OE品质工程师核心技能提升培训01
品质工程技能系统与提升培训班
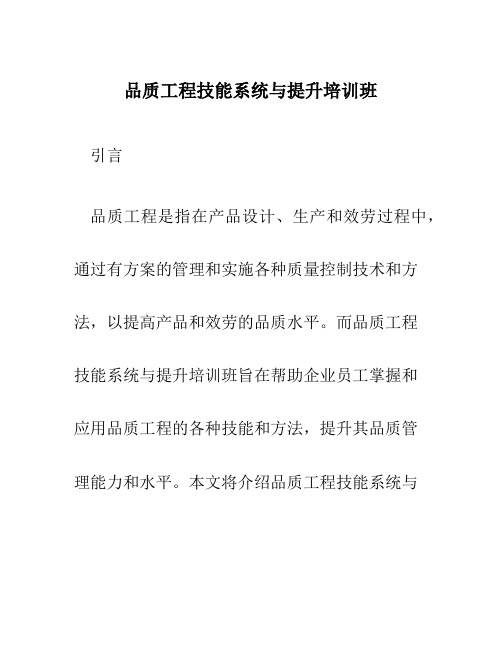
品质工程技能系统与提升培训班引言品质工程是指在产品设计、生产和效劳过程中,通过有方案的管理和实施各种质量控制技术和方法,以提高产品和效劳的品质水平。
而品质工程技能系统与提升培训班旨在帮助企业员工掌握和应用品质工程的各种技能和方法,提升其品质管理能力和水平。
本文将介绍品质工程技能系统与提升培训班的内容和目标,以及它对企业和员工的价值和意义。
品质工程技能系统与提升培训班的内容和目标品质工程技能系统与提升培训班的内容包括以下几个方面:1.品质管理根底知识:介绍品质管理的根本概念、原理和方法,帮助员工了解品质管理的重要性和作用;2.测量与检验技术:介绍各种测量和检验技术,如测量仪器的使用和校准、统计抽样等,以帮助员工掌握合理的测量和检验方法;3.缺陷分析与问题解决:介绍常见的缺陷分析和问题解决方法,如鱼骨图法、五问法等,以及如何制定改良措施和跟踪效果;4.过程能力评估与改良:介绍过程能力评估的方法和工具,如流程图绘制、SPC等,以及如何分析和改良过程能力;5.变革与创新管理:介绍变革和创新管理的根本原理和方法,帮助员工主动适应和应对市场变化;6.团队合作与沟通技巧:培养员工团队合作和沟通的能力,提高团队协作效率和工作质量。
品质工程技能系统与提升培训班的目标是:1.提高员工的品质管理意识和能力,增强其对品质的责任感和主动性;2.培养员工的问题解决和改良能力,提高工作效率和生产质量;3.增强员工的团队合作和沟通能力,提高团队的协作效果;4.推动企业品质管理水平的提高,提升企业竞争力。
品质工程技能系统与提升培训班对企业和员工的价值和意义品质工程技能系统与提升培训班对企业和员工都具有重要的价值和意义。
对企业而言,它可以帮助企业提高产品和效劳的品质水平,提升企业在市场竞争中的地位和竞争力。
首先,品质工程技能系统与提升培训班可以帮助企业员工掌握各种品质管理技能和方法,提高其对产品和效劳的质量要求和标准的认识。
其次,培训班可以培养员工的问题解决能力和改良意识,促进持续改良和创新,提升产品和效劳的质量水平。
最新OEE培训讲义

I.OEE 的组成
OEE=Availability ×Performance efficiency ×Quality rate
设备综合效率=时间稼动率×性能稼动 率×合格品率
焦点:它衡量的目的在设备及制程的改 善,而不是对人的评价。
OEE培训讲义
2017-10-16
注意事项
欢迎大家参加本次课程,本课程将为您 打下一个基本的OEE知识基础,提高您的能 力和水平.请提前5分钟到场签到;
请注意以下的几点: 1、手机 上课期间请将您的手机开为振动
或关闭. 2、吸烟 在课堂内请不要吸烟. 3、其它
上课期间请不要大声喧哗, 举手提问, 不要随意走动.
结束语:
谢谢大家
重点:掌握造成OEE低下的各类型损失, 并加以改善。
II.OEE挂图
III.OEE的损失结构图
IV.OEE的计算---Availability时间稼动率
Availability的计算练习
Availability = B / A [练习] 某公司每班上班总时间为540分钟,其中用餐时间与
IV.OEE的计算---Performance性能稼动率
Performance的计算练习C
Performance = D / C [练习] 某公司每班上班总时间为540分钟,其中用餐时间与休
息为60分钟,上班前的交接班为10分钟,每班操作前 点检时间额定为10分钟。A=540-60-10-10=460 7月5日每班订单量为10k,每个的生产标准时间为2.76 秒,当日切换工程与调整总共花了30分钟,设备中途 故障与修复总时间为15分钟。另外这一班生产过程中 小停止10次,每次额定估算值为2分钟15=415, C=B*60/2.76=9021, D=9000, D/C=9000/9021=0.997 请计算这一班的Performance.
经典OEE培训教材

• 应对措施
– 了解损坏的原因及发生的时间和地点,然后运用根源问题解决 办法来解决
– 使用SMED技术来减少甚至消除设置调整的必要,并实现标准 化的第一轮通过流程
– 如果因为进线部件和原材料的变化而导致损坏,从而需要进行
调整来补偿就要建立部件质量拒收的限制,并使供应商质量管
理也参与到此管理流程
12
6. 质量缺陷
16
质量缺陷
计划外停 机
机器故障
速度下降
换线
损坏
4
OEE计算 – 模型
可编辑
六种重大损失降低机器效能说明
一班总工作时
可使用总工时
操作时间(停工时间 损失)
机器运转时间 (速度损失)
增值 (缺陷损失)
* 计划内停工排除在OEE计算之外
计划内停工*
机器故障 换线 计划外停工 速度降低 损坏 质量缺陷
可用时间 = (可使用总工时) - (窝工时间损失) (可使用总工时)
• 由PLC控制器衡量
• 应对措施 – 明确实际设计速度,最大速度,以及造成速度受限的物理原因 – 请工程人员进行程序检查并进行修改 – 应用Machine Kaizen来查找低速的原因并对设计速度提出质 疑
11
5. 损坏
可编辑
• 定义:工艺处理流程中,即“线上”即被查出的部件
• 由手写废品记录登记测量(注:假设每个部件的损坏造成生产该 部件全部时间的损失,从而将损坏部件数量转化为时间损失)
• 除机器故障或换线的所有计划 管理 外的停产 • 问题根源解决方法
• 由于机器运行速度较设计速度 慢而造成的时间损失 • 问题根源解决方法
• 在组装或调整中的损坏部件 • 问题根源解决方法
oee培训ppt课件
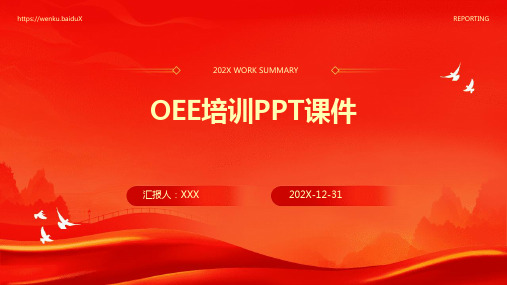
OEE培训PPT课件
汇报人:XXX
202X-12-31
REPORTING
目录
• OEE基本概念 • OEE的重要性和影响 • 如何提高OEE • OEE的监控与改进 • OEE的未来人和时间节点,确保措施的 有效执行。
对改进措施进行风险评估和经 济效益分析,确保措施的公道 性和可行性。
跟踪改进效果
实施改进措施后,持 续监测OEE数据的变 化情况,评估改进效 果。
根据跟踪结果,及时 调整和优化改进措施 ,持续提高OEE水平 。
对改进效果进行统计 分析和可视化展示, 便于团队成员了解改 进成果。
下落生产成本
提高装备效率可以下落生产成本,因为装备效率的提高意味 着生产进程中所需的人力和物力资源更少,能源消耗更低, 从而下落了生产成本。
OEE培训可以帮助员工更好地掌握成本控制的方法和技能, 通过优化生产流程、减少浪费等措施,进一步下落生产成本 。
提升产品质量
01
装备效率的提高可以提升产品质 量,因为装备的稳定高效运行可 以减少产品缺陷和不良品率。
PART 04
OEE的监控与改进
OEE数据收集与整理
确定数据收集的指标
根据装备特点和生产要求,确定需要收集的OEE指标,如开机率 、故障率、准备时间等。
制定数据收集计划
确定数据收集的时间间隔、采集人员和采集方式,确保数据的准确 性和实时性。
数据整理与存储
对收集到的数据进行整理、分类和存储,便于后续的分析和查询。
备用装备
配备备用装备,在主装备故障时,能 够迅速切换到备用装备,保证生产连 续性。
提高操作员技能
培训教育
定期对操作员进行技能培训和安 全教育,提高操作员的专业素养
OEE培训教材[1]
![OEE培训教材[1]](https://img.taocdn.com/s3/m/ca50586a33d4b14e84246895.png)
小组名
小组成员
4.掌握实际 情况
1.对损失进行 鉴别/分类
短时临时停工
停机时间分层处理
100%
现象鉴别
2.选择主题 并证明
3.了解工艺/ 设备
5.确定目标 目标
机理 原理
减少○○小停机
6.制定计划
8.提出对策
实施QC的详 细措施清单
7.原因分析
实施部署计划 (谁、什么、 怎么样、何时)
其中它是先做6大损失到9大损失到12大损失不断的摸索 才有今天的成绩。数据显示联合利华洗衣粉的产量从2004 日产260T/D到2010年日产近1000T/D。其中生产机器只增 了50%。在OEE的数据支撑下结合一些优良的管理方法再 加上公司员工的群策群力下设备的效率平均提高了48.6%
OEE对洽洽是一个陌生的管理方法,对我们来说OEE的 引进是对洽洽百利无一害的。同时联合利华给了我们一个 好的启示和带头作用。
–生产效率PE (E/P) –操作效率OE (E/O)
l 利用率:
–资产利用率AU (U/T) –操作利用率OU (O/T) –生产利用率PU (P/T) –有效利用率EU (E/T) …
OEE培训教材[1]
OEE 表格
原来
修改制作
在修改的
你会选择那种表?
OEE培训教材[1]
中国员工的画像
l 海尔总裁张瑞敏关于人的品质有一段精彩的论述; “如果训练一个日本人,让他每天擦六遍桌子,他一定
l
生产维修
OEE培训教材[1]
TPM是由八大支柱组成的
World Class Manufacturing 世界级工厂
5S VCS 活动
OEE培训教材[1]
质量管理OE意识培训 赵晓敏精品文档86页PPT

6、最大的骄傲于最大的自卑都表示心灵的最软弱无力。——斯宾诺莎 7、自知之明是最难得的知识。——西班牙 8、勇气通往天堂,怯懦通往地狱。——塞内加 9、有时候读书是一种巧妙地避开思考的方法。——赫尔普斯 10、阅读一切好书如同和过去最杰出的人谈话。——笛卡儿
1、不要轻言放弃,否则对不起自己。
2、要冒一次险!整个生命就是一场冒险。走得最远的人,常是愿意 去做,并愿意去冒险的人。“稳妥”之船,从未能从岸边走远。-戴尔.卡耐基。
梦 境
3、人生就像一杯没有加糖的咖啡,喝起来是苦涩的,回味起来却有 久久不会退去的余香。
质量管理OE意识培训 赵晓敏精品文档 4、守业的最好办法就是不断的发展。 5、当爱不能完美,我宁愿选择无悔,不管来生多么美丽,我不愿失 去今生对你的记忆,我不求天长地久的美景,我只要生生世世的轮 回里有你。
OEE培训资料ppt课件
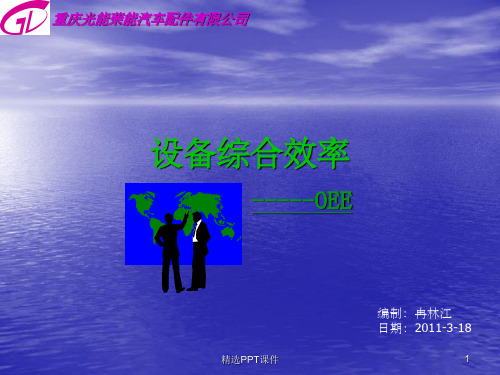
精选PPT课件
15
重庆光能荣能汽车配件有限公司
谢 谢 大 家!
精选PPT课件
16
1. 停工和故障的损失 设备失效需要执行维护操作。其原因有:
–机器过载 –螺钉和螺帽松开 –过渡磨损 –缺少润滑油 –污染物
4. 降低速度的损失
设备在低于其标准设计速度运行导致的 损失。其原因有:
–机器磨损 –人为干扰 –工具磨损 –机器过载
2. 换装和调试的损失
从一种产品到另一种产品换产的时间损 失,或运行时对设置的改动。其原因有:
2. 设备效率损失的分类
大分类 计划损失 停止损失 性能损失 不良损失
中分类 交班时间/就餐/休息/生产中断/预防维修 设备故障/动力事故/换产/流量不足 流量调节/资材短缺/品质问题
瞬间停止/速度降低/空转
不良/再作业
Hale Waihona Puke 公司认可的损失影响OEE 的损失
精选PPT课件
7
重庆光能荣能汽车配件有限公司
影响OEE的六大损失
重庆光能荣能汽车配件有限公司
设备综合效率
-----OEE
精选PPT课件
编制:冉林江 日期:2011-3-18
1
重庆光能荣能汽车配件有限公司
OEE(设备综合效率)
01.设备综合效率的定义 02. 设备效率损失的分类 03. 设备综合效率的计算
精选PPT课件
2
重庆光能荣能汽车配件有限公司
1.设备综合效率的定义
多数企业的OEE标准
世界级企业的OEE标准
废品/返工8%
准备时间10%
设备OEE 50%
停机13%
小中断19%
精选PPT课件
5%
设备OEE培训ppt课件

方案停机时间
非方案停机时间
1.一级保养时间 2.交接班时间 3.中午吃饭时间 4.其他方案停机时间
1.缺点时间 2.工艺调试时间 3.其它方案外停机时间
时间开动率=〔方案时间-非方案时间〕/ 方案时间*100%
OEE的目的
OEE的一个最重要目的就是减少普通制造业所存在的六大 损失:停机损失、换装调试损失、暂停机损失、减速损失、 启动过程次品损失和消费正常运转时产生的次品损失。
甲班的合格率100加工数量10设备的六大损失和oee的关系设备六大损失加工数量不合格数量合格率100加工数量负荷时间停止时间时间开动率100负荷时间理论循环时间加工数量性能开动率100利用时间设备综合效率的计算负荷时间可利用时间真正利用时间创造价值的运转时间1
设备综合利用率—OEE
主讲人:胡楚平 2021-3-30
加工数量
OEE案例
设某设备某天任务时间为8h, 班前方案停机15min, 故 障停机30min,工装调整25min, 产品的实际加工周期 为0.6 min/件, 一天共加工产品450件, 有20件不合格, 求这台设备的OEE? 根据上面可知: 方案运转时间 =8 x 60 -15 =465 (min) 实践运转时间 =465-30-25=410 (min) 时间开动率 =〔410/465〕*100%=88.1% 性能开动率 =〔450*0.6〕/410*100%=65.8% 合格品率 =〔450—20〕/450*100%=95.5% OEE = 时间开动率x性能开动率x合格品率=55.4%
• OEE是一个独立的丈量工具,它用来表现实践的消费才干相对于实际产 能的比率。国际上对OEE的定义为:OEE是设备综合效率的缩写,它由 时间开动率,设备性能开动率以及产品合格率三个关键要素组成
OEE基础入门

OEE的定义OEE是Overall Equipment Effectiveness(全局设备效率)的缩写。
一般,每一个生产设备都有自己的理论产能,要实现这一理论产能必须保证没有任何干扰和质量损耗。
OEE就是用来表现实际的生产能力相对于理论产能的比率,它是一个独立的测量工具。
OEE是由可用率,表现性以及质量指数三个关键要素组成:OEE=可用率*表现指数*质量指数其中:可用率=操作时间/计划工作时间它是用来评价停工所带来的损失,包括引起计划生产发生停工的任何事件,例如设备故障,原材料短缺以及生产方法的改变等。
表现指数=理想周期时间/(操作时间/总产量)=(总产量/操作时间)/生产速率表现性是用来评价生产速度上的损失。
包括任何导致生产不能以最大速度运行的因素,例如设备的磨损,材料的不合格以及操作人员的失误等。
质量指数=良品/总产量质量指数是用来评价质量的损失,它用来反映没有满足质量要求的产品(包括返工的产品)OEE基础入门——OEE系列知识培训之一随着市场竞争的日趋激烈,生产企业要想持续获得理想的效益,其中一个重要环节就是要持续提升其生产效率——在具有“制造大国”之称的中国的今天,效率已成为众多企业是否可以赢利的关键甚至是决定性因素。
然而,中国目前大部分生产企业,特别是民营生产企业,其表面上看似良好运作的生产车间实际上并没有以最好的状态进行工作,设备和操作人员的价值存在很大的改善空间,这无形中为企业造成了巨大的损失。
但是,绝大多数企业的管理人员并没有意识到这一点,或者说只是有感观上的感觉,但缺乏定量的数据,而没有采取有效的措施予以解决。
为了解决这一问题,国际制造业提出了全局设备效率(OEE)的概念。
全局设备效率OEE是一种简单实用的生产管理工具,在欧美的制造业和中国的跨国企业中已得到广泛的应用,全局设备效率指数已成为衡量企业生产效率的重要标准,也是TPM(Total Productive Maintenance)实施的重要手法之一。
OEE培训教材资料
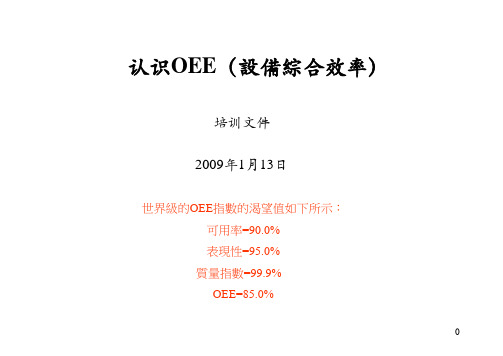
2、分析說明
根據OEE系統所提供的資料,你可以方便的知道自己工廠存在什麼問題,例如, 如果你的可用率在某一個時間段很低,說明在六大損失中和OEE可用率損失有關的 故障太多,那麼,顯而易見,你應該把改善重點放在這些方面了!同樣,如果質量 指數或者生產率導致你的OEE水準降低,那麼你就應該把目光放在和它們有關的問 題點上。在表一中,我們只列舉了一些事件原因,其實它可以包括和生產有關的任 何方面,因此,你可以對生產做到全面的管理和改善。
設備預熱,調試等生產正式運行之前產 • 问题根源解决方法 生的次品 生產穩定進行時產生的次品
■
• 问题根源解决方法
十三、使用OEE时的注意事项
!
!
• OEE要应用在一台机器上(可视为一台机器的生产线) 而不能应用在整个生产线或全厂上,这样才有意义
• OEE要作为一系列一体化的综合关键业绩指标中的一部 分来运用而不能孤立使用,否则将造成生产批次规模加大 或有质量缺陷的产品 • OEE必须与精益原则相符,要确保对OEE的计算不会导 致浪费合理化、制度化,例如,绝不要允许给换线留出 时间
理系統。
2、能分析/跟蹤生產線設備的有效利用情況,以便最大
化挖掘設備生產潛力。
3、能分析/跟蹤產線上的潛在風險和六大損失,以便降
低生產成本、提高生產力。
4、能為企業精益生產管理提供可視化的生產報告。 設備:降低設備的故障以及維修成本,加強設備管理以延長設備 的使用壽命。 員工:通過明確操作程式和SOP,提高勞動者的熟練程度和有效 工作業績,從而 提高生產效率。 工藝:通過解決工藝上的瓶頸問題,提高生產力。 質量:提高產品直通率(FTT),降低返修率,減少質量成本,
认识OEE(設備綜合效率)
培训文件 2009年1月13日
质量管理OE意识培训 - 赵晓敏
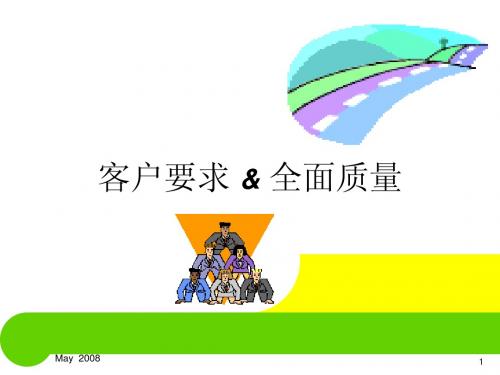
May 2008
12
全球采购和全球化
全球化
消除本地供应风险和 低成本国家再供应风险
May 2008
13
三种策略结合
全球化
低成本国家再供应
本地供应
国际化的供应商 供应商国际协作 在低成本国家开发资源,逐步向工业国出口
May 2008
14
OEM对供应商的期待
目标: 零缺陷
一直积极致力于降低成本
May 2008
10
本地化的优势
快速反应本地需求
省去运输
省去中转时间 省去具有风险的复杂进口程序 避免远距离管理供货商 避免了汇率风险
May 2008
11
全球化的优势
全球化的供应商有能力在全球供应
采购量 = 采购能力 更少的供应商 = 更多的时间和供应商共同工作 标准化 一 个解决方案= 降低成本和缩短开发周期
实施解决方案
May 2008
65
PDCA方法
检查CHECK
6. 检查结果
Check
检查结果
May 2008
66
PDCA方法
ACT标准
7. 将解决方案标准化 8. 推广解决方案 9. 交流成功经验 交流成功经验
推广解决方案
将解决方案标准化
Act
May 2008
67
你运用那些质量工具 ?
May 2008
21
日程安排
简介 全面质量的定义 从质量控制到全面质量 全面质量的原理和方法 三个阶梯图的简介
May 2008
22
定义
质量是 ?
构成一个企业的整体特征,它使该企 业有能力满足各种提出的和未提出的 需求
OEE培训[1]
![OEE培训[1]](https://img.taocdn.com/s3/m/a6d1d39948649b6648d7c1c708a1284ac85005cc.png)
解决方案
处理6大OEE损失
废品
产品或服务未达到制定的生产规范或客户要求
通过防误措施消除问题源 人工自动化(停止生产线,辨识和呼叫)-授权工人在发生意外情况或发现问题时,停止生产线
返工
产品需要非标准操作,以满足客户的规范要求(例如,产品在生产过程中损坏,需要维修)
损失
解决方案
OEE用作测量能力的方法
OEE
0.78
0.70
0.45
0.48
0.77
0.75
有效生产交期* (秒) (秒)
观测的 周期 生产交期
由于OEE损失导致生产交期调整
日程
整体设备效率(OEE) 什么是OEE? OEE计算 OEE的优点 结论 附录:OEE练习
主要着重点
OEE是一种监控和改进生产流程的有效性的有用的方法* OEE使我们可以清楚地看见六大主要生产能力损失: 停机 换模 轻微停机 速度降低 废品 返工 多个TEOA工具用作OEE的改进杠杆
OEE培训
学习目标
本课程结束时,您将学会: 解释确定整体设备效率(OEE)的目的 描述计算OEE时的步骤 理解OEE如何作为TEOA的一部分帮助推动绩效
日程
整体设备效率(OEE) 什么是OEE? 计算OEE 将OEE与绩效联系起来 结论 附录:OEE练习
什么是OEE?
定义:一种车间的工具,用于测量生产设备的运行状况,并与理论目标进行对比。
基于时间OEE =部件的理论生产数量部件的实际生产数量
基于部件
* 取决于时间和(或)部件数据的可用性
计算OEE – 范例
可用性 =
预计的 生产时间 生产时间
操作时间
480分钟
360分钟
OEE培训材料ppt课件
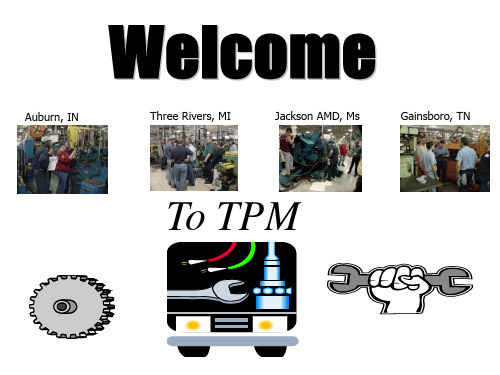
Three Rivers, MI
Jackson AMD, Ms
Gainsboro, TN
To TPM
六种损失对设备可生产时间的影响
8 小时
总机器可用时间
设备可用性角 度衡量
总可操作时间
6小时
停机损失
剩余操作时间
4.8小时
生产效率角度衡 量
速度损失
最终可操作时间 不良损失
3.2 小时
2. Observe proper "Lockout/Tagout" procedures when shutting down your equipment
for cleaning.
3. Systematically clean each part of the equipment using the checklist on the next
TPM Services
美国工厂 平均水平
30-45% OEE
55-70%
损失
隐藏的工厂
最大产
85% OEE 15%
损失
能
世界级
TPM Services
OEE
如何计算OEE
设备有效性 X 生产效率 X 质量结果
停机 换型 & 调整 其他
等待 & 微小停机 速度减缓
制程不良 开机或换型不良
提醒: OEE 衡量制造过程中的六种损失
page.
Note: An "abnormal condition" is defined as any condition within, or around the machine that affects the appearance and performance of the machine or production cell. a "normal condition" is defined as a condition in which the machine's appearance and performance is in "like new" condition and no waste is generated in time, resources, or materials. An abnormal condition can be a broken bolt, a leak, a worn or damaged part, it can also be a dirty part. As you document these conditions on your "Abnormality Summary Sheet" try and discover the reasons for them. Ask yourself the following questions:
OE品质工程师核心技能提升培训02

4 3
1 2
检查 销售
制 造
戴明循环
11
KEEP ON GOING FOR EXCELLENCE
质量管理
2.4
品质管理原则— 品质管理原则
ISO 9001
注意顾客: 注意顾客 须了解顾客现在及未来期望, 须符合顾客要求,并努力超越顾客期望. 下过程就是顾客. 领导统御: 领导统御 建立组织共同一致的目的及方向. 须刨造及维持使人员能够全力投入的内部环境. 全员参与: 全员参与 各阶层人员须完全的参与贡献能力.
KEEP ON GOING FOR EXCELLENCE
23
质量管理
4.4 供应链的品质管理
关系:相互依存 相互信赖 关系 相互依存.相互信赖 顾客第一 相互依存 相互信赖,顾客第一 供应链是左轮.公司是右轮 供应链是左轮 公司是右轮 供应链的品质管理 1.零件品质的目标管理 2.制造过程的稽核与辅导 3.品质变化的管理活动 4.品质改进的活动
[费根堡(Feigenbaum)所提倡] f. TQM:全面品质管理(Total Quality Management)
17
KEEP ON GOING FOR EXCELLENCE
质量管理
3.2
全面品质管理的意义
TQM
在所有阶段中 QC的想法.看法 由所有部门.所有 人员一起参与 活用QC手法 进行体系化活动
(precontrol)
27
KEEP ON GOING FOR EXCELLENCE
质量管理
5. 2 品质定义的扩大
1.ISO9001:1994版: 2.品质: 反应实体满足明 确和隐含需要的能力的 特性总合 3.不合格:没有满足某个 规定的要求 4.缺陷:没有满足某个预 期的使用或合理的期 望, 包括与安全性有关的要 求.
如何提升OEE—重要PPT课件
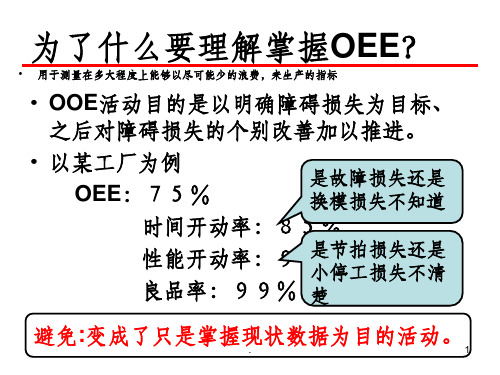
例)机械加工工序:刀具交换、锻造工. 序:模型故障
15
六大损失分析
首先为了要掌握各个损失的大小、绘制下列的图表。
上班时间 生产时间 负荷时间 开动时间 实质开动时间 价值开动时间
分
时间开动率
分
性能开动率
分
生产外时间
分
良品率
100% 计划停止
分
分
OEE
分 停止损失
%
分速度损失
%
分 分
1.故障停止损失 2.准备调整损失 3.刃具交换损失
OP5 OP4 OP3 OP2 OP1
如果某一工序停止 生产线全体也停止
假设各工序的OEE 是这样的・・・。
那么线整体的 OP1 85% OEE是多少呢?
OP2 80%
OP3 90%
85%×80%×90%×75%×80%=
OP4 OP5
75% 80%
36.72%
.
13
生产线的OEE变成了这样!
・多台的机械加工设备用传送带来连接的生产线
< 定位夹具的无交换性>
无 *交换与零件接合的定位夹具的前端
Байду номын сангаас
交
换
性
零件A(孔小)
零件B(孔大)
<夹紧装置的触动调整化>
零件A (孔大)
零件B (孔小)
触
由于是长形孔位置不易确定
动
化
废除长形孔、用孔型来定位
.
21
22
把部位・内容具体.化!
从次数和停止时间多的部分 开始对策!
停止时间
使用小停工的发生次数或者停止时间来绘制柱形图
刃具交換 7.6%(651分)
准备调整
品质工程技能与系统提升培训讲义PPT文档共48页
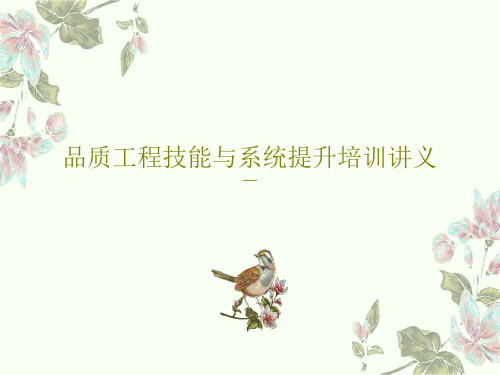
66、节制使快乐增加并使享受加强。 ——德 谟克利 特 67、今天应做的事没有做,明天再早也 是耽误 了。——裴斯 泰洛齐 68、决定一个人的一生,以及整个命运 的,只 是一瞬 之间。 ——歌 德 69、懒人无法享受休息之乐。——拉布 克 70、浪费时间是一桩大罪过。——卢梭
品质工程技能与系统提升培训讲义
16、自己选择的路、跪着也要把它走 完。 17、一般情况下)不想三年以后的事, 只想现 在的事 。现在 有成就 ,以后 才能更 辉煌。
18、敢于向黑暗宣战的人,心里必须 充满光 明。 19、学习的关键--重复。
20、懦弱的人只会裹足不前,莽撞的 人只能 引为烧 身,只 有真正 勇敢的 人才能 所向披 靡。
- 1、下载文档前请自行甄别文档内容的完整性,平台不提供额外的编辑、内容补充、找答案等附加服务。
- 2、"仅部分预览"的文档,不可在线预览部分如存在完整性等问题,可反馈申请退款(可完整预览的文档不适用该条件!)。
- 3、如文档侵犯您的权益,请联系客服反馈,我们会尽快为您处理(人工客服工作时间:9:00-18:30)。
质量管理
七.异常处置 异常处置
4. 范围 (1) 颜色管理 (2) 目视管理 (3) 视.听.嗅.触等感管的应用 (4) 治具 (5) 自动化
28
KEEP ON GOING FOR EXCELLENCE
质量管理
七.异常处置 异常处置
5.愚巧法例子: (1) 保险丝 (2) 跳动路面 (3) 驼峰路面 (4) 平交道自动警示系统 (5) 路面反光装置 (6) 萤光贴纸 (7) 瓦斯臭味 (8) 电梯载重管制 (9) 电梯门未关妥无法启动 (10) 三极插头插座\ (11) 以电眼或两手同按开关保 护床人员安全 (12) 电线编号 (13)以颜色区别各种管路 (14)点检表 (15)归档资料以颜色.符号区别
质量管理
三.如何迅速反应异常?
(三)目视管理 管理的结果与过程能透过看板.图表.灯号.颜色 … …等充 分显在化. (四)明确的异常反应处理制度 (五)鼓励基层人员提问题 基层人员若能提出问题,应多加赞赏. (六)培养部属数据观念 (七)基层干部于下班前或后,召集部属检讨当日的作业状况.
具体事例
12
16
KEEP ON GOING FOR EXCELLENCE
质量管理
五.异常分析的思考步骤 异常分析的思考步骤
(二)[异常现象]与[正常现象]比较,比找出 二 两者之间差异特征. (三)找出有关的变化 即过程(4M1E)中,新的或与 以往不同的作法. (四)将 [变化]与[差异特征] 或[变化]与[异常现象]结合, 以推演,并调查最可能之根本原因 (五)查证;以所收集的资料来证明原因是否合乎情理. 例一 例二 例三 例四
17
KEEP ON GOING FOR EXCELLENCE
质量管理
五.异常分析的思考步骤
不良率升高了 某金属加工厂,3/18领班甲发现A零件昨天的不良率大幅提 高了,3/16以前该零件的不良率一向维持于1%以下;但 ,3/16 1 3/17的不良率却高达5%,且有增加的趋势. 请各位建议领班甲如何进行异常分析.
质量管理
七.异常处置 异常处置
3. 方式 (1) 接触式 利用产品(形状.大小) 与设定装置是否接触,以测知有无 异常. (2) 定数式 利用实际动作次数与规定动作次数比较.以测知有无异 常. (3)动作的步骤式 利用实际动作步骤与规定动作骤比较.以测知有无异常. (4)发生异常时可用”引起注意方式”,”停止运转方式”与” 区别 不良品方式”. 27
KEEP ON GOING FOR EXCELLENCE
质量管理
.
四.异常分析的概念
结果 X Y 说明 正常过程下”应有的 实绩(结果)即基 准” “实际发生”的实绩
(一)过
程
异常分析即在找偏离正常过程之变化的真因. (二)异常真因”最多2-3个”. “通常为1个”.
13
KEEP ON GOING FOR EXCELLENCE
质量管理
四. 异常分析的概念
(三) 异常与改善
基准
基准
不 良5% 率 不 良5% 率 改善目标
若眼于使实绩维持于应有的水准 异常处理
KEEP ON GOING FOR EXCELLENCE
若眼于使实绩达成改善目标 改善
14
质量管理
四. 异常分析的概念
(四) 异常 为 什 么 分析原因少
未成交 抱怨率 达成率
29
KEEP ON GOING FOR EXCELLENCE
质量管理
B.异常问题解决的手法 异常问题解决的手法 ----8D&CLCA步骤 & 步骤
DO. 问题定义(现象) D1. 改善主题.选定小组成立与目标设定 D2. 现状分析 D3. 初步原因分析与拟定暂时防堵对策 D4. 实施真因分析与验证真因 D5. 列出选定及验证永久对策 D6. 执行永久对策及效果确认 D7. 防止再发及标准化 D8. 肯定与残余潜在问题
2
KEEP ON GOING FOR EXCELLENCE
质量管理
A .异常问题的产生与解决的观念 异常问题的产生与解决的观念 何谓异常问题? 一.何谓异常问题 何谓异常问题
应该做到而没有做到,不应该发生而发生 即维持活动发 应该做到而没有做到 不应该发生而发生,即维持活动发 不应该发生而发生 生了问题,实绩比管制基准不好 发生异常时,应立刻 实绩比管制基准不好,发生异常时 生了问题 实绩比管制基准不好 发生异常时 应立刻 进行异常问题分析. 进行异常问题分析 以基准,标准 规格 规定.目标 计划为比较基础, 以基准 标准.规格 规定 目标 计划为比较基础 标准 规格.规定 目标.计划为比较基础 其结果.原因 实施状况与预定的管理界限(与对 原因.实施状况与预定的管理界限 其结果 原因 实施状况与预定的管理界限 与对 策相关的界限) 策相关的界限 不相符合 或不能进行定量化分析 或者,在很难进行量化分析的情况下 定性) 在很难进行量化分析的情况下(定性 或者 在很难进行量化分析的情况下 定性 这些情况与普通的状态有差别时就叫做异常
改善
为 什 么 分析原因多
未成交件高 抱怨率高 达成率高
15
KEEP ON GOING FOR EXCELLENCE
质量管理
五.异常分析的思考步骤
(一)以层别想法多角度说明异常现象 例:异常是 什么人.厂家.什么机器…… 什么单位.地区.什么时间…… 什么产品.项目.部位…… (1)观察:三现 K.K.D 层别想法 (2)统计手法: 层别 推移图.管制图 直方图.柏拉图
5
KEEP ON GOING FOR EXCELLENCE
质量管理
谁没有问题?、 谁没有问题 、
我最行,都是别人的问题! 我最行,都是别人的问题!
家家有本难念的经! 家家有本难念的经
6
KEEP ON GOING FOR EXCELLENCE
质量管理
越早发现越容易解决
小孔不补,大孔知苦 小孔不补 大孔知苦
3
KEEP ON GOING FOR EXCELLENCE
质量管理
异常与索赔的概念图
以法律为基础的索赔 以公司内部标准为基础的索赔
怨言 潜在怨言 瑕疵(商品.服务) 可修理的瑕疵产品 异常 潜在异常
4
KEEP ON GOING FOR EXCELLENCE
质量管理
正确问题意识
谁没有问题? 谁没有问题 搭的士比较安全? 搭的士比较安全 生命只有一个单纯问题,就是每人皆有问题 就是每人皆有问题” 生命只有一个单纯问题 就是每人皆有问题”
质量管理
KEEP ON GOING FOR
EXCELLENCE
2010年 2010年8月
1
KEEP ON GOING FOR EXCELLENCE
质量管理
第五部分:品质工程师的异常问 第五部分 品质工程师的异常问 题解决手法
A.异常问题的产生与解决的观念 异常问题的产生与解决的观念. 异常问题的产生与解决的观念 B.异常问题解决的手法 异常问题解决的手法 1.问题的界定 问题的界定 2.问题解决小组的建议与能力 问题解决小组的建议与能力 需求 3.问题的理清与层别 问题的理清与层别 4.应急措施的实施与确认 应急措施的实施与确认 5.问题的根本原因分析与验证 问题的根本原因分析与验证: 问题的根本原因分析与验证 (常用的探究真因的统计工具 常用的探究真因的统计工具) 常用的探究真因的统计工具 C.异常问题解决的手法 异常问题解决的手法 1.永久改善对策立案及验证环圈 永久改善对策立案及验证环圈 2.永久改善对策实施及确认 永久改善对策实施及确认 3.防止再发措施 系统措施 防止再发措施/系统措施 防止再发措施 4.效果的肯定 效果的肯定 5.结案与肯定 结案与肯定 D.案例演练 案例演练
是否只解决表面的问题? 是否只解决已发生的问题?
9
KEEP ON GOING FOR EXCELLENCE
质量管理
二.异常管理的不合理现象 异常管理的不合理现象
(一) 担当单位划分不当,是由 品管或技术单位作原因分析. 下对策 (二) 异常处理与改善混为一谈 (三) 异常反应单只由品管填发 (四) 未能掌握时效 (五) 找理由,找借口未依据事 实 (六) 未能追根究底 (七) 未追踪确认效果 (八) 仅采治标措施 (九)缺乏过程的记录
19
KEEP ON GOING FOR EXCELLENCE
质量管理
六.
异常分析正确的态度
(二) 上司对异常应有的态度 1.[异常解决 重于 责任追究 异常解决] 重于{责任追究 责任追究} 异常解决 2.若部属于日常业务发生异常时,能于过程彻底分析, 并作再发防止:且属于{善意实施} 下的异常,最好不要太计较责任 的追究. 3.若部属未进行上项活动,而发生同样异常,则要严格追究责任. (三) 训练部属以{逻辑思考步骤}报告异常处理过程.
23
KEEP ON GOING FOR EXCELLENCE
质量管理
七.异常处置 异常处置
(四) 再发防止的具体作法针对异常真因进行下列动作. 1.检讨相关标准 检讨相关标准 (1) 标准有否?标准明确否? 答案若是否定.则增订标准. (2) 标准遵守否?若遵守标准而结果又不好,则修改标准. (3) 标准了解否?若不了解则须教育标准.
A
18
KEEP ON GOING FOR EXCELLENCE
质量管理
六.异常分析正确的态度
(一)分析者应有的态度 1.客观地自我检讨才会进步. (1)找原因,非找借口.理由. (2)根据数据,事实,而非猜测.假设. 2.锲而不舍,追根究底,5-WHY分析. 3.不可为分析而分析. (1)统计手法主要用于界定异常真象. (2)可能原因的推演则须配合专业知识.
22
KEEP ON GOING FOR EXCELLENCE