第4章物料需求计划
物料管理入门第四讲

作业
一、复习与思考
1、物料需求计划的两个主要目标? 2、物料需求计划系统的主要输入? 3、描述以下类型物料清单:多层物料清单、单层物料清单、多级物料清单、 简化物料清单、计划物料清单
4、为什么MRP程序储存单层物料清单? 5、物料清单有哪些用途? 6、谁负责下达计划订单?叙述下达计划订单对库存记录、生产作业控制和采 购部门的影响。
物料需求计划的环境
需求特征
独立需求 相关需求
生产计划与控制
MRP的目标
9 确定需求 ¾ 订购什么 ¾ 订购多少 ¾ 何时订购 ¾ 何时安排交付
9 保持优先权准确 ¾ 响应供需变化 ¾ 重新安排优先权
MRP流程的输入、输出
计划软件
9计算优先计划、发放和接受计划订单 9建议计划者需要有哪些行动以维持优先计划 9重新计算优先计划以确保物料需求到货期, 库存状态最新
100
150
100
150
200
计划接收量
300
预计可用库存 150
50
‐100
100
250
50
净需求
50
计划订单接收
300
计划订单下达
300
管理物料需求计划需要考虑的因素
9自下而上重新计划 条件改变采取的修正行动应该尽可能在产品结
构树的低层产生。
管理物料需求计划需要考虑的因素
9降低系统敏感性 • 计划员必须判断变化是否足以做出反应以及 订单是否应该下达 • 降低系统敏感性的方法之一是确定订单
7、什么是低层码?低层码的的主要用途? 8、叙述计划订单、已下达订单和确定订单的差异。谁来控制它们? 9、管理物料需求计划的3个重要因素是什么? 二、计算题
1、《物料管理入门》P83(4.5题) 2、《物料管理入门》P87(4.11题) 3、《物料管理入门》P92(4.17题)
第4章 ERP系统的构成
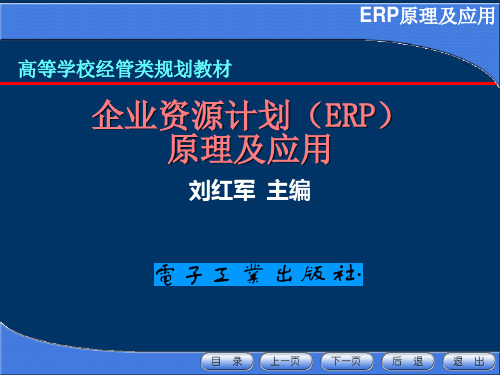
在MPS决定生产多少最终产品 MPS决定生产多少最终产品 再根据BOM BOM, 后,再根据BOM,把企业要生 产的产品的数量 产品的数量转变为所需生 产的产品的数量转变为所需生 产的零部件的数量 零部件的数量, 产的零部件的数量,
ERP原理及应用 原理及应用
4.能力需求计划 .
包括粗能力计划(RCCP)和细能力需求计划(RCP) 包括粗能力计划(RCCP)和细能力需求计划(RCP) (RCCP)和细能力需求计划 RCCP是对主生产计划所需的关键资源生产能力进行 是对主生产计划 是对主生产计划所需的关键资源生产能力进行 估算, 给出能力需求的概貌, 从能力方面对主生产 估算 , 给出能力需求的概貌 , 从能力方面对 主生产 计划的可行性进行评估 的可行性进行评估。 计划的可行性进行评估。 CRP是用来检查物料需求计划可行性,它根据物料需 CRP是用来检查物料需求计划可行性,它根据物料需 是用来检查物料需求计划可行性 求计划, 对工厂现有能力进行能力模拟 能力模拟, 求计划 , 对工厂现有能力进行 能力模拟 , 同时根据 工作中心能力负荷状况判断计划的可行性 判断计划的可行性。 各工作中心能力负荷状况判断计划的可行性。
ERP原理及应用 原理及应用
3.物料需求计划(MPR) .物料需求计划(MPR)
MRP模块主要功能 MRP模块主要功能 (1)MRP计算的数据源 )MRP计算的数据源 )MRP计算 (2)MRP计算 (3) 物 料需 求 计 划 和 主 生 对照现有库存量, 对照现有库存量,根据设定 产计划 规则, 计算, 的MPR规则,进行 规则 进行MPR计算, 计算 (4) 采 购申 请 单 和 生 产 任 生成加工单和采购单 务单 生成加工单和采购单,产生 报表, 报表 (5)任务分割和生产排产 MRP报表,包括明细表和会 总表以及例外报表等, 总表以及例外报表等,形成企 业生产计划。 业生产计划。
第4章 生产规划

可用资源
生产计划大纲 图4-1 生产规划功能
4.3 生产规划大纲的编制方法
信息收集 (1) 计划部门的信息:包括销售目标和库存目标,均以金额表示。 (2) 市场部门的信息:包括各时段产品的销售预测(以产品数量表
示)。 (3) 产品研发部门的信息:确认新产品设计的可能性,包括资源清单
和专用设备要求。 (4) 生产部门的信息:主要为资源可用性,如可用劳动力、可用机时
订单
生产规划 110 110 110 110 110 110 110 110 110 110
11月 100 310 110
12月 100 300 110
全年 1200
1320
3. 其他方法
实际运作过程中有采用数学方法,如线性规划、 线性决策规则、回归分析模型、仿真、搜索决 策规则等。
线性规划的运输方法
例:假设生产手机的生产过程包括4个主要工 序:贴片、测试、压制、成型。在过去6个月 中,在一条生产线上,有9个不同型号使用上 述生产制造设备,在这4个工序中用了47000 个直接工时,完成了这种系列产品5800 部手
机。生产计划大纲中下两个季度的计划为 7000部手机。
表4-12 能力计划系数法资源清单
计算步骤:
(1) 把年预测销售量1200辆按月平均分布,每月为100辆。 (2) 计算期初库存
期初库存=当前库存一拖欠订单=500-300=200辆 (3) 计算库存变化
库存变化=目标库存-期初库存-100-200=(-100)辆(库存减少) (4) 计算总生产需求
总生产需求=预测数量+库存变化=1200+(-100)=1100辆 (5) 把总生产需求量按时间段分配在整个计划展望期内,所得到的生
生产计划与物料需求规划管理制度

生产计划与物料需求规划管理制度第一章总则为了提高企业的生产效率,合理调配物料资源,保证生产计划的顺利实施,特订立本《生产计划与物料需求规划管理制度》(以下简称本制度)。
本制度适用于本企业的生产计划与物料需求规划管理工作。
全部相关部门和人员都必需严格遵守本制度的规定。
第二章生产计划管理第一节生产计划编制1.生产计划编制的目的是依据市场需求、产能和资源情形,订立合理的生产计划,确保生产任务的完成和交付时间的准确性。
2.生产计划由生产计划部门负责编制,各部门负责供应相关数据支持。
3.生产计划的编制周期为每月,包含生产任务分解、生产订单订立等内容。
具体编制过程由生产计划部门负责订立并报告有关部门。
4.生产计划应充分考虑资源和制约因素,确保可执行性和经济性。
第二节生产计划审核与发布1.生产计划的审核由生产计划部门和相关部门共同进行,包含生产调度部门、销售部门等。
2.生产计划审核的重要内容包含任务合理性、资源配备是否充分、交付时间是否符合要求等。
审核结果由审核人员签字确认,并将看法反馈给生产计划部门。
3.审核通过的生产计划由生产计划部门负责发布,并通知相关部门和人员。
第三节生产计划执行与监控1.生产计划的执行由生产调度部门负责,确保生产任务依照计划进行。
2.生产调度部门应及时与各部门沟通协调,解决生产过程中的问题和调整计划布置。
3.生产计划的执行过程中,生产调度部门应及时监控生产进度,确保任务定时完成,并及时报告生产计划部门。
第四节生产计划评估与调整1.生产计划的评估和调整由生产计划部门负责。
2.生产计划评估的重要内容包含完成情况分析、任务调整建议等。
评估结果应及时报告给相关部门,并依照需要进行相应的调整。
第三章物料需求规划管理第一节物料需求计划编制1.物料需求计划编制的目的是依据生产计划和库存情况,订立合理的物料采购计划,确保物料供应的准确性和及时性。
2.物料需求计划由采购部门负责编制,各部门负责供应相关数据支持。
生产计划与物料控制指南

生产计划与物料控制指南第1章生产计划概述 (4)1.1 生产计划的定义与作用 (4)1.2 生产计划的类型与编制方法 (4)第2章物料控制基本概念 (5)2.1 物料的定义与分类 (5)2.2 物料控制的目标与任务 (5)2.3 物料控制的关键环节 (6)第3章生产能力规划 (6)3.1 生产能力的概念与衡量 (6)3.1.1 设计生产能力:指企业在设计阶段根据市场需求和设备、工艺等条件所确定的生产能力。
(6)3.1.2 实际生产能力:指企业在实际生产过程中,由于设备、人员、物料等多种因素的影响,实际可以达到的生产能力。
(6)3.1.3 有效生产能力:指企业在现有生产条件下,排除无效作业和浪费后,实际发挥的生产能力。
(7)3.1.4 安全生产能力:指企业在考虑设备故障、维修、人员请假等因素后,仍能保持的生产能力。
(7)3.2 影响生产能力的因素 (7)3.2.1 人因素:包括员工素质、技能水平、劳动态度等。
(7)3.2.2 设备因素:包括设备功能、设备故障率、设备维护状况等。
(7)3.2.3 物料因素:包括物料质量、物料供应及时性、物料成本等。
(7)3.2.4 工艺因素:包括生产工艺水平、工艺流程合理性、工艺参数优化等。
(7)3.2.5 管理因素:包括生产计划合理性、生产组织有效性、质量管理水平等。
(7)3.3 生产能力规划的方法 (7)3.3.1 需求预测法:根据市场需求预测,结合企业现有资源,确定生产能力。
(7)3.3.2 滚动计划法:在现有生产计划的基础上,根据市场需求变化和生产实际情况,不断调整生产能力。
(7)3.3.3 线性规划法:利用线性规划模型,求解生产能力的最优配置。
(7)3.3.4 网络计划法:通过构建生产活动的网络图,分析关键路径,优化生产能力。
(7)3.3.5 模糊综合评价法:综合考虑多种影响因素,利用模糊数学方法对生产能力进行评价和规划。
(7)3.3.6 仿真法:通过模拟生产过程,分析不同生产策略下的生产能力,为决策提供依据。
自考《生产与作业管理》章节习题:第4章

自考《生产与作业管理》章节习题:第4章生产与作业系统计划制定名词解释1工业总产值:指以货币表现的工业企业在报告期内已生产的工业产品总量。
2工业增加值:是企业在报告期内以货币表现的工业生产活动的最终成果。
3出产期:指为了保证企业按时交货所确定的产品出产期限。
4主生产计划:指确定企业每一具体最终产品在每一具体时间段应生产数量,它是综合生产计划分解和细化,其时间段一般定为一周,有时定为日、旬、月,根据具体情况而定。
5待分配库存:指营销部门用来应对顾客在确定时间内供货的产品数量。
6期量标准:就是为制造对象(产品及零、部件)在生产期限与数量方面规定的标准数据。
7在制品:指从原材料进入企业到产成品出产,处于生产与作业过程的各个环节,正在储存、加工、运输、停留的毛培、零件、部件、产成品的总称。
8在制品定额:指在一定时间、地点和具体的生产组织条件下,为保证生产连续而均衡进行,所必须的在制品数量标准。
9批量:就是相同产品(或零件)一次投入和出产的数量。
10生产间隔期:指相邻两批相同产品(或零件)投入的时间间隔或产出的时间间隔。
11产品的生产周期:指一批产品从原材料投入生产起一直到产品出产为止的全部工作日数。
12生产提前期:指产品(零件)在各工艺阶段投入、产出的时间与成品出产时间相比所要提前的时间。
13物料需求计划(MRP):指运用计算机技术提出了把企业产品中的各种所需物料分为独立需求和相关需求两种类型的概念,并按时间确定不同时期物料需求,产生了解决库存物料订货的新方法。
14企业资源计划(ERP):之建立在信息技术基础上,以系统化的管理思想,以现实最合理地配置资源,满足市场需求,为企业与决策层和员工提供决策运行手段的管理平台。
15协同商务:指企业内部人员、企业与业务伙伴、企业与客户之间的电子化业务的交互过程。
16推动式方法:指每一生产车间和每个工作地按计划制造零部件,将加工完的零部件送往后续车间和后一道工序,同时,将完工信息反馈到计划部门。
《生产与运作管理》课程笔记

《生产与运作管理》课程笔记第一章绪论1.生产与运作管理概述生产与运作管理是指在一定的时间内,通过有效地组织人力、物力和财力等资源,按照市场需求和企业经营目标,进行产品或服务的生产活动。
它是企业经营管理的重要组成部分,直接关系到企业的经营效果和市场竞争力。
内容:包括生产运作系统的设计、运行和改进,具体涵盖产品和服务的选择、生产运作系统布局、质量管控、成本控制以及生产过程的规划与控制。
目标:提高生产效率、降低成本、保证产品质量、满足市场需求、提升客户满意度和实现可持续发展。
2.生产与运作管理的发展历程生产与运作管理的发展经历了从手工作坊到工业革命,再到现代生产方式的转变,逐步形成了科学管理体系。
产生背景:随着生产力的发展和市场需求的变化,传统的生产方式无法满足现代社会的需求,促进了生产运作管理理论的发展。
发展过程:从泰勒的科学管理理论,到福特的流水线生产模式,再到丰田的精益生产和敏捷制造,生产与运作管理不断适应时代变化,推动生产效率的提升。
现代特征:现代生产运作管理强调利用信息技术,优化资源配置,实施精细化管理和绿色生产,以适应全球化竞争和可持续发展的要求。
3.生产运作的分类根据产品形态和生产组织方式的不同,生产运作可以分为制造性生产和服务性生产。
制造性生产:指通过物理或化学作用,将原材料转化为新产品的过程,如汽车制造、电子产品组装等。
服务性生产:指不通过物质产品的转化,直接为顾客提供所需服务的过程,如餐饮服务、金融服务等。
4.生产过程组织生产过程组织是生产与运作管理的基础,涉及生产过程的空间组织和时间组织两个方面。
空间组织:主要解决生产设施的布局问题,包括工厂布局、设备布置、工作站设置等,目的是实现高效、安全和舒适的工作环境。
时间组织:主要解决生产活动的时序安排问题,包括作业计划、流程控制、交货期管理等,目的是确保生产的及时性和连续性。
第二章企业战略和生产与运作战略1.企业战略和战略管理概述基本概念:企业战略是企业为了实现其长期目标,通过对外部环境和内部条件的分析,制定的一系列行动计划。
现代生产管理与控制的方法--中级经济师考试辅导《工商管理专业知识与实务》第四章第五节讲义1
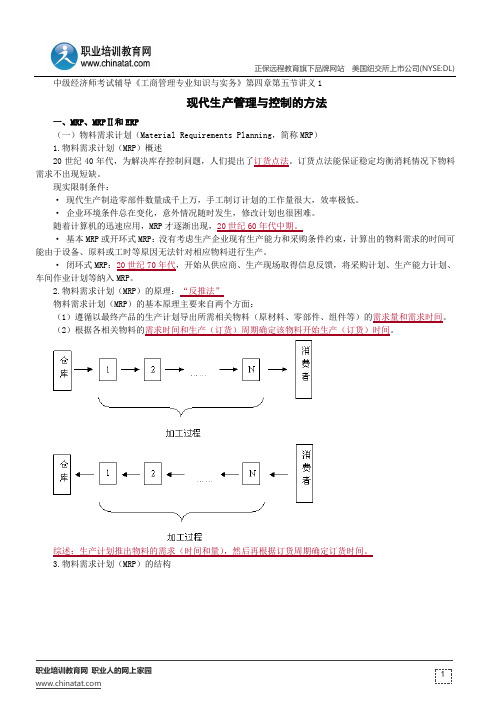
正保远程教育旗下品牌网站美国纽交所上市公司(NYSE:DL)
职业培训教育网职业人的网上家园
中级经济师考试辅导《工商管理专业知识与实务》第四章第五节讲义1
现代生产管理与控制的方法
一、MRP、MRPⅡ和ERP
(一)物料需求计划(Material Requirements Planning,简称MRP)
1.物料需求计划(MRP)概述
20世纪40年代,为解决库存控制问题,人们提出了订货点法。
订货点法能保证稳定均衡消耗情况下物料需求不出现短缺。
现实限制条件:
· 现代生产制造零部件数量成千上万,手工制订计划的工作量很大,效率极低。
· 企业环境条件总在变化,意外情况随时发生,修改计划也很困难。
随着计算机的迅速应用,MRP才逐渐出现,20世纪60年代中期。
· 基本MRP或开环式MRP:没有考虑生产企业现有生产能力和采购条件约束,计算出的物料需求的时间可能由于设备、原料或工时等原因无法针对相应物料进行生产。
· 闭环式MRP:20世纪70年代,开始从供应商、生产现场取得信息反馈,将采购计划、生产能力计划、车间作业计划等纳入MRP。
2.物料需求计划(MRP)的原理:“反推法”
物料需求计划(MRP)的基本原理主要来自两个方面:
(1)遵循以最终产品的生产计划导出所需相关物料(原材料、零部件、组件等)的需求量和需求时间。
(2)根据各相关物料的
需求时间和生产(订货)周期确定该物料开始生产(订货)时间。
综述:生产计划推出物料的需求(时间和量),然后再根据订货周期确定订货时间。
3.物料需求计划(MRP)的结构。
高级经济师-工商管理(第1-4章)内容总结和默写表
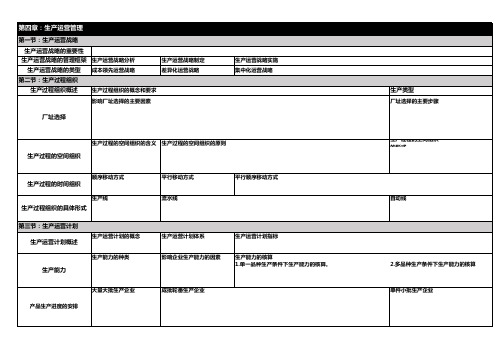
在制品定额 库存控制的基本方法 生产调度系统的组织 调度制度与方法
生产能力的核算 1.单一品种生产条件下生产能力的核算。
成批轮番生产企业
生产类型 厂址选择的主要步骤 生产过程的空间组织 的形式
自动线
2.多品种生产条件下生产能力的核算 单件小批生产企业
生产作业计划
生产作业计划的概念
第四节:生产运营控制 生产进度控制
生产进度控制的概述
在制品控制★
在制品控制的概念
库存控制★
第四章:生产运营管理
第一节:生产运营战略
生产运营战略的重要性
生产运营战略的管理框架 生产运营战略分析
生产运营战略制定
生产运营战略的类型 成本领先运营战略
差异化运营战略
第二节:生产过程组织
生产过程组织概述
生产过程组织的概念和要求
影响厂址选择的主要因素
厂址选择
生产运营战略实施 集中化运营战略
生产过程的空间组织
丰田生产方式
物料需求计划(MRP I )
概述 基本原理 结构
丰田生产方式概述
制造资源计划(MRP II) 概述 结构(5方面的结构特点)
丰田生产方式的思想和手段
企业资源计划(ERP)
概述 内容(生产/物流/财务/人力资源) 实施
✮在制品定额法:本车间产出量=后续车间投入量+本车间半成品外售量+(本车间期末库存半成品定额-本车间期初预计库存半成品结存量) ✮在制品定额法:本车间投入量=本车间产出量+本车间计划允许废品及损耗量+(本车间期末在制品定额-本车间期初预计在制品结存量) 例题:
库存控制的概念
生产调度★
生产调度的概念
期量标准
物料需求计划【共49张PPT】
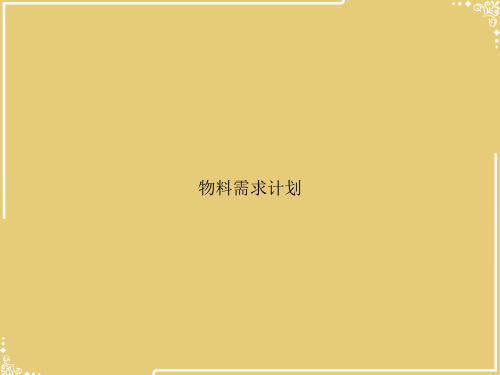
采购供应计划
每一项加工件的建议计划 • 需求数量 • 开始日期和完工日期
每一项采购件的建议计划 • 需求数量 • 订货日期和到货日期
MRP 的基本逻辑
四、MRPII的输入信息
MRP的输入有3个部分: • 主生产计划(产品出产计划MPS)
• 物料清单(产品结构文件,BOM) • 库存状态文件
物料清单(产品结构文件,BOM)
净需求=总需求—(预计到货量+现有量)+安全库存 于是,人们便思考:怎样才能在需要的时间,按需要的数量得到真正需用的物料?从而消除盲目性,实现低库存与高服务水平并存。 ERP是在MRP基础上发展起来的,以供应链思想为基础,融现代管理思想为一身,以现代化的计算机及网络通信技术为运行平台,集企业的各项管理功能为一身,并能对供应链上所有资源进行有效控 制的计算机管理系统。
件;要加工各种零件,就必须提前一定时间准备所需
数量的各种毛坯,直至提前一定时间准备各种原材料 。
其主要功能及运算依据为:
处 理 的 问 题 1. 生 产 什 么 ?生 产 多 少 ? 2. 要 用 到 什 么 ? 3. 已 具 备 什 么 ? 4. 还 缺 什 么 ? 何 时 需 要 ?
所 需 信 息 1. 切 实 可 行 的 主 生 产 计 划 ( M PS) 2. 准 确 的 物 料 清 单 ( BOM表 ) 3. 准 确 的 物 料 库 存 数 据 4. M RP的 计 算 结 果 ( 生 产 计 划 和 采 购 计 划 )
物料需求计划
本章学习目标
• 物料需求计划(MRP):
– Material Requirements Planning
• 制造资源计划(MRPⅡ ):
– Manufacturing Resource Planning
第4章-生产大纲

资源需求计划编制(续)
下面,由表1数据计算生产自行车、四轮车 和三轮车时,钢和工时的需求量。
计算钢需求量 产品类 计划生产量 单位需求量 总需求量 (辆) (吨) (吨) 自行车 1200 0.0051= 6.12 四轮车 500 0.0047= 2.35 三轮车 1000 0.0029= 2.90 总量 11.37或11.4吨
产品族:M0138 卡车 变量单位:辆 当前库存量:435 当前日期: 01/02/1996
销售规划
日期 09/11 /95 10/01 /95 11/07 /95 12/05 01/02 1/30 /96 /95 /96 2/27 /96 3/26 /96 4/23 /96
计划订货量
实际订货量 偏差 累计偏差 到期的客户订单 实际发货量
目标库存 100
库存改变:-100 平均月库存改变量:-8.33 总生产量:1100 返回
附:MTO环境下生产计划大纲编制(续)
例:假设某工厂对自行车编制生产规划, 计划展望期是1年,按月划分时区。年 末未完成订单数量为300辆,当前未完 成订单是420辆,自行车的年预测销售 量是1200辆。
返回
(4)协调可用资源和资源需求之间的差距
资源需求计划编制(续)
例:用资源消耗法确定资源需求 1)分析资源清单:资源清单是生产单位的产品大类 所必须的材料、标准工时和机器的记录,并标明材 料、劳动力和设备工时的数量。资源清单上的数值 是产品大类中所有产品的平均值。资源清单的具体 形式随不同的产品和不同的企业而不同。表1是制 造自行车、四轮车和三轮车的资源清单。
生产计划大纲
• 生产规划是为了体现企业经营规划而制定的 产品系列生产大纲,它用以协调满足经营规 划所需求的产量与可用资源之间的差距。生 产计划大纲是生产规划的表现形式。 • 生产计划大纲反映了如下问题:
供应链管理生产计划与执行指南
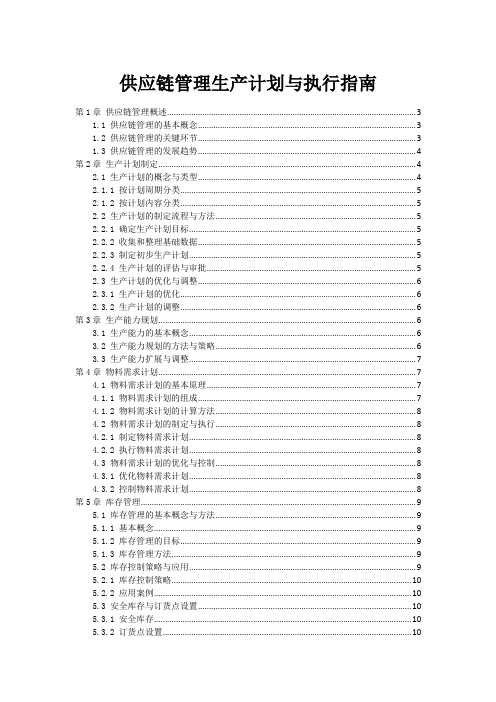
供应链管理生产计划与执行指南第1章供应链管理概述 (3)1.1 供应链管理的基本概念 (3)1.2 供应链管理的关键环节 (3)1.3 供应链管理的发展趋势 (4)第2章生产计划制定 (4)2.1 生产计划的概念与类型 (4)2.1.1 按计划周期分类 (5)2.1.2 按计划内容分类 (5)2.2 生产计划的制定流程与方法 (5)2.2.1 确定生产计划目标 (5)2.2.2 收集和整理基础数据 (5)2.2.3 制定初步生产计划 (5)2.2.4 生产计划的评估与审批 (5)2.3 生产计划的优化与调整 (6)2.3.1 生产计划的优化 (6)2.3.2 生产计划的调整 (6)第3章生产能力规划 (6)3.1 生产能力的基本概念 (6)3.2 生产能力规划的方法与策略 (6)3.3 生产能力扩展与调整 (7)第4章物料需求计划 (7)4.1 物料需求计划的基本原理 (7)4.1.1 物料需求计划的组成 (7)4.1.2 物料需求计划的计算方法 (8)4.2 物料需求计划的制定与执行 (8)4.2.1 制定物料需求计划 (8)4.2.2 执行物料需求计划 (8)4.3 物料需求计划的优化与控制 (8)4.3.1 优化物料需求计划 (8)4.3.2 控制物料需求计划 (8)第5章库存管理 (9)5.1 库存管理的基本概念与方法 (9)5.1.1 基本概念 (9)5.1.2 库存管理的目标 (9)5.1.3 库存管理方法 (9)5.2 库存控制策略与应用 (9)5.2.1 库存控制策略 (10)5.2.2 应用案例 (10)5.3 安全库存与订货点设置 (10)5.3.1 安全库存 (10)5.3.2 订货点设置 (10)第6章生产调度与控制 (10)6.1 生产调度的基本任务与方法 (10)6.1.1 基本任务 (10)6.1.2 方法 (11)6.2 生产进度控制策略 (11)6.2.1 滚动计划法 (11)6.2.2 逐级控制法 (11)6.2.3 阶段性控制法 (11)6.2.4 紧急调整法 (11)6.3 生产异常处理与改善 (11)6.3.1 生产异常处理 (12)6.3.2 生产改善措施 (12)第7章供应链协同管理 (12)7.1 供应链协同管理的重要性 (12)7.1.1 提高供应链整体效率 (12)7.1.2 降低库存成本和运输成本 (12)7.1.3 缩短产品生产与交付周期 (12)7.1.4 提升企业对市场需求的快速响应能力 (12)7.1.5 增强供应链风险管理能力 (13)7.2 供应链协同管理的策略与措施 (13)7.2.1 建立供应链合作伙伴关系 (13)7.2.2 优化供应链结构与流程 (13)7.2.3 信息共享与数据协同 (13)7.2.4 协同库存管理 (13)7.2.5 建立激励机制与风险共担机制 (13)7.3 供应链协同管理的实施与评估 (13)7.3.1 制定实施计划 (13)7.3.2 人员培训与团队建设 (13)7.3.3 监控与改进 (13)7.3.4 绩效考核与激励 (14)第8章生产计划与执行信息化 (14)8.1 信息化在供应链管理中的作用 (14)8.2 生产计划与执行信息系统 (14)8.3 信息化实施策略与案例分析 (15)第9章生产计划与执行绩效评价 (15)9.1 生产计划与执行绩效评价指标 (15)9.1.1 产量完成率:衡量实际完成产量与计划产量之间的比率,反映生产计划的执行程度。
第4章生产物流管理
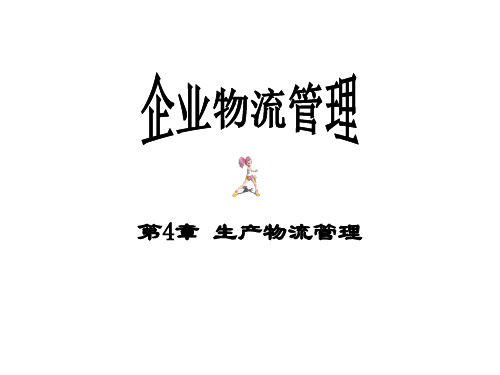
• 3.平行顺序移动方式
• 平行顺序移动方式是指一批零件或产品既保持每 道工序的平行性,又保持连续性的作业移动方式。 即是指一批零件在前一道工序尚未全部加工完毕, 将已加工好的一部分零件转送到下一道工序加工, 并使下道工序能连续地加工完该批零件的方式。 其具体做法是,当后道工序单件加工时间比前道 工序单件加工时间长,则前道工序往后道工序按 件运送;当后道工序单件加工时间比前道工序单 件加工时间短,后道工序的最后一个零件只能等 到前道工序所有零件加工完毕后,才能开始加工, 则后道工序的第一个零件加工时间,可从最后一 个零件的加工时间依次向前倒推确定。
②连续型生产物流
• 物流均匀,连续进行,不能中断,生产出的产品 和使用设备工艺流程都是固定并且标准化的,工 序之间几乎没有在制品储存。管理的重点是保证 连续供应物料和确保每个生产环节的正常进行, 由于工艺相对稳定,有条件采用自动化装置实现 对生产过程的实施监控。
• 连续型生产物流又分装配线生产与流程式生产。 装配线生产方式是指零部件按装配顺序,按一定 速率,从一个工作地到另一个工作地进行装配生 产。例如汽车和厨房用品的装配生产线等等。顾 名思义,流程式生产是按照预先确定的步骤连续 进行的产品的生产,石油精炼与化工企业正是采用 了流程式生产。
4.2生产物流合理组织
• 4.2.1生产物流的空间组织 • 生产物流的空间组织是指生产区域或工作地的布
置。目标是如何缩短工艺流程,从而缩短物流的 时间。一般有三种专业化组织形式为工艺专业化, 对象专业化和成组工艺.化. • 1.按工艺专业化形式组织生产物流 • 工艺专业化是把同类的生产设备集中起来,加工 按计划生产的工艺相同的各种产品,即加工对象 多样化,而加工工艺相同。
• (2)单件小批量生产指需要生产的产品品种多但每 一品种生产的数量少,生产重复度低。单件生产 过程特点:生产的组织分散,产品设计和零件制 造分散,设备使用通用机器。
最新MRP教学讲义ppt课件
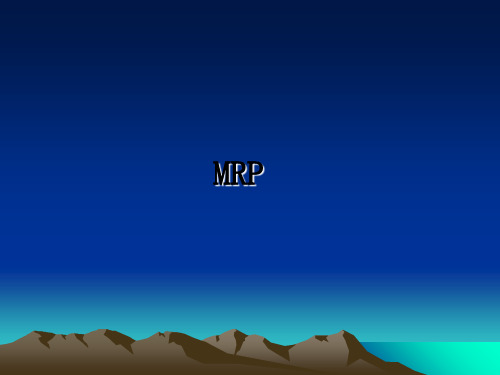
企业资源计划 Enterprise Resource Planning
企业资源计划 Enterprise Resource Planning
Break!
企业资源计划 Enterprise Resource Planning
ERP原理与设计
第4章 物料需求计划(MRP)
4.1 MRP 概述 4.2 MRP的基本原理 4.3 MRP编制 4.4 CRP
企业资源计划 Enterprise Resource Planning
MRP的发展历程
1. 基本MRP 2. 闭环MRP 3. MRP-II 4. ERP 5. ERP的未来
企业资源计划 Enterprise Resource Planning
第4章 物料需求计划(MRP) 4.1 MRP 概述
MRP概述
物料需求计划(Material Requirements Planning MRP )它是 20世纪六十年代发展起来的一种计划物料需求量和需求时间的系 统。这里的“物料”是泛指所有的材料、在制品、半成品、外购 件和产成品。开始时,它只计算需求量,是开环的,后来,从原 料供应厂商和生产现场取得了信息反馈,形成了闭环的MRP,这 才开始成为一种生产方式。80年代发展起来的制造资源计划( Manufacturing Resource Planning MRP Ⅱ ),不仅涉及物 料,而且涉及生产能力和一切制造资源,是一种广泛的资源协调 系统。它代表了一种新的生产管理思想,又是一种新的组织生产 的方式。MRP应包括在MRPⅡ中。 MRP和MRP Ⅱ 具 有广泛的适用性,但它们主要优点能在多品种小批量生产类型的 加工装配企业得到最有效的发挥。
MRP的起源
物料需求计划
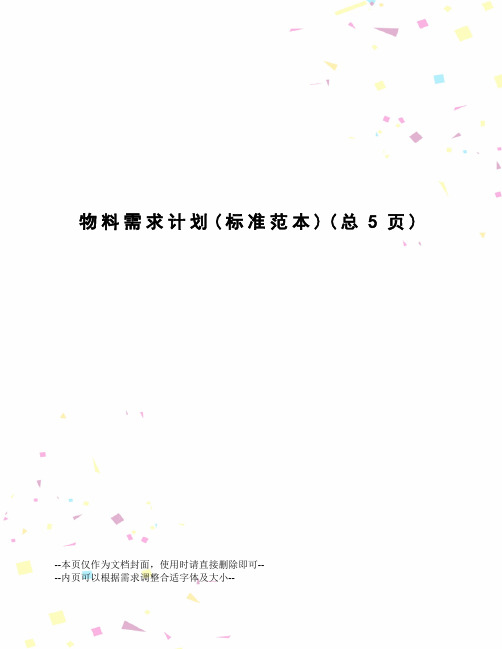
物料需求计划(标准范本)(总5页) --本页仅作为文档封面,使用时请直接删除即可----内页可以根据需求调整合适字体及大小--物料需求计划1.总则1.1. 制定目的规范物料分析作业,制定计算物料需求数量、交期的作业流程,使之有章可循。
1.2. 适用范围本公司用于产品生产使用的原物料的分析,并提出需求计划的作业。
1.3.权责单位1) 生管部负责本规章制定、修改、废止之起草工作。
2) 总经理负责本规章制定、修改、废止之核准。
2.各部门工作职责 2.1. 配合部门1) 业务部提供销售计划、客户订单资讯。
2) 资材部提供成品、半成品、原物料库存状况报表。
3) 生管部提供生产计划。
4) 技术部提供产品用料明细表。
5)采购部提供采购前置期、经济订购量、最小订购量。
2.2.责任部门生管部物控人员为用料分析之责任人员,负责制订物料需求计划。
3.物料需求计划步骤3.1.决定产品总需求量业务部决定产品总需求量。
总需求量一般由三个来源整合而成:物料需求计划(2019-2020年版) 内部资料 注意保管1)某期间(如一个月或一季度)的实际订单量。
2)该期间的预测订单量。
3)管理者决策改变前述数量(如为平衡淡旺季或调整产品结需要)。
3.2.决定产品实际需求量根据获得的总需求量,再依据该产品的成品存量状况予以调整,即得:实际需求量=总需求量-库存数量一般由业务部或生管部确认。
3.3.确定生产计划生管部依实际需求量确定生产计划,一般需做下述工作:1)产能负荷分析。
2)产销平衡。
3)中日程生产计划与细部生产计划。
3.4.分解出物料清单生管部物控人员负责物料清单的分析。
物料需求量=某期间之产品实际需求量*每一产品使用该物料数量3.5.区分物料ABC项目1)物控人员根据物料状况区分ABC项目,一般作如下区分:占总金额60%~70%的物料为A类。
占总金额余下之30%~40%的物料为B类及C类物料。
2)A类物料作物料需求计划,B类、C类物料使用订货点方法采购。
erp课后答案
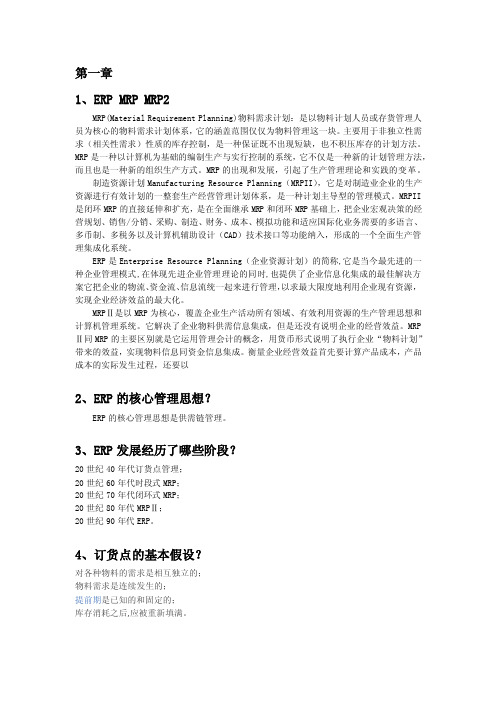
第一章1、ERP MRP MRP2MRP(Material Requirement Planning)物料需求计划:是以物料计划人员或存货管理人员为核心的物料需求计划体系,它的涵盖范围仅仅为物料管理这一块。
主要用于非独立性需求(相关性需求)性质的库存控制,是一种保证既不出现短缺,也不积压库存的计划方法。
MRP是一种以计算机为基础的编制生产与实行控制的系统,它不仅是一种新的计划管理方法,而且也是一种新的组织生产方式。
MRP的出现和发展,引起了生产管理理论和实践的变革。
制造资源计划Manufacturing Resource Planning(MRPII),它是对制造业企业的生产资源进行有效计划的一整套生产经营管理计划体系,是一种计划主导型的管理模式。
MRPII 是闭环MRP的直接延伸和扩充,是在全面继承MRP和闭环MRP基础上,把企业宏观决策的经营规划、销售/分销、采购、制造、财务、成本、模拟功能和适应国际化业务需要的多语言、多币制、多税务以及计算机辅助设计(CAD)技术接口等功能纳入,形成的一个全面生产管理集成化系统。
ERP是Enterprise Resource Planning(企业资源计划)的简称,它是当今最先进的一种企业管理模式,在体现先进企业管理理论的同时,也提供了企业信息化集成的最佳解决方案它把企业的物流、资金流、信息流统一起来进行管理,以求最大限度地利用企业现有资源,实现企业经济效益的最大化。
MRPⅡ是以MRP为核心,覆盖企业生产活动所有领域、有效利用资源的生产管理思想和计算机管理系统。
它解决了企业物料供需信息集成,但是还没有说明企业的经营效益。
MRP Ⅱ同MRP的主要区别就是它运用管理会计的概念,用货币形式说明了执行企业“物料计划”带来的效益,实现物料信息同资金信息集成。
衡量企业经营效益首先要计算产品成本,产品成本的实际发生过程,还要以2、ERP的核心管理思想?ERP的核心管理思想是供需链管理。
生产计划与生产管理控制流程指南

生产计划与生产管理控制流程指南第1章生产计划概述 (3)1.1 生产计划的定义与作用 (4)1.2 生产计划的类型与编制方法 (4)第2章生产能力规划 (5)2.1 生产能力的概念与计算 (5)2.1.1 生产能力的定义 (5)2.1.2 生产能力的计算 (5)2.2 生产能力分析与提升策略 (5)2.2.1 生产能力分析 (5)2.2.2 生产能力提升策略 (5)2.3 生产能力规划的步骤与方法 (6)2.3.1 生产能力规划的步骤 (6)2.3.2 生产能力规划的方法 (6)第3章生产任务分解与订单管理 (6)3.1 生产任务的分解与分配 (6)3.1.1 任务分解原则 (6)3.1.2 任务分配方法 (7)3.2 订单接收与评审 (7)3.2.1 订单接收 (7)3.2.2 订单评审 (7)3.3 订单优先级设定与排产 (7)3.3.1 订单优先级设定原则 (7)3.3.2 排产策略 (7)第4章物料需求计划 (7)4.1 物料需求计划的基本原理 (7)4.1.1 基于订单驱动 (8)4.1.2 基于需求预测 (8)4.1.3 动态调整 (8)4.1.4 精确计算 (8)4.2 物料清单(BOM)的构建与应用 (8)4.2.1 物料清单的构建 (8)4.2.2 物料清单的应用 (8)4.3 物料需求计划的编制与优化 (8)4.3.1 物料需求计划的编制 (9)4.3.2 物料需求计划的优化 (9)第5章生产进度控制 (9)5.1 生产进度监控与调整 (9)5.1.1 定义生产进度监控目标 (9)5.1.2 建立生产进度监控体系 (9)5.1.3 生产进度调整策略 (9)5.2 生产进度异常处理 (9)5.2.2 异常原因分析 (10)5.2.3 异常处理措施 (10)5.3 生产进度报告与分析 (10)5.3.1 生产进度报告编制 (10)5.3.2 生产进度分析 (10)5.3.3 生产进度报告的提交与反馈 (10)第6章质量管理 (10)6.1 质量管理体系与质量控制 (10)6.1.1 质量管理体系概述 (10)6.1.2 质量控制原则 (10)6.1.3 质量控制流程 (10)6.2 质量计划与检验流程 (11)6.2.1 质量计划制定 (11)6.2.2 检验流程设计 (11)6.2.3 检验实施与记录 (11)6.3 质量问题分析与改进 (11)6.3.1 质量问题识别 (11)6.3.2 质量问题分析 (11)6.3.3 改进措施制定与实施 (11)6.3.4 持续改进 (11)第7章设备管理 (12)7.1 设备维护与保养策略 (12)7.1.1 设备维护保养的重要性 (12)7.1.2 设备维护保养策略制定 (12)7.1.3 设备维护保养实施 (12)7.2 设备故障分析与预防 (12)7.2.1 设备故障原因分析 (12)7.2.2 设备故障预防措施 (12)7.3 设备效率(OEE)提升 (12)7.3.1 设备效率(OEE)概述 (12)7.3.2 提升设备效率的方法 (13)第8章人员管理 (13)8.1 人员配置与培训 (13)8.1.1 人员配置 (13)8.1.2 培训 (13)8.2 人员绩效评估与激励 (14)8.2.1 绩效评估 (14)8.2.2 激励 (14)8.3 班组管理与团队建设 (14)8.3.1 班组管理 (14)8.3.2 团队建设 (15)第9章成本控制 (15)9.1 生产成本构成与核算 (15)9.1.2 直接材料成本 (15)9.1.3 直接人工成本 (15)9.1.4 制造费用 (15)9.1.5 成本核算方法 (15)9.2 成本控制策略与方法 (16)9.2.1 成本控制策略 (16)9.2.2 预算控制 (16)9.2.3 成本分析 (16)9.2.4 绩效考核 (16)9.3 价值工程与成本优化 (16)9.3.1 价值工程概述 (16)9.3.2 价值工程方法 (16)9.3.3 成本优化策略 (16)9.3.4 成本优化案例分析 (16)第10章生产现场管理 (16)10.1 生产现场环境与布局优化 (17)10.1.1 环境优化原则 (17)10.1.2 布局设计原则 (17)10.1.3 生产现场环境优化实施 (17)10.1.4 生产现场布局优化实施 (17)10.1.5 作业流程与布局的协同优化 (17)10.2 生产现场5S管理 (17)10.2.1 5S理论基础 (17)10.2.2 5S实施步骤 (17)10.2.3 整理(Seiri)实施要领 (17)10.2.4 整顿(Seiton)实施要领 (17)10.2.5 清扫(Seiso)实施要领 (17)10.2.6 清洁(Seiketsu)实施要领 (17)10.2.7 素养(Shitsuke)实施要领 (17)10.3 生产现场安全与环保管理 (17)10.3.1 安全管理基本原则 (17)10.3.2 安全管理制度与措施 (17)10.3.3 安全生产教育与培训 (17)10.3.4 安全的预防与处理 (17)10.3.5 环保管理基本原则 (17)10.3.6 环保法规与标准遵循 (17)10.3.7 生产过程环保措施实施 (17)10.3.8 节能减排与资源循环利用 (17)第1章生产计划概述1.1 生产计划的定义与作用生产计划是企业生产管理的重要组成部分,是对生产活动进行科学、合理安排的一种方法。
- 1、下载文档前请自行甄别文档内容的完整性,平台不提供额外的编辑、内容补充、找答案等附加服务。
- 2、"仅部分预览"的文档,不可在线预览部分如存在完整性等问题,可反馈申请退款(可完整预览的文档不适用该条件!)。
- 3、如文档侵犯您的权益,请联系客服反馈,我们会尽快为您处理(人工客服工作时间:9:00-18:30)。
计划 投入 量
10 10 10 10 10 10 10 10 10 10
第四节 MRP计算过程
产品A的BOM结构如下图: A
ERP原理与应用
B(2)
C(1)
MRP件B和C的资料汇总如下表
物料C的独立需求
12345 67 独立 5 5 5 5 5 5 5
需求
12 3 4 5 6 7
B计划到货
40
C计划到货
采购订单 采购什么? 采购多少? 何时采购?
第三节 MRP工作原理
ERP原理与应用
二、MRP的生成与调整方式
再生式MRP:MRP生成后会对库存信息重新 计算,并覆盖原来的MRP数据,生成全新的 MRP。现行的ERP系统多采用此方式。
净改变式MRP:当MPS生成MRP的条件发生 变化时,需要相应的改变MRP的相关数据。 这种计算方法较复杂,生成时间较长。
第一节 MRP的定义与作用
二、物料需求计划的作用
❖ 物料需求计划主要解决的问题
ERP原理与应用
处理 MRP
需求 相关/独立
依据
MPS、BOM、 库存
对象 物料
指标
计划期
优先级
品种/数量 小时/天/周
时间
目的是在准确的时间、准确的地点、得到准确的物料,即在“需要的时 候得到需要数量的物料”。
第一节 MRP的定义与作用
用库存、计划量等。只保留该BOM中由X引起的对A的总需求量。在展 开到第2层时,将X对A的需求及C对A的需求合并后,计算A的计划量 等,并且需求的优先级以需求沈 时航 经间济为与 管优理先学。院
第三节 MRP工作原理
一、MRP运算的基本原理
➢ 由最终产品推算出 相关物料的需求量 和需求时间。
油墨 芯头
投入量和投入时间 计划产出量=计划投入量×损耗系数 计划产出时间=计划投入时间+提前期
4、利用计划产出量计算同一周期内更低一层相关项目 的毛需求量,进入下一个循环。
第四节 MRP计算过程
ERP原理与应用
三、MRP计算规则
❖ 根据主生产计划,逐层按物料清单展开并进行MRP 计算,直至所有产品的最低一层物料全部展开计算 完为止。
ERP原理与应用
4.计算MRP的计划投入计算步骤
❖ 计算预计可用库存 ❖ 计算净需求 ❖ 计算计划产出 ❖ 计算预计可用库存 ❖ 计算计划投入(考虑批量及产出率、废品
率)
第四节 MRP计算过程
5.确定下层BOM的毛需求
ERP原理与应用
根据上层BOM的计
划投入,确定下层 BOM的毛需求
第四节 MRP计算过程
30
库存现有
提前期
批量
B
65
2期
40
C
30
3期
30
ERP原理与应用
8 9 10 5 55
8 9 10
安全库存 0 0
ERP原理与应用
MRP件:B
类别
时 段
1
2
3
4
5
6
7
8
9 10
毛需求量 GR
计划接收量 SR 可用库存 POH 预计可用库存 PAB 净需求量 NR 计划产出量PORC 计划投入量 POR
物料需求计划
主要内容
1
MRP的定义与作用
2
物料清单
3
MRP工作原理
4
MRP计算过程
ERP原理与应用
第一节 MRP的定义与作用
ERP原理与应用
MRP是一种既要降低库存,又要不出现物料短缺的 计划方法。
保证生产----满足市场需求 控制库存----降低成本
MRP不仅说明供需之间品种和数量的关系,更重要 的是说明了供需之间的时间关系;不仅说明需用时间, 还要根据提前期说明下达计划的时间。
个
20300
镜片
2
片
20099
螺钉
2
个
ERP原理与应用
层次:0 层次
1 2 2 2 2 1 1
第二节 物料清单
ERP原理与应用
二、低层码(Low-Level Code,LLC)
1、低层码概念
❖ 物料的低层码(LLC)是系统分配给物料清单上的每 个物品一个从0至N的数字码。在产品结构中,最上 层的层级码为0,下一层的部件的层级码则为1,依 此类推。
❖ 物料清单表明了产品的组件、子件、零部件和原材 料之间的结构关系,包括每个组装件所需要的各个 下属部件的数量。
❖ 每种型号的产品都有自己唯一的物料清单,它决定 了构成一个产品所需的全部零部件及其装配关系。
第二节 物料清单
产品结构树
眼镜 LT=1
ERP原理与应用
0层
镜框(1) LT=2
镜片(2)
螺钉(2)
毛需求量 GR
5
计划接收量 SR
5
预计可用库存 PAB
三、MRP计算规则
❖ 独立需求直接记入毛需求量。 ❖ 安全库存直接记入毛需求量。 ❖ 同一物料在同一时段的毛需求量相加汇总。 ❖ 废品率和损耗率用批量调节。 ❖ MRP运算使用计划提前期,包括固定提前期、变
动提前期。
第四节 MRP计算过程
ERP原理与应用
例题1:产品A的MPS如下表所示:
1 2 3 4 5 6 7 8 9 10
第四节 MRP计算过程
2.确定主生产计划MPS
ERP原理与应用
第四节 MRP计算过程
3.确定MRP的毛需求(1层)
ERP原理与应用
根据MPS的计划投入确定第1层BOM的毛需求
第四节 MRP计算过程
4.计算MRP的计划投入(1层)
ERP原理与应用
得到第1层BOM的计划投入
第四节 MRP计算过程
❖ 毛需求量=上层物料计划投入量 × 物料单位所需数 量(BOM)
❖ 同一物料在不同产品结构中或在同一产品的不同层 次。利用低层码,顺序展开到最低一层后再进行 MRP计算。
❖ 低层码:指某种物料在该种物料所属的全部物料清 单中所处的最低层数,用0至n的数字表示。
第四节 MRP计算过程
ERP原理与应用
➢ 确定净需求量,如果在某个时间段上的预计库存 量小于零,则产生净需求量
净需求=本时段毛需求-前一时段末的可用库存量-本时段计 划接收量+安全库存量
第四节 MRP计算过程
ERP原理与应用
二、MRP计算步骤
3、生产计划产出量和产出时间 ➢ 使用批量规则,生成计划产出量和产出时间 ➢ 考虑损耗系数和提前期,下达订单计划,即计划
ERP原理与应用
MRP和订货点法的区别
订货 点法
MRP
消耗 依据 相关需求 库存
均衡 不均衡
历史 资料
产品结 构展开
不考虑 考虑
有余 减少
供给 优先级 定时 不考虑 需要时 考虑
第一节 MRP的定义与作用
ERP原理与应用
三、物料需求计划与其它模块之间的关系
❖MRP是ERP系统的核心模块之一
制造标准
结束
ERP原理与应用 NO
第四节 MRP计算过程
ERP原理与应用
二、MRP计算步骤
1、计算毛需求量
项目毛需求量=项目独立需求+父项的相关需求 父项的相关需求=父项的计划订单数量×项目用量因子
2.计算净需求量 ➢ 计算各个时间段上的预计可用库存量
预计可用库存=前一时段末的可用库存量 + 本时段计划接受量 - 本时段毛需求量 + 计划产出量
1层
LT=2
LT=1
镜架(1)
镜腿(2)
鼻托(2)
螺钉(4)
LT=1
LT=1
LT=1
LT=1
2层
眼镜的产品结构树
第二节 物料清单
一副眼镜的BOM
产品物料号:20000 物料号 物料名称
产品名称:眼镜
数量
计量单位
20100
镜框
1
副
20110
镜架
1
个
20120
镜腿
2
支
20130
鼻托
2
个
20099
螺钉
4
时 段
1
2
3
4
5
6
7
8
9 10
15 15 15 15 15 15 15 15 15 15
30
30 15 0 15 0 -15 0 -15 0 -15 0 30 15 0 15 0 15 0 15 0 15 0
15
15
15
30
30
30
30
30
30
第四节 MRP计算过程
例题2:低层码 1.确定BOM
ERP原理与应用
笔芯
➢ 根据物料的提前期 确定投产或订货时 间。
笔芯杠 笔帽
笔筒
ERP原理与应用
圆珠笔
第三节 MRP工作原理
一、MRP运算的基本原理
生产什么?
主生产计划 MPS
需要什么? 产品结构 (BOM)
物料需求计划 MRP
有什么? 库存信息
ERP原理与应用
生产订单
生产什么? 生产多少? 何时生产?
MRP工作原理
计划的任何调整均要符合MRP安全性的要求
第四节 MRP计算过程
一、MRP计算方法
开始
订单、预测、主生 产计划、系统设置
毛需求计算
已投入的计划
NO
净需求大于0
?
YES
计划产出量计算
提前期、成品率
计划接收量计算
现可用库存量、安 全库存量
预计可用库存计算 净需求量计算
计计划划投入入量量计计算算
完成?