螺杆挤压机的纺丝工艺参数_
熔纺双组分超细纤维成型工艺及其应用研究进展

研究与技术丝绸JOURNALOFSILK熔纺双组分超细纤维成型工艺及其应用研究进展Progressonprocessingandapplicationofmelt ̄spunbicomponentultra ̄finefibers曹㊀阳1ꎬ宋㊀兵1ꎬ3ꎬ张㊀恒2ꎬ王㊀亮1ꎬ钱晓明1(1.天津工业大学纺织科学与工程学院ꎬ天津300387ꎻ2.中原工学院纺织学院ꎬ郑州451191ꎻ3.明新旭腾创新研究院有限公司ꎬ江苏徐州221436)摘要:熔纺双组分超细纤维由于其原料和成型技术的组合多样性而备受青睐ꎮ然而ꎬ在现有的制备工艺中ꎬ熔纺双组分超细纤维存在如能耗大㊁难以细旦化和污染环境等问题ꎬ限制了其在实际生产和高质应用领域的进一步发展ꎮ并且在实际的生产过程中ꎬ不同的原料选择㊁组件使用及工艺调控等因素都对熔纺双组分超细纤维成型效果影响显著ꎮ因此ꎬ合理调控熔纺双组分超细纤维成型过程中各阶段影响因素对其综合性能进一步提升具有重大意义ꎮ为更全面理解熔纺双组分超细纤维的本质ꎬ本文以桔瓣型纤维和海岛型纤维为研究基体ꎬ探究了熔纺双组分超细纤维的纺丝成型机理及其影响因素ꎻ阐述了熔纺双组分超细纤维多样的开纤工艺(机械开纤㊁化学开纤和热能开纤)ꎻ归结了熔纺双组分超细纤维在合成革㊁空气过滤和医疗卫生等材料领域的应用ꎻ最后对熔纺双组分超细纤维广阔的发展前景进行了展望ꎮ关键词:双组分超细纤维ꎻ双组分熔融纺丝ꎻ纺丝机理ꎻ机械开纤ꎻ热能开纤ꎻ超细纤维合成革中图分类号:TS102.64ꎻTQ340.642㊀㊀㊀㊀文献标志码:A㊀㊀㊀㊀文章编号:10017003(2024)03006611DOI:10.3969∕j.issn.1001 ̄7003.2024.03.008收稿日期:20230808ꎻ修回日期:20231226基金项目:国家自然科学基金项目(52003306)ꎻ河南省重大科技专项项目(221100310500)ꎻ河南省高等学校重点科研项目(23A540003)ꎻ中国纺织工业联合会应用基础研究项目(J201805)作者简介:曹阳(1997)ꎬ男ꎬ硕士研究生ꎬ研究方向为双组分超细纤维非织造材料ꎮ通信作者:宋兵ꎬ工程师ꎬsongbing.012@163.comꎮ㊀㊀超细纤维一般是指单丝线密度小于0.44dtex的纤维ꎬ由于线密度与常规纤维的差异ꎬ超细纤维具有许多优良特性ꎬ如较好的悬垂性㊁耐磨性和抗皱性㊁手感柔软平滑等[1]ꎮ由于超细纤维的优异综合性能ꎬ利用其制备而成的非织造材料被广泛应用于超细纤维合成革㊁过滤材料㊁医用敷料和油水分离材料[2 ̄4]等诸多领域ꎮ超细纤维按照其原料的组分大致可以分为单组分和双组分超细纤维ꎮ前者的成型机理并不复杂ꎬ但是存在性能单一㊁应用范围窄等问题ꎻ而双组分超细纤维由于其原料㊁结构和工艺的多样性ꎬ具有许多单组分超细纤维所不具备的优异性能ꎮ目前ꎬ双组分超细纤维的制备方式主要有熔融纺丝法㊁静电纺丝法[5 ̄6]㊁闪蒸纺丝法和离心纺丝法[7 ̄8]等ꎮ其中ꎬ由熔融纺丝法所制备的双组分超细纤维具有优异的力学性能㊁良好的吸水性㊁较大的比表面积和可规模化生产等特性ꎬ被广泛投入实际应用之中[9]ꎮ根据纤维的截面形态ꎬ熔纺双组分超细纤维主要包括桔瓣型(实心桔瓣和中空桔瓣)和海岛型(定岛型和不定岛型)[10]ꎮ与此同时ꎬ熔纺双组分超细纤维还具有多样的开纤工艺(机械开纤㊁化学开纤和热能开纤)ꎮ原料㊁纺丝和开纤工艺的多样性为熔纺双组分超细纤维的制备提供了无限的可能性ꎮ然而ꎬ在实际的生产过程中ꎬ熔纺双组分超细纤维的制备存在如能耗大㊁开纤污染环境㊁纤维纤度难以达到使用要求等诸多问题[11 ̄12]ꎮ为推动熔纺双组分纤维的进一步发展ꎬ本文研究了熔纺双组分纤维的纺丝成型机理ꎬ总结了熔纺双组分纤维的开纤工艺ꎬ并探究了其在不同领域的应用ꎬ以期为超细纤维的成型先进化㊁应用广泛化和发展持续化提供理论基础ꎮ1㊀熔纺双组分超细纤维成型工艺近年来ꎬ双组分超细纤维的发展十分迅速ꎬ其成型工艺也越来越多元化ꎬ但由于制备技术的限制ꎬ目前仅熔纺双组分超细纤维可以实现规模化生产ꎮ本文主要依托于不断发展的熔纺非织造技术ꎬ对双组分超细纤维的成型机理和影响纤维成型的因素进行归结ꎮ1.1㊀桔瓣纤维纺丝成型桔瓣型纤维通常采用共轭纺丝工艺(图1)进行生产ꎬ首先将两种具有熔体黏度差异或互不相容的热塑性聚合物送入螺杆挤压机中熔融成纺丝流体ꎬ由计量泵对两种纺丝流体进行计量ꎻ再通过独特的桔瓣型喷丝板喷丝成型(图1(a))ꎬ使得两种聚合物均匀分配在一根纤维之中ꎮ基于两种聚合物之间具有较弱的界面力ꎬ在经过牵伸工序后可以制得具有较好取向度和机械性能的纤维长丝[13]ꎮ66第61卷㊀第3期熔纺双组分超细纤维成型工艺及其应用研究进展图1㊀共轭双组分超细纤维成型工艺Fig.1㊀Conjugatedbicomponentultra ̄finefiberformingprocess1.1.1㊀实心型桔瓣型纤维又可以分为实心桔瓣型和中空桔瓣型两种ꎮ其中ꎬ实心型桔瓣型纤维[14]是采用具有实心桔瓣结构的纺丝组件所制备出的纤维ꎮ但实心型桔瓣纤维由于两组分之间界面结合力较大ꎬ有时不易使得两组分开裂形成超细纤维ꎬ开纤率仅为60%~75%[15]ꎮ1.1.2㊀中空型中空型桔瓣纤维[16]是对实现桔瓣纤维的一种改进ꎬ该纤维是通过具有中空型桔瓣结构纺丝组件的制备而成的ꎮ将桔瓣纤维制备成中空状ꎬ能够有效减少两组分间的接触面积ꎬ减弱组分间界面张力ꎬ有利于纤维的开裂ꎬ开纤率可达88.5%~94.8%[17]ꎮ实心型与中空型桔瓣纤维的开纤差异性如表1所示ꎮ表1㊀实心型与中空型桔瓣纤维的开纤差异性Tab.1㊀Differenceoffibersplittingbetweensolidandhollowsegmentedpiefibers1.2㊀海岛纤维纺丝成型1.2.1㊀不定岛型不定岛型海岛纤维通常采用共混纺丝成型工艺进行制备(图2)ꎬ即在一定条件下把两种不相容的聚合物进行共混纺丝ꎮ在纺丝过程中ꎬ其中一种聚合物熔体以微小液滴形式(分散相)分布在另一种聚合物熔体(连续相)中ꎬ形成纤维[18 ̄19]ꎮ图2㊀不定岛共混双组分纤维成型工艺Fig.2㊀Unfiguredsea ̄islandblendedbiocomponentfiberformingprocess76Vol.61㊀No.3Progressonprocessingandapplicationofmelt ̄spunbicomponentultra ̄finefibers㊀㊀图2(a)为双组分共混聚合物在纺丝模头毛细孔中的流动状态示意ꎮ当双组分共混聚合物在熔融状态下通过纺丝毛细管模头时ꎬ在A区只会受到法向应力(垂直于表面的力)ꎬ但在B区时ꎬ法向应力和剪切力(平行于表面的力)都作用在双组分共混物上ꎬ从而导致液滴旋转㊁拉长成条形或椭圆形[20]ꎮ随后通过C区挤出ꎬ由于作用时间太短ꎬ在C区液滴形状并不会发生变化ꎮ图2(b)以聚乳酸∕聚乙烯醇(PLA∕PVA)不定岛纤维为例ꎬ当共混相PLA∕PVA受到拉伸力作用时ꎬPLA作为分散相液滴受力变得细长并且会发生聚结ꎬ而连续相PVA在这一过程中始终包裹着分散相PLA[21]ꎮ图2(c)为PLA∕PVA共混挤出物中液滴的聚合和变形以及不同直径的椭圆形PLA液滴的示意ꎮ不难看出ꎬ岛相组分在海相组分中发生了不同程度的变形ꎬ且尺寸大小不一ꎬ故所制备的纤维纤度分布是不均匀的ꎮ因此ꎬ在不定岛纺丝过程中ꎬ岛相组分会形成许多十分细小的液滴ꎬ并在热牵伸定型后以微细短纤维的形式分散于另一种聚合物(海组分)中ꎬ即不定岛型海岛纤维[22]ꎮ1.2.2㊀定岛型定岛型海岛纤维与桔瓣型纤维类似ꎬ同样采用共轭纺丝工艺成型(图1)ꎬ即将两种不同的聚合物(不同组分或不同浓度)分别由两个螺杆挤出机进行熔融ꎬ随后经由具有海岛分配系统的喷丝板喷出形成纤维(图1(b))ꎮ在进入喷丝孔之前ꎬ两种聚合物彼此分离ꎬ在进入喷丝孔瞬间ꎬ两种聚合物熔体接触ꎬ并在喷丝孔甬道中均匀混合ꎬ最后形成连续相均匀包覆分散相的纤维ꎬ即定岛型海岛纤维ꎮ与不定岛纺丝不同的是ꎬ定岛型海岛纤维在经过喷丝板后就已经形成了均匀分布的海岛纤维ꎬ后续牵伸成型工序并没有对纤维径向分布产生明显的影响[23]ꎻ而不定岛纺丝由于是共混纺丝成型ꎬ使得岛组分在整个纤维中的分布并不均匀ꎬ且需要牵伸的作用力使得岛组分由液滴形态转变为短纤形态ꎮ表2为定岛型海岛纤维和不定岛型海岛纤维的差异性ꎮ表2㊀定岛型和不定岛型海岛纤维的差异性Tab.2㊀Differencebetweenfiguredandunfiguredsea ̄islandfibers1.3㊀影响纤维成型的因素1.3.1㊀纺丝组件纺丝组件对于聚合物熔体的流动㊁纤维的直径和纤维的形态等起着决定性的作用ꎮ熔体分配板是双组分纤维纺丝的核心组件ꎬ桔瓣型和海岛型纤维通常需要特殊的分配系统来决定聚合物的分布ꎮ对于桔瓣型纤维来说ꎬ通常由于熔体分配板的配置ꎬ其截面 桔瓣 数量可以分为 2+2 瓣ꎬ 4+4 瓣和 8+8 瓣等ꎮ而随着 桔瓣 数量的增加ꎬ所制备纤维的直径会逐渐减小ꎮHills公司采用专有蚀刻工艺制造了海岛纤维的分配板(0.1~1.5mm)中的熔体流动通道ꎬ溶解海组分后能够得到300nm左右的超细纤维[24]ꎮ这种成本较低且允许高密度纺丝熔体通过的分配系统不久使得岛组分的所占的比例显著增大ꎬ同时也极大地推动了海岛纤维的产业化[25]ꎮ一般来说ꎬ喷丝组件内的熔体流动甬道直径越小ꎬ所能制备出的纤维直径就越小ꎬ但越精密的组件对聚合物原料的特性要求(如流变性能㊁热性能等)就越高ꎮ因此ꎬ聚合物原料对纤维的成型也至关重要ꎮ1.3.2㊀聚合物原料对于熔纺双组分纤维来说ꎬ聚合物原料的选用㊁熔体黏度和聚合物结晶度等对其成型都有着较大的影响ꎮ1)聚合物原料选用ꎮ对于熔纺双组分纤维来说ꎬ桔瓣型和海岛型两种纤维的原料选用遵循着不同的规则ꎮ为使纤维容易裂离ꎬ通常桔瓣型纤维需要选用两种互不相容的聚合物为原料ꎬ且两种聚合物需要具有较弱的界面结合力ꎬ如聚酯∕聚酰胺6(PET∕PA6)㊁聚乳酸∕聚丙烯(PLA∕PP)和聚乙烯∕聚酰胺6(PE∕PA6)等ꎮ否则ꎬ两种聚合物相容或粘结在一起就很难裂离[26]ꎮ而对于海岛纤维来说ꎬ聚合物同样应互不相容ꎬ同时应该选取易于溶解剥离的材料为海组分ꎮ目前ꎬ常用的海组分原料有低密度聚乙烯(LDPE)㊁碱溶性聚酯(COPET)㊁聚对苯二甲酸丁二酯(PBT)㊁PVA和聚苯乙烯(PS)等[27 ̄31]ꎬ常见的岛组分原料则有PET㊁PA6㊁PPS和PLA等ꎮ除了更易裂离方面ꎬ聚合物原料的组成对熔纺双组分纤维的性能通用具有较大的影响ꎬ为满足实际应用的需求(如高强㊁高弹㊁高耐热和生物相容性等)ꎬ通常选用具有不同特性的聚合物为主要原料进行熔融纺丝(如PET㊁PTT㊁PPS㊁PBAT等)ꎮ2)聚合物熔体黏度ꎮ聚合物的熔体黏度是影响纤维成型的一个重要因素ꎬ在纺丝工艺中的黏度差异很大程度上影响着聚合物的排列ꎮ一般情况下ꎬ在熔体黏度增大时ꎬ为保证聚合物的可纺性ꎬ需要提高纺丝温度来增大其流动性从而保障纤维的成型ꎮAyad等[32 ̄33]采用共轭纺丝工艺制备了PP∕PA6双组分非织造材料ꎬ并探究了PP和PA6中单个组86第61卷㊀第3期熔纺双组分超细纤维成型工艺及其应用研究进展分黏度(PP25和PP18)对横截面形态的影响ꎮ结果表明ꎬ低黏度的组分通常包裹在高黏度组分周围ꎬ且纤维截面呈现桔瓣型结构ꎮ研究认为ꎬ两种聚合物在熔融挤出时具有不同的流变行为ꎬ黏度的不匹配导致了聚合物不规则流动和聚合物之间的界面变形ꎮ3)聚合物结晶度ꎮ一般来说ꎬ聚合物的结晶度越大熔点就越高ꎬ需要的纺丝温度就越高ꎬ纤维成型过程中所需要的能量就越多ꎮDuo等[34]通过采用不同结晶度的PETꎬ制备了易开裂的PET∕PA6桔瓣型双组分非织造材料ꎮ研究发现ꎬ低结晶度PET所制备的桔瓣型双组分纤维开纤率远高于普通PET∕PA6桔瓣型双组分非织造材料ꎬ并且极大程度上降低了水刺工艺所产生的能耗ꎮ1.3.3㊀纺丝工艺纺丝工艺参数包括纺丝速度㊁卷绕速度㊁纺丝温度和牵伸工艺等ꎮ这些工艺参数对所制备纤维的形态㊁热性能㊁结晶性能和力学性能等方面有着较为直接的影响ꎮ1)纺丝∕卷绕速度ꎮ纺丝速度对纤维的力学性能㊁结晶性能有着很大的影响[35]ꎮAn等[36]采用高速熔融纺丝制备了高相对分子质量PET∕PP海岛纤维ꎮ研究发现ꎬ随着卷绕速度的逐渐增大ꎬ岛组分高相对分子质量PET的力学性能显著提高ꎮSong等[37]采用PVA为海组分ꎬPA6为岛组分ꎬ制备了水溶性PVA∕PA6海岛纤维ꎬ研究发现ꎬ随着纺丝速度的增大ꎬ纤维内部产生更高的大分子取向ꎬ从而使得纤维的结晶度逐渐增大ꎮRoungpaisan等[38]采用PLLA和PDLA为海岛两相组分制备了海岛纤维ꎮ发现随着卷绕速度的逐渐增大ꎬ岛组分纤维的直径逐渐减小ꎬ最低可达500nm左右ꎮ而当纺丝速度较低时ꎬ由于轴向导热效应ꎬ温度在纤维横截面方向上分布不均匀ꎬ会使纤维难以成型[39]ꎮ2)牵伸工艺ꎮ纤维的性能与其结构密切相关ꎬ而牵伸工艺很大程度上能够影响纤维的结构ꎮ一般情况下ꎬ牵伸力的增大能够增加纤维的取向ꎬ使得纤维沿纤维轴方向上排列得更加均匀[40]ꎮWang等[41]研究了牵伸力对PET∕PA6桔瓣型超细纤维性能的影响ꎬ研究发现随着牵伸力的增加ꎬ纤维直径逐渐减小ꎬ双组分纤维的结晶度和取向度增加ꎬPET组分的熔点也增加ꎬ纤维的断裂强度增加ꎬ断裂伸长率降低ꎮYasoshima等[42]采用共混纺丝制备了聚酯∕间规聚苯乙烯(PET∕SPS)海岛纤维ꎬ并对其进行激光牵伸ꎮ研究表明ꎬ在各组分聚合物的玻璃化转变温度下ꎬ可以稳定地对PET∕SPS共混纺丝纤维进行均匀热牵伸ꎬ如果PET含量较高ꎬ可以将纤维拉伸到较高的倍数ꎬ但SPS岛纤维会被拉断ꎮ拉伸后提取PET组分ꎬ可以得到平均直径为0.43μm的SPS纳米纤维ꎬ并具有300MPa左右的强度ꎮ2㊀开纤成型工艺仅经过纺丝工艺成型的双组分非织造材料由于纤维的开裂程度较弱ꎬ从而具有较大的纤维直径和较低的比表面积ꎬ使得其综合性能并不能满足一些特定应用的需求ꎮ对双组分超细纤维进行开纤的目的是获得更细的纤维形态和更细致的纤维结构ꎬ某些开纤方法还具有固网的作用ꎬ增加了双组分超细纤维高质化应用的可能性ꎮ当前ꎬ开纤的方法主要可以分为机械开纤㊁化学溶剂开纤和热能开纤三大类ꎬ如图3所示ꎮ图3㊀熔纺双组分纤维的开纤示意Fig.3㊀Schematicsketchofmelt ̄spunbicomponentfibersplitting2.1㊀机械开纤机械开纤是一种常用的开纤方式ꎬ其原理是基于桔瓣型纤维两聚合物之间较弱的界面结合力及相同的外力作用下两种聚合物所产生不同的应变ꎬ借助机械力使得纤维不同组分之间开裂剥离[43]ꎮ当前ꎬ机械开纤的方法主要有水刺和针刺两种ꎮ2.1.1㊀水刺法水刺法开纤是利用高压水针水流的能量对纤维长丝进行冲击ꎬ从而达到使纤维开裂目的ꎬ同时水刺还可以赋予非织造材料柔软的手感和优异的机械性能ꎬ如图4(c)所示为水刺装置ꎮShim等[44]采用数字体积成像技术探究了PET∕PA6桔瓣型双组分非织造材料的水刺开纤过程ꎮ结果表明ꎬ经过水刺开纤之后ꎬ水针射流喷射的部位纤维开裂程度较高ꎬ厚度方向上的取向度较高ꎬ纤维的开裂主要集中在织物的表面部分且开裂程度较为均匀ꎬ其开纤前后三维图像如图4(a)(b)所示ꎮNdaro等[45]研究了水刺工艺对碱溶性聚酯(COPET)∕PET海岛纤维性能的影响ꎬ发现水刺工艺使得纤维一定程度上的开裂ꎮ研究认为ꎬ这是由于两种聚合物之间较弱的界面结合力导致的ꎮAnantharamaiah等[46]采用水刺工艺探究了机械强力开裂PA6∕PE海岛纤维的可能性ꎬ并制备了具有极高比表面积的微纳米纤维ꎬ并且所制备材料比Evolon®的强力高出数倍ꎮ研究表明ꎬ水刺能够使得纤维一定程度地开裂和原纤化ꎬ如图4(d)所示ꎮ此外ꎬ过高的水刺强力会降低材料的撕裂强力ꎬ这归因于随着水刺对纤网的进一步加固ꎬ纤维之间的迁移率降低ꎮ96Vol.61㊀No.3Progressonprocessingandapplicationofmelt ̄spunbicomponentultra ̄finefibers图4㊀双组分纤维及其非织造材料的水刺开纤Fig.4㊀Hydroentanglefibersplittingofbicomponentfibersandnonwovensthereof2.1.2㊀针刺法针刺法是一种刚性的物理开纤方式ꎬ其开纤原理是利用刺针在纤维间的高速穿插使得纤维开裂ꎬ但是这种刚性的开纤方式同时也会造成部分纤维的损伤ꎮ杨娜娜等[47]探究了针刺工艺对PET∕PA6桔瓣型双组分纺黏超纤革基布结构和性能的影响ꎮ结果表明ꎬ针刺开纤后纤维直径接近胶原纤维直径ꎬ材料厚度随着针刺深度和针刺密度的增加而减小ꎬ断裂强力和撕裂强力则随着针刺深度和针刺密度的增加而增大ꎬ选择较低的针刺深度(7~8.6mm)和较小的针刺密度(720刺∕cm2)用于主针刺机加固ꎬPET∕PA6桔瓣型双组分纺黏超纤革非织造基材的断裂强力和撕裂强力较优异ꎮ虽然机械开纤能够有效实现双组分纤维的开裂ꎬ但是开纤过程能耗较大ꎮ因此ꎬ如何降低聚合物之间的界面结合力㊁减少开纤过程中的能耗ꎬ是当前熔纺双组分纤维需要进一步发展的方向ꎮ2.2㊀化学溶剂开纤利用双组分纤维中两种聚合物的不同化学特性ꎬ采用特定的化学溶剂溶解剥离其中一种聚合物ꎬ而另一种聚合物以超细纤维的形态保留下来ꎬ这种开纤方式就是化学溶剂开纤ꎮ化学溶剂开纤常用于海岛型超细纤维的制备ꎬ但同样可以用于制备桔瓣型超细纤维ꎮ目前ꎬ苯萃取法和碱减量法是化学开纤主要采用的两种方法ꎮ2.2.1㊀苯萃取法LDPE㊁PP和PS等[48 ̄50]可以溶于甲苯或二甲苯溶液中ꎬ利用这一原理ꎬ通过合理选用海岛组分的原料ꎬ可以进行苯萃取法开纤ꎮXu等[51]将改性后的胶原蛋白浸渍到PA∕LDPE非织造纤维中形成薄膜ꎬ并采用甲苯溶液对PA∕LPDE海岛非织造材料进行开纤ꎮ研究表明ꎬ萃取温度85ħ㊁时间110min时开纤效果最佳ꎬ萃取率达55%左右ꎮ2.2.2㊀碱减量法碱减量开纤是一种常用于海岛纤维的开纤方式ꎬ其海组分通常采用COPET为原料ꎮNam等[52]和Kang等[53]分别探究了PTT(弹性涤纶)∕PET和COPET∕PET海岛纤维的碱减量特性ꎮ研究发现ꎬ随着碱液浓度的增大ꎬ所获得的 岛 组分纤维越细ꎬ但纤维的强力有所下降ꎮ而且ꎬ随着碱处理温度的升高ꎬ处理时间的增长ꎬ海组分的去除效果越佳ꎮ目前ꎬ随着COPET的制备工艺逐渐成熟ꎬ碱减量开纤工艺也已经逐渐开始工业化ꎬ通常情况下ꎬ在氢氧化钠NaOH质量分数为5%㊁碱处理时间为30min的情况下ꎬCOPET作为海组分溶解度可达99%以上ꎮ除此之外ꎬHuang等[54]将聚乙醇酸(PGA)和聚乳酸(PLLA)共混ꎬ并以PLLA为海相ꎬ采用高速熔融纺丝法制备了PLLA∕PGA海岛纤维ꎮ经过热拉伸处理后ꎬ在三氯甲烷中溶解聚乳酸相ꎬ可生产出具有高度取向的超细㊁均匀且排列良好的PGA纳米纤维ꎮ07第61卷㊀第3期熔纺双组分超细纤维成型工艺及其应用研究进展总之ꎬ化学溶剂开纤可以采用各种各样的化学溶剂溶解海组分从而获得超细纤维ꎮ除此之外ꎬ化学溶剂还可以溶解岛组分用于研究海岛纤维中的岛相分布ꎬ同时这也是制备中空纤维的一种方式ꎮ但是ꎬ化学溶剂开纤存在着开纤溶液难以回收㊁污染环境㊁毒性强等诸多问题ꎬ亟待科研人员的进一步研究和发展ꎮ2.3㊀热能开纤对于桔瓣型纤维而言ꎬ热能开纤是利用在热作用下两种组分结构的不同ꎬ在纤维轴向上产生不同程度的收缩使纤维开裂ꎻ而对于海岛型纤维ꎬ利用海相聚合物(如水溶性PVA㊁水溶性聚酯)的热水溶性[55 ̄56]ꎬ溶解海组分后ꎬ从而形成超细纤维ꎮTran等[57]采用以PP和PLA为原料ꎬ采用后牵伸工艺(图5(a))以热能开裂PP∕PLA桔瓣型双组分纤维ꎮ研究发现ꎬPP和PLA在热性能和结晶性能上具有较大的差异ꎬ并且利用在加热㊁冷却和拉伸过程中PP和PLA不同的胀缩行为ꎬ从而实现纤维的开裂ꎬ如图5(b)(c)所示ꎬ可以看出纤维在经过热牵伸后已经出现了较高程度的开裂ꎮTran等[58]采用水溶性PVA为海组分ꎬPLA为岛组分制备了不定岛型双组分纤维ꎬ通过水溶性开纤去除PVA组分ꎬ制备了平均直径为60nm的PLA超细纤维ꎮ开纤工艺对于桔瓣型和海岛型纤维至关重要ꎬ但当前开纤工艺仍存在如能耗大㊁污染环境和回收困难等问题ꎮ因此ꎬ如何开发出具有低能耗㊁绿色环保和可循环利用的开纤工艺将是桔瓣型和海岛型双组分纤维未来主要的发展方向ꎮ图5㊀PP∕PLA桔瓣双组分纤维的热牵伸开纤Fig.5㊀PP∕PLAsegmented ̄piebicomponentfiberthermaldrawingfibersplitting3㊀熔纺双组分超细纤维的应用基于制备工艺的优势ꎬ双组分超细纤维具有优异的机械性能㊁较高的比表面积和可产业化生产等诸多特点ꎮ通过使用功能性原料或对其进行后处理加工和功能性整理ꎬ熔纺双组分超细纤维在超细纤维合成革㊁医疗卫生和空气过滤等领域具有良好的应用前景ꎮ3.1㊀超细纤维合成革出于对自然资源的保护ꎬ天然皮革已经逐渐被超细纤维合成革所代替[59]ꎮ超细纤维在形貌上与皮肤原纤维非常相似ꎬ由超细纤维形成的非织造材料具有较大的比表面积㊁较高的孔隙率和较好的吸湿透气性能ꎬ是天然皮革的理想代替产品[60]ꎮ赵宝宝等[61]以水性聚氨酯(WPU)膜为聚合物涂层ꎬ以PET∕PA6熔纺双组分桔瓣型非织造材料为基层材料ꎬ采用干法移膜技术制备了PET ̄PA6∕WPU合成革ꎮ由于PET∕PA6桔瓣型非织造材料具有超细的纤维形态和较高的孔隙率ꎬ所制备的合成革在机械性能方面优于天然皮革ꎬ并且透湿量可达到1673.8g∕(m2 24h)ꎬ同时实现了超细纤维合成革的绿色化制备ꎮ随着WPU发泡倍率的增加ꎬWPU膜的孔径减小ꎬ孔径数目增加ꎬ能够极大程度上满足合成革材料的透气性能和透湿性能ꎮDuo等[62]通过在PET∕PA6桔瓣型纤维上静电纺丝涂覆聚丙烯腈纤维ꎬ而后采用梳理 ̄水刺工艺制备了超细纤维革基布ꎮ研究表明ꎬ革基布的透湿性和柔软性相比于PET∕PA6桔瓣型非织造材料分别提高了28.2%和39.74%ꎮ3.2㊀空气过滤材料由于具有较大的比表面积和较细的纤维形态ꎬ双组分超细纤维在过滤领域也具有极其广泛的应用ꎮ田新娇等[63]基于海岛纤维研发制备了超细纤维滤料ꎬ以用于控制PM2.5ꎬ对其过滤性能进行了综合研究ꎬ并与常规针刺毡滤料和覆膜滤料对比ꎮ结果表明ꎬ海岛纤维滤料对微细颗粒有较好的捕集效果ꎬ对2.5μm颗粒的计数效率在94.9%左右ꎬ接近覆膜滤料的98.9%ꎬ高于针刺毡的61.3%ꎬ是控制细颗粒尤其PM2.5的新型滤料ꎻ海岛纤维滤料属于近表层过滤方式ꎬ残余阻力比覆膜滤料小ꎬ稳定阶段的清灰周期比覆膜滤料长ꎬ有利于延长滤料寿命㊁降低能耗和成本ꎮ朵永超等[64]以高收缩聚酯(HSPET)和PA6为原料制备了HSPET∕PA6桔瓣型超细纤维非织造材料ꎬ并探究了其过滤性能ꎮ该材料在未热收缩处理时对于粒径大于或等于1.5μm颗粒的过滤效率接近于100%ꎬ在过滤领域展现了广阔的应用前景ꎮ17Vol.61㊀No.3Progressonprocessingandapplicationofmelt ̄spunbicomponentultra ̄finefibers3.3㊀医疗卫生材料相较于其他医疗卫生用材料(如纺黏非织造材料或水刺非织造材料)ꎬ熔纺双组分超细纤维具有较大的比较面积和超细的纤维形态ꎬ能够有效屏蔽空气中的小颗粒ꎬ是理想的医用防护材料[65]ꎻ并且双组分超细纤维所制备非织造材料密集的纤维结构和孔隙使其具有较强的芯吸效应和优异亲水性能ꎬ可以应用于医用敷料之中ꎮJin等[66]以PA6和铜碳纳米颗粒(CuCNPs)为原料ꎬ采用熔融共轭纺丝工艺制备了PA6∕CuCNPs桔瓣型超细纤维ꎮ如图6(a)所示ꎬ由于CuCNPs的活性铜催化反应促进了杀菌活性氧物种的产生ꎬ该材料对大肠杆菌和金黄色葡萄球菌都表现出良好的抗菌活性(抗菌率约99%)ꎬ对白色念珠菌具有良好的抗菌活性(抗菌率约82%)ꎬ在医疗卫生领域具有广阔的应用前景ꎮJingjit等[67]以PA6和PE为原料ꎬ通过添加TiO2粒子ꎬ制备了桔瓣型双组分超细纤维ꎮ研究表明ꎬ含有1%TiO2的桔瓣型双组分超细纤维对金黄色葡萄球菌和肺炎克雷伯菌均表现出了较强的生物活性ꎬ如图6(b)(c)所示ꎮZhang等[68]采用浸渍涂层及热带黏合工艺制备了具有孔隙率可调的PET∕PA6双组份桔瓣型超细纤维织物ꎮ研究表明ꎬ所制备的样品具有较高的机械强力㊁较好的屏蔽性能(超疏水㊁高耐静水压㊁抗污㊁抗血液)及可调节的透气性能ꎮ图6㊀熔纺双组分桔瓣纤维的抗菌性能Fig.6㊀Antibacterialpropertiesofmeltspinningbicomponentorangesegmented ̄piefibers㊀㊀除此之外ꎬ双组分超细纤维在高档擦拭材料㊁防刺材料[69]㊁增强复合材料[70]和服装材料[71]等领域也具有广阔的应用前景ꎮ同时ꎬ这些广泛的应用领域为双组分超细纤维的进一步发展提供了强大的动力ꎮ4㊀结㊀语基于其独特的纤维结构和突出的综合性能ꎬ熔纺双组分超细纤维在合成革基布㊁医疗卫生㊁精密过滤㊁服装和土工材料等领域具有良好的应用前景ꎬ且在诸多应用之中已经被广泛生产并投入使用ꎮ但是在纤维的进一步细旦化㊁纺丝工艺的节能化及化学溶剂开纤的绿色化等方面依然亟待科研人员的进一步研究和改进ꎮ在原料选用方面ꎬ应进一步开发具有不同优异性能的聚合物原料ꎬ从而拓宽熔纺双组分纤维的原料多样组合ꎻ在工艺制备方面ꎬ应进行精密组件的研发㊁成型工艺的优化调控ꎬ从而提升熔纺双组分纤维的性能㊁实现纤维直径的进一步细化ꎻ在开纤方面ꎬ随着碳中和与节能减排等绿色环保概念的提出ꎬ应开发低能耗㊁无化学试剂和高效绿色开纤的方式ꎬ从而实现超细纤维的制备ꎮ水溶开纤作为一种绿色的开纤方式ꎬ为双组分超细纤维提供了良好的发展方向ꎮ随着非织造材料与工程的不断发展及多学科交叉理念的提倡ꎬ未来双组分纤维有望通过成型技术实现纤维形态的进一步细化㊁通过更多先进后整理技术实现功能化㊁通过原料和工艺结合实现产品的绿色化ꎬ进而更好地服务于社会ꎮ27。
高强型涤纶工业用全拉伸丝的工艺及设备分析

高强型涤纶工业用全拉伸丝的工艺及设备分析摘要:涤纶工业用全拉伸丝FDY具有低伸长、高模量、高强度及耐老化、耐疲劳等优点,因而在多领域中得到广泛应用。
本文以高强型涤纶工业用的FDY为对象,指出了其基本的工艺流程及生产特点,汇总了其主要设备,最后探讨了所需要的工艺条件,望能为此领域教学研究提供一些参考。
关键词:涤纶工业;全拉伸丝;高强型;工艺;设备近年,我国涤纶工业丝基于前期引进且消化吸收后,可采用国产的纺丝设备嫁接进口卷绕头,以此来进行涤纶工业丝的生产,且已步入规模化生产阶段。
涤纶工业长丝不仅有良好的力学性能,如低延伸度、高断裂强度及高模量等,而且还有各种良好的物理性能,如耐生物性、耐疲劳性、耐热、耐磨及耐光、耐冲击性等。
因此,其有着广泛的用途,已经成为橡胶骨架的重要材料。
针对涤纶工业长丝的生产、应用而言,属于一种高技术领域,无论是高模量低收缩(HMLS),还是高模量低收缩(HMLS),均数此领域研究的重、热点。
为了能够在此领域中有所创新,本文以涤纶工业用全拉伸丝(FDY)为对象,就其工艺及所用设备探讨如下。
1.工艺流程及生产特点分析FDY的基本工艺流程为:高黏度聚酯(PET)湿切片筛料、进行预干燥、干燥、挤压机进行熔融挤出、输送熔体、组件喷丝、缓冷、环吹风冷却、上油、多级拉伸与定形、卷绕、涤纶工业长丝的落筒与包装等。
针对涤纶工业长丝的生产来讲,其较之民用丝生产,主要特点为:(1)需要指出的是,由于工业丝生产所选的为高黏度切片,因此,有着较高的纺丝熔体黏度,以及较差的流动性,需采用各种有效且有针对性的措施,为其降解在合适范围提供保障,并以此实现对溶体均匀性、流动性的改善,最终生产出质量合格的工业丝;(2)各纺丝位有着较大的产量,而且还会有大量热量释放,所以需采用各种可行措施,为其充分冷却提供便利,并且有充足且均匀的上油量;(3)在纺工业丝过程中,后拉伸倍数与民用丝相比,显著偏高,需在设备、工艺上均需给予适当调整,以此为高倍数拉伸提供支撑与保障。
前纺知识——高速纺丝工艺流程
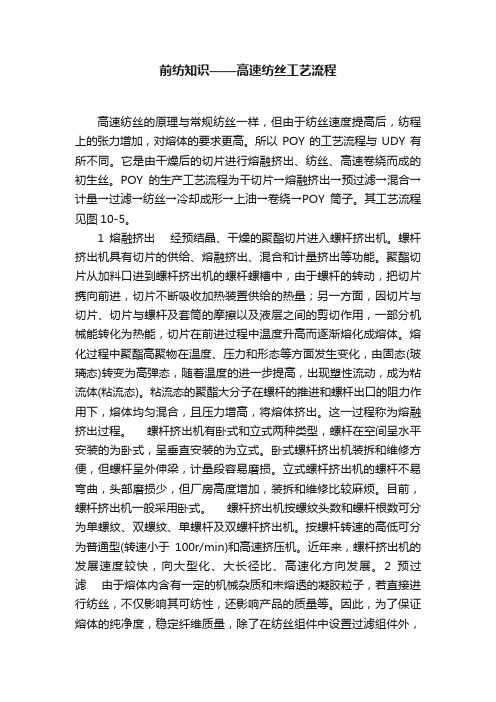
前纺知识——高速纺丝工艺流程高速纺丝的原理与常规纺丝一样,但由于纺丝速度提高后,纺程上的张力增加,对熔体的要求更高。
所以POY的工艺流程与UDY有所不同。
它是由干燥后的切片进行熔融挤出、纺丝、高速卷绕而成的初生丝。
POY的生产工艺流程为干切片→熔融挤出→预过滤→混合→计量→过滤→纺丝→冷却成形→上油→卷绕→POY筒子。
其工艺流程见图10-5。
1熔融挤出经预结晶、干燥的聚酯切片进入螺杆挤出机。
螺杆挤出机具有切片的供给、熔融挤出、混合和计量挤出等功能。
聚酯切片从加料口进到螺杆挤出机的螺杆螺槽中,由于螺杆的转动,把切片携向前进,切片不断吸收加热装置供给的热量;另一方面,因切片与切片、切片与螺杆及套筒的摩擦以及液层之间的剪切作用,一部分机械能转化为热能,切片在前进过程中温度升高而逐渐熔化成熔体。
熔化过程中聚酯高聚物在温度、压力和形态等方面发生变化,由固态(玻璃态)转变为高弹态,随着温度的进一步提高,出现塑性流动,成为粘流体(粘流态)。
粘流态的聚酯大分子在螺杆的推进和螺杆出口的阻力作用下,熔体均匀混合,且压力增高,将熔体挤出。
这一过程称为熔融挤出过程。
螺杆挤出机有卧式和立式两种类型,螺杆在空间呈水平安装的为卧式,呈垂直安装的为立式。
卧式螺杆挤出机装拆和维修方便,但螺杆呈外伸梁,计量段容易磨损。
立式螺杆挤出机的螺杆不易弯曲,头部磨损少,但厂房高度增加,装拆和维修比较麻烦。
目前,螺杆挤出机一般采用卧式。
螺杆挤出机按螺纹头数和螺杆根数可分为单螺纹、双螺纹、单螺杆及双螺杆挤出机。
按螺杆转速的高低可分为普通型(转速小于100r/min)和高速挤压机。
近年来,螺杆挤出机的发展速度较快,向大型化、大长径比、高速化方向发展。
2预过滤由于熔体内含有一定的机械杂质和未熔透的凝胶粒子,若直接进行纺丝,不仅影响其可纺性,还影响产品的质量等。
因此,为了保证熔体的纯净度,稳定纤维质量,除了在纺丝组件中设置过滤组件外,一般还需在熔体输送管道中或纺丝机的熔体分配管道上设置过滤器,通常称为预过滤器。
PPFDY工业丝生产工艺探讨
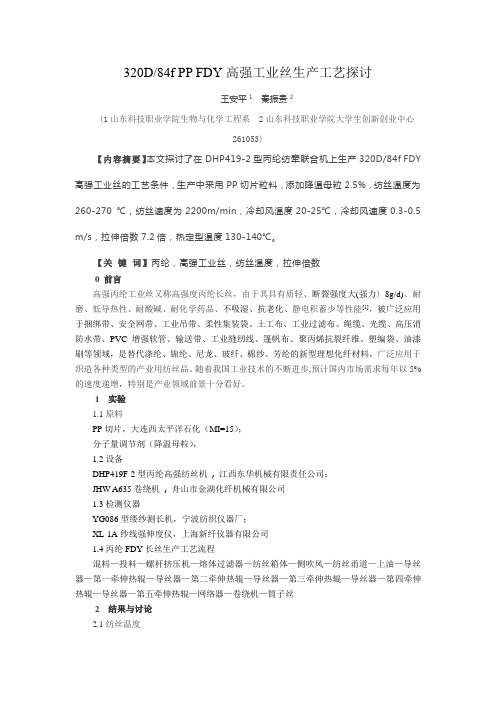
320D/84f PP FDY高强工业丝生产工艺探讨王安平1秦振贵2(1山东科技职业学院生物与化学工程系 2山东科技职业学院大学生创新创业中心261053)【内容摘要】本文探讨了在DHP419-2型丙纶纺牵联合机上生产320D/84f FDY 高强工业丝的工艺条件,生产中采用PP切片粒料,添加降温母粒2.5%,纺丝温度为260-270 ℃,纺丝速度为2200m/min,冷却风温度20-25℃,冷却风速度0.3-0.5 m/s,拉伸倍数7.2倍,热定型温度130-140℃。
【关键词】丙纶,高强工业丝,纺丝温度,拉伸倍数0 前言高强丙纶工业丝又称高强度丙纶长丝,由于其具有质轻、断裂强度大(强力〉8g/d)、耐磨、低导热性、耐酸碱、耐化学药品、不吸湿、抗老化、静电积蓄少等性能[1],被广泛应用于捆绑带、安全网带、工业吊带、柔性集装袋、土工布、工业过滤布、绳缆、光缆、高压消防水带、PVC增强软管、输送带、工业缝纫线、篷帆布、聚丙烯抗裂纤维、塑编袋、油漆刷等领域,是替代涤纶、锦纶、尼龙、玻纤、棉纱、芳纶的新型理想化纤材料,广泛应用于织造各种类型的产业用纺丝品。
随着我国工业技术的不断进步,预计国内市场需求每年以5%的速度递增,特别是产业领域前景十分看好。
1实验1.1原料PP切片,大连西太平洋石化(MI=15);分子量调节剂(降温母粒),1.2设备DHP419F-2型丙纶高强纺丝机,江西东华机械有限责任公司;JHW A635卷绕机,舟山市金湖化纤机械有限公司1.3检测仪器YG086型缕纱测长机,宁波纺织仪器厂;XL-1A纱线强伸度仪,上海新纤仪器有限公司1.4丙纶FDY长丝生产工艺流程混料—投料—螺杆挤压机—熔体过滤器—纺丝箱体—侧吹风—纺丝甬道—上油—导丝器—第一牵伸热辊—导丝器—第二牵伸热辊—导丝器—第三牵伸热辊—导丝器—第四牵伸热辊—导丝器—第五牵伸热辊—网络器—卷绕机—筒子丝2结果与讨论2.1纺丝温度纺丝温度直接影响聚丙烯的流变性能、聚丙烯的降解程度和初生纤维的预取向度。
挤出机常识与工艺(温度、螺杆)

2、熔融段
• A、螺杆排布: . 物料在此段要达到的目的是: 使加工物料获得物理变化和部分化学变化所需的能量,使组分间分布均匀和 初步分散,做到组分均质化、粘度接近。 .一般要求物料承受较大的剪切和机筒传热,使之熔融_一般设置捏合块,剪切 元件或反螺纹,且注意相间排列配合。 • B、温度设定 • a玻纤系,温度太低,树脂半融,到后段玻纤包覆性差;温度太高,树脂流动 提高,混炼与剪切作用变小,甚至出现高温降解,其设定原则: • 1、据基料不同和玻纤含量不同; • 2、扣除螺杆剪切输入的热量,略高于基料熔点范围内; • 3、熔融段后段(即玻纤加入口)熔体流动状况。 • b填充系,(提供强剪切使填充物,充分分散),熔融段高出基料熔点 10~20℃(尽量提高),使物料充分熔融均匀分布。 • c阻燃系,(保护好阻燃剂),其温度要偏低,特别是白色材料,尽可能降低。 • d玻纤增强阻燃系,设定温度介于前面两者间,以物料基本熔点为依据。 • b合金系,以两组熔融温度为依据,同时考虑组分比例及组分之热敏性等,适 当调整温度
⑶物料温度升高的来源:
• 1,螺杆的剪切和物料粒子间相互摩擦生 热——大部分。 • 2,筒体的传热。
(2)各段螺杆排布与温度设定
螺杆组合的作用:
• ①输送物料 • ②提供剪切——使加工物料获得物理变化和化学 变化所需的能量,使组分间分散和分布。 • ③建压
• 物料颗粒熔融过程的分析:
• 聚合物自由输送与预热——全充满或部分充满固体塞—— 固体摩擦、耗散与固态密集“海岛”结构的生成——固态 稀疏“海岛”结构—— 成型挤出。
•
②输送元件,螺纹式的
• 表示法:如“56/56”输送块,前一个”56”指导程为56MM,后一 个”56”指长度为56MM。 • 大导程,指螺距为1.5D~2D • 小导程,指螺距为0.4D左右。 • 其使用规律:随着导程增加,螺杆挤出量增加,物料停留时间减少, 混合效果降低。 • A、选用大导程螺纹的场合,以输送为主的场合,利于提高产量;热 敏性聚合物,缩短停留时间,减少降解;排气处,选用(也有选用浅 槽),增大表面积,利于排气,挥发等。 • B、选用中导程螺纹场合,以混合为主的场合,具不同的工作段逐渐 缩小的组合,用于输送和增压。 • C、选取用小导程螺纹的场合,为一般是组合上逐渐减小,用于输送 段和均化计量段,起到增压,提高熔融;提高混合物化程度及挤出稳 定。
FDY纺丝工艺

FDY纺丝工艺流程一、干燥工艺1,工艺要求:主要是:1、干燥后切片含水:<35PPM2、干燥后切片特性粘度降:<0.02设备:ROSIN干燥设备仿BM干燥设备工艺条件:(1)预结晶温度:介于切片玻璃化温度与熔点之间,一般控制在160-180度.(2)预结晶时间:8-30min,根据需要调整.(3)预结晶沸腾床风压:-5-0(cmwg)(4)干燥温度:温度越高,干燥效果越好.但过高会影响切片粘度降和色泽,一般控制在:160-185度.(5)干燥时间:使切片段含水量接近平衡含水,一般控制在4-12(H).(6)干空气露点:露点越低干燥效果越好.一般控制在<-30度.(7)干空气压力:一般控制在0.6~3.3kgf/c㎡一、纺丝工艺1、工艺要求:主要是:无油丝特性粘度降<0.04.2、设备:日本帝人.日本东丽.日本村田.德国Barmag及国产设备.3、工艺条件:(1)螺杆挤压各区温度A:进料段温度:切片熔点温度+(0-20)度B:压缩,计量段温度:+(10-40)度.(2)螺杆挤压机测量头压力:须保证计量泵吐出量的恒定和减少能耗,一般控制在:8-12mpa 纺丝箱体温度:采用联苯蒸汽加热保温,保持熔体温度不降低,一般控制在:285-298度.(3)组件压力:一控制在:12~28mpa(4)泵供量和转速泵供量(g/min)=纺速(m/min)*成品纤度(dtex)*N除以1000计量泵转速(RPM)=泵供量(g/mig)除以熔体密度(G/CM3)*泵规格(CM3/R)*泵效率(%)(5)冷却吹风A:风速:过大或过低会使纤维条干不均率上升,一般控制在0.3-0.7M/S.B:风温:保持熔体细流冷却长度不会过长,尽量减少各根单丝间冷却长度的偏差,一般控制在20-28度.C:风湿(相对湿度),一般控制在60-90(%)D:风压:一般控制在450~600PA(6)拉伸工艺:根据产品的质量(如物理指标和外观染色)和生产成本,等综合因素所决定的。
高速纺丝主要工艺参数
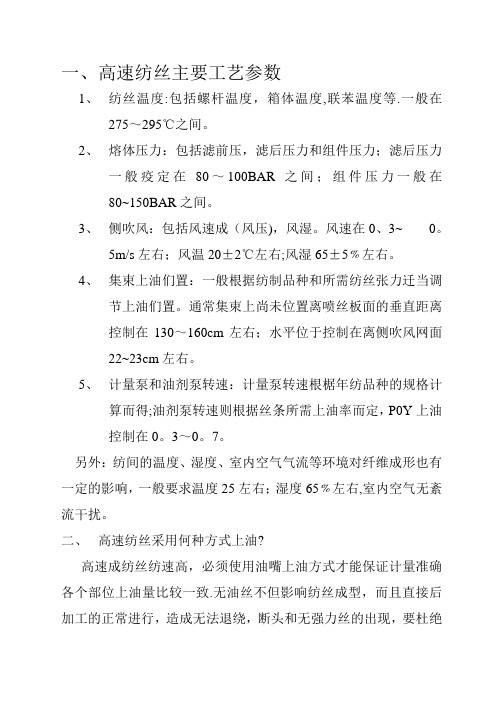
一、高速纺丝主要工艺参数1、纺丝温度:包括螺杆温度,箱体温度,联苯温度等.一般在275~295℃之间。
2、熔体压力:包括滤前压,滤后压力和组件压力;滤后压力一般疫定在80~100BAR之间;组件压力一般在80~150BAR之间。
3、侧吹风:包括风速成(风压),风湿。
风速在0、3~ 0。
5m/s左右;风温20±2℃左右;风湿65±5﹪左右。
4、集束上油们置:一般根据纺制品种和所需纺丝张力迁当调节上油们置。
通常集束上尚未位置离喷丝板面的垂直距离控制在130~160cm左右;水平位于控制在离侧吹风网面22~23cm左右。
5、计量泵和油剂泵转速:计量泵转速根椐年纺品种的规格计算而得;油剂泵转速则根据丝条所需上油率而定,P0Y上油控制在0。
3~0。
7。
另外:纺间的温度、湿度、室内空气气流等环境对纤维成形也有一定的影响,一般要求温度25左右;湿度65﹪左右,室内空气无紊流干扰。
二、高速纺丝采用何种方式上油?高速成纺丝纺速高,必须使用油嘴上油方式才能保证计量准确各个部位上油量比较一致.无油丝不但影响纺丝成型,而且直接后加工的正常进行,造成无法退绕,断头和无强力丝的出现,要杜绝无油丝产生。
三、POY含油一般以0.3~0.7﹪左右较为适当。
丝条含油率低会使纤维松散,摩擦阻力增大,发生毛丝;若含油量过高,会造成油污染增加.四、造成纺丝细丝的原因有哪些?主要原因是组件原因:1、喷丝板镜检不干净;2、分配板不干净;3、组件组装不合格;4、铲板不及时等,出现这种情况,应立即铲板或更换组件。
五、在什么情况下需要紧急更换组件?1、纺丝发生细丝,硬头丝、竹节丝等不正常丝,经板面清理后仍不能清除;2、组件漏浆严重,无法正常生产;3、卷绕毛丝、断头多,检查导丝器,丝道无损伤.六、熔体压力有哪三种?怎样设定熔体压力?熔体压力通常有螺杆出口压力(一般系过滤器前压)、滤后压力和组件压力三种。
滤后压力的确定一般是减去熔体管道的压力损失,保证熔体进入计量泵前的工作压力(一般不低于 3.0MPa),不致使各计量泵吐出量有差异.一般根据纺丝需要设定好一定的后压,前压(螺杆出口压力)则是为了保证后压的稳定,一般随过滤器芯使用时间的增加而增大。
锦纶66弹力丝纺丝工艺探讨
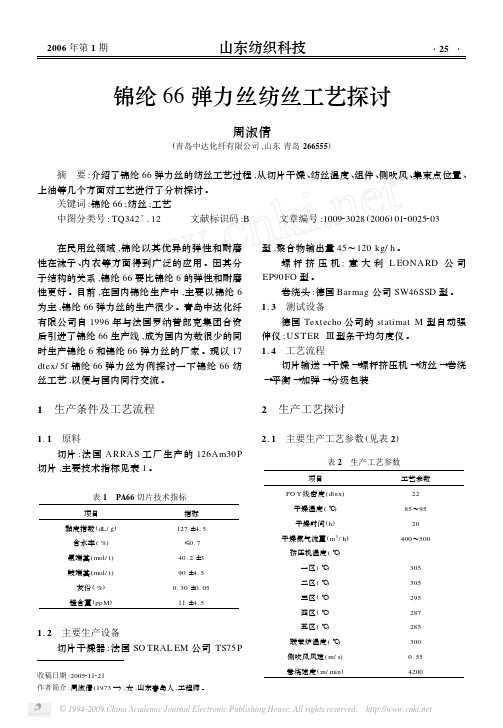
锦纶66弹力丝纺丝工艺探讨周淑倩(青岛中达化纤有限公司,山东青岛266555)摘 要:介绍了锦纶66弹力丝的纺丝工艺过程,从切片干燥、纺丝温度、组件、侧吹风、集束点位置、上油等几个方面对工艺进行了分析探讨。
关键词:锦纶66;纺丝;工艺中图分类号:TQ342+.12 文献标识码:B 文章编号:100923028(2006)0120025203 在民用丝领域,锦纶以其优异的弹性和耐磨性在袜子、内衣等方面得到广泛的应用。
因其分子结构的关系,锦纶66要比锦纶6的弹性和耐磨性更好。
目前,在国内锦纶生产中,主要以锦纶6为主,锦纶66弹力丝的生产很少。
青岛中达化纤有限公司自1996年与法国罗纳普郎克集团合资后引进了锦纶66生产线,成为国内为数很少的同时生产锦纶6和锦纶66弹力丝的厂家。
现以17 dtex/5f锦纶66弹力丝为例探讨一下锦纶66纺丝工艺,以便与国内同行交流。
1 生产条件及工艺流程1.1 原料切片:法国ARRAS工厂生产的126Am30P 切片,主要技术指标见表1。
表1 PA66切片技术指标项目指标黏度指数(dL/g)127±4.5含水率(%)≤0.7氨端基(mol/t)40.2±3羧端基(mol/t)90±4.5灰份(%)0.30±0.05锰含量(ppM)11±4.51.2 主要生产设备切片干燥器:法国SO TRAL EM公司TS75P收稿日期:2005211221作者简介:周淑倩(1973—),女,山东青岛人,工程师。
型,聚合物输出量45~120kg/h。
螺杆挤压机:意大利L EONA RD公司EP90FO型。
卷绕头:德国Barmag公司SW46SSD型。
1.3 测试设备德国Textecho公司的statimat M型自动强伸仪;U STERⅢ型条干均匀度仪。
1.4 工艺流程切片输送→干燥→螺杆挤压机→纺丝→卷绕→平衡→加弹→分级包装2 生产工艺探讨2.1 主要生产工艺参数(见表2)表2 生产工艺参数项目工艺参数PO Y线密度(dtex)22干燥温度(℃)85~95干燥时间(h)20干燥氮气流量(m3/h)400~500挤压机温度(℃)一区(℃)305二区(℃)305三区(℃)295四区(℃)287五区(℃)285联苯炉温度(℃)300侧吹风风速(m/s)0.55卷绕速度(m/min)42002.2 干燥工艺锦纶66的化学平衡含水率为0113%(重量百分比),ARRAS工厂提供给中达公司的切片含水率在017%左右,干燥标准是干燥后的切片含水率为011%,影响切片干燥效果的主要工艺参数是干燥温度、加热介质的露点和流量。
低收缩PBT纤维高速纺丝技术

低收缩PBT纤维高速纺丝技术应乃勇【期刊名称】《《纺织导报》》【年(卷),期】2019(000)010【总页数】3页(P49-51)【作者】应乃勇【作者单位】北京中丽制机工程技术有限公司【正文语种】中文聚对苯二甲酸丁二酯纤维(简称PBT纤维)是由高纯度对苯二甲酸(PTA)或对苯二甲酸二甲酯(DMT)与1,4-丁二醇酯化后缩聚的线性聚合物经熔融纺丝制得的纤维,属于聚酯纤维的一种。
该纤维的大分子链中不仅含有苯环和羧基所构成的共轭体,又具有比常规涤纶中更长的—CH2—链段结构,因此具有涤纶、锦纶和氨纶等 3种纤维的一些特点。
此外,其抗老化性、耐化学稳定性都比锦纶、氨纶高,弹性接近氨纶,弹性模量和锦纶相似,用其加工的服装舒适性较好。
纤维染色性能良好,可用分散染料染色,上染率比常规涤纶高,染色牢度高。
目前该纤维主要用于加工各种运动衣、滑雪衫、连裤袜、高尔夫球衫、泳衣以及医疗绷带、创可贴基布等弹性纺织品及簇绒地毯。
鉴于其优良性能,北京中丽制机工程技术有限公司(以下简称“中丽制机”)对其进行了试纺,并提出了纺丝工艺和装备的优化方案。
1 纺丝设备1.1 设备参数(表1)表1 主要设备参数挤压机带 3 个位,4、5 区带风扇,螺杆外径75 mm,长径比25立式过滤器面积/m2 0.6(过滤精度为25 μm)各级熔体管道内径/mm Φ28,Φ20,Φ8行星式双层计量泵排量(mL·r-1)12×1.6纺丝箱 3 位/箱,12头/位纺丝组件 12套/位喷丝板喷丝板外径85 mm,孔数36无风区高度/mm 100侧吹风风窗高度/mm 1 300(上端带百叶窗)第 1 热辊HGR1 外径220 mm,长度400 mm(张紧角2°)第 1 分丝辊SR1 外径110 mm,长度400 mm(张紧角1°)第 2 对热辊HGR2 外径220 mm,长度400 mm第 3 对热辊HGR3 外径220 mm,长度400 mm卷绕头型号 BWA55T-1500/10油轮宽度/mm 500 1.2 牵伸卷绕设备(图1)图1 牵伸卷绕设备1.3 设备设计要求1.3.1 PBT性能(表2)表2 PBT性能特性黏度/(dL·g-1)挤出胀大比1.0 227 250(255℃) 167 1.45流动温度/℃表观黏度/(Pa·s)黏流活化能/(kJ·mol-1)1.3.2 熔体管路及纺丝箱设计参数(表3、表4)表3 熔体管路设计参数产量/(kg·h-1) 108 总头数 36密度/(g·cm-3) 1.3 熔体停留时间/min 5.87纺丝温度/℃ 263 起始黏度/(dL·g-1) 1.0油水含量/% 1.0 最终黏度/(dL·g-1) 1.3纺丝速度/(m·min-1) 4 500 到计量泵前压力降/ MPa 2.754表4 纺丝箱设计参数剪切速率/(s-1)挤压机 7 24 1 1 700 0.94 250.4粗过滤0.4 0.8 36 0.1 0.01 250.4 0.227计量头 2.8 11.6 1 35 0.02 250.4 0.178管子 2.8 50 1 307.88 0.17 204.9 0.204 13.92管子 2.0 424 31 332.03 2.24 198.7 2.827 12.73静态混合器 2.0 10 3 31.42 0.05 198.5 1.977 12.73计量泵 3 25 0.04198.4管子 0.8 100 36 50.27 1.01 195.8 16.58组件 36 70 1.40 190.7直径/cm 长度/cm头数体积/cm3停留时间/min动力黏度/(Pa·s)压力降/MPaPBT熔体黏度对温度和剪切速率敏感性较大,为了保证熔体黏度和温度均匀,熔体管道各级管路的剪切速率应一致,本设计各级熔体管道的剪切速率均为15 s-1左右。
FDY纺丝工艺

FDY纺丝工艺流程一、干燥工艺1,工艺要求:主要是:1、干燥后切片含水:<35PPM2、干燥后切片特性粘度降:<0.02设备:ROSIN干燥设备仿BM干燥设备工艺条件:(1)预结晶温度:介于切片玻璃化温度与熔点之间,一般控制在160-180度.(2)预结晶时间:8-30min,根据需要调整.(3)预结晶沸腾床风压:-5-0(cmwg)(4)干燥温度:温度越高,干燥效果越好.但过高会影响切片粘度降和色泽,一般控制在:160-185度.(5)干燥时间:使切片段含水量接近平衡含水,一般控制在4-12(H).(6)干空气露点:露点越低干燥效果越好.一般控制在<-30度.(7)干空气压力:一般控制在0.6~3.3kgf/c㎡一、纺丝工艺1、工艺要求:主要是:无油丝特性粘度降<0.04.2、设备:日本帝人.日本东丽.日本村田.德国Barmag及国产设备.3、工艺条件:(1)螺杆挤压各区温度A:进料段温度:切片熔点温度+(0-20)度B:压缩,计量段温度:+(10-40)度.(2)螺杆挤压机测量头压力:须保证计量泵吐出量的恒定和减少能耗,一般控制在:8-12mpa 纺丝箱体温度:采用联苯蒸汽加热保温,保持熔体温度不降低,一般控制在:285-298度.(3)组件压力:一控制在:12~28mpa(4)泵供量和转速泵供量(g/min)=纺速(m/min)*成品纤度(dtex)*N除以1000计量泵转速(RPM)=泵供量(g/mig)除以熔体密度(G/CM3)*泵规格(CM3/R)*泵效率(%)(5)冷却吹风A:风速:过大或过低会使纤维条干不均率上升,一般控制在0.3-0.7M/S.B:风温:保持熔体细流冷却长度不会过长,尽量减少各根单丝间冷却长度的偏差,一般控制在20-28度.C:风湿(相对湿度),一般控制在60-90(%)D:风压:一般控制在450~600PA(6)拉伸工艺:根据产品的质量(如物理指标和外观染色)和生产成本,等综合因素所决定的。
高速纺丝主要工艺参数

一、高速纺丝主要工艺参数1、纺丝温度:包括螺杆温度,箱体温度,联苯温度等。
一般在275~295℃之间。
2、熔体压力:包括滤前压,滤后压力和组件压力;滤后压力一般疫定在80~100BAR之间;组件压力一般在80~150BAR之间。
3、侧吹风:包括风速成(风压),风湿。
风速在0、3~ 0。
5m/s左右;风温20±2℃左右;风湿65±5﹪左右。
4、集束上油们置:一般根据纺制品种和所需纺丝张力迁当调节上油们置。
通常集束上尚未位置离喷丝板面的垂直距离控制在130~160cm左右;水平位于控制在离侧吹风网面22~23cm左右。
5、计量泵和油剂泵转速:计量泵转速根椐年纺品种的规格计算而得;油剂泵转速则根据丝条所需上油率而定,P0Y上油控制在0。
3~0。
7。
另外:纺间的温度、湿度、室内空气气流等环境对纤维成形也有一定的影响,一般要求温度25左右;湿度65﹪左右,室内空气无紊流干扰。
二、高速纺丝采用何种方式上油?高速成纺丝纺速高,必须使用油嘴上油方式才能保证计量准确各个部位上油量比较一致。
无油丝不但影响纺丝成型,而且直接后加工的正常进行,造成无法退绕,断头和无强力丝的出现,要杜绝无油丝产生。
三、POY含油一般以0.3~0.7﹪左右较为适当。
丝条含油率低会使纤维松散,摩擦阻力增大,发生毛丝;若含油量过高,会造成油污染增加。
四、造成纺丝细丝的原因有哪些?主要原因是组件原因:1、喷丝板镜检不干净;2、分配板不干净;3、组件组装不合格;4、铲板不及时等,出现这种情况,应立即铲板或更换组件。
五、在什么情况下需要紧急更换组件?1、纺丝发生细丝,硬头丝、竹节丝等不正常丝,经板面清理后仍不能清除;2、组件漏浆严重,无法正常生产;3、卷绕毛丝、断头多,检查导丝器,丝道无损伤。
六、熔体压力有哪三种?怎样设定熔体压力?熔体压力通常有螺杆出口压力(一般系过滤器前压)、滤后压力和组件压力三种。
滤后压力的确定一般是减去熔体管道的压力损失,保证熔体进入计量泵前的工作压力(一般不低于3.0MPa),不致使各计量泵吐出量有差异。
涤纶短纤维纺丝工艺及其影响因素.

• (2)风湿: 65~85%;风湿对卷绕丝双折射率和纺丝稳定性 影响大 影响:冷却风带湿度→卷绕丝在纺丝甬道中的带电↓→飘丝↓
→空气比热和热焓↑→纺丝甬道中冷却风和丝束温度恒定
8
• (三)丝条冷却固化条件 • (3)风速(风量) :0.3~0.7m/s,与熔体吐出量有 关 • (4)吹出距离(缓冷区):吹风窗(环)与板面距 离 ,15cm;吹风面距丝束外缘距离1cm;高度20cm;环吹 头内经比喷丝板直径大2cm;风经倾斜多孔板到阻尼 层(由金属网、金属毡等材料制成)再送入纺丝筒 • (5)纺丝甬道:保护纤维并继续冷却。3.2-7m,圆 管Φ280mm。一般3.5m,甬道长,气流紊乱,湍流 严重,丝的摆动幅度大,碰撞摩擦
线密度波动
组件结构
13
7
• (孔分配板-纺 丝筒 • 2.工艺控制: • (1)风温:范围:20~30℃,±1 ℃,组件调换率、卷绕丝 双折射率、卷绕丝条干不匀率最低
影响: 风温↑→熔体丝条冷却不充分→并丝、粘结丝↑→卷绕丝条干不匀率↑ 风温↓→熔体在喷丝孔处快速冷却→拉伸应力↑→初生纤维预取向度↑,径向 双折射率差异大→纺丝性↓→能耗大
4
• 3.熔体均匀性 • (1)粘度:切片结构不匀或有凝胶粒子使粘
度不匀,从而使丝条结构不匀,出现硬头丝, 导致拉伸不匀 • (2)杂质:会阻塞喷丝孔,造成滤层压力升 高和使用周期缩短
• 熔体粘度不匀或存在胶粒会导致纺丝断头、线密度 不匀、产生硬头丝、后拉伸困难、染色不匀等缺陷
• 原因: • 原料差异;干燥均匀;熔融和纺丝过程杜绝与 氧气接触,防止氧化降解;控制加热区温度, 减少波动
10
• 2.纺丝(卷绕)速度:指牵引辊1000m/min • 影响:纺速↑→纺丝线上速度梯度↑、丝束与冷空气的摩擦阻 力↑→ 卷绕丝预取向度↑(双折射↑)、后拉伸倍数↓(初生 纤维内应力增大,沸水收缩率增大) 纺速↓→丝束张力↓→卷绕时发生跳动→纺丝稳定性↓、并丝↑ 喂入轮的速度:约提高1% • 3.喷丝头拉伸比:第一导丝盘速度与熔体喷出速度之比 • 影响:喷丝头拉伸比↑→后拉伸倍数↓→对卷绕丝预取向度影 响小 • 4.卷绕车间温湿度:夏20~27℃,冬20℃ ;相对湿度 60~75%
第三章熔体纺丝工艺原理总结

第三章熔体纺丝工艺原理总结概述熔体纺丝属于聚合物直接纺丝方法,相对于溶液纺丝方法而言,工艺简单,速度快,对环境影响较小,适合于几乎所有热塑性聚合物的纺丝。
溶液纺丝分为干法纺丝(使用挥发性溶剂)和湿法纺丝(采用非挥发性溶剂)两种方法。
由于涉及到溶剂的回收和物质交换,因此纺丝速度低于熔体纺丝,而且溶液纺丝成形过程中丝条所经受的拉伸少,纤维强力低,因此应用很少,只有少数聚合物纺丝使用。
PP、PE、PA 和PET一般采用熔体纺丝;醋酯、聚氨酯和一部分PAN采用干法纺丝;粘胶纤维、维纶、铜氨纤维和大部分PAN纤维采用湿法纺丝。
思考题:试比较熔体纺丝、干法纺丝和湿法纺丝法的工艺特征和产品特征。
第一节熔体纺丝成网工艺原理聚合物切片送入螺杆挤出机,经熔融、挤压、过滤、计量后,由喷丝孔喷出,长丝丝束经气流冷却牵伸后,均匀铺放在凝网帘上,形成的长丝纤网经固网工序(热粘合、化学粘合、水刺或针刺)加固后成为熔体纺丝成网法非织造材料。
1、工艺流程为:聚合物切片→切片烘燥→熔融挤压→纺丝→冷却→牵伸→分丝→铺网→加固→切边→卷绕2、纺粘非织造工艺参数:聚合物种类、熔融挤压条件、纺丝孔尺寸、冷却空气、拉伸/牵伸方式、固网方法(重点掌握热轧粘合工艺参数对纺粘非织造布结构和性能的影响)。
思考题:试画出化纤长丝生产和纺粘非织造布生产工艺流程图,并标出每个工艺步骤的名称和作用。
一、熔体纺丝工艺特点熔体纺丝工艺具有过程简单和纺丝速度高的特点,在熔体纺丝过程中,成纤高聚物经历了两种变化,即几何形状的变化和物理状态的变化。
几何形状的变化是指成纤高聚物经过喷丝孔挤出和拉长而形成连续细丝的过程;物理变化即先将高聚物变为易于加工的流体,挤出后为保持已经改变了的几何形状和取得一定的化纤结构,使高聚物又变为固态。
原则上讲,分解温度高于熔点温度(或流动温度)的热塑性高聚物都可以采用熔体纺丝法。
二、熔体纺丝工艺过程(以纺粘法非织造布生产过程为例)主要步骤:―高聚物纺丝熔体的制备;―熔体自喷丝孔挤出/纺丝;―挤出的熔体细流的冷却和拉伸成形;―成形的纤维长丝铺网与固网。
螺杆挤压机操作规程

螺杆挤压机操作规程一、螺杆挤压机工作原理螺杆挤压机进行污泥脱水分为两个过程:1、旋转过滤:污泥经絮凝剂絮凝后,形成一定强度的絮团,含有大量自由水的固液混合物经立式反应器溢流口进入旋转过滤机,污泥在螺旋轴叶片的推动下向前运动,由于重力作用进行自由脱水,滚筒与螺旋转向相反,使污泥在滚筒内不断翻滚,把絮团内部自由水不断的滤出,浓缩后的污泥经螺旋叶片推送中出料口,进入下一级脱水工序。
2、螺旋挤压:预脱水完的污泥经进料斗进入螺旋挤压机后,污泥在锥度螺旋轴和变径螺旋的作用下,使物液产生体积上压缩,从而使料液中的水分通过孔状滤筒迅速被分离出去,而固体物在不断压缩的作用下含水率逐渐下降而成为我们所需要的滤饼,最后在螺旋的输送作用下排出机外。
二、螺杆挤压机操作工艺流程目前,螺杆挤压机用于厌氧浮渣处理。
其基本处理工艺流程如上图:污泥通过添加PAM(聚丙烯酰胺絮凝剂)、PAC(聚合氯化铝)调理后,进入旋转过滤机浓缩过滤,预处理后污泥再进入螺旋挤压机进行深度脱水。
三、螺杆挤压机操作规程一)、开机前的准备工作1、检查设备的电器控制是否正常,确保设备处于正常的工作状态。
2、检查絮凝剂准备是否充足,絮凝剂制备系统储槽内保证有足够的药剂(不低于药剂储糟液位的三分之二),并开始制备絮凝药剂(药剂配比浓度为千分之二)。
3、系统的工艺条件是否充足,工艺水供给是否正常(工艺水供给压力不低于0.4 Mpa)。
4、确认进料阀门均已打开,液位计显示正常,DCS控制系统正常。
二)、开、停机程序形成较好絮团。
2、启动旋转过滤机的6-冲洗电磁阀及1-清水泵,调整冲洗水频率及压力,确保滤筒滤网出水顺畅,观察旋转过滤机出料浓度,使其达到合适的出料浓度。
3、观察污泥的絮凝效果,将聚合效果调整到絮团的机械强度和滤水性等技术特点符合挤压机的要求,如效果不佳,可通过调整滚筒,螺旋转速及立式絮凝反应器的搅拌速度,逐步调整。
4、等到挤压料仓内的液位达到指定液位后(50%以上),再启动4-污泥脱水机。
锦纶6生产工艺流程

1 概述:锦纶6主要以PA6干切片经熔融纺丝、牵伸、卷绕制取各种规格和用途的牵伸丝。
由于聚合物的特性不同,纺丝工艺与其它纤维有一定差异。
我公司生产的PA6产品基本流程为:干切片——投料斗——中间料仓——螺杆挤压机——纺丝箱体——熔体计量泵——纺丝组件、喷丝板——卷绕机牵伸辊——卷绕头卷饶成形——成品检验——成品——包装——入库2 切片投料及挤出:PA6干切片开包加入到投料斗,然后由气动阀控制进入中间料仓,被连续送入到螺杆挤压机内进行熔融、混合和计量。
螺杆挤压机有加热量装置,温度分区按工艺要求调定,螺杆又交流电机驱动,变频控制达到要求时挤出压力。
3 纺丝:熔体在螺杆机头压力下进入分配管道,按等距原则被均匀地送到各纺丝位,每个纺丝位带有高精密熔体计量泵,熔体经计量泵精确计量后,被均匀送到各个纺丝组件,经金属砂和滤网过滤后从喷丝板喷出成丝。
从喷丝板出来的熔融态丝条在优化的侧吹风装置中被以层流的侧吹风冷却。
丝条变为固态,纤维结构发生结晶取向变为大分子。
上油装置采用高精密的上油泵供油,使丝条具有工艺要求的含油量。
纺丝箱体和熔体管道都被保温至一定温度。
4 卷绕成形:纺丝下来的丝条经垂直再进入卷绕间,经分丝罗拉换向、分丝,然后在加热的牵伸辊(HOY为冷辊)上经牵伸网络后,进入高速卷绕头自动卷落筒。
5 成品:成品丝饼经物检织袜染色,分级后进入包装为成品。
锦纶6工业丝的生产工艺产品用途: 本机主要用于锦纶6工业丝的生产,适用于切片熔融纺丝牵伸卷绕一步法生产工艺。
主要规格:工艺流程: (干燥过的切片)→螺杆挤压机→出料头→熔体管道→纺丝箱→带徐冷及单体抽吸的侧吹风装置→上油装置→切丝、吸丝装置→喂入辊→热牵伸辊(四对)→网络器→卷绕头→成品丝筒。
双螺杆挤出机纺制的纤维素纤维
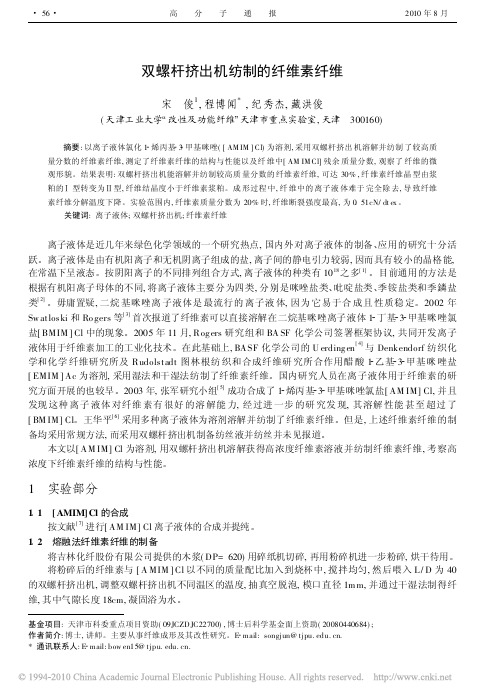
第8期
高
分
子
通
报
# 57 #
1 3
纤维中残余离子液体测定
分别称取不同质量分数的纤维 M 1 , 将其粉碎后置于三口烧瓶中, 加蒸馏水至烧瓶容量 2/ 3 处, 加热 至 90 ∃ , 搅拌 24h 至纤维变成白色 , 其间换水 3 次。洗过的纤维经真空烘箱烘干 , 称取质量 M 2 , 则 残余离子液体量 M 0 = M 1 - M 2 离子液体质量分数= M0 % 100 % M2
参考文献:
[ 1] [ 2] [ 3] [ 4] [ 5] [ 6] [ 7] [ 8] [ 9] 王均凤 , 张锁江 , 陈慧萍 . 过程工程学报 , 2003, 3( 2) : 177~ 185 张锁江 , 吕兴梅 . 离子液体 ∋ ∋ ∋ 从基础研究到工业应用. 北京 : 科学出版社 , 2006, 60 Sw at loski R P, Spear S K , H olbrey J D , et a1 J A m Ch em Soc, 2002, 124, ( 1) : 4974~ 4975 Frank H , Frank M , Eric U . Chem Fibers Int , 2006, 6: 342~ 343 Zhang H , Wu J, Zhang J, et al . M acr om ol ecu les , 2005, 38, 8272~ 8277 王华平 , 刘巍巍 , 张玉梅 , 王彪 . 中国 , 1851063, 2006, 10, 25 任强 , 武进 , 张军 , 等 . 高分子学报 , 2003, ( 3) : 448~ 445 杨之礼 , 王庆瑞 , 邬国铭 . 粘胶纤维工艺学 . 北京 : 纺织工业出版社 , 1991, 45~ 52 晏根成 . A M IM Cl 离子液体的合成与应用研究 . 哈尔滨 : 哈尔滨工程大学 , 2007
挤出机常识与工艺(温度、螺杆)

挤出机常识与工艺(温度、螺杆)一、挤出机分类认识产品代号及规格参数例如:SHJM-Z40×25×800,表示:螺杆直径为40mm,长径比为25,牵引辊筒长为800mm 的双螺杆混合塑料挤出改塑薄膜机。
1、“SH”类别代号,指双螺杆混合型(也有写:SHSJ,SJ指塑料挤出机)。
2、“J”组别代号,指挤出机。
3、“M”指品种代号,指吹塑薄膜机。
4、“Z”指辅助代号,指主要机组,另如是“F”指辅助机。
5、“40×25×800”指规格参数,指螺杆有直径为40mm,长径比为25,牵引辊筒长为800mm。
6、最后一位为厂商识别序号,一般不出现,被省略。
二、双螺杆混合挤出机的功能参数1、“D”为直径,衡量产量大小的一个重要参数。
2、“L/D”,指长度与直径的比例,直接影响到塑化度,是衡量用途的标志,一般塑料改性,用30-40左右,常用36:1或30:1。
3、“H”,螺槽深度,指其容料空间之大小。
4、“e”螺棱厚度,工艺上体现在剪切之大小。
5、“6”螺杆与机筒之间隙,挤出机质量的一个重要参数,一般在0.3-2mm,越过5mm挤出机是警介线。
6、“N”主机转速,指其最高值,指一个加工调整范围,极大影响产量及中高低速之划分。
(国产机一般500-600r/min),(如:max:600r/min,低速: 230-240r/min 、中速350r/min 、高速450-600r/min。
7、“P”,电机功率及加热功率。
三、螺杆排列及其工艺设定①螺杆的分段及其功能(1)螺杆一般分:输送段、熔融段、混炼段、排气段、均化段5个段。
a、输送段,输送物料,防止溢料。
b、熔融段,此段通过热传递和摩擦剪切,使物料充分熔融和均化。
c、混炼段,使物料组分尺寸进一步细化与均匀,形成理想的结构,具分布性与分散性混合功能。
d、排气段,排出水汽、低分子量物质等杂质。
e、均化(计量)段,输送和增压,建立一定压力,使模口处物料有一定的致密度,同时进一步混合,最终达到顺利挤出造粒的目的。