粉体材料粒度分布及颗粒形貌控制的实例分析
粉体粒径控制

粉体粒径是影响粉体性质和应用的非常重要因素,控制粉体粒径是一个复杂的过程,涉及到制备工艺、设备选择、操作条件等多个方面。
下面我将从不同角度阐述粉体粒径控制的重要性,并探讨一些控制方法。
首先,从粉体的应用领域来看,不同粒径的粉体在各个领域中都有广泛的应用。
例如,在建筑材料中,粒径适中的粉体可以作为骨料,提高混凝土的强度和耐久性;在医药领域,粒径较小的粉体可以方便运输和储存,同时易于进入细胞内部,提高药物的生物利用度。
因此,控制粉体粒径是满足不同应用需求的关键。
其次,粉体的粒径对其流动性、填充性、分散性等性质有显著影响。
粒径较粗的粉体往往流动性差,需要添加助流剂;而粒径较细的粉体则容易散布不均,需要采用分散剂。
这些性质直接影响着生产效率和产品质量,因此控制粉体粒径对于提高生产效率和产品质量具有重要意义。
那么,如何控制粉体粒径呢?首先,我们可以选择合适的制备工艺和设备。
例如,喷雾干燥法、气流磨等设备可以制备粒径较细的粉体;干法研磨、湿法研磨等工艺可以控制粉体的粒径分布。
其次,我们可以通过调整操作条件来控制粉体的粒径。
例如,在球磨过程中,转速和时间都会影响粉体的粒径分布;在气流磨中,风速和磨介速度也会影响粉体的粒径。
此外,还可以采用机械力化学法、等离子法等新型制备技术来控制粉体的粒径。
在实际生产中,我们还需要考虑到许多影响因素,如原料的性质、环境的湿度和温度、设备的清洁度等。
这些因素都会对粉体的粒径产生影响,需要我们采取相应的措施进行控制和调整。
例如,在湿度较大的环境中生产粉体时,我们可以通过添加干燥剂或采取其他干燥措施来降低湿度对粉体粒径的影响;对于设备的清洁度,我们可以定期进行设备清洗和消毒,以确保生产环境的卫生和安全。
总之,粉体粒径控制是满足不同应用需求和提高生产效率和产品质量的关键。
我们需要选择合适的制备工艺和设备、调整操作条件以及采用新型制备技术来控制粉体的粒径。
同时,我们还需要注意到许多其他影响因素,并采取相应的措施进行控制和调整。
粒度分布 标准和结果

粒度分布标准和结果
粒度分布描述了粉体样品中不同粒径颗粒的分布情况,具体是指不同粒径颗粒占颗粒总量的百分数。
其可以通过特定的仪器和方法进行测量,主要存在两种形式:区间分布和累计分布。
区间分布,也被称为微分分布或频率分布,表示一系列粒径区间中颗粒的百分含量。
这为粒度分布提供了更细致的信息,可以显示出在哪些粒径范围内颗粒最为集中。
累计分布,也叫积分分布,表示小于或大于某粒径颗粒的百分含量。
这种分布形式提供了对颗粒总体积或质量的相对比较,有助于了解主要颗粒群的大小。
对于粒度分布的标准,这主要取决于具体的应用和行业要求。
例如,在制药行业中,粒度分布可能需要在特定的粒径范围内,颗粒的含量不得低于一定百分比;而在陶瓷或磨料制造中,可能需要颗粒尽可能均匀分布,以获得最佳的物理性能。
对于粒度分布的结果,这通常以表格或图形的方式呈现。
图表上会显示一系列粒径区间与对应颗粒含量的关系,或者是颗粒含量随粒径变化的趋势。
对于累计分布,则可以绘制出小于或大于某粒径的颗粒百分含量曲线图。
为了确保结果的准确性和可靠性,通常需要对粒度分布进行多次测量,并使用统计方法对结果进行分析。
这包括计算平均值、标准差等指标,以评估粒度分布的集中程度和离散程度。
总的来说,粒度分布是描述粉体材料特性的重要参数之一,对于
产品的质量控制、工艺优化和性能预测都具有重要意义。
陶瓷粉末球形-概述说明以及解释
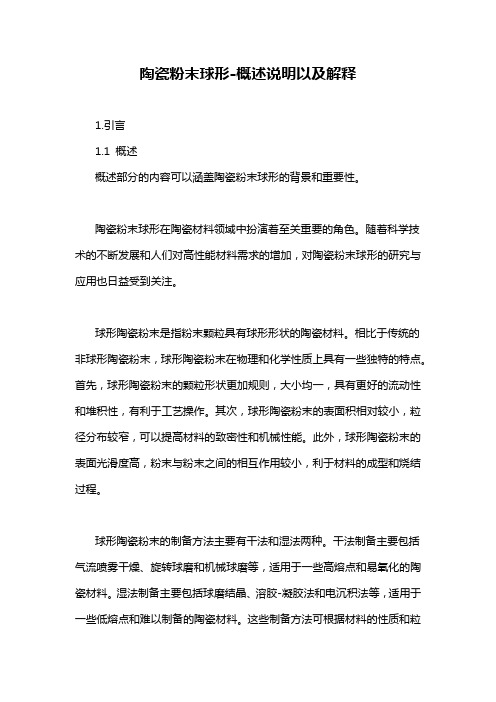
陶瓷粉末球形-概述说明以及解释1.引言1.1 概述概述部分的内容可以涵盖陶瓷粉末球形的背景和重要性。
陶瓷粉末球形在陶瓷材料领域中扮演着至关重要的角色。
随着科学技术的不断发展和人们对高性能材料需求的增加,对陶瓷粉末球形的研究与应用也日益受到关注。
球形陶瓷粉末是指粉末颗粒具有球形形状的陶瓷材料。
相比于传统的非球形陶瓷粉末,球形陶瓷粉末在物理和化学性质上具有一些独特的特点。
首先,球形陶瓷粉末的颗粒形状更加规则,大小均一,具有更好的流动性和堆积性,有利于工艺操作。
其次,球形陶瓷粉末的表面积相对较小,粒径分布较窄,可以提高材料的致密性和机械性能。
此外,球形陶瓷粉末的表面光滑度高,粉末与粉末之间的相互作用较小,利于材料的成型和烧结过程。
球形陶瓷粉末的制备方法主要有干法和湿法两种。
干法制备主要包括气流喷雾干燥、旋转球磨和机械球磨等,适用于一些高熔点和易氧化的陶瓷材料。
湿法制备主要包括球磨结晶、溶胶-凝胶法和电沉积法等,适用于一些低熔点和难以制备的陶瓷材料。
这些制备方法可根据材料的性质和粒径要求进行选择,以获得理想的球形陶瓷粉末。
球形陶瓷粉末的应用领域广泛。
在先进陶瓷材料中,球形陶瓷粉末常用于制备陶瓷膜、陶瓷纤维和陶瓷基复合材料等。
此外,球形陶瓷粉末还可以应用于电子器件、能源储存和传感器等领域。
通过控制球形陶瓷粉末的制备方法和粒径分布,可以调控材料的性能,满足不同应用场景的需求。
综上所述,球形陶瓷粉末具有良好的物理和化学性质,制备方法多样,应用领域广泛。
研究和开发球形陶瓷粉末具有重要意义,将在材料科学和工程领域产生深远的影响。
在接下来的文章中,我们将深入探讨球形陶瓷粉末的制备方法和应用领域,并展望其未来的发展趋势。
1.2 文章结构文章结构部分的内容可以包括以下信息:文章结构部分的目的是为读者提供对整篇文章的概览,让读者能够清晰地了解文章的组织结构和各个部分的内容。
本篇文章分为引言、正文和结论三个部分。
引言部分包括概述、文章结构和目的三个小节。
粉体粒度测试实验报告
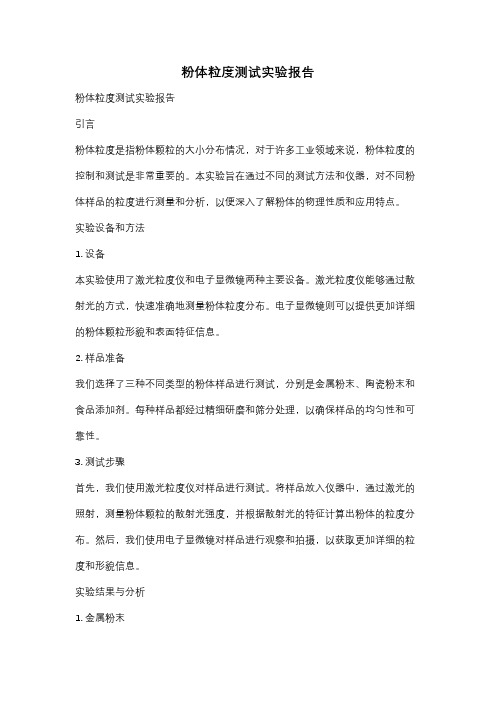
粉体粒度测试实验报告粉体粒度测试实验报告引言粉体粒度是指粉体颗粒的大小分布情况,对于许多工业领域来说,粉体粒度的控制和测试是非常重要的。
本实验旨在通过不同的测试方法和仪器,对不同粉体样品的粒度进行测量和分析,以便深入了解粉体的物理性质和应用特点。
实验设备和方法1. 设备本实验使用了激光粒度仪和电子显微镜两种主要设备。
激光粒度仪能够通过散射光的方式,快速准确地测量粉体粒度分布。
电子显微镜则可以提供更加详细的粉体颗粒形貌和表面特征信息。
2. 样品准备我们选择了三种不同类型的粉体样品进行测试,分别是金属粉末、陶瓷粉末和食品添加剂。
每种样品都经过精细研磨和筛分处理,以确保样品的均匀性和可靠性。
3. 测试步骤首先,我们使用激光粒度仪对样品进行测试。
将样品放入仪器中,通过激光的照射,测量粉体颗粒的散射光强度,并根据散射光的特征计算出粉体的粒度分布。
然后,我们使用电子显微镜对样品进行观察和拍摄,以获取更加详细的粒度和形貌信息。
实验结果与分析1. 金属粉末经过测试,金属粉末的粒度分布主要集中在10-50微米之间,呈现出较为均匀的分布特征。
电子显微镜观察发现,金属粉末颗粒表面较为光滑,形状规则,没有明显的凹凸和气孔。
这种粉末粒度适中,适合用于金属材料的加工和制备。
2. 陶瓷粉末陶瓷粉末的粒度分布相对较宽,主要分布在1-100微米之间。
电子显微镜观察发现,陶瓷粉末颗粒形状不规则,表面粗糙,存在一定数量的微小颗粒和孔隙。
这种粉末粒度分布广泛,适合用于陶瓷材料的制备和涂料的添加。
3. 食品添加剂食品添加剂的粉体粒度要求相对较高,需要粒度分布较为均匀,颗粒形状规则。
经过测试,食品添加剂的粒度主要分布在1-100微米之间,整体呈现出较为均匀的分布特征。
电子显微镜观察发现,食品添加剂颗粒表面光滑,形状规则,没有明显的杂质和气孔。
这种粉末粒度适中,适合用于食品加工和调味品的制备。
结论通过本次实验,我们成功地使用了激光粒度仪和电子显微镜对不同类型的粉体样品进行了粒度测试和分析。
碎散物料的粒度组成及分析
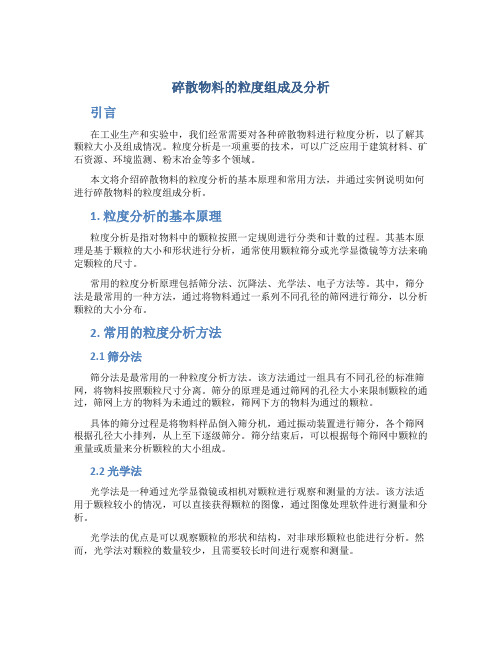
碎散物料的粒度组成及分析引言在工业生产和实验中,我们经常需要对各种碎散物料进行粒度分析,以了解其颗粒大小及组成情况。
粒度分析是一项重要的技术,可以广泛应用于建筑材料、矿石资源、环境监测、粉末冶金等多个领域。
本文将介绍碎散物料的粒度分析的基本原理和常用方法,并通过实例说明如何进行碎散物料的粒度组成分析。
1. 粒度分析的基本原理粒度分析是指对物料中的颗粒按照一定规则进行分类和计数的过程。
其基本原理是基于颗粒的大小和形状进行分析,通常使用颗粒筛分或光学显微镜等方法来确定颗粒的尺寸。
常用的粒度分析原理包括筛分法、沉降法、光学法、电子方法等。
其中,筛分法是最常用的一种方法,通过将物料通过一系列不同孔径的筛网进行筛分,以分析颗粒的大小分布。
2. 常用的粒度分析方法2.1 筛分法筛分法是最常用的一种粒度分析方法。
该方法通过一组具有不同孔径的标准筛网,将物料按照颗粒尺寸分离。
筛分的原理是通过筛网的孔径大小来限制颗粒的通过,筛网上方的物料为未通过的颗粒,筛网下方的物料为通过的颗粒。
具体的筛分过程是将物料样品倒入筛分机,通过振动装置进行筛分,各个筛网根据孔径大小排列,从上至下逐级筛分。
筛分结束后,可以根据每个筛网中颗粒的重量或质量来分析颗粒的大小组成。
2.2 光学法光学法是一种通过光学显微镜或相机对颗粒进行观察和测量的方法。
该方法适用于颗粒较小的情况,可以直接获得颗粒的图像,通过图像处理软件进行测量和分析。
光学法的优点是可以观察颗粒的形状和结构,对非球形颗粒也能进行分析。
然而,光学法对颗粒的数量较少,且需要较长时间进行观察和测量。
2.3 沉降法沉降法是一种通过颗粒在液体中的沉降速率来分析颗粒大小的方法。
该方法适用于细颗粒和胶体颗粒的分析。
沉降法的基本原理是根据斯托克斯定律,颗粒在液体中的沉降速度与颗粒直径成正比。
通过测量颗粒在一定时间内的沉降距离和时间,可以计算出颗粒的大小。
3. 碎散物料粒度组成分析的实例假设我们需要对一种建筑材料中的碎散物料进行粒度组成分析。
均匀沉淀法制备超细α-Al2O3陶瓷粉体的形貌控制研究
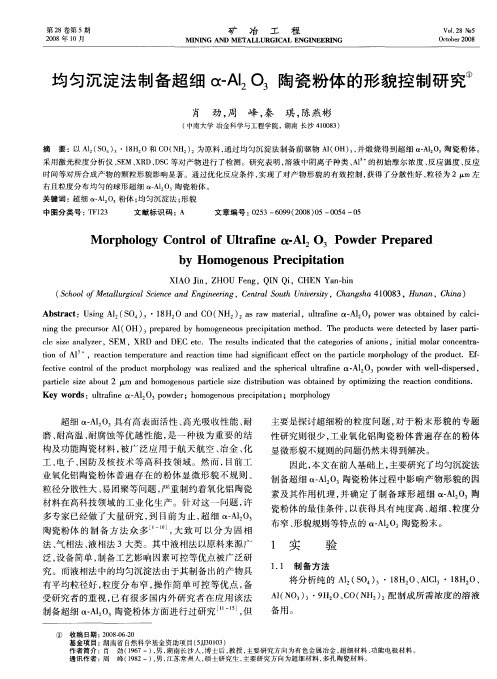
超细 0A 有高 表 面活性 、 【1 具 . O 高光 吸收 性 能 、 耐 磨、 耐高温 、 耐腐 蚀等 优 越 性 能 , 一种 极 为 重 要 的结 是
构及 功能 陶瓷材 料 , 广 泛应 用 于 航 天航 空 、 被 冶金 、 化 工、 电子 、 国防及 核 技 术 等高 科 技 领 域 。然 而 , 目前 工
第2 8卷第 5期
20 0 8年 1 O月
矿 冶 工 程
M I NG NI AND ETALLURGI M CAL ENGI NEER G
V0 . 8 № 5 12 0co e o 8 t b r2 o
均匀 沉淀 法 制备 超 细 O A2 3陶瓷 粉体 的形 貌控 制研 究① cI - 0
t n o “ i fA1 o
,
ra to e p r t r n e c in tm e h d sg iia tef c n t e p ril r h lg ft e p o u t Ef e ci n tm e au e a d r a t i a infc n fe to h a tce mo p o o y o h r d c . - o
采用激光粒度分析仪 、E X D、 S S M、 R D C等对产物进行 了检测 。研究表 明, 溶液 中阴离 子种类 、 l 的初始摩 尔浓度 、 A 反应温度 、 反应
时间等对所 合成产 物的颗粒形貌影 响显著 。通过优化反应条件 , 实现 了对产 物形貌 的有效 控制 , 获得 了分散性好 、 粒径为 2 m左
Ab t c :U igA 2 S 4 3・ 8 2 n O( H2 2 sr a r l ha n — 1 3 o e w so t ndb ac sr t s 1( O ) 1 H 0 a dC N ) a a m t a,u rf e A 2 w r a ba e ycli a n w e i i Op i — nn epeusr 1 O 3 rp rdb o oe eu r ii t nm to .T epout w r d t t yl e at i t rc r ( H) eae yh m gno s e pt i ehd h rd cs ee ee e b sr r— gh oA p p c ao cd a p i
粒度分析PPT课件
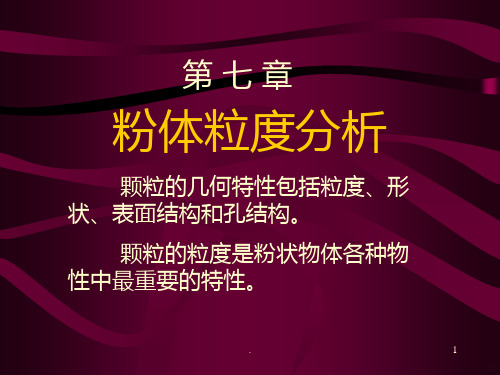
.
38
No Image
/10/29
.
39
nmin nmax n平均 S
特征粒径 x’min x’max x平均
S
检测 数
沉降 天平
1.09
1.36
1.19
0.08
28.5
38.7
33.2
3.70
12
激光 分析
0.81
0.99
0.89
0.05
21.5
28.3
25.6
2.09
12
.
31
激光法向细粉方向移动,细粉含量偏高。
因为其超声分散更彻底. 。
颗粒粒径累计分布表示小于(大于)某 粒径的颗粒占全部颗粒的百分含量与该粒 径的关系(积分曲线)。
.
15
平均粒径
粒径表示形式
算术平均直径
D1
1
100
idi
几何平均直径 logDg i logdi / i
调和平均直径 Dh i /i di
平均面积径 Ds idi2 / i
除了平均粒径,还须用偏差系数K偏 来说明粉体的均匀程度。
其中,
x 1 ln x S d 50
S ln d 50 d 16
d50, d16 分别为 筛析通过量为 50% 和16% 时 的粒径。
d50可作为特征粒径,相当于x’ ;S表示
颗粒分布宽度,相当于n值。
.
14
3. 粒群的平均粒径
实际粉体的颗粒大小也可以以平均粒径 表示。
颗粒粒径频率分布表示各个粒径相对应 的颗粒百分含量(微分曲线)。
1. 单个颗粒的粒径表示方法:
指定的线段:长轴径,短轴径,定方向径
固相烧结与液相烧结的影响因素

1以SiC 为例,分析影响液相烧结的因素及解决措施。
答:在液相烧结过程中,影响液相烧结的因素主要为以下几个方面:1、颗粒粒度与形状细颗粒有利于提高烧结致密化速度,便于获得高的最终烧结密度。
在颗粒重排阶段提高毛细管力便于固相颗粒在液相中移动(尽管会增加颗粒之间的摩擦力和固相颗粒之间的接触机会)。
在溶解-再析出阶段强化固相颗粒之间和固相/液相间的物质迁移加快烧结速度。
另外,细小晶粒的烧结组织有利于获得性能优异的烧结材料。
此外,颗粒重排阶段初期,颗粒形状影响毛细管力大小,形状复杂导致颗粒重排阻力增加,球形颗粒有利于颗粒重排,形状复杂的固相颗粒降低烧结组织的均匀性,综合力学性能较低在溶解-再析出阶段,颗粒形状的影响较小。
2、液相的影响[1]液相的粘度、表面张力、润湿性、数量等对烧结的影响。
液相的粘度愈低, 它们对固相的浸润愈好, 愈有利于烧结。
同时, 在一般情况下, 由于物质在液相中的扩散速度比在固相中快, 人们通常认为液相存在总是能促进烧结的, 但事实并非完全为人们所想像的那样。
在许多情况下液相存在反而阻碍烧结, 液相粘度降低和对固体浸润性能的改善并不一定总是有利于烧结的。
液相对烧结过程的作用主耍为两部分:首先是在液相毛细管力和由于表面曲率不同而引起的压力差的作用下所发生的固体颗粒重排过程,在这部分作用中, 液相对固相的浸润性能起重要作用。
其次为通过液相的重结晶过程。
润湿性液相对固相颗粒的表面润湿性好是液相烧结的重要条件之一,对致密化、合金组织与性能的影响极大。
润湿性由固相、液相的表面张力(比表面能)S γ、L γ以及两相的界面张力(界面能) SL γ所决定。
如图5—47所示:当液相润湿固相时,在接触点A 用杨氏方程表示平衡的热力学条件为cos S SL L γγγθ=+式中θ——湿润角或接触角。
完全润湿时,0θ=,cos SSL L γγγθ=+式变为S SL L γγγ=+;完全不润湿时,θ>90,则S L L S γγγ≥+。
颗粒球形度的表征、分级及其应用

颗粒球形度的表征、分级及其应用李 叶1殷喜平1*杨正红2(1. 中国石化催化剂有限公司 北京 100029;2. 仪思奇(北京)科技发展有限公司 北京 100096)摘 要 粉体颗粒的两个重要特性就是粒度和形貌,而颗粒形貌最重要的特征是球形度。
虽然球形度如此重要,但其概念却异常混乱,定义多达10种以上。
国家标准中的球形度名称及定义也各不相同,造成了使用上的混乱和困扰。
本文旨在以ISO 9276-6为基础,对涉及球形度的所有粒形参数进行了梳理,力求给出更加科学的命名、定义及分级,并明确其参数表征特点,使术语更加规范。
本文明确了宏观(磨圆度/紧实度)、介观(类球度/圆润度)和微观(钝度/粗糙度)三个不同层级的球形度表征参数,提出需要针对颗粒特性、产品和工艺性能的特定应用,选择最适当的球形度表征层级和颗粒形状参数。
关键词 图像法;颗粒形状;球形度;卫星化粉体;圆润度;钝度 中图分类号 TB44 文献标志码 ACharacterization,classification and application of particle sphericityLi Ye 1; Yin Xiping 1; Yang Zhenghong 2( 1. SINOPEC Catalyst Co., LTD., Beijing 100029, China; 2. Insearch Technology Development Beijing Ltd, Beijing 100096, China)Abstract Size and shape are two important characteristics of powder particles, and the most important characterization of particle shape is sphericity. Despite of so important, the concept of sphericity is very confused which has more than 10 definitions ,even the names and definitions of sphericity in the national standards are also different, which caused in confusion and trouble in application. Based on ISO 9276-6, this paper aims to sort out all particle parameters related to sphericity, try to give more scientific term in Chinese, definition and classification, and clarify the characteristics of parameters for more standardized terms. Three different levels of sphericity characterization parameters are determined, involving macroshape (psephicity (irregularity )/ compactness), mesoshape (sphericity / roundness) and microshape (bluntness / roughness) descriptors. It is proposed that the most appropriate level of sphericity characterization and particle shape descriptors should be selected based on the specific application of particle characteristics, products and process performance.Keywords Imaging method ;Particle shape; Sphericity; Satellite powder; Roundness; Bluntness近10年以来,以颗粒粒径和颗粒含量两个参数为基础进行的二维粒度分析正在向以颗粒粒径、颗粒形状和颗粒含量三个参数为基础的三维分析快速发展。
水泥的最佳颗粒分布及其评价方法
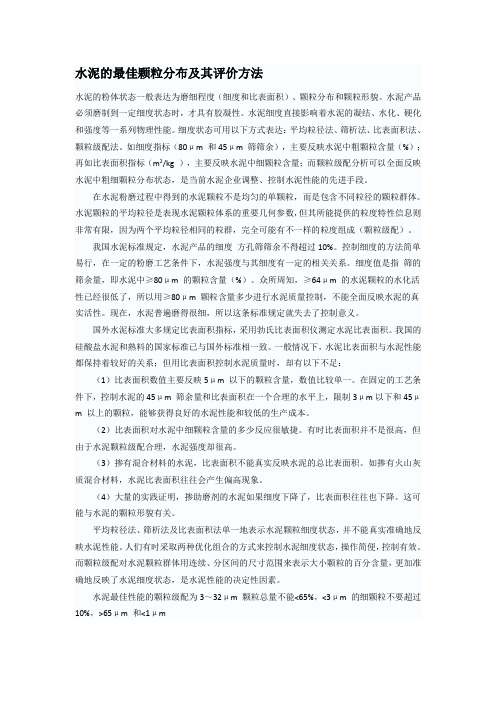
水泥的最佳颗粒分布及其评价方法水泥的粉体状态一般表达为磨细程度(细度和比表面积)、颗粒分布和颗粒形貌。
水泥产品必须磨制到一定细度状态时,才具有胶凝性。
水泥细度直接影响着水泥的凝结、水化、硬化和强度等一系列物理性能。
细度状态可用以下方式表达:平均粒径法、筛析法、比表面积法、颗粒级配法。
如细度指标(80μm 和45μm 筛筛余),主要反映水泥中粗颗粒含量(%);再如比表面积指标(m2/kg ),主要反映水泥中细颗粒含量;而颗粒级配分析可以全面反映水泥中粗细颗粒分布状态,是当前水泥企业调整、控制水泥性能的先进手段。
在水泥粉磨过程中得到的水泥颗粒不是均匀的单颗粒,而是包含不同粒径的颗粒群体。
水泥颗粒的平均粒径是表现水泥颗粒体系的重要几何参数,但其所能提供的粒度特性信息则非常有限,因为两个平均粒径相同的粒群,完全可能有不一样的粒度组成(颗粒级配)。
我国水泥标准规定,水泥产品的细度方孔筛筛余不得超过10%。
控制细度的方法简单易行,在一定的粉磨工艺条件下,水泥强度与其细度有一定的相关关系。
细度值是指筛的筛余量,即水泥中≥80μm 的颗粒含量(%)。
众所周知,≥64μm 的水泥颗粒的水化活性已经很低了,所以用≥80μm 颗粒含量多少进行水泥质量控制,不能全面反映水泥的真实活性。
现在,水泥普遍磨得很细,所以这条标准规定就失去了控制意义。
国外水泥标准大多规定比表面积指标,采用勃氏比表面积仪测定水泥比表面积。
我国的硅酸盐水泥和熟料的国家标准已与国外标准相一致。
一般情况下,水泥比表面积与水泥性能都保持着较好的关系;但用比表面积控制水泥质量时,却有以下不足:(1)比表面积数值主要反映5μm 以下的颗粒含量,数值比较单一。
在固定的工艺条件下,控制水泥的45μm 筛余量和比表面积在一个合理的水平上,限制3μm以下和45μm 以上的颗粒,能够获得良好的水泥性能和较低的生产成本。
(2)比表面积对水泥中细颗粒含量的多少反应很敏捷。
显微镜法测试粉体粒度粒度分布及形貌 1

实验二显微镜法测试粉体粒度、粒度分布及形貌一、目的意义显微镜就是少数能对单个颗粒同时进行观测与测量的方法。
除颗粒大小外,它还可以对颗粒的形状(球形、方形、条形、针形、不规则多边形等)、颗粒结构状况(实心、空心、疏松状、多孔状等)以及表面形貌等有一个认识与了解。
因此显微镜法就是一种最基本也就是最实用的测量方法,常被用来作为对其她测量方法的一种校验甚至确定的方法。
本实验的目的:通过使用生物显微镜观察粉末的形状与粒度掌握:1、制样方法及计算方法2、数据处理3、粒度分布曲线的描绘二、方法实质生物显微镜就是透光式光学显微镜的一种。
用生物显微镜法检测粉末就是一般材料实验室中通用的方法。
虽然计算颗粒数目有限。
粒度数据往往缺乏代表性,但它就是唯一的对单个颗粒进行测量的粒度分析方法。
此法还具有直观性可以研究颗粒外表形态。
因此称为粒度分析的基本方法之一。
测试时首先将欲测粉末样品分散在载玻片上。
并将载玻片置于显微镜载物台上。
通过选择适当的物镜目镜放大倍数与配合调节焦距到粒子的轮廓清晰。
粒径的大小用标定过的目镜测微尺度量,样品粒度的范围过宽时,可通过变换镜头放大倍数或配合筛分法进行。
观测若干视场,当计数粒子足够多时,测量结果可反映粉末的粒度组成,进而还可以计算粉末平均粒度。
三、仪器与原材料物镜测微尺、标准测微尺、生物显微镜、分散剂(酒精、环乙醇等)、玻璃棒、吸管粉末试样(雾化粉、电解粉)四、测试方法1、显微镜使用前的准备将目镜测微尺放入所选用的目镜中,并将目镜与物镜安装在显微镜上,将标准测微尺(每小格10微米)置于载物台上通过旋转公降螺钉(注意:不得使物镜接触载玻片1),调节焦距标定目镜测微尺一格比代表的长度(u)。
2、样品的制备用显微镜测试的粉末应经过筛分,否则由于粉末粒度范围过宽,测试中需经常更换物镜或目镜,不仅造成测试工作的不便而且由于视场范围的变化引起测试的不准确。
粉末样品由于具有发达的表面积,因而有较高的表面能,使粉末颗粒产生聚集,形成团块,影响粉末粒度的测定,所以制样过程中应使颗粒聚集体分散成单个颗粒,一般就是将少量粉末样品(0.01克左右)放置在干净的载玻片上,滴上数滴分散介质,用另一干净载玻片覆盖其上。
颗粒质量全程控制
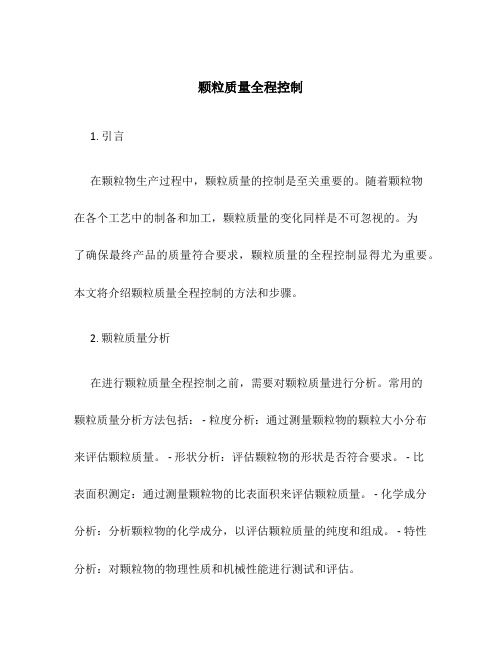
颗粒质量全程控制1. 引言在颗粒物生产过程中,颗粒质量的控制是至关重要的。
随着颗粒物在各个工艺中的制备和加工,颗粒质量的变化同样是不可忽视的。
为了确保最终产品的质量符合要求,颗粒质量的全程控制显得尤为重要。
本文将介绍颗粒质量全程控制的方法和步骤。
2. 颗粒质量分析在进行颗粒质量全程控制之前,需要对颗粒质量进行分析。
常用的颗粒质量分析方法包括: - 粒度分析:通过测量颗粒物的颗粒大小分布来评估颗粒质量。
- 形状分析:评估颗粒物的形状是否符合要求。
- 比表面积测定:通过测量颗粒物的比表面积来评估颗粒质量。
- 化学成分分析:分析颗粒物的化学成分,以评估颗粒质量的纯度和组成。
- 特性分析:对颗粒物的物理性质和机械性能进行测试和评估。
3. 颗粒质量控制方法在全程控制颗粒质量的过程中,以下几个方法是常用的:3.1 原材料质量控制颗粒质量的全程控制始于原材料的质量控制。
确保所使用的原材料符合要求的标准是保证最终产品质量稳定的前提。
进行原材料质量控制可以采取以下措施: - 选择合适的供应商,确保原材料的稳定供应。
- 制定严格的进货标准,对原材料的外观、纯度、含水量等指标进行监控。
- 对每批原材料进行化学成分分析和物理性能测试,确保符合要求。
3.2 工艺参数控制在颗粒物的制备和加工过程中,工艺参数对颗粒质量起着至关重要的作用。
控制以下工艺参数可以实现颗粒质量的控制: - 温度控制:不同的颗粒物对于温度的要求不同,通过严格控制温度可以调控最终颗粒质量的物理性质。
- 搅拌速度控制:搅拌速度对颗粒物的形状和分布有着重要影响。
根据不同的要求,调整搅拌速度可以得到不同的颗粒形状。
- pH值控制:在某些颗粒物的合成过程中,pH值的控制对颗粒质量具有重要影响。
3.3 检测与监控在颗粒生产过程中,对颗粒质量进行实时检测和监控是确保颗粒质量全程控制的关键环节。
常用的检测和监控方法包括: - 在线粒度仪:实时监测颗粒物的粒度分布,并及时调整工艺参数,以保持颗粒质量稳定。
粉体材料粒度分布及颗粒形貌控制的实例分析

粉体材料粒度分布及颗粒形貌控制的实例分析制备粒度均一分散的超细粉是粉末结构形貌控制的主要目标之一。
调节体系过饱和度、添加晶种控制晶核数、促进或阻碍团聚的发生等,是粒度控制的主要策略。
在体系溶解度较大的情况下,Ostwald陈化也可调节颗粒粒径及其单分散性。
在化学沉淀制粉过程中,微观均匀混合是体系粒度控制的最主要内容。
•各个微小区域内过饱和度微小变化将导致晶核数目大量变化,从而使晶核大小不一。
•强制混合是保证微观状态一致、制取粒度均一的超细粉末的有效措施。
•由于超细粉体极大的表面能,粉末颗粒的形成除了经历了成核、生长等过程外,还可能发生聚结与团聚。
•如何有效地控制粉体的团聚也是超细粉末尺寸分布控制研究的一个重要内容。
二、粉体形貌控制粒子形貌包括形状、表面缺陷、粗糙度等,但主要指形状。
纳米粉体,尤其是超微颗粒往往表现出很多形状,除了与其晶型结构有关外,还取决于其合成方法及相应的操作条件。
如在湿化学法体系中,颗粒的形状对操作条件极其敏感,溶质浓度、反应体系中阴离子的种类、反应体系是否封闭等因素均可能影响颗粒的形状。
•一般认为,液相中的超微颗粒可选择性吸附溶液中的简单离子、络离子及有机化合物分子,且不同晶面上被吸附物的种类和数量均有所不同。
•而溶质浓度、阴离子种类、温度、pH值等操作条件的细微变化均可能影响晶面的吸附情况,这些吸附通过改变晶面的比表面能或生长速度常数而促进或抑制晶面的生长,进而影响超微颗粒的形状。
•因此,不同操作条件下形成的超微粒子往往呈现多种形态。
此外,添加剂也可改变粉体的形貌。
比如,在超细粉体α-Fe2O3合成中,研究者发现陈化时添加柠檬酸、酒石酸,α-Fe2O3粉末呈短柱状、片状或层状,而添加有机磷酸可以得到轴比很大的适宜作磁记录介质的针状粉末。
通过添加柠檬酸还可以制备得到阻燃材料用的等轴细棱形片铝钠石和细小片状Mg(OH)2。
添加异种物质进行粉末形状控制应考虑以下几点:•母晶的晶格结构、•剩余的原子价、•异种物质分子的极性基大小形状以及配位。
沉淀法制备纳米粉体及其形貌控制

制 , 易 发 生 不 均 匀 成 核 而 使 制 得 的 粉 体 粒 度 不
均匀。
2 2 间 接 沉 淀 法 .
作 者 简 介 : 字 菲 ( 9 4一) 女 , 程 师 。 王 16 , 工
淀 。 了避 免 共 沉 淀 法 本 质 上 存 在 分 别 沉 淀 的倾 向 , 为
纳 米 材 料 按 其 结构 形 态 分 为 4类 : 1 零 维 纳 米 ()
晶体 , 即纳 米 粒 子 ; 2 一 维 纳 米 晶体 , 在 一 维 方 向 () 即 上 晶粒 尺 寸 为 纳 米 量 级 ,如 纳 米 厚 度 的薄 膜 或 层 片 结 构 或 一 维 的纤 维 ;( )二 维 纳 米 晶体 , 所 谓 的量 3 即 子 线 ;( )三 维 纳 米 晶体 , 在 三 维 方 向上 的 晶 粒 均 4 即 为 纳 米 尺 度 , 常 指 纳 米 晶 体 材 料 。 米 材 料 的 制 备 通 纳 包 括 纳 米粉 体 、 米 薄膜 材 料 、 米 块 体 材 料 和 纳 米 纳 纳 复合 材料 的 合 成 与 制备 …。 湿 法 制 备 纳 米 氧 化 物 粉
2 3 水 解 沉 淀 法 .
体 , 优 点 是 无 需 苛 刻 的物 理 条 件 , 可 能 得 到 1 其 就 0~
1 m 性 能 较 优 异 的 纳 米 粉 体 l沉 淀 法 是 在 溶 液状 5n 。 态 下 将 不 同化 学 成 分 的 物 质 混 合 ,在 混 合 溶 液 中加
入 适 当 的 沉 淀 剂 以制 取 纳 米 粒 子 的 前 驱 体 沉 淀 物 ,
再将此沉淀物进 行洗涤 、 干燥 或煅 烧 , 而 制 得 相 应 从 的 纳 米 粒 子 。沉 淀 法 按 其 特 点 可 分 为 直 接沉 淀 法 、 闻
超声雾化热分解法制备超细SnO2粉体及其形貌和粒度控制

征产 物 的物相 。
3 实 验 结 果 与 讨 论
在 喷雾 热 分解 过 程 中 , 驱 体 溶 液 雾 化 为 细小 液 前
滴后 , 由载 气带 入 到 高 温 反 应 炉 中, 极 短 的 时 间 内 , 在 经过 溶剂 蒸发 、 质沉 淀 、 溶 干燥 、 属盐 热分 解 、 结 成 金 烧
蒸发, 引入 草 酸二 甲酯 使 液 滴 内部 与 表 层 同 时发 生沉 淀 反应 得到 了实 心球 形 氧化 铈 超 细 粉 ; T.S h n 用 amE 有 机锡 为前 驱体制 备 了 S O , 到 的一 次 颗粒 粒 径 在 n :得
1n 左右; 7m G.Ko ocn o E 等 以 S CI 5 O 为 rte k v n 4・ H2
学试 剂 厂) 采用 去离 子水 配 制成前 驱 体溶 液 。喷雾 热 , 分 解装 置 采 用 立 式 装 置 , 驱 体 溶 液 经 过 超 声 喷 嘴 前 ( ONO- K, 7 06 S TE 8 0 —0型 ) 化 成 液 滴 , 用 载 气 ( 雾 利 模 拟空气 成分 的 N: o 混合 气体 ) 入 电阻加 热 炉 内 与 2 带 的石英 管 ( 内径 为 9 mm, 为 1 0 mm) 5 长 40 中进行 反 应 。 收集 的粉体 经去 离子 水 超声 洗涤 3次 , 乙醇洗 涤 3次 ,
以有 效调 控 粉 体 的 粒 度 与 形 貌 。 当反 应 条 件 为 温 度
6 0 、 驱 体 盐 溶 液 浓 度 0 4 lL、 气 流 量 1 4 / 0℃ 前 . mo/ 载 2L h和 柠 檬 酸 浓 度 0 O 4 lL 得 到 的 S O2 粒 大 小 . 0 mo/ , n 颗
8 ℃真 空干 燥后送 样 分 析 。 O
第2章 粉体粒度分析及测量 PPT课件

等体积球当量径dV:与颗粒同体积球的直径
V = dV3
6
dv
3
6v
等表面积球当量径dS:与颗粒等表面积球的直径
d s
s
当量直径
等体积比表面积球当量径dSV 或面积体积直径,与颗 粒具有相同的表面积对体积之比,即具有相同的体积比
表面积的球的直径
d2 SV
S
/
6
d3 SV
V
d sv
6V S
dv3
np N
100%
这种频率与颗粒大小的关系,称为频率或频度分布。
h 1 2 3 4 5 6 7 8 9 10 11 12 总和
表2-5 颗粒大小的分布数据
最小:1.5 最大:12.2
△Dp/μm
np
1.0~2.0
5
2.0~3.0
9
3.0~4.0
11
4.0~5.0
28
5.0~6.0
58
6.0~7.0
60
统计平均径是平行于一定方向(用显微镜)测得的颗 粒投影像的线度,又称定向经。
粒径名称
定
义
定 方 向 径 沿一定方向测得颗粒投影的两平行线间的距
(Feret 径)dF 离。
定方向等分径
(Martin 径或马 沿一定方向将颗粒投影像面积等分的线段长度
丁直径)dM
)
定向最大径
沿一定方向测定颗粒投影像所得最大宽度的线 段长度
2、扁平度和伸长度
扁平度m
短径 厚度
b h
伸长度n
长径 短经
l b
3、丘奇(Church)形状因子
c
=
dF dM
4、圆形度
圆形度定义了颗粒的投影与圆的接近程度。
磷酸锰铁锂粉体指标

磷酸锰铁锂粉体指标磷酸锰铁锂是一种新型的锂离子电池正极材料,常用于电动汽车、电动自行车等储能设备中。
其粉体指标是评价其性能和质量的重要指标之一、本文将从结构、颗粒形貌、比表面积、粒度分布等方面介绍磷酸锰铁锂粉体的指标。
首先,磷酸锰铁锂的结构主要由锰酸锂(LiMn2O4)、锰酸亚铁(Li2Mn2O4)和锰酸黑色(LiMnO2)等组成。
这些组分的比例和配方对磷酸锰铁锂的性能有重要影响。
其中,锰酸锂是电池的正极活性物质,锰酸亚铁和锰酸黑色是电池的中性物质。
因此,磷酸锰铁锂的结构稳定性对于电池的循环寿命和容量保持率至关重要。
其次,磷酸锰铁锂的颗粒形貌对其电极性能也有很大影响。
一般来说,颗粒形状不规则或多面体的粉体比规则形状的粉体具有更好的电化学性能。
这是因为不规则形状的颗粒有更大的比表面积,可以提供更多的活性位点,从而增强电池的反应性能和放电容量。
第三,粒度分布是评价磷酸锰铁锂粉体质量的重要指标之一、通常使用粒度分析仪对磷酸锰铁锂粉体进行粒度分布测试,得到的数据可用于确定其平均粒径、粒径分散程度等参数。
较小的粒径可以提高电极材料的反应速率和离子传导性,但也容易引起颗粒堆积和极化现象。
因此,粒度分布的合理设计有助于提高磷酸锰铁锂电极材料的性能。
此外,磷酸锰铁锂粉体的比表面积也是评价其电极性能的重要参数之一、比表面积是指单位质量的材料拥有的表面积,通常用平方米/克(m²/g)来表示。
较大的比表面积表示颗粒的表面积较大,有更多的活性位点和电池反应界面,可以提高电极的电化学性能。
总之,磷酸锰铁锂粉体的指标包括结构、颗粒形貌、比表面积和粒度分布等。
这些指标对磷酸锰铁锂电池的性能和循环寿命有着重要影响,通过合理设计和控制磷酸锰铁锂粉体的指标,可以提高电池的性能和稳定性。
- 1、下载文档前请自行甄别文档内容的完整性,平台不提供额外的编辑、内容补充、找答案等附加服务。
- 2、"仅部分预览"的文档,不可在线预览部分如存在完整性等问题,可反馈申请退款(可完整预览的文档不适用该条件!)。
- 3、如文档侵犯您的权益,请联系客服反馈,我们会尽快为您处理(人工客服工作时间:9:00-18:30)。
粉体材料粒度分布及颗粒形貌控制的实例分析
制备粒度均一分散的超细粉是粉末结构形貌控制的主要目标之一。
调节体系过饱和度、添加晶种控制晶核数、促进或阻碍团聚的发生等,是粒度控制的主要策略。
在体系溶解度较大的情况下,Ostwald陈化也可调节颗粒粒径及其单分散性。
在化学沉淀制粉过程中,微观均匀混合是体系粒度控制的最主要内容。
•各个微小区域内过饱和度微小变化将导致晶核数目大量变化,从而使晶核大小不一。
•强制混合是保证微观状态一致、制取粒度均一的超细粉末的有效措施。
•由于超细粉体极大的表面能,粉末颗粒的形成除了经历了成核、生长等过程外,还可能发生聚结与团聚。
•如何有效地控制粉体的团聚也是超细粉末尺寸分布控制研究的一个重要内容。
二、粉体形貌控制
粒子形貌包括形状、表面缺陷、粗糙度等,但主要指形状。
纳米粉体,尤其是超微颗粒往往表现出很多形状,除了与其晶型结构有关外,还取决于其合成方法及相应的操作条件。
如在湿化学法体系中,颗粒的形状对操作条件极其敏感,溶质浓度、反应体系中阴离子的种类、反应体系是否封闭等因素均可能影响颗粒的形状。
•一般认为,液相中的超微颗粒可选择性吸附溶液中的简单离子、络离子及有机化合物分子,且不同晶面上被吸附物的种类和数量均有所不同。
•而溶质浓度、阴离子种类、温度、pH值等操作条件的细微变化均可能影响晶面的吸附情况,这些吸附通过改变晶面的比表面能或生长速度常数而促进或抑制晶面的生长,进而影响超微颗粒的形状。
•因此,不同操作条件下形成的超微粒子往往呈现多种形态。
此外,添加剂也可改变粉体的形貌。
比如,在超细粉体α-Fe2O3合成中,研究者发现陈化时添加柠檬酸、酒石酸,α-Fe2O3粉末呈短柱状、片状或层状,而添加有机磷酸可以得到轴比很大的适宜作磁记录介质的针状粉末。
通过添加柠檬酸还可以制备得到阻燃材料用的等轴细棱形片铝钠石和细小片状Mg(OH)2。
添加异种物质进行粉末形状控制应考虑以下几点:
•母晶的晶格结构、
•剩余的原子价、
•异种物质分子的极性基大小形状以及配位。
液相化学法制粉往往是在高温、强搅拌等条件下进行,由于粉末生长的物理化学条件要求苛刻,影响因素复杂,粉末结构形貌往往难以精确控制。
虽然有关湿法化学制粉中粉末结构形貌控制研究已有不少报道,但主要是通过改变反应物浓度、溶液pH值、反应时间、反应温度和添加物种类及数量来实现。
总体来看,这项工作还处于研究起始阶段,有许多技术和理论问题有待于进一步探讨。
对粉体材料而言,颗粒形貌与粒度,亦是决定其性能的重要因素。
有关粉体结构形貌的控制研究已为其应用展现了诱人的前景,但目前粉末结构形貌控制研究还存在许多问题,还有待行业专家及科研院所深入的研究探索。
粉体圈作者:敬之。