加工精度与粗糙度
各种加工方法的经济精度和表面粗糙度

各种加工方法能够达到的尺寸的经济精度表1 孔加工的经济精度表2 圆锥形孔加工的经济精度表3 圆柱形深孔加工的经济精度表4 花键孔加工的经济精度表5 外圆柱表面加工的经济精度表6 端面加工的经济精度(mm)表7 用成形铣刀加工的经济精度(mm)注:指加工表面至基准的尺寸精度。
表8 同时加工平行表面的经刘精度(mm)注:指两平行表面距离的尺寸精度。
表9 平面加工的经济精度注:1 表内资料适用于尺寸<1m,结构刚性好的零件加工,用光洁的加工表面作为定位和测量基准。
2 端铣刀铣削的加工精度在相同的条件下大体上比圆柱铣刀铣削高一级。
3 细铣仅用于端铣刀铣削。
表10 公制螺纹加工的经济精度表11 花键加工的经济精度表12 齿形加工的经济精度各种加工方法能够达到的形状的经济精度表13 平面度和直线度的经济精度表14 圆柱形表面形状精度的经济精度注:形状精度等级的公差值见附表2、3。
表15 曲面加工的经济精度表16 在各种机床上加工时形状的平均经济精度各种加工方法所能够达到的相互位置的经济精度表17 平行度的经济精度表18 端面跳动和垂直度的经济精度表19 同轴度的经济精度表20 轴心线相互平行的孔的位置经济精度注:对于钻、卧镗及组合机床的镗孔偏差同样适用于铰孔。
表21 轴心线相互垂直的孔的位置经济精度注:在镗空间的垂直孔时,中心距误差可按上式相应的找正方法选用。
各种加工方法能够达到的零件表面粗糙度表22 各种加工方法能够达到的零件表面粗糙度各类型面的加工方案及经济精度表23 外圆表面加工方案表24 孔加工方案表25 平面加工方案——机械篇标准公差及形位公差附表1 标准公差值注:基本尺寸小于1mm时,无IT14至IT18。
13 22-4-25 10:32附表2 平面度、直线度公差值附表3 圆度、圆柱度公差值附表4 平行度、垂直度、倾斜度公差值附表5 同轴度、对称度、圆跳动、全跳动公差值参考文献1 《金属机械加工工艺人员手册》修订本上海科学技术出版社1981年2 《机械制造工艺学》顾崇衔等编著陕西科学技术出版社1982年3 《航空机械设计手册》第三机械工业部612所编1979年4 《机械制造工艺学课程设计简明手册》华中工学院机械制造工艺教研室编1981年5 《机械工程手册》第46篇机械工业出版社1981年6 《圆柱齿轮加工》上海科学技术出版社1979年切削用量切削用量的选择原则正确地选择切削用量,对提高切削效率,保证必要的刀具耐用度和经济性,保证加工质量,具有重要的作用。
普通车床的加工精度范围表

机械零部件用作不同的机械部位,车床加工精度也是不同的,与其匹配的加工形式和加工工艺也不同。
本文围绕介绍车、铣、刨、磨、钻、镗等常见的几种加工形式所能达到的加工精度。
一、车削工件旋转,车刀在平面内作直线或曲线移动的切削加工。
车削一般在车床上进行,用以加工工件的内外圆柱面、端面、圆锥面、成形面和螺纹等。
车削加工精度一般为IT8—IT7,表面粗糙度为1.6—0.8μm。
1)粗车力求在不降低切速的条件下,采用大的切削深度和大进给量以提高车削效率,但加工精度只能达IT11,表面粗糙度为Rα20—10μm。
2)半精车和精车尽量采用高速而较小的进给量和切削深度,加工精度可达IT10—IT7,表面粗糙度为Rα10—0.16μm。
3)在高精度车床上用精细修研的金刚石车刀高速精车有色金属件,可使加工精度达到IT7—IT5,表面粗糙度为Rα0.04—0.01μm,这种车削称为"镜面车削"。
二、铣削铣削是指使用旋转的多刃刀具切削工件,是高效率的加工方法。
适于加工平面、沟槽、各种成形面(如花键、齿轮和螺纹)和模具的特殊形面等。
按照铣削时主运动速度方向与工件进给方向的相同或相反,又分为顺铣和逆铣。
铣削的加工精度一般可达IT8—IT7,表面粗糙度为6.3—1.6μm。
1)粗铣时的加工精度IT11—IT13,表面粗糙度5—20μm。
2)半精铣时的加工精度IT8—IT11,表面粗糙度2.5—10μm。
3)精铣时的加工精度IT16—IT8,表面粗糙度0.63—5μm。
三、刨削刨削加工是用刨刀对工件作水平相对直线往复运动的切削加工方法,主要用于零件的外形加工。
刨削加工精度一般可达IT9—IT7,表面粗糙度为Ra6.3—1.6μm。
1)粗刨加工精度可达IT12—IT11,表面粗糙度为25—12.5μm。
2)半精刨加工精度可达IT10—IT9,表面粗糙度为6.2—3.2μm。
3)精刨加工精度可达IT8—IT7,表面粗糙度为3.2—1.6μm。
论机械零件的加工精度与表面粗糙度

论机械零件的加工精度与表面粗糙度摘要:机械产品的性能和使用寿命与组成产品的零件加工质量密切相关,零件的加工质量是保证产品质量基础,衡量零件加工质量的主要指标是加工精度和表面粗糙度。
零件的表面质量是机械零件加工质量的重要内容之一,机械零件的表面质量对零件使用时的耐磨性、配合精度、疲劳强度、抗腐蚀性等有很大的影响,提高加工表面的质量,对保证零件的使用性能、提高零件及其机器的寿命具有重要的意义。
本文对机械加工表面质量进行了分析,指出了影响机械加工表面质量的因素,并提出了提高机械加工表面质量的措施,对工程实践有一定的指导作用。
关键词:机械零件表面质量机械加工加工精度表面粗糙度机械零件的加工质量,除加工精度外,表面质量也是极其重要的一个方面。
任何机械加工方法所获得的已加工表面都不可能达到理想状态,总会存在一定程度的微观几何形状误差、划痕、裂纹、表面金相组织变化和表面残余应力等缺陷,这些缺陷会影响零件的使用性能、寿命、可靠性。
因此,机械加工既要保证零件的尺寸、形状和位置精度,又要保证机械加工表面质量。
机械加工表面质量,是指零件在机械加工后被加工面的微观不平度,也叫粗糙度,产品的工作性能、可靠性、寿命在很大程度上取决于主要零件的表面质量。
研究机械加工精度与表面粗糙度的关系,其目的就是为了掌握机械加工中各个工艺对加工表面质量影响的规律,以便利用这些规律来控制加工过程,最终达到改善产品质量、增强产品使用性能的目的。
1、影响机械零件质量的两个重要因素机械零件的机加工质量包含尺寸精度和表面质量,机械零件的表面质量又包含加工表面的几何特点和表面层的物理化学性能两个方面的内容。
1.1 加工精度加工精度是指零件经过加工后的尺寸、几何形状以及各表面的相互位置等参数的实际值与设计理想值相符合的程度,而它们之间的偏离程度就是加工误差,加工误差的大小即反映了加工精度的高低。
加工精度是衡量零件加工质量的主要指标,在机械加工过程中,会有很多因素影响工件的加工质量,如何使工件的加工达到质量要求,以及如何减少各种因素对加工精度的影响,就成为加工前必须考虑的问题。
机械加工中的表面粗糙度与加工精度分析

机械加工中的表面粗糙度与加工精度分析引言:在机械加工过程中,表面粗糙度和加工精度是两个关键参数。
表面粗糙度是指工件表面的不规则度,而加工精度则是衡量加工结果与设计要求的接近程度。
这两个参数直接影响着产品的质量、性能和寿命。
本文将分析机械加工中表面粗糙度与加工精度的关系,并探讨一些改善加工质量的方法。
一、表面粗糙度与加工精度的定义和测量方法1. 表面粗糙度的定义表面粗糙度是指工件表面的不平滑度或不规则度。
它是由加工过程中切削工具与工件表面摩擦及切削引起的微小凹凸所形成的。
表面粗糙度可以以数值形式表示,通常使用Ra(均方根粗糙度)或Rz(最大峰值粗糙度)进行表征。
越小的数值表示表面越光滑。
2. 加工精度的定义加工精度是指工件实际加工结果与设计要求的接近程度。
它通常用公差来表示,是加工过程中所能保持的最大形状偏差。
加工精度的标准可以根据具体的产品需求而定,如汽车制造中的零件加工精度要求较高,需要达到很小的公差。
3. 表面粗糙度的测量方法表面粗糙度的测量可以使用多种仪器和方法。
常见的测量仪器有表面粗糙度仪、激光扫描仪和电子显微镜等。
这些仪器可以测量出工件表面的纹理、高度和形状等参数,并根据国际标准对其进行评价和分类。
二、表面粗糙度与加工精度的关系1. 表面粗糙度对加工精度的影响表面粗糙度对加工精度有直接影响。
当工件表面粗糙度较大时,切削刀具与工件表面的接触面积会增大,切削力也会增加。
这样容易导致加工误差和形状偏差的增大,从而降低加工精度。
2. 加工精度对表面粗糙度的影响加工精度对表面粗糙度也有一定的影响。
在加工过程中,加工工艺参数的选择和控制是保证加工精度的关键。
如果加工参数选择不当,容易造成工件表面过度磨损或过度切削,从而导致表面粗糙度的增加。
三、改善加工精度与表面粗糙度的方法1. 选择合适的加工工艺与刀具在机械加工过程中,选择合适的加工工艺和刀具是提高加工精度和控制表面粗糙度的关键。
不同材料和工件形状适合不同的加工工艺和刀具。
零件的加工精度与表面粗糙度的关系

零件的加工精度与表面粗糙度的关系嘿,朋友们!今天咱们来聊聊零件加工精度和表面粗糙度这两个家伙,那可真是机械加工世界里的一对“活宝”。
你可以把加工精度想象成一个超级挑剔的美食家。
这个美食家呀,要求每道菜(零件)的配料比例、烹饪时间、火候大小等等都得精准到不能再精准,就像加工精度要求零件的尺寸、形状得精确到头发丝儿那么细的差别。
比如说,它就像那种要求蛋糕上的裱花每一朵都一模一样的糕点师,容不得半点差错。
而表面粗糙度呢?它就像是这个美食表面的那层“皮”。
如果加工精度是内在的精确要求,那表面粗糙度就是外在的“颜值”担当。
它要是粗糙得像砂纸,那这个零件就好比一个脸上长满疙瘩的人,看起来就不那么赏心悦目啦。
有时候,这俩家伙就像一对欢喜冤家。
加工精度一心想把零件打造得如同艺术品一样完美,每个细节都严丝合缝。
可表面粗糙度就像个调皮的小鬼,时不时地出来捣个乱。
就好比你精心打扮去参加舞会,结果一阵大风把你的头发吹得像个鸟窝,这个鸟窝就像是粗糙的表面,破坏了整体的精致感。
要是加工精度很高,表面粗糙度却很差,那就像一个穿着高级定制西装,脚下却踩着一双破草鞋的人,看起来特别滑稽。
反之,如果表面粗糙度很好,加工精度却不行,就像是一个徒有其表的花瓶,外表光滑亮丽,但是内在结构一塌糊涂,根本没法好好使用。
它们之间的关系就像是一场微妙的舞蹈。
加工精度领舞的时候,表面粗糙度就得紧紧跟上它的步伐。
如果加工精度向前迈了一大步,表面粗糙度却还在原地踏步,那这个零件的质量就会像一个瘸腿的马,跑起来摇摇晃晃的。
不过呢,要想让它们配合好也不是那么容易的事儿。
这就好比让两个性格迥异的人合作一样。
加工精度就像个严肃的老学究,整天念叨着各种标准和规则;而表面粗糙度呢,有时候像个没长大的孩子,随性得很。
但不管怎么说,在机械加工这个大舞台上,它们两个缺一不可。
只有当加工精度和表面粗糙度手拉手,和谐共处的时候,才能生产出既好用又好看的零件,就像一对完美搭档的超级英雄,拯救机械世界于“危难”之中呢。
粗加工、半精加工、精加工 国标 表面粗糙度

粗加工、半精加工、精加工国标表面粗糙度【主题】粗加工、半精加工、精加工国标表面粗糙度【导言】在工程制造领域,粗加工、半精加工、精加工是我们经常会遇到的工艺术语,而国标表面粗糙度则是评定加工质量的重要标准。
本文将对这些主题进行全面解读,帮助您更深入地理解工程制造中的精度和粗糙度要求。
一、粗加工、半精加工、精加工的定义和区别1. 粗加工:指在工件上去除余量,但不要求高精度和光洁度的加工工艺。
通常是为了消除初始形状和大小偏差,使工件成为半成品状态,为后续的半精加工或精加工提供基础。
2. 半精加工:介于粗加工和精加工之间的加工过程,既要求加工精度,又要求较高的表面质量。
通常需要在粗加工的基础上进行二次加工,以获得更高的尺寸精度和表面质量。
3. 精加工:指在半成品上进行的高精度、高光洁度的加工工艺。
其目的是满足产品的特定精度要求,使产品达到设计要求的形状和表面状态。
二、国标表面粗糙度参数及其意义1. Ra值:表面粗糙度平均值,通常用于评定表面的整体光洁度,Ra值越小,表面越光滑。
2. Rz值:通常称为最大高度,是指由表面轮廓上最高点到最低点之间的距离,反映了表面的不规则程度。
3. Rt值:最大毛坯高度,是指在测定长度内,最大的毛坯表面高度差,用于评定最大局部高度差。
这些国标表面粗糙度参数是工件表面质量的重要指标,对机械零件的密封性、耐磨性、传动精度等都有着重要的影响。
三、文章总结和回顾本文首先对粗加工、半精加工、精加工进行了定义和区别,帮助读者了解工件加工的不同阶段和要求;接着介绍了国标表面粗糙度参数及其意义,让读者对表面质量的评定有了更清晰的认识。
笔者在个人观点中指出,粗加工、半精加工、精加工在工程制造中具有重要意义,对工件的质量、精度和表面质量都有着不可替代的作用,而国标表面粗糙度则是这些工艺的重要评定标准。
希望读者在实际工程应用中能够充分重视这些关键要素,从而保证制造出更加精密和优质的产品。
通过本文的阅读,相信您对粗加工、半精加工、精加工和国标表面粗糙度已经有了更深入的理解。
常用加工精度对照表
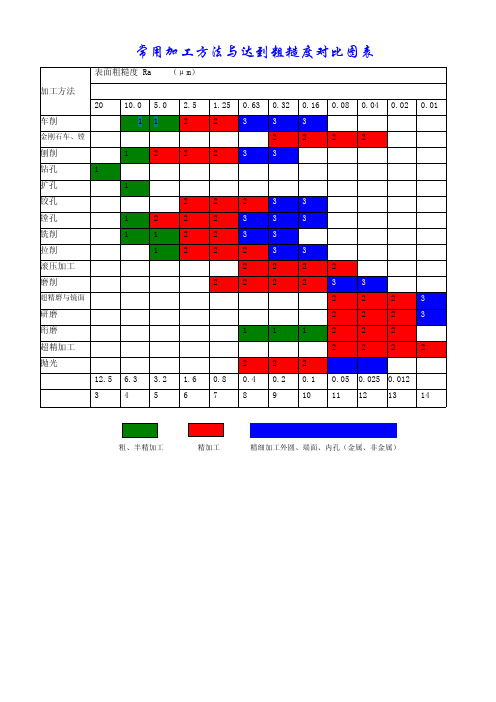
常用加工方法与达到粗糙度对比图表粗、半精加工精加工精细加工外圆、端面、内孔(金属、非金属)孔加工方案与经济公差序号加工方案经济公差等级表面粗糙度Ra(μm)适用范围1钻IT11-1320加工未淬火钢及铸铁的实心毛坯,也可用于加工有色金属(表面粗糙度稍差),孔径<(15-20)mm 2钻-铰IT8-9 5.0-2.53钻-粗铰-精铰IT7-8 2.5-1.254钻-扩IT1120-10.0同上,但孔径>(15-20)mm5钻-扩-铰IT8-9 5.0-2.56钻-扩-粗铰-精铰IT7 2.5-1.257钻-扩-机铰-手铰IT6-70.63-0.1608钻-(扩)-拉IT6-7 2.5-0.160大批大量生产(精度视)9粗镗(或扩孔)IT11-1320-10.0除淬火钢外各种材料,毛坯有铸出孔或锻出孔10粗镗(粗扩)-半精镗(精扩)IT8-9 5.0-2.511粗镗(扩)-半精镗(精扩)-精镗(铰)IT7-8 2.5-1.2512粗镗(扩)-半精镗(精扩)-精镗-浮动镗刀块精镗IT6-7 1.25-0.6313粗镗(扩)-半精镗-磨孔IT7-8 1.25-0.32主要用于加工淬火钢,也可用于不淬火钢,但不宜用于有色金属14粗镗(扩)-半精镗-粗磨-精磨IT6-70.32-0.16015粗镗-半精镗-精镗-金刚镗IT6-70.63-0.080主要用于精度要求较高的有色金属加工16钻-(扩)-粗铰-精铰-珩磨钻-(扩)-拉-珩磨粗镗-半精镗-精镗-珩磨IT6-70.32-0.040精度要求很高的孔17以研磨代替上述方案的珩磨IT6以上0.160-0.010平面加工方案与经济公差序号加工方案经济公差等级表面粗糙度Ra(μm)适用范围1粗车-半精车IT8-910-5.0端面2粗车-半精车-精车IT6-7 2.5-1.53粗车-半精车-磨削IT7-9 1.25-0.324粗刨(或粗铣)-精刨(或精铣)IT7-910.0-2.5一般不淬硬平面(端铣的表面粗糙度较好)5粗刨(或粗铣)-精刨(或精铣)-括研IT5-6 1.25-0.160精度要求较高的不淬硬平面批量较大时宜采用宽刃精刨方案6粗刨(或粗铣)-精刨(或精铣)-宽刃精刨IT6 1.25-0.327粗刨(或粗铣)-精刨(或精铣)-磨削IT6 1.25-0.32精度要求较高的淬硬平面或不淬硬平面8粗刨(或粗铣)-精刨(或精铣)-粗磨-精磨IT5-60.63-0.0409粗铣-拉IT6-9 1.25-0.32大量生产,较小的平面(精度视拉刀的精度而定)10粗铣-精铣-磨削-研磨IT5以上高精度平面外圆表面加工方案与经济公差序号加工方案经济公差等级表面粗糙度Ra(μm)适用范围1.粗车IT11-1380-20适用于淬火钢外的各种金属2.粗车-半精车IT8-910.0-5.03.粗车-半精车-精车IT6-7 2.5-1.254.粗车-半精车-精车-滚压(或抛光)IT6-70.32-0.0405.粗车-半精车-磨削IT6-7 1.25-0.63主要用于淬火钢,也可用于未淬火钢,但不宜加工有色金属6.粗车-半精车-粗磨-精磨IT5-60.63-0.1607.粗车-半精车-粗磨-精磨-超精加工(或轮式超精磨)IT50.160-0.0208.粗车-半精车-精车-金刚石车IT5-60.63-0.040主要用于要求较高的有色金属的加工9.粗车-半精车-粗磨-精磨-超精磨或镜面磨IT5以上0.040-0.010极高精度的外圆加工10.粗车-半精车-粗磨-精磨-研磨IT5以上0.160-0.010各种毛坯表面层厚度(mm)自由锻件模锻件铸件磁钢≤1.5磁钢≤1灰口铸铁1-4合金钢2-4合金钢≤0.5铸钢2-5。
数控加工精度如何计算公式

数控加工精度如何计算公式数控加工是一种高精度加工方法,能够实现复杂零件的高精度加工。
在数控加工中,精度是一个非常重要的指标,它直接影响着加工零件的质量和精度。
因此,了解如何计算数控加工精度是非常重要的。
本文将介绍数控加工精度的计算公式,并对其进行详细解析。
数控加工精度的计算公式主要包括以下几个方面,定位精度、重复定位精度、加工精度和表面粗糙度。
1. 定位精度的计算公式。
定位精度是指数控机床在进行定位移动时,其实际位置与期望位置之间的偏差。
定位精度的计算公式如下:定位精度 = |实际位置期望位置|。
2. 重复定位精度的计算公式。
重复定位精度是指数控机床在进行多次定位移动后,其重复定位的精度。
重复定位精度的计算公式如下:重复定位精度 = |最大偏差最小偏差|。
3. 加工精度的计算公式。
加工精度是指数控机床在进行加工时,其加工尺寸与设计尺寸之间的偏差。
加工精度的计算公式如下:加工精度 = |加工尺寸设计尺寸|。
4. 表面粗糙度的计算公式。
表面粗糙度是指加工表面的粗糙程度,通常用Ra值表示。
表面粗糙度的计算公式如下:表面粗糙度 = Ra值。
以上是数控加工精度的计算公式,下面我们将对这些公式进行详细解析。
首先是定位精度的计算公式。
定位精度是指数控机床在进行定位移动时,其实际位置与期望位置之间的偏差。
定位精度的计算公式是通过实际位置减去期望位置来得到的,其绝对值就是定位精度。
定位精度越小,表示机床的定位移动越准确。
接下来是重复定位精度的计算公式。
重复定位精度是指数控机床在进行多次定位移动后,其重复定位的精度。
重复定位精度的计算公式是通过最大偏差减去最小偏差来得到的,其绝对值就是重复定位精度。
重复定位精度越小,表示机床的多次定位移动的一致性越好。
然后是加工精度的计算公式。
加工精度是指数控机床在进行加工时,其加工尺寸与设计尺寸之间的偏差。
加工精度的计算公式是通过加工尺寸减去设计尺寸来得到的,其绝对值就是加工精度。
各种加工方法的加工经济精度及粗糙度

N5
3.2
0.4
微辨加工痕迹的方晌
听縻、金刖白牛刀的精牛、箱 绞、冷拉、拉刀加工、抛光等
N4
1.6
0.2
不可辨加工痕迹的方向
N3
0.8
0.1
最光面
暗光泽面
N2
0.4
0.05
亮光泽面
N1
0.2
0.025
镜状光泽面
精磨、研磨、抛光、超糖磨、
镜面磨削等
0.1
0.012
雾状镜面
0.05
镜面
N12
200
50
粗糙面
明显可见刀痕
锯断、粗车、粗铳、粗刨、
钻孔以及用粗纹锤刀、粗砂
轮等加工
Nil
100
25
可见刀痕
N10
50
12.5
微见刀痕
N9
25
6.3
半光面
可见加工痕迹
冷拉、精车、精绞、粗绞、粗
磨、刮削、粗拉刀加工等
N8
12.5
3.2
微见加工痕迹
N7
6.3
1.6
看不见加工痕迹
N6
6.3
0.8
光面
外圆加工中各种加工方法的加工经济精度及粗糙度
加工 方法
加工情况
加工经济 精度仃)
表面粗糙
度Ra(um)
车
粗车
12-13
10-80
半精车
10-11
2.5-10
精车
7-8
1.25-5
金刚石车(镜 面车)
5-6
0.02-1.25
铣
粗铣
12-13
10-80
半精铣
11-12
表面精度等级和粗糙度的关系

表面精度等级和粗糙度的关系表面精度等级和粗糙度的关系是一种非常重要的工程概念,尤其是在制造业领域,这一点更是如此。
表面精度等级和粗糙度是表面质量评估的两个主要参数,通过这两个参数可以评估表面的光洁度和光滑度。
在这篇文章中,我将讨论表面精度等级和粗糙度之间的关系,并探讨如何使用这些参数来评估表面质量。
1. 表面精度等级表面精度等级是表面质量的一种度量,用于描述表面的光洁度和精度。
它通常用数字表示,数字越小,表明表面质量越高。
表面精度等级定义了表面的光洁度和平坦度,并给出了与每个等级对应的允许的缺陷和不良表面。
2. 粗糙度粗糙度是指表面的凹凸度或不平坦度。
它是一个测量表面粗糙度的参数。
粗糙度值越大,表面越不平坦。
通过光学或机械手段可以测定粗糙度。
3. 表面精度等级和粗糙度的关系表面精度等级和粗糙度之间存在严格的关系。
表面精度等级是对表面质量的一个量化描述,而粗糙度则是用数值来描述表面的凹凸度或不平坦度。
这两个参数可以互相转换,通常通过一个统一的指标来表示表面质量,从而评估和比较不同表面的质量。
4. 如何评估表面质量在评估表面质量时,通常需要同时考虑表面精度等级和粗糙度这两个因素。
表面精度等级是用来量化表面的平坦度和光洁度,而粗糙度则是用数字来描述表面的凹凸度和不平坦度。
一个高质量的表面应该具有较低的表面精度等级和较低的粗糙度值。
在制造过程中,可以通过使用高精度机床和精确的加工工艺来获得高质量表面。
然而,对于一些不可避免的表面缺陷,比如瑕疵和划痕,通常可以通过增加表面精度等级和减小粗糙度值来减少它们的影响。
总体而言,表面精度等级和粗糙度是评估表面质量的两个关键指标,它们在制造过程中非常重要。
通过使用适当的测量工具和加工工艺,可以获得高质量的表面,从而提高产品性能和寿命。
各种加工方法的加工经济精度及粗糙度

8
刨
粗刨
11-13
5-20
半精刨
8-11
精刨
6-8
宽刀精刨
6
插
拉
粗拉
10-11
5-20
精拉
6-9
平磨
粗磨
8-10
半精磨
8-9
精磨
6-8
精密磨
6
刮
25x25
内点数
8-10
研磨
粗磨
6
精磨
5
精密磨
5
砂带磨
精磨
5-6
精密磨
5
滚压
7-10
精心搜集整理,只为你的需要
5-6
精珩
5
研磨
粗研
5-6
精研
5
精密研
5
挤
滚珠、滚柱扩孔器,挤压头
6-8
平面中各种加工方法的加工经济精度及表面粗糙度
加工方法
加工情况
加工经济精度(IT)
表面粗糙度Ra(um)
周铣
粗铣
11-13
5-20
半精铣
8-11
精铣
6-8
端铣
粗铣
11-13
5-20
半精铣
8-11
精铣
6-8
车
粗车
8-11
半精车
6-8扩Biblioteka 粗扩12-135-20
一次扩孔
11-13
10-40
精扩
9-11
铰
半精铰
8-9
精铰
6-7
手铰
5
拉
粗拉
9-10
一次拉孔
10-11
精拉
7-9
推
半精推
各种加工方法的加工经济精度及粗糙度

各种加工方法的加工经济精度及粗糙度加工方法是指将工件通过一定的手段和工具,经过一系列的操作和加工过程,使其达到预期的形状、尺寸和表面质量等要求的方法。
根据加工的具体要求和工件的特点不同,采用的加工方法也会有所差异。
下面将对常用的加工方法进行分析,包括加工经济、精度和粗糙度等方面。
1.切割加工切割加工是指通过切削刀具对工件进行切割和分离的加工方法,常见的有锯床、剪床、冲床等。
切割加工一般是用于中小批量生产,具有加工速度快、经济性好的特点。
但是由于切割刀具的形状和工艺的限制,其加工精度相对较低,且切割面往往存在毛刺等粗糙度问题。
2.车削加工车削加工是指利用车床上的刀具进行旋转切削的加工方法,适用于工件的外表面和内孔的现场加工。
车削加工具有加工精度高、表面质量好的特点,尤其适用于加工长度较长的工件。
但是车削加工一般速度较慢,且对车床的精度要求较高,加工成本较高。
3.铣削加工铣削加工是指通过铣床上的刀具进行切削的加工方法,适用于平面、曲面和螺纹等多种形状的加工。
铣削加工具有加工速度快、加工效率高的特点,能够实现多种加工方式,具有较高的经济性。
但是铣削加工对机床的刚性和稳定性要求较高,且铣削后的表面质量一般较差,需要进行后续处理。
4.电火花加工电火花加工(EDM)是指通过快速的电火花放电技术对工件进行加工的方法。
电火花加工具有非常高的精度和表面质量,能够加工出复杂的形状和细小的孔洞。
虽然电火花加工速度相对较慢,但是能够实现无模具、无切削力的加工方式,适用于高难度的工件加工。
然而,电火花加工一般需要进行后续的抛光处理,以达到更好的表面质量。
5.抛光加工抛光加工是指利用砂纸、磨料等工具将工件表面进行刮削和磨擦的加工方法,用于提高工件的表面光洁度和精度。
抛光加工具有较好的加工精度和表面质量,但是加工速度相对较慢,且需要一定的手工操作,劳动强度较大。
综上所述,不同的加工方法在加工经济、精度和粗糙度等方面存在不同的特点。
加工精度等级与粗糙度对照

加工精度等级与粗糙度对照说到加工精度和表面粗糙度,这可是个大话题啊!你瞧,很多人可能觉得这俩概念离自己很远,其实不然。
在我们的日常生活中,它们可是无处不在,像是生活中的调味品,恰到好处才行。
你想想,买个手机壳,表面光滑,拿在手里感觉特别舒服,回头一看,哎呀,这个加工精度得多高啊!就像是工匠们在打磨一块木头,要做到心中有数,手中有活儿,才能做出个精美的艺术品。
说到粗糙度,很多人可能会想,这个不就是表面不平滑吗?可不止如此哦。
粗糙度可分成好多等级,每个等级都有自己的“个性”。
例如,一级粗糙度,简直就像刚出生的小婴儿,光滑得让人忍不住想摸摸;而三级粗糙度,嘿,感觉就像你家那只调皮的小猫,毛毛糙糙的,有点儿不那么温柔。
这些表面特性,就像人一样,五花八门,百态千姿,各有千秋。
说到这里,有些朋友可能会问,那这精度和粗糙度到底有什么关系呢?我跟你说,这就像是谈恋爱,精度高的地方就像是彼此的默契,粗糙度则是生活中的小摩擦。
比如说,精度不够,零件可能就不那么契合,导致整体性能下降,简直是个大麻烦。
而如果粗糙度过高,那就像你们之间总有争吵,没办法和谐相处,影响得很。
让我们回到那些精密的机械设备。
它们的加工精度可谓是让人刮目相看,动辄就能达到微米级别,简直像是科学家们的玩具。
可是,若是粗糙度不合适,机器运转时可就会像人走路穿了双不合脚的鞋,磕磕绊绊的,不得劲。
你想象一下,整个车间的工人都在紧张忙碌,机器哐啷哐啷地响,结果最后却因为这粗糙度没处理好,浪费了多少时间和金钱,真是让人心疼啊。
不过,有时候我们也不能只盯着这些数字和等级。
就像人际关系,不仅要看外表的光滑,更要注重内在的交流和理解。
加工精度和粗糙度的对比,往往是在提醒我们,做事情不能只看表面。
表面光滑固然好,但内在的匹配和运转才是关键。
想要让生活过得更顺利,得找准自己的定位,和别人合拍,才能事半功倍。
嘿,聊到这儿,你是不是也在想,生活中有没有让你注意到的加工精度和粗糙度呢?比如说,早晨匆匆忙忙,做个早餐,切个菜,刀的锋利度和表面光滑度都得跟得上,才能切得利索,不然可就像是猫抓过的肉,乱七八糟的。
不同的加工方法可能达到的尺寸精度及表面粗糙度
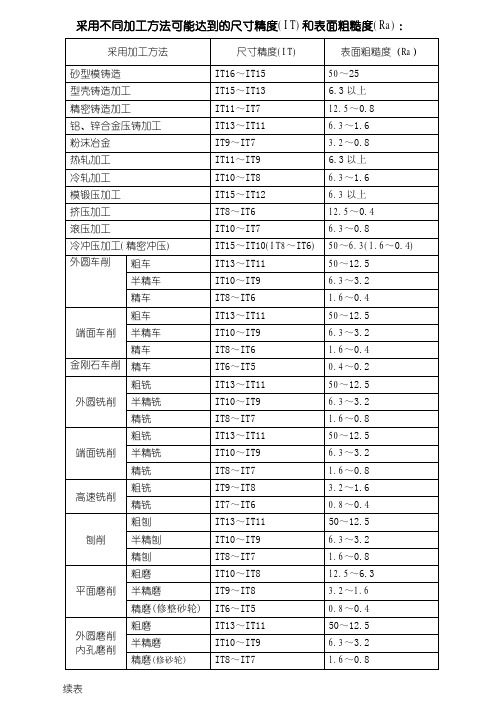
2.基本尺寸小于或等于 1mm 时无 IT14 至 IT18。
0.4~0.2
6.3~0.4
0.05~0.01 0.8~0.2 3.2~0.4 6.3~0.05 0.4~0.2 0.8~0.4 0.8~0.05 0.8~0.4 0.4~0.2 0.4~0.2 0.2~0.1
机械切削加工尺寸未注公差(單位:mm)
公称尺寸
f-精密级
0.5~3
±0.05
>3 ~6
±0.05
50~12.5 25~6.3 50~12.5 6.3~3.2 3.2~1.6 0.8~0.4 25~12.5 6.3~3.2 1.6~0.8 0.8~0.2 12.5~25 6.3~1.6 1.6~0.8 0.8~0.4 0.8~0.1 50~0.8 50~12.5
IT8~IT7 IT10~IT8 IT9~IT8
切削加工:粗加工:IT13~IT11 Ra:50~12.5 ; 半精加工:IT10~IT8 Ra:6.3~1.6 ; 精加工:IT7~IT5 Ra:0.8~0.2 ; 精密加工:IT5 以下 Ra:0.1~0.025 ; 超精加工:IT3 以下 Ra:0.025 以下的最光面.
1.粗糙面(如 Ra:50、25、12.5)的粗加工公差等级:T13~IT11,如粗车、粗铣、粗刨、 粗镗、毛锉、锯断、钻孔、倒角等,适用于没有配合要求的自由面; 2.半光面(如 Ra:6.3、3.2、1.6)的半精加工公差等级:IT10~IT8,如半精车、半精铣、半精镗、 粗磨、扩孔等,适用于接触面、不甚精确定心的配合面; 3.光面(如 Ra:0.8、0.4、0.2)的精加工公差等级:IT7~IT5,如精车、精拉、精铰、精铣、 精磨、座标磨、研磨、抛光等,适用于要求精确定心的重要配合面; 4.最光面(如 Ra:0.1、0.05、0.02)的超精加工公差等级:IT5 以下,如研磨、珩磨、超精磨、抛光、 镜面磨等,适用于高精度、高速运动的零部件的配合表、较重要的装饰面,如镜面模仁等;
加工中心精度标准

加工中心精度标准加工中心是一种高精度、高效率的加工设备,其精度标准直接影响着加工质量和加工效率。
在加工中心的使用过程中,我们需要对其精度标准有一个清晰的认识,以便更好地进行加工操作和质量控制。
首先,加工中心的精度标准包括了几个方面,其中最主要的包括定位精度、重复定位精度、加工精度和表面粗糙度。
定位精度是指加工中心在进行定位时的精确度,也就是工件在加工中心上的位置精度。
重复定位精度是指加工中心在多次定位后,再次回到原来位置时的精确度。
加工精度是指加工中心在进行切削加工时的加工精确度,也就是工件加工后的尺寸精度。
表面粗糙度是指加工中心加工后工件表面的粗糙度。
其次,加工中心的精度标准对加工质量有着直接的影响。
如果加工中心的精度标准不达标,就会导致加工出来的工件尺寸不准确,表面粗糙度大,甚至出现加工失误等问题,从而影响加工质量。
因此,我们在使用加工中心时,需要对其精度标准进行严格的把控,确保加工出来的工件符合要求。
另外,加工中心的精度标准也对加工效率有着重要的影响。
精度标准越高的加工中心,通常意味着加工效率越高,因为其可以更精确地进行加工操作,减少了加工调试的时间,提高了加工的效率。
而精度标准低的加工中心则可能需要更多的调试时间,加工效率相应地降低。
最后,为了确保加工中心的精度标准,我们需要做好日常的维护保养工作,定期进行设备的检测和校准,及时发现并排除设备的故障,保证设备处于良好的工作状态。
同时,我们还需要对加工中心的操作人员进行专业的培训,提高其对设备操作的熟练程度,减少人为因素对设备精度的影响。
综上所述,加工中心的精度标准对加工质量和加工效率有着重要的影响,我们需要对其有一个清晰的认识,并采取相应的措施来保证设备的精度标准,以便更好地进行加工操作和质量控制。
各种加工方法的加工精度

各种加工方法的加工精度一:车削车削中工件旋转,形成主切削运动。
刀具沿平行旋转轴线运动时,就形成内、外园柱面。
刀具沿与轴线相交的斜线运动,就形成锥面。
仿形车床或数控车床上,可以控制刀具沿着一条曲线进给,则形成一特定的旋转曲面。
采用成型车刀,横向进给时,也可加工出旋转曲面来。
车削还可以加工螺纹面、端平面及偏心轴等.车削加工精度一般为IT8—IT7,表面粗糙度为6。
3—1.6μm。
精车时,可达IT6—IT5,粗糙度可达0.4—0.1μm.车削的生产率较高,切削过程比较平稳,刀具较简单。
二:铣削主切削运动是刀具的旋转。
卧铣时,平面的形成是由铣刀的外园面上的刃形成的。
立铣时,平面是由铣刀的端面刃形成的。
提高铣刀的转速可以获得较高的切削速度,因此生产率较高.但由于铣刀刀齿的切入、切出,形成冲击,切削过程容易产生振动,因而限制了表面质量的提高。
这种冲击,也加剧了刀具的磨损和破损,往往导致硬质合金刀片的碎裂。
在切离工件的一般时间内,可以得到一定冷却,因此散热条件较好。
按照铣削时主运动速度方向与工件进给方向的相同或相反,又分为顺铣和逆铣。
顺铣铣削力的水平分力与工件的进给方向相同,工件台进给丝杠与固定螺母之间一般有间隙存在,因此切削力容易引起工件和工作台一起向前窜动,使进给量突然增大,引起打刀.在铣削铸件或锻件等表面有硬度的工件时,顺铣刀齿首先接触工件硬皮,加剧了铣刀的磨损。
逆铣可以避免顺铣时发生的窜动现象。
逆铣时,切削厚度从零开始逐渐增大,因而刀刃开始经历了一段在切削硬化的已加工表面上挤压滑行的阶段,加速了刀具的磨损。
同时,逆铣时,铣削力将工件上抬,易引起振动,这是逆铣的不利之处。
铣削的加工精度一般可达IT8—IT7,表面粗糙度为6.3—1。
6μm。
普通铣削一般只能加工平面,用成形铣刀也可以加工出固定的曲面。
数控铣床可以用软件通过数控系统控制几个轴按一定关系联动,铣出复杂曲面来,这时一般采用球头铣刀。
数控铣床对加工叶轮机械的叶片、模具的模芯和型腔等形状复杂的工件,具有特别重要的意义。
各种加工方法的经济精度和表面粗糙度
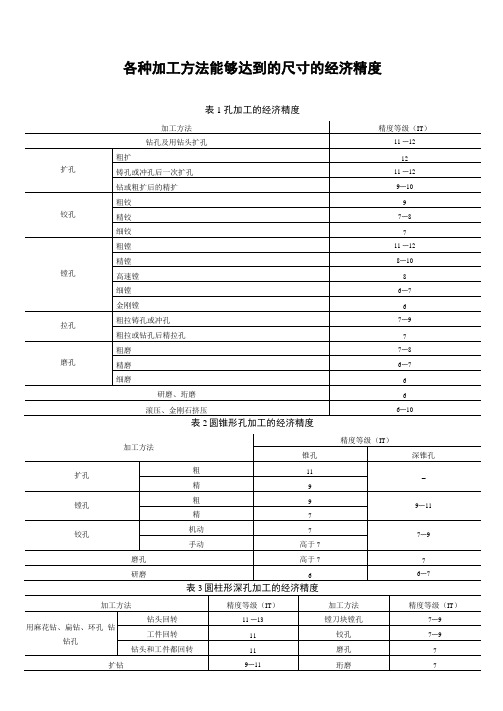
各种加工方法能够达到的尺寸的经济精度表1 孔加工的经济精度表2圆锥形孔加工的经济精度表3圆柱形深孔加工的经济精度6mm7mm91<1m2端铣刀铣削的加工精度在相同的条件下大体上比圆柱铣刀铣削高一级。
3细铣仅用于端铣刀铣削。
11各种加工方法能够达到的形状的经济精度2315各种加工方法所能够达到的相互位置的经济精度表19同轴度的经济精度表20 轴心线相互平行的孔的位置经济精度注:对于钻、卧镗及组合机床的镗孔偏差同样适用于铰孔。
表21轴心线相互垂直的孔的位置经济精度各种加工方法能够达到的零件表面粗糙度表22 各种加工方法能够达到的零件表面粗糙度各类型面的加工方案及经济精度表23外圆表面加工方案标准公差及形位公差附表1标准公差值1mm IT14IT1813 22-2-21 16:331 《金属机械加工工艺人员手册》修订本上海科学技术出版社1981年2 《机械制造工艺学》顾崇衔等编著陕西科学技术出版社1982年3 《航空机械设计手册》第三机械工业部612所编1979年4 《机械制造工艺学课程设计简明手册》华中工学院机械制造工艺教研室编1981年5 《机械工程手册》第46篇机械工业出版社1981年6 《圆柱齿轮加工》上海科学技术出版社1979年切削用量切削用量的选择原则正确地选择切削用量,对提高切削效率,保证必要的刀具耐用度和经济性,保证加工质量,具有重要的作用。
1粗加工切削用量的选择原则:粗加工时加工精度与表面求不高,毛坯余量较大。
因此,选择粗加工的切削用量时,要尽可能保证较高的单位时间金属切除量(金属切除率)和必要的刀具耐用度,以提高生产效率和降低加工成本。
金属切除率可以用下式计算:Z k vfa X1000式中Zw——单位时间内的金属切除量(mm3/s);v --- 切削速度(m/s);f --- 进给量(mm/r);a p -------- 切削深度(mm)。
提高切削速度、增大进给量和切削深度,都能提高金属切除率。
加工精度和表面粗糙度
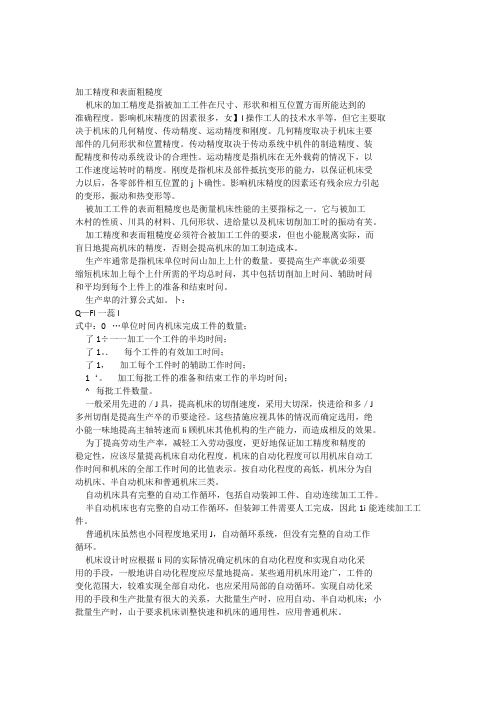
加工精度和表面粗糙度机床的加工精度是指被加工工件在尺寸、形状和相互位置方而所能达到的准确程度。
影响机床精度的因素很多,女】I操作工人的技术水半等,但它主要取决于机床的几何精度、传动精度、运动精度和刚度。
几何精度取决于机床主要部件的几伺形状和位置精度。
传动精度取决于传动系统中机件的制造精度、装配精度和传动系统设讣的合理性。
运动精度是指机床在无外载荷的情况下,以工作速度运转时的精度。
刚度是指机床及部件抵抗变形的能力,以保证机床受力以后,各零部件相互位置的j卜确性。
影响机床精度的因素还有残余应力引起的变形,振动和热变形等。
被加工工件的表而粗糙度也是衡量机床性能的主要指标之一。
它与被加工木村的性质、川具的材料、几伺形状、进给量以及机床切削加工时的振动有芙。
加工精度和表而粗糙度必须符合被加工工件的要求,但也小能脱离实际,而盲日地提高机床的精度,否则会提高机床的加工制造成本。
生产牢通常是指机床单位时问山加上上什的数量。
要提高生产率就必须要缩短机床加上每个上什所需的平均总时问,其中包括切削加上时问、辅助时问和平均到每个上件上的准备和结束时问。
生产卑的汁算公式如。
卜:Q—Fl一蕊l式中:0 …单位时间内机床完成工件的数量;了1÷一一加工一个工件的半均时间;了1。
.每个工件的有效加工时间;了1,加工每个工件时的辅助工作时间;1‘。
加工每批工件的准备和结束工作的半均时间;^ 每批工件数量。
一般采用先进的/J具,提高机床的切削速度,采用大切深,快进给和多/J多州切削是提高生产卒的币要途径。
这些措施应视具体的情况而确定选用,绝小能一味地提高主轴转速而li顾机床其他机构的生产能力,而造成相反的效果。
为丁提高劳动生产率,减轻工入劳动强度,更好地保证加工精度和精度的稳定性,应该尽量提高机床自动化程度。
机床的自动化程度可以用机床自动工作时间和机床的全部工作时间的比值表示。
按自动化程度的高低,机床分为自动机床、半自动机床和普通机床三类。