机械制造技术课程设计推动架课程设计
推动架课程设计说明书

推动架课程设计说明书一、概述推动架是机械设备中常见的一种机构,主要用于将动力传递给目标对象。
本次课程设计旨在让学生了解推动架的基本原理、设计方法及应用,培养学生的实践能力和创新思维。
二、设计任务1. 设计一款推动架,能够承受一定的负载,并具有良好的传递性能。
2. 确定推动架的结构形式、零部件材质及选型。
3. 完成推动架的图纸绘制及说明。
4. 对推动架的性能进行评估。
三、设计过程1. 确定推动架的结构形式:推动架的基本结构形式有单轴推动架、双轴推动架等,根据实际需求和条件,我们选择了单轴推动架作为设计对象。
2. 计算推动架的承载能力:根据推动架的受力情况,计算出最大承载能力,以确保其能够承受预期的负载。
3. 选择零部件材质:根据实际工况和成本考虑,我们选择了铝合金作为推动架的零部件材质。
4. 零部件设计及选型:根据推动架的结构形式和承载能力,进行零部件的设计和选型,包括连杆、轴承、支架等。
5. 图纸绘制及说明:完成推动架的图纸绘制,包括零件图、装配图及尺寸标注等,并编写相应的说明文档。
6. 性能评估:通过模拟实验和实际测试,对推动架的性能进行评估,确保其能够满足预期的使用要求。
四、图纸及说明1. 图纸:推动架装配图、连杆零件图、轴承零件图等。
2. 说明:包括推动架的结构形式、工作原理、零部件选型及装配注意事项等。
五、总结本次推动架课程设计,通过理论学习和实践操作相结合的方式,使学生深入了解了推动架的基本原理、设计方法及应用。
同时,也锻炼了学生的动手能力和创新思维,为其今后从事相关领域的工作打下了坚实的基础。
六、建议与改进1. 在设计过程中,可以适当增加一些虚拟仿真技术的应用,以提高设计的效率和准确性。
2. 在材料选择上,可以考虑使用更轻质的材料,如钛合金或高强度塑料,以进一步提高推动架的性能和效率。
3. 在图纸绘制和说明编写方面,可以更加注重细节和准确性,以提高图纸的可读性和理解性。
4. 可以增加一些实际案例的分析和讲解,以帮助学生更好地理解和应用所学知识。
机械课程设计推动架dwg图

机械课程设计推动架dwg图一、教学目标本课程旨在通过机械课程设计,使学生掌握推动架DWG图的基本知识与绘制技巧。
具体目标如下:1.知识目标:使学生了解推动架的结构与功能,理解DWG图的基本概念与绘制方法。
2.技能目标:培养学生能够独立绘制推动架DWG图的能力,提高学生的空间想象力和绘图技巧。
3.情感态度价值观目标:培养学生对机械设计的兴趣,增强学生的创新意识和团队合作精神。
二、教学内容本课程的教学内容主要包括以下几个部分:1.推动架的结构与功能:介绍推动架的基本结构,理解其在工作中的作用和功能。
2.DWG图的基本概念与绘制方法:学习DWG图的基本元素,掌握绘制和使用推动架DWG图的技巧。
3.绘制推动架DWG图的实践操作:通过实际操作,训练学生独立绘制推动架DWG图的能力。
三、教学方法为了提高教学效果,我们将采用以下几种教学方法:1.讲授法:通过讲解推动架的结构与功能,使学生掌握基本知识。
2.案例分析法:分析实际案例,使学生更好地理解推动架DWG图的绘制方法。
3.实验法:让学生在实验室中亲自动手绘制推动架DWG图,提高其实际操作能力。
四、教学资源为了支持教学,我们将准备以下教学资源:1.教材:选用权威、实用的教材,为学生提供系统的学习材料。
2.参考书:提供丰富的参考资料,帮助学生拓展知识面。
3.多媒体资料:制作精美的课件,提高课堂趣味性。
4.实验设备:提供充足的实验设备,确保学生能够顺利进行实践操作。
5.在线资源:利用网络资源,为学生提供更多的学习资料和交流平台。
五、教学评估本课程的评估方式包括以下几个方面:1.平时表现:评估学生在课堂上的参与度、提问回答等情况,以考察其对课程内容的理解和掌握程度。
2.作业:布置适量的作业,评估学生的完成情况,以检验其对知识的应用和巩固能力。
3.考试:进行期中和期末考试,全面测试学生对课程知识的掌握程度。
评估方式要求客观、公正,能够全面反映学生的学习成果。
我们将根据学生的表现,给予及时的反馈和指导,帮助其提高。
机械制造技术课程设计---推动架课程设计

机械制造技术课程设计---推动架课程设计一、设计目的通过本课程设计,学生将掌握推动架的结构、工艺及数控加工技术的应用等知识和实践能力,使其具备推动架的加工能力,提高其工程实践能力和综合素质。
二、教学内容和要求1.推动架的设计和结构分析。
2.推动架的工艺分析和加工流程的制定。
3.推动架的CNC数控加工和质量控制。
4.课程设计要求:设计一套能够实现推动架负荷自动传递的机构,要求结构合理,稳定可靠,使用寿命长,能够满足不同工况下的工作需求。
三、教学方法1、理论授课和实践操作相结合,教师通过现场案例教学和讲课,让学生感受实践操作中的问题,提高学生的综合素质和实践能力。
2、通过小组合作的方式让学生分工合作,提高理论联系实际和解决问题的能力。
3、采用现代教育技术手段如数字化媒体等,加强教学互动性,提高教学效果。
四、教材和参考书目1、《机械制造基础》2、《数控机床加工工艺手册》3、《数控机床编程技术》4、《机械制造工艺学》5、《机械设计基础及其应用》五、教学进度及难点:第一周:推动架的结构分析及工艺分析主要内容:了解推动架的结构及工艺分析:包括传递动力的机械和液压传动系统的设计原理,工作原理和优化方法。
难点:掌握推动架的结构,包括动力传递系统和工作原理分析。
第二周:推动架CAD设计主要内容:掌握CAD绘图技术,设计推动架的CAD图。
难点:根据前期的结构分析和工艺分析来进行CAD设计,学生需要综合运用CAD、力学和机械制造等知识来进行设计。
第三周:推动架的CAM编程主要内容:学会使用CAM编程软件进行推动架的编程。
难点:学习CAM编程软件的使用方法和CAM编程的流程。
第四周:推动架的数控加工主要内容:掌握数控加工的操作和方法,对推动架进行数控加工。
难点:学生需要充分理解数控编程,以及数控加工的原理和方法,根据CAM编程得到的程序进行加工。
第五周:推动架的组装和调试主要内容:了解推动架的组装和调试及质量控制。
难点:拆卸和装配操作要求准确,需要了解推动架的性能指标,进行质量控制。
机械制造技术课程设计推动架课程设计报告书

课程设计说明书设计课题:推动架加工工艺及夹具设计学生:学号:班级:机械指导教师:年月1.1.1推动架加工工艺及夹具设计的任务书容:1. 零件图 (1)2. 毛坯图 (2)3. 机械加工工艺过程综合卡片 (3)4. 夹具装配图 (4)5. 夹具零件图 (5)6. 课程设计说明书 (6)原始资料: Q=4000台/年, n=1台,班级学号:机械:指导老师:年月目录一零件分析————————————————1二零件工艺规程设计———————————————1 1 确定零件生产类型————————————————1 2选择毛坯、确定毛坯尺寸、设计毛坯图——————————1 3选择加工方法制定加工工艺路线—————————————2 4工序设计—————————————————————4 5确定切削用量基本时间—————————————————6三夹具设计————————————————16 四设计小结————————————————18五参考文献————————————————18 附1机械加工工艺过程卡片附2机械加工工序卡片一、零件的分析(一)、零件的功用题目所给的零件是B6065牛头刨床推动架,是牛头刨床进给机构的中小零件,φ32mm 孔用来安装工作台进给丝杠轴,靠近φ32mm 孔左端处一棘轮,在棘轮上方即φ16mm 孔装一棘爪,φ16mm 孔通过销与杠连接杆,把从电动机传来的旋转运动通过偏心轮杠杆使推动架绕φ32mm 轴心线摆动,同时拨动棘轮,带动丝杠转动,实现工作台的自动进给。
(二)、零件的工艺分析由零件图可知,其材料为HT200,该材料为灰铸铁,具有较高强度,耐磨性,耐热性及减振性,适用于承受较大应力和要求耐磨零件。
(零件图见附图1)由零件图可知,φ320.0270+mm 、φ160.033+mm 的中心线是主要的设计基准和加工基准。
该零件的主要加工面可分为两组:1、φ320.027+mm 孔为中心的加工表面这一组加工表面包括:φ320.027+mm 的两个端面及孔和倒角,φ160.019+mm 的两个端面及孔和倒角。
推动架课程设计说明书

目录.序言............................................. ........................ (2)第1章零件的分析 (2)1.2零件的作用................................. ............ ...... ......... . (2)1.2零件的工艺分析.................. ..................... ............ ... (2)第2章选择毛坯,确定毛坯尺寸,设计毛坯图 (3)第3章选择加工方法,制定工艺路线 (4)3.1机械加工工艺设计......... ........................ .................. (4)3.2确定工艺过程方案... ............ ............ .................. .. (5)第4章确定切削用量及基本时间............... . (5)4.1 工序Ⅰ切削用量及基本时间的确定......... .. (5)4.2工序Ⅱ切削用量及基本时间的确定......... . (7)4.3工序Ⅲ切削用量及基本时间的确定 (8)4.4工序Ⅳ切削用量及基本时间的确定...... ...... ..................... (9)4.5工序Ⅴ切削用量及基本时间的确定 (10)4.6工序Ⅵ的切削用量及基本时间的确定............ ............... ............ (11)4.7工序Ⅷ的切削用量及基本时间的确定 (12)4.8工序Ⅸ的切削用量及基本时间的确定...... ........................ ............ (13)4.9工序Ⅹ的切削用量及基本时间的确定......... .................. ............ (14)第5章夹具设计 (14)5.1定位基准的选择.................................... ............... ............ (14)5.2切削力和卡紧力计算 (15)5.3定位误差分析 (15)5.4夹具设计及操作的简要说明 (15)设计总结 (16)参考文献...................................................... ........................ (16)B6065牛头刨床机械加工工艺规程及工艺装备设计:序言大三上学期我们进行了《机械制造技术基础》课的学习,为了巩固所学知识,并且在我们进行毕业设计之前对所学各课程的进行一次深入的综合性的复习,也是一次理论联系实际的训练,因此,我们进行了本次课程设计就我个人而言,我希望能通过这次课程设计,了解并认识一般机器零件的生产工艺过程,巩固和加深已学过的技术基础课和专业课的知识,理论联系实际,对自己未来将从事的工作进行一次适应性训练,从中锻炼自己分析问题、解决问题的能力,为今后的工作打下一个良好的基础,并且为后续课程的学习大好基础。
推动架课程设计
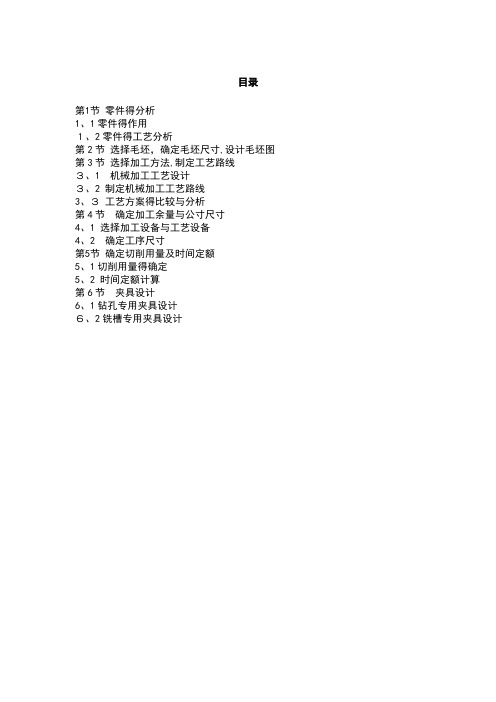
目录第1节零件得分析1、1零件得作用1、2零件得工艺分析第2节选择毛坯,确定毛坯尺寸,设计毛坯图第3节选择加工方法,制定工艺路线3、1 机械加工工艺设计3、2 制定机械加工工艺路线3、3工艺方案得比较与分析第4节确定加工余量与公寸尺寸4、1 选择加工设备与工艺设备4、2 确定工序尺寸第5节确定切削用量及时间定额5、1切削用量得确定5、2 时间定额计算第6节夹具设计6、1钻孔专用夹具设计6、2铣槽专用夹具设计第1节零件得分析1、1零件得作用据资料所示,可知该零件就是B6065牛头刨床推动架,就是牛头刨床进给机构得中小零件,φ32mm孔用来安装工作台进给丝杠轴,靠近φ32mm孔左端处一棘轮,在棘轮上方即φ16mm孔装一棘爪,φ16mm孔通过销与杠连接杆,把从电动机传来得旋转运动通过偏心轮杠杆使推动架绕φ32mm轴心线摆动,同时拨动棘轮,带动丝杠转动,实现工作台得自动进给。
零件图如下1、2零件得工艺分析由零件图可知,其材料为HT200,该材料为灰铸铁,具有较高强度,耐磨性,耐热性及减振性,适用于承受较大应力与要求耐磨零件。
由零件图可知,φ32、φ16得中心线就是主要得设计基准与加工基准。
该零件得主要加工面可分为两组:1、φ32mm孔为中心得加工表面这一组加工表面包括:φ32mm得两个端面及孔与倒角,φ16mm得两个端面及孔与倒角。
2、以φ16mm孔为加工表面这一组加工表面包括,φ16mm得端面与倒角及内孔φ10mm、M8-6H得内螺纹,φ6mm得孔及120°倒角2mm得沟槽。
这两组得加工表面有着一定得位置要求,主要就是:1、φ32mm孔内与φ16mm中心线垂直度公差为0、10;2、φ32mm孔端面与φ16mm中心线得距离为12mm。
由以上分析可知,对这两组加工表面而言,先加工第一组,再加工第二组。
由参考文献中有关面与孔加工精度及机床所能达到得位置精度可知,上述技术要求就是可以达到得,零件得结构工艺性也就是可行得。
推动架夹具课程设计

推动架夹具课程设计一、课程目标知识目标:1. 学生能理解推动架夹具的基本概念、分类及工作原理。
2. 学生掌握推动架夹具在设计过程中的关键参数计算方法。
3. 学生了解推动架夹具在工业生产中的应用及其重要性。
技能目标:1. 学生能够运用所学知识,进行简单的推动架夹具设计。
2. 学生通过课程学习,培养解决实际工程问题的能力,具备一定的创新设计意识。
3. 学生能够使用相关软件或工具,进行推动架夹具的模拟分析。
情感态度价值观目标:1. 学生对机械设计产生兴趣,提高对工程技术的热爱。
2. 学生培养严谨的科学态度,注重实践操作与理论知识的结合。
3. 学生在学习过程中,形成团队协作意识,学会尊重他人意见,提高沟通能力。
课程性质:本课程为机械设计相关课程,旨在让学生掌握推动架夹具的基本知识和设计方法。
学生特点:学生为高中二年级学生,具备一定的物理和数学基础,对实际工程问题有一定的好奇心。
教学要求:结合学生特点,注重理论与实践相结合,培养学生的动手能力和解决实际问题的能力。
通过课程学习,使学生在知识、技能和情感态度价值观方面得到全面提升。
教学过程中,将课程目标分解为具体的学习成果,便于教学设计和评估。
二、教学内容1. 推动架夹具概述- 夹具的定义、分类及作用- 推动架夹具的组成及工作原理2. 推动架夹具设计原理- 夹紧力计算- 夹具定位及导向设计- 传动系统设计3. 推动架夹具设计方法- 设计步骤与注意事项- 常用设计软件介绍- 设计案例分析4. 推动架夹具应用与优化- 工业生产中的应用场景- 夹具性能评价与优化- 创新设计理念5. 实践操作- 简单推动架夹具设计实践- 夹具模拟分析与优化- 团队协作完成设计项目教学内容安排:- 第一章:第1课时,了解夹具基本概念及分类- 第二章:第2-3课时,学习推动架夹具设计原理- 第三章:第4-5课时,掌握设计方法及软件应用- 第四章:第6课时,探讨夹具应用与优化- 第五章:第7-8课时,实践操作与项目完成教学进度:- 前四个课时,每周1课时,共计4周- 实践操作部分,每周2课时,共计2周教材章节对应:- 《机械设计基础》第三章:机械传动设计- 《机械设计基础》第四章:机械零件设计- 《机械设计实践》第五章:夹具设计实例分析教学内容确保科学性和系统性,结合课程目标,注重理论与实践相结合,培养学生的实际操作能力。
机械制造技术基础课程设计推动架加工工艺规程设计及钻孔专用夹具设计【全套图纸】
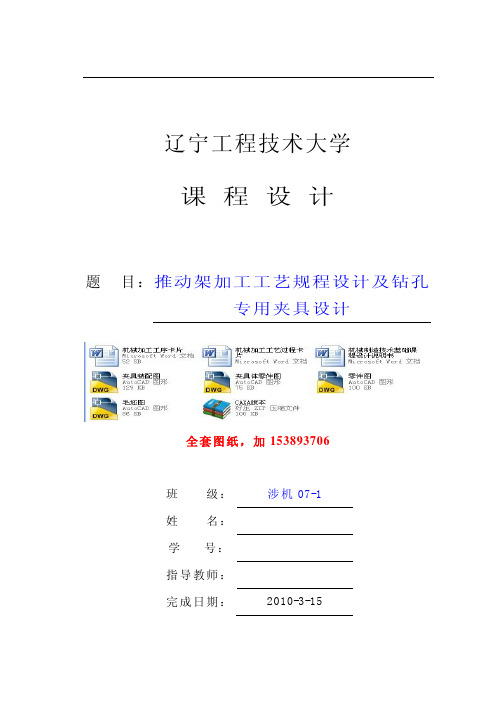
辽宁工程技术大学课程设计题目:推动架加工工艺规程设计及钻孔专用夹具设计全套图纸,加153893706班级:涉机07-1姓名:学号:指导教师:完成日期:2010-3-15一、设计题目推动架加工工艺规程设计及钻孔专用夹具设计二、原始资料(1)被加工零件的零件图(草图)1张(2)生产类型:中批或大批大量生产三、上交材料(1)被加工工件的零件图1张(2)毛坯图1张(3)机械加工工艺过程综合卡片1张(4)与所设计夹具对应那道工序的工序卡片1张(5)夹具装配图1张(6)夹具体零件图1张(7)课程设计说明书(约5000~8000字)1份四、进度安排(参考)(1)熟悉零件,画零件图2天(2)选择工艺方案,确定工艺路线,填写工艺过程综合卡片5天(3)工艺装备设计(画夹具装配图及夹具体图)9天(4)编写说明书3天(5)准备及答辩2天五、指导教师评语成绩:指导教师冷岳峰日期摘要介绍课程设计的主要内容及意义(机械制造技术基础课程设计是我们在学完了大学的全部基础课、专业基础课以及专业课后进行的。
这是我们在进行毕业设计之前对所学的各科课程一次深入的综合性总复习,也是一次理论联系实际的训练。
因此,他在我们的大学四年生活中占有重要的地位。
我这次设计的是推动架,有零件图、毛坯图、夹具装配图、夹具零件图各一张,机械加工工艺过程卡片和与所设计夹具对应那道工序的工序卡片各一张。
首先我们要熟悉零件,题目所给的零件是推动架。
了解了推动架的作用,接下来根据零件的性质和零件图上各端面的粗糙度确定毛坯的尺寸和机械加工余量。
然后我们再根据定位基准先确定精基准,后确定粗基准,最后拟定推动架的工艺路线图,制定该工件的夹紧方案,画出夹具装配图。
就我个人而言,我希望通过这次课程设计对自己未来将从事的工作进一步适应性的训练,希望自己在设计中能锻炼自己的分析问题、解决问题、查资料的能力,为以后的工作打下良好的基础。
由于能力有限,设计尚有很多不足之处,希望各位老师给予指导。
推动架课程设计书铣端面
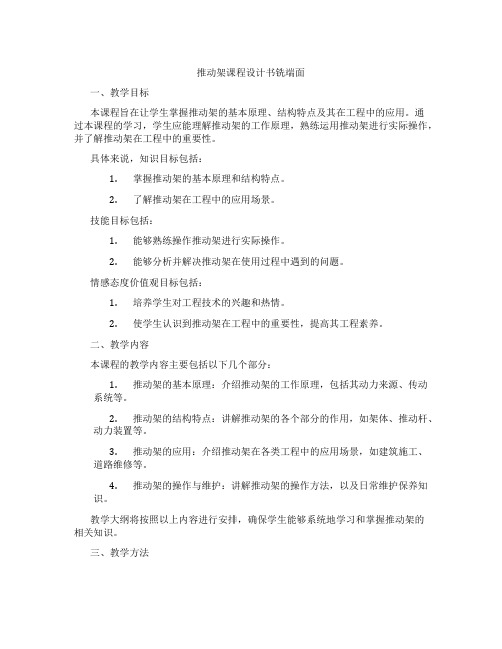
推动架课程设计书铣端面一、教学目标本课程旨在让学生掌握推动架的基本原理、结构特点及其在工程中的应用。
通过本课程的学习,学生应能理解推动架的工作原理,熟练运用推动架进行实际操作,并了解推动架在工程中的重要性。
具体来说,知识目标包括:1.掌握推动架的基本原理和结构特点。
2.了解推动架在工程中的应用场景。
技能目标包括:1.能够熟练操作推动架进行实际操作。
2.能够分析并解决推动架在使用过程中遇到的问题。
情感态度价值观目标包括:1.培养学生对工程技术的兴趣和热情。
2.使学生认识到推动架在工程中的重要性,提高其工程素养。
二、教学内容本课程的教学内容主要包括以下几个部分:1.推动架的基本原理:介绍推动架的工作原理,包括其动力来源、传动系统等。
2.推动架的结构特点:讲解推动架的各个部分的作用,如架体、推动杆、动力装置等。
3.推动架的应用:介绍推动架在各类工程中的应用场景,如建筑施工、道路维修等。
4.推动架的操作与维护:讲解推动架的操作方法,以及日常维护保养知识。
教学大纲将按照以上内容进行安排,确保学生能够系统地学习和掌握推动架的相关知识。
三、教学方法为了提高学生的学习兴趣和主动性,本课程将采用多种教学方法,如讲授法、讨论法、案例分析法和实验法等。
1.讲授法:用于讲解推动架的基本原理、结构特点和应用。
2.讨论法:学生针对推动架的操作和维护进行讨论,提高其问题解决能力。
3.案例分析法:通过分析实际工程案例,使学生更好地理解推动架在工程中的应用。
4.实验法:安排实验室实践,让学生亲手操作推动架,提高其实际操作能力。
四、教学资源为了支持教学内容和教学方法的实施,丰富学生的学习体验,我们将选择和准备以下教学资源:1.教材:选用权威、实用的推动架教材,为学生提供系统的理论知识。
2.参考书:提供相关领域的参考书籍,帮助学生拓展知识面。
3.多媒体资料:制作精美的PPT、视频等多媒体资料,生动展示推动架的原理和操作。
4.实验设备:准备充足的推动架实验设备,确保每个学生都能亲手操作。
推动架夹具设计课程设计

推动架夹具设计课程设计一、课程目标知识目标:1. 让学生掌握推动架夹具的基本结构、工作原理及其设计方法;2. 使学生了解并掌握推动架夹具设计中涉及的力学、材料力学、机械制图等相关知识;3. 培养学生对现有推动架夹具进行改进和创新的能力。
技能目标:1. 培养学生运用CAD软件进行推动架夹具设计的能力;2. 培养学生运用相关计算方法进行力学分析和材料选型的能力;3. 提高学生在团队协作中沟通、讨论、解决问题的能力。
情感态度价值观目标:1. 培养学生对机械设计产生兴趣,激发学生的创新意识和实践欲望;2. 培养学生严谨、认真、负责的工作态度,形成良好的职业素养;3. 培养学生关注工程实际,学会从实际出发,解决实际问题的方法。
课程性质分析:本课程属于机械设计领域,具有较高的实践性和应用性。
课程内容紧密结合实际工程案例,以培养学生的实际操作能力和创新思维为主要目标。
学生特点分析:学生处于高中阶段,具有一定的物理、数学基础,对机械设计有一定了解。
学生好奇心强,求知欲旺盛,但实践经验不足,需要通过实际操作来提高设计能力。
教学要求:1. 注重理论与实践相结合,提高学生的实际操作能力;2. 引导学生通过团队合作,培养沟通协调能力和解决问题的能力;3. 关注学生的个性化发展,激发学生的创新意识和潜能。
二、教学内容1. 推动架夹具基本结构及工作原理- 理解推动架夹具的组成部分及其功能- 掌握推动架夹具的工作原理和力学特性2. 推动架夹具设计相关理论知识- 学习力学、材料力学基本理论在夹具设计中的应用- 掌握机械制图基础知识,能读懂并绘制夹具图纸3. 推动架夹具设计方法及步骤- 学习夹具设计的流程和方法- 掌握CAD软件在夹具设计中的应用4. 力学分析和材料选型- 学习力学分析的基本方法,进行夹具强度、刚度分析- 掌握常见工程材料的性能特点及应用5. 推动架夹具设计实例分析- 分析实际工程案例,了解夹具设计的成功经验- 学习从实际出发,解决工程问题的方法6. 创新设计及团队合作- 培养学生创新思维,进行夹具设计的改进和创新- 学习团队协作,提高沟通协调和解决问题的能力教学内容安排和进度:第一周:了解推动架夹具基本结构及工作原理第二周:学习推动架夹具设计相关理论知识第三周:学习力学分析和材料选型第四周:掌握推动架夹具设计方法及步骤第五周:进行推动架夹具设计实例分析第六周:创新设计及团队合作实践教材章节及内容:第一章:推动架夹具概述第二章:夹具设计基础知识第三章:力学分析及材料选型第四章:夹具设计方法与步骤第五章:夹具设计实例第六章:创新设计及团队合作实践三、教学方法1. 讲授法:- 在讲解推动架夹具的基本结构、工作原理以及设计相关理论知识时,采用讲授法,结合教材内容,系统阐述相关概念、原理和方法;- 通过PPT、动画等教学辅助手段,生动形象地展示夹具的构造和动作原理,帮助学生理解和记忆。
推动架课程设计说明书

绪论本文是有关推动架工艺步骤的说明和机床夹具设计方法的具体阐述。
工艺设计是在学习机械制造技术工艺学及机床夹具设计后,在生产实习的基础上,综合运用所学相关知识对零件进行加工工艺规程的设计和机床夹具的设计,根据零件加工要求制定出可行的工艺路线和合理的夹具方案,以确保零件的加工质量。
据资料所示,推动架是牛头刨床进给机构中的小零件,其主要作用是把从电动机传来的旋转运动通过偏心轮杠杆使推动架绕其轴心线摆动,同时拨动棘轮,带动丝杠转动,实现工作台的自动进给。
在设计推动架机械加工工艺过程时要通过查表法准确的确定各表面的总余量及余量公差,合理选择机床加工设备以及相应的加工刀具,进给量,切削速度、功率,扭矩等用来提高加工精度,保证其加工质量。
第章引言机械制造业是国民经济的支柱产业,现代制造业正在改变着人们的生产方式、生活方式、经营管理模式乃至社会的组织结构和文化。
生产的发展和产品更新换代速度的加快,对生产效率和制造质量提出了越来越高的要求,也就对机械加工工艺等提出了要求。
在实际生产中,由于零件的生产类型、形状、尺寸和技术要求等条件不同,针对某一零件,往往不是单独在一种机床上用某一种加工方法就能完成的,而是需要经过一定的工艺过程。
因此,我们不仅要根据零件具体要求,选择合适的加工方法,还要合理地安排加工顺序,一步一步地把零件加工出来。
机械加工工艺规程制订1.1.1生产过程与机械加工工艺过程生产过程是指将原材料转变为成品的全过程。
它包括原材料的运输、保管于准备,产品的技术、生产准备、毛坯的制造、零件的机械加工及热处理,部件及产品的装配、检验调试、油漆包装、以及产品的销售和售后服务等。
机械工工艺过程是指用机械加工方法改变毛坯的形状、尺寸、相对位置和性质使其成为零件的全过程。
机械加工工艺过程的基本单元是工序。
工序又由安装、工位、工步及走刀组成。
规定产品或零件制造过程和操作方法等工艺文件,称为工艺规程。
机械加工工艺规程的主要作用如下:.机械加工工艺规程是生产准备工作的主要依据。
推动架专用夹具课程设计

推动架专用夹具课程设计一、课程目标知识目标:1. 学生能理解推动架专用夹具的基本结构及其工作原理;2. 学生能掌握推动架专用夹具在机械加工中的应用和操作步骤;3. 学生能了解推动架专用夹具在工业生产中的重要性。
技能目标:1. 学生能运用CAD软件进行简单的推动架专用夹具设计;2. 学生能通过实际操作,掌握推动架专用夹具的安装与调试方法;3. 学生能运用推动架专用夹具进行简单的机械加工,并分析加工过程中的问题。
情感态度价值观目标:1. 学生培养对机械设计和制造领域的兴趣,激发创新意识和动手实践欲望;2. 学生形成良好的团队合作精神,学会在团队中分享观点、交流经验;3. 学生认识到推动架专用夹具在提高生产效率和保障产品质量方面的重要性,增强责任感和使命感。
课程性质分析:本课程为机械制造与自动化专业课程,以实践操作为主,理论教学为辅,注重培养学生的动手能力和实际应用能力。
学生特点分析:学生为高年级学生,已具备一定的机械基础知识和技能,对专业知识有较高的学习热情。
教学要求:结合学生特点和课程性质,课程目标应注重理论与实践相结合,突出实用性,培养学生解决实际问题的能力。
通过具体的学习成果分解,使学生在课程结束后能够达到预定的技能和知识水平。
二、教学内容1. 推动架专用夹具的基本概念与分类:介绍夹具的定义、作用、分类及选用原则,结合教材第二章内容,使学生了解推动架专用夹具的基本知识。
2. 推动架专用夹具的结构与工作原理:详细讲解推动架专用夹具的结构组成、工作原理及性能特点,对应教材第三章内容,让学生掌握夹具的核心技术。
3. 推动架专用夹具的设计方法:教授CAD软件在夹具设计中的应用,结合教材第四章内容,指导学生完成简单夹具的设计任务。
4. 推动架专用夹具的安装与调试:分析夹具的安装步骤、调试方法及注意事项,依据教材第五章内容,培养学生实际操作能力。
5. 推动架专用夹具在机械加工中的应用:探讨夹具在机械加工中的应用实例,结合教材第六章内容,使学生了解夹具在实际生产中的重要性。
推动架课程设计说明书
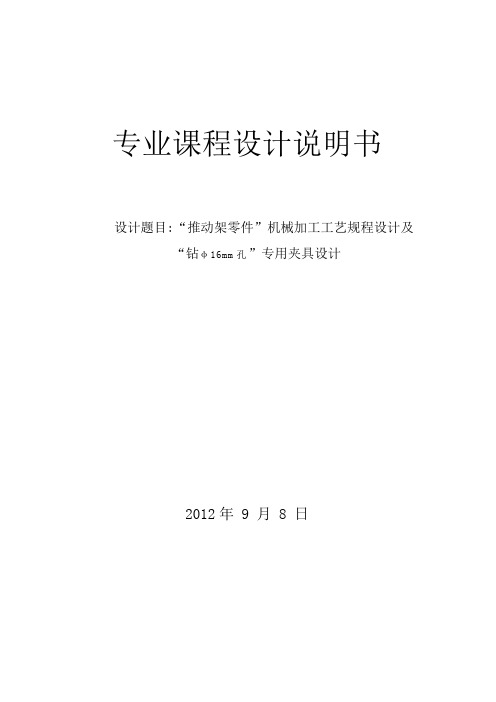
专业课程设计说明书设计题目:“推动架零件”机械加工工艺规程设计及“钻φ16mm孔”专用夹具设计2012年 9 月 8 日专业课程设计任务书题目:“推动架零件”机械加工工艺规程设计及“铣φ32mm端面”专用夹具设计加工件图纸:(见附页)生产纲领:年产量××件,批量生产目录前言一、工件的结构工艺性分析1.1推动架的技术要求推动架的技术要求见表1.11.2推动架工艺分析分析可知本零件材料为灰口铸铁,HT200。
该零件具有较高的强度,耐磨性,耐热性,减震性,适应于承受较大的应力,要求耐磨的零件。
刨床推动架具有两组工作表面,他们之间有一定的位置要求。
由零件图可知,φ32+0.027 0、φ16+0.019 0孔的中心线是主要的设计基准和加工基准。
该零件的主要加工面可分为两组:1.φ32mm孔为中心的加工表面这一组加工表面包括:φ32mm的两个端面及孔和倒角,φ16mm的两个端面及孔和倒角。
2.以φ16mm孔为加工表面这一组加工表面包括,φ16mm的端面和倒角及内孔φ10mm、M8-6H的内螺纹,φ6mm的孔及120°倒角2mm的沟槽。
这两组的加工表面有着一定的位置要求,主要是:1.φ32mm孔内与φ16mm中心线垂直度公差为0.10;2.φ32mm孔端面与φ16mm中心线的距离为12mm。
由以上分析可知,对这两组加工表面而言,先加工第一组,再加工第二组。
由参考文献中有关面和孔加工精度及机床所能达到的位置精度可知,上述技术要求是可以达到的,零件的结构工艺性也是可行的。
另外考虑到零件的精度不高可以在普通机床上加工。
二、加工工艺规程设计2.1 确定毛坯的制造形式推动架是一个结构较复杂的零件,要求材料要容易成型,切削性能好,同时要求强度要高,重要表面的表面硬度也要高,故选用铸铁材料HT200,铸铁材料是最常见的材料,其优点是:容易成型,切削性能好,价格低廉,且吸振性好。
为了得到较好的强度和表面硬度,可在加工过程中进行调质处理,淬火,同时为了消除内应力对工件的影响,可进行适当的人工时效处理(如果需要的话)。
机械制造技术课程设计推动架课程设计

课程设计说明书设计课题:推动架加工工艺及夹具设计学生姓名:学号:班级:机械指导教师:年月1.1.1 推动架加工工艺及夹具设计的任务书内容: 1. 零件图⋯⋯⋯⋯⋯⋯⋯⋯⋯⋯⋯⋯⋯⋯⋯⋯⋯ 1 张2.毛坯图⋯⋯⋯⋯⋯⋯⋯⋯⋯⋯⋯⋯⋯⋯⋯⋯⋯ 2 张3.机械加工工艺过程综合卡片⋯⋯⋯⋯⋯⋯⋯⋯ 3 张4.夹具装配图⋯⋯⋯⋯⋯⋯⋯⋯⋯⋯⋯⋯⋯⋯⋯ 4 张5.夹具零件图⋯⋯⋯⋯⋯⋯⋯⋯⋯⋯⋯⋯⋯⋯⋯ 5 张6.课程设计说明书⋯⋯⋯⋯⋯⋯⋯⋯⋯⋯⋯⋯⋯ 6 张原始资料:Q=4000 台/年, n=1 台,班级学号:机械姓名:指导老师:年月目录一零件分析————————————————1二零件工艺规程设计———————————————1 确定零件生产类型————————————————1 12 选择毛坯、确定毛坯尺寸、设计毛坯图——————————13 选择加工方法制定加工工艺路线—————————————24 工序设计—————————————————————45 确定切削用量基本时间—————————————————6三夹具设计————————————————16四设计小结————————————————18五参考文献————————————————18附 1 机械加工工艺过程卡片附 2 机械加工工序卡片一、零件的分析(一)、零件的功用题目所给的零件是 B6065 牛头刨床推动架,是牛头刨床进给机构的中小零件,φ32mm 孔用来安装工作台进给丝杠轴, 靠近 φ32mm 孔左端处一棘轮, 在棘轮上方即 φ16mm 孔装一棘爪, φ16mm 孔通过销与杠连接杆, 把从电动机传来的旋转运动通过偏心轮杠杆使推动架绕 φ32mm 轴心线摆动,同时拨动棘轮,带动丝杠转动,实现工作台的自动进给。
(二)、零件的工艺分析由零件图可知,其材料为 HT200,该材料为灰铸铁, 具有较高强度, 耐磨性,耐热性及减振性,适用于承受较大应力和要求耐磨零件。
机械课程设计推动架

机械课程设计推动架一、教学目标本课程旨在通过推动架的机械设计教学,让学生掌握以下知识目标:1.了解推动架的基本结构和工作原理。
2.掌握推动架的设计方法和步骤。
3.熟悉推动架的常用材料和加工工艺。
4.能够运用CAD软件进行推动架的二维和三维设计。
5.能够分析和解决推动架在实际工作中可能遇到的问题。
6.具备一定的创新能力和团队合作能力。
情感态度价值观目标:1.培养学生对机械设计的兴趣和热情。
2.培养学生具备工程伦理和社会责任感。
3.培养学生具备创新精神和团队合作精神。
二、教学内容本课程的教学内容主要包括以下几个部分:1.推动架的基本结构和工作原理。
2.推动架的设计方法和步骤。
3.推动架的常用材料和加工工艺。
4.推动架的CAD二维和三维设计。
5.推动架在实际工作中可能遇到的问题及解决方案。
6.创新设计和团队合作。
三、教学方法为了提高教学效果,本课程将采用以下教学方法:1.讲授法:讲解推动架的基本原理、设计方法和步骤等。
2.案例分析法:分析实际工作中的推动架案例,引导学生解决实际问题。
3.实验法:让学生动手操作,实际体验推动架的设计和制作过程。
4.讨论法:分组讨论,培养学生的团队合作能力和创新思维。
5.项目驱动法:布置相关设计项目,让学生在实践中掌握知识。
四、教学资源为了支持本课程的教学,我们将准备以下教学资源:1.教材:《机械设计基础》、《推动架设计手册》等。
2.参考书:相关学术论文、专利、设计手册等。
3.多媒体资料:教学PPT、视频教程、CAD软件教程等。
4.实验设备:推动架模型、CAD软件、测量工具等。
5.在线资源:相关、论坛、学习平台等。
通过以上教学资源,我们将为学生提供全面、丰富的学习体验,帮助学生更好地掌握推动架的机械设计知识。
五、教学评估本课程的教学评估将采用多元化评价方式,全面客观地评价学生的学习成果。
评估方式包括:1.平时表现:通过课堂参与、提问、小组讨论等环节,评估学生的学习态度和积极性。
- 1、下载文档前请自行甄别文档内容的完整性,平台不提供额外的编辑、内容补充、找答案等附加服务。
- 2、"仅部分预览"的文档,不可在线预览部分如存在完整性等问题,可反馈申请退款(可完整预览的文档不适用该条件!)。
- 3、如文档侵犯您的权益,请联系客服反馈,我们会尽快为您处理(人工客服工作时间:9:00-18:30)。
课程设计说明书设计课题:推动架加工工艺及夹具设计学生姓名:学号:班级:机械指导教师:年月1.1.1推动架加工工艺及夹具设计的任务书内容:1. 零件图……………………………………………1张2. 毛坯图……………………………………………2张3. 机械加工工艺过程综合卡片……………………3张4. 夹具装配图………………………………………4张5. 夹具零件图………………………………………5张6. 课程设计说明书…………………………………6张原始资料:Q=4000台/年,n=1台,班级学号:机械姓名:指导老师:年月目录一零件分析————————————————1二零件工艺规程设计———————————————1 1 确定零件生产类型————————————————1 2选择毛坯、确定毛坯尺寸、设计毛坯图——————————1 3选择加工方法制定加工工艺路线—————————————2 4工序设计—————————————————————4 5确定切削用量基本时间—————————————————6三夹具设计————————————————16 四设计小结————————————————18五参考文献————————————————18 附1机械加工工艺过程卡片附2机械加工工序卡片一、零件的分析(一)、零件的功用题目所给的零件是B6065牛头刨床推动架,是牛头刨床进给机构的中小零件,φ32mm 孔用来安装工作台进给丝杠轴,靠近φ32mm 孔左端处一棘轮,在棘轮上方即φ16mm 孔装一棘爪,φ16mm 孔通过销与杠连接杆,把从电动机传来的旋转运动通过偏心轮杠杆使推动架绕φ32m m 轴心线摆动,同时拨动棘轮,带动丝杠转动,实现工作台的自动进给。
(二)、零件的工艺分析由零件图可知,其材料为HT200,该材料为灰铸铁,具有较高强度,耐磨性,耐热性及减振性,适用于承受较大应力和要求耐磨零件。
(零件图见附图1)由零件图可知,φ320.0270+mm 、φ160.033+mm 的中心线是主要的设计基准和加工基准。
该零件的主要加工面可分为两组:1、φ320.027+mm 孔为中心的加工表面这一组加工表面包括:φ320.027+mm 的两个端面及孔和倒角,φ160.019+mm 的两个端面及孔和倒角。
2、以φ160.033+mm 孔为加工表面这一组加工表面包括,φ160.0330+mm 的端面和倒角及内孔φ100.10+mm 、M8-6H的内螺纹,φ6mm 的孔及120°倒角2mm 的沟槽。
这两组的加工表面有着一定的位置要求,主要是: 1、φ320.0270+mm 孔内与φ160.033+mm 中心线垂直度公差为0.10;2、φ320.0270+mm 孔端面与φ160.0330+mm 中心线的距离为12mm 。
由以上分析可知,对这两组加工表面而言,先加工第一组,再加工第二组。
由参考文献中有关面和孔加工精度及机床所能达到的位置精度可知,上述技术要求是可以达到的,零件的结构工艺性也是可行的。
二、零件工艺规程设计(一)、确定零件生产类型零件的生产纲领 N=Qn (1+a+b )其中,产品的年产量Q=4000台/年,每台产品中该零件的数量n=1件/台,零件备品率a=4%,零件的废品率b=1%。
Q=4000×1×(1+4%+1%)=4200件/ 年 从此结果可知,该零件为成批成产。
(二)选择毛坯,确定毛坯尺寸,设计毛坯图1、 选择毛坯根据零件材料确定毛坯为灰铸铁HT200,通过计算和查询资料可知,毛坯重量约为0.72kg。
生产类型为中小批量,可采用一箱多件砂型铸造毛坯。
由于φ32mm的孔需要铸造出来,故还需要安放型心。
此外,为消除残余应力,铸造后应安排人工时效进行处理。
2、确定加工余量、毛坯尺寸和尺寸由《机械制造技术基础课程设计指南》表5-1可知,查得该铸件的尺寸公差等级CT为8~12级,取CT=10级。
查表1-9确定各加工表面的总余量3、零件的毛坯图(详细见附图2)(三)选择加工方法,制定工艺路线1、基面的选择基面选择是工艺规程设计中的重要设计之一,基面的选择正确与合理,可以使加工质量得到保证,生产率得到提高。
否则,加工工艺过程会问题百出,更有甚者,还会造成零件大批报废,使生产无法进行。
2、粗基准的选择对一般的轴类零件来说,以外圆作为基准是合理的,按照有关零件的粗基准的选择原则:当零件有不加工表面时,应选择这些不加工的表面作为粗基准,当零件有很多个不加工表面的时候,则应当选择与加工表面要求相对位置精度较高大的不加工表面作为粗基准,从零件的分析得知,B6065刨床推动架以外圆φ50mm 作为粗基准。
3、精基准的选择精基准的选择主要考虑基准重合的问题。
选择加工表面的设计基准为定位基准,称为基准重合的原则。
采用基准重合原则可以避免由定位基准与设计基准不重合引起的基准不重合误差,零件的尺寸精度和位置精度能可靠的得以保证。
为使基准统一,先选择φ32mm 的孔和φ16的孔作为精基准。
4、零件表面加工方法的选择零件各表面的加工方法和方案选择,首先要保证加工表面的加工精度和表面粗糙度的要求,另外还要考虑生产率和经济方面的要求,在选择时,应根据各种加工方法的特点及其经济加工精度和表面粗糙度,结合零件的特点和技术要求,慎重决定。
(1) φ50mm 的外圆两端面保证尺寸450.080.25--mm ,表面粗糙度6.3 粗铣 (2) φ35mm 的外圆两端面保证尺寸20mm ,表面粗糙度2.5 粗铣——半精铣——精铣(3) 粗铣深9.5mm 宽6mm 的槽。
(4) 粗车φ27mm 的端面。
(5) 钻、扩、粗、精铰φ32mm 的孔,倒角45°。
(6) 钻φ10mm 的孔。
(7) 钻、扩、粗铰、精铰φ160.019+mm 孔,倒角45°。
(8) 钻、精铰螺纹孔φ6mm 的孔,攻丝M8-6H 。
(9) 钻、精铰φ6mm 的孔,锪120°的倒角。
(10)φ160.033+mm 的孔,采用先钻φ10的孔,然后反拉、扩、铰孔。
(11)拉沟槽R3。
5、制定工艺路线 工序方案工序1 铣φ32mm 孔和φ160.0190+mm 孔在同一基准的两个端面工序2 铣φ32mm 孔的端面、铣φ160.019+mm 孔的端面工序3 车φ27mm 端面工序4 铣深9.5mm 宽6mm 的槽 工序5 钻、扩、铰φ32mm ,倒角45°。
工序6 钻、扩、粗铰、精铰φ160.019+mm,倒角45°。
工序7 钻φ10mm 的通孔和反拉、扩、粗铰、精铰φ160.033+mm 孔,倒45°角;钻φ6mm 的孔,锪120°的倒角;钻螺纹孔φ6mm 的孔,攻丝M8-6H 。
工序8 拉沟槽R3。
工序9 钳工去毛刺工序10 终检工序11 入库(四)工序设计1、选择加工设备与工艺装备(1)选择机床根据不同的工序选择机床工序1、2、4是粗铣、半精铣。
各工序的工步数不多,选用X6132万能铣床。
工序3选用CA6140。
工序5、6、7选用用Z535立式钻床。
工序8选用L6110卧式拉床。
(2)选择夹具本零件除粗铣及钻孔等工序需要专用夹具外,其他各工序使用通用夹具即可。
(3)选择刀具,根据不同的工序选择刀具1.铣刀依据资料选择高速钢圆柱铣刀直径d=60mm,齿数z=10,及直径为d=50mm,齿数z=8及切槽刀直径d=6mm。
2.钻φ32mm的孔选用锥柄麻花钻。
+mm的孔。
倒角45°,选用3.钻φ6mm锪120°的倒角和钻、半精铰φ160.019专用刀具。
+mm钻孔。
刀具:选择高速钢麻4.车φ27mm的端面,φ10mm孔和φ160.033花钻,α=120°,45度车刀。
do=φ10mm,钻头采用双头刃磨法,后角5.钻螺纹孔φ6mm.攻丝M8-6H 用锥柄阶梯麻花钻,机用丝锥。
6.拉沟槽R3选用专用拉刀。
(4)选择量具本零件属于成批生产,一般情况下尽量采用通用量具。
根据零件的表面的精度要求,尺寸和形状特点,参考相关资料,选择如下:1.选择加工面的量具用分度值为0.05mm的游标长尺测量,以及读数值为0.01mm测量范围100mm~125mm的外径千分尺。
2.选择加工孔量具因为孔的加工精度介于IT7~IT9之间,可选用读数值0.01mm 测量范围50mm~125mm的内径千分尺即可。
3.选择加工槽所用量具槽经粗铣、半精铣两次加工。
槽宽及槽深的尺寸公差等级为:粗铣时均为IT14;半精铣时,槽宽为IT13,槽深为IT14。
故可选用读数值为0.02mm测量范围0~150mm的游标卡尺进行测量。
2、确定工序尺寸1、面的加工(所有面)根据加工长度的为50mm,毛坯的余量为4mm,粗加工的量为2mm。
根据《机械工艺手册》表2.3-21加工的长度的为50mm、加工的宽度为50mm,经粗加工后的加工余量为0.5mm。
对精度要求不高的面,在粗加工就是一次就加工完。
2、孔的加工1. φ32mm.毛坯为空心,通孔,孔内要求精度介于IT7~IT8之间。
查《机械工艺手册》表2.3-8确定工序尺寸及余量。
钻孔:φ31mm. 2z=0.75mm扩孔:φ31.75mm 2z=0.18mm粗铰:φ31.93mm 2z=0.07mm精铰:φ32H7+mm.2. φ160.019毛坯为实心,不冲孔,孔内要求精度介于IT7~IT8之间。
查《机械工艺手册》表2.3-8确定工序尺寸及余量。
钻孔:φ15mm. 2z=0.85mm扩孔:φ15.85mm 2z=0.1mm粗铰:φ15.95mm 2z=0.05mm精铰:φ16H7+mm的孔3. φ10、φ160.033毛坯为实心、不冲出孔,孔内要求精度介于IT8~IT9之间。
查《机械工艺手册》表2.3-8确定工序尺寸及余量。
钻孔:φ10mm反拉孔:φ15mm 2z=0.85mm扩孔:φ15.85mm 2z=0.10mm粗铰:φ15.95mm 2z=0.05mm精铰:φ16H84.钻螺纹孔M8毛坯为实心、不冲出孔,孔内要求精度介于IT8~IT9之间。
查《机械工艺手册》表2.3-8确定工序尺寸及余量。
钻孔:φ7.8mm 2z=0.16mm粗铰:φ7.96mm 2z=0.04mm精铰:φ8H7 5.钻φ6mm 孔毛坯为实心、不冲出孔,孔内要求精度介于IT8~IT9之间。
查《机械工艺 手册》表2.3-8确定工序尺寸及余量。
钻孔:φ5.8mm 2z=0.02mm 精铰:φ6H7(五)确定切削用量及基本时间切削用量包括背吃刀量a P 、进给量f 和切削速度v 。
确定顺序应该是a P 、f ,再确定v 。
工序1切削用量及基本时间的确定1切削用量本工序为铣φ32mm 孔和φ16mm 孔在同一基准上的两个端面,所选刀具为高速钢圆柱铣刀其直径为d=60mm ,齿数z=8。