氨渗漏试验(C法)
氨渗漏法在氯乙烯转化器致密性检验中的应用

一
、
在压力为 04 MP , . 4 a气温 为 2 ℃( 2 试验时 当地平均气温 ) , 时 需向转化器 内充氨量( 本例 00 2 。 . m ) 7
氯乙烯转化器是氯碱化工企业生产过程 中的关键设备 。由
上下封头 、 上下管板、 换热管 、 壳体等构成 。 其主体部分 由 87根 2 2 号钢  ̄ 7 x . m无缝钢管与材料为 1Mn 0 5 mm 35 m 6 Ⅱ的上下管板
四 、 验 程序 试
定温度及催化剂 的作用下 , 转化为氯 乙烯 ( C 。该反应过 V M)
程 中, 1 HC 气体是过量的 , 为了避免干燥 的 H 1 C 气体遇水生成盐 酸腐蚀设 备造成设备损坏甚至报废 ,则必须保证混合气及反应 环境干燥 , 这就对换热管与上下管板连接的焊缝质量提 出了严
存放 。
3配制清洗剂并清洗转化器上下管板及焊缝 .
由于氯乙烯转化器上下管板与换热管及热偶管在焊接过程 中, 会受到碱性物质 的污染 , 如不将这些碱性物 质清洗掉 , 试验 时这些碱性物质遇到酚酞试剂也会使酚酞试剂变红 ,影响试验
结果 。因此在试 验前 ,必须用清洗剂清洗转化器上下管板及焊
氯 乙烯转化器壳程容积计算( ) 略 。计算可得转化器壳程净
容积 。 单 台转化器充氨量 的计算 ( 。按 1 略) %体积计算单 台转化
器 充氨 量 。
困 设 叠 与 僖 27 1 置 理 维 0 №2 0
维普资讯
一
1 o 氨气在标准状况下的体积 (.24 ml 0 2m ) 0
将上 面括号 内的数据代入 ( ) 1式计算 , 可得单 台转化器需充
常用检验焊缝的几种方法

常用检验焊缝的几种方法焊接过程中检验包括检验在焊接过程中焊接工艺参数是否正确,焊接设备运行是否正常,焊接夹具夹紧是否牢固,在操作过程中可能出现的焊接缺陷等。
焊接过程中检验主要在整个操作过程中完成。
成品的焊接质量检验检验方法很多,应根据产品的使用要求和图样的技术条件选用。
1.非破坏性检验非破坏性检验是指在不损坏被检验材料或成品的性能、完整性的条件下进行检测缺陷的方法,包括外观检验、致密性检验和无损探伤检验。
(1)外观检验焊接接头的外观检验是以肉眼直接观察为主,一般可借助于焊缝万能量规,必要时利用5-10倍放大镜来检查。
外观检测主要是为了发现焊接接头的表面缺陷,如焊缝的表面气孔、咬边、焊瘤、烧穿及焊接表面裂纹、焊缝尺寸偏差等。
检验前,须将焊缝附近10-20mm范围内的飞溅物和污物清除干净。
(2)致密性检验:致密性检验是检验焊接管道,盛器,密闭容器上焊缝是否存在不致密的缺陷。
常用的检验方法有:气密性实验;氨气实验;煤油实验;水压试验和气压实验。
(3)无损探伤检验:是非破坏性检验中的一种特殊的检验方式,是利用渗透,磁粉,超声波,射线等检验方法来发现焊缝表面的细微缺陷及存在于焊缝内部的缺陷。
目前,这类检验方法已在重要的焊接结构中被广泛应用。
2.破坏性检验破坏性检验是从焊件或试件上切取试样或以产品的整体破坏做试验,以检查其力学性能等的检验方法。
它包括力学性能试验,化学分析,腐蚀试验,金相试验,焊接性试验等。
在生产中,焊接成品的质量检验很重要占有很重要的地位。
它不仅在于发现焊接缺陷,检验焊接接头的性能,以确保产品的焊接质量和安全使用,严重的缺陷可导致受压容器的爆炸,造成直接经济损失或灾难性事故而且通过各种检验可对缺陷作出客观的判断,才能对焊缝作出可靠的结论,看其是否所规定的技术要求和保证结构使用的安全可靠。
下面介绍几种检验焊缝质量的方法:(1)气密性实验:一般检验管道,盛器,密闭容器上焊接是否存在不致密的缺陷,以便及时发现,进行排除并修复。
氨渗漏方法
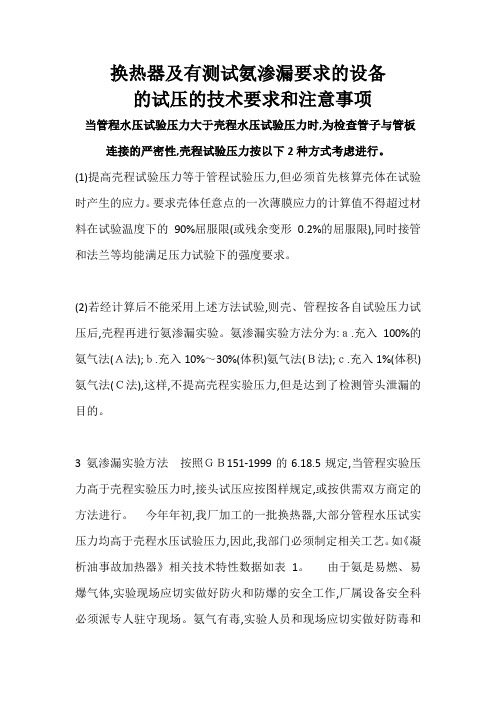
换热器及有测试氨渗漏要求的设备的试压的技术要求和注意事项当管程水压试验压力大于壳程水压试验压力时,为检查管子与管板连接的严密性,壳程试验压力按以下2种方式考虑进行。
(1)提高壳程试验压力等于管程试验压力,但必须首先核算壳体在试验时产生的应力。
要求壳体任意点的一次薄膜应力的计算值不得超过材料在试验温度下的90%屈服限(或残余变形0.2%的屈服限),同时接管和法兰等均能满足压力试验下的强度要求。
(2)若经计算后不能采用上述方法试验,则壳、管程按各自试验压力试压后,壳程再进行氨渗漏实验。
氨渗漏实验方法分为:a.充入100%的氨气法(A法);b.充入10%~30%(体积)氨气法(B法);c.充入1%(体积)氨气法(C法),这样,不提高壳程实验压力,但是达到了检测管头泄漏的目的。
3 氨渗漏实验方法按照GB151-1999的6.18.5规定,当管程实验压力高于壳程实验压力时,接头试压应按图样规定,或按供需双方商定的方法进行。
今年年初,我厂加工的一批换热器,大部分管程水压试实压力均高于壳程水压试验压力,因此,我部门必须制定相关工艺。
如《凝析油事故加热器》相关技术特性数据如表1。
由于氨是易燃、易爆气体,实验现场应切实做好防火和防爆的安全工作,厂属设备安全科必须派专人驻守现场。
氨气有毒,实验人员和现场应切实做好防毒和隔离操作的工作。
为了不影响正常生产,氨渗透试验安排在周末进行。
氨渗漏(B法)实验方法分为抽真空法和置换法。
结合我厂实际情况,建议采用置换法,拟订的置换法具体实施过程如下。
(1)按工艺及规范完成该试压产品的水压试验,水压试验合格后使产品保持充满试压水状态;(2)打开放气排水阀门排水,同时打开(惰性气体)氮气压力钢瓶的阀门充入氮气;(3)当放气排水管在水池水中的管口在水池中有氮气溢出(即有大量气泡)时,关闭放气排水阀门和(惰性气体)氮气压力钢瓶的阀门;(4)打开氨气压力钢瓶阀门,充入氨气,使压力达到0.09MPa(表压);(5)关闭氨气压力钢瓶阀门,停止充氨;(6)打开(惰性气体)氮气压力钢瓶氨门,充入氮气,使压力达到0.60MPa(表压);(7)将检漏显示剂(或试纸)紧密涂敷在管板上,并始终保持湿润状态。
氨渗漏试验工艺守则

氨渗漏试验工艺守则1 适用范围适用于钢制压力容器的氨渗漏试验。
产品设计文件有特殊要求时,应按设计文件执行。
2 引用标准HG20584-1998《钢制化工容器制造技术要求》3 试验方法氨的渗透性较好,且极易溶于水,比较适用于压力容器的渗漏检测。
氨渗漏试验方法分三种,具体采用哪种试验方法应根据设计图样要求。
3.1 充入100%氨气法(A法)此法常用于检漏容器的充氨空间不大、所充氨气的压力较低、并能将其间抽真空,真空度约为93.7kPa[50毫米汞柱(绝压)]的情况下进行检查的场合。
3.2 充入10%~30%(体积)氨气法(B法)此法常用于检漏容器的充氨空间较大、且不易达到93.7kPa[50毫米汞柱(绝压)]的真空或显得不经济的情况下。
3.3 充入1%(体积)氨气法(C法)此法常用于检漏容器的充氨空间大的情况。
4 试验注意事项4.1 氨是易燃、易爆气体,试验现场应切实做好防火和防爆的安全工作;4.2 氨气有毒,试验人员和现场应切实做好防毒和隔离操作的工作;4.3 压力容器的氨渗漏试验应在液压试验合格后进行。
试验前,压力容器焊缝表面及两侧的油污等杂物应清理干净。
5 试验程序5.1 充入100%氨气法(A法)程序5.1.1 试验设备、工具a 液氨钢瓶和带阀门管路;b 真空压力表;c 水箱;d 真空泵和带阀门的吸入管路及排出管路;e 扳手、钢丝钳等装卸工具;f 酚酞试纸或酚酞试剂(也可用石蕊试剂)。
酚酞液的配方为1%酚酞、50%酒精、50%水。
图1 A法氨检漏试验安装图5.1.2 试验过程5.1.2.1 将一个充氨空间的两个检漏口(A、B)分别设置在相距最远的两端处。
5.1.2.2 按图1 安装和连接密封试验管路。
5.1.2.3 开动真空泵,使充氨空间抽真空至真空度93.7kPa[50毫米汞柱(绝压)]。
5.1.2.4 用检测显示剂、试剂或试纸,涂敷在所有检测焊缝的内侧。
5.1.2.5 充入氨气,使压力达到2~3kPa[200~300水柱(表压)]为止,并保压12小时,检验试纸或试剂是否变色(泄漏),如有泄漏,修补后重新进行液压试验和100%氨渗漏试验。
设备氨渗漏试验方法

设备氨渗漏试验方法1. MDI 装置中设备严禁漏水,大修期间部分重要设备需要氨渗漏试验,氨渗漏试验方法采用中《〉〉B 法,即充入10〜30% (体积)氨气法。
2. 准备工作:按图1所示,准备好如下设备、配件及工具。
换热器图1a. 充有液氨的液氨瓶及连接软管的接头(连接软管的接头必须加工成倒刺形状 的,以免脱落)b. 氨用压力表c. 接0. 7MPa 氮气的软管d. 酚酰试剂 配方:1%酚酰,50%酒精,50%水e. 白绵布,塑料布,水箱(水桶)f. 泄氨(胶管),充氨用管路(最好用氧气管)g. 拆装工具 3. 试验程序: 3.1按图1连接好管路3.2充氮气置换(关闭出口阀,进行充氮到0. 4MPa,然后开出口阀卸压。
循环上 述步骤4-5次),直至出口氧含量<0. 5%,关闭出口阀充氛氛用压力表氛用压力表3.3氮气置换完毕后,按图纸气密性试验要求或根据具体使用情况制定气密压力作气密,检查有无泄漏情况,无泄漏情况保压30min,保压后泄压至0. lMPa o3.4根据表1中所列压力,氨浓度,保压关系,充入氨气。
表13.5充氨完毕,充入氮气达到试验压力,进行保压试验,保压时,要注意环境温度的变化,环境温度变化过大会引起设备内部的压力不稳定,容易出现危险情况。
3.6连接中性水,清洗上下管板及管内杂质、锈迹等,用压缩气体吹干,清理要干净彻底(尤其做过气密的设备,管板及管中的肥皂水一定用水冲刷干净并吹干),否则将影响试验效果。
3.7将白绵布清洗(防止漂白剂漂白过的白绵布含碱性),拧干水份,浸透酚酰试剂。
3.8将浸透酚猷试剂的白绵布紧贴管板之上,将塑料布迅速盖好,始终保持酚酰的湿润状态。
3.9保压开始后,每半小时检查一次,观察白绵布上有无红色斑点出现,并做好记录。
3.10试漏完毕后,如果没有漏点出现,则进行泄氨进程,小心开启排出管路阀门进行泄氨至盛有水的水箱中,直至压力表数值为0。
3.11泄氨完毕后用氮气进行反复置换5遍,清除氨气,合格后拆除试漏管道及仪表,并进行清干净。
任务四 压力容器的强度计算及校核
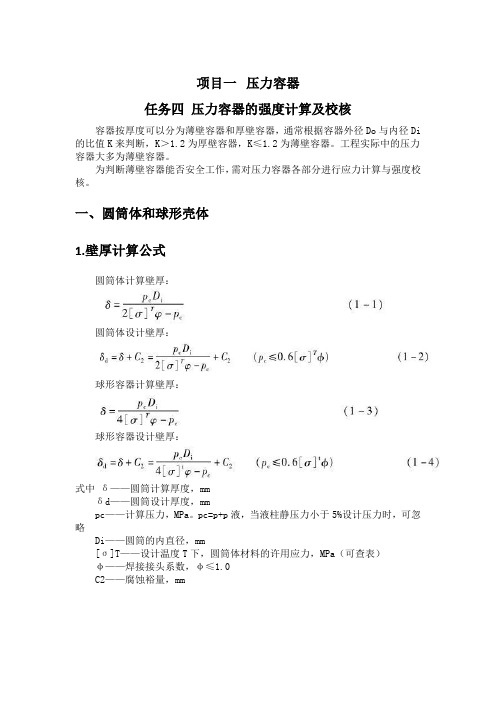
项目一压力容器任务四压力容器的强度计算及校核容器按厚度可以分为薄壁容器和厚壁容器,通常根据容器外径Do与内径Di 的比值K来判断,K>1.2为厚壁容器,K≤1.2为薄壁容器。
工程实际中的压力容器大多为薄壁容器。
为判断薄壁容器能否安全工作,需对压力容器各部分进行应力计算与强度校核。
一、圆筒体和球形壳体1.壁厚计算公式圆筒体计算壁厚:圆筒体设计壁厚:球形容器计算壁厚:球形容器设计壁厚:式中δ——圆筒计算厚度,mmδd——圆筒设计厚度,mmpc——计算压力,MPa。
pc=p+p液,当液柱静压力小于5%设计压力时,可忽略Di——圆筒的内直径,mm[σ]T——设计温度T下,圆筒体材料的许用应力,MPa(可查表)φ——焊接接头系数,φ≤1.0C2——腐蚀裕量,mm2.壁厚校核计算式在工程实际中有不少的情况需要进行校核性计算,如旧容器的重新启用、正在使用的容器改变操作条件等。
这时容器的材料及壁厚都是已知的,可由下式求设计温度下圆筒的最大允许工作压力[pw]。
式中δe——圆筒的有效厚度,mm设计温度下圆筒的计算应力σT:σT值应小于或等于[σ]Tφ。
设计温度下球壳的最大允许工作压力[pw]:设计温度下球壳计算应力σT:σT值应小于或等于[σ]Tφ。
二、封头的强度计算1.封头结构封头是压力容器的重要组成部分,常用的有半球形封头、椭圆形封头、碟形封头、锥形封头和平封头(即平盖),如图1-4所示。
工程上应用较多的是椭圆形封头、半球形封头和碟形封头,最常用的是标准椭圆形封头。
以下只介绍椭圆形封头的计算,其他形式封头的计算可查阅GB150—2011。
图1-4 封头的结构型式2.椭圆形封头计算椭圆形封头由半个椭球面和高为h的直边部分所组成,如图1-5所示。
直边h的大小根据封头直径和厚度不同有25mm、40mm、50mm三种,直边h的取值可查表1-7。
表1-7 椭圆形封头材料、厚度和直边高度的对应关系单位:mm图1-5 椭圆形封头椭圆形封头的长、短轴之比不同,封头的形状也不同,当其长短轴之比等于2时,称为标准椭圆形封头。
氨渗漏方法
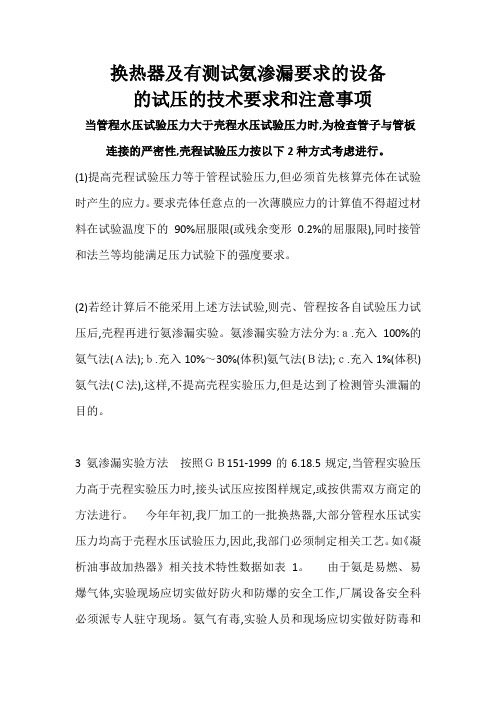
换热器及有测试氨渗漏要求的设备的试压的技术要求和注意事项当管程水压试验压力大于壳程水压试验压力时,为检查管子与管板连接的严密性,壳程试验压力按以下2种方式考虑进行。
(1)提高壳程试验压力等于管程试验压力,但必须首先核算壳体在试验时产生的应力。
要求壳体任意点的一次薄膜应力的计算值不得超过材料在试验温度下的90%屈服限(或残余变形0.2%的屈服限),同时接管和法兰等均能满足压力试验下的强度要求。
(2)若经计算后不能采用上述方法试验,则壳、管程按各自试验压力试压后,壳程再进行氨渗漏实验。
氨渗漏实验方法分为:a.充入100%的氨气法(A法);b.充入10%~30%(体积)氨气法(B法);c.充入1%(体积)氨气法(C法),这样,不提高壳程实验压力,但是达到了检测管头泄漏的目的。
3 氨渗漏实验方法按照GB151-1999的6.18.5规定,当管程实验压力高于壳程实验压力时,接头试压应按图样规定,或按供需双方商定的方法进行。
今年年初,我厂加工的一批换热器,大部分管程水压试实压力均高于壳程水压试验压力,因此,我部门必须制定相关工艺。
如《凝析油事故加热器》相关技术特性数据如表1。
由于氨是易燃、易爆气体,实验现场应切实做好防火和防爆的安全工作,厂属设备安全科必须派专人驻守现场。
氨气有毒,实验人员和现场应切实做好防毒和隔离操作的工作。
为了不影响正常生产,氨渗透试验安排在周末进行。
氨渗漏(B法)实验方法分为抽真空法和置换法。
结合我厂实际情况,建议采用置换法,拟订的置换法具体实施过程如下。
(1)按工艺及规范完成该试压产品的水压试验,水压试验合格后使产品保持充满试压水状态;(2)打开放气排水阀门排水,同时打开(惰性气体)氮气压力钢瓶的阀门充入氮气;(3)当放气排水管在水池水中的管口在水池中有氮气溢出(即有大量气泡)时,关闭放气排水阀门和(惰性气体)氮气压力钢瓶的阀门;(4)打开氨气压力钢瓶阀门,充入氨气,使压力达到0.09MPa(表压);(5)关闭氨气压力钢瓶阀门,停止充氨;(6)打开(惰性气体)氮气压力钢瓶氨门,充入氮气,使压力达到0.60MPa(表压);(7)将检漏显示剂(或试纸)紧密涂敷在管板上,并始终保持湿润状态。
氨试漏技术条件1
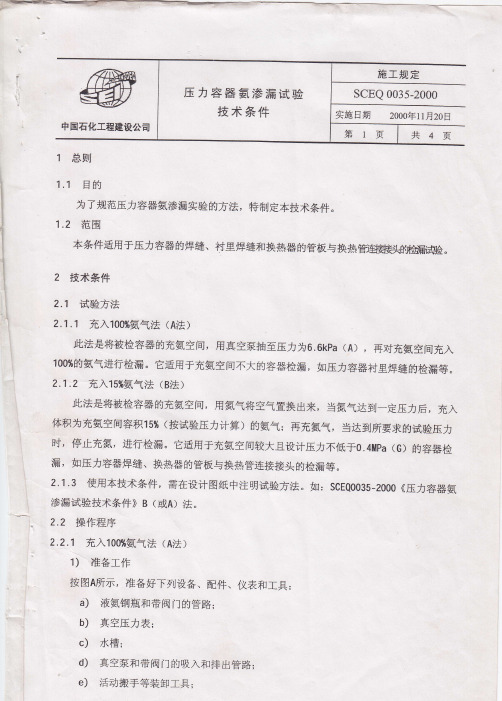
h) 试验全部进行完毕后,拆 除试验用设备,并 将容器内部清
理干净。
工具 按图B所 示 ,准 备好下列设备、配件、仪表和 a, 液氨钢瓶 、氮气钢瓶和带阀门的管路。
:
b, 压力表 。 c, 流量计 。 d, 水槽 。 e, 活动搬手等装卸工具。
,
哂
sEGQ0035-2000
第
4页
共
4页
压力为常压时,打 开氮气阀门3,缓 慢通入体积为充氨空间容积3~5倍 (按 常压计算 )的 氮 气进行吹扫 。然后拆除液氨和氮气钢瓶 ,并 通入压缩空气吹扫 ,直 至将氨气吹除干净为止。
0
试验 。
对检查不合格的部位 ,应 在氨气充分清除干净后进行修复 ,然 后再重复进行上述
2.1 试验方法
2,1,1 充入100%氨 气法 (A法 )
此法是将被检容器的充氨空间,用 真空泵抽至压力为6,6kPa(A),再
10毗 的氨气进行检漏 。它适用于充氨空间不大的容器检漏 ,如
对充氨空间充入
压力容器衬里焊缝的检漏等 。
2.1.2 充入15%氨 气法 (B法 )
此法是将被检容器的充氨空间,用 氮气将空气置换出来 ,当 氮气达到— 定压力后 ,充 入 体积为充氨空间容积习 5%(按 试验压力计算 )的 氨气 ;再 充氮气 ,当 达到所要求的试验压力 时,停 止 充氮 ,进 行检漏。它适用于充氨空间较大且设计庄力不低于0.硼 Pa(G)的 容器检 漏 ,如 压力容器焊缝、换热器的管板与换热管连接接头的检漏等。
;
、
1.2。
绻表面及两 侧 的油污等杂物 应清理于净 。
条 2款 的氨渗透试验 方法时 ,应 在 容器液压试验 后进 行 :焊
氨检漏——精选推荐

第五部分:泄漏检测通用工艺规程1. 主题内容及适用范围1.1 本工艺规程规定了本公司制承压设备金属材料受压部件的溶化焊焊接接头的泄漏检测。
1.2 本规程仅适用于氨泄漏检测技术,其他元素检测如有涉及公司将安排委托检测。
2. 引用标准HG20584-2011《钢制化工容器制造技术要求》附录ANB/T47013.8-2015《承压设备无损检测》第八部分附录G3. 人员要求进行氨泄漏检测的人员需经过公司氨泄漏检测培训的检验人员,未经培训人员不得参与。
4. 检测设备,仪表准备1. 氨用压力表,真空表。
2. 真空泵及吸入和排除管路。
3. 液氨钢瓶和带阀门管路。
4. 惰性气体(氨气)钢瓶及带阀门的管路。
5. 酚酞试纸。
6. 防毒面具及防护工具。
7. 装满水的水箱。
8. 整套装卸工具。
4.1 所用设备,仪表均在检定时间内且完好使用。
4.2 。
表面应当无油脂、油液、油漆以及可能影响检测的污物,清理后。
应当充分干燥。
4.3……泄漏检测应当在耐压试验前进行。
5 检测方法5.1 冲入100%氨气法(A法)5.1.2 将一个充氨空间的两个检漏空(A.B)分别设置在相距最远的两端处,连接好密封试验管路,开动真空泵,使真空度达到P3.7KPA,将酚酞试纸涂敷在检测焊缝的外侧,充入氨气,是压力达到2-3KPA.充氨气时,真空泵直到泵口出口处有氨气排出时停止抽真空。
当真空表指针。
0时,将装置中的U型管前阀门打开。
5.1.3 注意事项:氨瓶必须定置,充氨要小心,不能使液氨渗入到充氨空间里。
5.1.4 保压时间应为12小时。
5.1.5 泄漏检测结束后,关闭氨瓶,开动真空泵,关闭管路,打开排出管路,抽出氨气,排出管路必须插入水箱中。
拆出氨瓶,吸入空气,直到无氨气排出才停止真空泵,然后拆除设备进行清理。
5.2 充入10%-30%(体积)氨气法(B法)5.2.1 用3-5倍充气空间容积的惰性气体(如氮气),置换充气空间里的空气,直至出口氨含量小于或等于0.5%然后关闭排出口管路阀门。
检查氨渗漏试验

烟台万华16万吨/年MDI工程夹套内管氨渗施工技术交底编制: 日期:审核: 日期:审批: 日期:中国化学工程第六建设公司宁波项目经理部二○○四年十二月目录1 编制说明2 编制依据3 试压准备及方法4 安全操作注意事项5 现象判断及补救措施6 技术措施用料7 质量保证体系1.编制说明1.1为确保万华MDI工程夹套管焊接施工质量,根据业主要求及烟台本部生产装置多年的工程施工质量管理经验,我单位特针对现装置内的所有夹套内管进行氨渗试验,编制此方案的基本原则和思路:安全可靠、稳妥可行、技术成熟、经济合理。
1.2工程量清单735分离装置790装置管廊083全厂工艺及供热外管2 编制依据2.1 《工业金属管道工程施工及验收规范》GB50235-972.2 《现场设备、工业管道焊接工程施工及验收规范》GB50236-982.3 《工业安装工程质量检验评定统一标准》GB51252-942.4 《工业管道工程质量检验评定标准》GB50184-942.5 《夹套管施工及验收规范》FJJ211-8626《石油化工剧毒、易燃、可燃介质管道施工验收规范》SH3501-200227夹套管氨渗相关规定(业主文件)28《钢制化工容器制造技术要求》HG20584-1998(附录A 压力容器氨渗漏试验方法)3 试压准备及方法3.1.1 氨渗试验前所有探伤工作都已经结束,管道上的伴热管线接头已按要求开孔焊接完毕。
内管的所有焊口都必须裸露在外,便于氨渗检查3.1.2夹套外管已经按要求进行了预安装并处于活动状态可以自由伸缩3.1.3试压用临时管道和盲板已焊接完毕3.2试验方法采用充入10~30%(体积)氮与氨气混合加压法;3.3 准备工作选择适当的试压场地(见附图),以免试压过程中氨气渗漏影响其他施工人员,按示意图A-1所示,准备好下列设备、管件、管道、仪表和装卸工具等:(1)液氨压力钢瓶和连接软管接头(软管接头必须加工成倒刺形状,以免脱落);(2)氨用压力表(0-1.0Mpa );(3)氮气及泄氨软管(耐压0.7MPa 以上);(4)酚酞试剂(用固体酚酞调配,配方为:1g 酚酞,10ml 水,90ml 酒精);(5)白绵布、塑料布;(6)泄氨用水箱或水桶;(7)充氨用软管(用内径为Φ10的氧气带); (8)DN20,2.5MPa 以上球阀(法兰连接形式);(9)氮气钢瓶和连接软管(软管接头必须加工成倒刺形状,以免脱落);(10)DN10,2.5MPa 不锈钢针形阀;(11)试漏瓶及肥皂水(检验充氨、充氮管路严密性);氨瓶氮气钢瓶压力表压力表放空取样口水槽示意图A-1 氨渗漏试验安装图3.4 试压步骤(1)按示意图A-1安装和连接;(2)用3-5倍充气空间容积的氮气置换充气空间里的空气,直至出口氧含量小于等于0.5%,以避免形成氨气和空气的爆炸混合物(其爆炸极限为15%--18%)。
氨渗漏检查在换热器泄漏检查上的应用
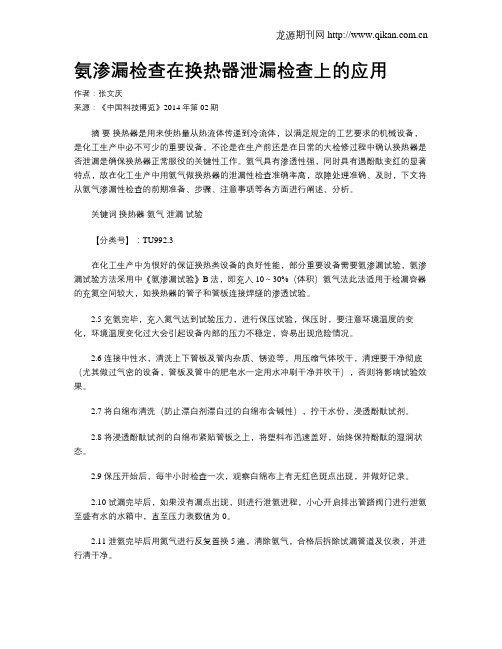
氨渗漏检查在换热器泄漏检查上的应用作者:张文庆来源:《中国科技博览》2014年第02期摘要换热器是用来使热量从热流体传递到冷流体,以满足规定的工艺要求的机械设备,是化工生产中必不可少的重要设备。
不论是在生产前还是在日常的大检修过程中确认换热器是否泄漏是确保换热器正常服役的关键性工作。
氨气具有渗透性强,同时具有遇酚酞变红的显著特点,故在化工生产中用氨气做换热器的泄漏性检查准确率高,故障处理准确、及时,下文将从氨气渗漏性检查的前期准备、步骤、注意事项等各方面进行阐述、分析。
关键词换热器氨气泄漏试验【分类号】:TU992.3在化工生产中为很好的保证换热类设备的良好性能,部分重要设备需要氨渗漏试验,氨渗漏试验方法采用中《氨渗漏试验》B法,即充入10~30%(体积)氨气法此法适用于检漏容器的充氮空间较大,如换热器的管子和管板连接焊缝的渗透试验。
2.5 充氨完毕,充入氮气达到试验压力,进行保压试验,保压时,要注意环境温度的变化,环境温度变化过大会引起设备内部的压力不稳定,容易出现危险情况。
2.6 连接中性水,清洗上下管板及管内杂质、锈迹等,用压缩气体吹干,清理要干净彻底(尤其做过气密的设备,管板及管中的肥皂水一定用水冲刷干净并吹干),否则将影响试验效果。
2.7 将白绵布清洗(防止漂白剂漂白过的白绵布含碱性),拧干水份,浸透酚酞试剂。
2.8 将浸透酚酞试剂的白绵布紧贴管板之上,将塑料布迅速盖好,始终保持酚酞的湿润状态。
2.9 保压开始后,每半小时检查一次,观察白绵布上有无红色斑点出现,并做好记录。
2.10 试漏完毕后,如果没有漏点出现,则进行泄氨进程,小心开启排出管路阀门进行泄氨至盛有水的水箱中,直至压力表数值为0。
2.11 泄氨完毕后用氮气进行反复置换5遍,清除氨气,合格后拆除试漏管道及仪表,并进行清干净。
2.12 试漏完毕后,如果有漏点出现,仔细记录下漏点位置,进行修复,修复完好后,重复3.2~3.11,直至无漏点为止。
管道程序文件

1目的质保手册是企业压力管道安装质保体系的最高层次文件。
为保证其权威性、严肃性、完整性、有效性,特制定本程序。
2适用范围适用于本企业压力管道安装质保手册的管理。
3职责3.1 质管办负责质保手册的编制、发放、更改管理。
3.2 质保工程师确定受控手册的发放范围。
3.3 受控手册的持有者负责手册的使用与保管。
4 工作程序4.1 质保手册的编制4.1.1 质管办依据总经理指令,负责组织编制质保手册。
4.1.2 质管办组织相关部门对质保手册初稿进行讨论、修改,定稿后报质保工程师审核,总经理批准颁布。
4.2质保手册的发放4.2.1 质保手册由质管办统一编号,并按使用对象,标识控制状态:a)受控即为有效。
受控质保手册,是企业质量保证的法规依据或证明;b)非受控质保手册,是企业向用户或其它方提供的质保体系证明。
4.2.2 受控质保手册的发放a)质管办负责按确定发放清册,编号发放、签收、登记。
b)受控质保手册的发放对象(持有者)是公司级领导,有关职能部门负责人、质控系统责任人和质量管理部门专业管理人员。
4.2.3非受控质保手册的发放当用户或其它相关方需要手册时,由企业相关部门向质管办提出经领导签字的书面申请,登记发放。
非受控质保手册不执行以下程序。
4.3质保手册的更改4.3.1 质保手册在执行过程中,各部门可提出修改意见,书面报质管办,但未经正式批准修改之前,仍按原规定内容执行。
4.3.2 质管办依据国家相关法规、法令、标准、企业质量方针的调整及有关部门的修改意见等,提出局部修改或再版的意见,经质保工程师审核、总经理批准后,方可更改或重新编写质保手册。
4.3.3 质管办依照总经理指令,负责手册的更改或换版。
手册的修改须填写“文件修改申请表”和“修订文件审批表”。
4.3.4质保手册的更改分换页、换版两种。
4.3.5质管办具体负责质保手册的更改:a)建立质量保证体系文件控制清单,记载更改标记、具体内容、更改执行人、更改依据、时间、更改数量等;b)“文件修改通知单”和需更换的更改页发至受控质保手册的持有者,并在文件发放回收登记表上签收;c)手册持有者应配合质管办,实施更改,更换下来的废页由质管办负责回收,统一销毁;d)当质量管理标准、企业组织机构、质量方针、经营方向发生重大变化时,经总经理批准,由质管办负责实施手册的换版和之后的受控手册的回收及新版手册的发放工作。
压力容器审图中图纸常见错误
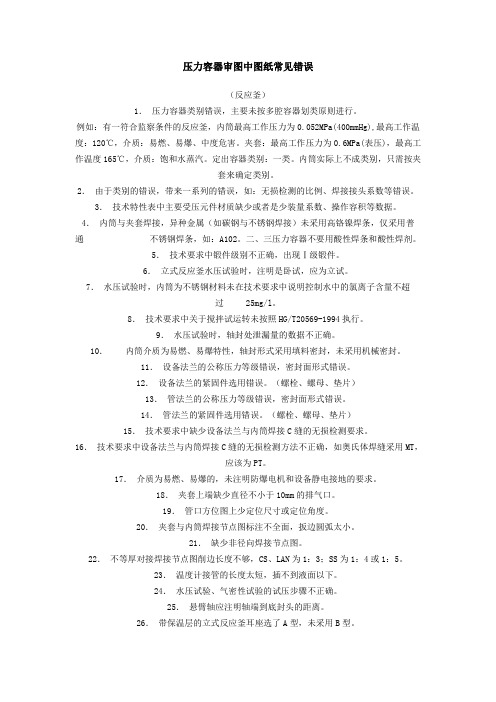
压力容器审图中图纸常见错误(反应釜)1.压力容器类别错误,主要未按多腔容器划类原则进行。
例如:有一符合监察条件的反应釜,内筒最高工作压力为0.052MPa(400mmHg),最高工作温度:120℃,介质:易燃、易爆、中度危害。
夹套:最高工作压力为0.6MPa(表压),最高工作温度165℃,介质:饱和水蒸汽。
定出容器类别:一类。
内筒实际上不成类别,只需按夹套来确定类别。
2.由于类别的错误,带来一系列的错误,如:无损检测的比例、焊接接头系数等错误。
3.技术特性表中主要受压元件材质缺少或者是少装量系数、操作容积等数据。
4.内筒与夹套焊接,异种金属(如碳钢与不锈钢焊接)未采用高铬镍焊条,仅采用普通不锈钢焊条,如:A102。
二、三压力容器不要用酸性焊条和酸性焊剂。
5.技术要求中锻件级别不正确,出现Ⅰ级锻件。
6.立式反应釜水压试验时,注明是卧试,应为立试。
7.水压试验时,内筒为不锈钢材料未在技术要求中说明控制水中的氯离子含量不超过25mg/l。
8.技术要求中关于搅拌试运转未按照HG/T20569-1994执行。
9.水压试验时,轴封处泄漏量的数据不正确。
10.内筒介质为易燃、易爆特性,轴封形式采用填料密封,未采用机械密封。
11.设备法兰的公称压力等级错误,密封面形式错误。
12.设备法兰的紧固件选用错误。
(螺栓、螺母、垫片)13.管法兰的公称压力等级错误,密封面形式错误。
14.管法兰的紧固件选用错误。
(螺栓、螺母、垫片)15.技术要求中缺少设备法兰与内筒焊接C缝的无损检测要求。
16.技术要求中设备法兰与内筒焊接C缝的无损检测方法不正确,如奥氏体焊缝采用MT,应该为PT。
17.介质为易燃、易爆的,未注明防爆电机和设备静电接地的要求。
18.夹套上端缺少直径不小于10mm的排气口。
19.管口方位图上少定位尺寸或定位角度。
20.夹套与内筒焊接节点图标注不全面,扳边圆弧太小。
21.缺少非径向焊接节点图。
22.不等厚对接焊接节点图削边长度不够,CS、LAN为1:3;SS为1:4或1:5。
压力容器制造工艺守则C17氨渗漏试验
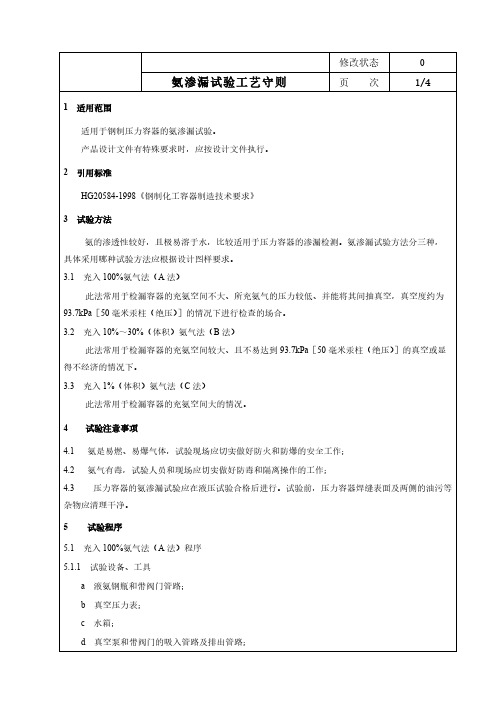
氨渗漏试验工艺守则页次1/41 适用范围适用于钢制压力容器的氨渗漏试验。
产品设计文件有特殊要求时,应按设计文件执行。
2 引用标准HG20584-1998《钢制化工容器制造技术要求》3 试验方法氨的渗透性较好,且极易溶于水,比较适用于压力容器的渗漏检测。
氨渗漏试验方法分三种,具体采用哪种试验方法应根据设计图样要求。
3.1 充入100%氨气法(A法)此法常用于检漏容器的充氨空间不大、所充氨气的压力较低、并能将其间抽真空,真空度约为93.7kPa[50毫米汞柱(绝压)]的情况下进行检查的场合。
3.2 充入10%~30%(体积)氨气法(B法)此法常用于检漏容器的充氨空间较大、且不易达到93.7kPa[50毫米汞柱(绝压)]的真空或显得不经济的情况下。
3.3 充入1%(体积)氨气法(C法)此法常用于检漏容器的充氨空间大的情况。
4 试验注意事项4.1 氨是易燃、易爆气体,试验现场应切实做好防火和防爆的安全工作;4.2 氨气有毒,试验人员和现场应切实做好防毒和隔离操作的工作;4.3 压力容器的氨渗漏试验应在液压试验合格后进行。
试验前,压力容器焊缝表面及两侧的油污等杂物应清理干净。
5试验程序5.1 充入100%氨气法(A法)程序5.1.1 试验设备、工具a 液氨钢瓶和带阀门管路;b 真空压力表;c 水箱;d 真空泵和带阀门的吸入管路及排出管路;5.2.2.3 启动真空泵抽真空至真空度20kPa[608毫米汞柱(绝压)]。
修改状态0氨渗漏试验工艺守则页次4/45.2.2.4 根据表列压力、氨浓度、保压时间的关系,充入表列压力、浓度的氨气和氮气混合气体。
如不具备抽空条件,应抽样分析氨浓度,达到指标后开始保压。
0.150.30.6 1.0试验压力(MPa)氨气浓度(%)30201510保压时间(小时)151264注:①提高检漏压力或氨气浓度,保压时间可以缩短,降低检漏压力或氨浓度,保压时间就要延长。
②按混合气中含15%(体积)氨气的比例,将充入氨气的量换算成充氨混合气体总压力的数值。
焊接质量检测方法:密封性检验

焊接质量检测方法:密封性检验焊接质量检测是指对焊接成果的检测,目的是保证焊接结构的完整性、可靠性、安全性和使用性。
除了对焊接技术和焊接工艺的要求以外,焊接质量检测也是焊接结构质量管理的重要一环。
这次我们来讲一下焊接质量检测方法:密封性检验那么怎样检测焊接接头的密封性呢?一般情况下,可采用以下几种方式进行检测:1、沉水试验用于受较小内压的小型容器或管道。
检验前先对容器或管道充以一定压力(0.4-0.5MPa)的压缩空气,然后沉水以检验密封性,如右泄漏;水中必有气泡发生。
这也是检查自行车内胎是否漏气的常用乎段。
2、盛水试验以水自重所产生的静压检验结构有无渗漏现象。
以目测为主,适用于不受压但要求有密封性的一般焊接结构。
3、氨渗漏试验用途与煤抽渗漏试验相同,其灵敏度高于煤油渗漏试验。
试验前先在焊缝便于观察一侧粘贴浸过质量分数为5%的HgNO3,水溶液或酚酞试剂的白纸条或绷带,然后在容器内充氨气或加有体积分数为1%氮气的压缩空气。
如有泄漏,就会在白纸条或绷带上泛出色斑。
浸过质量分数为5%HgNO3水溶液的为黑斑,浸过酚酞试剂的为红斑。
4、煤油渗漏试验用于受较小内压及要求有一定密封性的焊接结构。
煤油渗透性强,非常适合焊缝的密封性检验。
检验前先在焊缝便于观察一侧刷石灰水,于燥后在焊缝另一侧刷涂煤油,如有穿透性缺陷,石灰层上会泛出煤油斑或煤油带。
观察时间为15-30min。
5、氦质谱试验氦质谱试验是目前密封性检验的最有效手段,氦质谱仪灵敏度极高,可检出体积分数为10-6的氦。
试验前先在容器内充氦,然后在容器焊缝外侧检漏。
缺点是氦气价昂及检验周期较长。
尽管氦气有极强穿透力,但极微小缝隙(此类缝除用其他手段无法检出)的穿透仍须较长时间,一些厚壁容器的检漏往往长达数十小时。
适当加温可加快检漏速度。
6、气密性试验气密性试验是锅炉、压力容器及其他要求气密性重要焊接结构的常规检验手段。
介质为洁净空气,试验压力一般等于设计压力。
氨渗漏试验作业指导书
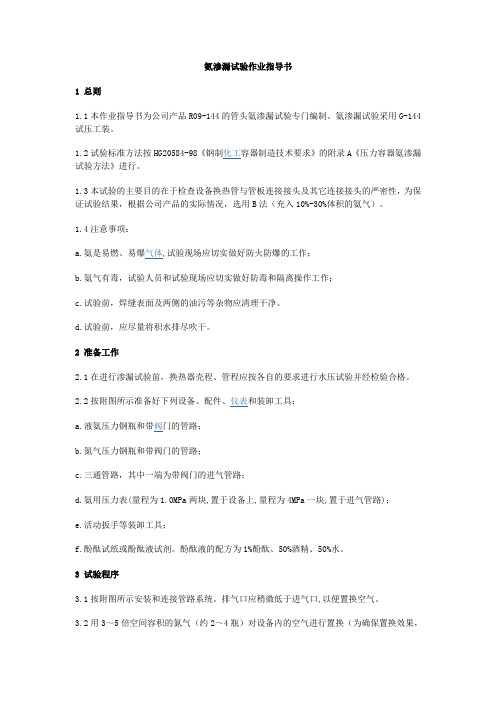
氨渗漏试验作业指导书1 总则1.1本作业指导书为公司产品R09-144的管头氨渗漏试验专门编制。
氨渗漏试验采用G-144试压工装。
1.2试验标准方法按HG20584-98《钢制化工容器制造技术要求》的附录A《压力容器氨渗漏试验方法》进行。
1.3本试验的主要目的在于检查设备换热管与管板连接接头及其它连接接头的严密性,为保证试验结果,根据公司产品的实际情况,选用B法(充入10%-30%体积的氨气)。
1.4注意事项:a.氨是易燃、易爆气体,试验现场应切实做好防火防爆的工作;b.氨气有毒,试验人员和试验现场应切实做好防毒和隔离操作工作;c.试验前,焊缝表面及两侧的油污等杂物应清理干净。
d.试验前,应尽量将积水排尽吹干。
2 准备工作2.1在进行渗漏试验前,换热器壳程、管程应按各自的要求进行水压试验并经检验合格。
2.2按附图所示准备好下列设备、配件、仪表和装卸工具:a.液氨压力钢瓶和带阀门的管路;b.氮气压力钢瓶和带阀门的管路;c.三通管路,其中一端为带阀门的进气管路;d.氨用压力表(量程为1.0MPa两块,置于设备上,量程为4MPa一块,置于进气管路);e.活动扳手等装卸工具;f.酚酞试纸或酚酞液试剂。
酚酞液的配方为1%酚酞、50%酒精、50%水。
3 试验程序3.1按附图所示安装和连接管路系统。
排气口应稍微低于进气口,以便置换空气。
3.2用3~5倍空间容积的氮气(约2~4瓶)对设备内的空气进行置换(为确保置换效果,也可先将设备充满水,再以氮气置换,应尽可能排尽积水)。
以避免形成氨气和空气的爆炸混合物。
3.3试验过程中严禁携带火种进现场及对设备进行敲击。
3.4上述过程经检验和安全人员确认后,由操作人员按下表的规定缓慢充压:3.5将检漏显示剂(或试纸)紧密涂敷在管板上,并始终保持在湿润状态。
3.6关闭三通进气管路阀门。
在检漏压力下,保压时间按表所示。
保压开始后半小时、1小时各检查一次,以后每间隔2小时检查一次,以试纸上无红色斑点出现为合格。
焊缝质量检测
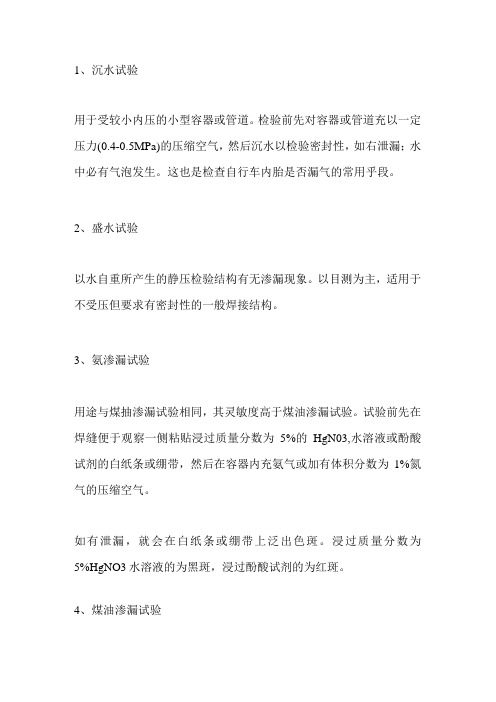
1、沉水试验用于受较小内压的小型容器或管道。
检验前先对容器或管道充以一定压力(0.4-0.5MPa)的压缩空气,然后沉水以检验密封性,如右泄漏;水中必有气泡发生。
这也是检查自行车内胎是否漏气的常用乎段。
2、盛水试验以水自重所产生的静压检验结构有无渗漏现象。
以目测为主,适用于不受压但要求有密封性的一般焊接结构。
3、氨渗漏试验用途与煤抽渗漏试验相同,其灵敏度高于煤油渗漏试验。
试验前先在焊缝便于观察一侧粘贴浸过质量分数为5%的HgN03,水溶液或酚酸试剂的白纸条或绷带,然后在容器内充氨气或加有体积分数为1%氮气的压缩空气。
如有泄漏,就会在白纸条或绷带上泛出色斑。
浸过质量分数为5%HgNO3水溶液的为黑斑,浸过酚酸试剂的为红斑。
4、煤油渗漏试验用于受较小内压及要求有一定密封性的焊接结构。
煤油渗透性强,非常适合焊缝的密封性检验。
检验前先在焊缝便于观察一侧刷石灰水,于燥后在焊缝另一侧刷涂煤油,如有穿透性缺陷,石灰层上会泛出煤油斑或煤油带。
观察时间为15∙30min05、氢质谱试验氧质谱试验是目前密封性检验的最有效手段,氢质谱仪灵敏度极高,可检出体积分数为10-6的氨。
试验前先在容器内充氨,然后在容器焊缝外侧检漏。
缺点是氨气价昂及检验周期较长。
尽管氨气有极强穿透力,但极微小缝隙(此类缝除用其他手段无法检出)的穿透仍须较长时间,一些厚壁容器的检漏往往长达数十小时。
适当加温可加快检漏速度。
6、气密性试验气密性试验是锅炉、压力容器及其他要求气密性重要焊接结构的常规检验手段。
介质为洁净空气,试验压力一般等于设计压力。
试验时压力应逐级递增。
达到设计压力后,在焊缝或密封面外侧涂肥皂水并以肥皂水是否冒泡为检验依据。
因气密性检验有爆炸危险,因此应在水压试验合格后进行。
气密性试验与气压试验是不一样的:1、它的目的不同,气密性试验是检验压力容器的严密性,气压试验是检验压力容器的耐压强度。
其次试验压力不同,气密性试验压力为容器的设计压力,气压试验压力为设计压力的1.15倍。
氨渗漏试验工艺守则(最新)

1 适用范围适用于钢制压力容器的氨渗漏试验。
产品设计文件有特殊要求时,应按设计文件执行。
2 引用标准 HG20584-2011《钢制化工容器制造技术规定》3 试验方法氨的渗透性较好,且极易溶于水,比较适用于压力容器的渗漏检测。
氨渗漏试验方法分三种,具体采用哪种试验方法应根据设计图样要求。
3.1 充入100%氨气法(A法)此法常用于检漏容器的充氨空间不大、所充氨气的压力较低、并能将其间抽真空,真空度约为93.7kPa[50毫米汞柱(绝压)]的情况下进行检查的场合。
3.2 充入10%~30%(体积)氨气法(B法)此法常用于检漏容器的充氨空间较大、且不易达到93.7kPa[50毫米汞柱(绝压)]的真空或显得不经济的情况下。
3.3 充入1%(体积)氨气法(C法)此法常用于检漏容器的充氨空间大的情况。
4 试验注意事项4.1 氨是易燃、易爆气体,试验现场应切实做好防火和防爆的安全工作;4.2 氨气有毒,试验人员和现场应切实做好防毒和隔离操作的工作;4.3 压力容器的氨渗漏试验应在液压试验合格后进行。
试验前,压力容器焊缝表面及两侧的油污等杂物应清理干净。
5.1 充入100%氨气法(A法)程序5.1.1 试验设备、工具a 液氨钢瓶和带阀门管路;b 真空压力表;c 水箱;d 真空泵和带阀门的吸入管路及排出管路;e 扳手、钢丝钳等装卸工具;f 酚酞试纸或酚酞试剂(也可用石蕊试剂)。
酚酞液的配方为1%酚酞、50%酒精、50%水。
图1 A法氨检漏试验安装图5.1.2 试验过程5.1.2.1 将一个充氨空间的两个检漏口(A、B)分别设置在相距最远的两端处。
5.1.2.2 按图 1 安装和连接密封试验管路。
5.1.2.3 开动真空泵,使充氨空间抽真空至真空度93.7kPa[50毫米汞柱(绝压)]。
5.1.2.4 用检测显示剂、试剂或试纸,涂敷在所有检测焊缝的内侧。
5.1.2.5 充入氨气,使压力达到2~3kPa[200~300水柱(表压)]为止,并保压12小时,检验试纸或试剂是否变色(泄漏),如有泄漏,修补后重新进行液压试验和100%氨渗漏试验。
- 1、下载文档前请自行甄别文档内容的完整性,平台不提供额外的编辑、内容补充、找答案等附加服务。
- 2、"仅部分预览"的文档,不可在线预览部分如存在完整性等问题,可反馈申请退款(可完整预览的文档不适用该条件!)。
- 3、如文档侵犯您的权益,请联系客服反馈,我们会尽快为您处理(人工客服工作时间:9:00-18:30)。
氨渗漏试验工序
1、试验方法
按HG/T20584-2011附录A中C法(充入1%(体积)氨气法)进行氨渗漏检验管头焊缝。
2、准备工作
液氨钢瓶、氮气钢瓶、带阀门的管路;压力表;排泄水槽;白纸和酚酞试剂(1%酚酞、49%酒精、50%水)。
3、操作程序
1)壳程内部用压缩空气彻底吹扫,内部保持干燥。
2)内部干燥后打开氮气阀门及排气阀门(保证排气管口浸没在水槽中),充入足量的氮气进行置换。
3)置换完成后,关闭排气阀门,缓慢打开充氨阀门进行充氨,充入1%(体积)氨气,充氨完成后,关闭充氨阀门;
4)打开充氮阀门,缓慢加压至试验压力0.11MPa时,停止充氮,关闭充氮阀门。
5)将检漏酚酞试纸贴在检测部位,试纸始终保持湿润状态。
6)试验压力保压10min,然后降至设计压力,检查试纸是否变色。
无变色为合格。
7)检漏试验完毕后,打开排气阀进行泄压,排气管口必须浸没在水槽中,泄压过程应缓慢。
8)压力表压力降为0后,打开充氮阀门,将设备内部氨气彻底置换干净,置换过程中同样保证排气管口浸没在水槽中。
4、注意事项
1)氨气属易燃易爆有毒气体,试验现场必须防火、防爆、通风,操作人员做好个人防护;
2)氨渗漏在专门的试验场地,并设置标识,无关人员禁止进入或接近;
3)试验过程中安排专人进行检验和监控;
4)试验过程中严禁带压拧紧或松动螺栓等;
5)氨气瓶应立置,并与设备保持一定距离,开启氨气瓶时应缓慢开启,严禁液氨进入设备,操作人员必须做好个人防护,拆除软管时应注意防止软管内残余氨气喷射入眼或面部。