机械零件检验作业指导书模板_图文.
机加工检验作业指导书

机加工检验作业指导书[1]SL/01机加工检验作业指导书一、适用范围规定了工程机械机械加工件的技术要求,适用于各类机械加工件。
二、作业要求1、凡机械加工件必需符合产品图样、工艺规程和作业要求。
2、经加工的零件外表不允许有锈蚀和磕碰、划伤、裂纹等缺陷。
3、除有特别要求外,加工后的零件不允许留有尖棱、尖角和毛刺。
4、滚压精加工的外表,滚压后不得有剥离及脱皮现象。
5、精加工后的外表、摩擦面和定位面等工作外表不允许在其上打印标记。
6、经加工后的零件在搬运、存放时,必需防止受到损伤、腐蚀及变形。
7、成组配对加工的零件,如:齿轮箱上下盖等需有标记。
三、未注尺寸公差参阅附件:技术标准 JB/T 5936-91 四、未注外形和位置公差参阅附件:技术标准 JB/T 5936-91 五、未注公差角度的极限偏差参阅附件: 技术标准 JB/T 5936-91 六、螺纹、键和键槽参阅附件:技术标准 JB/T 5936-91七、中心孔1、图样中未注明、加工中又需要中心孔的零件,在不影响使用和外观的状况下,加工后中心孔可以保存。
2、中心孔需符合 GB 145 的规定。
八、检验规章1、凡经机械加工件,由制造厂质量检验部门按图样、有关技术文件和本要求进展检查和验收。
2、机械加工件的外观按规定要求进展检查。
3、主要机械加工件需每件检查几何外形与尺寸。
九、标志1、入库的机械加工件应有的标志2、标志的位置应不使机械加工件的质量受到损伤。
3、机械加工件入库应附有吊牌。
其中应注明:名称、零件名称、图号; 制造日期。
编制/日期: 审批:下面是赠送的团队治理名言学习,编辑删除感谢1、沟通是治理的浓缩。
2、治理被人们称之为是一门综合艺术--“综合”是由于治理涉及根本原理、自我认知、才智和领导力;“艺术”是由于治理是实践和应用。
3、治理得好的工厂,总是单调乏味,没有仸何激劢人心的大事发生。
4、治理工作中最重要的是:人正确的事,而不是正确的做事。
5、治理就是沟通、沟通再沟通。
检验指导书模板

样品小批批量特管1材料[B]1/N 1/N 1/2月记录2硬度[B]1/N 1/N 1/N 记录3外径[B]N/N 20/N 10/N 记录4N/N 20/N 2/N 记录5N/N 2/N 2/N 记录6N/N 2/N 2/N 记录7内径[B]N/N 20/N 10/N 记录8N/N 2/N 2/N 记录9N/N 20/N 2/N 记录10高度[B]N/N 20/N 10/N 记录11高度[B]N/N 20/N 10/N 记录12N/N 20/N 2/N 记录13N/N 20/N 2/N 记录14N/N 20/N 2/N 记录15倒角N/N 5/N 1/N 记录16退刀槽N/N 5/N 1/N 记录17油槽N/N 5/N 1/N记录18高度N/N 5/N 记录19外圆N/N 5/N 记录20外圆N/N 5/N 记录21角度N/N 5/N 记录21外观N/N 20/N 10/N 记录22产品标识N/N 20/N 1/N 记录23产品包装A/N A/N A/N 记录24产品清洁A/N A/N A/N 记录25厂家报告A/NA/NA/N 记录处数更改文件日期标记处数清洁度试验第一页备注端面粗糙度0.8芯轴+千分表0.001圆柱度仪TALYROUND365↗ 0.015 A 数显高度尺0.001内径千分表0.001零(部)件重要性: A—关键 B—重要 C—一般更改文件号日期2-Φ6游标卡尺0-150mm/0.02游标卡尺0-150mm/0.02游标卡尺0-150mm/0.02签字齐全目测编制/日期: 校对/日期: 审核/日期:圆柱度 0.005圆柱度仪TALYROUND365粗糙度0.4数显高度尺0.00131.5±0.0427±0.04圆柱度 0.01Ф30(0,+0.021)对比卡0.8粗糙度仪FORM TALYSURF 无毛刺、磕碰目测供应商代码+5T18H 17.2高度尺0.02Φ42.5共一页质量特性控制方法检验频次重要性生效日期质量特性: 关键 重要 一般图纸版本光谱分析仪Q4UVTasman检验手段58-63HRC产品图号外径千分尺25-50mm/0.001对比卡0.8洛氏硬度计HRD-150Ф32 X 30°游标卡尺0-150mm/0.02∥ 0.02 C 粗糙度 0.8数显高度尺0.001↗ 0.01 A 芯轴+千分表0.001xx检验指导卡产品名称签字检验简图(一)序号GCr15 GB/T18254Ф37(-0.025,+0.009)项目技术尺寸要求标记技术要求实物视图(二)Φ54R1对比规0.5xR1无破损、淋湿、标识清楚目测15°角度尺1′目测123745689101112131415161718192023456789101111314115161718222321222319221注:1、泡泡图可单独设为1页注:1、泡泡图可单独设为1页2、关于小批、批量检测频次,供应商须根据自己的实际情况进行设定3、检验手段中,量检具、设备的型号、规格必须详细。
机加工件来料检验作业指导书

审查
制定
a.交验制品表面不允许存在扭曲、弯曲变形、裂纹、缺损、伤痕、开裂等缺陷;
b.焊接件焊口应焊接牢固可靠,表面光滑平整,不允许存在气孔,砂眼,漏焊,夹杂等焊接缺陷;表面去掉焊杂涂刷防腐底漆;
c.切割件表面不允许存在、开裂、及凹凸缺Байду номын сангаас、伤痕毛剌等缺陷;
d.切削件表面应符合图纸精度标准要求,棱角倒钝;
e.糟弯件、压弯件、冷作件表面应光滑平整,不允许有凹凸不平弯曲、扭曲、毛刺等制造缺陷;
分发编号:
零部件名称
机加工件
DAB分类
D
外购外协件检验指导书
文件编号
版次
3.0
图号
通用
规格、型号
通用
发行日期
页次
1/1
序号
检验项目
技术要求
验收器具
抽检比例
备注
名称
规格
1
2
3
4
标志:
外观:
几何尺寸:
机械性能:
1)送检单与零件号名称、图号、规格、型号、数量是否一致,是否有检验合格标志;
1)表面应平整光滑,不允许存在以下缺陷:
f.组合配件、组合总成件必需满足图纸装配设计要求,转动灵活,装配牢固可靠;表面去污浊毛刺;并进行防腐处理;
1)尺寸及公差应符合图纸要求;
1)配件物理机械性能及化学元素应附合图纸材料要求;
2)配套件材质检验报告由配套厂家提供;(安全项)
目测
目测
万能量具
材质报告
厂方报告
材料批次
No.
修订日期
修订内容
修订单
机械加工产品检验作业指导书

一汽解放青岛汽车厂质量保证部技术文件编号:IPQC-JYZD-7-2009 批准:宋宗强机械加工产品检验作业指导书2008年12月31日发布2009年1月1日实施一汽解放青岛汽车厂质量保证部发布前言本检验作业指导书依据有关汽车标准及一汽解放青岛汽车厂技术文件制定。
是一汽解放青岛汽车厂质量保证部技术文件之一。
本检验作业指导书与国家标准、企业标准及相关技术文件相一致。
从实施之日起,原《IPQC-JYZD-7-2008机械加工产品验作业指导书》同时废止。
各相关部门检验机械加工产品质量时,都需要按本检验作业指导书的规定执行。
本标准由一汽解放青岛汽车厂质量保证部起草。
本检验作业指导书起草人:林桂升本检验作业指导书审核人:石建通1 主要内容与适用范围本检验作业指导书规定了机械加工产品的检验方式及质量记录。
本检验作业指导书主要适用于机加工车间。
2 引用标准下列标准包括的条文,通过在本检验作业指导书中的引用而构成本标准的条文。
在本检验作业指导书发布时,所示版本均为有效。
所有标准都会被修订,使用本标准的各方应探讨使用下列标准最新版本的可能性。
CA/CBG-1-82 切削零件未注公差尺寸的公差CA/CBG-9-91 未注公差角度的极限偏差3 检验及质量记录规定3.1所有机加工产品必须按产品标准、技术要求等进行自检控制。
3.2检验零件时,按控制计划合理选用量检具,并正确操作。
3.3未注公差尺寸的极限偏差3.3.2 两孔的中心距和孔与零件边缘距离的未注公差尺寸的公差按下表执行。
(以孔径为基本尺寸查选。
当两孔径不相等时,其轴心距的公差按两孔直径的算术平均值确定。
)如3.3.4 L查选。
3.3.5 螺纹长度尺寸L未注公差的极限偏差:对非全螺纹,长度L偏差为0~+1.5P;对全螺纹,长度L偏差为-1.5P~0。
(P:螺纹的螺距)3.4 正常路线件3.4.1 对有明确公差要求的尺寸,检查员按不低于1/30的频次抽检并形成质量记录。
《机械加工过程检验作业指导书》

《机械加工过程检验作业指导书》BR/QGS12.05文件版本:V1.0受控性质:发放编号:持有人:机械加工过程检验作业指导书2010-08-26 发布 2010-08-27实施常州博瑞电力自动化设备有限公司发布机械加工过程检验作业指导书 BR/QGS12.05目录目的 ..................................................................... .......................................................1 12 范围 ..................................................................... .......................................................1 3 职责 ..................................................................... .......................................................1 4 工作程序、要求及方法 ..................................................................... (1)4.1 检验条件 ..................................................................... .. (1)4.1.1 检验工具 ..................................................................... (1)4.1.2 检验依据 ..................................................................... (1)4.2 检验项目及要求...................................................................... .. (1)4.3 记录表单 ..................................................................... .. (2)4.4 判定结论 ..................................................................... .. (3)4.5 检验结果统计及异常情况处理 ..................................................................... (3)4.6 处理方式 ..................................................................... .............................................................. 3 5 相关文件 ..................................................................... .. (3)5.1 BR/QPS13《不合格品控制程序》 ................................................................... . (3)5.2 BR/QGC05.24《工件去毛刺作业指导书》 ................................................................... ........... 3 6 记录 ..................................................................... . (3)6.1 BR/QGS12.05-01《机械加工过程员工自检记录表》 (3)6.2 BR/QGS12.05-02《过程巡检记录表(机械车间)》 (3)6.3 BR/QGS12.05-03《过程检验记录表(机械车间)》 (3)6.4 BR/QGS12.05-04《机械加工过程检验不合格记录表》 (3)机械加工过程检验作业指导书 BR/QGS12.05机械加工过程检验作业指导书 1 目的通过规范机械加工过程检验,使其满足产品要求。
检验作业指导书

2、 若在尺寸精度、形位精度上存在致命或重要缺陷若其超差值在要求精度值1/3以内时
允许让步接受若超过精度的1/3则报废。
3、 若在外观质量上存在一般性缺陷允许让步接受若存在致命或重要缺陷则报废。
6附表4.JL368Q、JL462Q、JL465Q、JL466Q机油泵外协外购件入厂验收标准
8. 大平面平面度 √6.泵体表面轻微颜色不均匀 √
9. 安装螺孔位置度 √7.泵体表面严重颜色不均匀 √
10. 螺纹孔精度 √
11. 螺纹孔位置度 √
12. 螺纹孔底孔直径 √
13. 壳体密封性 √
注若存在上述缺陷按照下列要求处理
1、 若在重要性能、壳体密封性、水封密封性、轴承转动灵活性上存在致命或重要缺陷则
总成产品缺陷分级指导书见附表3。
2.2、外协外购件入厂验收标准
2.2.1、外检人员依据“外协外购件入厂验收标准”对当批产品
按照GB2828-87调整型抽样方案检验标准即AQL检验制进行验
收并如实填写Q/HT R1201-02《外协外购件入厂检验登记台帐》
及HT/QPR2701《报验单》。
JL474Q水泵等系列产品。 2、 作业标准 2.1、 产品缺陷分级指导书
2.1.1、产品缺陷分为三级
A 致命缺陷B重要性缺陷C一般性缺陷
2.1.2、JL465系列机油泵总成产品缺陷分级指导书见附表1JL474Q
系列机油泵总成产品缺陷分级指导书见附表2JL474Q系列水泵
13. 骨架面螺孔的位置度 √
14. 连接螺纹孔精度 √
15 基座面螺孔的位置度 √
注若存在上述缺陷按照下列要求处理
4、 若在性能参数、内腔清洁度、转动灵活性上存在致命或重要缺陷则必须进行返修处理。
检验作业指导书范本

检验作业指导书范本一、检验目的本次检验的目的是为了确保作业的质量和准确性,以便达到预期的效果。
通过检验,能够及时发现和纠正问题,保证作业的正常进行。
二、检验范围本次检验的范围包括但不限于以下内容:1. 作业的设计和布置;2. 作业所采用的工具、材料和设备;3. 作业的操作流程和方法;4. 作业的标准和要求。
三、检验准备1. 检验人员的资格和培训要求;检验人员应具备相关的专业知识和经验,并接受过相应的培训,对于常见的问题能够做出准确的判断和决策。
2. 检验所需的工具和设备;根据具体的检验内容,选择适当的工具和设备进行检验,确保检验的准确性和可行性。
3. 检验标准和要求;参照相关的标准和要求,明确检验的指标和评判标准,以确保检验的公正性和客观性。
四、检验步骤1. 检验前准备工作;检验前要对检验所需的工具和设备进行检查和校准,确保其正常运行和准确度。
2. 开展实际检验工作;按照作业指导书的要求,逐项进行检验,检查作业的设计、工具设备的使用和操作流程的合理性和准确性。
3. 记录检验结果和问题;在检验过程中,对发现的问题和不合格项进行记录,并标明具体的情况和原因,以便进行后续的处理和改进。
4. 提出评价和建议;根据检验结果和问题记录,对作业的质量和准确性进行评价,提出相应的改进和完善的建议,以期提高作业的效率和质量。
五、检验结果的处理1. 不合格项的处理;对于检验中发现的不合格项,应制定相应的纠正措施,并责令相关责任人进行整改,直至合格为止。
2. 合格项的认定;对于符合检验标准和要求的项,应认定为合格,并进行相应的记录和归档。
六、检验报告1. 检验结果的总结和分析;将检验过程中的整体结果进行总结和分析,包括合格和不合格项目的比例、问题的类型和出现的频率等内容。
2. 问题的处理情况;对于检验中发现的问题进行详细的处理情况说明,包括整改的措施、责任人及整改进度等信息。
3. 改进和完善的建议;结合检验结果和问题分析,提出具体的改进和完善的建议,以期提高作业的质量和效率。
机械作业指导书格式
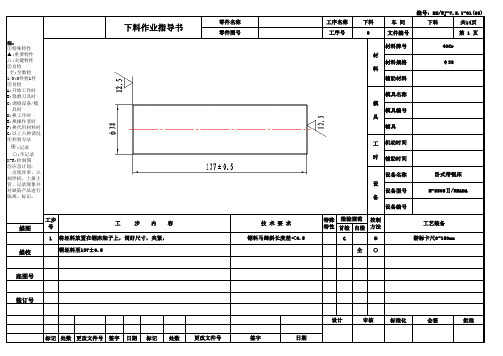
材料牌号材料规格辅助材料模具名称模具编号辅具机动时间辅助时间设备名称设备型号设备编号描图首检自检1G⊕描校全○底图号装订号标准化会签批准设计审核将坯料放置在锯床架子上,调好尺寸,夹紧,锯料马蹄斜长度差<0.5游标卡尺0-150mm锯坯料至137±0.5设备卧式带锯床H-2505Ⅱ/RMADA 检验规范控制方法工艺装备模具工步号工 步 内 容技 术 要 求特殊特性材料工时注:①特殊特性▲:重要特性△:关键特性②自检全:全数检1/N:N件检1件③首检A:开始工作时B:修磨刀具时C:调修设备/模 具时D:换工序时E:换操作者时F:换代用材料时G:以上六种请况④控制方法 ⊕:记录 ○:不记录X-R:控制图⑤应急计划: 出现异常,立刻停机、上报主管、记录现象并对缺陷产品进行隔离、标识。
40Cr φ38材料重量材料牌号技术要求检验设备辅助工具机动时间辅助时间设备名称设备型号设备编号描图介质温度(℃)时间(秒)首检自检1装筐67070空气描校底图号装订号标准化会签批准设计工艺装备装炉方式装炉温度(℃)加热温度(℃)加热时间(分)保温时间(分)注:①特殊特性▲:重要特性△:关键特性②自检全:全数检1/N:N件检1件③首检A:开始工作时B:修磨刀具时C:调修设备/工 装时D:换工序时E:换操作者时F:换代用材料时G:以上六种请况④控制方法 ⊕:记录 ○:不记录X-R:控制图⑤应急计划: 出现异常,立刻停机、上报主管、记录现象并对缺陷产品进行隔离、标识。
材料检验方法工时设备工步号工步内容操 作 要 求将毛坯轴间隙装筐铁筐单层入炉,按操作规程天车审核退火吊钩40Cr井式炉RJJ-60-97控制方法检验规范特殊特性冷却毛坯种类毛坯尺寸材料牌号夹具名称夹具型号工装名称工装编号切削液机动时间辅助时间设备名称设备型号设备编号主轴转速切削速度进给量切削深度描图r/min m/minmm/r mm首检自检1360G⊕描校1/10○底图号装订号设计游标卡尺0-150mm翻转工件,平端面至135+0.5钻中心孔B4/10工艺装备三爪夹紧外径,平一面见平YT车刀18普通车床SK360-2控制方法工时工装工步号工 步 内 容技术要求进给次数特殊特性检验规范三爪卡盘材料设备审核注:①特殊特性▲:重要特性△:关键特性②自检全:全数检1/N:N件检1件③首检A:开始工作时B:修磨刀具时C:调修设备/工 装时D:换工序时E:换操作者时F:换代用材料时G:以上六种请况④控制方法 ⊕:记录 ○:不记录X-R:控制图⑤应急计划: 出现异常,立刻停机、上报主管、记录现象并对缺陷产品进行隔离、标识。
检验作业指导书模板
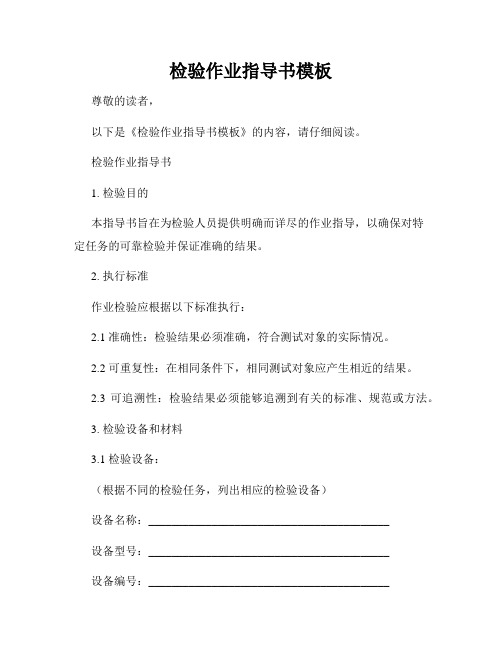
检验作业指导书模板尊敬的读者,以下是《检验作业指导书模板》的内容,请仔细阅读。
检验作业指导书1. 检验目的本指导书旨在为检验人员提供明确而详尽的作业指导,以确保对特定任务的可靠检验并保证准确的结果。
2. 执行标准作业检验应根据以下标准执行:2.1 准确性:检验结果必须准确,符合测试对象的实际情况。
2.2 可重复性:在相同条件下,相同测试对象应产生相近的结果。
2.3 可追溯性:检验结果必须能够追溯到有关的标准、规范或方法。
3. 检验设备和材料3.1 检验设备:(根据不同的检验任务,列出相应的检验设备)设备名称:__________________________________________设备型号:__________________________________________设备编号:__________________________________________(根据不同的检验任务,列出相应的检验材料)材料名称:__________________________________________材料规格:__________________________________________材料批号:__________________________________________ 4. 检验方法和步骤4.1 检验方法:(根据不同的检验任务,列出相应的检验方法)方法名称:__________________________________________方法步骤:__________________________________________方法依据:__________________________________________ 4.2 检验步骤:(根据不同的检验任务,列出相应的检验步骤)步骤一:____________________________________________步骤二:____________________________________________步骤三:____________________________________________ 5. 检验记录和报告(根据不同的检验任务,列出相应的检验记录内容)记录项目:__________________________________________记录内容:__________________________________________记录方式:__________________________________________ 5.2 检验报告:(根据不同的检验任务,列出相应的检验报告内容)报告项目:__________________________________________报告内容:__________________________________________报告要求:__________________________________________ 6. 质量控制6.1 仪器校准:(根据不同的检验设备,列出相应的校准要求)设备名称:__________________________________________校准标准:__________________________________________校准周期:__________________________________________ 6.2 样品保存:(根据不同的检验样品,列出相应的保存要求)样品名称:__________________________________________保存条件:__________________________________________保存期限:__________________________________________ 7. 安全和环境要求7.1 安全要求:(根据不同的检验任务,列出相应的安全要求)要求一:____________________________________________要求二:____________________________________________要求三:____________________________________________ 7.2 环境要求:(根据不同的检验任务,列出相应的环境要求)要求一:____________________________________________要求二:____________________________________________要求三:____________________________________________ 8. 审核和批准指导书编制:编制人:____________________________________________日期:______________________________________________签名:______________________________________________指导书审核:审核人:____________________________________________日期:______________________________________________签名:______________________________________________指导书批准:批准人:____________________________________________日期:______________________________________________签名:______________________________________________感谢您对本指导书模板的关注与使用。
12 检验作业指导书(机筒 螺杆)

序号
频次缺陷分类1
1份/批
CR
21份/批CR
3全数MI 4全数CR 5
全数CR 全数MA 全数MA 全数MA 71次/件
MA
QW-SJSH-IQC-ZY12
版 本A16检查规格测量器具目测项 目外观特性
日 期新制
审 核
外购(机筒、螺杆)
检 验 作 业 指 导 书
文件编号2015-1-23
内 容页 次
批 准
1 / 1
制 作
B、C、H
资料规格型号尺寸
规格型号符合采购合同(或采购确认单)、图纸及外购件汇总表的要求,材质、表面处理、出厂检验等资料齐全。
检 查 要 点
外观特性机筒相对位置螺杆旋向(1)游标卡尺读数时,视线应与尺面垂直,对同一尺
寸应多测几次,取其平均值来消除偶然误差。
(2)千分尺测量注意要在测微螺杆快靠近被测物体时
应停止使用旋钮,而改用微调旋钮,避免产生过
钢卷尺
法兰连接孔方向、位置;进料口方向位置。
检验螺筒螺杆热处理硬度符合设计要求。
机体表面金属面无锈蚀,划痕、等缺陷;机筒焊缝符合要求。
目测螺旋方向确认检查
目测标准依据
本作业规范参照本公司图纸、工艺以及相关资料。
不合格品按《不合格品处理程序》执行。
A、D、E、G 游标卡尺硬度计
目测表面处理千分尺硬度
包装
完整、无伤
目测
包装防护(有无碰拉伤)完整。
外观表面无缺陷直径 F
按以上图示要求选择测量点。
零部件检测作业指导书
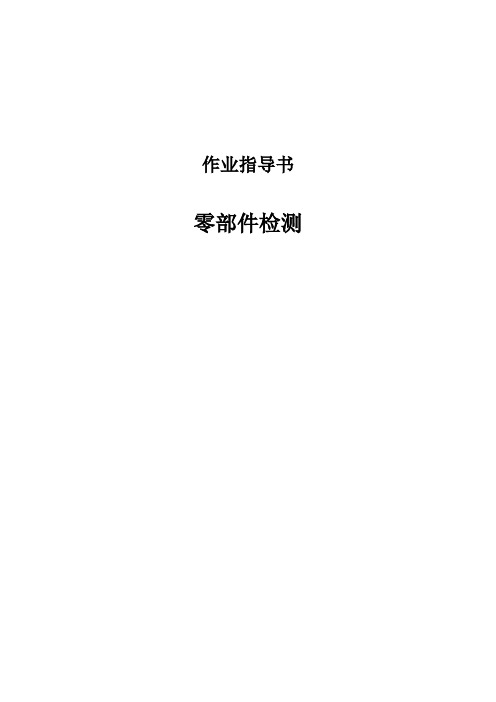
4.1.2.1 用扫描枪扫描主阀条形码,检查核对读取的编号与实物一致,确保
条形码信息正确录入 HMIS 检修系统中。
4.1.2.2 主阀配件检修限度需符合表 1 规定。
表 1 零件检修限度表
序号
名称
检测项目
原型 (mm)
限度 (mm)
检测器具
滑阀厚度不小于
17±0.15
16
1
滑阀
游标卡尺
缓解槽深度不小于
图5
4.3.2.2 用通针疏通触杆Φ1.5mm 孔及Φ4mm 孔,疏通时,采用小于各孔径的 通针疏通,通针硬度小于零部件硬度,如图 6。
图6
4.3.3 KZW 系列调整阀配件检查 4.3.3.1 各零部件状态良好,不得有损伤,裂纹。 4.3.3.2 各零部件连接部位或铆接部位状态良好,不松动。 4.3.4 KZW 系列调整阀配件测量 4.3.4.1 测量显示活塞Φ8 mm 柱面,柱面直径小于Φ17.6mm 时更换,划伤时 可用细砂纸或油石打磨修理,各柱塞及铜套表面须光滑,如图 7。
0.5mm 刀口尺
1mm
游标卡尺或 样板
4.3.7 T-1 系列调整阀配件检查
4.3.7.1 各零部件状态良好,不得有损伤,裂纹。各零件表面不得有目视可 见的污垢、沙尘、水分、纤维物和其它污物。 4.3.7.2 各零部件连接部位或铆接部位状态良好,不松动。
各零部件检测不合格者严禁使用。 4.4 检查阀体双头螺柱 对主阀、半自动缓解阀、紧急阀要双头螺栓逐一检查,双头螺柱松动时,须 分解检查,重新组装时,装入阀体端螺纹须均匀涂抹螺纹锁固剂,并严格执 行先紧固双头螺柱再组装压紧阀盖螺母的组装顺序,不得在双头螺柱上先装 上阀盖螺母再向阀体上组装双头螺柱。 4.5 检修记录填写 4.5.1 将 120/120-1 阀检测结果录入 HMIS 系统,在《型货车空气控制阀主阀 检修记录》(ZG-03),《120/120-1 型货车空气控制阀紧急阀检修记录》(ZG05)的 “零部件检查”填写相应的检测数据(检测数据精确到小数点后 2 位),并在“检测”栏录入工作者名,检查录入无误。 4.5.2 将 KZW 系列传感配件的检测结果填入《KZW 系列传感阀检修记录》(ZG16)“检测结果”栏,并在“检测”栏加盖工作者名章。 4.5.3 将 KZW 系列调整阀配件检测结果填入《KZW 系列调整阀检修记录》(ZG18)“检测结果”栏,并在“检测”栏加盖工作者名章。 4.5.4 将 WG-1A/C 型传感阀配件检测结果填入《WG-1A/C 型传感阀检修记录》 (ZG-20)“检测结果”栏,并在“检测”栏加盖工作者名章。 5. 设备故障处置 工作者在设备点检和操作过程中,要注意观察设备状态,发现异常,立即停 机检查处理,属于自修范围的故障由工作者处理。超出自检自修范围的故
检验标准作业指导书【范本模板】

压力表
1
每年1次
灶前燃气压力(kPa):天燃气2。0KPa,液化气2。8KPa
一级
压力表
1
每年1次
热效率符合标准要求。
一级
测试
1
每年1次
表面温升
易接触部位(旋钮等)-金属及其相同材料不大于室温加35K
二级
温度计
1
每年1次
易接触部位(旋钮等)-陶瓷及其相同材料不大于室温加45K
二级
温度计
1
每年1次
常明火点火燃烧器无离焰、回火、熄火,主火燃烧器点燃或熄灭时,不应产生熄火现象。常明火点火燃烧器在2—3燃气条件下,保持点燃状态,主火燃烧器应被点燃,且不发生爆燃。
一级
目测
1
每年1次
火焰传遍所有火孔时间≤4S,无爆燃。
一级
目测
1
100%
火焰状态:清晰、均匀、无黄焰、无黑烟。
一级
目测
1
100%
燃烧噪音符合标准要求
一级
声级计
1
每年1次
熄火噪音符合标准要求
二级
声级计
1
每年1次
热工性能
烟气中氧(O2)含量:≤14%一级烟分析仪1每年1次
正常工况,a=1时,烟气中CO含量:≤0。1%
一级
烟气分析仪
1
每年1次
特殊工况,a=1时,烟气中CO含量:≤0。2%
一级
烟气分析仪
1
每年1次
表前燃气压力(kPa):天燃气2.1KPa,液化气2。9KPa
二级
目测
5
100%
性能
燃气系统气密性
15kPa压力下,漏气量应小于0.14L/h.
检验作业指导书

检验作业指导书1.目的规范检验工作,提高产品质量,确保产品满足组织的品质要求。
2.范围适用于我司自制或委外协作加工的所有加工件。
3.职责品质部是本公司的质量管理部门,负责产品检验工作并记录验收结果。
4.内容检验流程-检验方法-判定标准-检验报告-不良品处理-纠正预防措施4.1检验流程供应商按照采购订单送货到公司将送货单给仓库,仓库按照采购订单及收货单上的名称、编号、数量对来料进行验收;如发现有缺件、编号与名称不符等情况验可退货给供应商,验收合格后,仓库开立《来料检验通知单》交品质部检验,品质部按照图纸、技术规范、及抽样水准对来料进行抽样检验。
接到仓库开立的来料检验通知单后,检验员需在半小时内进行检验工作,整理好该批次的相关图纸及检验工具,到现场进行验收工作,检验合格的部件粘贴“绿色”合格标签;检验不合格粘贴“红色”不良标签,并填写《品质异常处理单》召集相关部门进行原因分析和改善;将检验结果记录每日检验日报表中;并跟进不合格品的处理及改善效果,将检验合格的产品交由仓库入库。
相关表单文件及抽样水准《进料品质控制流程》《来料检验通知单》《机架过程品质控制流程》《品质异常处理单》《来料检验日报表》《问题点记录表》4.2 检验方法原材料核对:核对产品的名称、材质、型号规格、图号、材质证明、厂家的出厂检验记录。
成品外观检验:表面不允许有砂孔、毛刺、裂纹、塑性变形,不允许有明显的划痕、凹凸、折痕、污渍、色差等,必须符合工艺或技术文件标准,零部件的编号规则及位置与相关技术文件或图纸规定要一致。
尺寸、角度、形位误差的检验:根据标准要求选择合适的检验器具或配合其他辅助检测工具进行检验,并详细真实的记录检验结果。
按照图纸标注的长宽、孔径、距离、角度、槽、标注公差、螺纹长宽及纹牙、表面处理,逐一进行检验,重要部件做好检验数据记录,必要时可进行简单的装配查看配合是否异常,必须符合图纸技术要求。
机架件注意其图纸要求的材质及表面处理要求,严格按照图纸尺寸公差验收,加工成型后不得有沟痕、碰伤等损坏表面,降低强度及寿命的缺陷,去边角及毛刺。
机加工作业指导书模板

机加工作业指导书模板一、目的本作业指导书旨在规范机加工作业流程,确保产品质量和生产效率。
通过明确操作步骤、注意事项和质量标准,提高员工技能水平,降低生产成本。
二、适用范围本作业指导书适用于所有从事机加工作的员工,包括但不限于车工、铣工、钳工等。
三、作业准备1. 确认设备完好,检查工具是否齐全、完好。
2. 确认图纸、工艺文件齐全,理解加工要求。
3. 穿戴好劳动防护用品,如眼镜、手套等。
四、操作步骤1. 根据图纸和工艺文件,选择合适的刀具和切削参数。
2. 调整设备参数,如转速、进给量等,确保加工精度。
3. 对工件进行粗加工,去除多余材料。
4. 进行精加工,保证尺寸精度和表面粗糙度。
5. 检查工件质量,对不合格品进行返工或报废。
五、注意事项1. 严格遵守设备操作规程,避免发生安全事故。
2. 保持工作场所整洁,避免因杂物影响加工精度。
3. 定期检查刀具磨损情况,及时更换磨损严重的刀具。
4. 在加工过程中,保持注意力集中,避免出现误差。
5. 完成每道工序后,及时清理设备和工作场所。
六、质量标准1. 尺寸精度符合图纸要求。
2. 表面粗糙度符合工艺文件要求。
3. 工件无裂纹、气孔等缺陷。
4. 工件稳定可靠,无松动现象。
5. 保证工件加工精度和外观质量。
七、记录与报告1. 对每道工序的加工情况进行记录,包括加工时间、刀具使用情况等。
2. 对不合格品进行记录,分析原因并提出改进措施。
3. 定期向上级汇报工作进展和质量情况。
4. 对重要工序进行拍照或录像,以备后续分析和改进。
八、培训与考核1. 对新员工进行岗前培训,包括设备操作、安全知识等。
2. 定期组织技能培训和交流活动,提高员工技能水平。
3. 对员工进行定期考核,包括操作技能、产品质量等方面。
4. 根据考核结果对员工进行奖惩和调整工作岗位。
通用机加件检验作业指导书

6.检验步骤……………………………………………………………2
7.过程检验……………………………………………………………2
8.成品检验……………………………………………………………3
9. 相关文件及记录……………………………………………………7
8.
外观缺
陷类型
缺陷所处
表面类型
允许范围
A级表面
B级表面
C级表面
基材花斑
金属表面
不允许
不允许
S总≤被测面积的5%
浅划痕
所有表面
不允许
L≤50×0.4,P≤2
P≤5
深划痕
所有表面
不允许
不允许
不允许
凹 坑
非拉丝和
喷砂面
不允许
直径≤0.5,P≤2
不限制
凹凸痕
所有表面
不允许
不允许
直径≤2.0,P≤5抛光区Fra bibliotek金属表面
不允许
不允许
S总≤被测面积的5%
烧 伤
拉丝面
不允许
不允许
不限制
水 印
电镀、氧化
不允许
S≤3.0,P≤2
不限制
露 白
镀彩锌
不允许
不允许
S≤4.0,P≤3
修 补
喷塑、电泳漆
不允许
S≤3.0,P≤1
S总≤被测面积的5%
颗 粒
所有表面
不允许
直径≤1.0,P≤2
直径≤3.0,P≤5
挂具印
所有表面
不允许
不允许
不限制
d、凹坑:由于基体材料缺陷,或在加工过程中操作不当等原因而在材料表面留下的小坑状痕迹;