精益生产示范线
2024年精益生产示范区经验总结样本(2篇)

2024年精益生产示范区经验总结样本1. 引言精益生产是一种高效、灵活和高质量的生产管理方法,旨在通过降低浪费、提高生产效率和质量,实现企业的持续改进和竞争优势。
____年,我国启动了精益生产示范区建设,以推动制造业的转型升级和提高全国制造业的竞争力。
作为2024年精益生产示范区建设的总结报告,本文将总结经验与教训,为未来精益生产示范区的发展提出建议。
2. 建设过程2.1 建设目标制定精益生产示范区的建设应明确目标和指标,例如提高生产效率10%、降低人力成本20%等。
通过设定具体目标,可以使建设过程具有针对性和可衡量性,并为后续改进提供方向。
2.2 基础设施建设基础设施的建设是精益生产示范区的基础,包括生产线的设计和布局、物流和仓储设施的优化、信息系统的建设等。
在建设过程中,应充分考虑生产过程中的各种交互影响和支持,确保基础设施的有效和高效运行。
2.3 人员培训和管理精益生产需要具备一定的技能和思维方式,因此,在示范区的建设过程中,人员培训和管理至关重要。
应通过培训和激励机制激发员工的参与和积极性,同时建立适当的绩效评估和奖励机制,以推动精益生产理念在示范区的落地和传播。
2.4 数据采集和分析精益生产强调数据驱动和事实决策,因此,在示范区建设过程中,应建立完善的数据采集和分析系统。
通过采集和分析生产过程中的关键数据和指标,可以及时发现问题和瓶颈,并进行适当的调整和改进。
3. 经验与教训3.1 成功经验3.1.1 目标导向明确的目标和指标可以激发示范区企业的动力和创新意识,推动企业在精益生产实践中取得实质性的改进和进步。
3.1.2 领导支持优秀的领导是精益生产示范区建设的重要保障,他们应能够提供足够的资源和支持,同时发挥良好的指导和激励作用,以推动整个示范区的发展。
3.1.3 团队合作建设精益生产示范区需要多个企业和部门的协作与配合。
在示范区建设过程中,促进各方之间的良好沟通和合作,形成有效的团队合作机制,对于示范区的成功发展至关重要。
推行精益生产的顺序与步骤(一)
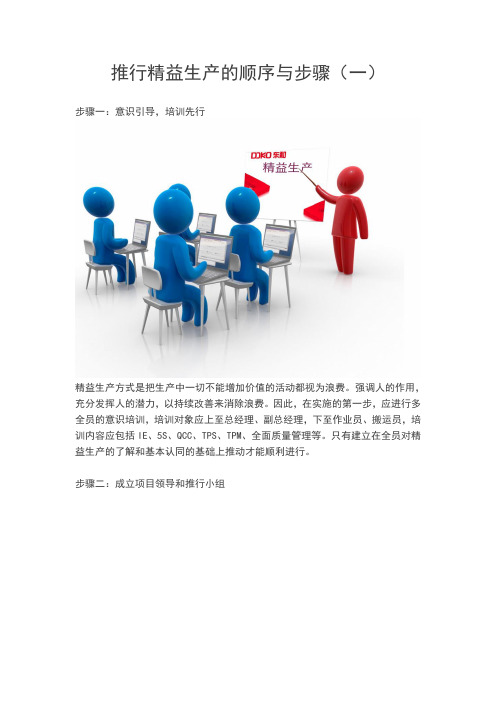
推行精益生产的顺序与步骤(一)步骤一:意识引导,培训先行精益生产方式是把生产中一切不能增加价值的活动都视为浪费。
强调人的作用,充分发挥人的潜力,以持续改善来消除浪费。
因此,在实施的第一步,应进行多全员的意识培训,培训对象应上至总经理、副总经理,下至作业员、搬运员,培训内容应包括IE、5S、QCC、TPS、TPM、全面质量管理等。
只有建立在全员对精益生产的了解和基本认同的基础上推动才能顺利进行。
步骤二:成立项目领导和推行小组企业在实施精益生产的时候,应建立一个叫"精益生产委员会"的组织。
一般来说,总经理应是精益组织的负责人,组织应包括生产管理部门、制造部门、生产技术部门、品质部门的等相关部门的主管,要确立负责人的改善职责。
实施精益生产应做好计划,包括系统的实施计划、年度计划和月度计划。
计划应该包括项目、分析、责任人、完成时间等,并按照PDCA的方式进行记录。
步骤三:示范线改善,体现成果,建立改善样板区域精益生产的实施开始3到6个月,当5s取得初步成果的时候,可以选择一条生产线进行示范改善。
有的企业把示范线改善,叫做"对象线改善"或"小范围改善"。
改善的内容要尽可能的运用精益的工具,选择示范线进行改善的时候,应该选择流水作业的线,要认真确认好改善前的状态,包括:成品及使用零件清单、现状平面布置Layout图、现状物与情报流程图、现行各工程C/T时间调查、线边库存状况调查、送货频率及数量等。
改善应该循序渐进,并落实每个事情的责任人,还应注意多运用头脑风暴的方法、集思广益。
改善的信息应及时的向改善小组内的成员发布,确保同步进行,合作顺畅。
改善小组的负责人,要每日对改善的进度进行确认。
改善要即使做好成果统计和成果发布,让全员感受到精益生产的好处。
步骤四:现场改善,5S开始5S是改善现场的基础。
实施精益生产,先从现场环境改善入手,通过整理,清理掉现场的一些不要品,减少空间的占用;通过整顿,让现场的物品按秩序摆放,方便拿取;通过清扫,让现场变的干净,设备得到及时的保养;通过持续的检查、整改,让员工养成维持的习惯,并及时的更新各种表格,从而保持现场良好的环境,提高生产的效率和产品的质量。
精益示范区(线)建设步骤一:成立精益推进组织

精益示范区(线)建设步骤一:成立精益推进组织
在开展精益示范区(线)的建设过程中,要充分应用精益生产的思想、方法和工具,充分协调好企业内部各方面资源,按照精益示范区(线)建设的相关要求,制定详细的精益示范区(线)推进方案和实施计划,带动全员共同按照实施计划有序开展精益示范区(线)的各项建设工作。
成立精益生产推进组织
各子公司要成立精益示范区(线)的三级精益推进组织:领导组、推进组和实施组,明确各组织人员的管理职责和分工。
(1)领导组由公司领导和各职能部室领导组成,制定总体建设计划和目标,领导推进组和实施组开展工作。
(2)推进组由精益办带领各职能部门相关业务人员共同成立,负责根据领导组的要求制定具体的推进实施计划,并在实施过程中跟踪、协助、评价。
(3)实施组由精益示范区(线)创建单位成立,主要成员由创建单位的七大任务职能人员组成,按照推进组制定的推进计划,共同开展计划实施工作。
精益生产-精益示范线建立
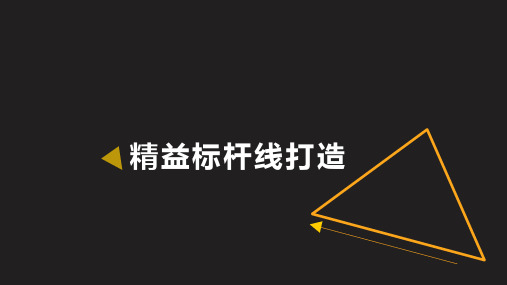
精益标 杆线
5 线上及时品管 6 标准化作业 7 7S和目视化管理 8 价值流管理
3 标杆线改善路径
3 标杆线改善路径
3 标杆线改善路径
3 标杆线改善路径
3 标杆线改善路径
3 标杆线改善路径
3 标杆线改善路径
3 标杆线改善路径
一周一标杆 榜样的力量
“
一
周
一周的时间
产品或品种
2 PQ/PR分析
2 PQ/PR分析
2 PQ/PR分析
2 PQ/PR分析
工序与工序 1-2 2-3 3-4 4-5 5-6
距离(m) 1.2 42.3 1 18.3 14.2
工序与工序 6-7 7-8 8-9
距离(m) 46.2 11.5 37.1
共170.8米
2 PQ/PR分析
精益标杆线打造
精益是什么?
到底该如何定义?
精益 不是回魂丹
精益 是保健药
近 进 走 精益 走 精益
V=F/C
老板满意
量化效果
耗费时间
精益=
(客户需求+诊断) 指标(率)
CONTENTS
01 什么是标杆
02 PQ/PR分析
03 04 标杆线改善路径
案例分享
01
什么是标杆
1 什么是标杆
1.启动大会召开
1.样板区负责人召开日例会,部署当日计划 (早上9:00,下午16:00,每次30分钟) 2. 样板区巡回指导,如出现进度不良召集临 时紧急会议
1. 先由整理开始清除不要物 2. 样板区地面、周边公共区域、设备大清扫 3. 调整现场布局,整体区域规划、画线,物 料进出位置三定
周 五
企业建立精益生产示范区(线)的目的
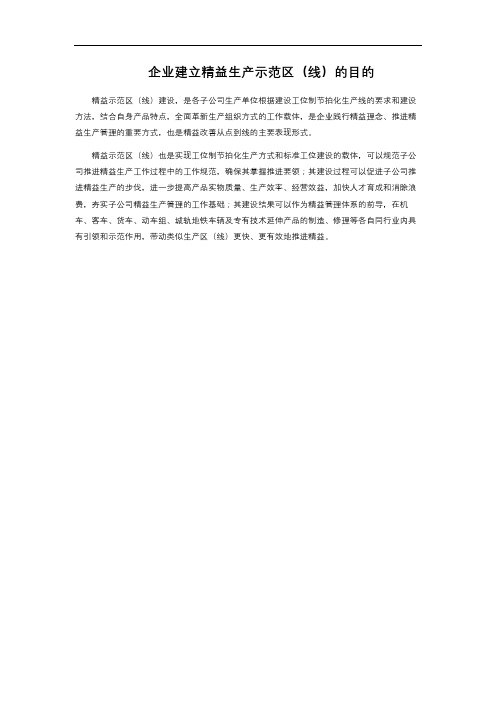
企业建立精益生产示范区(线)的目的
精益示范区(线)建设,是各子公司生产单位根据建设工位制节拍化生产线的要求和建设方法,结合自身产品特点,全面革新生产组织方式的工作载体,是企业践行精益理念、推进精益生产管理的重要方式,也是精益改善从点到线的主要表现形式。
精益示范区(线)也是实现工位制节拍化生产方式和标准工位建设的载体,可以规范子公司推进精益生产工作过程中的工作规范,确保其掌握推进要领;其建设过程可以促进子公司推进精益生产的步伐,进一步提高产品实物质量、生产效率、经营效益,加快人才育成和消除浪费,夯实子公司精益生产管理的工作基础;其建设结果可以作为精益管理体系的前导,在机车、客车、货车、动车组、城轨地铁车辆及专有技术延伸产品的制造、修理等各自同行业内具有引领和示范作用,带动类似生产区(线)更快、更有效地推进精益。
精益示范线项目计划与改善报告

精益示范线项目计划与改善报告1. 项目简介本项目旨在利用精益生产方法,改善公司生产线的效率和质量,减少浪费,提高客户满意度。
1.1 项目背景公司生产线的效率和质量一直是公司的瓶颈,同时也限制了公司的发展。
为了提高公司的竞争力,我们决定采用精益生产方法,对生产线进行改善。
通过优化生产线流程,减少浪费,提高质量和效率,最终达到增加产能和提高客户满意度的目标。
1.2 项目目标本项目通过引入精益生产方法,旨在实现以下目标:•减少生产线上的浪费:通过精益方法,减少生产线上的浪费,包括时间、人力、材料和能源等方面的浪费,提高生产线的效率。
•提高生产线的质量:通过精益方法,改善生产线的流程和质量控制系统,减少次品率,提高产品质量和客户满意度。
•提高公司的竞争力:通过提高生产线的效率和质量,提高公司产能并降低成本,增强公司的竞争力。
2. 项目计划2.1 项目组织为了保证项目的顺利推进和实现项目目标,我们组成了一个专门的项目组,包括以下人员:•项目负责人:负责项目的整体规划、组织、协调和监督。
•精益专家:负责精益方法的引入和指导。
•生产线主管:负责生产线的日常管理和生产绩效的改善。
•质量控制主管:负责生产线的质量控制和质量指标的改善。
•信息技术主管:负责建立和维护信息系统。
2.2 项目流程本项目分为以下几个主要流程:1.项目启动:成立项目组,确定项目计划和目标,建立项目管理机制。
2.流程分析:通过对生产流程的分析,确定当前存在的问题和改进机会。
3.改进方案制定:制定改进方案,并进行评估,确定最终方案。
4.方案实施:实施改进方案,并进行效果评估。
5.持续改进:持续监测并改进生产线的流程和效果,保证项目的持续改进。
2.3 项目计划表步骤时间负责人备注项目启动第1周项目负责人成立项目组,确定项目计划和目标,建立项目管理机制。
流程分析第2-3周生产线主管通过对生产流程的分析,确定当前存在的问题和改进机会。
改进方案制定第4-5周精益专家制定改进方案,并进行评估,确定最终方案。
精益生产:减少七大浪费的综合途径
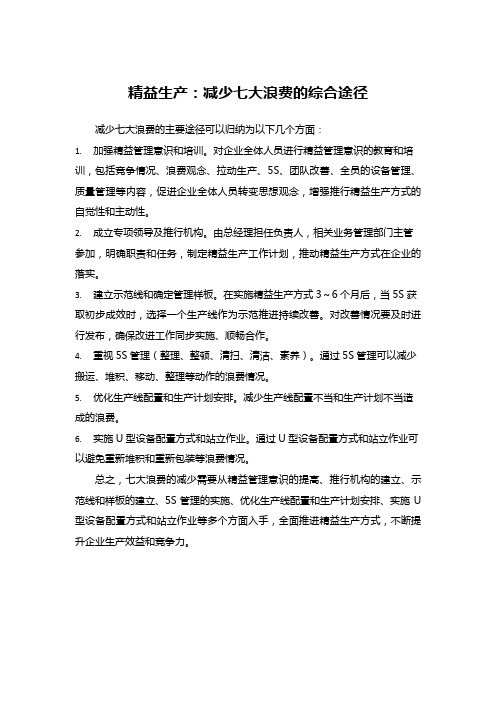
精益生产:减少七大浪费的综合途径减少七大浪费的主要途径可以归纳为以下几个方面:
1.加强精益管理意识和培训。
对企业全体人员进行精益管理意识的教育和培训,包括竞争情况、浪费观念、拉动生产、5S、团队改善、全员的设备管理、质量管理等内容,促进企业全体人员转变思想观念,增强推行精益生产方式的自觉性和主动性。
2.成立专项领导及推行机构。
由总经理担任负责人,相关业务管理部门主管参加,明确职责和任务,制定精益生产工作计划,推动精益生产方式在企业的落实。
3.建立示范线和确定管理样板。
在实施精益生产方式3~6个月后,当5S获取初步成效时,选择一个生产线作为示范推进持续改善。
对改善情况要及时进行发布,确保改进工作同步实施、顺畅合作。
4.重视5S管理(整理、整顿、清扫、清洁、素养)。
通过5S管理可以减少搬运、堆积、移动、整理等动作的浪费情况。
5.优化生产线配置和生产计划安排。
减少生产线配置不当和生产计划不当造成的浪费。
6.实施U型设备配置方式和站立作业。
通过U型设备配置方式和站立作业可以避免重新堆积和重新包装等浪费情况。
总之,七大浪费的减少需要从精益管理意识的提高、推行机构的建立、示范线和样板的建立、5S管理的实施、优化生产线配置和生产计划安排、实施U 型设备配置方式和站立作业等多个方面入手,全面推进精益生产方式,不断提升企业生产效益和竞争力。
产品精益生产示范线总结ppt课件

可编辑ppt
3
历程概述
9600KW逆变器柜精益生产线的建立还要追溯到2009年,当时该 项目也是作为项目管理模式中的经典案例在组织实施,由当时的项目经 理李跃丰先生负责.该项目正如我们之前所描述的背景一样,有诸多特性 和值得挑战的因素包含在内.经过近一年的准备和试制,终于在2009年 9月成功进行首件评审,这件事也算是联诚的一个大事件.
可编辑ppt
5
改善目标
序号
项目
改善总体工作目标
改善前状况
1 实现准时化生产 一线生产员工35人,产能25台车/月
2 产品质量提升 3 生产现场优化 4 工艺工装改进 5 成本控制
用户经常投诉,满意度低,使用满意率仅为30%
物流线路不清晰,中转项点多,中转线路长,时 间长;可视化管理模糊. 制造周期长,其中总装工序处于无工装状态, 周期为6天;供应商没有纳入实时控制,油漆周 期9天
35 6月32起7月30起
30
25
8月22起
20
15
9月10起
10
5
0 顾客质量投诉
6月15起 7月10起 8月5起 9月1起
顾客现场返工
可编辑ppt
6月 7月 8月 9月
14
四--(1)逆变器柜系列工艺工装改善的效果.
3
342
0
7月
8月
9月
自检(单位:h) 交检(单位:h) 验收(单位:h)
可编辑ppt
12
三--(2)产品的内部质量问题得到了全面有效的控制,一次交检合格率 达到了98%,满足用户要求。
100%
98%
80%
60%
65%
精益生产示范线建设的工具、方法和创新点

精益生产示范线建设的工具、方法和创新点
1.以基本工具应用的常态化夯实公司基础管理
(1)5S:坚持持续推进5S管理,每月进行5S点检、评价。
(2)TPM:开展TPM活动,转变观念,提升自主保全意识和能力,每月点检、通报。
(3)目视化:生产现场全面推进目视化管理。
(4)改善活动:每月度进行全员改善提案评奖活动。
2.以关键工具的突破应用增强企业内涵式发展
(1)在高速动车组生产线全面实施节拍化拉动式生产方式。
(2)全面实施应用作业要领书,试点开展作业组合,标准化作业。
(3)生产线应用物料配送看板,部分区域应用生产指示看板。
(4)制定年度工作方案,全员参与,持续推进。
3.以节拍化拉动式生产为主线,构建精益生产体系围绕生产现场的节拍化拉动式生产,从生产技术准备到制造交付全过程,提升异常反馈速度,拉动各职能部门服务于现场的工作,形成相关的规则和机制,建立精益生产模式。
工艺:进行工序分割,工序写实,平衡工序能力,提出瓶颈工序改善方案等。
生产:编制下达节拍生产推移计划,分厂以总装为最终用户,编制三日节拍动态计划。
物流:实施准时化,分时段配送,减少物流配送搬运等浪费。
现场:实施物料三定、期量管理、目视化管理,提升作业效率,创造良好作业环境。
供应链:引导供应商开展精益生产,对供应商进行节拍化供货需求管理。
4.运用表单管理增强员工的统计分析、发现问题能力推广拓展精益标准化工位建设,标准化工位管理以表单管理为载体,通过管理表单将班组运行标准落实到日常工作中,从安全、质量、生产、成本、人事、环境保全等7个方面对班组的日常工作进行规范。
精益示范生产线建设实施方案

乙烯分公司成品车间精益示范生产线建设实施方案乙烯分公司成品车间二〇一九年三月为落实华锦集团办联字{2019}1号文件《关于做好示范企业、示范项目及示范生产线创建工作的通知》精神,成品车间紧紧围绕狠抓安全管理、狠抓设备单元安全责任制、提高工作标准、提高工作效率、持续抓好全价值链体系化精益生产五大重点任务,依据《中国兵器工业集团有限公司精益生产线建设评价规范(2018修订版)》,以“基础再建再提高、动能再造在提升、优势再创再提速”为总领,用创业的理念、创业的精神、创业的标准,全力推进精益示范生产线的创建工作。
一、成品车间基本概况成品车间承担着30万吨/年聚乙烯装置、25万吨/年聚丙烯一装置、6万吨/年聚丙烯二装置、4万吨/年聚苯装置的产品包装、码垛、储存、付货。
车间共有员工141人,其中女员工41人,男员工100人。
包装、叉车、付货三个生产岗位,其中包装岗位有8条包装生产线,叉车岗共有30台叉车;聚合物仓库建筑面积18000㎡,最大的存储的能力8000t。
二、精益管理情况介绍成品车间认真贯彻集团公司部署要求,将精益管理的思想理念逐步融入生产管理的各个环节,全员参与、持续改善,提升管理水平,通过制定方案开展好示范活动,将全体职工凝聚起来,负起责任,在全价值链的各环节消除浪费,起到示范引领作用,在2012年,付货岗被评为辽宁省巾帼文明岗。
1、精益管理目标引领,包装现场的精益改善将公司关键绩效指标改善作为成品车间精益管理工作出发点和落脚点,构建成品车间精益关键绩效指标考评体系,该体系包括生产运营、质量与计量、人力资源、安全环境、员工士气等指标并以此作为确立改善课题、实施改善计划、评价改善收益的重要依据,逐级分解,车间安全、生产、设备专业分级分类管控。
以质量、效率、成本、安全等方面相关目标要求为统领,强化通过过程改善,支撑经营指标的达成。
(1)以客户需求为牵引、提高产品的外观质量,提升客户满意度。
因每日外付货量较大约为1800吨,而付货过程需要用3吨的柴油叉车,每次可叉运2吨,往来叉运产品需要1800次,每日工作时间需要至少13小时,长时间,高负荷的作业,柴油叉车产生l 大量的尾气,而叉车尾气具有一定的粘性,易附着在产品的外包装表面,污染外包装。
精益示范线项目实施方案

精益示范线项目实施方案一、项目背景精益示范线(Lean Production Line)是指通过优化生产过程,实现生产效率的最大化,减少浪费,提高产品质量的一种管理方法。
在当前市场竞争日益激烈的背景下,企业需要提升自身生产效率,降低生产成本,以提高竞争力。
本项目旨在引入精益示范线的理念和方法,实施生产过程优化,提高企业的生产效率和产品质量。
二、项目目标1. 提升生产效率:通过优化生产流程,减少不必要的浪费和时间,提高生产效率,降低单位产品成本。
2. 提高产品质量:通过精细化管理和过程标准化,减少产品缺陷率,提高产品质量。
3. 降低生产成本:通过优化生产过程,减少不必要的资源浪费,降低生产成本。
4. 增强企业竞争力:通过提高生产效率和产品质量,降低生产成本,提高企业竞争力。
三、项目步骤1. 现状分析与评估:对企业现有的生产流程进行全面分析和评估,明确存在的问题和改进空间。
2. 制定优化方案:基于现状分析的结果,制定符合企业实际情况的精益示范线优化方案,明确实施的目标和重点。
3. 培训与指导:对生产线相关人员进行精益生产理念和方法的培训,提高员工的意识和技能。
4. 流程改造与优化:根据优化方案,对生产流程进行改造和优化,包括生产设备布局优化、工艺流程优化、物料配送优化等。
5. 实施监控与改进:建立监控机制,对优化后的生产线进行监控和评估,及时发现问题并进行改进。
6. 成果展示与总结:对优化后的生产线进行成果展示,总结项目经验和教训,为其他生产线优化提供参考。
四、项目措施1. 设立项目团队:成立项目团队,由专业人员负责项目的组织和管理,确保项目顺利进行。
2. 培训计划:制定培训计划,对生产线相关人员进行精益生产理念和方法的培训,提高员工的意识和技能。
3. 设备改造和优化:根据优化方案,对生产线的设备进行改造和优化,提高设备的效能和可靠性。
4. 工艺流程优化:对生产过程中的工艺流程进行优化,减少不必要的环节和浪费。
精益示范线上的精益班——中国兵器北方惠安公司科研一所氧化剂二班速写

34中国军转民大学、河南机械研究所、610所等单位加强技术合作,借脑发展,着力打造国防及民用系统高端铜合金产品生产研发基地,打造铜型材生产“强人”企业。
先后成功开发了静触头、缺角静触头、大截面L排等异型排和静触头连续挤压开坯、一次拉拔成型新工艺;利用新建的铜排(管棒)折弯生产线的数控冲剪机、折弯机,实现了折弯排、3D折弯管、3D折弯杆的供货。
铜材公司积极组织铬套精锻毛坯、内圆外D形管,以及折杆、折弯、异型管材等新产品的开发工作。
结晶器公司在强化与大型钢铁企业的战略合作,巩固、开发结晶器产品市场的同时,积极与中冶京城、赛迪、南方等合作,开发研制成功钻石型结晶器。
新产品的开发延伸了铜加工产业链,优化了公司民品结构,拓宽了发展空间,扩大了产销规模和市场份额,进一步稳固了以军为本、民品兴业的战略架构。
管理体现正能量为提高产品市场竞争力,从优化工艺、完善制度、精简流程、安全生产等方面入手,不断提升基础管理水平,强化制约公司科学发展基础管理相对薄弱的短板,各项管理进一步贴近市场和现场,认真做好生产的组织工作,合理调整环节,科学安排班次,达到快速反映以满足市场需求的目标。
重点抓好长线产品的刀排、D型管的过程控制,特别是重点抓好挤压机开坯,提高材料的利用率。
加强与销售部门的信息沟通。
紧紧围绕市场订单合同开展品种、数量、质量、交货期的落实工作,科学合理的制订生产计划,合理调配人员并严格执行,生产效率进一步提高。
建立起市场快速反应机制,面对时间短、要求高、任务重的产品,公司立刻精心组织,技术人员通过技术方案比较、挑选,从设计、工具工装的采购、试生产、成品,到迅速交付,快速的反应机制,支持了市场的进一步开发。
建立了生产计划评审机制,每当接到新的生产计划后,生产单位立即组织技术、机电、调度、质量、技安,以及检验等人员对生产计划进行评审,对技术要求高、加工难度大的产品提前做好应急预案,把客户的要求和技术质量难点提前做好生产准备。
中国北车精益生产示范线工作汇报

Page 10
第
(二
部分
具体做
精益生产示范线建设
方案评审 建线实施 资金保障 激励到位 学习借鉴
Page 11
第
(二
部分
具体做
1. 方案评审
精益生产示范线建设
方案设计
内部评审
公司精益办 组织评审
方案确认
方案核审
方案完善
Page 12
第
(二
部分
具体做
2. 建线实施
精益生产示范线建设
1 2 3 4
2. 内部互相学习
在公司内部,我们还不定期组织各精益示范线建线单位 相互观摩学习,互通有无,相互促进,共同提高
Page 16
第
(三
部分
精益生产示范线建设
该条示范线是成都公司最 早设计、建设的精益示范 线,到8月底,已基本建 成。与建线前相比,变化 主要体现在:
构架翻 转台
设8个 工位
精益示范线建设情
Page 21
第
(三
部分
精益生产示范线建设
精益示范线建设情
4条总组装精益示范线按计划推进
电机总组装精益线
8月份完成了16个品 种、315台电机的生产 任务,并将以往每月下 旬完成当月80%生产任 务的顽疾优化为上中下 旬分别完成“2:3: 5”。其中:物流的准时 供应能力得到了较大提 升
Page 22
第
部分
后续计划
(一
学习贯彻 277 号文件精
组织各建线单位深入学习贯彻该文件精神、深刻领会并掌握精益生产示范区 (线)的评价办法和评价标准,并反复对照、检查精益线方案,查漏补缺
(二
年内建成 6 条精益生产示范
精益示范区(线)建设步骤三:论证方案、明确责任、完善制度
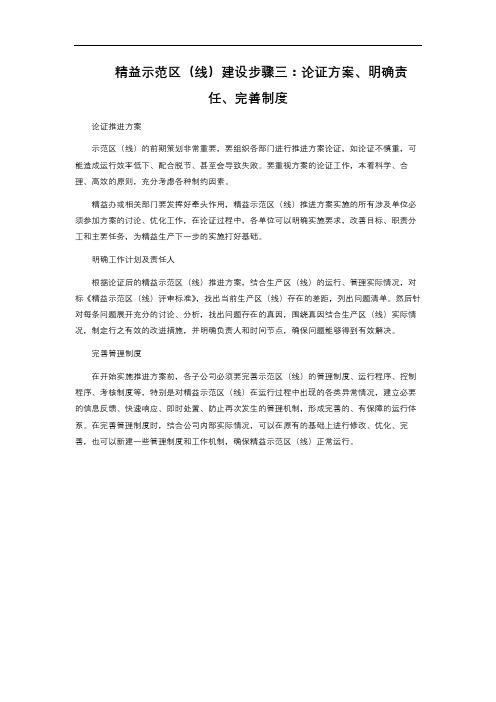
精益示范区(线)建设步骤三:论证方案、明确责
任、完善制度
论证推进方案
示范区(线)的前期策划非常重要,要组织各部门进行推进方案论证,如论证不慎重,可能造成运行效率低下、配合脱节、甚至会导致失败。
要重视方案的论证工作,本着科学、合理、高效的原则,充分考虑各种制约因素。
精益办或相关部门要发挥好牵头作用,精益示范区(线)推进方案实施的所有涉及单位必须参加方案的讨论、优化工作,在论证过程中,各单位可以明确实施要求,改善目标、职责分工和主要任务,为精益生产下一步的实施打好基础。
明确工作计划及责任人
根据论证后的精益示范区(线)推进方案,结合生产区(线)的运行、管理实际情况,对标《精益示范区(线)评审标准》,找出当前生产区(线)存在的差距,列出问题清单。
然后针对每条问题展开充分的讨论、分析,找出问题存在的真因,围绕真因结合生产区(线)实际情况,制定行之有效的改进措施,并明确负责人和时间节点,确保问题能够得到有效解决。
完善管理制度
在开始实施推进方案前,各子公司必须要完善示范区(线)的管理制度、运行程序、控制程序、考核制度等,特别是对精益示范区(线)在运行过程中出现的各类异常情况,建立必要的信息反馈、快速响应、即时处置、防止再次发生的管理机制,形成完善的、有保障的运行体系。
在完善管理制度时,结合公司内部实际情况,可以在原有的基础上进行修改、优化、完善,也可以新建一些管理制度和工作机制,确保精益示范区(线)正常运行。
精益示范区(线)建设步骤二:制定推进方案

精益示范区(线)建设步骤二:制定推进方案制定精益示范区(线)推进方案在成立精益推进组织后,推进组在领导组的指导下,编制精益示范区(线)的推进方案,要明确工作思路和推进目标,制定详细的推进计划和负责人,明确工作流程和参与推进人员职责。
推进方案一般可以分为以下几个部分。
(1)明确建设目的建设目的相当于精益示范区(线)创建工作体系的大脑,在推进方案中,要首先明确建设目的,统一全员思想,才能更好、更有思路、更有目标、更有效地开展各项推进工作(2)明确工作思路工作思路是精益生产示范区(线)创建工作体系的中枢神经,清晰的工作思路可以让全员共同参与,使精益示范区(线)的建设工作事半功倍,所以必须要有明确、清晰的工作思路。
一般的精益示范区(线)建设工作思路如下:掌握生产区(线)的现状和管理要求一对标《精益示范区(线)评审标准》,找出差距一针对存在的差距制定推进目标一对目标进行分解,落实推进责任人一定期组织评审,把握推进进度一目标达成后进行标准化,未完成的工作根据实际情况继续制定推进计划,组织实施。
(3)明确建设目标清晰的目标能为精益示范区(线)创建工作指引正确的工作方向,所以必须要明确建设目标。
为保证精益示范区(线)创建工作得到有效、有序开展,要集中突破推进过程中的难点,推进组要在领导组的领导下,与实施组共同协商,针对精益示范区(线)的效率、效益、消除浪费等方面制定切实可行、可量化的、明确的改善目标值,如:a.生产效率提升10%;b.产品质量提升20%;c.设备可动率提高15%;d.人员减少2人;e.生产成本降低5%(4)明确奖惩制度结合自身情况和工作计划,针对精益示范区(线)建设过程中各层级人员对精益推进的支撑情况,制定管理办法或管理规定,明确奖惩制度,鼓励和督促各层级人员共同开展精益示范区(线)的各项推进工作。
该奖惩制度必须经过各部门会签,达成共识,并由推进组严格执行。
- 1、下载文档前请自行甄别文档内容的完整性,平台不提供额外的编辑、内容补充、找答案等附加服务。
- 2、"仅部分预览"的文档,不可在线预览部分如存在完整性等问题,可反馈申请退款(可完整预览的文档不适用该条件!)。
- 3、如文档侵犯您的权益,请联系客服反馈,我们会尽快为您处理(人工客服工作时间:9:00-18:30)。
328 342 42 34
346 243
82
55
138121.75 182 19
15 90 87
1350 131.95
10 15 20 25 30 31 33 35 40 45 50
工序号
手 作 业 自动加工 交换时间
工序生产能力
2000 1500
Ⅳ 设备布置方案
齿轮室布局依据
1#线
433
363
精益生产示范线
(齿轮室)
精益推进办公室
2009年5月22日
I. 生产线概述 II. 需求节拍和目标节拍 III. 未来工序平衡图 IV. 设备布置方案(多方案评估) V. 标准人力配置表 VI. 标准作业组合表和作业票 VII. 内部材料流转器具方案 VIII.参考附件
Ⅰ生产线概述
序号
内容
1 占地面积
小车4件, 去毛刺
25-1
工作台2件, 翻转,去毛 刺
20-2
工作台2件, 去毛刺
25-2
工作台2件
30-1
工作台2件
30-2
工作台2件,
翻转
工作台2件
平麽
31
2#线转入
小车 10件
35
小车 10件
40
成品车 20件
45
成品车 20 件
50
Ⅶ 内部材料流转器具方案
2#线
小车4件, 去毛刺
25-3
工作台2件, 翻转,去毛 刺
20-3
行吊
工作台2 件, 翻转
15-2
工作台2件,
翻转
小车 2件
行吊
行吊
行吊
15-1
10正面
10反面
ቤተ መጻሕፍቲ ባይዱ
毛坯
工作台2件, 去毛刺
25-4
转1#线
平麽
工作台2件
30-1
工作台2件
30-2
参考附件
363
10
15-1 15-2
594
391
612
20-1
25-1 30-1
平麽
31
594 20-2
346 25-3
501
30-2
2#线
433
10
363 15-1
363 15-2
448 20-3
30工序更改工艺后需重新测时
391 25-3
346 25-4
612
30-3
501
30-4
平麽
Ⅴ 标准人力配置表
5 齿轮室加工工序共11个,有6个共用工序。
Ⅱ 需求节拍和目标节拍
? 需求节拍TT=20Hr/500 =144s ? 目标节拍TT1=2OHr/450=160s
Ⅲ 未来工序平衡图
Ⅲ 齿轮室线工序能力图
工序时间分布表
500
400 间s300 时200
100
0
43.5 3
3
4
3
366 300 31 60
■理论人力1(按10序324件/天)=∑CT/TT=4242/222=19.1人 19.1*3=57.3人
■理论人力2(按10序去除换刀时间产能363件/天)=∑CT/TT=4242/198=21.4人 21.4*3=64人
■实际人员63人(不含班长、终检等共7人)
线别 1# 2# 共用 合计 备注
2 设备总数量 24 台,其中老线 15 台,新线 13 台,两线共用设备 6 台。(老线清洗机、新线水检箱未使用)
3 齿轮室人员总数70人,两条生产线,其中老线 52人,新线 49 人, 有 6个工序为共用工序,人数31人(含班长)。
4 目前齿轮室有4种产品型号,(R61557010008 、R61540010009 、 AZ150010932 、AZ150010933 ),其中常用型号R61557010008
现状
理论
方案1
方案2
方案3
?工序人力配置明细
工序代号 工序名称 10 20
人力
备注
Ⅵ 标准作业组合表和作业票
Ⅸ 齿轮室价值流图
Ⅶ 内部材料流转器具方案
1#线
行吊
毛坯
工作台2 件, 工作台2件,
行吊 小车2件
翻转
翻转
10反面
行吊
10正面
15-1 行吊 15-2
工作台2件, 翻转,去毛 刺
20-1