PFMEA-组装
PFMEA分析范例
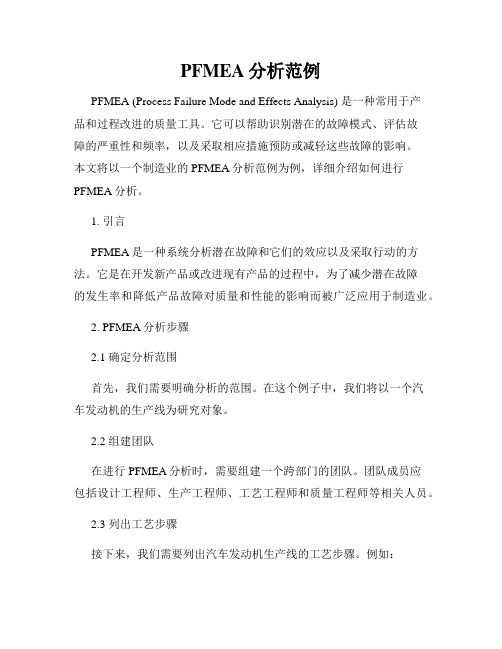
PFMEA分析范例PFMEA (Process Failure Mode and Effects Analysis) 是一种常用于产品和过程改进的质量工具。
它可以帮助识别潜在的故障模式、评估故障的严重性和频率,以及采取相应措施预防或减轻这些故障的影响。
本文将以一个制造业的PFMEA分析范例为例,详细介绍如何进行PFMEA分析。
1. 引言PFMEA是一种系统分析潜在故障和它们的效应以及采取行动的方法。
它是在开发新产品或改进现有产品的过程中,为了减少潜在故障的发生率和降低产品故障对质量和性能的影响而被广泛应用于制造业。
2. PFMEA分析步骤2.1 确定分析范围首先,我们需要明确分析的范围。
在这个例子中,我们将以一个汽车发动机的生产线为研究对象。
2.2 组建团队在进行PFMEA分析时,需要组建一个跨部门的团队。
团队成员应包括设计工程师、生产工程师、工艺工程师和质量工程师等相关人员。
2.3 列出工艺步骤接下来,我们需要列出汽车发动机生产线的工艺步骤。
例如:- 工艺步骤1:原材料采购和检验- 工艺步骤2:加工零部件- 工艺步骤3:组装零部件- 工艺步骤4:测试与质检- 工艺步骤5:包装和出厂2.4 识别潜在故障模式对于每个工艺步骤,团队成员需要一起识别潜在故障模式。
例如,在工艺步骤1中,可能存在以下潜在故障模式:- 检验不准确导致不合格原材料被误用于生产- 供应商延迟交付原材料,导致生产停滞2.5 评估故障严重性和频率在确定潜在故障模式后,团队成员需要评估每个故障的严重性和发生频率。
例如,在工艺步骤1中,检验不准确可能导致以下严重性和频率评估:- 严重性:高,因为不合格原材料可能导致发动机故障,导致安全隐患和质量问题- 频率:低,因为QC检验通常能准确发现不合格原材料2.6 识别潜在故障效应接下来,团队成员需要识别潜在故障对产品和过程的效应。
例如,在工艺步骤1中,检验不准确的潜在故障可能导致以下效应:- 效应1:生产线停滞,影响生产计划和交货时间- 效应2:不合格原材料出现在最终产品中,影响产品质量和客户满意度2.7 采取预防和纠正措施在识别潜在故障效应后,团队成员需要采取相应的预防和纠正措施来减轻故障的影响或防止故障发生。
PFMEA范本

PFMEA范本1. 引言在产品开发和制造过程中,PFMEA(Process Flure Mode and Effects Analysis)是一种常用的风险管理工具。
它旨在通过识别和评估潜在的故障模式和对整个过程和产品的影响,来减少和控制风险。
本文将介绍一个典型的PFMEA范本,以供参考和使用。
2. 范本结构本PFMEA范本共分为以下几个部分:2.1 项目信息:包括项目名称、文件编号、作者、修订日期等基本信息。
2.2 过程描述:描述被评估过程的详细步骤和流程。
2.3 评估团队:列出参与评估的团队成员和职责。
2.4 风险评估:将故障模式、故障影响、故障原因和风险等级进行评估和记录。
2.5 风险控制措施:对每个故障模式和风险级别,列出相应的控制措施和改进计划。
2.6 控制计划:制定具体的控制计划和相应的实施和监控措施。
2.7 和建议:评估结果,提出改进建议和措施。
3. 范本示例3.1 项目信息项目名称:某产品的组装过程文件编号:PFMEA-001作者:3.2 过程描述过程名称:产品组装过程步骤:(此处展示详细的产品组装过程步骤)3.3 评估团队本次PFMEA评估由以下成员组成::质量经理,负责组织和指导评估工作:工程师,负责收集和分析相关数据:操作工程师,负责过程的实际操作和观察3.4 风险评估-故障模式-故障影响-故障原因-风险等级-漏装影响产品外观和性能人为操作不慎 9 -部件损坏影响组装质量和工作进度零部件质量不过关 7 -3.5 风险控制措施对于漏装现象,加强员工培训,完善操作规程,提高操作技能。
对于部件损坏,加强供应商质量管理,建立严格的零部件检验标准。
3.6 控制计划对于漏装现象,加强操作记录和日常监控,并制定漏装预防措施。
对于部件损坏,要求供应商提供质量报告,并建立零部件质量整改机制。
3.7 和建议通过对产品组装过程的PFEMA评估,我们发现漏装和部件损坏是当前的两个主要风险。
我们推荐加强员工培训和操作规程的改进,也要求供应商提供更高质量的零部件,以提高整体组装质量和效率。
PFMEA整合_
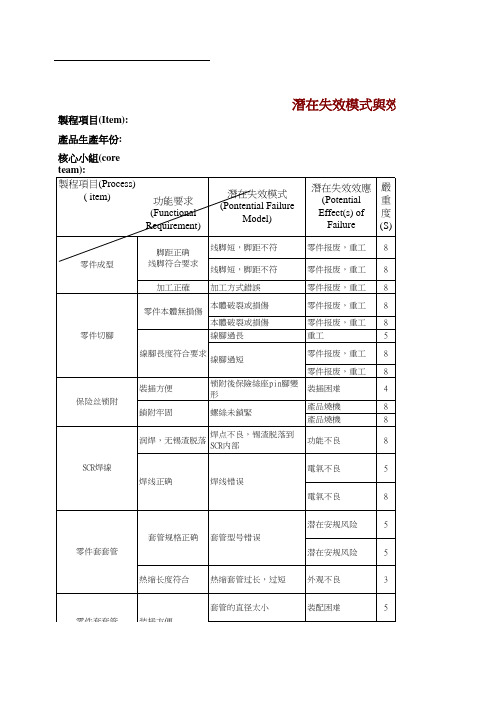
Short 不良 (三) Tapping Function Tapping 不良
8 8 5 5 7 7
5 3 7 5 5 6 6 6 4 3 6 6 6 5
机器防潮
干燥剂漏放 缓冲材放错
功能不良 作业困难 產品功能不良/客 訴 功能不良 外观不良 客户抱怨 客户抱怨 線材易脫落,功能 不良 黏貼歪斜需重工, 增加作業工時 重工;客户抱怨 附件損壞;客户抱 怨 運輸過程中易損傷 產品 木箱無法有效固定
潛在失效模式與效應分析(製程PF
製程項目(Item): 產品生產年份: 核心小組(core team): 製程項目(Process) ( item) 功能要求 (Functional Requirement)
脚距正确 线脚符合要求 加工正確 零件本體無損傷 零件切腳 線腳長度符合要求
潛在失效模式 (Pontential Failure Model)
7 零件位置装插正确 错件 功能不良 7
浪費工時 零件插件作業方便 插件困難 作業困難,增加作 業工時
5 3 7
零件装插方向正确 反向
功能不良
10
7
手插件
7
6
高翘 符合品质规范
功能不良
6
5
7 7 7
无线尾
功能不良
8
8
8
漏焊
功能不良 重工
漏焊
功能不良 重工
8
8
锡桥
影响外观
4
7
短路
功能不良
7
7 波峰焊 焊点圆润 吃锡饱满 符合品质规范 影响外观 锡尖 高压不良 安距不足 8 4
8 8
1.燒機 重工
8 8 4
(二) FUT Function 2.誤判 重测
组装过程pfmea分析表
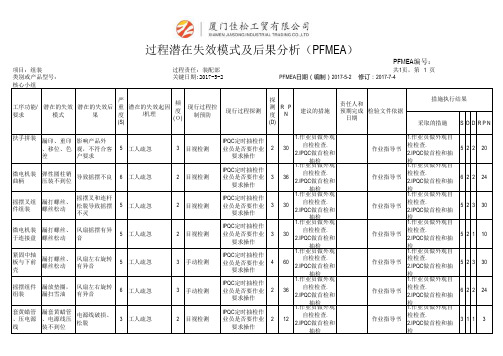
核心小组采取的措施S O D R P N扶手拼装漏印、重印、移位、色差影响产品外观,不符合客户要求5工人疏忽3目视检测IPQC定时抽检作业员是否要作业要求操作2301.作业员做外观自检检查.2.IPQC做首检和抽检作业指导书1.作业员做外观自检检查.2.IPQC做首检和抽检52220微电机装曲柄弹性圆柱销压装不到位导致摇摆不良6工人疏忽2目视检测IPQC定时抽检作业员是否要作业要求操作3361.作业员做外观自检检查.2.IPQC做首检和抽检作业指导书1.作业员做外观自检检查.2.IPQC做首检和抽检62224摇摆叉组件组装漏打螺丝、螺丝松动摇摆叉和连杆松脱导致摇摆不灵5工人疏忽2目视检测IPQC定时抽检作业员是否要作业要求操作3301.作业员做外观自检检查.2.IPQC做首检和抽检作业指导书1.作业员做外观自检检查.2.IPQC做首检和抽检52330微电机装于连接盘漏打螺丝、螺丝松动风扇摇摆有异音5工人疏忽2目视检测IPQC定时抽检作业员是否要作业要求操作3301.作业员做外观自检检查.2.IPQC做首检和抽检作业指导书1.作业员做外观自检检查.2.IPQC做首检和抽检52110紧固中轴板与下前壳漏打螺丝、螺丝松动风扇左右旋转有异音5工人疏忽3手动检测IPQC定时抽检作业员是否要作业要求操作4601.作业员做外观自检检查.2.IPQC做首检和抽检作业指导书1.作业员做外观自检检查.2.IPQC做首检和抽检52330摇摆组件组装漏放垫圈,漏扫雪油风扇左右旋转有异音6工人疏忽3手动检测IPQC定时抽检作业员是否要作业要求操作2361.作业员做外观自检检查.2.IPQC做首检和抽检作业指导书1.作业员做外观自检检查.2.IPQC做首检和抽检62224套黄蜡管、压电源线漏套黄蜡管、电源线压装不到位电源线破损、松脱3工人疏忽2目视检测IPQC定时抽检作业员是否要作业要求操作2121.作业员做外观自检检查.2.IPQC做首检和抽检作业指导书1.作业员做外观自检检查.2.IPQC做首检和抽检3113责任人和预期完成日期检验文件依据频度(O)现行过程控制预防现行过程探测探测度(D)R PN建议的措施类别或产品型号:关键日期:2017-5-2PFMEA日期(编制)2017-5-2 修订:2017-7-4措施执行结果工序功能/要求潜在的失效模式潜在的失效后果严重度(S)潜在的失效起因/机理过程潜在失效模式及后果分析(PFMEA)PFMEA编号:项目:组装过程责任:装配部共1页,第 1 页。
PFMEA分析范例
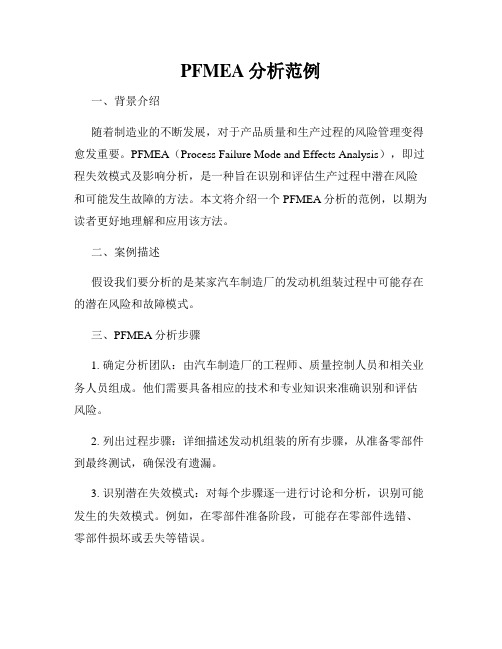
PFMEA分析范例一、背景介绍随着制造业的不断发展,对于产品质量和生产过程的风险管理变得愈发重要。
PFMEA(Process Failure Mode and Effects Analysis),即过程失效模式及影响分析,是一种旨在识别和评估生产过程中潜在风险和可能发生故障的方法。
本文将介绍一个PFMEA分析的范例,以期为读者更好地理解和应用该方法。
二、案例描述假设我们要分析的是某家汽车制造厂的发动机组装过程中可能存在的潜在风险和故障模式。
三、PFMEA分析步骤1. 确定分析团队:由汽车制造厂的工程师、质量控制人员和相关业务人员组成。
他们需要具备相应的技术和专业知识来准确识别和评估风险。
2. 列出过程步骤:详细描述发动机组装的所有步骤,从准备零部件到最终测试,确保没有遗漏。
3. 识别潜在失效模式:对每个步骤逐一进行讨论和分析,识别可能发生的失效模式。
例如,在零部件准备阶段,可能存在零部件选错、零部件损坏或丢失等错误。
4. 评估失效后果:对于每个失效模式,评估其对整个发动机性能和安全性的影响。
例如,零部件选错可能导致发动机无法正常工作或者存在严重的安全隐患。
5. 评估失效发生概率:考虑各种因素,如操作人员技能水平、设备可靠性、材料质量等,评估失效的发生概率。
例如,操作人员技能水平较低可能增加零部件选错的概率。
6. 计算风险优先级数值(RPN):根据失效的后果和发生概率,计算风险优先级数值。
RPN的计算公式为:RPN = 后果严重性 ×发生概率 ×检测能力。
例如,如果某个失效模式的后果严重性评分为10,发生概率为8,检测能力为9,则该失效模式的RPN为720。
7. 制定改进措施:对于RPN值较高的失效模式,制定相应的改进措施来降低风险。
例如,针对零部件选错,可以加强操作人员的培训和审查流程,以减少错误发生的概率。
8. 实施改进措施:将制定的改进措施纳入发动机组装过程,并确保实施有效。
PFMEA在SMT装配中的应用

分析工作打下 良好的基础,建立一个优选 的系统。 是:印刷焊膏——贴装元器件—一A 1 o 检验——回流焊接——焊点检验 ,该装配过程涉及的主要设备有丝
印机 、贴 片机 、 回流 焊炉 和检测 设 备 。焊 锡球 是单 面贴 装工 艺过程 中常见 的失 效模 式之 一 ,其 因果分 析 图
如图 1 示。 所
抑制焊料球产生的焊膏,装配前检测焊膏品质。() 2 助焊剂缺陷——活性 降低 ,频度为 3 ,检测难度为 6 ,
风险指数 P N 为 9 。() R 0 3 模板缺陷——开孔尺寸不当、焊盘过大等 ,频度为 5 ,检测难度为 4 ,风险指数
P N 为 10 ()回流温度曲线设置不当, R 0。4 频度为 7 检测难度为 5 风险指数 P N 为 15 现行控制措施: , , R 7。
工
程
8 9
利 用 UGI I软件 对产 品进行 布 线仿真 ,具 体流 程 如下 :先设 计结 构平 面 图样 ,进 行 实体建 模 ;给零件 赋予
各连接端子位号; 在装配实体模型的基础上, 依据工艺布线原则和图纸接线关系 , 进行产品的主线束布设; 利用 U I模块功能,创建各类文本 ,建立所需特征库;生成三维实体走线 图 ( GI 见图 1 ; G I ) U I进行干涉分
装 配工 艺 。
32 瞬态 电磁干扰测试方法 .6
徐 亮
由于同步装置工作时有脉冲高电压、大 电流输出,产生的电磁环境十分复杂和恶劣,对周围的组件及
测试 系统产 生较严 重 的影 响 , 台面联试 、半 总装联 试及 总装 联试 等不 同状 态下 ,经 常 出现 由于干 扰 问题 , 在 影响 程控等 装置 正常 工作 ,使系 统联试 工作无 法正 常进行 ,严重 时还会 造成程 控 等装置 损坏 。因此 ,需要
汽车焊接工艺文件2-焊装PFMEA(专业课堂)

5
详细课资
FMEA分类
CFMEA——概念FMEA DFMEA——设计FMEA PFMEA——过程FMEA MFMEA——机器FMEA
6
详细课资
DFMEA与PFMEA区别
1、DFMEA 聚焦于零件的功能,而PFMEA 聚焦于制造步骤或过程; 2、PFMEA 假定产品的设计是符合设计意图的。由设计弱点引发的潜在失效模式 也可 以包含在PFMEA 中。 他们的影响及如何避免应覆盖在DFMEA 中。
制造/装配厂产生缺陷时便得出相应的定级结果。 装配厂产生缺陷时便得出相应的定级结果。最终顾客 度
最终顾客永远是首先考虑的。如果两种可能都 永远是首先考虑的。如果两种可能都存在的,采用两 级
存在的,采用两个严重度值中的较高者 。
个严重度值中的较高者 。(制造/装配后果)
别
(顾客的后果)
当潜在的失效模式在无警告的情况下影响到车 或可能在无警告的情况下对(机器或总成)操作员造 10 辆安全运行和/或涉及不符合政府法规的情况时, 成危害 严重度定级非常高
5)编制日期 填入编编制制日F期ME为A原FM始EA稿编的制日生效期日及期最,新比修关订键的日日期期早。,(此Q公日司期只不填原能始更稿改日期)
表头 6)核心小组 列出有权确定和/或执行任务的部门的名称和个人的姓名(建议 所有参加人员的姓名、部门、电话、地址等都应记录在一张分发表上。) 7)零件名称: 工位名称
当潜在的失效模式在有警告的情况下影响到车 或可能在有警告的情况下对(机器或总成)操作员造 9 辆安全运行和/或涉及不符合政府法规的情况时, 成危害 严重度定级非常高
车辆/项目不能工作(丧失基本功能)
电子产品生产过程PFMEA
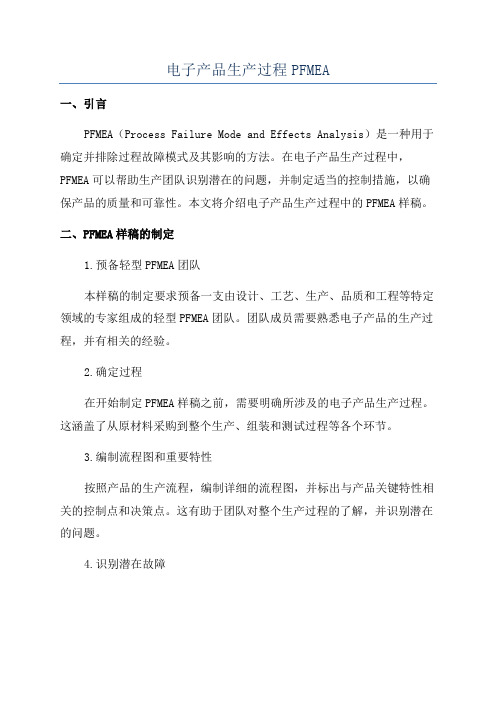
电子产品生产过程PFMEA一、引言PFMEA(Process Failure Mode and Effects Analysis)是一种用于确定并排除过程故障模式及其影响的方法。
在电子产品生产过程中,PFMEA可以帮助生产团队识别潜在的问题,并制定适当的控制措施,以确保产品的质量和可靠性。
本文将介绍电子产品生产过程中的PFMEA样稿。
二、PFMEA样稿的制定1.预备轻型PFMEA团队本样稿的制定要求预备一支由设计、工艺、生产、品质和工程等特定领域的专家组成的轻型PFMEA团队。
团队成员需要熟悉电子产品的生产过程,并有相关的经验。
2.确定过程在开始制定PFMEA样稿之前,需要明确所涉及的电子产品生产过程。
这涵盖了从原材料采购到整个生产、组装和测试过程等各个环节。
3.编制流程图和重要特性按照产品的生产流程,编制详细的流程图,并标出与产品关键特性相关的控制点和决策点。
这有助于团队对整个生产过程的了解,并识别潜在的问题。
4.识别潜在故障团队成员根据其专业知识和经验,识别并记录可能会导致产品故障的潜在失效模式。
这些模式可能包括材料的质量问题、设计缺陷、工艺控制不良等。
5.评估故障后果对每种失效模式,团队成员需要评估其对产品和过程的影响。
这可能包括产品的功能性能下降、产品无法使用、生产延误、不良的质量声誉等。
6.评估现有控制措施的有效性对于已经实施的控制措施,团队成员需要评估其在减少潜在失效模式发生和影响时的有效性。
如果发现控制措施不足或不起作用,需要提出相应的改进方案。
7.评估潜在失效模式的严重程度、频率和检测能力对于每个失效模式,团队成员需要对其严重程度、发生频率和检测能力进行评估,并根据评估结果计算出风险优先级数(Risk Priority Number, RPN)。
这有助于团队确定需要优先关注的失效模式。
8.制定改进计划根据评估结果,团队成员需要制定改进计划,明确改进的目标、方法和时间表。
改进计划可以包括设计优化、工艺改进、质量控制等方面的措施。
PFMEA分析范例

PFMEA分析范例1. 引言PFMEA(Process Failure Mode and Effects Analysis)是一种常用的质量管理工具,用于识别和评估制造过程中存在的潜在故障模式及其对产品质量的影响。
本文将通过一个实例来展示PFMEA分析的过程和方法。
2. 实例描述假设我们正在开发一种新型电动汽车电池组装工艺,并希望通过PFMEA分析来发现潜在的故障模式并采取相应的措施预防。
3. PFMEA步骤3.1 选择分析范围首先,我们需要确定要分析的工艺范围。
在本例中,我们选择了电动汽车电池组装工艺中的关键步骤:电池包装、电池连接和充电检测。
3.2 收集工艺信息接下来,我们收集与每个工艺步骤相关的信息,包括工艺流程、设备、材料和人员等。
针对电池包装步骤,我们列出了以下信息: - 工艺流程:电芯装载、包装封装- 设备:电芯装载机、包装机- 材料:电芯、包装材料- 人员:操作工、质检员3.3 识别故障模式在此步骤中,我们识别潜在的故障模式,即制造过程中可能发生的问题。
针对电池包装步骤,我们列出了以下故障模式: - 电芯装载不准确- 包装封装不牢固3.4 评估故障影响在此步骤中,我们评估每个故障模式对产品质量的影响程度。
针对电芯装载不准确这一故障模式,我们评估了以下影响: - 电池运行时间缩短- 电池性能下降3.5 评估故障原因在此步骤中,我们分析导致每个故障模式出现的可能原因。
针对电芯装载不准确这一故障模式,可能的原因包括:- 操作工技能不熟练- 设备故障3.6 识别和实施控制措施在此步骤中,我们确定并实施控制措施以防止故障模式的发生。
针对电芯装载不准确这一故障模式,可能的控制措施包括: - 培训操作工,提高技能水平- 定期维护设备,确保其正常运行3.7 重新评估和更新PFMEA最后,我们重新评估已实施的控制措施并更新PFMEA表格。
如果控制措施有效,我们将确认问题得到了解决。
如果问题仍存在,我们需要重新评估并采取进一步的纠正措施。
PFMEA分析范例
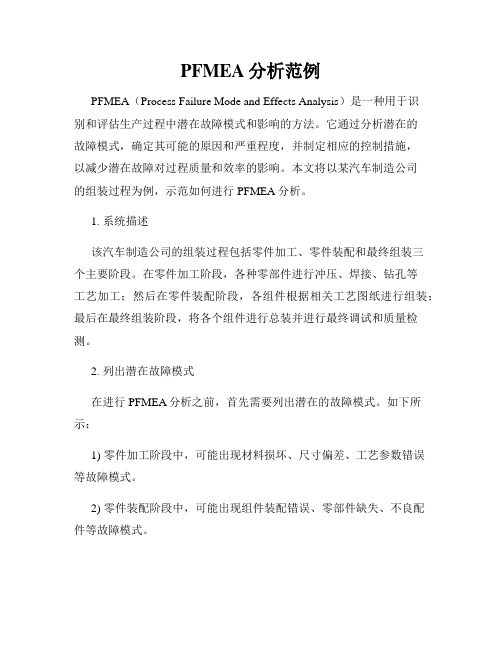
PFMEA分析范例PFMEA(Process Failure Mode and Effects Analysis)是一种用于识别和评估生产过程中潜在故障模式和影响的方法。
它通过分析潜在的故障模式,确定其可能的原因和严重程度,并制定相应的控制措施,以减少潜在故障对过程质量和效率的影响。
本文将以某汽车制造公司的组装过程为例,示范如何进行PFMEA分析。
1. 系统描述该汽车制造公司的组装过程包括零件加工、零件装配和最终组装三个主要阶段。
在零件加工阶段,各种零部件进行冲压、焊接、钻孔等工艺加工;然后在零件装配阶段,各组件根据相关工艺图纸进行组装;最后在最终组装阶段,将各个组件进行总装并进行最终调试和质量检测。
2. 列出潜在故障模式在进行PFMEA分析之前,首先需要列出潜在的故障模式。
如下所示:1) 零件加工阶段中,可能出现材料损坏、尺寸偏差、工艺参数错误等故障模式。
2) 零件装配阶段中,可能出现组件装配错误、零部件缺失、不良配件等故障模式。
3) 最终组装阶段中,可能出现组装错误、传动系统故障、电子系统故障等故障模式。
3. 评估故障原因在列出潜在故障模式之后,需评估每种故障模式的可能原因。
具体评估过程如下:1) 零件加工阶段中,材料损坏的原因可能是供应商提供的原材料质量不合格,尺寸偏差的原因可能是机床设备调整不当,工艺参数错误的原因可能是人工操作失误。
2) 零件装配阶段中,组件装配错误的原因可能是工人操作不规范,零部件缺失的原因可能是供应链管理不善,不良配件的原因可能是供应商提供的配件质量不合格。
3) 最终组装阶段中,组装错误的原因可能是工人操作失误,传动系统故障的原因可能是组装过程中零部件配合不良,电子系统故障的原因可能是控制芯片质量问题。
4. 评估故障严重程度在评估故障原因后,需要评估每种故障模式的严重程度,即故障发生时可能造成的影响程度。
具体评估过程如下:1) 零件加工阶段中,材料损坏可能导致后续组装工序无法进行,尺寸偏差可能导致产品性能下降,工艺参数错误可能导致产品质量问题。
新版PFMEA案例朱春佳老师

新版PFMEA案例朱春佳老师在当今竞争激烈的制造业领域,产品质量和可靠性的保障至关重要。
而 PFMEA(过程潜在失效模式及后果分析)作为一种有效的风险管理工具,对于优化生产过程、预防潜在问题具有不可忽视的作用。
在这一领域,朱春佳老师以其丰富的经验和专业的知识,为我们带来了许多具有借鉴意义的新版 PFMEA 案例。
朱春佳老师深知,新版 PFMEA 的实施并非简单地填写表格,而是需要深入理解产品和过程的每一个细节。
以某汽车零部件生产企业为例,朱老师在进行 PFMEA 分析时,首先对整个生产流程进行了详细的梳理。
从原材料的采购、入库检验,到零部件的加工、装配,再到成品的检验、包装和出货,每一个环节都没有放过。
在原材料采购环节,朱老师通过与供应商的沟通和对历史数据的分析,识别出可能存在的供应商质量不稳定、原材料规格不符合要求等潜在失效模式。
针对这些问题,提出了加强供应商评估和审核、增加原材料抽检频率等预防措施,有效地降低了原材料质量问题对后续生产的影响。
在零部件加工过程中,朱老师发现由于设备老化和操作人员技能不足,可能会导致尺寸超差、表面粗糙度不符合要求等问题。
为了解决这些问题,他建议制定设备维护计划、加强操作人员培训,并引入先进的加工工艺和检测手段,从而提高了零部件的加工质量和一致性。
装配环节也是容易出现问题的地方。
朱老师观察到由于装配工艺不合理和工装夹具的精度不够,可能会出现零部件装配不到位、紧固力不足等情况。
为此,他与工艺工程师一起优化了装配工艺,改进了工装夹具的设计,并制定了严格的装配检验标准,确保了产品的装配质量。
在成品检验环节,朱老师指出检验标准不够明确和检验设备精度不足可能会导致不合格产品流出。
于是,他协助企业重新制定了详细的检验标准,引进了高精度的检验设备,并对检验人员进行了专业培训,大大提高了产品的合格率。
除了汽车零部件行业,朱老师在电子行业的新版 PFMEA 案例也同样精彩。
在一家手机制造企业中,朱老师针对手机主板的生产过程进行了深入的 PFMEA 分析。
PFMEA-组装

项目名称过程责任部门FMEA No.产品类型
关键日期
页码共
编制
核心小组
修订日期
预防探测
采取的措施S E V O
C C
D
E F
R P N
虚焊
1.连接保护线路板后使电池的整体内阻较大;
2.复合带脱落
7
1.超焊机能量不稳定;
2.参数设置错误
82
112
设备1h校验一次,参数做实验已重新确认
2.1
设备1h校验一次,参数做实验已重新确认
歪斜 1.电芯外观差;2.影响客户操作
5员工操作不当
31
15
复合带焊反 1.外观不良;2.影响客户操
作;3.连接保护
线路板后使电池的整体内阻较大
7员工操作不当38168
加强培训,检验
2.1
实验确认焊反后,反装时其色泽与正常差异大,可检验
73363
潜在的失效原因/机理
频度
数
O C C
现行过程控制
作业指导书WI-BM/CT-001/A/A (A200)
员工自检、
QC巡检
措施结果
不易探测度
D E F 风险顺序数R P N 建议的措施责任及目标完成日
期周员芳 张峰
工艺优化组
编制日期
过程功能/要求潜在失效模式潜在的失效后
果
严重度数S E V
级别电池超焊铝镍复合带,使外部保护
线路板能连接1
潜在失效模式及后果分析
(PFMEA )
超焊铝镍复合带工艺部、生产部、品质部、机电部
PFMEA-CT-002/A 523450A/试产
1页
表格编号/版次:QR7510-03。
工艺品生产PFMEA分析范例
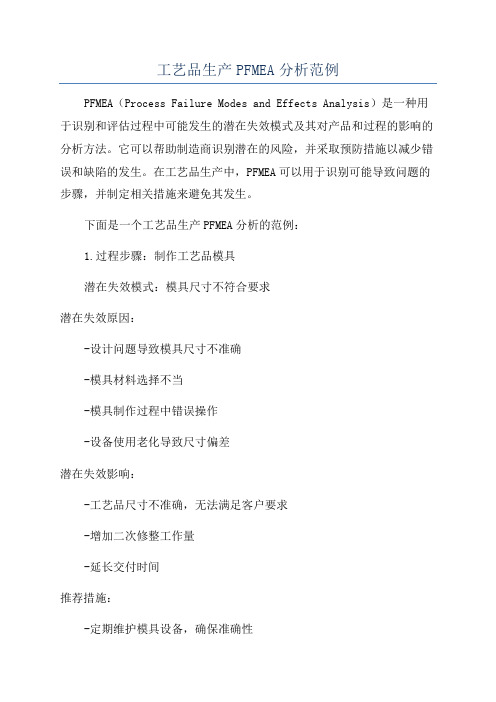
工艺品生产PFMEA分析范例PFMEA(Process Failure Modes and Effects Analysis)是一种用于识别和评估过程中可能发生的潜在失效模式及其对产品和过程的影响的分析方法。
它可以帮助制造商识别潜在的风险,并采取预防措施以减少错误和缺陷的发生。
在工艺品生产中,PFMEA可以用于识别可能导致问题的步骤,并制定相关措施来避免其发生。
下面是一个工艺品生产PFMEA分析的范例:1.过程步骤:制作工艺品模具潜在失效模式:模具尺寸不符合要求潜在失效原因:-设计问题导致模具尺寸不准确-模具材料选择不当-模具制作过程中错误操作-设备使用老化导致尺寸偏差潜在失效影响:-工艺品尺寸不准确,无法满足客户要求-增加二次修整工作量-延长交付时间推荐措施:-定期维护模具设备,确保准确性-选用高质量的模具材料-制作模具前进行尺寸验证-建立模具维护记录,进行及时维修和更换2.过程步骤:涂装工艺潜在失效模式:涂层不均匀潜在失效原因:-涂料质量不稳定-涂料喷涂过程中的操作问题-涂装设备故障-涂装环境不合理潜在失效影响:-工艺品表面不均匀,影响外观质量-涂层易剥落或老化-浪费大量的涂料推荐措施:-选择高质量的涂料供应商-使用标准操作规范进行涂装-定期维护和校准涂装设备-创建合适的涂装环境,并确保温度和湿度的稳定3.过程步骤:组装工艺潜在失效模式:组装不完全潜在失效原因:-部件尺寸不匹配-人员操作不当-部件损坏或缺失-装配设备故障潜在失效影响:-工艺品功能不正常-降低产品质量-退货和客户投诉推荐措施:-进行部件尺寸验证和检查-建立装配操作标准,培训操作人员-检查和保养装配设备-实施零件追溯系统,确保零件的准确性和完整性这只是一个简单的PFMEA分析范例,实际应用中可能需要更详细和全面的分析。
在进行PFMEA时,应该团队合作,包括工艺工程师、生产工程师、质量工程师和操作人员。
他们应该共同审查和评估每个过程步骤的潜在失效模式、原因和影响,并提出相应的措施来预防和纠正潜在的问题。
PFMEA案例5
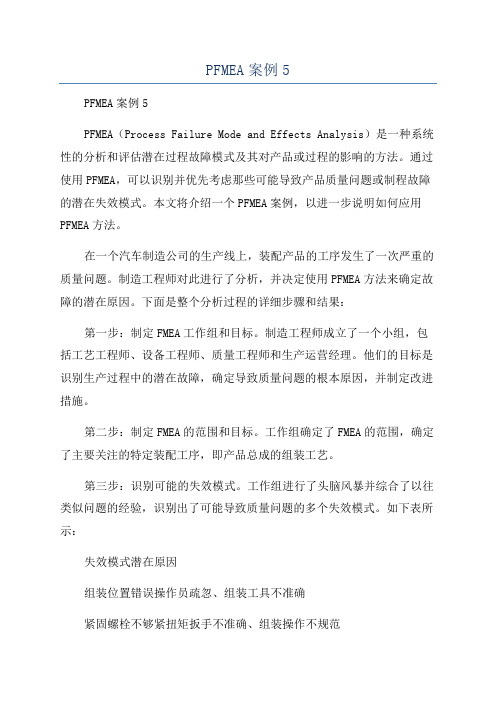
PFMEA案例5PFMEA案例5PFMEA(Process Failure Mode and Effects Analysis)是一种系统性的分析和评估潜在过程故障模式及其对产品或过程的影响的方法。
通过使用PFMEA,可以识别并优先考虑那些可能导致产品质量问题或制程故障的潜在失效模式。
本文将介绍一个PFMEA案例,以进一步说明如何应用PFMEA方法。
在一个汽车制造公司的生产线上,装配产品的工序发生了一次严重的质量问题。
制造工程师对此进行了分析,并决定使用PFMEA方法来确定故障的潜在原因。
下面是整个分析过程的详细步骤和结果:第一步:制定FMEA工作组和目标。
制造工程师成立了一个小组,包括工艺工程师、设备工程师、质量工程师和生产运营经理。
他们的目标是识别生产过程中的潜在故障,确定导致质量问题的根本原因,并制定改进措施。
第二步:制定FMEA的范围和目标。
工作组确定了FMEA的范围,确定了主要关注的特定装配工序,即产品总成的组装工艺。
第三步:识别可能的失效模式。
工作组进行了头脑风暴并综合了以往类似问题的经验,识别出了可能导致质量问题的多个失效模式。
如下表所示:失效模式潜在原因组装位置错误操作员疏忽、组装工具不准确紧固螺栓不够紧扭矩扳手不准确、组装操作不规范螺纹未涂抹防松剂未执行涂抹防松剂的工艺步骤第四步:确定失效模式的严重程度。
工作组对每个失效模式进行了评估,并根据潜在的影响程度和可能的后果,给予了一个评分,从1到10的量表。
如下表所示:失效模式严重程度评分组装位置错误8紧固螺栓不够紧9螺纹未涂抹防松剂6第五步:确定失效模式的频率。
工作组对每个失效模式进行了评估,并根据之前发生的类似问题的频率,给予了一个评分,从1到10的量表。
如下表所示:失效模式频率评分组装位置错误6紧固螺栓不够紧4螺纹未涂抹防松剂5第六步:确定失效模式的检测能力。
工作组对每个失效模式进行了评估,并根据当前的检测能力,给予了一个评分,从1到10的量表。
PFMEA装配模版

PFMEA装配模版如何提高工作效率。
在现代社会,工作效率成为了一个越来越受重视的问题。
随着竞争的日益激烈,提高工作效率已经成为了每个人都必须面对的挑战。
无论是在个人生活中,还是在企业管理中,提高工作效率都是一个重要的课题。
那么,如何提高工作效率呢?本文将从个人角度和企业管理角度分别探讨这个问题。
首先,从个人角度来看,提高工作效率需要培养良好的工作习惯。
首先要有一个清晰的工作计划,合理安排时间,合理分配任务,避免拖延和浪费时间。
其次,要保持专注,避免分心和浪费精力。
另外,要学会管理时间,避免时间浪费,提高工作效率。
此外,要树立正确的工作态度,积极主动地面对工作,不断学习和提高自己的工作能力。
最后,要保持良好的身体和心理状态,保持充沛的精力和积极的心态,才能更好地提高工作效率。
其次,从企业管理角度来看,提高工作效率需要建立科学的管理制度。
首先要明确工作目标,明确员工的工作任务和责任,合理分配资源,确保工作目标的实现。
其次,要建立有效的沟通渠道,保持信息畅通,确保员工之间和部门之间的协作和配合。
另外,要建立有效的激励机制,激励员工积极主动地面对工作,提高工作效率。
此外,要建立科学的绩效考核制度,及时发现和解决工作中的问题,提高工作效率。
最后,要建立良好的企业文化,营造和谐的工作氛围,激发员工的工作激情,提高工作效率。
总之,提高工作效率是一个复杂的系统工程,需要个人和企业管理共同努力。
个人要培养良好的工作习惯,保持专注,管理时间,树立正确的工作态度,保持良好的身体和心理状态,才能更好地提高工作效率。
企业管理要建立科学的管理制度,明确工作目标,建立有效的沟通渠道,建立有效的激励机制,建立科学的绩效考核制度,建立良好的企业文化,才能更好地提高工作效率。
希望本文的探讨能够对提高工作效率有所帮助。
装配过程 PFMEA实例(中英文)

80
CPK requirement on shaft OD對轉子內徑要求CPK
130
1
Pulley Press壓皮帶輪
Wrong Assembly Dimension組裝尺寸錯誤
Not Meet Customer Unit和客戶的部件不相配
8
Wrong Machine Setup
機器設定錯誤
2
100% Visual Check目視全檢
壓軸承
Distance Between 2 Bearings too Long
両軸承間距太長
1)No Axial Play沒有軸向遊隙
2) Motor Not Meet Performance Spec電機不符合性能要求
3) Noise / Vibration噪音/振動
5
6
8
Wrong Machine Setup
Broken Magnet磁環破裂
1) Noise / Vibration噪音/振動
2) Motor Not Meet Performance Spec電機不符合性能要求
8
6
Wrong Machine Setup
機器設定錯誤
2
Visual Check 100%目視全檢
Check setup 1time/day or before re-supply每天一次檢查設定或換型時
2
3
32
48
110
1
Rotor Coin轉子上壓環形痕
No Coin沒有環形痕
Loose coin壓環太鬆
Noise/Vibration噪音/振動
Inoperable motor電機無法動作
钣金结构件装配PFMEA库

PQM_TQC_SHEET METALFailure Mode and Effects Analysis (FMEA) Failure Modes and Effects Analysis (FMEA): 小钣金组装工序Process/Product: Requirements Management FMEA Date:FMEA Team: List names here of the people (Revised)Black Belt:Page:Process工序潜在失效模式 潜在失效后果 严重度(S)潜在失效起因频度(O)现行过程控制预防 现行过程控制探测探测度(D)RPN建议措施责任人和完成日期措施执行结果采取的措施及生效日期严重度 频度探测度 RPN小钣金组装银漆溢出引起脏污、外观不良6放置过程中触碰8隔开放置线尾目视全检4192避免在组装线涂银漆,前工序完成63472拉铆高出表面影响插拔、刮手、面膜凸起7沉孔过小3制定关键岗位线尾用手进行触摸全检484采用自动沉孔机714287手工拉偏、用力不足6制定关键岗位线尾用手进行触摸全检41681、全检;2、增加拉铆工装;73484拉空(针对空心拉钉)板间间隙,影响强度8铆接时压力不足,物料没有贴死2采用治具,将铆接的物料强制拘束固定线尾目视全检580拉钉断裂,影响强度8拉钉枪嘴与拉钉不匹配2设备专人管理,专人登记发放线尾目视全检580拉钉头掉落内部金属异物,烧板7设计没有预留排料孔51、采用手动摇晃产品,检测是否有异/2、采用气枪吹出来;线尾对产品进行摇动,确保无晃动声音51751、研发优化设计,增加排料孔;2、对于封闭腔体,建议采用空心拉钉;72570拉铆拉错位置后工序无法装配7两个孔太近,且尺寸相似5制定关键岗位线尾目视全检51751、增加拉钉遮蔽工装;72570拉钉用错影响强度与装配7拉钉领料时发生混料21、两种以上拉钉时需要拆分工序;线尾目视全检5707拉钉领料时发生混料21、专人配料;2、每批生产完成及时退库;线尾目视全检570漏拉铆影响强度与装配7拉铆位置多,漏作业51、分工位作业(工位限制拉铆数量)2、配料制目视41401、采用自动拉铆装;2、CCD72456用错螺钉影响强度及功能7螺钉领料时发生混料21、两种以上螺钉钉时需要拆分工序;线尾目视全检5707螺钉领料时发生混料21、专人配料;2、每批生产完成及时退库;线尾目视全检570漏螺钉影响强度与装配7螺钉位置多,漏作业51、分工位作业(工位限制螺钉数量)2、配料制线尾目视全检41401、采用自动螺钉机;2、CCD72456后环节无法拆卸、螺丝打花、塑胶件开裂影响功能和外观7校准力矩过大21、开线专人点检;2、点检后采用封签;首尾检6847同一工序两种不同力矩电批2不同力矩分不同工序操作目视684螺钉未打紧影响强度与功能8力矩偏小21、开线专人点检;2、点检后采用封签;首巡尾检696影响强度与功能8漏点螺纹胶2SOP针对螺纹胶增加具体的要求,员工培训后按照SOP要求执行首巡尾检696螺钉凸出表面外观问题7螺钉打斜3SOP要求螺钉装配时手法,员工线前培训线尾目视全检4841、采用自动螺钉机;2、CCD72456 7螺孔金属异物3增加吹气工装线尾目视全检48473484面膜混料错混料8发料时混料31、专人配料;2、每批生产完成及时退库;线尾目视全检5120面膜撕手位增加二维码,上线前扫码确认82580面膜翘起、起泡外观不良5金属表面脏污3SOP要求酒精擦拭干净外观目视检验3455面膜长时间暴露空气,未粘贴3面膜粘贴时才允许揭开外观目视全检345撕一个贴一个533455粘贴后未按压3SOP要求粘贴后必须按压外观目视检验345面膜粘贴歪斜外观不良51、未使用工装5严格管控需要使用工装外观目视全检375限制必须使用工装5537552、没有定位基准5要求设计人员增加定位基准外观目视全检37553、操作错误,面膜未对正5L角+横线对正先目视全检,发现问题再卡尺测量375CCD检测55375条码贴反外观不良5手工作业,粘贴难定位3靠SOP指引,自检互检外观目视全检345条码断线、模糊无法扫描7打印设备故障31、专人打印、专人管理/2、设备定期维护;扫描设备全扫描识别121条码贴错错混料8条码领错料11、系统防呆,订单直接打印;2、条码系统防呆,扫描错误报警条码系统防呆18条码起翘外观问题,无法扫描5粘贴动作不标准3SOP针对条码粘贴要点提要求,粘贴完需要按压外观目视全检345条码重复错混料8条码打印、领用不规范1条码系统防呆,扫描重复报警条码系统防呆18漏扫描错混料8扫描枪损坏1条码系统防呆,未扫描无法入库条码系统防呆18条码扫不上错混料8条码不清晰1条码系统防呆,未扫描无法入库条码系统防呆18包装不合理产品变形,影响功能外观7包装设计不合理3O Q C出货抽检O Q C出货时抽检6126新产品导入评审时需要考虑包装缓冲能力72684漏附件影响装配6附件未称重及扫描3已经执行称重、扫描称重、目视354附件自动打包机62336簧片翘起(包装)影响功能和外观6包装时刀卡刮擦簧片导致翘起2采用吸塑盒周转O Q C出货时抽检672对称物料装错(包装)影响装配与功能7没有进行防呆设计3按照SOP要求进行包装作业O Q C出货时抽检61261、产品设计时需要考虑防呆设计;2、包装设计时需要考虑防呆设计;72684漏封箱产品变形,影响功能外观7手工作业,人员专业性差3靠SOP指引,自检首检,抽检,尾检4841、采用自动封箱机;72456。
- 1、下载文档前请自行甄别文档内容的完整性,平台不提供额外的编辑、内容补充、找答案等附加服务。
- 2、"仅部分预览"的文档,不可在线预览部分如存在完整性等问题,可反馈申请退款(可完整预览的文档不适用该条件!)。
- 3、如文档侵犯您的权益,请联系客服反馈,我们会尽快为您处理(人工客服工作时间:9:00-18:30)。
频
度
级 潜在的失效原因/ 数
别
机理
O
C
C
现行过程控制
预防
探测
不
易 探 测 度 D E
风 R险 P 顺 建议的措施 N序
数
责任及目 标完成日
期
措施结果
SO 采取的措施 E C
VC
F
电
池
超
焊
铝
路 板 能 连 接
镍 复 合 带 , 使
外
部
保
护
线
虚焊
1.连接保护线路
板后使电池的
整体内阻较
7
大;2.复合带脱
落
歪斜
1.电芯外观 差;2.影响客 5 户操作
1.外观不良;2.
影响客户操
复合带焊反
作;3.连接保护 线路板后使电
7
池的整体内阻
较大
1.超焊机能量不 稳定;2.参数设 8 置错误
设备1h校验
2
112
一次,参数 做实验已重
新确认
员工操作不当
作业指导书
3
WI-BM/CT- 员工自检、 001/A/A QC巡检
1
15
(A200)
员工操, 检验
设备1h校验
2.1
一次,参数 做实验已重
新确认
实验确认焊 反后,反装 2.1 时其色泽与 7 3 正常差异 大,可检验
DR EP FN
3 63
表格编号/版次:QR7510-03
潜在失效模式及后果分析
(PFMEA)
项目名称
超焊铝镍复合带
过程责任部门 工艺部、生产部、品质部、机电部 FMEA No.
PFMEA-CT-002/A
产品类型
523450A/试产
关键日期
页码
1页
共
1
编制
周员芳 张峰
核心小组
工艺优化组
编制日期
修订日期
过程功能/ 要求
潜在失效模式
潜在的失效后 果
严 重 度 数 S E V