在生产过程中的等待:① 操作人员、班组长等待生产计划调度员安排下一个工作;② 设备坏了,等待机修工来维修;③ 产品做完了,等待检验员的检验;④ 产品做完一道工序了,等待换模具、刀具、数控机床换程序。
⑤ 有人没事做,有事没人做;(2)设备的等待(3)材料物资的等待(4)生产场地的等待(5)其他时间的等待① 缺料的,在等料;② 缺工具的,在等工具;③ 缺图纸的,在等图纸;④ 缺模具、刀具的,在等模具、刀具;⑤ 上道工序为瓶颈工序的,下道工序在等上道工序;以上的各种等待都是浪费,处理方法还是那句老话,打破部门壁垒,每个人、每个部门都把自己手头的工作做好,做到位,做彻底,效率就提高了,成本就控制住了。
值得注意的是,以上7大浪费,其中的移动搬运环节、检验检查环节和等待停顿环节,有的能完全消灭,有的则不能完全取消,要视具体情况而定。
7大浪费

七大浪费(一)库存的浪费1.定义库存的浪费是指由于过多的原材料、在制品或最终成品而导致的较长的前置期、陈旧过时品、毁损品、运输与储存成本及延迟。
2.具体表现和影响库存浪费的具体表现和影响为:过度的库存会严重积压流动资金,并且占用资金(损失利息)及额外的管理费用;产生不必要的入库、出库、登账、盘点、防护、寻找、搬运等管理成本浪费;不必要的库房空间、料架、堆高机、自动搬运系统等投资浪费;使用时的重新整理,价值衰减,因订单或设计变更而变成呆料废料;由于企业大量的管理问题都通过安全库存予以缓冲和解决,所以堆积的库存最容易掩盖管理问题、隐藏管理失误,是改革的最大障碍。
(二)搬运的浪费在制造型企业内部,物品的取放、堆积、排列、移动、整列等等搬运的动作大都是无附加价值的动作,由这些所造成的浪费即为搬运的浪费。
搬运的动作会直接造成时间、空间、容器、载具、输送带、人力等等的浪费,并间接造成库存、管理上的浪费,更糟糕的是,搬运过程还经常发生物品的损伤,也会造成许多质量性连锁浪费。
应对搬运的浪费,管理者首先应该思考的是如何予以免除,这就需要从厂房布局、设备布置、生产过多/过早、库存中转、波动干扰、流量失衡、计划变更等等造成搬运浪费的主要原因着手予以考虑。
只有当实在无法避免搬运的行为时,才考虑如何搬运更有效率。
(三)等待的浪费1.定义和表现等待的浪费是指因断料、作业不平衡、计划不当等造成无事可做的等待,也称之为停滞的浪费。
从企业资源的角度来看,包括资金、厂房空间、机器设备、原材辅料、人员以及信息等企业资源之间的相互等待,都属于这种浪费,其具体的表现有:生产线的品种切换;每天的工作量变动很大,当工作量少时,便无所事事;时常因缺料而使机器闲置;因上游工序延误,导致下游工序无事可做;机器设备时常发生故障;生产线未能取得平衡。
2.产生的原因分析在企业的各种浪费之中,等待浪费所产生的原因是最为复杂的,最主要的包括以下几个方面:企业所处行业的淡旺季变化会导致在淡季的资源闲置;企业业务部门接单不力,使得企业生产订单不足,进而导致相关资源闲置;企业生产部门受牛鞭效应和被动接单的双重影响,生产量波动大,生产订单时间不确定,从而出现生产排程困难、忙闲不均的现象;接单排单不良,排程像蛇吞蛋也会导致忙闲不均;企业生产排程受到外部干扰和内部计划逻辑不当的共同影响,总是变来变去无法确定,这样也会导致相关资源等来等去;离岛式的车间布局;现场管理不当,使得生产线不安定;流水线设计不当,造成生产线不平衡。
工作中的七种浪费
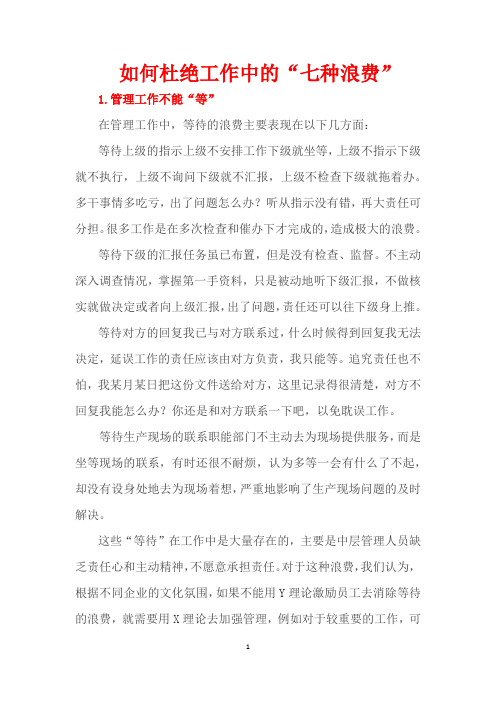
如何杜绝工作中的“七种浪费”1.管理工作不能“等”在管理工作中,等待的浪费主要表现在以下几方面:等待上级的指示上级不安排工作下级就坐等,上级不指示下级就不执行,上级不询问下级就不汇报,上级不检查下级就拖着办。
多干事情多吃亏,出了问题怎么办?听从指示没有错,再大责任可分担。
很多工作是在多次检查和催办下才完成的,造成极大的浪费。
等待下级的汇报任务虽已布置,但是没有检查、监督。
不主动深入调查情况,掌握第一手资料,只是被动地听下级汇报,不做核实就做决定或者向上级汇报,出了问题,责任还可以往下级身上推。
等待对方的回复我已与对方联系过,什么时候得到回复我无法决定,延误工作的责任应该由对方负责,我只能等。
追究责任也不怕,我某月某日把这份文件送给对方,这里记录得很清楚,对方不回复我能怎么办?你还是和对方联系一下吧,以免耽误工作。
等待生产现场的联系职能部门不主动去为现场提供服务,而是坐等现场的联系,有时还很不耐烦,认为多等一会有什么了不起,却没有设身处地去为现场着想,严重地影响了生产现场问题的及时解决。
这些“等待”在工作中是大量存在的,主要是中层管理人员缺乏责任心和主动精神,不愿意承担责任。
对于这种浪费,我们认为,根据不同企业的文化氛围,如果不能用Y理论激励员工去消除等待的浪费,就需要用X理论去加强管理,例如对于较重要的工作,可以用5W1H来进行计划分解,然后进行控制、检查和考核。
实际上,X和Y理论都不能从根本上解决问题,X+Y相辅相成也许更好一些。
2.把无序变有序“没有规矩,不成方圆”,这句古语说明了秩序的重要性。
缺乏明确的规章、制度、流程,工作中容易产生混乱,这是众所周知的。
但如果有令不行、有章不循,按个人意愿行事造成的无序浪费,更是非常糟糕的事。
职责不清造成的无序由于制度、管理等方面的原因,造成某项工作好像两个部门都管,却纠缠不休,整天扯皮,使原来的有序反而变成无序,造成极大浪费。
某个部门某个人,当看到一项工作比较紧急,如果不做就会影响到公司利益时,进行了补位。
公司内部存在的七种浪费

1.七种浪费之一:等待的浪费
等待就是闲着没事,等着下一个动作的来临,这种浪费是无庸置疑的。 造成等待的原因通常有:作业不平衡、安排作业不当、停工待料、品质 不良等。
另有一种就是“监视机器”的浪费,为了使自动设备能正常运转,例如: 排除小故障、补充材料等等,通常还会另外安排人员站在旁边监视。所 以,虽然是自动设备,但仍需人员在旁照顾,特称之为“闲视”的浪费。 当制造部在生产新产品发生一些问题时,生产技术部和品管部是否能立 即解决而不需要现场人员长时间等待? 如何减少这种等待需要大家加以反思。 反思在KTC中是否存在的等待浪费现象?
2.七种浪费之二:搬运的一旁的搬运过程 如:搬运的距离很远; 小批量的运输; 出入库次过多等。
搬运的浪费若分解开来,又包含放置、堆积、移动、整理 等动作的浪费
有些人想到用输送带的方式来克服,这种方式仅能称之为 花大钱减少体力的消耗,但搬运本身的浪费并没有消除, 反而被隐藏了起来。
何谓浪费
何谓浪费:
不产生任何附加价值的
动作、方法、行为和计划
用不同的评判标准去判断 一个动作、行为、方法或计划时, 所得到的浪费程度都会不同。
现场活动包括“有附加价值的”和“没有附加价值的”活动,那些不产生附加价 值的活动应坚决予以消除
生产现场中的七种浪费概述 精益生产方式中所指出的浪费,和大家日常生活中所提到的浪费有着截 然不同的含义,即:在工业生产中,凡是不能直接创造价值的一切活动, 均视为浪费。 精益生产方式将所有浪费归纳成七种: ■等待的浪费; ■搬运的浪费; ■不良品的浪费; ■动作的浪费; ■加工的浪费; ■库存的浪费; ■制造过多(早)的浪费。
6.七种浪费之六:库存的浪费(5) Ⅵ.设备能力及人员需求的误判: 由于库存量的存在,设备能力不平衡时也看不出(库存越多,越不容易看 出来)。人员是否过剩,也无法了解。由于有较多的库存,供应部门需要 增加人员,制造一线需要更多的人员来生产产品用于补充库存,需要增添 设备来保证生产库存所需要的设备能力,从而形成新一轮的浪费。 到底为什么要有库存量,最大的理由是“怕出问题”——出现故障怎么办? 会不会因部分设备出问题,而影响整条生产线或工厂的生产呢? 于是乎为了不使影响扩大,库存便成了必要,众多的问题也被隐藏起来, 所有进步、赚钱(发现问题、解决问题就是赚钱)的步调自然变慢了。无 怪乎精益生产方式称库存为万恶之源,绝对不允许它存在,如果现在已经 有了库存,也要行进一切办法,将之降低,力争零库存。 (注:零库存的“零”并非指数学意义上的“完全没有”的意思,而是指 把库存“尽量减到最少的必要程度”。)
企业常见的七大浪费

企业常见的七大浪费 Last revision date: 13 December 2020.中国式现场管理之五十:企业常见的七大浪费企业常见的七大浪费现场混乱,插不进脚;员工仪容不整,两眼无光;物料混放,标志不清;设备故障不断,苟延残喘;人海战术,加班加点但还是要待工待料…这是国内不少企业的现状。
一切不增加对客户和企业价值的活动都是浪费。
在此前提下,企业每产一件产品就在制造一份浪费。
伴随企业运营中各业务环节不被察觉或不被重视的浪费,日本企业管理界将之形象地比喻为“地下工厂”。
日本专家通过长期的实践和研究发现,企业内有七种常见的浪费:1.等待浪费等待并非加工过程,不能改变物料的形状、尺寸、性质和状态从而改变韧料的功能,所以等待不创造价值。
待工和待料是两种最常见的等待情形。
常见的等待现象有:物料供应或前工序能力不足造成待料,监视设备作业造成员工作业停顿,设备故障造成生产停滞,质量问题造成停工,型号切换造成生产停顿。
造成等待的常见原因有:流水线能力不平衡,计划不合理,设备维护不到位,物料供应不及时等。
2.搬运浪费搬运也非加工过程,不能改变物料的形状、尺寸、性质和状态从而改变物料的功能,而且搬运过程中的放置、堆积、移动、整理等造成空间、时间、人力和工具等浪费,可谓费时费力费资源。
3.不良浪费美国零缺陷大师克劳斯比说:“任何事情没有一步做到位都会造成额外或本。
”质量不良也不例外。
常见的不良浪费有:材料损失,设备折旧,人工损失,能源损失,价格损失,订单损失,信誉损失等。
4.动作浪费多余的动作、不合适的动作增加员工作业强度、降低生产效率,因此也是一种浪费。
常见的浪费动作有:两手空闲,单手空闲,作业动作停止,动作幅度过大,左右手交换,步行多,转身角度大,移动中变换动作,未掌握作业技巧,伸背动作,弯腰动作,重复动作及不必要动作。
5.加工浪费每提高一级加工精度将增加数倍甚至数十倍的费用。
过高的加工精度造成浪费,它付出了额外的成本,或造成了不必要的高质量。
精益生产七大浪费

1.直接的财务问题。说明库存和在制品增加,资金周转率低,制造时间变长,资金和利息被占用, 会造成库存空间的浪费,这在现金流量表中是很明显的。
2.产生次要问题。搬运和堆积会产生废物;先进先出的工作造成困难;产品积压导致不良品的发生, 物流阻断过程时间变长,现场工作空间变小,存在滞留仓库的风险和不良品的风险。
1. 优化工艺流程,对生产流程进行全面分析,找出其中的瓶颈和不必要的环节,进行优化和改进。 采用更高效的加工方法和设备,减少加工时间和工序。 2. 减少调整时间,通过标准化作业、快速换模等技术手段,减少设备调整和准备时间,提高设备的 利用率。 3. 提高加工精度,采用先进的加工技术和设备,提高加工精度,减少废品和返工,降低加工成本。 4. 引入自动化和智能化,利用自动化设备和智能化系统,提高生产的自动化水平,减少人工干预, 降低加工误差和浪费。 5. 加强质量控制,建立严格的质量控制体系,对原材料、半成品和成品进行严格检测,确保产品质 量符合标准,减少因质量问题导致的加工浪费。 6. 培训员工,加强员工培训,提高员工的技能水平和质量意识,使他们能够熟练掌握加工工艺和操 作方法,减少因操作不当导致的浪费。 7. 持续改进,建立持续改进的机制,鼓励员工提出改进建议,不断优化加工过程,提高生产效率和
5.建立持续改进文化
建立持续改进文化是实现精益生产的关键之一。通过建立持续改进文化,可以使员工充分认识到 浪费的危害和价值,从而积极参与到消除浪费的行动中来。例如,可以定期组织员工进行交流和 分享经验,以提高员工对精益生产的认识和实践水平。
(三)不良品的浪费
(1)不良品浪费对企业生产经营产生了诸多不利影响: (2)成本增加:不良品的产生会增加原材料、人力、设备等资源的浪费,导致生产成本的 增加。 (3)产能降低:不良品的产生会导致生产线停机、返工时间增加,进而降低了企业的产能。 (4)产品质量下降:不良品的产生会影响产品的质量,降低了产品的市场竞争力。 (5)顾客满意度下降:不良品的产生会导致交货延迟、产品质量问题等,降低了顾客的满 意度。
企业管理工作中常见的7种浪费.doc

企业管理工作中常见的7种浪费1为了能使经营管理革新活动深入有效地开展下去,我们首次提出管理工作中的七种浪费这个概念,来引导大家共同参与这项工作。
七种浪费之一:等待的浪费管理工作中的等待浪费主要有以下几种情况:等待上级的指示。
上级不安排工作就坐等,上级不指示就不执行,上级不询问就不汇报,上级不检查就拖着办。
算盘珠子不拨不动,缺乏主动精神。
你多干事多吃亏,出了问题怎么办?听从指示没有错,再大责任可分担。
很多工作的完成,是在几次检查、催办下完成的,造成极大的浪费。
等待外部的回复。
我已与你联系过了,静待回音,什么时候回复不是我能决定的,延误工作的责任应该由对方负责,我只能等。
等待其它部门或其他人的联系。
你不找我去协助,我就可以躲避,总有原因可以找,就说情况不清楚。
对其它相关工作不关心,没兴趣,多一事不如少一事,等就等吧,没啥了不起。
等待下级的汇报。
任务虽已布置,但是没有检查,没有监督。
不主动去深入实际调查研究,掌握第一手资料,只是被动地听下级的汇报,没有核实,然后作决定或向上级汇报,瞒天过海没有可信度,出了问题,责任往下级身上一推。
等待生产现场的联系。
较严重的等待是生产现场对于技术、品质、资材等部门服务、指导、指示、供应的等待,三现主义的缺乏是等待中的最致命原因之一,严重影响生产现场工作的及时解决。
上述情况,在工作中是大量存在的,这种缺乏工作责任心、主动性和工作积极性,满足现状、消极怠工的情况引发的浪费所造成的危害更大,危害企业的正常运行。
七种浪费之二:协调不利的浪费管理中相互配合、协调不利,造成工作停滞浪费主要有下述几种情况:工作进程的协调不利。
某项工作在两个部门间协调不利、交接不清,工作进度受到影响,相互之间都不主动联系。
某些工作应哪个部门负责没有明确界定,处于部门间的断层,工作缺乏协作精神和交流意识,都在观望停滞,认为应该别的部门负责,结果工作没人管了,原来的小问题被拖成了大问题。
领导指示的贯彻协调不利。
工作实际当中的7大浪费

工作实际当中的“七种浪费”七种浪费之一:等待的浪费等待就是闲着没事,等着下一个动作的来临,这种浪费是无庸置疑的。
造成等待的原因通常有:作业不平衡、安排作业不当、停工待料、品质不良等。
以性能试验课等待电控盘为例,由于电控盘不能按要求及时入厂,有可能无法按期交货,而当电控盘入厂后,又需要抢进度,可能会出现加班、质量问题等。
另有一种就是“监视机器”的浪费,有些工厂买了一些速度快、价格高的自动化机器,为了使其能正常运转或其他原因,例如:排除小故障、补充材料等等,通常还会另外安排人员站在旁边监视。
所以,虽然是自动设备,但仍需人员在旁照顾,特称之为“闲视”的浪费。
例如在产品检测过程中,调试人员和氦检人员站在产品旁边等待,这种情况是否还有?除了在直接生产过程中有等待外,其他管理工作中就没有等待这种浪费发生吗?当制造部在生产新产品发生一些问题时,技术部和品质保证部是否能立即解决而不需要现场人员长时间等待?如何减少这种等待?七种浪费之二:搬运的浪费大部分人皆会认同搬运是一种无效的动作,也有人会认为搬运是必须的动作,因为没有搬运,如何做下一个动作?很多人都有这种想法。
正因为如此,大多数人默认它的存在,而不设法消除它。
有些人想到用输送带的方式来克服,这种方式仅能称之为花大钱减少体力的消耗,但搬运本身的浪费并没有消除,反而被隐藏了起来。
搬运的浪费若分解开来,又包含放置、堆积、移动、整理等动作的浪费。
今年以来,生产管理部和制造部每月均对总生产工时进行汇总分析,发现在实际作业时间减少的同时,总工时却在增加,经仔细分析后发现,是两个工厂间的运输工时居高不下,特别是由二工厂向一工厂搬运原材料的工时占大多数。
怎么样克服?日本三洋大型课为减少搬运,把四个车间合并成两个,一些零部件的加工由原来在别处加工变成在生产线旁进行加工,从而减少搬运。
在不可能完全消除搬运的情况下,应重新调整生产布局,尽量减少搬运的距离。
大家可以考虑一下本公司的生产布局应该怎样变更?如何最大限度地减少搬运?七种浪费之三:不良品的浪费产品制造过程中,任何的不良品产生,皆造成材料、机器、人工等的浪费。
企业常见的七大浪费共7页

中国式现场管理之五十:企业常见的七大浪费企业常见的七大浪费现场混乱,插不进脚;员工仪容不整,两眼无光;物料混放,标志不清;设备故障不断,苟延残喘;人海战术,加班加点但还是要待工待料…这是国内不少企业的现状。
一切不增加对客户和企业价值的活动都是浪费。
在此前提下,企业每产一件产品就在制造一份浪费。
伴随企业运营中各业务环节不被察觉或不被重视的浪费,日本企业管理界将之形象地比喻为“地下工厂”。
日本专家通过长期的实践和研究发现,企业内有七种常见的浪费:1.等待浪费等待并非加工过程,不能改变物料的形状、尺寸、性质和状态从而改变韧料的功能,所以等待不创造价值。
待工和待料是两种最常见的等待情形。
常见的等待现象有:物料供应或前工序能力不足造成待料,监视设备作业造成员工作业停顿,设备故障造成生产停滞,质量问题造成停工,型号切换造成生产停顿。
造成等待的常见原因有:流水线能力不平衡,计划不合理,设备维护不到位,物料供应不及时等。
2.搬运浪费搬运也非加工过程,不能改变物料的形状、尺寸、性质和状态从而改变物料的功能,而且搬运过程中的放置、堆积、移动、整理等造成空间、时间、人力和工具等浪费,可谓费时费力费资源。
3.不良浪费美国零缺陷大师克劳斯比说:“任何事情没有一步做到位都会造成额外或本。
”质量不良也不例外。
常见的不良浪费有:材料损失,设备折旧,人工损失,能源损失,价格损失,订单损失,信誉损失等。
4.动作浪费多余的动作、不合适的动作增加员工作业强度、降低生产效率,因此也是一种浪费。
常见的浪费动作有:两手空闲,单手空闲,作业动作停止,动作幅度过大,左右手交换,步行多,转身角度大,移动中变换动作,未掌握作业技巧,伸背动作,弯腰动作,重复动作及不必要动作。
5.加工浪费每提高一级加工精度将增加数倍甚至数十倍的费用。
过高的加工精度造成浪费,它付出了额外的成本,或造成了不必要的高质量。
常见的加工浪费情形有:加工余量过大、过高的精度、不必要的加工等,其造成的浪费有:设备折旧、人工损失、辅助材料损失、能源消耗等。
精益生产之七大浪费及5S管理
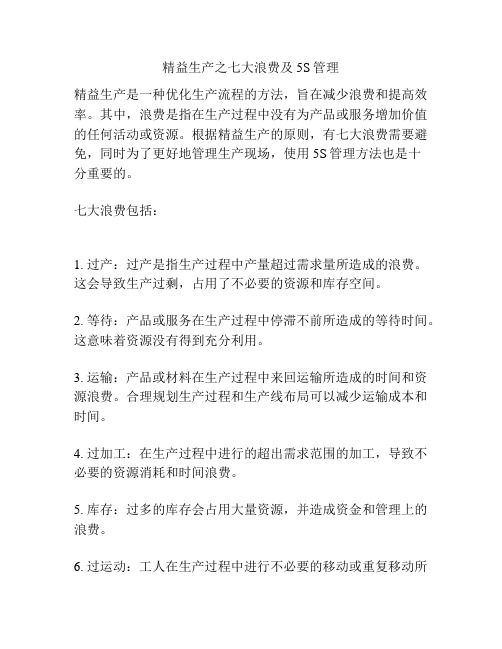
精益生产之七大浪费及5S管理精益生产是一种优化生产流程的方法,旨在减少浪费和提高效率。
其中,浪费是指在生产过程中没有为产品或服务增加价值的任何活动或资源。
根据精益生产的原则,有七大浪费需要避免,同时为了更好地管理生产现场,使用5S管理方法也是十分重要的。
七大浪费包括:1. 过产:过产是指生产过程中产量超过需求量所造成的浪费。
这会导致生产过剩,占用了不必要的资源和库存空间。
2. 等待:产品或服务在生产过程中停滞不前所造成的等待时间。
这意味着资源没有得到充分利用。
3. 运输:产品或材料在生产过程中来回运输所造成的时间和资源浪费。
合理规划生产过程和生产线布局可以减少运输成本和时间。
4. 过加工:在生产过程中进行的超出需求范围的加工,导致不必要的资源消耗和时间浪费。
5. 库存:过多的库存会占用大量资源,并造成资金和管理上的浪费。
6. 过运动:工人在生产过程中进行不必要的移动或重复移动所造成的浪费。
此外,工作场所的布局也可能导致不必要的运动。
7. 失效:产品或设备因为质量问题或故障导致不能正常使用所带来的浪费。
这包括废品、次品和修理等。
为了管理生产现场,5S管理方法可以帮助提高工作效率和质量。
5S分别代表整理、整顿、清扫、清洁和遵守。
1. 整理:整理工作场地,确定需要的物品和设备并清除不需要的物品。
2. 整顿:确定合理的工作流程和布局,确保工作区域的物品和设备放置得井井有条。
3. 清扫:保持工作区域的清洁和整洁,确保工作环境安全和舒适。
4. 清洁:定期进行清洁工作,包括设备和机器的保养和维护,以确保其正常运行。
5. 遵守:遵守标准和规定,执行工作流程,并及时纠正和改进。
精益生产的目标是通过减少浪费和提高效率来提供更高质量的产品和服务。
而5S管理方法可以帮助企业管理生产现场,提高工作效率和质量。
通过合理应用这些原则和方法,企业可以提升竞争力,并更好地满足客户需求。
精益生产的目标是通过减少浪费和提高效率来提供更高质量的产品和服务。
管理工作中的“七种浪费”

管理工作中的“七种浪费”本田生产方式中所归纳的“七种”浪费,主要再次发生在生产现场,但是消耗产生这些浪费的深层次的原因是什么?客观存在如果仅仅关注现场存在的问题,而不解决被现象所掩盖的本质问题,无疑是舍本逐末,即使表面上惊天动地,但实际效果也很有限。
为了多层面能使经营管理革新活动深入有效地开展下去,我们首次提出管理工作中的七种中均浪费这个范式,来引导大家共同可以参与这项工作。
七种浪费之一:等待的浪费管理工作中的等待浪费主要有以下情况:等待上级的指示。
上级不安排工作就坐等,上级不指示就不执行,上级不询问就不汇报,上级不检查就拖着办。
算盘珠子不拨不动,缺乏主动精神。
你多干事多吃亏,出了问题怎么办?听从指示没有错,再大责任可分担。
很多工作的完成,是在几次检查、催办下完成的,造成极大的浪费。
等待外部的回复。
我经已与你联系过了,静待回音,什么时候回复不是我能下定决心的,延误工作的责任应该由对方负责,我只能等。
等待机会其它部门或其他人的联系。
你不找我去协助,我就可以躲避,总有原因可以找,就说情况不清楚。
对其它相应工作不关心,没兴趣,多一事不如少一事,等就等吧,没啥了不起。
等待下级的汇报。
任务虽已布置,但是没有检查,没有监督。
不主动去深入实际调查学术研究,掌握第一手资料,只是被动地听下级的汇报,没有核实,然后作决定或向上级汇报,瞒天过海没法可信度,出了问题,责任往下级身上一推。
等待机会生产现场的联系。
较严重的等待是生产第二日对于技术、品质、资材等部门服务、指导、指示、供应的等待,“三现主义”的缺乏是等待中的最致命原因之一,严重影响生产当晚工作的及时生产解决。
上述情况,在工作中是大量存在的,这种缺乏组织工作责任心、主动性和工作积极性,满足现状、消极怠工的情况引发的浪费所造成的危害更大,危害企业的正常运行。
七种浪费之二:协调不利的浪费管理中相互配合、协调不利,造成工作停滞浪费两种主要有下述几种情况:教育工作进程的协调不利。
管理工作中的“七种浪费”
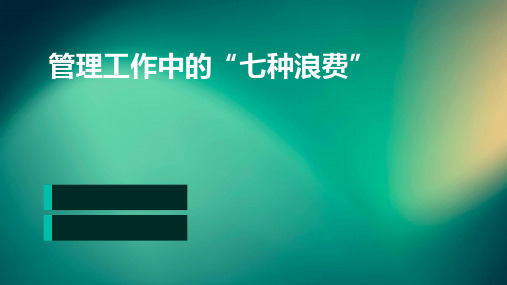
设备维护与更新
定期对设备进行维护和保养,及 时更新设备和技术,确保设备正 常运行,减少因设备故障导致的
时间浪费。
05 库存的浪费
定义
• 库存的浪费是指企业持有过多的原材料、在制品 和成品,这些库存不能及时转化为现金,导致企 业资源的浪费。
管理工作中的“七种浪费”
目 录
• 过量生产的浪费 • 等待的浪费 • 搬运的浪费 • 动作的浪费 • 库存的浪费 • 不良品的浪费 • 管理的浪费
01 过量生产的浪费
定义
01
过量生产的浪费是指生产或提供 超过实际需求或市场需求的物品 或服务所造成的浪费。
02
这种情况通常会导致库存积压、 增加存储和管理成本、降低资产 周转率等负面影响。
原因分析
01
02
03
操作流程不规范
缺乏明确的操作流程或流 程设计不合理,导致员工 在工作中出现混乱和重复 操作。
员工技能不足
员工缺乏必要的技能和培 训,无法高效地完成工作 任务,导致动作浪费。
设备维护不当
设备故障或维护不当,导 致工作效率降低,增加不 必要的动作和时间浪费。
解决方法
优化操作流程
通过制定明确的操作流程和规范, 减少重复和不必要的动作,提高
搬运的浪费是指生产过程中物料在存 放、移动、运输等环节中产生的无附 加价值的劳动和时间的消耗。
搬运的浪费通常表现为物料在生产线 之间的重复移动、过多的库存、不合 理的布局等。
原因分析
01
02
03
04
生产计划不准确
生产计划未能准确预测市场需 求,导致物料提前或延后到达
,增加了搬运次数。
- 1、下载文档前请自行甄别文档内容的完整性,平台不提供额外的编辑、内容补充、找答案等附加服务。
- 2、"仅部分预览"的文档,不可在线预览部分如存在完整性等问题,可反馈申请退款(可完整预览的文档不适用该条件!)。
- 3、如文档侵犯您的权益,请联系客服反馈,我们会尽快为您处理(人工客服工作时间:9:00-18:30)。
何谓浪费
何谓浪费:
不产生任何附加价值的
动作、方法、行为和计划
用不同的评判标准去判断 一个动作、行为、方法或计划时, 所得到的浪费程度都会不同。
现场活动包括“有附加价值的”和“没有附加价值的”活动,那些不产生附加价 值的活动应坚决予以消除
生产现场中的七种浪费概述 精益生产方式中所指出的浪费,和大家日常生活中所提到的浪费有着截 然不同的含义,即:在工业生产中,凡是不能直接创造价值的一切活动, 均视为浪费。 精益生产方式将所有浪费归纳成七种: ■等待的浪费; ■搬运的浪费; ■不良品的浪费; ■动作的浪费; ■加工的浪费; ■库存的浪费; ■制造过多(早)的浪费。
Ⅰ.产生不必要的搬运、堆积、放置、防护处理、找寻等浪费。 当库存增加时,搬运量将增加,需要增加堆积和放置的场所,需要增加 防护措施,日常管理和领用时需要增加额外时间等,甚至盘点的时间都 要增加,这些都是浪费。
库存是万恶的根源
6.七种浪费之六:库存的浪费(2) Ⅱ.使先进先出的作业困难。 当库存增加时,以钢板为例,新入厂的钢板压在原来的钢板上,先入库 的要想优先使用,就必须进行额外的搬运。而如果为省事,先使用新入 厂的钢板,原来的钢板长期放置会带来如生锈、划伤等一系列质量问题 的发生。
6.七种浪费之六:库存的浪费(1) 精益生产方式认为:“库存是万恶之源”。 这是丰田对浪费的见解与传统见解最大不同的地方,也是丰田能带给企 业很大利益的原动力。
精益生产方式中几乎所有的改善行动皆会直接或间接地和消除库存有关。 精益生产方式为什么将库存看做是万恶之根源,而要想尽办法来降低它 呢?因为库存会造成下列的浪费:
Ⅲ.损失利息及管理费用。
当库存增加时,用于生产经营活动的资金会大量沉淀在库存上,不仅造 成资金总额增大,还会增加利息和库房的管理费用。而这些常常是隐含 在公司的管理费用中,只有专门列出,才能发现存在问题的严重性,进 而正视它,并努力解决。
6.七种浪费之六:库存的浪费(3) Ⅳ.物品的价值会减低,变成呆滞品。 当库存增加时,库存量会大于使用量,甚至会造成长期的积压,特别是 当产品设变时,这种问题可能会显得更加严重。 原来为了保证能按时交货,过多的准备了生产用原材料、单品等,当顾 客发出设计变更时,原来库存品有可能将不能使用,从而造成大量物资 的积压。 为处理这些积压物资,只能当作废钢、废料进行处理,从而造成实际价 值降低,成本升高,利润减少。 想一想库存中的积压物资,当初是以什么价格购入,而目前的价格是多 少,就会明白了。
2.七种浪费之二:搬运的浪费(2) 实例: 日本三洋在对生产管理部和制造部每月均对总生产工时进行汇总分析时, 发现在实际作业时间减少的同时,总工时却在增加,经仔细分析后发现, 是两个工厂间的运输工时居高不下,特别是由二工厂向一工厂搬运原材料 的工时占大多数。怎么样克服?日本三洋大型课为减少搬运,把四个车间 合并成两个,一些零部件的加工由原来在别处加工变成在生产线旁进行加 工,从而减少搬运。在不可能完全消除搬运的情况下,应重新调整生产布 局,尽量减少搬运的距离。 大家可以考虑一下本公司的生产布局应该怎样变更?如何最大限度地减少 搬运?
1.七种浪费之一:等待的浪费(1) 管理工作中的等待浪费主要有以下几种情况: ●等待上级的指示。 -上级不安排工作就坐等,上级不指示就不执行,上级不询问就不汇报,上 级不检查就拖着办。 -算盘珠子不拨不动,缺乏主动精神。 -觉得多干事就多吃亏,一旦出了问题怎么办?听从指示没有错,再大责任 可分担。 -所以很多工作的完成,是在几次检查、催办下完成的,造成极大的浪费。 ●等待外部的回复。 -我已与你联系过了,静待回音,什么时候回复不是我能决定的,延误工作 的责任应该由对方负责,我只能等。 -等待其它部门或其他人的联系。 -你不找我去协助,我就可以躲避,总有原因可以找,就说情况不清楚。 -对其它相关工作不关心,没兴趣,多一事不如少一事,等就等吧,没啥了 不起。
.七种浪费之一:等待的浪费
等待就是闲着没事,等着下一个动作的来临,这种浪费是无庸置疑的。 造成等待的原因通常有:作业不平衡、安排作业不当、停工待料、品质 不良等。
另有一种就是“监视机器”的浪费,为了使自动设备能正常运转,例如: 排除小故障、补充材料等等,通常还会另外安排人员站在旁边监视。所 以,虽然是自动设备,但仍需人员在旁照顾,特称之为“闲视”的浪费。 当制造部在生产新产品发生一些问题时,生产技术部和品管部是否能立 即解决而不需要现场人员长时间等待? 如何减少这种等待需要大家加以反思。 反思在KTC中是否存在的等待浪费现象?
第二部分
管理中的“七种浪费”
管理工作中的七种浪费概述
丰田公司的精益生产方式中所归纳的“七种”浪费,主要 发生在生产现场,但是产生这些浪费的深层次的原因是什 么?
如果仅仅关注现场存在的问题,而不解决被现象所掩盖的 本质问题,无疑是舍本逐末,即使表面上轰轰烈烈,但实 际效果也很有限。 为了能使经营管理革新活动深入有效地开展下去,我们首 次提出管理工作中的七种浪费这个概念,来引导大家共同 参与这项工作。
7.七种浪费之七:制造过多(早)的浪费(1) 上面提到库存是万恶之源,而制造过多或提早完成,在丰田则被视为最大 的浪费。 精益生产方式所强调的是“适时生产”,也就是在必要的时候,做出必要 的数量的必要的东西。此外都属于浪费。而所谓必要的东西和必要的时候, 就是指顾客已决定要买的数量与时间。 假设客户只要100个,而每个1元,如果生产了150个,这售价却不会是150 元,因为多余的50个并没有卖出去,仅是变成库存,因此利润也就无从产 生,换句话说,多做了是浪费。 而制造过早同样也是浪费,但为什么有很多工厂会一而再地过多与过早制 造呢?最大的原因在于他们不明白这是一种浪费,反而以为多做能提高效 率,提早做好能减少产能损失。 (不做白不做,机器还不是一样停着?),显然这是一种极大的误解。
4.七种浪费之四:动作的浪费 要达到同样作业的目的,会有不同的动作,哪些动作是不必要的呢? 是不是要拿上、拿下如此频繁? 有没有必要有反转的动作、步行的动作、弯腰的动作、对准的动作、直角 转弯的动作等?
若设计得好,有很多动作皆可被省掉!
在管理理论中,专门有一种“动作研究”,但实施起来比较复杂,我们完 全可以用上述的基本思想。
6.七种浪费之六:库存的浪费(5) Ⅵ.设备能力及人员需求的误判: 由于库存量的存在,设备能力不平衡时也看不出(库存越多,越不容易看 出来)。人员是否过剩,也无法了解。由于有较多的库存,供应部门需要 增加人员,制造一线需要更多的人员来生产产品用于补充库存,需要增添 设备来保证生产库存所需要的设备能力,从而形成新一轮的浪费。 到底为什么要有库存量,最大的理由是“怕出问题”——出现故障怎么办? 会不会因部分设备出问题,而影响整条生产线或工厂的生产呢? 于是乎为了不使影响扩大,库存便成了必要,众多的问题也被隐藏起来, 所有进步、赚钱(发现问题、解决问题就是赚钱)的步调自然变慢了。无 怪乎精益生产方式称库存为万恶之源,绝对不允许它存在,如果现在已经 有了库存,也要行进一切办法,将之降低,力争零库存。 (注:零库存的“零”并非指数学意义上的“完全没有”的意思,而是指 把库存“尽量减到最少的必要程度”。)
上面简单地介绍了七种浪费的概念,但所提出的问题仅是冰山露 出海面的部分,大量的问题隐藏在水面之下,而且生产现场中的 问题由于目视可见,解决起来相对容易一些,而管理部门存在的 问题则隐藏较深,解决起来较困难,但如果解决了,则见效大。 真正从思想上认清“浪费”带来的危害,从而真正在行动上去消 除“浪费”,降低成本,提高效率,增加效益。
2.七种浪费之二:搬运的浪费(1)
主要指不必要的移动或把东西暂放在一旁的搬运过程 如:搬运的距离很远; 小批量的运输; 出入库次过多等。
搬运的浪费若分解开来,又包含放置、堆积、移动、整理 等动作的浪费
有些人想到用输送带的方式来克服,这种方式仅能称之为 花大钱减少体力的消耗,但搬运本身的浪费并没有消除, 反而被隐藏了起来。
6.七种浪费之六:库存的浪费(4) Ⅴ.占用厂房空间,造成多余的工场、仓库建设投资的浪费。 当库存增加时,就需要额外增加放置场所。当生产旺季的时候,库存品 增加,使用场地面积不够,从而投资扩建;但当生产淡季的时候,以前 放置区又会长时间闲置,投资回报率下降,造成浪费。 另外,因库存所造成的无形损失,绝不亚于上述的有形损失,精益生产 方式认为库存会隐藏问题点,而“问题”在精益生产方式中被认为是宝 藏,问题如果能不断地被发现解决,则利益便会不断地产生。库存隐藏 问题点,造成下列后果: 没有管理的紧张感,阻碍改进:库存量一多,因机械故障、不良产品所 带来的不利后果不能马上显现出来,因而也不会产生对策。由于有了充 足的库存,出现问题时可以用库存先顶上,问题就可以慢慢解决甚至不 用解决,最起码是被掩盖住了,不急迫了,不会被上级追究了,于是乎 本部门的工作成绩就出来了。
培训教材
第一部分
现场工作的“七种浪费”
引言
竞争力提升
品质提升
合理化成本降低
形象提升
改
善
动作改善、作业流程改善、物流改善、设 备模 夹治具改善、品质改善、管理改善等 浪费 动作标准化、作业流程标准化、操作流程 标准 化、包装运输标准化等 整理、整顿、清扫、清洁、素养等
消除浪费 标 准 化 现场5S
3.七种浪费之三:不良品的浪费 产品制造过程中,任何的不良品产生,皆造成材料、机器、人工等的浪费。 任何修补都是额外的成本支出。精益的生产方式,能及早发掘不良品,容 易确定不良的来源,从而减少不良品的产生。这一条比较好理解,关键是 第一次要做正确,但实施起来却很困难。 精益生产方式的思想之一就是要用一切办法来消除、减少一切非增值活动, 例如检验、搬运和等待等造成的浪费,具体方法就是推行“零返修率”, 必须做一个零件就合格一个零件,第一次就做好,更重要的是在生产的源 头就杜绝不合格零部件、原材料流入生产后道工序,追求零废品率。 消除不良品要从源头抓起,从产品的设计阶段、零件加工阶段、生产作业 阶段、包装阶段等各个方面考虑如何减少不良品的产生。