汽车转向梯形优化设计
车辆优化设计理论与实践课件:优化设计在汽车上的应用实例 -

用值,即
g8 ( X ) 1 [ 1] 0
g9 ( X ) 2 [ 2] 0
g10 ( X ) j [ j] 0
7)齿轮轴的最大挠度应不大于其许用值,
即
g11( X ) f 1max [ f 1] 0
g12 ( X ) f 2max[ f 2] 0
6.3 变速器传动齿轮的优化设计
Z1
Z2
Z3
Z4
6.3 变速器传动齿轮的优化设计
对于二级圆柱齿轮传动装置而言,影响承载
能力系数 (X ) 的独立变量仅有传动比 i 、
螺旋角 和第一、二级传动的中心距变动系 数 1 、2 。因此设计变量为
X [x1 x2 x3 x4]T [i 1 2]T
为提高齿轮的接触强度,应尽量增大承载能 力系数,也就是使其倒数最小。对第一级和 第二级齿轮传动来说,应分别使其最小
4)齿轮模数应大于零,即 g5 (X ) x3 0
5)齿轮轴的最小尺寸若分别规定为 d1min 和 d 2min ,则有
g6 ( X ) d1min x4 0 g7 ( X ) d 2min x5 0
6.3 变速器传动齿轮的优化设计
6)轮齿的弯曲应力及接触应力不大于其许
os1
2m
c
os2
赛车转向梯形优化设计
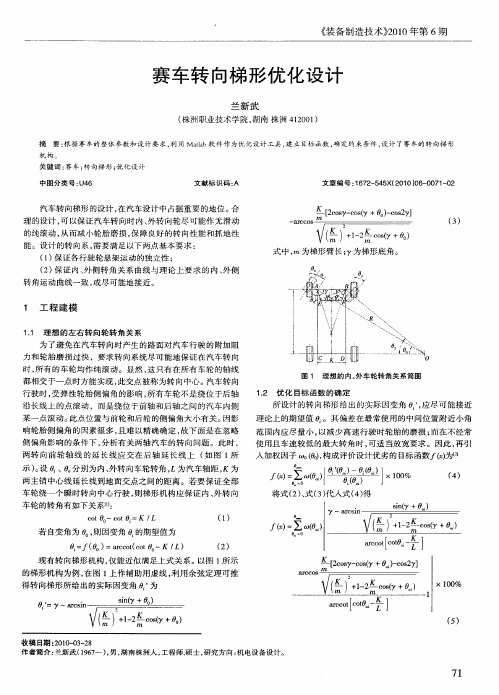
曼警 ●1
! 』 量 童圣
l¨ l
!
I f rc i n c c q =  ̄c r g u ̄t o i . e ] l a t ) y ( i2一 x I0 . . ̄ = 0s a= 2 O 18f f  ̄ . x 2 . m m
} |3一 c s f 1 卜 c 0 m n 驰 “j o , c ,扭( , t+蠊 l , 缸
3 外观 结构 设计
在设 计汽油发电机组的外观结构时 ,我们 充分考虑和 追 求产品的差异化 。产 品差异化 , 是增强产 品竞争 力、 占领市 场
L 5 0 Y单相 汽油发 电机 组在与 同类 发电机组相 比 ,具有 W5 0 C
性 能优越 、 外观精美等 优点 , 是一款具有相 当市场竞争力 的汽 油发 电机组 产品。该款发 电机组 自上市 以来 , 深受客户欢迎 ,
式中 , 为最小传 动角 , 6 为设计变量 /及 7的函数1 7 / , " 2 1 。
在 M TA A L B软件上 编辑 目标 函数 的优化 约束 条件 的 M 7 2
赛 车优化前后理 想和实际 的汽车左 右车轮转角 的关 系 曲 线如 图 6所示 , 当外轮转 角为虽大 2 。时 。 2 出现最大理论 与实 际 A k r n转角偏差 , 38 , eema 为 .。 存在轮胎 的磨 损 , 但是在外 轮
( 下转 第 8 0页 )
Eq ime t up n Ma ua t n e h oo yNo6,01 n fcr gT c n lg . 2 0 i
到 2 0h 0 。
襄 3 可 靠性、 耐久性试验表
的一种有效方式 。朗沃德 L 5 0 Y单相汽油发电机组 由汽 W5 0 C 油发动机 、 单相发 电机 、 框架 、 面板 、 电器 仪表 、 隔热板 、 减震软 垫等零部 件组成 , 减震 性能和发 电机隔热效果非常好 , 而且采 用 目前市场上 少有的圆弧 面板 设计 ,把一些影 响外 观的螺栓 紧固件完全 隐藏起来 , 工精细 , 做 外型饱满 、 圆滑 , 获得中华 并 人 民共和 国国家知识产权局两项专利保护 。
汽车转向梯形机构在不同目标函数下的优化2010

设 计与研 究汽车转向梯形机构在不同目标函数下的优化廖林清,王金龙,谢 明,屈 翔,张 君(重庆理工大学重庆汽车学院,重庆400050)Optimization Design of t he Steering Trapezoidal Mechanism wit h Different ObjectiveFunctionsL IAO Lin 2qing ,WANG Jin 2long ,XIE Ming ,QU Xiang ,ZHANG Jun(Chongqing Automobile College ,Chongqing University of Technology ,Chongqing 400050,China ) 摘要:基于汽车转向梯形机构的平面模型,依据阿克曼原理,以外转向轮转角误差、转向中心误差Ⅰ、转向中心误差Ⅱ和转向前束误差建立4种目标函数,应用C ++Bulider6.0软件编译优化设计程序,结合优化设计实例,分析4种目标函数下的优化效果,结果表明以转向中心误差Ⅰ为目标函数最合理.关键词:转向梯形机构;目标函数;优化设计中图分类号:U463.4文献标识码:A文章编号:100122257(2010)022*******收稿日期:2009210219基金项目:重庆市科技攻关计划项目(CSTC ,2009AB6021)Abstract :According to t he Ackerman princi 2ple ,four kinds of objective f unctions including t he angular error of out side steering tire ,steering cen 2ter error Ⅰ,Ⅱ,steering toe 2in error are established based on t he planar model of t he steering trape 2zoidal mechanism in t his paper.The optimization result s under t he conditions of t he four kinds of objective f unctions are analyzed combined wit h op 2timized cases by using t he C ++Bulider6.0soft 2ware.The result s indicate t hat it ’s t he best solu 2tion when steering center error Ⅰis selected as t he objective f unction.K ey w ords :steering t rapezoidal mechanism ;objective f unction ;optimization design0 引言汽车转向梯形机构的设计对转向性能起决定性作用,在汽车设计中占重要地位,精确的转向梯形机构能够更好地满足阿克曼原理,保障良好的转向性能.转向梯形机构有整体式和断开式2种,当汽车前悬架采用非独立悬架时,采用整体式转向梯形机构.整体式转向梯形机构有结构简单,调整前束容易,制造成本低等优点[1].整体式转向梯形机构不满足阿克曼原理.汽车转向过程中,当内转向轮转过一个角度时,实际外转向轮转角与理论外转向轮转角间有误差,产生外转向轮转角误差;前轮转向中心会偏离后轮轴线,形成转向中心误差;转向前束角[2]不全为零,存在转向前束误差.目前对转向梯形机构的优化设计,目标函数有以下几种:以外转向轮的绝对误差的最大值或相对误差的极大值为目标函数[3],这种方法只考虑转向过程中的最大误差,不能对整个转向过程进行综合分析;以两转向轮轴线交点的运动轨迹为目标函数[4-5],这种方法需要将交点坐标值与轴距进行比较,才能得到优化结果,不够直观;以转向轮转角误差为目标函数[6-8],这种方法选择不同转向轮为自变量时得到的优化结果不同,并且优化后的转向梯形机构存在转角误差很小,但前轮转向中心偏离后轮轴线较远的不理想情况.本文以转向中心误差和转向前束误差建立目标函数,以整体式转向梯形机构的优化设计为例,对目标函数进行研究.1 整体式转向梯形机构优化设计的目标函数1.1 以外转向轮转角误差建立目标函数对于如图1所示的整体式转向梯形机构,传统的优化设计中常用外转向轮转角误差作为目标函数[1].设内转向轮转角α为自变量,外转向轮转角β为因变量.按照阿克曼原理可求得理论外转向轮转角β,从转向梯形机构的平面模型可推导出实际外转向轮转角β′.β′应尽可能接近β.由于小转角在使用中较频繁,大转角较少使用,所以引入加权系数ω(α).设x 为设计变量;αmax 为内转向轮的最大转角.由外转向轮转角误差建立的目标函数为:f (x )=∑αmaxα=0ω(α) arccosk -r cos (θ0-α)k 2+r 2-2k r cos (θ0-α)arccot cot α+kl+arccosr (1-2cos 2θ0)-k[cos (θ0-α)-2cos θ0]k 2+r 2-2kr cos (θ0-α)-θ0arccot cot α+kl-1×100%(1)图1 整体式转向梯形机构1.2以转向中心误差Ⅰ建立目标函数整体式转向梯形机构不满足阿克曼原理,在汽车转向时,前轮转向中心O 点不在后轮轴线上,如图2所示.此时,转向中心误差可以用O 点到后轮轴线的距离|O H |来表示.将|O H |记为转向中心误差Ⅰ,从图2可知:|O H |=kcot β-cot α-l(2)在整个转向过程中,转向中心误差Ⅰ的总和越小则表示梯形机构越好,同样引入加权系数ω(α),由转向中心误差Ⅰ建立的目标函数f (x )为:f (x )=∑αmaxα=0ω(α)‖O H ‖=∑αmax α=0ω(α)kcot β-cot α-l(3)1.3 以转向中心误差Ⅱ建立目标函数整体式转向梯形机构不满足阿克曼原理,在汽车转向时,两前轮在后轮轴线上的交点分别为O 1,O 2,如图2所示.转向中心误差也可以O 1,O 2在后轮轴线上的距离|O 1O 2|来表示.将|O 1O 2|记为转向中心误差Ⅱ,从图2可知:|O 1O 2|=l !(cot α-cot β)+k (4)在整个转向过程中,转向中心误差Ⅱ的总和越小则表示梯形机构越好,同样引入加权系数ω(α),由转向中心误差Ⅱ建立的目标函数为:f (x )=∑αmaxα=0ω(α)‖O 1O 2‖=∑αmax α=0ω(α)|l ・(cot α-cotβ)+k |(5)图2 转向中心1.4 以转向前束误差建立目标函数转向前束的定义:当满足阿克曼原理时,两前轮轴线与后轮轴线汇交于一点,此时转向前束角为0.当不满足阿克曼原理时,两前轮轴线的交点不在后轮轴线上.此时可以假想将内外转向轮回转轴线按相反方向偏移一个相等的角度Δθ,使转向轮回转轴线和后轮轴线三者交于一点,满足阿克曼原理,这个假想的偏移角度Δθ就是转向前束角[2].整体式转向梯形机构的转向前束如图3所示,则有内外转向轮转角的关系为:cot (β+Δθ)-cot (α-Δθ)=kl(6)从式(6)可得:Δθ=arccot (2+2B +A C )±(2+2B +A C )2+4(A -C )(A -B C )2(A -C )(7)A =cot β-cot α;B =cot β!cot α;C =k l在转向过程中,转向前束值越小说明梯形机构的误差越小,同样引入加权系数ω(α),由转向前束误差建立的目标函数为:f (x )=∑αmaxα=0ω(α)|Δθ|(8)图3 转向前束2 设计变量与约束条件的确定2.1 设计变量在汽车设计中,对转向梯形机构的设计主要是选择合适的梯形臂长度r 和梯形底角θ0,因此选取r 和θ0两个参数为设计变量.即x ={r ,θ0}(9)2.2 约束条件在转向过程中,其误差在最常使用的中间位置附近小转角范围内应尽量小,以减小高速行驶时轮胎的磨损;而在不经常使用且车速较低的最大转角时,可适当放宽要求.并且考虑到多数使用工况下转角θ0小于20°,且10°以内的小转角使用得更加频繁,因此取加权系数为:ω(α)=1.50°<α≤10°1.010°<α≤20°0.520°<α≤αmax(10)r 和θ0两个参数过小时,会使横拉杆上的转向力过大;当r 过大时,将使梯形布置困难;当θ0越大,梯形越接近矩形,f (x )值就越大.所以各设计变量的取值范围构成的约束条件为:r -r min ≥0r max -r ≥0θ0-θ0max ≥0(11)其中梯形臂长度r 常取为r min =0.11k 、r max =0.15k;梯形底角θ0min =70°.3 优化设计实例某种汽车的转向传动机构参数为:轴距l =4700mm ,两主销间的距离k =1480mm ,梯形臂长r =199.8mm ,梯形底角θ0=75.5°,内转向轮的最大转角αmax =42°.根据上述建立的目标函数、设计变量和约束条件,选用C ++Bulider6.0软件编译优化设计程序.对实例分别在4个目标函数下进行优化计算,得到优化前后的设计变量如表1所示,优化前后的误差曲线如图4所示.表1 优化前后的设计变量设计变量优化前优化后外转向轮转角误差转向中心误差Ⅰ转向中心误差Ⅱ转向前束误差梯形臂长度(mm )199.8162.8162.8162.8162.8梯形底角(°)75.575.674.174.376.7 从表1可以看出,整体式转向梯形机构优化设计时,选择的目标函数不同,得到的梯形底角的最优值不一致,梯形臂长度的最优值基本一致.所以选择不同的优化目标函数对梯形底角有影响,但对梯形臂长度基本没有影响.在转向梯形机构中,梯形底角的变化会改变内、外转向轮的转角关系以及前轮转向中心的运动轨迹,梯形臂长度直接影响转向梯形机构的布置,引起汽车转向性能的改变.图4 优化前后的误差曲线从图4可以看出,以外转向轮转角误差为目标函数优化后,误差值变化不大,优化效果不太明显;以转向中心误差Ⅰ为目标函数优化后,优化效果显著,而且转角小于20°的误差值都很小,转向效果最好;以转向中心误差Ⅱ为目标函数优化后,虽然误差的总和减小了,但转角大于10°的误差都比原来增大了;以转向前束误差为目标函数优化后,误差总和减小了,大转角范围内的误差也减小了,但20°转角附近的误差明显增大.所以4个目标函数中,以转向中心误差Ⅰ为目标函数,优化结果较理想.4 结束语通过以上分析和优化设计实例可知:选择的目标函数不同,求解的梯形底角的最优值不相同,梯形臂长度的最优值基本相同.4个目标函数中,传统的以外转向轮转角为目标函数,优化效果不明显.以转向中心误差Ⅰ为目标函数最合理,优化效果显著,优化后的转向梯形机构更精确,能够更好地满足阿克曼原理.参考文献:[1] 王望予.汽车设计[M ].北京:机械工业出版社,2004.[2] 吴晓建.齿轮齿条式转向机构转向特性研究[D ].重庆:重庆理工大学,2009.[3] 王国安,郝子军.轮式推土机转向梯形优化设计[J ].西安公路学院学报,1986,(9):89-112.[4] 周全申,等.车辆转向机构设计与分析[J ].河南工业大学学报(自然科学版),2006,(4):60-66.[5] Mitchell Wm C ,Staniforth Allan ,Scott Ian.Analysis ofackermann steering geometry [A ].Motorsports Engi 2neering Conference and Exhibition[C].USA.2006.[6] Leishman Robert ,Chase Kenneth.A new tool for de 2sign and analysis of optimized rack and pinion steering Mechanisms[C].USA ,2009.[7] 姚明龙,王福林.车辆转向梯形优化设计及其求解方法的研究[J ].机械设计与制造,2007,(5):24-26.[8] 陈朝阳,张代胜.汽车转向梯形最优化设计[J ].安徽工学院学报,1982,(3):28-36.作者简介:廖林清 (1966-),男,四川眉山人,教授,硕士研究生导师,主要从事现代设计法的教学与应用研究.挠性陀螺仪内外接头的质量控制贺新华,田梦君(西北工业大学机电学院,陕西西安710072)Quality Cont rol of t he J unction Between Inside and Out side of Flexible Gyro scopeHE Xin 2hu a ,TIAN meng 2jun(School of Mechanical Engineering ,Northwestern Polytechnical University ,Xi ’an 710072,China ) 摘要:从理论分析计算的角度,分析了关键尺寸(宽度和厚度)对内外挠性接头性能的影响,研究了困扰批生产的接头外观的控制等,保证了接头的质量,提高了接头加工效率和合格率,降低了生产成本.关键词:内外挠性接头;尺寸控制;外观控制中图分类号:T H123文献标识码:A文章编号:100122257(2010)022*******收稿日期:2009209203Abstract :In terms of t heoretical analysis ,t he key parameters (widt h and t hickness )impacting on t he performances of flexible junction and t he con 2t rol strategy which conf used batch p roduction were analyzed and t he result s were given at last.The st rategy not only assured t he ability of gyroscopebut also imp roved t he efficiency of processing and t he acceptance rate was improved.K ey w ords :flexible gyroscope ;size control ;ap 2pearance cont rol0 引言内外挠性接头是挠性陀螺仪的关键部位,它把飞轮转子与底座电机的驱动轴连接起来,是引起陀螺仪基本误差的元件[1].可以说挠性接头性能的好坏,从某种程度决定了整个陀螺仪性能的好坏.接头的尺寸,外观设计要求很严,材料价格昂贵,批量生产中,超差、报废较多,直接经济损失较大.挠性接头的品质因素F M 对接头的性能起决定作用,其与总漂移误差成反比,即F M 越大,表示精度越高,因此,为了提高陀螺仪的精度,应尽可能增大F M .由F M =(J Z +I e )/(2I e -I Z ),可知,F M 与陀。
(汽车行业)汽车转向梯形机构设计

(汽车行业)汽车转向梯形机构设计汽车转向梯形机构是汽车行业中非常重要的部件之一。
它将驾驶员的转向操作转换成前轮方向的运动,使车辆能够按照驾驶员的意愿进行转向。
因此,汽车转向梯形机构的设计非常重要,不仅需要考虑其机械结构的合理性,还需要考虑其动态特性和安全性能。
汽车转向梯形机构的设计要解决的一个重要问题是机构的传动比和传动精度问题。
传动比指的是驾驶员转动方向盘所能使车辆前轮转向的程度,而传动精度则是指机构传动过程中的误差大小。
通常情况下,传动比需要保证较大的转角与较小的转动力之间的关系,以提供足够的转向力,并使驾驶员的操作更为轻松顺畅。
传动精度则需要尽可能小,以确保转向的准确性和稳定性。
汽车转向梯形机构的设计需要考虑多个部件的合理组合和配置。
其中最主要的部件包括转向节、拉杆、摇臂、拉杆座等。
转向节是转向梯形机构的核心部件,它连接前轮和拉杆,并将前轮转向运动传递到拉杆上。
拉杆是连接前轮和转向节的杆状部件,摇臂则是连接转向节和转向柱的中间件。
拉杆座则是固定拉杆和转向柱的底座。
在设计汽车转向梯形机构时,还需要考虑到动态特性和安全性能。
动态特性主要指机构的响应速度、稳定性以及阻尼。
为了保证机构的响应速度和稳定性,一般需要提高机构的阻尼系数。
同时,还需要考虑防震和抗干扰能力,以确保机构在恶劣路况和异常干扰情况下能够正常运行。
安全性能则是汽车转向梯形机构最重要的考虑因素之一。
机构在运行过程中需要抵御较大的转向力和扭矩。
此外,在车辆发生碰撞时,转向梯形机构也需要能够提供足够的承载能力,以避免驾驶员和车辆受到过大的损伤。
在实际应用中,汽车转向梯形机构的设计需要满足多种使用条件和环境要求。
例如,机构必须在各种温度、湿度和油渍等环境下都能够正常工作,同时还要满足标准化和规范化的要求,以确保产品的质量和可靠性。
总之,汽车转向梯形机构的设计是汽车工程中至关重要的部分。
要实现合理的设计,需要考虑多种因素和要求,包括传动比、传动精度、机构的动态特性、安全性能、使用条件和环境要求等。
汽车整体式转向梯形机构优化设计

AU T0 瓶0 BI L E AI PLI ED TE C f { N OL OG Y
2 0 l 4 第3 期
2Ol4 N0.3
汽 车整体 式转 向梯 形机构 优化设计
刘旋 ,李腾 飞 ,郑帅广
( 长 安大 学 ,陕 西 西 安 7 1 0 0 6 4 )
Li u Xu a n , Li Te n gf e i , Zhe n g S h u a i g ua n g
( C h a n g ’ a n Un i v e r s i t y , S h a a n x i Xi ’ a n 7 1 0 0 6 4 1
上应始终交于一点 ( 即瞬时转 向中心) ,使各车轮在 侧转 向车轮转角, 为汽车轴距, 为两主销中心
作者简介: 刘旋 ,车辆工程硕士研究生。 研究方向:纯电动
客车。
2 9
汽车实用技术
2 0 1 4年第 3期
夹 角 ;称 的余角 为梯 形底角 ; m 为转 向梯 形臂 在 水平 面 的投 影长 度 ,即转 向梯形 的腰 长 ; b为转 向横 拉杆 长度 。由几何关 系得
转 向过程 中始 终处 于 纯滚 动状 态 ,从 而提 高 轮胎 使
引言
整 体 式转 向梯 形 是 由转 向横 拉 杆 、两 个 转 向梯 形 臂 和汽 车前 轴 组成 。其主 要 缺 点是 一侧 转 向轮 向 上 下 跳动 时 ,会 影 响到 另 一侧 转 向轮 的运 动 。这种
用寿 命 ,保 证汽 车操 纵 的轻便 性和 稳 定性 卜 。
Abs t r a c t : Th e pa p e r s t ud i e d o v e r a l l c a r s t e e r i n g t r a p e z o i d wi t h M TALAB t o h a v e a o p t i ma l d e s i g n whi c h e ns u r e d a l l t h e wh e e l s we r e t u ni r n g ro a u n d t h e s a me i n s t a n t a ne o u s c e n t e r a s s o o n a s p os s i b l e nd a a l s o t he wh e e l o f d i fe r e n t c i r c u mf e r e n c e we r e t u ni r ng ro a u n d a s a p u r e r o l l i n g mo t i o n wi t h o u t s l i d i n g .
汽车整体式转向梯形机构仿真计算与优化

汽车整体式转向梯形机构仿真计算与优化首先,需要进行操纵性能仿真计算。
操纵性能是指车辆在转向过程中的稳定性、准确性和操纵力的大小。
通过建立车辆动力学模型,可以模拟车辆在不同转向输入下的行驶状态,并计算车辆的操纵性能参数,如转向响应时间、转向幅度和操纵力矩等。
通过对不同转向梯形机构参数的变化进行仿真计算,可以评估梯形机构对操纵性能的影响,并进行优化设计。
其次,还需要进行力学性能仿真计算。
力学性能是指转向机构在不同工况下的强度、刚度和耐久性等。
通过建立转向机构的有限元模型,可以分析转向机构在不同工况下的应力、应变和位移等力学参数,评估转向机构的设计是否满足强度和刚度要求,并进行优化调整。
同时,还可以通过应用疲劳分析方法,预测转向机构在长期使用过程中的损伤、疲劳寿命和可靠性等问题,以提高整体转向机构的耐久性。
最后,需要进行优化设计。
在进行仿真计算的基础上,可以通过参数优化和结构优化方法,对转向机构的参数和结构进行调整和改进。
例如,通过对齿条、滚珠丝杠、主动齿轮和从动齿轮等关键部件的几何参数进行优化,可以减小滚动摩擦和间隙,提高转向机构的机械效率和动力传递精度。
同时,还可以通过改变转向机构的布局和材料选择,减少转向机构的质量,并提高其刚度和强度,从而提升整体转向机构的性能。
综上所述,汽车整体式转向梯形机构的仿真计算与优化是确保汽车操纵性和稳定性的重要环节,能够通过操纵性能仿真计算、力学性能仿真计算和优化设计方法,对转向机构的性能进行评估和改进,提高汽车整体转向梯形机构的性能和可靠性。
齿轮齿条式转向器双梯形转向机构的优化设计
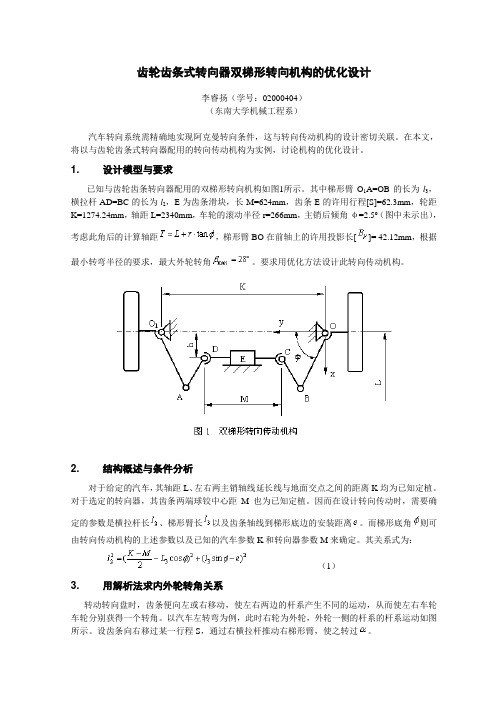
齿轮齿条式转向器双梯形转向机构的优化设计李睿扬(学号:02000404)(东南大学机械工程系)汽车转向系统需精确地实现阿克曼转向条件,这与转向传动机构的设计密切关联。
在本文,将以与齿轮齿条式转向器配用的转向传动机构为实例,讨论机构的优化设计。
1.设计模型与要求已知与齿轮齿条转向器配用的双梯形转向机构如图1所示。
其中梯形臂O1A=OB的长为l3,横拉杆AD=BC的长为l2,E为齿条滑块,长M=624mm,齿条E的许用行程[S]=62.3mm,轮距K=1274.24mm,轴距L=2340mm,车轮的滚动半径r=266mm,主销后倾角φ=2.5o(图中未示出),考虑此角后的计算轴距,梯形臂BO在前轴上的许用投影长[]= 42.12mm,根据最小转弯半径的要求,最大外轮转角。
要求用优化方法设计此转向传动机构。
2.结构概述与条件分析对于给定的汽车,其轴距L、左右两主销轴线延长线与地面交点之间的距离K均为已知定植。
对于选定的转向器,其齿条两端球铰中心距M也为已知定植。
因而在设计转向传动时,需要确定的参数是横拉杆长、梯形臂长以及齿条轴线到梯形底边的安装距离。
而梯形底角则可由转向传动机构的上述参数以及已知的汽车参数K和转向器参数M来确定。
其关系式为:(1)3.用解析法求内外轮转角关系转动转向盘时,齿条便向左或右移动,使左右两边的杆系产生不同的运动,从而使左右车轮车轮分别获得一个转角。
以汽车左转弯为例,此时右轮为外轮,外轮一侧的杆系的杆系运动如图所示。
设齿条向右移过某一行程S,通过右横拉杆推动右梯形臂,使之转过。
图2 转向传动机构几何关系如图2所示,取梯形右底角顶点O为坐标原点,则可导出齿条行程S与外轮转角的关系:(2)另外,由图可知:(3)而,(4)(5)将(4)、(5)表达式代入(3)式。
因此,利用(2)式便可求出对应于任一外轮转角的齿条行程S,再将S代入公式(3)(4)(5),即可求相应的内轮转角。
将上述公式结合起来便可将表示为的函数,记作。
汽车断开式转向梯形机构的优化设计
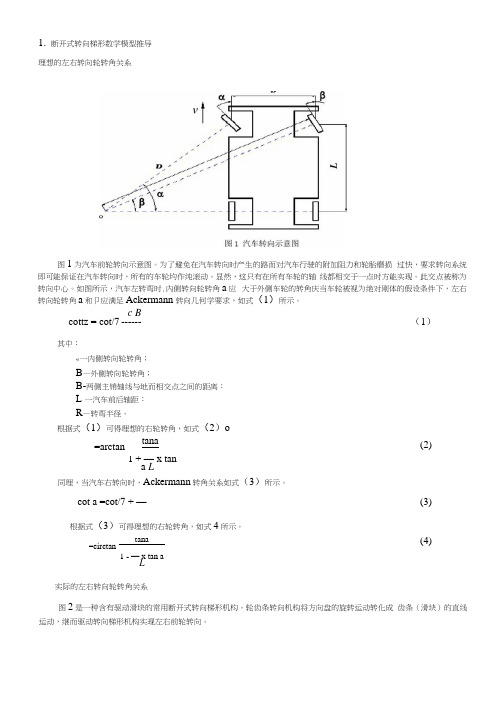
1.断开式转向梯形数学模型推导理想的左右转向轮转角关系图1为汽车前轮转向示意图。
为了避免在汽车转向时产生的路而对汽车行驶的附加阻力和轮胎磨损过快,要求转向系统即可能保证在汽车转向时,所有的车轮均作纯滚动。
显然,这只有在所有车轮的轴线都相交于一点时方能实现。
此交点被称为转向中心。
如图所示,汽车左转弯时.内侧转向轮转角a应大于外侧车轮的转角庆当车轮被视为绝对刚体的假设条件下,左右转向轮转角a和卩应满足Ackermann 转向几何学要求,如式(1)所示。
c Bcottz = cot/7 ------ (1)其中:«一内侧转向轮转角;B—外侧转向轮转角;B-两侧主销轴线与地而相交点之间的距离:L 一汽车前后轴距:R—转弯半径。
根据式(1)可得理想的右轮转角,如式(2)otana (2) =arctan1 + — x tana L同理,当汽车右转向时,Ackermann转角关系如式(3)所示。
(3)cot a =cot/7 + —根据式(3)可得理想的右轮转角,如式4所示。
tana(4)=circtan1 - — x tan aL实际的左右转向轮转角关系图2是一种含有驱动滑块的常用断开式转向梯形机构。
轮齿条转向机构将方向盘的旋转运动转化成齿条(滑块)的直线运动,继而驱动转向梯形机构实现左右前轮转向。
图中:厶一转向机齿条左右球较中心的距离;L 2 一左右横拉杆的长度;厶一左右转向节臂的长度:厶•一车轮中心至转向主销的距离:S] —转向齿条从中心位置向左的位移量: s 2 一转向齿条从中心位宜向左的位移量:y —转向齿条左右球狡中心连线与左右转向主销中心连线之偏距,图示位置取正值,反之取负值: S 。
一直线行驶时,转向齿条左球钱中心和左转向主销的水平距离:一转向节骨与汽车纵轴线的夹角。
运用余弦泄理和三角函数变换公式,经推导可得: ______________________-Cv - S xcos a = cos (ZAOB + Z.BOY )= 一;----- - ------------2厶(丁 +尸)A 点的坐标值为:v CxS-yx>jA 2 + B 2-C 2B2x (/+r )2*…Cxy + SxyjA 2 + B 2-C 2 沧=_ ------------- —zn ----------2x (/+S') 其中:A = -2LyxS,B = _2厶xy,C = 15,-1^-y 2-~s\ F —表示转向齿条弐球钱中心和左转向主销中心的实际距藹,对于直线行驶时,g = S 。
- 1、下载文档前请自行甄别文档内容的完整性,平台不提供额外的编辑、内容补充、找答案等附加服务。
- 2、"仅部分预览"的文档,不可在线预览部分如存在完整性等问题,可反馈申请退款(可完整预览的文档不适用该条件!)。
- 3、如文档侵犯您的权益,请联系客服反馈,我们会尽快为您处理(人工客服工作时间:9:00-18:30)。
转向梯形的优化设计1.转向梯形机构概述 (3)2.整体式转向梯形结构方案分析 (3)3.整体式转向梯形机构优化分析 (4)4.整体式转向梯形程序编写 (7)5.转动传动机构强度计算 (12)6.转向梯形的优化结果 (13)7.转向梯形结构设计图形 (13)8.结论 (15)转向梯形机构优化设计方案一、转向梯形机构概述转向梯形机构用来保证汽车转弯行驶时所有车轮能绕一个瞬时转向中心,在不同的圆周上做无滑动的纯滚动。
设计转向梯形的主要任务之一是确定转向梯型的最佳参数和进行强度计算。
一般转向梯形机构布置在前轴之后,但当发动机位置很低或前轴驱动时,也有位于前轴之前的。
转向梯形有整体式和断开式两种,选择整体式或断开式转向梯形方案与悬架采用何种方案有联系。
无论采用哪一种方案,必须正确选择转向梯形参数,做到汽车转弯时,保证全部车轮绕一个瞬时转向中心行驶,使在不同圆周上运动的车轮,作无滑动的纯滚动运动。
同时,为达到总体布置要求的最小转弯直径值,转向轮应有足够大的转角。
二、整体式转向梯形结构方案分析图5.1 整体式转向梯形1—转向横拉杆 2—转向梯形臂 3—前轴整体式转向梯形是由转向横拉杆1,转向梯形臂2和汽车前轴3组成,如图5.1所示。
其中梯形臂呈收缩状向后延伸。
这种方案的优点是结构简单,调整前束容易,制造成本低;主要缺点是一侧转向轮上、下跳动时,会影响另一侧转向轮。
当汽车前悬架采用非独立悬架时,应当采用整体式转向梯形。
整体式转向梯形的横拉杆可位于前轴后或前轴前(称为前置梯形)。
对于发动机位置低或前轮驱动汽车,常采用前置梯形。
前置梯形的梯形臂必须向前外侧方向延伸,因而会与车轮或制动底板发生干涉,所以在布置上有困难。
为了保护横拉杆免遭路面不平物的损伤,横拉杆的位置应尽可能布置得高些,至少不低于前轴高度。
三、整体式转向梯形机构优化分析汽车转向行驶时,受弹性轮胎侧偏角的影响,所有车轮不是绕位于后轴沿长线上的点滚动,而是绕位于前轴和后轴之间的汽车内侧某一点滚动。
此点位置与前轮和后轮的侧偏角大小有关。
因影响轮胎侧偏角的因素很多,且难以精确确定,故下面是在忽略侧偏角影响的条件下,分析有关两轴汽车的转向问题。
此时,两转向前轮轴线的延长线应交在后轴延长线上,如图5-2所示。
设θi 、θo 分别为内、外转向车轮转角,L 为汽车轴距,K 为两主销中心线延长线到地面交点之间的距离。
若要保证全部车轮绕一个瞬时转向中心行驶,则梯形机构应保证内、外转向车轮的转角有如下关系:LKi o =-θθcot cot (1)图1 理想的内、外车轮转角关系简图若自变角为θo ,则因变角θi 的期望值为:)/cot(cot )(0L K arc f o i -==θθθ (2)现有转向梯形机构仅能近似满足上式关系。
以图所示的后置梯形机构为例,在图上作辅助用虚线,利用余弦定理可推得转向梯形所给出的实际因变角i 'θ为[])cos(212cos )cos(cos 2arccos )cos(21)sin(arcsin020020'θγγθγγθγθγγθ+-+⎪⎭⎫⎝⎛-+--+-+⎪⎭⎫⎝⎛+-=m K m K m Km K m K i (3)式中:m 为梯形臂长;γ为梯形底角。
所设计的转向梯形给出的实际因变角i 'θ,应尽可能接近理论上的期望值i θ。
其偏差在最常使用的中间位置附近小角范围内应尽量小,以减少高速行驶时轮胎的磨损;而在不经常使用且车速较低的最大转角时,可适当放宽要求。
因此,再引入加权因子)( θω0,构成评价设计优劣的目标函数为)(x f%100)()()()()(max1⨯⎥⎦⎤⎢⎣⎡-=∑=oi i oi i oi i i oi o oi x f θθθθθθθωθθ (4) 由以上可得:[]%100cot cot )cos(212cos )cos(cos 2arccoscot cot )cos(21)sin(arcsin)()(0200201max⨯⎥⎦⎤⎢⎣⎡-+-+⎪⎭⎫⎝⎛-+--⎥⎦⎤⎢⎣⎡-+-+⎪⎭⎫⎝⎛+-=∑=L K arc m K m K m KL K arc m K m K x f oi i oi i i oi o oi θθγγθγγθθγθγγθωθθ (5) 式中:x 为设计变量,⎥⎦⎤⎢⎣⎡=⎥⎦⎤⎢⎣⎡=m x x x γ21;θomax 为外转向车轮最大转角,由图2得 a D L -=2arcsinminmax o θ (6)式中,Dmin 为汽车最小转弯直径;a 为主销偏移距。
考虑到多数使用工况下转角θo 小于20°,且10°以内的小转角使用得更加频繁,因此取:⎪⎪⎩⎪⎪⎨⎧≤<≤<≤<=max205.020100.11005.1)(o o o o o θθθθθω (7)建立约束条件时应考虑到:设计变量m 及γ过小时,会使横拉杆上的转向力过大;当m 过大时,将使梯形布置困难,故对m 的上、下限及对γ的下限应设置约束条件。
因γ越大,梯形越接近矩形,值就越大,而优化过程是求的极小值,故可不必对γ的上限加以限制。
综上所述,各设计变量的取值范围构成的约束条件为:00min max min ≥-≥-≥-γγm m m m (8)梯形臂长度m 设计时常取在mmin=0.11K ,mmax=0.15K 。
梯形底角γmin=70°此外,由机械原理得知,四连杆机构的传动角δ不宜过小,通常取δ≥δmin =40°。
如图5-2所示,转向梯形机构在汽车向右转弯至极限位置时达到最小值,故只考虑右转弯时δ≥δmin 即可。
利用该图所作的辅助用虚线及余弦定理,可推出最小传动角约束条件为:02cos )cos (cos )cos(cos 2cos min max min ≥--++-K mo γγδθγγδ (9)式中:δmin 为最小传动角。
δmin=40°,故由式a D L o -=2arcsinminmax θ可知,δmin为设计变量m 及γ的函数。
由式(6)、式(7)、式(8)和式(9)四项约束条件所形成的可行域,如图3所示的几种情况。
图3b 适用于要求δmin 较大,而γmin 可小些的车型;图5-3c 适用于要求γmin 较大,而δmin 小些的车型;图3a 适用介于图3b 、c 之间要求的车型。
图3 转向梯形机构优化设计的可行域四、整体式转向梯形程序编写(1)优化编程所需数据:轴距:L=2775mm 轮距:K=1560mm 最小转弯半径:R=5300mm 转向梯形臂:m 计算可得底边长:L-2*a (2)function fuun .m 编辑过程 在MATLAB 窗口新建一个空白M 文件将下式输入function c=theatar()%建立主函数global options L b r a K thetamax cl cr fi0 %定义全局变量K=1638; %input('输入主销中心线间距(mm)'); %依次给予几个变量赋值L=3308; %input('输入轴距(mm)');thetamax=40; %input('输入外转向轮最大转角(度)');x(1)=175; %input('臂长(mm)');x(2)=74.5; %input('底角(度)');b=8; %input('内倾角(度)');r=2; %input('后倾角(度)');a=1; %input('外倾角(度)');thetamax=thetamax*pi/180; %单位转换,弧度与度数转变lb(1)=0.11*K; %设置上下限lb(2)=1.2217; %acot(K/(1.2*L));ub(1)=0.13*K;ub(2)=pi/2;fil=linspace(0,thetamax,61);lb=[lb(1),lb(2)];ub=[ub(1),ub(2)];x0=[x(1),x(2)];% A=[0.251 0.372];% b=[0.143];[y,fval]=fmincon('fuun',x0,[],[],[],[],lb,ub,[]);%利用工具箱中的x = fmincon(fun,x0,A,b,Aeq,beq,lb,ub,nonlcon)进行计算Y=y;%[y,resnorm]=lsqnonlin('fuun',x0,lb,ub,options) %betae(i) y = fmincon(fuun,x0,[],[],[],[],lb,ub) for i=1:61 %设置60个区域fil=linspace(0,thetamax,61);%betae(i)=acot(cot(fil(i))-(K/L));fi=fii(r*pi/180,b*pi/180);%以下将各公式单位转换,并代入公式dt=delta(r*pi/180,fii(r*pi/180,b*pi/180));%=dtd=Di(fii(r*pi/180,b*pi/180),a*pi/180,delta(r*pi/180,fii(r*pi/180,b*pi/180)));%=dMid_w=Ww(a*pi/180,delta(r*pi/180,fii(r*pi/180,b*pi/180)),Di(fii(r*pi/180,b*pi/180),a*pi/180,d elta(r*pi/180,fii(r*pi/180,b*pi/180))));%=wa1(i)=alfa(fi,d,fil(i),Mid_w);A(i)=K*cos(b*pi/180)-x(1)*cos(2*(b*pi/180))*cos(x(2)*pi/180+fil(i));B(i)=x(1)*sin(x(2)*pi/180+fil(i));C(i)=K*cos(b*pi/180)*cos(x(2)*pi/180+fil(i))-2*K*cos(b*pi/180)*cos(x(2)*pi/180)+2*x(1)*(cos(b* pi/180)^2)*(cos(x(2)*pi/180)^2)-x(1);fir(i)=abs(fiir(A(i),B(i),C(i),x(2)*pi/180));a2(i)=alfa2(fi,d,fir(i),Mid_w);cl(i)=acos((cos(lamta(d,fil(i)))-sin(a*pi/180)*sin(a1(i)))/(cos(a*pi/180)*cos(a1(i))))*180/pi;cr(i)=acos((cos(lamta(d,fir(i)))-sin(a*pi/180)*sin(a2(i)))/(cos(a*pi/180)*cos(a2(i))))*180/pi; betae(i)=acot(cot(cl(i)*pi/180)-(K/L));Aa(i)=K*cos(b*pi/180)-y(1)*cos(2*(b*pi/180))*cos(y(2)+fil(i));Ba(i)=y(1)*sin(y(2)+fil(i));Ca(i)=K*cos(b*pi/180)*cos(y(2)+fil(i))-2*K*cos(b*pi/180)*cos(y(2))+2*y(1)*(cos(b*pi/180)^2)*(c os(y(2))^2)-y(1);fira(i)=abs(fiir(Aa(i),Ba(i),Ca(i),y(2)));a2a(i)=alfa2(fi,d,fira(i),Mid_w);% cl(i)=acos((cos(lamta(d,fil(i)))-sin(a*pi/180)*sin(a1(i)))/(cos(a*pi/180)*cos(a1(i))))*180/pi; cr1(i)=acos((cos(lamta(d,fira(i)))-sin(a*pi/180)*sin(a2a(i)))/(cos(a*pi/180)*cos(a2a(i))))*180/pi; endplot(cl,betae*180/pi,'r',cl,cr,'b',cl,cr1,'--g');% plot(cl,cr1,'--b');axis([0,40,0,45]);xlabel('外转向轮输入角(单位:度)');ylabel('内转向轮输出角(单位:度)');title('右轮初始值实际转角-理想转角-优化值实际转角随左输入角的变化曲线');text( 2,38,'红线代表理想转角的变化曲线','FontSize',8,'backgroundcolor',[1 0.4 0.4]);text( 2,36,'蓝线代表实际转角的变化曲线','FontSize',8,'backgroundcolor',[0.4 0.4 1]);text( 2,34,'绿线代表优化后转角的变化曲线','FontSize',8,'backgroundcolor',[0.6 1 0.8]);hold onEnd%子函数,定义个变量的意义function lt=lamta(d,fil)lt=acos((cos(d))^2+(sin(d))^2*cos(fil));endfunction a1=alfa(fi,d,fil,w)a1=asin(-cos(fi)*cos(d)-sin(fi)*sin(d)*cos(fil-w));endfunction a2=alfa2(fi,d,fir,w)a2=asin(-cos(fi)*cos(d)-sin(fi)*sin(d)*cos(fir+w));endfunction d=Di(fi,a,dt)d=acos(-cos(fi)*sin(a*pi/180)-sin(fi)*cos(a*pi/180)*cos(dt));endfunction w=Ww(a,dt,d)w=asin(cos(a*pi/180)*sin(a*pi/180)/sin(d));endfunction dt=delta(r,fi)dt=asin(sin(r*pi/180)/sin(fi));endfunction fi=fii(r,b)fi=acos(cos(r*pi/180)*cos(b*pi/180));endfunction fir=fiir(A,B,C,fi0)fir=fi0-2*atan((B+(sqrt(A^2+B^2-C^2)))/(A-C));end附录二在同一文件下编辑theatar.m 进行绘图编辑function c=theatar()%主函数global options L b r a K thetamax cl cr fi0 %定义全局变量K=1638; %input('输入主销中心线间距(mm)'); %给予几个变量赋值L=3308; %input('输入轴距(mm)');thetamax=40; %input('输入外转向轮最大转角(度)');x(1)=175; %input('臂长(mm)');x(2)=74.5; %input('底角(度)');b=8; %input('内倾角(度)');r=2; %input('后倾角(度)');a=1; %input('外倾角(度)');thetamax=thetamax*pi/180; %单位转换lb(1)=0.11*K; %设置上下限lb(2)=1.2217; %acot(K/(1.2*L));ub(1)=0.13*K;ub(2)=pi/2;fil=linspace(0,thetamax,61);lb=[lb(1),lb(2)];ub=[ub(1),ub(2)];x0=[x(1),x(2)];% A=[0.251 0.372];% b=[0.143];[y,fval]=fmincon('fuun',x0,[],[],[],[],lb,ub,[]);Y=y;%[y,resnorm]=lsqnonlin('fuun',x0,lb,ub,options) %betae(i) y = fmincon(fuun,x0,[],[],[],[],lb,ub) for i=1:61 %设置60个区域fil=linspace(0,thetamax,61);% betae(i)=acot(cot(fil(i))-(K/L));fi=fii(r*pi/180,b*pi/180);%以下将各公式单位转换,并代入公式dt=delta(r*pi/180,fii(r*pi/180,b*pi/180));%=dtd=Di(fii(r*pi/180,b*pi/180),a*pi/180,delta(r*pi/180,fii(r*pi/180,b*pi/180)));%=dMid_w=Ww(a*pi/180,delta(r*pi/180,fii(r*pi/180,b*pi/180)),Di(fii(r*pi/180,b*pi/180),a*pi/180,d elta(r*pi/180,fii(r*pi/180,b*pi/180))));%=wa1(i)=alfa(fi,d,fil(i),Mid_w);A(i)=K*cos(b*pi/180)-x(1)*cos(2*(b*pi/180))*cos(x(2)*pi/180+fil(i));B(i)=x(1)*sin(x(2)*pi/180+fil(i));C(i)=K*cos(b*pi/180)*cos(x(2)*pi/180+fil(i))-2*K*cos(b*pi/180)*cos(x(2)*pi/180)+2*x(1)*(cos(b* pi/180)^2)*(cos(x(2)*pi/180)^2)-x(1);fir(i)=abs(fiir(A(i),B(i),C(i),x(2)*pi/180));a2(i)=alfa2(fi,d,fir(i),Mid_w);cl(i)=acos((cos(lamta(d,fil(i)))-sin(a*pi/180)*sin(a1(i)))/(cos(a*pi/180)*cos(a1(i))))*180/pi;cr(i)=acos((cos(lamta(d,fir(i)))-sin(a*pi/180)*sin(a2(i)))/(cos(a*pi/180)*cos(a2(i))))*180/pi; betae(i)=acot(cot(cl(i)*pi/180)-(K/L));Aa(i)=K*cos(b*pi/180)-y(1)*cos(2*(b*pi/180))*cos(y(2)+fil(i));Ba(i)=y(1)*sin(y(2)+fil(i));Ca(i)=K*cos(b*pi/180)*cos(y(2)+fil(i))-2*K*cos(b*pi/180)*cos(y(2))+2*y(1)*(cos(b*pi/180)^2)*(c os(y(2))^2)-y(1);fira(i)=abs(fiir(Aa(i),Ba(i),Ca(i),y(2)));a2a(i)=alfa2(fi,d,fira(i),Mid_w);%cl(i)=acos((cos(lamta(d,fil(i)))-sin(a*pi/180)*sin(a1(i)))/(cos(a*pi/180)*cos(a1(i))))*180/pi;cr1(i)=acos((cos(lamta(d,fira(i)))-sin(a*pi/180)*sin(a2a(i)))/(cos(a*pi/180)*cos(a2a(i))))*180/pi; end%绘制图像plot(cl,betae*180/pi,'r',cl,cr,'b',cl,cr1,'--g');% plot(cl,cr1,'--b');%定义各轴意义axis([0,40,0,45]);xlabel('外转向轮输入角(单位:度)');ylabel('内转向轮输出角(单位:度)');title('右轮初始值实际转角-理想转角-优化值实际转角随左输入角的变化曲线');%定义各曲线意义text( 2,38,'红线代表理想转角的变化曲线','FontSize',8,'backgroundcolor',[1 0.4 0.4]);text( 2,36,'蓝线代表实际转角的变化曲线','FontSize',8,'backgroundcolor',[0.4 0.4 1]);text( 2,34,'绿线代表优化后转角的变化曲线','FontSize',8,'backgroundcolor',[0.6 1 0.8]);hold onEnd%进行子函数定义function lt=lamta(d,fil)lt=acos((cos(d))^2+(sin(d))^2*cos(fil));endfunction a1=alfa(fi,d,fil,w)a1=asin(-cos(fi)*cos(d)-sin(fi)*sin(d)*cos(fil-w));endfunction a2=alfa2(fi,d,fir,w)a2=asin(-cos(fi)*cos(d)-sin(fi)*sin(d)*cos(fir+w));endfunction d=Di(fi,a,dt)d=acos(-cos(fi)*sin(a*pi/180)-sin(fi)*cos(a*pi/180)*cos(dt));endfunction w=Ww(a,dt,d)w=asin(cos(a*pi/180)*sin(a*pi/180)/sin(d));endfunction dt=delta(r,fi)dt=asin(sin(r*pi/180)/sin(fi));endfunction fi=fii(r,b)fi=acos(cos(r*pi/180)*cos(b*pi/180));endfunction fir=fiir(A,B,C,fi0)fir=fi0-2*atan((B+(sqrt(A^2+B^2-C^2)))/(A-C));end程序运行结果%100)()()()()(max1⨯⎥⎦⎤⎢⎣⎡-=∑=oi i oi i oi i i oi o oi x f θθθθθθθωθθ考虑到多数使用工况下转角θo 小于20°,且10°以内的小转角使用得更加频繁,因此取:五、转动传动机构强度计算1、转向拉杆⎪⎪⎩⎪⎪⎨⎧≤<≤<≤<=max 205.020100.11005.1)(o o o o o θθθθθω拉杆应该有较小的质量和足够的刚度。